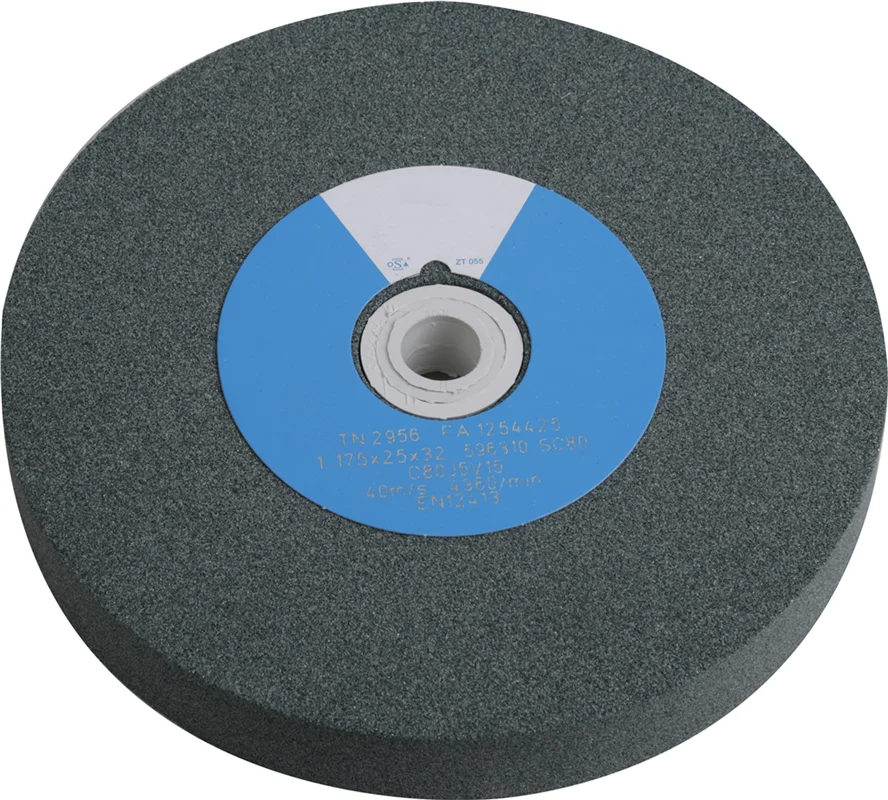
Centrifugal Disc Finisher: A metal polishing machine is a mechanical device used to improve the surface finish of metallic components by reducing surface roughness, removing oxidation, and enhancing appearance. These machines are critical in industries where surface quality is essential, such as automotive, aerospace, medical devices, cookware, jewelry, and manufacturing of precision tools. The polishing process can also increase corrosion resistance and prepare metal parts for further coating or painting.
Metal Polishing Machine Working Principle
The working principle of a metal polishing machine involves the abrasion of the metal surface using a rotating wheel or belt embedded with abrasive materials. As the workpiece comes into contact with the abrasive surface, microscopic layers of the material are removed. This process smooths out irregularities, scratches, or other imperfections. Depending on the intended finish, the process may include several stages of polishing with abrasives of progressively finer grits.
2. Types of Metal Polishing Machines
There are several types of machines used for polishing metal, each suited to specific applications:
- Manual Polishing Machines: These are operated by hand and provide high flexibility. They are ideal for intricate or custom work, such as jewelry and small components, but are labor-intensive.
- Semi-Automatic Polishing Machines: These machines combine manual loading with automated polishing cycles. They offer better consistency than fully manual systems and are commonly used in small-scale industrial setups.
- Fully Automatic CNC Polishing Machines: Controlled by computer numerical control (CNC) systems, these machines offer high-speed, precision polishing for mass production. They are capable of working on complex geometries and ensure uniform surface finish across all parts.
- Belt Polishing Machines: These use abrasive belts and are suitable for flat or curved surfaces. They can remove heavy oxidation, weld seams, or surface defects quickly.
- Buffing Machines: These use soft cloth wheels with fine abrasives or polishing compounds. Buffing is often the final step in the polishing process to achieve a mirror-like finish.
3. Applications
Metal polishing machines are used in a wide range of industries:
- Automotive Industry: To polish engine parts, bumpers, and trims for aesthetic appeal and corrosion resistance.
- Aerospace: For improving surface integrity and fatigue resistance of critical components.
- Medical Equipment: Surgical tools and implants require ultra-smooth finishes for hygiene and performance.
- Cookware and Utensils: For achieving a clean, reflective surface that is easy to maintain.
- Architectural Hardware: Door handles, railings, and decorative fittings are polished for enhanced visual appeal.
4. Advantages of Metal Polishing
- Enhanced Appearance: Polishing produces a shiny, aesthetically pleasing finish.
- Improved Corrosion Resistance: A smoother surface reduces the accumulation of moisture and corrosive agents.
- Ease of Cleaning: Polished surfaces are easier to maintain and clean.
- Improved Functionality: In moving parts, polishing can reduce friction and wear.
- Pre-Coating Preparation: A smooth base ensures better adhesion of paints or coatings.
5. Challenges and Considerations
While metal polishing provides numerous benefits, there are also challenges:
- Heat Generation: Excessive heat during polishing can warp the metal or degrade its properties.
- Material Loss: Polishing removes material, which may be unacceptable in precision components.
- Health Hazards: Dust and fumes from polishing operations can pose health risks if proper ventilation and protective equipment are not used.
- Surface Contamination: If abrasive compounds are not properly cleaned off, they can contaminate subsequent manufacturing steps.
6. Environmental and Safety Aspects
Modern metal polishing machines are increasingly designed with environmental considerations. Features like dust collectors, noise dampening, and enclosed systems help to reduce emissions and improve workplace safety. Additionally, many industries now prefer water-based or eco-friendly polishing compounds to reduce chemical waste.
7. Future Trends
With the rise of automation and Industry 4.0, metal polishing machines are becoming more intelligent and adaptive. Integration with robotic arms, AI-powered defect detection, and real-time process monitoring are becoming standard in high-end polishing setups. Moreover, additive manufacturing and 3D printing have created demand for polishing machines capable of handling unconventional shapes and materials.
Conclusion
Metal polishing machines play a vital role in modern manufacturing and product finishing. Whether it is for aesthetics, performance, or protective purposes, the right polishing technique and machinery can significantly enhance the quality and value of metal components. As technology evolves, so too will the capabilities and applications of these versatile machines, making them indispensable tools in numerous industries.
A metal polishing machine is a specialized piece of equipment used to refine and smooth the surface of metal components through mechanical abrasion. Its primary function is to enhance the aesthetic appearance of the metal, improve its resistance to corrosion, and in some cases, prepare it for further processes such as coating or painting. These machines work by removing small amounts of surface material using abrasive wheels, belts, or compounds, which can vary in coarseness depending on the desired finish. Polishing can result in a matte, satin, or mirror-like reflective finish, depending on the technique and materials used.
The process involves placing the metal workpiece in contact with a rotating polishing medium under controlled pressure and speed. As the abrasive interacts with the surface, imperfections such as scratches, oxidation, and minor dents are removed. The smoother the desired finish, the finer the abrasive required, and the more time and precision needed in the polishing process. In many industries, a multi-stage polishing process is adopted, starting with a coarse abrasive to shape or clean the surface and ending with a fine polish to achieve a high-gloss result.
Metal polishing machines come in various forms. Some are designed for manual operation, allowing the user to guide the workpiece by hand and apply polishing compounds manually. These are often used for intricate or delicate components such as jewelry, custom metalwork, or restoration projects. On the industrial side, semi-automatic and fully automatic machines are common. Semi-automatic machines require manual loading but execute the polishing cycle automatically, improving efficiency and consistency. Fully automatic machines, particularly those integrated with CNC systems, can handle complex shapes and volumes with minimal human input. These systems are ideal for mass production in industries such as automotive, aerospace, and medical manufacturing, where precision and uniformity are paramount.
Among the different types of polishing machines, belt polishers are widely used for flat or slightly curved surfaces, offering rapid material removal and a consistent finish. Buffing machines, on the other hand, use softer wheels and polishing compounds to impart a high-shine finish and are usually the final step in a polishing process. Some systems incorporate robotic arms to handle and manipulate parts with complex geometries, enabling uniform polishing on surfaces that are difficult to reach manually.
The applications of metal polishing machines span a wide range of industries. In the automotive sector, parts like wheels, trims, and engine components are polished to enhance their visual appeal and durability. In aerospace, critical components are polished to exacting standards to ensure optimal performance and safety. In the medical field, instruments and implants must be polished to a high degree of cleanliness and smoothness to meet stringent regulatory standards. Similarly, consumer products such as kitchenware, door handles, and decorative fixtures are polished to improve their appearance and feel.
While metal polishing offers many benefits, it also presents several challenges. The process can generate significant heat, which, if not controlled, may distort the workpiece or affect its mechanical properties. Material removal, though often minimal, may be unacceptable in precision applications. Furthermore, dust and fumes generated during polishing pose health and safety risks, making protective equipment and ventilation systems essential. Proper handling of polishing compounds and waste materials is also important to minimize environmental impact.
Modern polishing machines are evolving to address these challenges. Many are now equipped with advanced safety features, dust extraction systems, and noise reduction technologies. The integration of automation and smart control systems allows for real-time monitoring and adjustments, enhancing efficiency and consistency. In line with environmental concerns, manufacturers are increasingly adopting water-based or biodegradable polishing compounds that reduce harmful emissions.
As industries continue to push for higher quality, sustainability, and efficiency, metal polishing machines are becoming more sophisticated and versatile. The demand for machines capable of handling unconventional shapes, exotic materials, and custom finishes is rising, particularly with the growth of technologies like additive manufacturing and 3D printing. Consequently, the role of metal polishing machines in shaping, refining, and finishing metal products remains crucial, and their importance in the production chain is only expected to grow in the future.
8. Key Components of a Metal Polishing Machine
A typical metal polishing machine consists of several core components, each playing a critical role in the operation:
- Motor/Drive System: This is the heart of the machine, providing the rotational force required for polishing wheels or belts. Motors vary in power depending on the type of work—high-torque motors are often needed for heavy-duty or high-volume applications.
- Polishing Wheel or Belt: These are the abrasive components that come into contact with the metal surface. Polishing wheels can be made of cloth, felt, sisal, or other materials and are often used with polishing compounds. Abrasive belts, on the other hand, are commonly made from materials like aluminum oxide or silicon carbide.
- Workpiece Holder or Jig: In semi-automatic or fully automatic machines, the part to be polished is held in a fixture or jig to ensure stability and repeatability during the process. These can be customized to fit complex geometries.
- Control Panel/System Interface: Modern polishing machines come equipped with digital control panels or CNC interfaces. These allow operators to precisely control variables such as speed, pressure, polishing time, and compound application.
- Dust and Fume Extraction System: Since polishing can create fine particulate matter, many machines are equipped with dust extraction or vacuum systems to maintain a clean and safe environment.
- Coolant or Lubrication System (optional): In some applications, a cooling fluid or polishing slurry is used to prevent overheating, reduce friction, and improve surface finish.
9. Polishing Compounds and Abrasives
The success of a polishing process greatly depends on the type and quality of abrasive materials or polishing compounds used. These are generally categorized as:
- Cutting Compounds: Contain coarse abrasives for initial material removal. Common examples include emery and tripoli compounds.
- Polishing Compounds: These are finer and used to bring out a shine. Rouge compounds (such as red or white rouge) are popular for achieving mirror finishes.
- Dry vs. Wet Compounds: Some compounds are applied as dry powders or bars, while others are in liquid or paste form. Wet polishing often results in better control over heat and finish.
- Custom Slurries: In precision or high-tech industries, slurries with specific chemical and abrasive properties are used to meet strict surface quality requirements.
10. Process Control and Quality Assurance
To ensure consistent and high-quality polishing, modern machines employ various process control strategies:
- Variable Speed Control: Adjusting the speed of the polishing wheel or belt allows the machine to adapt to different materials and finish requirements.
- Pressure Monitoring: Sensors can measure the pressure applied to the workpiece, ensuring that it remains within safe and effective limits.
- Cycle Time Programming: In automated systems, polishing time is precisely controlled for repeatability across multiple parts.
- Surface Finish Inspection: Quality control may involve using tools like surface profilometers, gloss meters, or visual inspection stations to verify that the target finish is achieved.
- Feedback Systems: Advanced machines can include feedback loops with machine vision or force sensors to automatically adjust the process in real time.
11. Maintenance and Longevity
Proper maintenance is essential to keep a metal polishing machine operating efficiently and safely. Key maintenance practices include:
- Regular Cleaning: Dust and residue from abrasives can clog components and reduce efficiency. Routine cleaning is necessary, especially in machines with built-in extraction systems.
- Inspection of Wear Parts: Polishing wheels, belts, and motor brushes should be inspected regularly for wear and replaced as needed to maintain optimal performance.
- Lubrication of Moving Parts: Bearings, drive shafts, and other mechanical parts should be lubricated according to the manufacturer’s guidelines to avoid mechanical failure.
- Calibration: Machines with electronic sensors and control systems should be calibrated periodically to maintain accuracy.
- Software Updates: CNC and smart polishing machines may require firmware or software updates to incorporate new features or bug fixes.
12. Safety Considerations
Operating a metal polishing machine involves several safety risks. Employers and users must take the following precautions:
- Personal Protective Equipment (PPE): Operators should wear safety goggles, dust masks or respirators, gloves, and hearing protection.
- Training and Supervision: Only trained personnel should operate polishing equipment, especially automated or high-power systems.
- Emergency Stop Systems: Machines should have easily accessible emergency stop buttons to quickly shut down operations in case of malfunction.
- Guarding and Shields: All rotating parts should be adequately shielded to prevent accidental contact.
- Ventilation: Proper airflow is necessary to handle fumes and fine dust, particularly when polishing toxic metals or using chemical-based compounds.
13. Customization and Integration
Many manufacturers offer customized polishing solutions tailored to the needs of specific industries. These custom systems may feature:
- Multiple Polishing Heads: For simultaneous multi-surface treatment.
- Robotic Integration: For parts that require complex handling or rotation during polishing.
- Inline Conveyor Systems: For integration into continuous production lines.
- Automatic Compound Dispensers: To ensure even and consistent application of polishing materials.
Such customization allows for scalability and efficient integration into broader manufacturing or finishing workflows.
Rotary Table Polishing Machine: Detailed Overview
A Rotary Table Polishing Machine is a specialized type of surface finishing equipment designed for high-efficiency, consistent, and repeatable polishing of metal components. It is widely used in mass production environments where uniform surface quality, precise control, and high throughput are critical. The defining feature of this machine is its rotary table, which continuously indexes or rotates to bring workpieces into contact with polishing tools, making it suitable for both flat and contoured parts.
1. Working Principle
The Rotary Table Polishing Machine operates on the principle of mechanical abrasion combined with controlled automation. The machine features a circular rotary table that holds multiple workpieces, either on individual fixtures or mounted directly. As the table rotates—either continuously or in indexed steps—each workpiece is brought sequentially into contact with polishing stations arranged around the perimeter.
Each polishing station may consist of:
- Abrasive wheels
- Buffing mops
- Belts
- Brushes
- Compound applicators
The table can be configured to stop at each station for a fixed time (indexing mode) or rotate continuously at a slow speed for uninterrupted processing. The speed, pressure, and duration of contact are controlled through a central control system, often integrated with PLC or CNC automation.
2. Key Features and Components
A Rotary Table Polishing Machine is comprised of the following essential components:
- Rotary Indexing Table: A heavy-duty, precisely machined turntable that holds multiple fixtures or clamps for securing workpieces.
- Polishing Heads: These may include belt grinders, buffing wheels, or flap wheels. Each head is typically adjustable in multiple axes to suit complex geometries.
- Compound Dispensers: Automated systems for applying polishing or abrasive compounds consistently during operation.
- Pneumatic or Hydraulic Pressing Mechanisms: These apply consistent pressure between the polishing head and the workpiece, ensuring uniform results.
- Control System: Most modern systems include a programmable logic controller (PLC) or a CNC interface, allowing for exact parameter control, recipe saving, and error detection.
- Safety Guards and Dust Extraction: Enclosures and exhaust systems maintain operator safety and minimize environmental impact.
3. Applications
Rotary Table Polishing Machines are widely used across industries for polishing metal parts of various shapes and sizes. Common applications include:
- Automotive Parts: Brake levers, handles, alloy wheel components, and decorative trims.
- Hardware: Door handles, locks, knobs, and hinges.
- Cookware and Cutlery: Spoons, ladles, pots, and pans.
- Medical Instruments: Surgical tools, orthopedic implants, and dental instruments.
- Sanitary Fittings: Faucets, valves, and pipe fittings.
The machine is ideal for applications that demand uniform surface quality across high volumes of parts.
4. Advantages
Rotary Table Polishing Machines offer several key benefits:
- High Productivity: Multiple workpieces can be processed simultaneously, reducing cycle time.
- Consistent Quality: Automation ensures uniform polishing across all parts, minimizing human error.
- Versatility: Machines can be configured for different part sizes, shapes, and materials with interchangeable tooling and fixtures.
- Compact Design: Despite their capabilities, rotary systems are often more space-efficient than linear production lines.
- Reduced Labor: Once loaded, the machine performs tasks autonomously, reducing the need for skilled manual polishing.
5. Machine Variants and Customization
Depending on the application, rotary table polishing machines may be designed in different formats:
- Single-head vs. Multi-head Configuration: For sequential polishing steps like roughing, intermediate, and final buffing.
- Horizontal vs. Vertical Axis Table: Depending on the orientation and gravity requirements of the workpiece.
- Manual Loading vs. Robotic Integration: For either basic setups or high-throughput automated cells.
- Wet or Dry Polishing: Machines may include coolant systems to manage heat and dust.
Customization is common, with tailor-made jigs, tooling, and polishing programs developed to match the client’s part geometry and finish requirements.
6. Maintenance and Operational Considerations
Like any industrial machinery, rotary table polishers require regular maintenance to ensure long-term efficiency and product quality:
- Routine inspection of belts, wheels, and motors
- Lubrication of rotary and head drive components
- Calibration of pressure sensors and speed controls
- Cleaning and replacement of filters in the dust extraction system
Operators must also be trained to monitor noise, vibration, or any deviations in finish quality that could signal equipment wear or malfunction.
7. Safety and Compliance
Given the presence of rotating parts, abrasive materials, and dust generation, safety is critical:
- Fully enclosed stations protect operators from direct exposure.
- Emergency stop mechanisms and interlock switches prevent unintended access during operation.
- Integrated fire suppression systems may be required when polishing combustible metals like aluminum or titanium.
- Compliance with standards such as CE, ISO, or OSHA may be necessary depending on regional regulations.
8. Innovations and Industry 4.0 Integration
Advanced rotary polishing systems are now integrating Industry 4.0 technologies, such as:
- Real-time performance monitoring
- Predictive maintenance via sensors
- Automated defect detection using cameras
- Remote diagnostics and software updates
- Energy-efficient motors and drives
These innovations not only increase efficiency but also help reduce downtime and production costs.
Conclusion
The Rotary Table Polishing Machine is a high-performance solution for companies that require efficient, repeatable, and high-quality surface finishing. With its combination of automation, precision control, and adaptability, it plays a vital role in modern manufacturing processes. From high-end automotive parts to everyday consumer goods, these machines help deliver the polished surfaces that define quality and professionalism in metal products.
A rotary table polishing machine is an advanced type of surface finishing equipment used predominantly in industrial settings for polishing metal components with high precision and consistency. Unlike conventional polishing systems, which typically handle one part at a time, the rotary table configuration allows multiple parts to be processed in a continuous or indexed circular motion, improving throughput and ensuring uniform results across all workpieces. The central component of the machine is its rotating table, which holds jigs or fixtures that securely position the metal parts. As the table turns, either in continuous rotation or indexed steps, each part is sequentially presented to various polishing stations mounted around the machine’s perimeter.
Each polishing station may be outfitted with different types of abrasive or buffing heads, including belts, flap wheels, mops, or brushes, depending on the surface finish requirements. Some machines are designed with just one head for simple applications, while more advanced models can feature multiple heads for multi-step processes such as pre-polishing, intermediate finishing, and final buffing. These polishing heads can often be adjusted in several axes to accommodate varying part geometries, from flat surfaces to complex contours. Automation in rotary table machines plays a critical role. Most are equipped with PLC or CNC systems that control table rotation speed, polishing head pressure, contact time, and the application of polishing compounds. This precision ensures high repeatability and minimal variation between parts, which is essential in industries like automotive, sanitary hardware, kitchenware, and medical instruments, where surface finish quality directly affects both function and aesthetics.
The design of rotary table polishing machines makes them particularly suitable for mass production. Multiple parts can be loaded onto the table and processed in one continuous cycle, dramatically reducing idle time and increasing productivity. Some systems incorporate robotic loading and unloading arms to further enhance automation, reducing labor costs and the potential for human error. Additionally, machines can be tailored for wet or dry polishing depending on the materials being processed and environmental safety standards. Safety and environmental considerations are integral to the design. The enclosed structure of many rotary systems not only protects operators from direct exposure to moving parts and flying debris but also facilitates effective dust and fume extraction. Many machines are also designed to handle combustible dust safely, especially when processing materials like aluminum or magnesium, which pose explosion risks if not properly managed.
The choice of abrasives and compounds is another critical aspect of performance. Coarse abrasives are used for initial surface leveling and defect removal, while finer compounds are employed in later stages to achieve high-gloss or mirror finishes. In some high-precision applications, such as polishing medical implants or optical components, special polishing slurries or chemical-mechanical processes may be used. Maintenance of rotary table polishing machines involves regular inspection of polishing heads, replacement of worn abrasives, lubrication of moving parts, and cleaning of dust filters and extraction ducts. Advanced models may include sensor-based monitoring systems that provide real-time feedback on wear and performance, enabling predictive maintenance and minimizing unplanned downtime.
Modern rotary polishing machines are increasingly equipped with smart features that support Industry 4.0 integration. These include data logging, remote diagnostics, and process optimization based on historical performance. They can also interface with factory-level MES (Manufacturing Execution Systems) or ERP (Enterprise Resource Planning) software, allowing seamless integration into broader production workflows. The flexibility, precision, and efficiency of rotary table polishing machines make them a vital asset in any manufacturing process where surface quality is paramount. Their ability to deliver consistent, repeatable results while minimizing operator involvement and maximizing output makes them one of the most preferred systems for large-scale and high-value production environments.
Beyond the mechanical and operational advantages, rotary table polishing machines contribute significantly to improving overall product quality and brand perception. A polished, uniform finish not only enhances the visual appeal of a component but can also increase its functional value by reducing friction, preventing corrosion, and improving cleanliness, especially in industries with stringent hygiene standards such as medical, food processing, and pharmaceuticals. The machine’s precision ensures that every part, whether it’s a surgical instrument or a decorative hardware fitting, meets the exact same specifications, supporting rigorous quality control systems like ISO 9001 and similar standards.
One of the key factors contributing to the widespread adoption of rotary table polishing machines is their adaptability. With interchangeable tooling and programmable settings, the same machine can be configured to process a wide variety of materials including stainless steel, brass, aluminum, titanium, and even non-metallic items like plastic or composite parts in specialized applications. This versatility is particularly valuable in industries with diverse product lines or in job-shop environments where flexibility is essential. Machine builders often offer customized solutions that include specific jigs and fixtures tailored to unique part geometries, ensuring maximum surface contact during the polishing process for optimal results.
Another major area where rotary table polishing machines shine is in labor efficiency. Traditional manual polishing is highly labor-intensive, requiring skilled technicians to maintain consistent pressure and angle, which is not only time-consuming but also physically demanding. Over time, this can lead to fatigue-related quality fluctuations and potential repetitive strain injuries. In contrast, a rotary table machine automates these repetitive motions, reducing the need for direct manual intervention and freeing up skilled labor for more value-added tasks like inspection, programming, or maintenance. This not only boosts overall productivity but also makes the polishing process more ergonomic and sustainable for manufacturers.
The environmental aspect of polishing operations has also come under increased scrutiny, especially with rising global emphasis on green manufacturing. Rotary table polishing machines help address these concerns by enabling more efficient use of materials and compounds, reducing wastage through controlled dispensing systems, and offering better containment of dust and emissions. With integrated filtration systems, manufacturers can ensure compliance with environmental regulations while maintaining a cleaner, safer working environment. Moreover, some modern machines are being designed with energy-efficient motors and components that contribute to lower overall power consumption and operational costs.
From a financial standpoint, while the initial investment in a rotary table polishing machine can be significant, the long-term return on investment (ROI) is often highly favorable. This is due to the combination of reduced labor costs, higher throughput, improved product quality, and fewer reworks or rejects. In highly competitive markets where visual appeal and durability can make or break a product, the ability to deliver flawless finishes reliably and at scale becomes a powerful differentiator. For OEMs and subcontractors alike, such machines can open doors to new contracts, premium product segments, and stricter industry sectors that demand consistent surface performance.
Looking forward, innovations continue to push the capabilities of rotary polishing systems. Developers are exploring the use of AI-based process optimization, where machine learning algorithms analyze polishing results and adjust machine parameters in real time for continuous improvement. Robotic integration is also evolving, allowing robots not just to load and unload parts but also to perform intelligent in-process repositioning of workpieces for optimal surface coverage. Some advanced models even feature automated vision systems to inspect polished parts before unloading, eliminating defective items from the line without operator involvement.
In summary, the rotary table polishing machine stands as a cornerstone of modern surface finishing technology. It blends mechanical precision, automation, and versatility in a compact, efficient system capable of handling high-volume production with minimal variation. As industries continue to demand higher standards of appearance, performance, and cleanliness, rotary table polishers will remain indispensable tools, continually evolving to meet the needs of advanced manufacturing environments.
Belt Polishing Machine
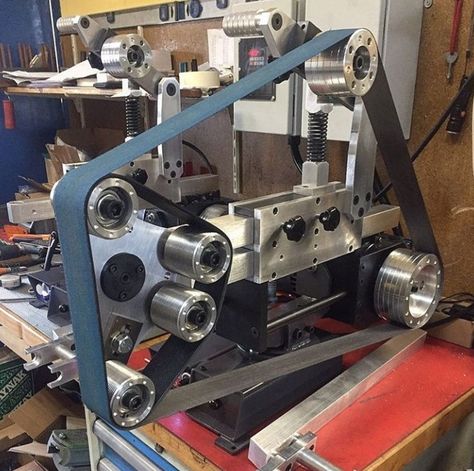
A Belt Polishing Machine is a widely used surface finishing system designed to polish, grind, or finish metal and non-metal components using an abrasive belt. Unlike rotary or wheel-based polishers, belt polishing machines use a continuous abrasive loop (belt) that moves over rollers or a platen, allowing for high-speed, linear polishing. These machines are valued for their versatility, efficiency, and ability to produce uniform surface finishes across flat, curved, and complex surfaces. They are especially useful in both manual and automated industrial applications where speed and precision are required.
The basic structure of a belt polishing machine consists of a motor-driven belt assembly mounted on a rigid frame. The belt is tensioned between two rollers—one driven by a motor and the other acting as an idler. In many cases, additional contact wheels or platens are incorporated beneath the belt to provide consistent backing and pressure during polishing. Depending on the application, the belt can be positioned horizontally, vertically, or at an angle. Belt speeds and pressure can be adjusted to suit different materials and polishing requirements. In more advanced systems, variable frequency drives (VFDs) allow fine-tuning of speed for better control over the finish quality.
One of the defining features of belt polishing machines is the choice of abrasive belts. These belts come in a wide range of grit sizes and materials, including aluminum oxide, zirconia alumina, silicon carbide, and ceramic abrasives. Coarse belts are used for heavy stock removal or descaling, while fine belts are used for surface refinement and pre-polishing. For ultra-fine finishing or mirror effects, polishing compounds can be applied alongside non-woven or cloth-backed belts. The ability to swap belts quickly and easily makes the machine adaptable for multi-stage processes without requiring different tools.
Belt polishing machines come in many formats. Bench-top models are used for smaller parts and manual operations, while standalone floor models offer higher power and throughput. Backstand belt grinders are a popular variant in workshops for deburring, shaping, and polishing parts of various sizes. Wide belt polishers, used in sheet metal processing, can handle large flat panels with excellent uniformity. In automated production lines, belt polishing heads may be mounted on robotic arms or integrated into conveyor systems to handle repetitive, high-volume polishing tasks.
In terms of application, belt polishing machines are found across numerous industries. In metal fabrication, they’re used to remove mill scale, weld seams, and scratches from steel, stainless steel, and aluminum parts. In the automotive sector, they polish body components, bumpers, and engine parts. The aerospace industry uses them to prepare surfaces for coatings and ensure fatigue resistance. Cutlery, cookware, hand tools, and decorative hardware are also polished using belt systems for that final aesthetic finish. Even wood, plastic, and composite parts can be polished using belt systems with the right belt type and speed control.
The machines are appreciated for their uniform surface coverage, which reduces the risk of over-polishing or inconsistent finish—a common challenge in manual buffing. The linear motion of the belt makes it ideal for removing lines and creating directional grain finishes like satin or brushed textures. Additionally, the belt’s continuous motion helps dissipate heat more effectively than a wheel, reducing the risk of overheating or warping the workpiece.
Maintenance is relatively straightforward but important to preserve machine performance. Belts should be checked regularly for wear or clogging and replaced as needed. Rollers, bearings, and tension systems need to be cleaned and lubricated periodically. Dust collection is essential, as the belt action generates fine metal particles; most industrial models come with built-in or attachable dust extraction systems to keep the workspace safe and clean. Proper guarding and safety features—like emergency stops and overload protection—are standard and must be maintained to meet safety regulations.
Modern belt polishing machines may include automation features, such as digital control panels, touchscreens, programmable settings, and even integration with robotic or CNC systems. These improvements help reduce setup times, improve repeatability, and ensure high-quality finishes in complex production environments. For companies looking to modernize, there are options to retrofit older belt polishers with digital drives or sensors for process control and feedback.
In summary, the belt polishing machine remains one of the most versatile and indispensable tools in surface finishing. Its ability to combine high material removal rates with precision and surface refinement makes it ideal for a wide range of industries. Whether used manually by a skilled operator or integrated into an automated line, this machine delivers fast, reliable, and consistent finishes, making it a key asset in modern manufacturing and fabrication operations.
A belt polishing machine is a highly efficient and adaptable surface finishing tool designed to polish, smooth, or grind a wide variety of materials, most commonly metals. The core of the system is a continuously looping abrasive belt that moves at high speed over a series of rollers, allowing for linear contact with the workpiece. This setup enables the machine to deliver uniform surface finishes across both flat and contoured surfaces, making it especially useful in industries that demand precision, speed, and repeatability. The belt’s abrasive action can be used for both aggressive material removal and delicate surface refinement, depending on the grit of the belt and the pressure applied.
These machines come in a range of configurations, from compact bench-mounted units to large industrial systems integrated into production lines. At the heart of every machine is a motorized drive roller that propels the abrasive belt, an idler roller for tensioning, and often a contact wheel or platen behind the belt to provide support during polishing. The belts themselves are available in various grit sizes and abrasive materials such as aluminum oxide, silicon carbide, zirconia, and ceramic, each chosen based on the specific material and finish requirements of the part being processed. This variety gives operators significant control over the finishing outcome, whether it’s for heavy deburring, satin finishing, or mirror polishing.
Belt polishing machines are extremely versatile and can be adapted to different working positions—horizontal, vertical, or angled—to suit a range of part shapes and sizes. In many systems, adjustable arms or tilting heads provide access to hard-to-reach surfaces and edges. For manual applications, operators hold the workpiece against the moving belt, while in automated systems, the workpiece may be guided beneath the belt by conveyors, robots, or pneumatic actuators. The simplicity and reliability of the belt mechanism, combined with the ease of changing belts for different tasks, make these machines a staple in both custom workshops and high-volume industrial facilities.
Their applications are extensive and span multiple industries. In metal fabrication, they are used for deburring, descaling, and surface preparation of steel and aluminum parts. In the automotive sector, belt polishers are employed for finishing components like bumpers, exhaust parts, and trim. The kitchenware industry relies on them to polish stainless steel pots, pans, and utensils. In aerospace and defense manufacturing, the machines prepare surfaces to meet exacting specifications for coatings and fatigue resistance. Even wood, composites, and plastic parts can be processed with specialized belts designed for non-metallic materials, further highlighting the machine’s adaptability.
One of the most notable advantages of the belt polishing machine is its ability to produce consistent, directional finishes such as satin or brushed textures. The linear motion of the belt naturally imparts a uniform grain pattern, which is difficult to achieve using rotating wheels. Additionally, the belt’s continuous movement helps to dissipate heat, reducing the risk of thermal damage or distortion to sensitive workpieces. This thermal efficiency, combined with adjustable speed controls, allows the machine to work effectively across a range of materials and thicknesses without sacrificing surface integrity.
From a safety and maintenance perspective, belt polishing machines are generally easy to manage. Most models come with integrated guards, spark containment features, and dust extraction ports to control airborne particles. Routine maintenance includes checking the condition of the belts, inspecting bearings and rollers, and ensuring proper belt tracking and tension. In high-volume production environments, machines may be equipped with monitoring systems that track belt wear and alert operators when a change is needed, minimizing downtime and preventing damage to parts or equipment.
Technological advancements have enhanced the performance and functionality of belt polishing machines. Today, many industrial units feature programmable logic controllers (PLC), digital touch interfaces, and even integration with robotic systems for automatic loading, positioning, and unloading. These smart machines can store multiple polishing recipes, adapt in real time to different part geometries, and maintain consistent quality with minimal operator intervention. Additionally, energy-efficient motors and regenerative braking systems help reduce the environmental footprint and operational costs of these machines.
The economic benefits of belt polishing machines are significant. Their ability to perform fast, consistent finishing reduces manual labor, increases throughput, and minimizes material waste. They help manufacturers meet tight tolerances and aesthetic standards with minimal rework, which is essential in competitive markets. Whether used in batch production or as part of a continuous finishing line, belt polishing machines offer the kind of performance, flexibility, and reliability that modern manufacturers demand.
The belt polishing machine also stands out in terms of its adaptability to various polishing and finishing needs. While some systems are designed for specific tasks like heavy deburring or coarse grinding, others are equipped to handle fine polishing or even mirror finishes, depending on the type of abrasive belt used. For example, a coarse grit belt might be employed for removing heavy oxidation or rust from metal surfaces, while a fine grit belt can be used for achieving a smooth, even surface ideal for decorative purposes. In industries where aesthetic quality is paramount, such as in the production of kitchenware, bathroom fittings, or automotive parts, belt polishing machines can create uniform, high-gloss finishes that enhance the appearance and durability of the product.
The efficiency of the belt mechanism makes it an attractive choice for mass production as well as for custom or low-volume jobs. In high-volume manufacturing, the ability to continuously feed parts into the system or use automated conveyors for part handling means that manufacturers can significantly reduce cycle times. This increased throughput is crucial in industries where tight production schedules and high output are essential for meeting market demands. Automated belt polishing systems, integrated into conveyor lines or robotic cells, can polish large numbers of parts with consistent quality, which is especially important for products that require a flawless finish across thousands of identical units.
In job shops or environments where parts vary greatly in size or complexity, a belt polishing machine offers exceptional flexibility. With the ability to change belts easily and adjust operational parameters such as speed, pressure, and angle, manufacturers can quickly switch between different tasks. For instance, one machine might be used to polish decorative trim one day, then switch to deburring complex aerospace components the next. This flexibility helps reduce the need for multiple machines, ultimately saving on equipment costs, floor space, and training time for operators.
Furthermore, belt polishing machines are highly customizable to meet specific production needs. Manufacturers can opt for specialized accessories like vacuum systems to enhance dust extraction, coolant delivery systems for wet polishing, and specially designed contact wheels for unique finishes. For example, a contact wheel with a soft rubber coating may be used in delicate applications to prevent damage to the workpiece, while harder contact wheels might be used for high-pressure grinding or finishing tasks. This level of customization makes the belt polishing machine a valuable tool across industries like aerospace, medical device manufacturing, electronics, and automotive where precision, surface quality, and material integrity are key.
In terms of material versatility, belt polishing machines are highly effective on a wide range of materials. While they are most commonly used for metals such as steel, stainless steel, aluminum, and brass, they are also effective on plastics, composites, and wood when paired with the appropriate abrasives. For example, in the wood industry, belt polishing is used to smooth surfaces and create an attractive finish for furniture, cabinetry, and flooring materials. Similarly, plastic and composite parts can be polished to remove marks, smooth edges, and enhance visual appeal without compromising the material’s integrity.
Despite all the advantages, operators must be aware of some challenges associated with belt polishing machines. Over time, abrasive belts wear out, and their performance can degrade if not regularly replaced or maintained. Belt tracking and tensioning also need to be carefully managed to prevent issues such as misalignment or premature wear. A poorly tensioned belt can cause uneven polishing, while a misaligned belt can damage both the machine and the workpieces. Regular maintenance of the tensioning system, the rollers, and the drive mechanisms ensures the machine operates smoothly and efficiently over time.
In addition to maintenance, it’s essential to consider operator safety when working with belt polishing machines. While most machines come with built-in safety features like emergency stop buttons and protective guards, the high-speed operation and the dust generated by abrasive belts require caution. Proper training for operators is essential to ensure they understand how to use the machine safely, as well as how to perform routine maintenance and change belts. Furthermore, implementing dust collection systems is critical not only to maintain a clean work environment but also to comply with health and safety regulations, especially when polishing metals that generate harmful dust.
Finally, sustainability has become an important consideration for modern manufacturing equipment. Belt polishing machines are no exception, as manufacturers are increasingly looking for ways to reduce energy consumption and waste. Many newer models feature energy-efficient motors and advanced dust extraction systems that minimize power usage and reduce the environmental impact of operations. Additionally, the ability to reuse or recycle certain types of abrasives, combined with innovations in cleaner compound dispensing, is helping to make the polishing process more eco-friendly.
In conclusion, the belt polishing machine is a versatile, reliable, and highly efficient tool for achieving superior surface finishes across a wide variety of materials. Whether in high-volume manufacturing, specialized custom work, or automated production lines, its flexibility and adaptability make it an essential part of many industries. The ability to achieve fine finishes consistently, coupled with the ease of maintenance and integration with other automated systems, ensures that the belt polishing machine will continue to be a key asset in modern manufacturing environments. As technologies evolve, further improvements in automation, energy efficiency, and sustainability will likely expand the capabilities and application of these machines, making them even more indispensable in the future of surface finishing.
Disc Polishing Machine
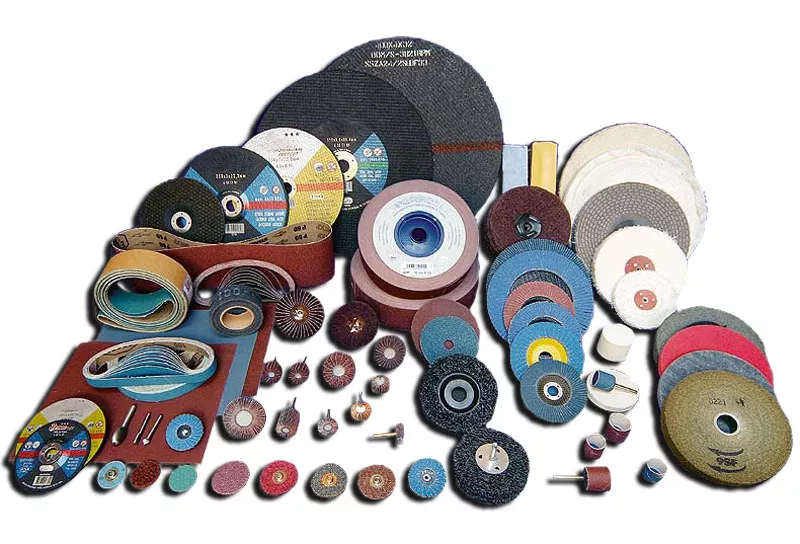
A Disc Polishing Machine is a versatile surface finishing tool used to polish, smooth, and refine the surfaces of various materials, typically metals, but also plastics, ceramics, and composites. It operates through the use of a rotary disc mounted on a motorized spindle, which rotates at high speeds while the workpiece is pressed against it or moved across its surface. The machine’s primary function is to achieve high-quality finishes, such as mirror-like surfaces or fine, satin textures, with minimal effort compared to manual polishing.
