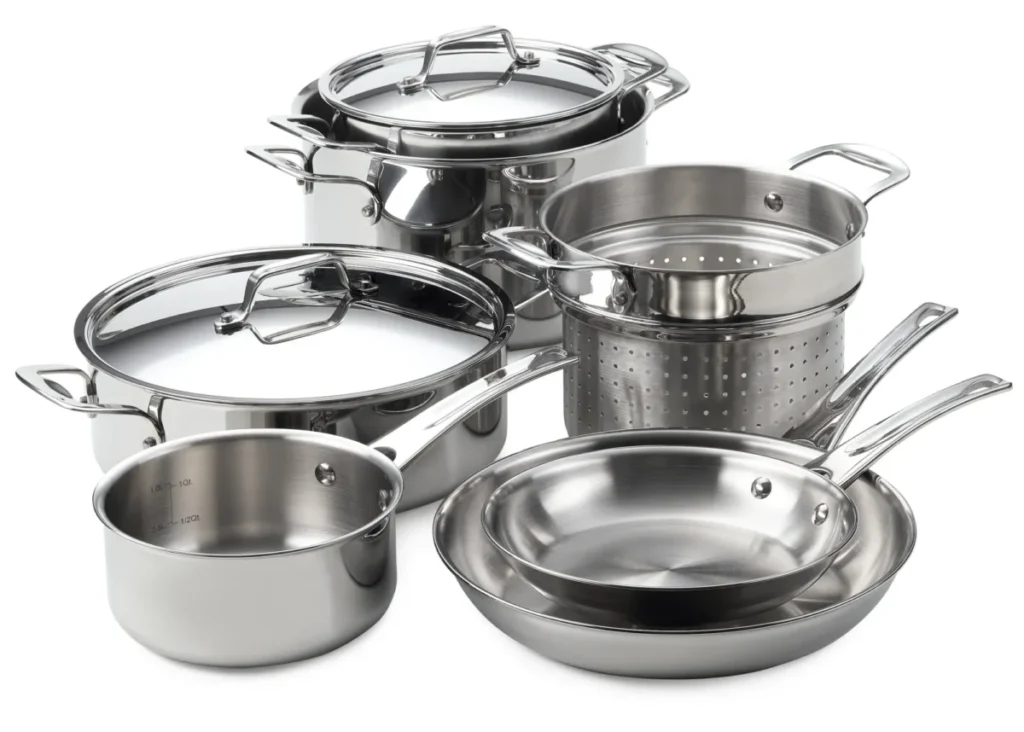
Sheet Metal Roasting Pan Production Machine: the process of Sheet metal cookware production machinery production, generally involves several stages of forming, shaping, and finishing metal to produce items like pots, pans, lids, and other kitchenware. Below is a breakdown of common machines and tools used in the manufacturing process:
Primary Machinery for Sheet Metal Cookware Production
1. Metal Cutting Machines
- Shearing Machines: For cutting large metal sheets into smaller blanks.
- Laser Cutters / Plasma Cutters: For precision cutting, especially for complex shapes or designs.
2. Stamping & Blanking Presses
- Used to cut the metal blanks and form them into rough cookware shapes.
- Hydraulic or mechanical presses are common.
3. Deep Drawing Presses
- This is a key process where flat blanks are drawn into deep shapes (e.g., pots, pans).
- Hydraulic deep drawing machines are commonly used for consistent force and quality.
4. Trimming Machines
- After deep drawing, excess material is trimmed to finalize the shape.
- Often automated to improve precision and efficiency.
5. Spinning Machines (for round cookware)
- CNC metal spinning lathes are used to form and finish circular cookware like bowls or frying pans.
- Ideal for stainless steel and aluminum cookware.
6. Annealing Furnace
- Used to soften the metal between forming stages to reduce stress and cracking.
- Controlled heating and cooling process.
7. Polishing / Buffing Machines
- For surface finishing—makes cookware shiny and smooth.
- Includes automatic polishing machines and belt grinding machines.
8. Surface Coating/Anodizing Line
- For non-stick coatings (Teflon), enamel coating, or anodizing (especially for aluminum cookware).
- Involves cleaning, spray coating, and baking ovens.
9. Riveting Machines
- For attaching handles and knobs to cookware.
10. Induction Base Welding Machine
- Used for applying stainless steel or ferromagnetic layers to the bottom of aluminum cookware (for induction cooking compatibility).
11. Leak Testing Machines
- Ensures cookware (especially pressure cookware) is properly sealed.
Additional Equipment
- CNC Press Brakes: For bending and shaping handles or brackets.
- Spot Welding Machines: For joining small parts.
- Hydraulic Riveters: For ergonomic and high-speed handle assembly.
Optional Automation
- Robotic arms for loading/unloading.
- PLC-controlled production lines for high-volume, repeatable output.
In sheet metal cookware production, the process starts with cutting raw metal sheets—typically stainless steel or aluminum—into appropriately sized blanks using shearing machines or laser cutters for precision. These blanks are then moved to stamping or blanking presses, where they are shaped roughly into the initial cookware form. Next comes deep drawing, which is a critical forming process that stretches the metal into a deeper shape like a pot or pan using a hydraulic press. Depending on the complexity, this might require multiple draws with intermediate annealing, where the metal is heated in a furnace to relieve stress and prevent cracking.
Once the basic shape is formed, trimming machines remove excess material to get a clean edge. For round cookware, CNC metal spinning machines are often used to refine the shape and form features like flared rims or rounded bases. After shaping, the cookware goes through surface treatment. Polishing and buffing machines smooth out the metal, giving it that shiny, reflective finish you see on store shelves. If the cookware is non-stick, it proceeds to a coating line where it’s cleaned, sprayed with PTFE or ceramic coatings, and baked in curing ovens.
For cookware meant for induction cooking, an induction base—often a disc of stainless steel—is welded to the bottom using high-frequency welding machines. Handles and knobs are attached next, typically by riveting or spot welding, depending on the design. At this point, the cookware is tested for quality—leak testing is common for pressure cookware to ensure proper sealing and durability. Some production lines may include robotic arms for loading, unloading, or polishing to increase throughput and consistency.
The entire process can be semi-automated or fully automated, depending on production volume and investment. Advanced setups use PLC-controlled systems with robotic integration, allowing for continuous, high-speed production with minimal manual handling. The combination of forming, finishing, coating, and assembly ensures cookware is not only functional but also durable and aesthetically pleasing.
