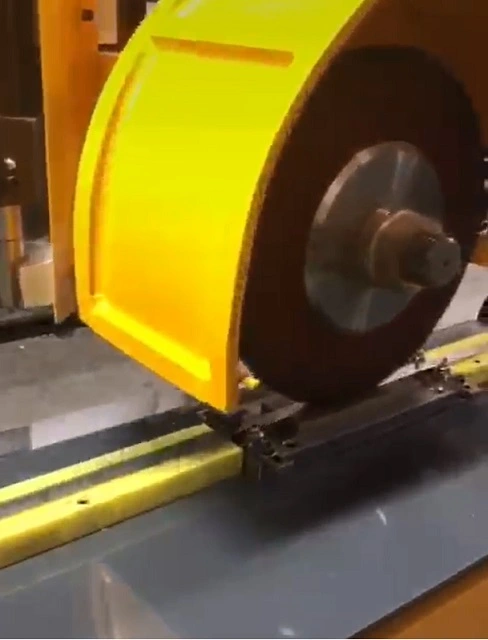
Flat bar polishing machine is an essential tool designed to polish the flat surfaces of metal bars used in various industries. These machines help in achieving a smooth, clean, and aesthetically pleasing finish, which is crucial for both functional and decorative applications. This article provides a comprehensive overview of flat bar polishing machines, their types, applications, benefits, and how to select and maintain them effectively.
1. What is a Flat Bar Polishing Machine?
A flat bar polishing machine is a device used to polish and finish the flat surfaces of metal bars, such as stainless steel, aluminum, brass, and other alloys. These machines typically feature abrasive belts, brushes, or discs that remove imperfections and create a polished surface. Key components of a flat bar polishing machine include:
- Polishing Heads: Equipped with abrasive materials for grinding and polishing.
- Control System: Allows operators to adjust speed, pressure, and other parameters.
- Support Frame: Holds the flat bar securely during polishing.
- Dust Collection System: Captures debris and ensures a clean working environment.
2. Types of Flat Bar Polishing Machines
- Manual vs. Automatic: Manual machines require operator intervention, while automatic machines operate based on programmed settings.
- Portable vs. Stationary: Portable machines can be moved to different locations, while stationary machines are fixed in one place.
- Specialized Machines: Designed for specific materials and finishes, ensuring optimal performance and quality.
3. Applications of Flat Bar Polishing Machines
Flat bar polishing machines are utilized across various industries, including:
- Metalworking: Polishing metal bars for structural and decorative purposes.
- Construction: Finishing flat bars used in building frameworks and structures.
- Automotive: Polishing components like trim pieces and structural bars.
- Aerospace: Ensuring high-quality finishes for aerospace components. Examples include polishing stainless steel bars for architectural features, aluminum bars for automotive trim, and brass bars for decorative elements.
4. How Flat Bar Polishing Machines Work
The process of flat bar polishing typically involves several steps:
- Preparation: Inspecting the flat bar and setting up the machine.
- Initial Polishing: Using coarse abrasives to remove imperfections and rough spots.
- Intermediate Polishing: Switching to finer abrasives for a smoother surface.
- Final Polishing: Applying the finest abrasives or polishing compounds to achieve a mirror-like finish.
- Inspection and Finishing: Checking the quality and applying any protective coatings if necessary. Technologies used include mechanical polishing, chemical polishing, and electropolishing, each suited for different materials and surface requirements.
5. Benefits of Using Flat Bar Polishing Machines
- Improved Surface Finish and Cleanliness: Ensures the flat bars are free from contaminants and defects.
- Enhanced Durability and Lifespan: Regular polishing prevents corrosion and wear, extending the life of the bars.
- Compliance with Industry Standards: Meets the rigorous standards of industries like construction, automotive, and aerospace, ensuring safety and quality.
- Increased Efficiency: Automating the polishing process can save time and labor costs.
6. Selecting the Right Flat Bar Polishing Machine
When choosing a flat bar polishing machine, consider the following factors:
- Material and Size of Flat Bar: Ensure the machine can handle the specific material and dimensions.
- Industry Requirements: Different industries have unique standards and requirements.
- Budget and Cost-Effectiveness: Balance the initial investment with long-term benefits and return on investment.
- Manufacturer Support and Warranty: Choose reputable manufacturers that offer good customer support and warranty options. Tips for selection include consulting with industry experts, reviewing customer testimonials, and comparing different models’ features and specifications.
7. Maintenance and Safety Tips
- Regular Maintenance: Inspect and replace worn parts regularly, clean the machine after use, and ensure all components are in good working condition.
- Safety Measures: Train operators on proper usage, wear appropriate personal protective equipment (PPE), and follow manufacturer guidelines to prevent accidents.
- Best Practices: Conduct regular inspections, keep a maintenance log, and update machine software if applicable.
8. Leading Manufacturers and Models
Several manufacturers are renowned for producing high-quality flat bar polishing machines, including:
- XYZ Corp: Known for their robust and reliable machines.
- ABC Ltd.: Offers a range of models with advanced features.
- DEF Industries: Specializes in customizable machines for various industries. Notable models include the XYZ5000, ABC200, and DEF1000, each praised for their efficiency, ease of use, and durability. Features to look for include automated controls, high-quality abrasives, and effective dust collection systems.
Conclusion
Flat bar polishing machines are vital tools for maintaining the integrity, cleanliness, and durability of flat bars used in various industrial applications. By understanding the different types, applications, and benefits of these machines, businesses can make informed decisions that enhance their operational efficiency and product quality. Regular maintenance and adherence to safety protocols ensure the long-term performance and reliability of these machines, making them a worthwhile investment for any industry relying on high-quality flat bar finishes.
Flat bar polishing machines are specialized tools designed to polish the surfaces of flat bars made from various materials, including stainless steel, aluminum, and other alloys. These machines are essential in industries where the surface quality, appearance, and hygiene of flat bars are critical. This article explores the components, workings, advantages, and applications of flat bar polishing machines.
What is a Flat Bar Polishing Machine?
A flat bar polishing machine is used to achieve a smooth, high-quality finish on the surfaces of flat bars. These machines utilize abrasive belts, wheels, or brushes to remove imperfections and enhance the surface finish. The goal is to produce flat bars that meet industry standards for appearance and functionality.
Components of a Flat Bar Polishing Machine
- Main Frame: Provides structural support and stability for the machine.
- Motor: Powers the abrasive belts, wheels, or brushes.
- Abrasive Tools: Belts, wheels, or brushes that perform the polishing action.
- Workpiece Holders: Secure the flat bar in place during polishing.
- Conveyor System: Moves the flat bars through the machine for continuous polishing.
- Control System: Manages speed, pressure, and movement of the abrasive tools.
- Coolant System: Reduces heat generated during polishing.
- Dust Collection System: Captures dust and debris generated during the process.
- Safety Features: Includes protective guards, emergency stop buttons, and safety interlocks.
How a Flat Bar Polishing Machine Works
- Setup: The flat bar is secured on the conveyor system or workpiece holders.
- Abrasive Selection: Appropriate abrasive belts, wheels, or brushes are chosen based on the material and desired finish.
- Polishing Process: The motor powers the abrasive tools, which are applied to the flat bar’s surface as it moves through the machine.
- Inspection and Finishing: The polished flat bar is inspected for quality, and any necessary touch-ups are performed.
- Cleaning: The flat bar is cleaned to remove any remaining polishing residues.
Types of Flat Bar Polishing Machines
- Automatic Flat Bar Polishing Machines: Fully automated systems for high-volume production with minimal human intervention.
- Semi-Automatic Flat Bar Polishing Machines: Require some manual setup and operation but offer automated polishing cycles.
- Portable Flat Bar Polishers: Smaller, mobile units for on-site or smaller-scale operations.
Advantages of Using Flat Bar Polishing Machines
- Improved Surface Finish: Achieves a smooth, reflective surface that meets industry standards.
- Hygiene and Cleanliness: Essential for industries like food and pharmaceuticals where cleanliness is critical.
- Efficiency: High-speed operation reduces processing time and labor costs.
- Consistency: Automated machines ensure uniform quality across batches.
- Versatility: Suitable for a wide range of flat bar sizes and materials.
Applications of Flat Bar Polishing Machines
Flat bar polishing machines are used in various industries, including:
- Construction and Architecture: Polishing flat bars used in structural components, railings, and decorative elements.
- Automotive: Finishing flat bars used in vehicle frames, bumpers, and other components.
- Food and Beverage: Polishing flat bars used in equipment and machinery to meet hygiene standards.
- Pharmaceuticals: Ensuring flat bars meet strict hygiene and surface finish standards for medical equipment.
- Metalworking: Polishing flat bars used in tools, machinery, and equipment.
- Aerospace: Polishing flat bars used in aircraft structures and systems.
