A base grooving machine, as you mentioned, is a specialized machine used for creating grooves on the bottom surface of pots and pans. These grooves serve various purposes such as improving heat conduction, preventing sticking, and enhancing the overall performance of the cookware.
Here are some general features and information about a base grooving machine:
- Purpose: The machine is specifically designed for grooving the base of pots and pans to enhance their cooking capabilities.
- Groove Patterns: The machine can create different types of groove patterns, such as concentric circles, radial lines, or custom designs, depending on the desired functionality and aesthetic appeal.
- Operation: The machine typically consists of a rotating drum or a tool holder with cutting blades or wheels that make precise grooves on the base of the cookware. The cookware is placed onto a fixture or chuck that holds it securely in place during the grooving process.
- Adjustable Parameters: The machine allows for adjusting various parameters such as groove depth, width, spacing, and pattern geometry to meet specific requirements and achieve desired results.
- Materials: Base grooving machines are designed to work with different types of cookware materials, including stainless steel, aluminum, cast iron, and other compatible materials commonly used for pots and pans.
- Automation: Some base grooving machines may feature automation capabilities, such as programmable controls, to enhance productivity and repeatability in the grooving process.
- Safety Features: Safety mechanisms are typically incorporated into the machine to ensure operator safety, such as guards, emergency stop buttons, and safety interlocks.
It’s important to note that specific features and capabilities of a base grooving machine can vary depending on the manufacturer and model. If you have a particular machine in mind, I recommend referring to the manufacturer’s documentation or contacting them directly for detailed information and specifications tailored to that specific machine.
Please keep in mind that using specialized machines like a base grooving machine may require proper training and expertise to ensure safe and efficient operation.
Base Grooving Machine
A base grooving machine is a specialized tool used to create grooves or indentations on various surfaces, particularly on the base or bottom of cookware, appliances, or other objects. They are commonly employed in industrial settings, manufacturing facilities, and metalworking workshops.
Key Components of Base Grooving Machines
Base grooving machines typically consist of several key components:
- Grooving Wheel or Tool: The grooving wheel or tool is the primary working element of the machine, responsible for creating the grooves or indentations on the workpiece. Various groove shapes and sizes can be achieved using different wheel or tool configurations.
- Workpiece Holder: The workpiece holder securely holds the workpiece in place while it is being grooved. It allows for precise positioning and control over the grooving process.
- Adjustable Grooving Depth: An adjustable grooving depth mechanism allows for precise control over the depth of the grooves, ensuring consistency and meeting specific design requirements.
- Rotational Speed Control: Rotational speed control allows for adjusting the speed of the grooving wheel or tool, optimizing the grooving process for different materials and desired finishes.
- Lubrication System: A lubrication system is often integrated into base grooving machines to provide lubrication to the grooving wheel or tool and the workpiece interface, reducing friction and minimizing wear.
1. Grooving Wheel or Tool:
The grooving wheel or tool is the primary working element of the machine and is responsible for creating the grooves or indentations on the workpiece. It typically consists of a hardened steel or carbide disc with a specific profile, such as a V-groove, U-groove, or rounded groove. The wheel’s profile determines the shape of the groove that will be created on the workpiece.
Types of Grooving Wheels:
- Carbide-Tipped Grooving Wheels: These wheels are highly wear-resistant and are suitable for grooving harder materials such as stainless steel and cast iron.
- Diamond-Coated Grooving Wheels: These wheels offer exceptional sharpness and durability and are used for precision grooving applications.
2. Workpiece Holder:
The workpiece holder securely clamps the workpiece in place while it is being grooved. This ensures that the workpiece is held firmly and accurately, preventing it from moving or shifting during the grooving process. The workpiece holder can be designed to accommodate various workpiece shapes and sizes.
Types of Workpiece Holders:
- Fixed Workpiece Holders: These holders are designed for specific workpiece shapes and sizes and provide precise positioning.
- Adjustable Workpiece Holders: These holders can accommodate a range of workpiece shapes and sizes and offer flexibility in positioning.
3. Adjustable Grooving Depth:
An adjustable grooving depth mechanism allows for precise control over the depth of the grooves, ensuring consistency and meeting specific design requirements. This mechanism can be adjusted manually or through computerized control systems.
