
Automated Circular Shearing Machine: Metal forming and shearing machines are essential in manufacturing processes for shaping and cutting metal materials. Here’s an overview of these machines:
Metal Forming Machines
These machines are used to shape metal into desired forms through deformation, without removing material. The key metal forming processes include:
- Rolling: The metal is passed through rollers to reduce its thickness and shape it into sheets, plates, or coils.
- Forging: Metal is heated and then compressed between dies to shape it, often used for producing strong components like crankshafts.
- Extrusion: Metal is forced through a die to create long objects with a uniform cross-section, like rods or pipes.
- Stamping: A punch presses down on the metal sheet to form a specific shape, commonly used in car manufacturing.
- Bending: Metal is bent using force to achieve a desired angle, often used in sheet metal fabrication.
Key Types of Forming Machines:
- Presses: These use a die and a punch to apply force to the material, typically in stamping or forging.
- Roll Formers: Machines that apply pressure to form long sheets into various profiles.
- Extruders: Machines used for extrusion processes, especially in producing tubes, pipes, and profiles.
2. Metal Shearing Machines
Shearing machines are used to cut metal sheets or plates into specific sizes or shapes without removing material (as opposed to machining). This process involves applying a shear force to the metal, which shears the material along a straight line.
Types of Shearing Machines:
- Mechanical Shears: Utilize a mechanical drive to move the blade and cut metal. Often used in high-speed operations.
- Hydraulic Shears: These use hydraulic pressure to apply the shearing force and are more flexible in terms of the force they can apply.
- Guillotine Shears: A popular type of shear with a straight blade that moves vertically, suitable for cutting thick metal sheets.
Applications of Metal Forming and Shearing:
- Automotive Industry: Forming and shearing are used to create parts like body panels, frames, and structural components.
- Construction: Metal sheets and plates are often formed and sheared to create elements like beams, columns, and supports.
- Aerospace: Lightweight, strong parts made by forming and shearing are essential for aircraft manufacturing.
Metal forming and shearing machines are vital in the manufacturing process, particularly in industries that require precise shaping and cutting of metal materials. These machines enable the transformation of raw metal into usable forms such as sheets, tubes, or structural components. Metal forming involves the use of various techniques to alter the shape of the material without removing any of it, ensuring the preservation of material integrity and strength. Common methods include rolling, forging, extrusion, and stamping, each suited to different types of products, ranging from automotive parts to aerospace components.
On the other hand, shearing machines are used to cut metal sheets or plates into specific dimensions or shapes, using sharp blades that apply a shear force. These machines are designed to produce clean, straight cuts without the need for material removal. Shearing is commonly used for cutting thin to medium-thickness materials and is crucial for creating parts that require exact measurements and edges. Hydraulic shears, mechanical shears, and guillotine shears are some of the most common types, each offering unique advantages in terms of cutting capacity and precision.
Both forming and shearing technologies are critical in ensuring that metal products meet the required specifications for strength, durability, and precision, whether they’re used in construction, automotive, or industrial machinery.
The role of metal forming and shearing machines extends beyond just shaping and cutting; these processes are also central to optimizing production efficiency, material waste reduction, and overall cost-effectiveness in manufacturing. By using these machines, manufacturers can handle large volumes of materials with high consistency, ensuring that each component is made to specification and meets quality standards.
Metal forming techniques, especially when combined with automation and advanced control systems, allow for high-speed production of complex shapes and parts, minimizing human error and increasing throughput. For instance, in stamping or pressing operations, dies are used to create precise shapes in a single stroke, offering high productivity for mass production runs. This process is commonly used in industries where high volumes of parts are needed, such as automotive manufacturing, where everything from body panels to smaller components are stamped out with incredible speed and accuracy.
In the case of shearing, modern machines can handle different thicknesses and materials, from thin sheets to thicker plates. The efficiency and accuracy of shearing machines are crucial for industries like steel manufacturing, construction, and appliance production, where large quantities of metal sheets need to be cut into uniform sizes for further processing or assembly.
Furthermore, both metal forming and shearing contribute to material conservation. Instead of cutting away material to achieve a shape, forming processes manipulate the material into the desired form, often using less raw material and resulting in less waste. Shearing, while removing some material, can also be highly efficient in terms of waste minimization, especially when paired with technologies like nesting software that optimize the arrangement of parts on sheets to reduce scrap.
The development of CNC (computer numerical control) technology has also revolutionized these machines. With CNC, metal forming and shearing machines can operate with greater precision and flexibility, producing complex parts with minimal human intervention. This is especially beneficial for industries that require high levels of customization or production of parts with intricate designs.
Overall, these machines are essential to a wide range of industries, offering the capability to produce durable, high-quality metal components at scale. Whether through large-scale manufacturing, small-batch custom work, or continuous processing, metal forming and shearing are foundational technologies in modern industry, pushing the boundaries of what can be achieved in metalworking.
As industries continue to evolve and demand higher levels of precision, efficiency, and adaptability, metal forming and shearing machines are increasingly becoming more advanced. Technological innovations, such as robotics, AI-driven processes, and the integration of Industry 4.0 principles, are further enhancing their capabilities.
For example, robotic arms are now often integrated with metal forming machines for tasks like loading, unloading, and even fine-tuning the positioning of materials. This automation reduces human labor and increases the consistency of each part produced. In some cases, robots can work alongside human operators, taking on dangerous or repetitive tasks, thus improving workplace safety while maintaining high throughput.
In advanced forming technologies, such as hydroforming (where high-pressure hydraulic fluid is used to form metal into complex shapes), the machines are now becoming more adaptable to different types of materials and part designs. The ability to work with materials like aluminum, high-strength steels, and composites has opened up new possibilities in industries such as automotive and aerospace, where lightweight, high-strength components are crucial for fuel efficiency and performance.
In shearing machines, recent advances have focused on precision cutting, allowing for tighter tolerances and more intricate cuts. Machines with integrated laser cutting or plasma cutting technologies offer higher cutting speeds and improved accuracy, especially for complex shapes. These technologies enable shearing operations to achieve fine edges and tight tolerances without the need for additional finishing processes.
Another significant trend is the increasing emphasis on sustainability. In both metal forming and shearing, there is a growing push to reduce energy consumption, recycle scrap metal, and lower the environmental impact of production processes. Some newer machines are designed to be more energy-efficient, with electric drives replacing traditional hydraulic systems to reduce power consumption and improve control. Recycling metal scrap and optimizing cutting patterns to minimize waste are also becoming standard practices, contributing to a circular economy.
As digital technologies advance, smart manufacturing practices are being incorporated into metal forming and shearing. IoT (Internet of Things)-enabled machines can collect data in real-time, providing insights into machine performance, material flow, and product quality. This data can be used for predictive maintenance, helping to prevent downtime and extend the life of the equipment. Predictive algorithms can analyze data to forecast when parts will need maintenance or replacement, reducing unplanned outages and increasing overall productivity.
Additionally, 3D printing is beginning to complement traditional metal forming methods. While 3D printing in metals is still evolving, it’s being used to produce prototypes or low-volume, highly customized parts that would otherwise require expensive tooling. In the future, 3D printing may be combined with conventional forming techniques to create hybrid manufacturing processes that leverage the benefits of both.
The continual advancements in materials science are also shaping the future of metal forming and shearing. Advanced alloys and composite materials are increasingly being used in industries like aerospace, automotive, and electronics, demanding new forming and cutting technologies. For example, the automotive industry is moving toward more lightweight materials, which may require new methods to form or shear without compromising strength or durability.
In summary, the future of metal forming and shearing is marked by increased automation, precision, and sustainability. Innovations in robotics, AI, smart manufacturing, and material science are creating opportunities for manufacturers to produce higher-quality products more efficiently while minimizing waste and reducing their environmental impact. As these technologies continue to evolve, the possibilities for innovation in metalworking will only grow, helping to meet the demands of industries worldwide.
Rotary Circular Shearing Machine

A Rotary Circular Shearing Machine is a specialized type of shearing machine used primarily for cutting materials into circular shapes or strips. Unlike traditional shearing machines that use linear cutting motions, rotary shearing involves circular blades that rotate continuously to perform the cutting action. These machines are often used in industries where high-speed, continuous cutting of materials like metal coils, sheets, or wires is required.
Key Features:
- Rotary Blade Mechanism: The cutting action in a rotary circular shearing machine is accomplished by rotating blades, which move in a circular motion. These blades are typically mounted on a rotating drum or spindle and engage with the material as it moves through the machine.
- High Cutting Speed: The rotary motion allows for faster cutting speeds, making these machines ideal for high-volume production environments, such as those in the steel, automotive, and wire industries.
- Precision: Rotary circular shearing machines are capable of producing precise cuts, especially when equipped with advanced control systems like CNC (Computer Numerical Control), which ensures accurate alignment and cutting tolerances.
- Continuous Operation: One of the significant advantages of rotary shearing is that it can operate continuously, cutting materials as they are fed through the machine without the need to stop and reset for each cut. This is particularly beneficial in applications like coil slitting, where long sheets or coils need to be cut into narrower strips.
- Material Types: These machines can typically handle a wide range of materials, including metals (such as steel, aluminum, and copper), plastics, and sometimes even certain types of rubber, depending on the design.
- Adaptability: Rotary shearing machines can be adapted to cut materials in various thicknesses, widths, and diameters. The machine may also be equipped with adjustable blade settings to accommodate different cutting requirements.
Common Applications:
- Coil Slitting: Rotary circular shearing machines are often used to slit large coils of metal into narrower strips, which can then be processed further or used in manufacturing.
- Wire Cutting: These machines are suitable for cutting wires into specific lengths or creating precise circular sections for further processing.
- Sheet Cutting: For industries that require the cutting of metal sheets into circular or strip-shaped pieces, rotary circular shearing machines provide an efficient, high-speed solution.
- Automotive and Aerospace Parts: When manufacturing parts that require precise circular cuts or continuous length cuts (such as gasket material or various metal components), these machines are ideal due to their precision and speed.
Advantages:
- Speed and Efficiency: The continuous cutting process allows for fast production rates, which is critical in high-volume manufacturing environments.
- Minimal Material Waste: The precision of rotary shearing can help minimize material waste, especially when paired with optimized cutting patterns.
- Versatility: These machines can be adapted for different material types, thicknesses, and cutting requirements, making them versatile for various applications.
Limitations:
- Initial Setup Costs: While these machines are highly efficient, they can have higher upfront costs, especially if they are automated or feature advanced control systems like CNC.
- Maintenance: Like any machine with moving parts, rotary shearing machines require regular maintenance to ensure the blades are sharp and the system is running smoothly. Blade wear can reduce cutting efficiency, requiring periodic replacement or sharpening.
- Limited to Certain Cuts: Rotary shearing is typically used for cutting in circular or straight lines. It may not be suitable for making more intricate or complex cuts that require precise angular or irregular shapes.
In summary, a Rotary Circular Shearing Machine is a highly efficient tool for high-speed, continuous cutting of materials into circular shapes or strips. With its ability to handle large volumes of material, produce precise cuts, and minimize waste, it’s an essential tool in industries like metal processing, automotive manufacturing, and wire production.
A Rotary Circular Shearing Machine is specifically designed to handle continuous cutting processes with high speed and precision. It operates by using rotating blades that cut through materials in a circular motion, making it highly efficient for tasks that involve slitting or cutting metal coils, sheets, or other materials into narrow strips or circular shapes. These machines are widely used in industries that require rapid processing of materials, such as in steel mills, automotive manufacturing, and wire production. The key benefit of this type of machine is its ability to perform high-volume cutting operations without the need for frequent stops, allowing for uninterrupted, continuous production runs.
The rotary action of the blades provides a clean, precise cut, and because the cutting is done in a continuous motion, material handling can also be more streamlined. This process is ideal for producing products with consistent widths and lengths, such as strips of metal for further processing or specific applications like automotive parts or industrial components. In addition to metals, these machines can often handle various materials like plastic or rubber, making them versatile across different industries.
One of the advantages of using rotary circular shearing machines is their efficiency in terms of speed. The continuous nature of the cutting process allows for faster production, which is crucial when dealing with high volumes of material. In addition, rotary shearing can reduce material waste. With proper setup and control, the cutting patterns can be optimized to make the best use of the raw material, further improving the efficiency of the process.
Although these machines offer high-speed performance, they do require regular maintenance, especially to keep the blades sharp. Blade wear is inevitable, and the cutting performance can deteriorate over time without proper upkeep. Another consideration is that rotary shearing is primarily suited for straight-line or circular cuts. While this is ideal for many applications, it may not be suitable for more complex or intricate cutting shapes that require flexibility in terms of angles or non-linear cuts.
Overall, rotary circular shearing machines are essential for industries that require quick, reliable, and precise cutting of materials. Whether it’s slitting coils of steel, cutting wire into lengths, or producing metal strips, these machines enable manufacturers to meet high production demands while maintaining precision and reducing waste.
As technology continues to advance, the design and functionality of rotary circular shearing machines are also evolving. One significant trend is the integration of automation and smart technology. Many modern machines now incorporate CNC (Computer Numerical Control) systems, which allow for precise adjustments to the cutting parameters, such as blade speed, pressure, and cutting depth. This enhances the overall accuracy and consistency of the cuts, ensuring that the final products meet stringent quality standards.
In addition, sensor technology is increasingly being used to monitor the cutting process in real-time. Sensors can detect issues such as blade misalignment or material inconsistencies, alerting operators to potential problems before they lead to costly defects or downtime. This level of monitoring not only improves the quality of the finished products but also extends the lifespan of the machine by ensuring that it operates within optimal parameters.
Another area of improvement is in the energy efficiency of rotary circular shearing machines. As industries become more environmentally conscious, manufacturers are striving to reduce energy consumption in their operations. Newer machines are being designed with more energy-efficient motors and hydraulic systems that reduce power usage without compromising performance. This is an essential factor, especially for companies aiming to reduce operational costs and meet sustainability goals.
The material handling aspects of rotary shearing machines have also seen improvements. Automated loading and unloading systems, often integrated with robotic arms, are streamlining the workflow. These systems can load coils or sheets of material into the machine, remove finished products, and even stack or pack them for shipment—all without manual intervention. This level of automation not only reduces labor costs but also minimizes human error, contributing to faster turnaround times and fewer quality control issues.
Moreover, advancements in cutting blades are contributing to improved performance. Modern blades are made from advanced materials, such as carbide-tipped or diamond-coated metals, which offer superior durability and longer service life compared to traditional steel blades. These materials can withstand the wear and tear of continuous cutting, reducing the frequency of blade replacements and minimizing downtime for maintenance.
With the increasing demand for customization in manufacturing, rotary circular shearing machines are also being designed to handle a wider variety of materials and thicknesses. Whether it’s cutting high-strength alloys used in aerospace or lightweight materials like aluminum for automotive applications, the versatility of these machines is essential for meeting the diverse needs of modern industries.
In conclusion, rotary circular shearing machines continue to be a cornerstone in many industrial processes, thanks to their speed, precision, and efficiency. As automation, sensor technology, and energy-efficient systems become more integrated into these machines, they are not only enhancing production capabilities but also helping companies stay competitive in a rapidly evolving marketplace. By offering high-volume, continuous, and precise cutting capabilities, these machines are shaping the future of manufacturing across various sectors.
Looking further into the future of rotary circular shearing machines, we can expect continued advancements that will push the boundaries of efficiency, precision, and adaptability. One of the key developments is the integration of artificial intelligence (AI) and machine learning (ML). These technologies can help optimize the cutting process in real-time by analyzing data from sensors and other sources. AI could be used to predict and adjust parameters like cutting speed, pressure, and blade angle, adapting to changes in the material being processed or in the wear of the blades. This dynamic adaptability can significantly reduce the need for manual intervention, ensuring a smooth and automated operation with minimal downtime.
Additionally, 3D modeling and simulation tools are becoming more common in the design and optimization of rotary shearing machines. By using these tools, manufacturers can simulate the entire cutting process before physical production, identifying potential issues such as material distortion or inefficiencies in cutting patterns. This can lead to better machine setups, fewer errors, and optimized cutting paths, which translates into faster production times and reduced material waste.
Another trend is the increasing focus on precision cutting at finer tolerances. Industries like aerospace, electronics, and medical devices often require parts that have incredibly tight tolerances, and rotary circular shearing machines are being developed to meet these exacting standards. The ability to consistently achieve micron-level accuracy in cutting without compromising speed or throughput will make these machines even more valuable in specialized fields that demand high-performance components.
As part of the broader trend toward sustainability, there will also be continued improvements in reducing the environmental impact of rotary shearing machines. These could include further enhancements to energy-efficient motors, the use of environmentally friendly lubricants, and better systems for recycling metal scrap generated during the cutting process. More manufacturers will adopt closed-loop systems where scrap is collected, processed, and reused within the same production cycle, minimizing waste and maximizing the use of raw materials.
Another important development will likely be advanced human-machine interfaces (HMIs). As machines become more sophisticated, operators will need more intuitive ways to interact with them. The future of rotary circular shearing machines might involve touchscreen displays, voice-controlled systems, or augmented reality (AR) interfaces that allow operators to interact with the machine in more advanced ways. These interfaces could display real-time diagnostics, provide visual representations of the cutting process, and even guide operators through troubleshooting steps, making it easier to manage the machines and respond quickly to issues.
Finally, with the global trend toward Industry 4.0, rotary circular shearing machines will become even more integrated into the broader manufacturing ecosystem. This will include seamless communication with other machines on the shop floor, sharing data to ensure smooth workflows and optimized production scheduling. By syncing with ERP (Enterprise Resource Planning) and MES (Manufacturing Execution Systems), these machines can help create a more connected, transparent, and efficient production environment, allowing manufacturers to monitor performance across their entire operation in real time.
In essence, the future of rotary circular shearing machines is likely to be characterized by an even greater emphasis on automation, precision, sustainability, and interconnectedness. These advancements will allow manufacturers to meet the growing demands for speed, quality, and efficiency in industries ranging from automotive to aerospace and beyond, positioning rotary circular shearing machines as an essential tool in the future of manufacturing.
Automated Circular Shearing Machine
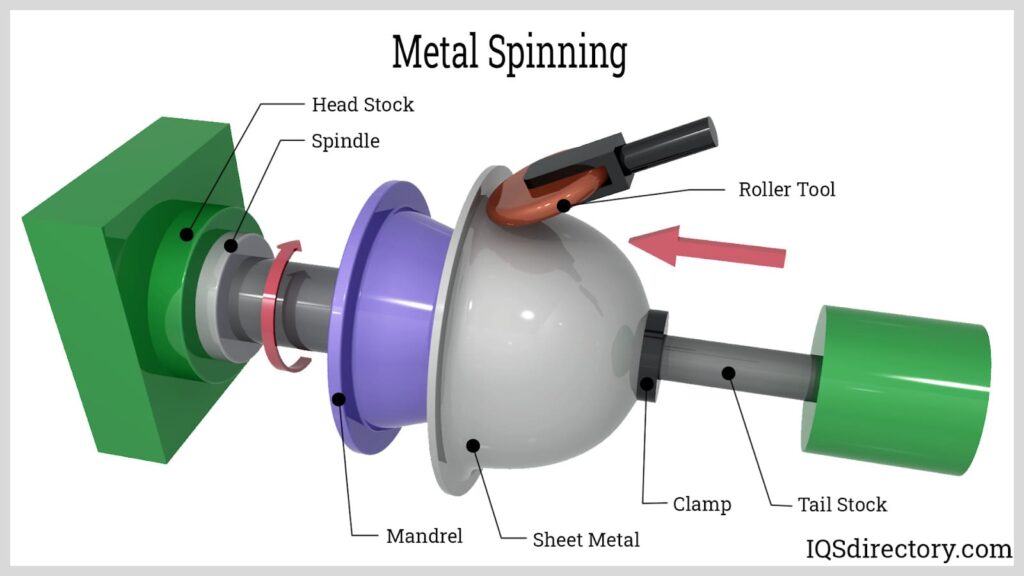
An Automated Circular Shearing Machine is a sophisticated, high-efficiency machine designed for cutting materials into circular or strip shapes using automated processes. These machines are an advanced version of traditional circular shearing systems, offering enhanced precision, speed, and consistency. The integration of automation allows for seamless, high-volume production with minimal human intervention, making them ideal for industries that require high throughput and precision.
The primary function of an automated circular shearing machine is to cut materials like metal coils, sheets, or wire into predetermined lengths, widths, or circular sections. By automating various aspects of the process, these machines not only boost productivity but also reduce operational costs, improve material handling, and minimize the risk of errors.
Key Features of Automated Circular Shearing Machines:
- Automated Material Feeding: One of the key features of automated shearing machines is their ability to handle the material feeding process without human intervention. Rollers, conveyors, or robotic arms feed the material continuously into the machine, maintaining a consistent speed and pressure. This ensures that the cutting process is smooth and efficient.
- Precision and Control: Automated machines are equipped with CNC (Computer Numerical Control) systems or PLC (Programmable Logic Controllers) that allow operators to precisely program the cutting parameters. This includes adjusting the speed, cutting angle, and length, ensuring the material is cut exactly to specifications every time.
- High-Speed Cutting: The integration of automation enables these machines to work at high speeds, drastically improving production rates. The machine can operate continuously, producing large quantities of precisely cut material without requiring frequent stops for resetting or manual adjustments.
- Reduced Human Intervention: Automation reduces the need for manual labor in operating the machine, loading materials, or removing finished parts. This minimizes human error, improves safety, and reduces labor costs. The automation system ensures that the machine operates without the need for constant monitoring, allowing operators to focus on other tasks.
- Real-Time Monitoring and Diagnostics: Many automated machines are equipped with sensors and IoT (Internet of Things) technology to provide real-time data about the machine’s operation. This includes monitoring cutting speed, blade wear, material quality, and overall machine performance. Predictive analytics can be used to forecast when maintenance is needed, reducing unplanned downtime.
- Flexible Setup and Adjustments: Automated circular shearing machines are highly flexible, allowing for easy adjustment of settings to accommodate different materials, thicknesses, or product specifications. This adaptability makes them useful in industries with varying production needs, such as automotive, aerospace, and metal fabrication.
- Material Handling Systems: Advanced automated systems include material handling capabilities, such as automatic stacking, sorting, and packaging of finished products. This ensures that the parts are immediately ready for the next step in the production process or shipping, further improving overall efficiency.
Applications:
- Automotive Manufacturing: Automated circular shearing machines are commonly used to cut metal sheets into specific shapes and sizes for automotive components. Parts such as body panels, chassis, and structural components can be produced with high precision.
- Metal Coil Slitting: In industries that process large coils of metal, automated circular shearing machines are used to slit coils into narrower strips. These strips are then used in a variety of applications, including construction, appliance manufacturing, and more.
- Aerospace: In the aerospace industry, precision cutting is essential for producing lightweight, high-strength components. Automated shearing ensures that parts such as brackets, frames, and other critical components meet tight tolerances and performance standards.
- Construction and Structural Parts: Automated shearing machines are used to produce structural elements like beams, panels, and plates. These parts are often used in construction and heavy machinery manufacturing.
- Wire and Cable Cutting: These machines can also be used to cut wire or cables into exact lengths, which is particularly useful for industries that manufacture electrical components, wiring systems, or automotive parts.
Advantages:
- Increased Productivity: With automated systems, the machine operates continuously, significantly increasing output. The automation of material feeding, cutting, and part removal processes eliminates downtime, allowing for higher production rates.
- Improved Accuracy: Automated circular shearing machines provide consistent cutting quality, reducing errors associated with manual adjustments or human handling. The ability to program precise cutting parameters ensures that parts meet exact specifications every time.
- Cost-Effectiveness: By reducing labor costs, improving material utilization, and minimizing waste, automated systems help manufacturers achieve lower operational costs in the long run. Furthermore, the increased speed of operation means that more parts are produced in less time, improving the overall efficiency of the factory.
- Enhanced Safety: Automation reduces human involvement in the cutting process, decreasing the likelihood of accidents. Machines with automated safety systems, such as sensors and emergency stop functions, further improve worker safety on the shop floor.
Limitations:
- Initial Investment: While automated systems can provide significant cost savings in the long term, the initial investment required for purchasing and installing these machines can be high. The need for specialized training and setup also adds to the initial cost.
- Maintenance and Downtime: Despite automation, these machines still require regular maintenance. The complexity of the system may sometimes require specialized technicians for repairs, and downtime for maintenance can disrupt production if not properly managed.
- Flexibility: While automated systems are highly efficient, they may be less adaptable to highly customized production runs that require frequent changes in setup. For low-volume or highly customized products, non-automated systems might be more flexible.
Conclusion:
An Automated Circular Shearing Machine is a powerful tool for industries that need high-speed, high-precision cutting capabilities. By automating material feeding, cutting, and finishing operations, these machines provide improved productivity, precision, and safety while reducing labor costs and material waste. As automation technology continues to evolve, these machines are likely to become even more versatile and efficient, making them indispensable in industries such as automotive, aerospace, and metal processing.
Automated circular shearing machines continue to advance as industries seek ways to improve production efficiency and meet ever-tightening specifications. One of the biggest benefits of automation in shearing is the ability to integrate seamlessly into broader manufacturing systems. With advanced Industry 4.0 technologies, these machines can communicate with other machines and systems on the shop floor, contributing to a smarter, more interconnected production environment. For instance, a shearing machine might send data about its current operation—such as cutting speed, material type, or blade condition—directly to a central system that manages the entire production line. This allows manufacturers to keep track of the performance of each machine, make adjustments in real-time, and ensure that the entire operation is functioning at optimal efficiency.
Furthermore, AI and machine learning algorithms are being incorporated into automated circular shearing machines to further enhance their capabilities. These algorithms can analyze data from the machine’s sensors and predict when components might need maintenance or when performance might degrade. By detecting wear and tear on the blades or any irregularities in the material being cut, these systems can notify operators before issues lead to significant downtime, reducing unexpected maintenance costs. This predictive approach ensures that machines run for longer periods before needing repairs, improving the machine’s overall lifespan and reducing the chances of production delays.
The shift toward customization and flexibility in modern manufacturing also plays a role in the development of automated shearing machines. With consumers and industries alike demanding more personalized products and shorter production runs, machines need to be adaptable. Automated circular shearing machines are evolving to handle a wider range of material types, thicknesses, and sizes. This versatility is especially important for industries like aerospace, automotive, and medical device manufacturing, where precision is critical, and materials can vary widely depending on the specifications of each product.
While automation offers many advantages, such as reduced human error and increased efficiency, it also introduces challenges. For instance, the level of complexity in setting up and programming these machines can be a barrier for smaller manufacturers or those with less technical expertise. As machines become more automated and integrated, the learning curve can become steeper, requiring staff to be trained on advanced programming, troubleshooting, and machine maintenance. However, the investment in training often pays off by ensuring that operators can maximize the potential of these machines, leading to higher productivity and fewer errors in the long run.
Looking ahead, the role of sustainability in manufacturing will continue to drive the development of automated shearing machines. As industries are pressured to reduce their environmental impact, there will be a stronger emphasis on reducing material waste and energy consumption. Automated systems can play a crucial role in this effort by optimizing the cutting patterns and material flow to minimize waste during the shearing process. Moreover, as the demand for recycled materials increases, automated shearing machines that can process and cut scrap materials into usable shapes for reuse are likely to become more common. This closed-loop approach supports a more sustainable, circular economy where materials are continuously reused rather than discarded.
Automation in circular shearing also opens the door for increased integration with other manufacturing processes. For example, in industries where products need to undergo additional processing, such as welding, forming, or coating, automated shearing machines can be integrated into the production line to provide smooth transitions between stages. This reduces the need for manual intervention between processes and ensures that parts are cut with precision, ready for the next phase of production. The ability to automate these processes from start to finish reduces human error, improves part quality, and accelerates time to market.
As these machines become even more sophisticated, the future may also see the introduction of smart shearing systems that can learn and adapt over time based on real-world data. These systems could fine-tune themselves for different types of material, thickness, and desired outcomes without requiring manual intervention. As such, automated circular shearing machines will continue to be a core component of modern manufacturing, helping industries meet the growing demands for speed, precision, and sustainability while driving innovation and efficiency in production processes.
Looking further into the future of automated circular shearing machines, we can expect the evolution of more autonomous systems that minimize the need for human oversight. These machines may not only adjust cutting parameters dynamically based on real-time data but could also self-optimize by adjusting their performance based on wear patterns, material inconsistencies, or even the operating environment. For example, a machine could automatically detect when a blade is starting to dull and adjust the cutting speed or pressure to compensate, reducing the need for immediate blade replacement and ensuring consistent quality throughout production runs. This level of automation could be enhanced by advanced machine vision systems, which would allow the machine to “see” the material and detect any imperfections or variances before making a cut, ensuring that only perfect material enters the cutting process.
The trend of collaborative robotics (cobots) could also play a significant role in the next generation of automated circular shearing machines. Cobots, designed to work alongside humans, can assist in tasks that require high precision, flexibility, and dexterity, making them ideal for material handling and assembly tasks around shearing machines. These cobots would be programmed to load, unload, and sort materials quickly and efficiently, further reducing human involvement in repetitive or hazardous tasks. The integration of cobots could lead to highly flexible production environments where machines can easily switch between different product types or material configurations without the need for long setup times or manual intervention.
Additionally, cloud computing and data analytics are expected to become integral components of the future automated shearing machines. These machines could be connected to cloud platforms that provide comprehensive real-time monitoring, analysis, and reporting of machine performance across multiple sites or plants. Manufacturers could leverage cloud-based dashboards to monitor key performance indicators (KPIs), track productivity, and analyze trends across different production lines, enabling data-driven decisions to improve operational efficiency. These platforms could also facilitate remote diagnostics and troubleshooting, allowing technical support teams to fix issues without being physically present at the machine site, thus reducing downtime and increasing operational uptime.
The role of cybersecurity will also become more critical as automated circular shearing machines become more connected. With increased connectivity comes an increased risk of cyber threats, particularly in industries that rely heavily on automated systems and data-sharing networks. Manufacturers will need to invest in robust cybersecurity measures to protect both their machines and their sensitive production data from unauthorized access or attacks. This could include encrypted communication protocols, multi-factor authentication for system access, and real-time threat detection systems that monitor network traffic and alert operators to potential vulnerabilities.
Moreover, sustainable manufacturing practices will likely drive the development of even more eco-friendly automated circular shearing systems. Manufacturers are under increasing pressure to reduce their carbon footprints and energy usage, and automated shearing machines will evolve to meet these needs. Energy-efficient motors, advanced cooling systems, and improved waste management techniques are expected to become standard features. Additionally, some machines may incorporate zero-emission technologies, utilizing electric drives instead of traditional hydraulic or pneumatic systems, further contributing to the reduction of environmental impact.
The integration of additive manufacturing (3D printing) with shearing technology could also become more prominent. Although shearing machines primarily focus on subtractive processes (removing material), the synergy between additive and subtractive processes in certain industries could become more apparent. For instance, in the aerospace or automotive industries, components might first be printed using additive manufacturing and then finished or cut into specific shapes using an automated circular shearing machine. This hybrid approach could lead to innovations in material efficiency and faster prototyping, ultimately speeding up the time-to-market for new products.
In terms of material innovation, automated circular shearing machines will likely be adapted to handle cutting-edge materials such as composite materials, high-strength alloys, and even smart materials that can change their properties based on external stimuli. As industries move toward lighter, stronger, and more complex materials, the cutting technology must evolve to accommodate these materials without compromising the speed or quality of the cuts. This might involve the use of laser-guided cutting, ultrasonic waves, or abrasive water jets integrated into the shearing system to handle more difficult materials without damaging them.
Lastly, the future of automated circular shearing machines will likely see further advancements in human-centered design. The machines will be designed to be even more intuitive, with user-friendly interfaces that make it easier for operators to interact with the system. These interfaces might incorporate augmented reality (AR) or virtual reality (VR) elements that provide operators with an interactive view of the cutting process or maintenance procedures, enhancing the ease of use and accessibility of the machines. This will help operators with varying levels of expertise to manage the machine with confidence, improving overall productivity and reducing the risk of errors.
As the technology behind automated circular shearing machines continues to evolve, they will not only become more efficient but will also drive innovation in manufacturing processes across industries. By combining advanced automation, connectivity, sustainability, and adaptability, these machines will remain a vital tool in meeting the increasing demands for precision, speed, and customization in modern manufacturing.
The ongoing advancements in machine learning (ML) and artificial intelligence (AI) will continue to enhance the capabilities of automated circular shearing machines. One of the most promising applications of AI is in adaptive cutting strategies. AI could enable the shearing machine to analyze the material’s properties in real-time, such as its thickness, surface texture, or even underlying structural weaknesses. Based on this analysis, the machine could adjust its cutting parameters (speed, pressure, blade angle) dynamically to ensure optimal results for each specific material type. This could lead to even higher precision, especially when working with materials that have varying physical characteristics, such as steel alloys, composites, or specialty coatings.
Additionally, machine learning algorithms could be used to predict and optimize the cutting process. Over time, these algorithms would learn from the historical data generated by the machine, understanding patterns in material behavior, tool wear, and process performance. As a result, the system could continuously improve its cutting techniques to minimize waste, reduce energy consumption, and maximize throughput. These intelligent systems could even anticipate the need for blade replacement or adjustments, minimizing downtime and ensuring that the shearing machine operates at peak efficiency throughout its lifecycle.
In terms of maintenance, AI-powered predictive maintenance systems are becoming more widespread. These systems rely on continuous data collection from the shearing machine’s sensors to identify early signs of wear and tear, overheating, or component failure. For example, temperature sensors might detect rising temperatures in the motor or hydraulic system, which could indicate a problem. Using this data, the system can predict when parts need to be serviced or replaced, preventing unplanned downtime and extending the lifespan of the machine. This proactive maintenance model reduces the need for costly emergency repairs and helps manufacturers avoid extended production stoppages.
The introduction of robotics and automation integration is also transforming the way materials are handled in the shearing process. Collaborative robots (cobots) are being integrated with automated circular shearing machines to handle tasks such as loading and unloading materials, sorting, stacking, and packaging finished products. These cobots can work alongside human operators, handling repetitive or physically demanding tasks, and reducing the risk of injury while increasing operational efficiency. Moreover, the flexibility of cobots allows them to quickly adapt to different materials, part sizes, and production requirements, making them ideal for industries that require quick setup changes or low-volume, high-mix production runs.
Another important trend is the increasing use of robotic vision systems to assist in quality control. These systems use 3D cameras and machine vision algorithms to inspect the cuts in real-time, ensuring that each part meets strict quality standards. These systems can check for defects such as burrs, irregular edges, or dimensional inaccuracies, and can provide immediate feedback to the shearing machine or to operators for corrective actions. This is particularly useful in industries where even slight deviations in part quality can have significant consequences, such as aerospace, medical device manufacturing, or high-end automotive production.
To further improve sustainability, automated circular shearing machines will increasingly be designed with features that minimize energy consumption and reduce the environmental footprint. For example, machines may be equipped with energy recovery systems, such as regenerative braking in motors or heat exchangers that capture and reuse waste heat from the machine’s operations. Energy-efficient components, such as low-power sensors and drives, will further reduce the total power consumption. Moreover, the incorporation of eco-friendly materials in machine construction, such as recycled metals and biodegradable lubricants, will align with global efforts to create more sustainable manufacturing processes.
The drive toward circular manufacturing will also influence the design of automated shearing machines. These machines could be integrated into systems that recycle material scrap or by-products, transforming them back into useful raw materials for production. For example, scrap metal from the shearing process could be collected, processed, and reintroduced into the production cycle. The ability to recycle materials efficiently not only reduces waste but also lowers the cost of raw materials, making the entire production process more cost-effective and environmentally responsible.
As digital twins become more common, manufacturers will be able to create virtual replicas of their shearing machines and entire production lines. These digital models simulate real-world operations and allow for the testing of different production scenarios or configurations. By using a digital twin, manufacturers can predict how different changes in the production process—such as material type, cutting speed, or machine setup—will affect overall performance, without making any physical adjustments to the machine. This enables more informed decision-making, optimized machine configurations, and greater flexibility in production scheduling.
Augmented Reality (AR) and Virtual Reality (VR) are also poised to revolutionize how operators interact with automated shearing machines. AR could be used to overlay critical information about the shearing process directly onto the operator’s view of the machine, providing real-time data about cutting parameters, material status, or maintenance needs. VR training environments could allow operators to learn how to troubleshoot and repair machines in a simulated, risk-free environment before working on the actual equipment, reducing the chance of operator errors and speeding up the onboarding process for new employees.
Lastly, the push for global standardization in manufacturing processes will likely influence the design of automated circular shearing machines. International standards for machine performance, safety, and environmental impact are expected to become more widespread, ensuring that these machines operate reliably and safely across different industries and regions. Manufacturers will need to comply with these standards, which may also involve adapting their machines to meet different regulatory requirements for emissions, energy consumption, and worker safety.
In summary, the future of automated circular shearing machines is poised to be shaped by cutting-edge technologies like AI, machine learning, robotics, and sustainability-driven design principles. These advancements will make shearing machines more intelligent, efficient, and adaptable, allowing manufacturers to respond faster to market demands, reduce waste, and enhance the overall quality of their products. As industries continue to evolve and embrace these technologies, automated circular shearing machines will play an increasingly critical role in driving productivity, innovation, and sustainability in the global manufacturing landscape.
Custom CNC Metal Forming Machine
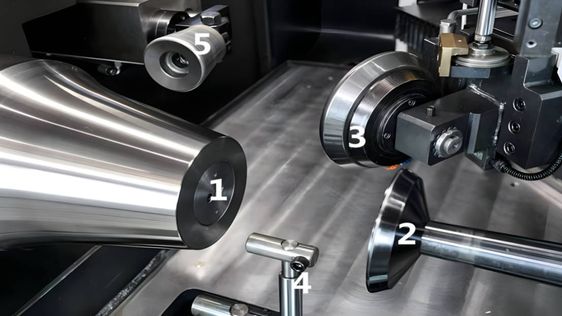
A Custom CNC Metal Forming Machine is a highly specialized piece of equipment used in various industries to shape and manipulate metal materials with precision. Unlike standard metal forming machines, which are typically designed for mass production of standard parts, a custom CNC (Computer Numerical Control) metal forming machine is tailored to meet the specific requirements of individual projects, materials, and part geometries. The customization allows for flexibility in design, accuracy, and the ability to handle complex and unique parts that may not be feasible with standard machines.
These machines leverage CNC technology to automate and control the metal forming process with extreme precision. CNC systems use digital instructions or programming to control the machine’s movements, ensuring that each part is formed exactly to specification. The custom aspect of these machines often includes modifications or unique setups to accommodate specific customer needs, material types, and production volumes.
Key Features of a Custom CNC Metal Forming Machine:
- Precision and Accuracy: CNC metal forming machines offer unparalleled precision, ensuring that each part meets tight tolerances. The system can control various parameters such as speed, pressure, and angles of movement, allowing for complex shapes to be formed accurately.
- Custom Tooling: One of the primary features of a custom CNC metal forming machine is the ability to create or modify tooling to meet specific requirements. Custom tooling allows the machine to handle non-standard part geometries, different metal types, and complex forming processes like bending, punching, stamping, or extrusion.
- Adaptability: These machines can be adapted to different production needs. Whether the requirement is for low-volume, high-mix production or a single custom prototype, the machine can be programmed and adjusted to suit the job. This makes it ideal for industries with ever-changing demands, such as aerospace, automotive, and medical device manufacturing.
- Complex Geometries: Custom CNC metal forming machines are often used to create parts with complex geometries that would be difficult or impossible to produce with traditional forming methods. This includes components with intricate curves, non-linear surfaces, or tight radii that require precise control and adjustment throughout the forming process.
