Cookware polishing machines are specialized equipment designed to achieve high-quality surface finishes on various types of cookware, including pots, pans, trays, and utensils. These machines utilize mechanical abrasion, polishing compounds, and buffing techniques to create smooth, reflective, and aesthetically pleasing surfaces on cookware products. They are commonly used in the cookware manufacturing industry to enhance the appearance, functionality, and marketability of cookware items. Here’s an overview of cookware polishing machines and their operation:
- Machine Types: Cookware polishing machines come in various configurations to accommodate different types of cookware and production requirements. Common types include rotary polishing machines, belt polishing machines, vibratory polishing machines, and robotic polishing systems. Each type offers unique features and capabilities suited to specific applications and production volumes.
- Polishing Heads: Cookware polishing machines are equipped with multiple polishing heads or stations, each containing abrasive wheels, buffing pads, or polishing brushes. These polishing heads may be arranged in a linear or rotary configuration, allowing simultaneous polishing of multiple surfaces or parts.
- Polishing Media: Polishing machines use a variety of polishing media, including abrasive compounds, polishing pads, buffing wheels, and polishing brushes, to achieve the desired surface finish on cookware. The selection of polishing media depends on factors such as the material, shape, and surface finish requirements of the cookware being processed.
- Process Control: Cookware polishing machines feature advanced control systems that allow operators to adjust parameters such as rotational speed, pressure, and polishing time to achieve consistent and uniform polishing results. Some machines may also incorporate automated controls and monitoring systems to optimize process efficiency and quality.
- Material Handling: Cookware polishing machines are designed to accommodate various types and sizes of cookware products. They may feature adjustable fixtures, conveyors, or loading/unloading mechanisms to facilitate efficient material handling and processing.
- Safety Features: Safety is a critical consideration in cookware polishing machines, given the high-speed rotating components and abrasive materials involved. Machines are equipped with safety guards, interlocks, and emergency stop systems to prevent accidents and ensure operator safety.
- Maintenance and Cleaning: Regular maintenance and cleaning are essential to ensure optimal performance and longevity of cookware polishing machines. This may involve routine inspection, lubrication, and replacement of worn components, as well as cleaning of polishing heads, media, and machine surfaces to prevent contamination and maintain polishing quality.
- Quality Assurance: Cookware polishing machines often incorporate quality assurance measures such as inspection systems, feedback mechanisms, and process monitoring to ensure that finished products meet quality standards and customer specifications.
Overall, cookware polishing machines play a vital role in the production of high-quality cookware products by providing efficient and consistent surface finishing solutions. By selecting the appropriate machine type, polishing media, and process parameters, manufacturers can achieve exceptional surface finishes that enhance the value and appeal of their cookware products.
Cookware Polishing

Cookware polishing is a critical step in the manufacturing process aimed at enhancing the appearance, functionality, and marketability of cookware products. Whether it’s pots, pans, pressure cookers, or stainless steel utensils, achieving a smooth, reflective surface finish is essential to meet customer expectations and quality standards. Here’s an overview of the cookware polishing process:
- Surface Preparation: Before polishing, the cookware undergoes thorough cleaning and surface preparation to remove any surface imperfections, residues, or contaminants. This step ensures that the surface is free from debris and ready for polishing.
- Selection of Polishing Equipment: Cookware polishing can be performed using various types of equipment, including rotary polishing machines, belt polishers, vibratory polishers, and robotic polishing systems. The choice of equipment depends on factors such as the type of cookware, production volume, and desired surface finish.
- Polishing Media and Compounds: Different types of polishing media and compounds are used in the polishing process to achieve the desired surface finish. Common polishing media include abrasive pads, buffing wheels, polishing brushes, and abrasive compounds. These materials are selected based on factors such as the material of the cookware and the desired level of polish.
- Machine Setup: The cookware is mounted on the polishing machine, and the appropriate polishing media and compounds are selected and applied to the surface. The machine is set up to control parameters such as rotational speed, pressure, and polishing time to achieve consistent and uniform polishing results.
- Polishing Process: The polishing process begins with the application of polishing media and compounds to the surface of the cookware. The cookware is then subjected to a combination of rotational and reciprocating motion, ensuring uniform contact and material removal across the entire surface. The abrasive particles in the polishing media gradually abrade the surface, smoothing out imperfections and producing a smooth, reflective finish.
- Progressive Polishing: Depending on the desired surface finish, multiple polishing steps may be required, each using progressively finer polishing media and compounds. This progressive approach helps to refine the surface texture, remove any remaining surface irregularities, and achieve the desired level of gloss and smoothness.
- Final Inspection and Quality Control: After polishing, the cookware undergoes thorough inspection to verify the surface finish, dimensional accuracy, and overall quality. This may involve visual inspection, surface profilometry, or other measurement techniques to ensure that the finished cookware meets the specified tolerances and quality standards.
Overall, cookware polishing is a critical step in the manufacturing process that helps to enhance the appearance and functionality of cookware products. By carefully selecting the appropriate polishing equipment, media, and compounds, manufacturers can achieve exceptional surface finishes that meet customer expectations and market demands.
External / Internal Buffing Machine for Pots, Pressure Cookers and SS Cookware
External and internal buffing machines for pots, pressure cookers, and stainless steel (SS) cookware are specialized equipment designed to achieve high-quality surface finishes on both the outer and inner surfaces of cookware products. These machines utilize buffing wheels, polishing compounds, and abrasives to create smooth, reflective, and aesthetically pleasing surfaces on cookware items. Here’s an overview of external and internal buffing machines for cookware:
- External Buffing Machines:
- Machine Design: External buffing machines for cookware are designed to polish the outer surfaces of pots, pressure cookers, and other cookware items. They may feature rotating buffing wheels, belts, or brushes arranged in a linear or rotary configuration to polish the external surfaces of the cookware.
- Buffing Heads: These machines typically include multiple buffing heads or stations equipped with abrasive wheels, buffing pads, or polishing brushes. The buffing heads may be adjustable to accommodate different cookware sizes and shapes.
- Process Control: External buffing machines allow operators to adjust parameters such as rotational speed, pressure, and polishing time to achieve consistent and uniform polishing results across the external surfaces of the cookware.
- Material Handling: Cookware items are loaded onto the machine manually or via automated conveyors. The machines may feature adjustable fixtures or clamps to securely hold the cookware during the buffing process.
- Internal Buffing Machines:
- Machine Design: Internal buffing machines are specifically designed to polish the inner surfaces of pots, pressure cookers, and other hollow cookware items. They may feature rotating or oscillating buffing heads, brushes, or abrasive belts to access and polish the internal surfaces of the cookware.
- Tooling: Internal buffing machines use specialized tooling, such as flexible shafts, articulated arms, or robotic end-effectors, to reach into the interior of the cookware and polish hard-to-reach areas.
- Process Control: Similar to external buffing machines, internal buffing machines allow operators to adjust parameters such as rotational speed, pressure, and polishing time to achieve consistent and uniform polishing results on the internal surfaces of the cookware.
- Material Handling: Cookware items are typically loaded onto the machine manually, and the internal buffing tooling is inserted into the cookware to polish the internal surfaces. Some machines may incorporate automated loading/unloading systems for increased efficiency.
- Quality Assurance: Both external and internal buffing machines may incorporate quality assurance measures such as inspection systems, feedback mechanisms, and process monitoring to ensure that finished cookware products meet quality standards and customer specifications.
- Maintenance and Cleaning: Regular maintenance and cleaning are essential to ensure optimal performance and longevity of buffing machines. This may involve routine inspection, lubrication, and replacement of worn components, as well as cleaning of buffing heads, tooling, and machine surfaces to prevent contamination and maintain polishing quality.
Overall, external and internal buffing machines for cookware play a crucial role in the production of high-quality cookware products by providing efficient and consistent surface finishing solutions for both the outer and inner surfaces of the cookware. By selecting the appropriate machine design, tooling, and process parameters, manufacturers can achieve exceptional surface finishes that enhance the value and appeal of their cookware products.
Sunray Finishing Machine for Pressure Cookers and Stainless Steel Parts
Sunray finishing, also known as sunray polishing or sunray brushing, is a specialized surface finishing technique used to achieve a unique aesthetic on stainless steel (SS) products such as pressure cookers, stock pots, and other kitchenware. This process creates a distinctive radial pattern resembling sun rays, which enhances the appearance and visual appeal of the finished product. Here’s an overview of sunray finishing for pressure cookers, SS, and stock pots:
- Surface Preparation: Before the sunray finishing process begins, the surface of the stainless steel pressure cooker, stock pot, or other cookware item is thoroughly cleaned and prepped to remove any dirt, grease, or contaminants. This ensures that the surface is free from imperfections and ready for the finishing process.
- Sunray Brushing Process: The sunray brushing process involves using specialized abrasive brushes or pads to create radial brush marks on the surface of the stainless steel. These brushes are typically arranged in a radial pattern and rotated at high speed, imparting a uniform radial pattern on the surface of the cookware.
- Directional Brushing: The radial brush marks are applied in a consistent direction across the surface of the cookware item, creating a uniform and aesthetically pleasing sunray pattern. The direction of the brushing can be adjusted to achieve different effects, such as more pronounced or subtle sunray patterns.
- Surface Finish Control: The depth and intensity of the sunray pattern can be controlled by adjusting factors such as the rotational speed of the brushing equipment, the pressure applied to the brushes, and the duration of the brushing process. This allows for precise control over the final appearance of the finished product.
- Quality Assurance: Throughout the sunray finishing process, quality assurance measures are implemented to ensure that the finished cookware items meet the desired standards of appearance and quality. This may involve visual inspection, surface profilometry, and other quality control techniques to verify the consistency and uniformity of the sunray pattern.
- Final Inspection and Packaging: Once the sunray finishing process is complete, the finished cookware items undergo a final inspection to ensure that they meet all quality standards and specifications. They are then carefully packaged and prepared for shipping or distribution to customers.
Overall, sunray finishing is a specialized surface finishing technique that adds a unique and visually appealing aesthetic to stainless steel cookware such as pressure cookers, stock pots, and other kitchenware items. By carefully controlling the brushing process and quality assurance measures, manufacturers can achieve consistent and high-quality sunray finishes that enhance the appearance and marketability of their products.
Lid Polishing Machine
A lid polishing machine is a specialized piece of equipment designed to achieve high-quality surface finishes on the lids of various types of containers, such as pots, pans, pressure cookers, and other kitchenware items. These machines utilize polishing techniques to create smooth, reflective, and aesthetically pleasing surfaces on the lids, enhancing the overall appearance and marketability of the finished products. Here’s an overview of a typical lid polishing machine:
- Machine Design: Lid polishing machines are typically equipped with rotating polishing heads or buffing wheels that come into contact with the surface of the lid. The machine may feature multiple polishing stations or heads to accommodate different types of lids and production requirements.
- Polishing Media: The polishing heads or buffing wheels are fitted with abrasive pads, polishing compounds, or buffing brushes to achieve the desired surface finish on the lids. These polishing media come in various grit sizes and compositions to accommodate different lid materials and surface finish requirements.
- Process Control: Lid polishing machines allow operators to adjust parameters such as rotational speed, pressure, and polishing time to achieve consistent and uniform polishing results. Some machines may also feature automated controls and monitoring systems to optimize process efficiency and quality.
- Material Handling: Lids are loaded onto the polishing machine manually or via automated conveyors. The machine may feature adjustable fixtures, clamps, or chucks to securely hold the lids during the polishing process.
- Polishing Process: The polishing process begins with the application of polishing media to the surface of the lid. The lid is then subjected to rotational motion, allowing the polishing heads or buffing wheels to come into contact with the surface and remove any surface imperfections or blemishes. The abrasive particles in the polishing media gradually smooth out the surface, producing a smooth, reflective finish.
- Progressive Polishing: Depending on the desired surface finish, multiple polishing steps may be required, each using progressively finer polishing media. This progressive approach helps to refine the surface texture, remove any remaining surface irregularities, and achieve the desired level of gloss and smoothness.
- Final Inspection and Quality Control: After polishing, the lids undergo thorough inspection to verify the surface finish, dimensional accuracy, and overall quality. This may involve visual inspection, surface profilometry, or other measurement techniques to ensure that the finished lids meet the specified tolerances and quality standards.
Overall, a lid polishing machine is a valuable asset in the production of high-quality kitchenware products by providing efficient and consistent surface finishing solutions for the lids. By carefully controlling machine setup, polishing parameters, and material handling, manufacturers can achieve exceptional surface finishes that enhance the value and appeal of their products.
Lunch Box Polishing
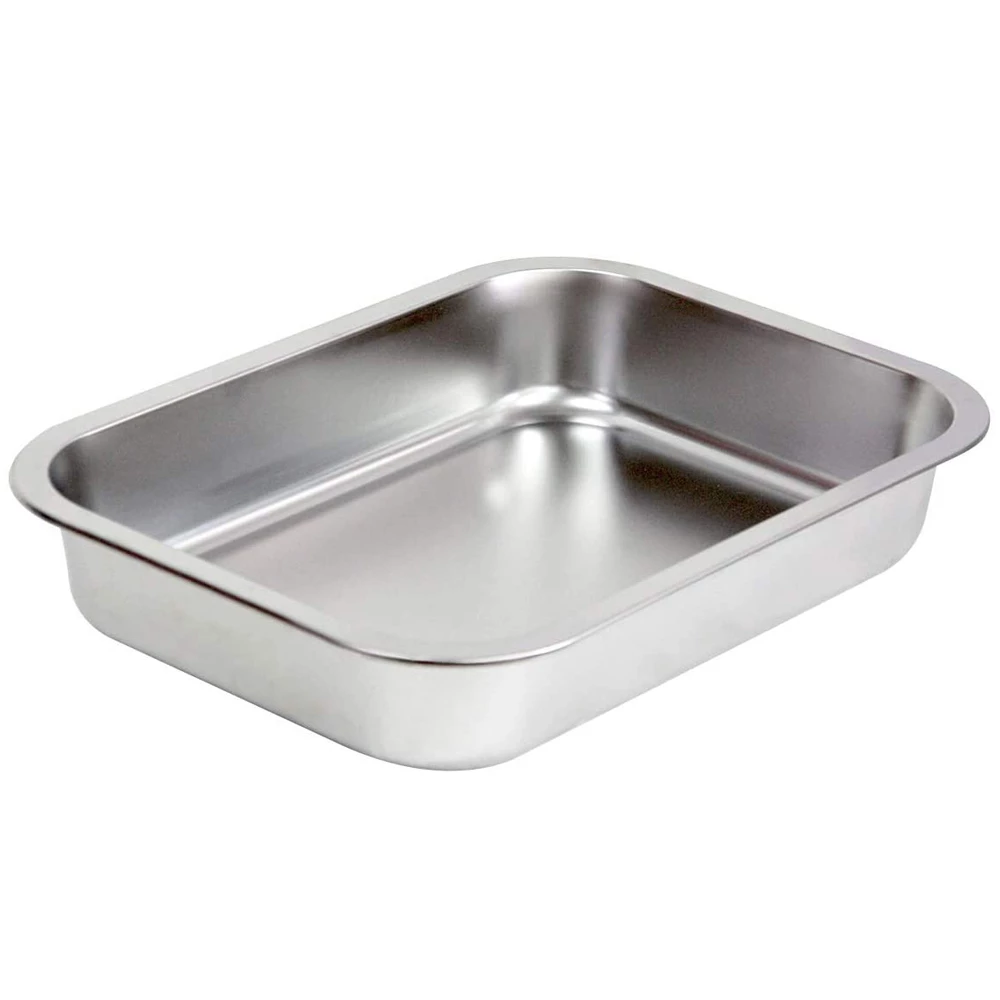
A lunch box polishing machine is a specialized piece of equipment designed to achieve high-quality surface finishes on lunch boxes and other food containers. These machines utilize polishing techniques to create smooth, reflective, and aesthetically pleasing surfaces on the lunch box exteriors, enhancing their appearance and appeal. Here’s an overview of a typical lunch box polishing machine:
- Machine Design: Lunch box polishing machines are typically equipped with rotating polishing heads or buffing wheels that come into contact with the surface of the lunch box. The machine may feature multiple polishing stations or heads to accommodate different types of lunch boxes and production requirements.
- Polishing Media: The polishing heads or buffing wheels are fitted with abrasive pads, polishing compounds, or buffing brushes to achieve the desired surface finish on the lunch boxes. These polishing media come in various grit sizes and compositions to accommodate different lunch box materials and surface finish requirements.
- Process Control: Lunch box polishing machines allow operators to adjust parameters such as rotational speed, pressure, and polishing time to achieve consistent and uniform polishing results. Some machines may also feature automated controls and monitoring systems to optimize process efficiency and quality.
- Material Handling: Lunch boxes are loaded onto the polishing machine manually or via automated conveyors. The machine may feature adjustable fixtures, clamps, or chucks to securely hold the lunch boxes during the polishing process.
- Polishing Process: The polishing process begins with the application of polishing media to the surface of the lunch box. The lunch box is then subjected to rotational motion, allowing the polishing heads or buffing wheels to come into contact with the surface and remove any surface imperfections or blemishes. The abrasive particles in the polishing media gradually smooth out the surface, producing a smooth, reflective finish.
- Progressive Polishing: Depending on the desired surface finish, multiple polishing steps may be required, each using progressively finer polishing media. This progressive approach helps to refine the surface texture, remove any remaining surface irregularities, and achieve the desired level of gloss and smoothness.
- Final Inspection and Quality Control: After polishing, the lunch boxes undergo thorough inspection to verify the surface finish, dimensional accuracy, and overall quality. This may involve visual inspection, surface profilometry, or other measurement techniques to ensure that the finished lunch boxes meet the specified tolerances and quality standards.
Overall, a lunch box polishing machine is a valuable asset in the production of high-quality food containers by providing efficient and consistent surface finishing solutions for the exteriors of lunch boxes. By carefully controlling machine setup, polishing parameters, and material handling, manufacturers can achieve exceptional surface finishes that enhance the value and appeal of their products.
Buffing, polishing, and grinding machines are commonly used in various industries, particularly in metalworking, automotive, and manufacturing, for surface finishing and material shaping. While they all work on similar principles of abrasion or friction, each type has a specific purpose and differs in terms of their operation, abrasives, and applications.
Here’s a breakdown of each type:
1. Buffing Machines
- Purpose: Buffing machines are used to achieve a high-gloss, smooth surface finish. They typically use soft cloth or felt wheels and finer abrasives, which make them suitable for polishing metals, plastics, and other materials.
- Operation: Buffing involves applying a polishing compound (usually a paste or wax) to the material’s surface and then using a rotating cloth or soft wheel to smooth and polish it.
- Common Applications:
- Automotive parts like chrome bumpers, wheels, and exhaust tips.
- Jewelry, watches, and decorative items.
- Some plastic products and components in electronics.
2. Polishing Machines
- Purpose: Polishing machines are used to smooth surfaces to a high degree and may provide a semi-gloss or gloss finish, depending on the materials and processes used.
- Operation: Like buffing, polishing is a process that uses fine abrasives, but the main difference is that polishing can also involve some heavier abrasives, and the wheels might be stiffer than buffing wheels. The goal is to reduce surface imperfections, scratches, and blemishes.
- Common Applications:
- Metal, wood, and stone finishes.
- Optical lenses and glass surfaces.
- Electronics components, like plastic cases or metal housings.
3. Grinding Machines
- Purpose: Grinding machines are used for removing material from a workpiece to shape or finish it, usually with a much coarser abrasive than buffing or polishing. Grinding is commonly used for achieving precise dimensions and smoothing rough surfaces.
- Operation: Grinding machines typically use rotating grinding wheels or abrasive belts that are much harder and rougher than those used for buffing or polishing. The process is often used to remove large amounts of material, especially for applications that require high precision.
- Common Applications:
- Surface grinding for flat, smooth finishes.
- Cylindrical and centerless grinding for cylindrical objects.
- Tool and die manufacturing.
- Sharpening of cutting tools.
Key Differences:
- Buffing: Soft wheels, light abrasives, and a focus on gloss and shine.
- Polishing: More abrasive than buffing but still focuses on smooth surfaces and can range from a satin to a high-gloss finish.
- Grinding: Coarse abrasives, used for material removal, shaping, and precision work.
Buffing, polishing, and grinding machines are essential tools for finishing and shaping surfaces in various industries, such as metalworking, automotive, and manufacturing. These machines differ primarily in the abrasives they use, the nature of the process, and the level of surface finish they achieve.
Buffing machines use soft cloth or felt wheels with fine abrasives to create a high-gloss, smooth finish. The process typically involves applying a polishing compound to the surface and then using the rotating wheel to smooth and shine the material. Buffing is commonly used for metals, plastics, and even jewelry, where a shiny, reflective surface is desired. The main goal of buffing is to enhance the aesthetic appearance of a material.
Polishing machines are similar to buffing machines but tend to use slightly coarser abrasives or stiffer wheels. Polishing is a process that aims to smooth and refine surfaces, often bringing them to a semi-gloss or glossy finish. While polishing still relies on abrasives, it may also involve the use of compounds to reduce imperfections and create a more uniform, smooth surface. This process is frequently used for metals, wood, stone, and even optical lenses where a high-quality finish is important.
Grinding machines are more aggressive and designed for material removal. These machines use hard, rough abrasives like grinding wheels or abrasive belts to shape or smooth a surface, often removing significant amounts of material in the process. Grinding is essential for precision work, such as in tool sharpening, surface finishing of metals, and the production of highly accurate parts. Unlike buffing and polishing, grinding can be used to correct dimensional issues and prepare surfaces for further finishing or assembly.
In summary, while all three machines work with abrasives to alter surface characteristics, buffing and polishing focus more on finishing and improving the appearance of a material, with buffing achieving a high-gloss shine, and polishing providing a smooth, even surface. Grinding, on the other hand, is a more heavy-duty process used to shape, smooth, and dimension materials with much coarser abrasives.
Buffing machines are typically used to achieve a high-gloss, smooth surface finish, especially on softer materials like metals and plastics. They use soft cloth or felt wheels, often loaded with a polishing compound that can be wax-based, abrasive, or chemical. The process works by applying the compound to the surface of the material and then using the rotating wheel to rub and smooth out imperfections, leaving behind a shiny, reflective finish.
The abrasives used in buffing are fine and designed to remove tiny amounts of material from the surface, gradually polishing it to a high luster. Buffing is more about refinement than material removal, so it’s typically done after the initial shaping or rougher finishing steps, like grinding or sanding. The result is a smooth surface free of visible scratches or marks.
Buffing is commonly used in industries where the appearance of the final product is important. For example, automotive parts like chrome bumpers, exhaust tips, and wheels often undergo buffing to achieve that mirror-like finish. Jewelry making also relies heavily on buffing to polish metals like gold, silver, and platinum. Buffing is also employed in the manufacturing of plastic products, where achieving a glossy finish is often a key part of the product’s appeal.
Polishing machines are designed to refine surfaces to a high degree of smoothness, often bringing them to a satin or semi-gloss finish, although they can also achieve a high-gloss result depending on the abrasives and techniques used. Polishing uses finer abrasives compared to grinding, but typically the wheels or pads are slightly stiffer than those used in buffing. Polishing machines can use a range of abrasive materials like polishing compounds, pastes, and powders that help smooth out surface imperfections while also enhancing the material’s appearance.
The key difference between polishing and buffing lies in the level of abrasive used. Polishing is often considered a more controlled, intermediate process. It’s used to eliminate any small scratches or minor blemishes that remain after processes like grinding or sanding, leaving behind a smoother and shinier surface without the aggressive removal of material. While buffing emphasizes the final shine, polishing focuses more on creating an even, uniform surface, making it especially important for applications that require precision.
Polishing machines are used across many industries, including the automotive, aerospace, and metalworking sectors. In automotive production, for instance, polishing is used for creating smooth and shiny finishes on car paint, chrome, and aluminum parts. In the optical industry, polishing is essential for lenses and glasses, where even a minor imperfection could affect functionality. It’s also crucial in the manufacturing of high-end consumer goods, where the final product needs to have a flawless, polished appearance to attract customers.
Grinding machines are used primarily for shaping or finishing materials by removing material from the workpiece. The process is more aggressive than buffing or polishing and typically uses coarser abrasives to achieve precise shapes, smooth surfaces, or remove excess material. Grinding is an essential step in manufacturing processes that require high precision, such as tool sharpening, surface finishing, or part fabrication.
There are several types of grinding machines, each suited for different applications. Surface grinders use a rotating grinding wheel to remove material from the surface of a workpiece, leaving behind a smooth and even finish. Cylindrical grinders are used for grinding cylindrical parts, while centerless grinders are often employed for long, straight workpieces. Additionally, there are also tool grinders, which are used to sharpen tools like drills, cutting tools, and milling cutters.
The grinding process can vary depending on the workpiece material and the required finish. The abrasive materials used in grinding are much harder and coarser than those used in buffing or polishing. These abrasives are mounted on rotating wheels or belts and work by cutting or scratching the material, gradually removing layers of material to refine the shape and surface. Unlike buffing and polishing, grinding can remove significant amounts of material, allowing for precise shaping of complex parts and fine-tuning of dimensions.
Grinding machines are commonly used in industries such as metalworking, tool and die manufacturing, automotive, aerospace, and machining, where precision and surface finish are critical. For example, grinding is often used to achieve exact tolerances in components like engine parts, gears, and bearings. Additionally, grinding machines are used to finish surfaces after casting or forging processes, removing any roughness or imperfections that might affect the performance or appearance of the part.
Centerless Grinding and Polishing Machine
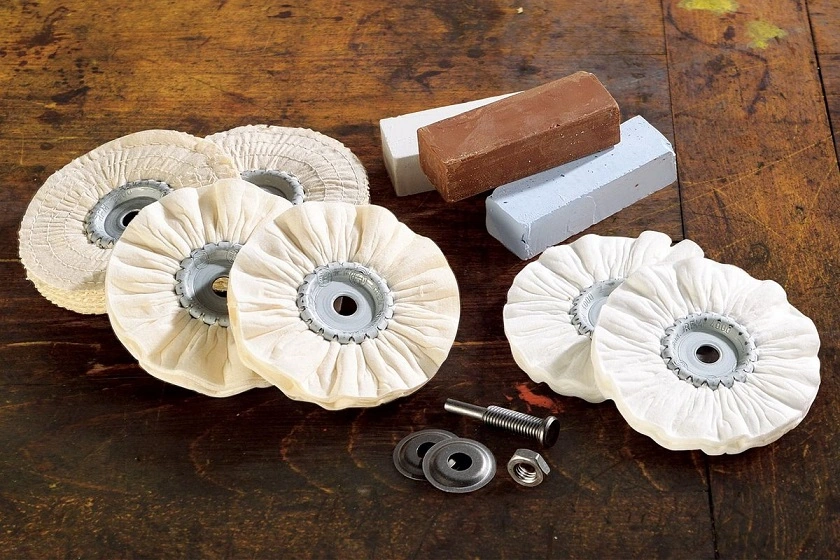
A centerless grinding and polishing machine combines the processes of centerless grinding and polishing into one integrated system, allowing for the efficient processing of cylindrical workpieces. This machine type is especially beneficial when working with long, slender parts or parts with a consistent shape, such as rods, tubes, or shafts.
Centerless Grinding Process:
In centerless grinding, the workpiece is held between two rotating wheels: a grinding wheel and a regulating wheel. The grinding wheel is responsible for removing material from the workpiece to achieve the desired shape or surface finish, while the regulating wheel controls the speed and position of the workpiece. The key advantage of centerless grinding is that the workpiece does not require centers (as in traditional grinding) to hold it in place. This makes it ideal for high-volume production and continuous processing of long parts without the need for frequent setup changes.
Key benefits of centerless grinding:
- High precision: Achieves tight tolerances and smooth surfaces.
- High throughput: The continuous feeding of parts makes it suitable for mass production.
- No need for part holding: The part is supported by the regulating wheel, which reduces setup times and eliminates the need for precise fixture adjustments.
Polishing Process:
In a combined centerless grinding and polishing machine, after the grinding stage, the workpiece often passes through a polishing stage where finer abrasives are applied. The polishing is done using softer polishing wheels or abrasive belts that are designed to smooth out the rough surface left by grinding. Polishing compounds (such as pastes or creams) can be applied to further enhance the surface finish.
The polishing process typically focuses on removing any scratches or minor imperfections caused by the grinding process, resulting in a smooth, shiny, and visually appealing surface. Polishing can also help in removing oxidation or tarnish from metals like stainless steel or aluminum.
Applications:
Centerless grinding and polishing machines are commonly used in industries such as:
- Automotive: For shafts, axles, and other cylindrical components.
- Aerospace: Precision components like rods and tubes are polished for smoother surfaces to reduce wear and improve performance.
- Metalworking: Bars, rods, and tubing are often processed in this way to achieve the required dimensional accuracy and surface finish.
- Medical device manufacturing: Used for polishing and finishing components like needles, pins, and guide wires, where both surface finish and precision are critical.
By combining both grinding and polishing in a single machine, manufacturers can achieve high throughput and improved efficiency, especially when processing large quantities of parts with high-quality surface finish requirements. The system minimizes the need for multiple machines and manual handling, streamlining the production process and reducing costs.
