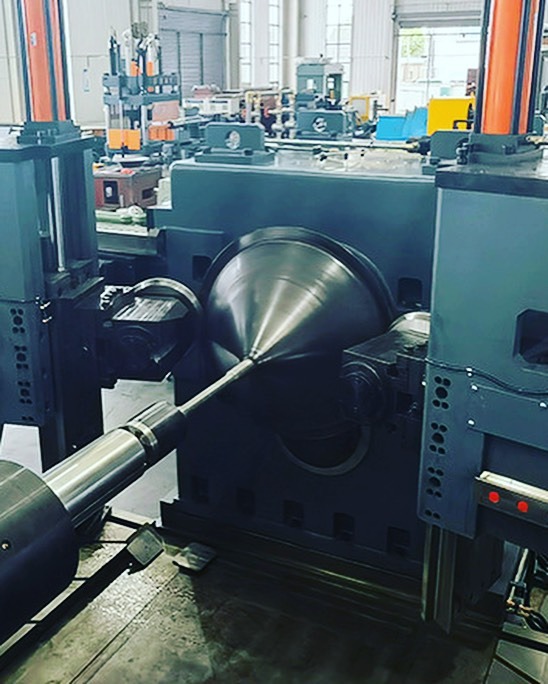
Custom-Made Metal Spinning Machine: A metal spinning machine is a tool used to form round metal parts by rotating a metal disc or tube at high speed and shaping it over a mold (called a mandrel) using a tool or roller. It’s a type of cold-forming process — meaning the metal is shaped without heating (although sometimes mild heating is applied for very tough metals).
Here’s how it works in a nutshell:
- A flat metal blank (usually aluminum, steel, brass, or copper) is clamped onto a mandrel.
- The machine spins the blank at high speed (like a pottery wheel, but for metal).
- A forming tool (often a blunt-tipped lever or roller) is pressed against the metal, forcing it to flow and take the shape of the mandrel.
- The result is a smooth, seamless, hollow part — like bowls, cones, hemispheres, or even rocket nose cones.
There are two main types of metal spinning:
- Manual spinning: An operator uses handheld tools to shape the metal. Very skill-based.
- CNC spinning: A computer controls the tools. Faster and much more consistent for production.
Typical applications:
- Lampshades
- Gas cylinders
- Musical instruments (like trumpets or cymbals)
- Aerospace parts
- Kitchenware
A metal spinning machine works by rotating a piece of metal, usually a disc or tube, at very high speeds while applying pressure with a tool to form the metal over a mandrel into the desired shape. The process is a type of cold working, meaning the metal isn’t usually heated much during shaping, though sometimes a little heat is used if the material is very hard or thick. Metal spinning can produce seamless, symmetric parts like cones, cylinders, spheres, or more complex curved profiles.
The operator or a computer-controlled arm uses tools like rollers or blunt-tipped levers to press against the spinning metal, gradually forcing it to match the mandrel’s contour. Thinner metals can be shaped quite easily, while thicker or tougher metals require stronger machines and sometimes lubrication or moderate heat. The finished part is typically very strong because the spinning process aligns the metal’s grain structure around the formed shape.
There are basic manual spinning setups where a skilled technician shapes the metal by hand, and there are advanced CNC machines where the entire shaping process is automated based on a programmed path. CNC spinning allows for much faster production rates, repeatability, and the ability to handle complex designs that would be very difficult to do by hand. Some machines are dedicated purely to spinning, while others can perform additional operations like shear forming, where the metal is actually thinned as it’s shaped, allowing for very lightweight and strong parts.
Applications of metal spinning machines are extremely broad. They’re used in industries like aerospace to make parts like rocket nozzles and satellite dishes, in automotive manufacturing for wheel hubs and other components, and in consumer goods like decorative lighting, kitchenware, and musical instruments. Metal spinning is favored when a design requires smooth, symmetrical, lightweight, and strong components without the cost or complexity of welding or casting.
In metal spinning, mandrels and spinning tools play crucial roles in shaping the metal.
A mandrel is a rigid tool over which the metal is shaped. It provides the template that determines the final form of the part. Mandrels can be made from a variety of materials like steel or aluminum, and they may be solid or hollow, depending on the part being made. For example, when producing a cylindrical part, the mandrel would match the inner diameter of the desired shape. When working on a part that requires both internal and external curves, the mandrel might be more complex, offering support for both.
Spinning tools are used to apply pressure and guide the metal as it deforms over the mandrel. These can be of various types:
- Rollers: These tools are typically used in high-speed CNC spinning. They’re designed to press the metal gently while it spins, ensuring that the material is formed evenly and symmetrically.
- Blunt-tipped tools: In manual spinning, a technician uses a fixed or adjustable tool that has a flat or rounded end to press down on the metal blank as it spins. This tool shapes the metal into the desired profile.
- Pneumatic or hydraulic tools: In advanced setups, pneumatic or hydraulic actuators may be used to control the force applied by spinning tools, allowing for consistent pressure to be applied across the entire surface of the part.
Another important element in metal spinning is lubrication. As metal is deformed, friction increases, which can lead to wear on the tools and difficulty in forming the part. Lubricants, like oils or pastes, are often applied to both the mandrel and the metal blank to reduce friction, prevent overheating, and ensure smooth deformation. Some machines are designed to apply lubrication automatically during the process.
In more advanced machines, like CNC metal spinning machines, the entire process — including the application of pressure and lubrication — is controlled by computer software. This ensures the precise replication of the part, regardless of the complexity of the design. These machines allow for high-volume production and can also handle intricate designs with tight tolerances.
The advantages of using metal spinning machines include:
- No welding or seams: Because the material is formed from a single piece, there are no welds or seams, which can be weak points in a part.
- High material efficiency: Metal spinning uses very little material waste since the process only reshapes the metal rather than cutting away large portions like in machining.
- Strength: The spinning process aligns the metal’s grain structure, often resulting in stronger, more durable parts compared to other forming methods.
- Flexibility: It’s suitable for making both simple and complex shapes, and it works well with a variety of metals and alloys.
If you’re interested, I can provide more details on different machine types, the process steps, or how metal spinning compares to other metal forming techniques. Let me know what you’d like to explore further!
Single-Action Metal Spinning Machine
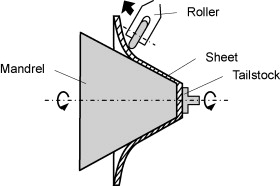
A Single-Action Metal Spinning Machine is a specific type of metal spinning equipment designed to spin and form metal parts by using a single spinning tool. In this machine, the primary movement is achieved by the rotation of the metal blank and the application of pressure from a single tool, which progressively shapes the blank over a mandrel. Here’s how it works in more detail:
Key Features of a Single-Action Spinning Machine:
- Spinning Tool: The “single-action” refers to the fact that only one tool is typically used to shape the metal during the spinning process. This tool applies the force directly to the metal as it spins, causing the material to conform to the shape of the mandrel.
- Manual or CNC Control: Single-action spinning machines can either be operated manually, where the technician physically guides the tool or CNC controlled, where the movements are automated to ensure precision and repeatability.
- Spinning Process: The blank (usually a flat disc of metal) is placed onto the mandrel and then rotated at high speeds. The spinning tool applies pressure at a specific point on the blank, forcing it to gradually take the shape of the mandrel. The operator moves the tool over the surface, typically in a circular or spiral motion, to progressively form the shape.
- Mandrel: The mandrel serves as the template around which the metal is spun. It can be simple (a straight cylinder for round parts) or complex (for parts with internal features or varying diameters). The choice of mandrel affects the shape and accuracy of the final part.
Advantages of Single-Action Metal Spinning Machines:
- Simplicity: These machines are simpler than multi-action machines, which may involve multiple tools applying pressure from different directions. This makes them easier to operate and maintain.
- Cost-effective: Since they require only one spinning tool and a relatively simple setup, single-action spinning machines can be more affordable than more advanced systems.
- Suitable for Smaller Parts: These machines are often ideal for producing small to medium-sized parts, particularly when only one tool is sufficient to create the desired shape.
- Flexibility: While primarily used for simpler shapes, single-action machines can still produce a variety of profiles and curves, depending on the blank, mandrel, and tool used.
Applications:
Single-action spinning machines are often used for the production of:
- Simple cylindrical or conical shapes: Parts like bowls, trays, cones, and simple cylindrical components can be easily made.
- Prototyping and low-volume production: Given their relatively lower cost and ease of use, these machines are popular for making prototypes or for smaller production runs.
- Decorative metal products: The smooth, seamless nature of spun metal is often used in decorative applications like lampshades, musical instrument bells, or metal art.
Manual vs. CNC Single-Action Spinning:
- Manual: In manual single-action spinning, the operator has to control the tool and apply the pressure at the right angles. This requires a high level of skill to produce consistent results.
- CNC: In CNC-controlled single-action machines, the movements of the tool are automated, allowing for more precise, repeatable results with much less skill required from the operator. CNC machines also allow for greater flexibility in part design and can handle more complex shapes compared to manual setups.
Single-action spinning machines are an efficient and versatile solution for creating high-quality, seamless parts, especially when the shape is relatively simple, and the cost needs to be kept low. Would you like more detailed comparisons between single-action and multi-action machines?
Multi-Action Metal Spinning Machines
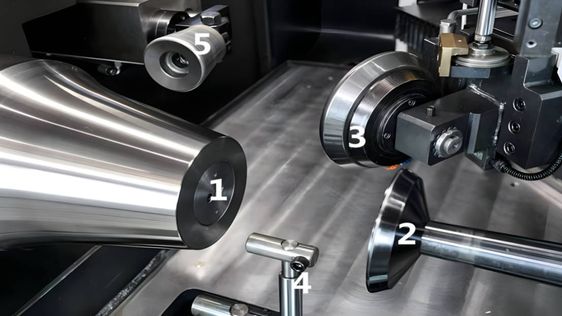
Unlike single-action machines, multi-action metal spinning machines use more than one tool to shape the metal, allowing for more complex forms and higher precision. These machines generally involve simultaneous or sequential movements of multiple tools that apply force from different directions to shape the metal. Some multi-action machines may include both rotating tools (to spin the metal) and stationary tools (to apply pressure).
Key Features:
- Multiple Tools: The most significant difference is the presence of multiple tools or rollers that apply force in different ways. These can include:
- Main forming tool (similar to the single-action spinning machine)
- Secondary tools that may push or pull the metal in different directions
- Rollers to help with forming more complex curves or profiles.
- Complexity and Accuracy: Multi-action machines are designed to create more intricate and varied shapes. The ability to apply force from several directions allows these machines to form parts that require more detailed geometry, such as parts with multiple contours, internal features, or thicker walls.
- Higher Precision and Repeatability: Because of the multiple tools and often automated movements (especially in CNC versions), multi-action machines offer superior accuracy and consistency, making them ideal for high-volume production of complex parts.
Applications:
- Advanced Aerospace Components: Parts that require complex geometries, like turbine blades or fuel tanks, benefit from multi-action spinning.
- Automotive: Complex housings, wheel rims, or other detailed metal components.
- Heavy-duty Parts: Components that require more robust shaping, such as those used in large machinery or industrial systems.
Differences Between Single-Action and Multi-Action Spinning Machines
- Complexity of Parts:
- Single-Action: Primarily suited for simple, symmetric parts like cones, cylinders, or domes.
- Multi-Action: Capable of producing complex, asymmetric, or multi-contoured parts. These could include shapes with varying wall thicknesses, intricate curves, or parts with both external and internal features.
- Number of Tools:
- Single-Action: Uses one tool to apply pressure and shape the metal. This simplicity makes it easier to operate and more cost-effective for basic designs.
- Multi-Action: Utilizes multiple tools to form the part. This added complexity allows for better control over the final shape, especially when forming more intricate designs or larger parts.
- Automation:
- Single-Action: Can be manual or CNC. In manual setups, the operator controls the shaping of the metal, which requires a high level of skill and experience. CNC versions automate the process, but the setup is simpler.
- Multi-Action: Almost always CNC-controlled, which ensures high precision and repeatability, making it suitable for mass production and complex parts.
- Speed and Efficiency:
- Single-Action: Generally slower and better for low to medium-volume production or prototyping. It’s ideal when speed isn’t critical and the part design is simple.
- Multi-Action: Faster and more efficient for large-volume production of complex parts. The use of multiple tools can reduce cycle time by applying force from several angles simultaneously.
- Tooling and Setup Costs:
- Single-Action: More cost-effective, as there’s less tooling required and the setup is simpler.
- Multi-Action: More expensive due to the additional tools, more complex setups, and the need for advanced automation, but offers greater versatility.
When to Use Single-Action vs. Multi-Action Spinning Machines
- Single-Action Machines are ideal for:
- Simple Parts: Items like light fixtures, musical instruments, kitchenware, and other products with simple geometries.
- Low to Medium Production Volumes: When you don’t need to produce high volumes of complex parts but still need high-quality, seamless products.
- Cost-Sensitive Projects: When tooling and setup costs need to be minimized, especially for prototyping or small batch runs.
- Smaller Parts: Small, symmetrical parts that don’t require multi-directional shaping or intricate details.
- Multi-Action Machines are ideal for:
- Complex Parts: Large, intricately shaped parts used in industries like aerospace, automotive, and industrial machinery.
- High-Volume Production: When producing large quantities of the same or similar complex parts that need precision and consistency.
- Precision and Detail: Parts that need tight tolerances, precise geometries, or where variations in wall thickness or curvature are needed.
Conclusion
Single-action and multi-action metal spinning machines serve different needs in the world of metal forming. Single-action machines are simpler, more cost-effective, and well-suited for producing straightforward parts in smaller volumes. On the other hand, multi-action machines are more advanced, capable of producing complex and precise parts for high-volume, high-precision applications.
To dive deeper into the operational mechanics and additional features of single-action versus multi-action metal spinning machines, let’s focus on specific aspects of the process and potential advancements that may affect performance, productivity, and quality:
Operational Differences: Single-Action vs. Multi-Action
- Tool Movement and Control:
- Single-Action Machines: The main tool (typically a forming tool or roller) applies pressure to shape the metal, and the operator (in manual machines) or the CNC system (in automated machines) controls the pressure and movement. In manual versions, operators must carefully control the tool’s angle and force to avoid defects. This requires good skill and experience to get consistent results.
- Multi-Action Machines: With multi-tool setups, the process is more automated and involves the coordinated movement of multiple tools. This can include rotary tools for the spinning action, stationary tools for shaping, and even specialized tools for specific tasks like trimming or deburring. Because the tools work in tandem, multi-action machines can apply consistent pressure from various angles, which is especially beneficial for more intricate shapes.
- Material Handling:
- Single-Action Machines: The simplicity of the tool system means the metal blank often requires manual handling. It’s spun at high speed, and the operator controls the tool’s movement to form the part gradually. While this allows for flexibility, it can be slower compared to multi-action machines for complex shapes.
- Multi-Action Machines: These machines may feature advanced material-handling systems that automatically adjust the position of the metal blank and ensure the tools are positioned at the correct angles. Some machines even include automated loading and unloading systems, reducing manual labor and enhancing efficiency for high-volume production.
- Customization and Versatility:
- Single-Action Machines: These machines are often more flexible in terms of customization. If an operator needs to change the design or part geometry quickly, it is easier to adjust a single tool, modify the blank, or swap out mandrels.
- Multi-Action Machines: Although multi-action machines are highly specialized and designed for specific tasks, they can handle a wide variety of part geometries. They excel when large batches of complex parts need to be spun with high precision. However, changing setups or tooling can be more involved and time-consuming than with single-action machines.
- Surface Finish and Quality:
- Single-Action Machines: The surface finish can be very smooth if the tool and metal are maintained well. However, there may be minor inconsistencies if the operator’s technique isn’t perfect, especially in manual setups. This can affect the overall quality of parts for highly sensitive applications.
- Multi-Action Machines: The use of multiple tools and automatic pressure control in multi-action machines results in a more consistent surface finish. The tool system can apply pressure more uniformly, which typically results in less distortion, fewer defects, and better overall quality, especially for complex or high-tolerance parts.
- Cycle Time and Production Speed:
- Single-Action Machines: For simpler parts, the cycle time can be quite fast. However, for more complex or larger parts, the time required to manually adjust tools and re-position the metal can lengthen the process. If higher volume or consistency is needed, multiple setups might be required, which increases downtime.
- Multi-Action Machines: These machines excel in high-speed, high-volume environments. The multiple tools work simultaneously, reducing the cycle time significantly for more complex parts. They can maintain faster production speeds without compromising quality, making them ideal for industries that require consistent, high-precision components.
Technological Advancements in Metal Spinning Machines
As with many manufacturing processes, advancements in technology have made both single-action and multi-action metal spinning machines more efficient, precise, and versatile.
- CNC Control:
- Single-Action: CNC single-action spinning machines have dramatically increased the consistency and precision of the process. With CNC control, even though only one tool is used, the machine can adjust pressure, tool speed, and direction automatically based on pre-programmed paths. This reduces the dependency on operator skill and provides repeatability in high-volume production.
- Multi-Action: Multi-action machines benefit greatly from CNC control, especially because they use multiple tools to shape the metal. The CNC system can coordinate tool movements with high precision, allowing manufacturers to produce parts with intricate geometries that would be almost impossible to achieve manually.
- Hydraulic and Pneumatic Systems:
- Single-Action: Some advanced single-action machines use hydraulic or pneumatic pressure to apply force more precisely. This helps to maintain consistent pressure during the spinning process and makes it easier to form thicker metals or larger parts with less effort.
- Multi-Action: Hydraulic and pneumatic systems in multi-action machines allow for even more complex operations. These systems can control the force applied by each tool separately, enabling the machine to handle parts that require varying pressures or shaping methods across different areas of the part.
- Material Pre-Heating:
- Single-Action: While most metal spinning is a cold-forming process, some machines incorporate mild pre-heating of the metal before spinning. This is especially useful when working with tougher metals like titanium or thick aluminum. Pre-heating can make the metal more pliable, reducing the force required and minimizing the risk of cracking.
- Multi-Action: Multi-action machines often incorporate integrated heating systems or are designed to work in environments where heat treatment is part of the process. These setups can further improve metal flow, reduce material strain, and enhance the final product’s integrity, particularly for more complex or larger parts.
- Automation and Robotics:
- Single-Action: While not as common, some single-action machines integrate robotic arms or automated loading systems to reduce manual intervention and speed up production. This is particularly useful in situations where parts are smaller, and the operator needs to handle multiple machines or perform other tasks.
- Multi-Action: In multi-action machines, automation is often taken to the next level. Robots can handle material loading, mandrel changeover, and even post-processing tasks like trimming, deburring, or quality checks. This reduces human error and increases throughput, particularly for mass production scenarios.
Conclusion
Choosing between a single-action and multi-action metal spinning machine depends on the complexity of the parts you want to produce, the production volume, the material you’re working with, and the desired precision.
- Single-action spinning is best for simpler, smaller parts or low to medium volume production, where simplicity and cost-effectiveness are more important than complex geometries.
- Multi-action spinning is ideal for high-precision, high-volume manufacturing of complex, detailed parts, especially when multiple contours, varied thicknesses, and intricate shapes are required.
Advancements in automation, CNC control, hydraulic/pneumatic systems, and robotics continue to improve both types of machines, making them more efficient and capable of handling a broader range of tasks and materials. If you have specific questions about how these technologies apply to your own projects or parts, feel free to ask!
Precision CNC Metal Spinning Machine
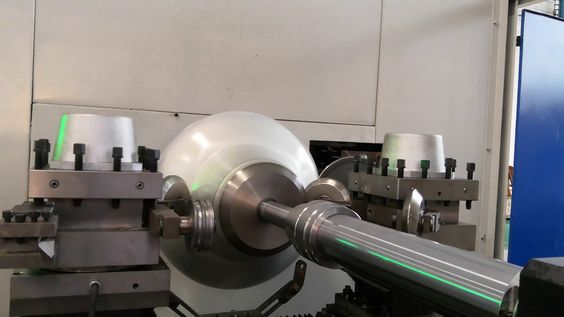
A Precision CNC Metal Spinning Machine is a type of automated, computer-controlled machine designed to create high-precision, intricate metal parts through the metal spinning process. These machines combine the principles of traditional metal spinning with the accuracy and efficiency of CNC (Computer Numerical Control) technology, enabling the production of complex and detailed parts with tight tolerances.
Key Features of Precision CNC Metal Spinning Machines:
- CNC Control:
- The most significant feature of a Precision CNC Metal Spinning Machine is its computer control system. CNC systems allow for precise, repeatable movements of the forming tool(s), mandrel, and other components. The machine follows a programmed path based on a 3D model or CAD design, which ensures accuracy and uniformity for each part produced.
- With CNC control, the machine can automatically adjust the tool’s position, pressure, and speed in real-time based on the material being used, ensuring optimal results throughout the production process.
- Multiple Axes of Motion:
- Multi-axis control is a key feature of high-precision CNC metal spinning machines. Typically, these machines use 3-axis or 5-axis configurations, where:
- 3-axis machines control the spinning tool (radially), mandrel position, and tool pressure along the length of the part.
- 5-axis machines offer even greater flexibility, allowing for more complex geometries with multiple angles and curvatures in the final part.
- These systems can move the tool not only along the usual X, Y, and Z axes but also tilt or rotate it in multiple directions to create parts with varying contours, angles, or asymmetrical shapes.
- Multi-axis control is a key feature of high-precision CNC metal spinning machines. Typically, these machines use 3-axis or 5-axis configurations, where:
- High-Precision Tools:
- Precision CNC machines are often equipped with specialized tooling designed for fine tolerances and smooth surface finishes. These tools are designed to apply pressure consistently and evenly to shape the metal without causing defects such as wrinkles, cracks, or material thinning.
- Rollers and forming tools are often used in conjunction with automatic feed systems to maintain a uniform shape throughout the spinning process.
- Hydraulic and Pneumatic Assistance:
- Many precision CNC metal spinning machines use hydraulic or pneumatic systems to assist with the application of force. These systems help maintain steady pressure, particularly when dealing with harder or thicker metals.
- Hydraulic pressure allows for more controlled, consistent shaping, while pneumatic systems may be used to assist with tool movement and part handling.
- Advanced Material Handling and Tooling:
- Precision CNC machines often include automated material handling systems, such as robotic arms or conveyors, to load and unload the metal blanks, which improves efficiency in high-volume production settings.
- The system may also include automatic mandrel changers, so different part designs can be produced without manual intervention, reducing setup time.
- Integrated Measurement and Quality Control:
- CNC metal spinning machines are often equipped with in-line measurement systems that continuously monitor the part’s dimensions during the spinning process. This ensures that any deviations from the design are immediately corrected.
- Some machines include laser scanners or CMM (Coordinate Measuring Machine) systems that compare the part to the original CAD model in real time, providing feedback to adjust the forming tool’s position or force if necessary.
Advantages of Precision CNC Metal Spinning Machines:
- High Accuracy:
- CNC control allows for tight tolerances, ensuring that each part is manufactured with consistent dimensions and quality. This is especially crucial for industries that require highly precise components, such as aerospace, medical devices, or electronics.
- Complex Geometries:
- Precision CNC metal spinning can create parts with complex geometries, including parts with multi-contour shapes, asymmetric features, or variable wall thicknesses. These machines excel at making intricate designs that would be difficult or impossible to produce with manual spinning or less advanced machines.
- Repeatability:
- Once a design is programmed into the CNC system, it can be reproduced thousands of times with the same level of precision. This makes CNC metal spinning ideal for high-volume production where consistency is critical.
- Material Efficiency:
- Like traditional metal spinning, CNC metal spinning is a subtractive process that doesn’t waste material, as the metal is simply deformed over a mandrel. This reduces scrap compared to other manufacturing methods like casting or machining.
- Reduced Labor and Setup Times:
- With automation in both the spinning and material handling processes, CNC metal spinning machines reduce the need for manual labor and long setup times. The CNC system controls the entire process, from tool positioning to speed and pressure, allowing operators to focus on monitoring rather than manual adjustment.
- Smooth Surface Finish:
- Due to the precision of CNC systems and the consistent application of pressure, the surface finish of the final part is usually smooth and free from defects. This is particularly important in industries where the aesthetic quality of the part matters, such as in decorative products or parts requiring a high degree of aesthetic appeal.
Applications of Precision CNC Metal Spinning Machines:
Precision CNC metal spinning machines are used in a wide variety of industries that require high-quality, complex metal parts. Some common applications include:
- Aerospace:
- Turbine components, nose cones, aircraft parts, and satellite dishes often require precision spinning to create complex geometries with tight tolerances.
- Automotive:
- Wheel rims, housings, exhaust components, and other intricate parts benefit from the flexibility and precision of CNC metal spinning.
- Medical Devices:
- Parts for implants, surgical instruments, and medical housing components require the accuracy and consistency that CNC metal spinning provides.
- Lighting:
- Lampshades and decorative light fittings often use precision spinning to form smooth, symmetrical designs with little waste.
- Consumer Electronics:
- Metal housings, reflectors, and heat sinks are produced using CNC metal spinning to ensure smooth finishes and accurate dimensions.
- Specialty Manufacturing:
- Components for military equipment, musical instruments, and scientific equipment all require the kind of precision that CNC metal spinning delivers.
Summary
A Precision CNC Metal Spinning Machine offers unmatched accuracy and flexibility in the production of high-quality, intricate metal parts. With the advantages of CNC control, multi-axis movement, and automated systems, these machines can create complex, symmetrical, and highly precise parts with little waste and high repeatability. They are particularly useful for industries like aerospace, automotive, medical, and consumer electronics, where precision, consistency, and surface finish are critical.
The combination of automation, sophisticated tooling, and real-time measurement ensures that precision CNC metal spinning can meet the demands of even the most complex designs, while also improving overall production efficiency.
A Precision CNC Metal Spinning Machine operates by using computer numerical control (CNC) technology to precisely shape metal into various geometries. The CNC system provides accurate control over the metal spinning process, enabling the creation of complex parts with high tolerances, especially for industries that require precision like aerospace, automotive, and medical devices. The machine works by spinning a metal blank—usually a flat disc or sheet of metal—at high speeds over a mandrel. The rotating metal is then shaped with a tool that presses and forms it against the mandrel, with the CNC system guiding the movement of the tool along various axes to achieve the desired shape. Unlike traditional manual metal spinning, the precision CNC system can control the pressure, speed, and movement of the forming tool, allowing for the production of parts with intricate curves, varying wall thicknesses, and specific tolerances. This process also reduces material waste, as the metal is deformed rather than cut away, and it can accommodate a wide range of materials, from aluminum and titanium to stainless steel and brass.
The advantages of using a CNC metal spinning machine include reduced labor costs, shorter setup times, and the ability to produce high-volume runs with minimal variation between parts. With automation integrated into these machines, tasks like loading, unloading, and material handling can be done efficiently, freeing up operators for other tasks and reducing the chance for human error. CNC metal spinning machines are also highly repeatable, meaning that once a design is programmed into the system, the machine can produce thousands of identical parts with consistent quality. Additionally, the ability to adjust the forming tool automatically based on material type or geometry further enhances the machine’s versatility, making it suitable for a wide variety of applications.
Beyond precision and repeatability, CNC machines can handle complex geometries that would be challenging for manual spinning processes. Parts like turbine components, medical implants, and automotive parts often require the level of control and precision that only CNC machines can provide. Surface finishes are another area where CNC metal spinning excels, producing smooth, consistent results with fewer defects and requiring less post-processing. In applications like lighting fixtures or decorative metal products, the aesthetic quality of the finished part is important, and CNC metal spinning helps achieve the required visual appeal.
CNC metal spinning machines can also offer significant improvements in material efficiency compared to other manufacturing processes. Since the metal is shaped rather than removed, there is typically less waste generated during production, which makes it an attractive option for industries focused on reducing costs and environmental impact. The precision control offered by CNC systems ensures that minimal excess material is used, which is especially important when working with costly metals like titanium or high-grade alloys.
The automation aspect of CNC metal spinning further enhances its efficiency. Many machines come with features like automatic tool changers, robotic loading/unloading systems, and in-process monitoring to ensure that parts are produced continuously and with minimal operator intervention. These automated functions reduce human error, increase throughput, and improve the overall cost-effectiveness of production, particularly for high-volume runs.
One of the standout features of precision CNC metal spinning is its ability to handle multi-axis movements. A CNC machine with 3, 4, or 5 axes allows the forming tool to move along multiple directions simultaneously, which is key to producing complex shapes that require multiple contours, non-symmetrical features, or intermediate angles. For example, creating a part with a variable radius, such as a reflector for lighting or a component with a deep, complex curvature, would be difficult on a traditional single-action machine. The ability to adjust the tool’s angle or movement allows the machine to create these sophisticated shapes more accurately and efficiently.
Another important aspect of CNC metal spinning is its versatility in terms of material. CNC machines can work with a wide variety of metals and alloys, each with its own set of challenges. Metals like stainless steel or titanium, which are commonly used in high-stress environments, require specific tooling, speeds, and forces to ensure the metal is formed correctly without cracking or weakening. The flexibility of CNC systems allows for these settings to be adjusted dynamically to accommodate different materials, ensuring the production of high-quality components regardless of the material.
In terms of post-processing requirements, precision CNC metal spinning can reduce the need for additional machining. Since the forming process produces parts with such high precision, less additional work like grinding, welding, or surface finishing is necessary. The smooth surfaces and precise dimensions typically require only minimal finishing to meet industry standards, further reducing labor and operational costs. In some cases, the part may be ready for use directly after spinning, particularly when surface finish quality is a primary concern.
While CNC metal spinning offers numerous advantages, it’s important to note that initial setup costs for CNC machines can be higher compared to traditional methods. The investment in CNC technology, especially for high-precision machines with multiple axes, can be significant. However, these upfront costs are offset by the efficiency gains, consistency, and flexibility the technology provides, particularly in large-scale production environments. As automation and CNC control become more sophisticated, the cost of these machines has steadily decreased, making them accessible to a wider range of manufacturers.
In the broader context of advanced manufacturing, CNC metal spinning plays an essential role in enabling industries to produce customized, complex, high-performance parts. Whether for aerospace, where parts need to withstand extreme conditions, medical, where precision and bio-compatibility are critical, or automotive, where strength and lightweight designs are key, CNC metal spinning provides an effective solution for meeting these diverse and demanding requirements. The advancements in control systems, tool design, and automation make CNC metal spinning not just a technique for producing standard parts, but a powerful tool for creating innovative and customized components with exceptional quality.
In conclusion, precision CNC metal spinning has transformed the manufacturing of metal parts by offering unparalleled control, accuracy, and efficiency. The process is ideal for producing high-quality, low-waste, complex components in a variety of industries, and the ability to integrate automation and multi-axis control makes it an excellent choice for both custom one-offs and high-volume production.
Double-Spindle Metal Spinning Machine
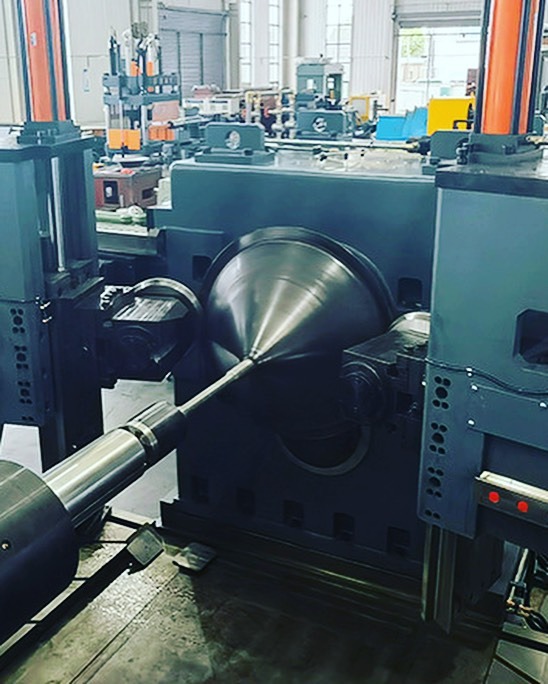
A Double-Spindle Metal Spinning Machine is a type of machine designed to enhance the efficiency and versatility of the metal spinning process. This machine utilizes two separate spindles, or rotational axes, which allows for simultaneous spinning operations on two parts or sides of a component, thus improving productivity, especially in applications requiring high-volume production.
Key Features of Double-Spindle Metal Spinning Machines:
- Two Spindles for Increased Efficiency:
- The primary feature of a double-spindle machine is the use of two spindles that can operate independently or in coordination. This setup allows for the spinning of two parts at once or simultaneous operations on different sides of a part, significantly improving throughput. When producing symmetrical or similar components, two parts can be processed at the same time, doubling production speed and minimizing downtime between setups.
- Enhanced Flexibility:
- The double-spindle configuration provides greater flexibility in the design and manufacturing process. With two spindles, a machine can handle more complex part shapes, especially when there is a need to form both sides of a part simultaneously. This is particularly useful for parts that have symmetrical or complex features, such as reflectors, lids, housing components, or other cylindrical and spherical shapes that require similar operations on both ends.
- Independent Control of Spindles:
- In more advanced double-spindle machines, the spindles can be controlled independently of each other. This means the machine operator can adjust the speed, pressure, and positioning of each spindle to suit the needs of different parts or to accommodate variations in material properties. Independent control allows for greater customization and the ability to manage multiple production runs with different specifications simultaneously.
- Increased Productivity:
- By performing two operations at once, double-spindle metal spinning machines effectively double the output without the need for additional machines or manual intervention. This is especially advantageous in high-volume manufacturing, where time and cost efficiency are critical. The ability to produce parts in parallel significantly cuts down cycle times, allowing manufacturers to meet tight deadlines and improve overall production efficiency.
- Reduced Setup Times:
- In a traditional single-spindle machine, a part must be set up, spun, and then removed before the next one is processed. In contrast, with a double-spindle machine, one part can be processed on one spindle while another part is prepared on the second spindle, reducing downtime between operations. This capability is especially beneficial when working with identical or similar parts, as it eliminates the need for frequent retooling or setup changes.
- Tooling and Material Handling:
- Depending on the machine’s design, tooling and material handling may be integrated with the spindles to further streamline operations. Some double-spindle machines include automated systems for loading and unloading parts, as well as quick-change tooling systems that allow for faster switching between part designs. In some cases, these machines can accommodate multi-tool setups to perform additional tasks, such as trimming, deburring, or even welding, during the spinning process.
- Higher Accuracy and Consistency:
- As with other CNC-controlled machines, double-spindle machines often feature CNC control for precise movements and operations. This results in high repeatability and consistency across parts, ensuring that parts are produced with tight tolerances and high-quality finishes. The ability to control both spindles allows for symmetric operations and more precise control over material flow, resulting in better shape accuracy and surface quality.
- Complex Part Production:
- For complex geometries that require spinning on both sides, a double-spindle machine is highly effective. Parts with dual contours, internal/external shapes, or asymmetric designs benefit from this machine’s ability to work on both ends of a part simultaneously, making the production of sophisticated designs more manageable.
Advantages of Double-Spindle Metal Spinning Machines:
- Faster Production:
- By processing two parts at once, double-spindle machines effectively reduce the time required to produce components, making them highly suitable for mass production. The simultaneous processing also cuts down on machine idle time, improving overall throughput.
- Cost Efficiency:
- The ability to double production output without requiring additional machines or operators translates to lower manufacturing costs per part. This makes double-spindle metal spinning machines particularly attractive for manufacturers focused on reducing labor and operational expenses while maintaining high-quality standards.
- Consistency and Precision:
- Like other advanced metal spinning machines, double-spindle machines are capable of producing parts with high dimensional accuracy and smooth finishes. Because the spindles are controlled by a CNC system, they can apply consistent force and speed, ensuring that each part produced meets strict quality standards.
- Versatility for Different Part Types:
- The flexibility to work on both sides of a part, or to handle two different parts at once, gives this machine an advantage when dealing with varied production requirements. Whether producing simple cylindrical shapes or more complex, multi-featured parts, a double-spindle machine can be adapted to accommodate a wide range of designs.
- Reduced Human Intervention:
- With automation and CNC control, the need for manual labor is minimized. This reduces the likelihood of human error and increases overall safety in the production process. The automation also leads to fewer adjustments and interventions by operators, improving operational efficiency and minimizing downtime for recalibration.
- Improved Surface Finish:
- The use of precise tooling, consistent force, and CNC control ensures that the parts produced on a double-spindle machine have superior surface finishes. This is important in industries like aerospace and medical devices, where surface integrity is crucial.
Applications of Double-Spindle Metal Spinning Machines:
Double-spindle machines are ideal for applications where high-volume production and symmetry are critical. Some typical applications include:
- Automotive parts: Housings, wheel rims, and other components that require symmetrical spinning operations on both sides.
- Aerospace: Parts like engine components, nozzle casings, and fuel tanks that require both sides to be shaped simultaneously to meet tight tolerances.
- Lighting: Reflectors, lids, and other components that need to be spun on both sides for aesthetic and functional purposes.
- Industrial components: Cylindrical or spherical housings, flanges, and other parts used in machinery and equipment that require precision and symmetrical shaping.
- Medical devices: Components such as implant housings, surgical tools, and medical instrument parts that need to be both accurate and smooth.
Conclusion:
A Double-Spindle Metal Spinning Machine offers a significant leap forward in productivity, precision, and flexibility compared to traditional metal spinning machines. With the ability to process two parts simultaneously or perform dual operations on a single part, these machines are ideal for high-volume production environments. The integration of CNC control, multi-axis capabilities, and automated systems further enhances the efficiency and quality of the process, making them highly suitable for industries where speed, accuracy, and consistency are paramount. Whether producing automotive components, aerospace parts, or decorative metal products, double-spindle metal spinning machines provide manufacturers with the ability to meet demanding production schedules and maintain high-quality standards.
A Double-Spindle Metal Spinning Machine is an advanced machine that enhances the efficiency and flexibility of the metal spinning process by using two spindles. This design allows for simultaneous spinning operations, enabling the production of two parts or two sides of a part at the same time. This capability drastically increases throughput and reduces cycle times, making it particularly valuable in high-volume manufacturing environments where time and cost efficiency are critical. By processing two parts simultaneously or working on both ends of a part, the double-spindle machine doubles production capacity without requiring additional machinery or manual labor.
The key advantage of this setup is its ability to perform dual operations, such as spinning, forming, or even trimming, on multiple parts or surfaces at once. This helps reduce downtime and machine idle time, as one spindle can be engaged with one part while the other spindle is processing another, allowing for continuous operation. In many cases, the spindles can be independently controlled, enabling greater flexibility in handling parts with different sizes, geometries, or material properties. This independent control ensures precise adjustments to each spindle’s speed, force, and tool positioning, allowing manufacturers to optimize the process for different types of components.
Double-spindle machines also offer reduced setup times. Since both spindles can handle parts at the same time, the need for frequent retooling or repositioning between cycles is minimized. This reduces labor costs and downtime, enabling faster turnarounds. The ability to process parts concurrently makes double-spindle machines highly efficient in producing symmetric parts or parts with similar features. The use of CNC (Computer Numerical Control) technology ensures that the movements of both spindles are precise and repeatable, leading to consistent, high-quality outputs with tight tolerances.
The versatility of double-spindle machines extends to a wide variety of applications. For example, in industries like aerospace and automotive, parts often require symmetrical or complex shapes that benefit from being processed on both ends simultaneously. Additionally, double-spindle machines are suitable for making components that need both internal and external shaping, such as reflectors or housing components in industries like lighting and medical devices. These machines can also work with a range of materials, from lightweight metals to high-strength alloys, ensuring that manufacturers can meet the demands of various industries.
Automated material handling systems and quick-change tooling options further enhance the capabilities of these machines, allowing for seamless integration into a fully automated production line. In some cases, robotic systems are used to load and unload parts, further reducing manual labor and increasing overall operational efficiency. The ability to run multiple parts through the machine at the same time also means that double-spindle metal spinning machines can handle large orders and tight deadlines without compromising on quality.
Overall, double-spindle metal spinning machines offer a significant productivity boost by reducing cycle times, improving consistency, and enabling more complex part designs. These machines are indispensable for high-volume production runs where efficiency, cost-effectiveness, and precision are critical. The integration of advanced CNC control, automation, and flexible tooling makes double-spindle metal spinning machines a versatile solution for producing high-quality parts across a range of industries.
Multi-Spindle Metal Spinning Machine
A Multi-Spindle Metal Spinning Machine takes the principles of single- and double-spindle machines even further by incorporating multiple spindles into the metal spinning process. This machine configuration is designed to handle the simultaneous processing of several parts or multiple areas of a part, making it highly efficient for high-volume, complex manufacturing. Multi-spindle machines are particularly useful when producing large quantities of identical or similar parts, where maximizing output and minimizing cycle times are crucial.
The key advantage of a multi-spindle metal spinning machine is its ability to perform multiple operations at once. Each spindle can be assigned to process a separate part or a different side of a single part, allowing for increased throughput. With several spindles working simultaneously, the overall production rate is significantly increased compared to machines with fewer spindles. These machines are ideal for industries that require high productivity and fast turnaround times, such as automotive manufacturing, aerospace, electronics, and consumer goods.
In many configurations, each spindle can be independently controlled by a CNC system, allowing for precise adjustments to the speed, pressure, and positioning of the tool and part. This independent control ensures that the machine can handle parts with different geometries or materials simultaneously. The flexibility of independent spindle control allows manufacturers to fine-tune the process to meet the specific requirements of each part being produced, such as different wall thicknesses, curvatures, or material types.
Another key benefit of multi-spindle metal spinning machines is their ability to reduce setup times. Since the machine can process multiple parts at once, the overall setup time per part is reduced, which is particularly beneficial when working with small batches or frequent part changes. The integration of automated tool changers, robotic loading/unloading systems, and in-line inspection systems further improves the machine’s efficiency, reducing human intervention and ensuring continuous operation.
The design of these machines also typically allows for flexible tooling and material handling. Many multi-spindle machines come equipped with features that enable quick and easy changes of tooling, accommodating different part designs or material specifications without requiring significant downtime. Additionally, material handling automation can be used to streamline the loading and unloading of parts, further reducing manual labor and ensuring consistent part production.
Multi-spindle machines can be configured with a variety of spindles, often ranging from 3 to 6 or even more, depending on the production needs. This configuration is ideal for producing symmetrical parts, circular components, and reflective surfaces, such as lighting fixtures, engine components, automotive parts, flanges, and spherical housings. The use of several spindles allows manufacturers to meet demanding production schedules while maintaining the precision and quality required for high-performance parts.
Another important feature of multi-spindle metal spinning machines is their ability to handle a wide range of materials. The CNC-controlled system ensures that each spindle can be adjusted to handle different materials, from soft metals like aluminum to high-strength alloys like titanium or stainless steel. The precision of the CNC system ensures that the forming process is optimized for each material, allowing for consistent and accurate part formation.
In terms of quality control, multi-spindle machines often integrate advanced measurement systems, such as laser scanners or CMMs (Coordinate Measuring Machines), which monitor the dimensions and shape of each part during the spinning process. These systems provide real-time feedback to ensure that parts meet strict tolerances, reducing the likelihood of defects and ensuring a high level of quality consistency across all produced parts.