- Versatility: These machines can be used for a wide variety of metal forming processes, such as:
- Bending: Precision bending of sheet metal to create specific angles or radii.
- Stamping: Forming parts by applying pressure to a metal sheet using dies to create desired shapes.
- Punching: Making holes or shapes in metal sheets through a punching process.
- Extrusion: Forcing metal through a die to create long parts of uniform cross-section, such as tubes or rods.
- Rolling: Continuously feeding metal through rollers to form shapes like coils, sheets, or profiles.
- Advanced Control Systems: The CNC system provides advanced control over the forming process, with features like real-time monitoring, automatic adjustments, and feedback loops to ensure high-quality results. These systems can also store and recall program settings, making it easier to repeat successful part production and scale up when needed.
- Material Flexibility: Custom CNC metal forming machines can handle a wide range of materials, from soft metals like aluminum to harder alloys like titanium and stainless steel. This versatility is important for industries that work with different materials for specific applications, such as electronics, medical devices, or industrial components.
- Integrated Quality Control: Many CNC metal forming machines come equipped with integrated quality control systems, such as vision inspection or laser measurement systems, to ensure that every part meets quality standards. This reduces the need for post-production inspection and minimizes the chance of defects.
- Reduced Setup Time: The customization of the machine, combined with the flexibility of CNC programming, allows for quick changes between production runs. Whether it’s a change in part design or a different metal, the machine can be adjusted through software, reducing setup times and increasing efficiency.
Applications of Custom CNC Metal Forming Machines:
- Aerospace Industry: The aerospace sector requires highly specialized parts made from materials like titanium and advanced composites. Custom CNC metal forming machines are used to create parts like turbine blades, brackets, housings, and structural components that must meet stringent standards for strength, weight, and precision.
- Automotive Manufacturing: In the automotive industry, these machines are used to produce parts such as chassis components, brackets, and body panels. The ability to form complex geometries is crucial in creating lightweight, durable parts for modern vehicles.
- Medical Device Manufacturing: Medical devices often require precision-forming of materials like stainless steel, titanium, and specialized alloys. Custom CNC metal forming machines are used to produce components like surgical instruments, implants, and casings for medical equipment, all of which must adhere to strict regulatory standards for safety and performance.
- Electronics: For electronic devices, custom CNC metal forming machines can be used to create enclosures, connectors, and other metal components that require precise dimensions and high-quality finishes. These machines help ensure that the metal parts are free from defects that could affect the performance of the electronic device.
- Custom Tooling and Dies: In industries that require frequent changes in part design, custom CNC metal forming machines are also used to create specialized dies, molds, and tooling that are used in stamping, injection molding, or extrusion processes.
- Defense and Military: The defense sector requires metal components with high strength and durability. Custom CNC metal forming machines can be used to produce parts for military vehicles, weapons systems, and other defense-related technologies, where precision and performance are critical.
Advantages of Custom CNC Metal Forming Machines:
- High Precision and Consistency: CNC technology ensures that every part is formed with high precision, which is crucial when dealing with tight tolerances and complex shapes. This consistency is especially important in industries where even slight deviations can lead to product failure.
- Reduced Waste: The accuracy of CNC metal forming allows for better material utilization, reducing waste during production. By precisely controlling the forming process, these machines help maximize the yield of usable parts from raw materials, reducing overall production costs.
- Flexibility for Prototyping and Low-Volume Production: Custom CNC metal forming machines excel in producing prototypes and low-volume runs. This flexibility is key for industries that frequently develop new products or require specialized parts that are not part of a standard production line.
- Enhanced Efficiency: With advanced programming and automated adjustments, these machines reduce the need for manual intervention, leading to faster cycle times and reduced labor costs. Once the machine is programmed, it can produce parts automatically with minimal oversight.
- Integration with Other Manufacturing Processes: Custom CNC metal forming machines can be integrated into larger manufacturing systems, enabling smoother transitions between different production processes, such as cutting, welding, or finishing. This integration can streamline workflows and reduce downtime between production stages.
Challenges and Limitations:
- Initial Cost: Custom CNC metal forming machines tend to be more expensive than standard machines due to their advanced features and customization options. The initial investment can be high, especially for industries that require machines with complex tooling and precise configurations.
- Complex Setup: While the customization of the machine provides flexibility, setting up a custom CNC metal forming machine for a new production run can be more complex and time-consuming compared to using a standard machine. Operators must program the machine with the correct parameters for each job, and specialized tooling may be required.
- Skill Requirements: Operating and programming a custom CNC metal forming machine requires specialized knowledge. Highly skilled operators and technicians are needed to ensure the machine runs efficiently, especially when it comes to troubleshooting or adjusting machine settings for specific materials or designs.
In conclusion, a Custom CNC Metal Forming Machine offers advanced, highly flexible, and precise metal forming capabilities that cater to industries with demanding production requirements. The ability to tailor the machine’s setup, tooling, and control system to specific applications allows manufacturers to produce complex parts with high precision, improving the overall efficiency, quality, and versatility of their production processes.
Custom CNC metal forming machines continue to transform the way industries approach precision manufacturing. As technology evolves, these machines integrate increasingly advanced features that make them indispensable in sectors that demand high-quality and highly intricate parts. One of the most notable advancements is the integration of advanced sensors and real-time monitoring systems that allow operators to monitor the machine’s performance while it’s running. These sensors can detect anomalies, material inconsistencies, or even tool wear, enabling immediate adjustments to be made to ensure continuous precision. This proactive system helps reduce errors during production and keeps the machine running at peak performance without the need for manual intervention.
Furthermore, custom CNC metal forming machines are being designed with advanced human-machine interfaces (HMIs) that provide operators with a more intuitive and user-friendly experience. Through touchscreens, voice commands, or even augmented reality (AR) systems, operators can interact with the machine in ways that make it easier to set up, monitor, and troubleshoot. These HMIs can show real-time data, provide feedback, and alert operators to any issues before they cause a production delay, ensuring that both the setup process and ongoing production runs smoothly.
In addition to increased connectivity, these machines can now be linked to broader manufacturing systems through industrial Internet of Things (IoT) technology. This connectivity allows for continuous data collection and analysis, which can then be used to optimize the machine’s operations, track performance metrics across multiple machines, and integrate with enterprise-level systems like Enterprise Resource Planning (ERP) or Manufacturing Execution Systems (MES). This connectivity also allows for remote monitoring, meaning that engineers or technicians can troubleshoot and even make adjustments from a distance, reducing the need for on-site visits and minimizing machine downtime.
As the demand for customization in consumer products continues to grow, CNC metal forming machines are being adapted to handle increasingly complex designs. This adaptability allows manufacturers to respond quickly to market demands and produce unique parts in smaller batches or even on-demand. In industries like aerospace and automotive, where custom parts are often needed for prototypes or low-volume production, custom CNC machines offer the flexibility to handle varying part sizes, material types, and geometries. This versatility not only improves production efficiency but also allows companies to innovate more rapidly, experimenting with different materials and designs without needing to invest in entirely new machines for each new project.
Sustainability is another key factor driving the evolution of custom CNC metal forming machines. Manufacturers are under pressure to reduce their carbon footprint and minimize waste, and these machines are increasingly being designed with sustainability in mind. With the ability to optimize material usage, custom CNC machines can minimize scrap metal, ensuring that the maximum amount of material is used efficiently. Moreover, many of these machines now feature energy-saving modes, which reduce electricity consumption during idle times or when the machine is not performing high-energy tasks.
The adoption of machine learning and artificial intelligence is also transforming the future of custom CNC metal forming machines. By learning from previous production runs, AI systems can make smarter decisions, adjusting cutting, forming, or shaping parameters automatically based on the material, complexity of the part, or environmental factors. These systems can optimize processes like cutting speed, pressure, and tool paths to achieve the best possible result while maintaining high efficiency and minimizing waste.
Moreover, as materials technology continues to advance, custom CNC metal forming machines will be designed to handle new, often more complex materials that were previously difficult to form. The increasing use of composite materials in industries like aerospace, automotive, and construction requires machines that can form parts with high strength-to-weight ratios and resistance to heat or corrosion. To handle these innovative materials, custom CNC machines are being adapted with special tooling and processing capabilities to form parts that meet the strictest industry standards.
The integration of additive manufacturing or 3D printing technology into custom CNC machines is also becoming more prominent. This hybrid approach allows manufacturers to 3D print part components or even tooling that can then be used in the traditional forming process. The ability to print custom dies, molds, or fixtures opens up new possibilities for complex designs that might have been cost-prohibitive or technically impossible to create using traditional methods. This integration of additive and subtractive technologies improves the flexibility of production, allowing manufacturers to switch between techniques depending on the specific needs of the project.
In parallel, robotics is being increasingly incorporated into CNC metal forming systems. Robotic arms can handle material loading, unloading, and even inspection, working seamlessly alongside the machine to ensure high productivity and safety. These robotic systems can take over repetitive tasks, such as handling heavy or difficult-to-manipulate materials, which allows human operators to focus on more complex tasks that require problem-solving or technical expertise.
As industries continue to pursue high-mix, low-volume production, the ability to quickly switch between different part designs and processes is becoming essential. Custom CNC metal forming machines are being designed with flexible setups that allow for rapid changeover between different projects. This flexibility reduces lead times and improves a company’s ability to handle diverse orders while maintaining high levels of precision and quality. These machines are ideal for industries that require unique parts or prototypes, where flexibility and precision are paramount.
With the continuous push for digitization in manufacturing, the role of smart factories is becoming more prominent. Custom CNC metal forming machines will be integrated into these smart factories, where data from all machines and processes will be gathered and analyzed in real time. This will provide manufacturers with actionable insights into performance, material usage, and potential improvements, leading to intelligent decision-making and the ability to predict and optimize production processes more efficiently than ever before.
In conclusion, the future of custom CNC metal forming machines is bound to be defined by ongoing advancements in automation, connectivity, sustainability, and materials innovation. The ability to handle complex designs, reduce waste, and improve production efficiency is what will continue to make these machines essential to industries across the globe. With greater intelligence, flexibility, and adaptability, custom CNC metal forming machines will drive forward the next generation of manufacturing, allowing for faster prototyping, smaller batch production, and enhanced product quality. These capabilities are pivotal to meeting the growing demands of highly specialized, precision-driven industries while ensuring greater sustainability and efficiency in production.
As the future of custom CNC metal forming machines continues to evolve, there are a few key trends and technological advancements that will shape their development and application in the years to come.
One of the most significant changes will be the integration of edge computing. With more and more machines becoming connected to networks and generating large amounts of data, edge computing will allow data processing to occur directly at the machine level, rather than sending all data to a central cloud server. This will reduce latency and allow real-time processing of critical machine data, enabling faster decision-making and immediate adjustments to the forming process. The integration of edge computing will be particularly beneficial for industries where time-sensitive production processes require quick, on-the-fly adjustments.
Another important development will be the rise of digital twins for CNC metal forming machines. A digital twin is a virtual replica of the physical machine, which mirrors its real-time operations and can be used for simulations and predictive analysis. By using a digital twin, manufacturers can test different setups, process parameters, and configurations in a virtual environment before applying them to the actual machine. This minimizes the risk of errors and ensures that production runs are optimized for efficiency and quality before they even begin. The ability to create and test different digital scenarios also improves the design phase for custom tooling, reducing time-to-market for new products.
Advanced material science is another area that will influence the future of CNC metal forming. As manufacturers work with new, innovative materials such as superalloys, composites, and nanomaterials, the forming processes will need to adapt to handle these advanced materials, which often require different properties for effective processing. Custom CNC machines will be designed with specialized tooling, temperature control, and material handling systems to ensure that these new materials can be formed into precise parts without compromising on their unique properties.
The need for enhanced operator training will also increase as these machines become more sophisticated. While CNC technology has always required a skilled operator, the complexity of modern, custom machines will necessitate new training methodologies. The use of virtual reality (VR) or augmented reality (AR) for operator training will allow workers to interact with simulated versions of the machines, giving them hands-on experience with machine setups, maintenance procedures, and troubleshooting without the need to work on the actual machine. This not only helps reduce errors and increase the operator’s skill level but also minimizes the risk of accidents or damage to expensive machinery during the learning phase.
Moreover, advanced predictive analytics will play a more prominent role in maintaining and optimizing custom CNC metal forming machines. By using machine learning algorithms to analyze historical production data, manufacturers can predict machine wear and potential breakdowns before they happen. This data can also be used to optimize production schedules, tool change intervals, and material usage, resulting in improved uptime, reduced waste, and more cost-effective production processes. Predictive maintenance powered by AI can also extend the lifespan of the machine, as it allows for timely servicing based on actual usage and wear patterns, rather than a set maintenance schedule.
Collaboration between human operators and machines will also continue to evolve, with more manufacturers opting for collaborative robotics (cobots). These lightweight robots can work alongside human operators, assisting with tasks such as material loading, unloading, and quality inspection. Cobots can significantly improve efficiency by reducing the strain on human operators and allowing them to focus on tasks that require higher-level decision-making or more precision. As cobots become more advanced, they will be able to learn and adapt to different environments, further enhancing their ability to work seamlessly with operators on a range of tasks in custom CNC metal forming applications.
One area where we can expect significant improvements is in the integration of renewable energy and energy-efficient technologies. As the demand for more sustainable manufacturing practices increases, custom CNC metal forming machines will incorporate technologies such as solar power, energy recovery systems, and low-energy motors. Solar panels or other renewable energy sources can be used to offset the power demands of CNC systems, while energy recovery systems can capture waste energy from the forming process and return it to the system, reducing overall energy consumption. These sustainability measures not only lower operating costs but also help meet increasingly strict environmental regulations.
The future of custom CNC metal forming machines will also see continued developments in automation software. The evolution of AI-driven software tools will provide manufacturers with more intuitive interfaces for programming and controlling complex machines. These systems will not only make the process of programming CNC machines easier but will also allow for more advanced operations such as self-calibration, automatic tool changeover, and real-time process optimization. With improved automation, CNC machines will be able to take on more tasks independently, increasing the level of autonomy in the manufacturing process and reducing the need for manual input.
Finally, advanced simulation software will continue to grow in importance for testing and optimizing the forming process. This software can model and simulate the entire forming operation—material behavior, tool interaction, and stress analysis—allowing manufacturers to predict how the material will behave under specific conditions. This reduces the number of physical prototypes required and ensures that the forming process is optimized for each unique material and part geometry.
In conclusion, custom CNC metal forming machines are poised to evolve rapidly, integrating the latest technologies such as artificial intelligence, edge computing, and augmented reality. The future of these machines will be defined by increased automation, greater material flexibility, sustainability initiatives, and the ability to work alongside humans in collaborative, adaptive environments. The next generation of custom CNC machines will provide manufacturers with even greater precision, speed, and efficiency, making them essential tools for industries that require high-quality, custom parts, all while reducing costs and increasing production flexibility. As industries continue to innovate, these machines will remain at the forefront of shaping the future of manufacturing.
As the future of custom CNC metal forming machines progresses, the next set of advancements will further enhance their capabilities, focusing on intelligent manufacturing ecosystems, greater material versatility, and advanced automation. Here are some additional considerations for the ongoing evolution of custom CNC metal forming technology:
One of the key areas of development will be intelligent manufacturing ecosystems. As more machines become interconnected, the rise of the smart factory will allow custom CNC metal forming machines to operate within a fully automated, integrated environment. These smart factories will rely on real-time data flow from sensors, production machines, robots, and other equipment to optimize the entire manufacturing process. Machines equipped with machine learning algorithms will continuously analyze this data, enabling them to improve production methods, detect inefficiencies, and even make real-time process adjustments autonomously. This level of automation could eventually result in self-optimizing production systems, where CNC machines can adapt to changing requirements and conditions without human intervention.
Moreover, the growing emphasis on Industry 4.0 technologies—such as the Internet of Things (IoT), cloud computing, and big data analytics—will significantly enhance the functionality of custom CNC machines. IoT-enabled sensors can collect detailed performance data from each machine, which can be analyzed in real time to monitor the condition of components like tools, motors, and spindles. This continuous stream of data allows predictive maintenance and process optimization, helping prevent unexpected downtime and improve the longevity of the machines. For example, the system might alert operators when a tool needs to be replaced or if a machine part is showing signs of wear, allowing for just-in-time maintenance.
The integration of cloud computing will further enable remote monitoring and control of the CNC machines. Operators and engineers will be able to access machine data, production metrics, and diagnostic information from anywhere, ensuring that they can stay informed and make adjustments as needed. This remote connectivity can help companies respond faster to production demands, troubleshoot issues remotely, and even access machine performance analytics to optimize the forming process.
Along with these intelligent systems, artificial intelligence (AI) will continue to evolve and integrate into custom CNC metal forming machines, leading to autonomous decision-making within the production process. AI-powered systems could analyze complex data patterns to fine-tune operational parameters such as cutting speed, temperature, or pressure, based on real-time feedback from the forming process. These systems could also be used for quality control, automatically detecting imperfections in finished parts by comparing them against digital models or known quality standards. This closed-loop feedback system would further reduce human error and ensure consistently high-quality outputs.
In parallel, machine vision systems are becoming more sophisticated, allowing CNC machines to inspect and analyze parts during and after the forming process. These vision systems can use advanced imaging techniques, such as 3D scanning or laser triangulation, to identify potential defects or irregularities in parts, ensuring that only flawless products leave the production line. Integrated machine learning models can help the vision systems improve over time, learning to detect even the most subtle defects, which would be hard for human inspectors to catch.
Another important trend is the growing use of sustainable materials and green manufacturing practices in custom CNC metal forming. As environmental concerns increase and regulatory pressures grow, manufacturers are turning to more sustainable approaches. The choice of materials is a significant part of this shift. For instance, recycled metals and lightweight alloys are becoming more commonly used, reducing environmental impact while still providing the necessary strength and durability for high-performance parts. Custom CNC machines are being designed to handle a broader range of materials, including those that are more challenging to process, like bio-based composites or recyclable thermoplastics.
To ensure sustainability, energy-efficient machine designs are becoming a priority. Manufacturers are working on improving the energy consumption of CNC metal forming machines, looking for ways to lower electricity usage during production. This includes the use of regenerative braking systems, variable speed drives, and more energy-efficient motors. Additionally, the industry is exploring ways to capture and repurpose waste heat from the forming process, further reducing the overall carbon footprint of manufacturing operations.
As material versatility continues to increase, the custom CNC metal forming machines of the future will need to handle even more challenging materials. These may include high-performance alloys, exotic metals, or even graphene-infused composites. These materials require specialized handling and processing capabilities, such as precise temperature control, laser-assisted forming or electroforming. The machines must be adaptable to these new materials while maintaining precision and avoiding material degradation during the forming process. Custom CNC systems will need to be designed to accommodate these innovations, requiring more advanced sensors, better temperature control, and novel tooling technologies.
As industries increasingly demand faster turnaround times and customization at scale, custom CNC metal forming machines will be designed with faster setup times and the ability to perform multiple processes in one setup. This could mean integrating multi-axis capabilities or hybrid manufacturing processes, where parts can undergo both additive and subtractive operations in a single run. This could significantly reduce lead times for custom parts, allowing manufacturers to fulfill small-batch or on-demand orders more efficiently and economically.
Furthermore, as global supply chains continue to evolve and change, flexibility in custom CNC systems will become more important. These machines will need to be agile enough to quickly adapt to fluctuations in demand, shifts in material availability, or changes in customer requirements. Manufacturers will need machines that can be easily reconfigured or adjusted to handle new part designs or materials, with minimal downtime or cost. The rise of modular machine designs will allow manufacturers to add or remove capabilities, such as new tooling options, robotic arms, or automation systems, based on the specific needs of their projects.
Additionally, the human-robot collaboration (cobots) trend will see further integration within the custom CNC metal forming machines. Cobots are well-suited for tasks such as part handling, tool change, and quality inspection, all of which can significantly improve the efficiency of the overall production process. These collaborative robots can work directly alongside operators without the need for safety cages, allowing for a seamless integration of human and machine effort. In a future smart factory, cobots and CNC machines will work in tandem, sharing information and optimizing workflows in real-time to ensure maximum throughput and precision.
As the global manufacturing landscape becomes more competitive, there will be an increased emphasis on digital twins for process optimization and performance tracking. These virtual representations of physical CNC machines can be used to simulate different operating conditions, test new processes, and troubleshoot potential problems before they occur in the real world. This ability to conduct comprehensive simulations without physical prototyping will lead to faster development cycles and more efficient product testing.
The advent of blockchain technology may also influence the future of custom CNC metal forming machines, especially in terms of traceability and quality assurance. Blockchain can help verify the authenticity and quality of parts throughout the supply chain, providing detailed records of each part’s production process. This technology can ensure that the final product meets the highest standards and provides customers with confidence that their parts have been manufactured according to specific requirements.
In conclusion, the future of custom CNC metal forming machines will be shaped by continuous advancements in automation, AI, sustainability, and material science. These machines will become more integrated, smarter, and more flexible, capable of handling increasingly complex materials and production requirements. With enhanced precision, real-time monitoring, and automation, the next generation of custom CNC metal forming machines will empower manufacturers to create high-quality, customized parts with greater speed and efficiency than ever before, all while reducing waste and improving sustainability. The evolution of these machines will ultimately reshape the landscape of modern manufacturing, enabling industries to meet the growing demands of the 21st century.
Hydraulic Custom Metal Forming Machine
A hydraulic custom metal forming machine is a specialized piece of industrial equipment used for shaping and forming metal components through the application of hydraulic force. These machines are widely employed in industries such as automotive, aerospace, heavy machinery, and construction, where high precision and large force applications are required. Hydraulic forming machines leverage the principles of fluid dynamics to apply consistent pressure, making them ideal for tasks that require forming large or complex shapes in metal sheets, tubes, and other forms of stock materials.
Key Components and Mechanism:
- Hydraulic System:
- At the heart of a hydraulic custom metal forming machine is its hydraulic system. This includes the hydraulic pump, cylinders, valves, and hoses. The hydraulic pump generates the pressure needed to move the cylinders, which are responsible for applying force to the metal material. The hydraulic fluid (often oil) transmits the force through the system.
- Hydraulic machines can exert much higher forces than mechanical presses, making them suitable for heavy-duty applications like bending, stamping, and deep drawing.
- Frame and Structure:
- The frame of the machine is designed to support the heavy forces generated by the hydraulic cylinders. It must be robust and able to withstand the stresses imposed during the forming process. Frames are typically made of high-strength steel to provide durability and prevent distortion over time.
- Hydraulic Cylinders:
- The hydraulic cylinders convert hydraulic energy into mechanical force. The size and number of cylinders determine the amount of force the machine can exert. Double-acting cylinders are often used to provide both upward and downward motion for the forming process.
- Tooling:
- Custom metal forming machines often come with a set of customized dies and tools designed to perform specific operations. Dies can be adapted for various forming processes, including bending, punching, drawing, and cutting.
- These tools are typically made from hardened steel to withstand the pressure and high temperatures associated with metal forming.
- Control System:
- Modern hydraulic custom metal forming machines are equipped with sophisticated control systems that allow precise control over parameters such as pressure, speed, and stroke length. These systems may include programmable logic controllers (PLCs) and human-machine interfaces (HMIs), which allow operators to set up, monitor, and adjust machine operations.
- Some machines also integrate advanced features like servo-hydraulic control, which offers more precise control of the hydraulic pressure and motion, making it easier to handle complex forms.
Types of Hydraulic Metal Forming Processes:
- Hydraulic Press Forming:
- In this process, metal sheets or blanks are placed between a male and female die. The hydraulic press applies pressure to the material to shape it into the desired form. This process is used for creating parts like automotive body panels, appliance components, and aerospace parts.
- It can be used for processes like deep drawing, bending, and stretching.
- Hydraulic Punching and Shearing:
- Hydraulic punching and shearing machines use hydraulic force to cut or punch holes in metal sheets or plates. These machines are essential for producing parts with precise holes or slots, like those required for electrical panels, sheet metal enclosures, and aircraft components.
- The shearing action is typically provided by a hydraulic ram that drives the punch through the material.
- Hydraulic Bending:
- Hydraulic machines can be used to bend metal sheets and plates by applying pressure from a hydraulic cylinder to a V-shaped die. This is commonly used for creating angles or curved shapes in sheet metal. The force exerted by the hydraulic machine ensures that the bending operation is consistent and accurate.
- Hydroforming:
- In hydroforming, high-pressure hydraulic fluid is used to form metal parts, especially in tube forming or deep drawing applications. The metal is placed inside a mold, and hydraulic pressure is used to form the metal into complex shapes. This is often used in industries like automotive for producing parts such as car chassis or engine components.
Advantages of Hydraulic Custom Metal Forming Machines:
- High Force Capability:
- One of the biggest advantages of hydraulic custom metal forming machines is their ability to exert immense force. The hydraulic system can apply far greater pressures than traditional mechanical presses, making it ideal for shaping hard, thick, or complex materials.
- Precision and Control:
- Hydraulic presses offer precise control over forming operations, allowing for the creation of highly accurate parts with consistent dimensions. The force can be adjusted during operation, which is crucial for handling delicate materials or complex geometries.
- Versatility:
- Hydraulic custom metal forming machines can be used for a wide range of metal forming processes, including bending, punching, deep drawing, shearing, and more. The flexibility to perform multiple processes with one machine makes them highly versatile for manufacturers.
- Adaptability for Customization:
- These machines can be customized with different tooling and die sets to produce a wide range of parts with different sizes, shapes, and features. This is particularly useful for industries that require custom parts in low to medium production volumes.
- Energy Efficiency:
- Hydraulic systems can be more energy-efficient in certain applications compared to mechanical systems. This is particularly true for processes that require intermittent force application, as the hydraulic system can be optimized to use only the energy needed for each stroke.
Applications of Hydraulic Custom Metal Forming Machines:
- Automotive Industry:
- Hydraulic custom metal forming machines are used extensively in the automotive sector to produce body panels, chassis components, and structural parts. Their ability to form large, complex shapes makes them ideal for creating parts with tight tolerances and high durability.
- Aerospace Industry:
- The aerospace industry uses hydraulic metal forming machines to create lightweight, high-strength components such as aircraft fuselages, wings, and engine parts. These machines can handle the high precision and material specifications required for aerospace applications.
- Construction and Heavy Machinery:
- For creating large metal parts used in construction machinery, hydraulic forming machines are used to shape components such as beams, frames, and structural supports. The high force capability allows for the forming of thick steel plates and other heavy materials.
- Consumer Goods Manufacturing:
- Hydraulic machines are also used to produce parts for consumer goods, such as household appliances, electronic enclosures, and small automotive components. Their ability to produce small to medium volumes of custom parts with intricate designs makes them ideal for this sector.
- Shipbuilding and Marine:
- In shipbuilding, hydraulic forming machines are used to create large metal components like hulls, propeller shafts, and engine parts. The large forming area and high-force capabilities allow for the production of oversized components that are essential in the marine industry.
Future Trends in Hydraulic Custom Metal Forming Machines:
- Increased Automation and AI Integration:
- The future of hydraulic custom metal forming machines will see increased integration with automated systems and AI-based controls. These systems will improve the machine’s ability to optimize forming processes in real time, predict maintenance needs, and increase overall efficiency.
- Hybrid Systems:
- The development of hybrid hydraulic machines, which combine servo-electric and hydraulic technologies, will allow for more precise control and energy efficiency while still maintaining the high force capabilities of hydraulic presses. These hybrid systems can provide more flexibility in production environments and reduce energy consumption.
- Eco-friendly Hydraulic Fluids:
- The industry is moving towards using biodegradable and environmentally friendly hydraulic fluids that are less harmful to the environment. This trend will help reduce the ecological impact of hydraulic forming processes.
- Smart Machine Features:
- The integration of smart sensors and cloud-based monitoring will allow operators to monitor the health of the hydraulic system and receive real-time updates on the status of production. This will enhance the efficiency of the machines, reduce downtime, and improve the overall manufacturing process.
In conclusion, hydraulic custom metal forming machines are essential tools for industries that require precise, high-force metal forming. Their versatility, ability to handle large components, and high control over the forming process make them invaluable in industries such as automotive, aerospace, construction, and more. As technology continues to evolve, these machines will become more energy-efficient, automated, and customizable to meet the ever-changing demands of modern manufacturing.
Hydraulic custom metal forming machines are expected to become even more advanced in the coming years as manufacturers continue to prioritize efficiency, sustainability, and automation. One of the significant trends is the integration of advanced data analytics and predictive maintenance systems. As machines become increasingly connected, real-time data from sensors embedded in the hydraulic systems will allow operators to monitor machine performance and detect issues before they lead to breakdowns. Predictive algorithms can analyze trends in the hydraulic fluid pressure, temperature, and system behavior to identify early signs of wear or failure, reducing costly downtime and improving overall machine reliability.
The development of servo-hydraulic systems is another key trend that will revolutionize the hydraulic forming machine landscape. Traditional hydraulic presses use a constant flow of hydraulic fluid to generate pressure, but servo-hydraulic machines employ electric motors to precisely control the fluid’s flow. This allows for more energy-efficient operation and greater control over the pressure and speed of the hydraulic cylinders. By optimizing energy usage, servo-hydraulic machines can significantly reduce operational costs while maintaining high levels of precision. These systems are particularly beneficial for applications that require dynamic adjustments during the forming process, such as complex forming or bending tasks.
There is also a growing interest in hybrid technologies that combine hydraulic power with other methods, such as electromechanical drives. These hybrid machines offer the best of both worlds—delivering the high-force capability of hydraulics with the precision and energy efficiency of electrical systems. Hybrid systems are designed to reduce energy consumption by using hydraulic power only when necessary, switching to electric power when lower force or more precision is required. This balance ensures that manufacturers can reduce their environmental footprint while maintaining optimal machine performance.
Another trend influencing hydraulic custom metal forming machines is the increasing emphasis on sustainability and green manufacturing practices. Hydraulic fluid, traditionally a petroleum-based product, is being replaced with biodegradable and more environmentally friendly alternatives. Additionally, the machines themselves are being designed with energy-saving features, such as variable-speed motors and regenerative braking systems, which recapture energy during the forming cycle and feed it back into the system. These advancements not only reduce energy consumption but also help manufacturers comply with increasingly strict environmental regulations and reduce the overall carbon footprint of their operations.
The future of hydraulic metal forming machines will also see further integration with Industry 4.0 technologies, particularly in the areas of automation and machine connectivity. As part of smart factories, these machines will be equipped with sensors and communication systems that allow them to exchange data with other machines, robots, and the central control system. This interconnected ecosystem will allow for real-time production monitoring, where operators can track each stage of the forming process remotely. By automating routine tasks and gathering data for analysis, manufacturers can optimize machine performance, reduce waste, and improve quality control across production lines.
In addition to automation, robotic integration will play a significant role in future hydraulic metal forming operations. Robots can be used to handle materials, load and unload parts, and even assist with post-forming processes such as inspection or assembly. The use of collaborative robots (cobots), which work alongside human operators, will enhance the flexibility and efficiency of hydraulic forming machines. These robots can be integrated with the forming machines to streamline workflows, allowing for faster changeovers and reducing human error during the production process.
As customization becomes more prevalent in industries like automotive and aerospace, hydraulic custom metal forming machines will evolve to offer greater flexibility in part design and production. Manufacturers will seek machines that can easily adapt to changing specifications, allowing for rapid prototyping and the ability to produce small batches of highly specialized parts. This is where modular design will come into play. Machines will be designed to accept a variety of modular tooling and dies, allowing operators to quickly change configurations to accommodate different part designs without the need for extensive downtime.
The growing demand for lightweight materials such as aluminum and composite metals will drive the development of hydraulic custom metal forming machines that can handle these materials without compromising on quality. For example, these materials may require different forming techniques or tooling that can handle high strength-to-weight ratios. Machines will be designed with advanced temperature control systems to ensure that the materials are properly heated or cooled during the forming process, preserving their properties and preventing deformation or damage.
Finally, digital twin technology will begin to be more widely used in hydraulic custom metal forming machines. A digital twin is a virtual model of the physical machine, which can simulate real-world behavior and processes. This allows for improved process optimization, remote diagnostics, and performance prediction. Operators and engineers can use the digital twin to test different configurations, identify potential issues before they occur, and optimize the forming process for better efficiency and product quality. By simulating various scenarios, manufacturers can make informed decisions and avoid costly mistakes on the production floor.
In conclusion, hydraulic custom metal forming machines are poised to become more intelligent, efficient, and sustainable in the near future. Through the integration of advanced technologies like servo-hydraulic systems, machine learning, robotics, and predictive maintenance, these machines will become central to the manufacturing industry’s push for higher precision, lower energy consumption, and greater flexibility. As industries demand more specialized parts with shorter lead times and at lower costs, hydraulic forming machines will continue to evolve, enabling manufacturers to meet the challenges of a rapidly changing marketplace.
As hydraulic custom metal forming machines continue to evolve, there will also be an increasing focus on user-friendliness and ease of integration with existing production systems. The user interfaces of these machines are becoming more intuitive, with touchscreen controls and advanced diagnostics that provide operators with real-time feedback on machine performance. This not only improves ease of operation but also allows for quicker troubleshooting and resolution of issues, reducing downtime and enhancing the overall efficiency of the manufacturing process. The incorporation of augmented reality (AR) could also be a game-changer, allowing operators to visualize machine performance, inspect parts, and access maintenance guides directly through AR glasses or mobile devices.
The need for rapid prototyping and small batch production will lead to further development of hydraulic forming machines capable of producing highly customized and complex parts in shorter timeframes. These machines will likely include features like quick-change tooling and advanced programmable logic controllers (PLCs) that make it easier to reconfigure the machine for different tasks without extensive downtime. The demand for flexibility in manufacturing processes, driven by trends such as on-demand production and mass customization, will continue to push these machines toward greater adaptability, allowing manufacturers to meet the needs of diverse industries, from automotive to consumer electronics.
Moreover, precision engineering will become even more critical as manufacturing tolerances shrink across industries. Hydraulic custom metal forming machines will be equipped with high-precision control systems that can adjust minute variations in force and stroke length, ensuring that the final product meets the exact specifications required. Coupled with laser measurement systems and 3D scanning for real-time inspection, these advancements will enable manufacturers to maintain strict quality control while producing increasingly complex parts.
The shift towards additive manufacturing and hybrid manufacturing processes will also influence the design of hydraulic custom metal forming machines. Hybrid machines, which combine traditional subtractive forming methods (like hydraulic forming) with additive techniques (such as 3D printing), will allow manufacturers to create intricate parts with a mix of additive and subtractive processes in a single operation. For example, a part could be formed hydraulically to achieve its general shape, and then 3D printing could be used to add finer details or specialized features. This hybrid approach will enable manufacturers to offer highly customized parts with minimal material waste and quicker production cycles.
In terms of material science, the development of new, stronger, and lighter materials will require hydraulic custom metal forming machines to handle a wider range of materials with varying properties. For example, the increasing use of high-strength steels, titanium alloys, and composite materials in industries like aerospace, defense, and automotive will necessitate the creation of specialized dies and tooling that can handle these advanced materials without damaging them. This will involve not only better temperature control and force management but also innovations in the design of the hydraulic system itself, such as dual-stage cylinders or specialized multi-point forming to distribute pressure more evenly across the material.
Sustainability will continue to be a primary driver for innovation in hydraulic custom metal forming machines. As manufacturers face increasing pressure from governments, consumers, and stakeholders to reduce their environmental impact, we will see more hydraulic forming machines that incorporate energy-saving technologies, such as regenerative hydraulic systems that capture and reuse energy during forming cycles. Additionally, closed-loop systems will be developed to recapture and filter hydraulic fluids, ensuring their long-term reuse and minimizing waste. These eco-friendly innovations not only reduce the carbon footprint of the manufacturing process but also help companies comply with regulations surrounding environmental sustainability.
Furthermore, the use of advanced coatings and surface treatments will be an essential consideration for hydraulic custom metal forming machines in the future. As part geometries become more complex and materials become more specialized, these treatments will play a key role in ensuring parts maintain their functionality, durability, and aesthetic qualities. Hydraulic forming machines will need to incorporate technologies that ensure parts are consistently treated with the appropriate coatings or finishes, whether for corrosion resistance, thermal protection, or wear resistance.
Global connectivity and the rise of global supply chains will also influence the design of hydraulic custom metal forming machines. As manufacturers strive to improve communication between different production facilities, machines will become more integrated with cloud-based platforms, enabling centralized control, monitoring, and data analysis across multiple locations. This integration will facilitate smoother coordination across supply chains, allowing for real-time tracking of materials, automated inventory management, and advanced planning systems that can adjust production schedules based on real-time demand or supply chain disruptions.
In terms of maintenance and servicing, hydraulic custom metal forming machines will evolve to include remote diagnostics and predictive maintenance capabilities. By leveraging Internet of Things (IoT) technology, these machines will be able to send performance data to remote service centers, where technicians can monitor the machine’s health and recommend maintenance or adjustments based on real-time data. This will not only reduce the need for on-site inspections but also improve the accuracy of repairs, ultimately extending the lifespan of the equipment and reducing the overall cost of maintenance.
The ongoing trend of miniaturization and micro-manufacturing will lead to the development of smaller, more compact hydraulic custom metal forming machines. These smaller machines will still be able to handle high precision tasks, enabling manufacturers to produce micro-sized parts or intricate features required in industries such as medical devices, electronics, and micro-mechanics. This trend will likely result in a new generation of compact hydraulic systems designed for micro-scale manufacturing processes.
Lastly, the growing emphasis on data-driven decision-making will drive the continued integration of artificial intelligence (AI) and machine learning algorithms into hydraulic custom metal forming machines. AI-powered systems will not only automate the control of hydraulic pressure and machine motion but also analyze production data to detect patterns, optimize process parameters, and predict the optimal settings for future jobs. By continuously learning from previous production runs, these AI systems will be able to improve the accuracy and quality of the forming process, making it even more efficient.
In summary, the future of hydraulic custom metal forming machines will be defined by a combination of greater precision, automation, and sustainability. As industries demand more complex, customized, and high-performance parts, these machines will continue to evolve with advanced technologies that enable manufacturers to meet the challenges of modern production. With the integration of AI, predictive maintenance, hybrid manufacturing techniques, and sustainable practices, hydraulic custom metal forming machines will play an essential role in shaping the future of global manufacturing.
As hydraulic custom metal forming machines continue to advance, the focus will also be on improving user experience and simplifying operation and maintenance. This includes streamlining the setup and calibration process for operators. In the past, hydraulic machines often required lengthy and complex setups, especially when switching between different types of metal or part designs. However, future machines are likely to incorporate automatic calibration systems that adjust machine parameters in real-time based on the type of metal, thickness, and desired part specifications. This will reduce operator training time and minimize errors during machine setup.
Moreover, machine safety will be a central area of improvement. Modern hydraulic metal forming machines are already equipped with various safety features such as safety shields, emergency stop buttons, and pressure relief valves. However, future innovations may include more advanced sensor-based safety systems that detect hazardous conditions in real-time, such as over-pressure scenarios, abnormal vibrations, or tooling misalignments. These sensors will automatically trigger safety protocols, potentially stopping the machine or alerting operators to mitigate risks before they escalate.
The integration of virtual reality (VR) and augmented reality (AR) technologies for training and maintenance will become more common in hydraulic forming machines. These technologies can provide immersive environments where operators can simulate various scenarios, learn how to interact with the machine safely, and troubleshoot problems without interrupting actual production. For example, AR glasses can display real-time data and machine diagnostics, guiding operators through repairs or adjustments. VR can also be used for testing new machine setups or configurations in a virtual environment before applying them in the real world, reducing trial-and-error in the production process.