The core component of a disc polishing machine is the rotating disc, which can be made from various materials, depending on the application. For example, cloth-backed discs are commonly used for final polishing stages, while non-woven abrasive discs might be used for finer smoothing, or resin-bonded abrasive discs for more aggressive grinding tasks. The disc can be treated with specialized polishing compounds to achieve the desired finish. As the disc spins, the abrasive action removes material from the workpiece, smoothing out imperfections and scratches to create a refined surface.
A disc polishing machine generally consists of a few key parts: the rotating disc or wheel, the motor or drive mechanism that powers the disc, and the support structure or frame. The workpiece is either manually placed against the rotating disc or automated systems are used to feed and position parts precisely in industrial settings. Pressure and speed settings can be adjusted based on the material being worked on and the type of finish desired. Higher speeds are generally used for rough polishing and material removal, while lower speeds are ideal for final finishing and achieving a high-gloss surface.
These machines are often equipped with dust collection systems to handle the debris produced during the polishing process. The polishing action creates a significant amount of dust, particularly when working with metals like aluminum or steel. Effective dust extraction systems are essential for maintaining a clean working environment, reducing the risk of respiratory issues, and complying with health and safety standards.
Disc polishing machines come in different configurations, such as bench-mounted models for smaller parts and tasks, and floor-standing models designed for larger, heavier components. In industrial applications, dual-disc or multi-disc machines are used to achieve higher throughput, as they can polish multiple parts simultaneously, improving efficiency and reducing cycle times. Some models also feature adjustable heads or tilting mechanisms, which allow operators to adjust the angle at which the workpiece meets the polishing disc, providing greater flexibility for different part shapes.
The most common applications of disc polishing machines are found in industries like metalworking, where they are used for deburring, polishing, and finishing stainless steel, aluminum, and brass parts. They are also widely used in the automotive industry to polish automotive trim, wheels, and engine components. Jewelry manufacturing, electronics, and aerospace industries rely on disc polishing for fine-tuning finishes on parts and components where precision and appearance are critical. Disc polishers are also essential in the manufacture of kitchenware, where items like cookware and cutlery are polished to a high shine.
The benefits of using disc polishing machines are numerous. One of the primary advantages is the consistent, repeatable finishes they provide. Because the machine is designed to apply uniform pressure and speed, it delivers consistent results across multiple parts, which is crucial in high-volume production environments. The use of specific polishing compounds allows for a wide range of surface finishes, from a dull matte to a high-gloss shine, depending on the desired end result. Additionally, the efficiency of disc polishing machines makes them ideal for both small-scale workshops and large-scale manufacturing operations, reducing labor costs and improving throughput.
Maintenance of a disc polishing machine is relatively simple but essential to ensure long-lasting performance. Regular checks should be made to ensure that the disc is free from any damage, cracks, or excessive wear. Over time, polishing discs can become clogged with polishing compounds or particles, so cleaning them regularly is important. The motor and other moving parts should also be lubricated as per the manufacturer’s guidelines to prevent excessive wear and ensure smooth operation.
Safety is an important consideration when using disc polishing machines, particularly because the high-speed rotating discs can be hazardous. Operators should be properly trained in handling the machine, and personal protective equipment (PPE) such as gloves, safety glasses, and dust masks should always be worn. Furthermore, ensuring that the machine is equipped with safety guards and emergency shut-off switches is crucial to prevent accidents.
In addition to basic polishing functions, many modern disc polishing machines come with advanced features like programmable settings for automated control over speed, pressure, and polishing time. Some systems even integrate with robotic arms or conveyors, making them ideal for fully automated production lines where high precision and repeatability are necessary. Integration with CNC controls or PLC systems can further enhance the machine’s versatility, allowing it to adapt quickly to different part sizes and specifications without requiring manual intervention.
Overall, the disc polishing machine is an invaluable tool in the manufacturing and surface finishing world. It combines efficiency, precision, and flexibility to produce high-quality, aesthetically pleasing finishes on a wide range of materials. Whether used in small-scale workshops or large industrial settings, disc polishing machines help manufacturers meet the rigorous demands of modern production, reducing labor costs, minimizing defects, and ensuring consistent quality across parts.
The disc polishing machine is one of the most effective tools for achieving consistent and high-quality surface finishes across various materials. Its basic design—comprising a rotating disc and a motor that drives it—allows for efficient polishing, smoothing, and even light grinding. The rotating disc can be made from a variety of materials such as cloth, paper, rubber, or resin-bonded abrasives, depending on the required finish and material of the workpiece. When polishing, the abrasive surface of the disc removes material from the surface of the workpiece, reducing imperfections, scratches, and other surface defects. The pressure applied to the workpiece, the speed of the disc, and the type of abrasive used all influence the quality of the finish, which can range from matte to high-gloss.
The disc polishing machine offers flexibility in terms of the types of finishes it can produce. For instance, in metalworking applications, it is commonly used for removing oxidation, rust, or scale from metals like stainless steel, aluminum, and brass. The machine’s ability to create smooth, even finishes makes it particularly valuable for industries where the appearance and surface integrity of the final product are critical, such as in the automotive, aerospace, electronics, and jewelry industries. Whether the goal is to create a brushed finish on automotive trim or a shiny surface on jewelry, the disc polishing machine can adapt to various polishing requirements, providing consistent, repeatable results with minimal effort.
In mass production environments, the disc polishing machine stands out due to its speed and efficiency. For example, in the production of cutlery or cookware, a disc polishing machine can significantly reduce the time and labor required for polishing large quantities of parts. The ability to adjust parameters such as speed and pressure means operators can easily tailor the polishing process to suit the material being worked on, whether it’s for light deburring or high-gloss finishing. This efficiency helps manufacturers meet tight production schedules and maintain high throughput while ensuring consistent quality. In automated systems, the disc polishing machine can be integrated into conveyor lines or robotic arms, further enhancing productivity by reducing manual intervention.
Cleaning and maintenance of the machine are important to ensure long-term performance. Over time, polishing discs may become clogged with compounds or particles, requiring regular cleaning to maintain their effectiveness. The machine’s motor, drive system, and other moving parts should also be maintained according to the manufacturer’s instructions to avoid wear and tear. Regular checks of the disc alignment, belt tension, and abrasive wear can prevent defects from affecting the surface finish and ensure smooth operation.
Safety is another critical factor when using a disc polishing machine. The high-speed rotating discs can pose risks to operators, especially if safety precautions are not followed. Wearing appropriate PPE (personal protective equipment) such as gloves, safety glasses, and dust masks is essential. Machines should be equipped with safety guards to prevent accidental contact with the rotating disc, and emergency shut-off switches should be readily accessible in case of malfunction. For systems with automated or robotic components, ensuring that these features are properly safeguarded is critical to preventing accidents.
In recent years, technological advancements have made disc polishing machines even more capable and efficient. Many models now include digital controls, allowing operators to set precise polishing parameters such as speed, pressure, and time. These machines may also come with automated feedback systems, ensuring that the polishing process is continuously adjusted for optimal performance. Some models incorporate CNC or PLC controls, enabling highly automated operations where the machine can be programmed to handle different parts and finishes with minimal human intervention.
Another exciting development is the integration of disc polishing machines with robotic systems. This automation reduces the need for manual labor and improves the consistency of the finish. Robotic arms equipped with specialized grippers can load and unload parts, while sensors and vision systems ensure that parts are positioned correctly for consistent polishing. This level of automation is especially useful in industries like aerospace and automotive, where precision and repeatability are vital.
The environmental impact of disc polishing machines is also a growing concern in modern manufacturing. Dust created during polishing can be hazardous to operators’ health, as well as to the environment. As a result, many newer machines are equipped with advanced dust collection systems to capture and contain airborne particles. Additionally, energy-efficient motors and controls are being incorporated into newer models to reduce energy consumption. The use of eco-friendly polishing compounds and reusable abrasives is also on the rise, further reducing the machine’s environmental footprint.
The versatility, efficiency, and precision of disc polishing machines make them an essential tool for many industries. Whether used for light polishing in custom workshops or as part of high-speed automated production lines, these machines offer a flexible and reliable solution for creating polished, smooth, and aesthetically pleasing finishes. Their ability to produce high-quality results consistently, combined with their adaptability to different materials and finishes, makes them a go-to choice for both small-scale and large-scale manufacturing environments. As new technologies emerge, these machines are expected to become even more efficient, user-friendly, and environmentally sustainable, solidifying their position as an indispensable tool in surface finishing applications.
As disc polishing machines continue to evolve, their capabilities expand in response to growing demands for precision, speed, and sustainability. Manufacturers are increasingly looking for ways to optimize production and reduce operational costs while maintaining high-quality finishes. This has led to the development of advanced automation and smart technologies that enhance the efficiency of disc polishing machines even further.
One area of improvement is the integration of adaptive control systems, which enable the machine to automatically adjust parameters like speed, pressure, and polishing time in real-time. These systems use sensors and feedback loops to monitor the polishing process, ensuring that the finish remains consistent across all parts, even as variables like material hardness or part geometry change. For example, in situations where the workpiece has an uneven surface or varies in thickness, the machine can automatically modify the polishing action to maintain an even finish, reducing the need for manual intervention and improving overall throughput.
Another trend in the evolution of disc polishing machines is the use of robotic arms for part handling and precision placement. Automated systems equipped with robotic arms can perform precise loading and unloading of workpieces, as well as fine-tune the positioning of each part during polishing. This integration helps eliminate human error and ensures that parts are polished uniformly, even in high-volume, continuous production environments. The ability to program these systems with specific polishing routines makes it easier to switch between different tasks, such as polishing different types of materials or creating various surface finishes, without having to reset or recalibrate the entire system.
In multi-disc systems, where several polishing discs are used simultaneously, automation plays a critical role in optimizing efficiency. These systems allow for the polishing of multiple parts at once, increasing throughput and reducing cycle times. When combined with automated part handling systems, multi-disc polishing machines can operate with minimal downtime, processing large batches of components with precision and consistency.
Moreover, data analytics and predictive maintenance are making their way into the disc polishing process. Manufacturers can now track machine performance and collect data on key operational parameters such as belt wear, motor efficiency, and polishing time. Using this data, machine operators can anticipate maintenance needs, reducing unexpected downtime and avoiding costly repairs. Predictive maintenance systems can send alerts when parts are nearing the end of their useful life, enabling operators to replace worn components before they cause issues. This proactive approach helps maintain optimal performance while reducing maintenance costs and increasing machine longevity.
The growing emphasis on sustainability has also spurred innovations in the disc polishing machine market. To address environmental concerns, manufacturers are designing machines that are more energy-efficient, using less power while still maintaining high performance. Some newer models incorporate energy-saving features, such as variable-speed drives and more efficient motors, which reduce electricity consumption. Additionally, the integration of eco-friendly abrasives and polishing compounds that are less harmful to the environment is becoming more common, aligning with the broader industry trend of reducing the carbon footprint of manufacturing processes.
Dust control systems have also seen significant improvements. Older models often relied on simple filters or basic collection mechanisms, which could be inefficient and ineffective in fully capturing harmful particles. Modern disc polishing machines are equipped with high-efficiency dust extraction systems that trap fine particles at the source, preventing them from becoming airborne and contaminating the workspace. These systems often include advanced HEPA filters, which can capture even the smallest particles, ensuring a safer and cleaner working environment for operators.
For industries that require specialized polishing finishes, such as in the aerospace and medical device sectors, disc polishing machines are now designed with greater flexibility. For example, some machines feature adjustable polishing heads that can tilt or rotate to accommodate different part geometries, ensuring that all surfaces—whether flat, curved, or intricate—receive an even finish. These machines can also handle delicate materials like titanium, which is commonly used in the medical field, or exotic alloys used in aerospace applications, without compromising the integrity of the material.
In the jewelry industry, where achieving a flawless surface finish is crucial for both aesthetic and functional reasons, the need for high precision has led to the development of fine polishing machines with extremely high-speed disc rotation. These machines can polish even the most intricate designs, ensuring that no part of the jewelry is overlooked. Additionally, they can achieve mirror-like finishes with minimal effort, making them ideal for processing fine metals like gold, silver, and platinum.
The automotive industry, particularly in the manufacture of exterior trim, wheels, and engine parts, has also benefited from advancements in disc polishing machines. These machines can handle both large and small components with ease, providing an impeccable finish that not only enhances the appearance of the vehicle but also improves corrosion resistance by creating smoother surfaces that are less prone to collecting dirt and moisture. Advanced disc polishing systems can also work with painted or coated surfaces, ensuring that the final finish matches the manufacturer’s high standards.
In research and development, disc polishing machines are used for a variety of applications, including the preparation of specimens for analysis. These machines can be used to polish materials for microscopic examination, ensuring that the surface is free of scratches and imperfections that might interfere with the study of microstructures.
The future of disc polishing machines looks promising, with advancements in automation, data-driven optimization, and sustainability paving the way for more efficient and eco-friendly manufacturing. As the demand for precision and quality continues to grow, these machines will evolve to meet the needs of increasingly diverse industries, helping manufacturers stay competitive in a global market.
In conclusion, disc polishing machines are an integral part of many industries, offering versatility, efficiency, and precision in the surface finishing process. Their ability to adapt to a wide range of materials and applications, coupled with advancements in automation, predictive maintenance, and environmental sustainability, ensures their continued relevance and importance in modern manufacturing. Whether for small-scale production or high-volume industrial operations, the disc polishing machine remains a cornerstone in the pursuit of perfect finishes.
Brush Polishing Machine
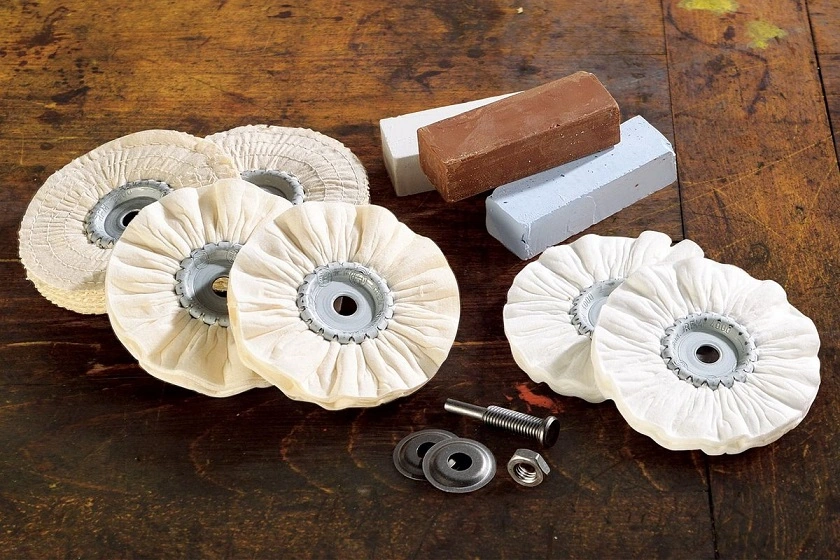
A Brush Polishing Machine is a specialized surface finishing tool primarily used to polish, deburr, and clean parts made from metals, plastics, and other materials. Unlike other polishing machines that use abrasive discs or belts, brush polishing machines utilize rotating brushes that can be made of different materials, including nylon, steel, or synthetic fibers, depending on the task at hand. These brushes are designed to produce a smooth and uniform finish on various surfaces, making them especially suitable for tasks like removing rust, smoothing rough edges, or achieving specific textures on workpieces.
The machine generally consists of one or more rotating brush heads, a motor that drives the brushes, and a mechanism to hold or move the workpiece. The brushes rotate at high speeds, and the workpiece is either fed manually or automatically to the brushes. The pressure applied by the brush to the workpiece, combined with the speed and type of brush used, determines the level of polishing or cleaning achieved. Brush polishing machines are often used for fine surface finishing, where an abrasive disc might be too aggressive or too coarse for the desired result.
One of the key advantages of using a brush polishing machine is its ability to achieve specific textures and finishes. For instance, circular or linear brushing can be used to produce specific grain patterns on metal surfaces, often seen in industries like architectural metalwork and automotive manufacturing. The use of wire brushes, in particular, is common for heavy-duty tasks like removing corrosion, rust, or oxide layers from metal parts. Wire brush polishing is also effective for cleaning parts like pipes or engine components, ensuring that they are ready for further processing, such as coating, painting, or welding.
In the metalworking industry, brush polishing machines are commonly used to clean or finish stainless steel, aluminum, and other metals that require a uniform appearance. Stainless steel is particularly popular in industries such as kitchenware, medical devices, and aerospace, where the surface finish is crucial not only for aesthetics but also for corrosion resistance and hygienic properties. The brush polishing process can help maintain a smooth, matte, or satin finish without the risk of over-polishing that might occur with traditional abrasive tools. Additionally, because the brushes can be softer than abrasive belts or discs, delicate surfaces are less likely to be damaged during the polishing process.
Brush polishing machines are available in various configurations, from bench-top models for small parts or low-volume tasks to large, automated systems that can polish numerous pieces simultaneously in high-volume production settings. These machines can be designed with multiple brush heads, each capable of different types of polishing, allowing for simultaneous multi-stage finishing. For example, one set of brushes might be used for rough cleaning and deburring, while another set could provide the final polish. This multi-stage process reduces cycle times and enhances efficiency, particularly in environments where speed is crucial.
The machine can also be equipped with features like adjustable speeds to accommodate different materials and desired finishes. For example, when working with softer metals like aluminum, slower speeds may be used to ensure a smooth, uniform finish without causing gouging or scratches. On the other hand, harder materials may require higher speeds or more aggressive brushes for effective polishing. Variable pressure settings allow the operator to control the amount of force applied to the workpiece, further enhancing the machine’s versatility.
A notable benefit of brush polishing machines is their ability to remove burrs, oxidation, and other surface contaminants from parts that are difficult to process with other polishing methods. This feature makes them an essential tool in industries such as automotive, where engine components or chassis parts must be deburred or smoothed to remove any sharp edges or imperfections that could affect performance or safety. The ability to effectively remove oxidation is also valuable in the electronic and aerospace sectors, where the integrity of parts must be preserved, and any contamination could affect the quality of the final product.
Brush polishing machines are also highly adaptable to different materials and shapes. For example, they can be used for polishing flat surfaces, curved components, or even intricate parts with detailed geometries, such as in jewelry or medical device manufacturing. This flexibility makes them suitable for a broad range of applications, from fine polishing to more aggressive deburring or cleaning tasks. In many cases, they are used in combination with other polishing methods, such as belt or disc polishing, to achieve a higher level of surface quality.
Dust control is an important consideration when using brush polishing machines, especially in industrial settings where large quantities of material are processed. The polishing process generates a significant amount of dust, particularly when working with metals. To address this, many brush polishing machines are equipped with integrated dust collection systems that capture airborne particles and direct them into a containment unit. These systems help maintain a clean working environment, improve air quality, and protect operators from harmful exposure to fine dust particles.
Safety is another important aspect of using brush polishing machines. While they are generally safer than machines that use more aggressive abrasive methods, operators should still follow safety guidelines. Protective guards around the brush heads are essential to prevent accidents caused by flying debris or accidental contact with the rotating brushes. Operators should also wear personal protective equipment (PPE), including gloves, safety glasses, and dust masks, to minimize the risk of injury and exposure to harmful dust.
In addition to their application in metalworking, brush polishing machines are also used for surface finishing in plastic and woodworking industries. For plastics, these machines can help remove marks, scratches, and imperfections that occur during the molding or fabrication processes, while in woodworking, they are used to create smooth, even finishes on furniture, cabinetry, and flooring. The versatility of brush polishing machines across different industries is a testament to their reliability and effectiveness as finishing tools.
In terms of maintenance, brush polishing machines are relatively easy to maintain compared to other types of polishing equipment. Brushes themselves will wear out over time and need to be replaced periodically, especially if they are used for heavy-duty tasks or on abrasive materials. Regular checks of the motor, brush heads, and dust extraction system are also essential to ensure that the machine operates at peak efficiency. Maintenance schedules and recommendations can vary based on the manufacturer and the specific model of the machine.
The future of brush polishing machines is likely to be shaped by further advancements in automation and intelligent controls. As industries continue to push for higher productivity and more consistent quality, the incorporation of smart sensors, data analytics, and machine learning will allow these machines to monitor and adjust the polishing process in real-time. These innovations will improve efficiency, reduce waste, and allow for greater precision in polishing a wide variety of materials.
In conclusion, brush polishing machines are an essential tool for achieving high-quality surface finishes in a variety of industries. Whether used for deburring, rust removal, or fine polishing, these machines provide a flexible, efficient, and safe solution for polishing a wide range of materials. With the ability to handle delicate surfaces, achieve specific textures, and remove contaminants, brush polishing machines continue to play a key role in both high-volume manufacturing and custom work environments.
Brush polishing machines are highly versatile tools that are designed to handle a wide range of surface finishing tasks across different industries. They are particularly useful for achieving smooth, uniform finishes on a variety of materials, including metals, plastics, and wood. By using rotating brushes made from materials like nylon, steel, or synthetic fibers, these machines can polish, deburr, clean, and texture parts to meet specific requirements.
One of the significant benefits of brush polishing machines is their ability to create specific textures on a workpiece’s surface. This is especially useful in industries where appearance and finish are crucial, such as in architectural metalwork or automotive manufacturing. The brushes can create distinctive grain patterns that are often desired in high-end metal products, from brushed finishes on stainless steel to satin or matte finishes. This method is especially favored for polishing materials like stainless steel, aluminum, and brass, which require a polished look that is resistant to rust and corrosion.
In metalworking, brush polishing is particularly advantageous because it is gentler than other abrasive methods. While abrasive discs or belt polishing machines may sometimes cause damage to delicate surfaces, brush polishing allows for more controlled abrasion, reducing the risk of scratches and gouges. This is particularly important in industries like aerospace, where metal components need to maintain their structural integrity while also having a smooth surface finish. The use of nylon or synthetic brushes makes this technique ideal for creating finishes on parts that need to undergo further processing, such as coating or welding, without compromising the quality of the material.
In addition to polishing, brush polishing machines are effective for cleaning and deburring. These machines are commonly used to remove oxidation, rust, paint, and other contaminants from surfaces. For instance, in the automotive industry, brush polishing is used to clean engine components, exhaust parts, and other metal components, ensuring they are free of rust or debris before they are further processed or painted. The abrasive nature of wire brushes allows them to remove tough contaminants like rust and grime without damaging the underlying material, making them essential tools for maintenance and repair work.
For applications in plastics and woodworking, brush polishing machines provide the same level of versatility. In plastics, they are used to smooth out surfaces that have become rough due to molding or fabrication processes. This ensures that the finished parts are ready for painting or coating without imperfections. Similarly, in woodworking, brush polishing machines are used to create smooth finishes on furniture, cabinetry, and flooring. These machines are also helpful in achieving specific effects, such as a rustic, weathered look in wood products.
The adaptability of brush polishing machines extends to different shapes and sizes of parts. They can be used to polish flat surfaces, curved components, or even intricate designs, such as those seen in jewelry or medical devices. This makes them a critical tool in custom work environments where precision and attention to detail are required. Multi-head polishing machines allow for simultaneous processing of multiple parts, improving productivity and reducing the time spent on individual polishing tasks.
Brush polishing machines are also equipped with various features that enhance their performance. For instance, adjustable speeds enable operators to customize the machine’s operation to suit the material and the type of finish required. The ability to change the pressure applied by the brush ensures that softer materials like aluminum are polished gently, while tougher materials like steel can handle a more aggressive polishing action. Many machines also offer the ability to change out brush heads, allowing for quick adjustments depending on the polishing task. This flexibility is especially valuable in high-volume production settings, where different parts with varying requirements need to be polished in quick succession.
Another crucial consideration when using brush polishing machines is the dust control. Polishing processes generate fine dust and debris, particularly when working with metals. This dust can pose health risks to operators and compromise the cleanliness of the work environment. As a result, modern brush polishing machines are often equipped with dust extraction systems that capture airborne particles as they are produced. These systems help maintain air quality, reduce cleanup time, and ensure that workers are not exposed to harmful dust, particularly when working with metals like aluminum, which can release dangerous dust particles when polished.
Maintenance of brush polishing machines is relatively straightforward but necessary to ensure long-term performance. Brushes themselves will need to be replaced periodically, particularly if they are used in heavy-duty operations or with abrasive materials. Regular checks of the motor, brush heads, and dust collection systems are essential for optimal machine performance. Proper maintenance also helps prevent breakdowns and extends the life of the equipment. Manufacturers usually provide guidelines for regular inspections and replacement schedules, making it easy for operators to keep their machines in good working order.
Safety is a key consideration when operating brush polishing machines. While they are generally safer than machines that use more aggressive abrasives, they still present potential hazards due to the rotating brushes. Protective guards should always be in place to shield operators from flying debris, and personal protective equipment (PPE) such as gloves, safety glasses, and dust masks should be worn. Proper training and adherence to safety protocols are crucial for minimizing the risk of accidents.
Looking ahead, the future of brush polishing machines is likely to see further innovations in automation, data analytics, and energy efficiency. As industries continue to push for faster production times and more consistent results, brush polishing machines are becoming increasingly integrated with robotic systems. These machines can be programmed to handle a variety of parts and finishes with minimal human intervention. In addition, advancements in smart technology may allow for real-time monitoring of machine performance, giving operators insights into potential maintenance needs or adjustments in the polishing process. Furthermore, eco-friendly innovations, such as more efficient dust extraction systems and the use of biodegradable abrasives, will continue to shape the industry towards more sustainable practices.
In conclusion, brush polishing machines are invaluable tools in a wide range of industries due to their versatility, efficiency, and ability to create high-quality finishes. Whether used for polishing, deburring, cleaning, or texturing, they provide reliable and consistent results across materials like metals, plastics, and wood. Their adaptability, ease of maintenance, and ability to work on both simple and intricate parts make them an essential component of surface finishing processes in various manufacturing environments. As technology advances, the capabilities of brush polishing machines will continue to expand, offering manufacturers even greater precision, productivity, and sustainability.
Centrifugal Disc Finisher
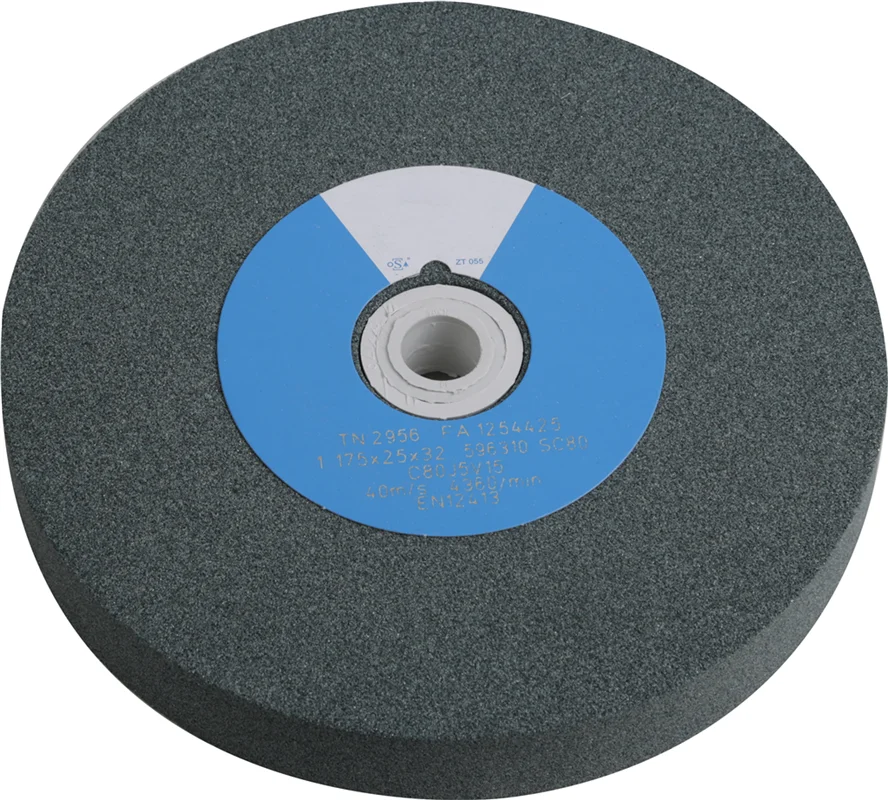
A Centrifugal Disc Finisher (CDF) is a type of mass finishing machine used primarily for polishing, deburring, descaling, and surface smoothing of small to medium-sized parts. It is widely employed in industries such as automotive, aerospace, electronics, medical devices, and metalworking. The centrifugal disc finishing process is known for its high efficiency, precision, and ability to handle a wide range of materials, including metals, plastics, ceramics, and composites.
The basic operating principle of a centrifugal disc finisher involves the use of a rotating disc to create a highly turbulent finishing environment. The machine consists of a circular disc, a container or bowl that holds the workpieces and media, and a high-speed motor that drives the rotation of the disc. As the disc spins at high speeds, it creates a centrifugal force that pushes the workpieces and abrasive media towards the sides of the bowl. The force generated within the system causes the media to act as a cutting or polishing tool, gently abrading the surfaces of the workpieces.
A key feature of a centrifugal disc finisher is its ability to generate a much higher level of energy density compared to other mass finishing machines, such as vibratory finishing systems. This allows the centrifugal disc finisher to achieve faster processing times, making it ideal for high-volume production environments. In addition, the system offers superior control over the process, as the speed of the disc and the angle of the workpieces can be adjusted to achieve the desired finish on each part.
One of the advantages of centrifugal disc finishing is its uniformity. The rotational motion ensures that all parts are evenly exposed to the abrasive media, resulting in a consistent finish across all components. This is especially important when processing parts with intricate shapes or delicate surfaces. In addition, the centrifugal force helps to maintain a highly uniform flow of the workpieces and media, which ensures that all surfaces, including corners, edges, and other hard-to-reach areas, are polished or deburred effectively.
The abrasive media used in centrifugal disc finishing can vary depending on the type of material being processed and the desired finish. Common types of media include ceramic, plastic, steel, and synthetic materials, each offering different levels of aggressiveness and finishing characteristics. For example, ceramic media is often used for its durability and effective cutting power, while plastic media is softer and more suitable for delicate surfaces that require finer polishing. The choice of media is essential to ensure that the machine provides the desired level of surface improvement without damaging the workpieces.
Centrifugal disc finishers are especially well-suited for parts that require precise deburring. The machine’s ability to handle parts with sharp edges and small burrs makes it an essential tool in industries like automotive, where components like gears, engine parts, and fasteners must undergo deburring to ensure safety, proper assembly, and smooth operation. In aerospace, centrifugal disc finishers are used to polish and deburr critical components such as turbine blades and other high-precision parts that need to meet strict standards for finish quality and durability.
The processing time in a centrifugal disc finisher is typically much faster than other mass finishing methods. Depending on the material and finish required, a part may only need a few minutes to achieve the desired result, making it an excellent choice for environments where speed and efficiency are critical. The machine can process large quantities of parts simultaneously, which enhances productivity and reduces labor costs. The system is also highly adaptable, as it can handle both small and complex parts in a range of materials, including those with intricate features, fine tolerances, or delicate surfaces.
In addition to polishing and deburring, centrifugal disc finishers are also used for cleaning and descaling parts. The high-energy environment in the machine can remove oils, grease, and other contaminants from the surfaces of parts, which is particularly valuable in industries where cleanliness and precision are essential. For example, in medical device manufacturing, parts must be free from any contaminants before assembly, and the centrifugal disc finisher helps achieve this level of cleanliness.
Another advantage of centrifugal disc finishers is their environmentally friendly design. Many models are equipped with advanced filtration systems that capture and recycle finishing fluids and debris, reducing waste and minimizing the environmental impact. The machines also use relatively low amounts of water and consumables, making them more sustainable compared to traditional finishing methods. Additionally, the ability to process large batches of parts in a single cycle helps reduce energy consumption and overall operational costs.
The adjustability of centrifugal disc finishers adds to their versatility. In addition to controlling the speed and direction of the disc rotation, many machines offer variable angle settings that allow the user to modify the incline of the bowl to optimize the finishing process for different part geometries. Some models also come with automated control systems that can monitor the progress of the finishing process and make real-time adjustments to achieve the desired results.
While centrifugal disc finishers offer many benefits, they do require careful maintenance to ensure consistent performance. Regular inspection of the motor, disc, and bowl is necessary to ensure that there are no issues with the equipment. Additionally, the abrasive media will need to be replaced periodically, especially when it becomes worn out or clogged with debris. The system’s filtration components should also be cleaned and maintained to ensure proper function and efficiency.
In conclusion, a centrifugal disc finisher is an effective and efficient solution for mass finishing applications. Its ability to provide fast processing times, precise control, and consistent results makes it invaluable in industries that require high-quality deburring, polishing, and surface finishing. With its ability to handle a wide range of materials and part geometries, along with energy-efficient and environmentally friendly design, the centrifugal disc finisher is a key tool in modern manufacturing processes. As industries continue to demand faster production times and higher levels of precision, the centrifugal disc finisher will remain an essential tool in achieving these goals.
Continuing with the advantages of centrifugal disc finishers, they also offer significant improvements in quality control and process optimization. The ability to adjust parameters like speed, angle, and media type allows operators to fine-tune the finishing process for specific parts. This flexibility ensures that the quality of the finish remains consistent across batches, which is crucial in industries where parts need to meet strict specifications. The ability to create uniform finishes on a large number of parts at once reduces the potential for inconsistencies, which might arise when using other mass finishing techniques like vibratory tumbling.
Furthermore, the automation capabilities of centrifugal disc finishers are a major benefit in high-volume manufacturing environments. With automated systems, operators can load parts into the machine, set the desired parameters, and let the machine complete the process without much manual intervention. Automation can also enable the use of automated filtration systems, which help maintain the quality of the finishing media and ensure longer operational life. This system can be integrated with robotic handling equipment for a fully automated finishing solution that significantly reduces labor costs and the potential for human error. In some advanced models, smart sensors and machine learning algorithms can monitor the process in real-time, providing instant feedback to ensure that the parts are being processed according to the required standards.
The versatility of centrifugal disc finishers also extends to their compatibility with various finishing media, which can be easily swapped to achieve different finishes. This adaptability makes the machine suitable for industries that require a range of surface treatments, from polishing and deburring to surface texturing and cleaning. The choice of media also allows manufacturers to adjust the aggressiveness of the finishing process based on the material and the specific needs of the part. For example, softer media like plastic can be used for delicate components to prevent any damage, while harder media like ceramic is more suitable for tougher metals that need a more aggressive finish.
In the medical device industry, where precision and hygiene are paramount, centrifugal disc finishers help to achieve surfaces that are not only smooth but also free from contaminants. This is particularly crucial for implants, surgical instruments, and other parts that come into direct contact with the human body. A consistent, clean finish is necessary to ensure the performance and safety of these devices. Similarly, in the electronics industry, where parts such as connectors and housings require a smooth, clean surface to ensure proper functioning, centrifugal disc finishers are used to meet these exacting standards.
Another area where centrifugal disc finishers excel is precision deburring. When working with intricate or small parts that have sharp edges or burrs left from the manufacturing process, centrifugal disc finishers provide a gentle but effective way to remove these imperfections without altering the shape or integrity of the part. This is especially important in industries like aerospace, where burrs can impact the fit and performance of components such as turbine blades or engine parts. The centrifugal force applied in the machine makes it possible to remove burrs even in tight corners and on delicate features, which can be difficult to address using other methods.
The cost-effectiveness of centrifugal disc finishers is also an important consideration for manufacturers. While initial investments in these machines can be higher than some other mass finishing methods, the long-term benefits in terms of speed, uniformity, and quality control far outweigh the initial costs. The high throughput and ability to process large batches of parts simultaneously reduce per-part costs and increase productivity, making it a valuable tool for high-volume manufacturing. Additionally, the automated and efficient nature of these machines reduces the need for manual labor, helping to lower operational costs.
Centrifugal disc finishers also contribute to a safer working environment. By using a sealed chamber for the finishing process, the risk of exposure to hazardous dust or chemicals is minimized. This is especially important when finishing materials like metals or plastics, which can produce harmful fumes or particles. Moreover, many machines are equipped with integrated dust extraction systems to capture particles and ensure a clean and safe working environment for operators. The enclosed design of these systems also reduces the risk of accidents that can occur when using open-air machines.
Despite their many advantages, centrifugal disc finishers are not suitable for every application. They are most effective for parts that can be placed in a rotating bowl, meaning very large or irregularly shaped parts may not be ideal candidates for this type of mass finishing process. Additionally, the finishing results depend heavily on the type of media and process parameters, so achieving the desired outcome may require some experimentation, especially when working with new materials or complex geometries.
In summary, centrifugal disc finishers are a powerful tool for high-quality surface finishing in various industries. Their ability to handle small and delicate parts, deburr, polish, and clean with precision and efficiency makes them essential in modern manufacturing processes. With their advanced automation, cost-effectiveness, and environmentally friendly design, centrifugal disc finishers continue to be integral to industries such as aerospace, automotive, medical devices, and electronics, where high standards of quality and precision are required. As technology advances, these machines are expected to become even more efficient, precise, and adaptable, further solidifying their place as a crucial component in surface finishing applications.
Centrifugal Barrel Polisher
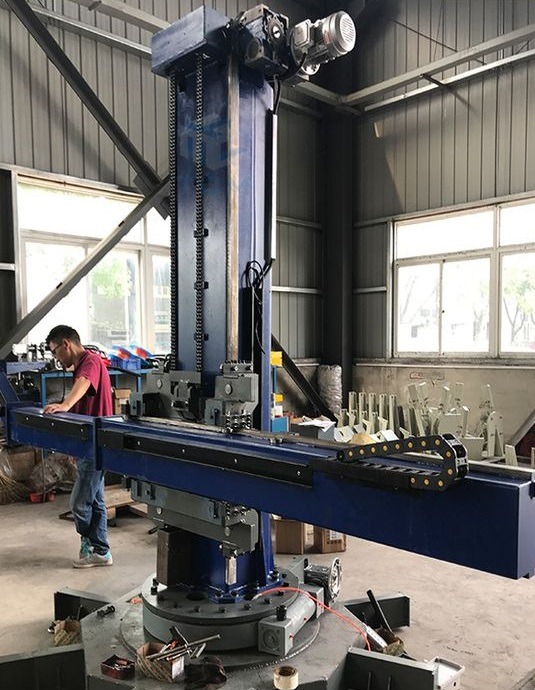
A Centrifugal Barrel Polisher (CBP) is another type of mass finishing machine used for polishing, deburring, and surface smoothing of parts, particularly in industries where high-quality finishes are required on small to medium-sized components. The centrifugal barrel polisher combines elements of both centrifugal force and barrel polishing systems, offering an efficient solution for achieving a variety of surface finishes on parts made from metals, plastics, ceramics, and composites.
How It Works
The centrifugal barrel polisher operates using a set of rotating barrels or drums, which are positioned within a centrifugal chamber. These barrels are loaded with workpieces and abrasive media. The entire chamber rotates at high speeds, generating centrifugal forces that push the media and workpieces towards the inside walls of the barrel. This high-speed rotation causes the abrasive media to act like a grinding or polishing tool, gradually smoothing or finishing the surfaces of the workpieces.
As the barrels spin, the workpieces are subjected to intense friction and impact from the abrasive media, which effectively deburrs sharp edges, removes oxidation, polishes the surface, or provides a smooth finish. The centrifugal force in this type of system is typically much higher than in conventional barrel polishing or vibratory finishing systems, making it an ideal solution for high-efficiency processing in both small batches and large volumes.
Advantages of Centrifugal Barrel Polishers
- High Processing Efficiency: The centrifugal forces created by the rotating barrels allow for faster finishing times compared to traditional barrel tumblers or vibratory finishing machines. This makes it a highly effective option for high-volume production settings, where speed is a key factor.
- Superior Finish Quality: The higher rotational speed and intense energy generated within the barrels result in a smooth and consistent surface finish. This is particularly valuable in industries such as aerospace, automotive, and medical device manufacturing, where high-quality surface finishes are essential for performance, durability, and safety.
- Adaptability: Centrifugal barrel polishers are suitable for a wide range of materials, including metals, plastics, and ceramics. The flexibility in choosing different types of abrasive media—such as ceramic, plastic, steel, or synthetic materials—enables manufacturers to tailor the finishing process to the specific requirements of each part and material.
- Deburring and Edge Radiusing: One of the primary applications of centrifugal barrel polishers is deburring, the process of removing sharp edges or burrs left behind from the machining or manufacturing process. The high-energy environment inside the barrels is effective at smoothing out rough edges and corners. The system is also adept at edge radiusing, which rounds off sharp corners to prevent damage or injury during handling or assembly.