A centerless grinding and polishing machine combines both grinding and polishing functions into a single, integrated system, streamlining the process for high-precision cylindrical parts. The key advantage of centerless grinding is that the workpiece doesn’t require centering or clamping at both ends, as with traditional grinding methods. Instead, the part is placed between two rotating wheels: a grinding wheel that removes material and a regulating wheel that controls the part’s speed and position. This setup allows the part to continuously move through the grinding process, making it ideal for mass production where high throughput and consistency are required.
After the grinding phase, the workpiece typically passes into the polishing stage. This stage uses softer, finer abrasives, often mounted on polishing wheels or abrasive belts. Polishing compounds, such as pastes or creams, are applied to smooth the rough surfaces left by grinding, effectively removing any imperfections, scratches, or oxidation. The result is a smooth, shiny, and aesthetically appealing finish on the part. This is especially important in industries like automotive and aerospace, where both precision and appearance are critical.
Combining both processes into one machine not only improves the speed and efficiency of production but also reduces the need for multiple machines and manual intervention. Parts like shafts, rods, tubes, and pins—commonly used in industries such as automotive, aerospace, and medical device manufacturing—benefit from this method, as they require both high dimensional accuracy and excellent surface finishes. The centerless grinding and polishing machine also minimizes the downtime between processes, as it can efficiently handle both material removal and surface refinement in one seamless operation, making it highly effective for high-volume manufacturing.
The integration of grinding and polishing in a single machine significantly improves efficiency in the manufacturing process. Instead of moving parts from one machine to another for different stages of finishing, a centerless grinding and polishing machine allows for continuous processing, which reduces cycle time and minimizes handling. This seamless transition from grinding to polishing is particularly beneficial when producing high-precision, high-volume parts, as it eliminates the need for multiple setups and adjustments.
By using centerless grinding, manufacturers can achieve tight tolerances and precise dimensions on cylindrical parts, as the regulating wheel helps maintain consistent positioning during the grinding process. Once the desired shape and rough finish are achieved, the polishing stage ensures that the surface is free from imperfections, scratches, and other defects, resulting in a smooth and visually appealing finish.
For industries where high-speed production and consistent quality are critical, this combination of grinding and polishing in a single machine offers several advantages. In automotive manufacturing, for instance, shafts, axles, and other cylindrical components can be processed efficiently, meeting both dimensional requirements and surface finish standards. In the medical industry, precision components like guide wires, pins, and needles can be polished to remove any roughness or irregularities, which is essential for their performance and safety.
Overall, the centerless grinding and polishing machine is an invaluable tool for manufacturers who need to produce parts that not only meet stringent tolerances but also possess a high-quality finish. By reducing the number of machines needed and automating the transition from one process to the next, manufacturers can boost productivity, lower costs, and ensure high consistency across production runs.
The centerless grinding and polishing machine’s ability to streamline the production process offers several operational advantages. By combining both grinding and polishing into a single system, it minimizes the need for manual handling, reduces machine setup times, and accelerates the production cycle. Since both processes are performed in sequence within the same machine, the risk of contamination or damage between different stages is minimized, ensuring that parts maintain their integrity throughout the manufacturing process.
In terms of operation, the machine allows for continuous feeding of workpieces, which is ideal for high-volume production environments. Parts can be fed into the system at a consistent rate, allowing for uninterrupted processing. This is particularly important in industries where large quantities of components need to be produced quickly and with high consistency, such as automotive manufacturing or industrial part production. The machine’s efficiency and automation help reduce labor costs and human error, making it a highly cost-effective solution for manufacturers.
Furthermore, the machine’s design can be adapted to handle various materials, including metals like stainless steel, aluminum, and brass, as well as other materials like plastics and composites. The use of customizable abrasive belts and polishing compounds allows the machine to be tailored to the specific needs of the workpiece, whether it requires a rough grind, a fine polish, or a combination of both. This versatility makes the centerless grinding and polishing machine a valuable tool for a wide range of industries, from metalworking and aerospace to medical device manufacturing and beyond.
The overall result is a high-throughput, high-precision production process that delivers consistent, high-quality parts with minimal downtime or manual intervention. As manufacturing technology continues to evolve, the demand for integrated systems like the centerless grinding and polishing machine is expected to grow, offering even greater productivity and cost savings for businesses that rely on high-volume, precision manufacturing.
CNC Polishing Deburring and Brushing Machine
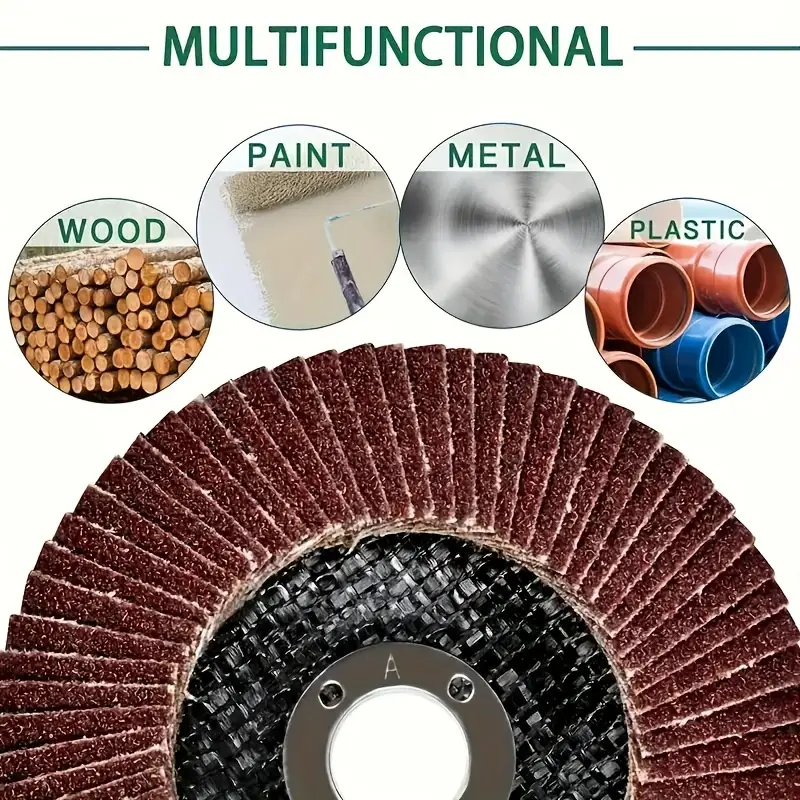
A CNC polishing, deburring, and brushing machine is an advanced automated system designed to perform multiple surface finishing operations, including polishing, deburring, and brushing, all with high precision and repeatability. The use of CNC (Computer Numerical Control) technology ensures that the machine can operate with a high degree of accuracy and consistency, making it suitable for industries that require high-quality surface finishes on complex or delicate components.
CNC Polishing:
In the polishing process, the machine uses abrasives or polishing compounds to smooth and refine the surface of the part. The CNC system controls the speed, pressure, and movement of the polishing tools, ensuring a uniform finish. Polishing helps eliminate surface imperfections such as scratches or oxidation, leaving the workpiece with a smooth, shiny, and aesthetically appealing surface. This is especially important for parts used in industries like automotive, aerospace, medical devices, and electronics, where both appearance and functionality are critical.
CNC Deburring:
Deburring is the process of removing sharp edges, burrs, or any unwanted material that remains after the part has been machined or cut. The CNC deburring system uses abrasive brushes or tools to smooth out rough edges and create a more refined finish. This process is crucial in preventing parts from being damaged during assembly, improving their safety and performance. Deburring is commonly used in industries like automotive, metalworking, and aerospace, where parts must meet strict safety and performance standards.
CNC Brushing:
Brushing involves the use of abrasive brushes to remove contaminants like rust, scale, or oxidation from the surface of the material. It can also be used to create a specific surface texture, such as a satin or matte finish. The CNC-controlled brushing system can adjust the brush’s speed, pressure, and movement to ensure uniformity and consistency across all parts. Brushing is often used in metal finishing to prepare surfaces for further coating, polishing, or as a final step to achieve a specific appearance.
Key Advantages:
- Precision and Repeatability: The CNC technology allows for precise control over all processes, ensuring uniform results across multiple parts.
- Automation: The automation of polishing, deburring, and brushing reduces the need for manual labor, improving efficiency and consistency while minimizing human error.
- Flexibility: CNC machines can be programmed to handle different parts with varying shapes and sizes, making them highly adaptable to different production requirements.
- Reduced Labor Costs: With automation, fewer operators are required, reducing labor costs and improving production speed.
- Surface Quality: The machine can deliver consistent, high-quality finishes that meet the demands of industries requiring precision and smooth surfaces.
Applications:
CNC polishing, deburring, and brushing machines are widely used in industries where surface finishing is crucial. For example, in the automotive industry, they are used to polish and deburr components like engine parts, wheels, and trim. In aerospace, these machines can be used to deburr turbine blades and other precision parts. Medical devices also benefit from these machines, ensuring that components like surgical instruments or implants have smooth, burr-free surfaces to meet stringent safety and regulatory standards.
Overall, CNC polishing, deburring, and brushing machines provide a versatile and efficient solution for high-quality surface finishing, significantly improving the manufacturing process’s speed, precision, and consistency. These machines are a vital part of industries where surface quality directly impacts both performance and safety.
The CNC polishing process in such machines is highly automated and controlled, offering precise adjustments to polishing speeds, pressures, and movements. This allows manufacturers to achieve highly consistent and uniform finishes across a wide range of parts, regardless of complexity or material. The precision afforded by CNC technology eliminates the need for constant manual adjustments, making it especially valuable in production environments where large quantities of parts need to be polished to a specific standard.
The polishing operation itself typically uses various polishing compounds and abrasive materials, which are applied through the machine’s polishing heads. These heads can be fitted with different types of tools depending on the desired finish, such as buffing wheels, abrasive pads, or belts. The flexibility of CNC allows for detailed programming, where each part can have a customized polishing cycle to ensure that the desired aesthetic or functional finish is achieved. Whether the goal is to achieve a mirror-like surface for decorative items or a more functional matte finish for industrial components, CNC polishing provides the versatility to meet diverse requirements.
For industries like automotive and aerospace, where appearance and performance go hand in hand, CNC polishing ensures that parts such as chrome finishes on car exteriors or turbine blades are both visually appealing and free of surface defects that could lead to premature wear or failure. The ability to consistently reproduce a high-quality finish ensures that the final product meets both aesthetic standards and durability expectations, thus enhancing the overall quality of the product and increasing customer satisfaction.
CNC polishing also allows manufacturers to minimize material waste. Since the machine can be precisely programmed to polish the surface without over-polishing or damaging the part, it ensures efficient use of materials and prevents unnecessary loss. This contributes to both cost-effectiveness and the environmental sustainability of the production process. Additionally, this controlled process reduces the need for post-polishing corrective measures, streamlining the entire production workflow.
The CNC deburring process is a critical step in the overall finishing of parts, especially after machining, cutting, or stamping. Deburring involves removing the unwanted edges or material that remains on the part after these processes, known as burrs. Burrs can form due to the cutting action of tools and can pose safety risks, affect the part’s performance, or hinder the assembly process. In a CNC deburring machine, this process is automated, ensuring that each part is consistently treated to remove burrs without damaging the rest of the workpiece.
CNC deburring machines use abrasive tools like brushes, belts, or rotary tools that are precisely controlled through the CNC system. The programming of the machine dictates the speed, pressure, and motion of the deburring tool, ensuring that the burrs are removed without altering the shape or integrity of the part. The deburring process can be adjusted for different materials and part geometries, which is especially useful in industries like automotive or aerospace where parts come in a variety of shapes and sizes and must meet strict dimensional and surface standards.
One of the key advantages of CNC deburring is its ability to handle high volumes of parts with little to no manual intervention. The automation reduces the potential for human error and ensures that each part is consistently deburred to the same standard. This is particularly important for parts that will undergo further processes like assembly or coating, as burrs can interfere with these steps or even cause defects in the final product. Additionally, by ensuring that sharp edges are smoothed out, deburring helps improve the safety of parts, especially in industries like medical device manufacturing, where sharp edges could pose serious risks.
In industries like metalworking, CNC deburring machines are commonly used to treat parts like gears, shafts, and automotive components. Aerospace applications also benefit from CNC deburring, especially for critical parts like turbine blades, where even a small burr can affect performance. By automating this process, manufacturers can significantly improve production speed, reduce costs, and enhance the overall quality and safety of their products.
The CNC brushing process is another essential function in surface finishing, primarily aimed at cleaning, preparing, or texturing the surface of a material. Brushing is typically used for the removal of surface contaminants such as rust, scale, oxidation, and residual particles that may have been left from previous manufacturing steps. It can also be employed to create specific surface textures, such as satin or matte finishes, which are often required in industries that demand both aesthetic appeal and functional properties.
In a CNC brushing machine, abrasive brushes or wire brushes are used to scrub the workpiece surface. The CNC control system adjusts parameters such as speed, pressure, and brushing direction to ensure uniform results across all parts. This allows for precise control over the brushing process, ensuring that the finish is consistent, whether it’s a light cleaning pass or a more aggressive texture creation.
The versatility of CNC brushing makes it useful for a wide variety of applications. For instance, in the metalworking industry, brushing is often used to clean stainless steel, aluminum, and other metals, removing oxidation and preparing the surface for subsequent treatments like coating, polishing, or painting. Automotive manufacturers may use brushing to prepare components like bumpers or trim pieces before further finishing steps. In aerospace, brushing is used to clean parts like turbine blades or engine components, where removing contaminants is crucial for both performance and safety.
Additionally, CNC brushing can be used to achieve a desired surface roughness or texture, which can improve the functionality of the part. For example, creating a slightly textured surface on metal parts can improve their adhesion to coatings, enhance friction for grip applications, or give them a matte aesthetic, which might be desirable in consumer products.
One significant advantage of using CNC-controlled brushing is that it allows for precise control over the finish, ensuring uniformity in high-volume production. The automation involved in CNC brushing also reduces the need for manual labor, minimizes human error, and speeds up the production process. For industries that require a high level of consistency, like medical device manufacturing, where clean and properly textured surfaces are critical for functionality and safety, CNC brushing offers a reliable and efficient solution.
Overall, CNC brushing, alongside deburring and polishing, forms a comprehensive surface finishing system that improves both the appearance and performance of components. By automating these processes, manufacturers can achieve higher precision, reduce labor costs, and ensure a higher level of consistency across large volumes of parts, contributing to overall productivity and product quality.
CNC Belt Grinding and Polishing Machine
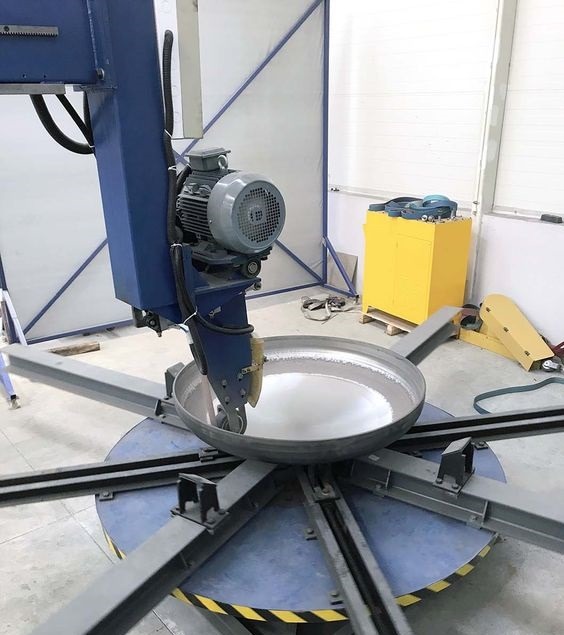
A CNC belt grinding and polishing machine is an advanced piece of equipment designed to perform both grinding and polishing operations using abrasive belts in a fully automated, computer-controlled manner. By integrating both grinding and polishing functions into one system, these machines allow manufacturers to achieve highly precise surface finishes while improving overall production efficiency and consistency. The CNC control system ensures that the process is repeatable, reliable, and optimized for various types of workpieces, materials, and finishes.
CNC Belt Grinding:
In belt grinding, an abrasive belt is used to remove material from the surface of a workpiece. The belt is mounted on rotating drums or pulleys, and as the workpiece is fed into the machine, it comes into contact with the moving abrasive belt. The grinding operation can remove rough material, correct surface irregularities, and shape parts to precise dimensions. CNC technology allows for exact control over the grinding parameters, including speed, pressure, and belt angle, ensuring that the material is removed evenly and efficiently.
CNC belt grinders are often used for high-precision tasks where dimensional accuracy is critical. They are ideal for grinding parts with complex shapes, such as cylindrical, flat, or contoured surfaces. CNC programming allows the machine to adjust settings for different materials—like metals, plastics, or composites—ensuring that each material is treated optimally. The abrasive belts come in various grit sizes, allowing manufacturers to select the right level of abrasiveness for the specific task, from coarse material removal to finer surface finishes.
CNC Belt Polishing:
The polishing stage typically follows grinding in a belt polishing operation, where finer abrasive belts are used to smooth and refine the surface of the part. The goal is to remove any scratches, tool marks, or roughness left from the grinding stage, resulting in a smoother, shinier surface finish. In some cases, a polishing compound may be applied to the belt to enhance the finish further, especially when a high-gloss or mirror-like finish is required.
Just as with the grinding process, CNC control plays a critical role in ensuring consistency during polishing. By adjusting variables such as belt tension, speed, and pressure, the machine can apply the right amount of force to the workpiece to achieve the desired surface finish without over-polishing or damaging the part. This level of control ensures that every part, regardless of size or complexity, receives the same high-quality finish.
Key Benefits:
- Precision and Automation: The CNC system allows for exact control of grinding and polishing parameters, ensuring uniform results across all parts and reducing the likelihood of errors or inconsistencies. This is particularly beneficial for mass production, where high precision and repeatability are essential.
- Versatility: CNC belt grinding and polishing machines can handle a wide variety of materials, including metals like stainless steel, aluminum, brass, and copper, as well as plastics and composites. The abrasive belts can be easily changed, allowing the machine to adapt to different grinding or polishing needs.
- Efficiency: Combining both grinding and polishing into a single machine reduces the need for multiple machines or processes, streamlining the production workflow and reducing downtime. The automated nature of CNC machines also reduces manual labor and minimizes the risk of human error, improving overall productivity.
- Cost Savings: By automating the grinding and polishing processes, manufacturers can reduce labor costs, improve throughput, and lower the cost per part, all while maintaining high-quality surface finishes.
- Surface Finish Control: CNC belt machines offer the ability to control the degree of finish applied to the part, making them highly adaptable for different surface textures. Whether a coarse finish is required for functional purposes or a high-gloss polish is needed for aesthetic appeal, CNC belt grinding and polishing machines can meet those needs.
Applications:
CNC belt grinding and polishing machines are used in a wide range of industries where precise surface finishes and dimensional accuracy are required. Some common applications include:
- Automotive: Grinding and polishing of components such as exhaust pipes, trim pieces, or engine parts.
- Aerospace: Precision grinding and polishing of turbine blades, shafts, and other critical components.
- Medical Devices: Parts like surgical instruments, implants, and medical device housings are ground and polished to meet stringent safety and functional standards.
- Metalworking: Finishing parts like gears, shafts, and other metal components, ensuring they meet tight tolerances and smooth surface finishes.
- Consumer Goods: Polishing of items like kitchenware, jewelry, and decorative metal products to achieve a high-quality appearance.
In conclusion, CNC belt grinding and polishing machines provide an efficient and highly flexible solution for achieving precision surface finishes. With the ability to handle a variety of materials and finishes, the integration of both grinding and polishing in a single machine offers manufacturers significant benefits in terms of quality, productivity, and cost-effectiveness. These machines play a crucial role in industries that require high-quality surface finishes for both functional and aesthetic purposes.
The CNC belt grinding process offers several key advantages, especially when it comes to achieving high-precision material removal. CNC technology enables precise control over the grinding parameters, such as speed, pressure, and belt angle, ensuring that the workpiece is ground evenly and efficiently. The automated nature of the CNC belt grinder eliminates the need for constant manual adjustments, making it ideal for high-volume production environments. It provides consistent results with tight tolerances, which is crucial in industries like automotive, aerospace, and medical device manufacturing, where dimensional accuracy is critical.
The use of abrasive belts allows for flexibility in the grinding process. Depending on the grit size of the belt used, manufacturers can select the appropriate level of abrasiveness for different tasks. For example, coarse belts are ideal for rough grinding and material removal, while finer belts are better suited for achieving smoother finishes. Additionally, CNC belt grinding machines can be easily adjusted to accommodate different shapes and sizes of workpieces, such as cylindrical, flat, or contoured surfaces, further enhancing their versatility.
CNC belt grinding machines are particularly useful for producing parts that require complex geometries or intricate contours. The ability to program the machine for specific part profiles enables manufacturers to grind parts with precision while ensuring minimal material wastage. This process is often used for applications that require a high degree of surface finish, such as in the aerospace industry for turbine blades, or in the automotive industry for engine components and other precision parts.
Moreover, CNC belt grinders can handle a wide range of materials, including metals (such as stainless steel, aluminum, and brass), plastics, and composites. The ability to easily swap out different abrasive belts based on the material being processed makes these machines adaptable to diverse production needs. Whether a manufacturer needs to grind a part made of steel or a delicate plastic component, the CNC belt grinder can be customized to suit the material’s specific characteristics, ensuring an optimal grinding process.
Another significant benefit is the increased productivity that CNC belt grinding machines offer. Since the process is automated, the need for manual labor is reduced, and parts can be ground continuously without significant downtime. This leads to faster production cycles and higher throughput, which is particularly important for manufacturers that produce large quantities of parts. In industries where speed and efficiency are key to maintaining competitiveness, CNC belt grinding machines help meet the demand for high-quality products in a timely manner.
Overall, the CNC belt grinding process plays a vital role in industries requiring precision material removal and surface finishing. By automating the grinding operation and offering flexibility in material and geometry handling, these machines help manufacturers achieve consistent, high-quality results with reduced labor and increased efficiency. This makes CNC belt grinding an essential tool for achieving both functional and aesthetic finishes in a wide range of applications.
The CNC belt polishing process builds upon the precise grinding foundation laid by the CNC belt grinding operation. After the initial grinding phase, which removes larger amounts of material and shapes the part, the polishing process uses finer abrasive belts or specialized polishing compounds to smooth the surface to a high finish. This stage is crucial for achieving a glossy or satin finish, eliminating any visible tool marks, scratches, or roughness from the grinding phase.
The key advantage of CNC belt polishing is the precision with which the polishing parameters are controlled. The CNC system manages variables like belt speed, pressure, angle, and tension, ensuring that the polishing process is applied consistently and uniformly across all workpieces. The fine abrasive belts used during the polishing process are designed to gradually refine the surface, reducing the roughness (Ra) to a level that meets the desired finish standard.
Key Factors in CNC Belt Polishing:
- Adjustable Speed and Pressure: CNC machines can fine-tune the speed of the abrasive belt and the pressure applied to the workpiece. This allows for different levels of finish, from achieving a smooth, matte surface to creating a high-gloss, mirror-like finish.
- Uniformity: The automated nature of CNC polishing ensures that every part is polished uniformly. This consistency is vital for industries like aerospace, where parts like turbine blades need to have an even, polished surface for both aesthetic and performance reasons. In automotive manufacturing, polished parts such as chrome bumpers, wheels, or engine components must meet exacting visual standards.
- Surface Finish Control: CNC belt polishing allows manufacturers to control the level of surface roughness. For example, it can be programmed to produce a satin finish on some parts, which might be desired for aesthetic reasons or to reduce glare, or a high-gloss finish for decorative or functional purposes, such as on jewelry, consumer electronics, or kitchenware.
- Material Compatibility: Like with grinding, CNC belt polishing machines are adaptable to a wide range of materials, including metals, plastics, and composites. The type of abrasive belt used can be varied based on the material being polished, ensuring the best possible finish without damaging the workpiece. For example, soft materials like aluminum may require a different belt type compared to harder materials like stainless steel.
Advantages of CNC Belt Polishing:
- Increased Productivity: The use of CNC systems automates the polishing process, reducing the need for manual labor and significantly improving production speed. Polishing can be performed continuously without interruptions, which is particularly advantageous for high-volume production runs. This leads to faster turnaround times and lower costs per part, making CNC belt polishing machines ideal for industries with high production demands.
- High-Quality Finishes: CNC belt polishing ensures that every part receives a consistent and high-quality finish. The automation eliminates the variability that can come with manual polishing, reducing defects, inconsistencies, and the need for rework. This is particularly important in industries where surface aesthetics and performance are critical, such as in medical device manufacturing, where parts must be free from scratches or defects that could compromise functionality.
- Reduced Waste and Optimal Material Use: Since CNC belt polishing is highly controlled, the process minimizes material waste by applying just the right amount of abrasive power to smooth the surface. Over-polishing or excessive material removal is avoided, which helps optimize material usage, lowers costs, and contributes to more sustainable manufacturing practices.
- Customization for Different Finishes: The ability to adjust parameters like belt tension, speed, and pressure allows CNC belt polishing machines to be highly customizable for various applications. This makes them suitable for a range of finishes, from a light polish to a high-gloss shine, ensuring that manufacturers can meet the specific requirements of each part.
Applications:
- Automotive Industry: CNC belt polishing is used to achieve high-gloss finishes on parts like exhaust systems, chrome trim, and engine components. The process is also used to smooth and polish parts that require both an aesthetic finish and resistance to corrosion, such as fuel injectors and other functional components.
- Aerospace: In aerospace, parts like turbine blades, engine components, and structural elements often require a polished finish to reduce friction, improve durability, and meet stringent visual standards. CNC belt polishing ensures that these components meet both functional and aesthetic criteria.
- Medical Devices: Medical instruments, implants, and devices require a smooth, polished surface to ensure safety, prevent bacterial build-up, and reduce the risk of infections. CNC belt polishing machines help achieve the necessary surface quality, removing any scratches, tool marks, or contamination from the manufacturing process.
- Consumer Goods: CNC belt polishing is used in industries like electronics, furniture manufacturing, and consumer goods to polish metal and plastic parts to a desired finish. For example, smartphone housings, kitchen appliances, and decorative metal objects require a high-quality polish for both appearance and durability.
In conclusion, CNC belt polishing is an essential part of surface finishing for many industries, offering high precision, repeatability, and efficiency. By automating the polishing process, manufacturers can achieve consistent, high-quality finishes with minimal labor and increased throughput, ultimately enhancing product quality and reducing production costs. This process is highly adaptable, making it suitable for a broad range of materials and finishes, which is essential for industries where both aesthetics and functionality are paramount.
The CNC belt grinding and polishing machine integrates multiple processes into one system, offering substantial advantages for modern manufacturing. By combining grinding and polishing in a single machine, manufacturers can streamline operations and reduce the need for separate machinery, which enhances overall efficiency and minimizes production costs. These machines typically feature both rough and fine abrasive belts that can be easily switched out or adjusted for specific tasks, allowing manufacturers to achieve both high material removal and detailed finishing with just one piece of equipment.
Automation and Control:
One of the standout features of CNC belt grinding and polishing machines is the level of automation and control they offer. CNC (Computer Numerical Control) technology allows for precise programming of all parameters involved in both grinding and polishing processes. This includes settings such as:
- Belt speed: Controls the abrasiveness and material removal rate during grinding and polishing.
- Pressure: Ensures the right amount of force is applied to the part to avoid over-polishing or under-polishing.
- Belt tension: Helps maintain the belt’s optimal performance and prevents slippage or uneven results.
- Path control: CNC systems can precisely control the path the workpiece takes through the machine, ensuring that the grinding and polishing are uniform across all surfaces.
This level of control leads to consistent and high-quality results across large production runs. Whether a company is producing hundreds or thousands of parts, each piece can receive the same surface finish without variability, improving the overall quality of the final product.
Precision and Repeatability:
The precision offered by CNC belt grinding and polishing machines ensures that parts are finished to tight tolerances, with little deviation in surface quality. The repeatability of the process is especially beneficial in industries that require strict quality standards. For example, in medical device manufacturing, it is essential that parts like surgical instruments or implants have a smooth, clean finish to prevent complications during use. Similarly, aerospace components like turbine blades and engine parts require precise surface finishes for optimal performance and to meet safety standards.
CNC systems can be programmed to adjust the settings based on the specific requirements of each part. For instance, if different components require different finishes, the machine can be reprogrammed to switch between aggressive grinding and fine polishing cycles. The flexibility of CNC also allows manufacturers to create complex surface finishes on irregularly shaped parts, which is particularly useful in industries like automotive or aerospace where parts often feature complex geometries.
Efficiency and Productivity:
CNC belt grinding and polishing machines contribute significantly to the efficiency of production lines. Since these machines are fully automated, they reduce the need for manual intervention, which minimizes human error and boosts throughput. Operators can load parts into the machine, and once the process begins, the machine runs independently, saving valuable time. This automation also results in reduced labor costs, as fewer personnel are needed to monitor and operate the machinery.
Additionally, the integration of grinding and polishing in one machine further enhances productivity. Traditionally, a manufacturer might need separate machines for grinding and polishing, which can lead to additional time spent transferring parts between processes and handling equipment. By combining both operations in one system, CNC belt grinding and polishing machines eliminate these extra steps and make the overall process faster and more streamlined.