Another significant development will be the integration of adaptive forming technology. This allows hydraulic forming machines to adjust the forming parameters in real-time, based on the material’s behavior during the process. For instance, sensors embedded in the die or hydraulic system could continuously measure the material’s stress, strain, or temperature and adjust the pressure or stroke length accordingly to ensure optimal results. This would result in fewer defects, greater part quality, and reduced material waste, as the machine can automatically compensate for variations in the material properties.
As industries become more specialized and require high-precision, high-volume production, hydraulic custom metal forming machines will continue to evolve to meet the demands of emerging sectors. For example, the electronics industry increasingly requires small, intricate metal parts with very tight tolerances. These parts need to be formed with utmost precision, and hydraulic forming machines will need to incorporate ultra-fine control of force, speed, and stroke to produce such components. Additionally, parts for industries like medical devices and nanotechnology may require forming techniques that take into account the effects of microstructures and surface finishes, pushing the capabilities of hydraulic machines even further.
The globalization of manufacturing will also demand that hydraulic custom metal forming machines become more internationally standardized. As manufacturers expand their operations to different regions and supply chains become more complex, there will be an increasing need for machines that can operate across different standards, including electrical specifications, control systems, and maintenance protocols. This could lead to the development of more universal machine platforms that can be easily adapted to local requirements, regardless of where the machines are deployed.
There will also be a focus on improving machine longevity and cost-effectiveness. Hydraulic systems are inherently subject to wear and tear due to the constant pressure and fluid dynamics involved. Innovations in materials science and lubrication technologies could lead to longer-lasting components that require less frequent maintenance and fewer fluid replacements. Additionally, improvements in hydraulic fluid formulations could enhance performance while reducing environmental impact. Machines could be designed to reduce energy consumption during idle times or optimize energy use based on load, further reducing operational costs.
Another evolving trend is the increase in automation and integration with other automated systems. As factories evolve toward Industry 4.0, the integration of hydraulic forming machines with automated guided vehicles (AGVs), robotic arms, and automated material handling systems will become more common. These machines will be able to function in a fully automated environment, where parts are fed into the machine, formed, and then moved to the next stage of production without human intervention. This trend towards fully autonomous production lines will minimize labor costs, reduce human error, and speed up production cycles, ultimately leading to more efficient operations.
In terms of collaboration and customization, future hydraulic forming machines will likely offer cloud-based platforms for customers to design and program parts remotely. Customers could upload part drawings, choose the appropriate forming parameters, and have the machine automatically adjust to produce the required parts. This service-oriented model will provide a more flexible manufacturing environment, where customers have control over their production runs and can adjust their designs quickly without the need for extensive retooling.
In the field of advanced materials, the hydraulic forming machines will have to deal with an increasing range of composite materials, multi-materials, and lightweight alloys. These materials often require specific conditions during forming, such as controlled temperature or pressure, and hydraulic machines will be equipped with more sophisticated material-specific programming to ensure that the appropriate forming techniques are used. As the demand for lightweight vehicles, high-performance electronics, and sustainable products grows, hydraulic custom metal forming machines will need to adapt to accommodate these innovative materials.
Finally, data analytics will become an essential tool in optimizing machine performance. By collecting and analyzing data on every forming cycle, manufacturers will be able to identify inefficiencies, predict when parts are likely to fail, and optimize machine settings for different materials and parts. This data-driven approach will not only enhance productivity but also lead to better overall quality control, with real-time insights enabling operators to spot trends and make proactive adjustments.
To sum up, the future of hydraulic custom metal forming machines will be shaped by a combination of technological advancements that focus on automation, precision, sustainability, and adaptability. As industries demand increasingly complex, customized, and high-performance parts, these machines will become more intelligent, energy-efficient, and flexible, meeting the needs of diverse sectors. With continuous improvements in control systems, automation, and material processing, hydraulic custom metal forming machines will play an integral role in the future of advanced manufacturing, helping companies stay competitive in an ever-evolving global market.
Rotary Custom Metal Forming Machine
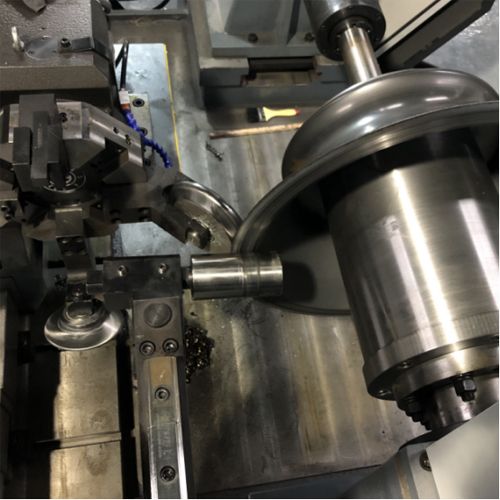
A rotary custom metal forming machine is a type of advanced manufacturing equipment that utilizes rotational motion to shape, form, or process metal materials. This machine is designed to produce precise, high-quality parts and components for various industries, including automotive, aerospace, medical devices, and heavy machinery. Unlike traditional metal forming machines, which may use linear or static forces, rotary custom metal forming machines leverage the rotational force to achieve specific geometries and material properties.
Key Features and Functions of Rotary Custom Metal Forming Machines
- Rotational Motion:
The core principle of a rotary metal forming machine is the use of rotational motion to deform or shape metal. This can involve rotating dies, rollers, or workpieces, and is ideal for processes like spinning, forging, coining, and shearing. The rotary action provides consistent and uniform pressure, allowing for high precision and repeatability. - Precision Control:
Rotary custom metal forming machines are equipped with advanced control systems that allow for precise adjustments of rotational speed, torque, and force. These adjustments are critical for ensuring that the metal is shaped with tight tolerances and without defects. The use of servo motors or AC motors allows for fine control, which is essential for high-precision applications such as creating thin-walled parts or intricate designs. - Customization:
As the name suggests, these machines are often highly customizable to meet the specific requirements of various industries and applications. The design of the dies, rollers, and tooling can be tailored to suit the exact geometry and material properties needed for different parts. Modular tooling systems enable manufacturers to quickly change tooling configurations, making these machines versatile and adaptable to a wide range of tasks. - High-Speed Production:
Rotary custom metal forming machines can operate at high speeds, allowing manufacturers to increase production throughput without sacrificing quality. This is particularly beneficial in industries where large volumes of parts need to be produced quickly, such as in the automotive sector for producing wheel rims or structural components. - Material Versatility:
These machines are capable of processing a variety of metals, including steel, aluminum, copper, titanium, and specialized alloys. They can also be used for forming materials that require high temperatures or specific handling during the forming process, such as superalloys or composite metals.
Common Applications of Rotary Custom Metal Forming Machines
- Rotary Spinning:
One of the most common applications for rotary custom metal forming machines is rotary spinning, where a flat sheet of metal is fed onto a rotating mandrel or die. The metal is then shaped by rollers or pressing tools that apply pressure along the rotating surface. This process is commonly used to form cylindrical parts, such as tubes, buckets, or housings in industries like aerospace and automotive. - Rotary Forging:
Rotary forging machines use rotating dies to deform metal billets into precise shapes, often with high strength properties. This process is used for producing gears, shafts, and other parts that require high load-bearing capacity. Rotary forging is highly efficient, reduces material waste, and can provide superior mechanical properties in the finished part. - Ring Rolling:
A rotary custom metal forming machine can also be used for ring rolling, where a metal ring is formed by applying rotational forces. This is commonly used to produce bearing rings, flanges, and turbine discs in industries like power generation and aerospace. The process allows for the creation of high-strength, lightweight rings that are essential for these applications. - Tube and Pipe Forming:
In rotary metal forming, tubes and pipes can be formed through a process that involves rotating a metal sheet or strip while feeding it into a set of rollers. The rollers gradually shape the metal into a tube, which can then be welded or finished as required. This technique is used for creating various tubing products, from industrial pipelines to medical devices. - Coining and Embossing:
Rotary machines can be used for coining or embossing, which involves pressing designs or logos into a metal surface. The rotary action allows for even pressure distribution and consistent results across large batches of parts. This is commonly seen in the production of coins, medals, and decorative components.
Advantages of Rotary Custom Metal Forming Machines
- High Efficiency:
The rotational motion helps distribute force evenly across the workpiece, which reduces material strain and increases the overall efficiency of the forming process. Machines can operate continuously, enabling faster production times and reduced cycle times. - Improved Material Properties:
Rotary forming processes, such as rotary forging, tend to improve the grain structure and mechanical properties of the material. The controlled deformation process can lead to stronger, more durable parts with better fatigue resistance. - Lower Material Waste:
Because of the precision involved in rotary forming, these machines often generate less scrap compared to other forming techniques. The metal is deformed in a way that minimizes the amount of material that is discarded, contributing to more sustainable production practices. - Enhanced Precision and Tolerances:
The ability to control rotational speed, pressure, and force in real-time allows manufacturers to achieve higher precision and tighter tolerances. This is particularly important for parts used in critical applications where high accuracy is essential, such as in medical devices or aerospace components. - Cost-Effectiveness for High-Volume Production:
While the initial investment in a rotary custom metal forming machine may be high, the long-term cost benefits are significant, especially in industries that require high-volume production. The ability to quickly switch tooling, automate the forming process, and reduce cycle times results in a lower cost per part produced.
Future Trends in Rotary Custom Metal Forming Machines
- Automation and Robotics:
The future of rotary custom metal forming machines will see greater integration with automation systems and robotic arms. Automated material handling, part inspection, and tool changes will help reduce human labor, increase production speed, and improve consistency across production runs. - Digitalization and Industry 4.0 Integration:
As with other manufacturing technologies, rotary metal forming machines will become more connected through Industry 4.0 technologies. This will include the integration of sensors, IoT devices, and real-time data analytics to monitor machine performance, optimize processes, and predict maintenance needs before failures occur. These smart systems will enable manufacturers to track and optimize their production in ways that were previously impossible. - Advanced Material Processing:
With the growing demand for lightweight, high-strength materials in industries like aerospace and automotive, rotary custom metal forming machines will be further developed to process advanced materials, such as composite alloys and high-temperature materials. These machines will also need to adapt to new multi-material forming processes, where different materials are combined in a single forming operation. - Hybrid Manufacturing:
As hybrid manufacturing methods gain popularity, rotary custom metal forming machines will likely incorporate elements of additive manufacturing or 3D printing to offer more flexibility in part design and production. This could include combining traditional rotational forming with layered metal deposition to create complex geometries or add features like cooling channels to parts in a single operation. - Sustainability:
In response to environmental concerns, future rotary forming machines will incorporate more sustainable practices, such as using biodegradable lubricants, energy recovery systems, and recyclable tooling. They will also focus on reducing the energy consumption of the forming process, ensuring that operations are more eco-friendly and compliant with environmental regulations.
In conclusion, rotary custom metal forming machines are essential tools in modern manufacturing that offer precision, efficiency, and versatility. They play a critical role in producing complex, high-quality parts for a wide range of industries. As technology continues to evolve, these machines will become even more advanced, integrating automation, data analytics, and sustainable practices to meet the growing demands of manufacturers around the world.
Rotary custom metal forming machines are likely to continue evolving as industries demand more intricate designs and high-performance materials. As the need for more advanced material processing increases, these machines will evolve to handle lightweight metals, alloys, and composite materials that are essential for industries like aerospace, defense, and automotive manufacturing. This will require improvements in the control systems, tool design, and material handling to ensure that the metal is processed without compromising strength, flexibility, or precision.
Additionally, the rise of smart manufacturing will likely drive the integration of machine learning and artificial intelligence in these systems. The machines will be able to monitor their own performance, identify inefficiencies, and make real-time adjustments to optimize the production process. For instance, AI could predict when certain parts of the machine are likely to wear out, triggering maintenance before a breakdown occurs, which will improve uptime and reduce the risk of expensive repairs. These advancements will be especially useful in industries with high-volume production, where any downtime can result in significant losses.
With the continued growth of Industry 4.0, rotary custom metal forming machines will become even more connected. These machines will communicate with other equipment and factory systems to share real-time data, such as operational conditions, inventory levels, and production progress. This integration will enable manufacturers to synchronize their operations more efficiently, improving overall workflow and reducing lead times. In addition, operators will be able to remotely monitor and control the machines through cloud-based platforms, making it easier to manage multiple production lines and facilities from anywhere in the world.
Sustainability will also be a driving factor in the development of rotary forming machines. Manufacturers will continue to seek ways to reduce their environmental footprint by designing machines that consume less energy, use renewable resources, and minimize waste. For example, machines may incorporate regenerative hydraulic systems that recycle energy during the forming process, reducing overall power consumption. Additionally, advances in materials technology could allow for the development of eco-friendly lubricants and biodegradable fluids, which will lower the environmental impact of the forming process.
Another key trend is the increasing emphasis on customization and small-batch production. As consumer demand for personalized and unique products grows, rotary custom metal forming machines will evolve to allow for faster switching between different part designs, reducing the downtime typically required for tool changes. With the integration of digital design platforms and real-time simulations, manufacturers will be able to design and produce one-of-a-kind parts quickly and efficiently. This trend will also drive the development of additive manufacturing techniques, such as 3D metal printing, which could be combined with rotary forming to create even more complex and tailored parts.
The focus on precision and quality control will continue to be a central consideration as rotary forming machines become more advanced. The ability to monitor material properties in real time, including stress, strain, and temperature, will allow manufacturers to ensure that every part meets the desired specifications. For example, sensors embedded in the tooling or die can detect changes in the material during the forming process, adjusting machine parameters automatically to maintain consistency and reduce defects. This will be particularly valuable in industries like medical devices and aerospace, where parts must meet strict regulatory standards.
As more industries shift towards automated and autonomous production lines, rotary custom metal forming machines will become key components in fully integrated manufacturing environments. This could include working in tandem with robotic systems that perform tasks like material handling, quality inspection, and packaging. These machines will need to be easily integrated into factory automation systems, with smart interfaces that allow seamless communication with other devices and systems in the factory.
Ultimately, rotary custom metal forming machines will continue to be at the forefront of modern manufacturing, offering significant benefits in terms of precision, efficiency, and customization. As industries demand more complex designs and higher performance from their parts, these machines will evolve to meet those needs, incorporating the latest advancements in automation, material processing, and data analytics.
As the demand for global collaboration increases, rotary custom metal forming machines will need to be adaptable to a variety of manufacturing environments and regulatory requirements across different regions. This might include the ability to work with different electrical standards, safety protocols, and localized language settings for control systems. The machines will likely feature universal interfaces and easy-to-implement configurations that make it easier to set up and maintain across multiple locations. Furthermore, cross-border manufacturing will drive the need for machines that can produce parts that meet a range of international certifications for industries like aerospace, medical, and automotive.
With the increasing complexity of parts being produced, rotary custom metal forming machines will need to focus even more on part traceability. The ability to track every component through every step of the manufacturing process will become essential. This includes knowing the precise material batch, machine settings, and production timeline for every part, which is crucial for industries where high reliability and safety are non-negotiable. Integrated barcode scanning or RFID technology will allow parts to be traced and monitored throughout the production process, enhancing accountability and ensuring quality control.
Additionally, rotary custom metal forming machines may become more flexible when it comes to multi-step operations. For instance, a single machine could integrate multiple forming processes like forging, spinning, and coining in one seamless operation. This could reduce the need for multiple machines and manual handling, streamlining workflows and lowering operational costs. As such, manufacturers may seek machines that are capable of completing complex, multi-step processes with minimal manual intervention and maximum efficiency.
With the continuing rise of additive manufacturing (AM) and hybrid manufacturing technologies, there may also be a shift towards combining rotary forming with 3D printing in certain applications. For example, rotary forming could be used to shape the primary structure of a part, while 3D printing might be employed to add intricate features or support structures in areas that would be difficult to achieve with traditional forming methods. Such hybrid machines could offer greater design freedom and reduce the need for multiple separate machines, thus further streamlining production workflows and reducing costs.
The digital twin technology could also play a significant role in the future of rotary custom metal forming machines. A digital twin refers to a virtual representation of the machine, which continuously updates based on real-time data from the physical system. Manufacturers can use digital twins to simulate how changes in parameters or materials might impact the end product, enabling them to optimize the production process before making actual changes on the machine. This real-time simulation will enhance predictive maintenance capabilities and reduce unexpected downtimes, as well as provide valuable insights into the overall efficiency of the manufacturing process.
Looking forward, rotary custom metal forming machines will continue to be central to industries requiring high-quality, high-precision metal parts. As new manufacturing trends emerge, these machines will evolve to incorporate cutting-edge technologies like artificial intelligence (AI), machine learning (ML), and advanced robotics, which will help them meet the demands of an increasingly competitive and globalized market. As a result, manufacturers will be able to produce more complex, customized parts with less material waste, lower costs, and shorter lead times. Additionally, advances in sustainability and eco-friendly practices will shape the future of these machines, driving the use of renewable materials, energy-efficient designs, and greener manufacturing techniques.
In sum, the future of rotary custom metal forming machines lies in continued innovation, particularly around the integration of smart technologies, the use of sustainable practices, and the increasing need for customization. By adapting to these changing needs, these machines will not only provide manufacturers with greater capabilities but will also pave the way for more efficient, high-quality, and environmentally responsible metal-forming processes. As technology continues to evolve, so too will the potential of rotary custom metal forming machines to meet the demands of industries and contribute to the future of manufacturing.
Custom Deep Drawing Metal Forming Machine
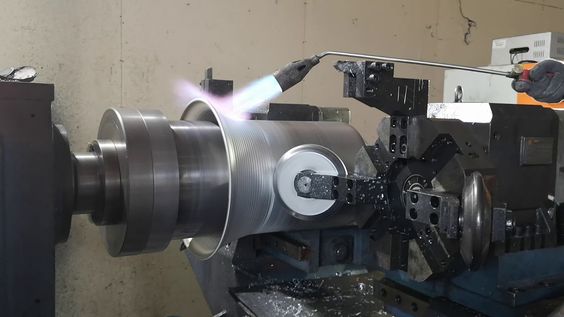
A custom deep drawing metal forming machine is a specialized piece of equipment used for shaping sheet metal into complex, hollow parts through a process called deep drawing. This process involves pulling a flat sheet of metal into a die cavity to form a part with significant depth and a reduced diameter, such as automotive body panels, cans, and kitchenware. Deep drawing is widely used in industries that require high-strength, lightweight components with a smooth surface finish and tight tolerances. The ability to customize these machines allows manufacturers to meet specific production requirements, including part complexity, material type, and desired output volumes.
Key Features of Custom Deep Drawing Metal Forming Machines
- Customizable Tooling:
One of the most important features of custom deep drawing machines is their ability to be tailored to specific part requirements. The dies, punches, and blank holders can be custom-designed to match the desired shape, material properties, and production volumes. Custom tooling is critical in industries that require specialized or highly complex parts, such as aerospace or medical device manufacturing. - Precision Control Systems:
Deep drawing involves the application of significant force to draw the metal sheet into a die, which can lead to high stress and potential defects like wrinkling, tearing, or thinning of the material. Custom machines are equipped with advanced control systems that allow precise adjustment of parameters like drawing speed, die pressure, and blank holder force. These controls are essential to ensure high-quality parts are produced consistently and efficiently. - Hydraulic Press Mechanism:
Most custom deep drawing machines use a hydraulic press to apply the necessary force to the metal sheet. These presses are capable of exerting very high pressures, which is necessary for forming deep parts. The hydraulic system can be adjusted for different pressures depending on the material type and thickness, allowing for greater flexibility in part design and production speed. - Variable Stroke and Speed:
Deep drawing involves multiple stages, and the stroke length and speed need to be adjusted depending on the size and complexity of the part being formed. Custom deep drawing machines often feature variable stroke lengths and adjustable speeds, which allow for precise control of the forming process. This flexibility is essential for achieving high-quality results and minimizing the risk of defects during production. - Die and Punch Design:
The design of the die and punch plays a critical role in the deep drawing process. Custom deep drawing machines often feature dies and punches that are designed for specific materials, geometries, and product designs. Custom tooling ensures that the metal sheet is drawn evenly and without defects, allowing for the creation of complex shapes such as automotive body panels, cans, or housing components. The tooling can be swapped out or adjusted to accommodate different product lines, enhancing the machine’s versatility. - Material Handling System:
Efficient handling of the metal sheets is key to the success of the deep drawing process. Custom machines are equipped with advanced material handling systems, which can include automated feeding systems, coil unwinders, sheet feeders, and conveyor belts. These systems reduce manual labor, improve cycle times, and ensure that the material is consistently placed into the die for optimal results. - Monitoring and Feedback Systems:
Many modern custom deep drawing machines are equipped with real-time monitoring systems that track various parameters, such as material thickness, die pressure, and forming speed. This data is continuously fed back into the machine’s control system, allowing for real-time adjustments to ensure consistent part quality. The use of sensors and vision systems can also help detect defects such as wrinkles, tearing, or misalignment, allowing operators to make immediate adjustments to prevent part failure. - Energy Efficiency:
With energy consumption being a significant operational cost, custom deep drawing machines are increasingly designed with energy efficiency in mind. Features such as regenerative braking on the hydraulic system, energy-efficient motors, and optimized press cycles help to reduce energy usage during production. These machines may also feature standby modes during non-productive cycles, helping to minimize electricity consumption. - Automation and Integration:
Many custom deep drawing machines are fully automated, with integrated systems for tool changing, part handling, and inspection. Automation can help reduce human error, increase throughput, and improve safety. Additionally, some machines are designed for Industry 4.0 integration, where sensors, IoT technology, and cloud-based monitoring allow operators to monitor machine performance remotely and analyze data for predictive maintenance and process optimization.
Applications of Custom Deep Drawing Metal Forming Machines
- Automotive Industry:
Deep drawing is heavily used in the automotive industry for forming components such as body panels, wheel rims, and fuel tanks. Custom machines are tailored to the precise needs of automotive manufacturers, allowing for the production of lightweight yet durable parts with complex shapes. As lightweight materials like aluminum and magnesium alloys become more common in automotive production, custom deep drawing machines are adapting to handle these new materials. - Packaging Industry:
The packaging industry also benefits from custom deep drawing machines, especially in the production of metal cans, bottles, and containers. Deep drawing allows manufacturers to create precise, uniform shapes with minimal waste, making it an ideal process for mass production in packaging. Machines can be customized for different types of metal, such as aluminum or tinplate, depending on the packaging material. - Consumer Goods:
Products such as kitchenware, appliance housings, and industrial containers often require deep drawing for their metal components. Custom deep drawing machines can be designed to form parts with high precision, reducing the risk of defects while maintaining consistency in design. - Aerospace and Defense:
The aerospace industry uses deep drawing for high-performance parts such as aircraft components, engine casings, and fuel tanks. These parts need to meet strict weight, strength, and durability specifications, and custom deep drawing machines allow for precise control over the forming process to meet these stringent requirements. - Medical Devices:
Medical device manufacturers often rely on deep drawing to produce metal housings, cans, and containers for devices such as surgical instruments and implants. Custom machines can be designed to form small, intricate parts with high precision, ensuring that each part meets the necessary medical standards for safety and quality.
Advantages of Custom Deep Drawing Metal Forming Machines
- High Precision:
The custom nature of these machines allows for precise control over the forming process, ensuring that parts are produced with tight tolerances. This is particularly important for industries like aerospace, automotive, and medical devices, where even small deviations can result in defects or performance issues. - Versatility:
Custom deep drawing machines can be designed to handle a wide range of materials, including stainless steel, aluminum, brass, and copper, as well as coated metals or special alloys. The ability to change tooling and adjust machine settings makes them highly versatile for different applications and production runs. - Material Efficiency:
Deep drawing is a highly material-efficient process because it minimizes scrap and waste. The precision and ability to form parts directly from sheet metal also reduce the need for additional machining or post-processing, which saves both material and time. - High-Volume Production:
Once the tooling is set up, custom deep drawing machines are capable of running high-volume production cycles with minimal downtime. This makes them ideal for industries that require mass production, such as automotive or packaging. - Enhanced Surface Finish:
The deep drawing process produces parts with a smooth, consistent surface finish, which is especially important for aesthetic parts or those that require coatings. The process also reduces the need for post-processing, which can be time-consuming and costly.
Future Trends in Custom Deep Drawing Metal Forming Machines
The future of custom deep drawing metal forming machines will likely involve increased automation, digitalization, and sustainability. As manufacturers seek to further optimize production, these machines will incorporate AI-driven systems for predictive maintenance, real-time monitoring of forming parameters, and advanced sensors for defect detection. Additionally, energy-efficient technologies and eco-friendly materials will continue to shape the development of deep drawing machines, reducing the environmental impact of the manufacturing process.
The demand for customized, high-precision parts will drive the need for increasingly flexible machines that can handle small-batch production and complex geometries. This flexibility will be facilitated by modular tooling systems, adjustable press parameters, and integrated automation systems that allow manufacturers to quickly adapt to changing production requirements.
In summary, custom deep drawing metal forming machines are crucial for producing high-quality, precise parts in industries that demand reliability, durability, and consistency. With advances in automation, precision control, and energy efficiency, these machines will continue to play an integral role in shaping the future of metal manufacturing.
Custom deep drawing metal forming machines are essential for creating parts that require both high precision and structural integrity. These machines allow for the shaping of a wide variety of materials, such as stainless steel, aluminum, and copper, into complex, deep, and hollow shapes with minimal material waste. The deep drawing process itself is particularly valuable because it produces components with a smooth surface finish and high strength-to-weight ratio, making it ideal for industries like automotive, aerospace, packaging, and consumer goods. Manufacturers increasingly turn to custom machines to meet specific production requirements, allowing for greater versatility and efficiency.
These machines are continuously evolving to integrate the latest technological advancements. Automation plays a significant role, as it reduces human error and enhances throughput. Through the use of advanced sensors, robotics, and real-time monitoring systems, custom deep drawing machines ensure consistent quality and optimal operation. These sensors can detect potential issues such as wrinkling, tearing, or misalignment, allowing for immediate corrective actions to be taken. The result is not only a reduction in defects but also an improvement in overall production speed and efficiency. With the rise of smart manufacturing, these machines will increasingly be connected to central systems that provide data analytics and insights, enabling manufacturers to make informed decisions that optimize the production process.
The focus on sustainability will also shape the future of custom deep drawing machines. As industries strive to reduce their carbon footprint, deep drawing machines are being designed to consume less energy and produce less waste. Innovations such as regenerative hydraulic systems that recover energy during the forming process, and energy-efficient motors that minimize power consumption, will become more common. Additionally, the use of eco-friendly lubricants and biodegradable fluids will help reduce the environmental impact of the forming process.
Customization is another key factor driving the demand for advanced deep drawing machines. Manufacturers increasingly require equipment that can be adapted to produce a wide range of parts with varying complexities. As consumers demand more personalized and unique products, the ability to quickly and efficiently switch between different designs and production runs is becoming a significant advantage. Custom deep drawing machines allow for this flexibility through adjustable tooling, press force, and stroke length parameters. This versatility enables manufacturers to cater to both high-volume production and small-batch runs, meeting the needs of industries that require fast turnaround times and high levels of customization.
Furthermore, the integration of additive manufacturing (3D printing) with deep drawing techniques is beginning to emerge as a promising trend. Hybrid manufacturing systems that combine the strengths of both processes can create parts with intricate geometries that would be difficult or impossible to achieve with traditional methods. This innovation opens up new possibilities for creating more complex, customized, and high-performance parts, particularly in industries like aerospace and medical devices, where the ability to design and produce one-of-a-kind components is crucial.
The demand for precision and quality control continues to grow, especially as parts become smaller and more intricate. Modern custom deep drawing machines are equipped with feedback loops that continuously adjust forming parameters in response to real-time data. This ensures that parts are consistently manufactured to exact specifications, reducing the need for post-processing and enhancing the overall efficiency of the production process.
In summary, custom deep drawing metal forming machines are at the forefront of modern manufacturing, enabling the production of high-quality, precise components for a wide range of industries. As technology continues to evolve, these machines will become even more capable, offering greater flexibility, efficiency, and sustainability. With advances in automation, data integration, and material science, custom deep drawing machines will continue to play a critical role in shaping the future of manufacturing.
As custom deep drawing metal forming machines continue to evolve, the trend toward digitization and data integration will become increasingly pronounced. More machines will incorporate Internet of Things (IoT) technology, enabling them to communicate with other equipment, sensors, and central control systems in real-time. This connectivity allows for a fully integrated smart factory where machines are able to share data about their performance, energy consumption, and production metrics, providing manufacturers with a clearer understanding of their operations. These connected systems also facilitate the use of predictive analytics, where machine performance data is analyzed to predict maintenance needs, reducing unplanned downtime and extending the lifespan of the machines.
Another area where digitization is making a significant impact is in the design and simulation phase. Traditionally, designing custom tooling and optimizing the forming process required extensive trial and error. However, with the advancement of computer-aided design (CAD) and computer-aided engineering (CAE) tools, manufacturers can now simulate the deep drawing process in a virtual environment. This enables them to predict how the material will behave under various forming conditions and identify potential issues before production begins. Virtual testing and optimization reduce material waste and costly tooling adjustments while accelerating the overall design process.
The integration of artificial intelligence (AI) is also expected to revolutionize custom deep drawing machines. AI can be used to improve process control by automatically adjusting machine parameters, such as pressure, stroke length, and forming speed, based on real-time data from sensors. Over time, the machine learns from past performance, making it more adept at identifying patterns and improving the consistency and quality of the parts being produced. This AI-driven approach not only enhances part quality but also increases the efficiency of production, allowing manufacturers to optimize their processes without the need for constant manual oversight.
The push for lean manufacturing practices is further driving the need for custom deep drawing machines that can operate more efficiently with less waste. These machines will increasingly feature advanced material handling systems, such as automated feeding and robotic part extraction, to reduce cycle time and minimize human labor. Automated quality inspection systems, using machine vision or laser scanning, will also become more common, providing real-time feedback on part quality without the need for manual inspections.
The push for greater sustainability will continue to influence the development of custom deep drawing machines. Manufacturers are under pressure to reduce their environmental impact, and deep drawing is an efficient process in terms of material use and energy consumption. However, there are still opportunities for improvement, particularly in energy recovery and material efficiency. Future machines may feature closed-loop systems that recover energy used during forming and recycle it back into the system, further reducing overall energy consumption. Additionally, as recycled metals and alternative materials become more prevalent, custom deep drawing machines will be designed to work with a wider variety of materials, including lightweight alloys, composites, and sustainable metals, to meet the growing demand for eco-friendly manufacturing.
The demand for highly specialized components across a broad range of industries will lead to the creation of more flexible and modular custom deep drawing machines. These machines will be able to handle a wide variety of part geometries and materials, allowing manufacturers to easily adapt to different customer needs and production schedules. Modular tooling systems that can be quickly changed or adjusted to accommodate different part designs will further enhance the machine’s flexibility. This adaptability is particularly important for industries that require low-volume, high-mix production, such as medical devices or aerospace components, where each part might have unique specifications.
In parallel with these advancements, there will be an increasing need for machines that can handle complex multi-stage forming processes. Custom deep drawing machines will likely incorporate additional forming techniques such as stretch forming, roll forming, and hydroforming within a single machine setup, reducing the need for multiple machines and simplifying the overall production process. Hybrid systems that combine multiple forming techniques will allow for the creation of more complex parts in fewer steps, enhancing overall efficiency and reducing the cost per part.
As the market for custom deep drawing machines becomes more competitive, manufacturers will be looking for ways to further differentiate their products. This could include offering machines with enhanced precision control for extremely tight tolerances, the ability to handle a wider range of materials, or machines that can work at higher speeds with lower energy consumption. Additionally, customers will increasingly value after-sales support and maintenance services, making it critical for manufacturers of custom deep drawing machines to offer comprehensive service packages that ensure machines remain in optimal condition over their entire lifespan.
In conclusion, custom deep drawing metal forming machines are on the cusp of a significant transformation driven by advances in automation, digitization, artificial intelligence, and sustainability. These innovations will make the machines more flexible, efficient, and environmentally friendly, while also enabling manufacturers to produce increasingly complex and customized parts with minimal waste and downtime. As industries continue to push the boundaries of design and manufacturing capabilities, custom deep drawing machines will remain at the heart of producing high-precision, high-strength metal components for a wide range of applications.
Custom Tube Forming Machine
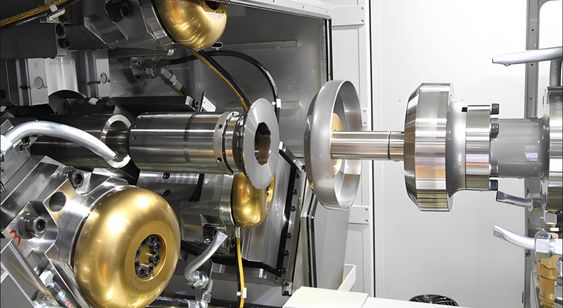
A custom tube forming machine is designed to fabricate tubes or cylindrical parts from various materials such as metals, plastics, or composites. These machines are tailored to specific production needs, including the ability to form complex tube geometries, bend, cut, and manipulate tube shapes while maintaining high precision and consistency. Custom tube forming machines are essential in industries like automotive, aerospace, energy, construction, and medical device manufacturing, where tubes are often used in applications ranging from structural supports to fluid transport systems.
Key Features of Custom Tube Forming Machines
- Adaptable Tube Geometry:
One of the key benefits of custom tube forming machines is their ability to handle a wide range of tube shapes and sizes. Custom machines can be adjusted to form tubes with varying diameters, wall thicknesses, and material types. This flexibility is crucial in industries requiring a broad range of custom-made parts with precise specifications. Machines can accommodate tubes with round, square, or rectangular profiles, or more specialized shapes like oval, elliptical, or triangular. - Advanced Bending and Forming Capabilities:
Tube forming machines typically include bending capabilities, allowing tubes to be shaped without compromising material strength or integrity. Mandrel bending, compression bending, rotary draw bending, and push bending are common techniques that may be incorporated into a custom tube forming machine, depending on the design and material properties. Custom machines can handle complex bends while maintaining tight radius limits, making them ideal for industries like automotive exhaust systems, aircraft tubing, and hydraulic piping. - Cutting and Joining Functions:
Some custom tube forming machines integrate cutting functions, enabling them to produce tubes of specific lengths with minimal waste. Laser cutting, sawing, and shearing are common methods used to cut tubes after they are formed. Additionally, these machines can include systems for welding, crimping, or flanging to join tube sections or create specific tube end shapes. This reduces the need for multiple machines in the production process, increasing efficiency and reducing production time. - Material Handling and Feeding Systems:
Custom tube forming machines often include automated material handling systems to manage tube coils or sheet metal and feed them into the forming system. Automated feeding systems improve accuracy, reduce labor costs, and minimize the risk of material damage during handling. Coil unwinders, tube feeders, and straightening mechanisms ensure that the material is precisely aligned and fed into the machine for consistent results. - Precision Control Systems:
Custom tube forming machines are equipped with advanced control systems that allow for fine adjustments of parameters such as forming speed, bending radius, and cutting length. These control systems enable the machine to form parts with tight tolerances and consistent quality, essential for applications in critical industries like aerospace and medical device manufacturing. - Automation and Integration:
Increasingly, custom tube forming machines are designed for high levels of automation, reducing the need for manual intervention and increasing throughput. CNC (Computer Numerical Control) systems allow for precise programming of tube forming operations, enabling the machine to run continuously with minimal setup. Integration with robotic arms for tube handling, as well as vision systems for quality control, ensures faster cycle times, enhanced part consistency, and reduced labor costs. - Real-Time Monitoring and Feedback:
Modern custom tube forming machines often feature built-in monitoring systems that provide real-time feedback on key parameters such as temperature, pressure, and material deformation. This allows operators to make immediate adjustments if any deviations from the desired part specifications are detected, ensuring high-quality output throughout the production run. - Customization Options:
The most significant advantage of a custom tube forming machine is its ability to be specifically designed for unique applications. Manufacturers can choose the types of tooling, bending capabilities, and material handling features based on the requirements of the products they are producing. This makes custom machines particularly valuable for low-volume production runs or specialized parts that require unique geometries. - Energy Efficiency:
As industries place increasing emphasis on sustainability, custom tube forming machines are designed with energy efficiency in mind. Features such as energy-efficient motors, regenerative systems for recovering energy from hydraulic presses, and optimized control systems help reduce overall power consumption during operation. This is particularly important for industries that use tube forming machines in continuous production settings.
Applications of Custom Tube Forming Machines
- Automotive Industry:
Custom tube forming machines are widely used in the automotive sector for producing exhaust systems, fuel lines, brake lines, and roll cages. These parts require high strength and precision, often with complex bends or specific geometries. Machines can be customized to handle the demands of these applications, ensuring high throughput and precise part formation. - Aerospace Industry:
In aerospace, tubes are used for critical systems such as fuel lines, hydraulic systems, and aircraft structural components. The materials used in aerospace are often lightweight alloys or high-strength metals, and custom tube forming machines are designed to handle these materials while maintaining strict tolerances and ensuring the structural integrity of the final part. - Energy Industry:
The energy sector, including oil, gas, and renewable energy, relies on tube forming for producing pipes, tubes, and connections used in pressure systems, flowlines, and heat exchangers. Custom tube forming machines are essential for shaping and bending tubes used in high-pressure environments, where precision and strength are critical. - Medical Device Manufacturing:
Medical devices such as stents, catheters, and medical tubing require highly precise forming to ensure functionality and patient safety. Custom tube forming machines allow for the production of tubes with small diameters, thin walls, and complex shapes, all while adhering to strict regulatory standards. - Construction and HVAC:
Tubes are commonly used in plumbing, HVAC (Heating, Ventilation, and Air Conditioning) systems, and structural supports. Custom tube forming machines can create tubes with specific dimensions and strength properties to meet the demands of these industries. - Consumer Goods:
In the production of products like furniture, appliances, and home decor, custom tube forming machines are used to create metal frames, supports, and structural components. The ability to produce these parts with precise bends and cuts enhances the final product’s quality and functionality.
Advantages of Custom Tube Forming Machines
- Precision and Accuracy:
Custom tube forming machines are designed to deliver high precision, ensuring that every part meets the required tolerances. This is especially important in industries where even minor deviations can compromise the functionality or safety of the final product. - Flexibility:
Custom tube forming machines can be tailored to produce a wide variety of shapes and sizes, making them highly versatile for manufacturers producing different types of tubes and components. The ability to switch between different part designs quickly increases production flexibility and reduces downtime. - Increased Productivity:
With features like automation, integrated material handling, and fast cycle times, custom tube forming machines enable manufacturers to increase productivity and meet demanding production schedules. The machines can run 24/7 with minimal supervision, improving overall efficiency and output. - Material Efficiency:
Custom tube forming machines are designed to minimize material waste by precisely cutting and shaping tube stock. This material efficiency reduces the cost of raw materials and helps manufacturers maintain more cost-effective production processes. - Lower Operating Costs:
The integration of automation and smart control systems helps reduce the need for manual labor, thereby lowering operating costs. Furthermore, energy-efficient designs help reduce the power consumption of the machine, leading to additional cost savings. - Quality Control:
Custom tube forming machines can be equipped with integrated inspection systems that ensure parts meet the highest quality standards. Vision systems or laser scanners can be used to check for dimensional accuracy, surface finish, and other criteria, ensuring that every part is free from defects.