Safety Considerations
Operating flat bar polishing machines involves several safety risks. Adhering to safety protocols is crucial:
- Training: Operators must be adequately trained in the machine’s operation and safety procedures.
- Protective Equipment: Use of appropriate personal protective equipment (PPE), such as gloves, goggles, and masks.
- Regular Maintenance: Ensures the machinery operates safely and efficiently.
- Coolant and Dust Collection: Proper systems to prevent overheating and control airborne particles.
- Emergency Procedures: Clear guidelines for handling emergencies, including fire suppression systems.
Future Trends and Innovations
The future of flat bar polishing machines looks promising with ongoing technological advancements:
- Automation and CNC Technology: Increasing use of computerized controls for higher precision and efficiency.
- Eco-Friendly Technologies: Development of more sustainable and environmentally friendly processes.
- Advanced Abrasive Materials: New abrasive materials that offer better performance and durability.
- Smart Manufacturing: Integration of IoT and AI for real-time monitoring and optimization.
Conclusion
Flat bar polishing machines are essential in modern manufacturing and material processing, enabling the production of high-quality, smooth, and aesthetically pleasing flat bars. Their applications span various industries where surface quality and cleanliness are critical. As technology continues to advance, flat bar polishing machines will play an increasingly significant role in meeting the demands for superior surface finishes and driving innovation in manufacturing processes.
EMS Metalworking Machines
We design, manufacture and assembly metalworking machinery such as:
- Hydraulic transfer press
- Glass mosaic press
- Hydraulic deep drawing press
- Casting press
- Hydraulic cold forming press
- Hydroforming press
- Composite press
- Silicone rubber moulding press
- Brake pad press
- Melamine press
- SMC & BMC Press
- Labrotaroy press
- Edge cutting trimming machine
- Edge curling machine
- Trimming beading machine
- Trimming joggling machine
- Cookware production line
- Pipe bending machine
- Profile bending machine
- Bandsaw for metal
- Cylindrical welding machine
- Horizontal pres and cookware
- Kitchenware, hotelware
- Bakeware and cuttlery production machinery
as a complete line as well as an individual machine such as:
- Edge cutting trimming beading machines
- Polishing and grinding machines for pot and pans
- Hydraulic drawing presses
- Circle blanking machines
- Riveting machine
- Hole punching machines
- Press feeding machine
You can check our machinery at work at: EMS Metalworking Machinery – YouTube
Applications:
- Beading and ribbing
- Flanging
- Trimming
- Curling
- Lock-seaming
- Ribbing
- Flange-punching
The Importance of Sheet Metal Machinery
Sheet metal machinery is vital for several reasons:
- Versatility: Sheet metal machinery can handle various types of metals, including steel, aluminum, copper, and brass, allowing manufacturers to create diverse products.
- Precision: Advanced machinery enables precise cutting and shaping, ensuring high-quality products with minimal errors.
- Efficiency: Automation and CNC technology have significantly improved production speed and efficiency, reducing labor costs and increasing output.
- Customization: Modern machinery allows for customization and flexibility in design, meeting the specific needs of different industries.
The historical evolution of sheet metal machinery reflects the broader trends in industrialization and technological advancement. From the development of simple tools to the introduction of computer numerical control (CNC) systems, the journey of sheet metal machinery is a testament to human ingenuity and innovation.
Section 2: Types of Sheet Metal Machinery
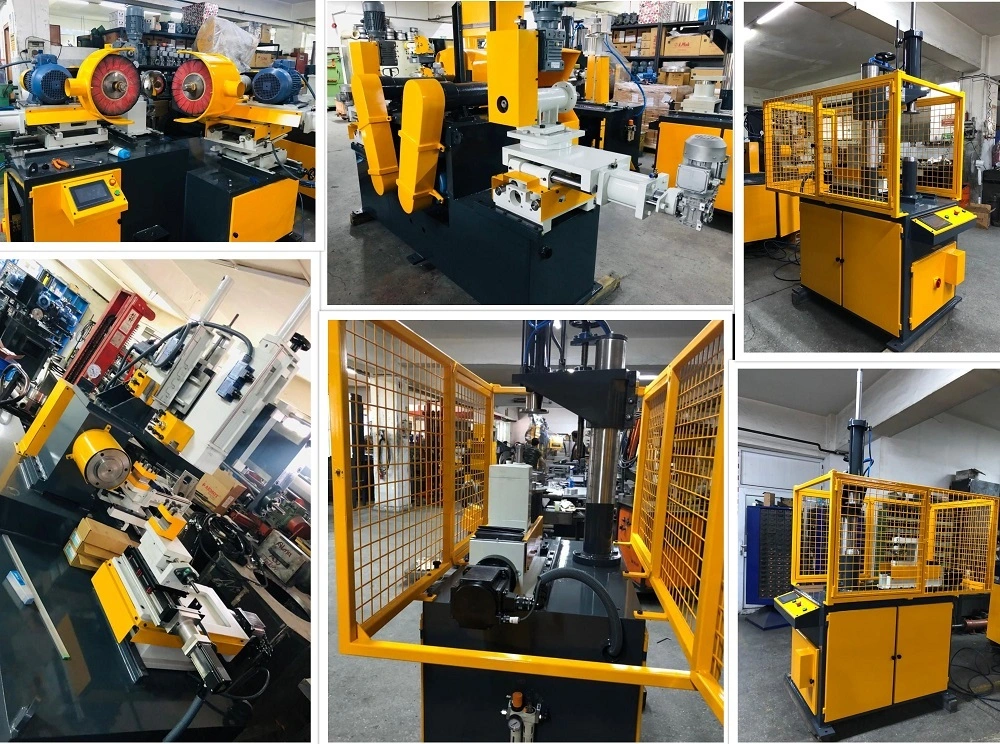
Sheet metal machinery encompasses a wide range of equipment designed to perform specific tasks in the metalworking process. Understanding the different types of machinery is essential for selecting the right tools for a particular application. This section explores the various types of sheet metal machinery and their functions.
Cutting Machines
Cutting machines are designed to slice through sheet metal with precision and speed. Key types include:
- Shearing Machines: Shearing machines use a blade to cut straight lines in metal sheets. They are ideal for producing square or rectangular shapes and are commonly used in the initial stages of metal processing.
- Laser Cutting Machines: Utilizing a focused laser beam, laser cutting machines offer high precision and are suitable for cutting complex shapes and patterns. They are widely used in industries requiring intricate designs, such as aerospace and automotive.
- Plasma Cutters: Plasma cutters use a jet of ionized gas to cut through electrically conductive materials. They are effective for cutting thick sheets of metal and are often used in industrial applications.
- Waterjet Cutters: Waterjet cutters use a high-pressure stream of water mixed with abrasive materials to cut metal. They are ideal for cutting heat-sensitive materials as they do not generate heat during the process.
Bending Machines
Bending machines are used to deform metal sheets into specific angles and shapes. Key types include:
- Press Brakes: Press brakes are versatile machines used to bend sheet metal by pressing it between a punch and a die. They are suitable for creating V-shaped, U-shaped, and custom profiles.
- Folding Machines: Folding machines are designed to fold sheet metal along a straight line. They are commonly used in the production of panels, enclosures, and boxes.
- Roll Bending Machines: Roll bending machines use rollers to bend metal sheets into curved shapes. They are ideal for creating cylindrical objects, such as pipes and tanks.
Forming Machines
Forming machines are used to shape metal sheets into specific forms. Key types include:
- Stamping Machines: Stamping machines use a die to shape metal sheets into specific forms. They are commonly used in mass production and are suitable for creating components with complex shapes.
- Punching Machines: Punching machines use a punch and die to create holes in metal sheets. They are widely used in the production of metal parts and components.
- Deep Drawing Machines: Deep drawing machines are used to form metal sheets into deep, hollow shapes. They are commonly used in the production of containers, automotive parts, and kitchenware.
Other Specialized Equipment
- CNC Machines: CNC machines are computer-controlled systems that automate the machining process. They offer high precision and are suitable for complex and repetitive tasks.
- Turret Punches: Turret punches are versatile machines used to punch holes in metal sheets. They are equipped with multiple tools, allowing for quick tool changes and increased efficiency.
- Hydraulic Presses: Hydraulic presses use hydraulic force to shape and form metal sheets. They are suitable for tasks requiring high force and precision.