Types of Grooving Depth Adjustment Mechanisms:
- Manual Grooving Depth Adjustment: This method involves manually adjusting the position of the grooving wheel or tool relative to the workpiece.
- Computerized Grooving Depth Adjustment: This method utilizes computer-controlled actuators to precisely adjust the grooving depth.
4. Rotational Speed Control:
Rotational speed control allows for adjusting the speed of the grooving wheel or tool, optimizing the grooving process for different materials and desired finishes. This control ensures that the grooving process is performed at the appropriate speed to achieve the desired groove quality and prevent damage to the workpiece.
Types of Rotational Speed Control Mechanisms:
- Variable Speed Drives: These drives allow for continuous adjustment of the rotational speed of the grooving wheel or tool.
- Step Speed Controls: These controls allow for selecting from a range of pre-defined rotational speeds.
5. Lubrication System:
A lubrication system is often integrated into base grooving machines to provide lubrication to the grooving wheel or tool and the workpiece interface. This lubrication reduces friction, minimizes wear, and prolongs the life of the grooving wheel or tool and the workpiece.
Types of Lubrication Systems:
- Oil Mist Lubrication: This system uses an oil mist to lubricate the grooving wheel or tool and the workpiece.
- Fluid Jet Lubrication: This system directs a stream of lubricant onto the grooving wheel or tool and the workpiece.
Applications of Base Grooving Machines
Base grooving machines are primarily used in the manufacturing process of cookware, appliances, and other metal components to create grooves or indentations that serve various functional and aesthetic purposes:
- Enhancing Grip and Stability: Grooves on the base of cookware, such as pots and pans, help to improve grip and stability when placed on stoves or cooktops, preventing accidental slips or spills.
- Ventilation and Heat Distribution: Grooves on the base of appliances, such as toasters or ovens, facilitate air ventilation and heat distribution, ensuring even cooking and preventing overheating.
- Decorative Accents: Grooves can also be used as decorative accents on various objects, adding visual appeal and enhancing the overall design aesthetic.
- Interlocking and Connection: Grooves can serve as interlocking or connection points for different components, such as aligning and securing lids on cookware or connecting parts of appliances.
- Creating Channels and Pathways: Grooves can be used to create channels or pathways for liquids or gases, such as drainage channels on cookware or ventilation paths on appliances.
Base grooving machines are versatile tools employed in various industries for creating grooves or indentations on the base or bottom of cookware, appliances, and other objects. These grooves serve functional and aesthetic purposes, enhancing performance, safety, and visual appeal.
Functional Applications:
- Enhancing Grip and Stability: Grooves on the base of cookware, such as pots and pans, provide a better grip on stoves or cooktops, preventing accidental slips and spills.
- Improving Heat Distribution: Grooves on the base of appliances, such as toasters or ovens, facilitate air ventilation and heat distribution, ensuring even cooking and preventing overheating.
- Creating Drainage Channels: Grooves can serve as drainage channels for liquids, such as in cookware, allowing water or oil to drain efficiently.
- Establishing Interlocking and Connection Points: Grooves can act as interlocking or connection points for different components, such as aligning and securing lids on cookware or connecting parts of appliances.
Aesthetic Applications:
- Adding Decorative Accents: Grooves can enhance the visual appeal of various objects, adding a decorative touch and complementing the overall design aesthetic.
- Creating Textured Surfaces: Grooves can create textured surfaces that provide tactile interest and enhance the overall feel of an object.
- Distinguishing Product Lines: Base grooving patterns can be used to differentiate between product lines, providing a unique visual identifier for each series.
Specific Applications:
- Cookware Manufacturing: Base grooving machines are widely used in the production of cookware, including pots, pans, and woks, to create grooves that improve grip, promote even heat distribution, and facilitate drainage.
- Appliance Manufacturing: Grooves are often incorporated into the base of appliances, such as toasters, ovens, and blenders, to enhance heat distribution, prevent overheating, and provide a secure grip on countertops.
- Automotive Components: Base grooving machines are used to create grooves on automotive components, such as engine blocks and brake rotors, for lubrication channels, airflow paths, and secure mounting points.