Following the main production and assembly, packaging becomes the final critical step before cookware is ready for distribution. First, each finished item is cleaned thoroughly—either manually or via ultrasonic washers—to remove any residue from polishing compounds or coating materials. Once clean, items may undergo a final inspection, where they are checked visually and sometimes by automated vision systems for defects like scratches, dents, coating inconsistencies, or incomplete rivets.
Next, barcodes or branding are often applied. This might include laser engraving for logos, pad printing for decorative elements, or labeling with product details. Some high-end cookware lines include serial numbers or QR codes to track manufacturing batches, which is useful for both marketing and quality control.
Packaging depends on the target market and branding. Automated packing machines can wrap cookware in protective film, insert them into cardboard boxes, and even shrink-wrap multi-piece sets. Eco-conscious manufacturers often use recyclable or minimal packaging, which requires precision fitting to avoid damage during transit. Inner packaging may include instruction manuals, warranty cards, and sometimes promotional material or recipe booklets.
The packaged cookware then moves to palletizing stations, where robotic arms or automated stackers organize boxes onto pallets for efficient shipping. Some lines are integrated directly with warehouse management systems, allowing real-time inventory updates as items are packed and labeled.
In a high-efficiency plant, the entire process—from metal sheet to boxed product—can be integrated into a continuous flow, with conveyors connecting each station. This ensures minimal downtime and faster turnaround times, especially important for fulfilling large retail or export orders.
Throughout the process, safety and environmental considerations are key. Fume extraction systems are used near coating and polishing stations, noise levels are controlled with acoustic enclosures around heavy presses, and water from cleaning processes is filtered and reused when possible. Energy-efficient hydraulic systems and inverter-controlled motors also help reduce operational costs and environmental footprint.
Continuing from there, maintenance and quality assurance are two pillars that sustain long-term efficiency and consistent product standards in cookware manufacturing. Every machine on the line—from deep drawing presses to coating ovens—requires a regular preventive maintenance schedule. This includes checking hydraulic fluid levels, inspecting press tool wear, replacing spinning lathe tips, calibrating welding and riveting tools, and ensuring the coating spray guns are delivering even and accurate layers. Most modern machinery includes built-in diagnostics or can be integrated into a central monitoring system (often via Industry 4.0 protocols) to alert operators before issues escalate into breakdowns.
Tooling management is especially crucial. In deep drawing, trimming, and stamping, dies and molds undergo wear and tear and must be reconditioned or replaced to maintain product precision. Tool changes need to be efficient to avoid extended downtime, and manufacturers often keep duplicate sets ready to swap in during multi-shift operations.
On the quality assurance side, standard operating procedures (SOPs) are implemented at every major stage—post-forming, post-polishing, post-coating, and pre-packing. For coated cookware, crosshatch adhesion tests and hardness tests (like pencil hardness) are performed regularly. In some factories, a salt spray chamber is used to simulate corrosion resistance, especially important for stainless steel products. For anodized aluminum items, oxide layer thickness is checked with digital micrometers or colorimetric sensors.
Traceability systems are becoming more common, with software tracking each unit’s production data—what batch of sheet metal was used, which press formed it, when it was coated, and by whom it was assembled. This is especially useful for handling returns or quality complaints and is often a requirement when exporting to regulated markets like the EU or North America.
Training for operators is another critical layer. Skilled workers ensure better output, catch problems early, and reduce waste. Training includes machinery operation, tool changeover techniques, quality control procedures, safety protocols, and basic troubleshooting. Some facilities even implement lean manufacturing practices and continuous improvement programs like Kaizen to boost efficiency, minimize scrap, and optimize the workflow over time.
Sheet Metal Pizza Pan Production Machine
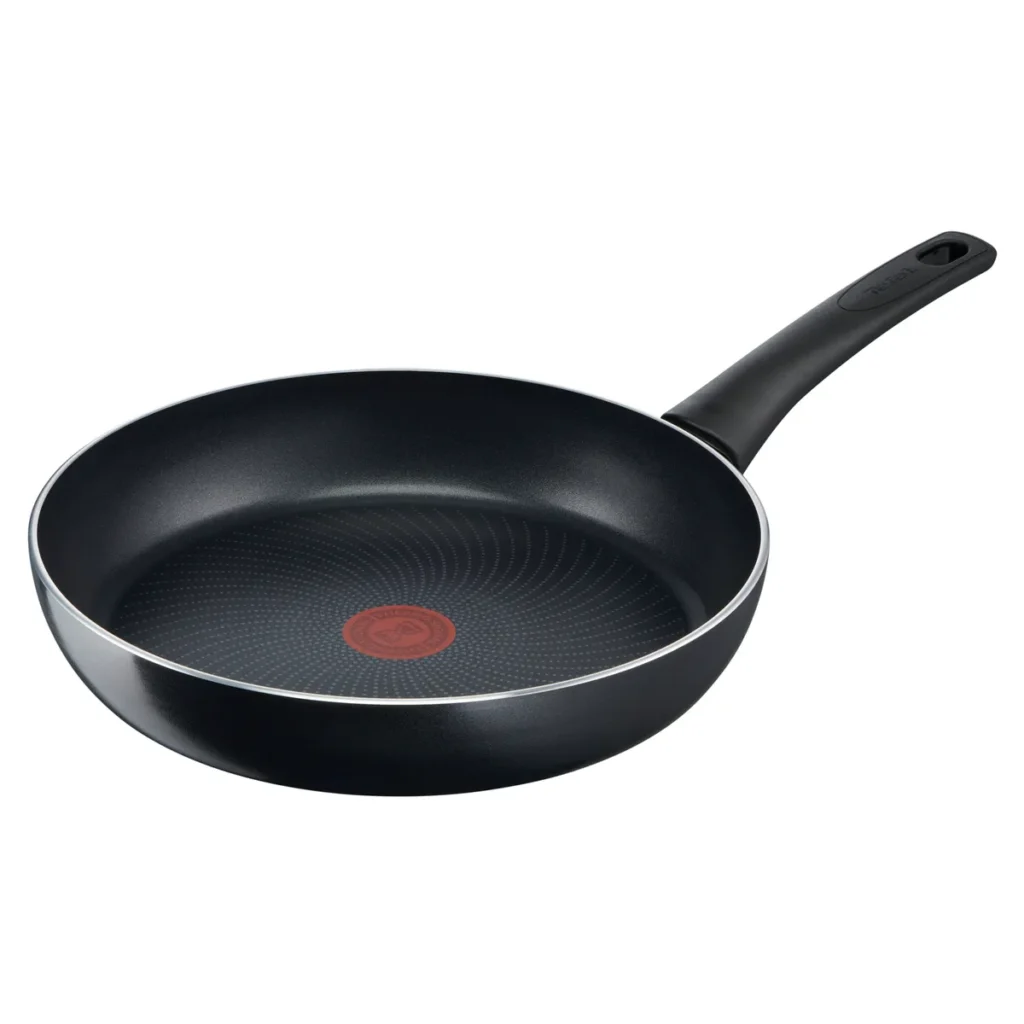
A sheet metal pizza pan production machine is typically a specialized setup or integrated line designed to manufacture round, shallow pans used in baking pizza. While the process is simpler than deep cookware like pots, it still requires precise forming, consistent quality, and a smooth finish. Here’s how the machinery and flow typically look:
Pizza Pan Manufacturing Process & Machinery
1. Metal Sheet Decoiler & Feeder
- Raw sheet metal (usually aluminum or aluminized steel) is loaded in rolls.