- Cleaning: In addition to polishing and deburring, centrifugal barrel polishers are effective for cleaning parts. The abrasive media used in the machine can remove dirt, oils, grease, and other contaminants from the surface of the parts. This is particularly important in industries like medical devices and electronics, where parts need to be thoroughly cleaned before further processing or assembly.
- Uniformity: The design of the centrifugal barrel polisher ensures that all parts are exposed to the abrasive media in a uniform manner, which leads to consistent finishes across large batches of components. This makes it ideal for processes where the finish must be applied evenly across parts with intricate or complex shapes.
- Automation and Reduced Labor Costs: Centrifugal barrel polishers can be equipped with automated systems for loading, unloading, and media handling. Automated systems improve productivity and reduce the amount of manual labor required, making the finishing process more efficient and cost-effective. Automated loading and unloading can significantly cut down cycle times and reduce human error in the operation.
- Compact Design: Compared to traditional vibratory finishers, which require large, open bowls or tubs, centrifugal barrel polishers often feature a more compact design that requires less floor space. This is especially advantageous for manufacturing environments with limited space or those looking to optimize the footprint of their finishing equipment.
Applications
- Automotive Industry: In the automotive industry, centrifugal barrel polishers are widely used for finishing parts like brake components, gears, valves, and engine parts. These components often require precise deburring and polishing to ensure proper fitment, smooth operation, and durability.
- Aerospace: Aerospace parts, such as turbine blades, fuel system components, and fasteners, require very specific surface finishes for both performance and safety. Centrifugal barrel polishers can provide the necessary deburring and polishing while maintaining the dimensional integrity and strength of these critical components.
- Medical Devices: In the medical device industry, parts like surgical instruments, implants, and prosthetics need to have smooth, precise surfaces to ensure both safety and performance. The centrifugal barrel polisher is commonly used for cleaning, deburring, and polishing these sensitive parts.
- Electronics: In electronics, centrifugal barrel polishers are used to finish parts such as connectors, circuit board components, and housing enclosures. The machines help to achieve a clean, smooth surface free of contaminants, which is necessary for the proper function of electronic devices.
- Jewelry: Jewelry manufacturers often use centrifugal barrel polishers to create smooth, shiny finishes on rings, necklaces, and other components. The machines provide a high degree of control, allowing the operator to achieve a uniform finish even on intricate or delicate parts.
- Cutlery and Kitchenware: In the manufacturing of cutlery, kitchen tools, and utensils, centrifugal barrel polishers are used to achieve polished finishes while simultaneously removing burrs and sharp edges that could cause injury.
Types of Media Used
The media used in centrifugal barrel polishers can vary depending on the material being polished and the desired finish. The most commonly used media types include:
- Ceramic media: Durable and suitable for metal finishing, ceramic media is often used for aggressive deburring and polishing. It is available in different shapes and sizes, including triangles, cylinders, and cones, to suit different finishing needs.
- Plastic media: Softer than ceramic media, plastic media is often used for delicate parts or for polishing applications where a finer finish is needed without causing damage to the part.
- Steel media: Steel media is typically used for heavier deburring applications or for parts that require a more aggressive cut.
- Synthetic media: Synthetic media is often used for high-precision or polishing applications where a fine, smooth finish is required.
- Rubber and foam media: These types of media are sometimes used in combination with softer abrasive compounds to achieve a finer, more polished surface.
Maintenance and Considerations
Like any mass finishing machine, the centrifugal barrel polisher requires regular maintenance to ensure optimal performance. The key maintenance tasks include:
- Cleaning and replacing abrasive media: Over time, the media used in the barrel will wear out and need to be replaced. Keeping the media clean ensures that the machine continues to operate efficiently.
- Inspecting the barrels: The barrels should be checked regularly for any wear or damage. Worn-out barrels may need to be replaced to maintain proper finishing results.
- Lubrication: The rotating parts of the machine, such as the motor and bearings, should be properly lubricated to prevent excessive wear and tear.
- Cleaning the filtration system: Many centrifugal barrel polishers have built-in filtration systems to remove debris and keep the finishing process clean. These filters should be cleaned or replaced periodically.
Conclusion
Centrifugal barrel polishers are a highly effective solution for industries that require high-quality finishes on small to medium-sized parts. With their high-speed operation, ability to produce consistent finishes, and adaptability to various materials, they offer significant advantages in terms of speed, precision, and efficiency. Whether used for deburring, polishing, cleaning, or surface smoothing, centrifugal barrel polishers are an essential tool in the manufacturing process for industries such as aerospace, automotive, medical devices, and electronics. Their versatility, combined with automated features and compact design, makes them an attractive option for manufacturers looking to improve the quality and efficiency of their mass finishing operations.
A Centrifugal Barrel Polisher (CBP) is a powerful mass finishing machine widely used for polishing, deburring, and smoothing parts, especially when a high-quality finish is required. The machine operates by using rotating barrels placed inside a centrifugal chamber. These barrels hold both the workpieces and abrasive media. When the chamber spins at high speeds, centrifugal forces push the media and parts towards the barrel walls. The resulting friction and impact from the abrasive media gradually smooth the surfaces of the workpieces, effectively deburring sharp edges, polishing, and cleaning parts.
The key advantage of a centrifugal barrel polisher is its ability to operate at high speeds, which generates a much greater amount of finishing energy compared to traditional methods like vibratory finishing or barrel tumbling. This increased energy density enables the machine to complete processes like polishing and deburring much faster, which makes it particularly suited for high-volume production environments. In industries such as automotive, aerospace, medical devices, and electronics, where surface finish and precision are critical, the centrifugal barrel polisher offers the efficiency and quality required.
One of the benefits of centrifugal barrel polishers is their versatility in handling a wide range of materials. Whether working with metals, plastics, ceramics, or composites, these machines can be configured to provide the right finishing solution by adjusting the abrasive media used. Media types range from ceramic and plastic to steel and synthetic materials, with each type suited for different tasks. For example, ceramic media is more aggressive and works well for heavier deburring, while plastic media is gentler and suitable for delicate parts that require a finer finish.
In addition to providing uniform and consistent finishes, centrifugal barrel polishers excel at handling a large volume of parts at once. The high energy generated inside the barrels ensures that even small or intricately shaped components receive the same level of attention as larger parts, resulting in a consistent and high-quality finish across all items in the batch. This capability is especially important in industries where parts need to be processed in large quantities, such as in automotive or electronics manufacturing.
Another significant advantage is the machine’s ability to perform multiple functions simultaneously. Not only do centrifugal barrel polishers remove burrs and smooth sharp edges, but they also help clean parts by removing oils, grease, and contaminants. The process can be tailored for specific needs, such as cleaning delicate medical devices or polishing automotive components. The machine can even be set up for edge radiusing, which is essential for applications where components need to have smooth, rounded edges to prevent damage or ensure a proper fit in assembly.
Additionally, centrifugal barrel polishers are compact compared to traditional vibratory finishers, which require large bowls or tubs. This compact design makes them ideal for environments with limited space, allowing manufacturers to optimize their floor space. Many models also feature automated systems for loading and unloading parts, as well as automated media handling, which further increases the machine’s efficiency and reduces labor costs.
The process inside the centrifugal barrel polisher also ensures that parts are finished in a manner that is consistent and repeatable. By adjusting factors such as the speed of rotation, the type of media, and the time spent in the machine, operators can achieve a precise surface finish for each batch of parts. This is especially important in industries where parts must meet strict specifications, such as in the medical field, where even the smallest imperfections can lead to significant issues.
For maintenance, centrifugal barrel polishers are designed to be relatively easy to maintain. The barrels, which are subject to wear over time, should be regularly inspected and replaced when necessary. Abrasive media will also need to be replenished, as they wear down during the finishing process. To maintain the efficiency of the system, the filtration systems that capture debris and contaminants should be cleaned and replaced as needed. Proper lubrication of the rotating parts is also essential to prevent excessive wear and ensure smooth operation.
Despite their high performance and speed, centrifugal barrel polishers may not be the best choice for very large parts or irregularly shaped components that cannot fit in the barrel or cannot rotate freely within it. In these cases, other finishing methods, such as tumbling or vibratory finishing, might be more appropriate. Additionally, while the centrifugal barrel polisher is incredibly efficient, it requires careful setup and selection of media to avoid damaging delicate parts or achieving undesirable finishes.
In conclusion, centrifugal barrel polishers are a versatile and highly efficient tool in mass finishing operations. Their ability to process a wide range of materials, produce consistent and high-quality finishes, and handle high volumes of parts with minimal labor makes them a valuable asset in industries such as automotive, aerospace, medical devices, electronics, and jewelry manufacturing. With their compact design, automation capabilities, and adaptability to various media, centrifugal barrel polishers offer manufacturers a reliable and efficient solution for achieving polished, deburred, and cleaned parts. As technology continues to improve, these machines will remain a key component of surface finishing operations, providing faster processing times and better-quality results across numerous industries.
Pipe Polishing Machine
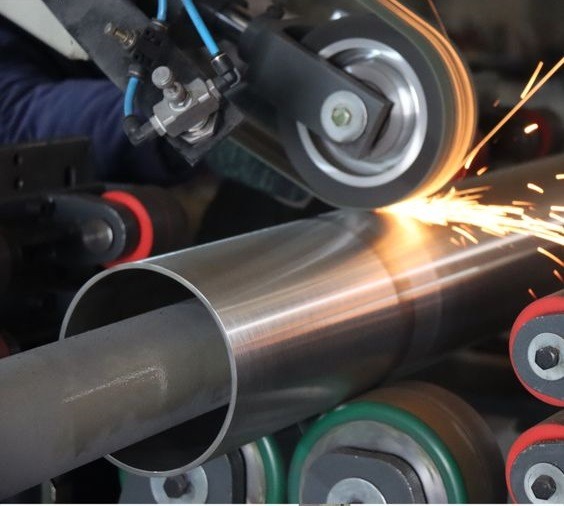
A Pipe Polishing Machine is designed to polish and finish the surfaces of pipes, tubes, and cylindrical workpieces to achieve a smooth, shiny, or decorative finish. These machines are commonly used in industries such as automotive, aerospace, construction, chemical, and food processing, where pipes are often required to meet strict surface finish standards. The polishing process typically involves removing surface imperfections, scratches, oxidation, and residues to provide a clean, aesthetically pleasing, and durable finish.
The pipe polishing machine operates by using abrasive materials (often in the form of belts, brushes, or buffing wheels) that come into contact with the surface of the pipe. The pipe is either manually or automatically fed through the machine, depending on the machine’s design. The abrasive material removes the top layer of the surface, gradually smoothing out imperfections and achieving the desired finish. These machines are capable of polishing various pipe materials, including stainless steel, carbon steel, aluminum, and copper, among others.
Types of Pipe Polishing Machines include:
- Belt Polishing Machines: These machines use abrasive belts that wrap around a rotating drum or wheel. The pipe is held firmly in place while the abrasive belt moves along its surface, removing imperfections and producing a uniform finish. Belt polishing machines are highly effective for achieving matte, satin, or mirror finishes on pipes and tubes. They are suitable for continuous production and can handle large volumes of parts.
- Brush Polishing Machines: These machines use brushes, often made of wire or nylon, to polish the surface of the pipe. The pipe is fed through the machine while the rotating brushes gently clean and polish the surface. Brush polishing is ideal for achieving a satin finish or for polishing delicate materials that need a gentler touch. They can also be used for deburring and cleaning pipes that have been welded.
- Buffing Machines: Buffing machines use soft buffing wheels and a polishing compound to provide a high-gloss finish on pipes and tubes. This process is often used in industries where an extra-smooth, shiny, or mirror finish is required. Buffing machines are typically used in the final stages of the polishing process to enhance the appearance of the pipe and provide a protective layer on the surface.
- Rotary Pipe Polishing Machines: In this type of machine, the pipe is rotated while abrasive materials are applied to its surface. The rotary action ensures that the entire circumference of the pipe is evenly polished. These machines are used for both light and heavy polishing tasks, depending on the material and the desired finish. They are also efficient at handling long pipes or tubes.
- Centrifugal Pipe Polishing Machines: These machines use centrifugal force to spin abrasive media against the pipe’s surface. The media, which can vary from ceramic to plastic or steel, removes surface defects and creates a polished finish. Centrifugal machines can handle larger volumes of pipes in less time and are commonly used for mass finishing processes.
The main benefits of using a pipe polishing machine include:
- Consistency: The machine ensures a uniform surface finish across all pipes, eliminating inconsistencies that may occur with manual polishing.
- Efficiency: Polishing machines can handle high volumes of pipes, making them ideal for large-scale manufacturing operations where speed is essential.
- Versatility: Many pipe polishing machines are adaptable to different types of abrasive media and can be used to achieve various finishes, such as satin, mirror, or matte.
- Improved Aesthetic Appeal: Polished pipes are visually more appealing, which is important in applications like decorative railings, handrails, or high-end kitchen appliances.
- Increased Durability: The polishing process often helps remove surface contaminants and oxidation, potentially increasing the pipe’s corrosion resistance and overall longevity.
However, it is important to select the appropriate polishing machine and abrasive material based on the pipe material, size, shape, and desired finish. Proper maintenance of the machine and the abrasives used is also essential for achieving optimal results and extending the machine’s lifespan.
A pipe polishing machine is a specialized tool used for achieving smooth, shiny, or decorative finishes on pipes and tubes. These machines are essential in various industries where pipes need to meet specific surface finish standards for aesthetic, functional, or hygienic reasons. Whether for stainless steel, aluminum, copper, or other materials, pipe polishing machines help remove surface imperfections such as scratches, oxidation, and weld marks, providing a polished and uniform appearance.
Pipe polishing typically involves abrasive materials like belts, brushes, or buffing wheels, which are used to smooth out the surface of the pipe as it moves through the machine. The pipe can be fed manually or automatically, depending on the machine’s design. As the abrasive media interacts with the pipe’s surface, it gradually wears away imperfections, resulting in the desired finish. The machine’s speed and the type of abrasive media used can be adjusted to achieve different finishes, from matte or satin to high-gloss or mirror-like finishes.
Belt polishing machines use abrasive belts that wrap around a rotating drum, applying a uniform finish across the surface of the pipe. These machines are effective in high-volume operations and are capable of providing finishes such as satin or matte, depending on the choice of abrasive material. Brush polishing machines use rotating brushes made from materials like wire or nylon to provide a gentler polishing action, often used for achieving a satin finish or cleaning pipes with delicate surfaces. Buffing machines are another type, which use soft buffing wheels and polishing compounds to create a glossy, high-shine finish on pipes, often in the final stages of the polishing process.
Rotary pipe polishing machines are designed to rotate the pipe as it is polished, ensuring that the entire circumference of the pipe receives an even finish. These machines are commonly used for both light and heavy polishing applications and can accommodate long pipes or tubes. In contrast, centrifugal pipe polishing machines use centrifugal force to apply abrasive media to the surface of the pipe, making them highly efficient for mass finishing applications where a large number of pipes need to be processed quickly.
Pipe polishing machines offer several benefits, such as consistency in achieving uniform finishes across all workpieces, efficiency in handling high volumes of pipes, and the versatility to adapt to different materials and desired finishes. The polishing process not only improves the appearance of pipes but can also increase their durability by removing contaminants and improving corrosion resistance. In industries like automotive, aerospace, construction, food processing, and medical devices, polished pipes are essential for meeting specific performance and aesthetic requirements. Additionally, these machines help improve the aesthetic appeal of the pipes, which is crucial in applications like decorative railings, kitchen appliances, or architectural elements.
Selecting the right polishing machine and abrasive media is essential for achieving the desired result. Factors such as the material of the pipe, its size, and shape, as well as the finish required, play a significant role in determining which type of machine and abrasives will be most effective. Proper maintenance of both the machine and the abrasives ensures optimal performance and longevity, making pipe polishing machines a vital tool in any manufacturing setting that requires high-quality surface finishes.
Pipe Polishing Machine
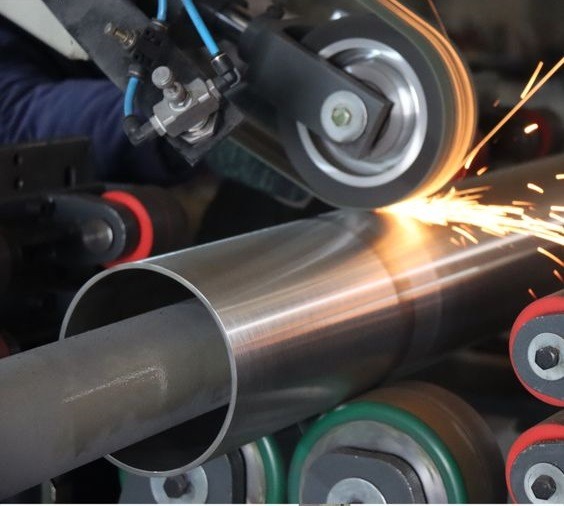
A Pipe Polishing Machine is designed to provide a high-quality finish to pipes and tubes, particularly in industries where surface appearance, durability, and cleanliness are crucial. These machines are used to remove surface imperfections like scratches, weld marks, oxidation, or burrs and to achieve smooth, glossy, or satin finishes on pipes made from metals such as stainless steel, aluminum, copper, and more. Pipe polishing is common in industries like automotive, construction, aerospace, medical devices, food processing, and decorative purposes.
The machine typically operates by using abrasive materials, such as belts, brushes, or buffing wheels, which are applied to the surface of the pipe as it is fed through the machine. The type of abrasive material, as well as the machine’s speed and settings, determines the type of finish achieved.
One common type of pipe polishing machine is the belt polishing machine, which uses abrasive belts that wrap around a rotating drum. The pipe is pushed through the machine, and the abrasive belt polishes the surface by coming into contact with it. Belt polishing machines are well-suited for high-volume production and can provide finishes ranging from matte to satin or mirror-like, depending on the abrasive chosen.
Another type is the brush polishing machine, which uses rotating brushes made from wire or nylon. These brushes polish the surface of the pipe gently, often creating a satin or matte finish. Brush machines are particularly useful for polishing delicate or irregularly shaped parts and are effective for cleaning as well.
Buffing machines, on the other hand, use soft buffing wheels and a polishing compound to provide a high-gloss, mirror-like finish. This type of machine is typically used in the final stages of polishing to give pipes a reflective, smooth surface.
For pipes that require polishing across the entire circumference, rotary pipe polishing machines are ideal. These machines rotate the pipe as it moves through the system, ensuring an even finish around the pipe. They are suitable for both light and heavy polishing tasks and can handle long pipes with ease.
Lastly, centrifugal pipe polishing machines use centrifugal force to apply abrasive media to the surface of the pipe. This method is especially efficient for high-volume production and mass finishing processes, as it speeds up the polishing process while delivering uniform results.
The key benefits of pipe polishing machines include uniformity, ensuring consistent finishes on large quantities of pipes; efficiency, enabling quick processing of large volumes; and versatility, with machines able to accommodate different pipe materials, shapes, and finishes. Pipe polishing can also enhance the durability of pipes by removing surface contaminants and providing a smoother surface that may resist corrosion better.
In addition to enhancing the appearance of pipes, these machines are also important for improving the functionality and performance of the pipes in various applications. The removal of surface imperfections can ensure that pipes fit together properly in assemblies, reduce friction in fluid flow applications, and provide a hygienic surface in industries such as food processing or pharmaceuticals. Proper machine maintenance and choosing the right abrasive media are essential to achieving optimal results and maintaining efficiency.
A pipe polishing machine is a specialized piece of equipment used to improve the surface quality of pipes and tubes, making them smoother and more aesthetically pleasing. These machines are essential in various industries where the pipes need to meet high standards of appearance, durability, and functionality. Polishing removes imperfections like scratches, weld seams, oxidation, or corrosion, leaving behind a clean, shiny, and uniform finish. The machines are used for pipes made from a range of materials, including stainless steel, aluminum, copper, and others, each of which requires a specific approach to achieve the desired finish.
The process involves the use of abrasive materials such as belts, brushes, or buffing wheels that come into contact with the surface of the pipe. The type of abrasive, speed of the machine, and the settings all determine the finish quality. A belt polishing machine, for example, uses abrasive belts wrapped around rotating drums. The pipe is guided through the machine while the abrasive belt polishes its surface. This method is suitable for mass production, providing a uniform satin or matte finish, or a mirror-like shine depending on the abrasive used.
A brush polishing machine, typically using wire or nylon brushes, works more gently, often creating a satin or matte finish. It is ideal for pipes that may be more delicate or need a finer touch. This type of machine is useful not only for polishing but also for cleaning, particularly in industries like food processing, where cleanliness is crucial. Buffing machines, which use soft buffing wheels, are commonly used to achieve high-gloss finishes. This is the final step in polishing when the goal is to create a mirror-like or glossy appearance.
Rotary pipe polishing machines offer another approach, where the pipe is rotated during polishing. This ensures that the entire circumference of the pipe receives a consistent finish, making these machines ideal for longer or cylindrical parts. Similarly, centrifugal pipe polishing machines utilize centrifugal force to push abrasive media against the pipe surface, making them highly efficient for mass finishing. They are commonly used for high-volume production environments, speeding up the polishing process without compromising on the quality of the finish.
The benefits of pipe polishing machines go beyond just improving aesthetics. They ensure consistency across a large number of parts, making it possible to maintain the same high quality for each unit processed. They also enhance the functionality of pipes in their intended applications. For instance, pipes with smoother finishes experience less friction, improving fluid flow in applications like plumbing or industrial machinery. The polished surface can also make pipes more corrosion-resistant, particularly when contaminants like rust or oil are removed during the polishing process.
These machines are versatile, capable of handling a wide variety of pipe sizes, shapes, and materials. Whether dealing with small, delicate components or large industrial pipes, a pipe polishing machine can be tailored to meet the needs of the job. They can handle high-volume operations efficiently, making them invaluable in industries where time and productivity are critical. Proper maintenance of the machine and the abrasives ensures longevity and consistent performance, allowing businesses to get the most out of their equipment.
Ultimately, a pipe polishing machine not only improves the appearance of pipes but also enhances their durability, performance, and suitability for specific applications. Whether for decorative purposes in architectural designs or functional requirements in industrial systems, these machines are indispensable tools for modern manufacturing.
Tube Outer Diameter Polisher
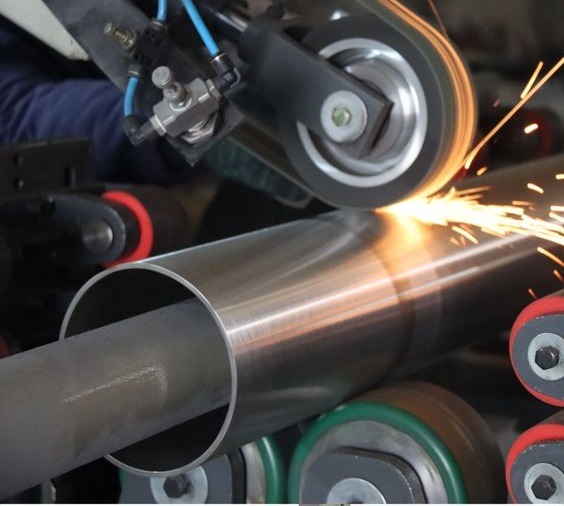
A Tube Outer Diameter Polisher is a specialized machine designed to polish the outer surface of tubes and pipes. This type of equipment is commonly used in industries where the tube’s appearance, smoothness, and functionality are crucial. The primary goal of this machine is to improve the outer diameter of tubes by removing imperfections, scratches, weld seams, oxidation, and other surface defects, ultimately achieving a smooth, shiny, or matte finish, depending on the application.
The machine works by feeding the tube through a system that uses abrasive materials like belts, brushes, or buffing wheels. These abrasive materials come into contact with the outer surface of the tube, and depending on the type of abrasive used, the tube’s surface is polished to a uniform finish. The tube is typically rotated during the process to ensure that the entire circumference of the outer diameter receives an even polish.
In a belt polishing machine, abrasive belts are wrapped around a rotating drum, and the tube is fed through the system while the belt polishes its surface. The high-speed movement of the abrasive belt effectively removes imperfections and can achieve various finishes depending on the grit of the abrasive material. These machines are efficient for processing large volumes of tubes and can provide consistent results across many parts.
For more delicate finishes, brush polishing machines use rotating wire or nylon brushes that provide a gentler polishing action. These machines are suitable for tubes that require a softer touch or a satin-like finish. Brush polishing is ideal for removing oxidation or cleaning the surface without altering the tube’s shape or structure.
For achieving a high-gloss, mirror-like finish, a buffing machine can be used in the final stages. These machines utilize soft buffing wheels along with a polishing compound to smooth the tube’s outer diameter to a high shine. This is especially important in industries like aerospace or medical devices, where appearance and a smooth surface are not only important for aesthetics but also for functionality, such as reducing friction or preventing contamination.
The tube outer diameter polisher can also be equipped with automation features that load and unload the tubes, ensuring efficient operation, especially in high-volume production environments. The precise control of polishing parameters, such as speed, pressure, and abrasive choice, allows operators to fine-tune the process to achieve the desired surface finish for different tube materials and applications.
These machines are essential in industries such as automotive, construction, medical device manufacturing, and decorative metalwork, where tubes are often exposed and require a polished appearance or smooth, functional surface. Additionally, polishing the outer diameter of tubes can improve their corrosion resistance and aesthetic appeal, making them more suitable for use in visible applications or where they are subject to harsh environmental conditions.
A key advantage of tube outer diameter polishers is their ability to process tubes of varying sizes and materials. The machines can handle tubes with small diameters to larger industrial pipes, making them versatile tools in any manufacturing facility. The use of abrasive media allows the machine to work on different metals, such as stainless steel, aluminum, copper, and others, each of which may require a unique approach in terms of abrasive selection and polishing technique.
In conclusion, a tube outer diameter polisher is a valuable tool for improving the appearance, performance, and longevity of tubes in a wide range of industries. Whether used to achieve a basic smooth finish or a high-gloss shine, these machines ensure consistent, high-quality results and can handle a variety of tube sizes and materials efficiently.
A tube outer diameter polisher is an essential machine in industries where the external surface of tubes needs to be polished for both aesthetic and functional purposes. These machines are used to remove surface imperfections such as scratches, oxidation, and weld seams from the outer diameter of tubes, leaving behind a smooth, uniform finish. This process improves not only the appearance but also the durability and performance of the tubes. Tube outer diameter polishers are crucial in applications where the pipes or tubes are exposed or need to meet strict surface finish standards for functionality, such as in medical devices, aerospace components, automotive systems, or decorative elements.
The machine typically operates by rotating the tube while abrasive materials, such as polishing belts, brushes, or buffing wheels, are applied to the surface. The rotating action ensures that the entire circumference of the tube receives an even polish, providing a consistent finish throughout. The type of abrasive material used, as well as the machine’s speed and settings, determines the final surface finish. For example, an abrasive belt polisher can achieve a satin or matte finish, depending on the grit of the abrasive. In contrast, buffing machines are used for achieving a high-gloss or mirror-like finish, especially in the final stages of polishing.
One of the key features of tube outer diameter polishers is their ability to handle high volumes of tubes efficiently. Many machines are equipped with automated feeding and unloading systems, which allow for continuous, high-speed operation, making them ideal for mass production environments. These machines can process tubes made from a variety of metals such as stainless steel, aluminum, copper, and other alloys, each of which may require different abrasive media or polishing techniques.
These polishers are designed for precision, allowing operators to adjust settings like speed, pressure, and abrasive choice, which ensures that the desired finish can be consistently achieved. Tube polishing not only enhances the aesthetic appeal but also plays a crucial role in improving the corrosion resistance and smoothness of the tube’s surface. A smoother tube surface can reduce friction in fluid flow applications, which is especially important in piping systems, heat exchangers, or any system where the tube will come into contact with various materials or fluids.
The versatility of tube outer diameter polishers allows them to be used for different tube sizes, from small diameter pipes to larger industrial tubes. This makes them an indispensable tool in both small-scale and large-scale manufacturing operations. By offering the ability to fine-tune the polishing process, these machines help manufacturers maintain high-quality standards and ensure that every tube or pipe meets the required surface finish specifications.
In conclusion, a tube outer diameter polisher is a critical piece of equipment for improving the quality, appearance, and durability of tubes in various industries. Whether the goal is to achieve a simple smooth surface or a high-gloss finish, these machines provide the necessary precision and efficiency to meet the demands of modern manufacturing. The ability to handle large volumes, work with different materials, and produce consistent results makes tube outer diameter polishers a valuable investment for businesses looking to enhance their production processes and product quality.
Tube Inner Diameter Polisher
A Tube Inner Diameter Polisher is a specialized machine designed to polish the inner surface of tubes and pipes. This type of equipment is essential in industries where the inner surface of tubes needs to meet specific surface finish requirements for both aesthetic and functional purposes. The primary objective of this machine is to smooth and refine the inner diameter of pipes, removing imperfections such as rust, oxidation, scale, scratches, and weld seams. This polishing process ensures that the interior surface is smooth, clean, and free of any contaminants, which is crucial for applications where flow efficiency, corrosion resistance, and hygiene are important.
The tube inner diameter polisher works by using abrasive tools such as brushes, abrasive belts, or polishing heads that are inserted into the tube. As the tube is rotated or moved through the machine, the abrasives come into contact with the inner surface, removing imperfections and leaving behind a smooth, polished finish. The abrasive materials can vary depending on the desired finish and the material of the tube being polished, such as stainless steel, aluminum, copper, or other metals.
One of the most common methods used for polishing the inner diameter of tubes is through abrasive brush polishing. These machines use rotating brushes that are inserted into the tube and rotated to polish the inner surface. The rotating brushes are typically made of materials such as nylon or wire and can be adjusted to provide different levels of abrasiveness. Brush polishing machines are particularly useful for cleaning, deburring, and achieving a satin or matte finish on the interior of the tube.
Another method is the use of abrasive belt polishing. This method involves running an abrasive belt through the inside of the tube, which rotates as the tube moves through the machine. The belt’s abrasive surface works to remove imperfections from the inner surface. This process is suitable for tubes with relatively larger diameters or those requiring a more uniform finish.
Some more advanced tube inner diameter polishers use rotating polishing heads or expandable mandrels that expand to fit the tube’s inner diameter. These heads or mandrels are equipped with abrasive materials, and as the head moves through the tube, it polishes the inner surface evenly. This type of machine is ideal for handling tubes of varying sizes, as the mandrel can adjust to fit different inner diameters, ensuring consistency in the finish across all parts.
The key benefits of tube inner diameter polishers include improving flow efficiency in pipes where smooth internal surfaces are critical for reducing friction in fluid transport systems. A polished inner surface reduces turbulence and increases the efficiency of fluid or gas flow through pipes, making them ideal for pharmaceutical, food processing, chemical, and aerospace industries where high-quality standards are mandatory. Additionally, a polished inner surface can increase the corrosion resistance of pipes by removing contaminants and ensuring the material is free from pitting or damage.
These machines are also critical in improving the hygiene of tubes, particularly in industries such as food, beverage, and pharmaceuticals, where sanitary conditions are paramount. A smooth, clean inner surface reduces the likelihood of bacterial growth or contamination in pipes that come into contact with consumables or medical products.
Moreover, tube inner diameter polishers are versatile in handling a wide range of tube sizes, from small-diameter tubes used in medical devices or instrumentation to larger pipes found in industrial settings. Adjustments can be made to accommodate different tube materials, ensuring that the right amount of abrasiveness is applied to achieve the desired surface finish without damaging the material.
In conclusion, tube inner diameter polishers are indispensable for ensuring the quality, functionality, and longevity of pipes and tubes across various industries. By providing a smooth, polished finish on the inner surface, these machines enhance flow efficiency, reduce maintenance needs, improve corrosion resistance, and ensure that the tubes meet strict performance standards. The ability to work with different tube sizes, materials, and finishes makes tube inner diameter polishers essential for modern manufacturing and production environments.
The tube inner diameter polisher plays a vital role in modern manufacturing, ensuring that tubes meet both aesthetic and performance standards. The precision required for polishing the inner surface of tubes is crucial, especially when tubes are used in systems where smooth flow and hygiene are paramount. These machines are often employed in industries where even the smallest imperfections on the inner surface can lead to significant performance issues or contamination risks.
In industries like pharmaceuticals and biotechnology, tube inner diameter polishers are essential for ensuring that piping systems used in drug production, medical devices, and laboratory equipment meet stringent hygiene standards. The smoothness of the interior surface is critical in preventing microbial growth, minimizing the risk of contamination, and ensuring that the product being transported remains pure and uncontaminated throughout the process.
In food processing, where food-grade tubes are used for transporting liquids and gases, the smooth, polished interior prevents the accumulation of bacteria, mold, or food residues that could spoil the product or affect quality. Polishing the inner diameter of tubes in these environments also facilitates cleaning processes, as smooth surfaces are easier to clean and sanitize effectively, ensuring compliance with health regulations.
Another area where tube inner diameter polishers excel is in aerospace and automotive industries, where they are used to polish tubes and pipes in fuel systems, hydraulic systems, and exhaust systems. In these applications, tube surface quality is essential to ensure the efficient transport of fluids and gases without the risk of corrosion or flow blockages, which could compromise the safety and performance of the systems.
For chemical processing, tube inner diameter polishers can be used to clean and polish pipes that carry corrosive chemicals, helping to maintain the integrity of the system and ensuring that there are no leaks or blockages that could lead to hazardous situations. The smooth interior of the tube also helps reduce the rate of corrosion, prolonging the lifespan of the equipment and reducing maintenance costs.
These machines can be customized to meet specific requirements in terms of tube size, material, and finish. Some models can accommodate a wide range of pipe diameters, from small precision tubes used in medical devices to large industrial pipes used in power plants or petrochemical facilities. The flexibility to adjust for different materials, such as stainless steel, copper, nickel alloys, and titanium, ensures that tube inner diameter polishers are versatile enough to be used in a wide range of applications.
In addition to the polishing itself, tube inner diameter polishers can also be equipped with features that help improve efficiency and productivity. For instance, automated loading and unloading systems allow for continuous operation, reducing downtime and increasing throughput in high-volume production environments. The ability to precisely control parameters like abrasive type, pressure, speed, and polishing time ensures that the desired surface finish is consistently achieved across batches.
With advancements in technology, many tube inner diameter polishers are now equipped with digital controls and feedback systems, allowing operators to monitor and adjust the process in real-time. This level of automation and control not only improves the precision of the polishing process but also enhances quality assurance and ensures that all tubes are finished to the exact specifications required for the application.
In conclusion, tube inner diameter polishers are indispensable in many industries where tube surface quality directly impacts product performance, safety, and hygiene. They enable manufacturers to achieve the necessary standards for flow efficiency, corrosion resistance, and cleanliness, ensuring that tubes used in critical applications meet both functional and regulatory requirements. As industries continue to demand higher performance and stricter compliance with quality standards, tube inner diameter polishers will remain an essential part of the manufacturing process.
Round Bar Polishing Machine
A Round Bar Polishing Machine is a specialized piece of equipment used to polish and finish the surface of round bars, which are commonly used in various manufacturing processes. These machines are designed to remove surface imperfections such as scratches, rust, oxidation, burrs, and other defects that may affect the quality, appearance, and functionality of round bars. Polishing round bars improves their surface finish, making them smoother, shinier, and more durable, which is especially important in industries that require high-quality metal components.
The primary function of a round bar polishing machine is to provide a consistent and uniform finish across the entire surface of the round bar. These machines typically use abrasive materials, such as polishing belts, brushes, or buffing wheels, to perform the polishing process. The round bars are fed through the machine, and the abrasive material comes into contact with the surface of the bar to remove imperfections and produce the desired finish.
In a belt polishing machine, an abrasive belt is wrapped around a rotating drum, and the round bar is fed through the system while the abrasive belt polishes its surface. The speed of the belt, the pressure applied, and the grit of the abrasive material can be adjusted to achieve different levels of finish, ranging from a satin or matte finish to a mirror-like shine. Belt polishing machines are particularly suitable for high-volume production, as they offer efficient processing and consistent results.
A brush polishing machine uses rotating brushes made of wire, nylon, or other materials to polish the surface of the round bar. These brushes provide a gentler polishing action, making them ideal for achieving a satin or matte finish. Brush polishing machines are often used for cleaning, deburring, and polishing round bars with delicate or irregular surfaces. They are also effective for removing oxidation or rust from metal surfaces without causing damage.
For achieving a high-gloss or mirror-like finish, a buffing machine can be used. Buffing machines typically use soft buffing wheels combined with a polishing compound to smooth the surface of the round bar to a high shine. This is particularly useful in industries such as aerospace, automotive, and decorative metalwork, where the appearance of the metal components is a key factor in the final product.
Some round bar polishing machines are equipped with automation features, such as automatic feeding, positioning, and unloading systems, to increase productivity and reduce manual labor. These machines can handle bars of varying lengths and diameters, and adjustments can be made to accommodate different materials, such as stainless steel, aluminum, brass, and other metals.
The benefits of round bar polishing machines go beyond just improving the appearance of the bars. Polishing also enhances the durability of the bars by removing contaminants and creating a smoother surface that is less prone to corrosion and wear. The polished surface can also reduce friction in applications where the round bar will come into contact with other components, such as in machinery, piping systems, and automotive parts.
In addition to their functional advantages, round bar polishing machines also play a critical role in industries where aesthetic quality is important. Decorative metals, such as those used in furniture, architecture, and jewelry, often require a high level of finish that only a polishing machine can provide. The smooth, shiny surface achieved through polishing can make the round bar more attractive and suitable for use in visible applications.
In conclusion, a round bar polishing machine is an essential tool in manufacturing environments where metal bars need to be finished to specific standards of appearance and performance. These machines provide consistent, high-quality results, improve the durability and functionality of the bars, and can be customized to meet the needs of different industries. Whether used for polishing functional components or decorative pieces, round bar polishing machines ensure that the final product meets the desired specifications and quality standards.
Round bar polishing machines offer a wide range of advantages across different sectors, making them a key piece of equipment in the manufacturing process. One significant benefit is their ability to handle bars of various lengths and diameters, allowing for flexibility in production. These machines can be tailored to meet specific requirements for different industries, such as construction, automotive, aerospace, medical, and manufacturing. Whether producing parts for heavy machinery, consumer products, or specialized metal components, these machines are indispensable for ensuring a polished, professional finish.
The automated features in modern round bar polishing machines are another significant advantage, particularly in large-scale manufacturing environments. With automation, the polishing process becomes faster and more efficient, reducing the need for manual labor and minimizing human error. Automated loading and unloading systems streamline the entire process, ensuring a seamless operation that maximizes throughput. Operators can also fine-tune the machine’s settings to ensure the proper polishing time, speed, and pressure, resulting in a consistent finish for each batch.
The versatility of the machine is also evident in its adaptability to different metal types. Whether polishing stainless steel, copper, aluminum, or brass, the machine can accommodate the unique properties of each material. Different abrasives and polishing techniques are used to ensure the surface is treated appropriately without compromising the integrity of the metal. For example, stainless steel, known for its corrosion resistance, benefits from polishing to maintain its appearance and strength in high-stress environments, while aluminum and brass require gentler polishing techniques to preserve their delicate surfaces and prevent damage.
Surface finish consistency is critical in industries where precision and quality are paramount. Polishing helps eliminate inconsistencies in the material, such as rough patches, scale, or oxidation, that could impact the functionality of the component. In aerospace, medical, and automotive industries, where parts often need to perform under extreme conditions, a smooth, flawless surface finish is essential for the longevity, efficiency, and safety of the parts.
Beyond aesthetic benefits, round bar polishing can also improve the mechanical properties of the bars. For example, a smoother surface can reduce wear and friction in moving parts, leading to longer-lasting components. In hydraulic systems or piping systems, smooth round bars help fluids or gases flow more efficiently, minimizing energy loss due to friction and pressure drop. In applications like bearing surfaces or gears, the smoothness achieved by polishing reduces the potential for damage, enhancing the overall performance and reliability of the machinery.
Furthermore, round bar polishing machines contribute to environmental sustainability. By improving the durability and lifespan of components, the need for frequent replacements or repairs is reduced, leading to less waste and fewer materials being discarded. Polishing also makes it easier to clean and maintain metal surfaces, especially in sensitive industries where cleanliness is essential. For instance, polished round bars used in food production systems or pharmaceutical applications are easier to sanitize, reducing the risk of contamination.
Maintenance of these polishing machines is also straightforward, which helps prolong the life of the equipment and maintain consistent output quality. Regular upkeep, such as replacing abrasive belts or brushes, ensures that the machine continues to perform efficiently. Some machines come with self-diagnostic systems that alert operators to potential issues, reducing downtime and the need for extensive maintenance.