Versatility and Adaptability:
CNC belt grinding and polishing machines are highly versatile and can handle a variety of materials, including:
- Metals: Such as stainless steel, aluminum, brass, and copper, which are commonly used in automotive, aerospace, and industrial applications.
- Plastics: For use in industries like electronics and consumer goods.
- Composites: Including materials used in high-performance industries like aerospace and automotive, where lightweight yet durable materials are essential.
The ability to switch between abrasive belts with different grit sizes allows the machine to adapt to varying levels of material removal and surface finishing. For example, a coarse belt might be used initially for grinding, followed by a finer belt for polishing. This flexibility makes CNC belt grinding and polishing machines suitable for a wide range of applications across multiple industries.
Environmental and Cost Benefits:
Another important benefit of CNC belt grinding and polishing is the reduction of waste material. The automated nature of the machine ensures that the correct amount of material is removed during grinding and polishing, preventing over-polishing, which can lead to unnecessary waste. Additionally, the machine’s precision ensures that each part is processed optimally, reducing the need for rework or reprocessing.
In terms of cost savings, CNC machines are often more cost-effective in the long term compared to manual or less automated processes. Although the initial investment in CNC equipment may be higher, the savings in labor costs, reduced scrap rates, and increased throughput result in a significant return on investment. Moreover, the ability to maintain consistent surface finishes across large production volumes helps manufacturers meet customer demands for high-quality products, leading to improved customer satisfaction and brand reputation.
Applications of CNC Belt Grinding and Polishing Machines:
The versatility of CNC belt grinding and polishing machines makes them suitable for a wide range of industries, including:
- Automotive: Grinding and polishing of components like engine parts, exhaust systems, and trim pieces.
- Aerospace: Precision finishing of turbine blades, engine parts, and structural components.
- Medical Devices: Polishing surgical instruments, implants, and other devices to meet cleanliness and functional standards.
- Consumer Goods: Polishing metal or plastic parts for high-end electronics, jewelry, and home appliances.
- Metalworking: Preparing and finishing metal parts, such as gears, shafts, and machine components, for various industrial applications.
In conclusion, CNC belt grinding and polishing machines offer a highly efficient and precise solution for manufacturers that need to achieve both material removal and fine surface finishes. The integration of both processes into a single automated system not only increases productivity and consistency but also reduces waste and operating costs. With the flexibility to handle a wide range of materials and the ability to fine-tune parameters for each specific task, these machines are an invaluable tool in modern manufacturing, ensuring high-quality results and a competitive edge in the marketplace.
Cookware Polishing Machines
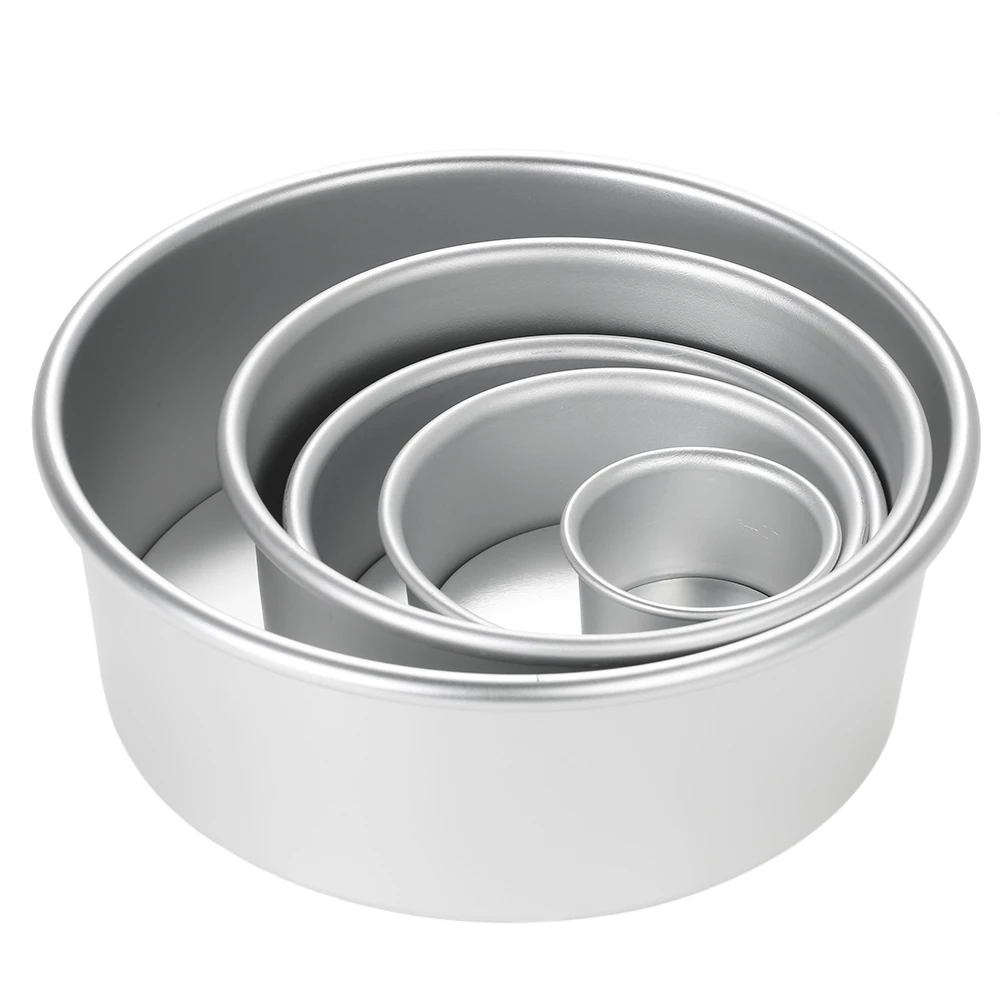
Cookware polishing machines are specialized equipment designed to provide high-quality finishes to cookware items such as pots, pans, utensils, and other kitchenware products. These machines are used in the manufacturing process to improve the appearance of cookware while ensuring smooth, shiny, and durable surfaces. Polishing cookware not only enhances its aesthetic appeal but also plays a vital role in improving its functionality, such as ease of cleaning and resistance to staining or corrosion.
Types of Cookware Polishing Machines:
- Rotary Polishing Machines: Rotary polishing machines are widely used in cookware manufacturing to achieve a high-gloss finish on metal surfaces, particularly stainless steel cookware. These machines utilize rotating abrasive wheels or belts to polish the cookware’s surface. The workpiece is typically placed on a turntable or fixture that spins while the polishing tools move across the surface. The abrasive action removes scratches, dullness, and imperfections, leaving behind a smooth, shiny finish. Advantages:
- Efficient for mass production of cookware.
- Provides a high-gloss finish suitable for premium cookware products.
- Suitable for both small and large cookware items like frying pans, pots, and lids.
- Belt Polishing Machines: Belt polishing machines use continuous abrasive belts that move over the surface of the cookware. The belts come in various grit sizes depending on the required finish. These machines are versatile and can be used for both grinding (material removal) and polishing (smooth finish). The flexibility of belt polishing machines allows them to handle a variety of cookware shapes, from flat pans to deeply contoured pots. Advantages:
- Ideal for continuous production lines due to their speed and efficiency.
- Ability to achieve smooth, satin, or mirror-like finishes depending on belt choice.
- Suitable for a wide range of cookware materials, including stainless steel, aluminum, and non-stick-coated products.
- Centrifugal Polishing Machines: These machines use centrifugal force to polish cookware items, typically smaller or highly detailed parts. The cookware is placed in a rotating drum with abrasive media. The centrifugal action causes the parts to tumble against the media, which polishes the surfaces. This method is ideal for polishing intricate cookware items such as handles, knobs, and other smaller parts that require a detailed finish. Advantages:
- Ideal for polishing intricate or small cookware components.
- Can provide uniform results across all parts, making it suitable for items with complex shapes.
- Less aggressive compared to other polishing methods, minimizing the risk of damage to delicate items.
- Vibratory Polishing Machines: In vibratory polishing machines, cookware items are placed in a container with abrasive media. The container vibrates, causing the cookware and media to rub against each other, leading to a polishing action. This method is used primarily for deburring and polishing small parts, like cookware handles or smaller utensils, rather than large cookware pieces. Advantages:
- Effective for polishing small cookware items or parts.
- Provides a smooth, uniform finish without requiring manual labor.
- Ideal for batch processing, as multiple parts can be polished simultaneously.
- Robotic Polishing Systems: Robotic polishing systems combine automation with advanced polishing techniques. These systems typically use robotic arms equipped with polishing tools such as abrasive pads, brushes, or belts. The robots are programmed to move over the cookware items with high precision, ensuring consistent and uniform polishing results. These systems are particularly useful for large-scale production lines, where a high level of automation is desired. Advantages:
- High precision and repeatability in polishing cookware items.
- Can be integrated into automated production lines, increasing production efficiency.
- Can be programmed for different polishing operations depending on the cookware material and desired finish.
Key Benefits of Cookware Polishing Machines:
- Enhanced Aesthetic Appeal: Polishing improves the visual appearance of cookware, giving it a shiny, reflective surface that is often associated with high-quality products. A polished surface is more attractive to consumers and helps to distinguish cookware in the competitive kitchenware market.
- Increased Durability: Polished cookware is more resistant to rust, stains, and scratches. The smooth surface prevents food from sticking and makes the cookware easier to clean. Additionally, polishing reduces the potential for corrosion, especially in metal cookware like stainless steel and aluminum.
- Improved Food Release: A smooth, polished surface allows for better food release during cooking, which is especially important for non-stick cookware or items with stainless steel surfaces. Polishing helps reduce the friction between food and cookware, making cooking and cleaning more efficient.
- Uniform Surface Finishes: Polishing machines ensure that the finish on cookware is consistent across all pieces. For manufacturers, this uniformity is crucial for branding, as it ensures that every product meets the same high-quality standards.
- Automation and Efficiency: Cookware polishing machines, especially CNC-controlled systems, can work continuously, reducing the need for manual labor. The automation of polishing tasks improves overall productivity and can handle high volumes of production with consistent quality. This is particularly beneficial for manufacturers aiming to meet large-scale demand.
Applications of Cookware Polishing Machines:
- Stainless Steel Cookware: Most cookware items made from stainless steel, such as pots, pans, and kitchen accessories, benefit from polishing. The polishing process helps remove welding seams, scratches, and tarnishing that may occur during the manufacturing process.
- Aluminum Cookware: Aluminum cookware, which often has a matte or dull appearance after casting, can be polished to a shiny, smooth surface. Polishing also improves its resistance to corrosion.
- Non-Stick Coated Cookware: Non-stick pans and pots are polished to ensure the smoothness of the cooking surface, aiding in food release and ease of cleaning.
- Cookware Components: Handles, knobs, lids, and other small components of cookware are also polished for both aesthetic appeal and improved function. These smaller parts benefit from processes like centrifugal or vibratory polishing.
Conclusion:
Cookware polishing machines are integral to the manufacturing process of high-quality kitchenware. They not only enhance the aesthetic appeal of the cookware but also improve its functionality, durability, and ease of maintenance. Whether it’s a high-gloss finish on stainless steel pots or a satin finish on non-stick pans, these machines provide the precision and efficiency necessary for mass production while maintaining high standards of quality.
Cookware polishing machines, by offering high precision and automation, significantly streamline the production process in cookware manufacturing. As industries demand higher productivity and consistent product quality, these machines have become vital to meeting those needs. Their ability to combine both material removal (grinding) and surface finishing (polishing) in one unit makes them especially efficient for high-volume production runs.
Key Features of Cookware Polishing Machines:
- Versatility in Polishing Techniques: Cookware polishing machines can be tailored to deliver various types of finishes, depending on the cookware material and the required final look. For example, stainless steel cookware often requires a mirror finish for aesthetic purposes, while aluminum or cast iron cookware may be polished to a satin or matte finish to enhance durability and ease of cleaning.
- Adjustable Polishing Parameters: These machines are equipped with adjustable settings for belt speed, pressure, and polishing angles. Manufacturers can fine-tune these parameters based on the material of the cookware, the desired finish, and the level of polishing required. Whether polishing large frying pans or smaller utensils, this flexibility ensures that each product is finished to the correct standard.
- High-Volume Production Capability: Since polishing cookware is often part of a continuous production process, having machines that can handle large batches is crucial. Polishing systems like rotary polishing machines and belt grinders are capable of efficiently processing large quantities of cookware in a relatively short amount of time, making them ideal for large-scale manufacturers who need to meet high demand.
- Automated Control Systems: Modern cookware polishing machines often come with advanced CNC controls, which automate the entire polishing process, ensuring repeatable results. These systems are designed to reduce human error and improve consistency, making the polishing process less dependent on operator skill and more on machine programming. Automated polishing systems can be programmed for different types of cookware, optimizing both grinding and polishing steps for each part.
- Efficient Material Handling: Many cookware polishing machines include integrated systems for material handling that move parts automatically through different stages of the polishing process. This system can handle various sizes and shapes of cookware, minimizing downtime and operator involvement. The ability to quickly load, polish, and unload parts ensures an efficient and continuous workflow, critical for meeting tight production deadlines.
- Safety and Ergonomics: Cookware polishing machines are designed with safety and operator ergonomics in mind. Features like dust collection systems, protective enclosures, and emergency stop mechanisms help to minimize health risks associated with exposure to abrasive materials and polishing compounds. Ergonomically designed machines reduce strain on operators and increase the overall safety of the work environment.
Benefits for Manufacturers:
- Consistency and Quality: One of the primary benefits of using polishing machines in cookware production is the consistency in the finish. Automated polishing ensures that each piece of cookware receives the same quality of finish, which is particularly important for ensuring that products meet the high standards expected by consumers. It is essential for manufacturers to maintain this uniformity, especially for premium cookware lines where the visual appeal is as important as the functionality.
- Cost-Effectiveness: While the initial investment in cookware polishing machines may be substantial, the long-term benefits far outweigh the costs. Automation reduces labor costs, as fewer operators are needed to oversee the polishing process. Moreover, the efficiency and speed of the machines help reduce the production time per unit, ultimately decreasing the overall cost of manufacturing.
- Customization for Various Materials: The ability to fine-tune polishing parameters based on the material type ensures that the machine can handle a variety of cookware materials. Stainless steel, aluminum, non-stick-coated materials, and even copper cookware can be polished with the appropriate tools and settings. This makes the machine a versatile asset for cookware manufacturers who produce a wide range of products.
- Sustainability and Waste Reduction: Since polishing machines are designed to work with precision, they help minimize material waste by ensuring that only the necessary amount of material is removed during the polishing phase. Additionally, the machines can be equipped with dust collection systems that capture abrasive particles and polishing residues, reducing environmental pollution and improving workplace air quality.
- Enhanced Consumer Experience: High-quality finishes are crucial for creating a strong consumer impression. Cookware with a smooth, shiny, and aesthetically pleasing surface is more likely to be perceived as high-quality and durable. Polishing also improves the cookware’s non-stick properties, particularly with materials like stainless steel or aluminum, making them easier to clean and maintain. For consumers, these features enhance the overall cooking and cleaning experience, which can positively influence purchasing decisions.
Conclusion:
Cookware polishing machines are indispensable in modern cookware manufacturing. By automating the polishing and finishing processes, these machines offer increased productivity, consistent product quality, and significant cost savings. The ability to handle different cookware materials, produce uniform finishes, and enhance the aesthetic and functional properties of cookware ensures that manufacturers can meet both consumer demands and industry standards. For companies aiming to produce high-quality cookware at scale, investing in advanced polishing machines is a key step toward achieving success in the competitive kitchenware market.
In addition to the key features and benefits already outlined, cookware polishing machines continue to evolve, driven by advancements in automation, robotics, and material science. These developments are pushing the boundaries of what these machines can achieve in terms of speed, precision, and versatility.
Advanced Features of Modern Cookware Polishing Machines
- Integration with Robotic Systems: Many modern cookware polishing machines are now integrated with robotic arms, allowing for more precise control of polishing operations. Robotic polishing systems can handle the complex geometry of cookware, including pots with intricate handles, knobs, and lids. The robotic arm can be programmed to adjust its position and polishing technique based on the specific shape and size of the cookware. This level of flexibility is particularly useful in high-mix, low-volume production environments where customization is often required.
- Advanced Surface Finish Capabilities: Cookware polishing machines are equipped with advanced tools that allow for a variety of surface finishes, such as:
- Matte finishes: Ideal for certain cookware styles that emphasize a sleek, modern aesthetic.
- Mirror finishes: Common in premium cookware, where a high-gloss shine is desired.
- Satin finishes: Offering a balance between gloss and matte, satin finishes are often preferred for cookware that balances functionality and visual appeal.
- Textured finishes: Some specialized machines can apply specific patterns or textures to the cookware’s surface for unique designs or added functionality, such as improving non-stick properties.
- Adaptive Polishing Technology: Modern cookware polishing machines can adapt to different material types, taking into account the unique characteristics of various metals, alloys, and coatings. For example, polishing machines may adjust pressure, speed, or abrasive types depending on whether they are working with stainless steel, aluminum, copper, or non-stick-coated cookware. This adaptability ensures that each material is polished effectively without damaging its surface or compromising its appearance.
- Data-Driven Monitoring and Control: Many CNC-driven cookware polishing machines are equipped with sensors and feedback systems that monitor real-time data during polishing operations. These systems track key parameters such as pressure, speed, temperature, and polishing time. Data analytics can be used to optimize machine settings, ensuring the perfect finish while reducing wear on abrasive materials. This level of monitoring also allows for predictive maintenance, helping manufacturers avoid unexpected downtime and reduce maintenance costs.
- Automated Loading and Unloading Systems: As part of an integrated production line, automated loading and unloading systems can seamlessly feed cookware into polishing machines and remove finished items with minimal human intervention. This automation not only improves productivity but also reduces the risk of defects caused by manual handling. The system can handle various sizes and shapes of cookware, efficiently sorting and loading parts into the polishing machine for processing.
- Eco-Friendly Polishing: As sustainability becomes a critical focus in manufacturing, cookware polishing machines have incorporated eco-friendly solutions. Advanced filtration systems capture harmful particles and prevent contaminants from entering the environment. In addition, some machines utilize water-based or less abrasive compounds, reducing the need for chemical polishing agents that can be harmful to both the environment and workers. These eco-conscious features align with the increasing consumer demand for environmentally responsible manufacturing processes.
Challenges and Considerations in Cookware Polishing Machine Integration
- Material Compatibility: Although cookware polishing machines are highly adaptable, manufacturers must ensure that the abrasives, compounds, and techniques used are compatible with the material of the cookware. For example, polishing aluminum may require gentler abrasives compared to stainless steel, and using the wrong abrasive could damage the cookware or fail to produce the desired finish. It is crucial to test different polishing setups and materials before implementing them on a large scale to avoid costly errors.
- Initial Investment and Return on Investment (ROI): The upfront cost of automated and robotic polishing systems can be significant, especially for smaller manufacturers or startups. However, the long-term savings in labor costs, improved productivity, and consistent product quality typically provide a strong return on investment. It is essential for businesses to evaluate the potential ROI based on factors such as production volume, energy efficiency, and material waste reduction when considering the purchase of these machines.
- Maintaining Consistency Across Different Batches: Maintaining consistent finishes across large batches of cookware is essential, particularly in high-end cookware lines where uniformity is expected. Variations in polishing techniques, abrasive materials, or machine settings could result in inconsistencies in the final product. Manufacturers need to ensure their machines are regularly calibrated and that operators are well-trained to handle any changes in product specifications or material types.
- Training and Expertise: While automation reduces reliance on human labor, there is still a need for skilled operators who can set up, maintain, and troubleshoot the polishing machines. As technology evolves, ongoing training is crucial for ensuring that staff can keep up with new polishing techniques, machine programming, and maintenance protocols. Proper training ensures the machines operate at peak efficiency and minimizes the risk of errors that could impact product quality.
- Customization for Unique Cookware Designs: Cookware items can come in a variety of shapes and sizes, from large stock pots to small saucepans, and this variability can present challenges for polishing machines. Specialized attachments or fixtures may be required to hold non-standard cookware securely during the polishing process, ensuring an even finish. The ability of machines to handle these custom designs while maintaining efficient production schedules is crucial for manufacturers dealing with diverse product lines.
Future Trends in Cookware Polishing Machines:
- AI and Machine Learning Integration: The future of cookware polishing machines will likely involve the incorporation of artificial intelligence (AI) and machine learning algorithms. These technologies can optimize polishing operations in real-time, adjusting machine parameters based on sensor data to achieve the best possible finish. AI-driven systems could also predict potential defects or areas requiring additional polishing, further enhancing quality control.
- 3D Surface Scanning for Precision: Future polishing machines could integrate 3D surface scanning technology, allowing for highly precise control of polishing based on the topography of the cookware surface. This could lead to even more accurate polishing, ensuring that every detail, including curves, edges, and corners, is finished to perfection. Such advancements would be particularly beneficial for cookware with complex geometries or high-end designs.
- Collaborative Robots (Cobots): Collaborative robots, or cobots, will likely play a more significant role in cookware polishing in the future. These robots can work alongside human operators, assisting with tasks such as holding, positioning, or feeding cookware into the polishing machines. Cobots are designed to be safe around humans and can enhance the flexibility of production lines without the need for dedicated, isolated spaces.
- Sustainability Innovations: As consumer awareness of environmental issues continues to grow, cookware manufacturers will increasingly adopt sustainable polishing practices. This could include using biodegradable abrasives, minimizing water and energy usage, and implementing closed-loop systems that recycle polishing compounds and materials. The continued development of eco-friendly solutions will play a vital role in the long-term viability of cookware polishing operations.
Conclusion:
The evolution of cookware polishing machines reflects the ongoing push for greater efficiency, quality, and sustainability in the manufacturing process. With innovations like robotic arms, AI-driven systems, and sustainable polishing methods, these machines are set to further enhance the quality of cookware while reducing environmental impact and operational costs. For manufacturers, investing in these advanced polishing technologies will not only increase productivity and reduce waste but also ensure their products meet the ever-rising expectations of consumers seeking high-performance, aesthetically appealing cookware.
Continuing from the previous insights, there are several additional advancements and factors that are shaping the future of cookware polishing machines and the broader cookware manufacturing industry. These advancements highlight a shift towards increased automation, precision, and sustainability, aiming to provide a better consumer experience while maintaining cost-efficiency and environmental responsibility.
Innovations in Cookware Polishing Machines:
- Enhanced User Interfaces and Automation Integration: The evolution of Human-Machine Interfaces (HMIs) plays a significant role in making cookware polishing machines easier to operate and more intuitive. With touchscreen controls, operators can access real-time data, adjust polishing parameters, and troubleshoot issues seamlessly. The integration of Industry 4.0 technologies allows polishing machines to be linked into larger factory automation systems, creating fully automated production lines. These systems can communicate with inventory and quality control systems to ensure that every batch meets specifications.
- Energy-Efficient Systems: As sustainability becomes an ever-greater priority for manufacturers, energy-efficient cookware polishing machines are gaining traction. Energy consumption can be optimized through technologies such as variable frequency drives (VFDs) that control the speed of motors in response to workload requirements. These systems allow the machines to adjust their energy use based on demand, ensuring that power is not wasted during low-intensity operations. Additionally, advanced cooling systems reduce energy use associated with temperature regulation, minimizing the environmental footprint of the polishing process.
- Smart Polishing and Surface Measurement: New developments in smart polishing techniques involve the integration of precision measurement tools like laser scanners or ultrasonic sensors that can detect variations in surface texture in real time. These sensors can analyze the surface of cookware during the polishing process, ensuring that the desired finish is consistently applied. For example, using laser technology, a polishing machine can measure the exact roughness of the surface and adjust its polishing behavior accordingly. This level of control allows for precision polishing that is adaptive to the specific geometry of each cookware item, ensuring uniformity even across complex shapes.
- Zero-Waste Polishing Technologies: Environmental concerns continue to push innovations in waste reduction. Zero-waste polishing technologies involve advanced systems that capture and recycle polishing agents, abrasives, and even particulate matter produced during the polishing process. Closed-loop systems allow for the continuous reuse of polishing compounds and abrasives, reducing material costs and minimizing waste. These systems contribute significantly to eco-friendly manufacturing practices, reducing environmental impact and complying with increasingly strict environmental regulations.
- Advanced Abrasive Materials: The development of new abrasive materials that provide higher efficiency, durability, and consistency in the polishing process is another major trend. Materials like diamond-impregnated abrasives or ceramic-based polishing agents are gaining popularity for their ability to provide a superior finish with less effort and longer lifespan. These abrasives are designed to work across a wide range of materials, ensuring effective polishing without damaging sensitive cookware surfaces like non-stick coatings.
- Voice-Controlled and Remote Operation: To further enhance automation and streamline operations, some polishing machines are now equipped with voice control capabilities. Operators can issue commands and make adjustments without physically interacting with the machine, which can be particularly useful for reducing downtime and increasing overall production efficiency. Additionally, remote operation via cloud-connected devices is becoming more common. Manufacturers can monitor the performance of polishing machines remotely, adjust settings, and troubleshoot issues without needing to be physically present on the factory floor.
Impacts of These Innovations on Manufacturers:
- Reduced Lead Time: By integrating robotic automation and precision polishing technology, cookware manufacturers can significantly reduce lead times. Automated systems that operate without human intervention can run 24/7, allowing for round-the-clock production and faster turnaround times. This helps meet growing consumer demand and improves a manufacturer’s ability to keep up with market trends.
- Higher-Quality Finishes: Innovations in measurement, smart polishing, and precision robotics ensure that the final finish on cookware is consistently high-quality. The ability to deliver precise, defect-free finishes means manufacturers can produce cookware with better visual appeal and durability. Premium cookware, which often commands higher prices, benefits the most from these advancements. This is especially critical for brands that focus on high-end markets, where aesthetic and functional quality is non-negotiable.
- Scalability: The use of automation and robotics makes it easier to scale production. Cookware manufacturers can increase output without compromising on quality or increasing labor costs. Automated polishing systems can be integrated into larger production lines, allowing manufacturers to scale their operations efficiently while maintaining consistent results across multiple batches of cookware.
- Cost Savings: As manufacturers adopt more efficient systems for polishing, such as zero-waste technologies and energy-saving devices, they can significantly reduce operational costs. Not only does this lower energy consumption, but the reuse of polishing compounds and abrasives reduces material costs. Over time, these savings accumulate and contribute to a healthier bottom line.
- Compliance with Regulations: As environmental regulations around waste and energy consumption tighten, investing in eco-friendly polishing machines helps manufacturers remain compliant. Zero-waste systems and energy-efficient technologies ensure that manufacturers meet increasingly stringent environmental standards, which is especially important for global companies operating in multiple regions with varying regulations.
- Improved Worker Safety and Comfort: Advanced polishing machines with automated features reduce the need for workers to manually handle heavy cookware or abrasive materials. Ergonomically designed systems and automated functions reduce physical strain and improve workplace safety. Features such as dust collection systems, automated loading and unloading, and remote monitoring ensure that workers are not exposed to harmful polishing residues or harsh chemicals, creating a safer and more comfortable working environment.
Challenges of Implementing Advanced Technologies:
- High Initial Capital Investment: While the long-term benefits of advanced cookware polishing machines are clear, the initial capital investment can be a significant barrier, especially for smaller manufacturers. Upgrading to robotic systems, smart polishing technologies, or zero-waste solutions often requires a substantial investment. Smaller manufacturers may find it challenging to afford such systems, despite the potential for long-term savings. Financing options, grants, or subsidies from government agencies may help alleviate these challenges.
- Technology Integration and Training: As manufacturers adopt more advanced polishing systems, they must ensure that their staff is properly trained to operate, maintain, and troubleshoot these new technologies. Staff will need to understand the intricacies of robotic arms, automated interfaces, and smart sensors to maximize the performance of these machines. This requires ongoing investment in training and development.
- System Compatibility: Integrating new polishing technologies into existing production lines may require modifications or even a complete overhaul of the workflow. Manufacturers must ensure that the new systems are compatible with existing machinery and that the production process remains smooth after the integration. This transition can take time and may disrupt production schedules temporarily.
- Maintenance and Downtime: As with any advanced technology, maintaining cutting-edge cookware polishing machines requires specialized knowledge and tools. Regular maintenance schedules, repairs, and software updates will be necessary to keep the machines running at peak performance. Any malfunction or breakdown could lead to production delays, which can be costly for manufacturers, especially when producing large volumes of cookware.
Future Outlook:
As technology continues to evolve, cookware polishing machines will become even more capable, precise, and sustainable. The ongoing focus on automation, energy efficiency, and environmental responsibility will likely make these machines more accessible and affordable to a broader range of manufacturers. These innovations promise to improve the overall production process, allowing manufacturers to deliver higher-quality products while optimizing cost-efficiency and reducing environmental impact.
In the coming years, manufacturers will continue to look for ways to reduce waste, improve product quality, and enhance sustainability—all of which will be supported by advancements in polishing technology. As these systems become more refined and integrated into the broader manufacturing ecosystem, they will help shape the future of cookware production, ensuring that cookware is not only functional and attractive but also manufactured responsibly.