Future Trends in Custom Tube Forming Machines
The future of custom tube forming machines will be shaped by advancements in automation, digitization, and material science. As industries move toward more customized production runs and the demand for complex tube geometries increases, tube forming machines will become more flexible and capable of handling a broader range of materials, including lightweight alloys, composites, and sustainable materials.
AI-powered systems will further improve the performance of custom tube forming machines, enabling them to adjust automatically to changing production conditions and optimize the forming process. Additionally, the integration of real-time data analytics and predictive maintenance will enhance the efficiency of these machines by preventing downtime and optimizing machine performance.
Sustainability will also play a larger role, with more manufacturers seeking to reduce waste, improve energy efficiency, and incorporate eco-friendly materials into their products. Custom tube forming machines will need to adapt to these demands by becoming more energy-efficient and capable of handling recycled materials without compromising the quality or integrity of the formed tubes.
In conclusion, custom tube forming machines are an essential part of modern manufacturing, offering precision, versatility, and efficiency for a wide range of industries. As technology continues to advance, these machines will evolve to meet the growing demand for customized, high-performance parts with even greater flexibility and sustainability.
Custom tube forming machines are essential tools for the production of tubes and cylindrical parts, providing versatility and precision to meet specific industry needs. These machines are designed to handle a wide variety of materials, including metals, plastics, and composites, making them indispensable in sectors such as automotive, aerospace, energy, medical devices, and construction. The key advantage of custom machines is their ability to adapt to complex geometries, various tube sizes, and unique bending or cutting requirements. Manufacturers can produce tubes with different profiles, including round, square, rectangular, and even more specialized shapes, offering unparalleled flexibility.
These machines often incorporate advanced technologies such as CNC controls, automated feeding systems, and robotic arms for material handling. This integration of automation improves cycle times, reduces manual labor, and increases throughput. Real-time monitoring and feedback mechanisms, often utilizing sensors and vision systems, further enhance the quality of production, ensuring that each part meets strict tolerances without the need for extensive manual checks.
The capabilities of custom tube forming machines extend to bending, cutting, and joining processes, all of which can be integrated into a single production unit. These machines often feature advanced bending techniques such as rotary draw bending and mandrel bending, allowing for sharp bends without compromising the structural integrity of the material. For cutting, options like laser cutting, sawing, and shearing are commonly employed, while processes like welding, crimping, and flanging enable parts to be joined or finished according to specific requirements.
One of the standout features of custom tube forming machines is their adaptability. Manufacturers can design these machines to handle various materials, including high-strength alloys, lightweight metals, or flexible plastics, each of which may require different settings or tooling. This adaptability is essential in industries such as aerospace or medical device manufacturing, where parts may be subject to rigorous performance standards.
In addition to the core forming processes, tube forming machines are also being designed with sustainability in mind. With the growing emphasis on reducing energy consumption and waste, many machines now incorporate features like energy recovery systems or eco-friendly lubricants. These machines are also increasingly capable of working with recycled materials, supporting the broader push toward circular manufacturing processes.
As the manufacturing landscape evolves, digitization plays an increasingly important role in the operation of custom tube forming machines. The integration of IoT (Internet of Things) technology, predictive analytics, and artificial intelligence enables the machines to make real-time adjustments, optimize operations, and perform predictive maintenance, ensuring both high performance and extended machine lifespans. The use of digital twins and simulation software allows for virtual testing and optimization, reducing the need for physical prototypes and streamlining the design process.
The demand for highly customized components continues to grow, particularly in industries where products are subject to specific, unique requirements. Custom tube forming machines meet this need by providing the ability to produce small batches or even one-off parts while maintaining consistency and quality. This flexibility is particularly valuable for low-volume production runs, where speed and accuracy are paramount.
Looking ahead, the future of custom tube forming machines will likely see even further integration of robotics, smart technologies, and energy-efficient designs. The combination of these innovations will enhance the versatility, precision, and sustainability of tube forming, ensuring that manufacturers can meet the ever-changing demands of various industries while improving their operational efficiencies. The ongoing development of these machines will continue to reshape manufacturing, allowing for the production of increasingly complex and specialized parts with reduced environmental impact.
As custom tube forming machines evolve, the integration of cutting-edge technologies will continue to enhance their capabilities, pushing the boundaries of what is possible in precision and efficiency. The application of machine learning and AI-driven optimizations will allow these machines to automatically learn from past production runs, improving their ability to predict and adjust for variations in materials, temperature, and pressure. Over time, this results in a more reliable production process that reduces human intervention and maximizes output.
Moreover, the growing trend of digitalization in manufacturing will lead to even more advanced control systems. These systems will not only allow manufacturers to remotely monitor the machine’s performance but also analyze historical production data to optimize future runs. Real-time feedback will empower operators to make instant adjustments, ensuring that the final product consistently meets the desired specifications without requiring additional inspection or adjustments.
The demand for multi-functional machines that can perform a range of operations—such as forming, bending, cutting, welding, and finishing—within a single process will likely increase. Manufacturers will continue to seek ways to streamline their production lines by reducing the number of machines and the need for complex part transfers between different stages of production. Custom tube forming machines that integrate multiple operations in one workflow will be key to achieving this efficiency. This approach will not only reduce the need for additional machinery but will also minimize the handling of materials, decreasing the likelihood of damage and improving overall process flow.
Sustainability will remain a top priority, as companies aim to meet stricter environmental regulations and reduce their carbon footprints. Custom tube forming machines will be designed to consume less energy and incorporate more sustainable materials in their construction. In particular, energy-efficient motors, recyclable components, and closed-loop systems for water and oil recycling will become standard features. The future may also see the introduction of solar-powered or regenerative systems that capture energy during operation to power the machine, further contributing to energy savings.
In line with this focus on sustainability, there will likely be an increased demand for custom tube forming machines capable of working with recycled or alternative materials. Many industries are turning to composite materials, biodegradable plastics, and lightweight alloys in an effort to reduce the environmental impact of their products. Custom tube forming machines will need to adapt to these new materials by incorporating specialized tooling and settings that maintain material integrity while achieving the desired forming results.
The flexibility of custom tube forming machines will also enable them to cater to industries that require increasingly complex tube shapes. As industries like aerospace, automotive, and medical devices continue to push the boundaries of design and functionality, the need for innovative geometries and tighter tolerances will increase. These machines will need to be capable of forming tubes with intricate bends, complex cross-sections, and even multi-material compositions, which will allow for the creation of parts with optimal performance characteristics and reduced weight.
Furthermore, the ability to produce customized, small-batch components with minimal lead times will become increasingly important. This will be especially relevant in industries where rapid prototyping and fast product iteration are essential, such as in medical devices and aerospace. The speed at which manufacturers can design, form, and test new tube designs will be a critical competitive advantage, and custom tube forming machines will play a crucial role in this process by enabling quick adjustments to tooling, parameters, and processes.
Another area that will continue to grow is the use of hybrid manufacturing. Custom tube forming machines may begin to incorporate additive manufacturing (3D printing) to complement traditional forming processes. For example, 3D printing could be used to produce complex part features or specialized tooling that would otherwise be difficult or expensive to create using traditional methods. The integration of these technologies will enable manufacturers to create more intricate, customized, and lightweight parts with fewer manufacturing steps, thus reducing production costs and material waste.
Collaboration between custom tube forming machine manufacturers and their customers will also become more critical. As industries continue to require highly specific and tailored parts, the role of engineering collaboration during the design phase will be crucial in ensuring that machines are built to meet the unique needs of individual production runs. Custom tube forming machine manufacturers will offer more consulting services to help clients optimize their production lines, and engineers will work closely with manufacturers to design machines that fit seamlessly into their operations.
As the demand for high-precision tubes in fields like medical devices, space exploration, and nuclear energy increases, custom tube forming machines will become even more specialized to meet the exacting standards of these industries. This could involve the development of machines that can form tubes with extremely tight tolerances, ultra-thin walls, or the ability to incorporate additional features such as integrated sensors or electronic components within the tube structure.
Looking toward the future, the role of custom tube forming machines will be pivotal in enabling innovative manufacturing processes that deliver high-quality, durable, and sustainable products. As industries demand more flexibility, efficiency, and precision, these machines will continue to evolve, incorporating cutting-edge technology and materials to meet the challenges of tomorrow’s manufacturing environment.
Multiple Roller Flow Forming Center

A Multiple Roller Flow Forming Center is an advanced manufacturing system used primarily for the production of high-strength, high-precision cylindrical and hollow components, especially in industries like aerospace, automotive, energy, and heavy machinery. Flow forming is a specialized process that involves the plastic deformation of a material—typically metal—through the use of rollers that apply controlled pressure to elongate and thin the material into the desired shape.
Key Features and Functions of a Multiple Roller Flow Forming Center
- Roller-Based Deformation Process:
Flow forming is essentially a rotary forming process where the workpiece, usually in the form of a tube or disk, is rotated while a series of rollers gradually deform the material. The rollers apply incremental pressure, causing the material to flow and form the desired shape. The process works by gradually thinning and lengthening the material without the need for cutting, making it ideal for producing parts with thin-walled, high-strength geometries. - Multiple Rollers for Precision:
A multiple roller flow forming center uses several rollers positioned around the workpiece, typically in a symmetrical configuration. Each roller applies a specific amount of pressure at a precise point on the material, ensuring uniform deformation. This method allows for the controlled formation of components with complex shapes and precise dimensions. The multiple rollers offer more uniform material distribution and reduced tooling wear, resulting in better consistency and product quality. - High Precision and Strength:
The primary advantage of multiple roller flow forming is the ability to produce components with high dimensional accuracy, smooth surface finishes, and enhanced material properties. By selectively thinning and stretching the material, flow forming increases the strength of the part, particularly in areas that require higher mechanical properties. The process is ideal for parts like hollow shafts, tubes, conical sections, and gears, where the material needs to be reshaped without compromising strength or functionality. - Material Efficiency:
Flow forming is a highly efficient process in terms of material utilization. Because the process involves deforming rather than cutting the material, there is less waste produced compared to traditional machining techniques. The ability to use the material more effectively leads to reduced scrap rates and lower production costs. It is particularly advantageous for expensive alloys and materials like titanium or stainless steel, which are commonly used in aerospace and automotive manufacturing. - Versatility in Material and Geometry:
A multiple roller flow forming center can process a wide range of materials, including high-strength steel, titanium alloys, aluminum, and composites. The process is flexible and capable of forming complex geometries, including tapered shapes, flared ends, and parts with varying wall thicknesses. The ability to produce parts with such diverse and complex geometries makes this technology particularly valuable in industries that require custom or specialized components, such as aerospace or defense. - Process Flexibility:
Multiple roller flow forming centers offer significant flexibility in terms of production. Depending on the machine configuration, the rollers can apply different types of forces (radial, axial, or combined), and the machine can be adjusted to form components of varying sizes, lengths, and shapes. This adaptability allows manufacturers to produce both small-batch and high-volume runs without the need for significant retooling. - Reduced Tooling Costs:
Because the process involves rollers and not traditional cutting tools, tooling costs are lower. The rollers themselves are subject to wear, but they are designed for durability, and the wear rate can be controlled through process optimization. In addition, the no cutting nature of the flow forming process eliminates the need for expensive cutting tools or complex dies, making it more cost-effective than other forming methods. - Energy Efficiency:
Flow forming, especially when compared to traditional forging or machining, is a relatively energy-efficient process. The process does not require high energy inputs like those needed for melting or casting, making it an attractive option for manufacturers looking to reduce their energy consumption and environmental impact. The incremental deformation applied by the rollers requires relatively low force, further enhancing energy efficiency.
Applications of Multiple Roller Flow Forming Centers
- Aerospace Industry:
In aerospace, components must often meet stringent requirements for strength, weight, and performance. Multiple roller flow forming is ideal for producing lightweight, high-strength parts such as fuel tanks, wing spars, exhaust systems, and turbine blades. The process allows manufacturers to create thin-walled parts with excellent material properties, such as high fatigue resistance and improved tensile strength, essential for the demanding conditions of aerospace applications. - Automotive Industry:
The automotive sector benefits from flow forming, especially for components such as wheels, brake drums, and suspension parts. The process allows for the formation of lightweight but strong parts that can handle high stresses and dynamic loads. Additionally, flow forming can be used to produce high-strength hollow shafts or tubes for critical parts like chassis components and drive shafts. - Energy Sector:
Flow forming is widely used in the energy sector, especially for producing components in gas turbines, wind turbine parts, piping, and pressure vessels. Parts such as housings, flanged components, and valves require a combination of strength and resistance to extreme conditions, which flow forming provides. The ability to form thick-walled, high-pressure components with tight tolerances makes flow forming particularly useful in these high-stakes applications. - Defense and Military:
Military and defense applications often demand parts that must withstand extreme pressures, vibrations, and temperatures. Flow forming can be used to manufacture turret housings, missile casings, tank components, and radar domes. The ability to produce lightweight, high-strength parts with minimal material waste is invaluable in the defense industry, where performance and cost-effectiveness are both key considerations. - Industrial Machinery:
Flow forming is also employed in the production of industrial machinery parts, such as gears, cylindrical shells, valves, and pumps. These components require high precision, strength, and durability, all of which can be achieved with flow forming. The ability to produce parts with complex profiles, like tapered sections and conical shapes, is also a major advantage for these applications. - Medical Devices:
The medical device industry increasingly demands custom-made, high-performance components for devices such as catheters, prosthetics, and surgical instruments. Flow forming can be used to produce hollow tubes with fine wall thicknesses and precise geometries, ensuring that components meet the stringent requirements of medical applications.
Advantages of Multiple Roller Flow Forming Centers
- High-Precision and Consistency:
The multiple roller configuration allows for uniform deformation, ensuring high precision in the final product. This level of control results in parts with consistent dimensions and smooth surface finishes, reducing the need for additional finishing processes. - Improved Material Properties:
The incremental deformation process enhances the strength and ductility of the material, improving the mechanical properties of the formed part. The process is especially beneficial for materials that require precise manipulation to achieve optimal strength-to-weight ratios. - Cost-Effectiveness:
With lower material waste, reduced tooling costs, and the ability to produce complex parts in a single process, multiple roller flow forming centers offer significant cost advantages. The ability to produce high-quality parts with minimal scrap makes it a cost-effective alternative to traditional machining and forging. - Flexibility in Production:
The system can be adapted to produce both low-volume and high-volume parts, making it ideal for industries with fluctuating demand or those requiring custom components. The same machine can produce a wide variety of shapes and sizes, offering unmatched flexibility. - Energy Efficiency:
The process is energy-efficient, especially when compared to other methods like forging or casting, as it requires less power to deform the material. This makes it a more environmentally friendly option in industries that are focused on reducing their carbon footprint. - Minimal Tooling Wear:
The rollers are designed for long-lasting use, and because flow forming doesn’t involve cutting or excessive heat, there is less wear on the tooling, which leads to longer machine life and reduced downtime.
Future Trends in Multiple Roller Flow Forming Centers
- Automation and Smart Manufacturing:
The future of multiple roller flow forming centers will likely involve greater integration of automation and smart technologies. This includes robotic material handling, CNC-controlled adjustments, and real-time monitoring to further enhance precision, productivity, and reliability. Smart sensors and predictive analytics will help anticipate maintenance needs, further reducing downtime and optimizing performance. - Sustainability:
As industries continue to prioritize environmental sustainability, future multiple roller flow forming systems will likely focus on reducing energy consumption, material waste, and emissions. Innovations in green manufacturing technologies may drive more eco-friendly machines and processes, including the use of recycled materials. - Advanced Materials:
As new materials continue to emerge, the multiple roller flow forming process will evolve to accommodate these changes. Composites, lightweight alloys, and advanced metals will increasingly be incorporated into flow forming systems, enabling the production of even more specialized parts for industries like aerospace and automotive. - Customization:
The growing demand for custom and highly specialized parts will drive further advancements in customizable flow forming machines. Manufacturers will require even more adaptable and versatile machines that can handle complex geometries and specific material requirements to meet the needs of various industries.
In conclusion, multiple roller flow forming centers are integral to the production of high-performance components in industries that require precision, strength, and material efficiency. As technology advances, the flexibility, sustainability, and capabilities of these machines will continue to evolve, meeting the demands of an increasingly complex and competitive manufacturing environment.
Multiple roller flow forming centers are becoming increasingly important in advanced manufacturing, offering unparalleled precision and efficiency for producing high-performance components. These systems allow manufacturers to shape materials, particularly metals, with minimal waste, using controlled deformation rather than traditional cutting. This results in products that maintain the integrity and strength of the material while achieving complex geometries and precise dimensions. The ability to process materials such as high-strength alloys, aluminum, titanium, and composites makes these machines indispensable in sectors like aerospace, automotive, medical devices, and energy.
The main appeal of multiple roller flow forming is its ability to produce thin-walled, high-strength parts, which are crucial in industries requiring components that need to withstand extreme conditions while being lightweight. The controlled deformation process allows for significant material savings, as there is little to no scrap compared to traditional machining methods. This makes flow forming not only more economical but also environmentally friendly, as it reduces the need for raw material and minimizes waste generation.
Moreover, the versatility of multiple roller systems enables them to produce a wide range of complex shapes and profiles. These machines can handle components with varying wall thicknesses, tapered sections, or even flanged edges, all of which are difficult to achieve through conventional forming or machining processes. The ability to produce both simple and intricate shapes with a high degree of accuracy ensures that these machines meet the diverse demands of various industries.
In aerospace, the precision offered by multiple roller flow forming centers is invaluable for producing lightweight, durable components such as turbine blades, fuel tanks, and structural parts. The flow forming process enhances the material’s mechanical properties, providing components that can endure the high stresses and temperatures found in aviation environments. Similarly, in the automotive industry, these systems allow manufacturers to produce gears, suspension components, and brake drums that combine high strength and low weight, crucial for enhancing vehicle performance and fuel efficiency.
The process also contributes to the growing demand for customized and small-batch production. With the increasing trend toward bespoke designs, particularly in industries like medical devices and defense, manufacturers require flexible systems capable of producing highly specialized parts. Multiple roller flow forming centers meet this need, offering quick changes between part designs without significant retooling, which improves lead times and reduces costs for low-volume runs. This flexibility is especially advantageous for applications that demand frequent design iterations or the rapid development of prototypes.
With advances in automation, sensor technology, and machine learning, the future of multiple roller flow forming centers looks even more promising. These machines will become even smarter, with real-time monitoring systems that ensure consistent quality and precision throughout production. Automation will help minimize human intervention, reduce errors, and improve overall efficiency, leading to more reliable and cost-effective production. Predictive maintenance algorithms will further increase machine uptime and reduce operational disruptions, allowing manufacturers to maximize output.
The growing emphasis on sustainability will also influence the development of multiple roller flow forming centers. Innovations in energy efficiency, the reduction of material waste, and the ability to process recycled materials will ensure that these systems are in line with the global push toward greener manufacturing. The integration of closed-loop systems for energy recovery and the use of environmentally friendly lubricants will further enhance the environmental footprint of these machines.
As industries continue to evolve and demand more complex, high-performance parts, multiple roller flow forming centers will remain at the forefront of manufacturing technology. Their ability to produce strong, lightweight, and precise components with minimal waste makes them a crucial tool in meeting the challenges of modern industrial production. The combination of high performance, material efficiency, and design flexibility will continue to drive their adoption across various high-tech sectors, ensuring their place in the future of advanced manufacturing.
As multiple roller flow forming centers continue to evolve, their integration with other cutting-edge technologies will further enhance their capabilities. The incorporation of additive manufacturing or 3D printing in combination with flow forming is a potential area of growth. For instance, 3D printing could be used to create intricate tooling or even customized features within the formed component itself. This hybrid approach can provide an even more efficient and flexible way to produce complex parts with optimal material properties.
The use of real-time data analytics will become more prevalent in flow forming centers, with sensors embedded throughout the machine to provide live feedback on material flow, temperature, pressure, and other variables. This data can be analyzed to adjust parameters on the fly, ensuring that each part is produced to the exact specifications. Manufacturers will have the ability to monitor machine health, track production performance, and predict potential failures before they occur, leading to reduced downtime and increased productivity.
In addition to real-time monitoring, advanced simulation software will play a key role in the future development of flow forming processes. Engineers will be able to simulate the entire forming process in a virtual environment, predicting how materials will behave under different conditions and optimizing the tooling and machine settings. This predictive modeling will allow manufacturers to experiment with new materials, geometries, and production techniques without the need for costly trial and error in the physical world.
The application of artificial intelligence (AI) in multiple roller flow forming centers will lead to the development of intelligent systems capable of making adjustments based on past production data. AI-driven systems will learn from previous runs and automatically make process optimizations, such as adjusting roller speeds or pressure levels, to maximize both efficiency and part quality. Over time, this will allow the system to become more autonomous, requiring less human intervention and improving overall consistency across production runs.
As materials continue to advance, the demand for high-performance alloys and composite materials will only increase. Flow forming centers will need to adapt to handle these new materials, which often have unique properties that require specialized tooling and process parameters. For example, advanced titanium alloys, carbon fiber composites, and lightweight magnesium alloys may need customized tooling or heat treatment stages to ensure that the material properties are not compromised during the forming process. The ability to process such materials will be a key driver for flow forming technology, especially as industries like aerospace, defense, and automotive push the limits of material performance.
In the realm of multi-material processing, multiple roller flow forming centers will likely evolve to process not just one material, but multiple materials within the same component. This could be particularly useful in applications such as medical devices or automotive parts, where different material properties are required in different sections of a component. For example, a medical implant might require a highly biocompatible surface layer with a strong internal structure, while an automotive component might require lightweight outer sections and strong, fatigue-resistant inner parts. The ability to integrate multiple materials into a single part could be achieved through advanced flow forming technologies, opening up new possibilities for custom designs.
Looking ahead, customization and on-demand production will become even more crucial. As industries increasingly demand parts tailored to specific applications, the flexibility of multiple roller flow forming systems will be critical. The ability to adjust machine parameters quickly, switch between different part designs, and accommodate small-batch runs will allow manufacturers to respond more quickly to market demands. This agility is especially important in industries where supply chains are more complex, and the ability to deliver just-in-time components is essential.
Moreover, globalization will continue to drive the demand for localized manufacturing, where companies look to produce components closer to their end markets to reduce lead times and shipping costs. Multiple roller flow forming centers, which offer modular design and flexible production capabilities, will allow manufacturers to establish production facilities in diverse regions, reducing the need for centralized manufacturing and creating more resilient supply chains.
As digital manufacturing advances, these flow forming centers will become more integrated into larger smart factories where machines communicate with each other, share data in real-time, and work in tandem to produce complex assemblies. This interconnected environment will increase the efficiency of production lines, allowing companies to take full advantage of automation, real-time monitoring, and predictive analytics to optimize every aspect of production.
Another key factor in the continued growth of multiple roller flow forming centers will be the rise of collaborative robotics or cobots. These robots can work alongside human operators to handle heavy or repetitive tasks, such as loading and unloading parts, while allowing the human operator to focus on more complex tasks that require critical thinking and problem-solving. The integration of cobots will enhance safety on the production floor and improve the ergonomics of operators’ work environments.
In terms of maintenance and support, predictive maintenance technologies will become more refined. By monitoring the health of the rollers, motors, and other components in real-time, machine operators can be alerted to any potential issues before they lead to costly downtime. This system of continuous monitoring will allow manufacturers to schedule maintenance when it’s needed most, reducing the frequency of unscheduled repairs and increasing the lifespan of the equipment.
As industries continue to embrace Industry 4.0 principles, the use of cloud-based systems and remote diagnostics will become more common. Operators will be able to access real-time data, receive maintenance alerts, and even control the machine remotely from anywhere in the world. This level of connectivity will allow manufacturers to optimize their operations on a global scale and enable seamless collaboration between different production facilities.
With all these technological advancements, multiple roller flow forming centers will become smarter, more adaptable, and more efficient, making them an indispensable part of the future manufacturing landscape. As the demands of various industries become more complex, the need for precision, efficiency, and material performance will drive further innovation in flow forming processes, ensuring that these machines continue to play a critical role in producing high-quality, customized components for years to come.
High Speed Precision Spinning Machine
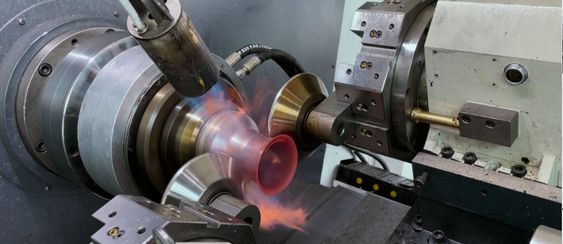
A High-Speed Precision Spinning Machine is an advanced manufacturing system designed to produce precise and complex rotational components through the process of spinning. Spinning, also known as rotational forming, involves the deformation of a thin disc or cylindrical workpiece using a rotating mandrel and a set of tools (usually rollers or spinners) to shape the material into a desired form. This process is widely used in industries that require high-precision, thin-walled components with consistent geometries, such as aerospace, automotive, medical devices, and industrial machinery.
Key Features and Benefits of High-Speed Precision Spinning Machines
- High-Speed Operation:
High-speed precision spinning machines operate at significantly higher rotational speeds compared to traditional spinning machines. This increase in speed allows for faster processing times and higher throughput, making these machines ideal for high-volume production environments. The ability to form parts quickly and efficiently also reduces energy consumption and increases productivity, offering a cost-effective solution for manufacturers. - Precision and Accuracy:
One of the primary advantages of high-speed precision spinning is the exceptional dimensional accuracy it provides. The process allows manufacturers to create parts with tight tolerances and smooth surface finishes, which is especially important in industries such as aerospace and medical devices, where even the smallest defect can affect part performance. The precision offered by these machines makes them ideal for creating parts with intricate shapes, thin walls, and uniform thicknesses. - Material Versatility:
High-speed spinning machines can handle a wide variety of materials, including metals such as aluminum, stainless steel, titanium, and copper. Additionally, they can be used to spin both ferrous and non-ferrous alloys as well as composite materials. This versatility allows manufacturers to create parts from a broad range of materials with different mechanical properties, making high-speed precision spinning suitable for diverse applications. - Thin-Walled Components:
High-speed precision spinning is particularly well-suited for the production of thin-walled components. The process works by gradually stretching and thinning the material to achieve the desired shape. This allows manufacturers to create components that are lightweight yet strong, which is crucial for industries such as aerospace, where weight reduction is a significant factor. Thin-walled parts produced by precision spinning can maintain high structural integrity, making them ideal for use in demanding applications. - Improved Material Properties:
The spinning process results in the work hardening of the material, which enhances its strength and fatigue resistance. This is particularly beneficial for parts that will be subjected to high levels of stress or cyclic loading. For example, in aerospace and automotive applications, parts like turbine blades, exhaust components, and brake discs benefit from the increased material strength achieved through spinning. - Complex Geometries:
High-speed precision spinning machines are capable of producing parts with complex geometries that would be difficult or impossible to achieve using traditional machining techniques. For example, the process can create conical, parabolic, or bell-shaped parts with high precision. The ability to produce these intricate shapes with minimal tooling makes high-speed spinning machines valuable for manufacturers who require custom, complex components. - Cost-Effective Production:
High-speed precision spinning is a cost-effective manufacturing process for producing high-quality parts, especially when compared to more traditional methods like casting, forging, or machining. The spinning process generates less material waste, as it uses the existing material efficiently, without the need for heavy machining or extensive finishing processes. This reduction in waste and the ability to reuse materials makes the process economically advantageous, especially for high-volume production runs. - Reduced Tooling Costs:
The tooling used in high-speed precision spinning is generally simpler and less expensive than the tooling required for processes like casting or die forging. The use of rotary tools and mandrels in the spinning process often reduces the need for intricate molds, leading to lower setup and maintenance costs. This makes high-speed spinning a more affordable option for manufacturers looking to produce custom parts in both small and large quantities. - Enhanced Surface Finish:
One of the notable features of high-speed precision spinning is the smooth surface finish it imparts to the parts. The continuous deformation of the material while it is spun at high speeds results in a finely polished surface with minimal defects. This is particularly beneficial in applications where a smooth or mirror-like finish is required, such as in aerospace, optics, and medical device manufacturing. - Minimal Post-Processing:
Because high-speed precision spinning produces parts with high accuracy and surface quality, there is often little to no need for additional post-processing or finishing. This reduces the overall manufacturing time and cost, as parts can often be used directly after spinning, particularly when precise geometries and surface finishes are required.
Applications of High-Speed Precision Spinning Machines
- Aerospace:
In the aerospace industry, high-speed precision spinning is used to create components like turbine blades, engine housings, fuel tanks, and wing parts. These components must meet stringent requirements for weight, strength, and fatigue resistance, and spinning is ideal for producing lightweight, high-strength parts with complex geometries. The ability to produce thin-walled components with excellent material properties makes this technology indispensable in aerospace manufacturing. - Automotive:
The automotive industry relies on high-speed precision spinning to produce parts such as brake discs, wheels, drivetrain components, and exhaust system components. The process is particularly beneficial for producing parts that need to withstand high stresses and temperatures while maintaining a lightweight profile. Spinning is also used to manufacture hydraulic cylinders, suspension components, and gear housings with complex shapes. - Medical Devices:
High-speed precision spinning is used to create medical components such as surgical instruments, implants, prosthetic components, and catheters. The precision and smooth surface finish provided by the spinning process are essential in the medical field, where part performance and biocompatibility are critical. Additionally, the ability to produce customized, small-batch parts makes spinning an ideal choice for the medical device industry. - Energy:
In the energy sector, high-speed precision spinning is used to produce components for gas turbines, wind turbine parts, and nuclear reactors. These components often require the high strength-to-weight ratio and fatigue resistance that spinning provides. The ability to produce parts with thin-walled structures makes high-speed spinning ideal for creating energy-efficient components in power generation systems. - Consumer Electronics:
Precision spinning is also used in the production of casings and housing components for consumer electronics such as smartphones, laptops, and televisions. The high precision and smooth finish offered by the spinning process are key to creating aesthetically pleasing, durable, and lightweight products that meet the demands of modern electronics manufacturing. - Industrial Equipment:
High-speed precision spinning is applied in the manufacture of pressure vessels, tanks, pumps, valves, and industrial housings. The ability to form these components with high precision and minimal material waste is essential in industries that require components capable of withstanding high pressure, temperature, and mechanical stress. - Optics and Light Manufacturing:
Precision spinning is widely used in the production of reflective surfaces, lenses, mirrors, and optical components. The smooth finish and high precision of the spinning process make it ideal for creating parts that require optical clarity and uniform thickness, which is critical in the manufacture of high-quality optics for instruments, cameras, and other optical devices.
Advantages of High-Speed Precision Spinning Machines
- Faster Production Cycles:
The high-speed operation of these machines leads to faster production cycles, which is especially beneficial in industries with high-volume requirements. Faster processing times help manufacturers meet tight deadlines and improve overall productivity. - Energy Efficiency:
High-speed spinning is more energy-efficient than many traditional manufacturing processes, such as casting or machining. The controlled deformation process requires less energy, reducing both operating costs and the environmental impact of production. - Improved Design Flexibility:
The ability to produce complex shapes and custom designs with ease makes high-speed precision spinning a flexible solution for manufacturers. Parts can be customized for specific applications, whether in terms of material, shape, or size, making the process highly adaptable to varying customer requirements. - Material Efficiency:
Unlike traditional machining processes, which remove material from a larger workpiece, spinning uses the material efficiently by reshaping it. This reduction in material waste is both cost-effective and environmentally friendly, particularly when using expensive alloys or specialized materials. - Reduced Tooling Costs:
The tooling used in high-speed precision spinning machines is typically less expensive than that used for casting or forging, making the process more cost-effective for manufacturers. Moreover, the tooling is generally more durable, requiring fewer replacements over time. - High-Quality Parts with Minimal Post-Processing:
High-speed precision spinning often results in parts with high dimensional accuracy and smooth surfaces, minimizing the need for additional post-processing or finishing steps. This reduces the overall production time and cost, making it a highly efficient manufacturing process.
Conclusion
High-speed precision spinning machines represent a highly advanced and efficient solution for producing high-quality, precision components in a wide range of industries. Their ability to create complex geometries with thin walls, combined with fast production times and material efficiency, makes them a key tool in modern manufacturing. As industries continue to demand higher performance, lighter weight, and more precise components, high-speed precision spinning will continue to be a vital technology for meeting these needs. With the integration of smart technologies, automation, and advanced materials, the potential of high-speed precision spinning will only continue to expand, offering exciting possibilities for the future of manufacturing.
High-Speed Precision Spinning Machines represent a transformative leap in manufacturing technologies, offering the ability to produce intricate, high-precision components rapidly and efficiently. As industries continue to push the boundaries of performance, the need for lightweight, high-strength, and complex components grows, making spinning machines more relevant than ever. Their capability to handle a wide range of materials—including metals, composites, and even certain plastics—gives manufacturers the flexibility to produce parts for a variety of demanding applications, all while maintaining material integrity and minimizing waste.
In industries such as aerospace, automotive, and medical devices, the importance of high-precision manufacturing cannot be overstated. Components often must meet stringent standards for weight, strength, and durability, and high-speed precision spinning delivers all of these in a highly efficient process. By enabling the creation of thin-walled parts with superior mechanical properties, spinning machines help reduce material consumption and energy costs, all while maintaining or even improving the performance of the final part.
One of the major advantages of these spinning machines is their ability to produce customized and small-batch components at a relatively low cost, without the need for highly expensive molds or extensive tooling. As industries continue to demand more personalized and custom-fit components—whether it’s a specialized part for aerospace engines, medical implants, or consumer electronics—the flexibility of high-speed spinning machines becomes crucial. Their ability to produce low-cost, high-quality parts in a variety of shapes and sizes allows manufacturers to better respond to customer needs, especially in high-precision applications.
Further advancements in automation and data analytics will continue to enhance the performance and efficiency of high-speed precision spinning machines. With real-time feedback and intelligent optimization, future systems will be able to fine-tune the spinning process on the fly, ensuring even greater consistency and reducing the possibility of defects. The combination of high-speed operation and predictive maintenance will ensure that machines remain operational longer and require fewer unscheduled repairs, which is crucial for industries where downtime is costly.
As material science advances, high-speed spinning machines will be required to adapt to the increasing range of advanced materials used in modern manufacturing. The ability to handle specialized alloys, such as high-temperature-resistant materials, or composite components used in advanced aerospace and automotive applications, will be key to staying at the forefront of precision manufacturing. This will demand new techniques for tool materials and machine configurations, ensuring that they can accommodate the unique properties of these advanced materials without compromising part quality.
The growing importance of sustainability in manufacturing will also shape the development of high-speed precision spinning machines. The ability to minimize material waste, reduce energy consumption, and recycle materials during the manufacturing process will become increasingly important. High-speed spinning, which typically generates minimal waste compared to other methods such as casting or machining, positions itself as a highly sustainable process. In industries where sustainability goals are a driving factor, such as in automotive or electronics, manufacturers will likely find high-speed spinning a valuable option.
In addition, as industries seek to lower their environmental impact and produce parts locally, high-speed spinning machines will play a vital role in localized manufacturing and on-demand production. The flexibility and efficiency of these machines make them ideal for producing components directly at the point of need, reducing transportation costs and cutting down on carbon footprints associated with global supply chains.
Ultimately, the high-speed precision spinning machine is not just a tool for manufacturing, but a critical enabler of innovation. The technology will continue to evolve, integrating with Industry 4.0 concepts like smart factories, machine learning, and advanced robotics, further enhancing its role in producing high-performance components with ever-greater precision and efficiency. As demand for customization, higher performance, and more complex parts increases across multiple industries, high-speed precision spinning will remain a key technology in meeting these challenges, ensuring that it stays at the cutting edge of manufacturing processes.
As the technology behind high-speed precision spinning continues to advance, manufacturers will increasingly integrate smart capabilities into their systems. These innovations could include the ability for machines to self-optimize during production runs, adjusting parameters like speed, pressure, and temperature in real-time based on feedback from sensors embedded within the machine. This would not only improve the efficiency of the production process but also further reduce the likelihood of defects, leading to higher consistency and fewer rejections. Additionally, machines that can automatically adjust to handle different materials and part designs without requiring manual intervention would be highly valuable in industries with fluctuating demands or diverse production needs.
The integration of artificial intelligence (AI) will be a game changer, enabling predictive capabilities that go beyond simple machine learning algorithms. With AI, machines could learn from vast amounts of data generated during previous production cycles and then apply this knowledge to predict and prevent potential issues before they occur. For instance, AI-driven systems could predict material flow behavior, suggest optimal tool configurations, and identify trends that might point to an underlying problem with the material or machine. By leveraging AI in this way, manufacturers can enhance the predictive maintenance capabilities of high-speed spinning machines, ultimately reducing downtime and improving overall machine reliability.
As Internet of Things (IoT) technology becomes more ubiquitous in industrial manufacturing, high-speed spinning machines will be able to integrate into broader digital ecosystems. This will allow for better communication between machines, operators, and external systems, creating an interconnected manufacturing environment where real-time data is constantly shared, analyzed, and acted upon. For example, machines could automatically adjust to changes in raw material quality or environmental factors, or operators could monitor the health of machines remotely, receiving instant alerts for any abnormal conditions that might affect production quality.
Digital twins—virtual replicas of physical machines—will also become more common in high-speed spinning operations. These digital models will allow engineers and operators to simulate the spinning process, experiment with different designs and parameters, and optimize machine performance without physically altering the machine. The ability to predict how changes in the design or material properties affect the final product will be crucial for industries that require high levels of precision, such as aerospace, medical device manufacturing, and defense.
With the growing emphasis on sustainability in manufacturing, high-speed precision spinning machines will need to further develop their ability to minimize material waste and energy consumption. Innovations in energy recovery systems could allow machines to recycle energy that would otherwise be lost during operation, such as through the use of regenerative braking or energy-saving drive systems. Additionally, the ability to recycle scrap material generated during the spinning process, either by reusing it in the same production run or sending it to be remelted and reused, will become more important as manufacturers strive to achieve zero-waste or closed-loop production systems.
The continued demand for customization and short-run production will push high-speed precision spinning machines to adapt to faster setup times and more flexible configurations. With industries increasingly requiring bespoke parts in low quantities, machines will need to be able to change setups quickly to accommodate different part designs, materials, and geometries. This could be achieved through modular tool systems, automated changeovers, and quick-change mandrels. The ability to switch between different part designs without extensive downtime will allow manufacturers to meet customer needs more efficiently and effectively, while maintaining cost-effectiveness in production.
In terms of global competitiveness, the advancement of high-speed precision spinning machines will give manufacturers a competitive edge, particularly in industries where high precision, speed, and customization are critical. Companies that invest in state-of-the-art spinning technology will be able to offer faster turnaround times, produce high-quality custom parts at scale, and maintain lower operating costs, all while improving their sustainability practices. As customers increasingly demand more personalized products and as lead times shorten, manufacturers who embrace this technology will be able to respond to changing market demands with greater agility.
Furthermore, advancements in automation and robotics will continue to improve both safety and ergonomics in high-speed precision spinning environments. Automated material handling, such as the use of robotic arms to load and unload parts or tools, will reduce the physical strain on operators and improve workplace safety. This will be particularly beneficial in high-precision industries where there is little room for error and where operators are often required to work with heavy or difficult-to-handle materials. Robots could also assist in quality inspection, scanning parts for defects or inconsistencies that might otherwise be overlooked during manual inspection.
As the field of advanced manufacturing technologies expands, the integration of additive manufacturing (3D printing) with high-speed spinning is a potential area of growth. 3D printing could be used to create complex tooling or even hybrid parts that combine spun material with 3D printed elements to optimize strength, weight, and functionality. This hybrid approach would expand the scope of what can be achieved in part design and manufacturing, combining the strengths of both technologies for even greater flexibility and capability.