Section 3: Technological Advancements in Sheet Metal Machinery
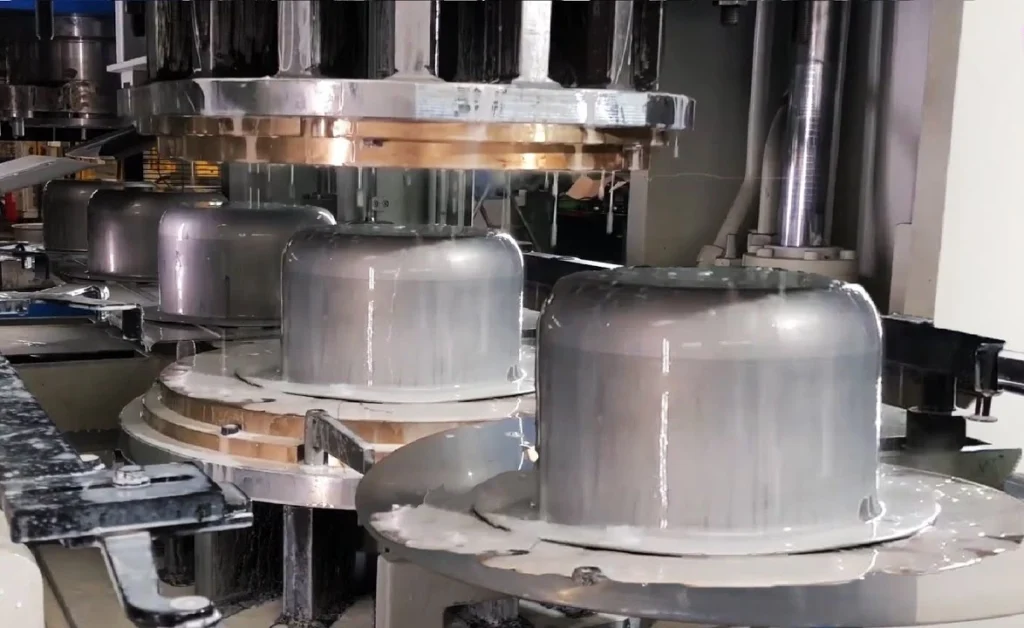
The sheet metal machinery industry has seen significant technological advancements in recent years, driven by the need for increased efficiency, precision, and automation. This section explores some of the key technological innovations shaping the industry.
CNC Technology and Automation
Computer numerical control (CNC) technology has revolutionized sheet metal machinery by automating the machining process. CNC machines are programmed with specific instructions, allowing for precise and consistent production. The benefits of CNC technology include:
- Increased Precision: CNC machines can achieve high levels of precision, reducing errors and improving product quality.
- Enhanced Efficiency: Automation reduces the need for manual labor, increasing production speed and efficiency.
- Flexibility: CNC machines can be easily reprogrammed to accommodate different tasks, making them ideal for small and large-scale production.
Integration of AI and IoT
The integration of artificial intelligence (AI) and the Internet of Things (IoT) is transforming sheet metal machinery by enabling smart manufacturing. Key benefits include:
- Predictive Maintenance: IoT sensors can monitor machine performance and predict maintenance needs, reducing downtime and extending equipment lifespan.
- Quality Control: AI algorithms can analyze production data to identify defects and improve quality control processes.
- Data-Driven Decision Making: Real-time data from IoT devices can inform decision-making, optimizing production processes and resource allocation.
Energy-Efficient Machines
With increasing environmental concerns, the demand for energy-efficient sheet metal machinery is on the rise. Manufacturers are developing machines that consume less energy while maintaining high performance. Key features include:
- Energy-Efficient Motors: Modern machines are equipped with energy-efficient motors that reduce power consumption.
- Advanced Control Systems: Advanced control systems optimize machine operations, minimizing energy waste.
Section 4: Applications of Sheet Metal Machinery
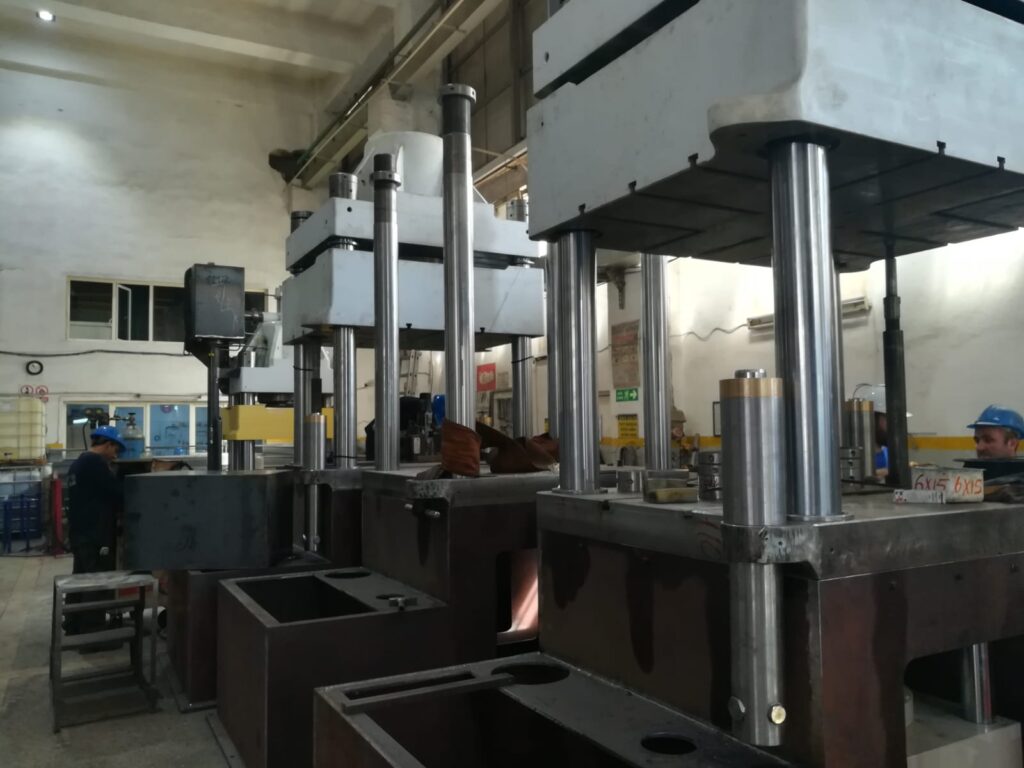
Sheet metal machinery is used in various industries, each with specific applications and requirements. This section explores some of the key industries and their use of sheet metal machinery.
Automotive Industry
The automotive industry relies heavily on sheet metal machinery for the production of vehicle components. Key applications include:
- Body Panels: Sheet metal machinery is used to produce body panels, such as doors, hoods, and fenders, ensuring high precision and quality.
- Chassis Components: Bending and forming machines create chassis components, providing structural integrity and support.
Aerospace and Defense
The aerospace and defense industries require high precision and quality in their components. Sheet metal machinery is used for:
- Aircraft Structures: Cutting and forming machines produce aircraft structures, such as wings and fuselage components, ensuring safety and performance.
- Defense Equipment: Sheet metal machinery is used to produce components for defense equipment, such as armored vehicles and weapons systems.
Construction and Architecture
In the construction and architecture industries, sheet metal machinery is used to produce a wide range of products, including:
- Architectural Panels: Cutting and bending machines create architectural panels used in building facades and interiors.
- HVAC Systems: Sheet metal machinery produces components for HVAC systems, ensuring efficient heating, ventilation, and air conditioning.
Consumer Electronics
The consumer electronics industry relies on sheet metal machinery for the production of components such as:
- Enclosures: Cutting and forming machines create enclosures for electronic devices, providing protection and aesthetics.
- Heat Sinks: Sheet metal machinery produces heat sinks, which dissipate heat and ensure the proper functioning of electronic components.
Section 5: Key Manufacturers and Market Leaders
The sheet metal machinery industry is highly competitive, with several key manufacturers leading the market. This section highlights some of the top companies and their contributions to the industry.
Trumpf Group
Trumpf Group is a global leader in sheet metal machinery, known for its innovative solutions and high-quality products. Key offerings include:
- Laser Cutting Machines: Trumpf is a pioneer in laser cutting technology, providing machines with high precision and efficiency.
- Punching Machines: Trumpf’s punching machines are known for their versatility and automation capabilities.
Amada Co., Ltd.
Amada is a leading manufacturer of sheet metal machinery, offering a wide range of equipment for various applications. Key products include:
- Press Brakes: Amada’s press brakes are renowned for their precision and reliability, catering to the needs of diverse industries.
- Bending Machines: Amada provides advanced bending machines with innovative features, enhancing productivity and efficiency.
Bystronic Group
Bystronic Group is a prominent player in the sheet metal machinery market, focusing on cutting and bending solutions. Key offerings include:
- CNC Laser Cutting Machines: Bystronic’s CNC laser cutting machines are known for their precision and speed, meeting the demands of modern manufacturing.
- Press Brakes: Bystronic’s press brakes offer advanced automation and control, improving production efficiency.
Salvagnini Group
Salvagnini Group specializes in automated sheet metal processing solutions, providing a comprehensive range of machinery. Key products include:
- Automated Bending Machines: Salvagnini’s automated bending machines offer high precision and efficiency, reducing labor costs and increasing output.