In summary, the next generation of cookware polishing machines will be smarter, more efficient, and more sustainable, supporting manufacturers in delivering high-quality products while maintaining competitive advantage in a rapidly evolving market.
Surface Polisher for Trim Parts & Bowls & Metals

Surface Polishers for Trim Parts, Bowls, and Metals are specialized machines designed to finish and polish the surfaces of various metal products, including trim parts for automobiles, kitchenware such as bowls, and other metal components used in industrial or consumer applications. These machines are vital for achieving the high-quality, smooth, and aesthetically appealing surfaces that are often required in these products, ensuring that they meet both functional and visual standards.
Key Features of Surface Polishers for Trim Parts, Bowls, and Metals:
- Versatility in Material Handling: Surface polishers are designed to handle a variety of metals such as stainless steel, aluminum, brass, copper, and precious metals like gold and silver. These machines can be adjusted to polish different types of materials, whether it’s for creating a mirror finish on automotive trim or a satin finish on kitchen bowls. This versatility makes them ideal for industries ranging from automotive to home goods manufacturing.
- Multiple Polishing Stages: These machines are typically equipped with several polishing stages to progressively refine the surface. Initial stages may involve coarse grinding to remove imperfections, followed by fine grinding and polishing stages to achieve a smooth, reflective finish. Some models even include buffing or brushing stages to enhance surface texture and give a final shine.
- Adjustable Speed and Pressure Settings: To cater to different materials and desired finishes, surface polishers for trim parts, bowls, and metals allow the operator to adjust key parameters such as speed, pressure, and abrasive material. For delicate metals or items with intricate shapes, lower speeds and lighter pressure are used to prevent damage, while for sturdier metals or larger items, higher settings are applied for more efficient polishing.
- CNC or Automated Control: CNC-based surface polishers offer greater precision and consistency by controlling the polishing parameters via computer programming. These systems can automate the entire polishing process, ensuring uniform results across a large batch of components, which is essential in high-volume production. The ability to precisely program speed, pressure, and abrasives helps achieve a high-quality finish with minimal human intervention.
- Rotary and Vibratory Polishers: There are two common types of polishers for these applications:
- Rotary polishers use rotating heads or wheels to polish the surface of the workpiece. These are commonly used for polishing trim parts or flat surfaces.
- Vibratory polishers use vibrational motion to move the polishing media around the workpiece, often used for bowls and more intricate parts where a consistent finish across all surfaces is required.
- Belt and Disc Polishing: For polishing flat or large surfaces, belt polishing machines are often employed. They use wide abrasive belts that can quickly remove imperfections and provide a fine finish. For smaller, more detailed components like trim parts, disc polishing machines are more commonly used. These are effective for working on parts with curved or irregular shapes, ensuring an even finish across the piece.
- Dust and Fume Extraction Systems: Polishing processes generate significant dust, debris, and fumes, especially when abrasive materials are involved. Modern surface polishers are equipped with dust extraction systems that capture and filter these particles, ensuring a clean working environment and improving air quality. This is especially important in industries where compliance with health and safety regulations is necessary.
- Customization for Specific Parts: Many surface polishers are highly customizable to accommodate different types of parts. For trim parts, which can be small and have complex geometries (e.g., contours and edges), machines can be outfitted with custom fixtures or supports to ensure the part stays in place during the polishing process. For bowls, machines can have adjustable arms or holders that allow the round shape to be polished uniformly without any damage.
Benefits of Using Surface Polishers for Trim Parts, Bowls, and Metals:
- Consistent Quality: Polishing machines ensure that every product receives the same level of surface treatment, which is essential in mass production. Whether polishing small trim pieces or large bowls, these machines guarantee uniformity in the finish, reducing variations caused by manual polishing.
- Enhanced Aesthetic Appeal: The main purpose of polishing is to improve the appearance of the product. A well-polished metal surface adds a shiny, reflective quality, which is especially desirable in consumer products like kitchenware or automotive trim. A high-quality finish also improves the marketability of products by giving them a premium look and feel.
- Improved Durability: Polishing not only improves the visual appeal of a product but also enhances its durability. A smooth, polished surface is less prone to corrosion and wear compared to rough or unpolished surfaces. For example, polished stainless steel bowls are more resistant to staining and easier to clean, making them ideal for kitchen use.
- Time and Cost Efficiency: Automated or semi-automated surface polishers are faster than manual polishing, reducing the time required to finish each piece. This increases the overall throughput of a production line, allowing manufacturers to meet high-volume demand. Additionally, reducing manual labor results in cost savings over time.
- Reduced Labor Costs: As polishing becomes more automated, the reliance on skilled labor decreases. The machine can take over tasks that were once labor-intensive, freeing up workers for more complex tasks. Automation also reduces human error, ensuring that polishing is done precisely as per the required specifications.
- Customization of Surface Finish: Surface polishers offer a high degree of customization when it comes to surface finishes. Depending on the application, manufacturers can choose from a variety of finishes, including mirror-like gloss, satin, matte, or textured finishes. This allows them to meet specific customer preferences or product requirements.
- Better Product Handling and Reduced Damage: Polishing machines often come with specialized holders or fixtures to secure the product during the process. This minimizes the risk of scratches or damage that could occur if the product were handled manually. For delicate parts like trim pieces, ensuring proper handling is crucial to maintaining their integrity throughout the polishing process.
- Eco-Friendly: With the integration of closed-loop systems for polishing media and dust extraction technologies, modern surface polishers can be more environmentally friendly. They help reduce waste and ensure that pollutants are captured and properly disposed of, minimizing the machine’s environmental impact.
Applications of Surface Polishers for Trim Parts, Bowls, and Metals:
- Automotive Trim Parts: Automotive parts, especially exterior trims, handles, and moldings, require a precise finish for both aesthetic appeal and resistance to corrosion. Surface polishers are essential for achieving high-quality finishes on trim parts, such as chrome-plated bumpers, door handles, and exhaust tips.
- Kitchenware and Bowls: In the kitchenware industry, metal bowls, pots, pans, and other utensils often require a smooth, polished surface to enhance their durability and appearance. Polishing not only makes these products aesthetically pleasing but also ensures that they are resistant to food residue buildup, corrosion, and stains. Stainless steel bowls, in particular, benefit from polishing as it gives them a sleek and shiny surface, which is highly desirable for home and professional kitchens.
- Industrial Metal Components: Surface polishers are used to finish large metal components used in industrial settings, such as gears, machine parts, and decorative metal finishes for appliances or machinery. The smooth surface enhances the part’s functionality, such as reducing friction or improving the part’s resistance to wear and tear.
- Jewelry and Decorative Metal Items: Polishing machines are commonly used in the production of jewelry or decorative items made from precious metals. The ability to produce a mirror-like finish is critical in high-end jewelry manufacturing, and polishing machines ensure a flawless final product.
Conclusion:
Surface polishers for trim parts, bowls, and metals play a critical role in achieving the desired surface finishes for a wide range of products across industries. From improving aesthetics to enhancing the durability of metal components, these machines offer manufacturers the ability to produce high-quality, consistent products quickly and efficiently. With advanced features such as automation, customizable polishing stages, and eco-friendly systems, surface polishers are an essential tool for manufacturers who want to meet consumer demands for premium finishes and maintain competitiveness in the marketplace.
Advanced Technologies in Surface Polishers:
- Robotic Polishing Systems: One of the most exciting advancements in surface polishing for trim parts, bowls, and metals is the use of robotic arms for polishing. These robotic systems can handle complex geometries and delicate surfaces with high precision. They are often used in combination with CNC and vision systems to automate the polishing process. Robotic arms equipped with rotating polishing tools can adjust their movements based on the shape and size of the part, ensuring a consistent finish on every piece. This level of automation reduces the need for manual intervention, increases throughput, and improves safety in high-volume production environments.
- High-Frequency Polishing: High-frequency polishing techniques are becoming increasingly popular for achieving ultra-fine finishes, especially in the automotive and high-end kitchenware markets. This method involves using specialized polishing tools that vibrate at very high speeds. The vibration helps to smooth out even the tiniest surface imperfections without the need for heavy abrasion, which could damage delicate surfaces. It’s particularly useful for achieving a flawless, mirror-like finish on metals like stainless steel, aluminum, and brass.
- Nanotechnology-Based Polishing: The application of nanotechnology in polishing is an emerging trend. By using nano-scale abrasives, polishing machines can achieve ultra-smooth surfaces with fewer defects and imperfections. This technology allows for the microscopically smooth finishes that are increasingly in demand for both functional and decorative metal parts. Nanotechnology can be particularly useful in the polishing of medical devices, aerospace components, and high-end consumer goods, where precision and surface quality are critical.
- Sustainability and Green Polishing: Modern surface polishers are increasingly focusing on sustainability. New polishing processes are designed to reduce the consumption of abrasives and chemicals, minimizing waste. Some manufacturers are integrating bio-based polishing compounds and environmentally friendly abrasives into their systems, ensuring that the polishing process has a smaller environmental footprint. Additionally, water-based polishing agents are being used as alternatives to traditional solvents, which helps reduce air and water pollution while still providing high-quality finishes.
- AI Integration and Predictive Maintenance: Artificial Intelligence (AI) and machine learning are beginning to play a role in polishing technologies, especially in the context of predictive maintenance. Sensors embedded within polishing machines can continuously monitor the system’s performance and analyze factors such as motor load, vibration levels, and abrasives wear. AI algorithms can predict when maintenance is needed or when certain components might fail, allowing manufacturers to perform proactive maintenance and avoid unexpected downtime. This reduces overall operational costs and keeps machines running smoothly.
Expanded Applications of Surface Polishers:
- Aerospace and Aviation Parts: In the aerospace industry, precision is key. Surface polishers are used to finish critical components such as turbine blades, engine parts, and landing gear. These parts require smooth, defect-free finishes to ensure their aerodynamic efficiency and to reduce wear during operation. Polishing also enhances the part’s resistance to corrosion, which is essential for ensuring the longevity and safety of aerospace components.
- Furniture and Architectural Metalwork: For architectural and furniture applications, polished metals are often used for structural components, decorative finishes, and even furniture hardware. Polished finishes can provide a contemporary, sleek look that enhances the design of residential and commercial spaces. Trim parts, such as handles, knobs, and brackets, often undergo polishing to ensure that they meet both aesthetic and functional requirements. Surface polishers can handle a range of metal finishes, from matte to high-gloss, depending on the project’s needs.
- Marine Industry: Marine applications, including the construction of ships, yachts, and other vessels, often require polishing for both aesthetic reasons and to prevent rust and corrosion. Stainless steel is a popular material for marine components due to its resistance to saltwater corrosion, but it must be polished to ensure that the metal remains shiny, clean, and functional over time. Surface polishers designed for marine environments must be able to handle large parts, such as handrails, fittings, and propellers, ensuring that the polished finish is long-lasting in harsh conditions.
- Food Processing Equipment: In the food processing and pharmaceutical industries, metal surfaces need to be polished to meet hygienic standards. Stainless steel surfaces must be polished and finished to minimize the risk of bacterial growth and make cleaning easier. Polishing also removes any residual machining marks that could harbor contaminants. Surface polishers used in these industries are often designed to meet strict regulatory standards, ensuring that the finish is not only functional but also compliant with hygiene and safety regulations.
- Custom Metal Products: As customization becomes more prevalent across industries, manufacturers increasingly use surface polishers to create unique, customized metal products. This includes bespoke kitchenware, custom automotive parts, and tailor-made industrial components. Polishing machines are capable of producing one-of-a-kind finishes that meet the exact specifications required by customers, whether it’s for a limited-edition item or a personalized piece.
Operational Efficiency:
- Increased Throughput: With the adoption of advanced automation and robotic systems, manufacturers can now process a higher volume of parts in less time. For example, a robotic arm-based polisher can perform continuous polishing without the need for frequent breaks, which improves efficiency and increases throughput. This results in a shorter lead time and more units produced per shift, driving higher productivity and faster delivery times.
- Reduced Need for Manual Labor: Manual polishing can be labor-intensive, requiring significant time and skilled labor to achieve consistent results. By automating the polishing process, manufacturers can reduce their reliance on manual labor, which not only saves time but also minimizes the risk of human error. With robotic and CNC systems taking care of the polishing, operators can focus on other tasks, increasing overall productivity.
- Flexible Operation for Varied Workpieces: Surface polishers today are designed to handle a wide range of workpieces, from small, intricate trim parts to large, heavy-duty metal components. The ability to easily switch between different part sizes and shapes without the need for significant reconfiguration makes these machines highly adaptable. Whether polishing a small bowl or a large automotive component, operators can adjust the machine settings to meet the specific requirements of each piece, enhancing overall flexibility.
- Reduced Material Wastage: Automated polishing systems are designed to use abrasives and polishing compounds more efficiently. With better control over the polishing process, the system can apply just the right amount of pressure and abrasives to achieve the desired finish, leading to reduced material wastage. This not only reduces costs but also helps improve the sustainability of the polishing process by minimizing resource consumption.
- Improved Surface Integrity: One of the most significant advantages of using a high-quality surface polisher is the preservation of the material’s integrity. Polishing removes surface imperfections and ensures that the material underneath is smooth and uniform. This is particularly crucial in industries like automotive, where the finish not only affects the appearance of the trim parts but also plays a role in the longevity and performance of the product. By avoiding over-polishing and ensuring consistent pressure, surface polishers maintain the integrity of the metal, extending the product’s life.
Conclusion:
Surface polishers for trim parts, bowls, and metals represent a critical investment for manufacturers aiming to achieve high-quality finishes, increase production efficiency, and reduce operational costs. The continued advancement of robotic systems, CNC control, and smart technologies is pushing the capabilities of surface polishers, ensuring that manufacturers can meet the demands of precision, sustainability, and aesthetic appeal across various industries. These machines allow for the creation of products that not only meet the functional requirements of the market but also stand out visually, helping brands differentiate themselves in competitive sectors.
Continued Advancements in Surface Polishing Technology:
- Smart Polishing Machines: Smart technology in surface polishing machines is revolutionizing the industry by providing real-time monitoring and control. These systems are integrated with advanced sensors and IoT capabilities, allowing operators to remotely monitor and adjust machine parameters. For example, sensors can detect if the polishing wheel or abrasive material is starting to wear out or if any operational issues arise, triggering maintenance alerts or adjustments before the problem affects the finish quality. This real-time data collection allows manufacturers to optimize machine performance and extend the lifespan of equipment, reducing downtime.
- Hybrid Polishing Systems: Hybrid polishing systems combine different polishing techniques, such as rotary, vibratory, and belt polishing, into a single machine. This innovation allows manufacturers to seamlessly transition between polishing methods based on the material type or specific finish required. For example, a system might start with coarse belt grinding to remove imperfections, then switch to a rotary polishing stage to refine the surface, and finally finish with a vibratory stage for evenness and shine. Hybrid systems offer great flexibility and can significantly improve productivity and consistency for manufacturers who process a variety of parts.
- AI-Based Quality Control: Integrating artificial intelligence (AI) into polishing machines not only aids in maintenance prediction but also enhances quality control. AI systems can analyze the surface finish in real time, checking for defects or inconsistencies that could be invisible to the human eye. Using machine vision and deep learning algorithms, AI can evaluate whether the surface has been polished to the desired standard and automatically make adjustments, ensuring that all products meet the required specifications. This closed-loop system ensures that every part is polished consistently, leading to better product quality and fewer rejects.
- Ultrasonic Polishing: Ultrasonic polishing is a specialized technique that utilizes high-frequency vibrations (ultrasound) to achieve an ultra-smooth finish on materials like metals, ceramics, and plastics. In this process, a polishing tool vibrates at ultrasonic frequencies, transferring energy to the workpiece. This allows for the removal of microscopic imperfections and provides a high-quality, mirror-like finish. Ultrasonic polishing can be applied to both flat and complex shapes, making it ideal for polishing delicate or intricate parts such as medical implants, aerospace components, and precision electronics.
- Continuous Polishing Process: Some surface polishers are designed with a continuous polishing process, allowing materials to be polished continuously as they move through the machine. This method is especially effective for high-volume production runs, where parts need to be polished in a consistent manner without stopping and starting. It is often used for long, flat items such as metal sheets, pipes, and extruded profiles, as well as for automotive trim parts. The continuous polishing process helps reduce cycle times and increases throughput while ensuring that the surface quality remains consistent throughout the production run.
Extended Applications of Surface Polishers:
- Medical Device Manufacturing: Polishing is an essential part of the medical device manufacturing process, particularly for components like surgical instruments, implants, and prosthetics. A highly polished surface ensures that medical devices are free from any harmful contaminants, reducing the risk of infections. Additionally, smooth surfaces help improve the longevity and effectiveness of devices, such as hip implants, which must withstand years of wear in the human body. Polishing machines used in the medical industry are often sterilizable and must meet strict regulatory standards, ensuring they don’t compromise product safety.
- Electronics and Precision Parts: Electronic components, including connectors, displays, and micro-electromechanical systems (MEMS), often require precision polishing to achieve the high level of finish required for signal clarity and performance. For instance, in smartphone manufacturing, components such as stainless steel frames, buttons, and back panels are polished to achieve a smooth, high-quality surface that enhances the product’s durability, aesthetic appeal, and tactile feel. The level of precision required for these parts often necessitates the use of advanced polishing machines with CNC control and robotic handling to achieve the desired level of accuracy.
- Luxury Goods and Jewelry: Polishing is an essential process in the production of luxury goods and jewelry, particularly for items like watches, rings, bracelets, and necklaces. Jewelry manufacturers use highly specialized polishing systems to achieve mirror finishes on precious metals such as gold, platinum, silver, and gemstone settings. These machines can accommodate delicate designs, ensuring that every piece of jewelry not only has a brilliant shine but also maintains its structural integrity. Jewelry polishing machines often feature high-precision controls to avoid damaging fragile stones or intricate metalwork while achieving the perfect surface finish.
- Home Appliances: The production of home appliances such as refrigerators, microwaves, and coffee makers involves metal components that must be polished to enhance both appearance and functionality. Stainless steel is commonly used in these appliances due to its resistance to corrosion and its modern, sleek aesthetic. Surface polishers help create a smooth, shiny finish on the metal surfaces of these products, making them more attractive to consumers while also ensuring that the surfaces are easier to clean and more resistant to fingerprints, scratches, and other forms of damage.
- Architectural and Decorative Metalwork: In the construction and architecture industries, polished metals are frequently used in decorative metalwork and structural components. For example, polished stainless steel is commonly used for exterior facades, columns, railings, and elevators in high-rise buildings, while brass or copper may be used in the design of custom architectural elements such as door handles and light fixtures. Surface polishers help ensure these components have the necessary level of smoothness and reflectivity to meet the aesthetic needs of modern architectural designs.
Operational Advancements and Benefits:
- Higher Efficiency with Multi-Stage Processes: Many modern surface polishers employ a multi-stage process that enables different polishing techniques to be applied in sequence. For instance, a component may first undergo coarse grinding to remove material, followed by intermediate polishing to smooth the surface, and then a final high-polish stage for a glossy finish. By combining these steps into one continuous process, manufacturers can achieve high-quality finishes more quickly and efficiently, eliminating the need for multiple machines and reducing handling times.
- Advanced Safety Features: As with any heavy-duty machinery, safety is a crucial concern in polishing operations. Many modern surface polishers are equipped with advanced safety features, such as safety guards, emergency stop buttons, and automatic shutdown systems to prevent accidents or injuries. Some machines are also designed to operate with noise-reduction and vibration-damping technologies to provide a safer and more comfortable working environment for operators. Additionally, ergonomically designed machines reduce the risk of worker fatigue, allowing for more comfortable and efficient operation during long shifts.
- Reduction in Polishing Time with Automation: With the advent of automated polishing systems, the time required to achieve a high-quality finish has been drastically reduced. Automated systems can continuously polish parts without the need for constant human oversight, allowing for faster processing times. For example, robotic arms with adaptive polishing heads can precisely follow the contours of irregularly shaped parts and continuously apply the right amount of pressure and abrasive material. This reduces the overall polishing cycle time, increases throughput, and enables manufacturers to meet higher production quotas.
- Cost Savings and Reduced Waste: Automated surface polishers with integrated monitoring systems can significantly reduce material waste by adjusting the polishing parameters based on the type of material and part. For example, if the system detects that a part is made of a softer material or is particularly delicate, it can automatically adjust the pressure and abrasive speed to minimize wear on both the part and the abrasive material. Additionally, many modern machines are designed to use recyclable polishing media and have built-in systems for waste collection and recycling, further reducing operational costs and the environmental impact of the polishing process.
- Customizable Finishes for Market Differentiation: The ability to produce customizable surface finishes is a powerful tool for manufacturers who want to differentiate their products in the market. For instance, offering a range of finishes from matte to high-gloss, or creating textured or brushed finishes, allows companies to cater to a wider range of customer preferences. Additionally, customizable finishes are essential in industries such as luxury goods, where consumers expect personalized, high-quality products that reflect their tastes.
Conclusion:
The landscape of surface polishing technology continues to evolve with smarter, faster, and more sustainable solutions. These innovations offer manufacturers the ability to increase operational efficiency, achieve high-quality finishes, and reduce costs. Whether in the automotive, medical, electronics, or luxury goods industries, advanced polishing machines are enabling manufacturers to meet rising consumer expectations for precision, aesthetic appeal, and durability while improving their production processes. The integration of technologies such as AI, robotics, and multi-stage automation ensures that surface polishers remain at the forefront of industrial manufacturing, offering both enhanced capabilities and significant operational advantages.
Further Developments in Surface Polishing Technology:
- Surface Polishing with Adaptive Control Systems: A significant leap in surface polishing technology is the introduction of adaptive control systems that adjust the polishing parameters in real time based on feedback from the material. These systems use advanced sensors and algorithms to continuously monitor the surface finish as the polishing process occurs. If a surface begins to exhibit imperfections or if the material type requires different treatment (e.g., harder or softer metal), the system can adapt the pressure, speed, and abrasiveness accordingly. This not only ensures a perfect finish but also reduces the risk of damaging delicate parts or over-polishing, thereby maintaining the integrity of the material.
- Automated Finishing for Small and Complex Parts: With advancements in robotic arms and artificial intelligence, surface polishing machines are increasingly able to handle small, intricate parts that require precision finishing. These systems are designed with fine control mechanisms to allow the polishing of highly detailed or irregularly shaped components. For example, components like medical devices, optical lenses, and aerospace parts often require polishing that accommodates their tiny, complex structures. The development of micro-polishing techniques enables these parts to achieve high-precision finishes, making them suitable for high-tech applications where every micron counts.
- Polishing for Additive Manufacturing (3D Printed Parts): The rise of additive manufacturing (AM), or 3D printing, has introduced a new challenge in the world of surface finishing. Additive manufacturing often leaves parts with layered surfaces, which require additional polishing to achieve a smooth, professional finish. To address this, specialized polishing machines have been developed to handle 3D-printed metal and polymer parts. These systems use a combination of abrasive media, vibratory techniques, and CNC controls to process parts with complex geometries or internal structures. As additive manufacturing grows in industries such as aerospace, automotive, and medical devices, the demand for high-quality surface finishes on 3D printed parts will continue to rise, driving innovation in polishing technology for these applications.
- Self-Cleaning Polishing Surfaces: The future of surface finishing also includes self-cleaning surfaces, particularly for industries where cleanliness is critical, such as medical, food, and pharmaceutical sectors. Innovations in surface coatings and nano-structured polishing materials are making it possible to create surfaces that resist contamination and are easier to clean. These coatings can be applied during the polishing process itself, improving the surface’s resistance to dirt, bacteria, and stains. For example, self-healing coatings can repair minor scratches or imperfections on the polished surface over time, maintaining the aesthetic and hygienic properties of the material.
- Polishing with Ultrathin Abrasives and Superfinishing: To achieve the highest level of surface finish, ultrathin abrasives are being utilized. These abrasives are capable of working on microscopic levels, removing only the smallest amounts of material to achieve an ultra-smooth, mirror-like finish. This is particularly beneficial in applications where the surface finish is more than just aesthetic — for instance, in the case of precision machinery or optical components. Ultrathin abrasives can be used in combination with superfinishing techniques, which are highly effective in eliminating surface flaws without compromising the material’s integrity.
Emerging Trends in Polishing Processes:
- Eco-Friendly Polishing Materials: As environmental concerns continue to grow, there has been a significant push toward eco-friendly polishing processes. This includes the use of biodegradable abrasives, water-based polishing compounds, and sustainable polishing cloths. These materials are increasingly popular in industries aiming to reduce their environmental footprint. For example, water-based slurries and abrasive pads made from recycled materials are being used in place of traditional chemical agents, which can be harmful to the environment. As the industry moves toward more sustainable manufacturing practices, companies are also adopting methods that minimize the use of non-renewable resources and reduce waste during polishing processes.
- Smart Polishing for Surface Analytics: New developments in surface analytics are revolutionizing the way surface finish quality is assessed. Smart sensors are now able to measure surface roughness, gloss, and texture in real time during the polishing process. These sensors are often integrated with machine vision systems to detect minute variations in surface quality that might be missed by the human eye. The data generated by these sensors can be used to fine-tune the polishing process, ensuring that every part is finished to the exact specification required. This real-time quality control significantly reduces the number of defective products and ensures consistency across production runs.
- Polishing for High-Temperature Materials: The demand for high-temperature materials, especially in industries like aerospace and nuclear energy, requires polishing techniques that can handle extreme conditions. Polishing machines designed for these materials use diamond abrasives or ceramic-based materials to achieve the necessary smooth finish while maintaining the integrity of high-performance alloys. For example, superalloys used in turbine engines need to undergo polishing processes that preserve their heat-resistant properties while removing surface imperfections that could affect their performance.
- Laser Polishing Technology: Laser polishing is a rapidly advancing method that uses a laser beam to melt a small portion of the material’s surface, smoothing out any imperfections and creating a highly reflective finish. This method is particularly useful for materials that are difficult to polish with traditional abrasives, such as titanium, ceramics, or hard metals. The laser polishing process can be applied to both flat and complex geometries, making it suitable for a wide range of industries, including medical, aerospace, and automotive. Laser polishing offers a non-contact solution, reducing wear on tooling and providing highly controlled precision.
- Polishing for Decorative Finishes: In addition to functional finishes, there is an increasing demand for decorative or artistic finishes on metal products, particularly in the luxury goods, interior design, and automotive industries. Surface polishing is used to create unique textures, brushed finishes, or patterned surfaces that add value and aesthetic appeal. Manufacturers are using specialized polishing machines equipped with texturing rollers or rotary tools to create intricate designs on surfaces, giving products a personalized or upscale appearance. These decorative finishes are gaining popularity for products such as luxury watches, furniture, architectural metalwork, and high-end automobiles.
Benefits and Future Outlook:
- Increased Customization and Flexibility: As technology continues to evolve, surface polishers will become even more flexible and capable of handling a wider variety of materials and finishes. The ability to easily switch between different polishing techniques or achieve custom surface patterns will be crucial for industries where bespoke design is becoming more common. Whether it’s creating a polished surface for a one-of-a-kind product or adjusting the polishing settings to meet the needs of a unique material, these advanced machines will provide manufacturers with more control and versatility.
- Higher Precision and Automation: The integration of automated systems and robotics will continue to push the boundaries of surface polishing, improving both precision and throughput. For example, CNC-controlled polishing machines can achieve incredibly fine surface finishes with tolerances as low as microns. Automation will also reduce human errors, lower the cost of labor, and help scale up production. The increased accuracy and efficiency of these systems will allow manufacturers to meet the high demands of industries like aerospace, automotive, and electronics, where precision is paramount.
- Reduction of Lead Times: As polishing technology advances, lead times for manufacturing are expected to shrink, allowing for faster turnarounds in production. The automation of the polishing process, alongside continuous polishing systems and advanced robotic arms, will significantly reduce the time required to achieve high-quality finishes, especially in high-volume production runs. This will enable manufacturers to meet shorter delivery deadlines and respond more quickly to market demands.
- Cost-Efficiency and Waste Reduction: The evolution of surface polishers will also bring about improvements in cost-efficiency and waste reduction. As machines become more intelligent, they will be able to optimize the use of abrasive materials and polishing agents, reducing overall consumption. Additionally, advanced waste management systems will collect and recycle polishing compounds and abrasives, further reducing environmental impact and costs. As these technologies mature, manufacturers will see a significant reduction in operating costs while contributing to more sustainable practices.
Conclusion:
The future of surface polishing technology is characterized by rapid advancements in automation, precision, and sustainability. Manufacturers are embracing cutting-edge technologies like robotics, AI, and smart sensors to enhance their polishing processes, achieving better results with fewer resources. With applications ranging from luxury goods and medical devices to automotive parts and aerospace components, surface polishing is becoming an indispensable process across a variety of industries. The next-generation polishing systems promise to offer even greater flexibility, efficiency, and environmental sustainability, driving improvements in both product quality and manufacturing processes. As industries demand higher performance, better aesthetics, and shorter production timelines, the evolution of surface polishers will continue to be a key factor in shaping the future of manufacturing.