- A decoiler unrolls the sheet, and a servo feeder pushes the sheet into the cutting or blanking station.
2. Blanking Press
- A mechanical or hydraulic press equipped with a die cuts round blanks.
- These blanks are the flat discs that will be formed into pans.
3. Shallow Drawing or Stamping Machine
- The blank is transferred into a shallow drawing die where it is formed into the basic pizza pan shape.
- This could be done in a single stroke or progressive dies depending on pan design (with or without ridges or perforation).
4. Trimming Machine
- Ensures the outer edge of the pan is clean, uniform, and smooth.
- Especially important for pans that will be stacked or nested.
5. Beading / Rim Forming Machine
- For pans with reinforced edges or rolled rims, this machine bends and compresses the rim for structural strength and safety.
- Optional but common for commercial-grade pans.
6. Perforation Press (Optional)
- For “crisper” pizza pans, this machine punches holes into the bottom of the pan.
- Increases airflow and helps with crispier crusts during baking.
7. Surface Polishing / Brushing Machine
- Depending on product grade, a brushing or polishing unit is used to give the pan a clean finish or brushed texture.
- Some pizza pans are also anodized or coated, which may follow here.
8. Non-stick Coating Line (Optional)
- If the pan is to be coated, it’s cleaned, spray-coated with a non-stick compound like PTFE or silicone, and passed through a curing oven.
- Coated pans also require dust-free environments for clean adhesion.
9. Stacking and Packing
- Finished pans are automatically stacked and optionally packed using shrink-wrap machines or inserted into boxes for distribution.
Machine Types Commonly Used
- Hydraulic or Mechanical Presses (25–100 tons depending on pan size)
- Servo Feeders and Straighteners
- Rotary Trimming Machines
- CNC Spinning Machines (for specialty edges or designs)
- Rim Rolling Machines
- Spray Coating Booths and IR Ovens
- Vibratory Finishing / Tumbler (for de-burring or softening edges)
Materials Used
- Aluminum (lightweight, good heat conductivity)
- Aluminized Steel (durable, often used in commercial kitchens)
- Hard-anodized Aluminum (premium pans)
Final Notes
A pizza pan line is relatively compact and modular, especially if you’re focusing on only one or two sizes. Most manufacturers custom-build or integrate machines depending on capacity—say, 500–2000 pans/hour. Automation is feasible and often cost-effective for large runs.
Sure thing. In a sheet metal pizza pan production setup, the process starts with coiled sheet metal—typically aluminum or aluminized steel—being fed into the system via a decoiler and a straightening feeder. The flat sheet is then directed into a press fitted with a circular blanking die, where round blanks are cut out. These blanks are what eventually become the pizza pans. From there, the blanks move to a shallow drawing or stamping press where they’re formed into the recognizable pan shape with a smooth base and shallow walls. This is usually done in a single stroke or sometimes with a progressive die setup if more detail is needed.
After forming, the outer rim of the pan often needs trimming to remove excess material and ensure the edge is perfectly round and smooth. For pans requiring additional structure, a rim forming or beading machine is used to roll or curl the edge, making it sturdier and safer to handle. Some pizza pans, especially those meant for professional kitchens, might go through a perforation press at this stage—this adds small holes to the bottom to improve airflow and create a crispier crust during baking.
Once the shape is finalized, the pans may pass through a polishing or brushing machine to enhance surface finish or achieve a specific texture. If a non-stick or hard-anodized surface is needed, the pans are cleaned, coated using automated spray booths, and then sent through a curing oven where the coating is baked onto the surface. For hard-anodized pans, an electrochemical process is used to thicken the natural oxide layer on the aluminum, improving durability and corrosion resistance.
At the end of the line, the pans are cooled, stacked, and moved to the packing station. Depending on the production scale, this could involve manual labor or be fully automated with robotic stackers and shrink wrap systems. Throughout the production process, quality checks are conducted—this includes checking shape consistency, rim integrity, perforation accuracy, and coating adhesion. If required, data from the machines can be collected for traceability, especially for export compliance or private label production.
A pizza pan production line is relatively efficient and doesn’t require a large footprint unless multiple sizes and styles are being produced simultaneously. With modern servo-controlled presses and CNC automation, one line can handle multiple sizes by swapping dies, and a medium-sized setup can easily produce several hundred to a few thousand pans per hour depending on complexity and finish requirements.
Continuing from there, one of the key advantages in pizza pan production is the relatively low forming depth compared to deeper cookware, which allows for faster cycle times and simpler tooling. This means that the presses used don’t need to be extremely high tonnage, making the machinery more accessible and cost-effective for small to mid-sized operations. A mechanical press in the 25–50 ton range is usually sufficient for forming standard pizza pans up to 16 inches, while larger industrial pans may require slightly more force and deeper tooling setups.
If a production line is designed for multiple pan sizes or styles—like flat pans, deep-dish, or crisper trays—it can be equipped with a quick-change die system. This reduces downtime when switching between products and helps keep throughput high. Tool and die maintenance becomes important here; since the edge quality and consistent pan depth are visually obvious to the end user, even slight inconsistencies in the tooling can lead to rejections or poor stacking performance. This is especially true in the case of commercial pans, where precise nesting is important for storage and transportation in kitchens.