- Flexible Manufacturing Systems: Salvagnini’s flexible manufacturing systems integrate various processes, streamlining production and improving flexibility.
Section 6: Selecting the Right Sheet Metal Machinery
Choosing the right sheet metal machinery is crucial for ensuring optimal performance and efficiency in manufacturing processes. This section outlines key factors to consider when selecting sheet metal machinery.
Material Type
The type of material being processed is a critical consideration when selecting sheet metal machinery. Different materials have varying properties, such as thickness, hardness, and ductility, which can impact machine performance. It is essential to choose machinery that can handle the specific materials used in production.
Precision and Accuracy
Precision and accuracy are vital factors in producing high-quality products. CNC machines offer high levels of precision, making them suitable for applications requiring intricate designs and tight tolerances. Manufacturers should consider the precision requirements of their applications when selecting machinery.
Volume and Production Capacity
The production volume and capacity of the machinery should align with the manufacturing needs. High-volume production may require automated machinery with fast processing speeds, while smaller production runs may benefit from flexible and versatile machines.
Cost Analysis and Budgeting
Cost is a significant consideration when selecting sheet metal machinery. Manufacturers should conduct a cost analysis to determine the total cost of ownership, including initial investment, maintenance, and operational costs. Budgeting should account for the long-term benefits of investing in high-quality machinery.
Maintenance and Support Considerations
Regular maintenance is essential for ensuring the longevity and performance of sheet metal machinery. Manufacturers should consider the availability of maintenance services and support when selecting machinery. Choosing machines with readily available spare parts and technical support can minimize downtime and ensure smooth operations.
Section 7: Safety and Environmental Considerations
Safety and environmental considerations are paramount in the sheet metal machinery industry. This section explores the key safety standards and environmental practices manufacturers should adhere to.
Safety Standards and Best Practices
Safety is a top priority in the sheet metal machinery industry, as the equipment can pose significant risks to operators. Key safety standards and best practices include:
- Operator Training: Operators should receive comprehensive training on machine operation, safety protocols, and emergency procedures.
- Machine Guarding: Machines should be equipped with guards and safety features to protect operators from moving parts and potential hazards.
- Regular Inspections: Regular inspections and maintenance can identify potential safety issues and ensure machines operate safely.
Environmental Impact and Sustainability
The sheet metal machinery industry has an impact on the environment, with energy consumption and waste generation being key concerns. Manufacturers can adopt sustainable practices to minimize their environmental footprint:
- Energy Efficiency: Using energy-efficient machinery can reduce power consumption and lower carbon emissions.
- Waste Reduction: Implementing recycling and waste reduction programs can minimize the environmental impact of manufacturing processes.
- Sustainable Materials: Choosing sustainable materials and suppliers can contribute to a more environmentally friendly supply chain.
Section 8: Challenges and Future Trends
The sheet metal machinery industry faces several challenges, but it also presents opportunities for innovation and growth. This section explores the current challenges and future trends in the industry.
Current Challenges
- Skilled Labor Shortage: The industry faces a shortage of skilled labor, with an aging workforce and a lack of new talent entering the field. Manufacturers must invest in training and development programs to address this issue.
- Rising Material Costs: Fluctuations in material costs can impact manufacturing profitability. Manufacturers should implement cost-effective strategies to mitigate the effects of rising material costs.
- Supply Chain Disruptions: Global supply chain disruptions can impact the availability of raw materials and components, affecting production timelines and costs.
Future Trends
- Automation and Industry 4.0: Automation and Industry 4.0 technologies will continue to drive innovation in the sheet metal machinery industry, improving efficiency and productivity.
- Sustainability and Green Manufacturing: The demand for sustainable and environmentally friendly manufacturing practices will increase, driving the development of energy-efficient machinery and processes.
- Advanced Materials: The use of advanced materials, such as composites and lightweight alloys, will expand, requiring new machinery and techniques for processing.
Section 9: Conclusion
Sheet metal machinery is a vital component of modern manufacturing, enabling the production of a wide range of products across various industries. With advancements in technology and automation, sheet metal machinery continues to evolve, offering increased precision, efficiency, and flexibility.
As manufacturers face challenges such as skilled labor shortages and rising material costs, innovation and adaptation will be crucial for success. By embracing new technologies and sustainable practices, manufacturers can overcome these challenges and capitalize on emerging opportunities.
The future of sheet metal machinery is bright, with continued advancements in automation, AI, and sustainable manufacturing practices shaping the industry. As the demand for high-quality and environmentally friendly products grows, sheet metal machinery will play a key role in meeting these needs and driving the future of manufacturing.
Section 5: Top Features Comparison of Sheet Metal Machinery
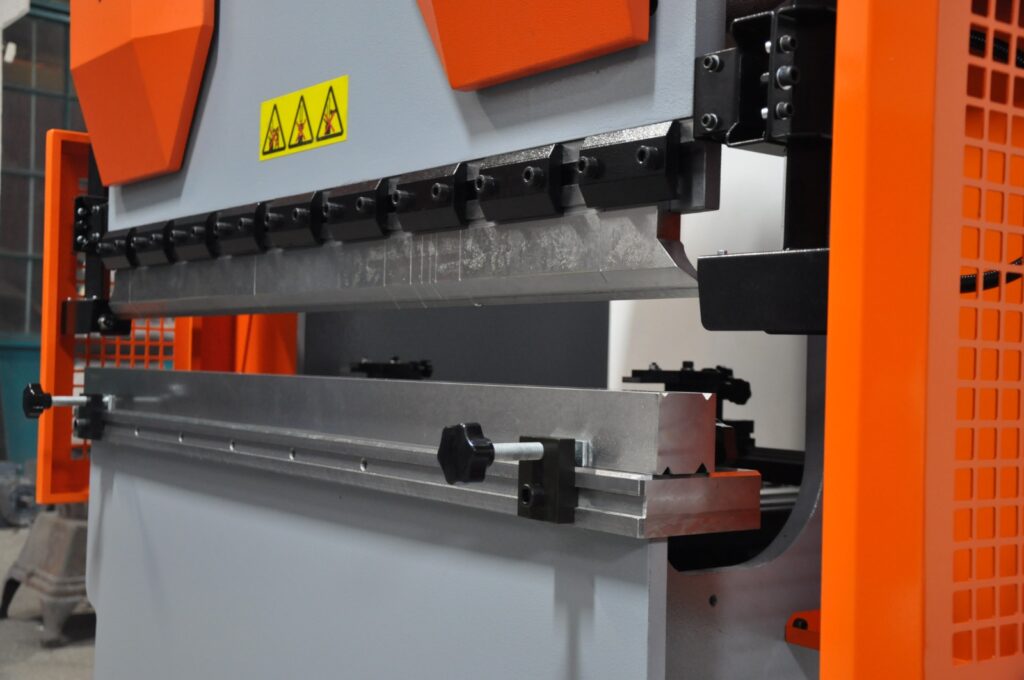
Selecting the right sheet metal machinery is critical for optimizing production processes and achieving desired outcomes. With a variety of machinery types available, understanding their features can guide manufacturers in choosing the best equipment for their specific needs. This section compares the top features of key sheet metal machinery, focusing on cutting, bending, and forming machines, as well as specialized equipment.
Cutting Machines: Feature Comparison
Cutting machines are essential for slicing sheet metal into desired shapes and sizes. The most common types include laser cutters, plasma cutters, and waterjet cutters. Here’s how they compare:
1. Laser Cutting Machines
- Precision: Laser cutting machines are known for their high precision, capable of achieving tight tolerances and intricate designs. They are ideal for applications requiring detailed work, such as electronics and aerospace components.
- Speed: These machines offer fast cutting speeds, making them suitable for high-volume production.
- Material Compatibility: Laser cutters work well with a variety of metals, including steel, aluminum, and titanium. However, they may not be suitable for thicker materials.
- Cost: Generally more expensive than other cutting methods, but the precision and efficiency can justify the investment for specific applications.
2. Plasma Cutters
- Thickness Handling: Plasma cutters excel at cutting through thick materials, making them ideal for heavy-duty applications like shipbuilding and construction.
- Speed: They offer fast cutting speeds but may not match the precision of laser cutters.
- Material Compatibility: Suitable for cutting electrically conductive metals such as steel, stainless steel, and aluminum.
- Cost: More affordable than laser cutters, making them a popular choice for many industrial applications.
3. Waterjet Cutters
- Versatility: Waterjet cutters can cut a wide range of materials, including metal, stone, glass, and composites, without causing thermal distortion.
- Precision: They offer high precision and smooth edges, suitable for detailed work and sensitive materials.
- Environmental Impact: Waterjet cutting is a clean process that does not produce hazardous waste or fumes.