- Industrial Components: Grooves can be created on various industrial components, such as valves, pump housings, and electrical connectors, for functional purposes, such as fluid flow paths, cable routing, and secure connections.
- Decorative Objects: Base grooving machines can be employed to create decorative grooves on various objects, such as vases, sculptures, and architectural panels, adding visual interest and enhancing their aesthetic appeal.
Base grooving machines play a crucial role in various manufacturing processes, ensuring precision, consistency, and functionality in the production of cookware, appliances, and other metal components.
The purpose of a base grooving machine is to create grooves or indentations on the bottom surface of pots and pans. These grooves serve several purposes, including:
- Enhanced Heat Conduction: The grooves increase the surface area of the base, allowing for better heat distribution and conductivity. This results in more even cooking and reduces the chances of hot spots.
- Non-Stick Properties: The grooves help to prevent food from sticking to the bottom of the cookware. They create small air pockets that act as a barrier between the food and the cooking surface, reducing the need for excessive oil or butter.
- Improved Cooking Performance: The grooves can enhance the cooking performance of the pots and pans by promoting faster and more efficient heat transfer. This can lead to reduced cooking times and energy savings.
- Aesthetic Appeal: In addition to their functional benefits, the grooves can also add visual interest to the base of the cookware, enhancing its overall appearance and attractiveness.
By using a base grooving machine, manufacturers can achieve consistent and precise grooves on a large scale, ensuring that the cookware products meet the desired specifications and quality standards. The grooves can be customized based on the specific requirements of the cookware design and intended use.
Overall, the purpose of a base grooving machine is to enhance the performance, functionality, and visual appeal of pots and pans by creating grooves that improve heat conduction, prevent sticking, and optimize cooking results.
Groove Patterns
The groove patterns created by a base grooving machine on pots and pans can vary depending on the specific design and intended use of the cookware. Here are a few common groove patterns that are often used:
- Straight Lines: Straight grooves running parallel or perpendicular to each other are a popular choice. These grooves can be evenly spaced or staggered, depending on the desired aesthetic and functional requirements.
- Radial Grooves: Radial patterns consist of grooves radiating from the center of the base outward. This pattern helps with heat distribution and can provide a visually appealing design.
- Spiral Grooves: Spiral patterns involve grooves that form a continuous spiral shape from the center to the outer edges of the base. This pattern enhances heat conduction and can give a unique and decorative look to the cookware.
- Diamond or Crosshatch Patterns: These patterns involve intersecting straight lines or diagonal grooves, creating a diamond or crosshatch design. These patterns provide additional surface area and enhance the non-stick properties of the cookware.
- Customized Grooves: Manufacturers can also create custom groove patterns based on specific design requirements or branding elements. These can include logos, symbols, or unique groove arrangements that differentiate the cookware in the market.
The choice of groove pattern depends on factors such as the intended cooking performance, aesthetic preferences, and brand identity. Manufacturers may experiment with different patterns to achieve the desired functional and visual characteristics of their pots and pans.
Base grooving machines can create a wide variety of groove patterns, each with its own unique functional and aesthetic characteristics. Some common groove patterns include:
1. V-Grooves: V-shaped grooves are the most common groove pattern, offering a balance of strength, grip, and aesthetics. They are often used on the bases of cookware, appliances, and other objects where a secure grip and even heat distribution are essential.
2. U-Grooves: U-shaped grooves provide a wider and deeper groove than V-grooves, offering greater stability and heat retention. They are often used on larger appliances and objects where a more substantial groove is required.
3. Round Grooves: Round grooves offer a smoother, more aesthetically pleasing appearance compared to V- and U-shaped grooves. They are often used on decorative objects and components where a subtle accent is desired.
4. Straight Grooves: Straight grooves are a simple and functional pattern that can be used for a variety of purposes, such as creating drainage channels, ventilation paths, and mounting points. They are often used on industrial components and appliances.
5. Chevron Grooves: Chevron grooves feature a zigzag pattern that adds visual interest and complexity to the surface. They are often used on decorative objects and components to create a distinctive design aesthetic.