In conclusion, high-speed precision spinning machines will continue to evolve, driving new levels of efficiency, quality, and customization in manufacturing processes. With the integration of AI, IoT, and advanced automation, these machines will become even more adaptive, predictive, and responsive to the needs of modern manufacturing. As industries demand more complex, lightweight, and high-performance parts, high-speed precision spinning will remain a key technology, capable of meeting these challenges while maintaining sustainability and cost-effectiveness. By embracing these technological advancements, manufacturers will position themselves to stay ahead of the competition and continue to deliver high-quality, precision-engineered components that meet the needs of the future.
High Performance Double Arm Spinning Machine
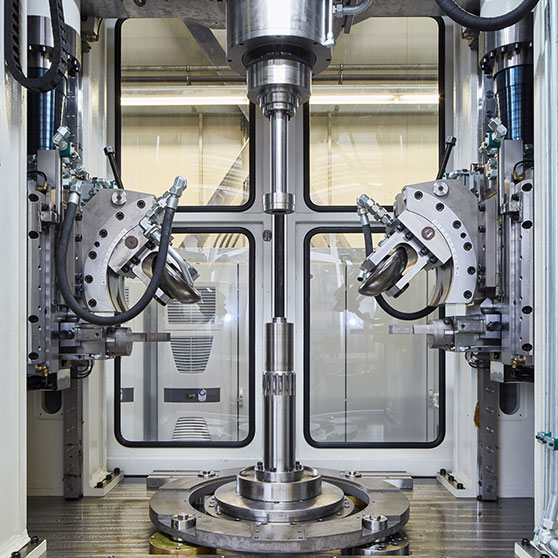
The High-Performance Double Arm Spinning Machine represents a significant advancement in the realm of metal forming and precision fabrication. Designed for applications that demand enhanced forming capabilities, speed, and control, this machine utilizes two synchronized spinning arms to perform complex shaping operations on metal blanks. The double-arm configuration not only increases the force distribution and stability during forming but also allows for greater precision and symmetry, which is critical in producing parts with tight tolerances and intricate geometries.
This machine is especially valuable in sectors such as aerospace, defense, and high-end automotive manufacturing, where components like turbine housings, rocket nozzles, pressure vessels, and structural domes must meet rigorous quality and dimensional standards. By applying forming pressure from both sides of the workpiece simultaneously, the double arm system minimizes deformation, reduces vibration, and maintains uniform wall thickness throughout the entire component. This results in superior structural integrity and material performance, often eliminating the need for secondary processing or welding.
Another key advantage of the double arm system is its ability to handle larger and thicker blanks than traditional single-arm spinning machines. The balanced force application reduces the stress on individual components of the machine, prolonging tool life and improving overall operational efficiency. These machines can work on a wide range of metals, including aluminum alloys, stainless steel, titanium, and superalloys, which are often required for high-stress, high-temperature applications.
From an automation standpoint, High-Performance Double Arm Spinning Machines often come integrated with CNC controls, servo-driven actuators, and real-time monitoring systems. This enables precise control over speed, feed, and pressure, allowing operators to fine-tune parameters to suit specific material and part requirements. The result is consistent production quality, reduced scrap rates, and the ability to replicate complex shapes across multiple production runs with high accuracy.
As with other advanced forming systems, these machines are being enhanced with smart technologies, including AI-driven process optimization, automated defect detection, and predictive maintenance tools. These features ensure minimal downtime, maximum throughput, and real-time adaptability to changes in material or design specifications. The machine can also be programmed to adjust on the fly to compensate for material springback or inconsistencies, which significantly reduces the risk of forming defects in critical applications.
In summary, the High-Performance Double Arm Spinning Machine is a cornerstone of modern precision forming. It combines strength, speed, and accuracy in a versatile platform that supports high-volume and high-specification production. As the demand for lightweight, high-strength, and geometrically complex components grows, especially in mission-critical industries, this machine will continue to play a vital role in enabling manufacturers to meet these evolving requirements with confidence and precision. Would you like to explore its typical applications or compare it with other spinning technologies?
The evolution of the high-performance double arm spinning machine is tightly linked to the growing complexity and precision requirements in modern manufacturing. As industries demand more from formed metal parts in terms of geometry, consistency, and strength, machines like this become indispensable. The synchronized motion of the two spinning arms allows for intricate shapes to be formed with a high degree of repeatability, especially in symmetrical components where any imbalance could lead to performance issues or failure. This level of control also means that manufacturers can push the limits of wall thinning, producing lighter yet stronger components—an essential attribute in aerospace and high-speed transport systems. The double-arm setup enables better heat dissipation during forming, reducing thermal distortion and improving metallurgical characteristics by maintaining more uniform temperature gradients across the workpiece.
In addition to mechanical advantages, these machines are often coupled with advanced material feeding and clamping systems that allow for seamless integration into automated production lines. Operators can pre-load a series of blanks, and the machine can index them automatically, dramatically increasing throughput and minimizing idle time. High-speed tooling changes enabled by quick-lock systems mean that even in small-batch or custom part production, downtime between setups is minimized. The dual-arm configuration is particularly well suited for forming non-axisymmetric or compound curved profiles, something that traditional single-arm machines struggle with. By being able to apply asymmetric pressures deliberately and in a controlled manner, these machines expand the design possibilities for engineers working on cutting-edge components.
Moreover, the software ecosystem surrounding double arm spinning machines is becoming increasingly powerful. Machine learning algorithms can now suggest optimized spinning paths and parameters based on historical data, material behavior, and part geometry. These systems can simulate toolpaths in virtual environments before actual production begins, ensuring that the first piece produced is often within tolerance. This not only saves time but reduces material waste significantly—critical in industries where the cost of raw material, such as titanium or Inconel, is exceptionally high. Additionally, integration with enterprise resource planning (ERP) and manufacturing execution systems (MES) allows full traceability of every part, from material lot to finished product, making quality assurance robust and audit-ready.
The role of real-time diagnostics is also growing in these systems. Embedded sensors monitor factors such as spindle vibration, tool wear, and temperature, all of which are crucial for high-precision forming. If an anomaly is detected—such as an unexpected spike in force or a deviation in spindle alignment—the machine can alert operators or even pause the process to prevent damage. In predictive maintenance models, this data feeds into dashboards that flag potential failures before they occur, reducing unplanned downtime and extending machine life. Over the long term, these capabilities transform spinning from a traditional, craftsmanship-dependent process into a repeatable, scalable, and highly intelligent operation.
Another significant aspect is the environmental benefit. With increasing focus on sustainable manufacturing, double arm spinning machines align well with industry goals. Their material efficiency—thanks to net-shape forming—results in minimal scrap generation. Energy usage is optimized by servo motors and regenerative drives that recover and reuse energy during deceleration phases. Some manufacturers are exploring the use of these machines in green facilities powered by renewable energy, further reducing their carbon footprint. Additionally, the longer lifespan of formed components and the reduced need for secondary machining mean lower resource consumption throughout the product lifecycle.
In competitive global markets, the ability to quickly adapt to new part designs is a strategic advantage, and double arm spinning machines are particularly agile in this respect. Tooling development for these systems is relatively fast, and CAD/CAM integration allows for seamless transition from digital model to physical part. Rapid prototyping, once dominated by additive manufacturing, is now being complemented by rapid forming, where functional prototypes can be created in production-grade materials in a matter of hours. This hybrid approach—combining forming and spinning with digital workflows—is helping manufacturers shrink development cycles and bring new products to market faster.
Looking forward, the convergence of technologies such as artificial intelligence, robotics, digital twins, and advanced materials will continue to elevate the capabilities of high-performance double arm spinning machines. As demand grows for highly specialized parts in aerospace propulsion, electric vehicle components, medical implants, and clean energy systems, the adaptability and precision of these machines will ensure they remain at the forefront of advanced manufacturing. Whether it’s forming a thin-walled nozzle for a hypersonic jet or a pressure dome for a fusion reactor, the double arm spinning machine provides the precision, strength, and efficiency required to meet the most demanding engineering challenges of the future.
This future-facing role of the high-performance double arm spinning machine is further reinforced by its expanding compatibility with multi-material systems. As advanced manufacturing increasingly involves dissimilar metal joining, composite-metal hybrids, and coated materials, the need for forming equipment that can handle such complexity without degrading the interface layers becomes critical. The double arm machine’s balanced force application and programmable pressure zones make it suitable for working with layered or bonded materials, preserving the integrity of interfacial adhesives or coatings during forming. This is especially relevant in sectors like aerospace and medical devices, where lightweight composites are combined with metal layers to optimize strength-to-weight ratios or meet biocompatibility standards.
Another growing use case is in cryogenic and high-temperature component manufacturing, where precision and material behavior under stress are tightly controlled. For example, components used in liquefied natural gas (LNG) transport or space propulsion systems often require forming of nickel-based superalloys with exceptional accuracy. The dual-arm spinning process offers superior control over the flow of these difficult-to-form materials, distributing the forming energy more evenly across the workpiece and reducing the likelihood of microcracking or grain distortion. This ensures the mechanical properties of the final part meet the exacting demands of such extreme operating environments.
In the realm of design freedom, the double arm configuration empowers engineers to think beyond conventional geometric limits. Components with variable wall thickness, internal radii, and asymmetric shapes can be manufactured with fewer processing steps and greater structural uniformity. Unlike machining or welding processes that often add stress or require multiple assembly stages, spinning can produce monolithic parts that reduce weak points and improve fatigue performance. This is particularly beneficial in structural aerospace parts, high-performance automotive wheels, and next-gen electric motor housings, where integrity and lightness are non-negotiable.
A less visible but equally critical benefit of these machines is their role in workforce development and knowledge retention. Traditional spinning often required years of experience and was heavily reliant on manual skill. The move toward CNC and automated double arm spinning shifts the skillset toward digital programming, process control, and data interpretation. This not only helps overcome the skilled labor shortage many industries face, but also creates more resilient and scalable production systems. Digital workflows allow knowledge to be encoded in machine programs, ensuring process consistency and enabling rapid training of new operators. In an era where skilled trades are aging out of the workforce, this transition is both timely and essential.
Furthermore, these machines offer exceptional value in prototyping and low-volume production, making them a viable solution even for startups and research institutions. The same platform that produces a production part can also be used to test material responses, optimize forming strategies, and validate new geometries. This accelerates the feedback loop between design and manufacturing, supporting agile product development cycles. Academic and industrial R&D labs are increasingly using double arm spinning setups as test beds for innovation in forming science, tool wear studies, and even in emerging applications such as forming of ultra-thin foils for battery or sensor components.
The technology’s upward trajectory is also shaped by its ability to scale across a broad range of part sizes. Modular machine designs allow for compact units focused on small precision parts as well as massive, gantry-style systems capable of forming parts several meters in diameter. This scalability ensures the double arm spinning machine is not limited to a specific niche but can serve across the spectrum of industrial needs—from compact pressure domes for medical gas systems to large transition cones in rocket fairings.
As supply chains become more regionalized and responsive manufacturing gains priority, the double arm spinning machine is positioned as a core asset in distributed production models. Its ability to switch between parts, handle a variety of materials, and operate with minimal setup time aligns perfectly with localized, just-in-time manufacturing strategies. In a world increasingly disrupted by geopolitical tensions and logistics volatility, machines that support flexible, high-mix, low-volume production close to the point of use offer both strategic and economic advantages.
Ultimately, the high-performance double arm spinning machine isn’t just an evolution of traditional forming equipment—it’s a convergence point for digital intelligence, mechanical precision, and manufacturing agility. Its integration into modern production systems will continue to shape the way complex, high-performance metal parts are conceived, designed, and produced. As part geometries become more sophisticated, material science continues to evolve, and performance expectations rise, these machines will remain central to unlocking new frontiers in design and engineering.
Vertical End Forming Spinning Machine
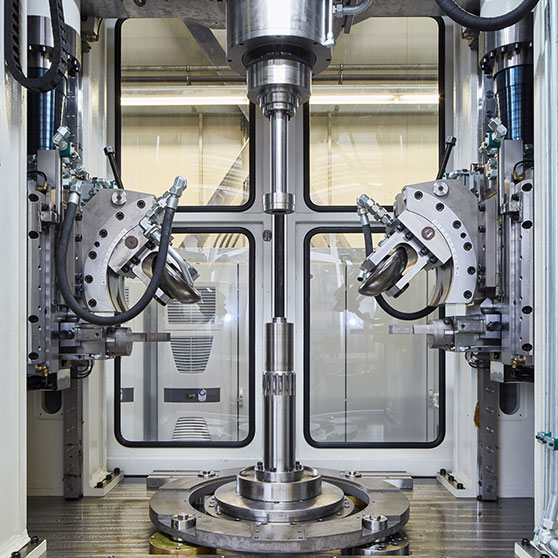
The Vertical End Forming Spinning Machine is a specialized piece of equipment designed to carry out precise metal forming operations on the ends of tubular or cylindrical workpieces in a vertical orientation. This configuration provides unique advantages for forming applications that require gravity-assisted loading, improved alignment, or compact machine footprints. Unlike horizontal spinning systems, the vertical setup naturally centers and supports the workpiece, which is particularly beneficial when working with long or large-diameter tubes that could otherwise sag or deflect under their own weight.
This type of spinning machine excels in applications where end flaring, necking, beading, curling, or closing is required, especially for components such as gas cylinders, automotive exhaust systems, refrigeration tubes, rocket motor casings, or high-pressure vessels. The vertical positioning enhances accessibility and tooling flexibility, enabling the machine to perform multiple forming actions in sequence or in combination, such as reducing and flaring a pipe end in a single cycle. This not only boosts productivity but also improves dimensional consistency and reduces the need for post-forming machining or welding.
The spinning process in a vertical end forming machine typically involves the rotation of the workpiece around its vertical axis while forming rollers or tools apply controlled pressure at specific positions to shape the end geometry. The tooling is usually servo-controlled and can operate along multiple axes, enabling complex profiles to be achieved with high repeatability. With CNC integration, operators can program exact forming paths, speeds, and pressures, which is essential for working with materials such as stainless steel, aluminum, titanium, or nickel alloys that require tightly controlled deformation to maintain mechanical properties.
In many configurations, vertical end forming spinning machines are equipped with automated loading/unloading systems, including lift tables, robotic arms, or gravity chutes, allowing for continuous and unattended operation. This is especially useful in high-volume manufacturing environments where speed and consistency are critical. Integrated clamping and centering systems further reduce setup times and ensure perfect alignment of the tube or shell before forming begins. For safety and quality assurance, modern systems also include sensor arrays, vision systems, and force feedback controls that monitor every forming cycle in real-time, ensuring defects are detected and addressed immediately.
The vertical orientation also aids in the management of debris and coolant, as gravity naturally directs material shavings or excess lubricants away from the work zone, maintaining a cleaner and more controlled forming environment. This is important for maintaining tool longevity and minimizing contamination in industries with stringent cleanliness requirements, such as food processing, medical equipment, or semiconductor component manufacturing.
With growing emphasis on lightweight structures and fluid efficiency in industries like HVAC, automotive, and aerospace, the ability to create smooth, optimized flow transitions and joint-ready ends is becoming increasingly valuable. Vertical end forming spinning machines support this demand by enabling the creation of aerodynamic and fluid-dynamic end shapes with minimal wall thinning and superior surface finish. Additionally, by eliminating the need for multiple forming stages or component welding, these machines contribute to both cost reduction and mechanical performance improvement.
As manufacturing continues to prioritize lean production and digital connectivity, vertical end forming spinning machines are being integrated into Industry 4.0 environments. They are capable of real-time data exchange with other equipment, adaptive process control based on material batch properties, and cloud-based monitoring for predictive maintenance and quality control. These capabilities help manufacturers maximize uptime, reduce waste, and achieve higher levels of traceability across the production process.
In summary, the Vertical End Forming Spinning Machine is a vital solution for precision forming of tubular components, offering unmatched accuracy, repeatability, and process flexibility in a vertically oriented platform. Its ability to form complex, functional end geometries in a compact footprint, combined with advanced automation and digital control systems, makes it an ideal choice for modern manufacturers looking to streamline production while maintaining the highest quality standards.
The ongoing development of vertical end forming spinning machines reflects broader trends in manufacturing technology, especially the push toward multi-functionality and modularity. Many modern machines are now built with interchangeable tooling heads and reconfigurable stations, allowing a single unit to perform a range of end forming tasks—such as tapering, doming, swaging, threading preparation, or forming tight-radius flanges—without requiring a full machine changeover. This adaptability supports small-batch or custom production just as effectively as high-volume runs, making the equipment suitable for a wider spectrum of manufacturers, from specialized component shops to integrated OEM production lines.
Another key advantage of vertical orientation is the ability to easily handle heavier or longer workpieces. In contrast to horizontal systems, where large tubes must be supported along their length to prevent deflection or vibration during rotation, vertical machines use gravity to maintain concentricity and reduce mechanical strain on bearings and drives. This translates to better forming accuracy and longer machine lifespan, especially when working with high-strength or thick-walled materials. It also simplifies loading processes, as operators or automated systems can lower workpieces directly onto the spindle without the need for complex alignment jigs or fixtures.
The structural design of vertical end forming spinning machines also enhances rigidity and minimizes the impact of external vibrations, which is critical when forming precision end features such as sealing faces, gasket seats, or threaded segments. These features often require exact tolerances to ensure leak-free performance or proper mechanical mating, particularly in components used for gas or fluid transfer under pressure. In sectors like chemical processing, hydraulic systems, and energy infrastructure, the ability to produce such features with minimal post-processing greatly enhances production efficiency and part reliability.
On the automation front, vertical end forming spinning machines are increasingly equipped with advanced human-machine interfaces that allow operators to visually simulate forming sequences, track tool wear, and adjust cycle parameters with intuitive touchscreen controls. These systems reduce the learning curve for operators while providing the data-rich environment needed for continuous improvement initiatives like Six Sigma or total productive maintenance. In environments where traceability is essential, machines can log process data per part, linking each component’s history to specific forming parameters and material lots.
Vertical spinning also supports hybrid processes where traditional spinning is combined with localized heating methods such as induction or resistance heating. This is particularly useful for forming hard or work-hardened alloys, where heat-assisted forming reduces tool wear and improves formability without compromising structural integrity. By precisely controlling the heat zone and combining it with synchronized pressure application, manufacturers can achieve complex geometries and maintain fine-grain microstructures, which are critical in fatigue-sensitive or pressure-critical applications.
Environmental considerations are also being addressed in newer machine models. Energy-efficient drives, regenerative braking systems, and closed-loop coolant management are standard in high-end vertical spinning setups, helping to reduce energy consumption and operational costs. Moreover, by minimizing material scrap and allowing near-net shape forming, these machines align with sustainability goals and material efficiency metrics, especially when processing expensive or rare metals.
From a broader perspective, the vertical end forming spinning machine embodies the fusion of mechanical innovation and digital intelligence. As industries seek to increase resilience, flexibility, and sustainability in their supply chains, such machines offer a pathway to decentralized, high-precision production that is scalable and adaptive. Whether forming ends on small refrigeration tubes or large pressure tank shells, the vertical system delivers consistent, repeatable results across a wide range of part sizes and material types. It is an enabling technology for any manufacturer seeking to optimize performance, reduce costs, and future-proof their forming capabilities in an increasingly competitive and fast-changing market.
As the demand for high-performance parts continues to rise in industries such as aerospace, automotive, energy, and medical devices, the vertical end forming spinning machine’s capabilities are becoming more critical. The continued evolution of materials science, particularly in areas such as composites, high-strength alloys, and superalloys, has led to increasingly complex geometries being required for end forming. These materials often present significant challenges, such as lower formability, increased hardness, or susceptibility to cracking under stress. The precision, control, and adaptability of vertical end forming spinning machines are essential in overcoming these challenges. By fine-tuning the application of pressure, rotational speed, and forming path, manufacturers can shape even the most difficult materials without compromising their mechanical properties.
Additionally, as part designs become more intricate, the need for integrated inspection systems is growing. Many vertical end forming spinning machines are now being equipped with on-the-fly measurement technologies, including laser profilometers, ultrasound sensors, and in-situ vision systems. These sensors track dimensional changes during the forming process, ensuring that the final part meets strict tolerances. Real-time feedback loops allow operators to make immediate adjustments to the process, whether it’s altering speed, pressure, or tool position. This level of process monitoring and control ensures that even complex parts can be produced with a high degree of consistency across large production runs. This integration also provides an opportunity to collect data for further analysis, supporting continuous process improvements and meeting the demands for greater product quality and compliance in industries with stringent regulatory standards.
The ability to form parts with intricate shapes and thin walls is also driving the use of vertical end forming machines in lightweighting applications. In industries like electric vehicles (EVs) and renewable energy, there’s an increasing demand for components that are both strong and light, such as structural supports, housings, and exhaust systems. These components often need complex end geometries that maximize structural integrity while minimizing weight. Vertical end forming spinning machines can achieve these delicate balance requirements by reducing material waste and optimizing part geometry in a way that traditional processes like machining or casting cannot.
Furthermore, as industries push for faster production cycles to keep up with market demands, vertical end forming spinning machines are being optimized for rapid changeovers and high uptime. The ability to adjust tooling and process parameters quickly, combined with automated loading/unloading and advanced process control, allows manufacturers to shift between different part designs and sizes without significant delays. This flexibility is crucial in industries where small-batch runs, customizations, and prototypes are becoming more common. Vertical end forming spinning machines help reduce lead times, making it easier for manufacturers to respond to customer requirements quickly and efficiently.
Another noteworthy aspect of vertical end forming spinning machines is their role in reducing the number of secondary operations required for finished parts. Since these machines are capable of achieving near-net shape or fully functional geometries with smooth finishes, the need for subsequent processes like welding, trimming, or machining is significantly minimized. This not only saves time and labor but also ensures that part integrity is maintained, especially in critical applications where post-processing could introduce weaknesses or defects.
As additive manufacturing technologies continue to mature, vertical end forming spinning machines are beginning to be used in tandem with 3D printing to produce hybrid parts that leverage the strengths of both technologies. For example, 3D printing can be used to create complex internal structures or customized tool geometries, while vertical end forming machines provide the precision and surface finish required for functional external geometries. This convergence of technologies enables the production of parts with superior properties—strength, weight, and performance—by combining the best of both worlds.
Looking ahead, the vertical end forming spinning machine is likely to continue its integration with robotics and artificial intelligence. AI-driven systems can predict potential forming issues based on material characteristics, part geometry, and real-time process data. These systems can also make decisions about optimal forming strategies in real time, reducing operator intervention and human error. Meanwhile, robots can handle tasks like part handling, tool changeovers, and quality inspection, ensuring that these machines operate at maximum efficiency and throughput while maintaining high levels of accuracy.
The combination of increased automation, advanced monitoring, and process control, alongside its core ability to form parts with high precision, positions the vertical end forming spinning machine as a critical tool in the future of precision manufacturing. As industries continue to demand better-performing, lighter, and more complex components, this machine will continue to evolve to meet those needs, ensuring manufacturers have the flexibility, speed, and accuracy to stay ahead of competition and deliver cutting-edge solutions to a range of industries.
Large-Diameter CNC Spinning Machine
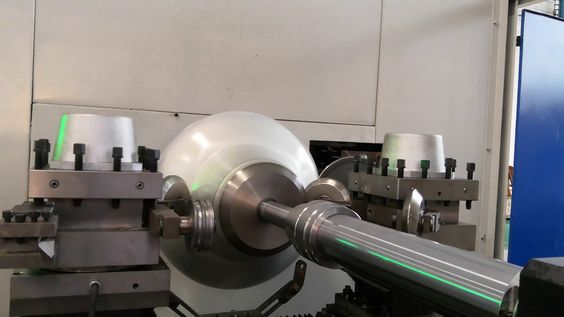
The Large-Diameter CNC Spinning Machine is a highly specialized piece of equipment designed to form large-scale metal components, often used in industries like aerospace, automotive, energy, and heavy manufacturing. These machines are capable of handling larger workpieces, such as large pipes, tubes, domes, and complex conical or spherical shapes, with precision and high repeatability. Their design focuses on achieving accurate geometries, smooth finishes, and material consistency across large parts, which are typically challenging to produce using traditional methods.
One of the defining features of a large-diameter CNC spinning machine is its ability to handle significant workpiece diameters—often ranging from 1 meter (3 feet) to over 10 meters (30 feet) in some configurations. This makes them essential for the production of parts such as pressure vessels, wind turbine components, large tank shells, rocket casings, and aerospace panels, all of which require both large dimensions and high structural integrity. These machines are equipped with robust, heavy-duty frames and powerful spindles capable of rotating large parts at varying speeds to achieve optimal material flow during the spinning process.
The CNC (Computer Numerical Control) aspect of these machines introduces a high degree of automation, precision, and flexibility. CNC systems enable the operator to program the exact path of the forming tool, the rotational speed of the workpiece, and the pressure applied by the rollers or other forming tools. This allows for complex geometries to be created with ease, whether it’s forming large-radius curves, tapered sections, or intricate profiles with thin walls and minimal distortion. The software-driven nature of CNC spinning machines makes them far more adaptable than their manual counterparts, capable of running multiple different part types with minimal setup changes, even for low-volume or custom orders.
A key benefit of CNC-controlled large-diameter spinning machines is their material efficiency. The process can achieve near-net shape forming, meaning that the workpiece is shaped with little to no waste material. This is particularly valuable when working with expensive or hard-to-machine materials like titanium, high-strength steel, or superalloys. The process eliminates the need for secondary operations like machining, welding, or grinding, reducing both production costs and lead times. By forming components directly from blanks, manufacturers can create complex shapes with minimal post-processing, reducing the likelihood of defects and increasing part strength.
Another significant advantage of large-diameter CNC spinning machines is their ability to form materials that are difficult to handle using other methods. Materials such as aluminum, copper, stainless steel, and high-temperature alloys can be spun without cracking, tearing, or inducing residual stresses—thanks to the precise control over tool movement and pressure application. This is especially beneficial for industries like aerospace, where high-performance parts need to meet stringent material properties and surface finishes.
In terms of automation, large-diameter CNC spinning machines often come with advanced features like automatic tool changers, robotic loaders and unloaders, and real-time monitoring systems. Automated tool changers allow for quick adjustments between different tool heads or rollers, which is important for reducing downtime during job changeovers. Robotic arms can load and unload large or heavy parts with precision, eliminating the need for manual handling and reducing the risk of injury. Real-time process monitoring ensures that the workpiece remains within the specified tolerances throughout the forming cycle, and sensors can detect variations in material behavior, tool wear, or any irregularities that might affect part quality. This integration helps improve operational efficiency and ensures a higher level of part quality and consistency.
Furthermore, precision control over the forming process is one of the key benefits of CNC spinning machines. The ability to adjust parameters such as rotational speed, roller position, and forming pressure in real-time provides a level of control over the material flow that would be difficult or impossible to achieve manually. This precision is crucial when working with large-diameter components where even small deviations in process parameters can lead to significant discrepancies in the final product, especially in highly engineered applications like rocket boosters or large industrial piping.
The integration of CAD/CAM software with CNC spinning machines also streamlines the process from design to production. Designers can directly input 3D models into the CNC system, which generates the necessary tool paths for forming the part. This digital workflow ensures that the transition from design to manufacturing is seamless, reduces human error, and improves overall production speed. Additionally, CNC software can simulate the forming process before actual production begins, allowing for any potential issues to be addressed early in the design phase. This significantly reduces the likelihood of costly mistakes or material wastage during the manufacturing process.
When it comes to production scale, large-diameter CNC spinning machines can be used for both high-volume manufacturing and low-volume, custom, or prototype production. In industries such as aerospace or defense, where low-volume, high-complexity components are often required, these machines provide a flexible, efficient solution. The ability to produce highly accurate prototypes or custom parts without the need for specialized tooling makes CNC spinning machines ideal for the rapid iteration cycles often needed in these sectors.
Energy efficiency is also an important consideration in modern large-diameter CNC spinning machines. Many machines now feature servo motors, regenerative braking systems, and energy-saving drives, which optimize power consumption during operation. These technologies not only help reduce operational costs but also make the machines more sustainable by minimizing their carbon footprint. Furthermore, some machines are equipped with closed-loop cooling systems that reduce waste and ensure a consistent operating temperature, which is essential for maintaining the quality of the final parts.
The flexibility, precision, and efficiency of large-diameter CNC spinning machines make them indispensable for manufacturers dealing with large-scale, high-performance components. As industries continue to push the boundaries of what’s possible in materials, part geometries, and performance specifications, these machines will be central to producing the next generation of advanced components—whether it’s in the aerospace industry, where lightweight, high-strength parts are needed for airframes and propulsion systems, or in energy sectors, where robust and durable components are critical for turbines and power generation systems.
In summary, large-diameter CNC spinning machines offer exceptional capabilities for forming large, complex components with precision and efficiency. With advancements in automation, digital control, and material handling, these machines are becoming even more versatile and integral to the production of critical parts in industries that demand high strength, performance, and material integrity. As technological improvements continue to emerge, these machines will remain a cornerstone of modern manufacturing, enabling manufacturers to meet the evolving challenges of tomorrow’s advanced part designs.
As large-diameter CNC spinning machines continue to evolve, there’s a growing trend toward further integration with digital technologies, automation, and smart manufacturing systems. One of the key developments is the increasing use of predictive maintenance and remote diagnostics. These technologies leverage sensors and real-time data analytics to monitor machine conditions and predict when maintenance is needed before a failure occurs. By analyzing vibration, temperature, pressure, and other critical parameters, manufacturers can avoid costly downtime, extend the lifespan of their machines, and ensure that production schedules are maintained. Additionally, cloud-based monitoring enables operators to access performance data from anywhere, making it easier to manage multiple machines across different locations or production facilities.
The rise of Industry 4.0 technologies has also impacted large-diameter CNC spinning machines. With the integration of IoT (Internet of Things) devices, these machines can now communicate with other machines and systems in a smart factory environment. This connectivity allows for optimized workflow management, with real-time adjustments to production schedules based on data from other parts of the factory. For example, a large-diameter CNC spinning machine could receive signals from upstream processes, such as laser cutting or tube bending operations, to adjust its speed or tooling requirements to match the material and dimensions being worked on. This level of coordination enhances overall efficiency, minimizes waste, and streamlines production timelines.
As industries shift toward more sustainable manufacturing practices, large-diameter CNC spinning machines are also becoming more environmentally friendly. Manufacturers are placing greater emphasis on reducing energy consumption, minimizing material waste, and recycling or reusing scrap material. Modern CNC spinning machines often incorporate closed-loop systems that manage coolant usage efficiently, servo-driven motors that optimize power consumption, and energy-efficient lighting and other components to minimize environmental impact. These features are particularly important for industries like aerospace, automotive, and renewable energy, where regulatory pressures and the need for green manufacturing practices are pushing companies to adopt more sustainable production methods.
The ability of these machines to produce high-precision parts with minimal waste is especially beneficial for industries focused on lightweighting. As companies look for ways to reduce the weight of components—whether in aerospace, automotive, or renewable energy applications—the precision offered by CNC spinning machines is crucial. By using these machines, manufacturers can create components with complex geometries that are both lightweight and strong, without compromising structural integrity. This is particularly relevant in industries like electric vehicles, where reducing weight is directly tied to improving energy efficiency and performance.
Additionally, the trend toward customization and rapid prototyping in many sectors is benefiting from the capabilities of large-diameter CNC spinning machines. These machines are increasingly being used in smaller production runs, where customization is key, whether it’s for prototypes, limited-edition products, or unique designs. The flexibility of CNC systems allows for quick adjustments to machine settings, which is perfect for industries requiring tailor-made parts with specific characteristics or dimensions. For example, in the aerospace industry, prototypes for components like fuel tanks, airframe sections, or fuselage skins often need to be formed with unique specifications. CNC spinning machines can produce these parts efficiently and accurately, even in small batches, without the need for expensive, time-consuming tooling changes.
Looking to the future, AI and machine learning are set to play a larger role in the operation of large-diameter CNC spinning machines. These technologies can be used to analyze historical production data, identify patterns, and optimize processes automatically. For instance, AI algorithms could adjust spinning parameters in real-time based on the material properties of each workpiece, ensuring that the forming process is always optimized for the best possible result. Machine learning could also be used to analyze past part designs and suggest improvements to increase efficiency, reduce material consumption, or enhance part strength.
Another exciting development is the potential integration of additive manufacturing (3D printing) with large-diameter CNC spinning. While spinning machines excel at forming complex shapes from solid metal blanks, additive manufacturing technologies are well-suited for creating intricate internal structures or customized tooling. Combining the two could lead to the development of hybrid production systems, where parts are both spun and 3D printed, resulting in components that are not only high-performance but also optimized for specific requirements in terms of weight, strength, and functionality.
The growing demand for high-precision, large-diameter components in industries like wind energy, nuclear power, and transportation is driving innovation in CNC spinning technology. As these industries continue to evolve, the need for components that meet stringent safety, performance, and durability standards will only increase. Large-diameter CNC spinning machines will play a crucial role in meeting these demands, ensuring that manufacturers can produce large, complex parts with the necessary properties for critical applications. Whether it’s producing the shell of a large pressure vessel or a specialized aerospace component, these machines offer the precision, efficiency, and flexibility needed to meet the challenges of the future.
In conclusion, large-diameter CNC spinning machines are at the forefront of modern manufacturing, providing high precision, flexibility, and efficiency for the production of complex, large-scale components. As technology continues to advance, these machines will evolve to incorporate smarter, more sustainable, and more efficient features, enabling manufacturers to meet the demands of industries that require cutting-edge performance, customized solutions, and rapid production timelines. With their ability to handle large parts with precision, reduce material waste, and integrate with other manufacturing processes, large-diameter CNC spinning machines will continue to be an essential tool in high-performance industries worldwide.
Looking forward, the future of large-diameter CNC spinning machines will likely be shaped by advancements in automation and robotics. As production facilities become more automated, the role of human operators may shift from direct machine control to overseeing and maintaining automated systems. Robotic systems will likely take on more of the material handling, tool changing, and part inspection tasks. For example, robotic arms can load and unload large parts into spinning machines with extreme precision, reducing the risk of human error and increasing throughput. By automating these tasks, manufacturers can not only speed up the production process but also improve the safety and ergonomics of the workplace by reducing the need for workers to handle heavy or hazardous materials.
The integration of smart manufacturing systems will also enable large-diameter CNC spinning machines to interact with other machines on the production floor. This interconnected environment will provide real-time data exchange, allowing for seamless communication between different types of equipment, such as CNC machines, 3D printers, and machining centers. By combining data from various sources, manufacturers can optimize their operations, increase overall efficiency, and achieve better synchronization between different production stages. This ability to monitor and adjust all aspects of production from a centralized platform is a key feature of Industry 4.0 and will likely become more prevalent as large-diameter CNC spinning machines evolve.
Another area where large-diameter CNC spinning machines will continue to see improvement is data analytics and process optimization. As more data is collected from machine sensors, operators will be able to analyze trends, identify potential issues before they become critical, and make real-time adjustments to improve the quality and consistency of parts. The integration of advanced machine learning algorithms will allow for adaptive process control, where the machine can “learn” from past production runs and adjust its settings accordingly. This will further improve part quality, reduce cycle times, and minimize material waste.
In terms of material diversity, large-diameter CNC spinning machines will also likely be designed to work with an even wider range of materials in the future. The demand for high-performance parts is pushing manufacturers to experiment with more advanced materials, including composite metals, alloy blends, and new high-strength, lightweight materials. Spinning machines will need to be adaptable to handle the unique characteristics of these materials, whether it’s high-temperature resistance, corrosion resistance, or flexibility. The integration of advanced sensors and material-specific programming will enable machines to optimize their forming processes based on the material’s properties, ensuring the highest quality result with minimal waste.
Sustainability will continue to play a significant role in the design and operation of large-diameter CNC spinning machines. The growing emphasis on circular manufacturing—where materials are reused and recycled in the production process—will likely influence the way these machines operate. CNC machines could be equipped with features that allow them to handle recycled or repurposed materials efficiently, further reducing the environmental impact of production. For instance, some machines might incorporate material sorting systems or work in tandem with closed-loop recycling systems to ensure that waste material is reintroduced into the production cycle, minimizing scrap and reducing the need for new raw materials.
The integration of advanced simulation and virtual reality (VR) will also likely be a game-changer in the future of large-diameter CNC spinning machines. Before beginning production, manufacturers will be able to virtually simulate the entire spinning process, from material deformation to tool paths, ensuring that all parameters are set correctly. VR could also be used for training purposes, allowing operators to practice and refine their skills in a simulated environment before handling real parts. This kind of training, combined with the ability to run simulations for quality control, will ensure more precise setups and reduce errors during production runs.
As the trend toward customized, on-demand manufacturing grows, large-diameter CNC spinning machines will play a central role in the rapid prototyping and short-run manufacturing of complex parts. Industries like aerospace, defense, and automotive require components that are tailored to exact specifications, often in low volumes. The ability to produce such parts with high accuracy and minimal lead time is a competitive advantage, and CNC spinning machines provide the ideal solution for meeting these requirements. Their versatility allows manufacturers to switch between different part types quickly, adapting to customer needs without compromising quality or production speed.
Finally, globalization will continue to drive demand for high-performance manufacturing equipment that can operate in a variety of environments and meet the needs of diverse industries. Large-diameter CNC spinning machines are essential for the production of critical components used in industries that span the globe, from wind energy farms in Europe to high-speed rail systems in Asia. The ability to scale production quickly and meet international standards for safety and quality will make these machines indispensable as global supply chains continue to expand.
In conclusion, the future of large-diameter CNC spinning machines is poised for exciting advancements driven by automation, connectivity, AI, and material innovation. These machines will continue to evolve to meet the increasing demands for precision, efficiency, and sustainability across a wide range of industries. As manufacturers embrace new technologies and adapt to shifting market needs, large-diameter CNC spinning machines will remain a cornerstone of modern manufacturing, enabling the production of complex, high-performance components that drive progress in aerospace, automotive, energy, and beyond.
High Performance Spinning Necking Machine
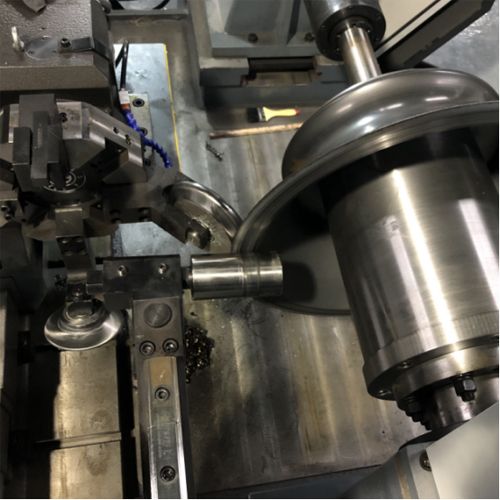
The High Performance Spinning Necking Machine is a specialized type of metal forming machine designed for shaping the neck or flange area of cylindrical or conical parts. This machine is often used in industries like aerospace, automotive, and pressure vessel manufacturing, where precise and consistent necking of large metal components is required. The process involves reducing the diameter of a section of a workpiece while maintaining its structural integrity, typically creating a tapered or necked-down region for further processing or for fitting into other components.
A key feature of high-performance spinning necking machines is their ability to handle high-tensile materials such as stainless steel, aluminum alloys, and titanium, which are commonly used in applications that require strength and durability. The necking operation can be performed on a variety of parts, including pressure vessels, tanks, exhaust systems, automotive parts, and aerospace components, which need to be designed with specific geometries and properties to meet stringent engineering standards.