- Cost: While initial costs can be high, the versatility and environmental benefits make them an attractive option for diverse applications.
Bending Machines: Feature Comparison
Bending machines are used to deform sheet metal into specific shapes. The main types include press brakes, folding machines, and roll bending machines. Here’s a comparison of their features:
1. Press Brakes
- Versatility: Press brakes are highly versatile, capable of producing a wide range of shapes and angles. They are used in automotive, aerospace, and construction industries.
- Precision: Modern press brakes with CNC control offer high precision and repeatability, ensuring consistent results.
- Material Thickness: Suitable for bending various material thicknesses, making them adaptable to different projects.
- Automation: Many press brakes come with automated features, reducing setup time and increasing efficiency.
2. Folding Machines
- Ease of Use: Folding machines are user-friendly, often requiring less operator expertise compared to press brakes.
- Speed: They offer fast processing times, making them suitable for high-volume production.
- Material Handling: Folding machines are ideal for thin and medium-thickness materials, commonly used in HVAC and sheet metal fabrication.
- Customization: They provide flexibility in folding complex profiles, catering to specific design requirements.
3. Roll Bending Machines
- Curved Shapes: Roll bending machines specialize in creating cylindrical and curved shapes, such as pipes and tanks.
- Material Thickness: Suitable for handling thick materials, making them ideal for heavy-duty applications.
- Efficiency: They offer efficient processing of long metal sheets, reducing material waste.
- Automation: Some roll bending machines come with CNC capabilities, enhancing precision and control.
Forming Machines: Feature Comparison
Forming machines shape metal sheets into specific forms. Key types include stamping machines, punching machines, and deep drawing machines. Here’s how they compare:
1. Stamping Machines
- Mass Production: Stamping machines are ideal for mass production, offering high-speed processing and consistency.
- Complex Shapes: Capable of producing complex shapes with multiple operations in a single pass.
- Tooling Costs: High initial tooling costs, but cost-effective for large production runs.
- Automation: Highly automated, reducing labor costs and increasing efficiency.
2. Punching Machines
- Precision: Punching machines offer high precision and accuracy, suitable for creating holes and intricate patterns.
- Flexibility: Equipped with multiple tools, allowing for quick tool changes and diverse applications.
- Speed: Fast processing speeds, making them ideal for high-volume production.
- Material Handling: Suitable for various materials, including steel, aluminum, and copper.
3. Deep Drawing Machines
- Hollow Shapes: Deep drawing machines specialize in creating deep, hollow shapes, such as containers and automotive parts.
- Material Utilization: Efficient material utilization, minimizing waste.
- Complex Designs: Capable of producing complex designs with smooth surfaces and high precision.
- Automation: Many deep drawing machines offer automation features, enhancing productivity and reducing labor costs.
Specialized Equipment: Feature Comparison
Specialized sheet metal machinery includes CNC machines, turret punches, and hydraulic presses. Here’s a comparison of their features:
1. CNC Machines
- Precision and Accuracy: CNC machines offer unparalleled precision and accuracy, suitable for complex and repetitive tasks.
- Automation: Fully automated, reducing the need for manual labor and increasing efficiency.
- Flexibility: Easily reprogrammable for different tasks, making them adaptable to changing production needs.
- Cost: High initial investment, but the benefits of automation and precision can outweigh the costs for many applications.
2. Turret Punches
- Versatility: Turret punches are versatile, equipped with multiple tools for punching, nibbling, and forming operations.
- Speed: High-speed processing, ideal for mass production.
- Tool Changes: Quick tool changes increase efficiency and reduce downtime.
- Material Handling: Suitable for various materials, including thin and medium-thickness sheets.
3. Hydraulic Presses
- Force and Power: Hydraulic presses offer high force and power, suitable for heavy-duty forming and shaping tasks.
- Precision: Modern hydraulic presses provide high precision and control, ensuring consistent results.
- Versatility: Adaptable to various applications, including forming, bending, and punching.
- Automation: Many hydraulic presses offer automated features, enhancing productivity and efficiency.
Conclusion
When selecting sheet metal machinery, manufacturers must carefully evaluate the features and capabilities of each type of equipment. Key considerations include precision, speed, material compatibility, and automation. By understanding the unique features of cutting, bending, and forming machines, as well as specialized equipment, manufacturers can choose the best tools to meet their specific production needs and optimize their operations.
Section 6: Most Widely Used Sheet Metal Machines

In the sheet metal industry, various machines are used for cutting, bending, forming, and shaping metal sheets into specific products and components. While the selection of machines depends on the specific needs and requirements of a manufacturing operation, certain machines stand out as being the most widely used across industries due to their versatility, efficiency, and reliability. This section explores the most popular sheet metal machines and their key features and applications.
1. Laser Cutting Machines
Overview:
Laser cutting machines are among the most widely used machines in the sheet metal industry. They use a focused laser beam to cut materials with high precision and speed. These machines are ideal for intricate designs and complex shapes.
Key Features:
- High Precision: Laser cutters provide exceptional precision, allowing for intricate designs and tight tolerances.
- Speed: They offer rapid cutting speeds, making them suitable for high-volume production.
- Versatility: Laser cutting machines can work with various materials, including steel, aluminum, brass, and titanium.
- Minimal Waste: The precision of laser cutting results in minimal material waste.
Applications:
- Automotive Industry: Used for cutting intricate parts and components, such as gears, brackets, and panels.
- Aerospace: Ideal for cutting complex shapes in aircraft components.
- Electronics: Used to create precise enclosures and intricate circuit board designs.
Why Popular:
Laser cutting machines are favored for their precision, speed, and versatility. They are essential in industries requiring high accuracy and complex designs.
2. Press Brakes
Overview:
Press brakes are essential machines for bending sheet metal into specific shapes and angles. They are used across various industries due to their versatility and precision.
Key Features:
- Versatility: Capable of bending a wide range of materials and thicknesses.
- Precision: Modern press brakes with CNC control offer high precision and repeatability.
- Automation: Equipped with automated features that reduce setup time and enhance productivity.
- Customizable: Press brakes can be customized with different tools and dies to accommodate various bending tasks.
Applications:
- Automotive: Used to bend chassis components, brackets, and other structural parts.
- Construction: Employed in creating metal frameworks, support beams, and architectural elements.
- HVAC: Used for forming ducts, vents, and other heating and cooling components.
Why Popular:
Press brakes are highly popular due to their versatility, precision, and ability to handle various bending tasks. They are indispensable in manufacturing operations that require custom bends and angles.
3. CNC Punching Machines
Overview:
CNC punching machines are used to create holes and shapes in sheet metal by using a punch and die. They offer high precision and speed, making them ideal for mass production.
Key Features:
- Automation: CNC control allows for automated punching processes, reducing the need for manual labor.
- High Precision: Capable of achieving tight tolerances and intricate designs.
- Flexibility: Equipped with multiple tools for various punching and forming operations.
- Efficiency: Offers fast processing speeds and quick tool changes.
Applications:
- Appliances: Used to create precise holes and shapes in appliance components.
- Electronics: Employed in creating enclosures and metal parts for electronic devices.
- Automotive: Used for producing various components, such as brackets and support structures.
Why Popular:
CNC punching machines are widely used for their speed, precision, and automation capabilities. They are essential for manufacturers seeking efficiency and high-quality results in mass production.
4. Hydraulic Shearing Machines
Overview:
Hydraulic shearing machines are used to cut sheet metal into specific sizes and shapes. They offer robust performance and are suitable for cutting thick materials.
Key Features:
- Powerful Cutting: Hydraulic shears provide strong cutting force, allowing them to handle thick and heavy materials.
- Precision: Equipped with advanced control systems for precise cutting.
- Versatility: Suitable for cutting various metals, including steel, aluminum, and copper.
- Safety Features: Designed with safety mechanisms to protect operators during operation.
Applications:
- Construction: Used for cutting metal sheets for structural components and frameworks.
- Shipbuilding: Employed in cutting thick steel plates for ship hulls and decks.
- Metal Fabrication: Used for producing custom-sized sheets for various applications.
Why Popular:
Hydraulic shearing machines are popular for their power, precision, and ability to handle thick materials. They are essential in industries requiring robust cutting capabilities.
5. Waterjet Cutting Machines
Overview:
Waterjet cutting machines use a high-pressure jet of water mixed with abrasive materials to cut sheet metal. They are known for their versatility and environmental benefits.
Key Features:
- Cold Cutting: Waterjet cutting does not generate heat, preventing thermal distortion of materials.
- Versatility: Capable of cutting a wide range of materials, including metals, stone, glass, and composites.
- Precision: Offers high precision and smooth edges, suitable for detailed work.
- Environmental Impact: Produces minimal waste and does not emit harmful fumes.
Applications:
- Aerospace: Used for cutting complex shapes in aircraft components and materials.