Another important factor is the choice of surface treatment. While bare aluminum is often acceptable, especially for lower-cost or single-use pans, higher-end products may require additional finishing. Hard anodizing not only improves wear resistance but also gives the pan a dark, matte finish that helps absorb heat evenly. Non-stick coatings are popular for home-use pans, but they require a cleanroom-like environment to prevent dust or oil contamination before curing. Coating adhesion is a common failure point if surface preparation (such as degreasing and etching) is not handled properly.
On the automation side, robotic arms or pneumatic pick-and-place systems can be added for blank transfer, forming press loading, and unloading to reduce manual handling. Laser sensors or vision cameras can also be used to detect pan alignment and ensure that each unit is formed and coated accurately. These systems become more important as production volumes increase or if defect tolerance is very low.
At the final stage, finished pans are stacked, sometimes nested with interleaving sheets or dividers if they have a non-stick finish. Packing machines wrap or box them according to the retail or bulk distribution needs. For large-scale export or OEM manufacturing, branding elements like embossed logos, QR codes, or printed sleeves are added either inline or in a secondary packaging station.
If you’re considering setting up such a line, one of the most critical decisions will be the balance between flexibility and output. A fully flexible line can handle many SKUs with relatively low changeover time but might be slower per unit. A dedicated high-speed line, on the other hand, will produce one or two products at extremely high volumes. Both approaches can be optimized based on your market, whether you’re serving domestic retail, food service supply, or private-label export contracts.
Building on that, if you’re planning the full production environment for pizza pans—especially with scalability in mind—factory layout, workflow optimization, and supply chain integration become the next crucial layers. The physical layout should aim for a linear or U-shaped flow to minimize backtracking and material handling. Starting with raw coil storage near the decoiler, the line should progress logically through blanking, forming, finishing, and finally to packing and palletizing. Each station ideally has buffer zones to prevent bottlenecks, especially between forming and coating processes, where timing and curing may differ.
Material handling can be semi-automated using conveyor belts or air-powered transfer systems between each step, especially from blanking to forming and from forming to coating. For instance, a vacuum pickup system can lift and place blanks into the forming press without human touch, keeping consistency high and reducing labor fatigue or injury risk. In medium- to high-capacity lines, robotic stackers or automatic cart systems can transport finished pans to the packing area or to holding racks before final inspection.
Sourcing materials efficiently is another big consideration. Aluminum coil stock should be ordered in pre-treated or mill-finished form to reduce upstream processing. If you’re doing non-stick or anodized pans, you may consider sourcing pre-coated aluminum sheets, though this limits flexibility in pan size and shaping. Alternatively, buying raw coil and integrating the anodizing or coating lines in-house offers full control but requires investment in chemical treatment systems and curing ovens, plus proper environmental compliance.
Environmental control is especially important for coating operations. The spray booths and curing ovens must be isolated from dust, moisture, and temperature swings, especially if you’re using PTFE-based coatings. Exhaust and filtration systems must be in place to meet safety and emissions standards. In the case of anodizing, chemical treatment tanks need precise pH, voltage, and timing controls, and wastewater from rinsing and etching stages must be properly treated before disposal or reuse.
From a business standpoint, production tracking and batch reporting are becoming more standard, even in mid-size plants. With basic PLC integration, you can track each batch from raw material to final packaging, allowing quick response in case of defects, customer complaints, or recall scenarios. If integrated with barcode or QR labeling, this also helps distributors and retailers manage inventory more efficiently.
In terms of labor, pizza pan production doesn’t require a huge team once the system is up and running, but it does require skilled technicians to manage die changes, maintain presses, and monitor coating quality. Operators are trained not just in safety and machine handling, but in identifying minor defects that could affect product quality downstream. For instance, a slight warp in a pan might not seem critical at forming but could lead to non-stick coating issues or warping under heat.
Lastly, for expanding product lines—like adding cake pans, pie tins, or baking trays—the core setup remains largely the same. You’d only need to adjust die sets, perhaps add or remove perforation steps, and modify the trimming or forming dimensions. This modularity makes pizza pan production a solid entry point into broader bakeware manufacturing.
Sheet Metal Steamer Basket Production Machine
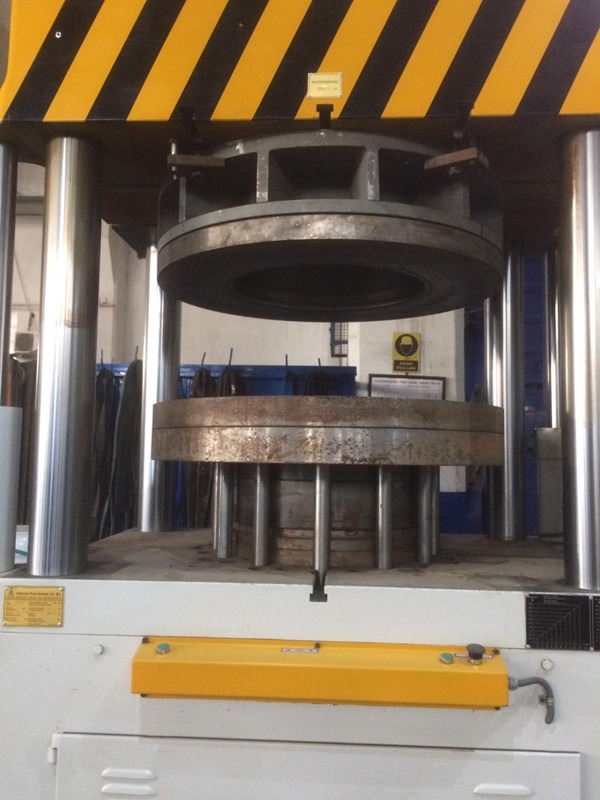
For a sheet metal steamer basket production machine, the process is somewhat similar to other cookware production lines but with some specific needs based on the design of steamer baskets, which typically require fine mesh or perforated sheet metal, along with a foldable or collapsible design. Here’s how the machinery involved would work and the steps for producing these baskets:
The process begins with raw sheet metal—typically stainless steel or aluminum—uncoiled and fed into the system. A decoiler and feeder prepare the sheet metal for cutting. For basic round or oval steamer baskets, the sheet is first blanked into circular or other appropriate shapes using a mechanical or hydraulic press equipped with a die. The blanks are then moved to the next station where perforations are added. For a steamer basket, perforations are essential because they allow steam to pass through the metal, cooking food evenly. These perforations can be made using a punch press with specialized tooling, creating a fine grid pattern or larger holes, depending on the desired function and aesthetic of the basket.