6. Herringbone Grooves: Herringbone grooves feature a diagonal crisscross pattern that resembles fish scales. They are often used on decorative objects and furniture to create a rich and textured surface.
7. Random Groove Patterns: Random groove patterns can be created to achieve a more organic and unpredictable look. They are often used on decorative objects and sculptures to add visual interest and uniqueness.
The specific groove pattern chosen depends on the desired function, aesthetics, and material being grooved. Base grooving machines are versatile tools that can create a wide variety of patterns to meet the specific requirements of various applications.
Operation
The operation of a base grooving machine involves several steps to ensure accurate and efficient groove formation on the pots and pans bases. Here is a general overview of the operation:
- Preparation: Before starting the operation, the machine needs to be set up and adjusted according to the desired groove pattern and dimensions. This includes adjusting the groove depth, width, and spacing, as well as positioning the pots and pans securely on the machine.
- Loading the Workpiece: The pots and pans are loaded onto the machine’s holding fixtures or clamps, ensuring they are properly aligned and secured in place. This step is crucial to maintain consistency and precision in groove placement.
- Groove Formation: The machine is activated, and the grooving tool or cutter is brought into contact with the base of the pots and pans. The tool applies pressure or cutting action to create the grooves according to the predetermined pattern. The machine may use various mechanisms such as rotating cutters or hydraulic/pneumatic systems to facilitate the groove formation process.
- Control and Monitoring: During the operation, the machine’s controls and monitoring systems ensure that the grooving process is carried out accurately and consistently. This may involve real-time feedback on groove depth, alignment, and other parameters to maintain quality control.
- Unloading and Inspection: Once the grooving operation is complete, the pots and pans are removed from the machine. They are inspected to ensure the grooves meet the required specifications in terms of depth, width, spacing, and overall appearance.
- Cleaning and Finishing: After grooving, the pots and pans may undergo further cleaning or finishing processes to remove any debris or burrs resulting from the grooving operation. This ensures the final product is smooth, visually appealing, and ready for subsequent manufacturing steps or packaging.
It is important to note that the specific operation of a base grooving machine may vary depending on the design and features of the machine itself. Manufacturers typically provide detailed instructions and guidelines for safe and efficient operation, which operators should follow to achieve consistent and high-quality results.
Adjustable Parameters
The base grooving machine usually offers adjustable parameters to accommodate different groove patterns and variations in pots and pans. Some of the adjustable parameters may include:
- Groove Depth: The machine allows for the adjustment of the groove depth, which determines the vertical dimension of the groove. This parameter can be set according to the specific requirements of the pots and pans being processed.
- Groove Width: The machine enables the adjustment of the groove width, which determines the horizontal dimension of the groove. This parameter can be set to achieve the desired width for the grooves on the pots and pans.
- Groove Spacing: The machine provides the flexibility to adjust the spacing between the grooves. This parameter determines the distance between each groove and can be customized based on the design or functional requirements of the pots and pans.
- Groove Pattern: The base grooving machine may offer different preset groove patterns or allow for the programming of custom groove patterns. This allows for the creation of various groove designs, such as straight lines, arcs, or more complex patterns, depending on the desired aesthetic or functional outcome.
- Speed Control: The machine typically provides adjustable speed control, allowing operators to set the speed at which the grooving tool or cutter moves across the base of the pots and pans. This parameter can affect the efficiency, accuracy, and quality of the grooving process.
- Feed Rate: The machine may offer the capability to adjust the feed rate, which determines how fast the pots and pans are moved through the machine during the grooving operation. This parameter can impact the overall production rate and the consistency of groove formation.
These adjustable parameters provide operators with the flexibility to adapt the base grooving machine to different pots and pans sizes, shapes, and design requirements. By fine-tuning these parameters, manufacturers can achieve precise and consistent groove patterns on their products.