Polishing Machine for Metals
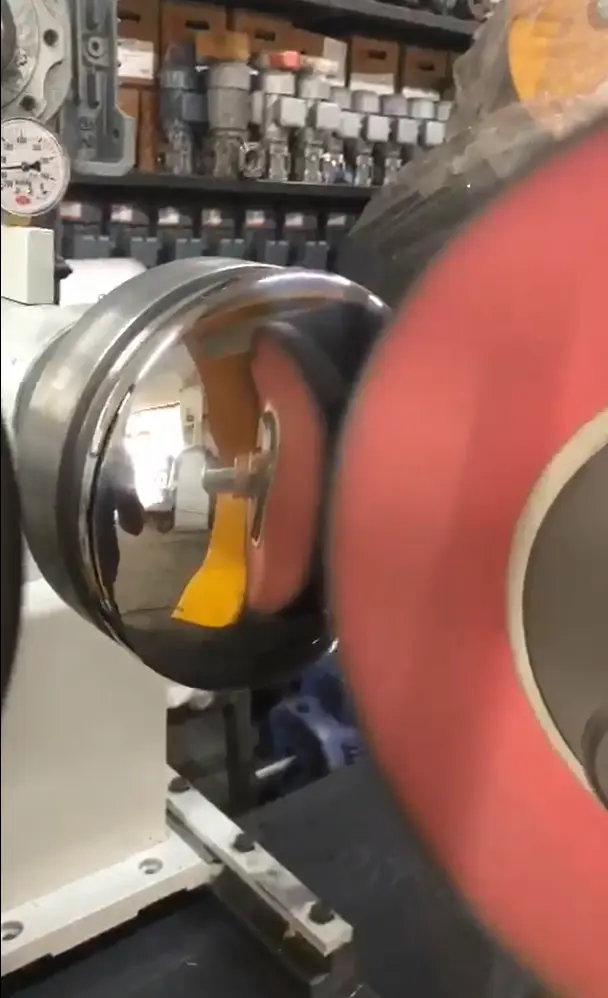
A Polishing Machine for metals is an essential piece of equipment in many industrial applications, especially in sectors like automotive, aerospace, jewelry, medical devices, and electronics. These machines are designed to enhance the surface finish of metal parts by removing imperfections, scratches, and oxidation, and to achieve a smooth, shiny, and reflective surface. The polishing process not only improves the aesthetic appeal of metal products but also enhances their functionality by increasing their resistance to corrosion and wear.
Types of Polishing Machines for Metals:
- Belt Polishing Machines: Belt polishing machines use abrasive belts to polish metal surfaces. They are ideal for high-volume, continuous polishing of flat or curved metal parts. These machines can handle different grades of abrasives, from coarse to fine, depending on the desired finish. They are highly effective for finishing sheet metals, pipes, bars, and other extruded profiles.
- Applications: Automotive body parts, stainless steel surfaces, metal trim.
- Advantages: Fast, continuous polishing; can achieve a uniform finish over large surfaces.
- Rotary Polishing Machines: Rotary polishing machines use a rotating buffing wheel or polishing pad that applies pressure and abrasive material to the surface of the metal part. These machines are great for achieving a high-gloss or mirror-like finish and can handle both flat and contoured surfaces.
- Applications: Jewelry, watches, precision components.
- Advantages: High-quality finish, versatile for different part shapes.
- Vibratory Polishing Machines: Vibratory polishing machines use vibration to move metal parts in a container along with abrasive media (like ceramic or plastic beads). The vibration causes the abrasive media to interact with the metal surfaces, polishing them uniformly. These machines are often used for finishing small parts or components that require a more delicate touch.
- Applications: Small metal parts, screws, bolts, medical implants.
- Advantages: Excellent for mass finishing, smooth and consistent results.
- Centerless Polishing Machines: A centerless polishing machine is used for finishing long, cylindrical metal parts without the need for a central holding fixture. The part is fed between two rotating wheels – one driving the part and the other applying the abrasive material. This method is typically used for polishing long shafts, tubes, and bars.
- Applications: Automotive shafts, pipes, small metal rods.
- Advantages: Ideal for high-volume production, minimal handling of parts.
- CNC Polishing Machines: CNC (Computer Numerical Control) polishing machines are automated systems that use robotic arms or precision CNC controls to polish complex metal components. These machines offer high precision and repeatability, making them suitable for applications requiring specific surface finishes with tight tolerances. CNC polishing can be used for intricate designs and parts with complex geometries.
- Applications: Aerospace components, medical devices, high-precision parts.
- Advantages: High precision, customizable, reduces human error.
- Handheld Polishing Machines: Handheld polishing machines are smaller, portable devices that allow for manual polishing of metal parts. These tools are commonly used in applications where large machines cannot be used or when local polishing is required. They are often equipped with buffing wheels, abrasive pads, or polishing cloths to apply the finishing touches to the metal surface.
- Applications: Decorative metal parts, small batch production, repair and touch-up.
- Advantages: Portable, ideal for small, custom projects or repairs.
Key Features and Benefits:
- Variable Speed Control: Many modern polishing machines come with variable speed controls, which allow operators to adjust the speed of the polishing process. This flexibility is crucial for working with different types of metal and achieving varying surface finishes, from coarse to ultra-fine. Slower speeds are ideal for finishing delicate parts, while higher speeds are used for heavy-duty polishing.
- Abrasive Media Options: The abrasive media used in polishing machines can vary based on the metal and desired finish. Some common types include:
- Cloth Buffing Wheels: Ideal for achieving a high-gloss finish on softer metals like aluminum.
- Non-woven Abrasive Pads: Perfect for polishing stainless steel and other hard metals while maintaining uniformity.
- Diamond Abrasives: Used for extremely hard metals, such as in aerospace or medical devices, where precision is critical.
- Dust and Debris Collection Systems: Polishing processes generate a significant amount of dust and debris, especially when dealing with metals like stainless steel or aluminum. Many modern polishing machines are equipped with dust extraction systems to keep the workspace clean, maintain operator safety, and ensure that the finished parts are free of contamination.
- Ergonomics and Ease of Use: Polishing machines, especially handheld or benchtop models, are designed with ergonomics in mind to reduce operator fatigue. Features like vibration-damping handles, adjustable arms, and easy-to-use controls make it more comfortable for operators to work with the machine for extended periods. This ensures higher productivity and consistent results.
- Automated Polishing Systems: In larger manufacturing settings, automated polishing systems can be used to enhance productivity. These systems often use robots or conveyor belts to move parts through a series of polishing stages, reducing labor costs and increasing throughput. Automated systems are ideal for industries that require high-volume production and consistent quality.
Applications:
- Automotive Industry: Polishing machines are widely used in the automotive industry for finishing parts like exterior body panels, chrome trim, wheels, and engine components. High-gloss finishes are particularly important for consumer-facing parts, where aesthetic appeal is crucial.
- Aerospace and Defense: The aerospace industry requires precision polishing for parts like turbine blades, aircraft components, and engine parts. Polishing improves the aerodynamic properties, strength, and durability of these components, ensuring they meet strict quality standards.
- Medical Devices: In the medical device industry, polishing is essential for parts like surgical instruments, implants, and prosthetics. The process removes sharp edges and imperfections, ensuring that devices are safe and smooth for use inside the human body.
- Jewelry and Decorative Metals: Jewelry makers and manufacturers of decorative metal products use polishing machines to achieve the fine, reflective finishes on products such as rings, bracelets, watches, and coins. These finishes enhance the visual appeal of the product and increase its market value.
- Electronics: Polishing is used in the electronics industry for parts like circuit boards, connectors, and connective metal components to improve the surface conductivity and appearance. Precision polishing is required to remove oxidation and achieve a smooth finish for high-performance electronic devices.
Advantages of Metal Polishing Machines:
- Improved Surface Finish: Polishing machines help in achieving high-quality, smooth, shiny, and uniform finishes that improve the appearance and function of metal parts.
- Enhanced Durability: Polishing also helps improve the corrosion resistance of metals by smoothing out rough spots where rust or oxidation could form.
- Increased Precision: For high-precision industries like aerospace or medical devices, polishing machines provide the necessary precision to meet tight tolerances and quality standards.
- Time and Labor Efficiency: Automated and high-performance polishing machines significantly reduce polishing time, allowing for faster production rates and lower labor costs.
Future Trends:
- Integration with AI and Robotics: The future of polishing machines for metals is leaning toward further integration with AI and robotics to offer intelligent control systems, precise automation, and customized polishing patterns. These advancements will lead to greater flexibility and precision in polishing processes.
- Sustainability and Eco-friendly Practices: As environmental concerns continue to grow, manufacturers are focusing on developing eco-friendly polishing solutions, such as water-based abrasives and recyclable materials. Furthermore, new dust collection and waste disposal systems are helping minimize the environmental impact of polishing operations.
- Smart Manufacturing: The implementation of smart sensors and IoT in polishing machines will allow for real-time monitoring of part quality, machine health, and process efficiency. These systems will enable manufacturers to achieve predictive maintenance, reducing downtime and improving overall productivity.
Conclusion:
Polishing machines for metals are critical in a variety of industries, from automotive and aerospace to medical devices and luxury goods. Whether in high-volume production or precision crafting, these machines enhance the aesthetic quality, durability, and functionality of metal products. With continued advancements in automation, AI, and sustainable technologies, the future of metal polishing looks poised for greater efficiency, customization, and eco-friendliness.
1. Belt Polishing Machines:
Belt polishing machines are particularly useful in industries that require high-volume production and continuous processing. These machines use a rotating abrasive belt to polish metal surfaces, and they can handle a wide range of metal types, from stainless steel to aluminum, brass, and copper.
- Abrasive Belt: The belt’s abrasive surface is designed to remove surface imperfections quickly and evenly. The abrasive material can be tailored for different finishes, such as coarse abrasives for initial stages or fine abrasives for polishing and finishing.
- Operation: Belt polishing machines generally consist of a workpiece support table, where the metal part is placed, and two rotating drums that pull the abrasive belt over the part’s surface. The part moves along the table as the belt smooths out the surface, removing scratches and marks, and achieving the desired finish.
- Advantages: These machines are efficient, especially for large metal sheets, tubes, or bars that require consistent, uniform polishing across their entire surface. Additionally, belt polishing machines can be used for a variety of finishes, including matte, satin, or high-gloss.
Applications:
Belt polishing is commonly used for metal finishing in applications such as:
- Stainless steel polishing for kitchen appliances, industrial equipment, and structural components.
- Automotive polishing for large car parts like body panels, wheels, and chrome bumpers.
- Pipe and tubing finishing for the construction and food industry, where smooth and clean surfaces are essential.
2. Rotary Polishing Machines:
Rotary polishing machines are designed to provide a high-quality, glossy finish on metal parts. These machines are often used for polishing complex geometries or parts with intricate curves that need to be polished evenly. Unlike belt polishing machines, rotary machines use polishing wheels or pads that rotate to provide a smooth, reflective surface.
- Buffing Wheels: Buffing wheels are used to polish the surface of metal parts, usually with the help of polishing compounds such as rouge or abrasive pastes. The buffing wheel applies pressure on the metal surface to remove the outer layer of the material, leaving behind a shiny finish.
- Rotary Action: The wheel rotates at a specific speed to ensure uniform polishing across the surface. Adjusting the wheel’s speed and applying the right amount of pressure allows for different levels of finish, from brushed finishes to mirror-like shines.
- Versatility: Rotary polishing machines are versatile and can be used for a wide variety of applications, including polishing flat, concave, and convex surfaces. These machines can also be equipped with multiple heads for simultaneous polishing of several parts.
Applications:
Rotary polishing machines are popular in industries such as:
- Jewelry manufacturing, where intricate metal pieces require a high-quality finish.
- Automotive industry, especially for smaller parts like emblems, trim pieces, or mirrors.
- Furniture and decorative metal polishing, often in the production of luxury items such as brass chandeliers or gold-plated accents.
3. Vibratory Polishing Machines:
Vibratory polishing is a mass finishing process that involves using vibration to polish metal parts with the help of abrasive media. In a vibratory polishing machine, parts and abrasive media are placed in a container, which vibrates to create friction and tumbling action, leading to the smoothing of rough edges and surfaces. This method is typically used for smaller parts or items that need to be polished in bulk.
- Vibration: The vibratory action causes parts to move in a circular or orbital motion within the container, allowing abrasive media to gently polish the surfaces. The process is generally slower than belt or rotary polishing but is highly effective for mass finishing.
- Media Options: The abrasive media used in vibratory polishing can range from ceramic and plastic beads to silicon carbide or aluminum oxide, depending on the required finish and the metal being polished.
- Advantages: Vibratory polishing is perfect for high-volume production of smaller parts like nuts, bolts, gears, jewelry components, and medical implants. The polishing process is more gentle, preventing damage to delicate parts while achieving a consistent finish.
Applications:
Vibratory polishing is commonly used in:
- Mass finishing for small metal parts in electronics, medical devices, and precision instruments.
- Screws, washers, and other components that require uniform deburring and surface smoothing.
- Medical and dental parts that need to have high-quality finishes without compromising their integrity.
4. Centerless Polishing Machines:
Centerless polishing machines are ideal for polishing cylindrical metal parts such as shafts, tubes, bars, and rods. These machines do not require a central fixture to hold the part, allowing the workpiece to be fed through the machine, making them suitable for continuous production runs.
- Working Principle: The workpiece is placed between two polishing wheels: one driving wheel that rotates the part and a second abrasive wheel that applies the polishing material to the part’s surface. The part moves continuously through the machine as both wheels rotate in different directions.
- Finish Variations: The pressure, speed, and abrasive material used in the centerless polishing machine can be adjusted to achieve different finishes. Common finishes include matte, satin, and mirror finishes.
- Advantage: These machines are especially suited for polishing long, slender parts, like tubes or bars, with consistent quality and speed.
Applications:
Centerless polishing machines are widely used in industries such as:
- Automotive for polishing long components like axles, steering rods, and drive shafts.
- Aerospace, where engine components and turbine blades require precise and high-quality finishes.
- Metal tubing used in construction, furniture, and handrails.
5. CNC Polishing Machines:
CNC polishing machines integrate computer-controlled systems that allow for high precision in polishing metal parts. These machines use automated robotic arms or CNC-controlled tools to apply polishing materials at controlled speeds and pressures, offering high repeatability and tight tolerance finishes.
- Precision Control: The CNC system enables precise control of polishing parameters, such as speed, pressure, and polishing compound application. This results in consistent, repeatable finishes across production runs.
- Automation: These machines can be programmed for different metal parts, allowing operators to set up multiple processes or batch processes with minimal intervention.
- Advantages: CNC polishing machines are perfect for industries where parts require precise surface finishes, such as aerospace, medical devices, and electronics.
Applications:
CNC polishing machines are ideal for industries that require high-precision and custom finishes, including:
- Medical equipment, such as surgical instruments and implants.
- Aerospace components, including turbine blades, engine parts, and landing gears.
- High-end consumer electronics and jewelry manufacturing.
As metal polishing technologies continue to evolve, there is a growing trend toward automation, precision, and eco-friendly solutions. Manufacturers are increasingly adopting robotic polishing systems, smart sensors, and sustainable polishing compounds to meet the increasing demands for high-quality finishes while improving productivity and reducing environmental impact. The continued development of polishing machines will enable industries to achieve finer, faster, and more efficient polishing processes.
6. Handheld Polishing Machines:
Handheld polishing machines are versatile tools used for manual polishing of metal surfaces, making them ideal for smaller projects, touch-ups, or areas where larger machines can’t reach. These machines allow the operator to control the process directly and are often used for finishing delicate or intricate parts.
- Polishing Pads and Wheels: Handheld machines are usually equipped with various types of pads, including felt, buffing cloth, and abrasive wheels, depending on the desired finish. These wheels can be used in combination with polishing compounds to achieve everything from a satin finish to a mirror-like shine.
- Portability and Ease of Use: These machines are designed to be lightweight and ergonomic, enabling the operator to hold and move them freely over the part’s surface. The ability to adjust speed settings makes handheld machines adaptable to a range of materials and finishes.
- Precision Control: Handheld polishing allows for detailed work on small metal components, such as hardware, decorative items, or jewelry pieces. Operators can focus on specific areas where a more delicate or higher-quality finish is required.
Applications:
Handheld polishing machines are used in various sectors:
- Jewelry: For polishing fine jewelry, including rings, necklaces, and pendants, to achieve a high-gloss finish.
- Small Custom Projects: Ideal for polishing parts in small workshops or custom projects, where specific details and personalization are required.
- Automotive Touch-ups: Handy for polishing small vehicle parts, such as chrome trim, wheels, or areas that need repair or restoration.
7. Polishing Machines for Specialty Metals:
Certain types of metal polishing require specialized machines, especially for materials that are delicate or have unique characteristics. These specialized machines ensure that even the most challenging metals, such as titanium, precious metals, or high-carbon steels, are polished to the highest standards.
- Titanium Polishing Machines: Polishing titanium and other hard metals can be challenging due to the material’s strength and abrasiveness. Specialized polishing machines, often with higher torque and specific polishing compounds, are used to achieve a smooth surface finish without damaging the material. These machines may use abrasive belts or rotary polishing systems.
- Precious Metals Polishing: For precious metals like gold, silver, platinum, and palladium, polishing machines are designed to apply a gentle touch to avoid scratching the surface. The goal is to create a reflective, mirror-like finish without removing too much material. This requires fine abrasives and polishing wheels with delicate handling.
- High-Carbon Steel Polishing: Polishing high-carbon steel is tricky, as it requires machines that can apply consistent pressure without damaging the integrity of the metal. Specialized polishing machines are equipped with tools and abrasives designed to handle the unique abrasion resistance of high-carbon steel, achieving a smooth, corrosion-resistant finish.
Applications:
- Aerospace: Polishing titanium and other hard alloys for use in aircraft parts and turbine blades.
- Jewelry Manufacturing: Polishing precious metals to create luxury items and high-end finishes.
- Medical and Dental Equipment: Titanium and other bio-compatible metals are polished for implants, surgical instruments, and other precision parts.
8. Automated Polishing Systems:
The trend toward automation in polishing machines has led to the development of fully automated polishing systems. These systems use robotic arms, conveyor belts, and programmable controls to polish metal parts with high precision and speed, minimizing the need for manual labor.
- Robotic Polishing: Robotic arms equipped with polishing tools can be programmed to polish parts automatically. These machines are ideal for handling large production runs or polishing complex shapes where consistency and high-quality finishes are essential. The robots can perform various polishing tasks, such as edge finishing, surface smoothing, and mirror polishing, all while maintaining uniformity across multiple parts.
- Conveyor Systems: In automated systems, metal parts can be placed on a conveyor belt that moves them through different stages of polishing. The parts are processed by different machines, each optimized for a specific polishing task. For example, one machine may handle rough grinding, while another completes the final high-gloss finish.
- Integration with AI: Modern automated polishing systems can also include AI and machine learning algorithms to continuously monitor the polishing process, adjust parameters in real-time, and ensure consistent quality. This integration leads to better process optimization, reduced human error, and faster production times.
Applications:
Automated polishing systems are often used in high-volume industries such as:
- Automotive Manufacturing: Polishing large numbers of car body panels, engine parts, and chrome trim quickly and efficiently.
- Electronics: Polishing metal components and connectors used in smartphones, computers, and consumer electronics.
- Industrial Manufacturing: Mass finishing of metal components such as machine parts, gears, and valves.
9. Eco-friendly Polishing Solutions:
As sustainability becomes increasingly important, the polishing industry is also focusing on developing eco-friendly polishing solutions. These innovations include water-based compounds, biodegradable abrasives, and dust extraction systems to reduce environmental impact and improve the health and safety of workers.
- Water-based Polishing Compounds: Traditional polishing compounds often contain solvents or chemicals that can be harmful to both the environment and human health. Water-based alternatives provide a greener option, reducing the amount of harmful chemicals released into the environment.
- Biodegradable Abrasives: New types of abrasives are designed to be biodegradable, ensuring that the waste material produced during the polishing process can decompose naturally, minimizing the environmental footprint.
- Dust Collection and Filtration: Polishing processes produce a significant amount of dust and particulate matter, which can be hazardous if inhaled. Advanced polishing machines are now equipped with dust collection systems and air filtration technologies that capture the dust and prevent it from contaminating the work environment.
Applications:
- Manufacturing: Many manufacturers are now using eco-friendly polishing compounds and abrasives to meet environmental standards and reduce waste.
- Consumer Goods: Companies that produce polished metal goods, such as cookware or electronics, are shifting toward more sustainable processes.
- Automotive: The automotive industry is adopting green polishing technologies to align with environmental regulations and reduce the carbon footprint of vehicle production.
10. Polishing Machines for High-Precision and High-Specification Parts:
Polishing machines for high-precision and high-specification parts are often used in industries where the surface finish of metal parts is critical to their performance, safety, or longevity. These machines are designed to handle parts that require exacting standards for finish, such as aerospace, medical, and electronics industries.
- Precision Polishing: These machines are equipped with sophisticated controls, including CNC systems, to achieve very tight tolerances and consistent surface finishes. The polishing process can be adjusted down to microns to ensure that parts meet stringent requirements.
- Microfinishing: In applications where ultra-smooth surfaces are required, such as bearing surfaces or engine components, high-precision polishing machines can achieve microfinishing, which smooths out the microscopic imperfections that could affect performance or wear.
- Lapping: Lapping is a precision polishing process that involves abrasive particles to achieve flatness and a mirror-like finish. It is often used for flat metal surfaces, such as gaskets, valves, and rotors.
Applications:
- Aerospace: Polishing turbine blades, engine components, and structural parts to meet high-precision standards.
- Medical: Polishing parts for implants, surgical instruments, and prosthetics, where smooth, non-reactive surfaces are critical.
- Electronics: Connectors, chips, and small metal components for consumer electronics that require high-quality finishes for optimal performance.
Conclusion:
Polishing machines for metals have a broad range of applications, from large-scale manufacturing to precision industries. With advancements in automation, eco-friendly technologies, and precision control, metal polishing is becoming faster, more sustainable, and more adaptable to the specific needs of different industries. Whether for mass production, luxury goods, or high-tech equipment, polishing machines continue to play a crucial role in achieving the desired surface finishes that meet both aesthetic and functional requirements.
11. Polishing Machines for Automotive Parts:
In the automotive industry, polishing machines are essential for achieving the shiny finishes and smooth surfaces required for both aesthetic and functional purposes. These machines can handle everything from chrome bumpers to engine components, car wheels, and interior metal parts.
- Wheel Polishing Machines: Specialized polishing machines are used for the abrasive polishing of car wheels, typically made of alloys like aluminum or chrome. These machines usually have high-speed rotary tools that create a glossy finish and remove surface imperfections like scratches, oxidation, or blemishes.
- Chrome Polishing: For chrome parts, such as bumpers, grills, and trim, polishing machines need to use fine abrasives and polishing compounds to avoid damaging the thin chrome layer. Chrome polishing is a delicate process requiring careful speed control and fine-tuned pressure.
- Parts Polishing: In automotive manufacturing, polishing machines are also used for engine components like valves, engine blocks, and intake manifolds. These parts require polishing for both performance enhancement (smooth surfaces for better airflow or reduced friction) and cosmetic appeal (clean, shiny parts).
Applications:
- Automotive Trim: Polishing chrome and metal trim pieces for exterior and interior use.
- Vehicle Body Panels: Using polishing machines to achieve high-gloss finishes on body panels, ensuring luxurious appeal and resistance to wear and corrosion.
- Engine and Performance Parts: Polishing engine parts for smooth surfaces and improved engine efficiency.
12. Polishing Machines for Metal Tubing and Pipes:
In industries that require metal pipes and tubes, polishing is essential to remove oxidation, scratches, or discoloration and to achieve the desired finish and smoothness. Polishing machines used for tubing and pipes are highly specialized to ensure that parts are both aesthetic and functional.
- Tube Polishing Machines: These machines are equipped with abrasive belts or rotary tools that can polish metal tubes with uniformity across the entire surface. They are typically used for polishing stainless steel, aluminum, and brass pipes and tubes.
- Pipe Polishing and Buffing: Pipes, whether used in construction, furniture, or kitchenware, are polished to improve visual appeal and prevent corrosion. Polishing machines with adjustable speeds allow for specific finishes, ranging from satin finishes to mirror-like shines.
- Finishing for Welded Pipes: Polishing is especially important for welded pipes, where the weld joint can create visible imperfections. Special polishing techniques can help smooth out the weld and blend it into the rest of the pipe, providing a seamless finish.
Applications:
- Architectural Metalwork: Polishing tubes and pipes used in handrails, balustrades, and furniture for a sleek and high-quality finish.
- Food and Beverage Industry: Polished pipes are used in the food processing and pharmaceutical industries, where smooth surfaces help prevent the build-up of bacteria and ensure easy cleaning.
- Automotive and Exhaust Systems: Polishing exhaust pipes or tubing used in vehicle manufacturing for both aesthetic appeal and performance.
13. Polishing Machines for Industrial Components:
Industrial polishing machines are often used for finishing heavy-duty metal parts used in construction, mining, and manufacturing. These machines are designed to handle large components, such as gears, valves, bearing surfaces, and machine tools.
- Large Component Polishing: Polishing machines for industrial components are built to handle large parts, such as gears, crankshafts, or machine housings, that require a smooth surface for optimal performance and longer lifespan. These machines often have larger polishing heads or drums that can handle the dimensions of the parts.
- Surface Roughness Control: In industries like automotive, aerospace, and heavy machinery, polishing machines are used to reduce surface roughness on components like bearing races, valve seats, and gears. The goal is to create surfaces that minimize friction, reduce wear, and ensure efficient performance over time.
- Polishing for Tight Tolerances: Many industrial components must meet very tight tolerances to perform optimally in high-stress environments. Polishing machines ensure that parts achieve the required smoothness and flatness, critical for maintaining machine accuracy and performance.
Applications:
- Heavy Machinery: Polishing of machine components such as gears, shafts, and bearings to ensure smooth operation and durability.
- Aerospace: Polishing critical aerospace components like turbine blades and structural parts that demand precise finishes for performance and safety.
- Construction Equipment: Polishing of parts used in construction machinery such as excavators, cranes, and earth-moving equipment to improve the lifecycle and performance.
14. Polishing Machines for Decorative Metalwork:
For artistic and decorative metal products, polishing machines are essential to create stunning finishes that enhance the aesthetic appeal of sculptures, decorative furniture, and custom-made pieces. These machines are designed for delicate work that brings out the intricate details of the metal’s surface.
- Polishing for Sculptures: Artists and manufacturers use polishing machines to bring metal sculptures to life by smoothing rough edges and creating reflective surfaces. Machines used for decorative metalwork often use buffing wheels, felt polishing pads, or abrasive pastes to achieve a highly detailed, glossy finish.
- Furniture Finishing: In the creation of decorative furniture, polishing machines ensure that brass, copper, silver, and other metals have a smooth and elegant finish. Polishing machines are often used to bring out the shine and glow in metallic furniture accents such as legs, frames, and decorative features.
- Custom Metal Parts: Many manufacturers use polishing machines for custom decorative parts, whether for luxury watches, architectural elements, or art pieces. The ability to fine-tune the polishing process ensures that each part gets the attention to detail it needs.
Applications:
- Art and Sculpture: Polishing metal sculptures or art pieces to achieve a smooth finish and highlight intricate details.
- Luxury Decorative Items: Polishing decorative brass, bronze, or gold-plated items for high-end interior design or luxury goods.
- Custom Furniture: Metal polishing for designer furniture to achieve an elegant finish that complements the overall aesthetic.
15. Hybrid Polishing Systems:
Hybrid polishing systems combine different polishing methods and technologies to offer multi-functional machines that can handle a wide variety of tasks. These systems allow for flexibility and customization, making them ideal for industries that need to polish parts with varying shapes, sizes, and materials.
- Combination of Rotary and Belt Polishing: Some hybrid systems combine rotary polishing with abrasive belts to take advantage of the benefits of both. This provides versatility, enabling the user to switch between methods depending on the type of metal or desired finish.
- Dual-Purpose Machines: These machines are designed to accommodate multiple polishing wheels or abrasive belts, making them useful for handling a range of parts, from flat panels to cylindrical tubes. Hybrid systems are often computer-controlled, allowing precise adjustments for each phase of the polishing process.
- Advanced Features: Many hybrid polishing machines integrate robotic arms, automated loading systems, and intelligent sensors to ensure consistent quality, speed, and efficiency in polishing operations.
Applications:
- General Manufacturing: Industries requiring versatility in polishing various types of metal parts often turn to hybrid systems to improve productivity and reduce operational costs.
- Precision Industries: Hybrid systems can be adapted to polish both large components and small, intricate parts with high precision in fields like electronics, aerospace, and medical devices.
Conclusion:
Polishing machines for metals are a key part of a wide range of industries, from automotive and aerospace to art and manufacturing. The variety of polishing methods, including rotary, belt, vibratory, and CNC systems, ensures that there is a suitable solution for every application, whether it requires high-speed mass production or precise, detailed finishing. The growing focus on automation, sustainability, and precision continues to shape the future of metal polishing, improving the speed, quality, and environmental impact of these processes. As industries continue to innovate and demand better finishes, polishing machines will remain crucial in delivering products that meet both functional and aesthetic requirements.