Once the perforations are made, the metal blanks need to be formed into the actual basket shape. This is typically done using a shallow drawing machine or a spinning machine. The shallow drawing machine will form the metal into the shape of the basket, which often has a shallow depth with slightly raised edges to keep food inside. Alternatively, for more intricate designs (like collapsible baskets), CNC spinning or hydraulic presses may be used to create more complex shapes, especially if the basket needs to be collapsible for storage purposes.
In some cases, the baskets might also include a folding rim or rolled edge to provide a more finished look and improve strength. For this, a rim forming or beading machine is used to roll the edges to a specific diameter, giving it a sturdier construction and sometimes a better grip. This is an essential step if the basket will be used frequently, as it adds durability and strength, especially when handling hot foods.
Once the basic shape is completed, any excess material around the edges may be trimmed to ensure a clean and consistent finish. Trimming machines can be used here to remove any burrs or excess metal from the formed baskets.
If the steamer baskets require a non-stick coating, the baskets will then go through a cleaning and coating line. In this process, the baskets are thoroughly cleaned to remove oils or residues left from the forming process. They may then go through a spray booth, where non-stick coatings, such as PTFE or ceramic-based materials, are applied. These coatings help ensure that food doesn’t stick to the metal surface during steaming. The baskets are then sent through an oven to cure the coating.
For additional durability and to give a more refined appearance, the baskets may undergo a polishing or brushing process to smooth the surface or give it a shiny, clean finish. This is often done with polishing wheels or brushes depending on the desired texture of the product.
Once completed, the steamer baskets are moved to the packing and labeling stage. This involves stacking the baskets, ensuring they are protected from scratches, and labeling them for shipment. Some baskets may be shrink-wrapped for protection during transit or boxed, depending on the customer’s needs.
The key equipment involved in the production of steamer baskets includes:
- Mechanical or hydraulic presses for blanking and shaping.
- Perforating presses for hole patterns.
- Shallow drawing or spinning machines for forming the basket shape.
- Rim rolling and beading machines for reinforcing edges.
- Cleaning and coating booths for non-stick coatings.
- Polishing machines for finishing.
- Trimming machines for edge cleanup.
- Packing systems for final handling.
If the production volume is high, automation can be incorporated to move parts between stages with robotic arms or conveyors, ensuring fast cycle times and minimal manual handling. These systems also help improve quality control by ensuring that every piece is formed and coated according to the same specifications.
In the production of sheet metal steamer baskets, the process starts with unrolling the raw sheet metal, which is typically stainless steel for its heat resistance and durability. The first step is blanking, where the metal is cut into circular or custom shapes using mechanical or hydraulic presses, depending on the scale of the operation. For basic round baskets, a punch press with a circular die is commonly used, but if the design requires more intricate shapes (like oval or custom sizes), a CNC laser cutter might be used for precision.
After the blanks are cut, the next stage is to add perforations. Perforations are essential for the steamer basket’s functionality, as they allow steam to pass through while cooking. These perforations can be made with a specialized punch press, which stamps out a uniform pattern of holes or a grid design in the metal. Depending on the design and purpose, the holes might vary in size, and the pattern can range from a fine grid to larger individual holes to allow for greater steam flow. The precise pattern of holes is vital, as it directly impacts the basket’s steaming efficiency.
Once the perforations are in place, the next step is forming the metal into the shape of the basket. A shallow drawing press or spinning machine is often used for this, where the metal is drawn into a shallow shape with raised edges. If the basket needs to be collapsible, a more complex process using hydraulic or mechanical presses is required to create foldable sides that can expand or collapse for easy storage. This step often requires precise control, as the shape and depth of the basket must be uniform to ensure it functions correctly during cooking.
After the basket is formed, the edges may need to be reinforced. This is done with a rim forming or beading machine, which rolls the edges to create a stronger, smoother finish. The rim provides structural integrity to the basket and prevents sharp edges, making it safer to handle.
Once the basic shape and structure are in place, any excess material is trimmed using trimming machines to clean up the edges and ensure that the basket has a uniform and clean finish. This step also removes any burrs or rough spots left from the forming process.
For added durability and functionality, especially if the basket will be used for steaming food, many steamer baskets are coated with a non-stick layer. This coating prevents food from sticking to the surface, making cleaning easier. After the basket is formed and trimmed, it is sent through a cleaning and coating line. First, it is cleaned thoroughly to remove oils, residues, and any dust from the forming process. Then, the basket is coated with a non-stick material, often PTFE or ceramic-based coatings, using automated spray booths. After coating, the baskets are cured in an oven, where the coating hardens and bonds to the metal, creating a smooth, non-stick surface.
Once the baskets have been coated and cured, they undergo a polishing or brushing process, which gives them a shiny or matte finish, depending on the desired look. This stage is optional but is commonly used for higher-end products to enhance their appearance and ensure a smooth surface that’s easier to clean.
Finally, the baskets are stacked and moved to the packing area. Here, they are checked for quality and packaged for shipment. Packaging can vary from simple shrink wrapping to more elaborate box packaging for retail, depending on the target market. Some systems are automated, with robotic arms or conveyors moving the baskets through the packing process, ensuring consistent handling and reducing manual labor.
Throughout the process, various quality checks are conducted to ensure that each basket meets the required standards. This includes checking the perforations for uniformity, ensuring the edges are smooth and free of sharp spots, and testing the non-stick coating for adhesion and durability. Automated inspection systems, such as visual cameras or sensors, can be integrated to detect defects during the forming and coating stages.
The production line can be adjusted for different sizes of steamer baskets by changing the dies or tooling in the presses and adjusting the size of the perforations. A modular approach allows manufacturers to handle multiple designs with relatively low downtime for setup changes, making the process more efficient and cost-effective. Automation helps with high-volume production, ensuring that baskets are formed and coated consistently, while also reducing the need for manual handling and increasing throughput.
As the production line continues to progress, the next important consideration is streamlining material handling and ensuring the proper flow of the steamer basket manufacturing process. For high-volume production, automation plays a critical role in minimizing labor costs and increasing consistency. The metal sheets, after being cut into blanks, are transferred to the perforating station using conveyors or robotic arms that place the blanks accurately into the punch press. After perforation, the baskets are moved efficiently to the forming presses, with minimal downtime. By utilizing automated transfer systems, the operation ensures that there is no bottleneck between stations, allowing for smooth continuous production.