In conclusion, multi-spindle metal spinning machines offer significant advantages in terms of efficiency, productivity, and versatility. With the ability to process multiple parts simultaneously, these machines are ideal for high-volume production of complex, symmetrical components across industries like aerospace, automotive, medical devices, and consumer electronics. The combination of CNC control, automation, and multi-spindle capabilities ensures that manufacturers can meet the demands of large-scale production while maintaining high-quality standards and precise tolerances. These machines provide a powerful solution for manufacturers looking to increase output, reduce costs, and improve overall production efficiency.
A Multi-Spindle Metal Spinning Machine significantly boosts productivity by enabling the simultaneous processing of multiple parts or multiple sides of a single part. This configuration is ideal for high-volume production where speed, efficiency, and minimal downtime are crucial. The machine typically uses between three to six spindles, though more spindles can be incorporated depending on the specific needs of the production. Each spindle operates independently or in coordination with the others, and can be controlled via a CNC (Computer Numerical Control) system for precise adjustments in speed, pressure, and positioning.
By utilizing multiple spindles, this machine can cut cycle times in half or more compared to machines with fewer spindles, as several parts can be processed simultaneously. This is particularly valuable in industries such as automotive, aerospace, electronics, and consumer goods where large quantities of identical or similar parts are required. Whether producing parts like automotive housings, reflectors, or engine components, the ability to work on multiple parts at once ensures that production is faster and more cost-effective. The independent spindle control ensures that parts of varying geometries or materials can be processed in parallel, improving the flexibility of the machine for a variety of production runs.
The increased efficiency of multi-spindle machines also leads to reduced setup times, as parts can be simultaneously processed without needing to adjust or retool the machine after every cycle. This, along with automated material handling systems and robotic loading/unloading, helps minimize human intervention and makes the machine ideal for continuous, automated production lines. These features contribute to a smoother, faster workflow, reducing the time between cycles and allowing manufacturers to meet tight deadlines.
Additionally, multi-spindle machines are highly customizable in terms of tooling. The quick-change tooling system allows manufacturers to switch between different part designs or material types without significant downtime. For example, a multi-spindle machine could seamlessly transition from working on aluminum parts to working on stainless steel components, with the CNC system adjusting the process parameters to suit each material. The flexibility to handle various materials, including lightweight metals like aluminum, high-strength alloys like titanium, and even difficult-to-form metals like stainless steel, gives manufacturers the ability to tackle a wide range of parts with different requirements.
In terms of precision, multi-spindle machines are equipped with advanced measuring and quality control systems to ensure that parts are produced with high accuracy and meet strict tolerances. Systems such as laser scanners and coordinate measuring machines (CMMs) provide real-time feedback on the dimensions and shape of each part as it is spun. This integration of quality control directly into the production process reduces the risk of defects and improves the consistency of each part.
The ability to handle complex, symmetrical parts with multiple features, such as flanges, spherical housings, or reflective surfaces, makes multi-spindle machines ideal for a wide range of industries. Parts that require high precision and consistency across all units benefit from this machine’s ability to process multiple components at once, ensuring that every piece is produced with the same quality and minimal variation. Furthermore, multi-spindle machines also enable the efficient production of custom parts or smaller runs, giving manufacturers the flexibility to adjust processes without slowing down overall productivity.
In conclusion, multi-spindle metal spinning machines provide an ideal solution for manufacturers looking to boost production speed, reduce costs, and maintain high-quality standards across large-scale manufacturing runs. The ability to process multiple parts simultaneously, combined with the flexibility of CNC control, automation, and quality control systems, ensures that these machines are versatile, efficient, and cost-effective. Whether for aerospace, automotive, medical, or consumer goods applications, multi-spindle machines enable the production of complex parts at scale while maintaining the precision and consistency needed for high-performance components.
The use of multi-spindle metal spinning machines not only enhances production efficiency but also contributes to cost reduction over time. By enabling the simultaneous processing of multiple parts, these machines eliminate the need for additional equipment and manual labor, which can significantly cut operational costs. The automated nature of these machines, including the ability to manage multiple spindles, reduces human error, ensures uniformity in production, and allows manufacturers to optimize labor usage. This makes them particularly appealing to businesses focused on scaling production without increasing overhead.
Another significant benefit is space efficiency. Since multiple spindles can handle several parts at once, manufacturers are able to consolidate operations into a single machine, freeing up floor space. In industries where space optimization is essential, such as in high-output facilities or smaller workshops, multi-spindle machines provide a compact solution that maximizes output while reducing the need for multiple machines. This is particularly advantageous in facilities with limited space or those aiming to streamline operations without compromising on throughput.
Moreover, advanced features integrated into multi-spindle machines, like automated monitoring systems, ensure that each part produced is checked for quality during the spinning process itself. Continuous monitoring can identify potential issues before they become defects, allowing for immediate corrections. This proactive quality control minimizes scrap and rework, which is a major cost-saving benefit for manufacturers. The high precision offered by these machines also leads to reduced material wastage, as parts are made to tighter tolerances, ensuring that less material is wasted during the spinning process.
In addition to the production and operational advantages, multi-spindle machines also contribute to sustainability goals in manufacturing. The reduction of material waste, coupled with the energy efficiency of CNC-controlled operations, makes these machines a sustainable choice for manufacturers looking to meet environmental standards. The reduction in waste and the more precise use of raw materials help lower the carbon footprint of production processes, making multi-spindle machines an attractive option for companies committed to sustainability.
From a design perspective, multi-spindle metal spinning machines can accommodate complex shapes and geometries, expanding the possibilities of what can be produced. Components with intricate details, such as flanges, housings, or even custom-designed reflective surfaces, can be created with high accuracy and low tolerances. These machines are particularly beneficial for industries that require specialized, high-performance parts, including aerospace, automotive, and medical manufacturing.
The capability of these machines to process different materials, from soft metals like aluminum to more rigid alloys like titanium, makes them adaptable to a wide variety of production needs. Whether creating parts for lighting, automotive components, or military-grade equipment, multi-spindle machines can be set up to produce parts with the necessary properties, such as strength, weight, and durability, ensuring that the final products meet industry specifications.
In conclusion, multi-spindle metal spinning machines offer a highly efficient, cost-effective, and precise solution for manufacturers aiming to scale production while maintaining stringent quality standards. These machines excel in high-volume manufacturing, where the simultaneous processing of multiple parts not only boosts output but also improves consistency across batches. With their ability to handle complex parts, various materials, and multiple geometries, multi-spindle metal spinning machines are indispensable in industries that require precision-engineered components at scale. Their automation, flexibility, and space efficiency make them a valuable tool for manufacturers seeking to optimize their operations, reduce costs, and enhance product quality.
Single-Spindle Metal Spinning Machine
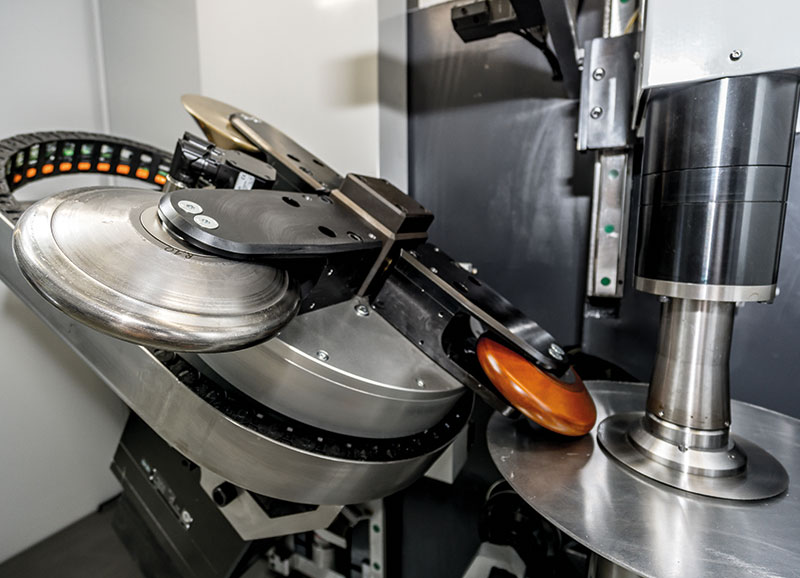
A Single-Spindle Metal Spinning Machine is the most basic and commonly used type of machine for metal spinning, where a single spindle is used to rotate the metal material while it is formed into the desired shape. This type of machine is widely used for producing symmetrical parts such as cylindrical, spherical, and conical shapes, which are common in industries like aerospace, automotive, lighting, and various consumer goods.
The core operation involves securing a flat disk or sheet of metal onto the spindle, which then rotates the material while a tool is applied to shape the material into a specific design. The process utilizes manual or CNC-controlled tools that press against the material to form it around a mandrel, creating the required shape. The machine’s simplicity makes it ideal for small-scale production or custom projects where high precision is necessary but in smaller volumes compared to multi-spindle machines.
Single-spindle machines are valued for their versatility as they can handle a wide range of materials, from aluminum to stainless steel, and are particularly useful for parts that don’t require high-volume output. Although they process only one part at a time, they allow for great flexibility in part design, often being employed to produce small, intricate components with detailed features.
The manual control of single-spindle machines provides operators with direct control over the spinning process, making them easier to use for prototypes, small batches, or parts with complex shapes that require frequent adjustments. Operators can modify parameters like spindle speed, feed rate, and pressure depending on the material and the desired outcome. For high-precision applications, many single-spindle machines now incorporate CNC control, allowing for more automated and consistent production of parts.
In terms of production capacity, single-spindle machines are typically slower than their multi-spindle counterparts since only one part is processed at a time. However, they are ideal for low to medium-volume production, particularly for custom-made parts, one-off prototypes, or when the production rate doesn’t justify the cost of more advanced machines. The machine’s affordability and simplicity also make it an attractive option for smaller workshops or businesses just starting out.
While single-spindle machines offer fewer spindles than more advanced machines, they still provide several benefits. Lower initial cost, reduced energy consumption, and ease of operation are significant advantages. Moreover, single-spindle machines can also handle a variety of tasks, such as trimming, beading, and flanging, adding to their flexibility.
In conclusion, a Single-Spindle Metal Spinning Machine is an essential tool in metal forming, offering simplicity, affordability, and flexibility for creating custom or low-volume parts. Despite its limitations in throughput compared to more advanced multi-spindle models, it is still highly valuable for applications requiring high precision and versatility, particularly in industries such as aerospace, automotive, lighting, and custom manufacturing. The balance of performance and cost makes single-spindle machines a popular choice in a variety of settings, from prototyping to smaller-scale production.
A Single-Spindle Metal Spinning Machine offers an efficient and cost-effective solution for creating metal parts with symmetrical shapes. Despite having only one spindle, which processes one part at a time, these machines provide significant flexibility and precision. They are ideal for applications where high customization is required, such as for creating parts with complex geometries or low-to-medium production volumes. These machines are frequently used in industries like aerospace, automotive, lighting, and medical device manufacturing, where precision is essential for producing parts like housings, reflectors, flanges, and engine components.
The machine works by rotating a metal disk or sheet on a spindle while a forming tool shapes the material. This can be done manually or with CNC (Computer Numerical Control) to improve the accuracy and consistency of the parts. For more intricate shapes or detailed features, operators can use hand tools to adjust the pressure or angle, allowing for fine-tuned results. With CNC capabilities, operators can automate the process for repeatable, high-quality outputs, ensuring that each part is consistently produced according to the design specifications.
One of the key benefits of a single-spindle machine is its simplicity. Since it is generally easier to operate and maintain than more complex machines with multiple spindles, it is a popular choice for smaller shops or businesses starting to invest in metal spinning. This also translates to a lower initial investment compared to multi-spindle machines, making it a more accessible option for companies with smaller production runs or those who require frequent changes in part designs.
Another advantage is its versatility. While it may only process one part at a time, a single-spindle machine can handle a wide variety of materials, including aluminum, brass, stainless steel, and titanium. This versatility allows manufacturers to produce parts that require different material properties, such as lightweight components for aerospace or durable parts for automotive applications. The ability to process multiple material types also helps businesses cater to diverse market needs without investing in multiple types of machines.
Though the throughput of a single-spindle machine is lower than that of more advanced, multi-spindle models, it still provides a valuable solution for custom, low-volume production runs. Since it processes one part at a time, it allows for greater control over the quality of each individual part. Operators can adjust the parameters for each specific part, ensuring that even complex or delicate components are formed with the desired precision. This makes the single-spindle machine a reliable choice for parts requiring fine tolerances or intricate features that might be difficult to achieve in high-volume production.
Additionally, these machines are ideal for prototype development or the production of one-off custom parts. When designing new products, engineers often need a way to quickly produce prototypes to test form, fit, and function before committing to larger-scale production. Single-spindle machines allow for rapid adjustments and modifications to designs, which can be crucial during the prototyping phase. They are also well-suited to custom orders, where the need for unique, non-repetitive components is common.
Maintenance and operation of a single-spindle machine are relatively straightforward, especially compared to more complex systems. With fewer moving parts and a simpler setup, these machines typically require less maintenance and downtime. This is an advantage for smaller operations, where minimizing machine maintenance is key to keeping production running smoothly and cost-effectively.
In terms of energy efficiency, single-spindle machines are also more economical, as they typically consume less power than their multi-spindle counterparts. This can be a key factor for businesses looking to reduce operating costs, especially in environments with tight profit margins.
In conclusion, a Single-Spindle Metal Spinning Machine provides a practical, affordable, and flexible solution for manufacturers producing low to medium volumes of custom parts. While it may not have the high throughput capabilities of multi-spindle machines, its ability to handle complex shapes, a variety of materials, and offer precision makes it a go-to option for industries requiring customization and high-quality standards. Whether used for prototyping, custom orders, or small batch production, the single-spindle machine remains a valuable asset in many metalworking operations.
Horizontal Spinning Lathe
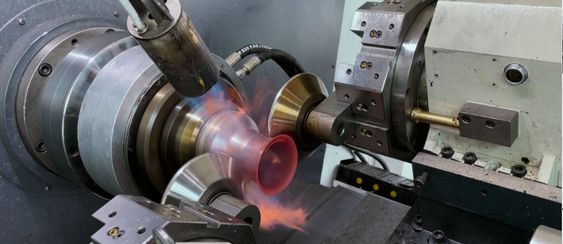
A Horizontal Spinning Lathe is a type of metal spinning machine designed for the creation of cylindrical, conical, and other symmetrical parts by rotating a metal blank or sheet. Unlike traditional vertical spinning lathes, where the workpiece rotates in a vertical orientation, horizontal spinning lathes position the workpiece horizontally. This configuration offers distinct advantages in terms of handling large or heavy parts, improving stability during the spinning process, and enabling a smoother workflow for certain types of workpieces.
In a horizontal spinning lathe, the workpiece is clamped onto a spindle that rotates horizontally. The operator uses tools that are applied against the rotating metal to shape it into the desired form. The workpiece is typically mounted on a mandrel, a tool that provides the support needed to shape the metal accurately. Horizontal spinning lathes are commonly used in the production of parts with symmetrical designs like reflectors, flanges, drums, housings, and spherical components, which are found across various industries, such as aerospace, automotive, defense, and lighting.
One of the main advantages of a horizontal spinning lathe is its ability to handle larger and heavier parts compared to vertical machines. The horizontal orientation allows gravity to assist in keeping the part stable and in position during the spinning process, which is particularly beneficial when working with larger diameter or thicker materials. This makes it a great choice for manufacturing large components or those that require significant structural integrity.
Another advantage of horizontal lathes is their ease of handling. The horizontal setup provides easier access for operators, who can work with the part from a comfortable, ergonomic position. Additionally, it can be easier to inspect parts during the spinning process since they are visible from a different angle compared to vertical machines. This visibility can help improve quality control, as operators can check the part’s progress as it is being spun.
Horizontal spinning lathes often come with CNC control, which enables highly accurate, repeatable, and automated processes. CNC systems allow for precise adjustments to speed, feed rate, and tool position, ensuring that parts are consistently manufactured within tight tolerances. The CNC functionality also allows for multi-axis control, enabling more complex parts to be spun with greater precision. Operators can program the lathe to create intricate designs with varying thicknesses, diameters, or geometries, further increasing the versatility of the machine.
The machine is particularly efficient for creating parts that have large diameters or wide faces. In reflector production (such as for lighting equipment or optical devices), for example, the horizontal spinning lathe allows the metal to be formed in one continuous motion, ensuring the surface remains smooth and uniform. For applications like aerospace or automotive manufacturing, where parts require consistent quality and uniform thickness, the precision offered by a horizontal spinning lathe is highly beneficial.
Horizontal spinning lathes can also offer better tool access and tool life. The horizontal arrangement makes it easier to set up and replace tooling, and because the machine is often designed to handle larger parts, tooling may last longer due to more uniform wear. This contributes to lower operational costs and higher productivity, as frequent tool changes or maintenance are minimized.
While horizontal spinning lathes are more specialized and are often used for certain types of parts, they offer significant benefits for larger, more complex components that require high precision. In addition to their ability to handle large workpieces, they provide stability, ease of access, and versatility, making them a valuable option in industries that require the production of large-diameter parts, symmetrical shapes, or components that demand high-quality standards.
Overall, the Horizontal Spinning Lathe is a powerful machine for metal spinning operations, especially when working with large parts, heavy materials, or complex geometries. Its horizontal configuration offers benefits in stability, accessibility, and ease of handling, while its precision and CNC control capabilities allow for efficient, high-quality production runs. Whether used for producing automotive housings, aerospace components, spherical shells, or reflective surfaces, horizontal spinning lathes are a crucial tool for manufacturers seeking to produce large, intricate, and high-quality metal parts.
A Horizontal Spinning Lathe is a specialized tool designed to produce high-quality, symmetrical parts by rotating a metal workpiece horizontally. The horizontal orientation provides unique benefits, especially when working with larger, heavier, or bulkier components. By positioning the workpiece horizontally, gravity naturally helps maintain stability, preventing the material from shifting or warping during the spinning process. This stability makes horizontal spinning lathes ideal for creating large components that require consistent material thickness and uniformity. Additionally, the horizontal setup provides a more accessible work environment for operators, who can position themselves comfortably and maintain better visibility of the part as it is being shaped.
The machine’s ability to handle larger diameter parts or heavier materials sets it apart from vertical spinning machines, making it especially useful for industries that require substantial components, such as automotive, aerospace, and defense manufacturing. Components like reflectors, flanges, spherical housings, and drums can be easily processed using a horizontal spinning lathe. For parts like reflectors used in lighting or optical systems, the horizontal machine offers a smooth, continuous forming process that helps maintain the desired surface finish and integrity of the part. The constant motion and control over the material ensure precision and minimize the risks of defects like wrinkles or distortion.
Another significant advantage of horizontal spinning lathes is their ability to perform complex spinning operations with greater ease and flexibility. CNC control is often integrated into these machines, providing automated processes that improve precision and repeatability. The CNC system allows for exact adjustments in parameters like spindle speed, feed rate, and tool pressure, resulting in a more controlled and consistent outcome. This is particularly beneficial for producing parts that need to meet tight tolerances and intricate shapes. Operators can program the machine for multi-axis control, enabling more complex geometries and varying thicknesses to be achieved with high accuracy.
The horizontal design also makes it easier to inspect parts during production, as operators can see the entire process from a different angle. This increased visibility allows for better monitoring and adjustment, reducing the chances of defects going unnoticed. Because the parts are positioned horizontally, the operator has easier access to the spinning area, which makes maintenance and tool changes more efficient. Tools tend to experience more uniform wear due to the improved stability of the workpiece, and the machine’s design often reduces tool wear over time, making the machine more cost-effective in the long run.
Horizontal spinning lathes are particularly useful for applications where large-diameter parts need to be produced with minimal distortion. Industries that manufacture automotive housings, aerospace components, or industrial equipment often require parts that must withstand high stress and extreme conditions. Horizontal lathes provide the necessary precision, strength, and versatility to create such parts while maintaining the integrity of the material. The machines are built to handle heavy materials, such as titanium and stainless steel, which are often used in aerospace and defense applications.
In addition to large parts, horizontal spinning lathes also excel at producing custom parts or low-to-medium-volume runs. The versatility of these machines allows manufacturers to adapt quickly to design changes, which is particularly useful for prototype development or when working with new materials. The ability to easily switch between different tool setups and adjust machine parameters gives manufacturers the flexibility to meet the unique requirements of each part, whether for small batch production or large-scale runs.
The precision and high-quality standards offered by horizontal spinning lathes are ideal for industries that demand exceptional craftsmanship. For example, in optical systems, lighting fixtures, or medical devices, the surface finish and shape accuracy are critical. Horizontal spinning lathes ensure that these components are produced with the utmost precision, which is essential for their proper functioning. In terms of energy efficiency, horizontal spinning lathes are often more economical than other machines due to their optimized designs and lower maintenance requirements, which results in reduced operational costs.
Overall, a Horizontal Spinning Lathe is a crucial piece of equipment in metal spinning, especially for industries that require large parts, complex shapes, and high-quality finishes. Its stability, precision, and flexibility make it an excellent choice for producing a wide range of components, from automotive parts to aerospace and defense applications. With advancements in CNC control and automation, horizontal spinning lathes continue to improve production speed and quality, while reducing material waste and downtime. This makes them indispensable for manufacturers looking to optimize their production processes and meet the ever-growing demand for high-performance, precision-engineered parts.
Vertical Spinning Lathe
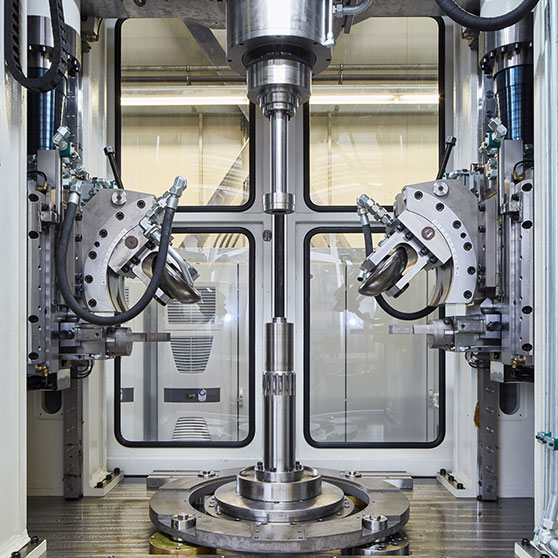
A Vertical Spinning Lathe is a type of metal spinning machine where the workpiece is mounted vertically on a spindle and rotated during the forming process. This setup is particularly advantageous for certain types of parts, especially when working with materials that require high precision or symmetrical shapes, such as reflectors, flanges, housings, and other circular or conical components. The vertical orientation provides several distinct benefits, making it an excellent choice for specific applications in industries like aerospace, automotive, lighting, and defense.
The key difference between a vertical and horizontal spinning lathe lies in the orientation of the workpiece. In a vertical spinning lathe, the workpiece is clamped onto a spindle that rotates in a vertical axis. The operator applies pressure from a spinning tool against the rotating metal, forming it around a mandrel to create the desired shape. Vertical lathes are often preferred for smaller, lighter parts or those that need to be formed with high precision over a shorter radius.
One significant advantage of a vertical spinning lathe is its ability to produce precise and consistent parts with minimal distortion. The vertical orientation helps to maintain better stability during the spinning process. As gravity works to keep the workpiece in place, the risk of material warping or shifting is reduced, leading to more accurate and uniform shapes. This makes vertical lathes particularly useful for high-precision components that require tight tolerances, such as parts used in aerospace or medical device manufacturing, where consistency and quality are paramount.
Vertical spinning lathes can also be easier to operate and maintain than horizontal machines in some cases. The setup of the machine allows the operator to be in a more ergonomic position when working with smaller parts. The machine is often more compact, making it ideal for smaller workshops or operations with space constraints. The vertical configuration can also make it easier to inspect the parts during production, as the operator has a direct view of the entire process. This visibility enhances quality control, as any irregularities or issues can be detected and corrected more easily during the spinning process.
Another notable advantage is the reduced footprint of vertical spinning lathes. Due to their compact design, these machines are ideal for manufacturers with limited space but who still require the ability to produce high-volume parts. The ability to rotate workpieces with high precision in a vertical plane can increase the overall throughput without sacrificing quality, making them well-suited for businesses focused on efficiency in mass production.
These lathes also offer ease of tool access and can accommodate various tooling types, from cutting tools to forming tools that press against the rotating metal. The vertical spindle allows for easier replacement of tools during production and less downtime. Furthermore, the use of CNC control in modern vertical spinning lathes enhances the machine’s ability to execute complex operations. With CNC capabilities, operators can program the lathe for multi-axis control, allowing for intricate shapes and forms that would be difficult to achieve with manual methods.
While vertical spinning lathes excel in producing small to medium-sized parts, their design also helps in the creation of highly detailed components. For example, in industries such as lighting, the precision needed to form reflective surfaces can be achieved with the stability and control offered by the vertical spinning process. Parts like optical reflectors, lenses, or automotive housings can be spun with smooth, uniform surfaces, ensuring optimal performance and quality.
The machine’s ability to work with a variety of materials, including aluminum, brass, stainless steel, and titanium, allows manufacturers to produce a wide range of parts with varying strength and durability characteristics. Vertical spinning lathes can handle both soft metals for lightweight applications and harder metals for high-strength components, making them versatile across different industries.
In conclusion, a Vertical Spinning Lathe offers a powerful and efficient solution for producing high-precision, symmetrical metal parts. Its compact design, ergonomic operation, and ability to handle complex geometries make it ideal for industries that require detailed and consistent components in low to medium production volumes. The vertical orientation enhances stability and precision, while the machine’s versatility allows manufacturers to work with a wide range of materials and produce intricate designs. For businesses looking for an efficient, high-quality spinning solution, vertical spinning lathes remain an essential tool in metalworking operations.
A Vertical Spinning Lathe is a specialized machine used to shape metal parts by rotating a workpiece in a vertical orientation. This configuration offers several advantages, particularly for smaller, high-precision components that require consistent, symmetrical shapes. The vertical alignment allows the workpiece to be securely mounted on the spindle, with gravity helping to keep the material stable and prevent shifting during the spinning process. This leads to improved accuracy, especially when producing parts with tight tolerances and complex geometries. Vertical spinning lathes are commonly used in industries that require high-quality, consistent parts such as aerospace, automotive, defense, and lighting.
The vertical setup helps maintain a high level of stability during the spinning process, reducing the risk of distortion and ensuring that the material is formed evenly. Parts such as reflectors, flanges, housings, and spherical components can be produced with superior accuracy and finish. Since the operator can work directly in line with the machine’s operation, this also facilitates better visibility of the spinning process, making it easier to monitor and correct any issues in real time. The vertical orientation is ideal for shorter radius or smaller diameter components, where the precision of the spin is critical.
Vertical spinning lathes are particularly beneficial for applications that require a smooth surface finish and consistent material thickness. These lathes can handle various materials, from lightweight aluminum to tougher metals like stainless steel and titanium. The ability to work with both soft and hard metals makes these machines versatile for a wide range of applications, including the production of automotive parts, aerospace components, and even medical devices. The machine’s flexibility is enhanced by the integration of CNC control, which automates many aspects of the spinning process, allowing for greater precision and repeatability.
Another advantage of vertical spinning lathes is their space efficiency. These machines are generally more compact than their horizontal counterparts, making them suitable for workshops with limited space. The vertical design also allows for easy access to the workpiece, improving ergonomics and reducing operator fatigue. The machine’s design ensures that parts are clearly visible throughout the spinning process, improving quality control by making it easier to spot any defects early in the production cycle.
In terms of maintenance, vertical spinning lathes are often simpler to maintain compared to more complex multi-spindle or horizontal machines. The ease of access to key components and tools allows for quicker maintenance and less downtime. Tool changes can be done efficiently, and the precision in tooling setup ensures that production can continue smoothly. For manufacturers looking for high throughput with consistent quality, vertical spinning lathes offer a cost-effective solution.
Despite their compact size and efficiency, vertical spinning lathes are also capable of handling intricate and detailed parts. The machine’s precise control over the speed and feed rate, especially with CNC integration, allows manufacturers to produce parts with highly detailed features and smooth finishes. This is particularly important for parts like optical reflectors, lighting equipment, or automotive housings, where uniformity in shape and finish is critical for the part’s performance. The ability to form these components with minimal variation helps reduce waste and improves overall production efficiency.
In conclusion, a Vertical Spinning Lathe offers a powerful solution for creating high-precision, symmetrical parts, especially in industries where accuracy and quality are paramount. The machine’s compact design, ease of operation, and CNC capabilities make it an excellent choice for businesses that need to produce high-quality parts in low to medium production volumes. Whether for automotive, aerospace, or medical applications, the vertical spinning lathe remains an indispensable tool in metalworking, providing stability, flexibility, and consistent results throughout the production process.
The Vertical Spinning Lathe is also favored for its efficiency in part handling. The vertical orientation simplifies the loading and unloading process, especially for smaller parts, as the operator can work from a convenient standing position. This allows for faster turnaround times between batches and minimizes the risk of handling errors, contributing to overall productivity in the shop. The design of vertical lathes, with their clear line of sight to the workpiece, also enhances the ability to make adjustments on the fly, ensuring that the part is being formed correctly and any potential issues can be addressed before they impact the quality of the final product.
Another important feature of vertical spinning lathes is their ability to handle both low and high volumes. While they may not be as fast as multi-spindle machines, they excel in environments where precision is more critical than sheer speed. For small batch production or custom part manufacturing, vertical spinning lathes are an excellent choice. This flexibility allows businesses to quickly adapt to changing demands, whether it’s creating one-off prototypes or a limited run of specialized parts.
Additionally, vertical spinning lathes are designed to offer consistent surface finishes, a crucial aspect in industries such as optics and lighting, where part appearance and surface quality are key to functionality. The smooth, uniform surface produced by these machines is vital for components that must interact with light or fit into precision-engineered assemblies, such as reflectors or housings. The consistency in surface finish, paired with the machine’s ability to produce uniform material thickness, ensures the part will perform as expected in its final application, minimizing the need for additional finishing or post-processing steps.
Vertical lathes also support advanced automation options. Many models come with robotic arms or material handling systems, allowing parts to be automatically fed into the machine and removed once they are finished. This further reduces labor costs and increases the throughput of the machine, particularly in environments where high volume and consistent quality are required. Automation also improves safety by reducing the need for manual handling of heavy or hazardous materials, and can extend the machine’s lifespan by reducing operator fatigue and error.
The versatility of vertical spinning lathes extends to their tooling options, which can be customized for specific tasks. For example, operators can use forming tools, cutting tools, or burnishing tools, depending on the desired finish and shape of the part. This flexibility allows the machine to be used for a wide range of applications, from simple cylindrical shapes to more complex geometries with varying thicknesses. The ability to customize tooling for different tasks ensures that the vertical lathe can handle a diverse set of projects without needing additional equipment or processes.
Maintenance on vertical spinning lathes is generally straightforward. Given their relatively simple design and fewer moving parts compared to multi-spindle machines, these lathes typically require less downtime for repairs or adjustments. Routine maintenance tasks, such as lubrication and tool checks, can be performed easily, contributing to a higher level of operational uptime. Regular maintenance not only ensures the longevity of the machine but also helps maintain the high precision required for the parts being produced.
Finally, as manufacturers look toward more sustainable and cost-efficient practices, vertical spinning lathes can contribute to reducing waste. The precise control over material deformation ensures that minimal scrap is generated during the spinning process. Additionally, the reduced energy consumption of vertical machines compared to larger, more complex multi-spindle systems can help lower overall operating costs, making them an attractive option for companies seeking to improve their environmental footprint while maintaining high levels of production efficiency.
In summary, Vertical Spinning Lathes remain a versatile, cost-effective, and precise solution for manufacturers who require high-quality, symmetrical parts. Their ability to handle a variety of materials, combined with their compact design, ease of use, and precision, makes them ideal for producing small to medium-sized parts in industries ranging from aerospace to medical device manufacturing. Whether for low-volume custom production or high-precision prototypes, the vertical spinning lathe offers significant benefits in terms of productivity, quality, and cost-effectiveness.
Mechanical Metal Spinning Machine
A Mechanical Metal Spinning Machine is a type of equipment used to form metal sheets or blanks into cylindrical or conical shapes through the application of mechanical force. This process, known as metal spinning, involves rotating a metal disc or sheet at high speed while a tool is applied to the material to stretch, shape, and form it into the desired geometry. The machine relies on mechanical systems, often powered by motors, gears, and hydraulic or manual mechanisms, to control the rotation speed and apply force during the spinning process.
In a mechanical metal spinning machine, the workpiece is typically mounted onto a spindle, and as the spindle rotates, the metal is shaped by a spinning tool. This tool is applied to the metal as it rotates, stretching the material and guiding it into the desired shape. The machine’s design allows for the creation of a wide range of shapes, from simple cylindrical parts to more complex conical or spherical geometries. The key to the process is the combination of rotational speed, tooling pressure, and the mechanical ability of the machine to form the metal effectively.
One of the main features of a mechanical metal spinning machine is its simplicity and ease of use compared to more advanced CNC machines. While CNC spinning machines offer high levels of precision and automation, mechanical machines are typically more manual or semi-automated. They often use geared mechanisms or hydraulic systems to apply consistent pressure and maintain rotational speeds. Operators can adjust settings like spindle speed and tool pressure to optimize the process for different materials and part designs. Mechanical machines can be easier to set up and maintain than more complex CNC systems, making them a good option for smaller workshops or low to medium-volume production runs.
The key advantage of mechanical metal spinning machines lies in their cost-effectiveness. These machines are typically more affordable than their CNC counterparts, making them an attractive option for businesses that need to produce parts without the large upfront investment required for automated systems. They can also be faster in certain applications, as the setup and operation are often less complex. Since the machine is manually controlled, operators have direct feedback during the spinning process, allowing for more flexibility when making adjustments or working on custom parts. This is particularly useful when producing prototypes or one-off parts that may require special adjustments.
These machines are commonly used in industries where low-volume production of symmetrical parts is required. For example, industries like aerospace, automotive, and lighting often need components with precise shapes, such as reflectors, housings, or drums, which are ideal candidates for mechanical metal spinning. The ability to work with a range of metals such as aluminum, brass, stainless steel, and copper makes mechanical metal spinning machines versatile for various applications.
The metal spinning process itself is highly efficient, as it generates little material waste compared to other methods like casting or stamping. The metal is simply stretched and formed, which can result in parts that are close to their final shape with minimal material waste. This can reduce production costs and improve overall efficiency. Additionally, the smooth surface finish achieved through the spinning process is often sufficient for many applications, reducing the need for additional finishing steps and further lowering production time and costs.
Mechanical metal spinning machines are also often used for producing parts that require high-strength or lightweight properties. The process can create thin-walled structures with uniform thickness, which is especially important in industries like aerospace where parts must be both lightweight and durable. The ability to create precise shapes and control the thickness of the material allows manufacturers to meet the performance requirements of various components while keeping material costs down.
One of the limitations of mechanical metal spinning machines is their manual nature. While this offers greater flexibility for low-volume runs or custom parts, it may not be as suitable for high-volume production where consistency and automation are critical. For large production runs, a CNC metal spinning machine would typically be more appropriate, as it can produce large quantities of parts with minimal operator intervention. However, for businesses that need to balance precision with cost-effectiveness and are focused on low to medium production volumes, a mechanical metal spinning machine is a reliable and efficient tool.
In summary, mechanical metal spinning machines offer a practical solution for manufacturers requiring custom or low-volume production of symmetrical metal parts. Their simplicity, cost-effectiveness, and ability to handle various materials make them an ideal choice for industries such as aerospace, automotive, lighting, and defense. While they may not offer the level of automation or precision of CNC machines, their flexibility, ease of use, and lower cost make them a valuable tool in many manufacturing environments.
A Mechanical Metal Spinning Machine is primarily designed for creating symmetrical metal parts through a process where a metal blank is rotated at high speeds, and a tool is applied to shape the material. This spinning process is used to create parts with cylindrical, conical, or even complex curves and radii. The machine typically uses a spindle and a set of mechanical systems, such as geared mechanisms or hydraulic presses, to rotate the metal blank and apply consistent pressure during the shaping process. The workpiece is mounted on a spindle that rotates as the operator or automated systems move the shaping tool to form the part.
The operation of mechanical spinning machines is often manual or semi-automated, which differentiates them from more sophisticated CNC machines. The manual nature gives operators more direct control over the process, making them ideal for jobs where flexibility is key. While not as precise as CNC metal spinning machines, they offer a practical and cost-effective solution for low- to medium-volume production. These machines can form parts that range from simple designs to more intricate geometries depending on the type of tooling and the experience of the operator. The operator typically adjusts spindle speed, tool pressure, and feed rate manually or through semi-automated controls to achieve the desired shape.
Mechanical spinning machines are versatile and capable of handling a range of materials such as aluminum, copper, brass, and stainless steel. The spinning process is often preferred over other metal forming methods, such as casting or stamping, due to the low material waste generated. As the material is stretched and formed rather than cut or shaved away, the process creates minimal scrap. This makes mechanical spinning machines an economical option for producing thin-walled, high-strength components with uniform thickness, making them particularly useful in industries like aerospace, automotive, lighting, and defense.
In addition to low material waste, the surface finish achieved by mechanical spinning is often quite smooth, reducing the need for additional finishing operations. This makes it ideal for parts that require aesthetic quality or high functional performance. For instance, in industries like lighting, reflectors and lampshades benefit from the smooth surface and uniform material properties that mechanical metal spinning provides. Similarly, automotive components like housings or drums are often produced using this method, as the metal can be formed into exact shapes while maintaining the required strength and durability.
One of the significant benefits of mechanical spinning machines is their cost-effectiveness, especially for businesses focused on producing low to medium volumes of parts. These machines are more affordable compared to automated systems like CNC spinning machines, and their setup is generally faster. Since they don’t require the same level of automation or sophisticated programming, they are often preferred by smaller workshops or for custom jobs that involve a variety of shapes or materials. The reduced upfront investment and maintenance costs make them an attractive option for companies that need flexibility but want to keep their operational costs low.
Mechanical metal spinning machines are typically best suited for producing parts in low-volume or custom production runs. Because they are manually operated or semi-automated, they allow for quicker adjustments in response to design changes or the need for specialized, one-off parts. However, for mass production or situations requiring high repeatability, more advanced CNC machines would be more appropriate. Despite this, the ability of mechanical machines to handle a wide range of materials and create parts with minimal waste makes them highly effective for many small-to-medium businesses or those focused on prototyping.
Another advantage of mechanical metal spinning machines is their simplicity of design, which makes them easier to maintain and repair compared to more complex machines. Their mechanical nature means there are fewer electronics or software components that might malfunction, leading to lower maintenance costs and quicker repairs. This is particularly beneficial in environments where downtime must be minimized. Routine maintenance tasks, such as lubrication and tool checks, can be performed with ease, ensuring the machine operates smoothly over long periods.
Overall, mechanical metal spinning machines offer an efficient, flexible, and cost-effective solution for producing a wide range of symmetrical metal parts. While they may not offer the same level of precision and automation as CNC machines, their ability to handle various materials, create high-quality finishes, and work with a variety of designs makes them a valuable tool in many manufacturing environments. They provide a great balance between affordability, versatility, and production speed, making them a preferred choice for industries requiring low-volume production, custom parts, or prototype development.
Hydraulic Metal Spinning Machine
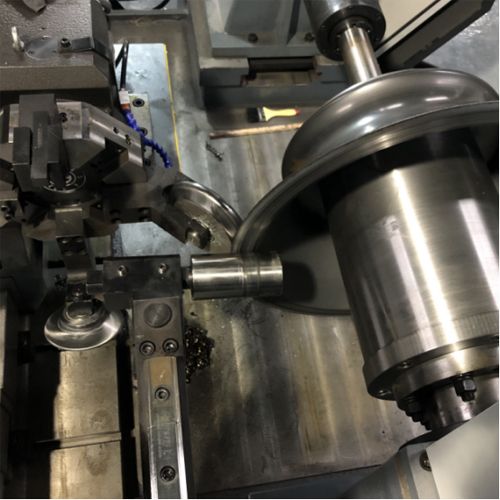
A Hydraulic Metal Spinning Machine utilizes hydraulic power to apply force to the workpiece during the spinning process. In this machine, the hydraulic system is responsible for providing the necessary force to shape the metal as it rotates. The workpiece is mounted on a spindle and is spun at high speeds while a forming tool is applied to the rotating material. The hydraulic mechanism, which uses fluid under pressure to generate force, enables smooth and consistent pressure application, making it highly effective for shaping metal parts with uniform thickness and smooth surface finishes.
The hydraulic system in these machines typically allows for precise control over the amount of force applied to the material, which is crucial when working with metals that require consistent deformation. Unlike mechanical spinning machines, which rely on gears and manual adjustments, hydraulic spinning machines provide greater flexibility and more consistent pressure. The hydraulic pressure is typically controlled via a pump and valves, which regulate the amount of force applied during the spinning process. This ensures that the material is formed without excessive distortion, which is especially important for parts that require tight tolerances.
One of the major benefits of hydraulic metal spinning machines is their ability to handle thicker materials and produce larger parts compared to other types of spinning machines. The increased force provided by the hydraulic system allows the machine to spin metal blanks that are more difficult to shape using manual or mechanical methods. This makes them suitable for creating large components, such as automotive parts, aerospace components, lighting fixtures, and even pressure vessels.
The hydraulic system offers smooth, controlled pressure, which is beneficial for producing parts with high precision and consistent material thickness. The uniformity in the wall thickness is especially important in applications where the part needs to have consistent strength throughout, such as in tanks or piping systems. The ability to apply constant force across the entire surface of the part helps to avoid material stress or distortion, which could compromise the quality or performance of the final product.
Another key advantage of hydraulic spinning machines is their ability to adjust quickly to different materials and part shapes. Whether working with aluminum, stainless steel, brass, or other materials, the hydraulic system can provide the right amount of pressure for various thicknesses and characteristics. This flexibility makes hydraulic metal spinning machines suitable for industries that require a wide range of metal parts, from thin-walled components to thicker, high-strength parts.
Hydraulic metal spinning machines are also highly effective for producing complex shapes with detailed features. Because the hydraulic system allows for precise control over the pressure and feed rate, operators can form intricate geometries with a high degree of accuracy. This makes them ideal for producing conical shapes, spherical components, and other complex forms used in aerospace, automotive, and energy sectors. The versatility of the hydraulic system also allows for easy adaptation when changes need to be made to the part design or when transitioning between different sizes and shapes.
In addition to their precision, hydraulic metal spinning machines offer increased productivity. The consistent pressure provided by the hydraulic system allows for faster production cycles compared to mechanical machines, as there is less need for manual adjustments during the process. The automated nature of the hydraulic system reduces the chances of human error and speeds up the overall process, making it a more efficient choice for medium to high-volume production.
These machines also offer a better surface finish than many other metal forming methods. The hydraulic force helps to evenly distribute pressure across the surface of the part, resulting in a smooth and uniform finish. This is especially beneficial for industries like lighting, where the visual quality of the parts is critical, or aerospace, where the parts need to meet strict performance standards.
However, one potential drawback of hydraulic metal spinning machines is their higher initial cost and maintenance requirements. Hydraulic systems involve more components, such as pumps, hoses, and valves, which can require more maintenance and repair over time. Additionally, hydraulic systems can be more complex to operate, requiring skilled technicians to ensure proper setup and operation. Despite these challenges, the advantages of hydraulic power, particularly in terms of force control and versatility, make these machines highly valuable for certain production needs.