Burr Removing Machine
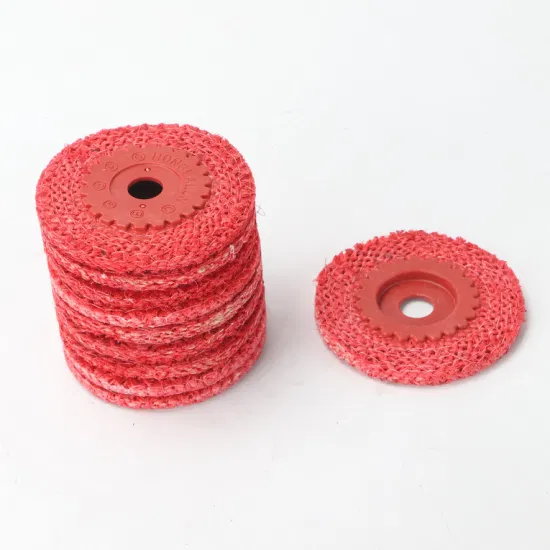
A burr removing machine is designed to remove burrs, which are unwanted projections or edges of material that form after manufacturing processes like cutting, grinding, or machining. Burrs are not only visually unappealing but can also affect the fit and function of components. Burr removal is an essential part of the post-processing stage in various industries, especially those dealing with metalworking, automotive, aerospace, and electronics.
Key Features of Burr Removing Machines:
- Abrasive Belts and Discs: Burr removing machines often use abrasive belts, discs, or brushes to effectively remove burrs from the edges of parts. The abrasives are chosen based on the material type and the level of burrs that need to be removed. These tools work by grinding or polishing the burrs off without affecting the integrity of the part.
- Rotary Brushes: Some machines use rotary brushes made of nylon or steel bristles, combined with abrasive particles, to gently remove burrs from complex geometries, without damaging the underlying surface. This method is especially useful for precision parts and delicate materials.
- Vibratory Finishing: Vibratory deburring machines use a combination of abrasive media and vibration to remove burrs. The workpieces are placed in a vibratory tub, where they are agitated with abrasive media to remove burrs gently. This process can be used for bulk parts that require a consistent, uniform finish.
- CNC Deburring: Some burr removing machines are equipped with CNC controls, allowing for high-precision deburring of parts. CNC burr removal machines can handle complex geometries and tight tolerances, ensuring that all burrs are removed efficiently without damaging the part’s features.
- Adjustable Settings: Burr removing machines often allow operators to adjust various parameters, such as speed, pressure, and abrasive type, to suit different materials and part shapes. This flexibility ensures that the machine can be used for a wide range of applications.
- Dust and Chip Collection: Since burr removal can create dust or metal chips, these machines are often equipped with dust collection systems to maintain a clean working environment. This is particularly important for ensuring worker safety and maintaining operational efficiency.
Types of Burr Removing Machines:
- Rotary Burr Removal Machines: These machines use rotary abrasives to grind off burrs. The workpiece is typically placed against a rotating abrasive wheel or disc, which removes the burrs while the machine is running at a controlled speed.
- Brush Deburring Machines: These machines use rotary brushes with abrasive fibers to remove burrs, often used for parts with delicate edges or complex shapes. This method is gentler than abrasive grinding and works well for precision parts in industries like electronics and aerospace.
- Vibratory Deburring Machines: In vibratory systems, the parts are tumbled together with abrasive media in a vibrating bowl or tub. The process is slower but ideal for high-volume production of small parts with relatively simple geometries.
- Centrifugal Barrel Finishers: These are high-speed machines where parts are placed in a barrel along with abrasive media. The barrel rotates rapidly, creating centrifugal force that makes the media grind against the parts to remove burrs. These machines are especially useful for small, intricate parts that need to be deburred evenly.
- CNC Burr Removal Machines: For complex parts that require highly precise deburring, CNC machines are programmed to automatically remove burrs in specific areas. These machines are often used in industries such as aerospace and medical devices, where precision is critical.
Applications of Burr Removing Machines:
- Automotive: Burrs often form on parts like engine components, brackets, transmission parts, and suspension components. Burr removing machines ensure that these parts have smooth edges, preventing interference with other components and improving fit and function.
- Aerospace: In aerospace manufacturing, turbine blades, airframe parts, and engine components must have burrs removed to meet strict safety and performance standards. Burr removing machines ensure the parts are free from sharp edges that could cause failures or safety risks.
- Electronics: Printed Circuit Boards (PCBs) and other electronic components often require burr removal to ensure proper connections and avoid damage to delicate parts. Burrs can also interfere with the assembly and functionality of electronic devices, so a smooth, clean finish is essential.
- Medical Devices: Medical device components such as surgical instruments, implants, and biomedical devices must be burr-free to avoid irritation or damage during use. The precision and cleanliness required in the medical industry make burr removal a critical step.
- Tool and Die Manufacturing: Burr removal is essential in the tool and die industry, as it helps ensure that cutting tools, molds, and dies operate correctly and do not compromise the precision of the final product. Burrs on tooling surfaces can cause inconsistent results or damage to the material being processed.
Advantages of Burr Removing Machines:
- Increased Product Quality: By removing burrs, these machines help improve the finish of parts, ensuring they meet high-quality standards. This is especially important for parts used in aerospace, medical, and automotive industries.
- Enhanced Safety: Burrs can be sharp and pose a risk to workers and machinery. By removing burrs, burr removing machines reduce the risk of cuts, abrasions, or damage during handling or operation.
- Improved Functionality: Burrs can affect the fit and function of components. For example, in gears or valves, burrs can interfere with smooth movement or assembly. Removing burrs ensures that parts work as intended.
- Cost-Effective: Burr removing machines allow for faster and more consistent burr removal, reducing the need for manual labor and ensuring that parts are processed quickly and efficiently. This can result in cost savings in labor and rework time.
- Flexibility: Many modern burr removing machines are adaptable to different materials and part shapes, making them versatile tools for a range of industries. Adjustable settings ensure that different types of burrs can be effectively removed without damaging the workpieces.
- Automation and Productivity: Automated burr removing machines are increasingly used in high-volume production settings, offering consistent results and improving productivity. Automation can minimize human error and speed up the process, making it easier to meet production deadlines.
Conclusion:
Burr removing machines play a crucial role in industries that deal with metal, plastic, and other materials that form burrs during manufacturing processes. These machines help to improve product quality, precision, and safety while reducing labor costs and increasing efficiency. Whether for automotive, aerospace, electronics, or medical devices, burr removing machines ensure that parts are ready for use with smooth, clean edges, contributing to better overall performance and functionality.
1. Burr Removing Machine Technology and Trends:
With the rise of automation and the demand for higher precision in manufacturing processes, burr removing machines have evolved to incorporate cutting-edge technologies that offer greater efficiency, flexibility, and consistency.
Advancements in Burr Removal Technology:
- Robotic Burr Removal: Robotic arms and automated robotic systems are increasingly being integrated into burr removal processes. These systems can be programmed to handle complex parts with precision, adapting to different geometries and materials. Robotic burr removal machines can also be equipped with vision systems to detect burrs and determine the most efficient way to remove them without compromising the quality of the part. Benefits:
- Precision in burr removal, especially for complex geometries.
- Consistency in part processing, reducing human error.
- Flexibility to work with a wide variety of parts and materials.
- CNC Burr Removal Machines: Computer Numerical Control (CNC) burr removal machines allow for high-precision deburring, where the process is controlled by software to ensure exact removal of burrs from parts. These machines are especially useful for parts that require intricate deburring due to their shapes or the materials involved. Benefits:
- Exact control of burr removal, ensuring no material is unnecessarily removed.
- Ability to handle parts with tight tolerances.
- Flexibility to work with a wide range of materials and sizes.
- Hybrid Burr Removal Systems: Hybrid systems combine different types of burr removal processes, such as abrasive brushing, vibratory deburring, and CNC systems, into a single machine. These hybrid systems are ideal for industries where parts with varying shapes and materials need to be deburred efficiently in a single operation. Benefits:
- Multi-functionality, capable of handling multiple deburring methods in one machine.
- Adaptable to a wide range of materials and geometries.
- Increased productivity, as parts can be deburred faster and more effectively.
- Intelligent Sensors and Monitoring: Advanced burr removal machines are increasingly incorporating sensors and smart monitoring systems to detect burrs and ensure optimal processing. These sensors can measure factors such as pressure, temperature, and vibration during the burr removal process. This feedback allows the machine to adjust parameters in real-time for better consistency and quality. Benefits:
- Real-time monitoring of burr removal progress.
- Self-adjusting systems that improve consistency and prevent over-processing.
- Data logging for quality control and process optimization.
Energy Efficiency and Environmental Considerations:
- Energy-Efficient Burr Removal: With increasing environmental concerns and the need for cost reductions, manufacturers are investing in energy-efficient deburring systems. These machines use less power, have reduced waste, and often come with eco-friendly abrasive materials, contributing to a lower overall environmental footprint. Benefits:
- Lower energy consumption, reducing operating costs.
- Reduced material waste, leading to fewer disposable parts.
- Compliance with sustainability regulations and goals.
- Water and Media Recycling: Many modern burr removing machines are equipped with closed-loop systems for water and abrasive media. These systems recycle the water and media used during the deburring process, which reduces consumption and ensures that abrasive materials can be reused multiple times before they need replacing. Benefits:
- Cost savings from reduced media and water usage.
- Lower environmental impact due to waste reduction.
- Compliance with environmental and waste management regulations.
- Eco-Friendly Abrasives: The abrasive materials used in burr removal are evolving to be more environmentally friendly. Biodegradable abrasives and non-toxic chemicals are gaining popularity in the deburring industry as manufacturers look to reduce their environmental impact. Benefits:
- Use of eco-friendly materials to minimize chemical waste.
- Safer operations, especially for workers exposed to abrasives.
2. Customization and Industry-Specific Solutions:
In addition to general-purpose burr removal machines, many companies now offer customized deburring systems tailored to meet the specific needs of different industries and applications. These customized machines ensure that manufacturers can maintain high standards of quality and precision, while improving overall operational efficiency.
Industry-Specific Burr Removal Applications:
- Automotive Industry: In the automotive sector, burr removal machines are designed to handle a variety of parts, such as engine components, brackets, transmission parts, and suspension components. Burrs in these parts can interfere with functionality, fit, and assembly. Specialized machines ensure that the parts are free from burrs without compromising their integrity. Customization Features:
- Robust construction to handle heavy-duty automotive parts.
- High-speed processing to keep up with mass production.
- Precision deburring for parts with tight tolerances, such as engine blocks and valves.
- Aerospace Industry: Aerospace components, such as turbine blades, airframe parts, and engine components, require burr removal processes that can meet rigorous safety and performance standards. Burrs in aerospace parts can lead to part failures, aerodynamic inefficiencies, or even safety hazards. Specialized burr removal machines for aerospace applications focus on precision and consistency. Customization Features:
- High-precision CNC systems for parts with complex geometries.
- Deburring without altering critical surfaces that affect part performance.
- Machines that can handle high temperatures and tough materials like titanium or superalloys.
- Medical Device Manufacturing: In the medical industry, burr removal is crucial for parts like surgical instruments, implants, and prosthetics. These parts require deburring without causing damage or compromising surface integrity, which is vital for patient safety and product performance. Specialized machines are designed to meet the industry’s stringent requirements for sterility, precision, and reliability. Customization Features:
- Gentle deburring methods to avoid compromising delicate surfaces.
- Machines that adhere to cleanroom standards for maintaining sterility.
- Precision deburring for parts that must meet tight tolerances for functionality.
- Electronics Industry: In the electronics industry, parts like printed circuit boards (PCBs) and connectors often have small burrs that can affect electrical connections or assembly. Burr removal machines in electronics must ensure that the parts remain functional and defect-free after deburring. Customization Features:
- Delicate deburring processes to preserve the integrity of small, intricate parts.
- Automated deburring systems for mass production of components like connectors and PCB edges.
- Non-destructive deburring for sensitive electronic parts.
3. Key Benefits of Automated Burr Removing Machines:
- Increased Productivity: Automated burr removing machines allow for high-speed, continuous deburring of parts, which greatly increases productivity in high-volume manufacturing environments.
- Reduced Labor Costs: By automating the burr removal process, companies reduce the need for manual labor, which can lower operational costs and improve the overall efficiency of the production line.
- Enhanced Consistency and Quality: Automation ensures consistent results across all parts, ensuring that burrs are removed uniformly and to the required quality standards. This results in fewer rejected parts and a better overall finish.
- Safety Improvements: By automating the deburring process, operators are less exposed to sharp edges, dust, and harmful chemicals that can arise from manual burr removal. This leads to a safer working environment.
Conclusion:
Burr removing machines play a critical role in industries that deal with metal, plastic, and other materials prone to burr formation. Through the integration of advanced technologies like robotic arms, CNC systems, and smart monitoring, these machines have become more efficient, precise, and flexible. As industries continue to demand higher precision, automation, and sustainability, burr removing machines will remain indispensable in ensuring high-quality, functional, and safe components.
4. Burr Removal in High-Volume Manufacturing:
Burr removal is especially critical in high-volume manufacturing environments, where parts are produced in large quantities. High-precision and high-efficiency machines are required to meet the demands of mass production, ensuring that each part is burr-free and meets strict quality standards.
Challenges in High-Volume Manufacturing:
- Inconsistent Burr Formation: In high-volume production, burrs can form inconsistently due to variations in material, machine settings, and part geometry. Burr removal machines must be adaptable and capable of handling these variations while maintaining consistent results across all parts.
- Minimizing Downtime: In fast-paced manufacturing environments, machine downtime can be costly. Burr removing machines must be reliable and able to maintain continuous operation to avoid disruptions to the production process.
- Maintaining Tolerances: Parts produced in high volumes often require tight tolerances to ensure proper fit and function in the final product. Burr removal machines must be capable of working within these tight tolerances to ensure that burr removal does not affect the part’s dimensions or performance.
Solutions for High-Volume Manufacturing:
- Automated Systems with Quick Changeovers: In high-volume production, automated burr removal machines that offer quick changeover capabilities are increasingly popular. These machines can be quickly reconfigured to handle different parts without significant downtime. Automated systems also help increase throughput by allowing for continuous operation, often in unmanned shifts.
- Multi-Station Systems: Multi-station burr removal systems are often used in high-volume applications to deburr multiple parts simultaneously. These systems may incorporate multiple abrasive wheels or tools that work in tandem to process different surfaces of a part, increasing throughput without compromising the quality of the deburring process.
- Robotic Integration: Robotic arms can be integrated with burr removal machines to handle the parts, position them precisely, and ensure that each part is deburred according to its specifications. Robots can work continuously, reducing the need for manual labor and improving consistency and cycle times.
- In-Line Monitoring and Inspection: In high-volume production, in-line monitoring systems are increasingly used to inspect parts in real-time. This allows for immediate detection of any issues with the burr removal process, enabling quick adjustments or rework to avoid defects. Vision systems and automated feedback loops ensure that each part meets the required deburring specifications.
- Robust Waste Management: High-volume deburring processes generate significant amounts of waste material, including abrasive particles, dust, and metal chips. Efficient waste management systems are critical to minimize waste buildup and ensure that the deburring process remains efficient. Many modern machines include dust collection units and chip conveyors to automatically remove waste, preventing clogging and maintaining the flow of the manufacturing process.
5. Material-Specific Considerations for Burr Removal:
Different materials present unique challenges when it comes to burr removal. Each material behaves differently under abrasion, requiring specialized equipment and abrasive types to achieve the best results. Understanding the material characteristics is crucial to selecting the right burr removal process.
Metal Burr Removal:
- Steel and Stainless Steel: Steel, including stainless steel, is one of the most common materials that form burrs in manufacturing. These materials tend to be tough and hard, requiring robust and aggressive deburring methods. Abrasive belts, brushes, and vibratory finishing are commonly used for steel and stainless steel burr removal.
- Common Techniques: Abrasive belt grinding, rotary brushing, vibratory deburring.
- Challenges: Hardness of the material can make burr removal more difficult, requiring high pressure or specialized abrasives.
- Aluminum: Aluminum is a softer metal and often forms fine burrs that can be difficult to remove without damaging the surface. Airflow deburring, abrasive brush systems, and vibratory tumbling are common methods for aluminum burr removal.
- Common Techniques: Brush deburring, vibratory finishing, airblast deburring.
- Challenges: The material is softer, which means care must be taken not to deform the part while removing burrs.
- Titanium and Superalloys: Titanium and superalloys are highly corrosive-resistant and hard materials commonly used in aerospace and medical applications. Burr removal for these materials requires specialized abrasives and often involves precision CNC systems for delicate deburring.
- Common Techniques: CNC deburring, abrasive blasting, robotic deburring.
- Challenges: Their hardness and high strength require robust systems that can effectively remove burrs without damaging the part’s surface integrity.
- Copper and Brass: Copper and brass are more malleable materials that often form burrs during machining processes. These materials can be deburred using abrasive brushing, vibratory finishing, or polishing techniques. The malleability of these metals makes them more forgiving, but care must still be taken to avoid surface scratching.
- Common Techniques: Rotary brushing, vibratory deburring, polishing.
- Challenges: The materials are softer, which can lead to abrasion and scratching if not carefully processed.
- Plastic and Composite Materials: Burrs also form on plastic parts during machining, but the removal process differs significantly due to the material’s softness and brittleness. Plastic burrs can be removed with abrasive brushing, sanding, or thermal deburring methods, often using low-pressure techniques to avoid damage.
- Common Techniques: Sanding, abrasive brushing, thermal deburring.
- Challenges: Brittleness and potential surface damage require care and appropriate abrasive choice.
Hard-to-Process Materials:
Some materials, like ceramics, carbon composites, and certain plastics, are more challenging to deburr. For these, ultrasonic deburring, laser deburring, and abrasive water jet cutting are sometimes used. These methods offer precision and can handle intricate parts without causing material damage.
6. Post-Deburring Processes and Finishing:
After the burr removal process, many parts undergo additional finishing steps to enhance their surface quality or prepare them for further operations. The post-deburring process is crucial to achieving the final desired surface finish and part performance.
Common Post-Deburring Processes:
- Polishing: After burr removal, parts often require polishing to achieve a smooth and glossy finish. This is especially common in industries such as medical devices, automotive, and consumer goods. Polishing can be done using abrasive belts, polishing wheels, or vibratory polishing.
- Passivation: For parts made from materials like stainless steel, titanium, and aluminum, post-deburring passivation is sometimes necessary to improve corrosion resistance. This process involves treating the metal to remove free iron and contaminants from the surface, leaving a clean and inert oxide layer.
- Coating: Many parts require coatings after burr removal to protect against wear, corrosion, or friction. Coating processes such as anodizing, electroplating, or powder coating are often applied after deburring to enhance the part’s performance and appearance.
- Cleaning: After deburring and polishing, parts are often cleaned to remove any residual dust, abrasive particles, or oils that may have accumulated during the process. This is typically done using ultrasonic cleaning, pressure washing, or chemical cleaning, depending on the material and the level of cleanliness required.
7. Future Trends in Burr Removal:
As manufacturing continues to evolve, burr removal technologies are likely to see further advancements to meet the demands of modern production environments.
- Automation and Artificial Intelligence: The use of AI-powered systems for real-time monitoring and adjustments during burr removal will continue to grow. AI can help optimize deburring processes by predicting the best parameters for different materials and geometries, improving part consistency and reducing the risk of human error.
- 3D Printing and Additive Manufacturing: As 3D printing and additive manufacturing continue to gain traction, new methods for deburring 3D printed parts will be developed. These parts often have support structures and fine burrs that require unique techniques for removal.
- Integration with Industry 4.0: The integration of burr removal systems with Industry 4.0 technologies, such as IoT sensors and cloud computing, will allow for smarter, more efficient burr removal. These systems will be able to collect data from the machines, analyze production trends, and automatically adjust parameters to optimize the process.
Conclusion:
Burr removal is an essential step in the manufacturing process that impacts product quality, safety, and functionality. With continued advancements in automation, material science, and process optimization, burr removal machines are becoming more precise, efficient, and adaptable to the diverse needs of modern industries. Whether for high-volume production, specialized materials, or complex geometries, these machines play a crucial role in delivering defect-free parts that meet stringent quality standards. As industries push the boundaries of innovation, burr removal technologies will continue to evolve to support sustainability, efficiency, and precision in manufacturing.
Porcelain and Ceramic Cookware Grinding Machine
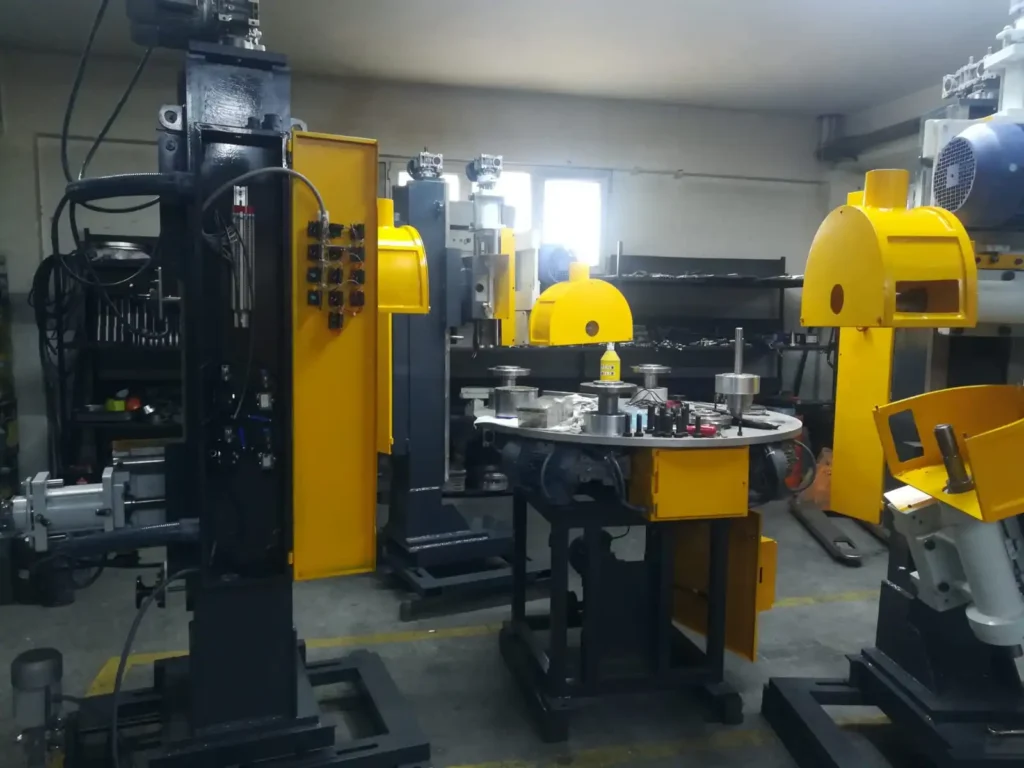
Porcelain and Ceramic Cookware Grinding Machines are specialized machines designed to handle the unique characteristics of porcelain and ceramic materials used in cookware manufacturing. These materials, while durable and heat-resistant, require precise processing during production to maintain their integrity and achieve the desired finish. Grinding machines for porcelain and ceramic cookware are typically employed for tasks such as shaping, smoothing, polishing, and surface finishing.
Here’s an overview of the key features, types, and considerations for these machines:
1. Functionality and Applications:
Grinding machines for porcelain and ceramic cookware are primarily used to:
- Smooth rough edges after the molding or cutting process.
- Polish surfaces to create a glossy, smooth finish, enhancing the cookware’s appearance and functionality.
- Remove excess material that could affect the shape or balance of the cookware.
- Shape intricate designs or handle high-precision grinding for items like porcelain pots, ceramic plates, or bowls.
- Refine surfaces before glazing or coating steps.
These machines are crucial in ensuring that ceramic cookware is aesthetically appealing, functional, and free of defects such as uneven surfaces or sharp edges.
2. Types of Grinding Machines for Porcelain and Ceramic Cookware:
A. Surface Grinding Machines:
Surface grinding machines are designed for grinding large, flat surfaces. These machines use a rotating abrasive wheel to remove material from the surface of the ceramic or porcelain cookware.
- Disc Surface Grinders: These machines use flat grinding discs to polish large surfaces, such as the bottom of ceramic pots or the outer surfaces of cookware.
- Rotary Surface Grinders: These grinders are used for more intricate work or for achieving smoother finishes, often on smaller cookware items or parts with curves. Advantages:
- Provides smooth, even surfaces.
- Capable of fine polishing and smoothing.
B. Cylindrical Grinding Machines:
Cylindrical grinding machines are used for grinding cylindrical objects such as ceramic or porcelain cups, mugs, or certain cookware items that have a round, tubular shape. The workpiece is held between centers or on a chuck while it is rotated, and the abrasive wheel grinds the outer surface.
Advantages:
- Precision grinding of round or tubular cookware items.
- Ability to achieve high tolerances on size and finish.
C. Belt Grinding Machines:
Belt grinding machines use a continuous loop of abrasive material to grind surfaces. These machines are ideal for grinding the edges and intricate contours of porcelain and ceramic cookware.
Advantages:
- Efficient for larger surfaces or irregular shapes.
- Versatile for a range of operations from rough grinding to fine polishing.
D. Angle Grinders and Handheld Grinding Machines:
For smaller porcelain and ceramic cookware items, angle grinders or handheld grinders are used. These are especially useful for finishing smaller, more intricate parts or for dealing with repairs or modifications.
Advantages:
- Portable and easy to handle.
- Useful for detailed or localized grinding on specific areas.
E. Vibratory or Tumbler Grinding Machines:
These machines use abrasive media to grind or polish cookware in bulk. They are ideal for polishing multiple pieces at once and are often used for post-production finishing or deburring processes. The parts are placed in a vibrating drum with abrasive media, and as the drum moves, the media grinds and polishes the surface of the cookware.
Advantages:
- Efficient for high-volume processing.
- Suitable for finishing or polishing multiple pieces simultaneously.
3. Key Features of Porcelain and Ceramic Cookware Grinding Machines:
- Adjustable Speed: Many grinding machines come with adjustable speed controls to accommodate different stages of the grinding process. Lower speeds are often used for rough grinding, while higher speeds are used for polishing.
- Dust and Particle Control: Grinding ceramics can produce a lot of dust and fine particles. High-quality grinding machines are equipped with dust extraction systems to minimize airborne particles and ensure a cleaner work environment.
- Coolant or Lubricant Systems: Some grinding operations, especially those involving harder materials, require the use of coolants or lubricants to prevent overheating, reduce friction, and ensure a smooth finish.
- Precision Control: These machines often feature fine-tuning controls that allow operators to set precise grinding depths or ensure an even surface finish, essential for the intricate designs of ceramic cookware.
- Automated Loading and Unloading Systems: In high-volume production, automated systems can be used to load and unload cookware from the grinding machine, enhancing efficiency and reducing manual handling.
4. Considerations When Choosing a Grinding Machine:
- Material Type: Ceramic and porcelain are brittle materials that can crack or break under improper handling. The grinding machine should be designed to handle these materials delicately, offering enough power to grind without damaging the cookware.
- Grinding Finish: Different stages of production may require different finishes. Some machines are designed for rough grinding, while others are optimized for polishing and achieving a fine surface.
- Automation vs. Manual: High-volume manufacturers may opt for fully automated grinding machines to reduce labor costs and increase efficiency. However, for small-scale operations or intricate designs, manual or semi-automated machines might be more suitable.
- Safety Features: Given that grinding ceramic materials can produce hazardous dust or shards, safety features such as dust collection systems, shielding, and operator safety controls are essential.
5. Benefits of Grinding Porcelain and Ceramic Cookware:
- Surface Refinement: Grinding improves the smoothness and overall finish of the cookware, making it more appealing for consumers and suitable for final processing steps like glazing.
- Defect Removal: Grinding helps remove imperfections such as rough edges, bumps, or burrs, ensuring that the cookware meets both aesthetic and functional standards.
- Enhanced Durability: Proper grinding and finishing can enhance the durability and functional properties of the cookware, making it resistant to chipping and improving its lifespan.
- Customization: Grinding machines can be used to add customized patterns or finishes on porcelain and ceramic cookware, which is essential for specialized or luxury products.
6. Maintenance and Care:
To ensure that porcelain and ceramic cookware grinding machines continue to perform optimally, regular maintenance is necessary. This includes:
- Cleaning the grinding wheels and abrasives to prevent buildup.
- Inspecting the coolant system to ensure it’s functioning correctly.
- Checking alignment and calibration to ensure the machine operates with the correct precision.
- Lubricating moving parts to prevent wear and tear.
Conclusion:
Grinding machines for porcelain and ceramic cookware are essential tools in the production of high-quality, aesthetically pleasing, and durable cookware. By utilizing specialized machines, manufacturers can ensure that every piece of ceramic or porcelain cookware meets the desired standards for smoothness, finish, and functionality. From high-volume automated solutions to more manual or semi-automated systems for smaller batches, the right grinding equipment ensures efficient and effective processing of cookware materials, leading to improved product quality and consumer satisfaction.
7. Emerging Trends in Porcelain and Ceramic Cookware Grinding:
As technology evolves, so do the methods and machinery used in porcelain and ceramic cookware grinding. Manufacturers are increasingly adopting advanced technologies to improve the precision, speed, and efficiency of their grinding operations.