Additionally, incorporating automated quality inspection systems throughout the production line can dramatically improve product consistency. At each stage—blanking, perforating, forming, and coating—vision cameras or sensors can be integrated to check for defects like misalignment, incorrect hole patterns, and imperfections in the edges or finish. This enables immediate corrective actions, preventing defective baskets from moving further down the line and reducing scrap rates.
For coating applications, drying and curing ovens must be properly calibrated to ensure that the non-stick coatings adhere uniformly to the baskets. The curing time and temperature must be precisely controlled to prevent any uneven surfaces or defects in the coating. To ensure long-lasting, durable non-stick finishes, some manufacturers opt for more advanced curing systems that control not just temperature but also humidity and air circulation within the oven. These systems help ensure the coatings are baked at optimal levels, which reduces the likelihood of peeling or degradation over time.
In terms of material sourcing, while stainless steel is the go-to material for most steamer baskets due to its heat resistance, corrosion resistance, and overall strength, manufacturers may choose to use aluminum for lighter, lower-cost alternatives. Aluminum is less expensive and easier to form, but it may not have the same level of durability and heat resistance as stainless steel. The choice between materials will depend on the target market—stainless steel is more common in higher-end, long-lasting products, while aluminum might be used for disposable or budget-conscious consumer products.
As the baskets exit the curing process, they are inspected for coating quality, and additional steps may be taken if necessary. For example, some baskets may undergo a second pass through the polishing system to enhance their finish and ensure a more visually appealing product. This is especially important if the steamer baskets are intended for retail markets, where aesthetics play a significant role in consumer decision-making.
Once the baskets are complete, the stacking and packing phase is automated to the greatest extent possible. Finished baskets are stacked according to size and type, with some models featuring nesting or collapsing designs for more compact storage. The baskets are then passed through a robotic arm or automated packing machine that groups them into sets or individual units for boxing or shrink-wrapping. Packaging can be designed for either bulk shipments or retail display, depending on the customer’s requirements.
Throughout the entire process, there is a strong emphasis on minimizing waste and maximizing efficiency. Lean manufacturing principles can be applied, such as using material recovery systems to recycle scrap metal and cutting down on energy consumption in the heating and curing stages. Many manufacturers also integrate data tracking systems for each batch of steamer baskets produced. This allows them to trace materials, machine settings, and coating processes, which is useful for quality control, inventory management, and meeting regulatory standards, especially if the baskets are being exported to markets with stringent product requirements.
Finally, if the production line is set up with scalability in mind, it’s possible to adjust production volume with relative ease. Modular machinery setups and flexible dies for the forming presses allow for quick changes between different basket designs or sizes, making it easier to diversify product lines. For example, if there is demand for larger or smaller baskets, changing the dies or the settings on the forming press allows manufacturers to quickly pivot without investing in entirely new production systems.
For companies looking to enter the steamer basket market, investing in automation and efficient production lines ensures that the operation is cost-effective, capable of scaling production volumes, and able to maintain high-quality standards. This approach can also help manage fluctuations in market demand, enabling the manufacturer to quickly adjust production capacity without incurring excessive costs.
As the steamer basket production line evolves, there are a few more critical considerations, particularly when it comes to optimizing maintenance schedules, managing supply chain logistics, and scaling for future growth.
Maintenance is one of the most crucial aspects of ensuring the longevity and efficiency of the production line. Every piece of machinery, from the decoiler to the punching press, must be regularly maintained to avoid unexpected downtime. Setting up a preventive maintenance (PM) schedule is essential to minimize unscheduled stoppages that can affect throughput. For example, press dies need to be regularly inspected and sharpened to maintain clean cuts, while conveyor systems require periodic lubrication and adjustments to avoid misalignment or jamming. Similarly, the curing ovens need temperature calibration checks and cleaning of vents and filters to maintain consistent heat profiles. By establishing a predictive maintenance system, perhaps integrated with machine learning or IoT (Internet of Things) sensors, manufacturers can anticipate wear and tear, order spare parts in advance, and minimize disruptions.
As for supply chain logistics, managing raw materials is key to keeping production running smoothly and minimizing costs. For a product like steamer baskets, it’s important to source high-quality stainless steel or aluminum at competitive prices. Long-term relationships with suppliers are essential, as is the ability to forecast demand accurately. Manufacturers might consider working with multiple suppliers to mitigate the risk of delays in case one supplier faces issues. Raw materials should be ordered in bulk to reduce unit costs, and managing inventory through automated systems can help avoid stock-outs or excess inventory.
When scaling up production, supply chain management systems can help optimize the movement of materials from suppliers to the production facility. Technologies such as enterprise resource planning (ERP) and supply chain management (SCM) software can improve coordination between procurement, manufacturing, and distribution, ensuring that production schedules are met, and materials are always on hand. Manufacturers may also look into setting up local supply partnerships or sourcing materials from sustainable and certified suppliers, which can improve the reliability and ethical standards of the entire supply chain.
Regarding scaling production, it’s important to consider how to expand your capacity without sacrificing quality. Investing in modular equipment allows manufacturers to add or remove production lines as demand fluctuates. For instance, additional forming presses, coating booths, or even inspection systems can be added to meet growing demand for different basket sizes or designs. If the market demands higher volumes, manufacturers might opt for larger, more automated lines that can handle higher throughput without significantly increasing labor costs. This could involve upgrading presses to higher-tonnage models or incorporating multi-station tooling that can handle multiple baskets in one press cycle.
Product diversification is another avenue for growth. If your company has mastered steamer baskets, expanding into other types of cookware like steamer inserts, baking trays, or colanders could leverage existing machinery while offering new product options. A flexible die system that can be easily adjusted for different shapes can help quickly adapt the production line for these new product types without major capital investment.
To ensure market competitiveness, it’s also important to maintain a focus on cost control. Constantly evaluating material costs, machine efficiency, and energy consumption can yield substantial savings. For example, if energy consumption in heating or curing processes is high, manufacturers may look into investing in energy-efficient ovens or alternative coating methods that require lower curing temperatures. Similarly, automating more stages of the process can reduce labor costs while increasing the speed and precision of the work. Lean manufacturing techniques, such as just-in-time (JIT) inventory management, can further reduce waste and improve operational efficiency.