In terms of customization, manufacturers can choose from a variety of polishing machine configurations to meet their specific needs. Some machines are designed for manual operation, giving operators full control over the polishing process, while others are fully automated to handle large quantities of parts with minimal intervention. Additionally, machines can be customized to provide different types of finishes, from matte and satin finishes to high-gloss mirror finishes, depending on the end-use of the product.
In conclusion, round bar polishing machines are an essential tool for ensuring the quality, functionality, and aesthetics of round bars used in various industries. Whether it’s for improving the surface quality, extending the lifespan of the parts, or enhancing their performance in specific applications, these machines provide an efficient and effective solution. As industries continue to evolve and demand higher precision, round bar polishing machines will remain integral to maintaining high standards of quality and performance across manufacturing processes. Their ability to handle various materials, sizes, and finishes makes them a versatile and invaluable asset to modern manufacturing operations.
Sheet Metal Polishing Machine
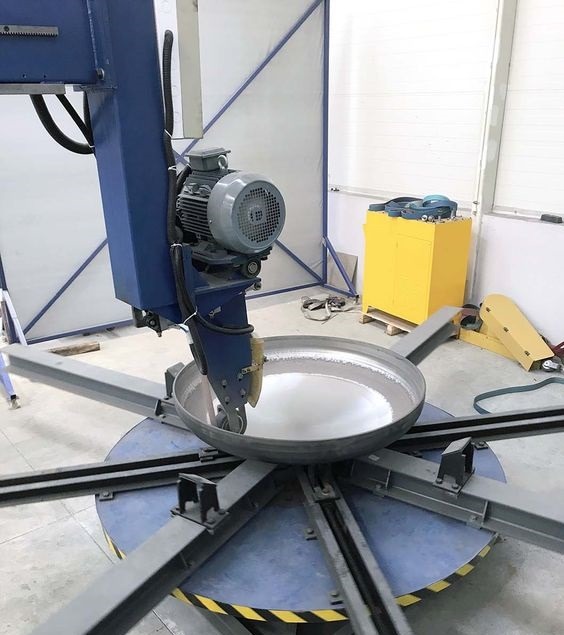
A Sheet Metal Polishing Machine is a specialized piece of equipment used to polish flat metal sheets, removing surface imperfections, improving surface finish, and enhancing the aesthetic appearance of the metal. These machines are designed to process sheet metal, which is often used in industries such as automotive, aerospace, construction, appliance manufacturing, and decorative metal products. The polishing process improves the sheet’s appearance, removes oxidation, rust, scratches, and other surface imperfections, and can also enhance the metal’s durability and corrosion resistance.
Sheet metal polishing machines typically use a variety of polishing methods, such as abrasive belts, brushes, or buffing wheels, to achieve the desired finish on the metal surface. These machines are often capable of handling large sheets of metal, which can vary in size, thickness, and material, including stainless steel, aluminum, brass, copper, and carbon steel.
One common type of sheet metal polishing machine is the abrasive belt polisher, which uses rotating abrasive belts to polish the surface of the sheet metal. The sheet is either fed into the machine or manually placed on the work surface, and the abrasive belt moves across the metal, grinding away any surface defects. The grit of the abrasive belt can be adjusted to achieve different finishes, from a rough finish to a high-gloss mirror-like shine. These machines are highly effective for removing rust, oxidation, scale, or scratches on metal sheets and can achieve a uniform finish across large surfaces.
Another type of sheet metal polisher uses brushes to perform the polishing. These brushes are typically made of wire, nylon, or other flexible materials and rotate across the metal surface. Brush polishing is particularly useful for achieving a satin or matte finish. It’s gentler than abrasive belt polishing, making it suitable for delicate metals or surfaces that need a softer finish. Brush polishers are also effective for deburring and removing any leftover residue after cutting or machining processes.
For achieving a high-gloss or mirror-like finish, buffing machines are commonly used. Buffing machines employ soft, rotating buffing wheels along with polishing compounds to create a smooth and shiny surface on the sheet metal. The polishing compound, often made of wax or abrasive materials, is applied to the buffing wheel, which then polishes the metal sheet to a glossy, mirror-like finish. This is ideal for industries where appearance is important, such as in decorative metal applications, furniture manufacturing, and consumer goods.
Modern sheet metal polishing machines are often equipped with automated systems to improve productivity and precision. Features such as automated feeding and unloading systems allow for continuous processing, making these machines highly efficient in mass production settings. The operator can adjust settings such as polishing pressure, speed, and abrasive grit to achieve the specific desired finish. Some advanced systems also incorporate digital controls and feedback mechanisms that allow operators to monitor and adjust the polishing process in real-time, ensuring consistent quality.
The benefits of using a sheet metal polishing machine are multifaceted. Firstly, polishing improves the appearance of the sheet metal, giving it a clean, shiny surface that is visually appealing. This is particularly important in industries where the aesthetics of the metal components are crucial, such as in architectural finishes, automotive trim, and appliances. Secondly, polishing enhances the corrosion resistance of the metal. By removing surface contaminants like rust or oxidation, polishing creates a smoother surface that is less likely to corrode over time, extending the lifespan of the metal.
Additionally, sheet metal polishing improves the mechanical properties of the metal. A smoother surface can reduce friction in applications where the metal will come into contact with other materials, leading to lower wear and tear on both the metal sheet and other components. This can be particularly beneficial in piping systems, machinery parts, and conveyor belts, where metal sheets or components experience constant movement or contact with other materials.
Another significant advantage of sheet metal polishing is that it can enhance hygiene in industries that require clean surfaces, such as food processing and pharmaceutical industries. Polished metal surfaces are easier to clean and sanitize, reducing the risk of contamination and ensuring compliance with health regulations.
In conclusion, a sheet metal polishing machine is a versatile and valuable tool for enhancing the quality, durability, and appearance of sheet metal in various industries. Whether used for improving the surface finish, providing corrosion resistance, or achieving a high-gloss finish for aesthetic purposes, these machines ensure that metal components meet both functional and aesthetic requirements. With the added benefits of automation, precision, and adaptability, sheet metal polishing machines play a crucial role in modern manufacturing, enabling the production of high-quality, finished metal products that meet the needs of diverse industries.
Sheet metal polishing machines continue to evolve with the advancement of technology and manufacturing processes. The introduction of automated systems, digital controls, and advanced abrasives has significantly improved the efficiency, consistency, and quality of the polishing process. Here are some additional considerations and trends in sheet metal polishing:
Automation and Efficiency
In modern manufacturing, automation is a key factor driving the adoption of sheet metal polishing machines. Automated systems allow for continuous operation without the need for constant manual intervention. This leads to higher productivity, particularly in high-volume production environments. Automated feeding systems ensure that sheets are consistently and accurately positioned in the machine, reducing setup time and human error. This is particularly beneficial in industries such as automotive manufacturing, where large quantities of metal sheets need to be polished with consistent results.
In some cases, sheet metal polishing machines can be integrated into fully automated production lines, where polishing is just one step in a series of processes, such as cutting, shaping, and assembling. The ability to seamlessly integrate polishing into the production flow helps reduce bottlenecks and allows for just-in-time production, which improves overall efficiency.
Digital Controls and Precision
As with many modern industrial machines, sheet metal polishing machines are increasingly being equipped with digital control systems. These systems allow operators to monitor and adjust parameters such as polishing speed, abrasive grit, pressure, and temperature in real-time. The integration of feedback mechanisms ensures that the machine constantly adapts to the workpiece, making adjustments for any variances in thickness or surface quality.
With the added precision of digital controls, manufacturers can achieve more consistent finishes across large batches of parts. This level of control is especially important in industries where product quality and consistency are critical, such as medical equipment manufacturing and electronics.
Advanced Abrasive Materials
The types of abrasives used in sheet metal polishing machines have evolved as well. Traditional abrasives, such as sandpaper and grinding wheels, have been supplemented with newer materials like diamond-coated abrasives, ceramic abrasives, and non-woven abrasives. These advanced abrasives offer improved cutting power, longer lifespan, and better surface finishes, especially on harder metals like stainless steel and titanium.
In addition, the use of polishing compounds and pastelike agents in buffing and brush polishing processes has become more refined. These compounds are specifically formulated to work with different metals and achieve varying levels of gloss and smoothness. For example, compounds with aluminum oxide or silicon carbide can be used for more aggressive polishing, while talc-based or wax-based compounds are ideal for creating a high-gloss finish.
Surface Finish Customization
With the increased demand for aesthetic appeal and functional performance, the ability to customize the surface finish of sheet metal has become more important than ever. Sheet metal polishing machines can now achieve a variety of finishes that meet specific customer needs. For example:
- Matte Finish: A softer, non-reflective surface, typically achieved using brush polishing or fine abrasive belts. This finish is often used in architectural or industrial applications where glare is not desirable.
- Satin Finish: A smooth, slightly reflective surface with a subtle sheen, which is ideal for automotive, appliance, and decorative products.
- High-Gloss / Mirror Finish: A highly reflective surface achieved through buffing or fine abrasive polishing. This finish is popular in decorative metal products, such as furniture, handrails, and luxury automotive parts.
As industries require more specialized finishes, sheet metal polishing machines are becoming more versatile, allowing manufacturers to offer a wide range of textures and appearances, depending on customer requirements.
Environmental Considerations and Sustainability
As industries continue to focus on sustainability and reducing environmental impact, modern sheet metal polishing machines are being designed with energy efficiency and environmental safety in mind. These machines are often equipped with systems that minimize abrasive waste, reduce energy consumption, and incorporate filtration systems to capture metal dust and particles created during the polishing process. This helps improve air quality in the factory and ensures compliance with health and safety regulations.
In addition, the use of eco-friendly polishing compounds that are non-toxic and biodegradable is becoming more common. Manufacturers are also exploring ways to recycle or repurpose abrasives to minimize the environmental footprint of the polishing process.
Maintenance and Longevity
Routine maintenance of sheet metal polishing machines is essential to ensure optimal performance and long service life. Regular maintenance practices include replacing abrasive belts or brushes, lubricating moving parts, and cleaning the machine to prevent the buildup of metal dust and debris. Machines equipped with self-diagnostic features can notify operators of potential maintenance needs, helping to prevent downtime and ensuring continuous production.
Some advanced polishing machines are also designed with easy access for maintenance and quick replacement of parts, allowing for minimal disruption to production. The use of high-quality components in these machines also contributes to their reliability and longevity, ensuring that they continue to deliver consistent results over time.
Industry-Specific Applications
Different industries require unique polishing solutions based on their specific needs. Some notable applications include:
- Automotive Industry: In automotive manufacturing, sheet metal polishing is crucial for producing parts like bumpers, grilles, exterior trim, and body panels with smooth, reflective finishes. These parts not only need to look good but also require resistance to corrosion and wear.
- Aerospace: Aircraft parts made from sheet metal, including aircraft panels and exterior components, require polished finishes to meet aerodynamic and aesthetic standards. The polishing process also enhances the durability and resistance to environmental stressors.
- Food and Beverage: Metal surfaces used in food processing or packaging need to be polished for hygiene and corrosion resistance. The smooth surface of the metal makes it easier to clean and sterilize, reducing the risk of contamination.
- Medical Equipment: Medical components, such as surgical instruments and medical housings, require a high level of surface finish to ensure sterility, durability, and smoothness, which are all crucial for patient safety.
Conclusion
Sheet metal polishing machines are essential tools in modern manufacturing, offering versatility and precision for creating high-quality metal products. From improving the aesthetic appeal of metal parts to enhancing their durability and performance, these machines are integral to industries that require smooth, shiny, and corrosion-resistant metal surfaces. With advancements in automation, digital controls, abrasive technology, and environmental considerations, sheet metal polishing machines are continuously evolving to meet the growing demands of the global market. As industries strive for greater efficiency, sustainability, and customization, these machines will remain a key component in the production of high-quality, finished metal products.
Wire Polishing Machine
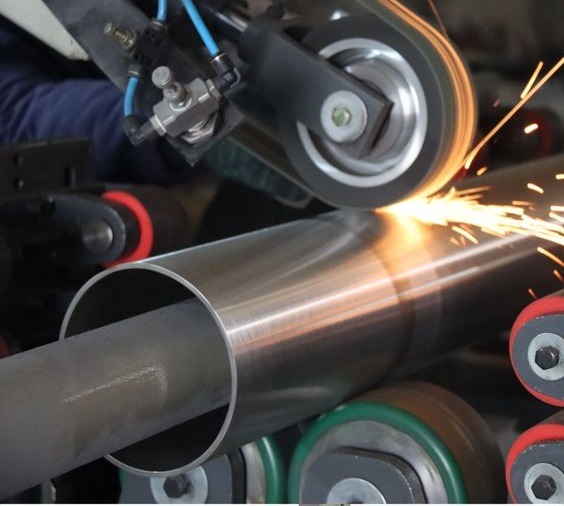
A Wire Polishing Machine is a specialized piece of equipment designed to polish wire material, removing surface imperfections, oxidation, rust, and other contaminants. These machines are widely used in industries where wire is a critical component, such as electronics, automotive, construction, furniture manufacturing, medical devices, and aerospace. The polishing process improves the surface finish, enhances the wire’s appearance, and can also contribute to its durability and corrosion resistance.
Wire polishing is particularly important for ensuring the wire is free of defects that could affect its performance or aesthetic quality. The process can be used to achieve a smooth, shiny, or matte surface finish, depending on the requirements of the application. Polishing wire is essential for strength, conductivity, corrosion resistance, and aesthetic appeal, especially in industries like jewelry making, medical wire manufacturing, and wiring for electronic components.
Types of Wire Polishing Machines
Wire polishing machines come in different configurations depending on the material, diameter, and the desired finish. Some of the common types of wire polishing machines include:
- Belt Polishing Machines:
- These machines use an abrasive polishing belt to smooth and shine the wire. The wire is fed through the machine, where it comes into contact with the rotating belt. The abrasive belt, which can be made of materials such as ceramic, silicon carbide, or aluminum oxide, polishes the surface of the wire, removing imperfections and achieving the desired finish.
- Belt polishing machines are versatile and can be used for different wire materials, including stainless steel, copper, aluminum, and brass.
- Brush Polishing Machines:
- These machines use brushes (made of wire, nylon, or other materials) that rotate against the wire’s surface. The rotating brushes clean, deburr, and polish the wire without being too aggressive, making them ideal for softer finishes like satin or matte. Brush polishing is also excellent for removing oxidation, corrosion, and fine debris from the wire’s surface.
- Brush polishers are often used for wires with a thinner diameter or those requiring a gentler polishing process.
- Buffing Machines:
- For achieving a mirror-like high-gloss finish, buffing machines are typically used. These machines use soft buffing wheels and polishing compounds to smooth the wire’s surface, resulting in a shiny, reflective finish. The polishing compound, typically a wax-based or abrasive paste, is applied to the buffing wheels, which then polish the wire.
- Buffing machines are especially useful in jewelry manufacturing and fine wire applications where appearance is critical.
- Centrifugal Polishing Machines:
- Centrifugal wire polishing machines use a rotating drum or centrifugal force to polish multiple wires at once. In these machines, the wires are placed in a rotating barrel along with polishing media and compounds. The centrifugal force causes the wires to move and rub against the polishing media, which results in polishing the surface.
- This type of machine is highly efficient for large quantities of wire and is commonly used in mass production settings.
Polishing Process and Parameters
The wire polishing process typically involves several stages:
- Preparation:
- Before polishing, the wire is usually cleaned to remove any dirt, oil, or other contaminants. This can be done using cleaning machines, ultrasonic cleaning, or chemical solutions.
- Polishing:
- The wire is fed into the polishing machine, where it undergoes the polishing action. The key parameters during polishing include:
- Abrasive Type: The choice of abrasive material (e.g., belt, brush, buffing compound) plays a significant role in determining the final surface finish.
- Pressure: The amount of pressure applied during the polishing process affects the aggressiveness of the polishing action.
- Speed: The rotation speed of the polishing component (brush, belt, or wheel) is adjusted depending on the material and the desired finish.
- Polishing Time: The amount of time the wire is exposed to the polishing surface determines the level of finish achieved.
- The wire is fed into the polishing machine, where it undergoes the polishing action. The key parameters during polishing include:
- Finishing:
- After the initial polishing, the wire may go through a final finishing stage where finer abrasives or compounds are used to give the wire an even smoother surface. This step helps achieve a higher gloss and a more uniform finish.
Benefits of Wire Polishing Machines
- Improved Aesthetic Appeal:
- Polishing improves the appearance of the wire by creating a smooth, shiny surface. This is particularly important in industries where the wire is used in decorative applications, such as jewelry, furniture, and architectural designs.
- Enhanced Durability:
- Polishing helps remove surface defects such as rust, oxidation, and scale that could compromise the wire’s strength or resistance to corrosion. This is especially important for wires used in aerospace, automotive, and marine applications, where durability is a critical factor.
- Corrosion Resistance:
- A polished wire surface is more resistant to corrosion because polishing removes oxidation and other contaminants. This is crucial for wires used in outdoor or harsh environments, such as marine wires and electrical cables.
- Increased Conductivity:
- For wires used in electronics, telecommunications, or power distribution, a polished surface ensures better electrical conductivity. A smooth surface reduces the likelihood of current loss or resistance, making the wire more efficient for electrical applications.
- Deburring and Cleaning:
- Polishing also serves the purpose of deburring (removing sharp edges or burrs left over from cutting or manufacturing) and cleaning the wire. This is critical for wires used in medical devices or surgical instruments, where smooth edges are necessary to prevent injury or to ensure proper functioning.
Industries That Benefit from Wire Polishing
- Jewelry Manufacturing:
- Polished wire is commonly used in jewelry making, where a shiny, smooth surface is essential for creating high-quality pieces. Wire used for making rings, necklaces, bracelets, and earrings requires polishing to achieve the desired finish.
- Electronics:
- In the electronics industry, wires need to be polished to ensure they have a high-quality finish for electrical conductivity. Polished wire is used in circuit boards, connectors, and cables for both performance and appearance.
- Aerospace:
- Wires used in aerospace components need to be polished to enhance both the aesthetic and functional properties of the wire. Polished wire is used in aircraft wiring, sensors, and electrical systems.
- Automotive:
- Automotive industries require wire polishing for components such as wiring harnesses, brake lines, and electrical wiring. Polishing ensures durability, corrosion resistance, and a smooth surface finish that can withstand harsh conditions.
- Medical Devices:
- Wires used in medical devices such as surgical instruments, stents, and needles must be polished for safety and smooth operation. The polished surface ensures the wires do not cause damage during use.
Conclusion
Wire polishing machines are essential tools in industries where wire quality is critical. By providing an efficient and effective method for improving the surface finish, corrosion resistance, and appearance of wire, these machines contribute to the overall performance and durability of wire products. Whether used in electronics, aerospace, jewelry, or medical applications, wire polishing machines ensure that the wire meets the required standards for functionality and aesthetics, making them a crucial part of modern manufacturing.
Wire polishing machines play a vital role in the production of high-quality wire products, enhancing their surface finish, appearance, and performance. These machines are engineered to handle various types of wire materials, such as stainless steel, copper, brass, and aluminum, to create smooth, polished surfaces that meet industry standards. They are particularly important in industries where the wire is subjected to stringent aesthetic, functional, and durability requirements.
The wire polishing process typically begins with cleaning the wire to remove any oils, dirt, or contaminants. Once cleaned, the wire is fed through the polishing machine, which uses different polishing techniques like abrasive belts, rotating brushes, or buffing wheels to achieve the desired finish. Abrasive polishing belts are often used for more aggressive cleaning and surface smoothing, whereas brush polishing is gentler and used for softer finishes. For a high-gloss, mirror-like finish, buffing machines with soft wheels and polishing compounds are utilized.
One of the key advantages of wire polishing machines is their ability to provide a consistent, uniform finish across large volumes of wire. This is especially useful in mass production environments, such as the manufacturing of wire for electrical cables, automotive wiring, and medical devices, where precision and consistency are critical. These machines also play an essential role in removing surface imperfections like oxidation, burrs, rust, or scaling, which can negatively affect the wire’s strength, conductivity, or aesthetic appeal.
Polished wire is in high demand in industries like jewelry manufacturing, where it is used to create delicate designs, such as rings, necklaces, and bracelets, all requiring smooth and shiny surfaces. The same polishing techniques are applied in the electronics industry to improve the conductivity of wires used in circuit boards and connectors. Additionally, in aerospace and automotive applications, polished wires are crucial for ensuring reliability and resistance to harsh environmental conditions, contributing to the longevity of electrical systems and components.
Beyond aesthetics, wire polishing also enhances the corrosion resistance of metal wires. By removing oxidation and other corrosive elements, the polished surface is less likely to degrade over time, extending the wire’s life, especially in marine or outdoor environments. The smooth surface also reduces friction and wear, which is important in applications where wires are exposed to mechanical stress.
In terms of automation, wire polishing machines have seen significant advancements. Modern machines can be integrated into automated production lines, allowing for continuous, high-volume polishing with minimal human intervention. These systems are often equipped with digital controls, enabling precise adjustments to parameters like polishing pressure, speed, and time, ensuring high-quality results with minimal operator involvement. This is particularly beneficial in large-scale manufacturing, where time efficiency and consistent quality are paramount.
Wire polishing machines also contribute to environmental sustainability by incorporating features like dust and debris collection systems, ensuring a cleaner working environment and reducing the release of harmful particles into the air. Additionally, the use of more eco-friendly polishing compounds and abrasives helps minimize the environmental impact of the polishing process.
Overall, wire polishing machines are an essential tool for ensuring that wire products meet the highest standards of quality, performance, and durability. Whether in the medical field, electronics, aerospace, or jewelry making, these machines provide the necessary polishing and finishing to make wire suitable for its intended application, offering benefits like improved conductivity, corrosion resistance, and aesthetic appeal. With continued technological advancements, these machines are becoming more efficient, versatile, and environmentally friendly, ensuring they remain crucial to the wire production industry.
Plate Polishing Machine
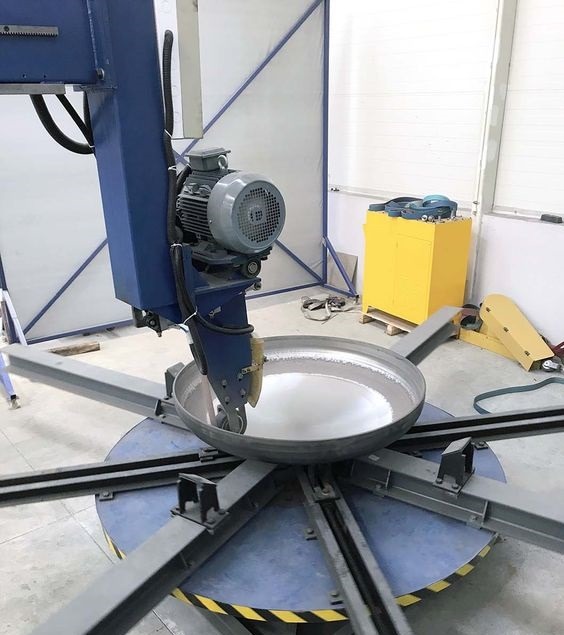
A Plate Polishing Machine is a specialized tool used to smooth, finish, and enhance the surface of metal plates, ensuring they meet specific aesthetic, functional, or technical requirements. These machines are employed in industries where metal plates are used for high-precision applications, such as in aerospace, automotive, construction, electronics, furniture, and medical sectors. The purpose of plate polishing is to improve the surface finish of metal plates by removing imperfections, oxidation, and other surface contaminants, and to provide the desired level of smoothness, gloss, or matte finish.
Plate polishing machines work by using different techniques that employ abrasive materials like polishing belts, brushes, or buffing wheels, along with polishing compounds or pastes. The key benefits of using a plate polishing machine include an enhanced surface appearance, better resistance to corrosion, improved wear resistance, and the ability to meet specific surface finish standards required by the industry.
The process begins with the preparation of the plate, which may involve cleaning to remove oil, dirt, or rust. Once cleaned, the plate is fed into the machine, where it comes into contact with the polishing element. Depending on the type of machine and the required finish, the plate is either manually or automatically guided through the polishing process.
There are several types of plate polishing machines, each suitable for specific tasks and materials. For example, belt polishing machines are often used for their versatility, employing an abrasive belt to polish a variety of metal plates, from soft materials like aluminum to harder metals such as stainless steel. These machines are designed to handle large plates or continuous sheets of metal and are effective in achieving smooth, uniform finishes.
Another type is the brush polishing machine, which utilizes rotating brushes to clean and polish the plate. This method is especially useful for achieving a satin or matte finish, removing lighter contaminants, and for use with delicate materials that require a gentler touch. The buffing machine is another option, providing high-gloss finishes through soft buffing wheels coated with polishing compounds.
Polishing plates with a centrifugal polishing machine can also be done, where the plates are subjected to centrifugal force in a rotating drum along with abrasive media. This is a high-efficiency process for mass production of metal plates that requires consistent finishes across large volumes of material.
In industries like aerospace, polished metal plates are critical for parts that require both an aesthetic finish and excellent durability. The polished surface reduces the risk of corrosion and improves the material’s performance under high-stress conditions. Similarly, in the automotive industry, polished plates are used for exterior and interior parts, as well as for components where smooth finishes are critical for functionality, such as engine components or transmission plates.
Moreover, plate polishing is often required for decorative metal plates used in architecture, furniture, and consumer goods. Polished metal plates offer a premium look and feel, with applications in architectural facades, wall panels, countertops, and appliances.
The quality of the polish can range from a matte finish, which provides a non-reflective, smooth surface, to a high-gloss finish, which results in a shiny, mirror-like surface. The choice of finish depends on the specific needs of the application, and the polishing machine allows for precise control over the final result.
In addition to aesthetic improvements, plate polishing machines can enhance the functional properties of metal plates. For instance, polishing can improve the corrosion resistance of metal surfaces by removing surface oxidation and contaminants. It also reduces the roughness of the plate, which can improve its wear resistance and extend its lifespan, particularly in industrial machinery and automotive parts.
In conclusion, plate polishing machines are essential tools in modern manufacturing and finishing processes, offering various techniques to improve the appearance and functionality of metal plates. They provide benefits like increased durability, improved corrosion resistance, and a superior surface finish, making them indispensable in many industries. As these machines continue to evolve, they are becoming more automated, energy-efficient, and capable of producing high-quality finishes across a variety of metal types and applications.
Plate polishing machines are crucial for industries that require high-quality, precise finishes on metal plates. These machines utilize various polishing methods to achieve different surface finishes, ranging from matte to high-gloss. The key goal is to improve the surface aesthetics, functionality, and durability of the metal plates, making them suitable for a wide range of applications. Whether it’s to enhance the appearance of decorative metal or to meet the technical requirements of industrial components, plate polishing machines play a vital role in producing high-performance products.
The polishing process typically begins with cleaning the metal plate to remove oils, dirt, or any other contaminants. After cleaning, the plate is fed into the polishing machine, which uses abrasive materials such as polishing belts, brushes, or buffing wheels to smooth out imperfections, remove rust, oxidation, or other surface defects, and achieve the desired finish. The choice of polishing technique and the materials used depend on the specific application, the type of metal, and the desired outcome.
Belt polishing machines are often favored for their versatility and are used to polish a wide variety of metal plates. The abrasive belts work by smoothing the surface while removing material, making them ideal for finishing large, flat surfaces of metal plates. For a gentler finish or to achieve a satin look, brush polishing machines can be used. These machines use rotating brushes to polish the surface of the plate without being as aggressive as belt polishers, making them suitable for more delicate tasks or specific finishing requirements. Buffing machines, on the other hand, are perfect for achieving a high-gloss, mirror-like finish. They use soft wheels coated with polishing compounds to refine the surface and bring out a shiny, reflective surface.
In more industrial settings, centrifugal polishing machines can handle large volumes of plates and are ideal for mass production. These machines use centrifugal force to apply abrasives to the metal plate, ensuring uniformity in the finish. This type of polishing is efficient and effective, especially when polishing large batches of parts or when a consistent finish is required across a variety of plates.
The benefits of using plate polishing machines extend beyond aesthetic improvements. Polishing removes surface oxidation and contaminants, which can enhance the corrosion resistance of metal plates. This is particularly important in industries like aerospace, automotive, and marine, where metal parts are exposed to harsh conditions and need to withstand wear and corrosion. By polishing the surface of the metal, the plates are not only made to look better but are also protected against potential environmental damage.
In industries like automotive and aerospace, polished metal plates are often used in high-stress applications, where the smooth surface helps reduce friction, wear, and the potential for mechanical failure. The polished finish can also enhance the metal’s strength and longevity, making it more reliable in applications where durability is critical.
Beyond functionality, polished metal plates are highly sought after in architectural and decorative applications. They are used in everything from building facades to countertops, furniture, and decorative metal elements in both residential and commercial settings. The aesthetic quality of the polished surface adds a premium, sophisticated look to the product, which is highly valued in high-end designs.
In addition to their versatility in achieving different finishes, plate polishing machines also contribute to efficiency and productivity. Automation in polishing processes allows for large-scale production of metal plates with consistent results, minimizing human error and labor costs. These machines can be integrated into continuous production lines, reducing downtime and increasing throughput, making them ideal for high-volume manufacturing environments.
Plate polishing machines are also evolving to be more environmentally friendly. Many modern machines are designed with features that reduce the environmental impact, such as dust collection systems that capture debris and eco-friendly polishing compounds that minimize harm to the environment. These advances ensure that the polishing process is not only efficient but also sustainable.
In conclusion, plate polishing machines are indispensable in industries where the appearance, performance, and durability of metal plates are crucial. By providing precise control over the polishing process, these machines help ensure that metal plates meet the required specifications, whether for decorative or industrial applications. They offer benefits such as enhanced surface finishes, improved corrosion resistance, and longer product life, making them essential for producing high-quality metal products in a variety of industries. With continuous advancements in technology, these machines are becoming more efficient, versatile, and environmentally conscious, further solidifying their importance in modern manufacturing.
Edge Polishing Machine
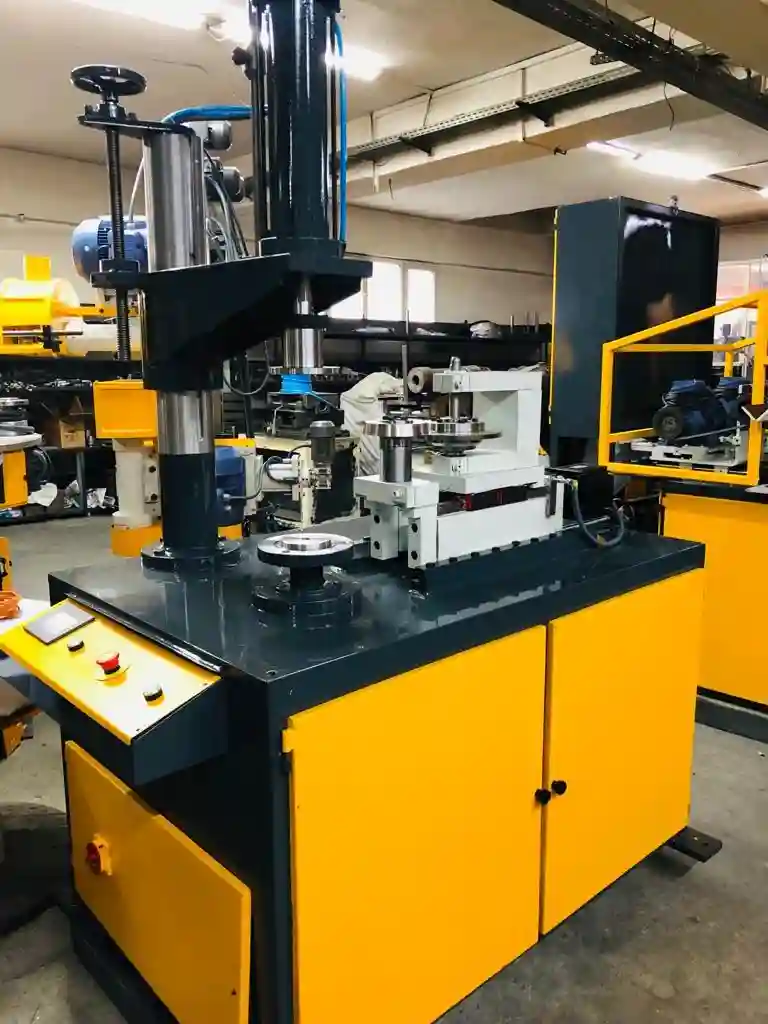
An Edge Polishing Machine is designed to polish the edges of various materials, particularly metal, glass, stone, and wood, to smooth or round off their sharp edges. This machine is commonly used in industries that require precision finishing for materials with sharp, unfinished edges that need to be smoothed for both aesthetic and functional purposes. These machines are especially important in industries like furniture manufacturing, construction, glass processing, metalworking, automotive, and electronics, where edge finishes can significantly impact the product’s appearance, safety, and overall quality.
The edge polishing process typically involves feeding the material through a machine that uses abrasive belts, wheels, or brushes to remove rough edges, burrs, and sharp points. The result is a smooth, rounded, or polished edge that improves the material’s safety, usability, and overall look. The level of polish can vary from a matte or satin finish to a high-gloss shine, depending on the material and the desired outcome.
Edge polishing machines come in several configurations depending on the application. Belt edge polishers use abrasive belts to smooth and round edges, making them suitable for a wide range of materials, including metal plates, wooden panels, and plastics. Brush edge polishers, on the other hand, utilize rotating brushes to gently polish the edges without the use of harsh abrasives. These machines are ideal for more delicate materials like glass or ceramics, where a softer touch is required to avoid damage.
For more precise edge finishing, disc polishers and buffing machines can be used. These machines work with rotating discs or wheels that apply polishing compounds to create a high-gloss finish. Disc edge polishing machines are commonly employed in glass manufacturing, where perfectly smooth, polished edges are crucial for both aesthetic and functional reasons, such as in window panes, mirror glass, and furniture pieces.
Edge polishing machines are also available in CNC (Computer Numerical Control) versions, which offer high precision and are capable of automated, consistent edge finishing across a large number of items. These machines allow manufacturers to program specific edge profiles, ensuring uniformity in products and reducing the potential for human error.
The key benefits of using an edge polishing machine include improving safety by eliminating sharp or hazardous edges that could cause injuries, especially in products like metal sheets, glass windows, and furniture. Additionally, polished edges can improve the overall appearance of the product, providing a high-quality finish that is more visually appealing. This is particularly important in industries like furniture, automotive, and construction, where attention to detail can impact the product’s marketability and consumer perception.
In industries such as automotive or aerospace, edge polishing is crucial for ensuring that components such as metal plates, panels, and interior parts meet safety and performance standards. Polished edges on metal parts can also reduce the risk of corrosion and wear, especially in areas where parts are in constant motion or exposed to harsh conditions.
Overall, edge polishing machines are integral in providing high-quality finishes to a range of materials. They help ensure that products meet both aesthetic and safety standards while improving the functionality and durability of the materials they process. Whether through abrasive polishing, brush polishing, or buffing, these machines allow manufacturers to achieve the desired edge quality, making them an essential tool in modern manufacturing and finishing processes.
Edge polishing machines are essential tools in various manufacturing processes, offering a reliable way to smooth, round, and polish the edges of materials like metal, glass, wood, and stone. These machines ensure that products meet both aesthetic and functional standards by eliminating sharp or rough edges that could cause damage, injury, or aesthetic imperfections. The process typically involves using abrasive materials like belts, wheels, or brushes that gently or aggressively polish the material’s edges to achieve a smooth, rounded, or glossy finish.
For example, metal sheets and metallic parts used in industries like automotive, construction, and electronics benefit from edge polishing as it helps reduce the risk of corrosion and improves the overall appearance of the component. In these industries, sharp edges could pose safety risks, especially in parts that are handled frequently or exposed to harsh environments. Polishing also contributes to extending the lifespan of components by removing imperfections that might accelerate wear and tear. Similarly, glass products such as windows, mirrors, or decorative panels require precise edge polishing to eliminate sharp corners, enhancing both the safety and aesthetic quality of the product.
One of the main advantages of edge polishing is the ability to achieve a consistent and uniform finish across large batches of materials. This is especially beneficial in mass production environments, where maintaining the same quality throughout the production process is critical. The use of automated machines, like CNC edge polishers, has streamlined this process by allowing for precise, repeatable finishes without relying on manual labor, which can be time-consuming and prone to error. These automated systems offer flexibility, enabling manufacturers to program different edge profiles and adjust parameters like speed and pressure to meet specific requirements.
Edge polishing machines are also adaptable to various materials, making them versatile tools in many sectors. Whether it’s the smooth, reflective edge of a stainless steel component or the softer, satin finish on a wooden panel, these machines can be customized to handle different types of materials and finishes. For example, abrasive belt polishers are often used for tougher materials like metal or plastic, while brush polishers are more suitable for delicate materials like glass or ceramics, ensuring that no damage occurs to the surface.
In addition to safety and aesthetic benefits, polished edges also contribute to improved functionality. For instance, in aerospace and automotive manufacturing, polished edges can reduce the friction between moving parts, improving performance and efficiency. Polishing also ensures that edges are free from burrs and sharp points, which could interfere with mechanical operations or damage other components. This is particularly critical in precision industries where every detail affects the product’s overall performance.
In sectors like furniture manufacturing, polished edges are crucial for producing high-end, attractive products. Whether it’s the smooth finish on a wooden table or the clean, rounded edges on metal furniture, the polishing process adds a level of refinement that enhances the product’s marketability. The use of buffing machines or disc polishers helps achieve high-gloss finishes, making the product look more luxurious and appealing to consumers.
Beyond aesthetic appeal, the polishing process can improve the durability of the material. Polishing can eliminate surface defects like oxidation or roughness, reducing the likelihood of future damage. This is particularly important for products exposed to the elements, such as outdoor furniture or architectural components. By providing a smoother surface, edge polishing can make materials less prone to corrosion, oxidation, or general wear, contributing to their longevity.
Overall, edge polishing machines are vital in modern manufacturing and finishing processes. They not only improve the safety and appearance of products but also enhance their functionality and durability. With the advancement of automated technologies and more efficient machinery, edge polishing has become faster, more consistent, and more environmentally friendly, ensuring high-quality results across a range of industries. Whether for decorative purposes, safety improvements, or performance enhancements, edge polishing machines continue to play a crucial role in producing high-quality materials and components.
Edge polishing machines have become indispensable in industries that require precise and consistent finishing of materials. These machines are particularly valuable in ensuring that the products not only look polished but also meet necessary safety and durability standards. The process helps to smooth rough edges, remove burrs, and eliminate sharp points that could cause injury or damage during handling. Additionally, polished edges contribute to a more refined appearance, making products look more professional and appealing to consumers.
The flexibility of edge polishing machines means they can be adapted to a variety of materials, from metals to plastics, glass, and wood. In the automotive industry, for example, edge polishing ensures that the edges of metal parts or components are smooth and free of imperfections that could affect their functionality or cause friction. This reduces the risk of wear and tear, which is essential for maintaining the performance and longevity of parts in high-stress environments. Similarly, metal parts used in the electronics and aerospace industries benefit from polished edges, which not only enhance the appearance but also improve the overall strength and durability of the components.
For glass products, such as windows, mirrors, or decorative panels, edge polishing is critical for both safety and aesthetic reasons. The smooth, polished edges eliminate sharp corners that could cause injury or harm, while also giving the glass a sleek, refined look. The same holds true for stone products used in construction, where polished edges are required to avoid injury and enhance the visual appeal of countertops, tiles, or building facades. The edge polishing process ensures that no rough surfaces remain, making the material more resistant to breakage and improving its overall resilience.
In industries like furniture manufacturing, edge polishing machines are used to achieve smooth, rounded edges on materials like wood, metal, or composite materials. These polished edges help to give furniture pieces a finished, high-quality look while ensuring they are safe to handle. Furniture pieces with well-polished edges also tend to be more durable, as the process helps to seal and protect the material from moisture or wear that could cause it to degrade over time.
One of the major benefits of using edge polishing machines is the ability to achieve a high level of precision. Modern machines, especially CNC-controlled edge polishers, offer exact control over the polishing process. This allows manufacturers to create specific edge profiles or finishes, whether it’s a simple rounded edge, a more intricate bevel, or a smooth, high-gloss shine. The automation of the polishing process ensures that products are polished uniformly and consistently, reducing the risk of human error and enhancing the overall quality of the final product.