- Architecture: Employed in creating intricate designs and patterns for architectural elements.
- Metal Fabrication: Used for custom cutting of metal parts and components.
Why Popular:
Waterjet cutting machines are widely used for their precision, versatility, and environmental benefits. They are ideal for applications requiring intricate designs and heat-sensitive materials.
6. Roll Forming Machines
Overview:
Roll forming machines are used to continuously shape metal sheets into specific profiles. They are widely used in industries requiring long, uniform parts.
Key Features:
- Continuous Production: Capable of producing long, uniform profiles with consistent quality.
- Versatility: Suitable for creating various profiles, including channels, angles, and beams.
- Efficiency: Offers high production speeds and minimal material waste.
- Customization: Machines can be customized to produce specific profiles and shapes.
Applications:
- Construction: Used for producing metal roofing, siding, and structural components.
- Automotive: Employed in creating long, uniform parts for vehicle frames and structures.
- Appliances: Used for producing metal components with consistent profiles.
Why Popular:
Roll forming machines are popular for their ability to produce long, uniform profiles efficiently. They are essential in industries requiring high-volume production of consistent parts.
Conclusion
The most widely used sheet metal machines are integral to modern manufacturing processes, offering a range of capabilities that cater to various industries and applications. From the precision and versatility of laser cutting machines to the robust performance of hydraulic shears, each machine plays a crucial role in shaping sheet metal into desired products. By understanding the features and applications of these machines, manufacturers can select the right equipment to optimize their operations and achieve high-quality results.
Section 7: Popular Sheet Metal Operations
Sheet metal operations are the processes used to transform raw metal sheets into specific shapes and products. These operations involve a variety of techniques, each suited to different applications and materials. Understanding the most popular sheet metal operations is crucial for manufacturers seeking to optimize their production processes and achieve high-quality results. This section explores the key operations in the sheet metal industry and their significance.
1. Cutting Operations
Cutting is one of the most fundamental operations in sheet metal fabrication, involving the separation of metal sheets into desired shapes and sizes. Several cutting techniques are widely used, each with its own advantages and applications:
A. Shearing
- Overview: Shearing involves cutting straight lines in metal sheets using a pair of sharp blades. It is commonly used for cutting flat metal sheets into rectangular or square shapes.
- Applications: Shearing is widely used in industries such as construction, automotive, and metal fabrication for creating basic shapes and panels.
- Advantages: This process is fast and cost-effective for producing straight cuts with minimal waste.
B. Laser Cutting
- Overview: Laser cutting uses a focused laser beam to precisely cut metal sheets into intricate shapes and patterns. It is ideal for applications requiring high precision and complex designs.
- Applications: Laser cutting is popular in industries like aerospace, electronics, and automotive for producing intricate components and decorative elements.
- Advantages: This technique offers high precision, speed, and the ability to cut complex shapes with minimal material waste.
C. Plasma Cutting
- Overview: Plasma cutting uses a jet of ionized gas to cut through electrically conductive metals. It is effective for cutting thick materials quickly.
- Applications: Commonly used in heavy industries such as shipbuilding, construction, and automotive for cutting thick steel plates and metal structures.
- Advantages: Plasma cutting is fast and cost-effective for thick materials, providing clean cuts with minimal finishing required.
D. Waterjet Cutting
- Overview: Waterjet cutting uses a high-pressure stream of water mixed with abrasive materials to cut through metal sheets. It is suitable for cutting heat-sensitive materials without causing thermal distortion.
- Applications: Used in industries such as aerospace, architecture, and metal fabrication for cutting a wide range of materials, including metals, stone, and glass.
- Advantages: This technique offers versatility, precision, and environmental benefits, as it does not produce hazardous waste or fumes.
2. Bending Operations
Bending operations involve deforming metal sheets into specific angles and shapes. These processes are essential for creating components with complex geometries and are widely used across various industries.
A. Press Brake Bending
- Overview: Press brake bending uses a punch and die to bend metal sheets into specific angles. It is one of the most common bending techniques in the industry.
- Applications: Used in industries such as automotive, construction, and metal fabrication for creating components with precise bends, such as brackets, enclosures, and panels.
- Advantages: Press brake bending offers high precision and repeatability, making it suitable for producing consistent results in high-volume production.
B. Roll Bending
- Overview: Roll bending involves passing metal sheets through a series of rollers to create curved shapes. It is ideal for producing cylindrical and conical components.
- Applications: Commonly used in industries such as construction, automotive, and shipbuilding for producing pipes, tanks, and structural components.
- Advantages: Roll bending is efficient for producing long, uniform curves with minimal material waste.
C. Folding
- Overview: Folding involves bending metal sheets along a straight line using a folding machine. It is commonly used for creating simple bends and folds.
- Applications: Used in industries such as HVAC, metal fabrication, and appliances for producing panels, enclosures, and ducts.
- Advantages: Folding is fast and efficient for producing simple bends with minimal setup time.
3. Forming Operations
Forming operations involve shaping metal sheets into specific forms and structures. These processes are essential for creating components with complex geometries and are widely used across various industries.
A. Stamping
- Overview: Stamping involves using a die to shape metal sheets into specific forms. It is commonly used for mass production of components with intricate designs.
- Applications: Used in industries such as automotive, electronics, and appliances for producing components such as brackets, connectors, and housings.
- Advantages: Stamping is cost-effective for high-volume production, offering fast processing speeds and consistent results.
B. Punching
- Overview: Punching involves using a punch and die to create holes and shapes in metal sheets. It is widely used for producing components with precise holes and patterns.
- Applications: Used in industries such as electronics, automotive, and metal fabrication for creating components such as enclosures, panels, and connectors.
- Advantages: Punching offers high precision and speed, making it ideal for mass production of components with repetitive patterns.
C. Deep Drawing
- Overview: Deep drawing involves pulling a metal sheet into a die cavity to create deep, hollow shapes. It is commonly used for producing containers and cylindrical components.
- Applications: Used in industries such as automotive, appliances, and packaging for producing components such as cans, fuel tanks, and kitchenware.
- Advantages: Deep drawing offers efficient material utilization and the ability to produce complex shapes with smooth surfaces.
4. Joining Operations
Joining operations involve combining metal sheets and components to create finished products. These processes are essential for assembling complex structures and are widely used across various industries.
A. Welding
- Overview: Welding involves joining metal components by melting and fusing them together. It is commonly used for creating strong, permanent joints.
- Applications: Used in industries such as automotive, construction, and shipbuilding for assembling components and structures.
- Advantages: Welding offers strong and durable joints, making it ideal for applications requiring high structural integrity.
B. Riveting
- Overview: Riveting involves joining metal components using rivets, which are mechanical fasteners that create strong, permanent joints.
- Applications: Used in industries such as aerospace, automotive, and construction for assembling components and structures.
- Advantages: Riveting offers strong and reliable joints, making it suitable for applications requiring high strength and resistance to vibration.
C. Adhesive Bonding
- Overview: Adhesive bonding involves joining metal components using adhesives. It is commonly used for applications requiring lightweight and flexible joints.
- Applications: Used in industries such as automotive, electronics, and appliances for assembling components and structures.
- Advantages: Adhesive bonding offers lightweight and flexible joints, making it suitable for applications requiring reduced weight and vibration damping.
Conclusion
The sheet metal industry relies on a variety of operations to transform raw metal sheets into finished products. Cutting, bending, forming, and joining operations each play a crucial role in the manufacturing process, offering unique advantages and applications. By understanding the most popular sheet metal operations, manufacturers can optimize their production processes and achieve high-quality results, meeting the demands of diverse industries and applications.
Section 8: How CNC is Used in Sheet Metal Forming
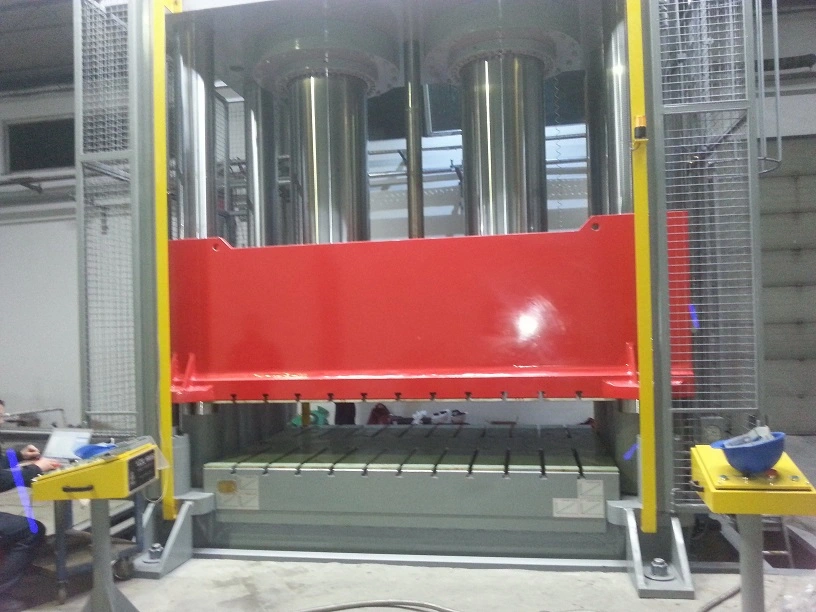
CNC (Computer Numerical Control) technology has revolutionized the sheet metal forming industry by introducing automation, precision, and efficiency into various forming processes. CNC systems control machinery using pre-programmed computer software, allowing for intricate and precise shaping of metal sheets. This section explores how CNC is utilized in sheet metal forming, detailing its applications, advantages, and impact on the industry.