A. Automation and Robotics:
Automation is a key trend in modern manufacturing. For porcelain and ceramic cookware grinding, automation offers several advantages:
- Increased Efficiency: Automated systems reduce manual labor and can handle high-volume production with consistency.
- Precision: Robots and automated systems can achieve consistent results, even in high-precision grinding tasks. This is crucial for ensuring uniformity in cookware pieces that may have complex shapes or delicate surfaces.
- Reduced Downtime: With automated systems, maintenance schedules can be optimized, and the machines can run continuously without the need for constant human intervention.
Example: Robotic arms integrated with grinding machines can load and unload cookware parts automatically, while also adjusting the grinding parameters to ensure each piece is treated correctly according to its material and design.
B. Integration of AI and Machine Learning:
Artificial Intelligence (AI) and machine learning are being incorporated into ceramic cookware grinding systems to improve the intelligence of the process. AI-driven systems can analyze data from sensors to:
- Optimize grinding parameters based on real-time feedback (e.g., material type, surface condition).
- Detect potential defects in the workpieces, ensuring that parts are within the required tolerance levels.
- Predict tool wear and suggest maintenance schedules to ensure optimal machine performance.
Example: AI algorithms can monitor the grinding process and automatically adjust the speed and pressure based on the current conditions of the material, reducing errors and increasing the overall quality of the finish.
C. Advanced Abrasive Materials:
The development of advanced abrasive materials is enabling better performance in grinding and polishing porcelain and ceramic cookware. These materials include:
- Diamond and CBN (Cubic Boron Nitride) abrasives: These are ultra-hard materials ideal for grinding harder ceramic and porcelain surfaces without generating excessive heat or damaging the cookware.
- Ceramic-based abrasives: These abrasives are specifically formulated to handle the fragile nature of porcelain and ceramic without causing chips or cracks.
- Superabrasives: These abrasives provide greater precision and are often used in applications requiring high-quality finishes, such as cookware grinding.
Benefits:
- These abrasives provide a longer lifespan for the grinding wheels.
- The abrasive materials help achieve ultra-smooth finishes with less pressure and heat, reducing the risk of thermal cracks or surface imperfections.
D. Precision Grinding for Complex Designs:
As consumer demand for more aesthetically pleasing cookware grows, manufacturers are increasingly designing pieces with intricate shapes, patterns, and textures. Advanced grinding machines can handle these complex geometries with high precision, ensuring that all surfaces of the cookware are smooth and polished, even in hard-to-reach areas.
- Multi-Axis CNC Grinding Machines: These machines can handle intricate or asymmetrical designs by controlling the grinding tool on multiple axes simultaneously. This allows manufacturers to grind and polish the cookware evenly, even with the most complex shapes.
- Automated Polishing Systems: These systems are designed to polish cookware using abrasive wheels that can move in multiple directions to create a uniform, flawless finish across all surfaces, including edges, handles, and lids.
E. Sustainability and Environmental Considerations:
Sustainability is becoming an essential factor in manufacturing, including for porcelain and ceramic cookware. Manufacturers are increasingly incorporating eco-friendly practices in their grinding and polishing processes:
- Energy-Efficient Machines: Modern grinding machines are designed to reduce energy consumption, helping manufacturers lower their carbon footprint while increasing productivity.
- Closed-Loop Coolant Systems: Closed-loop systems help recycle water and cooling fluids used in the grinding process, minimizing waste and environmental impact.
- Dust and Waste Management: New grinding machines incorporate improved dust collection systems to capture ceramic dust, reducing airborne particles and waste generated during production. This results in a cleaner environment and reduces the need for disposal of harmful waste.
Example: Some companies are exploring the use of water-based coolants or biodegradable lubricants to replace traditional cutting fluids, reducing the environmental impact and improving the safety of operators.
F. Digital Twins and IoT Integration:
The integration of IoT (Internet of Things) technologies and Digital Twin models is a growing trend. Digital twins are virtual replicas of physical grinding machines that allow manufacturers to simulate, monitor, and optimize the grinding process in real time.
- Remote Monitoring: Manufacturers can monitor machine performance and health from any location, adjusting operations as needed to ensure maximum productivity.
- Predictive Maintenance: IoT sensors embedded in grinding machines can collect data on machine health, such as vibrations, temperature, and tool wear. This data can be analyzed to predict when maintenance is needed, avoiding unexpected breakdowns and minimizing downtime.
Example: A digital twin of a grinding machine might predict that a certain grinding wheel will wear down after a set number of hours, alerting operators to replace it before it causes defects in the cookware.
8. Maintenance and Optimization:
Regular maintenance and optimization are essential to keep porcelain and ceramic cookware grinding machines running smoothly and efficiently.
A. Regular Calibration:
For precise grinding, regular calibration of the machine is essential. Ensuring that the grinding tool aligns perfectly with the part during each cycle helps maintain the accuracy of the grinding process and prevents defects such as uneven surfaces or incorrect edge shapes.
B. Tool Replacement and Reconditioning:
Since grinding wheels wear out over time, it’s crucial to replace or recondition them regularly. The wear and tear of grinding tools can affect the quality of the finish, so monitoring tool condition and scheduling timely replacements is vital.
C. Dust and Particle Control:
Maintaining the dust extraction system is essential for keeping the work environment safe and ensuring the machines operate efficiently. Accumulated dust can lead to clogging and reduce the efficiency of grinding machines. Regular cleaning of filters and ensuring that the extraction system is working optimally is critical.
D. Lubrication and Fluid Maintenance:
For machines that use coolants or lubricants during the grinding process, regular fluid checks and replacements are necessary. Clean coolant fluid helps reduce heat buildup and friction, ensuring that the grinding process is smooth and does not damage the porcelain or ceramic material.
9. Conclusion:
Grinding porcelain and ceramic cookware requires a combination of precision, efficiency, and innovation. With the increasing demand for aesthetic appeal, durability, and functionality, grinding machines for porcelain and ceramic cookware must be designed to handle a variety of materials and shapes, while delivering consistent, high-quality results.
As the industry moves forward, the adoption of advanced technologies such as automation, AI, robotics, and IoT integration will continue to shape the future of cookware grinding. These innovations will help manufacturers not only increase efficiency and reduce costs but also improve the overall quality of their products, meeting consumer demands for both form and function in ceramic and porcelain cookware. Sustainable practices and energy-efficient designs will also play a pivotal role in the future of grinding machine technologies, ensuring a cleaner and more eco-friendly production process.
10. Challenges and Solutions in Porcelain and Ceramic Cookware Grinding:
Grinding porcelain and ceramic cookware presents unique challenges due to the brittle and fragile nature of these materials. These challenges require careful consideration and specialized solutions to prevent material damage and ensure high-quality finishes.
A. Fragility of Ceramic and Porcelain:
One of the main challenges in grinding porcelain and ceramic cookware is the brittleness of these materials. Excessive force or improper handling can lead to cracks, chips, or fractures, especially if the material is not supported correctly during the grinding process.
Solution:
- Low-Force Grinding: Machines designed for porcelain and ceramic grinding are often engineered to apply gentle pressure while ensuring effective material removal. Using lower force or pressure during grinding helps avoid breakage and surface defects.
- Adaptive Grinding Technology: Advanced grinding machines equipped with force sensors or feedback loops can automatically adjust the grinding pressure and speed to prevent excessive force, especially when working with fragile materials.
- Soft Support Fixtures: Specialized support fixtures that cradle the cookware during grinding help distribute pressure evenly and reduce the risk of cracking.
B. Heat Generation:
Grinding processes, especially those involving high-speed rotation or aggressive abrasives, can generate substantial heat. If not managed properly, this heat can lead to thermal cracks or distortion in the cookware.
Solution:
- Cooling Systems: Many porcelain and ceramic grinding machines incorporate coolant or water-based lubrication systems to keep the material cool during grinding. This helps dissipate heat and prevent thermal damage.
- Advanced Abrasives: The use of diamond abrasives or CBN (Cubic Boron Nitride) abrasives, which are designed to operate at lower temperatures, can reduce the heat generated during grinding. These materials are harder and more effective at material removal, reducing friction and heat buildup.
C. Surface Finish Quality:
Achieving a consistent and high-quality finish is critical in porcelain and ceramic cookware, especially for products where aesthetics are a significant factor. Grinding can sometimes leave uneven surfaces, marks, or scratches.
Solution:
- Multiple-Stage Grinding: To achieve a flawless finish, manufacturers often use a multi-stage grinding process. This typically starts with rough grinding to remove large imperfections, followed by finer grinding steps to polish and refine the surface.
- Polishing Tools: Specialized polishing wheels or brushes are used after grinding to smooth out minor imperfections and create a reflective surface. Vibratory finishing machines are also employed to give a uniform finish across the cookware.
- Automated Inspection Systems: The use of advanced vision systems or automated optical inspection tools can help identify surface defects in real time. These systems provide feedback to operators, ensuring that only flawless pieces proceed through the production line.
D. Tool Wear and Abrasive Material Selection:
Due to the hardness and abrasiveness of porcelain and ceramic materials, grinding wheels and abrasives can wear down quickly, leading to inefficient grinding, reduced precision, and inconsistent finishes.
Solution:
- Quality Abrasives: Using high-quality abrasives, such as diamond or ceramic-based grinding wheels, can help mitigate the wear problem. These materials last longer and maintain their sharpness over time, ensuring consistent performance.
- Regular Tool Replacement and Maintenance: Implementing a preventive maintenance schedule that includes regular tool inspections and reconditioning ensures that the grinding equipment remains in optimal condition. Using monitoring systems to track tool wear and predict when replacement is needed can prevent disruptions in production.
E. Controlling Dust and Waste:
Grinding porcelain and ceramics generates significant dust and debris, which can pose environmental and safety concerns. The dust produced during grinding can also affect the quality of the product, as fine particles may adhere to surfaces.
Solution:
- Dust Collection Systems: Modern grinding machines are equipped with high-efficiency dust extraction systems that capture fine particles during grinding. These systems not only protect the health of operators but also ensure a cleaner work environment.
- Waste Management: Advanced systems for automated waste handling can help collect and filter dust or waste materials generated during grinding. This ensures that the waste is disposed of safely or recycled, reducing the environmental impact.
11. Key Considerations in Selecting Porcelain and Ceramic Cookware Grinding Machines:
When selecting the right grinding machine for porcelain and ceramic cookware, manufacturers should consider several factors to ensure the best performance and quality.
A. Material Compatibility:
Not all grinding machines are suitable for all types of ceramics or porcelain. Manufacturers need to assess the specific properties of the materials they’re working with, such as hardness, fragility, and thickness. Machines should be chosen that offer flexibility in handling various material types, whether hard porcelain or brittle ceramic.
B. Production Volume and Automation:
For high-volume production, automated grinding machines that can run continuously with minimal supervision are essential. These machines can handle larger quantities of cookware efficiently while maintaining consistent quality. For smaller-scale production or custom pieces, semi-automated or manual machines may be more appropriate, allowing for more flexibility in design and finishing.
C. Surface Finish Requirements:
The desired finish on the cookware plays a significant role in selecting the right grinding machine. If a high-gloss finish or mirror-like surface is required, a polishing machine or multi-stage grinding system would be ideal. If the goal is to achieve functional surfaces (e.g., removing burrs or smoothing edges), a simpler surface grinder or belt grinder may suffice.
D. Precision and Tolerances:
For some types of ceramic cookware, particularly those with intricate designs, high precision is critical. Machines that offer multi-axis control and precision adjustments can handle complex geometries and tight tolerances, ensuring that each piece is manufactured to specification.
E. Energy Efficiency and Sustainability:
Given the growing focus on environmental sustainability, it’s important to choose machines that offer energy-efficient operations and eco-friendly features. This can include energy-saving motors, closed-loop coolant systems, and machines designed to minimize waste and emissions.
12. Future Directions and Innovations in Grinding Technology:
As the demand for high-quality porcelain and ceramic cookware continues to grow, advancements in grinding technologies will drive the evolution of manufacturing processes. Here are some potential innovations on the horizon:
A. AI and Predictive Analytics:
The future of porcelain and ceramic cookware grinding will likely see more sophisticated AI-powered systems that can learn from data and improve their grinding processes. AI could help predict issues before they occur, optimize grinding parameters in real-time, and automatically adjust settings for different types of cookware.
B. 3D Grinding:
With the rise of 3D printing and additive manufacturing, there may be more applications for 3D grinding technologies, where specialized grinding heads or tools can be used to precisely finish complex geometries that are difficult to achieve with traditional grinding techniques.
C. Collaborative Robots:
In high-volume operations, collaborative robots (cobots) could work alongside human operators in the grinding and finishing process, helping to load and unload pieces while also assisting with delicate handling, especially in smaller-scale custom runs.
D. Advanced Surface Measurement Technologies:
The integration of 3D scanning and surface mapping technologies could enable real-time surface quality control. These systems could monitor the quality of each piece during grinding, flagging imperfections immediately and allowing operators to correct issues as they arise.
Conclusion:
The grinding process for porcelain and ceramic cookware plays a critical role in ensuring both the aesthetic and functional quality of the final product. With advancements in technology, manufacturers are able to meet the rising demands for high-precision, sustainable, and aesthetically pleasing cookware. As new innovations emerge, the ability to fine-tune the grinding process will enable greater flexibility and efficiency in producing high-quality cookware, while also addressing key challenges such as material fragility, dust control, and surface finish quality. By selecting the right equipment, incorporating advanced technologies, and adhering to best practices in maintenance and operation, manufacturers can continue to deliver products that meet the highest standards in both performance and design.
Flat Surface Polishing Machine
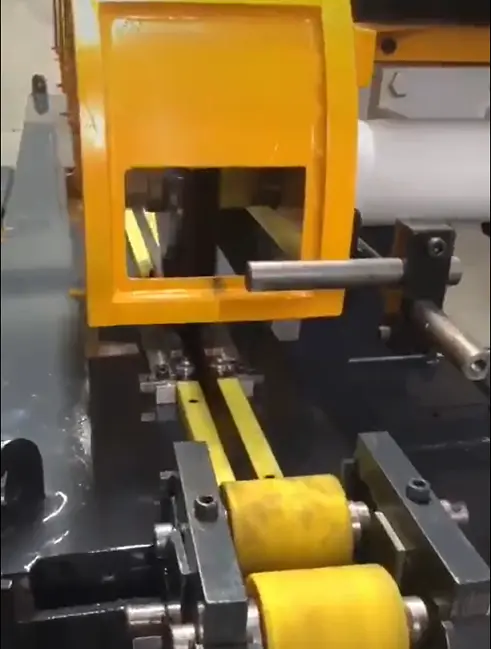
Flat surface polishing machines are designed to achieve smooth, high-quality finishes on flat surfaces of various materials, including metals, ceramics, glass, and plastics. These machines are commonly used in industries such as manufacturing, metalworking, and cookware production, where maintaining a precise, uniform surface finish is critical.
Key Features and Components of Flat Surface Polishing Machines
- Polishing Belt or Disc: Flat surface polishing machines typically use either abrasive belts or polishing discs, depending on the material and desired finish. These abrasives are available in different grit sizes, allowing operators to choose the appropriate level of abrasiveness for the specific application. The machine’s abrasive medium works by gradually smoothing out imperfections on the flat surface.
- Rotary or Linear Motion: The motion of the polishing tool is usually either rotary or linear. In rotary motion systems, the polishing head or wheel rotates on its axis to polish the surface. Linear motion systems use a back-and-forth or up-and-down movement to polish larger surfaces, ensuring an even finish.
- Pressure Adjustment: To ensure the polishing is uniform and does not damage the material, many flat surface polishing machines offer adjustable pressure settings. This allows operators to control the amount of force applied to the material during polishing, helping to avoid unwanted indentations, scratches, or heat damage.
- Speed Control: Flat surface polishing machines often feature variable speed control, allowing the operator to adjust the speed of the abrasive tool. Lower speeds are typically used for finer finishes, while higher speeds are used for heavy-duty polishing tasks, such as removing deep scratches or imperfections.
- Dust Extraction Systems: Since polishing generates dust and debris, many modern polishing machines come equipped with dust collection systems. These systems capture the dust produced during the polishing process, preventing it from contaminating the work environment and ensuring cleaner operations.
- Cooling Systems: Cooling fluids or sprays are sometimes employed to prevent heat buildup during the polishing process, especially when working with materials prone to thermal damage, such as porcelain, ceramics, or metals. These systems help maintain consistent surface quality and extend the lifespan of the abrasives.
Types of Flat Surface Polishing Machines
- Belt Polishing Machines:
- Structure: These machines use long abrasive belts that move around rollers, applying constant pressure on the surface.
- Applications: Typically used for polishing metals, plastics, or ceramics to achieve a consistent finish. They are ideal for working with flat surfaces on cookware, industrial parts, or automotive components.
- Disc Polishing Machines:
- Structure: These machines use a rotating abrasive disc or wheel to polish the surface.
- Applications: Often used in the final stages of surface finishing, disc polishing machines are great for achieving a mirror-like, glossy finish on metals, ceramics, or glass.
- Vibratory Polishing Machines:
- Structure: These machines use vibration to agitate the workpiece and abrasive media, providing a uniform polish.
- Applications: Suitable for polishing large numbers of parts at once, such as in mass production environments. Vibratory polishing is often used in industries like jewelry making and small appliance manufacturing.
- Centrifugal Polishing Machines:
- Structure: Similar to vibratory polishing but using centrifugal force for a more aggressive finish.
- Applications: Typically used for larger or bulkier workpieces that need a more intensive finish, such as in automotive or heavy machinery components.
- Double-Sided Flat Surface Polishing Machines:
- Structure: These machines simultaneously polish both sides of a workpiece by applying pressure from two separate polishing units.
- Applications: Commonly used in manufacturing industries for polishing thin materials, such as metal sheets, glass, or ceramics.
Applications of Flat Surface Polishing Machines
- Metal Industry: For polishing stainless steel, aluminum, brass, and other metals used in cookware, machinery, or automotive parts. These machines help achieve high-gloss finishes, often required in applications like decorative metalwork or precision machinery.
- Ceramic and Porcelain Industry: In the cookware industry, flat surface polishing machines are used to achieve smooth, scratch-free, and aesthetically pleasing surfaces for ceramic and porcelain dishes.
- Glass Industry: These machines are ideal for polishing flat glass surfaces, such as windows, mirrors, and automotive glass, to remove imperfections and give a high-shine finish.
- Plastic Industry: Used for polishing plastic components, often for consumer goods or precision plastic parts that require a smooth, glossy surface.
Advantages of Flat Surface Polishing Machines
- Consistency: Automated polishing machines offer consistent and uniform finishes across large batches of items, ensuring each piece meets the desired standard.
- Time Efficiency: These machines increase production speed, reducing the manual effort required to achieve a high-quality finish.
- Precision: The ability to control speed, pressure, and abrasiveness enables precise polishing, which is especially important when dealing with fragile or delicate materials like porcelain or glass.
- Customizability: Many flat surface polishing machines are adaptable, allowing manufacturers to select different abrasives or adjust settings to achieve the desired surface finish for specific materials.
Maintenance and Care
- Regular Inspections: Routine checks should be made to ensure abrasive belts or discs are not excessively worn or damaged. Regular tool changes or reconditioning are essential for maintaining consistent performance.
- Lubrication and Cooling: Ensure the cooling systems are functioning properly to prevent heat buildup during polishing, which can damage materials or lead to tool wear.
- Cleaning Dust Collection: Dust and debris should be removed from the dust collection systems regularly to prevent clogs and ensure effective dust extraction during polishing operations.
Conclusion
Flat surface polishing machines play a crucial role in achieving high-quality finishes on flat surfaces across various industries. From metal parts to ceramic cookware, these machines help improve both the aesthetic appeal and functional quality of the products. By offering precise control, customizable settings, and the ability to handle different materials, flat surface polishing machines are indispensable for mass production environments and industries that prioritize uniformity and consistency in their products.
Choosing the Right Flat Surface Polishing Machine
When selecting a flat surface polishing machine, several factors must be considered to ensure it meets the specific needs of your production process and material requirements:
1. Material Type and Hardness
Different materials require different polishing techniques and machines. Harder materials like metals (stainless steel, aluminum) or certain ceramics may need more aggressive polishing machines, such as those using heavier abrasives or more powerful motors. Softer materials like plastics or delicate ceramics require machines with adjustable pressure and more gentle abrasive options to avoid surface damage.
2. Surface Finish Requirements
Depending on the desired finish (e.g., matte, satin, or high-gloss), the machine specifications may vary. Some flat surface polishing machines offer advanced controls for fine-tuning polishing stages, allowing for a multi-stage process with progressively finer abrasives to achieve the perfect surface finish. The machine should also allow easy changes of abrasives to meet different finishing requirements.
3. Production Volume
For high-volume production, automated machines with continuous or semi-continuous processes are ideal. These machines typically come with features like automatic loading and unloading systems, increased throughput capacity, and the ability to work on larger batches at once. For lower-volume or more specialized production, machines with a more manual setup may be more appropriate.
4. Size of the Workpiece
Consideration must be given to the size of the workpieces being polished. Machines come in different configurations depending on whether you’re working with small components or large panels. For instance, machines that offer double-sided polishing are ideal for polishing large, flat surfaces like metal sheets or thick ceramics. Machines for smaller parts might be compact, with adjustable fixtures to handle varying sizes.
5. Automation and Customization
Automated polishing machines, such as those with CNC controls, offer enhanced precision and repeatability. If the production demands frequent changes in design or material, a more customizable machine with programmable settings might be necessary. Automation can also improve overall production efficiency by reducing the need for manual intervention and ensuring consistent results.
6. Ease of Use and Setup
Look for machines that are easy to set up and adjust, particularly for different materials or surface finishes. Machines that are difficult to operate or require extensive training can slow down production, while intuitive controls and preset programs can streamline operations. Machines with user-friendly interfaces or touchscreen controls are particularly helpful for minimizing operational errors.
7. Maintenance and Support
Like any industrial equipment, flat surface polishing machines require regular maintenance to ensure longevity and high performance. Choose a machine from a manufacturer that provides good after-sales support, including easy access to spare parts, technical assistance, and clear guidelines for machine upkeep. Machines that are easier to maintain with readily available consumables (e.g., abrasives, cooling fluids) can save time and money in the long run.
Emerging Trends in Flat Surface Polishing
As technology evolves, several trends are shaping the future of flat surface polishing machines:
1. Smart Polishing Machines
With the rise of Industry 4.0, smart polishing machines equipped with sensors and connected to a central network can automatically adjust to optimize performance. Data analytics can be used to monitor the wear of abrasives, predict maintenance needs, and track the quality of each product. This level of automation and monitoring allows for continuous improvement of processes and minimizes downtime.
2. Energy Efficiency
Energy consumption is a growing concern for manufacturers. Newer polishing machines are designed to be more energy-efficient, using lower power consumption motors and optimized cooling systems. These features not only help reduce operational costs but also contribute to a greener and more sustainable production environment.
3. Advanced Abrasive Materials
The development of advanced abrasive materials such as diamond-coated abrasives and superabrasives is changing the landscape of flat surface polishing. These abrasives allow for more efficient material removal, reducing processing time and improving surface quality. They also last longer than traditional abrasives, reducing the frequency of replacements.
4. Hybrid Machines
Hybrid machines that combine grinding, polishing, and finishing processes in one machine are gaining popularity. These machines allow manufacturers to complete multiple stages of surface finishing in a single pass, improving both time efficiency and overall productivity. They can handle different materials and finishes without requiring multiple machines.
5. Robotic Integration
Robotic arms are increasingly being integrated with polishing machines, especially for high-precision tasks. These robotic systems can be programmed for custom polishing paths and can work in collaborative environments alongside human operators. With robotic integration, polishing machines can be automated even further, improving throughput and reducing the need for human intervention in hazardous tasks.
6. Sustainable Polishing Practices
Environmental concerns are pushing manufacturers to adopt sustainable polishing practices. This includes using eco-friendly abrasives that have minimal environmental impact, along with closed-loop systems for dust and waste management. Additionally, some polishing machines are being designed to work with biodegradable or less harmful coolants and lubricants, which reduces the overall ecological footprint of the polishing process.
Conclusion
Flat surface polishing machines are essential for achieving high-quality finishes on various materials, ranging from metals and ceramics to glass and plastics. By selecting the right machine based on material type, desired finish, production volume, and other key factors, manufacturers can optimize their processes, improve product quality, and increase efficiency.
The advancements in automation, smart technology, and sustainability continue to shape the future of flat surface polishing, making these machines more efficient, cost-effective, and adaptable to various industry needs. As technology evolves, flat surface polishing machines will become even more integral to the production of precision components, consumer goods, and industrial products, driving improvements in surface quality and production workflows across various sectors.
Challenges in Flat Surface Polishing and Solutions
While flat surface polishing machines offer numerous advantages, several challenges may arise during the polishing process. Understanding and addressing these challenges can significantly enhance the quality and efficiency of operations.
1. Surface Defects and Imperfections
One of the most common issues in flat surface polishing is the appearance of defects such as scratches, grooves, or uneven finishes. These imperfections can occur due to improper abrasive selection, incorrect pressure, or poorly maintained equipment.
Solutions:
- Abrasive Selection: Choosing the correct abrasive material is essential for preventing surface defects. Softer abrasives are typically used for finer finishes, while coarser abrasives are ideal for initial rough polishing.
- Multiple Polishing Stages: Employing a multi-stage polishing process with progressively finer abrasives helps to eliminate scratches and uneven areas. Using finer abrasives at each stage can gradually smooth the surface, achieving a high-gloss finish without deep scratches.
- Quality Control: Implementing regular inspection systems, such as automated optical inspection (AOI) or surface scanning, can help identify imperfections early in the process. These systems can also assist in adjusting parameters in real-time to ensure consistency across parts.
2. Material Removal Rate and Over-polishing
Another challenge is achieving an optimal material removal rate without over-polishing or excessively thinning the workpiece. Over-polishing, particularly in thin or fragile materials, can lead to dimensional changes or degradation of material properties.
Solutions:
- Adjustable Speed and Pressure: Modern flat surface polishing machines come with variable speed and pressure controls that allow operators to fine-tune the polishing process. This ensures an even material removal rate and helps prevent over-polishing.
- Automatic Pressure Control: Advanced machines may include pressure sensors that adjust the force applied to the surface, ensuring it remains within safe limits for each type of material.
- Monitoring Tools: Incorporating real-time monitoring systems can track the removal rate and ensure that it stays within desired thresholds. This may include monitoring thickness reduction and adjusting polishing parameters accordingly.
3. Heat Generation
Polishing can generate heat, which may cause thermal damage to sensitive materials, especially ceramics, plastics, and certain metals. Excessive heat can lead to thermal stress, warping, or changes in material properties.
Solutions:
- Cooling Systems: Incorporating coolant systems or using coolants during the polishing process can significantly reduce the heat generated by friction. Some systems also spray a fine mist of coolant directly onto the workpiece or abrasive surface to dissipate heat.
- Low-Speed Polishing: Using lower polishing speeds can reduce friction and, consequently, heat generation. While this may increase the process time, it helps avoid heat-related damage to the material.
4. Dust and Debris Management
Polishing generates significant dust and debris, especially when working with abrasives like sandpaper, diamond discs, or belt abrasives. Dust can contaminate the environment, cause health risks, and lead to a mess in the production area.
Solutions:
- Dust Extraction Systems: Many flat surface polishing machines come equipped with integrated dust collection systems that capture fine particles during the polishing process. These systems help ensure a cleaner work environment and reduce health risks for operators.
- Closed-Loop Systems: Some systems use closed-loop filtration, where dust is not only captured but also filtered and returned into the production cycle, making the entire polishing process more sustainable and less wasteful.
5. Consistency Across Different Workpieces
In mass production, achieving consistent results across a large batch of workpieces is critical. Variations in surface finish or polishing quality can lead to product defects or deviations from specifications.
Solutions:
- CNC Polishing Machines: Machines equipped with CNC (Computer Numerical Control) systems ensure high precision and repeatability. By programming exact parameters for polishing, these machines can maintain a consistent quality across all pieces.
- Automated Handling Systems: For large batches, using automated loading and unloading systems helps ensure that all workpieces receive the same amount of polishing. This ensures uniform treatment and helps minimize human error.
- Sensors and Feedback Loops: Polishing machines with integrated sensors that measure surface quality in real-time can adjust the polishing parameters automatically to ensure consistency across all pieces.
6. Abrasive Wear and Machine Maintenance
As abrasives are used, they naturally wear down, affecting their effectiveness and leading to inconsistent polishing results. Additionally, machines themselves require regular maintenance to continue operating optimally.
Solutions:
- Regular Maintenance Schedules: Establishing a routine maintenance schedule, which includes checking the condition of abrasives and replacing them as necessary, ensures optimal performance. Monitoring abrasive wear and tear is vital to preventing subpar results.
- Advanced Abrasives: Using longer-lasting abrasives like diamond-coated abrasives or superabrasives can extend the lifespan of the polishing media, reducing downtime and improving consistency.
- Automated Tool Monitoring: Some advanced machines are equipped with sensors to monitor the wear of polishing tools. These sensors can alert operators when the abrasives need to be replaced or reconditioned, preventing sudden performance drops.
Innovative Technologies Enhancing Flat Surface Polishing
The flat surface polishing industry has seen several technological advancements aimed at improving the quality, efficiency, and versatility of polishing machines.