Edge polishing machines also improve productivity in high-volume manufacturing settings. They can be integrated into automated production lines, allowing for continuous operation without the need for manual intervention. This not only increases output but also reduces the time and labor costs associated with traditional hand polishing methods. The use of automated systems also ensures that products are finished to a uniform standard, which is critical for industries where consistency is key.
As edge polishing technology continues to evolve, machines are becoming more energy-efficient and environmentally friendly. Newer machines are designed with features like dust extraction systems that capture debris and prevent contaminants from spreading into the work environment. Additionally, manufacturers are increasingly using eco-friendly polishing compounds and abrasives, which reduces the environmental impact of the polishing process. These advancements make edge polishing machines not only more efficient but also more sustainable.
In conclusion, edge polishing machines play a vital role in modern manufacturing, offering a range of benefits that enhance the safety, durability, appearance, and performance of products. Whether in the automotive, aerospace, glass, or furniture industries, these machines ensure that materials are polished to the highest standards, helping manufacturers meet both functional and aesthetic requirements. As technology continues to advance, edge polishing machines will only become more efficient, versatile, and environmentally conscious, making them even more essential in the production of high-quality materials and components.
3D Surface Robotic Polishing Machine
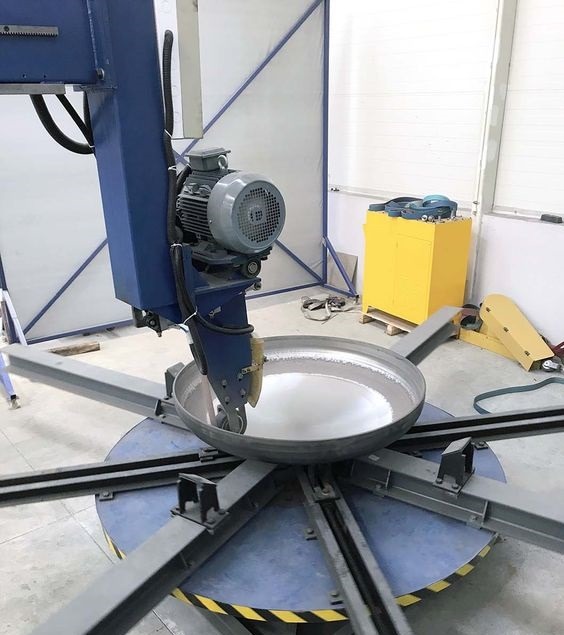
A 3D Surface Robotic Polishing Machine is an advanced, automated solution designed to polish complex, three-dimensional surfaces. This type of machine uses robotic arms equipped with polishing tools such as brushes, belts, or pads to finish surfaces with intricate contours, angles, and geometries that would be difficult or time-consuming to achieve with traditional polishing methods. These machines are often used in industries where products have complex shapes, such as aerospace, automotive, medical devices, and consumer electronics.
The key advantage of a 3D surface robotic polishing machine is its ability to provide consistent and precise polishing on surfaces that are not flat or uniform. For example, it can be used to polish the curved surfaces of a metal aircraft wing, the detailed contours of an automobile body part, or the complex geometries of medical implants. Unlike conventional methods that rely on manual labor or fixed machinery, robotic polishing machines can adapt to the surface geometry in real-time, adjusting the pressure, speed, and angle of the polishing tool to ensure an even, smooth finish.
Robotic polishing systems are equipped with advanced sensors, such as force feedback systems and vision systems, which help the robot “feel” the surface and make adjustments as needed. These sensors ensure that the polishing process is uniform, even on surfaces that may vary in shape or texture. The system can also be programmed to follow specific patterns or curves, making it ideal for applications that require precision and consistency.
The polishing robots are typically designed with multi-axis capabilities, allowing the robotic arm to move in multiple directions to reach all areas of a 3D surface. These systems can be equipped with a range of polishing tools, depending on the material and the desired finish. For example, abrasive belts or discs may be used for metal parts, while soft brushes or pads might be used for more delicate materials, like plastics or glass.
In addition to their ability to handle complex geometries, 3D robotic polishing machines offer several benefits over traditional methods. Automation increases productivity, as robots can operate continuously, reducing labor costs and improving throughput. The machines also reduce the risk of human error, ensuring that the finish is consistent across large batches of parts. The use of robotics also minimizes the need for manual intervention, making the process safer and more efficient.
Furthermore, precision is another key benefit of robotic polishing. The machines can consistently achieve very fine finishes, such as high-gloss surfaces or matte textures, depending on the requirements. In industries like aerospace and automotive, the ability to achieve a mirror-like polish on complex components is crucial for both aesthetic appeal and functionality. For example, polished metal surfaces in the aerospace industry not only look better but also have enhanced aerodynamic properties.
In the medical device industry, 3D surface polishing is essential for products like implants or surgical instruments, where surface smoothness is crucial for biocompatibility and ease of handling. Robotic polishing systems can precisely finish the surfaces of these components, ensuring they meet stringent regulatory standards and have the desired surface properties, such as smoothness or texture.
Another advantage of 3D robotic polishing is the ability to work with a wide range of materials, from metals and plastics to ceramics and composites. The versatility of robotic systems makes them suitable for a wide variety of industries and applications. The polishing process can also be customized to meet specific requirements, whether for removing scratches, adding gloss, or preparing surfaces for further processing like coating or painting.
The integration of AI and machine learning into robotic polishing systems is further enhancing their capabilities. These technologies enable the robots to learn from previous polishing tasks, improving efficiency and accuracy over time. The machine can analyze data from sensors and cameras to optimize the polishing process, reducing the need for manual adjustments and ensuring the highest possible quality.
In conclusion, 3D surface robotic polishing machines represent a significant advancement in automated finishing technology. They offer unparalleled precision, consistency, and flexibility, allowing manufacturers to polish complex 3D surfaces with ease. Whether used in aerospace, automotive, medical, or consumer electronics industries, these machines improve productivity, reduce labor costs, and enhance the quality of finished products. As robotic technology continues to evolve, the capabilities of these systems will only improve, offering even more sophisticated and efficient solutions for polishing a wide variety of materials.
3D surface robotic polishing machines have revolutionized the manufacturing and finishing processes, offering a level of precision and automation that was previously unattainable with traditional methods. The ability to polish complex three-dimensional surfaces with consistency and efficiency has made these machines essential in industries where intricate designs and fine finishes are crucial. The integration of robotic arms allows for greater flexibility in processing materials with unique shapes, curves, and contours. As a result, these machines are particularly useful for applications where products require both high aesthetic appeal and functional performance, such as in aerospace, automotive, medical device manufacturing, and consumer electronics.
One of the most important features of robotic polishing systems is their adaptability. Unlike fixed machines that may struggle with parts that have non-uniform or complex geometries, robotic polishing machines can adjust in real-time to the surface they are polishing. They use sensors and cameras to gather data, which is then processed to adjust the speed, angle, and pressure of the polishing tool. This ensures that the surface is polished evenly and uniformly, no matter how intricate the design. In industries like aerospace, where parts are often subjected to high stress and require precision in both form and function, the ability to achieve flawless, smooth finishes is critical for both performance and safety.
In automotive manufacturing, where sleek, smooth surfaces are a significant part of the visual appeal of vehicles, robotic polishing machines are used to achieve high-gloss, mirror-like finishes on metal and plastic parts. The ability to polish components such as engine covers, grilles, or bumpers without manual intervention allows for faster production rates and more consistent results, improving the overall quality of the final product. The same goes for consumer electronics, where polished surfaces not only improve aesthetics but also enhance the durability and ease of cleaning of products like smartphones, tablets, and laptop covers.
The medical industry benefits significantly from 3D robotic polishing machines, particularly in the production of implants, surgical instruments, and prosthetics. These devices require highly polished surfaces to ensure biocompatibility and to prevent the buildup of bacteria or other contaminants. Precision polishing is essential, as even the smallest imperfection can lead to issues with functionality or patient safety. Robotic polishing machines ensure that every part meets strict regulatory standards and delivers the desired surface finish, whether it’s for enhancing the overall functionality or preparing the surfaces for coating or other treatments.
Another major advantage is the reduction in human labor and the potential for human error. Traditionally, polishing complex parts required skilled labor and often involved lengthy manual processes. With robotic polishing systems, much of the manual labor can be automated, leading to faster turnaround times and greater consistency. This automation also frees up workers to focus on more complex or higher-value tasks while ensuring that the polishing process is standardized across all parts, which is particularly beneficial in mass production environments.
Moreover, robotic polishing machines allow for advanced material processing, making them versatile enough to handle a wide range of materials. Whether it’s metals, plastics, ceramics, composites, or even glass, these machines can be configured with the appropriate tools and abrasives to meet the specific needs of the material being polished. This makes them highly adaptable for use in diverse industries, from industrial manufacturing to electronics and biotechnology.
The integration of machine learning and artificial intelligence (AI) in robotic polishing machines is paving the way for even more sophisticated systems. These technologies allow the machines to continually optimize their polishing processes based on previous operations, improving efficiency, reducing waste, and ensuring high-quality finishes every time. AI algorithms can analyze sensor data to predict the best approach for each polishing task, taking into account factors such as the material’s properties, the desired surface finish, and the shape of the part. This helps to minimize errors, maximize the use of polishing materials, and ensure the most efficient use of energy.
Additionally, robotic polishing machines often come equipped with advanced features like dust collection systems, which help maintain a clean work environment by capturing excess polishing dust and debris. This not only improves the quality of the finished product by preventing contamination but also contributes to environmental sustainability by reducing waste and ensuring that the polishing materials are reused efficiently.
As the technology continues to evolve, the flexibility and performance of 3D surface robotic polishing machines will only improve. With increasing demand for high-quality finishes, especially in industries that require fine-tuned details and flawless surfaces, these machines are likely to become even more integral to the manufacturing process. The ongoing advancements in robotics, AI, and machine learning will push the boundaries of what’s possible, enabling manufacturers to polish increasingly complex shapes with greater efficiency and precision.
In conclusion, 3D surface robotic polishing machines are transforming how industries approach the polishing of intricate, three-dimensional surfaces. By automating the polishing process, improving consistency, and providing high-quality finishes on a variety of materials, these machines offer significant benefits in terms of productivity, safety, and product quality. As technology progresses, these machines will continue to play a crucial role in manufacturing, meeting the demands for precision and performance across a wide range of industries.
CNC Polishing Machine
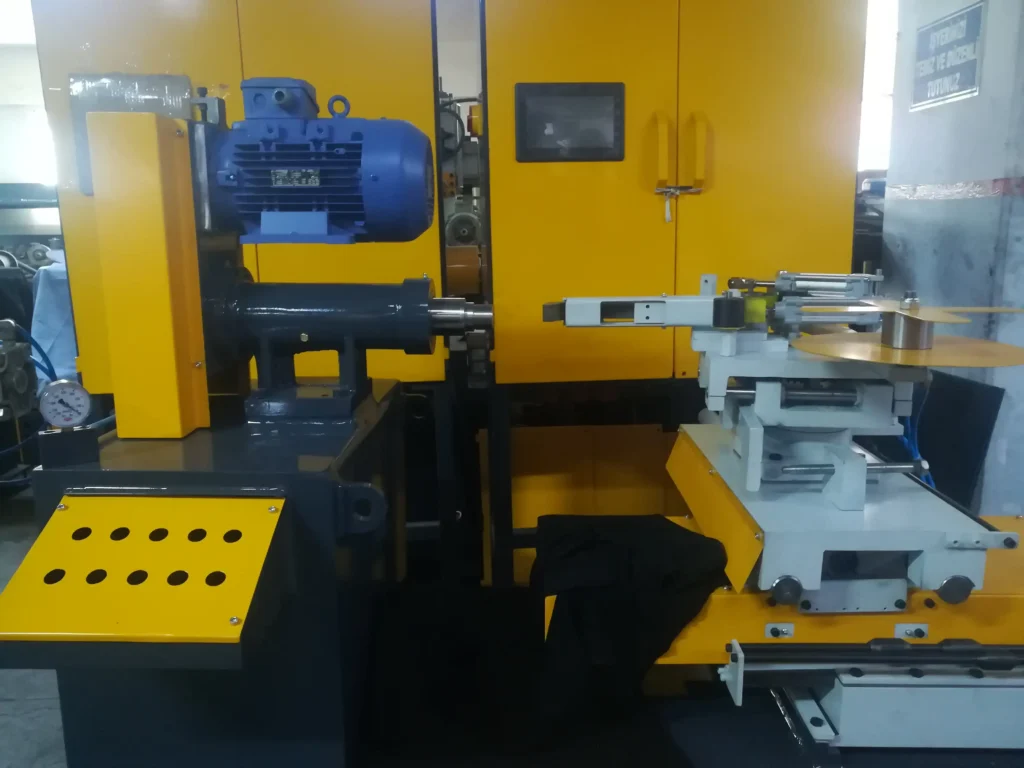
A CNC Polishing Machine is an advanced, automated system designed for high-precision polishing and finishing of materials using computer numerical control (CNC) technology. This type of machine allows for precise and repeatable polishing of a wide range of materials, such as metals, plastics, ceramics, and composites. CNC polishing machines are commonly used in industries that require high-quality finishes with tight tolerances, such as aerospace, automotive, electronics, medical device manufacturing, and jewelry making.
The main feature of a CNC polishing machine is its ability to automate the polishing process, using a computer-controlled system to guide the polishing tools and adjust parameters like speed, pressure, and motion. CNC systems can be programmed to polish complex surfaces, shapes, and geometries with high accuracy, ensuring a uniform and smooth finish across the entire workpiece. These machines are typically equipped with polishing heads, abrasive pads or brushes, and sophisticated software that allows operators to define polishing paths and adjust the process parameters to suit the material and desired finish.
CNC polishing machines are particularly useful when the surface finish needs to meet exacting standards. For instance, in aerospace and automotive industries, components such as turbine blades, engine parts, and gearboxes require smooth surfaces to reduce friction, enhance performance, and improve the lifespan of the components. CNC polishing ensures that these parts achieve the desired finish without any manual intervention, leading to more consistent and reliable results.
In the electronics industry, CNC polishing is essential for polishing semiconductor wafers, displays, and other delicate components. A smooth, precise finish is critical for ensuring the proper functionality and longevity of these parts. The machine’s high precision ensures that even the smallest imperfections are eliminated, which is especially important in the case of high-performance devices like smartphones, tablets, and computers.
One of the main advantages of a CNC polishing machine is its ability to perform high-precision polishing on intricate geometries. Unlike manual polishing, which is prone to human error and can be inconsistent, CNC machines follow precise, programmed paths and can repeat the same polishing process with exceptional accuracy. This is particularly beneficial for parts that have detailed contours, tight tolerances, or complex shapes, such as medical implants or surgical instruments. These parts require smooth, polished surfaces to ensure they are safe for use and meet regulatory standards.
CNC polishing machines also reduce the labor costs and time associated with traditional hand polishing. While manual polishing can be slow and requires a skilled technician, CNC systems can operate continuously, polishing multiple parts at once or running 24/7, depending on the production needs. This increased efficiency allows manufacturers to meet high production volumes while maintaining high standards of quality and consistency.
Another key advantage is the reducibility of human error. Since the process is automated, the likelihood of mistakes such as uneven polishing, over-polishing, or inconsistent pressure is minimized. This is especially important in industries where quality control is paramount. CNC machines can also be programmed to handle a variety of polishing operations, from rough polishing to fine finishing, all within the same system.
Moreover, CNC polishing machines can be integrated with other automation technologies, such as vision systems or force sensors, which enhance the machine’s ability to adjust in real-time based on the surface conditions of the workpiece. Vision systems can detect surface defects or imperfections, while force sensors ensure that the correct pressure is applied during the polishing process, preventing damage to sensitive materials.
The versatility of CNC polishing machines extends to the wide range of materials they can process. Whether it’s stainless steel, aluminum, brass, plastics, or glass, CNC polishing machines can be equipped with the appropriate tools and abrasives to handle each material type. This adaptability makes them an excellent choice for industries with diverse material requirements.
CNC polishing machines also contribute to environmental sustainability. By using closed-loop systems to capture and filter polishing debris, these machines reduce the environmental impact of the polishing process. In addition, abrasive materials and polishing compounds can be reused, reducing waste and minimizing the need for frequent material replacements.
As technology advances, CNC polishing machines continue to improve. New software algorithms, more powerful motors, and enhanced sensors allow these machines to deliver even finer finishes, faster cycle times, and increased flexibility. Some systems also offer remote monitoring and diagnostics, allowing manufacturers to track performance, troubleshoot issues, and optimize the polishing process for better efficiency and results.
In conclusion, CNC polishing machines are a critical tool in modern manufacturing. They offer precise, consistent, and high-quality polishing across a variety of industries. With the ability to automate the polishing process, reduce human error, and enhance efficiency, CNC machines are revolutionizing the way materials are finished, ensuring that parts meet stringent standards while improving production speed and reducing labor costs. As technology continues to evolve, CNC polishing machines will remain at the forefront of manufacturing, helping to meet the growing demands for high-performance, polished components in a range of industries.
The capabilities of CNC polishing machines continue to evolve with technological advancements, offering even greater flexibility and efficiency. One of the emerging trends is the integration of artificial intelligence (AI) and machine learning (ML) into CNC polishing systems. These technologies enable the machines to learn from previous polishing operations and adapt in real time. As the machine analyzes data from sensors and cameras, it can optimize its polishing paths, speeds, and pressure, continually improving the process and delivering an even better finish with each cycle.
In addition to AI and ML, CNC polishing machines are increasingly equipped with advanced automation features, such as robotic arms or multi-axis capabilities. This allows for more intricate polishing, especially on parts with complex geometries. These features enable the machine to polish not just flat surfaces, but also curved, angled, and even spherical surfaces, with the same level of precision and consistency. Multi-axis systems, for example, can adjust the tool’s orientation to match the geometry of the workpiece, ensuring that every angle of the surface is evenly polished.
Real-time monitoring and feedback systems have also become a significant part of modern CNC polishing machines. These systems allow operators to monitor the polishing process remotely and make adjustments as needed. Sensors can detect variables such as surface roughness or tool wear, and the system can automatically adjust parameters to compensate. This ensures that the polishing process continues smoothly, with minimal downtime or need for manual intervention.
CNC polishing machines are not only faster and more accurate than traditional methods but also much more cost-effective in the long run. By reducing reliance on manual labor, improving throughput, and enhancing consistency, manufacturers can achieve significant savings in both labor costs and material waste. This is especially important in high-volume production environments where maintaining high quality while keeping costs down is a priority.
Additionally, CNC systems offer a customizable approach to polishing. Whether the task requires a rough grind to remove large imperfections or a fine polish for achieving a high-gloss, mirror-like finish, the machine can be programmed to deliver the exact result needed. This level of flexibility makes CNC polishing machines invaluable in industries that require a wide range of surface finishes, from industrial components to high-end consumer products.
In the automotive industry, for example, the demand for precision-polished parts is increasing due to the trend towards aesthetic customization. Parts such as wheel rims, grills, and exhaust tips are often polished to achieve a sleek, high-gloss finish that enhances the vehicle’s appearance. CNC polishing machines can handle large-scale production runs while maintaining the intricate details and consistency required for these parts.
Similarly, in the medical sector, where biocompatibility and safety are critical, CNC polishing machines ensure that implants and surgical instruments meet strict regulatory standards. These machines can achieve smooth, defect-free finishes on critical components, reducing the risk of infection and ensuring that the medical devices function correctly.
Furthermore, jewelry manufacturing has benefitted greatly from CNC polishing. Fine jewelry, where the smoothness and finish of the metal or stone surface are essential for both aesthetics and value, can be produced with greater efficiency using CNC polishing machines. These systems can polish complex designs with intricate details, ensuring that each piece meets the high standards required for luxury goods.
Another key advantage is the ability to achieve repeatability. Once the CNC polishing machine is programmed for a particular part or product, it can repeatedly produce identical results for large production runs. This level of consistency is challenging to achieve with manual polishing, where slight variations in technique or pressure can lead to differences in the final finish. This repeatability ensures that each part or product maintains the same high standard, improving product quality and reducing the likelihood of defects or rework.
As sustainability becomes an increasing focus in manufacturing, CNC polishing machines are also becoming more environmentally friendly. Many modern systems incorporate energy-efficient motors and closed-loop polishing systems, which help to reduce energy consumption and minimize waste. Moreover, by improving the accuracy of the polishing process, these machines reduce the need for excessive use of abrasives or polishing compounds, which can often lead to waste or environmental contamination. This makes CNC polishing machines a sustainable choice for companies looking to minimize their environmental footprint while maintaining high production standards.
In conclusion, the continuous evolution of CNC polishing machines is reshaping manufacturing processes across multiple industries. With the integration of AI, machine learning, and advanced automation, these machines are becoming more adaptable, precise, and efficient. Whether it’s in aerospace, automotive, medical, jewelry manufacturing, or other sectors, CNC polishing machines are helping manufacturers meet the growing demand for high-quality finishes while improving productivity, reducing costs, and enhancing sustainability. As technology continues to advance, these machines will play an increasingly vital role in achieving precision polishing on a wide range of materials and complex shapes, providing a significant competitive advantage for businesses that rely on high-quality, polished products.
Fully Enclosed Automatic Polisher
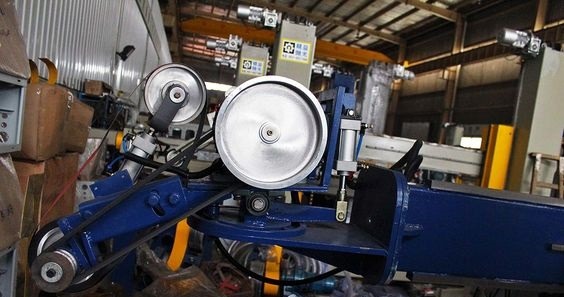
A Fully Enclosed Automatic Polisher is an advanced polishing machine designed to automate the polishing process in a controlled, enclosed environment. This type of machine is used to polish a variety of materials, including metals, plastics, ceramics, and composites, in industries where high-quality finishes are essential. The fully enclosed design ensures that the entire polishing process is conducted within a sealed area, offering several advantages, such as minimizing contamination, improving safety, and enhancing the efficiency of the polishing operation.
The key feature of a fully enclosed automatic polisher is its enclosed chamber, which helps prevent external contaminants, such as dust, dirt, or foreign particles, from interfering with the polishing process. This is especially important when working with materials that require a high degree of cleanliness and precision, such as in the aerospace, medical, electronics, and automotive industries. The sealed environment also helps contain the polishing debris, which is collected and filtered for reuse or disposal, contributing to a cleaner, more sustainable operation.
These machines are typically automated, meaning they can be programmed to perform a variety of polishing tasks with minimal human intervention. Once a workpiece is placed in the machine, it is polished according to the specifications programmed into the system, including the speed, pressure, type of abrasive used, and duration of polishing. Automation allows for consistent results across multiple parts, making it ideal for high-volume production environments where quality control is critical.
The polishing process in a fully enclosed automatic polisher typically involves the use of rotating polishing tools, such as abrasive wheels, belts, or pads, that are brought into contact with the workpiece. These tools move in a pre-programmed path that can be adjusted based on the size, shape, and material of the part being polished. Some systems also include oscillating motion or robotic arms to polish complex geometries, ensuring that even parts with intricate contours receive a uniform finish.
One of the primary benefits of fully enclosed automatic polishers is their ability to reduce human involvement in the polishing process. This minimizes the potential for errors, inconsistency, and contamination that can result from manual polishing techniques. Furthermore, the machine’s precision control ensures that the polishing process meets the exact requirements for each part, which is especially important for industries where surface finish is critical for functionality, performance, or appearance.
In terms of safety, the fully enclosed design provides several advantages. By containing the polishing process within a sealed area, the machine helps protect operators from exposure to polishing chemicals, abrasive particles, and dust generated during the operation. In addition, the machine can be equipped with safety features such as emergency shut-off buttons, alarms, and safety interlocks to ensure that operators can work safely around the machine. This is particularly important in industries that deal with hazardous materials or where worker safety is a top priority.
Another key advantage is the ability to achieve uniformity in the finish across large batches of parts. With a fully enclosed automatic polisher, each part receives the same level of attention and precision, ensuring that every workpiece has a consistent, high-quality surface finish. This repeatability is especially valuable in industries like automotive manufacturing, where components such as brake parts, engine covers, or exhaust pipes need to have a smooth, polished surface to ensure proper function and visual appeal.
In addition to polishing, some fully enclosed automatic polishers are designed to handle additional finishing operations, such as buffing, deburring, or graining, in a single machine cycle. This versatility eliminates the need for separate machines, improving overall efficiency and reducing costs. For example, in metalworking, the machine may be programmed to remove burrs from freshly machined components while simultaneously polishing the surface to a mirror-like finish.
Many fully enclosed automatic polishers are also equipped with dust collection and filtration systems. These systems help capture and remove harmful polishing debris, keeping the work environment clean and safe. The collected dust and particles can often be filtered and recycled, contributing to a more sustainable operation. Additionally, the sealed environment prevents dust from spreading to other areas of the facility, reducing the need for extensive cleaning and maintenance.
Fully enclosed automatic polishers are highly adaptable and can be customized for specific applications. Depending on the industry and the type of parts being polished, these machines can be equipped with various tools and polishing media, such as abrasive belts, brushes, buffing wheels, or vibratory systems. The flexibility to choose the right polishing method for each job ensures that the machine can meet a wide range of polishing requirements, from rough finishes to high-gloss mirror finishes.
The integration of advanced controls and automation software further enhances the capabilities of fully enclosed automatic polishers. These systems allow for precise control over the polishing process, with features such as programmable speed and pressure settings, feedback sensors, and remote monitoring. This makes it easier for operators to adjust the settings and optimize the process for different parts or materials, ensuring a high level of quality control and reducing downtime.
In conclusion, a fully enclosed automatic polisher is an advanced, automated polishing solution that offers numerous benefits, including consistent and high-quality finishes, enhanced safety, reduced contamination, and improved efficiency. The machine’s ability to operate in a sealed environment ensures that polishing is done in a controlled and clean setting, which is crucial for industries that demand precise, high-quality finishes. By automating the polishing process, these machines help reduce labor costs, improve throughput, and minimize errors, making them an ideal choice for industries that require high-volume, precision polishing.
The future of fully enclosed automatic polishers is poised for even more advancements, driven by emerging technologies such as Industry 4.0, smart manufacturing, and robotic integration. These developments are enhancing the flexibility, precision, and automation capabilities of polishing systems, making them even more efficient and adaptable to the needs of modern manufacturing.
Smart Features and Connectivity
As industries increasingly adopt smart manufacturing principles, fully enclosed automatic polishers are integrating with IoT (Internet of Things) devices, allowing for remote monitoring and data-driven insights. These connected systems can send real-time data to operators, providing detailed information on machine performance, tool wear, and polishing efficiency. This integration allows for predictive maintenance, which can anticipate when parts need to be serviced or replaced before they fail, minimizing downtime and preventing costly breakdowns.
With IoT connectivity, operators can remotely adjust machine settings, track the status of multiple machines at once, and receive automatic notifications if issues arise. This kind of connectivity ensures that the polishing process is as efficient and streamlined as possible, enabling better decision-making and optimization of the entire production process.
Advanced Automation and Robotics
Incorporating robotic arms into fully enclosed automatic polishers is another growing trend. These robots add more flexibility and precision by enabling the machine to polish complex shapes and parts that are difficult or impossible for traditional polishing tools to handle. Robotic arms can adapt to various angles, orientations, and contours, allowing for highly detailed and consistent polishing on components with intricate geometries.
Robots can also work in collaboration with other machines, such as CNC systems or vision systems, to dynamically adjust the polishing process. For example, a robotic arm might use a camera-based vision system to identify surface imperfections or detect when a part is fully polished, allowing it to stop or adjust in real time, ensuring no over-polishing or under-polishing.
Artificial Intelligence (AI) and Machine Learning
AI and machine learning (ML) are being integrated into polishing machines to further enhance their capabilities. By analyzing data from the polishing process, these systems can learn from past operations, recognizing patterns and making adjustments to optimize performance. AI can adjust variables like speed, pressure, and tool choice in real time to deliver the best possible finish for each specific part.
AI can also analyze the surface quality of the part during the polishing process, ensuring that it meets the desired standards. The ability to “learn” from previous operations means that machines can automatically improve their efficiency over time. This reduces the need for human intervention and makes the polishing process more predictable and reliable.
Sustainable Manufacturing Practices
As sustainability becomes an increasingly important consideration in manufacturing, fully enclosed automatic polishers are evolving to meet these demands. Many modern machines are designed with energy efficiency in mind, using low-energy motors, optimized cycle times, and advanced filtration systems that reduce waste and pollution. The dust collection systems in these machines not only capture abrasive particles and chemicals but also help in recycling the polishing materials, which can significantly reduce consumption and environmental impact.
Additionally, by automating the polishing process, manufacturers can minimize material waste and over-polishing—a common issue with manual polishing. With CNC-controlled polishing, the process is optimized to ensure just the right amount of material is removed to achieve the desired finish, reducing the amount of polishing compounds and abrasives needed.
Enhanced Versatility
The versatility of fully enclosed automatic polishers is another key benefit. Manufacturers can configure these machines for multi-functional purposes, allowing them to perform a variety of finishing operations, such as deburring, buffing, polishing, and even graining, all in a single cycle. This eliminates the need for multiple separate machines, improving workflow efficiency and reducing the footprint of the operation.
Moreover, the use of modular tooling systems allows manufacturers to quickly change polishing tools based on the material being processed, enabling one machine to handle different types of polishing tasks. This flexibility makes fully enclosed automatic polishers suitable for industries with diverse needs, such as automotive, aerospace, medical devices, and electronics, where multiple types of parts with varying requirements may be processed on the same production line.
Improving Production Speed
By integrating more advanced technologies like faster robots, automated loading and unloading systems, and shortened polishing cycles, fully enclosed automatic polishers are significantly improving production speed without sacrificing the quality of the finish. Automated systems can operate at high speeds while maintaining precision, allowing manufacturers to produce large quantities of polished parts quickly and consistently.
Moreover, the ability to run machines continuously without human intervention enables 24/7 operations, which further increases throughput and reduces lead times. This is especially beneficial in industries where large production volumes and fast delivery are essential.
Reduced Operational Costs
One of the most significant benefits of fully enclosed automatic polishers is the cost savings over time. By reducing the need for manual labor, minimizing errors, and increasing throughput, these machines can help companies lower their overall production costs. The automated nature of the system also reduces the risk of human error, ensuring that every part is polished consistently, which means less waste, fewer reworks, and improved product quality.
Furthermore, maintenance costs are minimized with advanced diagnostics, predictive maintenance, and fewer breakdowns. Many modern fully enclosed polishers are designed to self-monitor and provide feedback about the machine’s condition, ensuring that parts are serviced before they fail, reducing the cost of repairs and extending the lifespan of the equipment.
Conclusion
The fully enclosed automatic polisher is a highly advanced piece of equipment that has revolutionized the polishing industry by offering automation, precision, and a high level of control over the polishing process. With continuous advancements in AI, robotics, smart manufacturing, and sustainability, these machines are becoming even more efficient, adaptable, and environmentally friendly. As they evolve, fully enclosed automatic polishers will continue to be indispensable in industries that demand high-quality surface finishes and where the need for speed, precision, and repeatability is paramount. The shift toward more advanced automation and AI-powered systems is further enhancing their role in shaping the future of manufacturing.
Servo-Controlled Polishing Machine
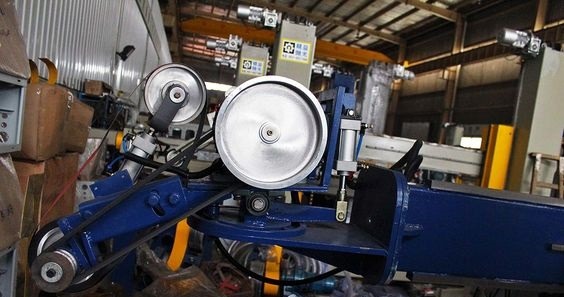
A servo-controlled polishing machine is an advanced type of polishing equipment that uses servo motors for precise control of the polishing process. These machines are widely used in industries where high accuracy, repeatability, and quality are essential for achieving a superior surface finish. Servo-controlled machines are designed to provide precise movements, allowing for fine adjustments to polishing speed, pressure, and angle, ensuring the best possible results for a variety of materials, including metals, plastics, ceramics, and composites.
Key Features and Benefits
- Precision Control: The main advantage of a servo-controlled polishing machine is the precise control it offers over the polishing process. Servo motors are known for their ability to provide consistent and smooth movements with high accuracy. This results in a uniform surface finish, even on parts with intricate shapes or complex geometries. The ability to fine-tune the polishing parameters ensures that the right level of abrasiveness is applied to the workpiece, preventing over-polishing or under-polishing.
- Adjustable Parameters: A servo-controlled machine allows operators to adjust key parameters, such as polishing speed, pressure, tool rotation, and path direction, based on the specific requirements of the workpiece. The ability to fine-tune these settings ensures that different materials and parts, whether flat or contoured, receive optimal treatment. This flexibility is especially useful in industries where the finishing process requires high precision, such as aerospace, automotive, and medical device manufacturing.
- Improved Consistency: One of the biggest challenges in manual polishing is maintaining a consistent finish across all parts. Servo-controlled polishing machines excel at providing repeatability and uniformity, which is crucial for mass production. Once programmed, the machine can perform the same polishing cycle on every part, ensuring that all items are finished to the same high standard without the variability that comes with human labor.
- Higher Efficiency: Servo motors are efficient in terms of energy consumption and operational speed. The precision they offer allows the polishing process to be carried out faster without sacrificing quality. This makes servo-controlled polishing machines ideal for high-volume production environments where speed and quality need to be balanced.
- Real-Time Feedback and Adjustment: Many servo-controlled polishing machines are equipped with feedback systems that allow for real-time monitoring of the polishing process. These systems can adjust polishing parameters on the fly, based on factors like surface roughness or tool wear, ensuring that the polishing operation continues smoothly. For example, if the machine detects that a part’s surface is not achieving the desired finish, it can automatically adjust the polishing pressure or speed to compensate.
- Advanced Automation and Integration: Servo-controlled polishing machines can be integrated into automated production lines, working seamlessly with other equipment, such as CNC machines, robotic arms, and conveyor systems. This level of integration enhances overall efficiency, enabling continuous polishing operations without the need for manual intervention. The machine’s automation also reduces human error, leading to improved product quality and lower labor costs.
- Reduced Wear and Tear: Since servo motors are designed to provide smooth, controlled movements, they experience less mechanical wear and tear compared to traditional motors. This helps reduce the maintenance needs of the machine, prolongs its lifespan, and ensures that the polishing process remains consistent over time. Servo-controlled systems also often feature self-diagnostic capabilities, alerting operators when maintenance is needed, preventing unplanned downtime.
- Versatility: Servo-controlled polishing machines can be used for a wide range of polishing applications, from rough polishing and deburring to high-gloss finishing. The ability to adjust the polishing process allows these machines to handle parts of varying sizes, shapes, and materials. They can polish flat surfaces, curved components, and even complex geometries with ease. This versatility makes servo-controlled machines valuable in a variety of industries, such as electronics, medical devices, automotive, and aerospace.
Applications of Servo-Controlled Polishing Machines
- Automotive Industry: Servo-controlled polishing machines are used in the automotive sector for polishing parts like engine components, wheel rims, and exterior panels. The precision of these machines ensures that parts have a smooth and uniform finish, which is essential for both aesthetic appeal and functional performance. These machines can also be used for mirror finishing or graining parts to achieve a specific surface texture.
- Aerospace Industry: In the aerospace industry, where high performance and safety are critical, servo-controlled polishing machines are used to polish parts like turbine blades, landing gear components, and aircraft structural parts. The ability to achieve a uniform finish and meet stringent quality standards is essential for the performance and longevity of aerospace components. Servo-controlled machines help achieve this by offering highly controlled polishing parameters.
- Medical Devices: In medical device manufacturing, precision is crucial to ensure that devices such as surgical instruments, implants, and prosthetics meet regulatory standards and are safe for use. Servo-controlled polishing machines are capable of polishing intricate medical parts to smooth, defect-free surfaces, minimizing the risk of infection or device malfunction. Their ability to deliver consistent finishes is critical for maintaining the quality of medical devices.
- Electronics: For the electronics industry, servo-controlled polishers are used to polish components like microchips, connectors, and heat sinks. These parts require a polished finish to ensure electrical conductivity, heat dissipation, and overall functionality. Servo-controlled machines offer the precision needed to polish small, delicate electronic components without damaging them.
- Jewelry and Luxury Goods: In the jewelry industry, where surface finish directly impacts the aesthetic appeal and value of the product, servo-controlled polishing machines are used to achieve high-gloss finishes on precious metals, gemstones, and other luxury materials. The ability to achieve a perfect, consistent shine on intricate designs is a key factor for manufacturers in this sector.
- Metalworking and Fabrication: Servo-controlled polishing machines are also used in metalworking for polishing stainless steel, aluminum, titanium, and other metals. These machines are ideal for finishing parts such as pipe fittings, valves, and flanges, which require a smooth surface to prevent corrosion and ensure functionality.
Conclusion
Servo-controlled polishing machines represent the cutting edge of polishing technology, combining precision, automation, and efficiency to meet the demands of modern manufacturing. By utilizing servo motors for precise control, these machines can deliver high-quality finishes on a wide range of materials and components, making them invaluable in industries that require consistent, repeatable results. Whether used for automotive parts, aerospace components, medical devices, or luxury goods, the versatility and accuracy of servo-controlled polishing machines help manufacturers achieve optimal surface finishes, reduce operational costs, and increase production speed. As technology continues to advance, these machines will play an even greater role in driving innovation and improving the quality of polished products across industries.
A servo-controlled polishing machine offers highly precise and efficient polishing solutions by utilizing servo motors to control the movement of polishing tools with great accuracy. The precision offered by servo motors allows for fine-tuning of various parameters such as polishing speed, pressure, and tool position, ensuring that the polishing process is optimized for different materials and geometries. These machines are commonly used across multiple industries, including automotive, aerospace, medical devices, electronics, and luxury goods, where consistent, high-quality finishes are crucial.
The servo-controlled system enhances automation and repeatability in the polishing process, providing uniform surface finishes across large volumes of parts with minimal human intervention. Once programmed, the machine can polish each workpiece consistently, eliminating the variability associated with manual polishing methods. This is particularly beneficial in environments where high-volume production is required, as it improves efficiency and productivity while reducing the likelihood of errors that could compromise the quality of the finished product.
One of the standout advantages of servo-controlled polishing machines is their ability to handle complex shapes and components with intricate geometries. The precise movement control allows these machines to polish curved, concave, or convex surfaces, which are often challenging for traditional polishing methods. Furthermore, the machine’s ability to monitor and adjust key parameters in real-time ensures that the desired surface finish is achieved for every part, reducing the risk of over-polishing or under-polishing.
These machines often come equipped with advanced control systems that provide detailed data on the polishing process. This allows operators to track performance, tool wear, and material usage, enabling predictive maintenance and reducing downtime. The continuous feedback loop also helps identify any issues early on, ensuring that production remains uninterrupted and machines operate at peak performance. Additionally, many servo-controlled polishing systems are integrated with other automated machinery, such as CNC machines, robotic arms, or conveyor systems, which streamlines the entire production process, making it more efficient and less reliant on manual labor.
In terms of sustainability, these machines contribute to reduced material waste and energy consumption. Since the servo motors are designed for efficient power usage and the polishing process is highly controlled, the machines consume less energy compared to traditional systems. Furthermore, the precise nature of the polishing process minimizes the amount of abrasive material required, reducing waste and making the process more environmentally friendly.
For manufacturers, one of the key benefits of servo-controlled polishing machines is the reduction of labor costs. With automation handling the bulk of the polishing tasks, operators can focus on monitoring and adjusting the machine’s settings rather than performing manual polishing. This also results in a more consistent quality of finish, as the machine eliminates the human variability inherent in manual polishing. The result is a more efficient production process with higher throughput and lower rejection rates.
The versatility of these machines allows them to be used for a wide range of applications. In the automotive industry, for instance, they are used to polish parts like engine components, wheel rims, and exterior panels, ensuring a high-quality finish that is both functional and aesthetically appealing. In the aerospace sector, where parts are required to meet strict quality and performance standards, servo-controlled machines provide the precision necessary to polish components such as turbine blades, landing gear, and aircraft fuselage parts.