In conclusion, a Hydraulic Metal Spinning Machine is an advanced and powerful tool used in industries that require high-precision, high-strength, and large or complex metal parts. The ability to apply controlled pressure, adjust easily to different materials, and produce detailed, intricate shapes makes it a go-to solution for manufacturing parts in aerospace, automotive, energy, and lighting sectors. Although they come with higher initial costs and maintenance requirements compared to mechanical or manual machines, their efficiency, precision, and flexibility make them an essential piece of equipment for producing high-quality metal components in medium to large-scale production runs.
A Hydraulic Metal Spinning Machine is particularly valued for its ability to produce parts with high precision and uniformity, especially when dealing with thicker or more difficult-to-form metals. The hydraulic system allows for constant and controlled force application, which is crucial when working with materials that need to be formed into complex shapes without compromising the integrity or strength of the part. This makes hydraulic spinning ideal for industries where quality and durability are paramount, such as aerospace and automotive manufacturing, where parts must meet strict tolerances and perform reliably under stress. The ability to consistently apply force without fluctuations makes it possible to achieve even wall thicknesses and smooth finishes that would be difficult to replicate with mechanical or manual systems.
In addition to handling thicker materials, hydraulic metal spinning machines can also work with a wide variety of metals, including soft metals like aluminum and copper to harder metals like stainless steel and titanium. The versatility of the hydraulic system enables it to adapt to different materials and varying thicknesses, allowing manufacturers to create a diverse range of parts. This flexibility makes it a highly sought-after solution in industries where manufacturers are producing a mix of standard and custom components.
The hydraulic power also provides a level of automation and consistency that reduces the risk of errors that can occur with manual operation. For instance, once the correct pressure settings are established for a given material and part shape, the hydraulic system will maintain this force consistently throughout the spinning process, ensuring a high level of repeatability across production runs. This consistency is important not only for achieving high-quality parts but also for maintaining production efficiency and reducing the need for rework or part rejection.
Another benefit of hydraulic metal spinning machines is their ability to handle complex, detailed geometries with ease. The controlled application of pressure is particularly useful for forming parts with intricate curves, conical shapes, and thin walls, which are often required in industries like lighting, where aesthetic quality is just as important as functionality. The ability to manipulate the material with precision ensures that the final product will meet the required strength, appearance, and fit specifications, often without the need for extensive post-processing.
Furthermore, hydraulic metal spinning machines often come equipped with advanced control systems, allowing for easy adjustments during the production process. Operators can adjust pressure, speed, and tooling position on-the-fly to accommodate changes in part design or material properties. This flexibility ensures that the machine can be adapted quickly for different production runs and custom parts, which is essential for manufacturers who deal with a variety of orders and need to switch between different products frequently.
Despite their many advantages, hydraulic metal spinning machines do come with some higher operational costs, particularly when it comes to maintenance. The hydraulic components, such as the pumps, valves, and hoses, require regular inspection and maintenance to ensure they are functioning properly. Over time, the hydraulic system can develop leaks or experience wear, which may require repairs or replacements of parts, adding to the operating costs. Additionally, the complexity of the hydraulic systems means that operators and maintenance personnel often require specialized training to operate and maintain the equipment safely and efficiently.
However, for many manufacturers, the benefits of hydraulic metal spinning far outweigh the challenges. The combination of high precision, flexibility, and control over material deformation makes these machines a top choice for producing high-quality metal parts in a wide range of industries. The automated force application reduces the risk of defects, while the consistent pressure ensures that each part produced meets the strictest quality standards. Whether it’s producing automotive components that need to withstand extreme conditions, aerospace parts that must meet rigorous specifications, or lighting fixtures with flawless finishes, hydraulic spinning machines provide the necessary capabilities to meet those demands.
Overall, the hydraulic metal spinning machine is a versatile and powerful tool that offers significant advantages in terms of precision, efficiency, and productivity. For manufacturers looking to produce high-quality, durable, and precisely formed metal parts, these machines offer a reliable solution that can handle a variety of materials and part shapes, making them an essential piece of equipment in modern manufacturing operations.
Rotary Shear Forming Machine
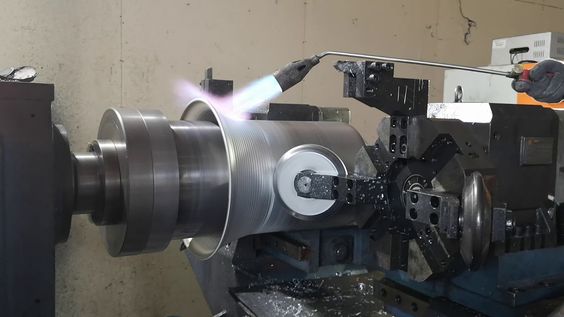
A Rotary Shear Forming Machine is a specialized piece of equipment used for shaping and forming metal sheets through a combination of shearing and rotational motion. This machine is commonly employed in industries where high-precision cuts and shapes are required, such as in metalworking, automotive, and aerospace manufacturing. The process involves using rotating tools or blades that cut or shape the material while it is held in place, enabling the formation of specific geometries with high efficiency.
The core function of a rotary shear forming machine is to apply a rotating shear force to the material, which can result in a clean and precise cut or shape. The metal sheet or blank is typically fed into the machine, and the rotating blades or shearing tools move across the material to cut it into the desired shape. This type of machine is particularly effective for working with thin metal sheets or coils, as it allows for fast and precise cuts without the need for complex tooling or excessive material waste. By rotating the cutting tool while simultaneously applying force, the machine ensures a high-quality finish and accurate dimensions.
One of the major benefits of rotary shear forming machines is their speed and efficiency. These machines are capable of high-volume production runs, as the rotary shear process can quickly cut and shape large quantities of metal in a short amount of time. This is especially useful for industries that require mass production of parts with uniform specifications, such as automotive manufacturers who need to cut metal body panels or aerospace companies producing lightweight metal components.
Another advantage of rotary shear forming machines is their ability to create parts with high precision and tight tolerances. Since the shearing process is highly controlled, the resulting parts are often free of burrs or other imperfections that can sometimes result from other cutting methods, such as stamping or laser cutting. The rotary motion ensures that the blades stay in constant contact with the material, which helps to produce smooth edges and reduce the risk of deformation during the cutting process.
Rotary shear forming machines also offer versatility in terms of the materials they can handle. While commonly used for sheet metal, these machines can also work with other materials, such as plastics, composites, or even thin non-ferrous metals, depending on the machine’s capabilities and the type of blades used. This flexibility makes them an ideal solution for manufacturers who need to cut a variety of materials and handle different part designs. Additionally, adjustable blade settings allow operators to tailor the machine to accommodate different thicknesses or types of materials, further enhancing its versatility.
The automation capabilities of rotary shear forming machines also play a significant role in their popularity in modern manufacturing environments. Many rotary shear forming machines are equipped with computerized controls, allowing for automated adjustments to cutting speeds, blade pressure, and other settings. This helps to optimize the cutting process, reduce human error, and increase overall production efficiency. In some advanced models, CNC systems can be used to precisely control the operation, ensuring repeatable accuracy and allowing for the production of complex shapes without the need for constant manual adjustments.
Despite their many benefits, rotary shear forming machines may have certain limitations. For instance, they may not be the best choice for thicker metal sheets or high-strength materials, as the shearing process can become less effective when dealing with tougher materials. In these cases, other metal forming methods, such as laser cutting, water jet cutting, or plasma cutting, may be more appropriate. Furthermore, while the machine provides precise cuts, it may not be the ideal choice for creating deep or intricate shapes, as the shearing process is typically better suited for simpler cuts and shapes.
Maintenance is also an important consideration for rotary shear forming machines. Since they involve rotating blades that come into direct contact with the material, blade wear and maintenance are common challenges. Regular inspection and replacement of blades are necessary to ensure optimal performance, and keeping the machine in good working condition is key to maintaining the quality of the cuts. Additionally, the rotating components may require lubrication and other upkeep to prevent wear and tear over time.
In summary, a Rotary Shear Forming Machine is a highly efficient and precise tool for cutting and shaping thin metal sheets and other materials. Its ability to quickly and accurately produce parts with clean edges and tight tolerances makes it an excellent choice for industries requiring high-volume production runs of metal components. With its versatility, speed, and automation capabilities, the rotary shear forming machine is a valuable asset in the metalworking, automotive, and aerospace industries. However, manufacturers should consider its limitations when working with thicker or stronger materials and ensure proper maintenance to keep the machine operating at peak performance.
A Rotary Shear Forming Machine is an essential tool in industries where high-speed, high-precision cutting and shaping of materials are required. It operates by rotating sharp, shearing blades across a metal sheet or coil, applying continuous force to create clean and accurate cuts. This process is especially effective for thin metal sheets, such as those used in the automotive, aerospace, and sheet metal fabrication industries, as well as for coils that need to be cut into specific lengths or shapes.
The speed and efficiency of rotary shear forming machines are significant advantages, particularly for high-volume production runs. These machines can handle large quantities of material, allowing for the rapid and consistent production of parts. This is particularly beneficial in environments where mass production is necessary, such as in the manufacturing of automotive body panels or aerospace components that require uniform cuts with minimal material waste.
The precision offered by rotary shear forming machines ensures that the parts produced meet strict tolerances. The clean cuts made by the rotating blades help to avoid defects such as burrs or jagged edges, resulting in high-quality parts that need little to no additional finishing. This is particularly useful for components where a smooth edge or a high level of surface quality is important, such as parts used in lighting or electronic housings. The machine’s ability to maintain uniform pressure across the material also helps to achieve consistent results across multiple parts, ensuring repeatability in production.
One of the key benefits of rotary shear forming machines is their versatility in handling a variety of materials. While primarily used for cutting sheet metal, these machines can also be used to cut other materials like plastics, composites, or even non-ferrous metals. The adjustable settings of the machine allow operators to work with different material thicknesses, making it adaptable for a range of applications. This versatility allows manufacturers to handle multiple production runs without needing to invest in different machines for each type of material.
Another advantage is the machine’s automation capabilities. Many rotary shear forming machines are equipped with automated controls that allow for easy adjustment of cutting speeds, blade pressure, and other parameters. This automation increases production efficiency, reduces the likelihood of human error, and ensures that parts are consistently produced to specification. In some advanced systems, CNC (Computer Numerical Control) integration enables even more precise control over the cutting process, making it possible to create complex shapes or patterns that would be difficult to achieve manually.
However, despite its many advantages, a rotary shear forming machine does have certain limitations. It is not ideal for cutting thicker metals or high-strength materials, as the shearing action becomes less effective on tougher materials. For cutting thicker sheets or harder metals, manufacturers may need to use other methods such as laser cutting or water jet cutting, which provide more power to handle these tougher materials. Additionally, while rotary shear forming machines are excellent for creating simple cuts or straight edges, they may not be as effective for forming parts with deep grooves or intricate features, as the cutting process is typically limited to more basic shapes.
The maintenance of rotary shear forming machines is also a critical consideration. Since these machines rely on rotating blades, blade wear can become a significant issue over time. To maintain cutting efficiency, operators must regularly check and replace the blades. Proper lubrication of moving parts is also essential to prevent excessive wear and ensure smooth operation. Regular inspection of the machine’s mechanical components, such as motors and drives, is necessary to ensure it continues to operate at peak performance.
Despite these challenges, the overall benefits of a rotary shear forming machine make it a valuable investment for manufacturers looking to produce high-precision, high-speed cuts in large quantities. Its ability to handle a range of materials, its efficient operation in high-volume production settings, and its precision make it ideal for industries that require consistent and accurate cuts. With proper maintenance and careful material selection, a rotary shear forming machine can be an integral part of a manufacturer’s production line, ensuring that parts are produced with the necessary quality, speed, and efficiency.
Double-Action Shear Forming Machine
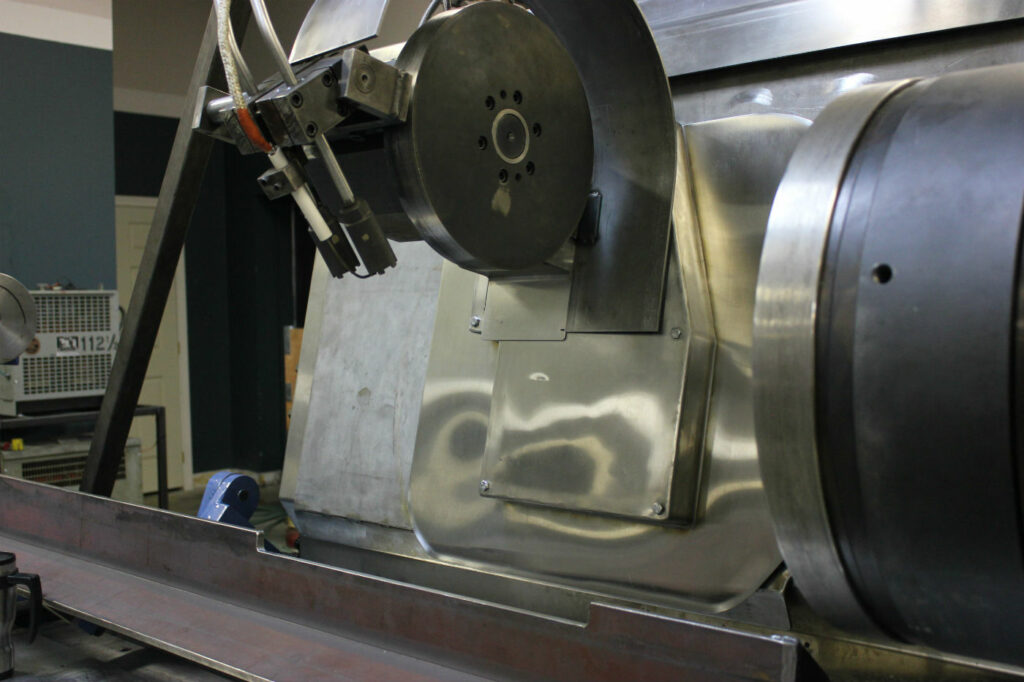
A Double-Action Shear Forming Machine is a specialized piece of equipment used in metalworking to shape and form metal sheets through a combination of shearing and forming actions. This machine uses two distinct sets of actions, hence the term “double-action,” to create intricate shapes and cuts with a high degree of precision. It is primarily employed in industries that require complex metal forming operations, such as aerospace, automotive, and industrial manufacturing, where parts must be created with tight tolerances and exact specifications.
In a double-action shear forming machine, the process involves two key movements: a shearing action that cuts the metal, and a forming action that shapes the material into the desired configuration. The shearing action is typically performed by a set of blades or cutting tools that apply force to the material to produce clean and accurate cuts. The forming action follows, where the machine uses a set of tools or dies to apply pressure to the metal, shaping it into complex geometries or specific profiles.
The double-action nature of this machine is advantageous because it allows for the combination of two essential operations—cutting and shaping—in a single, integrated process. This reduces the need for multiple machines or steps in the production process, streamlining operations and increasing overall production efficiency. It also helps to reduce the time and labor costs associated with producing complex parts.
One of the key benefits of a double-action shear forming machine is its ability to handle complex shapes and intricate geometries. The combination of cutting and forming actions allows manufacturers to produce parts with detailed contours, flanges, ribs, or other features that would be difficult or impossible to achieve with a single-action machine. This makes it ideal for producing parts used in aerospace and automotive applications, where high precision and complex shapes are often required.
The precision provided by a double-action shear forming machine is another major advantage. The integrated shearing and forming actions ensure that the material is cut and shaped to exact specifications, resulting in parts that meet tight tolerances and have minimal imperfections. This is particularly important in industries where high-quality standards are essential, such as in the production of aerospace components, where even the slightest deviation from specifications can result in failure or malfunction.
In addition to its precision, the speed and efficiency of a double-action shear forming machine make it a valuable asset for manufacturers. By combining two processes into one machine, manufacturers can produce parts more quickly, reducing cycle times and increasing overall throughput. This makes it ideal for high-volume production runs, as it can handle large quantities of parts while maintaining consistent quality. Additionally, the machine’s ability to form parts with minimal material waste further contributes to cost savings and resource efficiency.
Another important feature of double-action shear forming machines is their ability to handle a wide range of material types and thicknesses. The machine can be adjusted to accommodate various materials, such as steel, aluminum, copper, or composite materials, and can be fine-tuned to work with different thicknesses or hardness levels. This versatility allows manufacturers to use the same machine for a variety of projects and product lines, reducing the need for multiple machines or setups.
Despite the many advantages, there are some challenges associated with the operation of double-action shear forming machines. One of the primary concerns is the maintenance of the machine’s shearing and forming tools. The cutting tools, in particular, are subject to wear over time, especially when working with tougher materials, and may require regular sharpening or replacement. Additionally, since these machines involve both shearing and forming actions, the process can generate heat and friction, which can lead to tool degradation or damage if not properly managed. Regular maintenance and periodic checks are essential to keep the machine in optimal working condition.
Another potential limitation is the complexity of the machine. Double-action shear forming machines often require skilled operators to ensure the settings are adjusted correctly for different materials, thicknesses, and part designs. Proper training is necessary to handle the machine effectively and avoid errors in the forming process. Additionally, because the machine performs two operations in one, the setup and adjustment can take more time than a simpler, single-action machine.
In summary, a Double-Action Shear Forming Machine is a highly effective tool for manufacturers who need to produce complex metal parts with high precision and efficient use of materials. By combining shearing and forming actions in a single machine, it allows for faster production cycles, reduced material waste, and the ability to produce detailed shapes and components that meet tight tolerances. Though the machine requires regular maintenance and skilled operation, the benefits of increased speed, precision, and versatility make it an essential tool for industries such as aerospace, automotive, and industrial manufacturing.
A Double-Action Shear Forming Machine is an advanced tool used to shape and cut metal sheets or coils, combining two critical processes—shearing and forming—into a single machine. This integration makes it an efficient and versatile option for producing parts with high precision and intricate shapes, especially in industries like aerospace, automotive, and industrial manufacturing. The machine uses two distinct sets of actions: the first involves shearing the metal, often using rotating blades or cutting tools, while the second applies pressure to the material, forming it into more complex shapes such as contours, flanges, or ribs. By combining these actions, the machine streamlines the production process, eliminating the need for multiple machines or steps. This results in faster production times and reduced labor costs, making it ideal for high-volume manufacturing environments.
One of the main advantages of the double-action system is its ability to handle complex geometries and intricate features. The shearing action first trims the material to size, while the forming action shapes it, allowing for detailed contours and profiles that would be difficult to achieve with simpler machines. This makes it particularly useful for industries that require parts with high precision and tight tolerances, such as aerospace, where even minor deviations can affect the functionality of components. The precision of the machine ensures that the parts are formed accurately to the required specifications, reducing the likelihood of defects and the need for rework.
In addition to precision, the machine offers speed and efficiency. Since the shearing and forming operations are combined into one process, manufacturers can produce parts quickly without having to switch between different machines or steps. This is especially beneficial for high-volume production runs, where time efficiency is crucial. The ability to cut and form in a single operation also reduces material waste, as the machine can be set to minimize excess material during the process. This not only leads to cost savings but also contributes to a more sustainable production process.
The versatility of a double-action shear forming machine is another key advantage. The machine can handle a wide range of materials, including steel, aluminum, and composites, and it can be adjusted to work with different material thicknesses and hardness levels. This flexibility makes it an ideal solution for manufacturers who need to produce a variety of parts with varying specifications. By changing settings or using different dies, the machine can accommodate different designs and part geometries, allowing manufacturers to switch between projects quickly without the need for significant downtime.
However, there are some challenges associated with the operation of a double-action shear forming machine. One of the most significant issues is maintenance. The shearing and forming tools can wear out over time, especially when working with harder or thicker materials. Regular inspection, sharpening, or replacement of the blades and dies is required to maintain optimal performance. Additionally, because the machine performs two operations simultaneously, the tools may experience increased wear and tear, which can impact the quality of the finished parts if not properly managed.
Another consideration is the complexity of the machine. Double-action shear forming machines require skilled operators to adjust settings accurately for different materials and part designs. The integration of two actions—shearing and forming—can make setup and adjustments more involved compared to simpler machines, which may result in longer preparation times. Training and experience are essential to ensure that operators can handle the machine effectively and avoid errors that could compromise part quality or production efficiency.
Despite these challenges, the double-action shear forming machine provides significant benefits in terms of production speed, precision, and material efficiency. Its ability to combine cutting and forming in a single process makes it an invaluable tool in industries that require high-precision, high-quality parts in large quantities. By streamlining the production process and reducing material waste, the machine offers a cost-effective solution for manufacturers producing components that need to meet stringent tolerances and complex geometries. When maintained properly and operated by skilled personnel, a double-action shear forming machine can greatly enhance a manufacturer’s capabilities and throughput, making it an essential asset in modern manufacturing environments.
Single-Action Shear Forming Machine
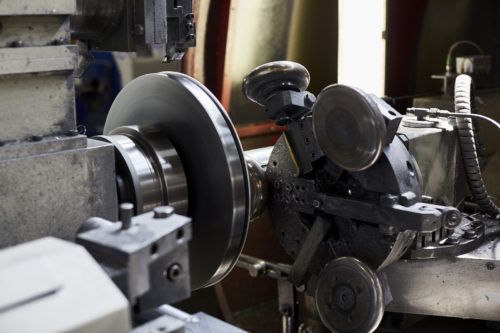
A Single-Action Shear Forming Machine is a specialized tool used to shape and cut metal sheets or other materials in a single operational step. It performs primarily shearing, where a cutting tool applies force to the material, resulting in clean, precise cuts. While its operation may focus primarily on cutting, it can also incorporate some degree of forming or shaping through the use of specific tools or dies. These machines are widely used in industries such as automotive, aerospace, sheet metal fabrication, and construction, where accurate cuts are crucial, and sometimes light forming is needed to create specific geometries or edges.
The single-action design of this machine means that it typically focuses on one main function at a time—shearing or forming—but is optimized to perform that task with high efficiency. The machine may involve a simple cutting tool or blades, which apply significant force to the material to shear it into the desired size or shape. For example, sheet metal can be cut into panels or strips, which is a common requirement in many manufacturing processes. The forming component in some models may involve light bending, curving, or edge rounding after the shearing process.
One of the key advantages of a single-action shear forming machine is its simplicity and ease of use. Because it focuses on one operation at a time, operators can quickly set up and start production, making it ideal for simpler parts or tasks that require high volume but less complexity in the design. This simplicity also means that maintenance and troubleshooting are generally more straightforward compared to more complex systems. There are fewer components involved, and since it focuses on shearing, there are typically fewer wear issues compared to machines that also perform more intricate forming operations.
The precision offered by single-action shear forming machines is another major benefit. These machines are designed to produce clean, accurate cuts with little or no deviation from the intended part geometry. The simplicity of the operation helps to ensure that the parts are cut consistently with high repeatability, making them ideal for mass production of identical parts that need to meet specific dimensional tolerances. For example, in automotive manufacturing, such parts might include body panels or structural components, where dimensional accuracy is essential for fitting and functionality.
In addition to cutting, the machine can also handle thin sheets of metal or other materials, making it versatile for a variety of industries. The machine’s adjustable settings allow it to handle various material thicknesses, providing flexibility in the types of materials that can be processed. This allows the machine to be used in a wide range of applications, from light-gauge metal used in electronic enclosures to heavier sheet metal used in structural components.
The speed and efficiency of a single-action shear forming machine are also notable. Since the process is relatively simple, it can produce high output rates, making it ideal for production runs where many identical parts need to be produced quickly. This is particularly useful in high-volume manufacturing settings where consistency and throughput are key factors.
However, there are some limitations to the machine’s capabilities. Since the forming action is typically minimal or non-existent in many single-action shear forming machines, they may not be suitable for producing more complex shapes or parts with intricate details. These machines excel at cutting and some basic forming, but for tasks that require deep or highly detailed forming—such as deep drawing, extrusions, or parts with complex curves—more advanced equipment, like a double-action shear forming machine or CNC machine, would be necessary.
Additionally, the wear on the cutting blades is an important consideration. Since the machine performs primarily shearing, the blades or cutting tools may experience significant wear over time, especially when working with harder materials or high volumes of production. Regular maintenance and blade sharpening or replacement are required to ensure the machine continues to perform at optimal levels. Fortunately, because the machine focuses on a single operation, maintenance tends to be simpler and less costly than with machines that have multiple functions.
Overall, a Single-Action Shear Forming Machine is an efficient, reliable tool for cutting and light forming of materials. Its focus on one process makes it ideal for simpler, high-volume production of parts that require clean cuts and minimal shaping. While it may not be suited for highly complex parts, its precision, speed, and ease of use make it an essential tool for manufacturers working with sheet metal and other materials where the main requirement is accurate cutting. By focusing on a single task, it offers manufacturers a cost-effective solution for producing high-quality parts quickly and consistently.
A Single-Action Shear Forming Machine is designed to streamline the metal shaping and cutting process, typically focusing on cutting or shearing operations, with minimal additional forming. It is a versatile machine used primarily in sheet metal fabrication where the goal is to produce accurate and clean cuts in metal or other materials. The machine uses a cutting tool or blades that apply force to the material to create straight and precise cuts. In some cases, the machine can incorporate a light forming operation, like edge rounding or bending, but its primary function is the shearing process.
One of the biggest advantages of a single-action shear forming machine is its simplicity. Unlike more complex systems that perform multiple tasks, the single-action shear machine is focused on performing one function very efficiently. This makes it a cost-effective solution for manufacturers that need to produce parts in high volume but do not require intricate shapes or detailed forming. The design is also beneficial for ease of maintenance, as there are fewer components to maintain compared to more advanced machinery. Regular upkeep mainly involves blade sharpening or replacement, which is simpler compared to machines that involve multiple forming tools or processes.
The speed of these machines is another significant benefit. Since they are designed for high-volume operations, the single-action shear forming machines are capable of producing parts quickly, reducing the overall production time. This makes them particularly useful in industries where fast turnaround and high productivity are essential. For example, in the automotive and construction industries, where sheet metal parts are often needed in large quantities, this machine can be a valuable asset to the production line.
In terms of precision, a single-action shear forming machine is well-suited for tasks that require high levels of accuracy. The shearing process ensures that the metal is cut to the correct dimensions, and this precision can be critical in applications where parts need to fit together seamlessly, such as in automotive bodywork or electrical enclosures. The machine can also produce clean edges that minimize the need for additional finishing processes, saving time and reducing costs.
However, the machine does have limitations. The primary limitation is its lack of versatility when it comes to forming complex shapes or designs. While the single-action shear forming machine is excellent for cutting straight lines or basic forms, it is not equipped to handle more intricate operations, such as deep forming, embossing, or creating complex profiles. For parts that require curves, undercuts, or detailed textures, a more specialized machine, like a double-action shear forming machine or CNC machine, would be required.
The materials that can be processed are also an important consideration. While the single-action shear forming machine can handle a variety of materials, it is most effective when working with thin to medium-gauge metals. For thicker or harder materials, the shearing process can become less effective, and more power or different cutting technologies might be necessary. This machine is generally best suited for aluminum, steel, and other metals in thinner gauges, as well as plastics and composites that are easier to shear.
Despite these limitations, the cost-effectiveness and simplicity of the single-action shear forming machine make it a popular choice for many manufacturers. Its ability to cut materials quickly and accurately in high-volume runs makes it a valuable tool in the production of parts that require minimal shaping beyond simple cuts. Its design is particularly beneficial in industries where mass production of basic shapes is needed, such as in automotive, aerospace, and electronics industries. By focusing on one task—cutting or shearing—it allows manufacturers to produce large quantities of parts efficiently, while maintaining a high level of quality and precision. This makes it a crucial asset in sheet metal operations and other manufacturing processes that prioritize speed and accuracy over complex designs.
Mechanical Shear Forming Machine

A Mechanical Shear Forming Machine is a type of equipment used in metalworking for shaping and cutting materials, particularly sheet metal. This machine operates using a mechanical drive, which typically involves a set of gears, motors, and levers to generate the force needed for shearing and forming operations. It is particularly suitable for producing parts that require precise cuts and light forming, such as metal panels, discs, and other simple geometries. The mechanical drive system provides a reliable and efficient way to apply the required forces, making these machines suitable for high-volume production.
In a mechanical shear forming machine, the primary function is to perform shearing, where cutting blades apply pressure to the material, causing it to separate into the desired shape. The forming action may be integrated into the process in some models, where light pressure is applied to bend or shape the material, creating parts with edges, flanges, or simple curves. This type of machine is often preferred when manufacturers need to produce large quantities of identical parts quickly and with minimal variation in dimensions.
The mechanical drive system gives these machines a significant advantage in terms of reliability and efficiency. The system is relatively simple, and because it operates on mechanical components, it can be maintained with ease. The components involved in the machine’s operation—such as the crank, flywheel, gears, and cutter heads—are designed for durability and long service life. The mechanical drive also ensures that the machine can operate with relatively consistent force over long periods, making it a solid choice for continuous production in environments that require reliable output.
Another key benefit of the mechanical shear forming machine is its precision. Since the machine is designed to cut materials quickly while maintaining tight tolerances, it can produce parts that meet exact specifications with minimal variation. This precision is particularly important in industries where part quality and dimensional accuracy are critical, such as in the automotive or aerospace sectors, where even small deviations can lead to fitting issues or operational problems.
The speed of the mechanical shear forming machine is also a significant advantage. These machines are capable of producing parts at a high rate, which makes them ideal for mass production. The mechanical drive system is designed for continuous operation, allowing the machine to cut and form large quantities of parts in a short period, increasing the overall throughput and reducing production costs. The ability to quickly adjust settings, such as cutting force or material thickness, further enhances the machine’s flexibility and speed in various manufacturing environments.
Versatility is another notable feature of the mechanical shear forming machine. While these machines are typically used for cutting sheet metal and thin materials, many models can accommodate different thicknesses and materials, such as aluminum, steel, and composite materials. The machine can also be adjusted to work with varying material thicknesses, providing manufacturers with the flexibility to work on a range of projects. This makes it a useful tool in industries where multiple types of materials are needed for different product lines.
However, despite its many advantages, a mechanical shear forming machine does have some limitations. For example, because these machines primarily focus on shearing and light forming, they may not be suitable for more complex tasks, such as deep drawing, intricate embossing, or forming of more detailed shapes. Parts requiring complex bends, undercuts, or high-depth forming will often need a more advanced system, such as a hydraulic shear forming machine or CNC machine, which are designed to handle a wider range of forming operations.
Additionally, the machine’s maintenance can require attention to mechanical parts, such as the gears, flywheels, and blades. These components undergo wear and tear over time, especially when the machine is used continuously. As the blades dull, their ability to produce clean cuts may diminish, requiring regular sharpening or replacement. Proper maintenance of the mechanical drive system, including lubrication of moving parts, is essential to keep the machine running smoothly and prevent breakdowns.
In summary, a Mechanical Shear Forming Machine is a reliable, efficient, and precise solution for high-volume cutting and forming of materials. It operates using mechanical components to provide consistent force, making it ideal for industries that require quick, consistent production of simple parts. Its precision, speed, and versatility make it a go-to machine for manufacturers working with sheet metal, particularly when parts need to be produced in large quantities with minimal variation. However, it is most effective for simpler shapes and is not suited for tasks that require deep or intricate forming. When maintained properly, a mechanical shear forming machine can be a valuable asset in mass production environments that prioritize speed, accuracy, and cost-effectiveness.
While the Mechanical Shear Forming Machine excels in providing quick and accurate production for simpler parts, there are other considerations manufacturers must account for when utilizing this machine. For one, the operational simplicity of mechanical shear forming machines can be both an advantage and a limitation, depending on the complexity of the task at hand. These machines typically perform well with materials that require straight cuts or basic forming, but they might not be the best option for more complex geometries or highly intricate designs.
In industries where production involves highly customized or detailed parts, such as in medical devices, aerospace components, or certain automotive applications, additional equipment like CNC machines or hydraulic presses might be required to handle the more detailed features of the parts. This is especially the case for parts that require deep drawing, embossing, or multiple bends and curves. In contrast, the mechanical shear forming machine is well-suited for tasks such as cutting metal sheets, shaping flanges, or simple edge forming.
Another important factor to consider when using a mechanical shear forming machine is operator skill and experience. While the machine is relatively straightforward in design, operators still need to be trained to ensure proper adjustment of settings such as cutting speed, pressure, and material thickness. Incorrect settings could lead to inconsistent results or even material damage, resulting in increased waste and reduced efficiency. Skilled operators can maximize the machine’s potential by ensuring that it runs smoothly and consistently, which is especially important when dealing with high-volume production.
Another aspect that can affect the machine’s performance is the type and condition of the tooling. The cutting blades or dies used in mechanical shear forming machines are subject to wear, particularly when dealing with harder or thicker materials. Over time, the blades can become dull, reducing the precision of cuts and the overall efficiency of the machine. Regular inspection, sharpening, or replacement of these components is essential to maintaining high-quality output and ensuring consistent performance over time. The wear and tear on the mechanical components can also affect the machine’s energy efficiency, as parts like the flywheel or gears may need to be lubricated or replaced to avoid unnecessary strain on the motor.
Despite these considerations, the cost-effectiveness of mechanical shear forming machines remains a significant advantage. For manufacturers focused on high-volume production of simple parts, these machines provide an excellent balance between price and performance. The relatively low initial investment and the ease of operation make them a compelling choice for businesses looking to produce large quantities of standard parts at a competitive cost.
Furthermore, these machines are relatively energy-efficient, especially in comparison to more complex systems that may require additional resources, like hydraulic systems or CNC controllers. The mechanical operation uses less energy than hydraulic or pneumatic systems, which can contribute to lower operational costs over time. Additionally, because the machine typically involves fewer components, it requires less upkeep and maintenance compared to more sophisticated machinery.
In industries where part uniformity is critical, mechanical shear forming machines are an excellent choice. The consistent precision of the cutting and forming operations helps ensure that each part produced is virtually identical, which is crucial for assembly lines that depend on the precise fit and functionality of components. For example, in automotive production, where many parts need to fit together seamlessly, the reliability and consistency of a mechanical shear forming machine can help minimize the risk of defects or production delays.
In conclusion, a Mechanical Shear Forming Machine is an effective tool for manufacturers seeking efficiency, reliability, and cost-effectiveness when producing parts that require cutting and basic forming. Its simplicity, precision, and high-speed capabilities make it ideal for mass production environments that focus on relatively simple parts and standard materials. However, for more complex applications or parts with intricate geometries, additional equipment may be needed. Regular maintenance, attention to tooling condition, and operator expertise are essential to ensuring the machine runs efficiently and delivers high-quality results. When used correctly, a mechanical shear forming machine can greatly enhance throughput and cost efficiency, making it a valuable asset for many industrial applications.
Hydraulic Shear Forming Machine

A Hydraulic Shear Forming Machine is an advanced tool used for cutting and forming metal or other materials by applying hydraulic force. This type of machine utilizes hydraulic cylinders to exert pressure, which makes it suitable for working with thicker materials or parts that require more force than mechanical systems can provide. Hydraulic shear forming machines are widely used in industries that need to shape large, heavy, or complex materials with high precision, such as aerospace, automotive, construction, and metalworking.
The primary operation of a hydraulic shear forming machine involves shearing, where blades or cutting tools apply force to the material, causing it to shear along a predetermined line. Hydraulic systems can provide much higher force than mechanical drives, making these machines ideal for cutting through thicker gauges of metal or harder materials like steel, aluminum, or composite metals. In addition to cutting, the machine can perform some degree of forming, such as bending or shaping edges, particularly when equipped with specialized dies or attachments.
The key advantage of a hydraulic shear forming machine is the control it offers over the amount of force applied. Hydraulic systems provide a level of precision and adjustability that allows operators to fine-tune the pressure for different materials or applications. This means that parts can be shaped with higher accuracy and without causing damage to the material. This flexibility is especially important when working with a variety of materials that may require different levels of force or when the design of the part involves intricate features such as curved edges or ribs that would be difficult to achieve with simpler mechanical systems.
Another advantage of hydraulic shear forming machines is their ability to handle complex geometries and parts that require deep forming or high-pressure forming. Unlike mechanical machines, which may be limited by the force generated by mechanical drives, hydraulic systems can provide more consistent force over a larger area, allowing for deeper or more detailed forms. For example, hydraulic machines can handle deeper drawing, embossing, or curved surfaces that would otherwise require a more sophisticated system like CNC machines or hydraulic presses.
The versatility of hydraulic shear forming machines is another important factor. These machines can be used for a wide range of materials, from thin sheets to thicker metals, and can be adjusted to accommodate different material thicknesses and hardness levels. The machine’s dies and tools can also be swapped out to accommodate various shapes or geometries, making it possible to quickly adapt the machine to different tasks or production runs.
In addition to their versatility, hydraulic machines offer speed and efficiency in production. Since the hydraulic system can generate a high level of pressure quickly, the machine is capable of producing parts at a faster rate than mechanical systems. This makes it ideal for industries that need to produce large quantities of parts with high consistency. The ease of operation is another advantage, as the machine can be programmed or manually adjusted to apply the correct amount of force and shaping pressure for different types of parts. The automation capabilities of hydraulic shear forming machines also help reduce the amount of labor required, as many of these systems come with automated controls and settings for various material types and thicknesses.
However, despite these advantages, there are some challenges and limitations with hydraulic shear forming machines. One of the main concerns is the cost. Hydraulic systems tend to be more expensive than their mechanical counterparts, both in terms of initial investment and maintenance. Hydraulic systems also require a consistent supply of fluid, and the fluid itself needs to be checked and maintained regularly to ensure smooth operation. Any issues with the hydraulic fluid or the system’s pressure can result in malfunctions or delays in production. The machines are also typically larger and more complex, which means they may require more space in a manufacturing facility and specialized training for operators.
Maintenance is another important consideration. Hydraulic systems, while powerful and efficient, are subject to wear and tear over time, especially with the high-pressure forces applied during operation. Components like hydraulic pumps, valves, and cylinders may require regular inspection and servicing to ensure optimal performance. If the hydraulic fluid is not properly maintained or if there is a failure in the hydraulic system, it can lead to performance issues or even breakdowns, causing delays in production. Regular maintenance schedules and the use of high-quality hydraulic fluid are essential for keeping the machine in good working order.
In summary, a Hydraulic Shear Forming Machine is a powerful and versatile tool that is particularly well-suited for cutting and forming thicker or harder materials with high precision. Its ability to control force and adapt to different materials makes it an essential machine for industries that require high levels of accuracy and the ability to handle complex geometries. While the machine’s initial cost and maintenance requirements may be higher than mechanical systems, the benefits of speed, efficiency, and precision make it a valuable asset for manufacturers working with high-tensile metals, complex designs, and large production volumes. When properly maintained and operated, hydraulic shear forming machines can significantly enhance production capacity, quality control, and overall throughput in metalworking and other related industries.
A Hydraulic Shear Forming Machine is a versatile and powerful tool that utilizes hydraulic force to perform cutting and forming operations on a variety of materials, particularly metals. These machines are widely used in industries like automotive, aerospace, construction, and metal fabrication for their ability to work with thicker materials or more complex shapes. The hydraulic system offers several advantages over mechanical alternatives, primarily because it can provide much greater force, allowing the machine to handle materials that require more pressure to shear or form effectively.
One of the key strengths of a hydraulic shear forming machine is its ability to apply precise force through hydraulic cylinders, which can be adjusted based on the material being processed. This level of control makes it especially useful for parts that need to be cut or shaped with high accuracy, as operators can fine-tune the machine’s settings for different thicknesses and hardness of materials. The machine’s ability to adjust the force also makes it adaptable to a wide range of materials, such as steel, aluminum, composites, and plastics, making it a flexible option for manufacturers working with diverse material types.
In addition to cutting, hydraulic shear forming machines can perform some basic forming operations, like bending, flanging, or shaping edges, which can be integrated into the shearing process. The high force generated by the hydraulic system also makes it possible to carry out deeper forming operations, such as deep drawing or embossing, which would be difficult to achieve with mechanical systems. This makes the hydraulic shear forming machine an excellent choice for more complex designs that require a combination of cutting and forming in a single operation.
The speed and efficiency of hydraulic shear forming machines also contribute to their popularity in high-volume production environments. Once set up, these machines can produce parts quickly, and the consistent force of the hydraulic system ensures that cuts are made accurately every time. Additionally, the automation capabilities of many hydraulic shear forming machines allow for quick adjustments, further speeding up the production process. This makes them ideal for industries that need to produce large quantities of parts rapidly while maintaining tight tolerances.
However, hydraulic shear forming machines do come with certain challenges. One of the primary concerns is the cost of the machinery and its operation. Hydraulic systems generally require a higher initial investment than mechanical machines, and maintenance costs can also be significant due to the need to maintain hydraulic fluids, pumps, and seals. The machine’s complexity means that it may require more specialized training for operators, as well as regular maintenance to ensure reliable operation. Additionally, hydraulic machines are typically larger and heavier than their mechanical counterparts, requiring more space in the workshop and more careful consideration of energy consumption.
Despite these considerations, hydraulic shear forming machines offer a range of benefits for manufacturers that require high precision, reliable performance, and the ability to handle a variety of materials and shapes. With proper maintenance, these machines can provide a long service life and continue to deliver high-quality parts, making them a valuable asset in industries where efficiency, part complexity, and material strength are essential.
Hydraulic shear forming machines also provide significant advantages in terms of precision and repeatability, which are crucial for industries that require high-quality parts with minimal variation. The consistent hydraulic pressure ensures that each cut or form is executed with the same force, resulting in identical products from one batch to the next. This is especially important in aerospace, automotive, and construction, where part tolerances must be maintained to ensure proper fit and functionality. The ability to achieve such consistency makes these machines highly valuable in mass production settings where product quality is paramount.
Another noteworthy feature of hydraulic shear forming machines is their ability to handle large workpieces. Unlike mechanical systems, which may have limitations on the size and thickness of the materials they can process, hydraulic machines can accommodate larger or thicker parts. This capability is particularly beneficial in industries that require the production of large panels, metal sheets, or large structural components. These machines can also perform cutting and shaping on harder materials, such as high-strength steel or composite materials, which would be difficult for mechanical machines to process effectively.
The flexibility of hydraulic shear forming machines extends beyond material types and thicknesses; they can also be used for various operations, from simple cuts to more complex shapes. With the appropriate tooling, hydraulic shear forming machines can be adapted for different forming techniques, such as bending, flanging, curving, and rib forming. This versatility makes them ideal for companies that need to produce a wide range of products, from basic metal parts to more specialized components that require intricate forming operations.
While the costs associated with hydraulic shear forming machines can be higher than those of simpler machines, manufacturers often find the investment to be worthwhile due to the efficiency gains and long-term durability the machines offer. The machines’ hydraulic components are robust and designed to withstand high pressures, making them less prone to wear compared to mechanical systems. The high force generated by the hydraulic system also means that the machine can cut through tough materials more effectively, which reduces wear and tear on other components, such as blades and dies.
Regular maintenance is essential for keeping hydraulic shear forming machines running smoothly. The hydraulic fluid, for example, must be monitored and replaced periodically to ensure that the system operates efficiently. Leaks or low fluid levels can impair the machine’s performance, and dirt or contaminants in the fluid can lead to component failure. Additionally, routine inspections of the machine’s hydraulic cylinders, pumps, and seals are necessary to prevent downtime. Fortunately, many machines are designed with ease of maintenance in mind, and regular servicing can extend their operational life while minimizing repair costs.