The machine utilizes a rotating workpiece that is gradually deformed by applying pressure with a tool, typically referred to as a forming roller or spinning tool. This tool shapes the material by pushing it into a mandrel or die, which serves as a guide to ensure that the neck or flange area is formed with high precision. The use of a CNC (Computer Numerical Control) system allows operators to program the exact parameters of the operation, including the tool path, spindle speed, pressure applied, and material feed rate, enabling highly repeatable and accurate results. The CNC control also allows for easy adjustments to accommodate different part designs and materials, making the machine adaptable for both small and large production runs.
One of the standout features of high-performance spinning necking machines is their ability to perform the necking operation with minimal material waste. The spinning process is often referred to as a near-net-shape technique, where the final component is formed close to the desired dimensions, significantly reducing the need for post-processing like machining, welding, or trimming. This not only results in cost savings but also ensures the material maintains its integrity and strength, which is particularly important when dealing with materials that are difficult or expensive to machine.
These machines are equipped with powerful servo motors and hydraulic systems that provide precise control over the force applied during the necking process. This is essential for achieving consistent wall thickness and minimizing defects such as cracking, warping, or material tearing, which can occur when the material is not properly controlled. Additionally, advanced cooling systems are often integrated into the machine to maintain optimal working temperatures, particularly when forming high-strength materials, ensuring that the part is not damaged by excessive heat buildup.
In industries where tight tolerances are critical, such as aerospace or medical device manufacturing, high-performance spinning necking machines offer a solution to produce parts with exceptional accuracy. The combination of high precision and the ability to process difficult materials makes them essential in the production of critical components like fuel tanks, reactor vessels, turbine casings, and specialized aerospace parts, all of which must meet rigorous specifications.
Moreover, these machines can be configured for multi-stage necking operations, where the necking process is performed in stages to reduce material deformation and ensure uniformity. This is particularly useful for parts that require a gradual transition between different diameters or require multiple reductions in size, such as those used in the manufacture of large industrial pipes or automotive components with flanges.
In terms of automation and efficiency, high-performance spinning necking machines are often integrated with robotic handling systems for loading and unloading parts. This integration minimizes human intervention, reduces labor costs, and improves safety in the workplace. Automated systems also contribute to increased production throughput by ensuring that parts are consistently handled and processed at high speeds, without sacrificing quality or accuracy.
As industries continue to push the boundaries of material science and design, the high-performance spinning necking machine will evolve to meet the growing demands for even higher precision, speed, and material versatility. Smart manufacturing technologies, including the use of AI-driven process optimization, will likely be integrated into these machines to further enhance performance. Machine learning algorithms could monitor production in real-time, adjusting process parameters to optimize material flow and reduce defects. Predictive maintenance systems could also be implemented to monitor the health of machine components, minimizing downtime and ensuring continuous, efficient operation.
Looking to the future, there is also the potential for the integration of hybrid manufacturing processes, combining spinning with additive manufacturing (3D printing) to produce parts with more complex internal geometries or tailored properties. This would allow manufacturers to create components with internal structures optimized for strength, weight, or performance, while still benefiting from the high precision and material efficiency of the spinning necking process.
In conclusion, the high-performance spinning necking machine is an essential tool for industries that require precise, high-quality necking operations on large or complex parts. Its ability to form high-strength materials, reduce material waste, and produce parts with tight tolerances makes it indispensable in sectors like aerospace, automotive, and pressure vessel manufacturing. As technology advances, these machines will continue to evolve, integrating smart technologies and automation to improve efficiency, flexibility, and precision in metal forming operations.
The high-performance spinning necking machine is a key player in advanced metal forming processes, offering exceptional precision and material efficiency. These machines are particularly beneficial for industries that require tight tolerances and high-strength materials. The ability to process a variety of metals, including stainless steel, aluminum alloys, and titanium, allows manufacturers to meet the strict demands of sectors like aerospace, automotive, and energy production. By leveraging the principles of spinning, the machine reduces the need for traditional machining, which often generates significant waste, making it both cost-effective and environmentally friendly. The ability to handle difficult materials, such as high-tensile alloys, without compromising their integrity further emphasizes the importance of this machine in precision manufacturing. As industries push for more customized and complex parts, the need for machines that can deliver such high levels of precision and adaptability becomes even more crucial.
In the future, the integration of robotic systems will likely become even more common, allowing for fully automated operations, from material handling to part inspection. This shift toward complete automation will help streamline production, increase speed, and reduce human error, which is especially important in high-stakes manufacturing environments where part defects can result in costly delays or safety hazards. Additionally, the use of IoT (Internet of Things) technology will allow for real-time monitoring of machine performance, offering data that can be analyzed to predict maintenance needs, reduce downtime, and enhance overall machine reliability.
As technology continues to advance, smart materials could be used more frequently, allowing these machines to work with previously unmanageable materials or to create components that perform better under extreme conditions. For example, future iterations of the spinning necking machine may be able to handle composite materials or new metal alloys that require even higher levels of control and precision during the forming process. This capability would further expand the range of applications for the machine, making it even more versatile and valuable in industries where innovation is key.
Sustainability efforts will continue to shape the future of high-performance spinning necking machines. As the demand for more sustainable manufacturing practices grows, these machines will likely incorporate energy-efficient technologies, such as regenerative drives or advanced cooling systems, to minimize energy consumption during production. Moreover, closed-loop systems could be implemented to recycle coolant and lubricants, further reducing the environmental footprint of the manufacturing process. The ability to incorporate more sustainable practices while maintaining high precision will allow manufacturers to meet both the economic and environmental challenges of the future.
In conclusion, the high-performance spinning necking machine represents a blend of tradition and innovation in the manufacturing world. With its ability to deliver precise, high-quality parts while reducing material waste and energy consumption, it will continue to be a cornerstone of industries that require complex metal forming. As manufacturers embrace digitalization, automation, and smarter technologies, the capabilities of these machines will only expand, enabling them to meet the evolving demands of a fast-paced, precision-driven world.
Looking ahead, the role of high-performance spinning necking machines in manufacturing will likely continue to evolve, driven by advancements in digital technologies and process automation. As industries demand faster production cycles with increasingly customized products, these machines will become more integral in responding to these needs. The integration of machine learning and artificial intelligence will be a key factor in the machine’s ability to adapt to new challenges. For instance, AI algorithms could analyze data from previous runs and adjust parameters in real-time to optimize the necking process, ensuring consistent quality while reducing the likelihood of defects. Such adaptive capabilities will enhance the machine’s ability to handle more complex materials and geometries, making it even more versatile across different industries.
The cloud-based monitoring of high-performance spinning necking machines will also become more commonplace, allowing operators to remotely track machine performance, monitor part quality, and even adjust machine settings from virtually anywhere. This capability not only enhances the convenience of machine operation but also helps in predictive maintenance, as real-time data can alert operators to potential issues before they result in costly downtime or production delays. The ease of accessing this data will also empower manufacturers to improve operational efficiency across multiple locations or global production networks, supporting their quest for lean manufacturing and cost optimization.
As global supply chains become more complex, the demand for flexible manufacturing systems that can quickly adapt to different product specifications will increase. High-performance spinning necking machines, with their precise control systems and ability to process a variety of materials, will become essential in this context. For example, industries like aerospace and automotive may require frequent changes in part designs due to evolving regulations or customer preferences. In such cases, a machine that can easily be reprogrammed for new part geometries and materials will provide manufacturers with the flexibility they need to stay competitive in a rapidly changing marketplace.
The emergence of additive manufacturing (3D printing) in combination with traditional processes like spinning necking will also likely open new possibilities for creating hybrid parts. For instance, certain internal geometries that were previously difficult or expensive to produce using traditional spinning processes could now be created using 3D printing, while the external shape and necking features could be formed using the spinning machine. This combination of technologies could result in parts with complex structures and optimized material properties that are lightweight yet strong, further pushing the boundaries of what is possible in industries such as aerospace, automotive, and energy production.
As regulatory pressures on sustainability and resource efficiency intensify, high-performance spinning necking machines will also play a pivotal role in supporting circular economy principles. These machines are already effective at minimizing waste, but future innovations could further reduce the environmental impact of the manufacturing process. Closed-loop systems that recycle materials, as well as the ability to work with recycled metals, will likely be implemented in future models, allowing manufacturers to reuse materials more efficiently. Moreover, these machines could potentially incorporate energy-harvesting technologies, which could convert waste energy from the spinning process into usable power, further enhancing their sustainability credentials.
In addition, the need for highly customized components in a wide variety of industries will increase as more products become specialized or demand shorter product life cycles. The spinning necking machine’s ability to produce parts with precise geometries, including customized necking features for unique fits and connections, will make it an essential tool in creating these specialized products. Whether it’s a one-off part for a bespoke project or a small production run for a niche market, these machines will provide the flexibility and precision required for such custom work. In the automotive sector, for example, manufacturers could use the machines to produce specialized exhaust components, tank parts, or structural elements, all tailored to specific requirements.
Another exciting development is the potential for in-situ quality control. While conventional inspection methods often rely on post-process testing, advanced spinning necking machines could integrate real-time inspection systems, such as laser scanning or 3D vision systems, to ensure that each part meets stringent quality standards as it is being formed. These in-process quality control systems would immediately detect deviations from the desired geometry or material properties, allowing for adjustments to be made in real-time, which would significantly reduce scrap rates and improve part consistency. This integration would be particularly beneficial in industries that deal with high-precision parts, such as the aerospace and medical device sectors.
As cybersecurity becomes a growing concern in the industrial sector, future high-performance spinning necking machines will likely incorporate enhanced security protocols to protect sensitive production data. These protocols would safeguard against unauthorized access to machine control systems and ensure that operational data is protected from tampering. As more machines become connected to cloud-based platforms and share data across networks, the need for robust cybersecurity measures will become even more critical in maintaining the integrity of the manufacturing process.
In summary, the future of high-performance spinning necking machines is closely tied to ongoing developments in automation, digitalization, and sustainable manufacturing practices. As industries continue to demand more precise, efficient, and adaptable manufacturing solutions, these machines will remain at the forefront, evolving to meet the challenges of new materials, complex geometries, and increasingly customized production requirements. Through advancements in machine learning, AI, robotics, and additive manufacturing, high-performance spinning necking machines will continue to play a pivotal role in creating high-quality components while reducing waste, improving efficiency, and supporting sustainability goals.
Forging Wheel Forming Machine
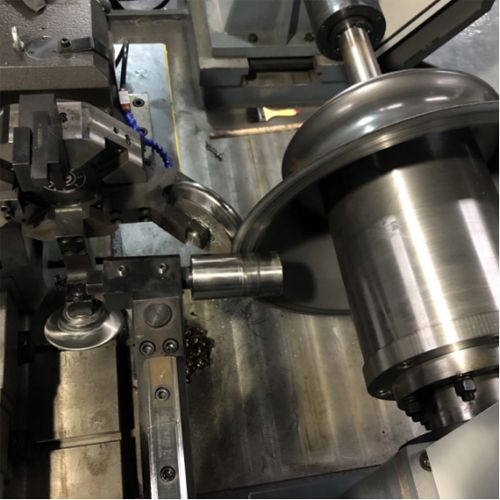
A Forging Wheel Forming Machine is a specialized piece of equipment used in the manufacturing of forged wheels, which are commonly used in industries such as automotive, aerospace, and railroad, as well as for heavy machinery and off-road vehicles. The machine is designed to produce high-strength, durable wheels by applying high-pressure forces to a heated billet of metal, causing it to deform and take the shape of a wheel. This forging process creates a stronger, more resilient part compared to casting or machining, which is critical for wheel applications that must endure high levels of stress and wear.
The primary function of a forging wheel forming machine is to shape a metal billet into a wheel by applying compressive force in a controlled environment. The process typically begins with heating the billet to a specific temperature, making the metal more malleable and easier to shape. The billet is then placed into the die or mold of the machine, and force is applied through a combination of hammering, pressing, or rolling to form the wheel shape. This process is known as closed-die forging, where the material is compressed into the desired form within a cavity.
There are a few variations of forging machines used for wheel production, including hammer-type forging machines, press-type forging machines, and roll-forging machines. Each type applies force in different ways but all rely on the principle of plastic deformation, where the material is reshaped under heat and pressure. In the case of the forging wheel forming machine, the focus is on ensuring that the wheel maintains the necessary strength and structural integrity to handle heavy loads and harsh environments.
The key advantage of forging over other forming processes, such as casting, lies in the resulting grain structure of the metal. During forging, the metal’s grain flow is aligned with the shape of the part, making the wheel stronger and more resistant to fatigue, cracking, and wear. This is especially important for wheels used in high-stress environments, such as those found in rail transport or heavy machinery, where the wheel needs to support significant weight while maintaining its shape over time.
In terms of the machine’s design, a Forging Wheel Forming Machine typically consists of several components:
- Heater: This component is responsible for heating the metal billet to the desired temperature before it is inserted into the die for forging.
- Die: The die is the mold that shapes the billet into the final form of the wheel. It may be custom-designed depending on the specifications of the wheel being produced.
- Forging Hammer or Press: This is the component that applies pressure to the billet, shaping it into the desired wheel form. Some machines use mechanical or hydraulic presses, while others use pneumatic or steam hammers.
- Cooling System: After the forging process, the part may be cooled to solidify the structure. Some machines have built-in cooling systems to ensure that the wheel maintains its properties as it cools.
- Ejector: Once the wheel is formed, it is removed from the die by an ejector mechanism, which ensures that the forged wheel can be safely retrieved without damaging the part.
The quality of the final forged wheel depends largely on several factors, including the temperature of the billet, the speed and force of the press or hammer, and the design of the die. Process control systems are often integrated into forging wheel forming machines to monitor and adjust these factors, ensuring that the parts meet the desired specifications.
Automation plays a significant role in modern forging wheel forming machines, enabling more precise control over the entire process. The use of CNC (Computer Numerical Control) systems in conjunction with robotic arms for handling billets and finished parts increases efficiency and reduces the need for manual intervention. Additionally, the integration of real-time monitoring and feedback loops allows for quicker detection of defects, such as cracks or material inconsistencies, enabling manufacturers to adjust the process before the defects become significant.
Forging wheel forming machines are also often integrated with heat treatment systems to enhance the mechanical properties of the forged wheels. Heat treatment processes such as quenching, tempering, or annealing are commonly used to further strengthen the wheel, increase its resistance to wear, and improve its overall performance. These processes can either be performed in separate furnaces or integrated directly into the forging system, depending on the complexity and production requirements.
As the demand for high-performance wheels continues to grow, especially in applications requiring lightweight yet durable parts, advanced materials and innovative forging techniques will shape the future of these machines. Alloy wheels, which offer improved strength-to-weight ratios, and the forging of composite materials are emerging areas where forging wheel forming machines may need to adapt in order to meet the requirements of next-generation vehicles and machinery.
In terms of sustainability, the forging process itself is energy-intensive, but ongoing developments in energy-efficient heating systems and automated material handling can help reduce energy consumption. The use of recycled materials, such as scrap metal, in the forging process also contributes to sustainability efforts by lowering the need for new raw materials.
In summary, the Forging Wheel Forming Machine is a critical piece of equipment used in producing high-strength, durable forged wheels. By utilizing advanced forging techniques and automation, these machines ensure that wheels meet the demanding requirements of industries where performance, safety, and reliability are paramount. As material science and manufacturing technologies continue to evolve, forging wheel forming machines will remain central to the production of high-quality, performance-driven wheels for a wide variety of applications.
Forging wheel forming machines are vital for the production of high-performance wheels used in sectors like automotive, aerospace, and heavy machinery. These machines rely on the principles of forging, a process that involves shaping metal through the application of heat and pressure, which results in a stronger, more durable product compared to other methods like casting. The high strength of forged wheels makes them ideal for environments where they must bear heavy loads and endure harsh conditions. The main advantage of forging is the alignment of the material’s grain structure, which improves the wheel’s resistance to cracking, fatigue, and wear. Forging ensures that the wheel will last longer and perform better under stress.
The process begins with heating the billet to a specific temperature, making it more malleable for shaping. The heated billet is then placed into the die of the forging machine, where force is applied to deform it into the shape of a wheel. This force is applied using different techniques, such as pressing, hammering, or rolling, depending on the machine’s design. The use of high-quality dies ensures that the forged wheel has the correct geometry and structural integrity.
Forging wheel forming machines are often equipped with several features that help ensure the consistency and quality of the final product. Heaters are used to bring the billet to the required temperature before it enters the die, while the dies themselves are meticulously designed to match the specifications of the wheel being produced. Forging presses or hammers apply the necessary force to shape the material, and cooling systems are in place to cool the forged part after the forming process, helping it maintain its strength and stability.
The production of forged wheels is often highly automated. With the use of CNC systems and robotic arms, manufacturers can ensure high precision and efficiency throughout the process. Automation also helps reduce human error, improving overall product consistency and reducing labor costs. Real-time monitoring allows for quick adjustments during production, ensuring the quality of each wheel and minimizing defects. The integration of heat treatment systems, such as quenching or tempering, can further enhance the mechanical properties of the forged wheels, making them more resilient to wear and tear.
In addition to increasing precision, automation and advanced control systems help reduce production time and costs. Modern forging wheel forming machines often incorporate smart technologies, such as IoT devices, which can monitor machine performance and detect issues before they lead to failures. These machines can also be equipped with systems that optimize the forging process based on real-time data, helping to reduce material waste and energy consumption.
As the demand for stronger, lighter, and more durable wheels continues to grow, particularly in industries like aerospace and high-performance automotive manufacturing, forging wheel forming machines are evolving to meet these new requirements. Advanced materials, including high-strength alloys and composite materials, are becoming more commonly used, and forging machines must be capable of handling these materials without compromising the wheel’s integrity. In addition, the shift towards more sustainable manufacturing processes is driving the adoption of recycled metals in the forging process, helping to reduce environmental impact.
In conclusion, the forging wheel forming machine is essential for producing high-strength wheels that meet the demanding standards of industries like automotive, aerospace, and heavy machinery. By utilizing advanced materials, precision engineering, and automation, these machines ensure that the final product is durable, lightweight, and capable of withstanding extreme conditions. As technologies continue to advance, these machines will likely become even more sophisticated, integrating new materials, processes, and automation systems to produce wheels that meet the evolving needs of the manufacturing world.
As we move toward the future, the continued advancement of forging wheel forming machines is expected to bring even more innovation, efficiency, and sustainability to the production of forged wheels. One of the key trends will likely be the integration of artificial intelligence (AI) and machine learning (ML) into the forging process. These technologies can enhance the precision of the machines by learning from historical data and adjusting parameters in real time to optimize the forging conditions. For example, the system could predict the optimal temperature for heating the billet, adjust the speed and force applied by the press, and even anticipate potential defects based on subtle variations in material properties or machine behavior.
Additionally, digital twins, which are virtual replicas of physical machines or processes, will play a significant role in improving the performance and efficiency of forging wheel forming machines. By creating a digital twin of the forging process, manufacturers can simulate and analyze different forging conditions before applying them in the real world. This allows them to test various scenarios, optimize machine settings, and identify potential issues without the risk of waste or defects in the physical product. These digital tools will be especially useful in the development of new products or the introduction of new materials, as they provide valuable insights without interrupting production.
Another exciting development is the potential use of robotic automation in material handling and part inspection. In addition to the robot arms that handle billets and forged parts, advanced robots with AI-driven vision systems could be used for in-line quality control. These robots would inspect each wheel during and after the forging process, identifying any defects or deviations from specifications. The ability to detect and correct issues in real-time would significantly reduce scrap rates, improve overall product quality, and shorten production cycles.
Sustainability will continue to be a major driving force in the evolution of forging wheel forming machines. Manufacturers are increasingly seeking ways to reduce their environmental footprint, and the forging industry is no exception. One promising approach is the use of energy-efficient heating systems, such as induction heating, which is more precise and energy-efficient compared to traditional furnaces. Induction heating allows for faster, more controlled heating of the billet, reducing energy consumption and improving overall process efficiency.
The adoption of closed-loop systems will also gain traction, allowing for the recycling of heat, energy, and even cooling fluids during the forging process. This will minimize the environmental impact of the process by reducing waste and improving resource efficiency. Additionally, there is an increasing focus on using recycled materials in forging, such as scrap metal, to reduce reliance on virgin raw materials. By improving the ability to handle recycled materials without compromising the quality of the finished product, forging wheel forming machines will contribute to the broader trend of circular manufacturing.
In terms of material science, new developments in advanced alloys and composite materials are pushing the boundaries of what is possible in wheel manufacturing. Materials such as titanium alloys, high-strength steels, and metal matrix composites are becoming more popular due to their superior properties, including high strength-to-weight ratios and resistance to corrosion. Forging wheel forming machines must evolve to handle these new materials, which may require adjustments to the forging parameters, die design, and even machine components to ensure the desired results. Furthermore, these materials often require specialized heat treatment processes, such as vacuum heat treatment, to achieve optimal mechanical properties, and the machines must be equipped to handle these advanced techniques.
The rise of smart factories and Industry 4.0 technologies will also impact the future of forging wheel forming machines. The integration of IoT sensors into the machines will enable real-time monitoring of machine performance, predictive maintenance, and remote diagnostics. By collecting data on factors such as temperature, pressure, and material flow, manufacturers can identify patterns that indicate potential issues before they cause downtime or defects. This will enable a more proactive approach to maintenance, reducing unplanned stoppages and improving machine longevity.
Moreover, the growing demand for customized and low-volume production will drive the need for more adaptable forging wheel forming machines. Traditional mass production methods may not be sufficient to meet the increasing need for specialized parts. Machines that can be easily reprogrammed or reconfigured for different wheel designs or material types will be essential in catering to this demand. Flexible manufacturing systems (FMS) that combine automation, robotics, and advanced software will provide manufacturers with the agility they need to respond to changing customer requirements and market trends.
As the focus on lightweighting increases in industries like automotive and aerospace, forging wheel forming machines will play a crucial role in producing wheels that not only meet performance requirements but also contribute to fuel efficiency and reduced emissions. Lighter wheels reduce the overall weight of vehicles, which can lead to significant improvements in fuel economy and overall vehicle performance. This trend will likely spur further innovation in materials and forging techniques, leading to the development of even lighter and stronger wheels.
In conclusion, the future of forging wheel forming machines is shaped by the convergence of advanced materials, digital technologies, automation, and sustainability initiatives. These machines will continue to evolve to meet the increasingly complex demands of industries that require high-performance wheels. With the integration of AI, robotics, and IoT technologies, forging wheel forming machines will become more precise, efficient, and adaptable, enabling manufacturers to produce higher-quality, more durable wheels at a lower cost and with a reduced environmental impact. The continued innovation in material science and manufacturing processes will ensure that these machines remain a cornerstone of modern manufacturing, supporting the production of wheels that meet the stringent requirements of tomorrow’s industries.
Ring Rolling Wheel Forming Machine
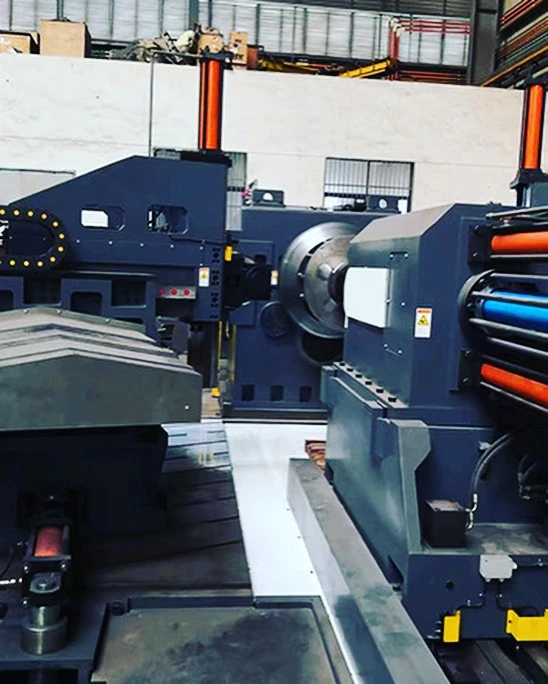
A Ring Rolling Wheel Forming Machine is a specialized type of equipment used in the manufacturing of rolled rings and wheel components primarily for industries that require high-performance parts such as the aerospace, automotive, energy, and railroad sectors. The primary purpose of this machine is to produce rings with specific dimensions, thickness, and material properties by using a process known as ring rolling, which is a type of hot forging that shapes a metal billet into a ring or wheel shape.
The ring rolling process involves a combination of radial force and axial compression, where a heated metal billet is deformed between two rollers, one of which is typically fixed while the other moves axially to reduce the ring’s thickness. This process enables the production of parts with superior mechanical properties, particularly high strength and excellent fatigue resistance, due to the continuous grain flow created during the rolling process.
Ring Rolling Wheel Forming Machines are used to create large-diameter rings, such as those used in wheel hubs, flanges, gaskets, and various types of wheels used in railcars, aerospace turbine rotors, gear components, and marine propellers. These components are critical in high-stress applications, where durability and performance are paramount.
The key process flow of a Ring Rolling Wheel Forming Machine includes the following steps:
- Heating: The billet is first heated to a specific temperature, often in the range of 1000–1250°C (1832–2282°F), depending on the material being used. This heat makes the metal more malleable and easier to deform.
- Rolling: Once heated, the billet is placed between two rollers. One roller is typically stationary, while the other moves along the axial direction to expand the billet radially. The machine applies controlled force in both the radial and axial directions to form the ring shape. This process creates a part with a continuous grain structure, improving its strength and resistance to cracking under stress.
- Cooling: After rolling, the ring is often cooled in a controlled manner to prevent thermal stresses. This cooling process may include forced air cooling or quenching, depending on the material and required mechanical properties.
- Shaping: After the ring is rolled, it may undergo additional machining or finishing processes to achieve the desired dimensions, surface finish, and tolerances. This could include processes such as grinding, polishing, or drilling.
Ring rolling machines are available in different configurations, with horizontal ring rolling machines being the most common. In these machines, the billet is placed horizontally, and the rollers rotate in a vertical direction. There are also vertical ring rolling machines, where the billet is positioned vertically, and the force is applied in the horizontal direction. Both types of machines can be equipped with automatic controls and robotic handling systems to improve efficiency and reduce the need for manual intervention.
Modern ring rolling machines often feature advanced control systems that enable precise control over temperature, pressure, and speed during the rolling process. This is crucial for ensuring that the final part meets the required specifications. CNC (Computer Numerical Control) integration allows for accurate monitoring and adjustment of the machine’s parameters, leading to consistent results even in the production of complex parts with varying dimensions or material types. Feedback systems that monitor temperature and force can also be employed to automatically adjust parameters and ensure the process stays within the optimal range, minimizing the chance of defects such as cracks or uneven material distribution.
In addition, automation plays a significant role in improving the efficiency and reliability of ring rolling operations. Robotic arms can be used to load and unload billets, transport finished rings, and handle quality control tasks such as inspecting dimensions or checking surface finishes. Real-time monitoring systems can detect any irregularities or issues with the part during the rolling process, triggering automatic corrections or stopping the machine for further inspection.
The materials used in ring rolling are typically high-strength alloys or forging-grade metals, including steel, titanium, nickel-based alloys, and aluminum alloys. These materials are selected based on their ability to withstand high levels of stress and perform in demanding environments, such as aerospace engines, rail systems, or heavy-duty vehicles. The material flow during the ring rolling process is critical, as improper material distribution can lead to defects like non-uniform thickness or internal voids. To ensure optimal results, the billet’s composition, temperature, and deformation rates must be carefully controlled.
One of the most important benefits of the ring rolling process is the reduced material waste. Since the billet is deformed rather than cut away, the process results in minimal scrap, which makes it more cost-effective than other methods such as casting or machining. This also makes ring rolling a more sustainable option, as it reduces the need for large quantities of raw material and minimizes energy consumption in the manufacturing process.
As industries push for more customized solutions and higher performance from their components, ring rolling machines will need to become even more adaptable. The increasing demand for lightweight and high-strength parts will drive the development of machines capable of handling new, advanced materials that offer improved strength-to-weight ratios. Additionally, the focus on sustainability will continue to influence ring rolling machine design, with manufacturers seeking ways to integrate recyclable materials into the forging process and optimize energy usage.
With the continued integration of smart manufacturing technologies, the future of ring rolling machines will likely include greater connectivity and intelligent automation. These features will allow for more seamless data collection, remote diagnostics, and predictive maintenance, improving uptime and reducing overall maintenance costs. Additive manufacturing could also play a role in the future of ring rolling, with some systems potentially combining traditional ring rolling with 3D printing to create complex geometries or hybrid parts that cannot be made using conventional methods.
In conclusion, a Ring Rolling Wheel Forming Machine plays a crucial role in the production of high-performance rings and wheels used in industries where strength, durability, and precision are essential. Through the use of advanced materials, automation, and precise control over the rolling process, these machines ensure that the forged parts meet the strict requirements of applications such as aerospace, automotive, and heavy machinery. As technologies continue to evolve, the future of ring rolling machines will focus on improving efficiency, reducing waste, and enabling the production of more complex, high-performance parts with greater sustainability.
A Ring Rolling Wheel Forming Machine plays a crucial role in the production of high-performance parts that are critical in demanding applications. This machine uses the process of ring rolling, which involves shaping a heated billet of metal into a ring by applying both radial force and axial compression. This results in a part with superior mechanical properties, such as high strength, excellent fatigue resistance, and uniform grain structure, which are especially important in industries like aerospace, automotive, and energy.
The machine’s design allows for the forging of large-diameter rings, often used in wheel hubs, flanges, gear components, and structural parts. The production of these rings often requires careful control over various parameters, such as the temperature of the billet, the speed of the rollers, and the force applied during the rolling process. Maintaining tight control over these factors ensures that the finished part meets the desired specifications for strength, dimensional accuracy, and surface finish.
The use of advanced materials like high-strength steels, titanium alloys, and composite metals has driven improvements in ring rolling machines. These materials are known for their performance in extreme conditions, such as high temperatures, heavy loads, or corrosive environments. The machine must be capable of handling these advanced materials without compromising on part integrity. This includes ensuring that the grain structure remains continuous and uniform, as this contributes to the strength of the forged ring.
One of the key advantages of ring rolling is its efficiency. The process generates minimal waste compared to other manufacturing techniques like casting, where much of the material is cut away. In addition, automation has become increasingly important in improving efficiency and reducing human error. By integrating CNC controls, robotic arms, and automated inspection systems, manufacturers can achieve greater precision and consistency throughout the production process. This automation also reduces the need for manual labor, lowering costs and speeding up production cycles.
As industries continue to demand customized components that can withstand high performance and extreme environments, ring rolling machines will likely become even more versatile. The trend toward lightweighting, especially in the automotive and aerospace sectors, demands the development of parts that not only perform well but also contribute to overall weight reduction. This places further pressure on ring rolling machines to handle complex geometries and advanced materials while still meeting rigorous performance standards.
The sustainability aspect of manufacturing is also becoming a focal point. With the global push for more sustainable production practices, manufacturers are increasingly looking for ways to incorporate recycled materials into the production process without sacrificing quality. Ring rolling machines can contribute to this effort by producing high-strength components with minimal material waste, thereby reducing the overall environmental impact of production. Additionally, energy-efficient heating methods, such as induction heating, have been incorporated into some machines, reducing the energy consumption during the heating phase of the process.
Furthermore, the future of ring rolling machines is closely tied to the digital transformation in manufacturing. The integration of smart technologies such as IoT sensors, AI-driven optimization, and real-time data collection will help manufacturers monitor and adjust the forging process to ensure higher levels of precision. Predictive maintenance enabled by machine learning will also allow for more efficient use of the equipment, reducing downtime and improving overall production rates. Through the use of digital twins, manufacturers can simulate the entire rolling process in a virtual environment, allowing them to optimize parameters before applying them to the physical machine.
The combination of advanced control systems, precision engineering, and automation makes ring rolling machines highly efficient and adaptable to the evolving demands of industries that rely on high-performance components. As new materials and manufacturing techniques continue to emerge, these machines will be at the forefront of innovation, capable of producing increasingly complex and durable parts. In the end, the role of Ring Rolling Wheel Forming Machines will be essential for maintaining the high standards required in industries where strength, precision, and durability are critical. With the continuous improvement in technology and automation, these machines will continue to evolve, ensuring that the manufacturing process remains at the cutting edge of efficiency, sustainability, and quality.
As the demand for high-performance components continues to rise across various industries, Ring Rolling Wheel Forming Machines will increasingly adapt to meet these challenges. The development of new materials will be one of the key drivers of this evolution. Manufacturers will need to ensure that ring rolling machines can work with advanced materials such as high-temperature alloys, superalloys, and composite materials, which are being used more frequently in fields like aerospace and nuclear power. These materials have specific characteristics that require precise handling during the rolling process, particularly with regard to their thermal properties and flow characteristics under deformation.
The trend toward customization and the need for shorter production runs will also shape the future of these machines. Instead of producing large quantities of a single part, manufacturers will increasingly need to create customized parts for specialized applications. This will require flexible, adaptable machines capable of quickly reconfiguring to handle different sizes, shapes, and materials. Innovations in modular machine design could allow manufacturers to retool their equipment to meet specific customer needs, improving the versatility of the production process.
In terms of precision, the future of ring rolling machines is likely to involve even greater integration of real-time monitoring and data analytics. Sensor technologies embedded within the machines will provide continuous feedback on every step of the process, including material temperature, deformation rates, and pressure distribution. These sensors will be connected to advanced software systems that can analyze the data in real-time, making adjustments to optimize the process. For instance, the software might detect a temperature variation in the billet that could lead to imperfections in the final product and automatically adjust the heating parameters to compensate. This type of real-time correction ensures consistent quality throughout the manufacturing process.
The integration of predictive maintenance will become a critical component of ring rolling operations. As these machines become more complex and capable, AI-driven maintenance systems will predict when parts of the machine are likely to fail based on usage patterns and real-time data. This reduces the likelihood of unexpected breakdowns and minimizes downtime, which can be costly in industries where high-volume, high-performance parts are needed. This predictive system will also help manufacturers extend the lifespan of their machines, improving the overall cost-effectiveness of the production process.
Looking ahead, sustainability will continue to be a major focus. Ring rolling machines will be expected to not only produce high-quality, precision components but also do so with minimal environmental impact. In addition to recycling materials, energy efficiency will become even more critical. New advancements in energy recovery technologies, such as the capture and reuse of waste heat from the forging process, will help manufacturers reduce their carbon footprint and operating costs. Green manufacturing practices will be implemented across the entire production process, with an emphasis on reducing emissions and water usage.
Another potential development is the integration of additive manufacturing with traditional ring rolling techniques. As 3D printing technologies improve, manufacturers may begin using hybrid processes that combine additive and subtractive methods with ring rolling. This could lead to the production of complex, geometrically optimized parts that are difficult or impossible to create using conventional methods alone. For example, a part might be created with a base structure via ring rolling, then finished or augmented with 3D printed features that enhance its performance or reduce weight.
Automation will continue to play a significant role in shaping the future of ring rolling. As production demands increase and customization becomes more common, manufacturers will lean more on robotic systems for material handling, billet loading, and quality inspection. These robotic systems will work seamlessly with the ring rolling machines, reducing the need for manual labor while ensuring high precision and consistency in the finished product. Automated quality control systems will use advanced machine vision and AI to inspect each ring for dimensional accuracy and surface finish, detecting defects or deviations from specifications before the part proceeds further down the production line.
The continued digitalization of manufacturing processes will also mean that ring rolling operations are increasingly interconnected with other parts of the factory. Smart factory concepts will lead to a more integrated approach, where ring rolling machines, material handling systems, and post-processing equipment are all linked to a central control system. This system can optimize workflows, minimize idle times, and adjust production schedules based on real-time demand or machine performance data. Cloud computing and big data analytics will allow manufacturers to access and analyze vast amounts of data from their machines, providing insights into potential improvements and enabling continuous process optimization.
The future of Ring Rolling Wheel Forming Machines is filled with exciting possibilities. As industries continue to push for lighter, stronger, and more specialized parts, these machines will evolve to meet these demands. Whether it’s through advancements in material science, machine intelligence, or sustainable practices, the future of ring rolling machines will be defined by their ability to produce high-performance, customizable, and environmentally responsible components with unprecedented precision and efficiency. With these innovations, ring rolling technology will remain a cornerstone of modern manufacturing, enabling industries to build the next generation of high-performance, durable products.
Multi-Spindle Wheel Forming Machine
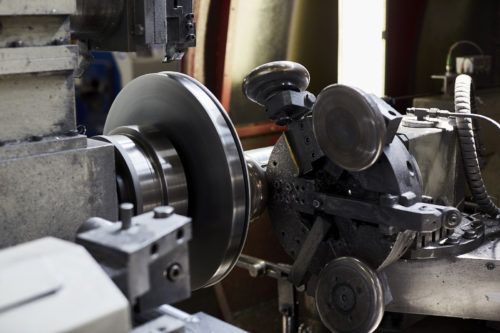
A Multi-Spindle Wheel Forming Machine is a type of manufacturing equipment used for the production of wheel components, particularly those used in high-performance and heavy-duty applications such as automotive, aerospace, and railway industries. This machine is designed to form, shape, or modify wheel-like components through the use of multiple spindles, each performing specific tasks during the production process. The versatility and precision of a multi-spindle design allow for high efficiency and flexibility in producing parts with complex geometries and intricate features.
The multi-spindle design allows for multiple operations to be performed simultaneously, significantly improving the speed and efficiency of wheel forming processes. Each spindle typically holds a different tool or performs a distinct function, such as cutting, drilling, milling, or tapping, all in a single setup. This minimizes the need for multiple machines or workstations, reducing cycle times and increasing overall productivity. The ability to perform several processes at once also enhances the accuracy of the components, ensuring consistent quality.
A Multi-Spindle Wheel Forming Machine is especially useful for high-volume production, where uniformity and precision are crucial. The machine’s setup can be tailored to handle various types of wheel forms, from traditional steel wheels to specialized alloy wheels, and even high-performance materials such as titanium or composite materials used in aerospace or motorsport applications.
Key features of a Multi-Spindle Wheel Forming Machine typically include:
- Multiple Spindles: The machine is equipped with several spindles, each of which can be fitted with different tools. This allows for simultaneous execution of different operations, like milling, drilling, and cutting, on the same component.
- Precision Control Systems: These machines are often equipped with advanced CNC (Computer Numerical Control) systems that provide precise control over spindle movements, feed rates, and tool changes. This ensures high accuracy and repeatability in the production process.
- Automatic Tool Changers: Some multi-spindle machines feature automatic tool changers, which allow for the quick exchange of tools without manual intervention. This feature improves production efficiency by reducing downtime.
- Multi-Axis Machining: To handle more complex shapes and forms, multi-spindle wheel forming machines often have multi-axis capabilities. These allow for more intricate machining of the wheel components, including precision contouring and profiling of the wheel’s surface.
- High-Speed Machining: The multi-spindle configuration helps increase the overall machining speed. Multiple tools working at the same time can dramatically reduce cycle times, which is particularly beneficial for high-volume production.
- Material Handling Automation: Many multi-spindle machines are integrated with automated material handling systems, such as robotic arms or conveyor belts, to load and unload the workpieces, reducing the need for manual intervention and increasing the speed and safety of the operation.
Applications of Multi-Spindle Wheel Forming Machines:
- Automotive Wheels: These machines are used to create components for automotive wheels, such as hubs, rims, and spoke features. By utilizing multiple spindles, the machine can perform all the necessary operations on a single wheel blank, reducing processing time and improving the consistency of the finished parts.