In medical device manufacturing, these machines are used to polish surgical instruments, implants, and prosthetics, where surface quality is critical for both patient safety and regulatory compliance. Similarly, in the electronics industry, servo-controlled polishing machines ensure that microchips, connectors, and heat sinks are polished to perfection, enhancing their functionality and durability. The luxury goods sector, including jewelry manufacturing, also benefits from the high-precision polishing these machines offer, ensuring that precious metals, gemstones, and other materials achieve a flawless, high-gloss finish.
As technology continues to evolve, servo-controlled polishing machines will likely become more advanced, incorporating AI-driven algorithms, machine learning for optimization, and even more energy-efficient designs. These innovations will make the machines even more adaptable to a wide range of materials and polishing requirements, while improving operational efficiencies and product quality. As industries continue to demand higher standards for surface finishes, servo-controlled polishing machines will remain a key tool for achieving the precise, reliable, and repeatable results needed in modern manufacturing environments.
PLC-Controlled Polishing System
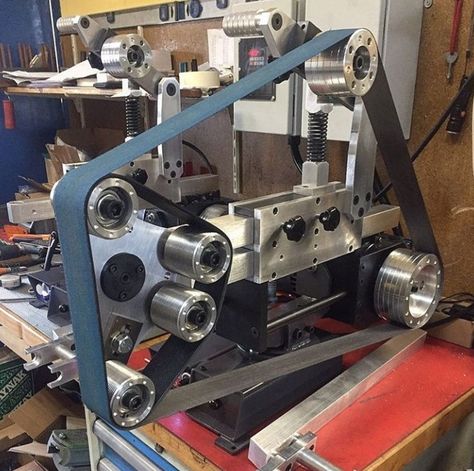
A PLC-controlled polishing system utilizes a Programmable Logic Controller (PLC) to automate and control the polishing process. This system replaces traditional manual operation with automation, providing precise control over various polishing parameters like speed, pressure, and tool rotation. By using a PLC, the system can be programmed to follow specific instructions and execute polishing tasks in a highly repeatable and efficient manner. The use of PLCs allows for better integration with other production systems, making it a valuable tool in modern manufacturing environments.
One of the main advantages of a PLC-controlled polishing system is the automation it offers. PLCs can be programmed to manage multiple aspects of the polishing process, such as the sequence of operations, timing, and adjustment of polishing conditions based on real-time data. This ensures a more consistent and predictable result compared to manual methods. The system can also be configured to handle complex polishing tasks, such as polishing parts with irregular shapes or intricate surfaces, with a high degree of precision.
A key feature of a PLC-controlled polishing system is its ability to integrate with other equipment on the production line. This enables seamless communication between the polishing system and machines such as CNC units, robotic arms, or conveyors, creating a fully automated and optimized production flow. Integration can significantly reduce labor costs by minimizing the need for manual intervention and enhancing overall process efficiency.
The programming capabilities of the PLC allow operators to adjust and customize the polishing cycle. Parameters such as polishing speed, pressure, tool rotation direction, and duration can be fine-tuned to meet the specific requirements of each part or batch. This flexibility makes PLC-controlled systems highly versatile, capable of polishing a wide range of materials and components, including metals, plastics, ceramics, and composites.
Another key benefit is monitoring and diagnostics. PLC-controlled systems can continuously monitor the polishing process and provide real-time data on various performance metrics, such as motor speed, tool wear, pressure levels, and surface finish quality. This data can be used to track performance over time, making it easier to optimize processes and identify areas for improvement. Many PLC systems are equipped with alarm and diagnostic functions that notify operators when certain parameters exceed safe limits, preventing potential damage to the workpieces or machinery.
Additionally, the repeatability offered by PLC-controlled polishing systems is crucial in industries where high-quality finishes are essential. The PLC can be programmed to follow a set sequence for polishing each part, ensuring that each workpiece receives the same level of attention and polish. This is especially important for industries like aerospace, automotive, and medical device manufacturing, where precision and consistency are critical.
PLC-controlled polishing systems also offer increased flexibility in the production process. By modifying the program, the system can be quickly adapted to handle different polishing tasks or changes in product specifications. This adaptability reduces downtime and improves the system’s overall utilization, which is important in industries where product designs and requirements are constantly changing.
In terms of maintenance, PLC systems can reduce the risk of unexpected failures. Since PLCs provide real-time feedback, operators can identify potential issues before they become serious problems, allowing for predictive maintenance. The system can also be programmed to carry out routine diagnostics and automatically adjust the polishing parameters to maintain optimal performance.
Overall, a PLC-controlled polishing system brings significant advantages in terms of automation, precision, efficiency, and versatility. By integrating advanced control and monitoring features, these systems help manufacturers achieve superior surface finishes while reducing labor costs and ensuring consistent product quality. The flexibility to handle various materials and component types, combined with the ability to customize and optimize the polishing process, makes PLC-controlled systems ideal for a wide range of industries, from automotive and aerospace to medical device manufacturing and electronics. As technology advances, these systems will continue to evolve, incorporating AI-driven optimization and real-time process adjustments, further enhancing their performance and capabilities.
A PLC-controlled polishing system not only enhances automation and precision, but it also brings significant improvements in quality control and efficiency. The ability to program the system to specific parameters means that operators can ensure that the polishing process is optimized for each unique part. These adjustments can be made based on factors such as the type of material being polished, the desired surface finish, and the specific shape or geometry of the part. For example, a part with a complex, contoured surface may require different pressure or speed settings than a flat part, and the PLC system can be programmed to automatically adjust accordingly.
The real-time monitoring and feedback capabilities provided by the PLC system further contribute to its effectiveness. With integrated sensors and feedback loops, the PLC can track and adjust parameters such as tool speed, pressure, temperature, and vibration. If any of these parameters fall outside of acceptable thresholds, the system can either correct the issue automatically or alert the operator to potential problems. This continuous monitoring ensures that the polishing process remains consistent, reducing the likelihood of defects or inconsistencies that can arise from manual processes or human error.
In addition to monitoring, many PLC-controlled polishing systems offer data logging features, which store information about each polishing cycle. This data can be used to generate detailed reports on the performance of the machine, individual polishing cycles, and even the wear and tear of the polishing tools. The ability to analyze this data allows manufacturers to make data-driven decisions, whether it’s adjusting the polishing parameters for future cycles, tracking the longevity of tools, or even improving the overall efficiency of the system.
Another key benefit of the PLC system is its ability to optimize energy usage. By precisely controlling the operation of motors and other equipment, the PLC can reduce energy consumption during idle times or when the system is running at lower capacities. This can result in cost savings over time, especially for high-volume production lines that run for extended periods.
Flexibility in the PLC-controlled polishing system also extends to its capability to be integrated with other factory systems. The system can be linked to enterprise-level solutions such as Enterprise Resource Planning (ERP) software or Manufacturing Execution Systems (MES), allowing for better visibility into production schedules, inventory management, and even quality control. By integrating with ERP or MES systems, a PLC-controlled polishing system can receive instructions directly from a central database, streamlining the process from order entry to final product delivery.
For companies with a diverse range of products, the customization options of the PLC-controlled system are invaluable. The ability to reprogram the system to handle different polishing tasks on the fly is a major advantage, particularly when dealing with high-mix, low-volume production. This adaptability ensures that the same machine can handle a variety of parts with different polishing requirements, without the need for significant setup time or manual intervention.
Safety features are also a crucial aspect of PLC-controlled systems. Given the complexity of the machinery and the potential risks associated with high-speed polishing processes, the PLC can include various safety protocols, such as automatic shutdown in the event of a malfunction, safety interlocks, or emergency stop functions. This reduces the risk of accidents and ensures a safe working environment for operators.
The system’s ability to ensure consistent product quality is especially important in industries where even minor imperfections can lead to significant issues. In industries such as aerospace, where component performance is critical, or medical device manufacturing, where safety and precision are paramount, the reliability and consistency offered by a PLC-controlled polishing system ensure that every piece is polished to the same high standard, reducing the need for rework or part rejection.
Maintenance is another area where PLC-controlled polishing systems shine. These systems are often designed with self-diagnostic capabilities, meaning they can flag issues before they cause significant downtime or damage. This capability extends the lifespan of the machinery and reduces overall maintenance costs. With the data provided by the PLC system, maintenance teams can schedule preventive maintenance more effectively, keeping the system running smoothly and reducing unplanned downtime.
Furthermore, operator interface is made more user-friendly through the PLC. Many modern systems come with a HMI (Human-Machine Interface), which is a touchscreen or graphical user interface (GUI) that makes it easy for operators to monitor and adjust the machine settings. The interface typically includes intuitive controls for starting and stopping the process, adjusting parameters, reviewing data logs, and setting up new programs. Some systems also allow for remote monitoring, so operators or managers can oversee the polishing process from any location, improving overall workflow and decision-making.
As industries evolve and demand for more sophisticated and efficient manufacturing processes increases, PLC-controlled polishing systems are expected to become even more advanced. Future systems may integrate Artificial Intelligence (AI) and machine learning to further enhance the optimization of the polishing process. For example, AI algorithms could analyze past polishing cycles to automatically adjust settings in real-time for optimal results based on surface texture, material hardness, or tool wear. This would further reduce the need for human intervention, enhance process control, and improve overall efficiency.
In conclusion, a PLC-controlled polishing system offers significant advantages in terms of automation, precision, efficiency, and flexibility. By integrating PLC technology into the polishing process, manufacturers can achieve consistent quality, reduce production costs, and improve operational efficiency. The customizability, data-driven monitoring, and real-time feedback features of PLC systems make them essential tools for industries such as automotive, aerospace, medical devices, and electronics. As technology continues to evolve, these systems will become even more capable, further optimizing polishing processes and supporting the growing demands of modern manufacturing.
Dual-Station Polishing Machine
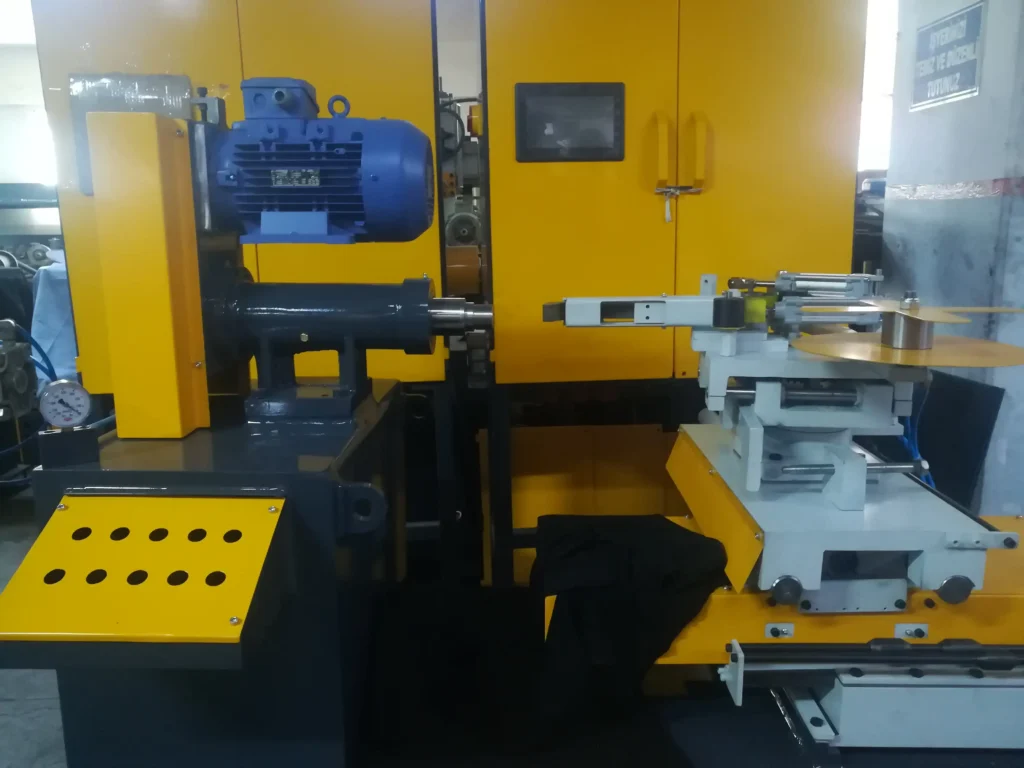
A dual-station polishing machine is an advanced piece of polishing equipment designed to enhance productivity and efficiency by enabling simultaneous polishing operations on two separate workpieces. This type of machine typically features two polishing stations or spindles, which allow the operator to polish two parts at once, reducing downtime and increasing throughput. The dual-station design is especially beneficial in environments where high-volume production is required, as it can significantly reduce the time spent on polishing tasks.
The primary advantage of a dual-station polishing machine is its ability to double the output compared to single-station systems. By working on two parts simultaneously, the machine maximizes the use of available polishing time, enabling faster processing of parts. This increased throughput is particularly useful in industries where parts need to be polished in large quantities, such as in automotive manufacturing, aerospace, electronics, and metalworking.
Key Features and Benefits
- Increased Efficiency: The most significant benefit of a dual-station polishing machine is the improved productivity. By operating two polishing stations at the same time, manufacturers can significantly cut down on cycle times. While one part is being polished on one station, the other part can be processed on the second station, effectively doubling the output without additional labor or machine time. This is ideal for high-volume production runs, where reducing processing time directly translates into higher production efficiency.
- Reduced Downtime: With two workstations, the machine can be set up to polish different parts or even parts with different polishing requirements simultaneously. This eliminates the need for time-consuming manual changeovers or reconfiguration between different polishing tasks. The system can be designed to allow one station to work while the other is being set up or loaded with new parts, minimizing downtime and improving overall system efficiency.
- Consistent Results: Dual-station machines maintain uniformity in polishing, ensuring that both workpieces receive the same level of finish, speed, and pressure during the polishing process. This consistency is particularly important when manufacturing parts that require precise surface finishes, such as automotive body panels, aerospace components, or medical devices. The ability to set the same parameters for both stations ensures that each part is polished to identical standards, which is essential for high-quality production.
- Space Optimization: In a factory setting, the dual-station design helps optimize floor space. Instead of requiring two separate machines, a single dual-station machine can handle two parts at once, reducing the amount of valuable floor space needed for polishing equipment. This is particularly beneficial in environments where space is limited, such as in manufacturing plants or industrial workshops.
- Flexible Applications: A dual-station polishing machine is highly versatile and can be adapted to a variety of polishing tasks. It can handle different types of parts, ranging from small metal components to larger plastic or ceramic parts, and is capable of providing different levels of polish (e.g., rough polishing, mirror finishes, or matte finishes). The ability to adjust polishing parameters such as speed, pressure, and polishing medium allows the machine to handle a wide range of materials and workpieces.
- Improved Safety: Since dual-station polishing machines are often automated, they reduce the amount of manual labor required. This leads to fewer human interactions with the machine, which improves safety and reduces the risk of accidents. Additionally, many dual-station systems come with safety features such as emergency stop buttons, protective shields, and sensor systems to detect any faults or irregularities during operation.
- Cost-Effectiveness: By increasing output and reducing the need for multiple polishing stations, dual-station polishing machines can provide a cost-effective solution for high-volume manufacturing. The savings come from the reduction in labor costs, maintenance, and energy consumption compared to running two separate single-station machines. The initial investment in a dual-station machine can be higher, but the long-term benefits in terms of productivity and efficiency often outweigh the upfront cost.
Applications
- Automotive Industry: In automotive manufacturing, dual-station polishing machines are commonly used to polish metal parts such as engine components, exterior panels, and wheel rims. The ability to process multiple parts simultaneously reduces production time and ensures a high-quality finish for each component. This is especially important in industries where surface finish quality is critical for both aesthetics and functionality.
- Aerospace: Aerospace manufacturers rely on dual-station polishing machines to handle parts like turbine blades, landing gear, and aircraft panels, all of which require a precise and smooth surface finish to meet strict performance standards. The ability to polish these parts simultaneously increases throughput and ensures that they meet the rigorous demands of the aerospace industry.
- Medical Devices: In the medical device industry, where precision and surface integrity are paramount, dual-station polishing machines can be used to polish surgical instruments, implants, and prosthetics. The consistency offered by the dual stations ensures that each device meets the necessary surface finish requirements, which is critical for both functionality and patient safety.
- Electronics: Dual-station polishing machines are used in the electronics industry to polish heat sinks, connectors, circuit boards, and other components that require smooth, conductive surfaces. The ability to process parts quickly and consistently is essential for maintaining the quality of electronic devices.
- Metalworking: Metalworking industries, including those that produce stainless steel and aluminum products, can use dual-station polishing machines to finish parts like pipes, fittings, flanges, and valves. The machine’s ability to work on two parts at once ensures that a large number of components can be polished efficiently without sacrificing quality.
- Luxury Goods and Jewelry: For the luxury goods industry, including jewelry manufacturing, dual-station polishing machines can be used to polish precious metals, gemstones, and other high-end materials. The ability to achieve a flawless finish on these delicate items is crucial for their aesthetic value, and the dual-station setup ensures that polishing can be completed more efficiently.
Conclusion
The dual-station polishing machine offers a highly efficient solution for industries requiring high-quality surface finishes. By allowing two parts to be polished simultaneously, the system reduces cycle times and increases throughput, making it ideal for high-volume production. With the added benefits of consistency, flexibility, and space optimization, this type of machine is a valuable asset in industries such as automotive, aerospace, medical devices, electronics, and luxury goods manufacturing. The ability to handle various polishing tasks with high precision ensures that dual-station polishing machines continue to be an essential tool in modern manufacturing processes, delivering superior surface finishes while boosting productivity and reducing operational costs.
The dual-station polishing machine is continually evolving to meet the increasing demands for precision, efficiency, and versatility in manufacturing. As industries progress and the need for more complex, high-quality finishes grows, these machines are being upgraded with advanced features that enhance their performance. Here are some additional aspects of dual-station polishing machines and their future developments:
Advanced Control Systems and Automation
Modern dual-station polishing machines are increasingly equipped with advanced control systems that allow for greater precision in the polishing process. These systems often include touchscreen interfaces, programmable logic controllers (PLC), and robotic automation, which enable operators to easily program and control the machine’s settings. This not only enhances the machine’s efficiency but also makes it possible to achieve highly specific polishing results for each workpiece.
In addition, feedback loops are integrated into the system, providing real-time monitoring and adjustments to key parameters such as pressure, speed, tool rotation, and abrasive application. By analyzing these metrics, the system can automatically optimize the polishing process to ensure a consistent finish, reducing human error and the need for manual adjustments.
The integration of AI (Artificial Intelligence) and machine learning is another exciting advancement. AI-powered dual-station polishing machines could use algorithms to analyze past data, predict potential issues, and adjust parameters dynamically to achieve the best finish. These technologies would further improve the consistency and repeatability of the polishing process, allowing manufacturers to meet even the most stringent quality standards with greater ease.
Customizable Polishing Parameters
One of the benefits of dual-station polishing machines is the customizability of the polishing parameters. Manufacturers can set specific parameters for each station depending on the workpiece material and desired finish. For example, a softer material like aluminum may require a different polishing speed or pressure compared to harder materials like stainless steel or titanium.
The flexibility of these machines allows operators to adjust parameters such as:
- Polishing Pressure: The pressure exerted on the workpiece is crucial in determining the surface quality. Excessive pressure can cause damage, while too little pressure may result in an incomplete finish.
- Polishing Speed: Different parts require different polishing speeds. Some parts may need slower speeds for a fine finish, while others might require higher speeds to remove more material quickly.
- Abrasive Materials: The choice of abrasive material—whether buffing compounds, abrasive pads, or polishing pastes—can affect the surface finish. Dual-station machines can handle different abrasives on each station, allowing for varied polishing tasks on separate parts.
- Cycle Time: Depending on the complexity of the part, cycle time can be adjusted for each station. More intricate workpieces might require longer polishing times to achieve a smooth surface, while simpler parts can be polished quickly.
Enhanced Tooling and Component Compatibility
Another important factor in the design of dual-station polishing machines is the compatibility of tooling with different workpieces. Manufacturers often require specific polishing tools and fixtures to handle the unique shapes and sizes of their parts. Dual-station polishing machines are designed to accommodate a wide range of tools, such as:
- Flap wheels
- Buffing pads
- Brushes
- Diamond-coated abrasives
Moreover, the machine’s ability to hold multiple tooling setups simultaneously can increase versatility. For example, if one station requires abrasive wheels for heavy material removal, the other station can be equipped with a polishing pad for finer finishing.
The ability to quickly switch tooling between stations without interrupting production ensures that the machine is adaptable to a wide range of polishing tasks, improving both flexibility and efficiency.
Integration with Other Manufacturing Systems
Modern dual-station polishing machines are often designed to be fully integrated into the larger production line. Integration with CNC machines, robotic arms, and automated conveyors creates a seamless workflow that automates much of the manufacturing process. As parts move through the production line, they can be automatically loaded onto the polishing machine, processed on both stations simultaneously, and then moved onto the next phase of production.
Additionally, many dual-station machines are designed with IoT (Internet of Things) capabilities, enabling them to communicate with other machines or central systems. This allows manufacturers to gather and analyze data from the polishing process in real time, helping to identify trends, troubleshoot issues, and further optimize production efficiency.
The data generated from these systems can also be used for predictive maintenance, where algorithms analyze usage patterns to determine when parts such as polishing pads, motors, or spindles may need maintenance or replacement, thereby reducing unplanned downtime.
Environmental and Sustainability Considerations
As sustainability becomes a more significant concern in the manufacturing world, dual-station polishing machines are evolving to meet green manufacturing goals. Modern systems often feature energy-efficient motors and low-waste designs, minimizing energy consumption and reducing the amount of consumables like abrasives and polishing compounds used.
Some machines are equipped with closed-loop systems that recycle polishing fluids and remove pollution, such as dust and waste materials, from the air. This not only contributes to a cleaner working environment but also reduces the overall environmental impact of the manufacturing process.
By reducing the need for excess raw materials and optimizing the use of abrasives, these systems also help cut down on the amount of waste generated, making dual-station polishing machines more environmentally friendly and aligned with modern sustainability standards.
Future Trends and Developments
The future of dual-station polishing machines is promising, with several potential developments on the horizon:
- Automation and AI Integration: As automation continues to progress, dual-station polishing machines will likely see deeper integration with AI and robotics. This will enhance their ability to adapt to different polishing tasks, automate setup changes, and analyze polishing results in real-time.
- Advanced Materials Processing: As materials science advances, dual-station polishing machines will be required to handle a wider range of materials, including composites, advanced ceramics, and 3D-printed parts. These new materials will require specialized polishing methods that these machines can adapt to through customizable tool setups and polishing parameters.
- Smarter Maintenance: As more systems become connected to cloud-based platforms, the ability to conduct remote monitoring and predictive maintenance will grow. Manufacturers will be able to track the health of their machines, receive maintenance alerts, and even troubleshoot issues from remote locations.
- Customization for Specialized Industries: Different industries often have specific needs when it comes to polishing. Dual-station polishing machines may continue to evolve to offer more tailored solutions for sectors such as medical device manufacturing, aerospace, and luxury goods, where precise polishing standards must be met.
- Robotic Assistance: Future dual-station polishing systems may integrate with robotic arms to handle workpieces more efficiently, especially when the parts are large, delicate, or difficult to manipulate by hand. This could open up new possibilities in fully automated polishing cells, where robots load, polish, and unload parts without human intervention.
Conclusion
A dual-station polishing machine is a highly efficient and versatile tool for modern manufacturing environments. Its ability to polish two workpieces simultaneously enhances throughput and reduces cycle times, which is crucial for industries requiring high-volume production. With features such as customizable polishing parameters, advanced automation, and integration with other systems, dual-station polishing machines are equipped to handle a wide range of materials and polishing tasks. As technology continues to advance, these machines will become even more sophisticated, offering smarter automation, increased precision, and enhanced environmental sustainability.
Automatic Load/Unload Polishing Machine
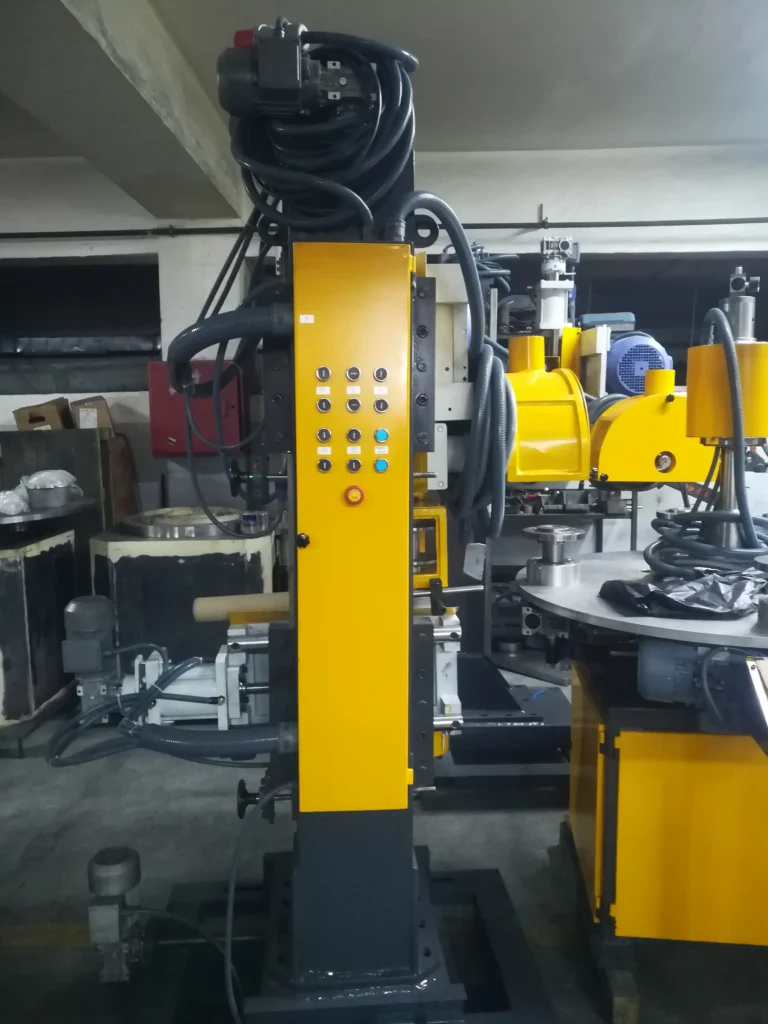
An automatic load/unload polishing machine is a specialized type of polishing equipment designed to improve production efficiency by automating the process of loading and unloading workpieces. This type of machine is commonly used in industries where high-volume production and consistent surface finishes are required. By automating the loading and unloading stages, these systems help minimize human intervention, reduce cycle times, and improve overall workflow.
Key Features and Benefits
- Automated Loading and Unloading The most significant advantage of automatic load/unload polishing machines is the automation of the loading and unloading process. Typically, these machines are integrated with robotic arms or automated conveyors to handle parts without human involvement. The automation system can pick up raw parts from a loading station, position them correctly in the polishing area, and after polishing, move them to an unloading station for further processing or packaging.
- Reduced Labor Costs By eliminating the need for operators to manually load and unload parts, labor costs are significantly reduced. Workers can be reassigned to more critical tasks, such as machine maintenance, quality control, or overseeing the operation of multiple polishing machines. The automated process ensures that the production line runs smoothly with minimal human oversight.
- Increased Productivity The automatic loading and unloading system streamlines the polishing process, allowing the machine to run continuously without downtime between cycles. While one part is being polished, the loading/unloading system can work on other parts, ensuring that the polishing machine is always operational. This leads to improved throughput, especially in high-volume production environments.
- Consistent Part Handling The automated system ensures that parts are consistently loaded and unloaded in the same manner every time, which contributes to uniformity in the polishing process. This is crucial in industries that require precise and consistent finishes, such as aerospace, automotive, medical devices, and electronics. The robotic arms or conveyors that handle the parts are programmed to ensure correct placement and orientation, preventing potential damage or mistakes that could occur with manual handling.
- Reduced Risk of Contamination or Damage Human handling can sometimes lead to contamination or damage, especially when dealing with delicate or sensitive parts. The use of automated loading/unloading systems helps mitigate these risks by providing precise, controlled handling. This is especially important in industries where contamination, such as oils, dirt, or fingerprints, can compromise the quality of the surface finish or the integrity of the parts.
- Minimized Cycle Time By automating the loading and unloading process, the overall cycle time for polishing is reduced. The polishing machine can focus on processing parts while the robotic or conveyor systems work simultaneously to handle the next batch of parts. This efficiency boost is essential for meeting tight production schedules, especially in industries with high-volume manufacturing demands.
- Enhanced Flexibility Some automatic load/unload polishing machines can be equipped with flexible systems that can handle a variety of part sizes and types. Whether polishing metal parts, plastic components, or ceramic items, the system can be adjusted to accommodate different workpieces, making it suitable for industries with diverse product lines. The flexibility of these machines allows manufacturers to meet varying customer demands without the need for frequent reconfigurations or manual interventions.
- Integration with Other Systems Many modern automatic load/unload polishing machines can be seamlessly integrated with other automation systems, such as CNC machines, robotic arms, inspection systems, and conveyors. This integration creates a fully automated production line where parts are moved from one station to the next without any human intervention. The system can be programmed to automatically adjust settings, monitor part quality, and track production data.
- Reduced Human Error Human errors, such as misloading parts, incorrect orientation, or inconsistent placement, can lead to defects or delays in production. By automating the loading and unloading process, the chances of human error are minimized, ensuring that the parts are consistently handled and processed correctly. This helps to maintain high levels of quality control and ensures that each part receives the desired surface finish.
- Space Efficiency Automatic load/unload polishing machines are designed to maximize the use of available space. By integrating the loading and unloading mechanisms into the same machine or station, manufacturers can save valuable floor space compared to systems where separate machines or manual stations are used for loading and unloading. This compact design is particularly beneficial in environments with limited space, such as small workshops or production facilities.
Applications of Automatic Load/Unload Polishing Machines
- Automotive Industry In automotive manufacturing, automatic load/unload polishing machines are used to polish metal parts such as engine components, wheel rims, and exterior panels. These parts often require high-quality finishes to ensure both aesthetic appeal and functional performance. The ability to automate the handling of parts throughout the polishing process significantly increases production efficiency and consistency.
- Aerospace Aerospace manufacturers rely on automatic load/unload polishing machines for polishing critical components such as turbine blades, landing gear, and aircraft fuselage parts. These parts must meet strict surface finish standards, and the automation of the load/unload process helps ensure that they are polished efficiently and without human intervention, reducing the risk of defects and maintaining high-quality production standards.
- Medical Device Manufacturing Medical devices, such as surgical instruments, implants, and prosthetics, require precise polishing to ensure that their surfaces are smooth, safe, and free from contaminants. Automatic load/unload polishing machines help maintain the necessary level of consistency and precision in polishing while reducing the risk of contamination from human contact. The automation also ensures that parts are polished in a controlled, repeatable manner.
- Electronics and Semiconductor Manufacturing The electronics industry uses automatic load/unload polishing machines to polish delicate components like circuit boards, connectors, heat sinks, and semiconductors. Precision polishing is essential to ensure proper electrical conductivity, thermal management, and overall functionality of the components. Automation in this area helps improve the speed and accuracy of polishing while maintaining high standards of cleanliness and quality.
- Jewelry and Luxury Goods In the jewelry industry, polishing is an essential step in achieving a high-quality finish on gold, silver, platinum, and precious gemstones. Automatic load/unload polishing machines are used to streamline the polishing of rings, necklaces, bracelets, and other items. The ability to handle large volumes of jewelry with precision and minimal handling reduces the potential for damage and ensures a consistent, high-quality finish across all pieces.
- Metalworking and Fabrication In metalworking and fabrication industries, parts such as pipes, fittings, flanges, and valves require a smooth, polished surface to meet industry standards and customer requirements. Automatic load/unload polishing machines ensure that these parts are polished quickly and uniformly, contributing to faster production times and reducing the need for manual labor.
Future Developments
The future of automatic load/unload polishing machines lies in advanced automation and intelligent systems. As industries move towards Industry 4.0, the integration of smart sensors, machine learning algorithms, and real-time monitoring will allow polishing machines to adapt to various production conditions and optimize the polishing process further. These advancements will enable systems to automatically adjust parameters based on part characteristics, wear and tear, and real-time feedback, improving both efficiency and quality.
Additionally, as manufacturers strive for greater sustainability, automatic load/unload polishing machines may incorporate energy-saving technologies and environmentally friendly polishing methods. Innovations such as closed-loop systems for recycling polishing fluids, dust collection systems, and low-energy motors will help reduce the environmental impact of polishing processes.
Conclusion
An automatic load/unload polishing machine is an essential tool for industries that require high-volume production and consistent surface finishes. By automating the loading and unloading process, these machines increase efficiency, productivity, and quality control while reducing labor costs and the risk of human error. Whether in the automotive, aerospace, medical, electronics, or luxury goods sectors, automatic load/unload polishing machines help streamline production and ensure that parts are polished to the highest standards. With future advancements in AI, IoT integration, and sustainability, these machines are poised to become even more intelligent, efficient, and adaptable to the evolving demands of modern manufacturing.
An automatic load/unload polishing machine is a critical component in modern manufacturing, particularly in high-volume industries where efficiency, precision, and consistency are paramount. These machines streamline the production process by automating the loading and unloading of workpieces, reducing manual labor, and increasing overall throughput. The integration of automation into these systems allows for continuous operation without the need for operator intervention during the load and unload phases, which significantly cuts down cycle times and minimizes human error.
The key advantage of these machines is their ability to handle parts automatically, ensuring that they are consistently positioned and oriented correctly for the polishing process. This eliminates the potential for mistakes that could arise from manual loading, such as misalignment or contamination. The automation also allows for faster transitions between workpieces, maintaining a continuous flow and reducing idle time, thus enhancing productivity. As parts are polished, the loading/unloading system can simultaneously work on new parts, allowing for minimal downtime and maximizing machine utilization.
One of the notable features of these polishing machines is their ability to work with a variety of workpieces, ranging from metal to plastic to ceramic materials. The versatility of these machines is crucial in industries like aerospace, automotive, and medical devices, where high precision and surface finish quality are essential. By customizing the polishing parameters for different materials and part shapes, manufacturers can achieve the desired finish while ensuring that each part meets the strict standards of quality.
Automatic load/unload polishing machines also provide a higher level of consistency in the polishing process. Since the parts are handled by the machine in a precise, controlled manner, the surface finish achieved is uniform across all workpieces. This consistency is vital in sectors like electronics, where even the smallest variations in surface finish can impact the functionality of components like circuit boards and semiconductors. Furthermore, these machines reduce the risk of contamination, which can be a significant concern in industries such as medical device manufacturing where cleanliness is critical.
The automation extends to real-time monitoring and adjustment, with many of these systems incorporating sensor-based feedback loops to adjust polishing parameters like speed, pressure, and abrasive material based on the type of part being polished. This ensures that the surface finish remains within specified tolerances, even as the system works with different materials or part geometries. Advanced PLC (Programmable Logic Controller) systems enable these adjustments to occur seamlessly without interrupting the polishing process, further enhancing efficiency.
The integration of robotic arms, conveyors, and even artificial intelligence (AI) is becoming more common in these machines, allowing for sophisticated automated workflows. These systems can be linked to other machines and production lines, enabling fully automated factories where polishing is just one part of a seamless process. This integration helps reduce the need for manual labor, decreases human error, and ensures that operations run with maximum efficiency.
In addition to improving efficiency and precision, automatic load/unload polishing machines contribute to reducing operational costs. With automated systems, manufacturers do not need to employ as many operators for repetitive tasks, freeing up staff to focus on more technical or strategic roles. Moreover, the reduction in cycle time and labor costs directly contributes to lower overall production costs, which can be particularly valuable in competitive industries.
Another key benefit of these systems is their ability to adapt to changes in production volume. Whether a manufacturer needs to produce a small batch of parts with tight tolerances or a large batch of standard items, the flexibility of automatic load/unload polishing machines allows them to scale up or down without compromising the quality of the finish. This adaptability makes them an attractive solution for industries that need to respond quickly to market demand changes or produce custom parts in addition to standard components.
The future of automatic load/unload polishing machines is shaped by ongoing advancements in artificial intelligence, data analytics, and robotics. As these technologies continue to evolve, polishing machines will become even more intelligent, capable of adjusting to new polishing challenges with minimal human input. Predictive maintenance, powered by IoT and machine learning, will allow manufacturers to foresee potential issues before they lead to machine downtime, keeping operations running smoothly.
As sustainability becomes more important in manufacturing, future systems may also feature energy-efficient designs and incorporate closed-loop systems to recycle polishing fluids, reducing waste and environmental impact. Moreover, innovations in polishing technology, such as the use of green abrasives or eco-friendly compounds, will contribute to making these machines more environmentally conscious.
In conclusion, automatic load/unload polishing machines represent a significant leap forward in manufacturing automation. By automating the loading and unloading processes, they increase efficiency, reduce labor costs, and enhance precision, all while ensuring consistent surface finishes. As industries continue to demand faster production and higher quality, these machines will continue to evolve, incorporating the latest technologies to meet the needs of modern manufacturing environments.
Automotive Parts Polishing Machine
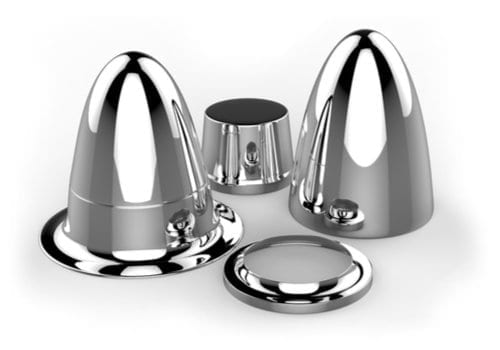
An automotive parts polishing machine is a specialized piece of equipment designed to give automotive components a smooth, shiny, and uniform finish. These machines are essential in the automotive manufacturing industry to enhance the aesthetic and functional qualities of various parts, including engine components, exterior panels, trim pieces, wheels, and more. Polishing is a crucial finishing process that not only improves the visual appeal of automotive parts but also enhances their durability and performance.
The machine’s main function is to polish and smooth surfaces through a combination of abrasive materials and controlled motion. It is used for a variety of automotive parts made from materials such as steel, aluminum, plastic, brass, copper, and other alloys commonly found in the automotive industry.
Key Features and Benefits of Automotive Parts Polishing Machines
- Surface Finish Quality Automotive parts often require a smooth, shiny finish, particularly for visible components like chrome trim, bumpers, grills, wheels, and engine covers. Polishing machines help achieve these high-quality finishes, removing imperfections like scratches, oxidation, pitting, and scuff marks to provide a mirror-like shine or a satin finish, depending on the requirements. The smooth finish can also help improve the part’s resistance to corrosion and enhance its overall performance.
- Customization for Different Parts Automotive parts vary widely in size, shape, and material composition. Polishing machines are often designed to handle different types of parts, whether they are large, intricate engine components, small interior trim pieces, or external body parts. Machines can be customized to accommodate parts of various shapes, such as curved, flat, or irregular geometries. Adjustable settings for speed, pressure, and polishing tool type allow manufacturers to tailor the polishing process for each specific part.
- Efficiency and Productivity Polishing automotive parts manually can be time-consuming and inconsistent, particularly for high-volume production environments. Automotive parts polishing machines automate this process, significantly improving throughput and efficiency. Automated systems reduce downtime between cycles, increasing the overall productivity of the production line. Machines can operate continuously, polishing multiple parts simultaneously or sequentially, depending on the design and requirements.
- Multiple Polishing Stages Many automotive parts require more than one stage of polishing to achieve the desired finish. For instance, a part may go through a rough polishing stage to remove large imperfections, followed by fine polishing to achieve a smooth, reflective surface. Two-stage or multi-stage polishing systems are often employed to ensure that parts are polished to the exact specifications at each step of the process. Different abrasives, polishing compounds, or pads are used at each stage to gradually refine the surface.
- Consistency and Precision Achieving a uniform surface finish across all parts is essential for high-quality automotive manufacturing. Polishing machines provide consistent results by controlling parameters such as pressure, speed, and abrasive selection, ensuring that all parts are polished evenly. This level of precision is especially important for parts that require specific tolerances or fitment in the assembly process, such as engine components or wheel rims.
- Reduction in Labor Costs Automating the polishing process reduces the need for manual labor, which is often time-consuming and can result in variability in quality. By reducing manual intervention, automotive parts polishing machines lower labor costs while ensuring that each part is polished to the same high standard. This is particularly advantageous in high-volume production, where consistency and speed are critical.