Moreover, advancements in control systems have made hydraulic shear forming machines even more user-friendly. Many modern machines come with digital controls and programmable logic controllers (PLCs) that allow for precise adjustments to the pressure, stroke, and speed. These digital systems can also store settings for specific materials or parts, allowing manufacturers to quickly switch between production runs without the need for extensive setup. This reduces setup time and increases the efficiency of the overall production process.
In terms of environmental considerations, hydraulic shear forming machines are generally more energy-efficient than other heavy-duty machines, particularly mechanical presses. While they still require electricity to power the hydraulic pumps, they do not require as much energy for mechanical motion or gearing systems. Additionally, the energy consumption is relatively consistent, as the hydraulic system operates at a fixed pressure, making energy costs more predictable. With proper maintenance, hydraulic shear forming machines are efficient in their use of resources, which is beneficial for companies looking to reduce operational costs and environmental impact.
In summary, Hydraulic Shear Forming Machines are powerful and versatile tools that are well-suited for industries requiring high-force, high-precision cutting and forming. They provide the flexibility to work with a wide range of materials, thicknesses, and part geometries, making them a popular choice in high-volume manufacturing environments. While they come with a higher initial investment and maintenance requirements, their ability to produce consistent, high-quality parts quickly and efficiently makes them a valuable asset for many manufacturers. With proper maintenance and operator training, hydraulic shear forming machines can deliver long-lasting performance, supporting the production of both simple and complex parts across various industries.
CNC Shear Forming Machine
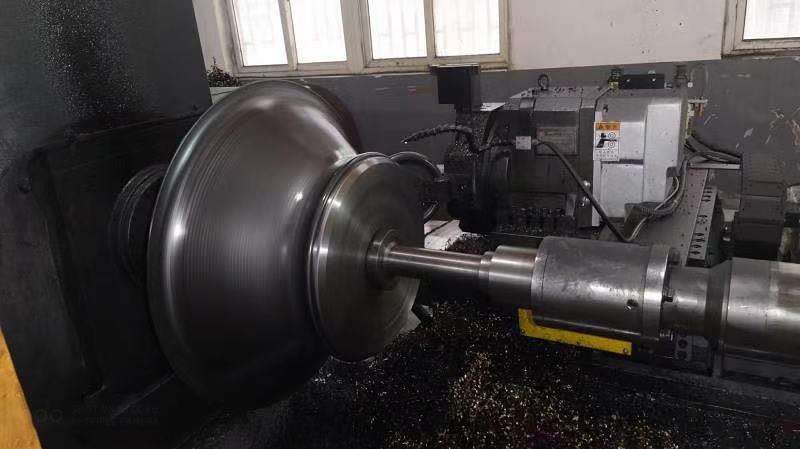
A CNC Shear Forming Machine is a highly advanced version of traditional shear forming machines, utilizing computer numerical control (CNC) technology to automate and precisely control the cutting and forming processes. This machine type combines the efficiency and high-force capabilities of hydraulic or mechanical shear forming machines with the precision and programmability of CNC systems. As a result, CNC shear forming machines are able to deliver highly accurate parts with complex geometries while significantly reducing the need for manual labor and minimizing human error.
The main advantage of CNC shear forming machines is their ability to automate the shearing and forming processes, allowing for high repeatability and precision in part production. The CNC controller can be programmed with exact parameters for each operation, including cutting speed, pressure, stroke length, and tool positioning. This makes the machine ideal for producing parts with tight tolerances and complex shapes that would be difficult or time-consuming to achieve with manual or mechanical systems. It also allows for rapid changes between production runs, making it easier to adapt the machine to different part designs without requiring extensive retooling or operator intervention.
The CNC shear forming machine can be used for a wide range of operations, including cutting, bending, flanging, curving, and deep drawing. By programming the CNC system, operators can perform a combination of these tasks in a single production cycle, streamlining the manufacturing process and increasing production efficiency. This flexibility is particularly beneficial for industries that require the production of custom parts or components with non-standard geometries, such as the aerospace, automotive, and medical device industries.
Another benefit of CNC shear forming machines is their ability to achieve complex shapes with high precision. For example, they can create parts with intricate curves, complex bends, or multiple flanges without the need for additional tooling or manual adjustments. This capability is especially valuable in industries where customization and product differentiation are important, such as in the production of unique metal parts for engineering projects or prototypes.
The speed and efficiency of CNC shear forming machines also make them a popular choice for high-volume production runs. Once a part’s specifications have been entered into the CNC system, the machine can produce hundreds or even thousands of identical parts with minimal operator involvement. This not only saves time but also helps to reduce production costs by minimizing labor requirements and human error. The consistent output from CNC-controlled machines also ensures that parts meet quality standards, leading to improved product consistency and fewer defects.
Despite these advantages, there are some factors to consider when choosing a CNC shear forming machine. The initial cost of CNC machines is typically higher than that of traditional manual or mechanical machines, due to the complexity of the control system and the precision components involved. In addition to the higher upfront investment, there may also be ongoing costs associated with training operators to use the CNC system effectively and maintaining the machine’s computer controls and hardware. However, for manufacturers that require high-volume production of parts with complex geometries or tight tolerances, the long-term benefits in terms of time savings, quality control, and reduced waste often outweigh these initial costs.
Maintenance of CNC shear forming machines is generally straightforward, but it requires a higher level of expertise compared to traditional machines. Regular maintenance tasks may include checking and calibrating the CNC controller, inspecting the hydraulic system (if applicable), and ensuring that the cutting tools are sharp and free from wear. The CNC software may also require updates or adjustments to accommodate new designs or production parameters. As with any advanced machinery, preventive maintenance is key to ensuring the longevity of the machine and minimizing the likelihood of costly breakdowns or delays.
In addition to the precision and automation benefits, CNC shear forming machines offer enhanced data tracking and process monitoring capabilities. Many modern CNC systems are equipped with sensors and feedback mechanisms that allow operators to track performance metrics, such as cutting speed, material thickness, and tool wear. This data can be used to optimize machine settings, improve production efficiency, and ensure the quality of each part produced. Advanced CNC machines may also have built-in diagnostic tools that alert operators to potential issues before they become serious problems, further reducing downtime and repair costs.
Another advantage of CNC shear forming machines is their ability to be integrated into larger automated manufacturing systems. For example, a CNC shear forming machine can be part of a fully automated production line, where parts are fed into the machine by a robotic arm, processed, and then moved to the next stage of production with minimal human involvement. This level of automation can lead to significant improvements in throughput, accuracy, and cost-effectiveness, particularly in industries with high production demands.
In conclusion, a CNC Shear Forming Machine is an advanced and highly precise tool that provides manufacturers with the ability to create complex, high-quality parts with minimal manual intervention. Its ability to automate shearing and forming operations, coupled with its high precision, makes it ideal for industries that require customization, complex geometries, and tight tolerances. While the initial investment and maintenance costs may be higher compared to traditional systems, the long-term benefits in terms of efficiency, quality control, and production speed often make it a valuable asset for manufacturers looking to improve their production processes. With regular maintenance and proper training, CNC shear forming machines can provide reliable, high-performance results for a wide range of manufacturing applications.
A CNC Shear Forming Machine is an advanced and precise tool that integrates the capabilities of traditional shear forming with modern CNC (Computer Numerical Control) technology. This allows manufacturers to automate and control the shearing and forming processes with high precision. By utilizing CNC systems, the machine can be programmed to perform various operations such as cutting, bending, flanging, and deep drawing with remarkable accuracy. This precise control allows manufacturers to produce parts with complex geometries, tight tolerances, and high consistency, which would be challenging or impossible to achieve with manual machines.
The main advantage of using a CNC shear forming machine is its ability to significantly reduce the human intervention needed for shaping and cutting metal or other materials. With CNC, each step of the process is controlled digitally, which not only speeds up production but also ensures that each part produced is identical to the next. This automation reduces the risk of errors and defects that can occur with manual processes, making CNC shear forming machines particularly valuable in high-precision industries like aerospace, automotive, and medical device manufacturing.
The versatility of a CNC shear forming machine allows it to handle a variety of materials, including metals such as steel, aluminum, and titanium, as well as composite materials. The ability to program and adjust the machine settings for different materials and thicknesses enhances its flexibility, enabling manufacturers to use the same machine for various projects without significant retooling. This adaptability makes CNC shear forming machines essential for businesses that produce custom or low-volume parts, as well as those that need to produce large batches with consistent quality.
Another significant advantage of CNC shear forming machines is their capacity to achieve intricate and complex shapes. With the precision of CNC control, the machine can perform detailed cutting and forming operations, including shaping curves, creating flanges, and performing deep drawing, all within tight tolerances. These capabilities make CNC shear forming machines ideal for applications that require unique part designs or complex geometries, such as enclosures, metal housing, or aerospace components.
In addition to the high precision and flexibility, CNC shear forming machines also improve production efficiency. After programming the machine, the production process becomes largely automated, reducing the need for manual adjustments or constant supervision. Once the parameters are set, the machine can continue producing parts at high speeds, making it suitable for high-volume production runs. This automation not only speeds up the process but also ensures a consistent output. As a result, CNC shear forming machines help manufacturers meet tight deadlines while maintaining quality control throughout the production process.
Despite these advantages, CNC shear forming machines are often more expensive than traditional manual or mechanical machines due to their advanced technology. The initial investment can be significant, especially for businesses that are just starting to incorporate CNC machinery into their operations. Additionally, while the machines reduce the need for manual labor, they still require skilled operators to program the system and perform routine maintenance. Training costs for CNC systems can also add to the overall expense.
Maintenance of CNC shear forming machines is generally straightforward but requires some specialized knowledge. Regular checks are necessary to ensure the hydraulic systems (if applicable), cutting tools, and CNC software are functioning properly. Ensuring the cutting tools remain sharp and the CNC system is calibrated correctly is crucial for maintaining the machine’s performance and producing parts with high accuracy. Preventive maintenance is key to minimizing downtime and maintaining operational efficiency.
In summary, CNC shear forming machines offer a significant improvement over traditional shear forming processes by providing high precision, flexibility, and automation. Their ability to produce complex shapes and handle various materials with consistency makes them invaluable tools for industries requiring tight tolerances and custom parts. Although the initial investment and maintenance costs can be high, the long-term benefits of increased productivity, reduced labor, and improved part quality often justify the cost for manufacturers. With regular maintenance and operator training, CNC shear forming machines can significantly enhance the efficiency and capabilities of a manufacturing operation.
CNC shear forming machines also play a vital role in reducing material waste during the manufacturing process. Since the machine is programmed to make precise cuts and shapes based on exact specifications, it reduces the likelihood of over-cutting or errors that would otherwise lead to discarded material. The ability to control every aspect of the process means that manufacturers can optimize the material usage, thereby improving cost efficiency and minimizing environmental impact. For industries where the material cost is significant—such as aerospace or automotive—this can result in substantial savings over time.
Another important benefit of CNC shear forming machines is their ability to integrate with other parts of a production line. Many CNC systems are designed to communicate with other machines or automation systems, allowing for seamless integration into a larger manufacturing environment. For example, parts processed by a CNC shear forming machine can be automatically transferred to the next stage of production, such as assembly or finishing, without manual intervention. This automation not only speeds up production but also ensures that the entire workflow is streamlined and efficient, reducing downtime and optimizing throughput.
Furthermore, the data collection and analysis capabilities of modern CNC shear forming machines are worth highlighting. With the ability to monitor various aspects of the machine’s performance, such as cutting force, speed, and tool wear, operators can gather real-time data on the machine’s output. This data can be used for predictive maintenance, where trends in machine performance are analyzed to predict when parts may fail or when maintenance is needed. By addressing potential issues before they become critical, manufacturers can avoid costly downtime and maintain a smooth, uninterrupted production process.
CNC shear forming machines can also be equipped with advanced error detection systems. These systems provide feedback to the operator or automatically adjust the machine settings if something goes wrong during the operation. For example, if a cutting tool starts to wear out or the material feed is inconsistent, the system can detect these issues and make the necessary adjustments to prevent defects in the final product. This increases the overall reliability and quality of the parts being produced and reduces the need for post-production inspections or rework.
Additionally, modern CNC shear forming machines can be operated remotely, especially in high-tech manufacturing environments. Remote operation allows operators to monitor and control the machine from a distance, which can be particularly useful in large production facilities or during overnight shifts when fewer staff are on-site. Remote monitoring also provides manufacturers with the ability to troubleshoot and adjust the system from anywhere, improving the overall flexibility and responsiveness of the operation.
CNC shear forming machines also offer the possibility of custom programming for specific tasks. For manufacturers producing unique or low-volume products, CNC machines allow for the creation of one-of-a-kind parts or prototypes with intricate specifications. Custom tool paths can be designed for special applications, enabling manufacturers to experiment with new designs or respond to customer needs with highly personalized products. This capability to rapidly prototype and produce small batches with consistent quality is a major advantage for industries such as custom metalworking, specialized manufacturing, and R&D labs.
Despite the impressive array of benefits, it’s important to note that CNC shear forming machines require careful management of the software systems. The programming and design of tool paths are typically done using CAD/CAM (Computer-Aided Design/Computer-Aided Manufacturing) software. These software systems must be kept up to date and require skilled personnel to design and optimize the cutting and forming paths. The precision of the CNC machine depends heavily on the accuracy of the programming and the design inputs, which underscores the importance of skilled operators and engineers who are proficient in both the software and the machine.
Lastly, safety is a crucial consideration when using CNC shear forming machines. Like any heavy machinery, CNC machines pose safety risks if not operated correctly. While these machines are often equipped with safety features such as automatic shut-offs and emergency stop buttons, proper training and adherence to safety protocols are still essential. Operators must be well-versed in the specific safety guidelines for the machine they are using and follow proper lockout/tagout procedures when conducting maintenance or repairs. Safety features can also include guards and sensors that prevent the machine from operating when an operator is too close to a dangerous area, ensuring that workers are protected from potential accidents.
In conclusion, CNC shear forming machines represent a significant leap forward in manufacturing technology, combining precision, automation, and flexibility to produce high-quality parts with minimal human intervention. These machines are ideal for industries requiring complex geometries, tight tolerances, and high production volumes. While the initial investment and training costs may be higher than traditional methods, the benefits in terms of efficiency, cost savings, part quality, and production flexibility make them a worthwhile investment for many manufacturers. As technology continues to evolve, these machines are likely to become even more advanced, incorporating features like artificial intelligence, machine learning, and smart automation to further optimize production processes and reduce human error.
Bowl Metal Spinning Machine
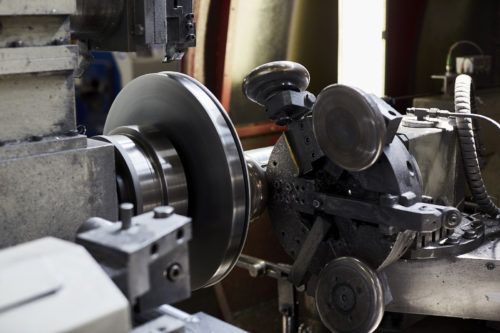
A Bowl Metal Spinning Machine is a specialized type of metal spinning machine used to form bowl-shaped parts or components by spinning metal sheets around a central axis. This machine is commonly used for manufacturing hollow, concave, or cup-shaped objects in various industries such as aerospace, automotive, appliances, and furniture, where precise, uniform shapes are needed for both functional and aesthetic purposes.
The basic principle of operation for a bowl metal spinning machine involves clamping a circular sheet of metal onto a rotating mandrel or a tool, which is then spun at high speed. A spinning tool is pressed against the sheet as it rotates, gradually forming the material into the desired shape, such as a bowl or a deep dish. The spinning tool applies pressure to shape the metal without cutting it, relying instead on the plastic deformation of the material to achieve the desired contour.
The key advantage of using a bowl metal spinning machine is its ability to produce seamless, strong, and lightweight parts with high precision. Since the process relies on forming the material rather than cutting it, there is less material waste, which is a major benefit for industries concerned with minimizing production costs. Additionally, the smooth, uniform surface that results from the spinning process can often eliminate the need for additional finishing or welding, which can save both time and money in the production process.
Bowl metal spinning machines can handle a variety of metals, including aluminum, copper, brass, steel, and even composite materials, making them versatile for different applications. The machine’s ability to work with a wide range of materials means that it can be used for producing parts with varying thicknesses, diameters, and depths.
One of the critical factors in the success of a bowl metal spinning machine is the speed and control of the spinning process. The machine typically features a motorized spindle that allows for the control of the rotational speed, which can be adjusted depending on the material being worked with and the desired outcome. The spinning tool used in the machine is carefully selected for the specific material and shape being formed, and it plays a critical role in ensuring the accuracy and smoothness of the final product.
Many modern bowl metal spinning machines come equipped with CNC (Computer Numerical Control) systems, which allow for precise control over the spinning process. CNC machines offer the advantage of being able to program and repeat operations with great accuracy, making them ideal for high-volume production runs and complex designs. With CNC controls, the operator can easily adjust parameters such as speed, pressure, and tool positioning, ensuring that the machine produces parts with consistent quality and tighter tolerances.
The main components of a bowl metal spinning machine include:
- Mandrel: A rotating tool that holds the metal sheet in place while the spinning operation is performed. It serves as the form around which the metal is shaped into a bowl.
- Spinning Tool: A tool that is used to apply pressure to the rotating metal sheet, gradually shaping it into the desired form. The spinning tool can be adjusted for different shapes, such as deep bowls or shallow dishes.
- Tooling System: A set of tools that can be swapped out to create different shapes and sizes of bowls, depending on the product requirements.
- Control System: In advanced machines, this includes CNC controls that manage the speed, pressure, and tool positioning for enhanced precision and repeatability.
- Feeding Mechanism: This part is responsible for feeding the metal sheet into the machine for spinning. It ensures the metal is aligned properly with the mandrel and spinning tool.
- Clamping System: Used to securely hold the metal sheet in place during the spinning process to prevent any movement or misalignment.
The machine’s versatility allows it to create parts with a wide range of diameters, from small, delicate components to large, industrial parts. Bowl metal spinning is particularly advantageous for low-to-medium-volume production runs because of its ability to produce highly complex shapes without the need for expensive molds or dies. It is also a cost-effective method for creating prototypes and custom parts.
The process is relatively quick, especially for shallow forms, and can be repeated with consistent results, making it ideal for industries where rapid prototyping or small-batch production is needed. Additionally, the ability to create seamless, welded-free designs is particularly valuable in industries that require parts with strength and integrity in their construction, such as in pressure vessels, medical devices, and aerospace components.
Maintenance of a bowl metal spinning machine generally involves regular checks and adjustments of the spindle, mandrel, and spinning tools to ensure smooth operation and to avoid wear that could affect part quality. Operators also need to regularly inspect the hydraulic systems (if the machine is hydraulically powered) and the CNC controls (if applicable), ensuring they remain calibrated and functional.
In conclusion, the Bowl Metal Spinning Machine is a powerful and efficient tool for creating complex, concave parts with a variety of material options. It is especially suitable for custom manufacturing, low-volume production, and industries requiring high-strength, seamless designs. The integration of CNC technology enhances its precision and repeatability, making it a valuable asset for companies seeking to optimize their manufacturing processes while maintaining high-quality standards.
A Bowl Metal Spinning Machine is designed for the specific purpose of shaping metal sheets into concave or bowl-like forms by rotating the material around a mandrel and using a spinning tool to shape it. This process is highly effective for creating parts that are often required in industries such as aerospace, automotive, and consumer goods, where strength, light weight, and complex geometries are necessary. By utilizing the spinning process, manufacturers can produce parts with minimal waste since the material is deformed rather than cut away, which reduces the cost of materials and minimizes the environmental impact of the production process.
The machine works by securing a metal sheet onto a rotating mandrel or form, after which a spinning tool presses against the sheet as it spins, gradually shaping it into the desired form. This method can produce seamless, hollow, and deep-drawn components without the need for welding or additional joining processes, which makes it particularly valuable in producing parts that must be strong yet light. Bowl-shaped parts are common in industries that require aesthetic appeal, functional utility, and efficiency, such as creating metal covers, caps, bowls, or vessels.
The spinning tool that presses against the metal can be made of different materials to suit the type of metal being used and the thickness of the material. This allows for precision shaping and smooth surface finishes, which is especially beneficial in applications where surface appearance is important. The method can be used for a wide range of metals, including light alloys like aluminum and more robust materials such as stainless steel, depending on the strength and durability requirements of the finished part. The ability to work with different materials also extends to specialized composite metals or even some plastics, depending on the machine setup.
Bowl metal spinning is particularly advantageous in situations where small to medium production runs are required or when parts need to be custom made. The flexibility of the machine, especially in adjustable tooling systems, means that it can accommodate a variety of part sizes and geometries. With minimal setup time, the machine can produce parts of varying depths, diameters, and wall thicknesses without the need for expensive molds or dies, which can be a significant cost-saving factor for manufacturers.
Many modern bowl metal spinning machines feature CNC technology, which allows operators to program the machine for precise control of the spinning process. The use of CNC technology makes it easier to replicate complex part shapes with a high degree of accuracy and repeatability, minimizing human error and improving the overall quality of the finished part. With CNC integration, manufacturers can create detailed programs that specify parameters such as rotational speed, tool pressure, and even specific shaping sequences to achieve the desired end result. The ability to quickly change between designs or adjust specifications on the fly makes the CNC-equipped bowl metal spinning machine particularly useful for industries where production requirements are subject to frequent changes or tight tolerances.
Additionally, the automation of the spinning process significantly increases production efficiency. By reducing manual labor and speeding up the process, CNC bowl metal spinning machines enable manufacturers to meet tight deadlines and increase throughput. This makes them especially valuable in industries where high-volume production and quick turnaround times are essential. CNC systems also provide data logging capabilities, allowing operators to track and analyze the performance of the machine. This data can be used to fine-tune processes, monitor the wear and tear of tools, and anticipate maintenance needs, further enhancing the machine’s efficiency and longevity.
One of the major benefits of the bowl metal spinning machine is its ability to produce parts without seams or welded joints. This feature is crucial in applications where strength and durability are key, as seams or welds can be weak points in a component. Since the metal is formed without cutting or welding, the resulting parts are typically stronger and more uniform, making them ideal for applications like pressure vessels, aircraft components, or automotive parts that need to withstand stress or pressure without fail. The seamless nature of the parts also contributes to aesthetics, giving the finished product a sleek, continuous form that often requires little additional finishing.
Another important advantage of bowl metal spinning is its suitability for rapid prototyping. Since the setup is relatively simple and flexible, manufacturers can quickly create prototypes of complex parts without needing to invest in expensive molds or tooling. This is particularly valuable in industries where custom parts or limited-run products are common. Designers can make changes to the design or adjust parameters on the CNC system, allowing for a fast and cost-effective way to produce prototypes for testing or evaluation.
Despite these advantages, the bowl metal spinning process does have some limitations. The depth and complexity of the part that can be produced depend largely on the material being used and the machine’s capability. Very deep or highly complex geometries may require additional tools or setups, and the process may become less efficient as the part size increases. Additionally, while the process is relatively cost-effective for producing smaller quantities, it may not be as suitable for extremely large-scale production runs compared to other manufacturing methods like stamping or injection molding.
In terms of maintenance, regular upkeep of the bowl metal spinning machine is crucial to ensure that it operates efficiently over time. The mandrel, spinning tools, and control systems need to be carefully inspected and maintained to avoid issues that could affect the quality of the parts being produced. Lubrication of moving parts, calibration of CNC systems, and monitoring of the machine’s electrical and hydraulic systems are also essential to prevent breakdowns and ensure continuous operation.
In conclusion, a Bowl Metal Spinning Machine is an essential tool in manufacturing processes that require the creation of concave or bowl-shaped parts with high precision and minimal material waste. Its ability to produce seamless, durable parts with varying geometries and sizes makes it an ideal solution for custom manufacturing, small-batch production, and rapid prototyping. The integration of CNC technology enhances the machine’s versatility and efficiency, making it suitable for industries that demand high-quality, consistent parts. With the proper maintenance and skilled operation, bowl metal spinning machines offer a highly efficient, cost-effective method for producing complex, high-strength components in a variety of industries.
The continued evolution of Bowl Metal Spinning Machines has introduced several advanced features and capabilities that enhance their performance, flexibility, and applicability in modern manufacturing. As industries demand higher precision, faster production times, and greater customization, these machines have become increasingly integrated with smart technology, such as IoT (Internet of Things) connectivity, real-time monitoring, and predictive maintenance systems. These improvements enable manufacturers to optimize operations, reduce downtime, and enhance overall efficiency.
With IoT integration, bowl metal spinning machines can now communicate with other machines or systems within the factory, enabling centralized control of the production process. This connectivity allows manufacturers to monitor the performance of the machine remotely, track usage data, and collect feedback from sensors embedded in various parts of the machine. By using real-time data, manufacturers can adjust machine settings, optimize performance, and anticipate potential problems before they lead to significant downtime.
Predictive maintenance is another powerful feature enabled by the incorporation of smart sensors and data analytics. By continuously monitoring key components such as the motor, spindle, and cutting tools, the system can detect signs of wear or malfunction. This proactive approach to maintenance minimizes the risk of unexpected breakdowns and extends the life of critical parts, reducing the overall maintenance costs. For example, if a sensor detects that a tool is starting to wear down or that a specific part is operating outside its optimal range, the system can notify the operator, allowing them to address the issue before it affects production.
The use of advanced simulation software has also enhanced the capabilities of bowl metal spinning machines. Before beginning the actual spinning process, operators can use software to simulate the entire operation, including the material flow, tool contact, and deformation behavior. This simulation helps identify potential issues and adjust settings before starting the production process, ensuring that the part will meet the required specifications. It also allows operators to experiment with different materials, thicknesses, and designs without incurring the cost of making physical prototypes, making it an ideal tool for design validation and testing.
As part of these advancements, modern bowl metal spinning machines are increasingly user-friendly and intuitive. The integration of touchscreen interfaces, graphical user displays, and programmable controls makes it easier for operators to interact with the machine and adjust settings with minimal training. Operators can quickly select preset programs for specific materials or products, minimizing setup times and reducing the likelihood of errors. The ability to store and recall programs also allows manufacturers to produce identical parts in subsequent production runs with ease.
Moreover, the integration of automated material handling systems has improved the throughput of bowl metal spinning machines. These systems automatically feed metal sheets into the machine, reducing the need for manual labor and increasing production efficiency. Automated loading and unloading systems can work in tandem with the spinning machine, ensuring a continuous workflow that minimizes delays between cycles. This is particularly valuable in high-volume manufacturing environments, where maintaining a constant production pace is critical.
With the growing demand for sustainability in manufacturing, bowl metal spinning machines are also becoming more eco-friendly. The reduction in material waste due to the forming process, as opposed to cutting, already contributes to minimizing environmental impact. However, additional sustainability measures include the use of energy-efficient motors and low-impact hydraulic systems that consume less power and fluid, thereby reducing the machine’s carbon footprint. Manufacturers are also increasingly focused on recycling scrap metal generated during the spinning process, ensuring that any off-cuts or surplus material are reused rather than discarded.
As industries continue to innovate and demand more customized products, bowl metal spinning machines will evolve to meet these needs. The ability to handle increasingly complex geometries, a wider range of materials, and higher production volumes will keep these machines at the forefront of manufacturing. The combination of precision, flexibility, efficiency, and automation makes them a vital part of the modern manufacturing landscape, particularly in fields like aerospace, automotive, medical device manufacturing, and consumer electronics.
In conclusion, the Bowl Metal Spinning Machine is no longer just a traditional tool for forming simple bowl shapes. Through the integration of CNC technology, predictive maintenance, IoT, and advanced simulation software, it has become a highly sophisticated and adaptable machine that serves a variety of industries with increasing levels of precision, efficiency, and sustainability. These machines are now integral to custom manufacturing, small-to-medium production runs, rapid prototyping, and large-scale production, making them indispensable for companies looking to stay competitive in an ever-evolving market. As technology continues to advance, bowl metal spinning machines will likely incorporate even more innovations, further enhancing their ability to meet the growing demands of modern manufacturing.
Large-Diameter Spinning Machine

A Large-Diameter Spinning Machine is a type of metal spinning machine specifically designed to handle the formation of large, wide-diameter parts made from sheet metal. These machines are essential for producing large, round components in industries that require strength, durability, and precision in their metal parts. Common applications for large-diameter spinning include the production of tanks, vessels, dome-shaped structures, reflectors, funnels, and other large, concave items often used in sectors such as aerospace, automotive, energy, and construction.
Large-diameter spinning machines are capable of handling materials of substantial thickness and diameter compared to standard metal spinning machines. They can process sheet metals such as aluminum, stainless steel, copper, and titanium, which are often required for high-stress applications. This capability allows manufacturers to create parts that are both lightweight and strong, essential for industries where material efficiency and structural integrity are paramount.
The primary function of a large-diameter spinning machine involves the process of rotational forming. In this process, a flat sheet of metal is clamped onto a rotating mandrel (or spinning tool), and a spinning tool applies pressure to the material to gradually form it into a hollow, circular shape. As the machine operates, the metal is continuously shaped, stretched, and deformed to fit the profile of the mandrel. The key advantage of using this method is that it results in seamless and weld-free parts, which are often stronger and more durable than those created through other processes, such as welding or casting.
One of the main benefits of large-diameter spinning machines is their ability to handle complex geometries with high precision, even when dealing with parts that are several meters in diameter. These machines are typically equipped with advanced control systems, such as CNC (Computer Numerical Control), which enables precise programming of the rotational speed, tool pressure, and movement to achieve complex shapes and maintain tight tolerances. This makes large-diameter spinning particularly suitable for producing parts that require high accuracy, such as those used in aerospace or military applications, where precision is essential for functionality and safety.
The machines also feature heavy-duty frames and high-torque motors to support the spinning of large, thick materials. These robust machines are built to withstand the forces generated during the spinning process and ensure stable operation, even with high material deformation. Additionally, some large-diameter spinning machines are equipped with hydraulic systems to provide the necessary force to shape the metal, especially when working with thicker materials or more complex designs that require additional pressure.
In terms of machine configuration, large-diameter spinning machines can either be horizontal or vertical. The choice of configuration depends on the specific requirements of the parts being produced and the available space in the manufacturing facility. Horizontal machines tend to be more suitable for larger parts and allow for easier loading and unloading of materials, while vertical machines are often used for smaller but still large parts and may provide better access to the part being formed, improving the accuracy of the operation.
The ability to perform multiple passes is another feature that enhances the versatility of large-diameter spinning machines. In many cases, especially when dealing with thicker materials or larger diameters, the spinning process is performed in multiple stages. The first stage may involve forming the basic shape, while subsequent passes refine the part’s geometry, ensuring that the final product meets the required specifications. This incremental approach reduces the risk of defects or material failure, as the part is formed gradually rather than subjected to a single, heavy deformation process.
In addition to the technical capabilities, large-diameter spinning machines are also designed with automation and operator safety in mind. Advanced models often include automated material handling systems, such as robotic arms or conveyor belts, to load and unload parts automatically, reducing the need for manual labor and improving efficiency. Safety features such as emergency stops, guards, and sensors are standard to ensure the well-being of operators and prevent accidents during operation.
Large-diameter spinning machines can be used in a wide range of industries. In aerospace, they are used to produce components like engine nacelles, fuel tanks, and reflectors for satellite dishes. In energy, particularly in oil and gas, large-diameter spinning is used for making pressure vessels, storage tanks, and pipeline components. The automotive and marine industries also rely on these machines to manufacture large parts such as fenders, exhaust systems, and dome-shaped covers.
Furthermore, large-diameter spinning machines allow for high production efficiency. While the initial setup might take some time due to the size of the materials involved, the actual spinning process is relatively fast. This makes large-diameter spinning ideal for medium-volume production, as well as for creating custom parts or prototypes in industries that require precise, large components.
In terms of maintenance, large-diameter spinning machines require regular care to ensure the longevity of the equipment and the consistency of part quality. This includes inspecting the spinning tools, mandrels, motors, and hydraulic systems. Operators must also monitor tool wear and adjust settings as needed to avoid defects in the parts being produced. Lubrication and cleaning are also important to keep the machine in optimal working condition.
In conclusion, a Large-Diameter Spinning Machine is a vital tool for producing large, high-strength, seamless parts with precise geometries, making it indispensable in industries that require large, functional, and aesthetically pleasing components. These machines offer significant advantages in terms of material efficiency, precision, and production flexibility, and their ability to handle a variety of materials and complex shapes makes them ideal for aerospace, energy, automotive, and construction applications. With advancements in CNC technology, automation, and smart monitoring systems, these machines are becoming more efficient and capable, allowing manufacturers to meet growing demands for larger and more complex parts in the modern marketplace.
A Large-Diameter Spinning Machine is crucial in industries that require the production of large, circular components with high precision and structural integrity. These machines can form metals like aluminum, stainless steel, copper, and titanium into parts that are used in a wide array of applications, including pressure vessels, tanks, reflectors, dome-shaped covers, and more. With their ability to handle large sheets of metal, these machines are designed for producing seamless parts that can be lightweight yet strong, crucial in sectors like aerospace, energy, automotive, and construction.
The spinning process itself involves rotating a metal sheet around a mandrel, with a spinning tool applying pressure to gradually shape the material into the desired form. The advantage of this method lies in its ability to create seamless parts that do not require welding, making the resulting product much stronger. Large-diameter spinning machines are equipped with high-torque motors, heavy-duty frames, and sometimes hydraulic systems to handle thick and large-diameter materials. This makes them perfect for forming parts that need to withstand significant stresses, like those found in pressure vessels used in the oil and gas industry or aircraft components.
These machines are often integrated with CNC (Computer Numerical Control) systems, allowing for precise control of the spinning process, including rotational speed, tool pressure, and movement. With CNC technology, manufacturers can produce parts with complex geometries and tight tolerances, which is particularly valuable for applications where safety and functionality depend on exact specifications. The CNC system allows for easy programming of various shapes and sizes, which can be adjusted based on the part’s needs, making the large-diameter spinning machine highly adaptable and versatile.
Moreover, large-diameter spinning machines are typically designed to operate efficiently, with features such as automated material handling systems. These systems help feed metal sheets into the machine and facilitate the loading and unloading of parts, reducing the need for manual labor and ensuring that production runs smoothly. Automated handling not only boosts productivity but also reduces the chance of human error and enhances safety by limiting operator involvement during the high-risk part of the process.
Although large-diameter spinning machines are capable of producing a wide range of parts, their operation involves some unique challenges. The material being spun must be carefully chosen, as thicker metals or harder alloys can require more force, making the spinning process more demanding. The ability to perform multiple passes through the machine is often necessary when forming particularly large or thick parts. In such cases, each pass refines the part’s shape and ensures it meets the required specifications. This process allows for gradual deformation, reducing the likelihood of material failure.
A significant advantage of large-diameter spinning machines is the cost-effectiveness they offer for custom manufacturing and medium-volume production. Unlike other methods such as stamping or casting, which require expensive molds or dies, large-diameter spinning involves a flexible setup that can quickly accommodate design changes. This makes it a preferred method for creating custom components and prototypes for industries that need to test designs quickly or respond to specific requirements without incurring the costs of tooling changes.
The machines can be configured as either horizontal or vertical, with each setup offering different benefits depending on the part being produced and the production environment. Horizontal configurations are typically used for larger, heavier parts, as they allow for easier access to the material during the spinning process. In contrast, vertical configurations can be ideal for smaller parts, allowing for better control over the geometry and providing easier access to the spinning tool, particularly for fine-tuning the process.
In addition to their versatility and precision, large-diameter spinning machines are increasingly equipped with smart features like IoT connectivity, allowing for real-time monitoring and predictive maintenance. These features help operators track the performance of the machine, monitor tool wear, and receive alerts when a potential issue is detected. This proactive approach to maintenance reduces downtime, extends the machine’s lifespan, and helps manufacturers avoid costly repairs. Predictive maintenance can also improve part quality by ensuring that the machine operates at peak efficiency, reducing the likelihood of defects in the finished components.
The modern advancements in large-diameter spinning machine technology also emphasize sustainability. These machines can contribute to waste reduction by forming parts with minimal material waste, as opposed to traditional cutting methods. Additionally, they are often designed to be more energy-efficient, using less power and hydraulic fluid, which not only reduces operational costs but also lowers the environmental impact of manufacturing. Recycling and reusing scrap materials are becoming more common practices in large-diameter spinning, further promoting sustainability in the industry.
Overall, the Large-Diameter Spinning Machine is an indispensable tool for creating high-strength, seamless parts required for a wide range of industries. Its ability to form large, complex components with minimal material waste, high precision, and flexible customization makes it a valuable asset in sectors where quality, safety, and efficiency are critical. With the continued integration of CNC technology, automation, and smart monitoring, large-diameter spinning machines will remain at the forefront of manufacturing for complex, high-demand parts.
As the demand for more complex, large-scale components increases across various industries, Large-Diameter Spinning Machines are continuously evolving to meet these needs. The introduction of advanced automation and intelligent systems has led to greater efficiency and higher quality control in production, making these machines more reliable and productive in mass production environments as well as for custom, low-volume runs.
One notable advancement is the integration of machine learning algorithms into the control systems of large-diameter spinning machines. These systems can learn from past production data to improve accuracy and optimize settings based on various variables, such as material thickness, hardness, and even the speed of rotation. Machine learning helps fine-tune the spinning process, allowing for better surface finishes, fewer defects, and faster cycle times. As a result, the need for manual intervention is reduced, and operators can focus on overseeing the process and maintaining the overall workflow.
Additionally, advanced sensors are now routinely used in large-diameter spinning machines to monitor real-time data from various components of the machine. These sensors track parameters like vibration, temperature, and tool pressure, providing insights into potential issues before they become problems. By using this data, operators can make informed decisions on adjustments to the spinning process, such as speed changes or tool repositioning, ensuring optimal performance throughout the operation.
Another key development in large-diameter spinning is the improved ability to work with exotic materials. Industries like aerospace and energy increasingly require the use of specialized alloys, including titanium, inconel, and other high-strength materials that can withstand extreme environments. These materials often present challenges in terms of malleability, but modern large-diameter spinning machines are equipped with tools that can handle these tough alloys without compromising precision or speed. The machines’ ability to manage these materials reduces the need for costly secondary processes such as heat treatment or welding, which further enhances their cost-effectiveness.
The use of 3D simulation software is also gaining traction in the operation of large-diameter spinning machines. By creating digital twins of the parts to be produced, manufacturers can simulate the spinning process before any physical operation begins. This allows operators to assess and refine the design for optimal material usage, tool wear, and product integrity. Moreover, simulations enable testing of different process variables (e.g., speed, pressure, and feed rates) to predict outcomes and adjust parameters accordingly. This level of pre-production analysis not only improves part quality but also shortens setup times, leading to faster turnarounds on complex projects.
Robotic integration in large-diameter spinning machines is also becoming more common, especially for loading/unloading operations. Robots can handle the heavy lifting associated with moving large and heavy workpieces in and out of the machine, significantly improving safety and reducing manual labor. Additionally, robots can be equipped with vision systems and advanced sensors to ensure that parts are positioned correctly, which minimizes the risk of errors or material wastage.
Furthermore, the integration of sustainable practices in large-diameter spinning machines is expanding. These machines are now more energy-efficient than ever, using systems that minimize energy consumption during the spinning process. The development of closed-loop hydraulic systems and more energy-efficient motors reduces the overall environmental impact. Additionally, some systems include automated waste recycling, where scrap materials generated during the spinning process are collected, sorted, and reused in the production cycle, further decreasing the environmental footprint of manufacturing.
As industries continue to demand shorter lead times and greater customization, large-diameter spinning machines will increasingly offer flexible production capabilities. For example, manufacturers can now use these machines for on-demand production runs of custom components. These machines allow for rapid prototyping and short-run production without the need for dedicated tooling, reducing the time from design to production and offering significant cost savings compared to traditional methods that require custom molds and dies.
Looking ahead, the future of large-diameter spinning machines will likely see even more integration of digital technologies. Smart factories that leverage AI and big data will allow large-diameter spinning machines to operate as part of a larger automated production system, with seamless communication between machines and systems across the entire manufacturing process. This will lead to even more optimized workflows, improved part quality, and lower production costs.
In summary, the continued development of Large-Diameter Spinning Machines is making them more efficient, versatile, and sustainable, addressing the evolving demands of industries like aerospace, automotive, energy, and beyond. With innovations in automation, machine learning, advanced materials handling, and smart technologies, these machines are set to continue playing a pivotal role in the production of large, high-performance metal components. The future holds even more exciting possibilities, as the integration of digital solutions transforms the metal forming industry into a more dynamic, flexible, and environmentally-conscious sector.
Metal Spinning Machine with Automatic Tool Changer
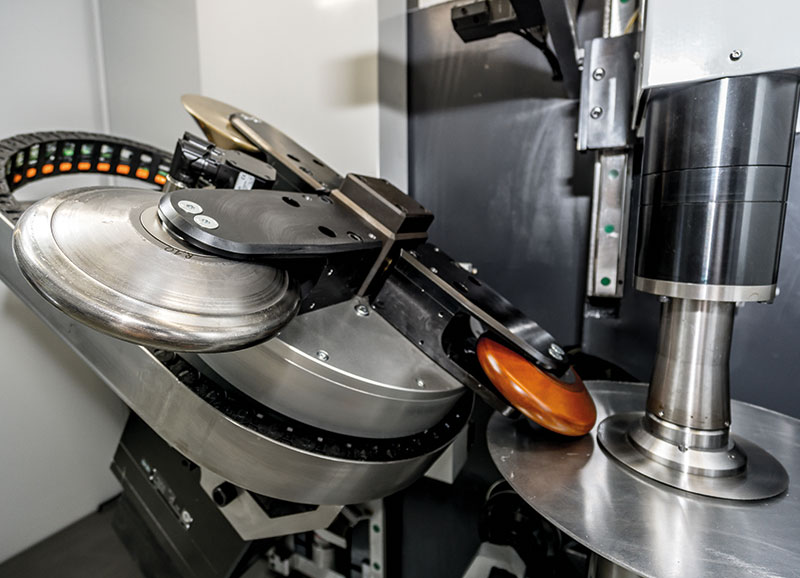
A Metal Spinning Machine with Automatic Tool Changer is a highly advanced form of the traditional metal spinning machine, designed to streamline the manufacturing process by automating the tool-changing function. This technology enhances the flexibility, speed, and overall efficiency of metal spinning operations, particularly in environments where a wide variety of parts with different shapes and sizes need to be produced. The addition of an automatic tool changer (ATC) allows for quick, precise, and automated switching between various tools without requiring manual intervention, saving significant time and improving overall productivity.
In a typical metal spinning process, a flat metal sheet is placed on a spinning mandrel, which rotates at high speeds while a tool presses and forms the metal into the desired shape. Metal spinning is often used for producing circular and cylindrical parts such as tanks, reflectors, dishes, and other hollow components. Depending on the specific design and complexity of the part, multiple tools might be required to perform different tasks, such as rough shaping, finishing, and trimming.
An Automatic Tool Changer (ATC) eliminates the need for operators to manually change tools during the spinning process. This automated system works by storing a variety of tools in a carousel or tool magazine, which can be programmed to automatically select and switch between tools based on the specific requirements of each production stage. For example, one tool may be used for the initial forming of the part, while another tool is required for finishing and smoothing the surface, and yet another for trimming excess material.
The use of an automatic tool changer in metal spinning machines provides several key benefits:
- Increased Productivity: By automating the tool-changing process, the machine reduces downtime between operations, allowing for continuous, uninterrupted production. This is particularly beneficial in high-volume manufacturing settings where fast cycle times are critical.