Lastly, quality control remains a top priority throughout the process. Given that the end product—steamer baskets—will be exposed to high heat and moisture, ensuring the product’s durability is paramount. Regular inspections at each production step, as well as end-of-line quality testing, are essential to guarantee the product is defect-free. For instance, the coating process should be closely monitored to ensure uniformity, and perforation patterns must be consistent. Non-stick coatings, in particular, require rigorous testing for adhesion, durability, and resistance to heat. The final product can also undergo a visual inspection and functionality test to ensure it meets industry standards for strength and steaming efficiency.
As the brand grows, expanding into larger markets requires the consideration of export standards and certifications. For steamer baskets, certifications such as ISO 9001 (for quality management) or FDA approval (if applicable, for food-safe coatings) may be necessary for certain markets. Having a clear understanding of these regulations and ensuring that all products comply can open up opportunities for international sales and help position the brand as a trusted name in cookware.
In conclusion, the production of sheet metal steamer baskets involves a series of interconnected processes, from raw material handling and forming to coating and packaging. By optimizing every stage—from equipment selection and automation to supply chain management and maintenance scheduling—manufacturers can create an efficient and scalable production environment. Continuous investment in machinery, technology, and quality control will ensure that steamer baskets not only meet customer expectations but also maintain profitability as the market grows.
Sheet Metal Roasting Pan Production Machine
The production of sheet metal roasting pans involves a similar approach to other cookware manufacturing processes but requires a few specific features to ensure the pan is durable, heat-resistant, and functional for roasting. Here’s how the machinery and processes for producing roasting pans typically work:
The process begins with the raw material, which is typically stainless steel or aluminum due to their heat resistance and strength. Stainless steel is more common for higher-end products due to its durability, non-reactivity with food, and ability to withstand high oven temperatures. Aluminum, on the other hand, may be used for more budget-friendly pans due to its light weight and relatively lower cost.
The first step is the decoiling and uncoiling of the metal sheets. The coils of metal are fed into the machine through a decoiler, which unwinds the material and prepares it for cutting into sheets. This process also aligns the metal for further operations.
Once the material is uncoiled, the next step is blanking. A mechanical or hydraulic press with a specialized die is used to cut the sheet metal into the required shape and size for the roasting pan. Roasting pans typically have a rectangular or oval shape, and the blanking process is crucial to creating uniform pieces that will form the body of the pan.
Next, the blanks are sent to the forming press, which shapes them into the deeper sides of the roasting pan. This process can be done with a deep-drawing press or shallow-drawing press, depending on the depth of the pan. The metal is drawn into a mold to create the characteristic high walls of a roasting pan. This stage may require multiple operations, especially if the pan has complex features, such as rolled edges or a reinforced lip for better grip.
After the pan is formed, the next step is to trim the excess material from the edges. This is done using trimming machines or edge forming presses, which remove any sharp edges and ensure that the pan has a clean and uniform appearance. It also ensures that there are no burrs or sharp edges left on the product, making it safer for handling.
If the roasting pan requires a reinforced edge for added durability and strength, a rim-forming machine may be used to create a smooth, rolled edge. This process helps prevent deformation and makes the pan more resilient to heavy use. The rolled edges also make the pan easier to handle, especially when hot.
The next critical step is surface finishing, which involves polishing, brushing, or coating the pan. If the roasting pan requires a non-stick coating, it will undergo a cleaning process to remove any oils, dust, or debris left from the forming and trimming stages. This ensures the coating adheres properly. Non-stick coatings, such as PTFE (Teflon) or ceramic coatings, are often used for roasting pans to prevent food from sticking and to make cleaning easier.
The coating is usually applied using spray booths that evenly coat the pan. After coating, the pan is sent through a curing oven, where the coating is baked onto the surface at a precise temperature. This curing process ensures that the coating adheres securely to the metal and forms a smooth, durable finish.
For pans that don’t require a non-stick coating, the surface may be treated with a brushed finish or polished to provide a shiny and aesthetically pleasing look. Polishing is especially important for stainless steel pans, as it enhances the appearance of the pan and helps resist staining.
Once the pans have been finished, they are subjected to a quality control inspection. This can include visual checks to ensure the pans are free of defects, such as scratches, dents, or uneven finishes. Some manufacturers also conduct functional tests to ensure the pans meet heat resistance standards and can withstand the high temperatures typically used in roasting.
After passing inspection, the pans move to the packaging area. Depending on the type of product, the pans may be stacked and packaged individually in protective wrapping or boxed for retail display. If packaging is for bulk shipment, protective inserts or cardboard dividers may be used to prevent the pans from scratching each other.
Key Equipment for Roasting Pan Production:
- De-coiler and feeder: To unwind and feed the raw material.
- Blanking press: For cutting the metal into the correct size and shape.
- Forming press (deep drawing or shallow drawing): To shape the pan’s sides.
- Trimming press: To clean up edges and remove excess material.
- Rim-forming machine: To roll the edges and add reinforcement.
- Coating booth: To apply non-stick coatings.
- Curing oven: To bake and cure the non-stick coatings.
- Polishing machines: To finish and shine stainless steel pans.
- Inspection stations: For quality control at various stages.
- Packaging systems: For boxing and preparing products for shipment.
In terms of automation, similar to other cookware production lines, incorporating robotic arms or conveyors can significantly enhance efficiency. Automated systems can transfer pans between stages, such as from the forming press to the coating booth, and from there to the curing oven and packaging stations. This reduces the need for manual labor, increases throughput, and ensures that each pan is handled in a consistent manner.
Material sourcing is also important for keeping costs down and maintaining quality. Stainless steel for high-end pans tends to be more expensive than aluminum, but the investment in stainless steel often results in a more durable, long-lasting product. Many manufacturers opt for high-quality stainless steel alloys that provide both durability and resistance to staining, rust, and corrosion. Aluminum, while lighter and more affordable, may not hold up as well over time compared to stainless steel, especially for products meant for heavy, long-term use like roasting pans.
If your roasting pans are intended for commercial use, ensuring compliance with food-safe standards is essential. For non-stick coated pans, ensure the coating is FDA-approved or meets other relevant food safety standards. Moreover, ISO certifications for quality management systems can help ensure that the production process is efficient and consistently produces high-quality products.
The packaging process can be adjusted based on whether the pans are being sold in bulk or individually. For bulk shipments, simpler packaging methods can be used, while individual retail packaging may involve more attention to aesthetic design, such as branded boxes or shrink-wrapping with product information.