- Polishing of Diverse Materials Automotive parts are made from a variety of materials, and each material requires a different polishing approach. Polishing machines are adaptable to handle a wide range of materials commonly used in automotive parts, such as aluminum alloys, stainless steel, plastic, and painted surfaces. The ability to switch between polishing materials or use different abrasives based on the material type ensures that the machine can deliver high-quality results regardless of the part’s composition.
- Dust and Contamination Control Polishing automotive parts can generate dust and abrasive particles that may compromise both the cleanliness of the work environment and the quality of the parts. Many modern automotive polishing machines are equipped with dust extraction systems and closed-loop filtration systems to collect and remove harmful particles from the air. This helps ensure that the parts remain free from contaminants that could affect their finish or performance, especially for highly sensitive components like engine parts or brake systems.
- Environmental Considerations Environmental concerns are increasingly influencing the design of automotive polishing machines. Some machines are equipped with energy-efficient motors, low-vibration systems, and eco-friendly polishing compounds to minimize their environmental impact. Additionally, closed-loop systems that recycle polishing fluids reduce waste, while dust extraction and filtration technologies ensure that the operation remains as environmentally friendly as possible.
- Robotic Integration For larger or more complex polishing tasks, robotic arms can be integrated with polishing machines to enhance flexibility and precision. Robotic systems allow for the automation of part handling, while robotic polishing arms can adapt to the shape and size of the parts being polished, providing a high level of precision. Robotic integration allows for more complex or delicate components to be polished without the risk of human error or damage.
Types of Automotive Parts Polishing Machines
- Belt Polishing Machines: These machines use continuous abrasive belts to polish automotive parts, commonly employed for large or flat components such as exterior panels, bumpers, and grills. Belt machines are ideal for removing oxidation, corrosion, and scratches from surfaces.
- Disc Polishing Machines: Disc polishing machines are typically used for smaller automotive parts or those that require a finer finish. The polishing process uses rotating discs to polish parts such as engine components, brake parts, and metal trim.
- Brush Polishing Machines: These machines use rotary brushes to polish parts. They are well-suited for delicate or intricate parts, such as chrome parts or interior trim pieces, where a gentler polishing action is needed.
- Rotary Polishing Machines: Rotary machines are versatile and used for both fine and rough polishing applications. They are often used in a variety of automotive parts, from engine covers to wheels, and provide efficient polishing with minimal part distortion.
- CNC Polishing Machines: For parts with complex geometries or strict tolerance requirements, CNC (Computer Numerical Control) polishing machines are used. These machines allow precise control over the polishing process and are often used for custom or high-precision automotive parts.
- Automated Polishing Systems: High-volume automotive manufacturers often utilize fully automated polishing systems. These systems feature robotic arms and conveyors that move parts between polishing stations, eliminating the need for human intervention and significantly improving efficiency.
Applications in the Automotive Industry
Automotive parts polishing machines are used across a wide range of applications, including:
- Exterior Trim Parts: Parts such as bumpers, grills, chrome trim, and wheel rims benefit from polishing machines that provide a smooth, shiny surface and remove imperfections.
- Engine Components: Polishing is often required for engine parts such as cylinder heads, valve covers, and exhaust systems, where smooth surfaces contribute to better heat dissipation and improved performance.
- Interior Parts: Components like dashboard trim, gear knobs, door handles, and center consoles often undergo polishing to improve both aesthetic appearance and tactile feel.
- Braking Systems: Parts like rotors and brake calipers are polished to ensure smooth operation, reduce wear, and extend the lifespan of braking components.
- Electrical Components: Items such as battery terminals, alternator housings, and electrical connectors require polishing to ensure proper conductivity and reduce the risk of corrosion.
Conclusion
An automotive parts polishing machine is an essential tool in modern automotive manufacturing, providing high-quality finishes to a wide variety of parts. These machines offer numerous benefits, including enhanced efficiency, consistency, and productivity, while reducing labor costs and ensuring precision in polishing. The ability to handle diverse materials and part sizes makes them an indispensable tool for automotive manufacturers, whether they are working with metal, plastic, or other materials. As the automotive industry continues to evolve, the demand for more advanced polishing machines that can integrate with robotic automation and handle more complex parts will continue to grow.
An automotive parts polishing machine is an essential tool in the automotive manufacturing industry, designed to give automotive components a high-quality surface finish. These machines are used for polishing various automotive parts, such as exterior panels, wheels, engine components, and trim pieces, with the goal of enhancing both the aesthetic appeal and functionality of the parts. The primary function of these machines is to remove imperfections like scratches, oxidation, and corrosion, leaving the parts with a smooth, shiny, or satin finish that improves their visual appearance and extends their lifespan.
The polishing process in these machines can vary depending on the part being polished, its material composition, and the desired finish. Typically, the polishing machines use abrasive materials like polishing pads, abrasive belts, or brushes, which rotate or move in a controlled manner to achieve the desired surface texture. The machines are designed to handle different types of materials commonly used in automotive parts, such as aluminum alloys, steel, plastic, and chrome. By adjusting parameters like speed, pressure, and abrasive type, manufacturers can fine-tune the polishing process for each specific part, ensuring consistent results across large production runs.
One of the significant advantages of using an automotive parts polishing machine is the efficiency it brings to the manufacturing process. In high-volume production environments, polishing parts manually would be time-consuming and prone to inconsistencies. Automating the polishing process not only speeds up production but also ensures that each part receives a uniform finish. This reduces human error, maintains high levels of consistency, and improves productivity. By increasing throughput and reducing manual labor, automotive polishing machines help manufacturers meet the high demands of modern automotive production while maintaining quality standards.
Polishing machines are equipped with various features to adapt to the specific requirements of automotive parts. Some machines are designed for rough polishing, where the goal is to remove oxidation, corrosion, or heavy scratches, while others are used for fine polishing, where a smooth, mirror-like finish is required. In many cases, parts undergo multiple stages of polishing, with the use of different abrasives or polishing compounds at each stage. This multi-step process ensures that the parts achieve the required surface finish while also preventing the risk of damaging delicate parts.
Moreover, the polishing process is essential not only for the aesthetic quality of automotive parts but also for their performance. For example, in parts such as engine components, brake systems, and exhaust manifolds, polishing contributes to improved heat dissipation, reduced friction, and better corrosion resistance. In some cases, a properly polished surface can also enhance the fitment of parts, ensuring that they function optimally within the assembly line or throughout the vehicle’s lifespan.
Automated polishing machines also help reduce the need for manual labor. While polishing can be a physically demanding and repetitive task, automated systems take over this responsibility, reducing the need for skilled operators and minimizing the risk of human error. This shift allows the workforce to focus on more technical tasks, increasing overall labor efficiency and reducing costs associated with human labor.
In addition to polishing, modern automotive parts polishing machines often feature advanced systems for dust extraction and filtration, ensuring that the work environment remains clean and that parts are not contaminated during the polishing process. These systems help improve the quality of the finish and prevent any particulate matter from interfering with the polishing or settling onto the parts being processed.
As automotive manufacturers continue to pursue sustainability and efficiency in their production lines, the design of polishing machines is also evolving. Manufacturers are increasingly incorporating energy-efficient motors, closed-loop fluid recycling systems, and eco-friendly polishing compounds to reduce the environmental impact of the polishing process. Additionally, some machines are equipped with robotic arms or conveyor systems to further automate the part-handling process, ensuring that parts are positioned and polished with high precision.
In the future, we can expect automotive parts polishing machines to become even more intelligent, incorporating technologies like artificial intelligence (AI) and machine learning. These advancements would enable machines to adapt to changes in part geometry or material composition, optimizing the polishing process in real-time. Predictive maintenance, powered by IoT (Internet of Things) sensors, will also become more prevalent, allowing manufacturers to anticipate when maintenance is required and reduce downtime.
The range of applications for automotive parts polishing machines is broad, as they are used for polishing parts across various areas of vehicle manufacturing. From chrome bumpers and wheel rims to engine components and interior trim, these machines play a crucial role in ensuring that automotive parts meet the required standards of quality, appearance, and functionality. Whether working with metal, plastic, or other materials, automotive parts polishing machines are versatile enough to handle a variety of components, making them indispensable in automotive manufacturing.
In conclusion, automotive parts polishing machines are vital to ensuring that the parts produced in the automotive industry not only meet stringent quality standards but also contribute to the overall performance, durability, and visual appeal of the final vehicle. The automation of the polishing process provides significant advantages in terms of efficiency, precision, consistency, and cost-effectiveness, while also enabling manufacturers to maintain high standards of quality control. As technological advancements continue, these machines will evolve to become even more automated, adaptive, and sustainable, further shaping the future of the automotive manufacturing industry.
Automotive parts polishing machines are also central to maintaining high standards of safety within the industry. Polishing critical components such as brake discs, suspension parts, and steering components ensures that they function as intended, with smooth, uniform surfaces that minimize wear and enhance performance. For instance, brake rotors require a precisely polished surface to ensure consistent friction and to prevent overheating or warping, both of which could compromise the safety of the vehicle. Similarly, engine components like cylinder heads and valve covers benefit from polishing as it reduces the potential for build-up, friction, and wear, contributing to engine longevity and efficiency.
Another area where polishing machines play a vital role is in aesthetic consistency for the automotive industry. Whether it’s polishing chrome finishes on a vehicle’s exterior or giving the final sheen to interior decorative parts, a consistent finish ensures that all parts meet the visual standards expected by customers. For premium or luxury vehicles, where the finish quality is integral to the overall design and appeal, polishing machines help to achieve a flawless surface that reflects light evenly and creates a premium look.
As vehicle designs become more intricate, especially with the rise of electric vehicles (EVs) and autonomous vehicles, the types of parts being polished are also becoming more complex. For example, some EV manufacturers require polishing of intricate battery enclosures or charging ports, which must not only look good but also function without compromising the safety and performance of the vehicle. The high precision needed for these parts often calls for robotic-assisted polishing systems that can adjust their motions based on part geometry or shape, making them more versatile and capable of handling custom parts.
The growing focus on lightweight materials in automotive manufacturing, such as carbon fiber, aluminum alloys, and composite materials, also adds a layer of complexity to the polishing process. These materials may require specialized polishing compounds and techniques to avoid damage during the process. Polishing machines designed for such materials often feature custom abrasives and flexible polishing heads that can mold to the part’s surface, ensuring a consistent finish without causing damage to the lightweight yet fragile materials. These machines are becoming essential as the automotive industry pushes for more fuel-efficient, sustainable, and high-performance vehicles.
The integration of advanced robotics and AI-driven systems is further transforming automotive parts polishing machines. With the increasing demand for customization and the growing number of unique parts being produced, robots are increasingly handling the polishing process. Robots equipped with vision systems can identify the part’s shape, material, and any imperfections, adjusting their actions accordingly. This allows the machine to automatically optimize the polishing parameters for each part, ensuring maximum efficiency and consistency while reducing the chance of human error. Additionally, AI algorithms can predict the wear and tear on the polishing tools, ensuring that parts are polished to perfection without the need for frequent adjustments.
As the automotive industry continues to prioritize sustainability, manufacturers are looking for ways to reduce the environmental impact of the polishing process. Innovations in this area include the development of eco-friendly abrasives and recyclable polishing fluids, which help reduce waste and consumption of resources. Machines with closed-loop systems for fluid recovery are becoming more common, allowing manufacturers to recycle polishing fluids, reducing costs and minimizing environmental impact. The trend toward green manufacturing also extends to the energy efficiency of the polishing machines themselves, with newer models designed to consume less power while still delivering the necessary performance.
In terms of maintenance, these machines are often equipped with smart sensors that monitor performance and wear. These sensors can provide real-time data to operators, alerting them to any abnormalities or the need for maintenance, which helps minimize downtime and prevent breakdowns. Predictive maintenance techniques, powered by data analytics, allow manufacturers to plan maintenance schedules more effectively, further improving the efficiency of production lines and reducing unexpected downtimes that could disrupt the manufacturing process.
The versatility and precision of automotive parts polishing machines are also becoming essential in the production of aftermarket parts. Aftermarket products often require unique finishes and more intricate designs, and polishing machines can be customized to meet these needs. Whether it’s for custom car parts like exhaust pipes, mirror trims, or performance accessories, polishing machines provide the necessary tools for producing high-quality, visually appealing products that stand out in the marketplace.
The demand for quality assurance in automotive parts manufacturing is also leading to the implementation of integrated inspection systems in polishing machines. By incorporating sensors that monitor surface quality during the polishing process, manufacturers can ensure that each part meets required specifications before moving on to the next stage in the production process. This approach helps reduce defects and ensures that only parts meeting the highest standards reach customers.
Moreover, as the automotive market moves toward globalization, with companies looking to produce parts for different markets with varying requirements, the ability to standardize polishing processes across different production facilities is crucial. Automated polishing machines are being designed to offer remote control and monitoring capabilities, enabling companies to oversee operations across multiple factories and ensure that processes are consistent worldwide. This connectivity also aids in troubleshooting and optimization, allowing operators and engineers to remotely adjust settings, monitor progress, and ensure uniformity in production.
Looking ahead, the future of automotive parts polishing machines will likely be influenced by advancements in additive manufacturing (3D printing). As 3D printing becomes more prevalent in automotive manufacturing, particularly for creating complex, customized parts, polishing machines will need to adapt to handle the unique surfaces produced by additive processes. This could include the development of specialized tools or polishing methods tailored for printed metals or composite materials, ensuring that 3D-printed components can achieve the same level of quality as traditionally manufactured parts.
In conclusion, automotive parts polishing machines are integral to the modern automotive manufacturing process. They not only improve the visual appeal of the parts but also enhance their functional performance, contributing to safety, durability, and efficiency. With advancements in robotics, AI, and sustainable manufacturing practices, these machines will continue to evolve, offering more precision, flexibility, and environmental responsibility. The ability to handle a wide range of materials, part geometries, and customization requirements makes them indispensable in the automotive industry, particularly as the sector continues to innovate and produce increasingly sophisticated vehicles.
Medical Instrument Polishing Machine
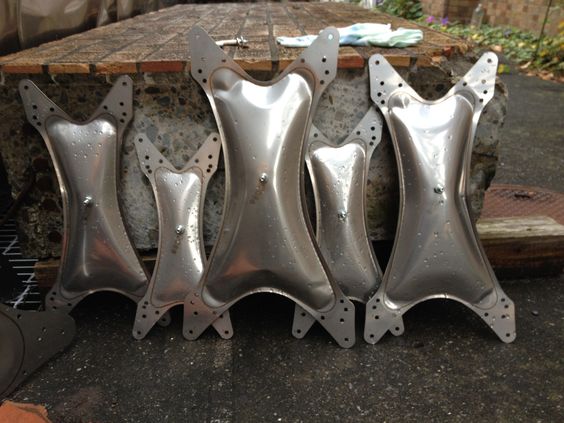
A medical instrument polishing machine is a specialized machine used to finish and refine medical instruments to meet strict standards of smoothness, cleanliness, and precision. These machines are used to polish various medical devices and instruments, ensuring that they are free of rough edges, burrs, or imperfections that could affect their functionality or the safety of patients. Polishing medical instruments is a crucial step in the manufacturing process because it improves the aesthetic appearance, sterilization readiness, and overall performance of these tools. Medical instruments such as scalpels, forceps, scissors, surgical knives, and needles benefit from the polishing process, which provides a smooth, shiny finish and ensures safety and ease of use.
Key Features and Benefits of Medical Instrument Polishing Machines:
- Smooth Surface Finish: The primary function of medical instrument polishing machines is to remove sharp edges, rough surfaces, and micro burrs that can result from the machining, cutting, or molding processes. These imperfections can lead to injuries or make it difficult for healthcare professionals to use the instruments correctly. The polishing process ensures that instruments have a smooth surface that is safe for both the practitioner and the patient. A smooth surface also helps prevent infections as it minimizes places where bacteria can accumulate.
- Precision and Consistency: Given the critical nature of medical instruments, precision and consistency are paramount. Polishing machines used in the medical field are highly accurate, ensuring that all parts of the instrument receive an even finish. Whether polishing small tips or larger components, the machines provide uniform results, ensuring that instruments meet medical standards for performance, safety, and quality. This level of precision is necessary for parts that must operate in highly sensitive environments, such as in surgery or diagnostic procedures.
- Material Compatibility: Medical instruments are made from various materials, including stainless steel, titanium, ceramics, and plastic. Each of these materials requires a different polishing approach, and medical instrument polishing machines are designed to accommodate this diversity. The machines are equipped with a variety of polishing wheels, abrasive belts, and pads suited to the material being polished. Specialized tools and techniques are used to ensure that materials such as hardened steel or titanium alloys are polished without damaging their structural integrity.
- Enhanced Durability: Polishing helps improve the corrosion resistance of medical instruments by ensuring that surfaces are free from imperfections that could promote rust or degradation over time. This is particularly important for instruments used in surgical procedures, which are exposed to frequent cleaning and sterilization. By enhancing the surface finish, polishing machines extend the lifespan of medical instruments, ensuring they continue to function effectively and safely for a long period.
- Cleaning and Sterilization: A polished surface makes cleaning and sterilization processes more efficient. Polished instruments are easier to clean because smooth surfaces do not retain dirt, blood, or biological materials as much as rough ones. This helps in achieving better sterilization and reduces the risk of infections. Additionally, polished instruments are more resistant to staining and oxidation, maintaining their cleanliness and appearance even after repeated cleaning and sterilization cycles.
- High Throughput and Efficiency: Medical instrument polishing machines are designed for high-volume production environments where consistent quality is critical. These machines can be automated, reducing the need for manual labor and increasing throughput while maintaining consistent polishing results. Automated polishing systems can handle large quantities of medical instruments in a short period, increasing overall efficiency in manufacturing operations. This is especially important for manufacturers producing instruments in bulk or for hospitals and clinics with high demands.
- Cost-Effectiveness: Polishing medical instruments by machine is more cost-effective than manual polishing, especially when dealing with large volumes. Automated machines not only reduce labor costs but also minimize the chances of human error, ensuring that instruments meet the highest standards without additional rework. This contributes to significant cost savings in both labor and material waste, making the polishing process more efficient and affordable in mass production.
- Compliance with Industry Standards: Medical instruments must meet stringent regulatory requirements set by healthcare authorities such as the FDA (Food and Drug Administration) and ISO (International Organization for Standardization). These standards govern the quality, performance, and safety of medical instruments, including the surface finish. Polishing machines help manufacturers adhere to these regulations by providing reliable and consistent surface finishes that ensure compliance with both national and international standards.
- Customization for Specific Instruments: Different types of medical instruments may require unique polishing processes depending on their shape, size, and intended use. For example, scalpels and surgical scissors require precise edge polishing, while forceps and tweezers may require different polishing methods for their tips and gripping areas. Medical instrument polishing machines can be adjusted or customized to polish various shapes and configurations, ensuring that each instrument receives the appropriate treatment for its specific needs.
- Automated Load/Unload Systems: Some advanced polishing machines incorporate automated load and unload systems, allowing for seamless handling of instruments. These systems transport instruments into and out of the polishing area, reducing manual handling and improving overall workflow efficiency. This level of automation reduces human contact with instruments and ensures a consistent polishing process from start to finish.
Types of Medical Instrument Polishing Machines:
- Belt Polishing Machines: These machines use abrasive belts that rotate around pulleys to polish the surface of medical instruments. They are suitable for larger parts or parts with flat surfaces, such as scalpel handles or forceps. Belt polishing is ideal for removing rough surfaces or finishing hard metals.
- Disc Polishing Machines: These use rotating discs coated with polishing compounds to smooth the surface of smaller, more delicate parts. Scissors, scalpels, and other precision tools are often polished using this method, which can be adjusted to different speeds and pressures to ensure a fine finish.
- Brush Polishing Machines: For more delicate or intricate instruments, brush polishing is often used. The brushes gently polish without causing damage to the tool, making them ideal for fine tips and delicate edges of medical instruments like forceps or surgical blades.
- CNC Polishing Machines: These highly automated machines use computer numerical control (CNC) to precisely control the polishing process, making them suitable for high-precision instruments. CNC machines can handle complex shapes and ensure uniformity in the polishing of intricate medical devices like orthopedic tools or implantable devices.
- Rotary Polishing Machines: Rotary machines employ rotating pads or wheels that apply even pressure to the surface. This method is often used in both rough polishing and fine polishing, making it versatile for a range of instruments, including surgical knives, dental tools, and scissors.
- Ultrasonic Polishing Machines: Some medical instruments, particularly those with complex geometries, are polished using ultrasonic vibration. This method is used to clean and polish delicate tools, such as micro-needles, with high-frequency sound waves that ensure a smooth, uniform surface without damaging the instrument.
Applications in the Medical Industry:
- Surgical Instruments: Instruments like scalpels, forceps, scissors, scalpels, and needle holders require polishing to ensure they are safe and functional for surgery. The sharpness and smoothness of these tools are crucial for precise incisions and minimizing tissue damage during operations.
- Diagnostic Tools: Instruments used for diagnostic purposes, such as endoscopes, catheters, and surgical probes, require polishing to ensure they are smooth, easily sterilized, and free of any imperfections that could hinder their performance or lead to infections.
- Dental Instruments: Dental tools such as scalers, cleaning devices, and dental probes need a smooth finish to ensure patient comfort and effectiveness. Polishing ensures that these instruments are not only functional but also aesthetically pleasing.
- Orthopedic Instruments: Bone drills, plates, and screws are polished to ensure smooth surfaces for insertion, minimizing friction and the risk of infections. Polishing is essential to create surfaces that are suitable for implantation and long-term use.
- Implantable Devices: Polishing machines are used for devices like artificial joints, stents, and dental implants to ensure that the surface is smooth and sterile, promoting better integration with the body and reducing the risk of complications.
Conclusion:
A medical instrument polishing machine plays a critical role in ensuring the quality and safety of medical instruments. By providing a smooth, precise finish, these machines help enhance the functionality, durability, and aesthetic appeal of medical devices. They also contribute to patient safety by ensuring that instruments are free from imperfections that could cause injury or infection. As the demand for high-quality, reliable medical instruments grows, polishing machines continue to evolve with automated systems, robotic arms, and AI-powered monitoring for even greater precision, efficiency, and compliance with medical standards. These machines will remain indispensable in the manufacturing of medical devices, ensuring that healthcare professionals have the tools they need to deliver the best care to patients.
Medical instrument polishing machines are crucial in ensuring that instruments used in healthcare settings meet the highest standards of safety, functionality, and cleanliness. They are designed to handle the delicate requirements of polishing various medical devices such as scalpels, forceps, scissors, surgical knives, needles, and dental tools, providing a smooth, precise finish that minimizes the risks associated with rough edges or imperfections. The polishing process eliminates sharp burrs, reduces friction, and improves the sterilization readiness of instruments, making them safer and more effective for use in procedures.
The machines used in polishing medical instruments come with advanced features that enable precise control over the polishing process. They can adjust for different materials, whether stainless steel, titanium, or ceramics, ensuring each instrument receives the appropriate level of treatment without damaging its structural integrity. This is particularly important for materials that are susceptible to wear, corrosion, or degradation over time. With the increasing focus on precision and patient safety, polishing machines must deliver consistent results to meet the stringent regulatory standards imposed by health authorities, including the FDA and ISO certifications.
Automation has become a key aspect of these polishing systems, allowing for high throughput and efficiency in large-scale production. Automated polishing machines are designed to process instruments quickly while maintaining high levels of accuracy and uniformity. This ensures that even in high-demand settings, such as hospitals, clinics, or large medical device manufacturers, instruments are polished consistently and on time. The integration of robotic arms and CNC technology enhances the ability to polish even the most intricate parts, offering customized solutions for different instrument shapes and sizes.
The role of polishing extends beyond surface finishing—it significantly contributes to the overall performance and durability of medical instruments. For example, polishing can improve the sharpness of cutting tools like scalpels and surgical knives, making them more effective for precise incisions. In tools like forceps or tweezers, smooth tips are essential for a firm and comfortable grip during procedures, while the polished surfaces also reduce wear and tear, extending the life of the instruments.
In addition to improving functional performance, polished instruments are easier to clean and sterilize. The smooth surfaces do not retain dirt, blood, or other biological material, which helps prevent contamination and promotes effective sterilization. This feature is especially critical in preventing hospital-acquired infections (HAIs), which can occur if instruments are not properly sterilized. Smooth, polished surfaces also make it easier for practitioners to work with the instruments, as there is less resistance when manipulating them, improving precision and reducing the risk of mishaps.
The shift toward sustainable and environmentally responsible manufacturing practices has also influenced the development of medical instrument polishing machines. Many machines now use eco-friendly polishing compounds, and closed-loop systems are being implemented to recycle polishing fluids, reducing waste and ensuring that the production process is more resource-efficient. This is in line with the broader push for green manufacturing practices, as the medical industry seeks to reduce its environmental footprint while maintaining high standards of quality and safety.
The future of medical instrument polishing is likely to see even more advanced automation, with the integration of AI and machine learning. These technologies can monitor the polishing process in real-time, detecting issues like uneven polishing, surface defects, or wear on polishing components. By continuously learning from the data gathered, the systems can adjust automatically to optimize the process, reducing human intervention and minimizing errors. Smart sensors embedded in polishing machines could track the condition of each instrument, ensuring that it is polished to the exact specifications required before moving on to the next stage of production.
Furthermore, the customization of polishing processes is becoming increasingly important as manufacturers cater to more specialized medical instruments. Polishing machines can now be tailored to suit specific procedures or individual instrument designs, ensuring that every tool, whether it’s a micro-needle, surgical probe, or dental scaler, receives the precise finish it needs. This allows manufacturers to meet the growing demand for customized and precision-engineered medical tools that are essential for specialized surgeries or advanced diagnostic procedures.
In the context of implantable devices, polishing machines are vital in ensuring that components like prosthetics, dental implants, or orthopedic implants have smooth, biocompatible surfaces that will reduce the risk of complications once implanted in the human body. The polishing process ensures these devices not only meet aesthetic expectations but also perform reliably and are compatible with the body’s tissue.
In summary, medical instrument polishing machines are indispensable in the medical manufacturing process, ensuring that instruments are not only functional but also safe, durable, and easy to sterilize. As technology continues to advance, these machines will become more efficient, precise, and adaptable, allowing for the production of increasingly complex and high-performance medical instruments. The ongoing integration of automation, robotics, and AI will further enhance their capabilities, helping manufacturers meet the evolving needs of the healthcare industry while maintaining the highest standards of safety and quality.
Metal Furniture Polisher
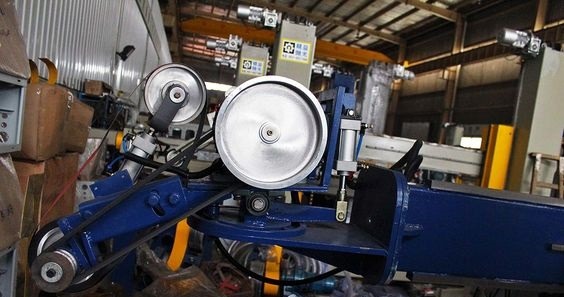
A metal furniture polisher is a specialized machine or tool used to smooth, polish, and finish metal surfaces on furniture pieces. This type of polisher is designed to enhance the aesthetic appeal, durability, and smoothness of metal components used in furniture like tables, chairs, shelves, frames, and cabinets. Whether it’s stainless steel, aluminum, brass, or iron, metal furniture polishers are essential for achieving the desired finish that is both visually appealing and functional.
The primary purpose of a metal furniture polisher is to remove imperfections such as scratches, dents, or rough spots, leaving a clean, shiny, and even surface. The polishing process also helps in removing oxidation, rust, and other contaminants that can degrade the quality of the metal and impact the furniture’s longevity. Additionally, it prepares the surface for protective coatings or paint, ensuring that the finish adheres well and lasts longer.
Types of Metal Furniture Polishers:
- Belt Polishers: These machines use rotating abrasive belts to smooth and polish metal surfaces. They are ideal for larger metal pieces or surfaces with flat or curved geometry, such as metal frames or furniture legs. Belt polishers are often used for removing rough spots and preparing surfaces for further finishing.
- Disc Polishers: Similar to belt polishers, disc polishers use rotating discs to apply abrasive materials to the metal. They are often used for more detailed polishing tasks and are suitable for smaller components like metal handles, brackets, or intricate design elements. Disc polishers can be fitted with different grades of abrasives to achieve varying levels of finish.
- Brush Polishers: Brush polishing machines use rotating brushes, often made of nylon, steel, or natural fibers, to polish metal surfaces. These machines are gentle on the material and are typically used for more delicate finishes, such as polishing ornate metalwork or fine details. Brush polishers can be used to bring out a matte or satin finish on metal surfaces, depending on the type of brush and polishing compound used.
- Robotic Polishers: Advanced polishing machines use robotic arms to precisely polish metal furniture components. These machines are fully automated and capable of high-volume polishing with consistent quality. Robotic polishers are often used in industrial settings for high-speed production of furniture pieces and can handle complex shapes and difficult-to-reach areas.
- Centrifugal Polishers: These machines use centrifugal force to apply polishing media to the metal surface. They are particularly useful for polishing smaller metal components or when a high degree of precision is required. Centrifugal polishers are effective at removing small imperfections and achieving a smooth, shiny surface on furniture components.
- Handheld Polishers: For smaller or more intricate tasks, handheld polishing tools are often used. These are portable and can be equipped with a range of polishing attachments like buffing wheels, abrasive pads, and sanding discs. Handheld polishers are ideal for fine detail work and are often used by craftsmen or in finishing touches.
Benefits of Metal Furniture Polishers:
- Enhanced Aesthetic Appeal: Metal furniture polishers help create a shiny, smooth surface that enhances the overall appearance of metal furniture. This polished finish is desirable for items like modern metal tables, chairs, and shelving units, as it gives them a premium look.
- Durability and Longevity: Polishing not only enhances the appearance but also protects the metal surface by removing oxidized layers, rust, and contaminants. This helps prevent future corrosion and extends the life of the furniture.
- Improved Cleaning and Maintenance: A smooth, polished metal surface is easier to clean, as it resists dirt accumulation and tarnishing. Regular polishing helps maintain the shine and integrity of the metal, reducing the need for frequent deep cleaning.
- Surface Preparation for Coatings: Metal furniture polishers prepare the metal surface for painting or coating by removing debris and ensuring a smooth surface for adhesion. This is especially important for metal furniture that is painted or coated for additional protection against the elements.
- Increased Resistance to Wear: Polished metal surfaces are generally more resistant to scratches and damage, which is important for furniture used in high-traffic areas or furniture that is exposed to the elements. The smooth finish reduces the chances of wear and tear.
Applications in Metal Furniture Production:
- Home Furniture: Metal furniture such as bed frames, dining tables, cabinets, and chairs benefit from polishing machines to create a clean, shiny finish that adds to the furniture’s aesthetic value and appeal.
- Outdoor Furniture: Metal furniture used outdoors, like patio sets, bistro tables, and lounge chairs, often undergoes polishing to ensure the metal is resistant to corrosion from exposure to weather elements like rain and humidity.
- Commercial and Industrial Furniture: In commercial and industrial settings, metal furniture polishers are used to maintain large-scale furniture pieces, such as workstations, storage units, tool cabinets, and shelving systems. A polished surface on such furniture not only improves its look but also enhances its durability and ease of maintenance.
- Art and Decorative Metal Furniture: For decorative metal pieces and artistic furniture designs, polishing is essential to achieve fine, high-quality finishes that highlight the intricate craftsmanship and design details. Artists and manufacturers use specialized polishing techniques to enhance the final look of these pieces.
In conclusion, metal furniture polishers play a critical role in achieving high-quality finishes for metal furniture. They ensure that the metal is smooth, polished, and ready for use in both functional and decorative applications. Whether through belt, disc, brush, or robotic polishing, these machines ensure the metal furniture meets both aesthetic and durability standards, contributing to the overall quality and longevity of the product.
Metal furniture polishers are versatile tools used to enhance the appearance and functionality of metal furniture. They work by polishing, smoothing, and finishing metal surfaces to achieve a clean, shiny, and even surface. Whether the furniture is made from stainless steel, aluminum, brass, iron, or other metals, these polishers are designed to handle a wide range of materials and produce high-quality finishes. The primary goal is to remove imperfections like scratches, dents, and rough patches, leaving behind a smooth and polished surface. This improves the visual appeal of the furniture and also makes it easier to maintain and clean.
The polishing process also helps to remove oxidation, rust, and other contaminants that may degrade the quality of the metal and reduce its longevity. By using a metal furniture polisher, manufacturers can improve both the durability and aesthetic value of metal pieces. In addition to enhancing the surface quality, polishing prepares metal surfaces for further processes such as painting, coating, or plating, ensuring that finishes like paint or protective coatings adhere more effectively.
Metal furniture polishers are available in a variety of designs, such as belt polishers, disc polishers, brush polishers, and robotic polishers, each catering to different types of furniture and polishing needs. For example, belt polishers are ideal for larger, flat metal pieces like table bases or chair frames, while brush polishers are better suited for more delicate and intricate metalwork, offering a softer touch for polished finishes. Robotic polishers are used in high-volume production environments, offering consistency and precision in finishing intricate designs or hard-to-reach areas.
The polishing process can also improve corrosion resistance by smoothing out metal surfaces, reducing the likelihood of rust or oxidation forming. This is especially important for metal furniture intended for outdoor use, as exposure to the elements can accelerate the degradation of the metal. Polishing helps to prevent these issues and ensure the longevity of the furniture.
Another key benefit is that polished metal surfaces are much easier to clean, as dirt, dust, and grime are less likely to adhere to a smooth surface. This makes metal furniture not only look better but also more hygienic and easier to maintain, which is especially important for furniture used in high-traffic or commercial environments.
In commercial, industrial, and residential settings, metal furniture polishers are essential in achieving a consistent and high-quality finish. Whether for home furniture, such as dining tables or bed frames, outdoor furniture, or more specialized items like decorative metal pieces or commercial furniture, these machines ensure the furniture meets the standards of both aesthetics and durability. As technology continues to evolve, metal furniture polishers are becoming more efficient, precise, and automated, improving both the production process and the quality of the finished product.
Exhaust Pipe Polishing Line

An exhaust pipe polishing line is a specialized system used in the automotive industry to polish and finish exhaust pipes. The primary function of this polishing line is to improve the aesthetic appearance, smoothness, and corrosion resistance of exhaust pipes. These pipes are often made from materials such as stainless steel or aluminum, and the polishing process helps ensure that the pipes are visually appealing, smooth to the touch, and durable over time.
The process typically involves several stages, including cleaning, abrasive polishing, and finishing, to achieve the desired finish. The polishing line usually consists of a series of machines or stations, each with a specific purpose, that work together to polish the exhaust pipes efficiently.
The first stage in the polishing line may involve removal of surface contaminants, such as oils, dust, or oxidation. This is typically done using abrasive blasting or a grinding process to prepare the pipe surface for the polishing stages. Once the pipes are cleaned, the next step is the abrasive polishing, where different grades of abrasive materials or polishing pads are applied to remove imperfections, scratches, and any rough spots.
Next, high-speed polishing machines are often used, where rotating abrasive wheels or pads apply pressure to the surface of the exhaust pipe. These machines use various techniques, such as rotary motion or vibratory polishing, to ensure an even, smooth finish. Different grades of abrasives can be used during this process to achieve various levels of finish, ranging from a satin finish to a high-gloss, mirror-like finish. The exhaust pipe is rotated or moved through these machines to achieve a consistent polish along its entire length.
Some lines may also include automatic polishing stations, which use robotic arms or automated systems to polish the pipes. These systems can be programmed to polish the pipes based on specific requirements, such as the pipe’s shape, size, or material, ensuring that each piece receives the correct amount of attention for a uniform finish.
After the polishing process, a final cleaning stage is typically necessary to remove any remaining abrasive materials or polishing compounds. The pipes may also undergo an inspection process to check for any imperfections or inconsistencies in the finish before they are sent to the packaging or shipping area.
The exhaust pipe polishing line can be set up for either manual or automated operation, depending on the scale of production. For large-scale manufacturing, fully automated lines equipped with conveyor systems, robotic arms, and CNC-controlled polishing machines can polish hundreds or thousands of exhaust pipes in a short period, ensuring high throughput and precision. Manual lines, on the other hand, are more suited for smaller production volumes or custom exhaust systems where hand-polishing is required for intricate or specialized work.
The benefits of using an exhaust pipe polishing line include improved visual appeal, better resistance to corrosion, and enhanced durability of the exhaust pipe. A polished surface can help to prevent the buildup of contaminants and corrosion, which can degrade the exhaust system over time, leading to a longer lifespan for the vehicle’s exhaust components.
Furthermore, the polished finish can also contribute to better heat dissipation, as smooth surfaces may reduce the amount of heat buildup along the surface, improving the performance of the exhaust system. Additionally, polished exhaust pipes are often preferred in aftermarket parts for custom vehicles or high-performance cars, where appearance is important, and a polished exhaust pipe can enhance the vehicle’s overall look.
Overall, an exhaust pipe polishing line is essential for manufacturing exhaust systems with high-quality finishes, ensuring both functional performance and appealing aesthetics. It helps manufacturers meet customer demands for durable, high-performance, and visually striking exhaust components, all while improving efficiency in the production process.
An exhaust pipe polishing line is a crucial system in the automotive industry that specializes in polishing exhaust pipes to achieve the best possible finish in terms of both aesthetics and performance. The primary goal is to enhance the appearance and durability of exhaust pipes, which are often made from metals like stainless steel or aluminum. This process not only provides a smooth, shiny finish but also improves corrosion resistance, heat dissipation, and overall longevity of the pipes. By eliminating imperfections like scratches, rough patches, and oxidation, the polishing line ensures that the exhaust pipes are not only visually appealing but also more resilient to the elements.
The polishing process typically starts with the cleaning of the pipes to remove any contaminants like dirt, grease, or previous oxidation layers. This can be done through abrasive blasting or grinding, preparing the metal surface for subsequent polishing. Once cleaned, the pipes move on to the polishing stages, where a variety of abrasive materials, including polishing pads and wheels, are used to gradually smooth and refine the surface. These stages might involve multiple steps with varying levels of abrasiveness, from coarse to fine abrasives, depending on the desired final finish.
During the abrasive polishing phase, high-speed machines are employed to apply these abrasive materials to the pipes. These machines can rotate or vibrate the pipes as they come into contact with the polishing tools. The goal is to remove any remaining imperfections while achieving a consistent and smooth finish across the entire surface. In some cases, robotic polishing systems can be used to ensure precision, with programmable settings allowing for tailored polishing depending on the specific design and requirements of each exhaust pipe.
After the polishing process, a final cleaning step is essential to remove any leftover polishing compounds or abrasives. The pipes may also undergo a quality inspection to ensure that the finish meets the required standards. This stage checks for any signs of defects or inconsistencies, ensuring that only high-quality exhaust pipes move forward in the production process. Once polished and cleaned, the pipes are ready for packaging and shipment to manufacturers or aftermarket suppliers, where they will be used in a wide range of vehicles, from everyday cars to high-performance or custom vehicles.
A key advantage of the exhaust pipe polishing line is its ability to enhance the corrosion resistance of the pipes. Polished surfaces are less prone to corrosion, helping to extend the life of the exhaust system. Additionally, smooth surfaces are easier to clean and maintain, which reduces the buildup of grime and soot that could otherwise affect the performance of the exhaust system. A well-polished exhaust pipe also offers aesthetic appeal, particularly in custom vehicles, where the appearance of the exhaust is as important as its functionality. High-performance vehicles, for example, often showcase polished exhaust pipes as part of their premium or sporty look.
Moreover, polished exhaust pipes contribute to better heat dissipation. The smooth finish allows for more efficient heat transfer, which can improve the overall performance of the exhaust system, especially in high-performance or racing vehicles. Exhaust pipes that are polished to a mirror finish not only stand out visually but also operate more efficiently, offering a balance of form and function.
Exhaust pipe polishing lines can vary in scale, with larger automated systems able to handle high volumes of exhaust pipes with precision and speed. These systems often include robotic arms, CNC-controlled machines, and conveyor belts to manage the entire polishing process. In smaller or custom applications, more manual systems may be used, with operators performing specific polishing tasks by hand or using simpler machines. No matter the scale, the goal remains the same: to produce exhaust pipes that are durable, aesthetically pleasing, and high-performing.