- Enhanced Precision: Automatic tool changers eliminate human error associated with manual tool changes. The precision with which the tool is swapped ensures that the correct tool is always in place, maintaining consistent quality and improving the accuracy of the final product.
- Reduced Labor Costs: Operators are no longer required to manually change tools, which reduces the need for skilled labor and the associated costs. The machine can run autonomously, reducing operator involvement and allowing workers to focus on monitoring the process or other value-added tasks.
- Improved Flexibility: Metal spinning machines with automatic tool changers are capable of handling a wide range of part designs without the need for extensive setup time or manual tool adjustments. This flexibility is especially useful in industries that require custom or low-volume production runs.
- Reduced Setup Time: Traditional metal spinning setups can take time to configure, particularly when changing between different tools. An automatic tool changer minimizes this setup time, allowing manufacturers to quickly switch between different tools and processes, thus speeding up production.
- Consistency in Tooling: The machine can be programmed to automatically perform specific sequences of operations, ensuring that the same tool is used in the exact same manner every time, providing consistent results for parts made in subsequent runs. This is particularly important in industries like aerospace or automotive, where high standards of precision and quality are required.
- Integration with CNC Systems: Many metal spinning machines with automatic tool changers are integrated with CNC (Computer Numerical Control) systems, which provide precise control over the machine’s movements and processes. This allows for highly complex, automated production sequences, where the machine can be programmed to perform multiple tasks with different tools at various stages of the operation.
The system’s tool magazine or carousel is typically designed to hold a range of tools, such as spinning tools, cutting tools, burnishing tools, and finishing tools, each suited to different stages of the spinning process. The ATC system is equipped with a robotic arm or mechanical mechanism that can quickly retrieve and replace the necessary tool. The changeover time is generally very short, allowing for minimal disruption to the production process.
Moreover, the maintenance and wear management of the tools become easier with an automatic tool changer. The machine can be set up to monitor tool conditions, alerting the operator when a tool is showing signs of wear or needs replacement. This helps ensure optimal performance and extends the lifespan of the tools.
Applications of a Metal Spinning Machine with Automatic Tool Changer are wide-ranging. It is especially useful in industries where highly customized parts are needed or where rapid production of a variety of parts is required. Some common applications include:
- Aerospace: For producing complex airframe components, engine parts, and reflectors.
- Automotive: For forming parts such as exhaust components, headlight reflectors, and fenders.
- Energy: For producing pressure vessels, turbine components, and storage tanks.
- Medical Devices: For creating medical equipment parts, such as surgical tools or implants.
- Consumer Electronics: For forming metal housings and enclosures for electronic devices.
As automation continues to advance, the role of the metal spinning machine with automatic tool changer is expected to grow. Further developments may include enhanced robotics for tool handling, more intelligent systems for process optimization, and the integration of machine learning to predict tool wear and adjust operational parameters. These innovations will continue to improve the speed, quality, and efficiency of the spinning process, allowing manufacturers to meet the increasing demands for complex, high-quality metal parts with shorter lead times and lower costs.
A Metal Spinning Machine with Automatic Tool Changer is a significant technological advancement in the field of metal forming, offering manufacturers increased flexibility, efficiency, and precision in their production processes. This type of machine eliminates the need for manual tool changes, which can often slow down production and introduce variability into the final product. By incorporating an automatic tool changer (ATC), the machine is able to automatically switch between different tools without requiring operator intervention, reducing downtime and allowing for continuous, streamlined operation.
The integration of an automatic tool changer into metal spinning machines helps improve productivity by speeding up the transition between different tasks during the spinning process. For example, when working on a complex part, a series of tools may be required, each serving a different function such as initial forming, trimming, and finishing. Instead of halting the production process for manual tool changes, the ATC system automatically selects and installs the correct tool, ensuring that each operation proceeds without unnecessary delays.
Moreover, the ability to program these machines using CNC (Computer Numerical Control) systems enhances their flexibility and precision. CNC control allows for complex part designs to be programmed into the system, which then guides the machine through each stage of the spinning process, including automatic tool changes. This level of automation not only speeds up production but also ensures consistent quality, as the tools are always in place when needed, and the machine can operate at optimal settings.
This technology is also highly advantageous in industries where the production of custom parts is common. For example, the aerospace, automotive, and energy sectors often require parts with highly specialized designs and varying dimensions. The ability to switch between different tools and carry out precise operations without interrupting the workflow makes this technology ideal for small to medium production runs, where setup times and part complexity are critical factors.
The automatic tool changer also plays a role in improving safety and reducing the risk of human error. Since the machine handles tool changes autonomously, operators are less likely to be exposed to the hazards associated with manually changing tools under high-speed, high-precision conditions. Additionally, the ATC system can be designed to track the wear and condition of tools, ensuring that tools are replaced or maintained at optimal intervals, further reducing downtime caused by tool failure or poor performance.
Another benefit is the reduction in manual labor, which can lead to cost savings over time. As the machine can operate with fewer operators and require less intervention, labor costs are reduced. This is particularly valuable for manufacturers who need to scale production quickly or work in environments where labor shortages are a concern. Automation also ensures that parts are produced with greater consistency, as the machine performs the same operations in the same sequence every time, eliminating the variability that can result from human intervention.
In terms of maintenance, an automatic tool changer provides improved management of tooling. By incorporating sensors and monitoring systems, the machine can detect wear patterns on tools and automatically alert operators when tools need sharpening, replacement, or maintenance. This predictive approach helps reduce unexpected downtime, as tools are replaced before they fail, leading to more reliable production.
Looking ahead, advancements in automation technology could further enhance the capabilities of metal spinning machines with automatic tool changers. The continued development of robotic systems for material handling and tool management, coupled with smart factory solutions that integrate data from multiple machines, will likely lead to even more efficient production processes. These machines may also be equipped with advanced artificial intelligence (AI) that can predict optimal settings, adjust for variations in materials, and even optimize tool usage based on real-time feedback.
In conclusion, a Metal Spinning Machine with Automatic Tool Changer represents a leap forward in manufacturing technology, providing significant benefits in terms of productivity, precision, and cost-effectiveness. As industries demand more complex and customized parts, the ability to automate tool changes and integrate advanced control systems will continue to make this technology a vital component in modern manufacturing. These machines not only enhance operational efficiency but also contribute to a safer, more sustainable production environment, making them an essential tool for industries that require high-quality, precision-formed metal parts.
As industries continue to evolve and the demand for more intricate and diverse metal parts grows, the Metal Spinning Machine with Automatic Tool Changer is poised to become an even more indispensable asset in advanced manufacturing. The integration of automation into metal spinning processes is expected to streamline production workflows even further, allowing manufacturers to meet the ever-increasing demands for customization, quality, and speed.
One of the key advantages of these advanced machines is their ability to work with a wide range of materials. With industries increasingly shifting toward the use of high-strength alloys and composite materials, the ability of the spinning machine to efficiently handle these tougher, more difficult-to-work materials while maintaining high precision is crucial. Automatic tool changers play a significant role in adapting to these varying material requirements by allowing the system to switch tools based on the specific material being processed. For instance, harder materials may require tools designed to withstand higher stresses or specific coatings to prevent wear. With an ATC system, the transition from one material to another can be done seamlessly and without manual setup, providing versatility in production.
Another noteworthy development is the growing integration of smart technologies within the metal spinning process. For example, sensor-driven feedback loops can be used to constantly monitor parameters such as pressure, temperature, and material deformation. These sensors communicate with the CNC system, enabling real-time adjustments to the spinning process to optimize performance. This adaptive control ensures that the machine operates at peak efficiency, reducing the chances of defects and waste. Moreover, the ability to track material behavior and adjust parameters accordingly can lead to the creation of more complex geometries that were previously difficult to achieve with traditional methods.
As the demand for high-precision components continues to grow in industries like aerospace, medical devices, and energy production, the role of the automatic tool changer becomes even more important. The flexibility provided by the ATC system means that manufacturers can switch between tools that are optimized for fine-tuning intricate designs and achieving tight tolerances. This precision is vital for creating parts that must meet stringent quality standards, such as turbine blades, aircraft fuselage components, and medical implants.
The scalability of metal spinning machines with automatic tool changers also allows manufacturers to handle both high-volume production and low-volume, high-mix manufacturing. The flexibility of these systems means they can be programmed to handle a variety of part sizes and designs, whether the demand is for thousands of identical parts or a smaller batch of customized components. This scalability is especially important for companies that produce prototypes, specialized parts, or products that require rapid market adaptation.
Furthermore, the integration of data analytics and machine learning with these systems opens new possibilities for process optimization. With data being continuously collected during production, manufacturers can analyze patterns in machine performance, tool wear, and material usage to predict and preempt issues before they arise. Predictive maintenance, based on the analysis of historical data, can be employed to forecast tool failure or wear, minimizing unplanned downtime and extending the life of the equipment. Additionally, this data can be used to fine-tune operational parameters for each type of part being produced, leading to even greater consistency and fewer defects.
The environmental impact of metal spinning is another area where these systems are making significant strides. Energy-efficient technologies incorporated into the machines ensure that power consumption is minimized during production, while automated processes help reduce material waste. Since the spinning process itself involves minimal material waste compared to traditional cutting methods, the combination of precision control, tool optimization, and reduced downtime further contributes to sustainability. Moreover, advancements in the reuse of scrap material and closed-loop recycling systems allow manufacturers to reduce their environmental footprint, as excess material from the spinning process can be collected, reprocessed, and reused.
In terms of user interface, the evolution of these machines includes advanced touch-screen panels and interactive dashboards that provide operators with real-time insights into machine performance. These interfaces offer a streamlined, intuitive way to monitor production status, change settings, and even troubleshoot issues remotely. As technology continues to advance, operators may also see the integration of augmented reality (AR), allowing them to virtually inspect parts and tools, troubleshoot problems, or receive instructions for maintenance or repair tasks.
The increased integration of robotics with these spinning machines also promises to enhance flexibility and precision. Automated robotic arms can be used not only for tool changes but also for material handling, part inspection, and post-processing tasks such as deburring or polishing. This reduces the reliance on manual labor and speeds up production processes while ensuring that each step is carried out with precision.
As these technologies continue to mature, the Metal Spinning Machine with Automatic Tool Changer will increasingly become the backbone of precision metal forming in industries that require complex shapes, high tolerances, and customization at scale. The role of automation in these machines will likely expand, incorporating even more advanced features like AI-powered quality control, real-time optimization algorithms, and full factory automation integration. These capabilities will ultimately provide manufacturers with the tools they need to meet the challenges of modern, fast-paced production environments, while also ensuring cost-effectiveness, quality, and sustainability.
In conclusion, the future of metal spinning machines with automatic tool changers is bright, driven by the need for high-speed, high-precision, and adaptable production methods across a wide array of industries. The growing use of automation, data analytics, AI, and robotics will only enhance the capabilities of these machines, further cementing their place as a critical component in the future of advanced manufacturing.
CNC Multi-Axis Metal Spinning Machine
A CNC Multi-Axis Metal Spinning Machine represents the cutting edge in precision metal forming technology, combining the versatility of Computer Numerical Control (CNC) with the advanced capabilities of multi-axis manipulation to produce highly intricate and complex shapes. These machines are designed to handle parts that require high precision and intricate geometric features, offering manufacturers the ability to create cylindrical, conical, and spherical components with fine details, often in industries like aerospace, automotive, energy, and medical device manufacturing.
The primary feature of a CNC Multi-Axis Metal Spinning Machine is its ability to move the tool and workpiece along multiple axes simultaneously. While traditional single-axis or two-axis machines move the tool or the part in a fixed, linear motion (typically along the X and Y axes), a multi-axis machine adds more degrees of freedom. Typically, these machines incorporate three, four, or even five axes, allowing for greater control over the part’s shape and the ability to perform complex operations without having to reposition the workpiece or tool manually.
These multi-axis systems allow for more dynamic tool paths, enabling the machine to rotate or tilt the workpiece in relation to the spinning tool. This allows the spinning tool to engage the part in multiple orientations, providing more control and flexibility to achieve complex contours, tight tolerances, and smooth finishes. It also enables manufacturers to produce parts with complex features, such as concave surfaces, sharp edges, or non-circular geometries, which would otherwise be difficult or impossible to achieve with traditional metal spinning methods.
The CNC aspect of these machines brings several key advantages:
- Precision: CNC control ensures that the movement of the workpiece and tool is highly accurate, with minimal deviation between the programmed design and the final product. Operators can input precise data into the CNC system, allowing the machine to follow complex paths and achieve fine tolerances.
- Automation: CNC Multi-Axis Metal Spinning Machines can be programmed to perform multiple tasks, such as forming, cutting, trimming, and finishing, in a continuous cycle. This automation reduces the need for manual intervention, which speeds up production, reduces human error, and minimizes downtime.
- Complex Geometry: Multi-axis capabilities allow the creation of intricate and highly detailed shapes. For instance, parts that require both curved and angular surfaces can be produced more easily, with precise control over the angle and depth of the cut or form.
- Flexibility in Design: CNC programming enables manufacturers to create a wide range of designs, from simple, repetitive shapes to highly customized, one-off parts. The ability to quickly modify the programming means that the machine can be used for prototyping, short-run production, or mass production, making it highly adaptable to various manufacturing needs.
- Reduced Setup Time: With multi-axis machines, the need for tool changes and repositioning of the workpiece is minimized. Parts can be spun and finished without requiring multiple setups, which reduces overall production time and improves the consistency of each part.
- Integration with CAD/CAM: Many CNC multi-axis metal spinning machines are designed to work seamlessly with Computer-Aided Design (CAD) and Computer-Aided Manufacturing (CAM) software. This integration enables manufacturers to directly input digital designs into the machine, allowing for quick and accurate translation of complex part geometries into actual products. Furthermore, the machine can automatically adjust its programming to account for variations in material, thickness, or other factors, improving part quality and consistency.
These machines can handle a variety of materials, including aluminum, stainless steel, titanium, copper, and other alloys commonly used in metal forming. They are especially useful in industries that require high-performance parts, such as aerospace and defense, where components must meet strict tolerances and material specifications to ensure safety and functionality.
One example of an application for a CNC multi-axis metal spinning machine is the production of aerospace engine components. These parts often require precise contours and thin walls, which are difficult to achieve through traditional manufacturing methods like casting or machining. With a multi-axis spinning machine, manufacturers can shape these parts more efficiently, reducing material waste and improving the structural integrity of the finished product.
The speed and accuracy of CNC multi-axis metal spinning also make it suitable for industries requiring high volumes of parts with uniform quality. For instance, automotive manufacturers often use these machines to produce lightweight yet durable components, such as vehicle body panels, exhaust components, and reflectors, which must meet both performance standards and aesthetic requirements.
Additionally, the ability to integrate robotic arms or automation systems with CNC multi-axis machines enhances productivity even further. Robotic automation can be used for loading and unloading parts, handling material, or post-processing tasks such as polishing, deburring, or inspection, creating a fully automated production line that minimizes manual labor and reduces production times.
In terms of maintenance and tool management, modern CNC multi-axis machines are equipped with sensors that monitor various aspects of the system, such as tool wear, vibration, and temperature. These sensors can provide real-time data that allows operators to perform predictive maintenance and avoid unplanned downtime. By constantly monitoring the condition of the tools, the machine can alert operators when tools need replacement or adjustment, ensuring optimal performance and extending the lifespan of the equipment.
The future of CNC multi-axis metal spinning is likely to be shaped by continued advances in robotics, machine learning, and artificial intelligence. As these technologies develop, we can expect to see even more automated and intelligent systems that can adjust the process parameters in real time to optimize quality, reduce waste, and improve production speeds. The integration of augmented reality (AR) could also play a role in improving operator training, troubleshooting, and maintenance, offering live instructions or digital overlays to guide operators in handling complex tasks.
In summary, a CNC Multi-Axis Metal Spinning Machine is an advanced, flexible, and precise tool for the production of high-quality metal components. By combining the precision of CNC control with the flexibility of multi-axis motion, these machines enable manufacturers to produce complex geometries, reduce cycle times, and maintain high levels of quality and consistency. As industries continue to demand more intricate designs, these machines will become increasingly important in achieving the precision and efficiency needed for modern manufacturing applications.
A CNC Multi-Axis Metal Spinning Machine is at the forefront of modern manufacturing technology, offering advanced capabilities for producing highly intricate and precise metal components. By incorporating multi-axis movement, these machines allow the tool and workpiece to move simultaneously along several axes, providing greater control and flexibility in shaping complex geometries. This feature is especially beneficial for creating components with both curved and angular surfaces, which would otherwise be challenging or time-consuming to achieve with traditional methods.
The integration of Computer Numerical Control (CNC) ensures that each movement of the machine is meticulously controlled, allowing for high precision and repeatability. This makes CNC multi-axis metal spinning machines particularly valuable in industries where tight tolerances and custom shapes are critical, such as aerospace, automotive, and medical device manufacturing. The machine’s ability to automatically adjust the tool’s path based on the pre-programmed design leads to minimal human error and ensures that each part is produced to exact specifications.
One of the standout advantages of these machines is their ability to automate complex processes, reducing the need for manual intervention. Once a design is programmed into the CNC system, the machine can carry out multiple tasks without the need for the operator to reposition the workpiece or switch tools manually. This capability results in significant time savings and helps streamline production, which is particularly beneficial for high-volume manufacturing. By reducing manual setups and tool changes, production efficiency increases, leading to shorter lead times and cost savings for manufacturers.
Another significant benefit is the flexibility these machines offer in terms of part complexity. A CNC multi-axis metal spinning machine can handle a wide range of shapes, from simple cylindrical components to intricate, asymmetrical designs. The ability to easily create non-circular, concave, or compound curved surfaces means that manufacturers can produce parts that would otherwise require multiple operations, such as machining or casting. This is especially valuable for industries that require highly specialized parts, such as turbine blades, aircraft fuselage panels, and medical implants, where precision and material integrity are of utmost importance.
Additionally, these machines are designed to work with a wide variety of materials, from common metals like aluminum and stainless steel to more specialized alloys, including titanium and nickel-based superalloys. This material versatility makes them adaptable to different manufacturing environments, allowing companies to meet diverse industry needs without requiring separate machines for different material types.
The integration of advanced software further enhances the capabilities of CNC multi-axis metal spinning machines. By using CAD/CAM software, manufacturers can input precise, complex designs directly into the CNC system, eliminating the need for manual calculations or adjustments. These programs can also simulate the entire process, allowing engineers to visualize the part before it is produced and identify potential issues, such as material deformation or tool interference, in advance. This proactive approach helps prevent costly mistakes and ensures that parts are made with the highest level of accuracy and efficiency.
In terms of maintenance and operational longevity, these machines are equipped with monitoring systems that track parameters such as tool wear, spindle performance, and vibration levels. These sensors allow for predictive maintenance, which helps to identify potential issues before they result in machine downtime. By addressing wear and tear before they lead to failure, manufacturers can ensure continuous production and extend the life of the equipment. Predictive maintenance is becoming increasingly important as manufacturers strive to reduce unplanned downtime and improve operational efficiency.
Another key aspect of CNC multi-axis metal spinning machines is their ability to perform multi-stage operations. For example, these machines can perform both forming and trimming in a single cycle, reducing the need for additional processing steps or manual intervention. This capability is especially beneficial when producing parts with complex contours or tight tolerances, as it minimizes the risk of introducing imperfections between stages.
Moreover, the robotic integration in these machines can further enhance automation. Robotic arms or other handling systems can be used to load and unload parts, handle materials, or even perform secondary operations such as deburring or polishing. This further reduces the reliance on manual labor and increases overall throughput, making the entire process more efficient and cost-effective. The ability to automate both primary and secondary operations helps to optimize production flow, especially in high-volume or batch manufacturing environments.
The potential for intelligent systems is also growing. As technologies such as artificial intelligence (AI) and machine learning (ML) continue to evolve, there may be opportunities to incorporate these capabilities into CNC multi-axis spinning machines. These technologies could enable the machine to automatically adjust its settings based on real-time feedback, optimizing performance and reducing the likelihood of errors. For example, an AI system could predict when a tool is likely to wear out and automatically adjust the feed rates or select a new tool from the tool changer to maintain optimal production speed.
In addition, as sustainability becomes an increasingly important consideration in manufacturing, CNC multi-axis metal spinning machines can contribute to environmentally friendly practices. Since metal spinning is a subtractive process that minimizes material waste compared to traditional machining methods, it is already a more sustainable choice. Moreover, these machines can be equipped with energy-efficient technologies and can be programmed to optimize the use of resources, further reducing environmental impact.
Looking to the future, the capabilities of CNC multi-axis metal spinning machines are likely to expand even further. As manufacturers continue to demand more complex, high-performance parts, these machines will continue to evolve to meet those needs. The integration of additive manufacturing or hybrid technologies, which combine traditional metal spinning with 3D printing, could offer additional possibilities for producing parts with even more complex geometries and material combinations.
In conclusion, the CNC Multi-Axis Metal Spinning Machine is a highly versatile and advanced tool that combines precision, flexibility, and automation to meet the demands of modern manufacturing. With its ability to create complex parts efficiently and accurately, it is a key asset in industries that require high-performance, customized components. The continued development of smart technologies, robotic automation, and machine learning will only enhance the capabilities of these machines, ensuring that they remain a crucial part of the manufacturing process for years to come.
The future of CNC Multi-Axis Metal Spinning Machines looks increasingly promising as advancements in technology continue to reshape manufacturing processes. The integration of artificial intelligence (AI) and machine learning (ML) is likely to play a major role in enhancing the capabilities of these machines, making them even smarter and more autonomous. For instance, AI could help optimize the spinning process by analyzing real-time data from sensors embedded in the machine, adjusting parameters such as speed, pressure, and tool orientation to maintain the highest levels of precision. These systems could also predict potential issues, such as tool wear or material inconsistencies, before they arise, allowing for proactive maintenance and minimizing downtime.
Furthermore, the rise of Industry 4.0 and smart factories means that CNC multi-axis metal spinning machines are becoming more connected and integrated with other parts of the production line. These machines can communicate with other automated systems, share data, and receive instructions in real-time, leading to a more collaborative and efficient manufacturing environment. Through advanced IoT (Internet of Things) technologies, these machines will be able to provide continuous feedback on production status, tool health, and part quality, enabling operators to make informed decisions about their processes without having to be physically present at the machine.
One of the key areas of development is the further integration of robotics. While many CNC multi-axis metal spinning machines already use robotic arms for handling materials or performing secondary operations, there is growing interest in incorporating more advanced robotic systems that can autonomously adapt to changes in the production process. This could involve robots adjusting the tooling or reprogramming machine movements based on real-time feedback from the system, thereby improving flexibility and reducing cycle times even further.
The ability to handle a wider range of materials is another exciting development. As industries increasingly demand advanced alloys, composite materials, and other specialized substances, CNC multi-axis metal spinning machines are being designed to work with a greater variety of materials. This includes materials that require specialized tooling or more complex processes to form. For example, certain aerospace components might need to be spun from high-temperature alloys or materials that require specific care to prevent deformation. The versatility of these machines allows them to adapt to these new materials without compromising quality or performance.
The sustainability aspect of CNC multi-axis metal spinning machines is also expected to see significant improvements in the coming years. As the manufacturing industry becomes more conscious of its environmental footprint, machines will be designed with even greater energy efficiency in mind. This includes the development of more energy-efficient motors, reduced waste generation, and the potential for closed-loop recycling systems that allow for the reuse of scrap metal and other materials directly in the spinning process. Furthermore, the precise nature of CNC metal spinning results in less material waste compared to traditional machining methods, contributing to reduced consumption of raw materials and more sustainable production practices overall.
There is also potential for hybrid manufacturing systems, where CNC multi-axis metal spinning is combined with additive manufacturing (3D printing). This hybrid approach would allow for parts that require both the precision of spinning and the flexibility of additive processes, enabling the creation of complex internal structures or hybrid materials that were previously impossible to produce using traditional methods alone. For example, certain aerospace components might benefit from the combination of spun outer shells with additive internal structures to optimize material usage and strength-to-weight ratios.
Moreover, the use of augmented reality (AR) and virtual reality (VR) in machine operation and training is an exciting avenue for enhancing the functionality of these systems. AR overlays could be used to guide operators through setup procedures, maintenance tasks, or troubleshooting, providing real-time information that enhances accuracy and efficiency. This could also extend to the training of new operators, as they would be able to interact with virtual representations of the machine and its processes, helping them learn the intricacies of CNC multi-axis spinning without the need for physical machines.
As industries continue to demand more customization and shorter production runs, the flexibility of CNC multi-axis metal spinning machines will become even more valuable. Rapid prototyping and small batch production are expected to become more prevalent, as these machines are well-suited to produce highly customized components without requiring extensive setup times. The ability to rapidly change tooling, adjust machine parameters, and quickly iterate on design modifications makes these machines ideal for industries where short lead times and high customization are critical, such as in the automotive, aerospace, and medical sectors.
Looking forward, the concept of digital twins could also be applied to CNC multi-axis metal spinning. A digital twin is a virtual replica of the physical machine or manufacturing process, allowing operators and engineers to monitor and analyze performance in real time. This would enable better decision-making, faster troubleshooting, and even predictive maintenance by continuously analyzing machine data, historical performance, and environmental factors. As digital twins become more sophisticated, they could be used to simulate the entire production process, from material input to finished part, further enhancing quality control and efficiency.
The evolution of CNC Multi-Axis Metal Spinning Machines will continue to be driven by the demand for greater precision, faster production cycles, and higher-quality parts across a wide range of industries. As technology advances, these machines will become increasingly capable, integrating with other digital technologies, leveraging automation, and embracing more sustainable practices. The result will be a new era of manufacturing that is faster, more flexible, and more responsive to the demands of the modern market, all while maintaining the high standards of quality that industries depend on.
As the field of CNC Multi-Axis Metal Spinning Machines continues to evolve, one of the most exciting prospects lies in automation and AI-driven processes that enhance the adaptability of these machines. For instance, through machine learning algorithms, these systems could continuously improve their operations by learning from past production cycles, identifying optimal parameters for specific tasks, and even compensating for minor deviations in material properties. The integration of AI could lead to machines that automatically adjust their settings, ensuring optimal performance without requiring human intervention, further reducing the risk of errors and the need for rework.
Additionally, collaborative robots (cobots) are beginning to play a role in enhancing the flexibility of CNC metal spinning machines. These robots can work alongside human operators, providing support for tasks like material loading, unloading, and even handling delicate operations. Unlike traditional industrial robots that work in isolation, cobots can operate safely in the same environment as human workers, facilitating more interactive and agile manufacturing processes. This allows manufacturers to respond quickly to changing demands and adapt to new products or designs without significant downtime for reprogramming.
In parallel with AI and robotic integration, sensor technology will become even more critical in refining the process. Advanced sensors can monitor the condition of tools, workpieces, and the environment, feeding real-time data back to the CNC system to adjust the spinning process on the fly. This could involve monitoring temperature, pressure, vibration, and tool wear, ensuring the process remains within optimal operating parameters. By doing so, the system can automatically compensate for environmental variations, material inconsistencies, and tool degradation, further reducing the likelihood of defects and improving part quality.
The use of data analytics in combination with these sensors will likely be another key development in future CNC multi-axis spinning systems. Manufacturers will be able to collect vast amounts of operational data from the machines, which can be analyzed to uncover trends, inefficiencies, or predictive maintenance needs. With the ability to monitor machine performance continuously, manufacturers can implement predictive analytics to anticipate when a component might fail or when maintenance should be scheduled, reducing unscheduled downtime and ensuring consistent production.
Another innovative direction for CNC Multi-Axis Metal Spinning Machines is their integration with 3D scanning and inspection systems. High-resolution 3D scanners could be used to inspect the finished part in real time as it’s being formed, comparing it with the original design specifications. If any deviations are detected, the machine could automatically adjust its parameters to correct the issue, ensuring the part meets quality standards. This process would effectively combine in-line quality control with the production process, enabling manufacturers to detect and correct defects immediately, rather than after the part has been completed.
Virtual reality (VR) and augmented reality (AR) are also poised to have a major impact on CNC multi-axis spinning operations. For example, VR could be used to simulate the spinning process, allowing operators to visualize tool paths and potential issues in a digital environment before actual production begins. This kind of simulation could significantly reduce the risk of mistakes, improve training, and allow for better decision-making in the design and production process. AR could be applied to provide real-time guidance to operators during setup or maintenance procedures, overlaying crucial information directly onto the machine or the operator’s workspace, helping them to optimize machine performance or troubleshoot issues faster.
The growing focus on sustainability will continue to influence the design and operation of CNC multi-axis metal spinning machines. As industries look for ways to minimize their carbon footprint, there is increasing interest in machines that use energy-efficient motors, incorporate recyclable materials, and minimize material waste. Future machines may feature systems that recover energy during the spinning process, such as regenerative braking, or closed-loop recycling systems that allow metal scrap and byproducts to be seamlessly returned to the production cycle. The precise nature of CNC metal spinning inherently produces less waste compared to traditional machining methods, and with further advances in sustainable technologies, this process can become even more eco-friendly.
The customization capabilities of CNC multi-axis spinning machines will also be enhanced by new software tools. The integration of cloud-based platforms could allow manufacturers to collaborate more easily, sharing designs and production data in real time across different teams or even across different facilities. These platforms could host design libraries, where users can quickly access and modify pre-configured spinning programs, dramatically reducing the time spent programming new parts and enabling faster response times for changes in customer orders or production schedules.
Moreover, the development of hybrid manufacturing processes, where CNC spinning is combined with additive manufacturing (3D printing), could enable the production of parts with internal features that are impossible to achieve with traditional techniques alone. For example, a component could be spun to form an outer shell and then printed with internal support structures to reduce weight, improve strength, or incorporate complex cooling channels for aerospace and automotive applications. These hybrid processes could revolutionize industries by enabling the production of parts with unprecedented design flexibility.
As the demand for high-precision and low-volume production continues to grow, CNC multi-axis metal spinning machines will be increasingly relied upon to create highly customized and intricate components. This trend is especially prominent in industries like medical devices, where custom implants and surgical tools are required, and in the aerospace sector, where parts must meet exacting standards for strength, lightweight performance, and aerodynamic efficiency.
The evolution of smart manufacturing systems means that future CNC multi-axis metal spinning machines will not only be highly automated and efficient, but will also be self-optimizing, able to adapt to new conditions and production requirements on their own. Through the use of advanced AI algorithms, sensors, and real-time data analysis, these machines will make adjustments in the process, optimizing tool paths, reducing scrap, and improving energy usage—all while maintaining strict quality control and meeting the most demanding production schedules.
As global supply chains continue to adapt to the challenges of an increasingly digital, connected world, the need for flexible, agile manufacturing processes will increase. CNC multi-axis metal spinning machines, with their capacity to rapidly change between different product designs and optimize production parameters on the fly, will be key enablers of these agile, responsive supply chains. This will ensure that manufacturers can continue to meet consumer demands for more diverse, personalized products while maintaining high efficiency and consistent quality.
In summary, CNC Multi-Axis Metal Spinning Machines are poised for continuous growth, incorporating the latest advancements in AI, robotics, automation, and digital technologies. These machines are evolving to meet the demands of industries that require precision, flexibility, and customization. As the manufacturing landscape becomes more interconnected, sustainable, and intelligent, these machines will play a central role in shaping the future of high-performance component production, ensuring they remain integral to the development of next-generation products across a wide range of industries.
Custom-Made Metal Spinning Machine
A Custom-Made Metal Spinning Machine is a highly specialized piece of equipment designed to meet the unique production needs of a manufacturer or industry. Unlike standard, off-the-shelf metal spinning machines, these machines are specifically tailored to the specific requirements of the customer, whether it’s for producing custom-shaped parts, working with unconventional materials, or achieving highly specific tolerances. Custom-made machines are often sought after when standard machines cannot meet the precision, flexibility, or operational needs required for specialized production runs.
Key Features of a Custom-Made Metal Spinning Machine:
- Tailored Design and Specifications: The most significant advantage of a custom-made machine is its ability to meet precise operational requirements. From the size and capacity to the specific tooling and control systems, every component can be adjusted to suit the intended application. Custom machines are often designed with a particular material (e.g., titanium, nickel alloys) or part geometry (e.g., asymmetrical shapes or large diameters) in mind.
- Flexible Tooling Systems: Custom machines often feature specialized tooling setups that allow for greater flexibility in handling complex part designs. This could include customized mandrels, rollers, forming tools, or cutting tools that are designed to handle specific features of a part, such as non-circular cross-sections, deep forms, or complex contours.
- Adaptation for Specific Materials: Custom metal spinning machines can be built to work with specialized or non-standard materials that are difficult to process using regular machines. For instance, exotic metals used in aerospace and medical device manufacturing, or highly reflective metals used in optics, may require specific tooling and process adjustments to prevent material damage or ensure high-quality finish and structural integrity.
- Advanced Control Systems: Custom-built machines can incorporate cutting-edge CNC systems or other advanced control systems, allowing for detailed, precise control over the spinning process. These systems can integrate multi-axis capabilities, enabling the machine to form complex shapes with greater accuracy. Additionally, custom machines can include feedback loops and sensor systems to monitor and adjust the process in real time, ensuring high-quality results throughout production.
- Enhanced Precision and Tolerances: Custom-made machines are typically designed to meet very tight tolerances and achieve high-quality finishes, making them ideal for industries that require parts with minimal deviation from design specifications. For example, in aerospace, automotive, or medical applications, the precision of a part can be critical to its functionality and safety, and custom machines help ensure that each part meets these stringent standards.
- Modular Components: A custom machine often uses modular components that can be replaced or upgraded easily. This modularity allows manufacturers to make adjustments to the machine as their needs evolve, offering long-term flexibility. Whether it’s adapting the machine to handle a new material, increase throughput, or introduce more advanced features, modularity ensures that the machine can evolve with the business needs.
- Automation and Robotic Integration: For manufacturers seeking high-volume production, a custom-made metal spinning machine may include automation features such as robotic arms for material handling, tool changing, or secondary operations (e.g., trimming, deburring). Automation helps reduce human intervention, speed up production, and ensure greater consistency and repeatability in manufacturing processes.
- Increased Efficiency and Reduced Waste: A custom-made machine can be designed to operate with minimal material waste by optimizing tool paths and spindle speeds. As the machine is built with specific products and processes in mind, the system can be fine-tuned to handle the material more efficiently, reducing costs associated with excess material usage and scrap.
- Specialized Safety Features: Custom-built machines often incorporate safety features that are tailored to the specific risks associated with the production process. This could include enhanced enclosures, interlock systems, or safety sensors designed to protect operators from potential hazards specific to the materials or processes involved.
Industries that Benefit from Custom-Made Metal Spinning Machines:
- Aerospace: In aerospace manufacturing, components such as turbine housings, fuel tanks, and engine casings require highly specialized geometries and materials. Custom-made metal spinning machines can be designed to handle exotic alloys like titanium and nickel-based superalloys, producing parts with extremely tight tolerances necessary for high-performance applications.
- Medical Devices: For the medical device industry, custom-made metal spinning machines are used to produce components such as surgical instruments, implants, and prosthetics, where precision, material compatibility (e.g., biocompatibility of metals), and intricate shapes are essential.
- Automotive: Custom machines are often needed to produce specialized parts for the automotive industry, such as wheel rims, exhaust components, and custom body panels. These parts often need to be lightweight, durable, and capable of withstanding high temperatures or other environmental stresses.
- Electronics and Optics: For companies producing specialized components in optics, electronics, or reflective surfaces, custom-made metal spinning machines can be designed to work with highly reflective metals or create intricate lenses, shields, or casing parts that require fine detail and a smooth finish.
- Energy and Power Generation: In the energy sector, particularly for nuclear and renewable energy applications, custom-made metal spinning machines can be designed to produce large and complex components, such as pressure vessels, turbine blades, and generator housings, which require both material strength and high precision.
- Art and Sculpture: Beyond industrial applications, custom machines can also cater to the art and design industries, where metal spinning is used to create unique, decorative elements for sculptures, architecture, and custom installations.
Advantages of Custom-Made Metal Spinning Machines:
- Tailored to Specific Needs: These machines are designed to meet the unique requirements of a particular production process, ensuring that manufacturers can produce the exact components they need.
- Improved Production Efficiency: By optimizing the machine for a particular task, manufacturers can reduce setup times, increase throughput, and minimize waste.
- Enhanced Precision: Custom machines allow for fine-tuned control over the spinning process, resulting in parts with exceptional quality and precise tolerances.
- Long-Term Investment: Custom machines are built to last, with parts and features specifically designed for a manufacturer’s processes. This results in a reliable long-term investment that will serve the company for many years.
Challenges of Custom-Made Metal Spinning Machines:
- Cost: Custom machines are typically more expensive than off-the-shelf models due to the engineering, design, and manufacturing time required. The upfront cost can be high, but this can be offset by the machine’s efficiency and long-term performance.
- Lead Time: Designing and manufacturing a custom metal spinning machine takes time, often several months, depending on the complexity of the requirements. This lead time must be factored into production schedules.
- Maintenance and Support: Custom machines may require more specialized knowledge for maintenance and repair, and manufacturers may need to ensure they have access to skilled technicians or support services.
Conclusion:
A Custom-Made Metal Spinning Machine offers unmatched flexibility, precision, and efficiency for manufacturers who require specialized equipment tailored to their unique production needs. By optimizing the machine for specific materials, part geometries, and production processes, companies can enhance their manufacturing capabilities, reduce waste, and ensure high-quality results. While these machines represent a significant investment, they offer significant long-term benefits, especially in industries that demand complex, high-precision components.
Custom-made metal spinning machines continue to push the boundaries of what is possible in manufacturing, offering highly personalized solutions that are finely tuned to each customer’s operational needs. These machines are not just modified versions of existing designs; they are often developed from the ground up, beginning with a detailed understanding of the specific production goals, materials to be spun, part geometries, and quality standards required by the client. This deep level of customization enables manufacturers to overcome challenges that would otherwise limit the use of conventional spinning equipment, opening new possibilities for innovation and efficiency.
The design process for a custom-made metal spinning machine often involves close collaboration between the equipment manufacturer and the end-user. Engineers gather precise information about the intended applications, including the range of part sizes, material properties, production volumes, and special surface finish requirements. Based on this information, every aspect of the machine — from the base frame and spindle design to the forming rollers, control systems, and safety features — is optimized to ensure the best possible performance. Special considerations, such as the need for ultra-high-speed spindles for thin-walled parts or heavy-duty frames for large, high-force applications, are factored in to ensure the machine can perform reliably under real-world conditions.
Because each custom machine is purpose-built, it can incorporate the latest available technologies, including high-precision servo motors, fully programmable CNC systems with multi-axis coordination, and integration with factory-wide digital manufacturing systems. This connectivity allows for real-time monitoring, predictive maintenance, and seamless coordination with other production equipment. Custom machines can also be designed with future-proofing in mind, allowing for later upgrades or modifications to adapt to evolving production needs, which protects the user’s investment as market demands change over time.
Customization can extend beyond just mechanical and control system design to include the integration of specialized forming methods, such as combined spinning and shear forming capabilities, or the ability to transition between hot and cold spinning processes depending on the material requirements. For instance, a custom machine may include integrated heating systems like induction coils or gas burners to heat the workpiece during forming, allowing it to achieve more extreme shapes or work with harder materials that would crack or fail during cold spinning. Similarly, advanced cooling systems can be built into the design to maintain process stability and improve part quality during high-speed operations.
Another important area of customization lies in tooling automation. In traditional spinning operations, changing tools between different parts can be time-consuming and labor-intensive. A custom-built machine can feature automated tool changers or quick-change tooling systems, minimizing downtime and making it easier to switch between different production runs with minimal operator intervention. This level of flexibility is particularly valuable for manufacturers who produce a wide variety of parts in small to medium batch sizes, where frequent changeovers would otherwise impact productivity.
In terms of materials handling, custom metal spinning machines can be designed with automated loading and unloading systems, including robotic arms, conveyors, or automated guided vehicles (AGVs). These systems reduce the physical demands on human operators, improve workplace safety, and enable higher overall equipment effectiveness. For extremely large or heavy workpieces, special handling solutions like hydraulic lifts, rotating platforms, or vacuum clamping systems can be integrated directly into the machine layout, ensuring that even the most challenging components can be spun efficiently and safely.
Customization also plays a critical role in ensuring compliance with specific industry standards and regulations. For instance, machines destined for aerospace production might require traceability systems that log every production parameter for each part made, while those used in medical device manufacturing might need to operate within cleanroom environments and adhere to strict contamination control protocols. A custom-designed machine can be tailored to meet all relevant standards, ensuring that it not only produces high-quality parts but also satisfies the rigorous compliance requirements of highly regulated industries.
While the initial design and build process for a custom-made metal spinning machine is more complex and time-consuming compared to purchasing a standard machine, the long-term advantages often far outweigh the initial investment. Manufacturers gain a piece of equipment that is perfectly aligned with their production goals, delivering better part quality, higher throughput, lower operating costs, and greater operational flexibility. Moreover, the customization process often sparks innovation, with engineers and manufacturers collaborating to develop new techniques, processes, or features that can provide a competitive advantage in the marketplace.
Looking forward, the demand for custom-made metal spinning machines is expected to grow as industries increasingly seek tailored solutions to meet unique product requirements and market expectations. The rise of personalization across consumer markets, the trend toward shorter product life cycles, and the growing emphasis on lightweight, high-performance materials all drive the need for highly specialized manufacturing equipment. As technology continues to advance, future custom-made machines may incorporate even more sophisticated automation, smarter control algorithms, and tighter integration with digital manufacturing ecosystems, making them even more capable, efficient, and adaptable.
Ultimately, custom-made metal spinning machines embody the intersection of craftsmanship and technology, providing manufacturers with the precision tools they need to produce innovative, high-quality parts that meet the demands of modern industry. They stand as a testament to the power of engineering to create solutions that are not just functional but transformational, enabling companies to reach new levels of productivity, quality, and design freedom.
The continued evolution of custom-made metal spinning machines is being shaped not just by technological innovation, but also by the increasingly specialized demands of various industries. For instance, in sectors like aerospace and defense, there is a constant need for lightweight, complex-shaped components that can withstand extreme stresses and temperatures. Custom machines are being designed with enhanced thermal management systems and reinforced structural elements to maintain precision even under these demanding conditions. Materials such as titanium alloys, Inconel, and other advanced composites are becoming more common in spinning operations, and the machines must be engineered specifically to handle the unique forming characteristics of these high-performance metals.
Another significant trend influencing custom machine development is sustainability. Many manufacturers are under pressure to reduce material waste, lower energy consumption, and increase overall manufacturing efficiency. As a result, custom metal spinning machines are increasingly incorporating energy-efficient drives, regenerative braking systems that recover energy during deceleration, and optimized tool paths that minimize scrap material. Some custom machines are designed to work with recycled metals or to facilitate easier recycling of offcuts and formed parts, aligning with broader corporate sustainability goals.
Moreover, the integration of artificial intelligence and machine learning into custom metal spinning machines is beginning to change how these machines operate. Smart systems can monitor vibrations, temperature, torque, and force feedback in real time, making automatic adjustments to optimize forming conditions. Over time, these systems learn the best process parameters for different materials and shapes, leading to better part quality, reduced setup times, and less dependency on highly skilled operators. Predictive maintenance features can also be built in, alerting operators before a potential breakdown occurs, thus minimizing unexpected downtime and extending machine life.