- Aerospace Components: In the aerospace industry, multi-spindle machines are used to produce wheels for landing gears, turbine components, and other critical wheel-based applications. The precision and material flexibility of the machine ensure that parts can meet the stringent requirements of aerospace standards.
- Railway Wheels: Multi-spindle machines are used in the production of railway wheels, which require significant strength and durability. The ability to machine multiple features, such as hubs and treads, in one go helps reduce production time and improve part integrity.
- Specialty and Custom Wheels: For specialized applications such as motorsport, heavy machinery, or even military vehicles, custom wheels with unique designs or specific performance requirements can be efficiently manufactured using multi-spindle technology.
Advantages of Multi-Spindle Wheel Forming Machines:
- Increased Efficiency: The simultaneous operation of multiple spindles reduces production time. Multiple processes, such as drilling, milling, and cutting, can be done at once, leading to faster completion of each part.
- Cost-Effectiveness: By eliminating the need for multiple machines or setups, a multi-spindle machine can significantly reduce labor costs and machine downtime. This leads to more economical production, especially in high-volume manufacturing.
- High Precision: The ability to control each spindle precisely ensures that all aspects of the wheel are produced to tight tolerances, which is essential for parts used in high-performance applications where accuracy is paramount.
- Reduced Setup Time: With the ability to switch tools quickly and perform several operations in one pass, setup times are greatly reduced, leading to a more streamlined production process.
- Versatility: Multi-spindle machines are highly adaptable, capable of working with a wide range of materials and part designs. Whether manufacturing a standard automotive wheel or a custom aerospace component, these machines can be configured to meet specific needs.
Challenges:
- Complexity in Maintenance: Due to the intricate nature of the machine, maintenance can be more complicated and may require specialized knowledge. Downtime caused by maintenance issues can disrupt production, so regular upkeep and monitoring are essential.
- Cost of Equipment: Multi-spindle machines tend to be more expensive than single-spindle or simpler machines, particularly for the higher-end models that include advanced automation and CNC control systems. However, the investment is justified by the significant productivity gains.
- Skill Requirements: Operators need to be highly skilled in programming and maintaining multi-spindle machines. CNC programming and understanding the intricacies of tool changes, spindle configurations, and part handling are critical for efficient operation.
In conclusion, Multi-Spindle Wheel Forming Machines represent a powerful tool in modern manufacturing, especially for industries requiring high-quality, high-precision wheel components in high volumes. Their ability to perform multiple machining operations simultaneously, combined with advanced control systems and automation, allows manufacturers to achieve faster production times, lower costs, and superior part quality. Whether for automotive, aerospace, or railway wheels, these machines are an essential part of the advanced manufacturing landscape, helping to meet the ever-growing demand for performance and precision in wheel forging.
The Multi-Spindle Wheel Forming Machine continues to play a pivotal role in industries that require the mass production of high-quality wheel components. As technology advances, manufacturers have sought to push the capabilities of these machines even further, allowing for the production of increasingly complex and sophisticated parts. One of the key benefits of multi-spindle machines is the ability to optimize material usage, which is critical in reducing waste and improving the overall sustainability of the manufacturing process. These machines help reduce scrap by ensuring that the wheel components are consistently formed with minimal material removal.
As industries move towards automation and smart manufacturing, multi-spindle wheel forming machines are incorporating AI-driven solutions that offer predictive capabilities, ensuring that the production process runs smoothly with minimal human intervention. These machines often feature real-time monitoring systems that collect data on spindle performance, tool wear, and the condition of the workpieces. This data can be analyzed to predict when maintenance will be required or to flag any potential issues that may arise during production, reducing the likelihood of defects or production delays.
In addition to predictive analytics, the future of multi-spindle machines is closely tied to digitization and connected systems. With the use of Internet of Things (IoT) technology, these machines can now be integrated into broader smart factory networks, providing insights into overall production efficiency. Through cloud-based platforms, manufacturers can monitor the performance of multiple machines across different sites, ensuring that each unit is working at peak efficiency. This connectivity also facilitates remote diagnostics and control, allowing technicians to troubleshoot and resolve issues from virtually anywhere.
The integration of additive manufacturing techniques with traditional subtractive methods in multi-spindle machines is another exciting development. By incorporating 3D printing capabilities, manufacturers can produce hybrid components that combine both additive and subtractive processes in a single setup. For instance, a wheel component may have complex geometries or lightweight features that can only be achieved through additive manufacturing, while traditional machining processes handle the structural aspects of the part. This hybrid approach offers tremendous flexibility and design freedom, enabling manufacturers to meet the demanding specifications required by high-performance applications.
The demand for customized wheel designs continues to grow, especially in the automotive, motorsports, and luxury vehicle sectors. Multi-spindle machines excel at producing components with complex designs and unique geometries. Custom features such as intricate spoke patterns, lightweight structures, or specific surface finishes can be achieved through the combination of precise machining and tool control offered by these machines. Manufacturers can use advanced simulation software to design and prototype these parts, ensuring that they meet both aesthetic and functional requirements before the actual production begins.
As the need for high-performance materials increases, multi-spindle machines are also evolving to handle more advanced alloys and composites. Materials like titanium, superalloys, and carbon composites are being used more frequently in wheel production due to their superior strength-to-weight ratios and resistance to extreme environments. Multi-spindle machines are equipped with enhanced cutting tools and more powerful spindles to handle the challenges presented by these hard-to-machine materials. The advanced cooling systems in these machines also help manage the heat generated during machining, preventing tool wear and ensuring that the components are produced with high precision.
With the increasing importance of energy efficiency, many modern multi-spindle machines are designed with energy-saving features to reduce consumption during the manufacturing process. This includes improvements in the power supply systems, the introduction of energy-efficient motors, and the optimization of machine operations to minimize unnecessary energy use. Moreover, manufacturers are focusing on reducing the carbon footprint of the entire production line, from raw material sourcing to finished product delivery. By incorporating more sustainable practices into their production processes, multi-spindle machines contribute to the growing push toward greener manufacturing.
Looking ahead, the future of multi-spindle wheel forming machines is undoubtedly linked to the broader trends in Industry 4.0. With ongoing advancements in artificial intelligence, machine learning, and automation, these machines will become more self-optimizing. For example, machine learning algorithms can be used to continuously improve the machining process by analyzing historical data and adjusting settings for optimal performance. This capability will lead to even more efficient production cycles, improved product consistency, and reduced reliance on manual labor.
In conclusion, multi-spindle wheel forming machines are a cornerstone of modern manufacturing in industries that rely on high-precision, high-performance wheel components. Their ability to handle complex geometries, work with advanced materials, and increase production efficiency makes them indispensable. As automation, AI, and sustainability become more central to manufacturing, these machines will continue to evolve, meeting the challenges of the future with greater versatility, precision, and efficiency. Manufacturers will increasingly rely on multi-spindle machines to produce parts that meet the growing demands for customization, performance, and environmental responsibility.
As the demand for advanced, high-performance components escalates, the future of multi-spindle wheel forming machines will be shaped by further innovations in automation, material science, and production efficiency. The continued integration of robotics into these systems will further enhance their capabilities, especially in terms of material handling, tool change automation, and finished part inspection. With the use of robotic arms, automated guided vehicles (AGVs), and robotic loaders, the workflow becomes highly efficient, reducing manual handling and increasing throughput.
Automation in multi-spindle machines will also extend to quality control. Traditionally, quality inspections in wheel manufacturing require significant manual input, such as visual checks or dimensional measurement. However, future systems will likely integrate vision systems and laser scanners, allowing for real-time measurement of each component during production. These systems will be able to identify defects such as dimensional deviations, surface imperfections, and material inconsistencies on the fly, ensuring that only parts that meet the highest standards reach the next stages of production.
A major trend in modern manufacturing is process integration. Multi-spindle machines will continue to evolve into multi-process systems where tasks like heat treatment, surface finishing, and assembly can be incorporated into the same production line. For instance, a multi-spindle machine could be combined with a heat treatment module to immediately heat-treat the wheel after it has been formed, eliminating the need for separate equipment and reducing handling time. Such integrated systems can significantly enhance overall efficiency and reduce the production footprint, which is essential in the push for more sustainable and resource-efficient manufacturing.
At the same time, adaptive manufacturing systems will become more prevalent. These systems leverage real-time data and feedback loops to adjust machine settings on the fly based on changes in the material’s properties, environmental conditions, or tool wear. For example, if the material being used in the wheel is slightly different in hardness than expected, the system can adjust the spindle speed, cutting force, or tool geometry to ensure optimal machining conditions. This type of intelligent system ensures consistent product quality and reduces the likelihood of defects, even when working with materials that have variable properties.
The increasing importance of data analytics will also shape the future of multi-spindle machines. Manufacturers will continue to integrate more advanced data analytics platforms to track machine performance, operator efficiency, and product quality. With these tools, operators and plant managers can make data-driven decisions about everything from machine maintenance schedules to inventory management and process optimization. By collecting and analyzing vast amounts of data, manufacturers can identify patterns that lead to improved operational workflows, higher-quality products, and greater cost savings.
One area that will see significant innovation is the integration of artificial intelligence (AI) into multi-spindle machines. AI can be employed to continuously optimize machining parameters based on ongoing production data. Machine learning models can analyze historical data to predict optimal tool speeds, feeds, and cutting conditions based on the materials and components being processed. These advanced AI systems could even adjust the machines’ operations in real time, ensuring that every part is produced as efficiently as possible. Additionally, AI could be used to analyze the wear and tear of machine parts, predicting failures before they happen, and enabling predictive maintenance strategies to minimize downtime and maintenance costs.
Sustainability will also continue to be a critical focus in the future of multi-spindle wheel forming machines. As industries worldwide strive for greener manufacturing practices, these machines will incorporate energy-efficient features and recycling systems. Manufacturers are exploring methods to recycle cutting fluids, reduce overall energy consumption, and lower carbon emissions during production. The development of low-energy machinery, coupled with waste heat recovery systems, will be a significant step in achieving sustainability goals. The shift toward circular economy principles means that even the machines themselves will be designed with reuse and recyclability in mind, ensuring that they remain energy-efficient and sustainable over their lifespan.
Furthermore, the demand for lightweight materials in sectors such as aerospace and automotive will drive further innovation in how multi-spindle machines process these materials. Aluminum alloys, magnesium, and composites are being increasingly used for wheel production due to their lighter weight and high strength-to-weight ratio. These materials often require different machining techniques compared to traditional materials like steel, and multi-spindle machines will need to adapt to these challenges by offering specialized tools, cooling systems, and machining strategies designed specifically for lightweight materials.
Finally, the growing trend of global supply chains and just-in-time manufacturing means that multi-spindle wheel forming machines will need to be highly flexible, allowing for the rapid production of custom wheel designs in smaller batch sizes. This flexibility will be achieved through advanced programming, allowing machines to quickly switch between different wheel designs, materials, and sizes without requiring lengthy retooling times. By incorporating advanced CAD/CAM software and real-time process optimization, manufacturers can quickly respond to market demands, customize products to specific customer requirements, and reduce the time between design and delivery.
The future of multi-spindle wheel forming machines will be defined by their ability to meet the increasing demands for speed, precision, customization, and sustainability. As manufacturing processes become more integrated, automated, and data-driven, multi-spindle machines will continue to play a central role in producing high-performance, high-precision wheel components. Their ability to handle diverse materials, complex geometries, and varied production volumes will make them indispensable in industries that require quality, efficiency, and innovation in wheel manufacturing. By incorporating AI, machine learning, and cutting-edge manufacturing technologies, these machines will evolve into highly adaptive and intelligent systems, ready to meet the challenges of tomorrow’s manufacturing needs.
Single-Spindle Wheel Forming Machine
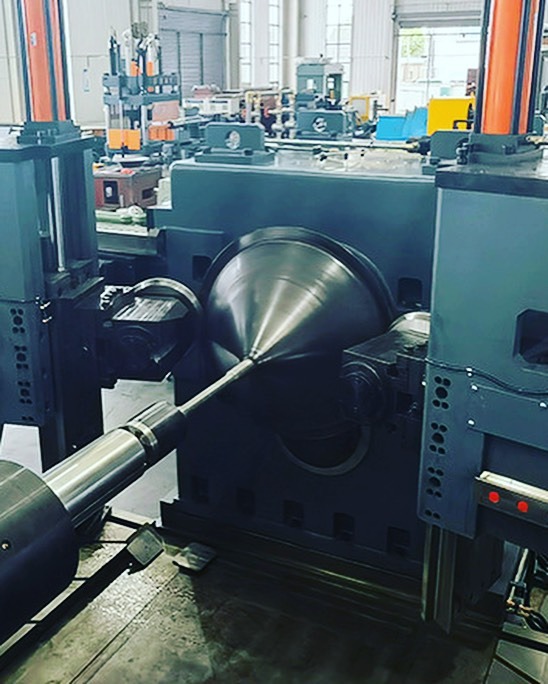
A Single-Spindle Wheel Forming Machine is a type of manufacturing equipment used to produce wheel components, primarily in the automotive, aerospace, and industrial machinery industries. This machine is designed to perform various machining processes on a single workpiece using a single spindle, which holds the cutting tool. Unlike multi-spindle machines, which have several spindles operating simultaneously, a single-spindle machine focuses on performing one operation at a time on the workpiece.
The single-spindle wheel forming machine is often used for precision operations, especially when the components being produced require detailed work and intricate designs. These machines are typically equipped with advanced CNC (Computer Numerical Control) technology, which allows for precise control over the movements of the spindle, cutting tools, and other components. CNC control ensures that each part is produced with high accuracy and repeatability.
The machine’s primary function is to form, shape, or modify wheel-like components by performing various processes such as milling, turning, drilling, or cutting. Single-spindle machines are typically employed in settings where high-quality, low to medium-volume production is required, and flexibility is essential. The key advantage of a single-spindle machine lies in its ability to work on complex geometries and customized designs with high precision.
Key Features of a Single-Spindle Wheel Forming Machine:
- Precision Control: Single-spindle machines often feature advanced CNC control systems that provide high levels of precision in machining. Operators can program intricate designs and ensure that each workpiece meets strict dimensional tolerances.
- Versatility: Although a single spindle limits simultaneous operations, these machines are still versatile and can handle various processes such as milling, boring, tapping, and turning. The machine can be reprogrammed for different tasks and adjusted to work with various materials.
- Efficient Setup for Customization: For small batch or custom wheel designs, single-spindle machines excel due to their ease of reconfiguration. Changes to machine setups, such as tool replacements or workpiece fixtures, can be quickly made, making them ideal for specialized or prototype production.
- Tool Change Flexibility: Some single-spindle machines come equipped with automatic tool changers, which allow for faster and more efficient tool swaps. This feature enhances the flexibility of the machine and reduces downtime during setup changes.
- Compact Design: Single-spindle machines are typically more compact compared to multi-spindle machines, making them suitable for shops with limited space or for smaller production environments. This compact design often results in a more cost-effective machine for businesses that don’t require the high-volume capabilities of multi-spindle machines.
- Manual and Automated Options: Single-spindle machines are available in both manual and automated configurations. While manual machines require more operator intervention, automated machines with CNC control allow for higher levels of consistency and reduced labor costs.
Applications of Single-Spindle Wheel Forming Machines:
- Automotive Wheels: Single-spindle machines can be used for precision operations on automotive wheel hubs, rims, and other wheel components. They are ideal for low-volume production runs of custom-designed wheels or specialized parts that need high precision.
- Aerospace Components: In aerospace manufacturing, single-spindle machines are employed to produce complex parts that require tight tolerances and high material integrity. These machines are especially useful for producing landing gear wheels, turbine components, and other critical parts in low quantities or prototype designs.
- Industrial Equipment: Heavy machinery wheels or components that require high strength and durability can also be produced on single-spindle machines. This could include wheels for cranes, forklifts, and other industrial vehicles.
- Prototype Production: Single-spindle machines are commonly used in prototype production, where custom, low-volume runs are necessary. Their ability to handle various materials, including metals, composites, and alloys, makes them adaptable to the needs of prototype developers.
- Custom Wheel Designs: Single-spindle machines are particularly suited for custom wheel manufacturing, where unique wheel geometries, material combinations, or design features are required. Their flexibility and precision make them ideal for creating one-off or limited edition wheels for high-end automobiles, motorcycles, and specialty vehicles.
Advantages of Single-Spindle Wheel Forming Machines:
- Precision and Accuracy: Single-spindle machines are often capable of achieving extremely high precision, which is critical in industries that require tight tolerances, such as aerospace and automotive. The CNC control system allows for fine adjustments and consistent results over multiple production cycles.
- Lower Capital Investment: Compared to multi-spindle machines, single-spindle machines are typically less expensive, making them a more accessible option for smaller manufacturers or businesses that need to produce high-quality components without investing in large, complex machinery.
- Flexible Operation: Single-spindle machines can handle a variety of operations, from simple turning to complex milling, making them versatile for a range of applications. They can easily switch between different tasks with minimal setup time.
- Customizability: The flexibility of single-spindle machines makes them ideal for customized production runs, where unique or bespoke designs are required. They can produce parts with a high degree of complexity, allowing manufacturers to cater to niche markets.
- Compact and Space-Saving: Their smaller footprint allows single-spindle machines to fit into smaller workshops or facilities, making them ideal for companies with limited space or those focused on smaller-scale production.
Challenges of Single-Spindle Wheel Forming Machines:
- Lower Throughput: Since single-spindle machines perform one operation at a time, their production speed is typically slower than that of multi-spindle machines. For high-volume production, multi-spindle machines are often preferred due to their ability to perform multiple operations simultaneously.
- Limited by Single Tool: As a single-spindle machine can only use one tool at a time, it may require tool changes to perform different operations, which can introduce downtime and increase the complexity of the setup.
- Limited Simultaneous Operations: Unlike multi-spindle machines, which can execute multiple operations on a single part in parallel, single-spindle machines are limited to one task at a time, which can affect overall efficiency when working on parts that require several operations.
- Maintenance and Downtime: Single-spindle machines, like all CNC equipment, require periodic maintenance to ensure optimal performance. While the machines are relatively simple compared to multi-spindle machines, downtime due to maintenance or tool wear can still impact production schedules.
Conclusion:
Single-Spindle Wheel Forming Machines are essential tools in precision manufacturing environments that require high accuracy, flexibility, and customization. While not as fast as multi-spindle machines, they excel in low to medium-volume production runs, custom designs, and prototype development. Their versatility, precision, and cost-effectiveness make them indispensable in the production of high-quality, custom wheel components across industries such as automotive, aerospace, and industrial machinery. These machines continue to evolve with advancements in automation, data analytics, and sustainability, ensuring that they remain a key part of modern manufacturing processes.
Single-Spindle Wheel Forming Machines continue to offer valuable benefits for manufacturers, especially those working on custom, low-to-medium volume runs. The ability to produce highly detailed, intricate parts with tight tolerances is one of the main advantages that these machines provide. The precision and flexibility of the single-spindle design make it ideal for manufacturers that need versatility in their production processes. For industries such as aerospace, automotive, and industrial machinery, where customization is often key, single-spindle machines allow for high-quality results without the significant upfront costs associated with larger, multi-spindle systems.
These machines are often used for producing a wide range of parts, including automotive hubs, rims, brake components, and other specialized wheel forms. They are equally beneficial for producing parts in low volumes, or prototypes, where quick changes in design or material choice are required. Their ability to rapidly switch between operations like turning, milling, boring, or tapping makes them a versatile tool on the production floor. Additionally, CNC control enables manufacturers to achieve a high level of repeatability, ensuring that each wheel or component meets strict specifications across multiple cycles.
When producing customized wheel components, the flexibility of single-spindle machines allows for the integration of unique material combinations, complex geometries, or specific surface finishes, all of which are often necessary for high-end products or niche applications. This level of flexibility, combined with the precision control offered by modern CNC systems, makes single-spindle machines ideal for creating bespoke designs, such as those used in luxury cars, motorsports vehicles, and custom motorcycles.
Moreover, these machines are typically easier and faster to set up than their multi-spindle counterparts. While multi-spindle machines are optimized for mass production and high-speed operations, single-spindle machines shine in applications requiring frequent retooling and adjustments. This is especially advantageous in small to medium shops where production needs might change frequently, or where there is a need to produce multiple versions of a part in a shorter amount of time. Single-spindle machines often have shorter setup times and can produce a wider variety of parts, making them ideal for manufacturers looking to adapt quickly to shifting customer demands or new design trends.
While single-spindle machines offer a high degree of flexibility, there are trade-offs to consider. As they work on only one part at a time, they do not have the same throughput capabilities as multi-spindle systems, which can simultaneously perform several operations on multiple parts. Therefore, single-spindle machines are best suited for low-volume production runs or when the complexity of the part demands a higher level of precision and customization. For large-scale production of simple components, multi-spindle systems will generally be more efficient due to their higher output.
In terms of maintenance, single-spindle machines are typically easier to service compared to more complex multi-spindle machines, as there are fewer components to manage. However, like all CNC machines, they do require periodic maintenance to ensure smooth operations. Regular checks on the spindle, tooling, and lubrication systems help prevent wear and tear, reducing the risk of downtime during production. The introduction of predictive maintenance using IoT technology is also becoming a more common practice, allowing operators to monitor machine performance and catch potential issues before they result in significant problems.
As smart manufacturing continues to grow, single-spindle machines are evolving alongside new technologies like artificial intelligence (AI) and machine learning. These innovations are being integrated into control systems to allow for real-time adjustments, ensuring that the machine operates at optimal levels without human intervention. This creates a more efficient production process by reducing the chance of errors and improving machine uptime. Data-driven insights into tool wear, material behavior, and process performance are helping operators fine-tune machine settings to produce parts with even higher precision and fewer defects.
Additionally, with sustainability becoming a larger concern across all industries, single-spindle machines are also adapting to greener manufacturing practices. The integration of energy-efficient components and recyclable materials is helping manufacturers meet environmental goals while maintaining high production standards. The adoption of energy-saving technologies, such as regenerative braking systems or variable-speed motors, reduces overall energy consumption during production. Manufacturers are also exploring ways to recycle cutting fluids and reduce waste generated during machining, further improving the environmental impact of the production process.
Looking toward the future, the role of single-spindle wheel forming machines in precision manufacturing will only continue to grow. As industries place greater emphasis on customization, performance, and sustainability, the flexibility, precision, and adaptability of these machines make them invaluable for creating complex, high-quality wheel components. They will remain an essential tool in the manufacturing landscape, offering a balance of flexibility, efficiency, and precision that is difficult to match by other machines in the same category. With ongoing innovations in automation, digitalization, and material science, single-spindle machines will continue to evolve, meeting the needs of modern manufacturing and paving the way for new, cutting-edge developments in wheel production and beyond.
The future of single-spindle wheel forming machines is poised to incorporate even more advanced technologies that enhance their capabilities and improve manufacturing outcomes. One area that is likely to see significant advancement is automation. As manufacturers strive for greater efficiency and lower operational costs, the integration of robotic automation systems with single-spindle machines will allow for seamless handling of materials, loading and unloading of parts, and even tool changes. These automated systems will reduce the need for manual intervention, increasing overall throughput while maintaining high levels of precision and reducing human error.
The integration of robotic arms or automated guided vehicles (AGVs) can further enhance the workflow of single-spindle machines, particularly in factories with high-mix, low-volume production. These automated systems could quickly move parts through different stages of the production process, improving material flow and minimizing downtime between operations. For example, once a part is formed, robotic arms could automatically move it to a post-processing station or even conduct secondary operations like grinding, polishing, or inspecting.
At the same time, artificial intelligence (AI) and machine learning are expected to play an even greater role in optimizing machine performance. AI algorithms can analyze data from sensors embedded in the machine, such as vibration sensors, temperature sensors, and force sensors, to predict wear on tools, detect anomalies in the machining process, and adjust parameters in real-time for optimal performance. This will not only improve part quality but also reduce tool wear, extend the lifespan of machine components, and minimize the need for manual adjustments. AI-powered systems can also enable more adaptive manufacturing, where the machine adjusts based on incoming data regarding the material properties, part geometry, and other variables to ensure consistent results even when working with a range of materials or designs.
With the increasing push toward smart factories, single-spindle machines will become more connected through the Industrial Internet of Things (IIoT). This connectivity will allow for real-time monitoring and control of machines, providing operators with instant feedback on machine health, production status, and performance metrics. Cloud-based analytics platforms will collect data from across the production floor, providing valuable insights into machine efficiency, utilization rates, and potential bottlenecks. Manufacturers can use this information to optimize workflows, schedule maintenance, and even forecast potential issues before they cause downtime, enabling a shift toward predictive maintenance.
In terms of sustainability, as demand for environmentally responsible production increases, single-spindle machines are likely to become more energy-efficient. Manufacturers will focus on designing machines that consume less power while still maintaining their high-performance standards. This may involve using energy-efficient motors, regenerative braking systems, or variable-speed drives to reduce energy usage during non-operational periods. Furthermore, the ability to recycle cutting fluids and minimize waste through more efficient manufacturing processes will be a key focus.
Another area of innovation will be additive manufacturing integration. While single-spindle machines are traditionally used for subtractive processes, some companies are exploring the hybridization of machining and additive manufacturing capabilities. This integration could allow manufacturers to create complex geometries and lightweight structures that were previously difficult or impossible to achieve with traditional methods. The combination of subtractive and additive processes in a single machine could provide manufacturers with unparalleled design flexibility, enabling the creation of wheel components that are stronger, lighter, and more optimized for performance.
Additionally, advanced material capabilities will continue to expand the scope of single-spindle machines. As industries like aerospace and automotive continue to demand lighter and more durable materials, single-spindle machines will be able to handle a broader range of advanced materials, such as composites, titanium alloys, and high-performance polymers. These materials often require specialized cutting tools and techniques, and the adaptability of single-spindle machines makes them well-suited for these evolving needs.
In terms of global competitiveness, single-spindle machines will remain a crucial tool for manufacturers looking to stay agile and competitive in the global market. As demand for custom parts and products increases, these machines’ ability to handle a wide range of production volumes, from single prototype parts to small or medium production runs, will be essential for manufacturers who must respond quickly to customer demands without sacrificing quality or precision.
As industries move toward more customized and demand-driven production models, the digital transformation of the manufacturing process will further influence the design and operation of single-spindle wheel forming machines. Integration with advanced design software, 3D modeling, and simulation tools will allow manufacturers to optimize the design process and ensure that parts are machine-ready as soon as they are conceptualized. In this context, the ability to easily transition between different part designs and materials, all while maintaining strict quality control, will become a key competitive advantage for businesses utilizing single-spindle technology.
Looking ahead, the future of single-spindle wheel forming machines is tied to the broader trends in industry 4.0, with continuous improvements in automation, data analytics, sustainability, and connectivity. These machines will evolve into smarter, more efficient, and more adaptable systems capable of handling increasingly complex tasks, producing high-quality parts with minimal human intervention, and offering faster production cycles. For manufacturers, the ongoing development of single-spindle machines will provide a pathway to achieving greater precision, higher productivity, and sustainability in the production of wheel components and beyond.
Spinning Wheel Forming Machine
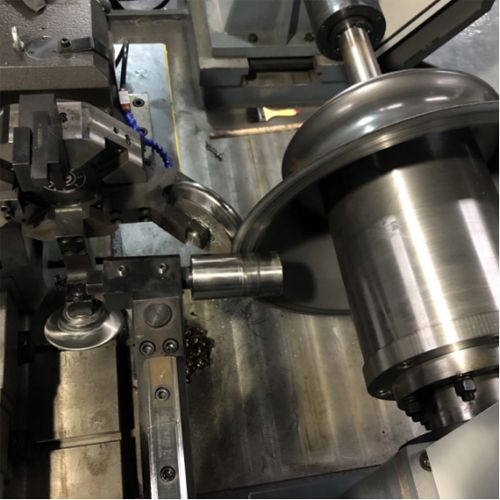
A Spinning Wheel Forming Machine is a specialized type of machinery used in the metal forming industry to shape and form metal discs or plates into wheel-like components through a process known as spinning. This process involves the continuous rotation of a flat disc or sheet of metal, which is gradually shaped into a hollow, circular form by applying pressure using tools that are either stationary or moving along a specific path.
Spinning is a highly versatile and precise method of manufacturing components with circular symmetry, typically used for metallic materials like aluminum, copper, steel, and titanium. It is especially useful for producing parts that require uniform wall thickness and high dimensional accuracy. The spinning wheel forming machine is commonly used in aerospace, automotive, industrial equipment, and consumer products industries, where precision and material strength are key requirements.
The machine typically operates in CNC-controlled settings, meaning that its operations are automated and can be precisely controlled to form complex geometries. This makes it suitable for both high-volume production and custom, low-volume runs where specific designs or specifications are needed.
Key Features of a Spinning Wheel Forming Machine:
- High Precision and Flexibility: The spinning process allows manufacturers to produce high-precision, complex geometries with consistent material thickness across the entire component. CNC-controlled machines can handle varying material types, thicknesses, and complex design features with ease.
- Versatility: The spinning wheel forming machine is capable of producing a wide variety of wheel components, such as motorcycle wheels, automotive wheels, aerospace components, and industrial parts like pulleys and flywheels. The machine can handle both large-diameter and small-diameter parts, making it adaptable to a range of production needs.
- Rotational Speed Control: These machines offer control over the rotational speed of the metal disc being spun. By adjusting this parameter, manufacturers can control the amount of deformation that occurs during the spinning process, ensuring the correct formation of the component.
- Tooling Options: The machine can be equipped with various types of tools, such as forming rollers, burnishing tools, and cutting tools, to achieve the desired shape and finish. These tools can be adjusted or replaced based on the specific requirements of the part being produced.
- Material Handling and Control: The machine typically includes systems for securely holding and rotating the metal disc. Advanced models may also feature automatic material feeding and positioning systems to optimize the production process and minimize waste.
- Reduced Material Waste: The spinning process is highly efficient, as it does not require the removal of large amounts of material like traditional machining. The material is formed and shaped from a disc or sheet without significant waste, making it a cost-effective method for producing parts, especially for components that are made from expensive metals.
Applications of Spinning Wheel Forming Machines:
- Automotive Industry: Spinning wheel forming machines are used in the production of automotive wheel rims, brake discs, and hub components. The spinning process ensures uniformity and strength in these critical parts, which are subject to high levels of stress and pressure.
- Aerospace Industry: In aerospace, spinning machines are used to create turbine components, nose cones, dome-shaped panels, and other critical components that require high precision and high strength-to-weight ratios. The ability to form complex geometries with thin walls and high strength makes spinning an ideal process for aerospace applications.
- Industrial Equipment: For industrial machinery, spinning machines can produce flywheels, gears, and other large, round components that are used in high-torque and high-performance environments. The ability to produce these components with precise tolerances ensures their reliability and performance in demanding applications.
- Consumer Products: Spinning wheel forming machines are also used in the production of decorative metal parts, lighting components, home appliance parts, and even musical instruments. The aesthetic and functional requirements for these products are often met by the versatility and precision of spinning technology.
- Renewable Energy: In renewable energy systems, such as wind turbines, spinning machines may be used to create rotor components or other wheel-like structures that require durability and strength to withstand harsh environmental conditions.
Advantages of a Spinning Wheel Forming Machine:
- High Material Efficiency: Since spinning involves deforming a metal sheet or disc, rather than cutting away material, there is minimal waste. This makes it an efficient and cost-effective manufacturing process, especially for high-value materials like titanium and aluminum.
- Superior Material Properties: Spinning enhances the grain structure of the material, aligning the grains in the direction of the force applied during spinning. This leads to improved strength and durability of the formed components, particularly in terms of fatigue resistance.
- Flexibility for Customization: Spinning machines can easily handle custom designs, offering manufacturers the ability to produce unique or small-batch parts without the need for costly molds or tooling. The process is also well-suited for prototypes or one-off designs that require detailed shaping.
- Surface Quality: The spinning process can produce parts with a smooth, high-quality surface finish. The burnishing tools used in spinning machines help to achieve a clean, polished finish without requiring additional steps like polishing or grinding.
- Cost-Effectiveness for Low-Volume Production: While spinning machines can also be used for high-volume production, they excel in scenarios where low-volume production is required. The quick changeover between different parts and the ability to work on multiple materials and sizes makes spinning an ideal process for small-scale runs.
Challenges of Spinning Wheel Forming Machines:
- Tool Wear and Maintenance: Due to the constant pressure and friction involved in the spinning process, the tools used in the machine can wear out over time. This can lead to maintenance challenges, as tooling must be regularly checked and replaced to maintain the desired quality.
- Limitations on Part Geometry: While spinning is great for forming wheel-like components and other round parts, it is not ideal for complex geometries that involve sharp angles, undercuts, or non-circular shapes. In these cases, additional processes like machining or casting may be needed.
- Material Thickness Limitations: Spinning works best on metals that are not too thick. For very thick materials, additional force may be needed, and the process may become less efficient or even impractical. Spinning is most effective when working with thin to medium-gauge metals.
- Skill Requirement: Operating a spinning wheel forming machine requires a certain level of skill and experience. While CNC technology has made the process more automated, understanding the nuances of material behavior, tool control, and part geometry is crucial for producing high-quality components.
Conclusion:
A Spinning Wheel Forming Machine is an essential tool in the manufacturing of circular, high-precision components across a wide range of industries. Its ability to produce strong, lightweight, and aesthetically appealing parts makes it a go-to technology for industries such as automotive, aerospace, industrial equipment, and consumer goods. The machine’s efficiency, versatility, and ability to create parts with minimal waste make it highly cost-effective, particularly for low-to-medium volume runs and custom designs. As manufacturers continue to demand high-quality, durable parts with complex geometries, the spinning process will remain a critical technique for forming wheel components and other circular structures, continuously benefiting from advancements in CNC automation and material science.
The Spinning Wheel Forming Machine continues to evolve, driven by advancements in automation, materials, and production technology. These machines are expected to integrate even more smart technologies, making them not only more efficient but also capable of handling more complex and varied tasks. With the continued adoption of Industry 4.0 principles, spinning wheel forming machines will increasingly become more connected, allowing manufacturers to monitor performance in real time, optimize production schedules, and predict maintenance needs. The use of sensors and AI could lead to systems that adjust automatically to changes in material properties or part designs, ensuring optimal results even with variations in material quality or part complexity. As manufacturers continue to push the boundaries of customization and precision in wheel and other circular component production, spinning wheel forming machines will play an integral role in achieving these goals. The flexibility and adaptability of the spinning process make it a key technology for industries requiring high-performance components, like aerospace and automotive, where precision and reliability are paramount. Moreover, the ability to work with a variety of materials, including lightweight metals and composites, will allow manufacturers to meet the increasing demand for high-strength, low-weight parts.
As technology advances, spinning wheel forming machines are expected to adopt more advanced material-handling systems, which could improve not only the efficiency of the spinning process but also the quality of the end products. For example, integrating systems for automated material feeding could allow the machine to work continuously without human intervention, leading to even more streamlined and efficient production processes. These systems could work in tandem with vision systems or automated inspection stations to ensure that each component meets precise specifications before it moves to the next stage of production. This integration of AI-driven quality control will help reduce the chances of defects and improve part consistency, all while reducing scrap rates and improving material efficiency.
The growing demand for customized and low-volume production in industries like luxury automotive, motorsports, and aerospace means that spinning wheel forming machines will increasingly be relied upon for high-precision, one-off or small-batch production. These industries often require parts that are uniquely designed for specific applications, and spinning machines are perfect for these needs due to their flexibility. For example, a high-performance automotive manufacturer may need custom wheel components for a special model, or an aerospace company may require a unique structural component that demands both high strength and light weight. With the growing trend toward personalized products and bespoke designs, spinning wheel forming machines provide the ideal combination of precision, adaptability, and efficiency.
The continuous improvement in sustainability will also impact the future of spinning machines. As industries face increasing pressure to adopt environmentally friendly practices, these machines are likely to incorporate energy-efficient technologies and waste-reduction strategies. This could include using regenerative braking systems to recover energy during machine operation, reducing overall power consumption. Additionally, new cutting-fluid technologies or dry machining methods may be employed to minimize waste and reduce the environmental impact of the production process. Recycling systems for metal scrap produced during spinning could further improve sustainability, with machines designed to efficiently separate, collect, and process these materials for reuse.
Moreover, the advancements in advanced materials and alloys will drive spinning wheel forming machines to work with a wider range of metals, including superalloys, high-performance composites, and lightweight materials. These materials are commonly used in sectors like aerospace, where strength-to-weight ratio is critical. Spinning machines will need to adapt to the unique characteristics of these advanced materials, which may involve adjusting the machine’s spinning speed, pressure, or tooling configuration.
The potential integration of additive manufacturing (3D printing) with spinning technology is another exciting area of development. In the future, we might see hybrid systems where spinning is used for forming a base shape, while additive manufacturing is used to add intricate features, reinforcing structures, or specific designs to the part. This hybrid approach would allow manufacturers to take advantage of the speed and precision of spinning while simultaneously benefiting from the design freedom offered by 3D printing.
As smart factories become the norm, spinning machines will not only be connected to each other but also to the entire supply chain. The Internet of Things (IoT) will enable real-time data exchange, providing manufacturers with insights into everything from machine health to inventory levels, and even customer demand. These machines could be part of an interconnected network of devices that work together to optimize the entire production process, reducing lead times, minimizing downtime, and ensuring parts are produced just in time.
Additionally, as robotics continue to advance, spinning machines may see an increased integration of robotic arms and automated tools for loading, unloading, and material handling, improving overall throughput. Robots could also be used for performing secondary operations such as deburring, polishing, or surface inspection, ensuring that the final product meets both functional and aesthetic requirements.
The increased use of digital twins, virtual replicas of machines and processes, will also allow manufacturers to simulate and optimize their spinning operations before they physically occur. This will enable better planning, quicker adjustments to machine settings, and improved forecasting of production timelines. By using digital twins in conjunction with real-time monitoring and predictive analytics, manufacturers can create a fully optimized spinning process, reducing the chances of unexpected downtime and improving production efficiency.
In conclusion, the future of spinning wheel forming machines is bright, with continued advancements in automation, smart manufacturing, sustainability, and material science driving the evolution of these machines. The ability to produce highly specialized, high-performance, and custom components will make spinning machines an integral part of modern manufacturing. By embracing new technologies and adapting to the demands of various industries, spinning wheel forming machines will continue to play a critical role in producing the precision parts needed for everything from aerospace and automotive to consumer goods and renewable energy systems. As industries demand ever-more complex, efficient, and sustainable manufacturing processes, the spinning machine will be at the forefront of this transformation, offering both flexibility and precision in a rapidly changing manufacturing landscape.