1. Artificial Intelligence (AI) and Machine Learning (ML)
AI and ML algorithms are becoming increasingly integrated into flat surface polishing machines to improve precision and performance. These systems can analyze data from sensors and cameras to detect surface defects and optimize polishing parameters automatically.
- Real-Time Quality Control: AI-based systems can identify inconsistencies in surface finish or dimensional accuracy and adjust machine settings in real-time, reducing defects and increasing efficiency.
- Predictive Maintenance: By continuously analyzing machine data, AI can predict when parts need maintenance or replacement, thus minimizing unexpected downtime and maintenance costs.
2. Adaptive Polishing
Adaptive polishing systems use sensors to detect the surface conditions of the workpiece and adjust the polishing process accordingly. These systems can measure factors like surface roughness, material hardness, and polishing pressure to optimize performance.
- Surface Feedback: Using sensors to gather real-time surface data, adaptive polishing systems ensure that the surface is polished evenly and consistently across varying material types and geometries.
- Dynamic Adjustment: The system automatically adjusts the pressure and speed of polishing to accommodate for different workpieces in the same batch, ensuring uniform results.
3. Robotic Polishing Systems
Robotic arms are becoming an increasingly popular solution for polishing complex or irregularly shaped workpieces. These systems can work with a variety of materials, including delicate ceramics or fragile plastics, and can be programmed for custom polishing paths.
- Precision and Flexibility: Robotic polishing offers flexibility in handling complex shapes and contours, ensuring that even intricate parts can achieve a high-quality finish.
- Automation: The use of robots reduces human intervention, improving efficiency, reducing labor costs, and minimizing errors in the polishing process.
4. Laser Polishing
Laser polishing is an emerging technique that uses high-powered lasers to melt and smooth the surface of a material without the need for abrasives. This technology can provide a smooth, mirror-like finish on materials like metals, plastics, and ceramics.
- Advantages: Laser polishing is a non-contact process, meaning there’s no risk of mechanical wear on the polishing tool. It also allows for precise, localized treatment, reducing the need for extensive setup or adjustment.
- Surface Quality: Laser polishing can achieve superior surface finishes that traditional abrasive polishing methods cannot, such as ultra-smooth, reflective surfaces.
Conclusion
Flat surface polishing machines play a vital role in a wide range of industries by providing high-quality finishes and enhancing the aesthetic and functional properties of materials. Despite the challenges associated with polishing processes, advanced solutions and continuous innovation in the field ensure that these machines remain indispensable to modern manufacturing operations.
By understanding the potential challenges—such as surface defects, abrasive wear, heat generation, and material removal rates—manufacturers can choose the right equipment, optimize their processes, and incorporate advanced technologies to improve performance. As automation, AI, robotic systems, and laser polishing continue to evolve, flat surface polishing machines will only become more efficient, precise, and adaptable, helping industries meet the increasing demands for high-quality, uniform finishes across various materials.
Sheet Metal Finishing Machines
Sheet metal finishing machines are crucial in many manufacturing processes, particularly in industries like automotive, aerospace, electronics, and consumer goods. These machines are designed to improve the surface quality of sheet metal parts by removing imperfections, enhancing surface texture, and providing desired finishes. Sheet metal finishing is a vital step to prepare materials for subsequent stages such as coating, painting, or further assembly.
Types of Sheet Metal Finishing Machines
- Belt Grinding and Polishing Machines
Purpose: These machines use abrasive belts to grind and polish metal sheets. They are versatile, able to work on various metals such as stainless steel, aluminum, and copper.
How It Works: Abrasive belts rotate at high speeds and are pressed against the sheet metal. The grinding or polishing action removes burrs, scratches, and oxidation, resulting in a smoother, more uniform finish.
Applications: Suitable for deburring, finishing welded seams, and creating satin or mirror finishes on metals. - Brush Polishing Machines
Purpose: Brush polishing machines use abrasive brushes to finish metal surfaces, providing a smooth and uniform texture.
How It Works: The metal sheet is moved across rotating brushes, which are mounted with abrasive materials like nylon or wire bristles. The brushes are effective for removing burrs, oxidation, and dirt from the surface.
Applications: Often used for cleaning, deburring, and achieving a brushed finish on metal surfaces, especially on stainless steel and aluminum. - Vibratory Finishing Machines
Purpose: Vibratory finishing machines utilize vibration to smooth and polish metal surfaces in a controlled environment.
How It Works: Metal sheets or parts are placed in a vibratory bowl with abrasives or media. The machine vibrates the bowl, causing the abrasive media to rub against the surface of the metal, smoothing out imperfections and creating a polished finish.
Applications: Ideal for small to medium-sized parts, providing consistent finishes on various metals and alloys. It’s commonly used in applications where parts have intricate shapes or where mass finishing is required. - Centrifugal Barrel Finishing Machines
Purpose: Centrifugal barrel finishing machines are used for high-efficiency metal polishing, deburring, and burnishing.
How It Works: These machines use barrels that rotate at high speeds, generating centrifugal forces that cause the metal parts and abrasive media to collide, resulting in the desired finish.
Applications: These are best for polishing, deburring, and edge radiusing, particularly for small or medium-sized parts that need a uniform finish. - Disc Finishing Machines
Purpose: Disc finishing machines use abrasive discs that rotate against the metal part to grind, deburr, or polish the surface.
How It Works: The metal part is placed on a rotating disc, and abrasive materials are used to finish the surface through friction. The disc’s rotation generates enough force to remove imperfections, creating a smooth, polished surface.
Applications: Common in applications requiring precise surface finishing, such as creating brushed effects or polishing sheet metal for aesthetic purposes. - Laser Polishing Machines
Purpose: Laser polishing is a non-contact, advanced finishing technology that uses lasers to melt the surface of the metal, smoothing it and removing imperfections.
How It Works: A high-powered laser beam is directed at the metal sheet, locally melting the surface layer. As the molten material cools, it solidifies into a smooth, glossy finish.
Applications: Laser polishing is often used in high-precision industries, such as aerospace, where the metal’s surface must be free of defects and have an ultra-smooth finish. - Shot Blasting Machines
Purpose: Shot blasting is a process where metal parts are sprayed with a stream of abrasive media (usually steel shots) at high speed to clean and finish the metal surface.
How It Works: A blast wheel throws abrasive media at the sheet metal part. The impact of the media removes dirt, rust, scale, and other contaminants, while also improving the surface finish.
Applications: Shot blasting is commonly used in steel or cast iron parts to clean the surface and prepare it for painting or coating. It can also create a textured surface on metal components. - Polishing Tumblers
Purpose: Polishing tumblers use a rotating drum to polish metal parts with abrasive media inside.
How It Works: The parts and abrasive media are placed inside a rotating drum or barrel. As the drum turns, the friction between the parts and media smooths out imperfections and polishes the surfaces.
Applications: Used for deburring, polishing, and finishing small parts in bulk, such as fasteners, screws, or connectors.
Applications of Sheet Metal Finishing Machines
- Automotive Industry
- Sheet metal finishing machines are used in automotive manufacturing to improve the surface finish of body panels, chassis components, and other metal parts. Finishing processes like polishing and deburring ensure that the final products are free of defects and have an aesthetically pleasing appearance.
- Aerospace Industry
- The aerospace sector requires high-precision finishes for metal components to meet strict performance and safety standards. Sheet metal finishing machines are used to achieve smooth, uniform surfaces on parts like turbine blades, brackets, and panels.
- Consumer Electronics
- Many consumer electronic products, such as smartphones, laptops, and appliances, feature metal components that require a high-quality surface finish. Sheet metal finishing machines are used to polish and clean these parts to create sleek, attractive finishes.
- Medical Devices
- For medical devices made from metals or alloys, a clean, smooth finish is essential to ensure functionality and avoid contamination. Sheet metal finishing machines help in cleaning, deburring, and polishing parts like surgical instruments, medical implants, and diagnostic equipment.
- Architectural and Decorative Metals
- In industries dealing with decorative metal products such as kitchenware, handrails, or furniture, sheet metal finishing machines provide a polished or brushed finish that enhances the aesthetic appeal and longevity of the products.
- Industrial Equipment
- Sheet metal finishing machines are also used in the production of industrial equipment to deburr sharp edges, remove oxidation, and create smooth surfaces that improve the durability and function of machinery.
Benefits of Sheet Metal Finishing Machines
- Enhanced Surface Quality
These machines significantly improve the surface finish of sheet metal parts by removing imperfections like burrs, scratches, and oxidation. A smooth surface ensures better adhesion of paints or coatings, contributing to a more durable and attractive final product. - Time and Cost Efficiency
Automated sheet metal finishing machines increase throughput and consistency, reducing the need for manual labor and the time it takes to complete finishing tasks. This helps improve overall production efficiency and reduces labor costs. - Improved Durability
By removing defects and improving surface smoothness, sheet metal finishing machines can enhance the longevity and resistance of metal parts to corrosion, wear, and fatigue. - Precision and Consistency
Automated sheet metal finishing machines provide consistent results, which is critical in industries where precision is important. For example, CNC-controlled finishing machines ensure uniform surface treatment across all parts in a batch. - Customization Options
Many sheet metal finishing machines offer customization options, allowing operators to adjust the polishing process to achieve specific finishes (e.g., matte, glossy, satin) based on customer requirements or product specifications.
Factors to Consider When Choosing a Sheet Metal Finishing Machine
- Material Type
Consider the type of metal you are working with. Some metals, such as stainless steel, require different abrasives or techniques compared to aluminum or copper. Choose a machine that is suitable for your specific material. - Finish Requirements
Determine the desired surface finish (e.g., smooth, brushed, polished). Different finishing machines are designed to achieve specific finishes, so it’s important to choose a machine that meets your quality standards. - Production Volume
If you need to process large volumes of parts, an automated, high-throughput machine would be more suitable. Conversely, for smaller batches or prototypes, manual or semi-automated machines may be more cost-effective. - Machine Flexibility
Machines that can handle a variety of finishing operations (e.g., grinding, polishing, deburring) are ideal for companies that need versatility. This can help reduce the need for multiple machines and streamline production. - Maintenance Requirements
Consider the maintenance needs of the machine. Machines with easier-to-replace parts or those that offer automatic maintenance alerts may help reduce downtime and keep operations running smoothly. - Budget
The initial cost and ongoing operating costs (energy consumption, maintenance, abrasives, etc.) should be evaluated when selecting a machine. Machines with advanced features may have higher upfront costs but can lead to significant savings in efficiency and labor over time.
Conclusion
Sheet metal finishing machines are essential in a wide range of industries to achieve high-quality surface finishes on metal parts. Whether it’s grinding, polishing, or deburring, these machines improve the aesthetic appeal, durability, and functionality of metal components. By choosing the right machine for the job, manufacturers can enhance product quality, reduce labor costs, and increase production efficiency, ensuring that parts meet the necessary specifications and industry standards.
Advanced Technologies in Sheet Metal Finishing
As industries evolve, the demand for more precise, faster, and cost-efficient finishing solutions grows. New technologies are being integrated into sheet metal finishing machines to improve surface quality, speed, and overall efficiency. Below are some of the most notable advancements:
1. Automation and Robotics in Sheet Metal Finishing
Automation is one of the most significant trends in sheet metal finishing. Integrating robotics with finishing processes has opened new possibilities for consistency, precision, and speed.
- Robotic Polishing and Grinding: Robotic arms with advanced polishing or grinding tools can handle irregularly shaped parts with high precision. These robots can be programmed to perform intricate finishing operations, ensuring consistent results across large batches of parts.
- Automated Deburring: Automated deburring systems can efficiently remove sharp edges and burrs from metal parts. These systems use robotic arms, belts, or other tools to handle parts in a precise, repeatable manner.
- Collaborative Robots (Cobots): Cobots work alongside human operators, increasing efficiency and safety. They can be deployed to assist in polishing, deburring, or grinding processes, handling the more repetitive or heavy tasks, which increases overall throughput.
2. CNC-Based Sheet Metal Finishing Machines
CNC (Computer Numerical Control) technology has revolutionized many manufacturing processes, and sheet metal finishing is no exception. CNC finishing machines provide high precision, repeatability, and the ability to perform complex finishing tasks with minimal human intervention.
- Precise Control: CNC machines offer precise control over polishing, grinding, and deburring processes, ensuring that metal parts achieve the desired finish every time.
- Versatility: CNC sheet metal finishing machines can be programmed to perform various tasks like polishing, grinding, and edge rounding, making them highly adaptable to different production needs.
- Integration with CAD/CAM: CNC systems can be integrated with CAD/CAM (Computer-Aided Design/Manufacturing) software, allowing for seamless design-to-production transitions. Manufacturers can upload design files directly to the CNC system, which then controls the polishing and finishing operations automatically.
3. Digitalization and IoT Integration
The integration of the Internet of Things (IoT) and digital technologies is enabling real-time monitoring, predictive maintenance, and performance optimization of sheet metal finishing machines.
- Real-Time Monitoring: IoT sensors placed on the machines can provide real-time data on various parameters, such as temperature, pressure, vibration, and speed. This data is analyzed to ensure optimal performance and to detect any deviations from the standard process.
- Predictive Maintenance: With IoT-enabled machines, manufacturers can predict when maintenance is needed by analyzing machine performance data. This reduces unexpected breakdowns and minimizes downtime, ultimately increasing operational efficiency.
- Cloud Connectivity: IoT-enabled machines can be connected to the cloud, allowing remote monitoring and control. This feature is especially useful for companies with multiple manufacturing facilities, as they can monitor all their machines from a centralized location.
4. Advanced Abrasive Technologies
New types of abrasives and polishing materials have emerged to enhance the performance of sheet metal finishing machines. These abrasives are designed to improve the efficiency, lifespan, and quality of the finished surface.
- Superabrasives: Materials like diamond abrasives and CBN (Cubic Boron Nitride) abrasives are now used in sheet metal finishing. These superabrasives provide exceptional hardness and durability, making them ideal for finishing harder materials like titanium and hardened steel.
- Nanotechnology Abrasives: Nanotech abrasives are designed to provide finer and smoother finishes, especially on precision metal parts. They offer an ultra-fine surface finish, reducing the need for multiple finishing steps.
- Eco-Friendly Abrasives: As the push for sustainability grows, environmentally friendly abrasives made from recycled materials or non-toxic substances are becoming more popular. These abrasives perform just as well as traditional materials while reducing environmental impact.
5. Laser-Assisted Polishing
Laser-assisted polishing is an emerging technique that uses a laser beam to enhance the polishing process. By melting a thin layer of the metal surface, the laser smoothens it without the need for physical contact, providing a glossy, mirror-like finish.
- Contactless Process: One of the main benefits of laser-assisted polishing is that it’s a non-contact process, meaning there’s no wear on the polishing tool. This results in more consistent and precise finishes.
- High Precision: Laser polishing can achieve an ultra-smooth finish, making it ideal for high-precision industries like aerospace and medical device manufacturing.
- Material Versatility: Laser polishing can be applied to a wide range of materials, including metals, ceramics, and composites, making it suitable for a diverse set of applications.
6. Water-Based Polishing (Hydro-finishing)
Water-based polishing, or hydro-finishing, is a process that uses water or aqueous solutions combined with abrasives to finish sheet metal surfaces.
- Eco-Friendly Process: Unlike traditional abrasive polishing methods that may involve solvents, hydro-finishing uses water-based solutions, reducing the environmental impact of the process.
- Reduced Heat Generation: This method generates less heat compared to traditional polishing, which is beneficial for preventing heat distortion, especially in sensitive materials.
- Smooth and Uniform Finish: Hydro-finishing provides consistent, high-quality finishes, often used for creating mirror-like surfaces on materials like stainless steel.
Key Considerations When Investing in Sheet Metal Finishing Machines
When selecting a sheet metal finishing machine, several factors need to be considered to ensure that the equipment aligns with your manufacturing requirements and long-term business goals.
1. Production Volume and Throughput
Consider whether your production line needs a high-throughput, automated solution or if a slower, more manual approach will suffice. High-volume production often requires automated or robotic systems to maximize speed, while small batch or prototyping work may benefit from more flexible, manual machines.
2. Surface Finish Quality
Different industries have different requirements for surface finishes. For example, the aerospace industry may require mirror-like finishes, while the automotive industry may prefer matte or satin finishes. Select a machine that is capable of achieving the required surface finish consistently.
3. Material Compatibility
Different metals, alloys, and coatings may require different finishing approaches. Ensure that the machine is compatible with the materials you intend to process. Some machines may be specialized for stainless steel, while others may work better for softer metals like aluminum.
4. Cost and Budget
When selecting a sheet metal finishing machine, consider the initial investment as well as long-term costs. High-tech, fully automated systems with advanced features will have a higher upfront cost but may offer greater efficiency and savings in the long run. Assess the total cost of ownership, which includes maintenance, tooling, and energy consumption.
5. Maintenance and Support
Machines require regular maintenance to ensure that they continue performing optimally. Consider the availability of spare parts, technical support, and the ease of maintaining the machine. Machines that require less maintenance or offer predictive maintenance features can reduce downtime and operational costs.
6. Environmental Impact
As sustainability becomes a bigger concern, it is important to consider the environmental impact of the finishing process. Machines that use eco-friendly abrasives, reduce energy consumption, or incorporate water-based finishing methods are increasingly sought after.
Conclusion
Sheet metal finishing machines play a critical role in improving the quality, appearance, and durability of metal parts. With advancements in automation, robotics, and digital technologies, the capabilities of these machines have expanded, enabling manufacturers to meet the increasing demands for precision and efficiency in metal finishing. Whether you are working with high-volume production or small batches, there is a wide variety of finishing machines and techniques available, each tailored to specific materials, processes, and surface finish requirements. Investing in the right sheet metal finishing machine can significantly enhance the quality of your products while improving production efficiency and sustainability.
Additional Considerations and Future Trends in Sheet Metal Finishing
As industries continue to evolve, several additional trends and considerations are influencing the development and use of sheet metal finishing machines. These trends aim to address the growing demand for high precision, sustainability, and efficiency.
1. Industry 4.0 and Smart Manufacturing
Industry 4.0 is driving the digital transformation of manufacturing, and sheet metal finishing is no exception. The integration of smart manufacturing technologies into sheet metal finishing machines enables greater control, automation, and real-time monitoring.
- Smart Sensors: These sensors are increasingly embedded into finishing machines to collect and analyze data on temperature, pressure, and machine wear. This allows for continuous monitoring, providing operators with valuable insights into machine performance and enabling them to adjust settings on-the-fly for optimal results.
- Advanced Data Analytics: By using data analytics, manufacturers can predict maintenance needs, adjust parameters to improve surface finishes, and optimize production schedules. The insights gathered from these systems allow for continuous improvement in the finishing process.
- Cloud Connectivity and Remote Access: Cloud technology is enabling manufacturers to monitor and control sheet metal finishing machines remotely. This feature is especially beneficial for facilities operating multiple machines or plants in different locations, providing a centralized platform for overseeing operations.
- Predictive Analytics: The combination of machine learning and big data can forecast potential machine malfunctions or quality issues before they occur, minimizing downtime and improving the consistency of the finished product.
2. Green Manufacturing and Sustainability
Environmental sustainability is becoming a top priority across all industries, including metal finishing. The demand for eco-friendly solutions and practices is prompting the development of new finishing technologies that reduce the environmental footprint of the production process.
- Energy-Efficient Machines: Newer sheet metal finishing machines are designed to consume less energy while maintaining high performance. Innovations in machine design, such as improved motor efficiency, energy recovery systems, and more efficient use of abrasives, are helping manufacturers reduce energy consumption and lower operating costs.
- Eco-Friendly Abrasives and Polishing Media: As part of the trend towards greener manufacturing, many companies are transitioning to abrasives and polishing media that have a lower environmental impact. Recycled abrasives, biodegradable compounds, and non-toxic materials are being used in place of traditional abrasives that may release harmful chemicals into the environment.
- Water Conservation: Traditional finishing methods often use significant amounts of water. Innovations such as closed-loop water systems, which recycle water for repeated use, are becoming more common. These systems reduce water waste and lower operating costs while still providing high-quality finishes.
- Waste Minimization: Many manufacturers are adopting zero-waste policies or finding ways to recycle waste from the finishing process. For example, used abrasives or media can be collected, cleaned, and reused in future finishing processes, reducing overall waste and the need for new resources.
3. Customization and Flexible Production
The need for customized finishes and flexible production runs is on the rise as manufacturers respond to customer demands for personalized products. To accommodate these needs, sheet metal finishing machines are becoming more adaptable.
- Modular Design: Many modern finishing machines are designed to be modular, allowing manufacturers to easily swap out components or adjust the machine configuration based on the requirements of specific projects. This flexibility ensures that manufacturers can handle a wide variety of materials, part sizes, and finish requirements without investing in multiple specialized machines.
- Adaptive Processes: Advanced systems now enable the automatic adjustment of process parameters, such as polishing speed, pressure, and abrasive type, based on the part being processed. These adaptive processes allow for faster transitions between different part designs or production runs.
- On-Demand Manufacturing: The shift toward on-demand and batch production means that manufacturers are looking for more flexible solutions for part finishing. Whether it’s a low-volume, high-mix operation or producing custom parts, manufacturers are investing in finishing equipment that can quickly adapt to changing production schedules.
4. High Precision Finishing for Specialized Applications
Some industries require extremely high precision in the finishing of sheet metal components. Industries such as aerospace, medical devices, and electronics demand a level of surface finish that meets stringent quality and performance standards.
- Microfinishing Machines: For applications that require ultra-fine finishes or micrometer-level tolerances, microfinishing machines are becoming more prevalent. These machines use advanced abrasive technology to achieve finishes with extremely low surface roughness values, often measured in nanometers.
- Electrochemical Finishing (ECF): In certain applications, electrochemical finishing techniques are used to improve the surface quality of metals without using abrasives. This process involves the use of an electrolyte solution and an electric current to remove material from the surface, resulting in a smooth, uniform finish. ECF is ideal for highly precise or delicate parts that cannot tolerate mechanical abrasives.
- Advanced Polishing for Medical and Aerospace Industries: The aerospace and medical sectors require specialized polishing techniques to create mirror-like finishes on metal parts, such as turbine blades, implants, and surgical instruments. These industries rely on polishing technologies that are not only precise but also non-destructive to the parts, preserving their integrity and strength.
5. Automated Systems for End-to-End Solutions
To streamline production processes and reduce human error, many sheet metal finishing machines are incorporating automated features that handle multiple tasks in one system. These automated systems can integrate the finishing process into a fully automated manufacturing line, improving overall production efficiency and reducing labor costs.
- Automated Loading and Unloading: Machines that automatically load and unload metal parts can help minimize manual labor and ensure consistent handling. This automation can also contribute to faster production cycles, reducing the time between finishing operations.
- Integrated Finishing Cells: Some finishing machines are now designed to work as part of an integrated system or finishing cell. These systems combine multiple finishing steps (such as grinding, polishing, deburring, and brushing) into a single automated process, further increasing throughput and reducing the chance of errors in finishing steps.
- Collaborative Robots (Cobots): Cobots are increasingly being used to work alongside human operators in finishing processes. These robots handle tasks such as loading/unloading parts, cleaning the machines, or even performing specific finishing tasks with high precision. Their ability to interact safely with human workers helps improve production flexibility and efficiency.
6. 3D Printing and Additive Manufacturing Finishing
Additive manufacturing (3D printing) is becoming more common in industries that require highly customized and complex parts. As this technology grows, the need for post-processing and finishing of 3D-printed metal parts is increasing.
- Post-Processing for 3D Printed Metals: Sheet metal finishing machines are often adapted for post-processing 3D printed metal parts. These parts can have surface roughness or imperfections due to the layer-by-layer printing process. Finishing machines like abrasive belt grinders, shot blasters, or laser systems are employed to smooth the surface, remove support structures, and refine the part to meet final specifications.
- Hybrid Manufacturing Systems: Hybrid systems that combine additive and subtractive manufacturing processes are also becoming more popular. These systems allow manufacturers to print metal parts with complex geometries and then use traditional finishing techniques (like grinding or polishing) to refine the part further. The combination of 3D printing and finishing in a single system can reduce time and costs, especially for prototype or low-volume production.
Conclusion
The sheet metal finishing industry is experiencing a significant transformation, driven by advancements in technology, the need for greater efficiency, and a growing focus on sustainability. With the rise of automation, digital technologies, and eco-friendly practices, the future of sheet metal finishing promises to be more streamlined, precise, and environmentally responsible. Manufacturers are increasingly adopting solutions that not only meet the demand for high-quality finishes but also contribute to operational savings and reduced environmental impact.
As the industry moves forward, sheet metal finishing machines will continue to evolve, integrating even more sophisticated technologies to improve surface quality, reduce waste, and increase production flexibility. Understanding these trends and technological advancements can help manufacturers stay ahead of the competition and meet the demands of modern production.
EMS Metalworking Machinery: Your Trusted Partner in Precision Metalworking
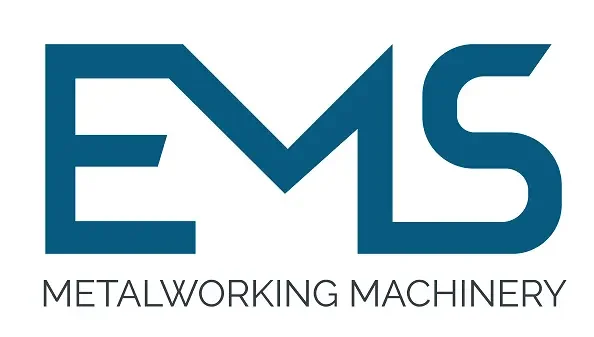
EMS Metalworking Machinery is a leading manufacturer of high-quality metalworking equipment, dedicated to providing innovative solutions that meet the evolving needs of industries worldwide. With a rich history of excellence and a commitment to technological advancement, we have earned a reputation for delivering cutting-edge machinery that ensures precision, efficiency, and durability.
Our Product Range:
- CNC Spinning Lathes: From precision bench lathes to heavy-duty industrial models, our lathes offer unmatched accuracy and performance for a wide range of applications, including machining shafts, gears, and other cylindrical components.
- Trimming Beading Machine: Our trimming beading machines are designed to provide exceptional cutting capabilities and versatility, enabling you to create complex shapes and intricate details with ease. Whether you need a horizontal or vertical trimming machine, we have the perfect solution for your needs.
- Hydraulic Deep Drawing Press Machines: Our hydraulic deep drawing press machines are built to deliver precise and powerful drawing operations, ensuring clean holes and exceptional surface finishes. We offer a comprehensive range to suit various applications.
- Grinding Machines: Our grinding machines are engineered for precision and efficiency, allowing you to achieve the highest levels of surface finish and dimensional accuracy. Whether you need a surface grinder, cylindrical grinder, or tool grinder, we have the equipment to meet your specific requirements.
- Sawing Machines: Our sawing machines are designed for fast and accurate cutting of metals, providing clean cuts and minimal burrs. From band saws to circular saws, we offer a variety of options to suit different materials and cutting needs.
- Custom Machinery: In addition to our standard product line, we also specialize in custom machinery fabrication. Our experienced engineers can work with you to design and build tailored solutions that meet your unique requirements and optimize your production processes.
Why Choose EMS Metalworking Machinery:
- Quality: Our machines are crafted with the highest quality materials and components, ensuring long-lasting performance and reliability.
- Precision: We are committed to delivering machinery that meets the most stringent tolerances and standards, ensuring exceptional accuracy in your metalworking operations.
- Innovation: We continuously invest in research and development to stay at the forefront of technological advancements, offering innovative solutions that enhance your productivity and efficiency.
- Customer Support: Our dedicated team of experts is always available to provide comprehensive support, from machine selection and installation to maintenance and troubleshooting.
- Customization: We understand that every business has unique needs, and we offer flexible customization options to tailor our machines to your specific requirements.
At EMS Metalworking Machinery, we are more than just a supplier of equipment; we are your trusted partner in metalworking success. By choosing EMS, you can be confident in the quality, reliability, and performance of your machinery, enabling you to achieve your business goals and stay ahead of the competition.
EMS Metalworking Machinery
We design, manufacture and assembly metalworking machinery such as:
- Hydraulic transfer press
- Glass mosaic press
- Hydraulic deep drawing press
- Casting press
- Hydraulic cold forming press
- Hydroforming press
- Composite press
- Silicone rubber moulding press
- Brake pad press
- Melamine press
- SMC & BMC Press
- Labrotaroy press
- Edge cutting trimming machine
- Edge curling machine
- Trimming beading machine
- Trimming joggling machine
- Cookware production line
- Pipe bending machine
- Profile bending machine
- Bandsaw for metal
- Cylindrical welding machine
- Horizontal pres and cookware
- Kitchenware, hotelware
- Bakeware and cuttlery production machinery
as a complete line as well as an individual machine such as:
- Edge cutting trimming beading machines
- Polishing and grinding machines for pot and pans
- Hydraulic drawing presses
- Circle blanking machines
- Riveting machine
- Hole punching machines
- Press feeding machine
You can check our machinery at work at: EMS Metalworking Machinery – YouTube
Applications:
- Beading and ribbing
- Flanging
- Trimming
- Curling
- Lock-seaming
- Ribbing
- Flange-punching