For applications requiring extremely tight tolerances, such as components for satellites or medical implants, the addition of in-process inspection and adaptive control technologies is becoming increasingly important. Custom machines can be fitted with laser scanning systems, ultrasonic sensors, or high-resolution cameras that inspect parts during the forming process. If a deviation from the desired geometry is detected, the machine can adjust tool pressure, spindle speed, or material feed rates instantly, maintaining consistency without stopping production. This closed-loop control approach is particularly valuable for industries where a single defect can lead to costly failures or rework.
Customization also extends into ergonomics and operator interface design. For shops where human-machine interaction is frequent, custom-built machines can include user-friendly features such as intuitive touchscreen controls, ergonomic loading and unloading positions, noise reduction measures, and enhanced lighting inside the working area. These improvements not only enhance operator comfort and safety but also improve productivity by making it easier to train new workers and reducing the likelihood of operator error.
In terms of physical machine layout, custom designs can be adapted to fit into limited factory spaces, or configured for specific workflows. Some custom metal spinning machines are designed with mobile bases or modular assemblies, allowing manufacturers to rearrange their production floors as needed. Others might feature dual-head setups or tandem arrangements, where two spindles work in parallel on the same part or on two different parts simultaneously, effectively doubling production capacity without doubling the factory footprint.
Globalization and the demand for just-in-time manufacturing also mean that many custom machines now include remote monitoring and support capabilities. Machine builders often offer remote diagnostics, where service engineers can log into the machine’s control system from anywhere in the world to troubleshoot problems, update software, or optimize performance settings. This reduces downtime dramatically and ensures that even highly specialized equipment remains operational without requiring lengthy service visits.
In the world of design, custom metal spinning machines open up new possibilities for architects, artists, and industrial designers who seek unique, large, or complex metal forms that are not feasible through traditional fabrication methods. Whether producing dramatic curved facades for buildings, creating artistic sculptures with flowing organic shapes, or fabricating limited-edition furniture pieces, custom machines allow for the realization of creative visions that would otherwise be impossible or prohibitively expensive.
The future potential for custom-made metal spinning machines appears boundless as advancements in digital manufacturing, smart automation, and materials science continue to converge. As industries become more demanding and product designs become increasingly intricate, the value of machines tailored precisely to their needs will only grow. The ability to seamlessly adapt a machine to new materials, new geometries, or new production volumes will provide manufacturers with a critical competitive edge. Thus, custom-made metal spinning machines will remain an essential cornerstone of modern advanced manufacturing, empowering innovation, enhancing quality, and enabling industries to meet the challenges of tomorrow.
Automated Metal Spinning Machine
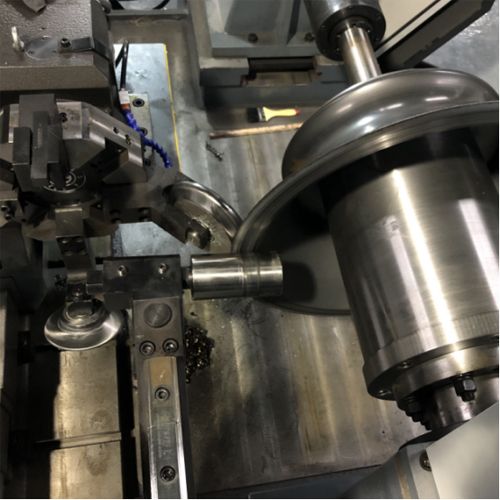
Automated metal spinning machines represent a major step forward in modern manufacturing, combining the traditional art of metal spinning with the precision and efficiency of automation technologies. These machines are designed to perform complex forming operations with minimal human intervention, making them ideal for high-volume production environments where consistency, speed, and quality are critical. By integrating CNC controls, servo motors, robotic handling systems, and advanced sensors, automated metal spinning machines can produce highly accurate parts while significantly reducing labor costs and production times.
At the heart of an automated metal spinning machine is a sophisticated CNC system that precisely controls the movement of the spinning roller and the workpiece. This allows for highly repeatable operations, even when producing intricate shapes or working with challenging materials. The CNC programming enables the machine to follow complex tool paths with a high degree of accuracy, ensuring that every part meets tight dimensional tolerances and surface finish requirements. Additionally, because the machine can be programmed to perform a sequence of forming operations automatically, it greatly reduces the need for skilled manual spinners and minimizes the risk of human error.
Robotic integration is another defining feature of automated metal spinning machines. Robotic arms can load raw blanks onto the spindle, remove finished parts, and even perform secondary operations such as trimming or inspection. This level of automation not only speeds up the production cycle but also improves workplace safety by reducing the need for operators to handle heavy or potentially hazardous materials directly. In many cases, multiple machines can be linked together into an automated production cell, with robots moving parts between different stations seamlessly, enabling lights-out manufacturing where the system runs continuously without human oversight.
Sensor technologies play a crucial role in enhancing the capabilities of automated spinning machines. Load sensors, torque monitors, temperature sensors, and optical scanners provide real-time feedback during the spinning process, allowing the machine to make instant adjustments to compensate for material variations or unexpected process disturbances. This adaptive capability leads to higher part quality and less scrap, even when working with difficult materials like high-strength alloys or variable-thickness blanks.
Automated metal spinning machines are highly versatile and can handle a wide range of applications, from producing small, thin-walled components for the electronics and aerospace industries to forming large, thick-walled parts for automotive, energy, and construction sectors. Machines can be configured for conventional spinning, shear forming, flow forming, or a combination of these processes, depending on the requirements of the part being manufactured. Additionally, automated systems can be designed to work with both cold and hot spinning processes, with integrated heating solutions such as induction heaters or gas burners that bring the material to the required forming temperature automatically during the production cycle.
One of the key benefits of automation in metal spinning is the ability to maintain consistent quality across large production runs. Automated machines can produce thousands of identical parts with little to no variation, which is crucial for industries where part-to-part consistency is mandatory. Furthermore, automated quality control systems can be incorporated, using vision systems or laser measurement devices to inspect parts immediately after forming. Any part that falls outside of preset tolerances can be flagged for rework or rejected automatically, further improving overall production efficiency.
Modern automated metal spinning machines also offer exceptional flexibility. Quick-change tooling systems and modular machine designs allow manufacturers to switch between different product types with minimal downtime. In many cases, tool changes can be completed automatically by the machine itself, using an integrated tool changer that selects and installs the correct roller or forming tool based on the CNC program. This flexibility is essential for manufacturers serving multiple industries or dealing with frequently changing customer demands.
Energy efficiency is another advantage of automated spinning systems. Advanced drive technologies, regenerative braking, and optimized process planning help reduce the energy consumption per part, which not only lowers operating costs but also supports broader environmental sustainability goals. Some automated machines are even equipped with energy monitoring systems that track usage in real time, allowing operators and plant managers to identify opportunities for further efficiency improvements.
As industries continue to move toward greater automation and digitalization, the role of automated metal spinning machines will become even more important. Integration with Industry 4.0 technologies — including IoT connectivity, cloud-based data analytics, and smart factory management systems — enables manufacturers to monitor machine performance remotely, predict maintenance needs, and continuously optimize production schedules based on real-time data. These capabilities help ensure that manufacturing operations remain agile, efficient, and competitive in an increasingly demanding global market.
In summary, automated metal spinning machines represent a powerful fusion of traditional metal forming expertise and cutting-edge automation technology. They enable manufacturers to achieve higher productivity, better quality, greater flexibility, and improved cost-effectiveness, all while maintaining the ability to produce complex, high-precision components across a wide range of industries. As automation technologies continue to evolve, the capabilities of these machines will only expand further, solidifying their place as an essential tool in the future of advanced manufacturing.
The advancement of automated metal spinning machines is not solely limited to improvements in mechanical and control technologies; it is also being influenced by a shift in how manufacturing systems are conceptualized. With the growing acceptance of fully automated and autonomous production lines, metal spinning machines are increasingly being designed as intelligent nodes within larger smart factory ecosystems. This means that these machines are no longer operating as isolated units but as interconnected parts of a data-driven network where real-time communication between machines, production management systems, and enterprise resource planning software enables seamless production optimization.
In these environments, automated metal spinning machines collect vast amounts of operational data, including spindle speeds, forming forces, tool wear rates, and production cycle times. This data is then processed by machine learning algorithms to optimize forming strategies, predict maintenance intervals, and even recommend design modifications to improve manufacturability. For example, if a slight change in material behavior is detected during spinning, the machine can automatically adjust the process parameters to maintain part quality without interrupting production. Over time, these self-optimizing capabilities lead to continuous process improvements without direct human intervention.
Another emerging area within automated spinning systems is the application of digital twin technology. A digital twin is a real-time virtual replica of the spinning machine and its processes, allowing manufacturers to simulate operations, predict outcomes, and test new part designs before actual production begins. By using a digital twin, companies can optimize tool paths, forecast material deformation, and even predict surface finishes, all within a virtual environment. This reduces the need for physical prototyping, cuts development costs, and significantly accelerates the time to market for new products.
Safety and ergonomics have also been revolutionized through automation. Automated metal spinning machines are designed with advanced safety systems that include interlocked doors, laser light curtains, and emergency stop circuits that react instantly to protect operators. Because the operator’s role shifts more toward programming, monitoring, and quality assurance, exposure to hazards such as flying debris, sharp edges, or intense heat is minimized. This not only improves overall workplace safety but also makes spinning operations more attractive to a broader range of workers, addressing the skills gap that many manufacturing sectors are currently facing.
The use of composite materials and hybrid metal structures in industries like aerospace and automotive has further expanded the requirements for automated metal spinning machines. Traditional machines, optimized primarily for metals like aluminum, mild steel, and copper, are now being adapted to handle materials with significantly different mechanical properties. Automated systems can be equipped with customized tooling, sophisticated heating and cooling controls, and adaptive forming strategies to spin complex composite-metal hybrid parts, which are increasingly used to achieve lighter, stronger, and more fuel-efficient products.
In addition, the aesthetic possibilities opened by automated spinning have captured the attention of industries focused on design, such as architecture, lighting, and luxury consumer goods. Metal spinning allows the creation of seamless, flowing shapes with minimal joints, and automation ensures that these forms can be replicated perfectly at scale. Designers are no longer constrained by the limitations of manual forming techniques and can now create bold, imaginative shapes that are both structurally sound and visually striking. Automation allows the consistent production of these complex designs with surface finishes that require minimal post-processing, thanks to precise control over tool pressure and forming speed.
As the demand for customization continues to grow, the concept of mass customization has become achievable with automated metal spinning machines. Unlike traditional manufacturing methods that require costly, inflexible tooling for each new design, automated spinning setups can switch between different product geometries rapidly by reprogramming the CNC system and changing tooling with minimal downtime. This enables manufacturers to offer bespoke products tailored to individual customer requirements without sacrificing the economies of scale associated with mass production.
Looking to the future, it is expected that artificial intelligence will play an even greater role in automated metal spinning. Future machines may not just react to problems in real time but anticipate them hours or even days in advance, ordering spare parts automatically, scheduling downtime for maintenance, or rerouting production tasks to other machines when necessary. Machine-to-machine communication will enable spinning machines to coordinate directly with downstream processes like welding, heat treating, and final assembly, creating truly integrated manufacturing systems capable of producing complex assemblies with minimal human intervention.
Thus, the automated metal spinning machine stands as more than just a piece of production equipment; it represents a strategic asset in the move toward fully automated, highly flexible, and data-driven manufacturing. It embodies the shift toward smarter, more efficient, and more resilient production processes capable of adapting dynamically to changes in demand, material availability, and technological innovation. In doing so, automated metal spinning continues to preserve the essence of one of the oldest metal forming techniques while redefining its role within the future landscape of global manufacturing.
The pace of technological advancement in automated metal spinning machines is driving entirely new manufacturing strategies where scalability, precision, and responsiveness to market needs are paramount. Factories equipped with advanced spinning automation are no longer tied to rigid production schedules; instead, they operate with high flexibility, capable of switching between different product lines almost instantaneously based on real-time market demands or urgent customer orders. This on-demand production capability gives manufacturers a huge competitive advantage, particularly in industries where lead time and customization can be the deciding factors between winning and losing business.
Moreover, automated metal spinning is increasingly converging with additive manufacturing technologies. Some experimental setups are exploring hybrid systems where metal spinning is combined with directed energy deposition or wire arc additive manufacturing, allowing parts to be partially built up through 3D printing techniques and then precisely formed to final geometry through spinning. This hybrid approach could dramatically reduce material waste, open up new design possibilities, and further decrease production times for complex components.
Another area where automation is expanding the boundaries of metal spinning is in quality certification and traceability. Industries like aerospace, medical, and defense require rigorous documentation proving that each manufactured part meets exacting standards. Automated systems can now generate a complete digital thread for each component, recording every process parameter — from forming force to temperature curves to spindle speed — and linking that data to the final product. This not only simplifies compliance with industry regulations but also enhances customer confidence and reduces liability risks.
Environmental sustainability is becoming a critical driver in the design of the next generation of automated spinning machines. Manufacturers are under increasing pressure to lower their carbon footprints, and metal spinning is inherently more material-efficient compared to machining, casting, or stamping. Automated systems magnify this advantage by optimizing material usage even further, ensuring minimal excess thickness and tighter control of part geometry. Furthermore, energy-efficient motor systems, optimized tool paths, and smart cooling systems are reducing energy consumption per part, supporting the transition to greener manufacturing practices.
Workforce dynamics are also evolving in the age of automated spinning. Rather than eliminating jobs, automation is shifting the skill sets required. Operators are being retrained as machine programmers, maintenance technicians, and process analysts. This transition not only makes the manufacturing workforce more resilient and adaptable but also creates new career pathways in an industry that has long struggled to attract young talent. Automated spinning systems are often equipped with user-friendly interfaces and augmented reality-based maintenance guides, making it easier for new personnel to become productive with less training time.
Market globalization is further fueling innovation. As companies look to localize production to be closer to end users and reduce logistics costs, the ability to rapidly set up, adapt, and scale automated spinning operations becomes crucial. Portable, modular spinning cells are emerging, designed for rapid deployment in diverse geographical locations. These self-contained units include integrated automation, tooling libraries, and digital control hubs, allowing companies to establish or expand production capabilities almost anywhere with minimal infrastructure requirements.
Even the basic physics of spinning is being pushed into new territories. Research into controlled vibration-assisted spinning, ultrasonic energy-enhanced spinning, and superplastic spinning at relatively low temperatures promises to unlock the ability to form ultra-high strength metals and novel composites that have previously been impractical or impossible to spin with conventional techniques. Automated systems can precisely coordinate the timing, amplitude, and frequency of these enhancements with the spinning process, opening up a whole new class of parts and materials for advanced applications.
As the digital transformation of manufacturing accelerates, the synergy between automated metal spinning machines and cloud-based manufacturing execution systems will deepen. Real-time dashboards displaying production metrics, predictive maintenance alerts, machine learning-driven process recommendations, and live quality control updates will become standard features. Factory managers and engineers will have unprecedented visibility into and control over their spinning operations, from individual part status to fleet-wide equipment health, accessible from anywhere in the world.
In essence, automated metal spinning machines are at the forefront of the industrial transformation that blends time-honored craftsmanship with futuristic technologies. They are poised not only to redefine how metal components are formed but also to influence broader manufacturing paradigms, driving industries toward greater agility, sustainability, and innovation. Their continued evolution will ensure that metal spinning — one of the oldest known manufacturing techniques — remains a vital and dynamic force in shaping the engineered products of the future.
Hot Metal Spinning Machine
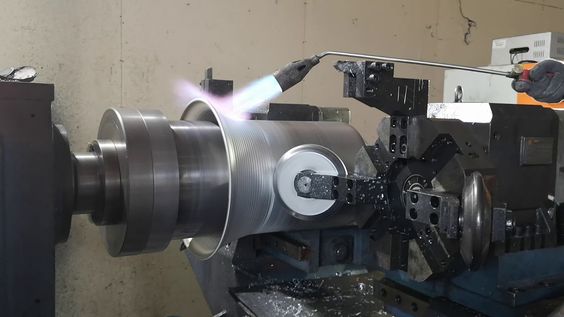
Hot metal spinning machines are specialized systems designed to form metals at elevated temperatures, allowing for greater ductility and reduced forming forces compared to cold spinning. In hot metal spinning, the workpiece — typically a thick, hard, or otherwise difficult-to-form metal — is heated to a temperature where it becomes significantly more malleable without reaching its melting point. This enables the production of complex shapes, heavy-duty parts, and high-performance components that would otherwise be impossible or highly impractical to spin using conventional cold methods.
The basic design of a hot metal spinning machine shares many similarities with a standard spinning lathe, but it is heavily modified to withstand and manage the intense thermal environment. Heat sources such as gas torches, induction coils, or resistance heaters are integrated into the machine, either mounted on adjustable arms or fixed around the work zone. These heating systems provide localized or full-piece heating, depending on the material and the forming requirements. Advanced temperature control systems monitor the heat in real time to maintain consistent conditions, which is crucial to avoid overheating, oxidation, or thermal stresses that could compromise the part’s structural integrity.
Hot spinning dramatically changes the material behavior during forming. Metals such as titanium, Inconel, stainless steels, and other high-strength alloys that exhibit very limited plasticity at room temperature become much more workable when heated. This expanded ductility reduces the risk of cracking, tearing, or excessive thinning during spinning, making it possible to create deeper, sharper, or more intricate forms. In many cases, the spun part achieves mechanical properties superior to those created by other forming methods, as the process can refine grain structures and enhance material strength through controlled deformation and thermal cycling.
Because the workpiece is hot, the rollers used in hot metal spinning machines are specially selected or coated to withstand high temperatures without degrading. Common roller materials include tool steels with high heat resistance, ceramics, or surface-treated alloys. Cooling systems may be integrated into the roller mounts to prolong tool life and maintain dimensional stability during operation. In some cases, the roller itself is preheated to minimize thermal shock and improve surface finish on the workpiece.
The control systems for hot metal spinning machines must also be adapted to handle the complexities introduced by temperature variation. Thermal expansion of the workpiece must be compensated for during forming, meaning that positioning systems must be precise and responsive. CNC-driven machines dominate the hot spinning sector, offering programmable control over spindle speed, roller force, feed rate, and heating parameters. These capabilities allow for the precise execution of complex spin profiles, multi-pass forming sequences, and variable-thickness wall designs.
Hot metal spinning opens up a wide range of applications across industries that demand parts with high strength-to-weight ratios, excellent thermal resistance, and superior fatigue properties. Aerospace applications are among the most prominent, with hot spinning used to manufacture engine components like cones, nozzles, and casings. In the energy sector, hot spinning is used for producing heavy-duty parts for gas turbines, pressure vessels, and nuclear containment systems. Automotive manufacturers use hot spinning to create specialized components like turbocharger housings and performance exhaust parts where high-temperature durability is essential.
Another significant advantage of hot metal spinning is material savings. Unlike machining, where material is cut away and wasted, spinning reshapes the original blank with minimal waste. For expensive materials like titanium or nickel-based superalloys, the ability to form parts close to their final shape without excessive machining represents substantial cost savings. This efficiency, combined with improved mechanical performance, makes hot spinning an attractive option for manufacturers dealing with high-value materials.
The development of simulation tools and forming models has greatly aided the advancement of hot spinning technology. Modern software allows engineers to model temperature distributions, stress fields, and material flow in the part during spinning, optimizing parameters before production begins. This predictive capability reduces trial-and-error experimentation, lowers development costs, and shortens time to production.
Despite its advantages, hot metal spinning requires careful process control and operator expertise, especially when transitioning between different materials or part geometries. Thermal management is critical, as uneven heating can lead to defects such as warping, surface oxidation, or undesirable microstructural changes. Protective atmospheres, such as inert gas shielding, may be used for particularly reactive materials like titanium to prevent surface contamination during heating and spinning.
The future of hot metal spinning machines is moving toward even greater levels of automation and intelligence. Machines capable of adaptive temperature control, real-time force feedback, and in-process quality monitoring are becoming more common. These advancements aim to make hot spinning as predictable, repeatable, and scalable as conventional cold spinning, but with the added benefit of forming the most demanding materials into ever more complex and high-performance shapes. In this way, hot metal spinning is expanding the frontiers of what can be achieved in metal forming technology, playing a critical role in the next generation of engineered components.
As the demand for lightweight, high-strength components continues to rise across industries like aerospace, defense, and energy, the role of hot metal spinning machines is becoming even more vital. One of the key factors driving this expansion is the increasing reliance on difficult-to-form materials such as titanium alloys, Inconel, and other nickel-based superalloys, all of which perform exceptionally well under extreme temperature and stress conditions but are notoriously hard to shape by traditional methods. Hot spinning offers a solution by enabling these challenging materials to be formed into complex geometries without compromising their mechanical integrity or surface quality.
Modern hot metal spinning machines are being designed with fully integrated systems that manage not only the forming operation but also the preheating and cooling cycles of the material. This allows the entire thermal process to be controlled precisely, ensuring that each stage — from initial heating through forming to final cooling — is optimized for the specific material being processed. Some machines use dynamic heating systems that adjust the intensity and distribution of heat based on real-time feedback from infrared sensors, ensuring uniform temperature across the workpiece, which is critical for maintaining consistent material properties and avoiding localized defects.
The introduction of robotic arms and automated handling systems is further transforming hot metal spinning operations. These robots can load blanks, adjust tooling, and even reposition parts during multi-stage spinning operations, reducing the need for human intervention in high-temperature environments. This not only improves safety but also increases the speed and repeatability of the manufacturing process. In some systems, collaborative robots equipped with heat-resistant end effectors work alongside human operators, assisting with tasks like precise part placement or auxiliary heating operations, blending the flexibility of human decision-making with the consistency of automation.
Another exciting frontier in hot metal spinning is the application of process monitoring and machine learning. By continuously analyzing data such as forming forces, spindle torque, roller position, material temperature, and part shape, advanced software algorithms can predict potential defects before they occur, adjusting parameters on the fly to correct issues. Over time, these systems “learn” the optimal conditions for spinning specific alloys or shapes, dramatically improving yield rates and reducing waste. Some systems even simulate thousands of variations digitally before ever beginning physical production, arriving at the best strategy based on virtual testing.
Surface engineering has also become an important aspect of hot spinning technology. Specialized roller coatings, including thermal barrier layers and anti-galling treatments, are being developed to improve the surface finish of hot-spun parts and extend the life of the tooling. For parts that require extremely high surface quality — such as reflectors, aerospace fairings, or medical equipment — these innovations allow hot spinning to achieve finishes that previously required extensive post-processing.
In large-scale applications, hot metal spinning machines capable of handling extremely heavy blanks — sometimes weighing several tons — have been engineered with massive reinforced frames, multi-motor drive systems, and synchronized roller assemblies. These machines produce large-diameter parts like rocket nozzles, wind turbine hubs, and pressure vessel domes, where traditional fabrication methods would involve complex welding, leading to potential weak points. Hot spinning such components from a single blank eliminates welds, resulting in a part with continuous grain structure and superior mechanical performance.
Meanwhile, sustainability is becoming a central theme in the development of hot spinning technologies. Energy recovery systems that capture and reuse waste heat from the spinning process are being introduced to lower the overall energy footprint. Water-based cooling systems and environmentally friendly lubrication methods are replacing older systems that relied on hazardous materials, aligning spinning operations with modern environmental regulations and corporate sustainability goals.
Customization is another major trend. Machine builders are offering modular designs where heating systems, roller configurations, control packages, and automation modules can be tailored to specific customer needs. This flexibility allows manufacturers to create spinning solutions for niche applications, from boutique aerospace parts to artisanal architectural elements, without the cost and complexity typically associated with bespoke machinery.
Looking forward, the integration of artificial intelligence, digital twins, and predictive maintenance platforms will continue to redefine the capabilities of hot metal spinning machines. These innovations will allow manufacturers to run entire spinning cells autonomously, schedule maintenance before failures occur, and simulate the complete lifecycle of a part — from raw blank to final installation — all from a centralized digital command center. As these systems evolve, the traditional boundaries between forming, machining, and additive manufacturing will continue to blur, leading to entirely new manufacturing methods where spinning plays a central, dynamic role in shaping the future of metal fabrication.
At the cutting edge of research and industrial development, hybrid systems that combine hot metal spinning with real-time material property modification are beginning to emerge. These systems not only form the material but also actively alter its microstructure during the spinning process. For instance, by carefully controlling the temperature gradients and deformation rates, it is possible to induce beneficial grain refinements, texture orientations, and even phase transformations within the metal, producing parts that are stronger, tougher, or more corrosion-resistant than those produced by traditional means. This concept, sometimes referred to as “integrated thermo-mechanical processing,” elevates hot spinning from a purely shaping operation to a simultaneous forming and enhancing technology.
This capability is particularly valuable in the aerospace and defense sectors, where performance demands often push materials to their limits. For example, turbine engine components that experience extreme thermal cycling benefit from a fine, stable grain structure that can be engineered directly during spinning, eliminating the need for separate heat treatments or complex forging operations. By integrating microstructural control into the forming process itself, manufacturers reduce costs, production times, and potential sources of error.
Another emerging innovation is the use of advanced materials for tooling and machine components exposed to extreme conditions. Developments in high-entropy alloys, ceramics, and carbon-carbon composites are enabling the design of rollers, mandrels, and fixtures that can withstand higher temperatures and stresses without deformation or wear. This means hot metal spinning machines can operate at even higher process temperatures, expanding the range of metals that can be spun effectively and improving part quality at the same time.
In terms of machine architecture, future hot spinning systems are moving toward highly modular, reconfigurable platforms. A single base machine may support multiple heating methods — such as switching between gas flame, induction, or infrared heating — depending on the part material and geometry. Roller heads and mandrels can be swapped out robotically, enabling one machine to produce an array of part sizes and designs with minimal downtime. Machine intelligence automatically adjusts not just spinning parameters, but also thermal profiles, tool geometries, and motion paths, turning each setup into a fully customized operation without extensive reprogramming.
Digital twin technology is becoming especially significant in the hot metal spinning world. By creating a fully detailed virtual model of the machine, the tooling, the blank, and the forming process, manufacturers can simulate the complete operation before the first piece of metal is ever loaded. This allows optimization of heating cycles, spinning strategies, and final part properties with incredible precision. As parts are spun, data from sensors embedded throughout the machine feeds back into the digital twin, continuously refining its accuracy. This creates a closed-loop system where the physical and digital versions of the process learn and improve together, enabling greater consistency and efficiency.
Moreover, the focus on operational safety is driving important advancements. Hot metal spinning inherently involves high temperatures, moving parts, and heavy loads, but modern safety systems are now deeply integrated into machine designs. Laser-based safety curtains, real-time temperature mapping with thermal cameras, emergency braking systems, and predictive alerts about thermal deformation risks ensure that operators and maintenance personnel can work safely even in demanding conditions. Some setups employ remote operation stations, allowing human oversight while keeping personnel at a safe distance from the hot zone.
Sustainability considerations are also influencing material choices and process design. Lightweight, high-efficiency insulation materials are being used to retain heat around the spinning zone, minimizing energy loss. Smart heating systems precisely target only the necessary areas of the blank, drastically cutting gas or electricity consumption. And because hot spinning typically requires fewer secondary operations like welding, grinding, and heat treatment, the overall carbon footprint of producing a spun part is significantly lower compared to traditional metalworking methods.
Applications for hot spun components continue to diversify. Beyond aerospace and energy, industries such as biomedical, architecture, and advanced transportation are recognizing the benefits of hot-spun parts. Biomedical implants made from hot-spun titanium alloys offer superior strength and bio-compatibility. Architectural elements spun from stainless steel or copper alloys provide both beauty and durability. Electric vehicle manufacturers use hot-spun aluminum components to create lightweight, high-strength structural elements critical to extending battery range and improving safety.
In the near future, it’s likely that hot metal spinning will become an integral part of highly flexible, decentralized manufacturing networks. Instead of centralized mega-factories, smaller regional production hubs equipped with advanced hot spinning capabilities will be able to rapidly produce customized parts locally, reducing transportation costs and supply chain vulnerabilities. These agile factories will be connected digitally, sharing process improvements, real-time production data, and quality control metrics across a global network, making metal manufacturing faster, smarter, and more sustainable than ever before.
All of these developments point to a future where hot metal spinning is not merely a niche or specialty process but a foundational technology in modern manufacturing, enabling innovations in design, performance, and efficiency across a wide array of industries and applications.
Cold Metal Spinning Machine
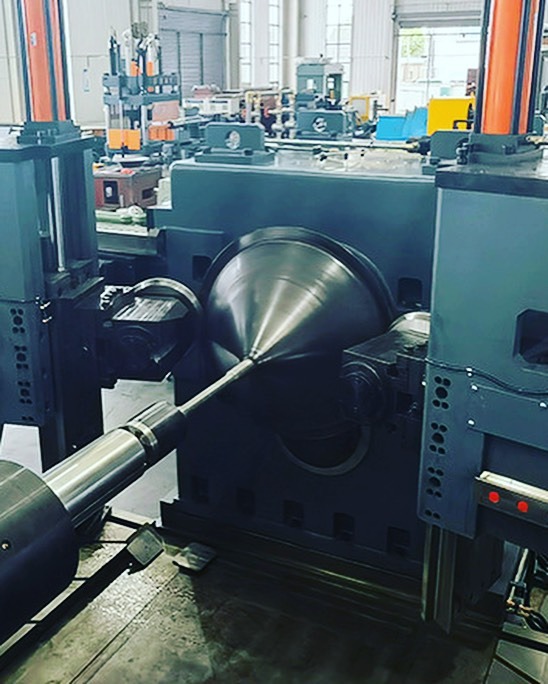
Cold metal spinning machines are designed to form metal workpieces at or near room temperature, relying purely on mechanical force rather than elevated temperatures to reshape the material. In cold spinning, a flat blank or preformed shape is mounted onto a mandrel and rotated at high speeds while rollers or tools apply localized pressure, gradually shaping the metal into a seamless, precise, and often complex geometry. The absence of high-temperature heating distinguishes cold spinning from hot spinning, resulting in a process that preserves the metal’s original material properties while enhancing certain mechanical characteristics like strength and hardness through work hardening.
The basic structure of a cold metal spinning machine is similar to a heavy-duty lathe, equipped with a robust spindle drive system to rotate the workpiece, and a carriage or turret that holds the spinning rollers. These rollers, often made from hardened steel or carbide, are meticulously shaped to suit specific forming operations. Some machines are manually operated, particularly for small-scale or artisanal production, while the majority of modern cold spinning machines use CNC control systems to manage roller movement, force application, feed rates, and rotational speeds with exceptional precision.
One of the major advantages of cold metal spinning is the ability to produce strong, high-quality parts without the need for additional heat treatment. The mechanical deformation involved in the process refines the grain structure of the metal, leading to improved tensile strength, fatigue resistance, and surface finish. This makes cold-spun parts highly desirable for industries where lightweight strength and reliability are critical, such as aerospace, defense, automotive, and medical manufacturing.
Since the material is not softened by heating, cold spinning typically requires higher forming forces compared to hot spinning. As a result, both the machine and the tooling must be designed to withstand significant stresses. Workpieces are often lubricated during the process to reduce friction between the roller and the material, prevent surface galling, and control the heat generated by deformation. Specialized lubricants tailored to specific metals like aluminum, steel, or copper are used to optimize performance and protect surface quality.
Cold metal spinning is ideally suited for ductile metals and alloys, such as aluminum, copper, mild steel, brass, and certain grades of stainless steel. The thickness of the starting material is an important factor: if the metal is too thick or too hard, the spinning forces required may exceed practical machine limits, or the material may crack or tear. In such cases, intermediate annealing steps or a shift to hot spinning may be necessary. However, for suitable materials and thicknesses, cold spinning can achieve excellent dimensional accuracy, tight tolerances, and complex contours with minimal material waste.
Tooling setup in cold metal spinning is typically quicker and less expensive than in other metal forming processes like deep drawing or stamping. Mandrels can be made from relatively inexpensive materials, such as mild steel or even wood for certain prototypes, because they mainly serve as a form rather than enduring full mechanical loads. Production runs can be easily adapted by changing the mandrel or modifying the roller path, making cold spinning an economical choice for both small-batch and medium-volume production runs.
Another key benefit of cold spinning is the production of seamless parts. Unlike welding or assembly operations that join multiple pieces of metal together, cold spinning shapes a single piece of material into the desired form without introducing seams, welds, or joints that could become failure points under stress. This integrity is especially valuable in applications like pressure vessels, rocket nose cones, gas cylinders, and fluid handling systems, where leaks, fractures, or weak points are unacceptable.
CNC cold metal spinning machines offer advanced capabilities like variable wall thickness control, complex multi-contour shaping, and integration with robotic systems for automatic loading and unloading. Some machines are equipped with multi-axis heads that allow for spinning combined with additional operations like beading, flanging, curling, and trimming, enabling the production of highly finished parts directly from the spinning machine without secondary processing.
Process monitoring and feedback systems are increasingly common in cold spinning setups. Sensors can track forming forces, roller position, part temperature, and spindle torque in real time, providing operators or the CNC system with data to adjust parameters dynamically and maintain consistent part quality. This is particularly important when dealing with sensitive materials where variations in material batch properties could otherwise lead to inconsistencies.
Sustainability is another strong point for cold metal spinning. Since it does not require large furnaces or gas heating systems, it consumes significantly less energy compared to hot forming processes. The low material waste and long tool life also contribute to the overall environmental friendliness of the process. Additionally, because cold-spun parts often require little to no machining afterward, there is less scrap generation and reduced use of coolants and cutting fluids.
Cold metal spinning continues to evolve alongside advances in material science, CNC programming, and machine design. Innovations like servo-controlled roller systems, adaptive path planning based on part feedback, and AI-driven quality assurance are pushing the boundaries of what can be achieved through cold spinning. As new materials, designs, and application demands emerge, cold metal spinning remains a versatile, efficient, and highly valuable technology in the modern manufacturing world.
Modern cold metal spinning technology is increasingly moving toward fully integrated production cells where spinning, trimming, measuring, and even non-destructive testing occur without ever removing the part from the spindle. This approach maximizes throughput and ensures that every part meets exacting quality standards immediately after forming. Inline laser scanning systems map the finished surface in three dimensions, comparing the actual geometry against the digital design in real time. If deviations are detected, automatic corrections are applied to subsequent parts, fine-tuning tool paths and roller pressures dynamically. This closed-loop manufacturing environment is especially important in industries like aerospace and medical device manufacturing, where consistency and traceability are crucial.
As machine builders push the capabilities of cold spinning, new materials that were once considered too brittle or hard for cold forming are being processed successfully thanks to better control over deformation rates, tool profiles, and material handling. Advanced aluminum-lithium alloys, high-strength low-alloy steels, and even certain grades of titanium are now within reach of cold spinning techniques, opening new possibilities for structural applications that demand both strength and lightweight properties. Specialized tooling materials, such as nano-grain carbide rollers and surface-treated mandrels, are helping extend tool life and improve part finish when working with these challenging metals.
Automation is a major driving force in cold spinning advancements. High-speed robotic arms equipped with vision systems are used not only to load and unload blanks but also to position pre-formed shells for multi-stage spinning operations. In some high-end facilities, fully autonomous spinning lines operate continuously, producing complex parts with minimal human oversight. These lines are monitored remotely through IIoT (Industrial Internet of Things) platforms, which collect and analyze massive amounts of data on machine health, process stability, and part quality, allowing for predictive maintenance and production optimization on a scale that was unthinkable just a few years ago.
Energy efficiency remains a strong selling point for cold spinning. As industries work toward carbon-neutral production goals, processes like cold spinning, which use mechanical energy rather than thermal energy, are increasingly favored. Some modern cold spinning machines incorporate regenerative braking systems that recover energy when the spindle decelerates, feeding it back into the system and reducing overall power consumption. Machine frames are now optimized through finite element analysis to minimize mass while maximizing rigidity, further improving energy efficiency and precision.
Another exciting area of development is the coupling of cold spinning with additive manufacturing technologies. In experimental setups, near-net-shape metal parts produced by methods like wire arc additive manufacturing (WAAM) or laser powder bed fusion are finished by cold spinning to achieve final dimensional accuracy and surface finish. This hybrid approach combines the design freedom of 3D printing with the material performance enhancements of cold forming, enabling the creation of parts that are both highly complex and mechanically robust.
Customization continues to be a hallmark of cold spinning systems. Machines are often built to match specific part families, with modular spindle drives, adjustable tailstocks, multiple tool turrets, and interchangeable workholding solutions. For industries like lighting, furniture, and decorative architecture, where design changes frequently, this flexibility allows manufacturers to respond quickly to new trends and customer demands without the need for major retooling or investment.
Cold spinning is also benefiting from a deeper understanding of metallurgical behavior under room-temperature deformation. Sophisticated simulation tools now model not just the shape change but also the evolution of microstructure, residual stresses, and potential defect formation during spinning. This enables engineers to design spinning processes that achieve not only the correct geometry but also the desired internal properties of the part. For instance, tailoring the spinning path and roller pressure can create regions of intentionally higher strength in areas subject to greater load, all within a single continuous forming operation.
Despite all these technical advancements, the essence of cold metal spinning remains rooted in craftsmanship and precision. Highly skilled operators and programmers work alongside machines to fine-tune processes, adapting to subtle differences in material behavior, tooling wear, and machine dynamics that no sensor or algorithm can yet fully predict. This blend of human expertise and technological innovation continues to define cold metal spinning as one of the most refined and versatile forming methods in the world of metal fabrication, ready to meet the evolving challenges of modern manufacturing.
As cold metal spinning technology progresses, its applications continue to expand into new sectors, with industries exploring innovative uses for this process that were previously unimaginable. For example, in the field of medical manufacturing, cold-spun components such as surgical instruments, orthopedic implants, and custom prosthetics are becoming increasingly common due to the precision, strength, and seamless qualities the process provides. Cold spinning’s ability to produce high-performance parts without the risk of heat-affected zones — critical in the case of sensitive materials like titanium — makes it a prime candidate for producing medical-grade components with tight tolerances and complex geometries.
Similarly, cold metal spinning is gaining traction in the renewable energy sector, particularly for producing specialized components for wind turbines, solar concentrators, and energy storage systems. The lightweight and strong properties achieved through cold spinning make it ideal for forming large, thin-walled components like turbine hubs and casings, which are subjected to extreme mechanical and environmental stresses. Additionally, the process minimizes material waste, which aligns with the sustainable design principles increasingly adopted by the renewable energy industry.
The automotive sector, too, has embraced cold metal spinning, particularly for creating high-strength, lightweight parts that contribute to vehicle fuel efficiency and performance. Cold-spun components like wheel rims, heat shields, and structural housings are more durable and offer superior surface finishes compared to parts made by traditional stamping or casting methods. Moreover, with an increasing emphasis on electric vehicles (EVs), cold metal spinning is well-suited for producing lighter and more efficient battery casings, as well as various components used in electric motors and drivetrains. The ability to tailor metal properties and reduce the number of processing steps enhances the speed and flexibility needed to meet the growing demand for electric vehicles.
In aerospace manufacturing, the ability to form complex, large-diameter parts like jet engine casings, nacelle components, and spacecraft parts through cold spinning has proven invaluable. Cold-spun parts offer superior structural integrity and are more cost-effective than alternatives, such as casting or forging. By avoiding the need for high-temperature treatments, cold spinning preserves the original properties of high-performance alloys, ensuring they remain suitable for the extreme conditions encountered in aerospace applications.
Moreover, cold metal spinning technology is beginning to see adoption in the defense industry for producing parts that require both precision and resilience under harsh operating conditions. Components such as armored vehicle parts, radar casings, and specialized military equipment benefit from the combination of high-strength materials and the custom geometries achievable with cold spinning. The process also allows for the production of lightweight, strong, and seamless parts that can withstand high-impact forces and thermal stresses.
The environmental impact of cold spinning is further minimized through innovations in waste management and recycling systems. Advances in automated sorting, cleaning, and reusing metal scrap have made it possible to capture and repurpose nearly all of the waste generated during the cold spinning process. Systems that collect and reprocess swarf (metal chips) allow manufacturers to recycle the material for future production, reducing reliance on raw materials and promoting a more circular manufacturing model.
Additionally, as the demand for custom and small-batch production increases, cold metal spinning is well-positioned to serve niche markets that require highly specialized components. These might include custom parts for the luxury goods industry, high-end audio equipment, bespoke jewelry, and even art installations. The precision and flexibility of the cold spinning process, coupled with the ability to work with a wide range of metals and alloys, provide manufacturers with the tools they need to create unique, high-quality items with low overhead costs and reduced lead times.
In terms of technology integration, cold spinning machines are becoming increasingly interconnected. The rise of Industry 4.0 principles — involving smart factories, the Internet of Things (IoT), and data-driven manufacturing — has introduced new possibilities for cold metal spinning. Machines equipped with advanced sensors and connected to cloud-based platforms provide real-time performance metrics and diagnostics, enabling predictive maintenance and ensuring the machines operate at peak efficiency. These systems also allow for remote monitoring and control, providing flexibility and reducing downtime. Some facilities even employ augmented reality (AR) tools to help operators visualize and adjust the process parameters in real-time, making it easier to troubleshoot problems and make adjustments on the fly.
The future of cold metal spinning is likely to see even further integration with other advanced manufacturing techniques. For instance, hybrid processes that combine cold metal spinning with laser cutting or additive manufacturing techniques could open up entirely new possibilities for producing intricate components with both complex geometries and fine surface finishes. Moreover, the ongoing evolution of machine learning and artificial intelligence could lead to even more sophisticated systems that can optimize the spinning process autonomously, learning from past operations to improve future performance.
The continuous advancement of materials science will also play a crucial role in shaping the future of cold metal spinning. As new, high-performance alloys and composites are developed, cold spinning will evolve to accommodate these materials, enabling the production of parts with properties that were once impossible to achieve through traditional forming processes. Additionally, innovations in tool coatings, like diamond-like carbon (DLC) or nano-structured materials, will further improve the wear resistance and performance of tooling, leading to longer lifespans and lower maintenance costs for machines.
With advancements in materials, automation, data analytics, and process optimization, cold metal spinning is poised to become an even more integral part of modern manufacturing. As industries continue to push the boundaries of design and performance, cold spinning offers a reliable, efficient, and sustainable way to produce high-quality, high-strength parts with complex shapes and tight tolerances. The process’s versatility ensures that it will remain a key manufacturing technology, meeting the challenges of tomorrow’s industries while contributing to the global push for more sustainable and efficient production methods.
Double-Cylinder Metal Spinning Machine
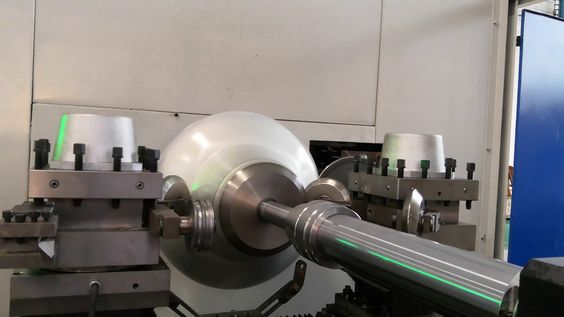
A double-cylinder metal spinning machine is a specialized type of metal spinning machine that utilizes two rotating cylinders or spindles to create symmetrical or complex parts with enhanced precision and control. This type of machine is particularly useful in manufacturing large-diameter, high-precision components, and is commonly employed in industries like aerospace, automotive, and defense, where strong, lightweight, and complex parts are needed.