Horizontal Wheel Forming Machine
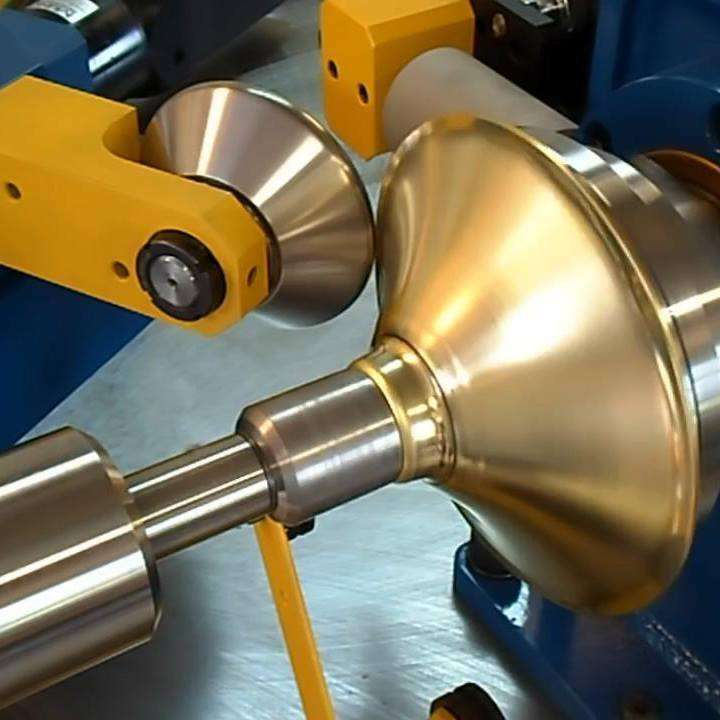
A Horizontal Wheel Forming Machine is a type of equipment used in the manufacturing of wheel-like components through processes such as spinning, forming, and shaping metal or composite materials. Unlike traditional vertical wheel forming machines, which operate with a vertically oriented workpiece, horizontal machines feature a horizontal axis, allowing for different material handling capabilities, unique production processes, and advantages in terms of flexibility and ease of part loading/unloading.
In a horizontal wheel forming machine, the workpiece is typically placed on a rotating spindle or rotary table that spins the metal or material, and tooling is applied to progressively form the part. This configuration is particularly useful for parts that require a high degree of precision, uniformity, and strength. Horizontal machines can be used for both small batch and high-volume production, depending on the specific design of the machine and its capabilities.
Key Features of a Horizontal Wheel Forming Machine:
- Horizontal Spindle Configuration: The primary distinction between horizontal and vertical forming machines is the position of the spindle. Horizontal orientation allows for more stable handling of larger, heavier parts, and facilitates the use of larger tools and dies to form the material.
- Flexible Material Handling: Horizontal machines offer advantages in loading and unloading materials. Because the machine rotates horizontally, it is easier to integrate automated loading/unloading systems that feed the material into the machine and remove the finished part with minimal intervention.
- Efficient Use of Space: While vertical machines may be better suited for certain types of parts or tooling, horizontal machines are generally more space-efficient, especially for larger parts. Their horizontal layout allows for optimized material flow and the efficient use of shop floor space.
- Precision Forming: The precision offered by horizontal machines is crucial for creating high-performance components. With CNC technology (Computer Numerical Control), the machine can be programmed to form complex geometries with high accuracy, making it suitable for critical applications in aerospace, automotive, and industrial sectors.
- Adaptability for Different Part Sizes: Horizontal wheel forming machines are designed to accommodate a range of part sizes. This adaptability allows manufacturers to handle everything from small, intricate wheel components to larger, heavier parts used in industrial equipment or large-scale machinery.
- Rotational Speed Control: Horizontal wheel forming machines are equipped with variable-speed controls to adjust the spinning speed of the workpiece, which allows manufacturers to control the deformation process and achieve the desired wall thickness and shape.
- Multiple Tooling Options: These machines can be equipped with various forming tools that progressively shape the part. Depending on the application, tools like rollers, presses, cutters, and burnishers may be employed to shape, smooth, and finish the part as it rotates.
- Automated Control Systems: Modern horizontal wheel forming machines are equipped with advanced control systems that enable real-time adjustments to operational parameters, improving part quality and consistency across different production runs.
Applications of Horizontal Wheel Forming Machines:
- Automotive Manufacturing: Horizontal wheel forming machines are used in the production of automotive wheel rims, brake drums, flywheels, and other circular components that require high durability and precision. The ability to handle large, heavy materials makes these machines ideal for producing automotive components.
- Aerospace Industry: In aerospace, horizontal machines are used to create turbine disks, wheel hubs, structural components, and other critical parts that need to meet stringent performance and strength requirements. The ability to maintain consistent material thickness and form complex geometries is crucial in this industry.
- Industrial Equipment: Horizontal wheel forming machines are used to produce gears, pulleys, clutch components, and other heavy-duty parts for machinery. Their ability to create durable, high-performance parts in high volumes makes them suitable for industrial applications.
- Renewable Energy: Components used in wind turbines or other renewable energy systems often require high-strength, lightweight properties. Horizontal wheel forming machines are employed to produce parts like rotor components or wind turbine hubs, where precision and material efficiency are crucial.
- Consumer Products: The machine can also be used for creating decorative metal parts, lighting components, kitchen appliance components, and other products that require high aesthetic value and structural integrity.
Advantages of a Horizontal Wheel Forming Machine:
- Improved Part Handling: The horizontal design of the machine makes it easier to handle larger, heavier parts. Automated material handling systems can be seamlessly integrated to improve efficiency and reduce the need for manual intervention.
- Increased Stability for Larger Parts: Horizontal machines provide a stable base for forming larger parts, reducing the risk of wobble or deformation during the spinning process. This stability ensures that the resulting parts are consistent in shape and size.
- Better Tool Access: The horizontal orientation allows for easier access to tooling, which is beneficial for maintenance, adjustments, and part changeovers. This design also allows the operator to work at an ergonomic level, reducing the need for bending or awkward positioning.
- Optimized Material Flow: With the horizontal axis, material can be fed in more easily, and the process flow tends to be more linear, reducing the risk of production bottlenecks. This design is particularly useful in environments that require quick changeovers or high production rates.
- Customization and Flexibility: Horizontal wheel forming machines are adaptable to a wide range of part designs, from basic wheel rims to more complex structural components. The machine’s versatility makes it ideal for manufacturers who need to produce a variety of parts or prototype designs with minimal downtime.
- Efficient Use of Floor Space: Horizontal machines are designed to take up less vertical space, making them a good fit for environments with limited height clearance. This feature is especially important in factories or production lines where vertical space is limited or reserved for other processes.
Challenges of Horizontal Wheel Forming Machines:
- Limited Reach for Some Geometries: While horizontal machines are ideal for certain shapes, there may be limitations in terms of producing more complex geometries or parts with very deep cavities or irregular profiles. In some cases, manufacturers may need to rely on additional processes like machining or casting.
- Tool Wear and Maintenance: As with other metal forming machines, tool wear is a significant consideration in the spinning process. Over time, tooling will need to be replaced or reconditioned, and maintaining tool quality is critical to ensuring consistent part quality. Regular maintenance of the machine itself is also necessary to ensure optimal performance.
- Material Thickness Restrictions: Horizontal wheel forming machines are most effective when working with materials of certain thicknesses. Extremely thick materials may require additional force or specialized tooling, which could increase machine wear or reduce efficiency. This is particularly important when working with high-strength materials like titanium or specialty alloys.
- Initial Setup and Customization: While horizontal machines are highly versatile, they can require more time and resources for custom setups, especially when transitioning between different part designs or materials. The complexity of configuring tooling and machine settings for each unique part can lead to longer setup times compared to simpler processes.
Future Developments in Horizontal Wheel Forming Machines:
As manufacturers continue to push the boundaries of precision, efficiency, and automation, horizontal wheel forming machines are likely to integrate even more advanced technologies. These could include smart sensors for real-time monitoring, predictive analytics for tool wear and maintenance, and robotic systems for enhanced material handling and part inspection. Additionally, as material science continues to evolve, these machines will need to adapt to new materials such as composites, advanced alloys, and 3D-printed materials, offering even more flexibility for a wider range of applications.
The incorporation of AI-based machine learning algorithms will further enhance the machine’s ability to automatically adjust operational parameters, optimize part quality, and reduce energy consumption. Green manufacturing practices, such as energy-efficient motors, waste-reduction systems, and the ability to recycle materials, will play a significant role in the ongoing development of horizontal wheel forming machines, aligning with broader trends in sustainable production.
In summary, the horizontal wheel forming machine is a highly versatile and efficient piece of equipment capable of producing high-precision, durable, and custom components across a variety of industries. Its adaptability, improved part handling, and ability to form larger components make it an essential tool in manufacturing sectors such as automotive, aerospace, industrial equipment, and renewable energy. As manufacturing demands evolve, these machines will continue to integrate new technologies to improve performance, sustainability, and customization.
Horizontal wheel forming machines will continue to evolve alongside advancements in automation, digitalization, and material technology. As manufacturing environments demand increased flexibility, speed, and precision, these machines will incorporate more adaptive control systems, enabling them to respond dynamically to changes in material properties or part specifications. With the rise of smart factories and Industry 4.0, horizontal wheel forming machines will become more integrated into intelligent production networks. This will allow for better coordination with other equipment and systems across the production floor, optimizing production schedules, minimizing downtime, and ensuring high-quality output.
Future models will likely incorporate real-time data analysis and predictive maintenance capabilities, reducing the risk of unexpected machine failures and enhancing operational efficiency. By continuously monitoring parameters such as spindle speed, material flow, temperature, and tool wear, these machines will be able to make autonomous adjustments, ensuring consistent part quality while minimizing waste and energy consumption. The use of advanced sensors and AI algorithms will allow for more accurate and faster adjustments, which will further improve precision and reduce human error.
Moreover, as the demand for customization in production grows, horizontal wheel forming machines will become increasingly capable of producing highly specialized parts with intricate designs. The integration of additive manufacturing (3D printing) into the spinning process will open up new possibilities, allowing manufacturers to combine traditional spinning techniques with additive processes to create complex geometries and optimized structures. This hybrid manufacturing approach will be particularly useful in industries like aerospace and automotive, where lightweight, high-performance components with custom features are in high demand.
The ability to work with a wide variety of materials, including advanced composites, lightweight metals, and new alloys, will further expand the capabilities of horizontal wheel forming machines. As industries push for stronger, lighter, and more durable materials, these machines will need to adapt to meet the evolving demands of material science. Innovations in laser-assisted forming, multi-material forming, and precision tooling will improve the versatility and performance of horizontal wheel forming machines, enabling them to create parts with superior strength-to-weight ratios and other enhanced properties.
In terms of sustainability, the adoption of more energy-efficient and eco-friendly practices will be a key consideration for future horizontal wheel forming machines. Manufacturers will continue to prioritize reducing their environmental impact, incorporating energy-saving technologies, recycling systems for material waste, and greener machining fluids. These machines may also incorporate closed-loop systems to capture and recycle energy from the process, ensuring that less power is wasted and the overall production process becomes more sustainable.
Additionally, as global supply chains become more interconnected and flexible, horizontal wheel forming machines will benefit from greater integration with cloud-based platforms and internet-of-things (IoT) technologies. These systems will allow for the seamless exchange of information between machines, suppliers, and customers, improving visibility across the entire supply chain. Real-time tracking of part production, tooling wear, and inventory management will help manufacturers make data-driven decisions, reduce lead times, and increase overall efficiency.
In summary, the future of horizontal wheel forming machines is promising, with continuous advancements in automation, precision, and material capabilities driving their evolution. These machines will remain at the forefront of manufacturing technologies, offering the flexibility, efficiency, and customization required to meet the challenges of modern industrial production. As industries demand increasingly complex, high-performance parts, horizontal wheel forming machines will continue to play a vital role in creating components for a wide range of applications, from automotive to aerospace, renewable energy, and beyond.
The ongoing evolution of horizontal wheel forming machines will likely involve deeper integration with advanced manufacturing technologies. The convergence of robotics, artificial intelligence (AI), and machine learning will lead to smarter systems that can optimize performance and enhance the flexibility of production. These intelligent systems will not only monitor machine performance but also adapt in real-time to changing materials, part designs, and production requirements.
Key Areas of Future Development:
1. Advanced Robotics Integration
The integration of robotic arms into horizontal wheel forming machines will streamline material handling, reduce labor costs, and improve overall production speed. These robots can handle the loading and unloading of parts, as well as tool changes and secondary operations such as polishing or deburring. In addition, collaborative robots (cobots) could work alongside human operators in a safe, intuitive environment, increasing overall throughput and enhancing flexibility for quick changeovers between different part designs.
2. Machine Learning and Predictive Analytics
By embedding machine learning algorithms, these machines will become capable of analyzing vast amounts of data from sensors, feedback loops, and historical performance to predict when components are likely to fail or require maintenance. This predictive capability will allow manufacturers to perform preventative maintenance before problems occur, reducing unexpected downtime and improving machine longevity. These advanced algorithms will also fine-tune machine parameters for each unique part, ensuring optimal process conditions and improving quality consistency.
3. Advanced Materials and Hybrid Manufacturing
With the continuous development of advanced materials—such as lightweight metals, superalloys, and composites—horizontal wheel forming machines will need to evolve to accommodate these materials’ unique properties. For example, the addition of laser-assisted forming or ultrasonic energy could be used in combination with traditional spinning methods to shape more challenging materials without compromising precision.
Moreover, hybrid manufacturing that combines spinning with additive manufacturing (3D printing) will offer incredible flexibility for creating complex geometries and customized designs. This could involve using spinning for primary shaping while employing 3D printing for adding intricate features or reinforcing structures.
4. Enhanced Automation and Smart Factory Integration
Horizontal wheel forming machines are expected to become integral parts of the larger smart factory ecosystem. As part of a network of interconnected machines, these systems will communicate with each other to ensure that the overall production process is as efficient as possible. Industry 4.0 concepts such as cloud-based production management systems, real-time data analysis, and IoT sensors will enable seamless tracking of materials, parts, and machines, reducing waste, increasing transparency, and allowing for dynamic reconfiguration of production schedules based on demand fluctuations.
5. Energy Efficiency and Sustainability
In the future, horizontal wheel forming machines will be designed with sustainability at the forefront. New technologies, such as regenerative braking systems, will allow machines to recover energy during the spinning process and reuse it, leading to a significant reduction in energy consumption. Additionally, eco-friendly cooling fluids and zero-emission motors will be used to further reduce the environmental footprint of these machines.
Another key area will be waste reduction. The adoption of technologies like closed-loop recycling systems for metal shavings and excess materials will minimize waste, improve material recovery, and reduce the overall environmental impact of manufacturing processes. Machines may be capable of sorting and recycling metal waste on-site, contributing to a circular economy and reducing dependency on raw material extraction.
6. Customization and On-Demand Manufacturing
As customization becomes increasingly important across industries such as luxury automotive, aerospace, and consumer goods, horizontal wheel forming machines will evolve to meet the demand for low-volume, high-variety production. Flexible tooling systems, rapid part changeover capabilities, and the ability to handle a wide range of materials will allow manufacturers to produce highly specialized components without compromising speed or efficiency.
This shift towards on-demand manufacturing means that horizontal wheel forming machines will not only need to process standard parts but also be capable of quickly adjusting to produce custom parts with specific geometry or design specifications. Machine setups will become faster and more intuitive, driven by user-friendly software that allows operators to configure machines for different part designs quickly.
7. Enhanced Surface Finish and Quality Control
The future will see significant improvements in the quality control processes integrated into the machine. Automated inspection systems using vision sensors, laser scanning, and X-ray imaging will monitor the quality of parts in real-time, automatically identifying defects and ensuring consistent product quality. These systems will be linked to the machine’s control system to provide feedback and adjust parameters as needed, ensuring that parts meet the required tolerances and specifications.
Furthermore, advancements in surface finishing technologies, such as laser polishing or electroplating, will allow for parts to be finished without the need for extensive post-processing. This will save time and reduce costs while achieving the desired surface quality and durability required for critical applications.
8. Autonomous and Remote Operation
As machine automation advances, autonomous operation and remote monitoring will become standard features. Operators will be able to monitor and control the machines from anywhere, providing greater flexibility for manufacturers to manage operations across multiple shifts, factories, or even regions. Remote diagnostics and troubleshooting will allow engineers and technicians to address issues before they become major problems, ensuring consistent performance and minimizing downtime.
Conclusion:
The future of horizontal wheel forming machines is shaped by the ongoing evolution of automation, digitalization, materials science, and sustainability. These machines will play a critical role in the next generation of precision manufacturing, offering unparalleled flexibility, efficiency, and adaptability for industries requiring high-performance components. By integrating smart technologies, predictive analytics, and advanced manufacturing techniques, horizontal wheel forming machines will continue to lead the way in producing customized, high-quality, and sustainable parts for a wide range of applications. As manufacturing challenges grow more complex, these machines will evolve to meet the demands of the industries they serve, helping to drive innovation in everything from automotive and aerospace to renewable energy and luxury goods.
Vertical Wheel Forming Machine
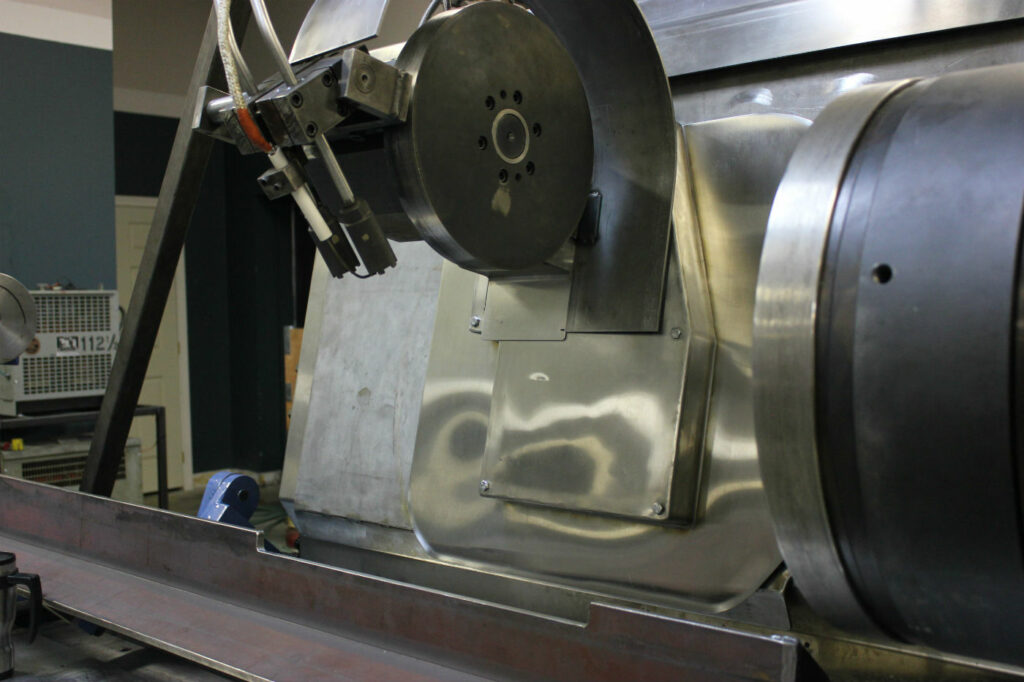
A Vertical Wheel Forming Machine is a type of equipment used for the manufacturing of wheel-shaped components through a spinning process, where the material is deformed into the desired shape using rotational forces. Unlike horizontal wheel forming machines, which operate with a horizontal axis, vertical wheel forming machines have a vertical spindle, where the workpiece is mounted and rotated vertically while the forming tools are applied to shape the part.
This machine is widely used in industries where precise and high-quality circular parts or components with uniform wall thickness are required. The vertical orientation offers certain benefits over other configurations, especially when dealing with specific part sizes, tooling arrangements, and material handling needs.
Key Features of a Vertical Wheel Forming Machine:
- Vertical Spindle Configuration: The workpiece is mounted vertically and rotated along a vertical axis. This setup allows for different material handling and part shaping characteristics compared to horizontal machines.
- High Precision and Uniformity: Vertical wheel forming machines provide exceptional precision in forming wheel-like components. The vertically mounted workpiece allows for controlled and consistent application of force, leading to parts with uniform wall thickness and minimal distortion.
- Compact Design: Vertical machines tend to be more compact than their horizontal counterparts. This can be advantageous in environments with limited space or in production lines where space optimization is essential.
- Automated Tooling Adjustments: Modern vertical wheel forming machines may incorporate CNC (Computer Numerical Control) or servo-driven systems, allowing for easy and quick changes to tooling, workpiece positioning, and operational parameters. This adds flexibility to the production process, enabling rapid setup for different parts.
- Material Handling Ease: The vertical orientation simplifies material handling. Parts can be easily loaded onto the machine using overhead cranes, forklifts, or automated systems, as the weight and orientation of the part align more naturally with the gravitational pull, reducing risks of damage during handling.
- Efficient Workpiece Support: The vertical design allows for optimal support during the spinning process. The weight of the part is typically distributed evenly across the machine’s axis, which helps maintain stability during high-speed rotations.
- Tooling Access: In vertical machines, tooling can be easily adjusted and maintained, with clear visibility of the workpiece. The machine’s configuration allows for quick inspection and modification of tooling setups without compromising part accuracy.
- Customization for Part Size and Shape: Vertical wheel forming machines can be easily customized to produce a wide range of part sizes and shapes. The flexibility of tooling, combined with adjustable spindle speeds, makes these machines suitable for a variety of wheel components, including those used in automotive, aerospace, and industrial equipment sectors.
Applications of Vertical Wheel Forming Machines:
- Automotive Industry: Vertical wheel forming machines are often used in the production of automotive wheels, brake drums, and flywheels. The precision provided by these machines ensures that the critical characteristics of the components, such as uniform thickness and high strength, are met for automotive applications.
- Aerospace Industry: The need for lightweight and high-strength materials in aerospace manufacturing means that vertical wheel forming machines are used to produce turbine disks, engine components, and other specialized parts that require high-performance characteristics and precise geometries.
- Industrial Equipment Manufacturing: Components such as gears, pulleys, clutch plates, and compressor wheels are often produced using vertical wheel forming machines. The uniformity and precision achieved by the vertical setup ensure that these parts meet the rigorous demands of industrial applications.
- Energy Industry: For the renewable energy sector, particularly in wind power, vertical wheel forming machines can be used to produce components for wind turbines, including rotor hubs and gearboxes. The ability to form strong yet lightweight parts is crucial in renewable energy systems.
- Consumer Goods: Components such as decorative metal parts, lighting fixtures, and kitchen appliance parts can be created using vertical wheel forming machines, offering both aesthetic quality and structural integrity.
Advantages of a Vertical Wheel Forming Machine:
- Space Efficiency: Vertical machines are typically more space-efficient than horizontal machines. This makes them ideal for workshops or production environments with limited space, or for applications where space optimization is important.
- Improved Part Handling: The vertical spindle configuration makes it easier to load and unload materials, especially larger or heavier parts. Automated material handling systems can be used effectively in conjunction with vertical machines, allowing for high-speed production without manual intervention.
- Increased Precision: The vertical design helps ensure a more precise forming process. The controlled application of force, coupled with the stable alignment of the spindle, minimizes variations in wall thickness, leading to more uniform and consistent parts.
- Operator Visibility and Accessibility: Vertical machines allow operators to work at an optimal height, providing good visibility of the workpiece. This makes it easier to monitor the forming process and inspect parts for any defects or inconsistencies.
- Tooling Flexibility: Vertical wheel forming machines often support a variety of tooling configurations, allowing manufacturers to easily switch between different part types, materials, or production processes. Quick-change tooling systems can be integrated to streamline part changeovers and reduce downtime.
- Lower Energy Consumption: The vertical orientation and simpler design tend to reduce overall energy consumption during the forming process. By minimizing friction and maintaining more consistent material flow, the machine requires less power to achieve optimal forming conditions.
- Simplified Maintenance: The vertical configuration makes maintenance easier since the work area is more accessible. Components such as the spindle, tooling, and other mechanical elements can be easily serviced, reducing downtime and maintenance costs.
- Customizable Spindle Speed and Force: Vertical wheel forming machines often come equipped with variable-speed spindles and adjustable pressure systems, allowing for customization based on the material type and specific part requirements. This flexibility ensures the machine can produce a wide variety of components, from soft materials to high-strength alloys.
Challenges of a Vertical Wheel Forming Machine:
- Limited Reach for Certain Geometries: While vertical wheel forming machines excel at producing wheel-shaped components, they may face limitations when forming parts with complex or intricate geometries that extend beyond the vertical axis. These types of components may require more specialized equipment or additional processes.
- Tool Wear: As with all metal forming processes, the wear and tear on the tooling can affect part quality and machine performance. Vertical wheel forming machines often require regular maintenance and tool replacements to ensure consistent results.
- Capacity for Large Parts: While vertical machines are excellent for medium-sized parts, they may face limitations when handling extremely large parts. In such cases, a horizontal machine or a larger custom configuration might be more suitable.
- Material Limitations: Some materials with extreme hardness or toughness may present challenges for vertical wheel forming machines, as these materials require more powerful machines or specific tooling arrangements to achieve proper deformation without damaging the machine.
Future Developments in Vertical Wheel Forming Machines:
- Automation and Smart Technologies: The integration of robotics, IoT sensors, and machine learning algorithms will make vertical wheel forming machines more intelligent and capable of autonomous operation. Real-time adjustments and predictive maintenance features will enhance machine efficiency and part quality.
- Hybrid Manufacturing: Vertical wheel forming machines may evolve to incorporate additive manufacturing or laser-assisted forming technologies, allowing for more complex parts to be created directly on the machine. This will enhance the machine’s versatility and reduce the need for multiple processes.
- Energy Efficiency: As sustainability becomes a key concern in manufacturing, vertical wheel forming machines will incorporate energy-saving systems and waste-reduction technologies, reducing their environmental impact while maintaining high performance.
- Material Advancements: The machines will evolve to handle a broader range of advanced materials such as composites, superalloys, and 3D-printed metals, expanding their use in industries like aerospace, medical devices, and renewable energy.
Conclusion:
Vertical wheel forming machines are essential tools in the production of high-precision, high-performance wheel-shaped components across various industries. Their space efficiency, precision, and versatility make them ideal for applications in automotive, aerospace, industrial equipment, and energy. As technology progresses, the integration of advanced automation, smart systems, and sustainable practices will make vertical wheel forming machines even more efficient and adaptable, ensuring their continued importance in the future of manufacturing.
The future of vertical wheel forming machines will continue to evolve with the integration of more intelligent automation, advanced material handling systems, and sustainable manufacturing practices. The growing demand for high-precision and customized parts, along with the need for increased production efficiency, will drive the development of machines capable of greater flexibility and adaptability. With the rise of Industry 4.0, these machines will be connected to smart networks, enabling manufacturers to monitor performance, gather data in real time, and optimize production schedules dynamically. The incorporation of artificial intelligence (AI) will enable vertical wheel forming machines to analyze production trends, predict failures, and adjust parameters automatically, resulting in better quality control and reduced downtime.
As more industries require lightweight, stronger, and high-performance materials, vertical wheel forming machines will be designed to handle advanced composites, superalloys, and other high-strength materials. These materials often pose challenges in terms of formability and tool wear, but with continuous improvements in tooling technology and machine capabilities, manufacturers will be able to produce more complex parts while maintaining high-quality standards. The use of hybrid manufacturing techniques, such as combining additive manufacturing with traditional spinning, will allow for the production of parts with intricate geometries and high precision, reducing material waste and enhancing the ability to meet custom specifications.
The trend towards sustainability will also shape the future of vertical wheel forming machines. In response to increasing environmental concerns, manufacturers will incorporate energy-efficient systems to reduce power consumption. This could include advanced features like regenerative braking, where the machine can capture and reuse energy during the forming process. Additionally, the implementation of closed-loop cooling systems will reduce water and fluid waste, while eco-friendly materials and lubricants will help minimize the environmental impact of production.
The demand for rapid prototyping and short-run manufacturing will lead to even greater flexibility in vertical wheel forming machines. These machines will allow for quick changeovers between different part types, making them ideal for industries that require low-volume production runs. The automation of tooling adjustments and adaptive process controls will further reduce setup times, enabling quicker transitions between different product lines and minimizing production delays.
In the automotive and aerospace sectors, where weight reduction is critical for improving performance, vertical wheel forming machines will continue to play a pivotal role in manufacturing lightweight components such as brake drums, flywheels, and turbine disks. The ability to produce parts with consistent wall thicknesses and precise geometries will be crucial in meeting the rigorous standards of these industries.
As material science continues to advance, vertical wheel forming machines will also be adapted to handle newer, more challenging materials. The integration of laser-assisted forming or ultrasonic vibration in the spinning process could be explored further to overcome the challenges posed by hard-to-form materials. Additionally, multi-material forming technologies, where different materials are combined during the forming process, will open up new possibilities for producing more complex and specialized components.
Vertical wheel forming machines will also be more integrated with robotics and AI-driven systems to enhance the precision and automation of the forming process. Robotic arms will assist in material handling, part manipulation, and secondary operations, such as trimming, polishing, and inspection, while vision systems will provide real-time quality control to detect and correct defects during production. These advancements will not only improve part quality but also increase throughput and reduce human error.
Moreover, the introduction of cloud-based monitoring and remote diagnostics will enable operators to track the performance of vertical wheel forming machines from anywhere in the world. This will allow for real-time troubleshooting, ensuring that any issues are addressed promptly and minimizing production downtime. Manufacturers will also be able to collect and analyze data over time to identify areas for improvement, further enhancing operational efficiency.
As the industry moves towards more customized and high-performance parts, the future of vertical wheel forming machines will be defined by their ability to adapt to diverse production needs. With ongoing improvements in machine learning, automation, and material capabilities, these machines will continue to be a cornerstone in the manufacturing of complex, high-precision components across a wide range of industries. The constant push for sustainability, efficiency, and innovation will keep shaping the design and functionality of vertical wheel forming machines, ensuring that they remain at the forefront of modern manufacturing processes.
The continuous evolution of vertical wheel forming machines will push boundaries in various aspects of manufacturing, from design to performance. With an increased focus on multi-material capabilities, these machines could seamlessly integrate a variety of metals, composites, and specialized alloys in a single forming process, creating parts with unique properties that were previously difficult or impossible to achieve. This could be particularly beneficial for industries like automotive and aerospace, where hybrid materials are becoming a significant trend for reducing weight while maintaining strength and durability.
As manufacturers increasingly seek to stay competitive in a global marketplace, there will be a greater emphasis on machine versatility. Vertical wheel forming machines will become more adaptable to different shapes and sizes, enabling production flexibility without sacrificing efficiency. This shift will be facilitated by advanced control systems that allow operators to easily adjust parameters, such as speed, force, and temperature, for varying material properties or production requirements. These systems will not only offer ease of use but will also improve the repeatability and consistency of the forming process, making it easier to produce high-quality parts at scale.
In addition, the integration of additive manufacturing (AM) techniques into vertical wheel forming machines will provide new avenues for part design. As 3D printing continues to mature, hybrid systems that combine both additive and subtractive processes will allow for the creation of highly intricate parts with complex internal structures that are difficult to achieve through traditional forming methods. By layering material in precise patterns and forming the outer contours with spinning or pressing, manufacturers will be able to produce near-net-shape components that require minimal finishing and thus reduce overall material usage and waste.
Data analytics will play an even more crucial role in optimizing the performance of these machines. As Industry 4.0 takes hold, real-time data from vertical wheel forming machines will be processed using machine learning algorithms to predict and mitigate potential issues before they occur. Predictive maintenance will be a major part of this advancement, allowing manufacturers to anticipate wear on critical components like spindles or tooling, reducing downtime and enhancing production uptime. This approach will also make it possible to fine-tune the forming process to optimize for material flow, part geometry, and process efficiency, reducing defects and improving part quality.
Furthermore, as part of the broader trend toward sustainability, energy-efficient designs will become a focal point for manufacturers. This could include the development of more efficient motors, energy recovery systems, and smart cooling technologies that minimize power consumption and reduce the carbon footprint of production operations. These innovations will allow manufacturers to meet stricter environmental regulations while maintaining high productivity and competitive pricing.
The future of vertical wheel forming machines will also be influenced by global supply chains and the increasing need for localization of production. As demand for on-demand manufacturing and custom parts rises, manufacturers will increasingly look to adopt flexible and agile systems that can quickly adapt to changing market needs. Vertical wheel forming machines, with their ability to be reconfigured for different part types, will play a key role in enabling this transition. Their ability to rapidly change tooling and adjust process parameters will make them ideal for industries focused on low-volume, high-mix production.
User experience will also become a more significant focus, with manufacturers developing more intuitive interfaces and controls. These advancements will allow less experienced operators to work with high precision and accuracy, making vertical wheel forming machines more accessible across industries and reducing the learning curve for new operators. With intuitive touchscreen interfaces, augmented reality (AR) for machine setup and diagnostics, and voice commands for hands-free operation, these machines will become more user-friendly and conducive to streamlined operation.
In the research and development space, vertical wheel forming machines will continue to be tested and optimized for use in specialized industries, such as medical device manufacturing. As the demand for precision parts in fields like orthopedic implants, prosthetics, and surgical instruments increases, these machines will be adapted to handle the delicate balance between biocompatibility, strength, and lightweight design. Customization and adaptability in forming processes will become key factors in producing these highly specialized components.
Lastly, as digital twins and advanced simulation tools become more prevalent in manufacturing, vertical wheel forming machines will be able to run simulated production scenarios before physical production begins. These virtual models will allow engineers to optimize processes in a digital environment, improving production planning, tooling design, and material selection. The incorporation of virtual reality (VR) will further enhance this by providing operators with a more interactive, hands-on experience, allowing them to visualize and simulate machine setups in real time.
In summary, the future of vertical wheel forming machines will be defined by a synergy of advanced materials, intelligent automation, sustainability, and user-centric design. These machines will continue to be indispensable in producing high-precision, high-performance parts across various industries. With ongoing developments in technology and manufacturing techniques, vertical wheel forming machines will remain at the forefront of innovation, helping manufacturers meet the challenges of an increasingly complex and demanding global market.
The trajectory of vertical wheel forming machines will not only focus on technological and process advancements but also on adapting to the changing needs of global industries. As globalization and digital transformation reshape how manufacturers approach production, these machines will evolve to meet more specific customer demands, from mass customization to shorter lead times.
One of the most notable trends will be the increasing demand for precision and quality in micro-manufacturing. Industries like electronics and medical technology will require vertical wheel forming machines capable of producing microscale components with extreme precision. The ability to form tiny, intricate features such as thin-walled components or small internal geometries will require the integration of advanced micro-forming technologies. Vertical wheel forming machines will need to become more adaptable in terms of tooling, force application, and speed control to meet these nano-scale production challenges.
As the push for automation intensifies, robotic assistance will be even more deeply integrated into vertical wheel forming processes. For example, collaborative robots (cobots) could work alongside operators, assisting in loading/unloading parts, checking dimensions, or even performing secondary processes like polishing or deburring. This will not only improve the speed of production but also enhance worker safety by reducing physical strain or exposure to hazardous processes.
Another emerging trend is the use of integrated inspection systems within vertical wheel forming machines. With the increasing complexity and precision of parts being produced, inline quality control systems will be incorporated to inspect components during the forming process, ensuring that dimensional accuracy and surface quality are maintained throughout the entire production run. Automated vision systems and laser scanning technologies could be used to measure critical dimensions in real-time, allowing for automatic adjustments to the process to correct defects before they result in part failures or waste.
Additive manufacturing and vertical wheel forming could also converge in the future to create hybrid machines. These systems would allow manufacturers to produce metal parts using a combination of traditional spinning and 3D printing techniques, providing the flexibility to create complex internal structures or features that would be difficult to form with spinning alone. This hybrid manufacturing would significantly reduce material usage and the need for extensive secondary operations, further streamlining production and reducing costs.
In addition to additive manufacturing, the combination of spinning with other advanced manufacturing techniques such as electrical discharge machining (EDM), laser cutting, or water jet cutting could lead to a more integrated approach to part production. These hybrid systems would allow for parts to be spun to their near-net-shape and then finished with precision cutting or ablation methods, creating a seamless workflow from initial forming to final part.
Another critical aspect of future developments in vertical wheel forming machines will be their digital integration. The machines will be increasingly connected to cloud-based platforms that allow for remote monitoring, real-time performance analysis, and predictive maintenance. Data collected from the machines will be analyzed to track performance trends, identify areas for improvement, and forecast potential failures before they occur. This smart factory approach will enable manufacturers to optimize machine uptime and part quality while reducing operational costs.
As industries move toward sustainability and more environmentally conscious practices, vertical wheel forming machines will be designed to reduce their carbon footprint and energy consumption. The push for energy-efficient designs will drive the development of more efficient power systems, the use of regenerative energy technologies, and energy recovery systems that help minimize the environmental impact of production processes. Further innovations in eco-friendly materials, such as biodegradable lubricants or greener materials that reduce waste or toxicity, will be implemented to comply with stringent environmental regulations.
At the same time, advancements in material recycling will be another key focus. Vertical wheel forming machines may be designed to handle recycled metals or materials that would otherwise go to waste, helping manufacturers minimize their environmental footprint. These machines could be equipped with technology to process scrap metal, ensuring that no valuable material is lost in the manufacturing process, thus contributing to a more circular economy.
The next generation of vertical wheel forming machines will also need to address the growing demand for personalized manufacturing. As more industries move toward bespoke production runs, where each part may be slightly different from the next, vertical wheel forming machines will have to provide the flexibility to adjust quickly and efficiently to these requirements. Flexible tooling systems, adaptive forming technologies, and software-driven automation will allow machines to produce custom parts in small batches without sacrificing cost-efficiency or lead time.
In the construction sector, vertical wheel forming machines could be used to create specialized parts for infrastructure projects, such as tunnels, bridge components, or reinforced piping. As the demand for durable and high-performance materials increases in the construction industry, these machines will play an important role in providing parts that meet stringent performance and safety standards.
Looking ahead, the global shift toward digitalization will mean that vertical wheel forming machines will be able to share information across the entire production network. Digital twins, a virtual representation of the physical machine, could be created to simulate, monitor, and optimize the performance of machines in real-time. Manufacturers will use this digital replica to monitor performance remotely, test new production techniques virtually, and predict potential issues before they arise, reducing costly downtime and improving overall productivity.
As artificial intelligence (AI) and machine learning (ML) become increasingly integrated into manufacturing systems, vertical wheel forming machines will use these technologies to optimize operations. These AI-driven systems can be used to predict the best process parameters, adapt the machine settings for different materials, and ensure quality control by flagging any potential defects in the forming process. AI algorithms could also adjust parameters in real-time to compensate for variations in material quality or environmental conditions, ensuring consistent and high-quality output.
In conclusion, vertical wheel forming machines are poised to undergo significant advancements in both technology and application. The combination of automation, data-driven analytics, hybrid manufacturing, sustainability efforts, and customization will propel these machines to meet the evolving needs of industries ranging from automotive and aerospace to medical devices and construction. As the manufacturing landscape continues to change, vertical wheel forming machines will adapt and become even more integral to the production of precision parts, offering higher efficiency, greater flexibility, and improved environmental performance.
EMS Metalworking Machines
We design, manufacture and assembly metalworking machinery such as:
- Hydraulic transfer press
- Glass mosaic press
- Hydraulic deep drawing press
- Casting press
- Hydraulic cold forming press
- Hydroforming press
- Composite press
- Silicone rubber moulding press
- Brake pad press
- Melamine press
- SMC & BMC Press
- Labrotaroy press
- Edge cutting trimming machine
- Edge curling machine
- Trimming beading machine
- Trimming joggling machine
- Cookware production line
- Pipe bending machine
- Profile bending machine
- Bandsaw for metal
- Cylindrical welding machine
- Horizontal pres and cookware
- Kitchenware, hotelware
- Bakeware and cuttlery production machinery
as a complete line as well as an individual machine such as:
- Edge cutting trimming beading machines
- Polishing and grinding machines for pot and pans
- Hydraulic drawing presses
- Circle blanking machines
- Riveting machine
- Hole punching machines
- Press feeding machine
You can check our machinery at work at: EMS Metalworking Machinery – YouTube
Applications:
Flange-punching
Beading and ribbing
Flanging
Trimming
Curling
Lock-seaming
Ribbing