CNC (Computer Numerical Control) technology has become a cornerstone in modern sheet metal forming, transforming how metal parts are manufactured. By integrating computer technology with traditional forming processes, CNC machines provide manufacturers with unparalleled precision, repeatability, and efficiency. This section delves into how CNC technology is applied in sheet metal forming, highlighting its applications, benefits, and impact on the industry.
1. CNC in Sheet Metal Forming Operations
CNC technology is used in various sheet metal forming operations, including bending, punching, and drawing. Each process benefits from the precision and automation provided by CNC systems:
A. CNC Bending
- Overview: CNC bending involves the use of CNC-controlled press brakes to bend sheet metal into specific angles and shapes. The CNC system precisely controls the movement of the punch and die, ensuring accurate and consistent bends.
- Applications:
- Automotive: CNC bending is used to produce components such as brackets, chassis parts, and body panels with precise angles and dimensions.
- Aerospace: The precision of CNC bending is crucial for manufacturing complex parts with tight tolerances, such as aircraft frames and structural components.
- HVAC: Used to form ducts and enclosures, ensuring accurate bends for proper fit and function.
- Advantages:
- Precision and Consistency: CNC bending ensures accurate and repeatable results, reducing the need for manual adjustments and minimizing errors.
- Complex Bends: CNC machines can perform complex bends and multiple angles in a single setup, enhancing productivity and flexibility.
- Reduced Setup Time: The CNC system stores bending programs, allowing for quick setup and changeovers between different parts.
B. CNC Punching
- Overview: CNC punching machines use a CNC-controlled turret to punch holes and shapes in sheet metal. The CNC system precisely controls the movement and operation of the punching tools, allowing for complex patterns and designs.
- Applications:
- Electronics: CNC punching is used to create enclosures and panels with precise cutouts for electronic components and connectors.
- Appliances: Used to produce parts with intricate patterns and perforations, such as washing machine panels and refrigerator shelves.
- Construction: CNC punching creates metal frameworks and structural components with precise holes for fasteners and joints.
- Advantages:
- High Speed and Efficiency: CNC punching offers rapid processing speeds and quick tool changes, making it ideal for high-volume production.
- Complex Patterns: The CNC system can produce intricate patterns and designs with high precision, reducing material waste and post-processing.
- Versatility: CNC punching machines can accommodate various tools and dies, allowing for diverse applications and material handling.
C. CNC Deep Drawing
- Overview: CNC deep drawing involves the use of CNC-controlled hydraulic presses to form metal sheets into deep, hollow shapes. The CNC system precisely controls the press’s movement, ensuring uniform material flow and shape accuracy.
- Applications:
- Automotive: CNC deep drawing produces components such as fuel tanks, oil pans, and exhaust systems, requiring high precision and structural integrity.
- Appliances: Used to form kitchenware and containers, ensuring smooth surfaces and accurate shapes.
- Packaging: CNC deep drawing creates metal cans and containers with consistent wall thickness and dimensions.
- Advantages:
- Uniform Material Flow: CNC deep drawing ensures consistent material flow and thickness, reducing defects and improving product quality.
- Complex Shapes: CNC machines can produce intricate and deep shapes with high precision, minimizing the need for additional processing.
- Efficiency: CNC deep drawing reduces cycle times and material waste, optimizing production efficiency.
2. Advantages of CNC in Sheet Metal Forming
The integration of CNC technology in sheet metal forming offers several advantages, enhancing productivity and product quality:
A. Precision and Accuracy
- Overview: CNC systems provide precise control over machine movements, ensuring accurate and consistent results in every operation. This precision is crucial for meeting tight tolerances and quality standards.
- Benefits:
- Reduced Errors: CNC machines minimize human errors, ensuring consistent product quality and reducing scrap rates.
- Tight Tolerances: CNC technology achieves tight tolerances, essential for industries such as aerospace and automotive where precision is critical.
- Consistent Quality: The repeatability of CNC machines ensures consistent quality across large production runs, enhancing customer satisfaction.
B. Automation and Efficiency
- Overview: CNC machines automate various forming processes, reducing the need for manual intervention and increasing production efficiency.
- Benefits:
- Increased Productivity: CNC automation reduces setup times and cycle times, allowing for faster production and higher output.
- Labor Savings: CNC machines require less manual labor, reducing labor costs and freeing up workers for other tasks.
- Optimized Workflow: CNC systems streamline production workflows, improving overall efficiency and reducing bottlenecks.
C. Flexibility and Adaptability
- Overview: CNC machines are highly flexible, allowing for quick changes in production without the need for extensive retooling or setup.
- Benefits:
- Rapid Prototyping: CNC machines facilitate rapid prototyping and testing, allowing manufacturers to quickly iterate and refine designs.
- Custom Production: CNC technology enables custom production and small-batch manufacturing, meeting diverse customer demands and requirements.
- Multi-Material Capability: CNC machines can handle various materials and thicknesses, providing versatility in production.
3. Impact of CNC Technology on the Sheet Metal Forming Industry
The adoption of CNC technology has significantly impacted the sheet metal forming industry, driving innovation and growth:
A. Improved Product Quality
- Overview: CNC technology ensures high precision and consistency in production, leading to improved product quality and customer satisfaction.
- Impact:
- Enhanced Performance: High-quality products perform better and have longer lifespans, increasing customer loyalty and brand reputation.
- Reduced Defects: CNC machines reduce defects and rework, minimizing waste and production costs.
- Competitive Advantage: Manufacturers using CNC technology can offer superior products, gaining a competitive edge in the market.
B. Increased Manufacturing Efficiency
- Overview: CNC automation streamlines production processes, reducing cycle times and increasing throughput.
- Impact:
- Cost Savings: Improved efficiency reduces production costs, allowing manufacturers to offer competitive pricing.
- Faster Time-to-Market: CNC machines enable faster production and shorter lead times, accelerating time-to-market for new products.
- Scalability: CNC technology supports scalable production, accommodating both small and large production runs with ease.
C. Innovation and Customization
- Overview: CNC technology fosters innovation and customization in product design and manufacturing.
- Impact:
- Design Freedom: CNC machines support complex and intricate designs, enabling manufacturers to create innovative products.
- Custom Solutions: CNC technology allows for custom production, meeting specific customer needs and requirements.
- Market Expansion: The ability to produce diverse and customized products opens up new market opportunities for manufacturers.
Conclusion
CNC technology has transformed the sheet metal forming industry, offering numerous benefits such as precision, efficiency, and flexibility. By automating various forming processes, CNC machines enhance productivity and product quality, driving innovation and growth in the industry. As manufacturers continue to adopt CNC technology, the sheet metal forming industry is poised for further advancements and opportunities, meeting the evolving demands of diverse industries and applications
Section 9: CNC Setup Process for Sheet Metal Forming
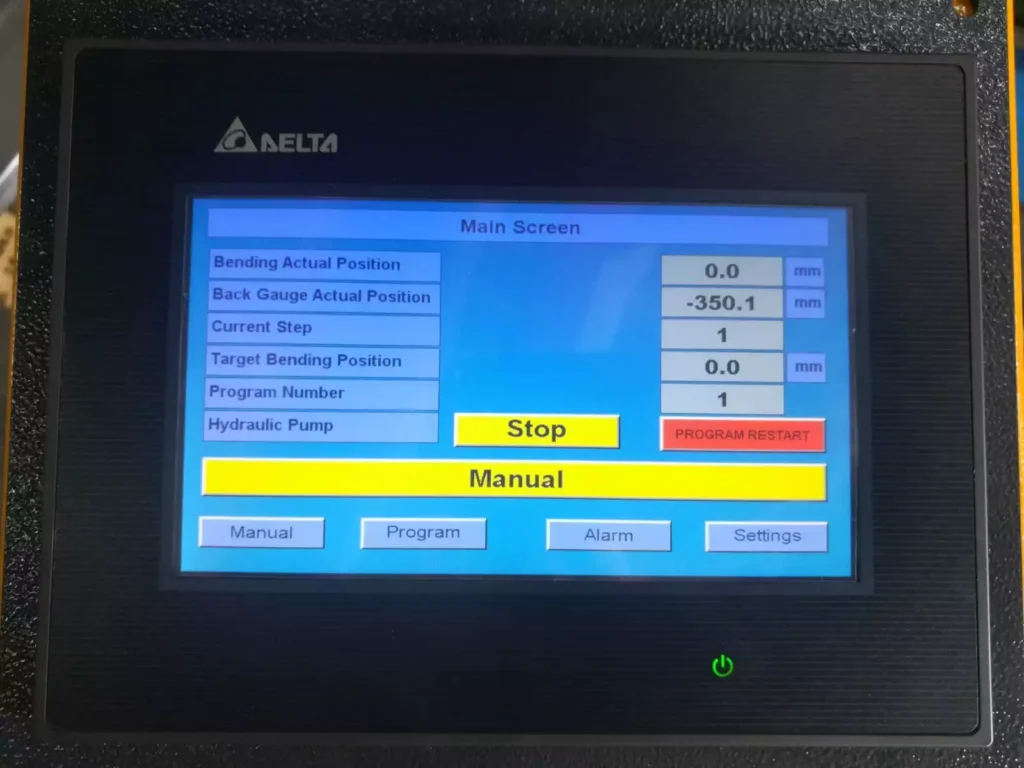
Setting up a CNC (Computer Numerical Control) machine for sheet metal forming is a detailed process that involves multiple steps to ensure the machine operates efficiently and accurately. The setup process is crucial for achieving the desired results and minimizing errors during production. Here’s a comprehensive guide to the CNC setup process in sheet metal forming.