In conclusion, an exhaust pipe polishing line is an essential part of the manufacturing process for producing quality exhaust systems. It improves both the functionality and aesthetics of exhaust pipes, ensuring they are smooth, durable, and resistant to corrosion. Whether for mass production or customized pieces, these lines provide an efficient way to meet the demands of modern automotive manufacturing and aftermarket customization.
Die & Mold Surface Polisher
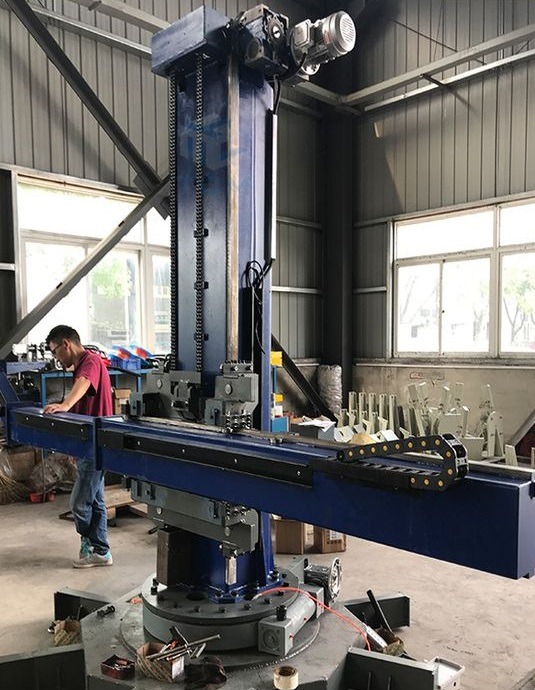
A die and mold surface polisher is a specialized machine or tool designed to smooth, polish, and finish the surfaces of dies and molds used in manufacturing processes, particularly in industries such as plastic injection molding, metal casting, and die-casting. These polishing machines are essential for ensuring that the molds and dies used to create various components are free of imperfections and have smooth, precise surfaces that meet stringent quality standards.
In die and mold manufacturing, surface quality is crucial because the surface of the die or mold directly affects the finish of the product it produces. Whether producing components for automotive, electronics, consumer goods, or medical devices, the finish of the mold can influence the appearance and functionality of the final product. A mold with a smooth, polished surface produces parts with fewer defects, better texture, and improved dimensional accuracy.
The polishing process typically involves multiple stages of abrasive treatment, starting with coarser abrasives to remove larger imperfections or rough surfaces, and progressing to finer abrasives for a mirror-like finish. The machine can utilize various types of abrasives, such as diamond pastes, polishing wheels, abrasive belts, or lapping compounds, to achieve the desired result. Polishing pads or brushes are often used to apply these abrasives and finish the surface of the mold or die.
For precision, many die and mold surface polishers are equipped with CNC (Computer Numerical Control) or robotic technology, allowing for automated polishing with high repeatability and accuracy. These systems can be programmed to polish the surface of molds and dies in a controlled manner, ensuring that the entire mold surface is evenly finished. Some polishing systems also feature vibratory polishing, where components are placed in a chamber that vibrates, allowing the polishing media to gently finish the surface.
Robotic polishing machines can also be used for larger or more intricate molds, offering consistent results while reducing the need for manual labor. These systems typically offer multiple axis movements to reach different angles and areas of the mold, making them ideal for complex or hard-to-reach surfaces.
The key benefit of using a die and mold surface polisher is the improved surface quality of the molds, which translates into better-quality products. A polished mold is less likely to cause defects in the final product, such as scratches, uneven surfaces, or surface contamination. This leads to higher production yields, improved product finish, and greater overall efficiency in the manufacturing process.
Polishing also helps in improving the lifetime of the molds and dies. By smoothing out rough areas, the surface is less prone to wear and tear, reducing the need for frequent mold repairs or replacements. Furthermore, a polished mold or die is easier to clean and maintain, as smoother surfaces prevent the accumulation of residue, dirt, or debris that can compromise the quality of the mold over time.
In addition to these functional benefits, the polished surface also enhances the appearance of the final product. Components created from molds with polished surfaces tend to have a more attractive finish, whether that’s a high-gloss or smooth matte appearance, depending on the intended use of the product.
Die and mold surface polishers are available in various forms, from manual polishing tools for smaller, more intricate molds to fully automated polishing systems for high-volume production. Depending on the complexity and scale of production, manufacturers may opt for machines that offer customizable polishing processes, enabling them to adjust parameters like speed, pressure, and abrasive grade for different mold types or materials.
In conclusion, a die and mold surface polisher is an essential tool in the production of high-quality dies and molds. It ensures that the surfaces of molds and dies are smooth, defect-free, and capable of producing top-tier products. Whether for small-scale or large-scale production, these machines help improve the efficiency, quality, and longevity of both molds and the products they produce.
A die and mold surface polisher is an important tool used in industries where high precision and smooth surfaces are essential, such as in plastic injection molding, die casting, and metalworking. It is specifically designed to refine and perfect the surfaces of molds and dies, which are integral in shaping components for a wide range of industries including automotive, aerospace, electronics, and medical devices. The polishing process is critical because the finish of the mold or die directly impacts the quality of the product it produces, influencing factors like texture, surface smoothness, and dimensional accuracy.
The polishing process typically begins with the use of abrasive materials, such as diamond pastes, polishing pads, wheels, and abrasive belts, which help remove any rough spots, imperfections, or residues from the mold or die surface. Initially, coarser abrasives are used to tackle more noticeable imperfections, and the process gradually transitions to finer abrasives for a smooth and refined finish. This multi-stage approach ensures that the surface becomes smoother with each pass, improving both the quality of the mold and the final product.
In many modern polishing systems, robotic or CNC technology is used to achieve a high level of precision. Automated polishing systems allow for repeatable, consistent polishing of the mold, ensuring that every surface is polished evenly. With the help of robotic arms or multi-axis CNC machines, these systems can work on complex mold geometries, ensuring that even hard-to-reach areas are polished thoroughly. This automation not only improves the efficiency of the polishing process but also reduces the potential for human error and increases the consistency of the finish across large production volumes.
Robotic polishing also allows for more flexibility, as the polishing parameters can be adjusted to accommodate different mold shapes, materials, and finishes. The integration of vibratory polishing is another option, where molds or dies are placed inside a vibrating chamber with abrasive media, allowing the abrasive materials to gradually refine the surface. This method is particularly effective for smaller parts or intricate mold designs that would otherwise be challenging to polish manually or with traditional methods.
One of the significant benefits of using a die and mold surface polisher is the enhanced surface quality. A well-polished mold or die results in higher-quality products with fewer surface defects, such as scratches, blemishes, or uneven finishes. This ultimately leads to higher production yields, fewer rejected parts, and better overall efficiency. It also ensures that plastics or metals cast from these molds are smooth, reducing the need for additional finishing steps or touch-ups.
Moreover, polished surfaces help extend the lifetime of molds and dies by reducing wear and tear. The smoother the surface of the mold, the less friction it creates during the molding or casting process, which helps prevent premature degradation. It also minimizes the accumulation of materials like plastic residue or metal buildup, which can otherwise compromise the mold’s functionality. This durability means that molds require less frequent maintenance, ultimately saving time and costs for manufacturers.
Additionally, the polishing process helps improve the cleanability of the molds. A smooth surface makes it easier to clean and maintain the molds, as dirt, dust, and residue have less chance of sticking to the surface. This is particularly important in high-precision industries, where any contamination could compromise the integrity of the mold and the final product.
The polishing process also impacts the appearance of the final products. Molds with polished surfaces produce products that have an aesthetically pleasing finish, whether a shiny, mirror-like finish for cosmetic parts or a matte, smooth surface for more functional components. This is especially important in industries like automotive and consumer electronics, where the appearance of a part can be just as important as its functionality.
A die and mold surface polisher can vary in complexity and scale, from small, manual polishing tools to fully automated polishing systems capable of handling large quantities of molds in an industrial setting. For small-scale or custom work, manual polishing might be preferred, where operators carefully apply abrasives and polish by hand, especially for intricate or custom molds. However, for large-scale manufacturing, automated polishing lines are used to increase speed, precision, and output, ensuring that hundreds or thousands of molds can be processed efficiently.
Ultimately, a die and mold surface polisher is an essential investment for industries that rely on high-precision molds. It ensures the production of molds and dies that are durable, high-quality, and capable of producing components with excellent surface finishes. With advancements in automation and robotic technology, these machines continue to improve in terms of efficiency, precision, and consistency, making them indispensable in modern manufacturing processes.
Wet Polishing Machine
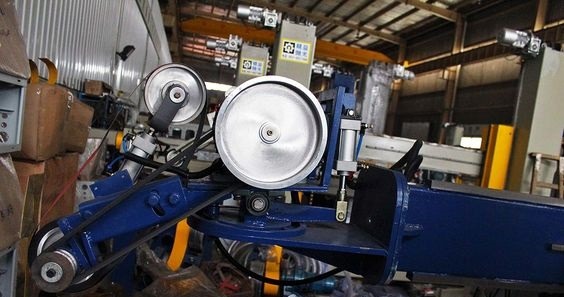
A wet polishing machine is a specialized tool used for polishing materials, typically metals, ceramics, stones, glass, or other hard surfaces, by applying water or another liquid during the polishing process. The primary purpose of using water or liquid is to reduce friction and heat generation, which helps prevent damage to the material being polished and ensures a smooth, even finish. The wet polishing process is commonly used in various industries, including automotive, construction, stonework, electronics, and metalworking.
The machine typically consists of a rotating pad or disc, which is used to apply an abrasive compound or polishing agent onto the material’s surface. As the material is polished, water or another liquid is continuously applied to help lubricate the polishing surface and remove debris generated during the process. The wet environment helps to prevent overheating, which could lead to material degradation, and it also ensures that abrasive particles are kept in suspension, enhancing the polishing efficiency.
Wet polishing machines are often equipped with a water delivery system that consistently applies a fine mist or stream of water over the polishing area. The abrasive pads used in wet polishing can be made of materials such as diamond, silicon carbide, or aluminum oxide, depending on the material being polished and the desired finish. These machines may operate at different speeds, with adjustments made based on the type of material and the finish required.
In addition to water, wet polishing machines may also use slurry mixtures that include water, abrasives, and polishing compounds to achieve a more refined finish. The slurry helps to polish the material more effectively by enhancing the abrasive action while maintaining a controlled environment that minimizes the risk of heat buildup.
Wet polishing is especially valuable when polishing materials that are prone to heat damage or discoloration. For instance, when polishing stone surfaces such as granite, marble, or concrete, the use of water prevents the material from becoming too hot, which could cause cracks or alter the appearance of the surface. Similarly, when polishing metals, water helps in preventing the buildup of heat that could cause the metal to warp or discolor.
Wet polishing machines are used in a variety of industries. In the stone industry, they are crucial for finishing and shining natural stones like marble, granite, and limestone. In metalworking, wet polishing machines are used for polishing metal surfaces, such as stainless steel, to achieve a smooth, reflective finish. Wet polishing is also important in the electronics industry, where delicate components require a high degree of precision and care to avoid damage during polishing.
These machines are highly beneficial for improving both the quality and efficiency of the polishing process. The continuous application of water reduces the need for frequent cleaning of the workpiece, as it keeps the surface free of excess debris and contaminants. Wet polishing also helps to extend the life of the polishing pads and abrasives, as it reduces wear and tear caused by friction and heat.
Overall, wet polishing machines provide a more controlled, efficient, and effective method of polishing various materials, especially those that are heat-sensitive or require a high-quality finish. By reducing heat, friction, and contamination during the polishing process, these machines ensure that the final surface quality is uniform, smooth, and free of defects.
A wet polishing machine is a highly effective tool used for polishing materials like metals, stones, ceramics, and glass by incorporating water or another liquid into the process. The use of water helps manage friction and heat during the polishing, making it particularly valuable for materials that could suffer from overheating or surface damage. By continuously applying liquid, typically water, during the polishing process, the machine ensures that the surface remains cool, while also preventing abrasive particles from settling and causing surface imperfections. This process is especially useful in industries where precision and smooth finishes are crucial, such as in the automotive, stonework, metalworking, and electronics sectors.
The wet polishing machine usually operates with a rotating disc or pad, which is used to apply abrasives or polishing compounds to the surface of the material being treated. As the material is polished, water is sprayed or misted over the surface to reduce the build-up of heat and to flush away debris created by the abrasive action. The result is a smooth, even finish without the risk of damaging the material. This technique is beneficial for hard materials that could be prone to cracking, discoloration, or warping if subjected to too much heat, like stone, marble, granite, and metals like stainless steel.
The machines are equipped with water delivery systems that ensure a constant flow of liquid, maintaining a wet environment throughout the polishing process. This reduces friction, thus preventing the workpiece from overheating. The water also helps clean the surface, keeping it free from dust, dirt, or abrasive residues. It makes the overall process more efficient as the debris is removed from the surface, preventing any grit from scratching or damaging the polished material. The liquid can also act as a lubricant, helping the polishing pads or abrasives move smoothly across the material.
Wet polishing machines are designed to work with different types of abrasives, ranging from diamond abrasives for hard materials like stone and ceramics, to silicon carbide or aluminum oxide abrasives for metals. Depending on the material and the desired finish, the abrasives can be swapped out to match the level of smoothness or shine required. The wet environment reduces the friction between the abrasive and the material being polished, extending the lifespan of the polishing pads while maintaining the effectiveness of the abrasives.
In industries like stonework, wet polishing machines are commonly used to achieve a high-quality finish on granite countertops or marble floors. The water helps prevent the stone from overheating, which could cause cracks or discoloration. For metal polishing, the machine ensures that the metal surface remains smooth and shiny without the risk of warping or discoloring due to excessive heat. Electronics manufacturers use wet polishing to achieve the precision finishes required for components such as semiconductors, where any surface imperfection could affect the functionality of the device.
The process is not just about improving the appearance of materials but also about enhancing their performance. Polishing with water helps achieve a mirror-like finish that not only looks good but also ensures a more uniform surface, which can be important for applications requiring precise fitment or aerodynamics. For example, in the automotive industry, polished metal parts improve both the aesthetics and the performance of exhaust systems or trim pieces, and in the aerospace sector, polished components are crucial for reducing drag and improving the overall efficiency of aircraft.
Moreover, wet polishing machines are cost-effective and environmentally friendly, as the continuous use of water reduces the need for excessive chemicals or solvents that can be harmful to the environment. The use of water ensures that the materials are cleaner and safer during the polishing process, creating a more sustainable production environment. Additionally, wet polishing systems can be more efficient than dry polishing methods because they reduce the risk of overheating and extend the life of both the polishing tools and the workpieces.
In conclusion, wet polishing machines play an important role in providing high-quality finishes for materials that require careful handling during the polishing process. By incorporating water or liquid into the process, they help control heat, reduce friction, and ensure that the surface remains smooth and defect-free. Whether in stone, metal, or ceramics, wet polishing machines are essential tools in industries where precision, smooth finishes, and durability are paramount.
Dry Polishing Machine
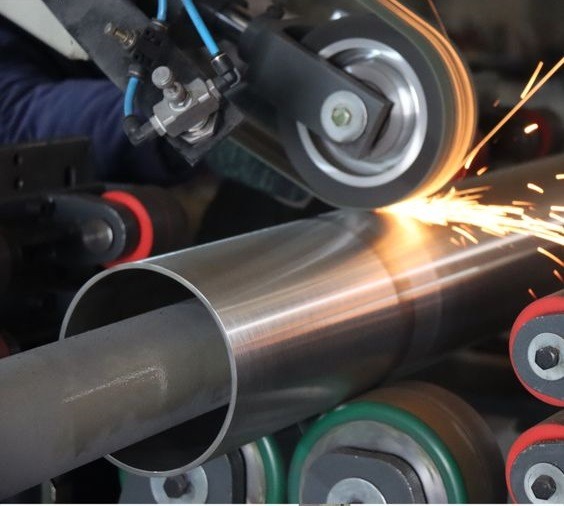
A dry polishing machine is a tool designed for polishing materials without the use of water or liquid. Unlike wet polishing, which incorporates water to reduce heat and friction, dry polishing relies solely on the abrasive action of the polishing pads or discs, which work in conjunction with the polishing compounds. Dry polishing is commonly used in industries where the use of water could cause damage, be impractical, or lead to unwanted residues on the material. These machines are often employed for polishing metal, wood, plastic, glass, and stone surfaces.
Dry polishing machines typically consist of a rotating polishing pad or disc, which applies abrasive compounds to the surface of the material. The material’s surface is then smoothed and refined through the abrasive action. The abrasives used can range from diamond abrasives for harder materials like stone or ceramics, to silicon carbide or aluminum oxide abrasives for metals and plastics. The process creates a smooth, high-quality finish by gradually removing layers of material, starting with coarser abrasives and progressing to finer grades for a polished, shiny result.
One of the primary benefits of dry polishing machines is the absence of water or liquid, which eliminates the need for water-based cleaning and drainage systems. This can be particularly advantageous in applications where water might interfere with the process or result in contamination. For example, in metalworking or electronics, using water could lead to rust formation or complications in electrical components. Dry polishing also eliminates the need for frequent cleaning or drying, making it a more convenient option in certain environments, especially in automated production lines.
Dry polishing is widely used for finishing metal parts and components in various industries. In automotive manufacturing, dry polishing machines are commonly used to achieve a high-gloss finish on components like exhaust pipes, engine parts, and trim pieces. The dry process is preferred here because it prevents rust from forming on the metal and helps achieve a clean, reflective surface. Similarly, in furniture manufacturing, dry polishing machines are used to create smooth, polished finishes on wood, plastic, and metal furniture.
Dry polishing is also popular in stone and marble polishing, where it can provide a high-shine finish on surfaces like countertops, floors, and tiles. While wet polishing is often used for stone surfaces to reduce heat, dry polishing can also be effective for softer stones, as it is faster and requires less cleanup. Furthermore, the process allows for a controlled finish with minimal mess, making it easier to maintain clean work environments.
Dry polishing machines can come in various designs, ranging from handheld tools for smaller, intricate work to stationary machines for larger-scale production. Some machines may incorporate vacuum systems to capture dust and debris produced during the polishing process, keeping the workspace clean and preventing the inhalation of harmful particles. This is particularly important when polishing materials like stone or metal, where fine dust can pose health risks. The versatility of these machines also makes them suitable for edge polishing or surface finishing, and they can be adapted to different materials and finishes based on the abrasives used.
The key advantage of dry polishing over wet polishing is its speed and simplicity. Since it does not require water or liquid, the process tends to be faster and can be performed in environments where water usage is limited or not practical. It also eliminates the need for post-polishing cleanup associated with wet processes, allowing for quicker turnaround times in manufacturing.
However, dry polishing does have some limitations compared to wet polishing. It generates more heat, which can be problematic for certain materials that are sensitive to temperature changes. In some cases, excessive heat buildup during the polishing process can lead to surface damage or discoloration, especially for delicate materials. Additionally, dry polishing generates more dust and debris, which can affect the cleanliness of the workspace and the health of operators if proper safety measures, like dust extraction systems, are not used.
In conclusion, dry polishing machines are essential tools in industries that require quick, efficient polishing without the use of water. They offer convenience, speed, and cost-effectiveness, making them suitable for a wide range of applications, from metalworking to stone polishing. However, like any process, dry polishing has its limitations, particularly in terms of heat management and dust generation, which need to be addressed through proper dust extraction systems and cooling methods for sensitive materials. Despite these challenges, dry polishing remains a widely-used technique due to its ability to achieve high-quality finishes in a variety of manufacturing settings.
A dry polishing machine works by applying abrasive pads or discs directly to a surface without the use of water or other liquids. This method relies on the friction generated between the abrasive material and the workpiece to smooth and refine the surface. Dry polishing is ideal for tasks where water could cause damage, is impractical, or could leave unwanted residues. It’s commonly used for materials like metal, plastic, stone, wood, and glass, providing an efficient way to achieve a polished finish without the complications of a wet process.
The machine typically features a rotating disc or pad, which is equipped with abrasive compounds such as diamond abrasives for harder materials like stone or ceramics, or silicon carbide for softer materials like metals or plastics. As the machine operates, the abrasives progressively smooth the surface, starting with coarser abrasives and working up to finer ones to achieve a high-gloss or smooth finish. This gradual process ensures that the material is polished effectively, removing imperfections and leaving behind a smooth, even surface.
A key benefit of dry polishing machines is that they eliminate the need for water, reducing the complexity of cleanup and maintenance. This can be particularly advantageous in certain industries, such as metalworking, where the use of water could cause rusting or contamination. Dry polishing machines are also more convenient for environments that do not have water disposal systems or where water use needs to be minimized. Additionally, because there’s no water involved, there’s less chance of residue buildup, and the materials stay dry throughout the polishing process, which can be beneficial in terms of achieving a cleaner finish without additional drying steps.
In industries like automotive manufacturing, dry polishing machines are used to achieve a high-quality finish on metal parts such as engine components, exhaust systems, and decorative trims. These parts require smooth, shiny finishes to meet aesthetic and functional requirements. Dry polishing is often preferred in this context because it avoids the risk of rust and corrosion that water could cause. Similarly, dry polishing is utilized in furniture and woodworking to give smooth finishes to wooden, plastic, or metal furniture pieces. It is especially useful for fine-tuning details and achieving a polished look on intricate or smaller components that require precision.
Dry polishing also finds use in stonework, where it can be employed to polish materials like marble, granite, and limestone. In stone polishing, it offers a quicker turnaround than wet polishing, especially for smaller tasks, and eliminates the cleanup associated with liquid-based processes. Though wet polishing is often more common for large-scale stone projects due to its ability to cool the stone and prevent overheating, dry polishing works well on softer stones and smaller surfaces that do not require extensive cooling.
One of the challenges of dry polishing is that it generates more heat due to the lack of water to cool the workpiece. Excessive heat can lead to surface damage, such as discoloration, burning, or warping, especially for heat-sensitive materials. However, advanced machines can incorporate dust extraction systems or other cooling mechanisms to help manage this issue, ensuring a smoother and safer process. Without water to capture debris, dry polishing also produces more dust, which can be harmful to both the operator and the environment. Adequate ventilation and dust extraction are essential in such environments to ensure both safety and cleanliness.
Dry polishing machines come in a variety of designs, from handheld tools used for smaller, detailed work to large, industrial machines used for high-volume production. In all cases, the goal is to provide a controlled polishing process that results in a high-quality finish. The machines can be used for different applications, such as edge polishing, surface finishing, or mirror-like finishing, depending on the needs of the material and the desired end result.
In conclusion, dry polishing machines are a versatile and efficient option for achieving polished finishes on a wide range of materials. They offer advantages in terms of speed, convenience, and simplicity by eliminating the need for water and reducing the complexity of cleanup. However, operators must be mindful of heat buildup and dust generation, implementing necessary safety measures to ensure a safe working environment. Despite these challenges, dry polishing remains a popular choice in various industries, from metalworking and automotive manufacturing to stone polishing and furniture finishing.
Abrasive Belt Polisher (Auto tensioning)
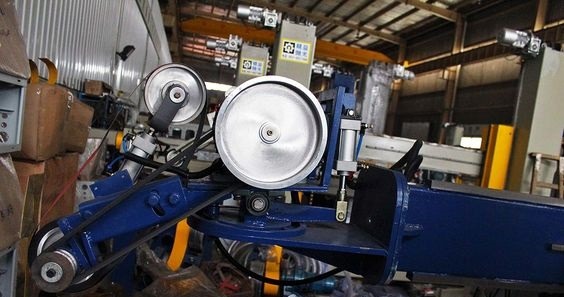
An abrasive belt polisher with auto tensioning is a specialized machine designed to polish and smooth the surface of various materials using an abrasive belt. The machine is equipped with an automatic tensioning system that ensures the abrasive belt remains properly tensioned during operation, improving the efficiency and consistency of the polishing process.
The auto tensioning feature is a key advantage in abrasive belt polishers, as it automatically adjusts the tension of the belt as it wears down during use. This ensures that the belt maintains optimal contact with the workpiece, leading to a consistent polishing effect and reducing the need for manual adjustments. The auto tensioning system typically includes sensors or a spring mechanism that monitors the belt’s tension and makes adjustments as necessary, preventing slippage or excessive wear of the belt.
Abrasive belt polishers are commonly used in industries such as metalworking, automotive manufacturing, and furniture production, where the goal is to achieve a smooth, even finish on various materials. The abrasive belts used in these machines can range in coarseness, depending on the material and the desired finish. Coarser belts are used for heavy material removal, while finer belts are used for polishing and achieving a smoother surface.
The machine operates by running the abrasive belt over the surface of the material. The workpiece is either fed manually or automatically into the machine, where the abrasive belt moves at high speed, grinding away any imperfections, scratches, or uneven areas. The result is a polished surface that can be smooth and shiny, or just uniformly finished, depending on the abrasive used.
The auto tensioning system helps to maintain the efficiency of the machine over time, reducing the frequency of maintenance and improving the overall lifespan of the abrasive belts. It also ensures that the polishing is consistent, which is particularly important in high-volume production environments where uniformity is crucial.
In addition to the auto tensioning feature, these machines may also have adjustable speed settings, allowing the operator to fine-tune the polishing process based on the material being worked on. Some models may include dust extraction systems to remove particles generated during polishing, improving air quality and ensuring a cleaner workspace.
Overall, an abrasive belt polisher with auto tensioning is a highly efficient tool for achieving a consistent, high-quality finish on a wide range of materials. The automatic tensioning feature minimizes the need for manual adjustments and enhances the overall performance and longevity of the machine, making it a valuable asset in industries requiring precise and efficient polishing.
An abrasive belt polisher with auto tensioning is a highly effective tool designed to improve the consistency and efficiency of the polishing process. The auto tensioning system is the standout feature, automatically adjusting the tension of the abrasive belt as it wears down. This ensures the belt remains in optimal contact with the material being polished, reducing the chances of slippage or uneven polishing. As a result, the polishing process becomes smoother and more efficient, with fewer interruptions for manual adjustments.
The machine typically operates by using a rotating abrasive belt that moves at high speeds to polish, smooth, or even out the surface of a variety of materials, including metals, wood, plastics, and composites. The abrasive belt can be made of different materials, including silicon carbide, aluminum oxide, or diamond abrasives, depending on the material being polished and the desired finish. The abrasive belt is a consumable, and its tension needs to be maintained properly to ensure consistent performance.
In a traditional abrasive belt polisher, operators would need to manually adjust the belt tension as it wears over time, but with the auto tensioning feature, the machine takes care of this. The system automatically detects any slack or change in the belt’s tension and corrects it, which helps maintain a smooth and uniform finish throughout the process. This is particularly beneficial in industries where high-quality surface finishes are critical, such as automotive manufacturing, metalworking, and furniture production.
The machine is versatile, able to handle both heavy material removal and polishing tasks, depending on the abrasive belt used. Coarse belts are employed to remove large amounts of material, such as smoothing rough surfaces or removing imperfections, while finer belts are used for polishing and achieving a smooth, shiny finish. This flexibility makes the abrasive belt polisher a popular choice in both small-scale workshops and large industrial operations.
Furthermore, the auto tensioning system contributes to the durability of the machine. Since the abrasive belt is maintained at the correct tension, it experiences less wear and tear, and the machine runs more efficiently over time. The risk of belt slippage is minimized, which reduces the chances of uneven polishing or grinding marks on the workpiece. This leads to more consistent results, especially in automated settings where multiple units need to be processed in succession.
Many models of abrasive belt polishers with auto tensioning also come with adjustable speed controls, allowing operators to fine-tune the belt’s speed for different materials or polishing requirements. The ability to control the speed enhances precision and provides more flexibility for working with various materials. Some machines are equipped with dust collection systems, which capture the particles and debris created during polishing, improving the work environment and helping maintain cleaner, healthier air quality in industrial settings.
In summary, an abrasive belt polisher with auto tensioning significantly enhances the polishing process by ensuring consistent tension and optimal performance of the abrasive belt. This feature reduces the need for manual adjustments, cuts down on maintenance time, and extends the lifespan of the machine and the abrasive belts. It is a reliable, efficient tool used in industries that require high-quality surface finishes and is well-suited for handling a variety of materials. Whether for heavy material removal or fine polishing, the auto tensioning system ensures that the job is done efficiently and with precision.
Compound Slurry Polishing Machine
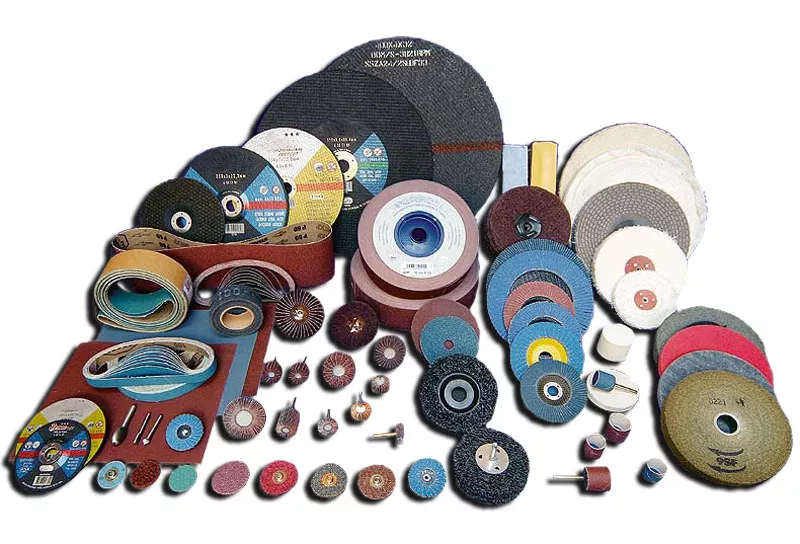
A compound slurry polishing machine is a specialized tool used for polishing and finishing surfaces of various materials, such as metals, ceramics, plastics, and glass, using a combination of abrasive compounds mixed with a liquid slurry. The slurry typically consists of abrasive particles suspended in a liquid, which acts as both a lubricant and a cooling agent during the polishing process. This method allows for precise control over the polishing process, producing high-quality finishes while minimizing surface defects and maintaining material integrity.
The machine operates by applying the compound slurry onto the surface of the material to be polished. The slurry is typically applied via rotating polishing pads or discs, which are in continuous motion as they come into contact with the workpiece. The rotating pad or disc helps spread the slurry evenly across the surface, ensuring a consistent application of the abrasive particles. These abrasive particles gradually wear away the imperfections or scratches on the material, creating a smooth and polished finish.
One of the key benefits of a compound slurry polishing machine is its ability to achieve a high-quality finish on materials that are often difficult to polish using dry or other polishing methods. The use of slurry provides several advantages, including cooling the material to prevent overheating, reducing friction, and removing debris generated during polishing. This results in a more uniform finish and reduces the risk of surface damage or imperfections, which can be common in dry polishing processes.
The machine’s versatility makes it suitable for a wide range of industries. For example, in metalworking, compound slurry polishing machines are used to achieve a mirror-like finish on metal parts, such as stainless steel, aluminum, and brass. The slurry helps smooth out the metal surface, removing any oxidation or surface corrosion and leaving behind a shiny, reflective finish. This type of polishing is commonly used for automotive components, aerospace parts, and architectural finishes.
In electronics, slurry polishing machines are employed for semiconductor and optical lens polishing, where precision and smooth surfaces are critical. The slurry helps achieve ultra-fine finishes that are essential for these sensitive applications, ensuring that no debris or imperfections interfere with the functionality of the components. The use of compound slurry also allows for a more controlled process, which is important in high-precision industries where even the smallest surface defect can lead to significant issues.
The compound slurry polishing machine is also commonly used in stone polishing, especially for materials like granite, marble, and quartz. The slurry helps prevent the stone from overheating, reducing the risk of cracking or discoloration during the polishing process. Additionally, the slurry enhances the polishing effect, allowing the stone to achieve a high-gloss finish that is both aesthetically pleasing and durable.
Maintenance of a compound slurry polishing machine involves regular cleaning of the polishing pads or discs, as well as ensuring that the slurry mixture is maintained at the proper consistency and composition for optimal polishing. Over time, the abrasive particles in the slurry will wear down, and the mixture may need to be replaced to maintain polishing efficiency.
In conclusion, a compound slurry polishing machine is an essential tool in industries requiring high-quality surface finishes. The use of slurry allows for controlled polishing, precise finishing, and better heat management, making it suitable for a wide variety of materials and applications. Whether for metal, stone, glass, or ceramics, the compound slurry polishing machine delivers consistent results while reducing the risk of surface damage and achieving superior finishes.
A compound slurry polishing machine is a highly effective tool designed to provide smooth, high-quality finishes on a wide range of materials, from metals and ceramics to plastics and glass. It works by utilizing a slurry mixture, typically made of abrasive particles suspended in a liquid, which acts as both a lubricant and a cooling agent during the polishing process. The slurry allows for precise control of the polishing process, enabling a finer finish with fewer imperfections compared to dry or other polishing methods. The machine uses rotating polishing pads or discs, which spread the slurry evenly across the surface of the material. As the pads rotate, they rub against the material, helping to smooth out any imperfections or scratches by gradually removing tiny amounts of the surface.
One of the key advantages of using a compound slurry polishing machine is that the slurry helps to cool the workpiece during the polishing process, preventing overheating. This is particularly important when working with materials like metals, which are sensitive to high temperatures and can become damaged if the polishing process generates excessive heat. Additionally, the slurry reduces friction between the abrasive particles and the material, which not only improves the polishing efficiency but also minimizes the risk of surface defects like burns, cracks, or warping. The liquid also serves as a cleaning agent, flushing away debris and particles created during the polishing process, leading to a cleaner work environment and more uniform finishes.
These machines are particularly useful in industries where achieving a flawless surface finish is critical. For instance, in metalworking, compound slurry polishing machines are used to polish metal parts, such as stainless steel, aluminum, and brass, to a high-gloss or mirror-like finish. This type of polishing is common in the automotive industry, where polished metal components are needed for aesthetic and functional purposes, as well as in aerospace and architectural applications. The ability to achieve a smooth, reflective surface on metal parts also makes these machines invaluable in industries like jewelry manufacturing, where polishing is crucial for visual appeal.
In electronics, compound slurry polishing machines play a critical role in the production of semiconductor components and optical lenses, where the precision and smoothness of the surface are vital to the component’s performance. The slurry-based polishing process enables the precise removal of any imperfections, ensuring that the final product meets stringent quality and performance standards. This is especially important for photolithography in semiconductor manufacturing, where even the smallest surface imperfection can affect the functionality of integrated circuits.
The use of slurry in the polishing process also benefits industries like stonework, particularly in the polishing of marble, granite, and quartz surfaces. Polishing stone without a slurry can lead to excessive friction and heat, potentially causing damage to the material. Slurry-based polishing, however, ensures that the stone remains cool while achieving a glossy, smooth finish. This is especially important in applications like countertops and flooring, where both aesthetics and durability are key. The slurry also helps reduce the risk of cracking or discoloration, which could occur if the stone is polished with dry or overly abrasive methods.
Maintaining a compound slurry polishing machine requires regular attention to the slurry mixture itself. Over time, the abrasive particles within the slurry will break down, and the slurry may need to be replenished or replaced to maintain effective polishing. The polishing pads or discs also need to be cleaned and replaced periodically, as they can become clogged with debris, reducing their effectiveness. Proper maintenance ensures that the machine operates efficiently, producing high-quality finishes without interruptions.
In summary, a compound slurry polishing machine is an essential tool for industries that require precise and high-quality surface finishes. The use of slurry provides several benefits, including better cooling, reduced friction, and the ability to maintain a consistent polishing action over time. Whether used in metal polishing, stone finishing, or electronics manufacturing, these machines help achieve superior finishes, improve efficiency, and reduce the risk of material damage during the polishing process.
The compound slurry polishing machine is particularly advantageous in high-volume manufacturing settings due to its ability to automate and streamline the polishing process. By combining both abrasives and liquid slurries, these machines are designed for consistency and efficiency, making them ideal for producing polished surfaces on a large scale. In industries where uniformity and precision are critical, such as semiconductor manufacturing and aerospace, the machine’s ability to maintain a consistent polishing action is invaluable. Operators can rely on the machine to produce polished materials with little manual intervention, ensuring higher productivity and reduced labor costs.
Moreover, compound slurry polishing machines are adaptable to a wide range of materials and finishes, from coarse to fine polishing, depending on the abrasive size used in the slurry and the speed settings of the machine. This versatility makes them highly sought after in metal finishing industries, where different stages of polishing may be required. The ability to adjust the abrasive content in the slurry allows for greater flexibility, allowing the machine to be used for initial rough polishing as well as final fine polishing stages, depending on the application. For example, in metal processing, it might be necessary to remove deep scratches or oxidation with a coarser abrasive before transitioning to a finer slurry for a smooth, glossy finish.
In the jewelry industry, compound slurry polishing machines are used to achieve the highly reflective finishes that are essential for fine jewelry. The slurry mixture can be tailored to the specific needs of each material, whether working with gold, silver, platinum, or precious stones. The precision and consistency offered by the slurry polishing process ensure that the final products meet high aesthetic standards while retaining the material’s integrity.
In optical lens polishing, compound slurry polishing machines are critical for achieving the precise clarity and smoothness required for lenses used in cameras, eyeglasses, and scientific instruments. The slurry aids in minimizing surface imperfections such as scratches or distortions that could affect the lens’s performance. The polishing process ensures that the lens remains free of contaminants, which is vital for optics in high-precision applications like microscopes or telescope lenses, where even minor imperfections can severely impact the quality of the image.
These polishing machines are also valuable in industries where surfaces are required to have a specific level of smoothness, such as medical device manufacturing. Components such as surgical instruments and implants often require a smooth, polished finish to ensure that they are both functional and safe for use. The slurry polishing process helps to eliminate micro-burrs, rough spots, or other imperfections that could compromise the performance or safety of the devices.
Another advantage of using a compound slurry polishing machine is its ability to improve the surface durability of materials. In industries such as automotive manufacturing, where parts are exposed to harsh conditions, polishing with a slurry mixture can enhance the corrosion resistance and durability of components. The smooth finish achieved through slurry polishing reduces the likelihood of dirt, water, or other contaminants adhering to the surface, making it easier to clean and maintain.
Environmental concerns are also addressed by compound slurry polishing machines. The use of liquid slurry reduces the amount of dust generated during the polishing process, creating a cleaner work environment. Additionally, slurry-based systems are often equipped with filtration and recycling systems that capture and reuse the polishing liquids, making the process more sustainable and reducing waste. This is especially beneficial in industries where large quantities of materials are polished regularly, as it can help to cut down on the overall consumption of water and chemicals.
Finally, in terms of operator safety, the liquid slurry provides an important cooling effect that helps to prevent heat buildup, reducing the risk of burns or other injuries. Moreover, slurry-based polishing machines often have built-in systems for managing the slurry mixture, such as automated systems for adjusting flow rates, controlling viscosity, and maintaining the correct proportions of abrasive to liquid. This ensures that the polishing process is carried out safely and efficiently, with less oversight required by the operator.
In conclusion, the compound slurry polishing machine plays an essential role in numerous industries that require high-quality finishes. Its versatility, efficiency, and ability to produce smooth, reflective surfaces with minimal manual intervention make it a valuable asset in industries ranging from automotive manufacturing and metalworking to electronics and medical device production. Whether polishing metals, stone, ceramics, or glass, these machines provide superior control over the polishing process, ensuring that every surface meets the required standards for quality, smoothness, and durability.
EMS Metalworking Machinery
We design, manufacture and assembly metalworking machinery such as:
- Hydraulic transfer press
- Glass mosaic press
- Hydraulic deep drawing press
- Casting press
- Hydraulic cold forming press
- Hydroforming press
- Composite press
- Silicone rubber moulding press
- Brake pad press
- Melamine press
- SMC & BMC Press
- Labrotaroy press
- Edge cutting trimming machine
- Edge curling machine
- Trimming beading machine
- Trimming joggling machine
- Cookware production line
- Pipe bending machine
- Profile bending machine
- Bandsaw for metal
- Cylindrical welding machine
- Horizontal pres and cookware
- Kitchenware, hotelware
- Bakeware and cuttlery production machinery
as a complete line as well as an individual machine such as:
- Edge cutting trimming beading machines
- Polishing and grinding machines for pot and pans
- Hydraulic drawing presses
- Circle blanking machines
- Riveting machine
- Hole punching machines
- Press feeding machine
You can check our machinery at work at: EMS Metalworking Machinery – YouTube
Applications:
Flange-punching
Beading and ribbing
Flanging
Trimming
Curling
Lock-seaming
Ribbing