EMS Metalworking Machinery: Your Trusted Partner in Precision Metalworking
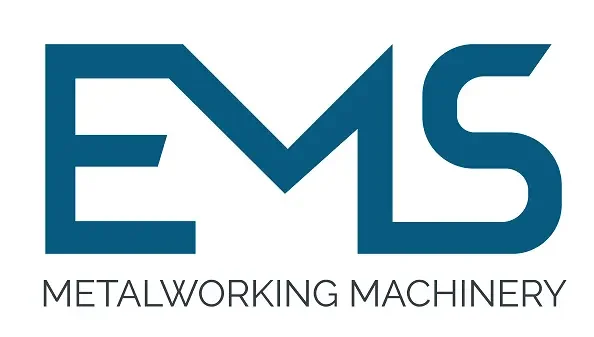
EMS Metalworking Machinery is a leading manufacturer of high-quality metalworking equipment, dedicated to providing innovative solutions that meet the evolving needs of industries worldwide. With a rich history of excellence and a commitment to technological advancement, we have earned a reputation for delivering cutting-edge machinery that ensures precision, efficiency, and durability.
Our Product Range:
- CNC Spinning Lathes: From precision bench lathes to heavy-duty industrial models, our lathes offer unmatched accuracy and performance for a wide range of applications, including machining shafts, gears, and other cylindrical components.
- Trimming Beading Machine: Our trimming beading machines are designed to provide exceptional cutting capabilities and versatility, enabling you to create complex shapes and intricate details with ease. Whether you need a horizontal or vertical trimming machine, we have the perfect solution for your needs.
- Hydraulic Deep Drawing Press Machines: Our hydraulic deep drawing press machines are built to deliver precise and powerful drawing operations, ensuring clean holes and exceptional surface finishes. We offer a comprehensive range to suit various applications.
- Grinding Machines: Our grinding machines are engineered for precision and efficiency, allowing you to achieve the highest levels of surface finish and dimensional accuracy. Whether you need a surface grinder, cylindrical grinder, or tool grinder, we have the equipment to meet your specific requirements.
- Sawing Machines: Our sawing machines are designed for fast and accurate cutting of metals, providing clean cuts and minimal burrs. From band saws to circular saws, we offer a variety of options to suit different materials and cutting needs.
- Custom Machinery: In addition to our standard product line, we also specialize in custom machinery fabrication. Our experienced engineers can work with you to design and build tailored solutions that meet your unique requirements and optimize your production processes.
Why Choose EMS Metalworking Machinery:
- Quality: Our machines are crafted with the highest quality materials and components, ensuring long-lasting performance and reliability.
- Precision: We are committed to delivering machinery that meets the most stringent tolerances and standards, ensuring exceptional accuracy in your metalworking operations.
- Innovation: We continuously invest in research and development to stay at the forefront of technological advancements, offering innovative solutions that enhance your productivity and efficiency.
- Customer Support: Our dedicated team of experts is always available to provide comprehensive support, from machine selection and installation to maintenance and troubleshooting.
- Customization: We understand that every business has unique needs, and we offer flexible customization options to tailor our machines to your specific requirements.
At EMS Metalworking Machinery, we are more than just a supplier of equipment; we are your trusted partner in metalworking success. By choosing EMS, you can be confident in the quality, reliability, and performance of your machinery, enabling you to achieve your business goals and stay ahead of the competition.
EMS Metalworking Machinery
We design, manufacture and assembly metalworking machinery such as:
- Hydraulic transfer press
- Glass mosaic press
- Hydraulic deep drawing press
- Casting press
- Hydraulic cold forming press
- Hydroforming press
- Composite press
- Silicone rubber moulding press
- Brake pad press
- Melamine press
- SMC & BMC Press
- Labrotaroy press
- Edge cutting trimming machine
- Edge curling machine
- Trimming beading machine
- Trimming joggling machine
- Cookware production line
- Pipe bending machine
- Profile bending machine
- Bandsaw for metal
- Cylindrical welding machine
- Horizontal pres and cookware
- Kitchenware, hotelware
- Bakeware and cuttlery production machinery
as a complete line as well as an individual machine such as:
- Edge cutting trimming beading machines
- Polishing and grinding machines for pot and pans
- Hydraulic drawing presses
- Circle blanking machines
- Riveting machine
- Hole punching machines
- Press feeding machine
You can check our machinery at work at: EMS Metalworking Machinery – YouTube
Applications:
- Beading and ribbing
- Flanging
- Trimming
- Curling
- Lock-seaming
- Ribbing
- Flange-punching