The CNC setup process for sheet metal forming involves several critical steps to prepare the machine for operation. This setup includes programming, tooling selection, machine calibration, and testing to ensure the CNC machine operates smoothly and produces high-quality results. This section provides a step-by-step guide to setting up a CNC machine for sheet metal forming.
1. Preparing the CNC Machine
A. Understanding Machine Specifications
- Overview: Before setting up a CNC machine, it’s essential to understand the machine’s specifications, capabilities, and limitations. This knowledge helps in selecting the appropriate tools and materials for the operation.
- Key Considerations:
- Machine Type: Identify the type of CNC machine being used (e.g., CNC press brake, CNC punching machine) and its specific features.
- Material Compatibility: Ensure the machine can handle the material type and thickness required for the operation.
- Tolerances and Precision: Understand the machine’s precision levels and tolerances to ensure accurate results.
B. Ensuring Machine Readiness
- Overview: Before starting the setup, ensure that the CNC machine is clean, properly maintained, and ready for operation.
- Steps:
- Cleaning: Clean the machine’s surfaces, removing any dust, debris, or previous material remnants that could affect performance.
- Maintenance Check: Perform a maintenance check, including lubrication of moving parts and inspection of electrical connections.
- Power Supply: Ensure the machine is connected to a stable power supply with the correct voltage and amperage.
2. Tooling and Material Setup
A. Selecting the Right Tools
- Overview: Selecting the appropriate tools is crucial for achieving the desired results in sheet metal forming. This involves choosing the correct punches, dies, and other tooling components.
- Key Considerations:
- Tool Type: Choose tools that match the specific forming operation (e.g., bending, punching) and material type.
- Tool Material: Select tooling materials that are compatible with the sheet metal material, ensuring durability and precision.
- Tool Size: Ensure the tools are the correct size and shape for the desired cuts, bends, or forms.
B. Installing Tools
- Overview: Once the appropriate tools are selected, they need to be installed correctly in the CNC machine.
- Steps:
- Tool Mounting: Securely mount the tools in the machine’s tool holder, ensuring proper alignment and positioning.
- Tool Calibration: Calibrate the tools to ensure they are accurately positioned for the operation. This may involve adjusting tool height, angle, and alignment.
- Tool Testing: Perform a test run to verify tool performance and ensure they are correctly installed.
C. Material Preparation
- Overview: Preparing the sheet metal material is an essential step in the CNC setup process, ensuring the material is ready for forming.
- Steps:
- Material Inspection: Inspect the sheet metal for defects, such as scratches, dents, or impurities, that could affect the final product.
- Material Cleaning: Clean the material surface to remove any contaminants that could interfere with the forming process.
- Material Positioning: Properly position the material in the machine, ensuring it is securely held in place and aligned with the tooling.
3. Programming the CNC Machine
A. Creating the CNC Program
- Overview: The CNC program contains the instructions that guide the machine’s operations, specifying the movements, speeds, and tools used during the process.
- Steps:
- CAD/CAM Software: Use computer-aided design (CAD) software to create the part design and generate a toolpath using computer-aided manufacturing (CAM) software.
- G-Code Generation: Convert the toolpath into G-code, the programming language used by CNC machines to execute commands.
- Program Optimization: Optimize the CNC program to minimize machining time, reduce tool wear, and enhance efficiency.
B. Uploading the CNC Program
- Overview: Once the CNC program is created, it needs to be uploaded to the CNC machine’s control unit.
- Steps:
- Data Transfer: Transfer the CNC program to the machine via USB, Ethernet, or other compatible methods.
- Program Verification: Verify the uploaded program on the machine’s interface, ensuring it matches the intended design and specifications.
- Program Simulation: Run a program simulation to visualize the machining process and identify potential issues before actual operation.
4. Machine Calibration and Testing
A. Calibrating the CNC Machine
- Overview: Calibration ensures the CNC machine operates with the desired precision and accuracy, aligning its movements with the programmed instructions.
- Steps:
- Axis Calibration: Calibrate the machine’s axes to ensure they move accurately and consistently along the specified paths.
- Tool Calibration: Verify tool positioning and alignment, ensuring the tools interact with the material as intended.
- Sensor Calibration: Calibrate sensors and feedback systems to ensure accurate monitoring and control of machine operations.
B. Conducting a Test Run
- Overview: A test run allows operators to validate the setup and identify potential issues before full-scale production.
- Steps:
- Material Sample: Use a sample piece of material to test the CNC setup, simulating the actual production process.
- Process Observation: Monitor the test run closely, observing tool performance, material behavior, and machine movements.
- Issue Identification: Identify and address any issues or discrepancies observed during the test run, making necessary adjustments to the setup or program.
5. Final Adjustments and Production
A. Making Final Adjustments
- Overview: After testing, make any final adjustments to the CNC setup to ensure optimal performance during production.
- Steps:
- Program Refinement: Refine the CNC program based on test run observations, making adjustments to toolpaths, speeds, or feeds as needed.
- Tool Adjustment: Make any necessary adjustments to tool positioning or alignment, ensuring they are correctly configured for production.
- Material Handling: Ensure material handling systems are properly set up to support efficient production flow.
B. Starting Production
- Overview: Once the setup is finalized, the CNC machine is ready for full-scale production.
- Steps:
- Production Initiation: Start the CNC machine and begin the production process, ensuring continuous monitoring of operations.
- Quality Control: Implement quality control measures to monitor product quality, ensuring that parts meet design specifications and standards.
- Ongoing Maintenance: Perform regular maintenance and inspections to keep the CNC machine in optimal working condition, minimizing downtime and maximizing efficiency.
Conclusion
The CNC setup process for sheet metal forming is a comprehensive and detailed procedure that requires careful planning, execution, and testing. By following the steps outlined in this guide, manufacturers can ensure their CNC machines are properly set up for efficient and accurate production, minimizing errors and maximizing productivity. As CNC technology continues to evolve, the setup process will become even more streamlined and efficient, enabling manufacturers to meet the demands of increasingly complex and precise manufacturing tasks.
EMS Metalworking Machines
We design, manufacture and assembly metalworking machinery such as:
- Hydraulic transfer press
- Glass mosaic press
- Hydraulic deep drawing press
- Casting press
- Hydraulic cold forming press
- Hydroforming press
- Composite press
- Silicone rubber moulding press
- Brake pad press
- Melamine press
- SMC & BMC Press
- Labrotaroy press
- Edge cutting trimming machine
- Edge curling machine
- Trimming beading machine
- Trimming joggling machine
- Cookware production line
- Pipe bending machine
- Profile bending machine
- Bandsaw for metal
- Cylindrical welding machine
- Horizontal pres and cookware
- Kitchenware, hotelware
- Bakeware and cuttlery production machinery
as a complete line as well as an individual machine such as:
- Edge cutting trimming beading machines
- Polishing and grinding machines for pot and pans
- Hydraulic drawing presses
- Circle blanking machines
- Riveting machine
- Hole punching machines
- Press feeding machine
You can check our machinery at work at: EMS Metalworking Machinery – YouTube
Applications:
- Flange-punching
- Beading and ribbing
- Flanging
- Trimming
- Curling
- Lock-seaming
- Ribbing