The basic concept behind a double-cylinder spinning machine is to allow two spindles to work in tandem, each controlling a different aspect of the forming process. This can improve the overall control of material flow, increase the speed of production, and allow for a more consistent and uniform product. The two cylinders generally rotate in opposite directions or at varying speeds, providing a balanced, precise control over the deformation of the material.
The machine’s design often includes a rotating workpiece mounted between two spindles, with each spindle typically controlling specific axes of motion or forces applied to the material. The material, usually a metal blank, is placed on a mandrel, and the spindles apply force through rotating tools, progressively shaping the metal into the desired form.
Key Features of a Double-Cylinder Metal Spinning Machine:
- Two Independent Cylinders: The dual-spindle design provides enhanced precision and the ability to produce more complex shapes. Each spindle may be responsible for different operations, such as one for the rotational motion and the other for axial movements or forming the metal along a specific axis.
- Enhanced Material Control: The dual-axis setup allows for better control over the material’s flow during the spinning process. The forces applied by the two cylinders can be precisely adjusted to minimize defects like wrinkling or thinning, resulting in higher-quality finished products.
- High Precision: The double-cylinder setup allows for finer control of the shaping process, making it ideal for parts that require high dimensional accuracy and consistency. This is particularly important in industries like aerospace, where component integrity and exacting tolerances are essential.
- Improved Surface Finish: The additional control provided by two cylinders often results in a smoother surface finish compared to traditional single-cylinder machines. This reduces the need for post-processing and improves the overall aesthetics and functionality of the part.
- Flexibility for Complex Parts: Double-cylinder metal spinning machines are well-suited for producing complex shapes, including parts with variable wall thickness, intricate contours, and larger diameters. The flexibility of the system allows for intricate, customized designs to be spun efficiently.
- Faster Production: With the ability to apply force more efficiently and manage material flow across multiple axes, double-cylinder machines can often achieve faster production times than single-spindle systems, especially for parts that require complex or symmetrical shapes.
Applications of Double-Cylinder Metal Spinning Machines:
- Aerospace: In the aerospace industry, double-cylinder spinning machines are used to manufacture parts like turbine components, engine casings, and structural elements, which need to meet high-strength, low-weight, and high-precision standards.
- Automotive: The automotive sector uses these machines for parts such as wheel rims, heat shields, and other structural components that require strength, durability, and lightweight properties.
- Defense: Double-cylinder machines are valuable in producing military components that must withstand extreme conditions. This includes parts like radar housings, armored vehicle components, and missile casings.
- Energy: The energy sector benefits from double-cylinder metal spinning for producing components used in turbines, reactors, and other power generation equipment, where precision and material performance are critical.
- Heavy Industry: Large components in industries like shipbuilding and machinery manufacturing can also be produced using double-cylinder metal spinning machines, offering durability and precision in the production of high-stress parts.
- Custom Parts: For custom, small-batch production, double-cylinder machines allow manufacturers to quickly adjust and produce intricate, specialized parts, particularly for high-end and niche applications.
Advantages of Double-Cylinder Metal Spinning Machines:
- Increased Production Efficiency: With two spindles working in tandem, these machines can form parts faster than single-spindle machines, reducing cycle times and increasing throughput.
- Better Quality Control: The dual spindle system enhances control over material deformation, improving consistency, and ensuring that the final part meets high-quality standards.
- Reduced Tooling Wear: The even distribution of forces between the two cylinders can help reduce excessive wear on tooling, prolonging tool life and minimizing maintenance costs.
- Versatility: These machines can handle a wide range of part sizes and shapes, from small, intricate components to larger, more complex forms, making them versatile across various industries.
- Lower Material Waste: Due to the precise control over the material, double-cylinder metal spinning typically results in less material waste compared to other metal-forming processes like casting or stamping.
- Customization: Manufacturers can use these machines to produce highly customized parts, whether for one-off prototypes or low-volume production, with the ability to adjust process parameters easily.
As manufacturers continue to demand higher precision, faster production, and better material utilization, the double-cylinder metal spinning machine remains a powerful tool in producing complex, high-performance metal parts efficiently. The machine’s ability to manage material flow and apply force on multiple axes opens up a range of applications that benefit from its precision, speed, and versatility.
The evolution of double-cylinder metal spinning machines continues to focus on improving automation, precision, and material efficiency. Advanced CNC systems are now integrated into these machines, enabling more complex geometries and customized part designs to be produced with high levels of repeatability and accuracy. By using intelligent software, operators can program the machine to perform multiple operations in a single cycle, minimizing human intervention and reducing the potential for error. Additionally, the introduction of real-time feedback systems, which monitor parameters like spindle speed, material temperature, and tool pressure, allows for continuous optimization during the manufacturing process. This real-time data collection helps ensure that parts are consistently produced to spec, with variations in material or tooling wear being automatically compensated for during the operation.
One of the key advantages of double-cylinder machines is their ability to handle materials that are difficult to form with traditional methods. For example, advanced alloys like titanium, Inconel, and high-strength steels, often used in aerospace and defense applications, can be spun with minimal risk of cracking or warping, due to the more controlled and distributed forces applied during the process. As these materials become more common in industries requiring high-performance components, the role of double-cylinder metal spinning machines in shaping these challenging materials will continue to grow.
Manufacturers are also increasingly focused on improving the energy efficiency of these machines. Newer models come equipped with regenerative drive systems, where energy is recovered during deceleration or idle periods and reused, contributing to a reduction in overall power consumption. Additionally, the optimization of machine structure through advanced simulations and material sciences has led to machines that are more lightweight yet still maintain the rigidity necessary for precision forming. This not only lowers the machine’s energy consumption but also improves its dynamic performance, allowing for faster cycle times without compromising part quality.
Another area where double-cylinder metal spinning machines are seeing growth is in hybrid manufacturing. In hybrid processes, metal spinning is combined with other forming or finishing techniques, such as additive manufacturing or laser cutting, to produce more complex parts with minimal post-processing. This allows manufacturers to take advantage of the benefits of both forming processes and additive technologies, creating parts with geometries that were previously too intricate or expensive to produce using traditional methods. The integration of advanced sensors and automation also makes these hybrid systems more feasible, as they can be programmed to adapt to the varying requirements of different stages of production.
The demand for sustainability in manufacturing processes continues to shape the development of double-cylinder metal spinning machines. As industries seek ways to reduce their environmental impact, the efficient use of materials becomes increasingly important. The precision and minimal waste associated with spinning ensure that manufacturers are making the most of their raw materials. Furthermore, the durability of the finished products, combined with the reduced need for secondary operations, contributes to lower overall resource consumption and less environmental pollution.
The versatility of double-cylinder metal spinning machines ensures their continued relevance in diverse industries. From aerospace to medical devices, automotive to energy, their ability to produce lightweight, high-strength parts with tight tolerances makes them indispensable. The integration of digital technologies and real-time data analysis is transforming these machines into highly adaptive, intelligent tools capable of meeting the challenges of modern manufacturing. As the demand for complex, customized, and sustainable products grows, double-cylinder metal spinning machines will continue to play a vital role in shaping the future of manufacturing.
As the future of double-cylinder metal spinning machines continues to unfold, ongoing advancements in materials science and manufacturing technology promise to expand their capabilities even further. One of the key trends in this progression is the development of advanced composite materials and alloys that are engineered specifically for the demands of high-performance industries. These materials, which include carbon fiber-reinforced metals, high-temperature ceramics, and novel lightweight alloys, offer new challenges and opportunities for double-cylinder metal spinning. The precision and control offered by these machines make them ideal for forming components from these innovative materials, as they allow manufacturers to achieve the desired properties — strength, flexibility, thermal resistance — while maintaining exacting tolerances.
With the rise of Industry 4.0 and the digitalization of manufacturing, double-cylinder spinning machines are becoming more interconnected with other systems in the factory. Machine-to-machine communication, via IoT (Internet of Things) networks, enables automated synchronization across the entire production line. This creates a more seamless workflow, reduces downtime, and improves overall efficiency. For example, if a part is deemed out of spec during production, the system can automatically alert downstream machines to adjust or reject the faulty part, reducing material waste and ensuring that only high-quality parts are passed through to the next stage.
Advanced simulation software is playing an increasingly important role in the design and operation of double-cylinder metal spinning machines. Engineers can now model the entire spinning process virtually before physical production begins. This allows for the optimization of tool paths, material flow, and spindle speeds in a digital environment, reducing trial-and-error and cutting down on setup times. The integration of artificial intelligence (AI) and machine learning algorithms into these simulation tools further enhances their ability to predict potential issues in real-time. These technologies allow the machine to adapt and fine-tune its parameters dynamically, ensuring consistent part quality and increasing the efficiency of the manufacturing process.
Another promising development is the incorporation of additive manufacturing (AM) technologies into the spinning process. In hybrid setups, the metal spinning machine could be paired with an additive manufacturing system to create complex parts layer by layer before being formed into the final shape using the spinning process. This can be particularly useful for producing parts with internal structures, such as those required in aerospace or medical applications, where lightweight yet strong geometries are needed. These hybrid systems are expected to bring significant cost savings and performance enhancements, as they allow for the creation of highly complex components without the need for expensive tooling or molds.
In terms of automation, the future of double-cylinder metal spinning machines will likely involve more sophisticated robotics to handle material loading, unloading, and part inspection. Robotic arms equipped with vision systems and advanced sensors will be able to perform quality checks in real-time, automatically adjusting the machine’s parameters if any deviations are detected in the part geometry. This level of automation allows for consistent, high-quality production while reducing the need for manual labor, thus lowering labor costs and minimizing human error.
The ongoing trend towards sustainability in manufacturing is also influencing the future of double-cylinder metal spinning machines. Manufacturers are under increasing pressure to reduce their carbon footprint and minimize waste in every step of production. The precision of metal spinning, coupled with its minimal material waste, makes it a highly sustainable manufacturing method. Moreover, as energy recovery systems become more common, the overall energy consumption of spinning machines is expected to decrease further, contributing to more eco-friendly production practices. This focus on sustainability is also driving research into more environmentally friendly lubricants, coolants, and other consumables, which can reduce the ecological impact of the production process.
The development of autonomous machines is another exciting avenue for the future. Fully autonomous double-cylinder metal spinning machines could be programmed to operate continuously with minimal human oversight. These machines would be able to adjust their own parameters based on real-time data from sensors, ensuring that the process remains optimal throughout production. This self-correcting mechanism would not only enhance the quality and efficiency of the process but also increase the lifespan of the machines themselves by reducing wear and tear from improper settings or operator errors.
As industries continue to embrace digital twin technologies, the concept of creating a virtual replica of the machine and its environment will become more prevalent. A digital twin of a double-cylinder spinning machine could be used to predict wear patterns, optimize maintenance schedules, and even simulate production scenarios to better understand the impact of various changes before they are implemented. This predictive approach to machine management would help reduce unplanned downtime and improve overall machine uptime, which is a critical factor in modern manufacturing.
With the continuous evolution of technology, double-cylinder metal spinning machines will remain a critical tool in the production of high-precision, high-performance components. Their ability to produce complex geometries, handle advanced materials, and integrate with digital manufacturing ecosystems will ensure their relevance in industries ranging from aerospace to medical devices and beyond. As new technologies like artificial intelligence, advanced robotics, and hybrid manufacturing systems are integrated into spinning operations, the potential for these machines to meet the ever-increasing demands of modern manufacturing will only continue to grow, making them indispensable to the future of precision metalworking.
Deep-Drawing Spinning Machine
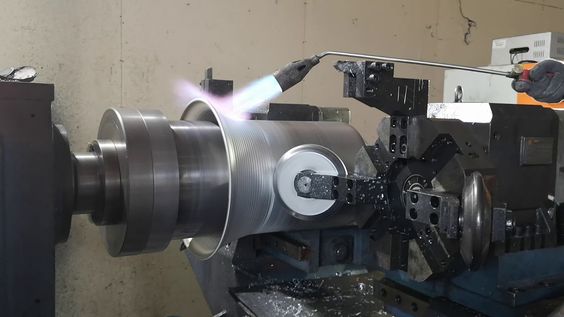
A deep-drawing spinning machine combines two metal-forming techniques — deep drawing and metal spinning — to create components that require both deep shaping and precision spinning. This hybrid process is particularly useful for producing complex, deep, cylindrical or conical parts, often with intricate geometries and thin walls, typically in industries such as aerospace, automotive, defense, and medical manufacturing.
Key Features of a Deep-Drawing Spinning Machine:
- Dual Process Combination: The deep-drawing process involves applying pressure to a metal sheet to form a deep, hollow part. When combined with spinning, the machine uses a rotating tool to further shape the part, often with the help of additional tools and mandrels. This allows for more precise control over the material’s shape and thickness distribution, which can be particularly important when making high-performance parts.
- Precision and Material Control: One of the main benefits of the deep-drawing spinning process is the enhanced control over material flow. The deep-drawing part of the process pulls the material into a cavity, while the spinning component refines the shape and ensures uniform wall thickness, eliminating the issues that might arise from traditional deep-drawing, such as thinning in certain areas.
- Complex Geometries: The combined approach allows for the creation of parts with highly complex shapes, such as deep cylinders, bowls, or conical forms, with precise dimensions and a smooth surface finish. It is particularly useful for producing parts with a combination of deep recesses and gradual curves.
- Material Efficiency: The precision achieved through the deep-drawing spinning process means that less material is wasted, leading to reduced scrap and lower material costs. Additionally, the ability to control wall thickness more effectively can prevent the need for post-processing, reducing overall production time and costs.
- High-Strength Parts: The deep-drawing and spinning combination can also improve the mechanical properties of the final part. The spinning process induces a compressive stress on the material, which can enhance the strength and fatigue resistance of the final component, making it ideal for high-stress applications.
- Versatility: Deep-drawing spinning machines can handle a wide range of materials, including aluminum, stainless steel, titanium, and other high-strength alloys. The ability to form both ductile and brittle materials gives manufacturers flexibility when selecting materials for specific applications.
Applications of Deep-Drawing Spinning Machines:
- Aerospace: In aerospace, deep-drawing spinning machines are used to create components like fuel tank parts, turbine casings, and other complex geometries that require high strength-to-weight ratios and precision. These parts often need to withstand high thermal and mechanical stresses, which is why the combination of deep drawing and spinning is ideal.
- Automotive: The automotive industry benefits from deep-drawing spinning machines for manufacturing lightweight, high-strength components, including wheel rims, structural parts, and casings. The process allows for the production of parts that require deep draws and complex shapes, contributing to improved vehicle performance and safety.
- Defense: The defense industry uses deep-drawing spinning machines to produce parts such as radar housings, missile components, and armored vehicle parts. These applications require materials that can handle extreme environmental conditions, and the process ensures high precision and durability.
- Medical Devices: Medical devices, such as surgical tools, implants, and casings for medical equipment, often require parts with complex shapes and tight tolerances. The deep-drawing spinning process is ideal for creating these types of components, as it ensures both structural integrity and precision.
- Heavy Equipment: Components used in heavy equipment, like housings for machinery, turbines, and engine parts, often need to be robust and capable of withstanding harsh conditions. Deep-drawing spinning machines are capable of creating these large, complex parts with high strength and durability.
- Energy Sector: In the energy sector, deep-drawing spinning machines are used to create parts for power generation equipment, including turbine blades, reactor components, and storage tanks. These parts require the combination of deep drawing and spinning to achieve both the necessary strength and the precise geometries needed for high-performance applications.
Advantages of Deep-Drawing Spinning Machines:
- Improved Precision: The combination of deep drawing and spinning allows for enhanced precision in the final part. The deep-drawing process provides the initial forming, while the spinning process refines the part to ensure exact dimensions, uniform wall thickness, and smooth surfaces.
- Higher Strength-to-Weight Ratio: Parts made with this process tend to be lighter yet stronger, thanks to the compression forces induced during spinning, which increases the material’s yield strength. This is particularly important in industries like aerospace and automotive, where reducing weight without sacrificing strength is critical.
- Cost-Effectiveness: While the equipment for deep-drawing spinning may be more specialized, the reduction in material waste and the lower need for post-processing make this process cost-effective over time. The ability to produce high-quality parts with fewer steps in the manufacturing process also reduces overall production costs.
- Flexibility in Design: Manufacturers can create intricate designs, from deep cylindrical components to complex geometries with varying thicknesses. This flexibility opens up new possibilities for design, especially when standard forming techniques may not be able to produce such shapes with the same accuracy.
- Shorter Lead Times: The combination of deep drawing and spinning typically results in faster production cycles compared to using each method individually. This is because the process is more efficient, with fewer stages needed to reach the finished product, thus shortening lead times for customers.
- Lower Material Waste: Since the process combines two methods that focus on precise material manipulation, deep-drawing spinning produces less waste material compared to traditional stamping or casting methods, where excess material is often trimmed away. This not only cuts costs but also contributes to more sustainable manufacturing practices.
Future Trends:
As industries increasingly focus on sustainability and cost-efficiency, the adoption of automated deep-drawing spinning machines is expected to rise. These machines, equipped with advanced sensors and data analytics, can automatically adjust parameters to optimize the forming process in real time, further improving precision and minimizing waste.
Additionally, advancements in material technology may allow the deep-drawing spinning process to be applied to a wider range of materials, including more complex composite materials or advanced high-performance alloys. This expansion of material capabilities could open up new applications in fields such as renewable energy, advanced robotics, and electronics.
Finally, the ongoing integration of Industry 4.0 technologies, including machine learning, artificial intelligence, and real-time monitoring systems, will enhance the capabilities of deep-drawing spinning machines. These technologies will allow for more intelligent automation, predictive maintenance, and optimized production schedules, improving both the efficiency and reliability of the manufacturing process.
In conclusion, deep-drawing spinning machines are highly versatile tools that provide manufacturers with the ability to create complex, high-performance components with exceptional precision and minimal waste. As technological advancements continue, the capabilities and applications of this hybrid forming process will only expand, making it a critical method for industries requiring sophisticated, high-quality parts.
Deep-drawing spinning machines are evolving rapidly with advancements in technology, leading to improvements in precision, efficiency, and versatility. One of the key developments is the integration of automation and robotics into the process. These machines are now equipped with automated systems for material handling, part inspection, and tool adjustments, which minimize human intervention and reduce the risk of errors. The incorporation of robotics also speeds up the production cycle, allowing for continuous, high-speed manufacturing with consistent quality across batches.
Incorporating real-time monitoring systems into deep-drawing spinning machines is another significant advancement. These systems can track the behavior of the material throughout the forming process, providing immediate feedback to operators. If any deviation from the desired specifications is detected, the system can automatically adjust parameters such as spindle speed, pressure, and tooling positions. This ensures that the parts remain within tight tolerances, improving the overall quality of the final product and reducing the need for costly rework.
As manufacturers continue to push for increased sustainability, deep-drawing spinning machines are being designed with energy efficiency in mind. New machines are being equipped with regenerative drive systems, which capture energy during braking or deceleration and return it to the system. This reduces energy consumption, making the machines more environmentally friendly and cost-effective to operate. Additionally, the use of advanced materials in the machine structure, such as lightweight alloys and composites, helps to reduce the overall weight of the machines, further enhancing their energy efficiency.
The ability to form complex parts with minimal material waste remains one of the most significant advantages of deep-drawing spinning machines. By applying controlled forces to the material in a way that minimizes distortion and thinning, manufacturers can produce components that meet exacting specifications while reducing scrap material. This is particularly valuable in industries where high-performance materials such as titanium, high-strength steels, and composites are used, as these materials are often expensive, and maximizing their use is critical for cost control.
Another exciting development is the integration of digital twin technology into deep-drawing spinning processes. By creating a virtual replica of the machine and its environment, manufacturers can simulate the entire forming process before production begins. This allows engineers to predict how the material will behave under different conditions, enabling them to optimize the process and make adjustments to the machine setup. This predictive capability helps prevent costly production errors and reduces the need for trial-and-error during the actual manufacturing process.
As industries such as aerospace, automotive, and medical device manufacturing demand increasingly complex and customized parts, deep-drawing spinning machines are adapting to meet these needs. Advances in CNC (computer numerical control) technology and multi-axis machining capabilities allow these machines to produce highly intricate geometries with exceptional precision. This ability to create custom parts on demand, with minimal lead time, is a significant advantage in sectors where time-to-market is critical.
With the push toward Industry 4.0, the future of deep-drawing spinning machines is intertwined with the broader trend of digital manufacturing. These machines are becoming increasingly connected to enterprise resource planning (ERP) systems, supply chain networks, and other digital infrastructure. This connectivity allows manufacturers to track production in real-time, monitor machine performance remotely, and even predict maintenance needs before breakdowns occur. As a result, downtime is reduced, and production efficiency is significantly improved.
Looking ahead, the continued development of hybrid manufacturing techniques is likely to play a pivotal role in the evolution of deep-drawing spinning machines. Hybrid processes, which combine traditional metal forming techniques with newer technologies such as additive manufacturing (3D printing), enable manufacturers to produce parts with complex internal geometries or integrated features that would be difficult or impossible to create using conventional methods alone. By combining the strengths of metal spinning and additive manufacturing, manufacturers can create lightweight, high-strength components that are both cost-effective and high-performance.
In summary, deep-drawing spinning machines are set to play an even more important role in the future of precision metal forming. With ongoing advancements in automation, energy efficiency, digital manufacturing, and hybrid techniques, these machines are becoming more capable, versatile, and sustainable. As industries continue to demand more complex, customized parts with higher precision and reduced lead times, deep-drawing spinning machines will remain at the forefront of innovation in manufacturing, providing the tools necessary to meet these challenges head-on.
The future of deep-drawing spinning machines is poised to integrate even more sophisticated technologies, including artificial intelligence (AI) and machine learning (ML), which will further enhance their capabilities. These technologies can be employed to analyze vast amounts of data collected during the forming process, enabling the machine to make intelligent decisions in real-time. By continuously monitoring the material’s behavior, machine parameters, and environmental factors, AI systems can predict potential issues before they arise, allowing for immediate corrective actions to ensure the production of high-quality parts. This could lead to fully autonomous metal forming systems where the machines can self-optimize without human intervention, further reducing operational costs and improving overall efficiency.
One of the significant areas of growth for deep-drawing spinning machines is in the customization of parts. As demand increases for products that are tailored to specific applications, manufacturers need more flexible and adaptable machines that can accommodate a variety of materials and designs. This is particularly important in industries such as medical device manufacturing, where bespoke parts are often required. Future deep-drawing spinning machines will likely feature even more adaptable tooling systems and customizable settings, allowing operators to quickly switch between different materials and design requirements without the need for extensive retooling or downtime.
Moreover, the development of multi-material forming capabilities could become a key feature of future deep-drawing spinning machines. The ability to combine different materials in a single part — for example, integrating metals with polymers or ceramics — opens up a whole new world of possibilities. This hybrid approach would be especially useful in industries such as aerospace, where components often require different material properties in different sections, such as high thermal resistance in one area and lightweight, high-strength properties in another. Multi-material metal spinning could enable the production of more efficient, functional, and cost-effective components.
The push towards sustainability and reducing environmental impacts continues to shape the evolution of deep-drawing spinning machines. As raw material costs rise and environmental regulations become stricter, manufacturers are increasingly looking for ways to minimize waste, conserve energy, and reduce emissions. Deep-drawing spinning, with its precision and minimal material waste, is inherently a more sustainable process than many traditional metal forming methods. However, manufacturers are exploring ways to make the process even greener by using more eco-friendly lubricants, coolants, and other consumables. Furthermore, innovations in machine designs that reduce energy consumption — such as the use of more efficient motors and regenerative braking systems — will make these machines even more environmentally friendly.
Another area of innovation is in the enhancement of the machine’s material handling capabilities. Advanced material handling systems that incorporate automation and robotics can streamline the entire process, from material loading to unloading and inspection. By reducing the need for manual handling, these systems will not only increase efficiency but also ensure higher safety standards. The integration of vision systems that can detect defects or anomalies in the material during processing will further ensure that only quality parts are produced, reducing scrap and rework.
As the manufacturing industry increasingly adopts additive manufacturing (AM) and digital twins, there will likely be greater synergy between traditional forming methods like deep-drawing spinning and emerging technologies. For example, 3D printing can be used to create highly complex part geometries that are then formed using deep-drawing spinning techniques. This combination of traditional and cutting-edge methods is likely to become more prevalent, allowing manufacturers to push the boundaries of part complexity, material properties, and overall performance.
Moreover, advanced simulation and modeling tools will continue to play a larger role in the development and operation of deep-drawing spinning machines. With improved simulation software, manufacturers can simulate the entire forming process before physical production begins, optimizing parameters such as material flow, tool movements, and machine setup. This ability to “see” the end result in a virtual environment before beginning production can reduce the need for costly prototypes, significantly shorten the design cycle, and prevent potential issues from arising during production.
In industries that require rapid prototyping, the potential for deep-drawing spinning machines to integrate with digital design tools and 3D printing technology offers manufacturers an avenue to quickly produce high-precision, high-quality parts. These hybrid methods will facilitate the creation of prototype parts with customized features or intricate geometries, all while maintaining the precision and material integrity required for final production. This could be especially beneficial in industries like automotive and aerospace, where prototype testing is often a lengthy process, and time-to-market is crucial.
Finally, as the demand for smart manufacturing grows, deep-drawing spinning machines will likely become a core component of “smart” factories. These factories will use machine-to-machine communication, sensors, and cloud-based systems to provide real-time feedback, optimize production schedules, and adjust processes based on live data from the factory floor. This connectivity will allow manufacturers to track not only the machine’s performance but also the entire production process, enabling quicker decision-making and more efficient resource management.
In conclusion, the future of deep-drawing spinning machines is tightly aligned with the ongoing advancements in digital manufacturing, sustainability, automation, and material science. These machines will continue to evolve into more intelligent, efficient, and adaptable systems, capable of handling complex geometries, diverse materials, and intricate designs. With the integration of advanced technologies like AI, robotics, multi-material forming, and hybrid manufacturing, deep-drawing spinning machines will remain a key tool in the production of high-precision, high-performance parts across various industries.
Orbital Spinning Machine
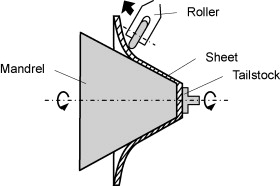
An orbital spinning machine is a specialized type of metal-forming machine used primarily for shaping and spinning metal components, typically cylindrical or conical parts. The orbital spinning process involves rotating a workpiece while a forming tool follows a circular path along the surface of the material. This type of machine is designed to create high-precision, low-tolerance parts with uniform wall thickness and smooth surface finishes, often used in industries like aerospace, automotive, and defense.
Key Features of an Orbital Spinning Machine:
- Rotational Movement: In orbital spinning, the metal part (workpiece) is held stationary on a mandrel or fixture, while the tool or spindle moves in an orbital or circular motion around the workpiece. This motion allows the tool to continuously form and shape the material by applying pressure to the metal surface.
- Tool Path: The key characteristic of orbital spinning is the movement of the tool in an orbital pattern. Unlike traditional spinning, where the tool moves linearly along the workpiece’s surface, orbital spinning creates more complex, highly controlled shapes due to the circular tool motion. This results in a smooth and even distribution of material along the part’s surface.
- Precision and Control: Orbital spinning machines offer high precision and are capable of producing parts with tight tolerances. The machine’s ability to control the tool’s orbital motion allows manufacturers to achieve accurate wall thickness distribution, which is especially important for parts that need to meet stringent specifications for strength and durability.
- Material Handling: The workpiece is typically mounted on a mandrel or a fixture that keeps it in place while the tool moves. Depending on the design of the machine, the workpiece may be pre-formed into a rough shape, or the orbital spinning machine may handle the entire shaping process from start to finish. The material, typically metal alloys such as aluminum, stainless steel, or titanium, is deformed incrementally by the orbital tool.
- Surface Finish: Orbital spinning machines can produce parts with high-quality surface finishes, reducing the need for post-processing. The smoothness of the surface, combined with the uniformity of the material distribution, makes orbital spinning particularly suitable for parts that require minimal secondary operations like polishing or grinding.
- Versatility: Orbital spinning is versatile and can be used to form a wide range of geometries, including cylindrical, conical, and even spherical parts. This makes the technology suitable for many industries, including aerospace, where components often require precise, lightweight, and durable parts, and automotive, where weight reduction and performance are key concerns.
- Reduced Material Waste: Because the orbital spinning process is highly controlled, there is less material wastage compared to other forming methods, such as stamping or casting. Material is only deformed in the areas where it is needed, allowing for better utilization of raw materials and reduced production costs.
Applications of Orbital Spinning Machines:
- Aerospace: In the aerospace industry, orbital spinning machines are used to create parts such as fuselage components, turbine casings, and other critical structural elements. These parts often need to meet strict requirements for strength, weight, and resistance to high temperatures and stress, all of which orbital spinning can provide.
- Automotive: For automotive applications, orbital spinning is used to create components like exhaust systems, heat shields, and other parts where precision and lightweight properties are essential. The process is capable of creating durable, high-strength parts while keeping weight to a minimum, which is crucial for improving fuel efficiency.
- Energy Sector: Orbital spinning is employed to create parts used in power generation equipment, including turbine housings, reactor pressure vessels, and components for renewable energy systems. These parts often require the ability to withstand high mechanical and thermal stresses, making orbital spinning an ideal choice due to its precision and strength-enhancing characteristics.
- Medical Devices: Medical device manufacturers use orbital spinning machines to produce parts like surgical tools, implants, and casings for medical equipment. These components need to meet exacting standards for both mechanical properties and surface finishes to ensure safety and performance.
- Defense: In defense applications, orbital spinning is utilized to create high-performance components for military aircraft, armored vehicles, and other specialized machinery. The ability to produce complex geometries with uniform material properties is essential for meeting the rigorous demands of defense manufacturing.
- Heavy Machinery: Orbital spinning is used in the production of parts for heavy machinery, such as housings, turbines, and engine components. The strength and durability required in these parts are often best achieved through the precision of orbital spinning.
Advantages of Orbital Spinning Machines:
- Enhanced Precision: The orbital motion of the tool allows for high levels of precision in part forming. The tool follows a consistent, circular path around the workpiece, ensuring even material distribution and preventing localized thinning or excessive material buildup.
- Improved Strength-to-Weight Ratio: The process of orbital spinning induces a compressive force on the material, which strengthens the final product. This is particularly important in industries where the parts need to be lightweight yet durable, such as aerospace and automotive.
- High-Quality Surface Finish: The continuous motion of the tool results in a smooth surface, which often requires less post-processing. This reduces labor costs and the need for additional operations, leading to faster turnaround times and lower overall production costs.
- Lower Material Waste: Orbital spinning is a material-efficient process that minimizes scrap by ensuring that only the necessary material is used. The precision of the tool’s motion helps avoid unnecessary thinning or distortion of the material.
- Adaptability to Complex Geometries: Orbital spinning is ideal for producing parts with complex shapes that might be difficult or impossible to achieve using other forming methods. The flexibility of the machine’s tool path allows for the creation of intricate designs with precise dimensions.
- Reduced Tool Wear: Because the tool’s movement is more gradual and controlled compared to linear spinning, there is less impact and wear on the tooling. This can extend tool life and reduce maintenance costs.
- High Throughput: Orbital spinning machines can operate at high speeds, enabling the production of large quantities of parts in a relatively short period of time. This is ideal for industries where fast production cycles and large-volume manufacturing are needed.
Future Trends:
The future of orbital spinning machines will likely see increased integration with Industry 4.0 technologies. The addition of smart sensors, data analytics, and real-time monitoring will enable more precise control over the forming process, improving the consistency of the final parts. These smart systems can monitor parameters such as temperature, pressure, and material deformation, adjusting machine settings in real time to optimize the process and reduce defects.
Additionally, automation and robotic arms are likely to become more common in orbital spinning machines. This will allow for faster and more consistent part handling, reducing manual labor and increasing production efficiency. Automation also opens the door for fully autonomous metal-forming processes, where machines can operate with minimal human intervention, reducing errors and improving overall productivity.
The application of multi-material forming techniques may also increase in orbital spinning machines. As manufacturers seek to produce parts with different material properties in specific areas, orbital spinning could be used to combine metals or incorporate composite materials into a single part, offering improved performance characteristics.
In conclusion, orbital spinning machines are highly effective tools for the production of precision metal parts with complex shapes, tight tolerances, and high-quality surface finishes. As manufacturing technologies continue to evolve, orbital spinning machines will likely become even more versatile and efficient, integrating smart technologies, automation, and multi-material capabilities to meet the growing demands of industries such as aerospace, automotive, energy, and medical device manufacturing.
Orbital spinning machines are becoming increasingly sophisticated as industries continue to demand higher precision, better material utilization, and faster production cycles. The integration of advanced technologies, such as artificial intelligence (AI) and machine learning (ML), will likely enhance the machine’s ability to predict and optimize the forming process in real-time. These systems can analyze data from sensors embedded in the machine, monitor variables such as temperature, pressure, and material flow, and automatically adjust machine parameters to improve part quality and minimize defects. Such systems will allow for more consistent results, reducing human intervention and increasing efficiency.
The rise of smart manufacturing is also influencing the development of orbital spinning machines. These machines will likely be able to communicate with other machines, sensors, and production systems across the factory floor, creating a fully connected environment. This connectivity enables manufacturers to track the status of the entire production process in real time, ensuring that any issues are identified and addressed quickly. The ability to monitor machine performance remotely means that operators can optimize settings without being physically present, which is particularly beneficial for global manufacturing operations.
As sustainability becomes an increasing focus in manufacturing, orbital spinning machines will likely continue to evolve to reduce energy consumption and minimize material waste. Advances in energy-efficient drive systems, such as regenerative braking or energy recovery features, will help lower the carbon footprint of orbital spinning processes. Additionally, the development of eco-friendly lubricants and coolants will further improve the sustainability of the process, reducing the environmental impact of the machines while maintaining high-quality production standards.
One of the most exciting future developments for orbital spinning machines is the potential for hybrid manufacturing. By combining traditional metal spinning with additive manufacturing (3D printing), manufacturers could create parts that are not only strong and lightweight but also feature complex internal geometries or integrated features that would be difficult to achieve using traditional methods alone. Hybrid processes could enable the production of components with both intricate, customized designs and enhanced material properties, opening up new possibilities for industries such as aerospace, automotive, and medical devices.
The demand for customization in parts will continue to drive the need for adaptable orbital spinning machines. The ability to quickly switch between different materials, designs, and geometries is essential in sectors like aerospace, where every component often requires specific material properties and precise measurements. This adaptability will be facilitated by automated tool changing systems, which will allow orbital spinning machines to handle a wider range of products with minimal downtime.
Furthermore, additive manufacturing could be employed in conjunction with orbital spinning to create custom mandrels or tooling for specific parts. By using 3D printing to create these tools, manufacturers could reduce lead times and costs associated with tool creation, as well as improve the flexibility of the machine to handle bespoke projects.
The future of orbital spinning machines is also likely to include multi-axis capabilities that allow for even greater flexibility in the forming process. Multi-axis machines can rotate the workpiece along multiple planes, enabling the production of more complex, detailed geometries. This would be particularly valuable in industries where high-precision, multi-faceted parts are required, such as in the production of turbine components, exhaust systems, and pressure vessels.
With advancements in material science, orbital spinning machines will continue to expand the range of materials that can be effectively formed. As new alloys and composite materials become available, these machines will adapt to process materials with diverse mechanical properties. This includes not only traditional metals like steel and aluminum but also more advanced materials like titanium and high-performance polymers. The ability to form these materials with precision and minimal waste will be crucial as industries move towards more advanced, lightweight, and durable components.
Robotic integration is another trend that will enhance orbital spinning machines. Robotic arms can handle tasks such as loading and unloading parts, adjusting the position of the workpiece, and even monitoring the progress of the forming process. With the help of machine vision systems, robots can inspect parts during the spinning process, ensuring that any deviations from specifications are immediately corrected. The addition of robotics will increase throughput, reduce the need for human labor, and further minimize human error in the production process.
As demand for high-performance components with minimal lead times increases, orbital spinning machines are poised to play an even more critical role in the manufacturing process. The continued evolution of these machines, driven by technological advancements such as AI, automation, hybrid manufacturing, and multi-material forming, will allow manufacturers to meet the ever-increasing challenges of producing customized, high-quality parts for industries ranging from aerospace to automotive to medical devices.
In conclusion, orbital spinning machines represent a vital tool in modern precision manufacturing. As technologies evolve, these machines will become more efficient, adaptable, and capable of producing increasingly complex and high-performance parts. The integration of advanced technologies will enable orbital spinning machines to meet the demands of industries that require lightweight, durable, and high-precision components, making them an essential asset in the future of manufacturing.
As the demand for more advanced manufacturing processes continues to grow, the role of orbital spinning machines in producing high-precision components will only expand. One of the significant trends driving this evolution is the push for automation in manufacturing. As orbital spinning machines become more integrated with automated systems, they will significantly reduce the need for human intervention in repetitive tasks. Automated loading and unloading systems, along with robotic arms for handling and positioning workpieces, will streamline the entire production process. This not only enhances production speed but also reduces human error and operational costs. With these advancements, orbital spinning machines will become more efficient, capable of producing large volumes of parts with minimal manual labor.
The integration of advanced sensors and machine vision systems will enable orbital spinning machines to perform real-time quality checks during the manufacturing process. These sensors will continuously monitor the workpiece, detecting any anomalies, such as material inconsistencies, dimensional deviations, or defects that may arise during the forming process. By catching these issues in real time, manufacturers can make immediate adjustments, preventing the production of faulty parts and minimizing waste. This level of precision will be particularly valuable in industries that require strict tolerances and high-quality finishes, such as aerospace and medical device manufacturing.
Big data analytics will also play an increasingly important role in the future of orbital spinning machines. With the ability to collect vast amounts of data during each production cycle, manufacturers will be able to analyze this information to improve process parameters and optimize machine performance. By leveraging predictive analytics, manufacturers will be able to forecast machine maintenance needs, avoid unplanned downtime, and further enhance the reliability and efficiency of their orbital spinning systems. Machine learning algorithms can be implemented to fine-tune machine settings based on historical data, continually improving the precision and speed of the process.
Another critical development in the future of orbital spinning machines is their ability to work with a broader range of advanced materials. As industries like aerospace, automotive, and renewable energy demand components made from lightweight, high-strength materials, orbital spinning machines will evolve to handle complex alloys and composite materials. These materials, which often have specific forming requirements, may include titanium, high-strength steels, and polymers reinforced with carbon or glass fibers. The versatility of orbital spinning will allow manufacturers to continue to produce parts from these advanced materials while maintaining the desired mechanical properties and surface finishes.
The potential for multi-material forming in orbital spinning is another exciting area of development. By combining different materials in a single part, manufacturers can tailor the properties of the final component to meet specific performance requirements. For instance, a part may have a core made from one material for strength and a surface layer made from another material for wear resistance or thermal protection. Orbital spinning machines equipped with advanced toolheads and material handling systems will make it possible to form these hybrid components without compromising on quality or precision.
As the importance of sustainability in manufacturing continues to rise, orbital spinning machines are positioned to play a role in reducing material waste and energy consumption. The precision of the orbital spinning process ensures that material is only deformed where necessary, which leads to less scrap and lower raw material costs. Moreover, innovations in energy-efficient drive systems, regenerative braking, and optimized cooling systems will help reduce the environmental impact of these machines. In addition, the development of eco-friendly lubricants and coolants will make orbital spinning processes more sustainable while maintaining the high-quality standards required for precision parts.
The ability to produce parts on-demand with reduced lead times will be another driving factor behind the growing adoption of orbital spinning machines. In industries like aerospace and automotive, where the ability to rapidly prototype and produce custom components is critical, orbital spinning machines with advanced CNC capabilities will enable manufacturers to create parts faster and with greater precision. With the increasing focus on just-in-time manufacturing, these machines will allow manufacturers to quickly respond to changing demands and reduce inventory costs.
As part of the ongoing trend toward digitization and smart manufacturing, orbital spinning machines will likely become more integrated into larger factory systems. Through the use of IoT (Internet of Things) technology, machines will be able to communicate with each other, sharing real-time data on production status, machine health, and performance metrics. This connectivity will enable manufacturers to better manage resources, optimize production schedules, and enhance supply chain visibility. In addition, real-time feedback from orbital spinning machines can be used to adjust parameters across the factory floor, ensuring that all processes are synchronized and operating at peak efficiency.
Advanced simulation and modeling tools will continue to improve the design and optimization of orbital spinning machines. These tools allow manufacturers to simulate the entire forming process before physical production begins, helping them predict material behavior, optimize tool paths, and identify potential issues. By leveraging simulations, manufacturers can reduce the need for costly trial-and-error testing and shorten development cycles for new parts. This digital approach will allow for faster iteration and better adaptation to new materials and designs, making orbital spinning machines even more adaptable to a range of manufacturing needs.
In the future, orbital spinning machines may also become more modular and customizable. This flexibility will enable manufacturers to configure their machines based on specific production needs, such as varying the number of axes, adding additional tooling stations, or integrating new technologies like additive manufacturing. This modular approach will ensure that orbital spinning machines can be tailored to different industries and production volumes, providing manufacturers with the agility they need to meet diverse customer requirements.
Lastly, globalization and the expansion of supply chains will continue to influence the development of orbital spinning machines. As manufacturers seek to lower costs, increase production capacity, and improve delivery times, orbital spinning machines that offer higher throughput, greater efficiency, and the ability to produce a wide range of parts will become increasingly valuable. These machines will also be critical in meeting the demands of global markets for custom, high-precision components that require minimal lead time and high reliability.
In summary, the future of orbital spinning machines looks promising, driven by advancements in automation, AI, robotics, and smart manufacturing. These machines will continue to evolve to meet the growing demands for high-precision, lightweight, and durable components in industries such as aerospace, automotive, medical devices, and energy. With improved materials, enhanced customization options, and sustainable manufacturing practices, orbital spinning machines will remain at the forefront of precision metal forming technology for years to come.
Electric Metal Spinning Machine
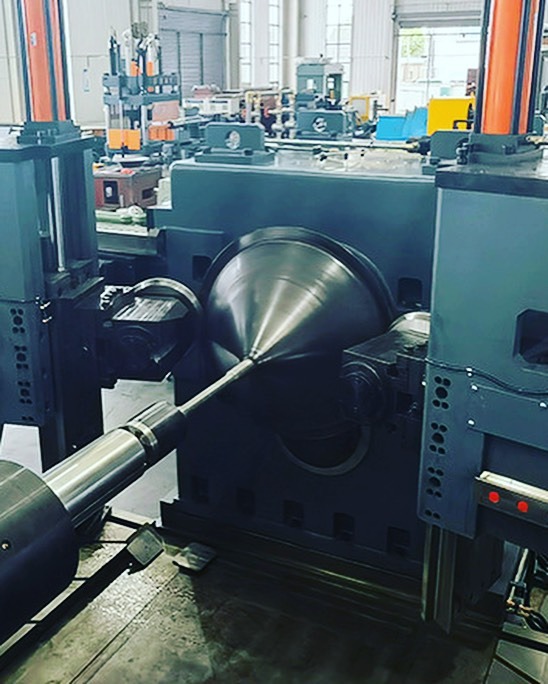
An electric metal spinning machine is a type of metal-forming equipment that uses electric-powered drives and motors to perform the metal spinning process. Unlike traditional metal spinning machines that may rely on mechanical or hydraulic systems for power, electric metal spinning machines are designed to provide a more energy-efficient, precise, and controllable means of shaping metal parts. These machines are used to create rotationally symmetric parts by spinning a flat metal sheet around a mandrel, with the sheet being progressively shaped into the desired form by applying pressure through tooling.
Key Features of Electric Metal Spinning Machines:
- Electric Drive Systems: Electric metal spinning machines are powered by electric motors, which offer precise control over rotational speed and torque. The electric drive system is often more energy-efficient compared to hydraulic or mechanical systems, and it can provide smoother, more consistent motion during the spinning process.
- Precision Control: One of the main advantages of electric metal spinning machines is the high level of precision they offer. The use of electric drives allows for more accurate control of the spinning process, enabling manufacturers to achieve tighter tolerances and higher-quality surface finishes. The ability to fine-tune rotational speeds and pressures allows operators to optimize the forming process for different materials and part geometries.
- Energy Efficiency: Electric systems are generally more energy-efficient than hydraulic or pneumatic systems because they do not require large amounts of fluid or air pressure to operate. This makes electric metal spinning machines more environmentally friendly and cost-effective in terms of energy consumption, particularly in high-volume production environments.
- Reduced Maintenance: Electric metal spinning machines typically require less maintenance compared to hydraulic machines, as they have fewer moving parts and no need for fluid-based systems. This can lead to lower maintenance costs and reduced downtime, contributing to increased productivity.
- Faster Response Time: Electric motors offer a quicker response time when adjusting speed or torque compared to traditional mechanical or hydraulic systems. This enables more flexible operation and faster adjustments during the metal spinning process, which can be important when working with varying part designs or materials.
- Programmable Control: Many electric metal spinning machines are equipped with CNC (Computer Numerical Control) systems, allowing operators to program specific part designs and parameters. The CNC system automates the process, ensuring consistent and repeatable results across multiple parts. This is particularly beneficial for complex geometries or when producing a large number of parts that require high levels of consistency.
- Less Noise and Vibration: Electric systems tend to produce less noise and vibration compared to hydraulic or mechanical systems, making them more suitable for use in environments where noise control is important. This can lead to a safer and more comfortable work environment for operators.
- Compact Design: Electric metal spinning machines tend to be more compact than their hydraulic or mechanical counterparts, as they don’t require large tanks, pumps, or piping for fluid or air systems. This can make electric machines a more space-efficient option, especially in facilities with limited floor space.
- Lower Operational Costs: Due to the reduced energy consumption and lower maintenance requirements of electric systems, operating costs for electric metal spinning machines are often lower than for hydraulic or mechanical machines. This can provide significant savings over time, particularly in high-production environments.
Applications of Electric Metal Spinning Machines:
- Aerospace: In the aerospace industry, electric metal spinning machines are used to produce high-precision components, such as turbine housings, fuselage sections, and engine parts. These components must meet stringent weight and strength requirements, and electric spinning machines can deliver the precision necessary for these demanding applications.
- Automotive: Electric metal spinning machines are commonly used in the automotive industry to produce lightweight, durable parts such as exhaust components, heat shields, and wheel covers. The ability to quickly adapt to different materials and designs makes these machines ideal for producing automotive parts that require both precision and strength.
- Medical Devices: In the medical field, electric metal spinning machines are used to create components for medical equipment, such as casings for surgical tools, implants, and other critical parts. The precision offered by electric spinning machines is essential for meeting the exacting standards required in medical device manufacturing.
- Energy and Power Generation: Electric metal spinning machines are used in the energy sector to produce components such as turbine casings, pressure vessels, and other parts for power generation equipment. The need for high-strength, lightweight components in energy systems makes these machines an ideal solution.
- Consumer Products: Electric metal spinning machines are also used in the production of various consumer goods, including kitchenware, lighting fixtures, and decorative metal parts. These machines can produce both functional and aesthetically pleasing products with high-quality finishes.
- Defense and Military: In the defense sector, electric metal spinning machines are used to produce parts for military vehicles, weapons systems, and aerospace applications. The precision and strength required for these components make electric metal spinning an ideal manufacturing method.
Advantages of Electric Metal Spinning Machines:
- Enhanced Precision: Electric metal spinning machines offer superior precision due to their finely controlled motor systems. This allows for better-quality parts with tighter tolerances, which is crucial in industries like aerospace, medical devices, and automotive.
- Cost-Effective: The energy efficiency of electric machines, combined with lower maintenance costs, can result in significant cost savings for manufacturers, especially in high-volume production environments.
- Environmentally Friendly: Electric spinning machines are more energy-efficient than hydraulic or pneumatic systems, contributing to a reduction in overall energy consumption and lowering the environmental impact of the manufacturing process.
- Improved Safety: Electric systems are typically safer to operate than hydraulic or pneumatic systems, as they do not involve high-pressure fluids or air that could potentially cause safety hazards. Additionally, the reduction in vibration and noise can contribute to a safer working environment.
- Faster Setup Times: Electric metal spinning machines, especially those with CNC capabilities, can be quickly reprogrammed for different parts or design specifications. This flexibility reduces setup times and increases production efficiency.
- Versatility: Electric metal spinning machines are capable of handling a wide range of materials, including metals like aluminum, stainless steel, titanium, and other alloys. The versatility of these machines makes them suitable for a variety of industries and applications.
- Reduced Downtime: The simplified design of electric metal spinning machines, with fewer components subject to wear and tear, leads to less downtime for maintenance and repairs. This can significantly increase productivity in manufacturing settings.
Future Trends in Electric Metal Spinning Machines:
- Integration with Smart Manufacturing: As manufacturing moves toward Industry 4.0, electric metal spinning machines will likely become more integrated with smart factory systems. This will allow for real-time monitoring of machine performance, predictive maintenance, and better integration with other processes in the factory.
- Advanced CNC and Automation: The continued advancement of CNC systems and robotics will enhance the capabilities of electric metal spinning machines, enabling them to handle more complex parts and higher production volumes with greater ease. Automation will also reduce the need for human intervention, leading to faster and more consistent production.
- Increased Material Compatibility: As new and advanced materials are developed, electric metal spinning machines will evolve to process these materials with the same level of precision and efficiency. This includes composites, high-strength alloys, and newer lightweight metals that are increasingly in demand in industries like aerospace and automotive.
- Customization and Flexibility: Future electric metal spinning machines may become more customizable, allowing manufacturers to adjust tooling and settings to suit specific part designs and materials. This flexibility will make electric spinning machines even more valuable for custom or low-volume production runs.
- Energy-Efficient Features: As sustainability becomes more important, future electric metal spinning machines are likely to incorporate even more energy-efficient features, such as regenerative drives, energy recovery systems, and optimized cooling systems. These improvements will reduce the environmental impact of metal forming while maintaining high performance and quality.
In conclusion, electric metal spinning machines represent a powerful and versatile tool for precision metal forming. With advantages in energy efficiency, precision, reduced maintenance, and versatility, these machines are ideal for a wide range of industries, including aerospace, automotive, medical, and defense. As technology continues to evolve, electric metal spinning machines will likely incorporate even more advanced features, driving innovation and meeting the growing demands for high-performance, custom metal components.
Electric metal spinning machines are set to play a major role in the future of metal forming as industries continue to seek more energy-efficient, precise, and adaptable manufacturing solutions. The ability to integrate seamlessly with other digital technologies like IoT and machine learning will significantly enhance the machine’s capabilities. By incorporating real-time data collection, these machines will be able to monitor their own performance, detect potential issues before they become major problems, and adjust parameters on the fly to ensure optimal production results. These innovations will make electric metal spinning machines even more reliable, efficient, and capable of handling increasingly complex tasks.
The development of smart tooling could further enhance the versatility of electric metal spinning machines. By integrating sensors into the tools themselves, manufacturers will be able to track tool wear and automatically replace or sharpen tools when necessary. This feature will help improve consistency across production runs and reduce the likelihood of defects, ultimately contributing to higher-quality products and lower scrap rates. Additionally, advancements in robotic automation could allow electric metal spinning machines to operate in tandem with automated systems for loading, unloading, and inspecting parts, reducing labor costs and increasing throughput.
As part of the ongoing trend toward sustainability, electric metal spinning machines may be designed to use eco-friendly materials and produce less waste. The precision offered by electric motors minimizes the amount of material that is wasted during the forming process, which can have a significant impact on reducing overall material costs and environmental footprint. Moreover, as industries strive to achieve zero-waste manufacturing, electric metal spinning machines could be used in conjunction with recycling and reprocessing technologies to further minimize material loss and make use of scrap materials.
In addition, advancements in multi-material processing will allow electric metal spinning machines to work with a variety of materials in a single part. For example, the ability to spin metal and composite materials together can create parts with tailored properties, combining strength, durability, and light weight in a single component. This capability is expected to be particularly useful in industries such as aerospace, automotive, and energy, where hybrid components made from a mix of materials can provide enhanced performance and meet stringent design requirements.
The development of virtual reality (VR) and augmented reality (AR) tools for electric metal spinning machines could also become a key feature in operator training and machine setup. By using VR or AR systems, operators could simulate the entire metal spinning process before working on the machine, allowing them to practice different setups and operations in a risk-free, virtual environment. This would reduce the need for trial-and-error testing on physical machines, saving both time and resources during the setup phase. Additionally, remote monitoring and diagnostics could be enhanced through AR, allowing operators or engineers to troubleshoot issues in real-time, even from a distance, which would reduce downtime and improve overall operational efficiency.
The push toward additive manufacturing will likely lead to integration between electric metal spinning and 3D printing technologies. This integration could enable manufacturers to produce hybrid components that combine traditional spinning methods with 3D printed features, such as internal geometries that would be impossible to create with conventional methods. This synergy could open new doors for customization, creating unique parts that are lighter, stronger, and more efficient.
Looking ahead, the future of electric metal spinning machines will be shaped by continued technological innovations and a focus on adaptability, efficiency, and sustainability. As manufacturing industries embrace smart manufacturing, digital twins, and artificial intelligence (AI), electric metal spinning machines will be equipped to meet the increasing demands for high-precision, complex parts. The ability to quickly adjust to new materials, manufacturing techniques, and production volumes will make these machines an indispensable part of modern manufacturing processes. Furthermore, as industries push for faster production times, reduced costs, and more sustainable operations, the demand for electric metal spinning machines will continue to grow, making them an essential tool in the future of advanced manufacturing.
As the field of electric metal spinning continues to evolve, it is likely that we will see further miniaturization of these machines, making them more suitable for applications in smaller-scale manufacturing environments. This could be particularly useful for industries that require high-precision components on a smaller scale, such as medical device manufacturers or those producing components for consumer electronics. By reducing the size and complexity of the machines without sacrificing performance, electric metal spinning machines could cater to both high-volume and low-volume production needs. This flexibility will allow manufacturers to remain competitive in a rapidly changing market where customization and adaptability are becoming increasingly important.
Another exciting development could be the integration of wireless technology and cloud computing in electric metal spinning machines. Wireless connectivity would allow for remote control, diagnostics, and monitoring of the machines, giving manufacturers the ability to manage their production processes from anywhere in the world. This level of connectivity could also facilitate data sharing between machines, production lines, and different facilities, enabling a more connected and streamlined manufacturing process. Additionally, the use of cloud-based software would allow manufacturers to store and analyze vast amounts of production data, helping to optimize processes and predict maintenance needs. This data-driven approach could result in more efficient operations, faster problem-solving, and greater uptime.
The development of hybrid production systems that combine electric metal spinning with other forming techniques could also become more prevalent. For example, incremental forming and laser-assisted spinning could be integrated with electric spinning to improve the forming process, especially for materials that are difficult to work with using traditional spinning methods. This hybrid approach would provide manufacturers with even more flexibility, enabling them to produce a wider variety of parts with more complex geometries while maintaining high precision and minimal material waste.
In the realm of smart tooling, the future of electric metal spinning machines could see even more advanced adaptive tooling systems. These systems could automatically adjust to different materials and geometries during the spinning process. For example, sensors embedded in the tooling could detect the type of material being used and adjust the pressure, speed, and other parameters accordingly. This adaptability would allow manufacturers to seamlessly work with a broader range of materials, from softer metals to high-strength alloys, without the need for constant recalibration or tooling changes. This could further increase the versatility of electric metal spinning machines, making them suitable for even more specialized applications.
Advanced material research will also play a key role in the development of electric metal spinning machines. As new materials are developed, particularly lightweight alloys, composite materials, and nanomaterials, electric spinning machines will need to adapt to these materials’ specific properties and challenges. Manufacturers will need to invest in technology that allows them to spin these advanced materials without compromising on quality or precision. This could lead to the development of new spinning techniques or the adaptation of existing machines to handle these innovative materials more effectively.
The future of electric metal spinning machines will also likely be influenced by the rise of personalized manufacturing and direct-to-consumer production. As 3D printing and other digital fabrication techniques become more common, manufacturers are beginning to explore the possibility of producing custom, made-to-order products on demand. Electric metal spinning machines, with their ability to produce high-precision parts in small batches, could play an important role in this shift toward mass customization. Consumers may be able to specify their own designs for components, and electric metal spinning machines could be used to produce them with high accuracy and speed, reducing waste and lead times in the process.
Moreover, as the demand for sustainability continues to increase across all industries, the role of electric metal spinning machines in closed-loop manufacturing systems may become more prominent. In these systems, scrap metal and other byproducts from the spinning process can be recycled and reused in the production of new parts. Electric spinning machines, with their precise material usage and minimal waste production, can be integral to such systems, helping manufacturers reduce their reliance on raw materials while also minimizing their environmental impact.
The potential to integrate additive and subtractive manufacturing processes could also lead to more efficient production workflows. Electric metal spinning machines could be used in combination with laser cutting, milling, or 3D printing to create complex, multifunctional parts. For instance, an electric metal spinning machine could form the base structure of a part, while additive manufacturing could be used to print fine details or internal structures that are impossible to form through traditional spinning techniques. This hybrid manufacturing approach could enable faster prototyping, more flexible production, and the ability to create parts with unique material properties.
Additionally, as industries like aerospace, automotive, and renewable energy continue to push for lighter, stronger, and more efficient parts, electric metal spinning machines will likely need to keep pace with these demands by integrating advanced simulation tools. These tools can simulate the behavior of materials under various forming conditions, predicting potential issues before they occur and allowing manufacturers to adjust parameters accordingly. With this level of preemptive insight, the production process will become more efficient, and the likelihood of defects or material failure will be minimized.
The potential for integration with other advanced manufacturing technologies like robotics, AI, and machine learning offers another exciting avenue for the future. Electric metal spinning machines could be paired with robotic arms for automated handling and AI-driven optimization algorithms that continuously improve the production process based on historical data. Machine learning models could predict the best parameters for each part based on factors such as material type, geometry, and desired finish, which would allow operators to fine-tune the process for maximum efficiency.
Finally, the evolution of global supply chains and distributed manufacturing models will drive the need for more flexible and adaptable production systems. Electric metal spinning machines, particularly those with advanced CNC and automation capabilities, will be able to cater to these decentralized models, enabling manufacturers to quickly adapt to changes in demand, supply, and production capacity. As supply chains become more dynamic, electric metal spinning machines will enable companies to produce high-quality, custom parts on demand, reducing lead times and improving overall responsiveness to customer needs.
In conclusion, the future of electric metal spinning machines is filled with exciting possibilities, from increased energy efficiency and precision to the integration of smart technologies and new materials. As industries continue to demand more advanced, adaptable, and sustainable manufacturing solutions, these machines will play a pivotal role in shaping the future of precision metal forming. Their ability to evolve with emerging trends, such as smart manufacturing, advanced materials, and mass customization, will ensure that electric metal spinning machines remain a vital tool in the production of high-quality, complex components across a variety of industries.
Pneumatic Metal Spinning Machine
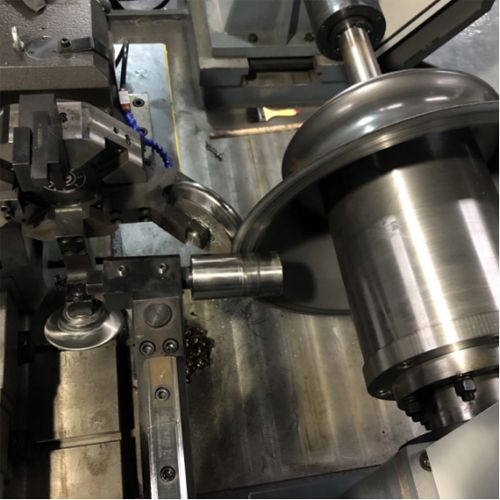
A pneumatic metal spinning machine is a type of metal forming equipment that uses compressed air to power the various movements required in the metal spinning process. Unlike traditional mechanical or hydraulic metal spinning machines that rely on mechanical drives or hydraulic pressure, pneumatic metal spinning machines utilize the force generated by compressed air to rotate the metal workpiece and apply shaping pressure through specialized tooling.
Key Features of Pneumatic Metal Spinning Machines:
- Compressed Air Power: The primary power source for pneumatic metal spinning machines is compressed air, which is supplied by an air compressor. This air is directed to pneumatic cylinders that control the movement of the machine’s components, including the spindle, tool carriage, and other critical parts. The use of compressed air provides a smoother, more consistent force compared to mechanical systems.
- Lightweight and Compact: Pneumatic systems are often lighter and more compact than hydraulic or mechanical systems. Since they do not require heavy hydraulic pumps, fluid reservoirs, or mechanical gear systems, pneumatic metal spinning machines tend to be more space-efficient, making them suitable for smaller workshops or environments with limited floor space.
- Variable Pressure Control: Pneumatic systems allow for precise control of the air pressure, which directly impacts the shaping force applied to the metal sheet. This enables operators to adjust the pressure according to the material being used or the complexity of the part being formed. The ability to fine-tune the air pressure allows for greater flexibility in working with different metals and part geometries.
- Fast Response Time: Pneumatic systems can react quickly to changes in pressure, allowing for faster adjustments during the spinning process. This quick response time is especially useful for production environments where high-speed operations and minimal downtime are critical.
- Reduced Maintenance: Pneumatic metal spinning machines generally require less maintenance compared to hydraulic or mechanical machines because they have fewer moving parts and no need for fluid reservoirs, pumps, or motors. The absence of hydraulic fluid eliminates the risk of leaks and reduces the need for regular oil changes, leading to lower operational costs.
- Energy Efficiency: Pneumatic systems can be more energy-efficient than hydraulic systems, as they use air to power the machine, which is generally less energy-intensive than hydraulic pumps and motors. However, energy efficiency can vary depending on the size of the compressor and the machine’s specific design.
- Safety and Cleanliness: Since pneumatic systems do not rely on oils or fluids like hydraulic systems, there is less risk of contamination or leaks. Additionally, compressed air is non-toxic and does not present the same environmental risks associated with hydraulic fluids. The use of air-powered systems can contribute to a cleaner and safer working environment.
- Control Precision: Pneumatic metal spinning machines often incorporate digital controls or CNC (Computer Numerical Control) systems that allow for precise adjustments to air pressure, rotational speed, and tool positioning. This level of control ensures high precision, repeatability, and consistency in the production of parts.
Applications of Pneumatic Metal Spinning Machines:
- Aerospace: Pneumatic metal spinning machines are used in aerospace to create lightweight, high-strength components such as turbine housings, air ducts, and housings for avionics and engine parts. The ability to produce parts with high precision and minimal material waste is crucial in the aerospace industry.
- Automotive: In the automotive industry, pneumatic metal spinning machines are used to produce components such as exhaust parts, fuel tanks, and wheel covers. The speed and precision of pneumatic machines are advantageous in mass production and assembly line environments.
- Consumer Electronics: Pneumatic metal spinning machines can be used to manufacture components for consumer electronics, such as casings for devices, control panels, and housings for sensors. These parts often require precision and a high-quality surface finish, which pneumatic machines can deliver.
- Medical Devices: The medical industry often requires precision metal components, such as casings for medical instruments, surgical tools, and implants. Pneumatic metal spinning machines can be used to create these parts with the necessary tolerances and surface quality.
- Energy and Power Generation: Pneumatic metal spinning machines are used in the energy sector to create parts such as turbine blades, pressure vessels, and reactor components. These parts require high strength and resistance to heat, making pneumatic metal spinning an ideal method for their production.
- Decorative and Household Items: Pneumatic metal spinning machines are also used in the production of decorative items, such as metal bowls, lamps, and lighting fixtures, as well as household items like cookware. The ability to create consistent and aesthetically pleasing designs is a major advantage for these applications.
Advantages of Pneumatic Metal Spinning Machines:
- Simplicity and Cost-Effectiveness: Pneumatic systems are relatively simple compared to hydraulic or mechanical systems, which often require more complex setups and more expensive maintenance. Pneumatic metal spinning machines tend to be more affordable in terms of both initial cost and ongoing maintenance.
- Cleaner Operation: Without the need for hydraulic fluids, pneumatic machines operate with less mess and fewer risks of leaks, which contributes to a cleaner working environment. The absence of oil-based fluids also makes pneumatic machines more environmentally friendly.
- Energy Efficiency: Pneumatic systems are generally more energy-efficient than hydraulic systems, especially in smaller machines. They require less power to operate and can help reduce overall energy consumption in manufacturing facilities.
- Flexibility and Speed: The speed of pneumatic systems and their ability to quickly adjust pressure and rotational speed make them suitable for high-speed production environments. This flexibility allows manufacturers to meet the demands of fast-changing markets.
- Minimal Downtime: Pneumatic metal spinning machines typically require less maintenance than hydraulic or mechanical systems, leading to less downtime and greater productivity. This is particularly important for high-volume production environments where continuous operation is essential.
- Enhanced Safety: The absence of hydraulic fluids and the relatively simple design of pneumatic systems contribute to a safer operating environment. Pneumatic machines are generally safer to operate, as there are fewer risks related to fluid leaks, overheating, or mechanical failures.
- Easier Operation and Training: Pneumatic metal spinning machines tend to be easier to operate and require less specialized training compared to more complex hydraulic or mechanical systems. The simplicity of pneumatic systems makes them more accessible to operators, reducing the learning curve and increasing overall productivity.
Limitations of Pneumatic Metal Spinning Machines:
- Limited Force for Heavy-Duty Applications: While pneumatic systems are highly effective for smaller-scale and precision applications, they may not provide the same level of force as hydraulic or mechanical systems. For larger or more complex parts that require significant forming force, a pneumatic machine might not be ideal.
- Dependence on Air Supply: Pneumatic machines rely on a continuous supply of compressed air, which can be a limitation if the air compressor is not adequately sized or if there is an interruption in the air supply. Ensuring a consistent and reliable air supply is essential for maintaining machine performance.
- Potential for Air Loss: In some cases, pneumatic systems can suffer from air loss due to leaks in the system, which can affect the performance of the machine. Regular maintenance and checking of air lines and seals are necessary to ensure that the system operates optimally.
- Lower Precision for Complex Parts: While pneumatic machines offer good precision for many applications, they may not be able to achieve the same level of detail or fine control as CNC machines or more advanced hydraulic systems. For very intricate or tight-tolerance parts, other systems may be more appropriate.
Conclusion:
Pneumatic metal spinning machines are an excellent option for many metal forming applications where energy efficiency, simplicity, and a cleaner operating environment are priorities. They offer benefits such as reduced maintenance costs, fast response times, and ease of operation, making them ideal for industries like aerospace, automotive, consumer electronics, and medical device manufacturing. While they may not be suitable for all types of parts, particularly those requiring extremely high forming forces or complex geometries, pneumatic metal spinning machines provide a cost-effective and reliable solution for a wide range of manufacturing needs. As technology continues to improve, pneumatic systems will likely become even more refined and capable, further expanding their applications in the manufacturing industry.
Pneumatic metal spinning machines represent an effective solution for manufacturers looking to balance performance, simplicity, and cost-efficiency in their production processes. With their reliance on compressed air, these machines are well-suited for various industries that require precision, reduced maintenance costs, and a cleaner environment. Although pneumatic systems may not always provide the same force as hydraulic or mechanical systems, their ability to create high-quality products at a lower cost makes them a popular choice for smaller-scale production runs and industries focused on rapid turnaround times. Their lightweight design, ease of operation, and reduced energy consumption make them ideal for businesses aiming to minimize operational costs while maximizing throughput.
In addition, the use of pneumatic systems helps streamline the production process by offering a smooth, consistent application of force, which is crucial for producing complex shapes with minimal waste. The system’s flexibility allows operators to easily adjust air pressure to meet the specific requirements of the material being used and the design specifications of the part. This adaptability makes pneumatic metal spinning machines particularly useful in producing small to medium-sized parts, especially in industries like automotive, aerospace, and consumer electronics, where high-precision and customizability are key.
The overall effectiveness of pneumatic metal spinning machines is closely tied to their maintenance and air supply. Regular checks on the compressed air system, along with routine maintenance to address any leaks or system inefficiencies, ensure continued machine performance. These systems offer reliability and consistency, even with prolonged use. As manufacturers continue to push for more sustainable practices, pneumatic metal spinning machines stand out due to their ability to run cleanly and without the environmental concerns associated with hydraulic fluid-based machines.
In industries where reducing downtime is critical, the pneumatic system’s rapid response time is another advantage, enabling quick adjustments during production without major interruptions. Furthermore, the simplicity of pneumatic controls reduces the need for complex training, making it easier for operators to get up to speed and manage the machines with minimal learning curves.
Looking to the future, advancements in pneumatic technology and the integration of smart systems could further enhance the capabilities of pneumatic metal spinning machines. The incorporation of sensors, machine learning, and real-time monitoring systems could provide even more precise control over the production process. These innovations could lead to smarter machines that automatically adjust parameters based on material behavior, improving both the efficiency and quality of the produced parts.
Pneumatic metal spinning machines are expected to remain a key part of the broader trend toward automation and more efficient manufacturing, offering an accessible and reliable option for companies looking to balance cost, quality, and flexibility. As industries demand faster production times, customization, and sustainable practices, pneumatic systems will likely continue to evolve, maintaining their place as an essential tool in the metal forming landscape. Their ability to adapt to new materials and technologies, coupled with their inherent advantages in cost, efficiency, and environmental impact, makes pneumatic metal spinning machines an attractive option for a wide range of applications across many sectors.
As manufacturing technology continues to evolve, pneumatic metal spinning machines are likely to become even more integrated with modern advancements such as Industry 4.0 and smart manufacturing. These machines, with their ability to operate efficiently in smaller-scale environments, will be essential in the shift towards decentralized production and on-demand manufacturing. The integration of IoT (Internet of Things) sensors into pneumatic systems will enable real-time data collection, which can be used for predictive maintenance, process optimization, and remote diagnostics. With sensors monitoring key performance indicators such as air pressure, temperature, and machine speed, manufacturers will be able to predict potential issues before they lead to downtime, increasing the overall reliability of the production system.
The data collected from pneumatic metal spinning machines can also be fed into centralized databases or cloud-based platforms where machine learning algorithms can analyze patterns and optimize machine settings automatically. This would allow operators to focus more on the creative and complex aspects of the manufacturing process while ensuring the system operates at peak efficiency. Furthermore, automated quality control systems could be employed to continuously monitor the output of the pneumatic machines, ensuring that each component meets the required specifications without the need for manual inspection. This will not only improve the quality of products but also enhance the overall throughput and productivity of the facility.
One of the significant advantages of pneumatic metal spinning is its adaptability in small to medium-scale production runs. In industries where low-volume, high-mix production is the norm, pneumatic systems allow for faster setup times and easier reconfiguration for different part geometries. The machines can easily be adjusted to handle different material types, thicknesses, and shapes, making them a versatile choice for industries such as aerospace, automotive, medical devices, and consumer electronics.
Moreover, as the global demand for customized and personalized products continues to rise, pneumatic metal spinning machines are well-positioned to support mass customization. Their ability to produce unique, custom parts on-demand, without requiring extensive retooling or significant lead times, allows manufacturers to meet specific customer needs with greater flexibility. This is particularly valuable in markets like consumer electronics, where customers demand increasingly personalized products with customized features and designs.
The demand for sustainability in manufacturing is also pushing the adoption of pneumatic metal spinning machines. These machines are naturally more energy-efficient compared to their hydraulic counterparts, as they consume less energy to operate. Additionally, the ability to use compressed air in the production process reduces the environmental footprint of the operation by minimizing the reliance on hydraulic fluids, which can be hazardous to the environment and require special disposal processes. By incorporating recyclable materials and eco-friendly practices, pneumatic metal spinning can contribute to the broader movement toward green manufacturing.
The evolving demand for lightweight materials and high-performance alloys in industries like aerospace and automotive further boosts the relevance of pneumatic metal spinning machines. As these industries continue to prioritize fuel efficiency and cost-effectiveness, the need for precision in shaping advanced materials is paramount. Pneumatic systems can provide the fine control necessary to form complex geometries with these challenging materials, ensuring that both strength and lightness are maintained in the final parts.
Furthermore, collaborative robots (cobots) are increasingly being integrated with pneumatic metal spinning machines to automate material handling, loading, and unloading tasks. These cobots, equipped with advanced sensors and AI-driven controls, work alongside human operators to streamline the production process, reduce manual labor, and minimize the risk of injury in hazardous environments. As cobots become more widely used, they could contribute significantly to improving the efficiency and safety of pneumatic metal spinning operations.
The future of pneumatic metal spinning machines also involves further innovation in tooling technology. As manufacturers push for more intricate, high-precision designs, pneumatic machines will likely be paired with advanced tooling systems that allow for greater customization and adaptation to different materials and geometries. The integration of laser-assisted forming, incremental forming techniques, or additive manufacturing could expand the capabilities of pneumatic spinning machines, enabling them to produce even more complex parts with ease.
Additionally, the development of next-generation pneumatic valves and actuators will further enhance the performance of these machines. More responsive and energy-efficient components will enable precise control over the application of force and rotation during the spinning process. This will help address challenges in creating parts with complex shapes, smooth surfaces, and minimal distortion.
In the context of global manufacturing trends, pneumatic metal spinning machines will become increasingly important as businesses seek to remain competitive in a fast-paced, global market. Their ability to offer precise, efficient, and sustainable production processes while maintaining flexibility in response to changing demands will ensure their place in the future of manufacturing. Whether used in large-scale production or specialized applications, pneumatic metal spinning machines will continue to support industries that rely on high-quality, precision-formed metal parts, making them a cornerstone of modern metalworking.
As the industry moves forward, the continued automation, integration with digital technologies, and focus on sustainability will drive the evolution of pneumatic metal spinning machines, enabling them to meet the growing demands for customized, high-performance components while minimizing environmental impact and maximizing operational efficiency.
Double-Action Metal Spinning Machine
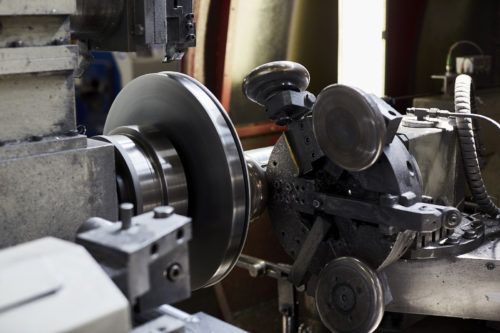
A double-action metal spinning machine is a specialized type of metal spinning equipment that is designed to work with metal sheets and form them into complex shapes using two separate actions. The term “double-action” refers to the fact that the machine uses two independent motions: one for rotating the metal workpiece and another for applying pressure to shape the metal. This method provides higher precision and allows for the creation of more intricate and detailed shapes compared to single-action spinning machines.
Key Features of Double-Action Metal Spinning Machines:
- Dual Motion Mechanism: The defining feature of double-action metal spinning machines is their dual-motion mechanism. One motion involves the rotation of the metal workpiece, while the second action involves the movement of a forming tool or mandrel that applies pressure to the metal to shape it. The rotation of the workpiece creates the necessary centrifugal force for forming, while the second motion provides the pressure required to mold the metal into the desired shape.
- Improved Precision: Double-action machines are ideal for producing parts with high precision, as the two actions allow for better control over the shape and thickness of the final product. The ability to control the pressure applied during the spinning process is crucial for achieving consistent results and meeting tight tolerances.
- Complex Shapes: The ability to apply two independent motions allows double-action metal spinning machines to produce more complex shapes that are difficult or impossible to achieve with single-action machines. This makes them suitable for industries that require intricate, detailed, or custom parts, such as aerospace, automotive, and medical device manufacturing.
- Tooling and Mandrel Use: Double-action machines often incorporate specialized tooling or mandrels that are used to support the metal during the spinning process. The mandrel serves as a template or guide that ensures the metal is formed into the correct shape. The forming tool applies pressure to the metal, pushing it over the mandrel and creating the desired geometry.
- Enhanced Material Forming: The double-action mechanism allows the machine to apply more force to the material, which is particularly useful when working with harder metals or thicker materials. This capability helps to reduce the risk of material tearing or distortion, ensuring a more consistent and reliable result.
- Customization of Parameters: Many double-action metal spinning machines offer the ability to adjust the pressure and rotational speed independently, which provides greater flexibility in forming different materials or parts. The ability to customize these parameters helps manufacturers adapt the machine to various types of metals, thicknesses, and shapes, improving versatility.
- Automation Options: Modern double-action spinning machines can be equipped with CNC (Computer Numerical Control) systems for automated control. This allows for precise adjustments during the spinning process and the ability to replicate complex designs with consistent quality. CNC control is especially valuable for high-volume production or when creating parts with intricate patterns or geometries.
Applications of Double-Action Metal Spinning Machines:
- Aerospace: Double-action metal spinning machines are commonly used in aerospace to produce complex components such as turbine housings, engine parts, and other high-precision metal parts. The ability to create strong, lightweight components with high accuracy is essential in this industry.
- Automotive: In the automotive industry, double-action spinning machines are used to produce parts like wheel covers, exhaust systems, and fuel tanks. These parts often require a combination of strength, flexibility, and precision, making the double-action system ideal for their production.
- Medical Devices: Medical devices such as surgical instruments, implants, and casings for medical equipment often require precise metal forming to meet strict regulatory standards. Double-action spinning machines are used to create these components with the necessary accuracy and surface finish.
- Consumer Electronics: Double-action spinning machines can be employed to create housings for electronics, including casings for phones, sensors, and control panels. The high precision provided by double-action machines ensures that these parts meet the required specifications for fit, function, and appearance.
- Energy: In the energy sector, double-action metal spinning machines are used to create components such as pressure vessels, reactor parts, and turbine blades. These parts often require both high strength and resistance to extreme conditions, which can be achieved through careful control of the spinning process.
- Lighting Fixtures and Decorative Items: Double-action metal spinning machines are also used to produce decorative items like lighting fixtures, metal bowls, and other intricate metal products that require high-quality finishes and detailed shapes.
Advantages of Double-Action Metal Spinning Machines:
- Increased Precision: The dual-action mechanism provides more control over the shaping process, allowing for the production of parts with higher precision and tighter tolerances. This is especially important when working with complex geometries or materials that require careful handling.
- Ability to Form Complex Shapes: Double-action machines can handle more intricate designs compared to single-action machines. The two separate motions allow for the creation of parts with complex contours, such as deep draws, flanges, or other non-cylindrical shapes.
- Improved Material Handling: The additional force provided by the second action helps to form thicker or tougher materials that may be challenging for single-action machines. This ensures that the metal is formed without tearing or becoming distorted.
- Consistency and Repeatability: With the addition of CNC control, double-action metal spinning machines can achieve consistent results across multiple parts, making them suitable for high-volume production. This repeatability is crucial for industries where every part must meet the same specifications.
- Reduced Material Waste: The precise control over the spinning process helps reduce material waste by ensuring that the metal is formed efficiently and accurately, minimizing the need for additional machining or post-processing.
- Customization and Versatility: The flexibility to adjust pressure, rotation speed, and other parameters makes double-action spinning machines versatile. They can be used for a wide range of materials, shapes, and applications, providing manufacturers with the ability to tailor the process to specific needs.
- Higher Production Speeds: While more complex than single-action machines, double-action machines can still achieve high production speeds, especially when combined with automated controls. This makes them suitable for both low and high-volume production.
Limitations of Double-Action Metal Spinning Machines:
- Complexity and Cost: Double-action machines are more complex and generally more expensive than single-action systems. The added components and more advanced mechanisms can increase both the initial investment and maintenance costs.
- Setup and Adjustment Time: While CNC controls can automate some aspects of the setup, double-action machines still require careful calibration and adjustments to ensure the correct pressure and motion settings. This may result in longer setup times compared to simpler machines.
- Limited Force for Large Parts: While double-action machines are capable of handling complex shapes, they may still face limitations when working with extremely large parts or materials that require very high forming forces. For such applications, other forming methods, such as hydraulic machines, may be more suitable.
- Maintenance Requirements: The added complexity of double-action systems means they may require more frequent maintenance and care compared to simpler machines. Regular inspection of the rotating components and the forming tool mechanisms is necessary to maintain optimal performance.
Conclusion:
Double-action metal spinning machines are an invaluable tool for manufacturers producing parts that require high precision, complex geometries, and consistent results. The combination of dual motion allows for more control over the shaping process, making it possible to create intricate and detailed parts that are essential in industries like aerospace, automotive, and medical devices. Although they come with higher upfront costs and maintenance requirements compared to simpler spinning machines, the benefits they offer in terms of precision, versatility, and repeatability make them a crucial asset for many high-precision manufacturing operations. As technology continues to advance, the integration of CNC controls, automation, and smart manufacturing techniques will further enhance the capabilities and efficiency of double-action metal spinning machines, ensuring they remain a key part of modern metalworking.
Double-action metal spinning machines are crucial for industries that require high precision and complex shapes. The dual-motion mechanism enables manufacturers to achieve better control over the metal-forming process, ensuring that even intricate designs are accurately produced. This versatility makes them indispensable in various sectors, including aerospace, automotive, medical devices, and consumer electronics. The precise shaping capability offered by these machines helps create parts that meet stringent tolerance requirements, reducing material waste and improving efficiency.
The ability to adjust key parameters like pressure and rotational speed independently allows manufacturers to tailor the machine to different materials, thicknesses, and shapes, which is particularly useful in low-volume, high-mix production. Double-action machines are also well-suited for producing parts that require both strength and lightweight properties, such as turbine components or lightweight automotive body parts.
Though more expensive and complex than single-action machines, double-action machines offer better performance, particularly when working with materials that are harder to shape or thicker in thickness. In addition, the incorporation of CNC (Computer Numerical Control) systems has enabled the automation of the spinning process, further enhancing repeatability and precision. This allows manufacturers to replicate complex designs consistently, making it easier to scale production.
As industries evolve and demand for more specialized products increases, double-action metal spinning machines will continue to play a significant role in delivering high-quality, intricate parts. Manufacturers will likely see an increase in demand for machines that combine precision with flexibility, and double-action spinning machines fit this need perfectly. Furthermore, technological advancements, such as the integration of AI-driven tools and automated feedback loops, may further optimize the performance of these machines, ensuring that they remain competitive in a fast-paced manufacturing landscape.
In conclusion, the dual-action metal spinning process offers significant advantages in terms of precision, versatility, and efficiency. These machines provide manufacturers with the ability to produce high-quality, complex metal parts while minimizing material waste and reducing the need for secondary processes. As industries continue to demand more customized and high-performance components, double-action metal spinning machines will remain at the forefront of advanced manufacturing technology, helping to meet the needs of a wide range of applications.
The future of double-action metal spinning machines looks promising, as advancements in materials, automation, and digital technologies will continue to enhance their capabilities. With the increasing demand for customization, high-precision components, and shorter production times, these machines will play an even more critical role in enabling manufacturers to meet these evolving requirements. The trend toward smart manufacturing is also expected to drive improvements in the control systems of double-action machines, making them more efficient, adaptable, and easier to integrate into modern, automated production lines.
One area where double-action metal spinning machines could see further development is in the integration of additive manufacturing techniques. Combining the precision of spinning with the versatility of 3D printing could allow manufacturers to create even more intricate parts or layers with custom shapes and properties that would be difficult or impossible to achieve with traditional methods alone. This hybrid approach could be particularly beneficial for industries like aerospace, where complex geometries and lightweight designs are critical for performance.
Another potential area of improvement is the optimization of the forming tools and mandrels used in double-action spinning. As material science continues to advance, new tools made from stronger, more durable, and wear-resistant materials will likely be developed. These tools could allow for the spinning of harder metals, thicker materials, or new alloys without compromising on precision or surface finish. Enhanced tooling could also reduce the frequency of tool changes, further improving the efficiency of the manufacturing process.
Additionally, advancements in sensor technology will enable more precise monitoring and control of the spinning process. Real-time feedback from sensors could be used to dynamically adjust parameters such as pressure, speed, and tool position, ensuring that the metal is formed to the exact specifications. This would not only improve product quality but also reduce the likelihood of defects or material waste, ultimately lowering production costs.
The growing emphasis on sustainability in manufacturing practices will also drive innovation in double-action metal spinning machines. Manufacturers are increasingly looking for ways to reduce energy consumption, minimize waste, and use more environmentally friendly materials. Pneumatic and electric-powered machines are likely to become more energy-efficient, and the use of recyclable metals and sustainable production methods could become more common.
Moreover, the ability to integrate with digital design tools will likely enhance the customization process. With the rise of parametric design software, double-action metal spinning machines could be directly linked to digital models, allowing for faster transitions from design to production. This could significantly shorten lead times for custom parts, making them more accessible for industries with rapidly changing design requirements.
As industries demand greater flexibility and efficiency, double-action metal spinning machines will continue to evolve to meet these challenges. The adoption of collaborative robots (cobots), which work alongside human operators, could further streamline production by handling tasks like loading and unloading parts or assisting with part inspection. This would not only increase throughput but also reduce the physical strain on operators and increase safety in the workplace.
In summary, the future of double-action metal spinning machines will be shaped by advancements in automation, digital technology, sustainable practices, and material science. These innovations will enhance their capabilities and make them even more essential for the production of high-quality, precision components across a wide range of industries. As manufacturers continue to seek ways to meet the growing demand for customized, high-performance parts, double-action metal spinning machines will remain at the forefront of advanced manufacturing, helping to drive the next generation of products and solutions.
EMS Metalworking Machines
We design, manufacture and assembly metalworking machinery such as:
- Hydraulic transfer press
- Glass mosaic press
- Hydraulic deep drawing press
- Casting press
- Hydraulic cold forming press
- Hydroforming press
- Composite press
- Silicone rubber moulding press
- Brake pad press
- Melamine press
- SMC & BMC Press
- Labrotaroy press
- Edge cutting trimming machine
- Edge curling machine
- Trimming beading machine
- Trimming joggling machine
- Cookware production line
- Pipe bending machine
- Profile bending machine
- Bandsaw for metal
- Cylindrical welding machine
- Horizontal pres and cookware
- Kitchenware, hotelware
- Bakeware and cuttlery production machinery
as a complete line as well as an individual machine such as:
- Edge cutting trimming beading machines
- Polishing and grinding machines for pot and pans
- Hydraulic drawing presses
- Circle blanking machines
- Riveting machine
- Hole punching machines
- Press feeding machine
You can check our machinery at work at: EMS Metalworking Machinery – YouTube
Applications:
Flange-punching
Beading and ribbing
Flanging
Trimming
Curling
Lock-seaming
Ribbing