As the production line ramps up or diversifies, it’s important to consider flexibility in the machinery. Using modular dies for forming presses and versatile coating systems allows manufacturers to adapt to different roasting pan sizes or product variations, such as adding handles, lid designs, or different coatings. A flexible production line allows manufacturers to easily accommodate market demands and experiment with new product designs.
The production of sheet metal roasting pans involves several key steps, each requiring specialized machinery to ensure the final product is both functional and aesthetically appealing. After the raw material, typically stainless steel or aluminum, is uncoiled from the supply rolls, the first step is to cut the metal sheets into precise shapes using a blanking press. This press ensures uniformity and accuracy in the shape of the pan, which is usually rectangular or oval for roasting pans. The blanks are then transferred to a forming press, which shapes the metal into the desired depth of the pan’s sides. This forming process can involve deep-drawing presses for pans that need deeper sides and shallow-drawing presses for more standard shapes.
Once the pan is shaped, trimming machines clean up the edges, ensuring they are smooth and free of burrs. For added durability, some pans undergo a rim-forming process, where a machine rolls the edges of the pan to reinforce them and make them safer to handle. If the pan requires a non-stick coating, the next step involves a coating process. This typically takes place in a spray booth where a thin layer of non-stick material like PTFE or ceramic is applied to the surface of the pan. The pan is then cured in a specialized oven, where the coating is baked to a hard finish, ensuring it adheres well to the metal.
For stainless steel pans that do not require a non-stick coating, a polishing or brushing machine may be used to give the pan a shiny or matte finish, depending on the desired appearance. This step is important not just for aesthetics but for the overall smoothness and ease of cleaning. After finishing, each pan goes through a quality control process. This may include visual inspections to check for surface defects, such as scratches or dents, as well as more functional tests to ensure the pan can withstand high temperatures without warping.
Once approved, the pans are then packaged. The packaging can be tailored to the type of market the pans are intended for. For retail markets, individual pans are often wrapped in protective materials and placed in custom boxes that include product information and branding. For wholesale or bulk shipments, simpler packaging may be used, such as shrink-wrapping or stacking the pans in larger containers for transport.
Throughout the process, automation is key to improving efficiency and reducing labor costs. Robotic systems can handle the transfer of pans between stages, and automated inspection systems can ensure the quality of each unit before it progresses to the next step. These advancements help reduce human error and ensure high production rates, which are particularly important when scaling up operations to meet demand.
The production of sheet metal roasting pans, like many cookware items, benefits greatly from a flexible and modular production line. This adaptability allows manufacturers to switch between different designs or sizes of pans with minimal downtime, which can be especially useful for catering to varied customer preferences. Additionally, materials and coatings must be chosen carefully based on the end-use of the pans. Stainless steel pans are typically used for their durability and high resistance to heat and corrosion, while aluminum pans may be favored for their lighter weight and cost-effectiveness in more budget-conscious markets.
Finally, as with any cookware production, meeting industry standards for safety and performance is essential. For non-stick pans, ensuring that the coatings are free of harmful chemicals and safe for food use is crucial. This often involves certifications from regulatory bodies, such as the FDA or international standards organizations, which ensure the product meets the necessary guidelines for consumer use.
As you continue to explore the production of sheet metal roasting pans, it’s important to focus on how to streamline and scale the operation effectively. Automation, for instance, can play a vital role in increasing throughput and reducing operational costs. Once the raw material is uncoiled and cut into blanks, automated systems can seamlessly transfer the material to the forming presses. These systems often rely on conveyor belts, robotic arms, or automated carts to move the pieces from one station to the next without manual intervention. This greatly reduces the time between stages and minimizes the risk of human error, ensuring that the pans are handled with precision.
Additionally, automated forming presses can adapt to varying pan designs, providing flexibility in the production process. For example, if a manufacturer wishes to switch between different pan sizes or types, the press dies can be easily changed or adjusted without requiring significant downtime. In some advanced production setups, smart dies are used, which can automatically adjust to the material’s thickness or the desired depth of the pan without the need for manual recalibration. This not only improves efficiency but also allows for higher production volumes without compromising on the quality of each pan.
The trimming and finishing stages also benefit from automation. Robotic trimming arms can precisely cut the edges of the pans, ensuring that they meet the required tolerances and are free from any sharp edges or defects. These systems are often equipped with vision systems that use cameras and sensors to detect flaws in the edges or surface of the pan before moving them to the next stage. If a pan is deemed defective, it can be automatically removed from the production line, reducing waste and improving overall yield.
For the coating process, especially when applying non-stick coatings, it’s essential to have automated spray booths that apply a consistent and even layer of coating across all surfaces of the pan. These booths can be fitted with high-precision nozzles that ensure the correct amount of coating is applied, reducing overspray and wastage. The curing ovens used to bake the coating onto the pans can also be monitored with advanced sensors that ensure the temperature is maintained within the optimal range. This is important for achieving a uniform and durable finish on the non-stick surface.
Once the pans are coated, whether with a non-stick layer or a polished finish, they move to the inspection and quality control stage. This is where the importance of advanced technology really comes into play. Automated vision inspection systems can scan the surface of each pan for imperfections like scratches, dents, or inconsistencies in the coating. These systems use high-resolution cameras and artificial intelligence to analyze the pans for defects, ensuring that only products that meet the highest standards are sent to the packaging stage.
After inspection, robotic arms or automated conveyors can then transfer the pans to the packaging area. In a fully automated line, packaging is done by machines that place each pan into its designated box or protective wrap. The boxes are then sealed, and they can either be stacked for bulk shipment or prepared for retail packaging, which often includes adding labels, branding, and product information.
The overall goal of automation in the roasting pan production line is to reduce human labor, improve consistency, and increase production speed. However, it’s equally important to consider the initial investment in automation. Although the upfront cost can be substantial, the long-term benefits in terms of reduced labor costs, increased efficiency, and the ability to scale production make automation a worthwhile investment. Moreover, as consumer demands evolve, having an automated system allows manufacturers to easily adjust to changes in design, size, or coating preferences.
Alongside automation, lean manufacturing principles can further help reduce waste and improve operational efficiency. For example, just-in-time (JIT) inventory systems can help manage raw material stock more effectively, ensuring that materials are only ordered when needed, reducing storage costs and the risk of overstocking. Additionally, continuous improvement initiatives, such as Six Sigma or Kaizen, can be implemented to identify areas for improvement and minimize defects in the production process. These principles can ensure that each step of the roasting pan production process is as efficient as possible, from raw material handling to packaging.
Finally, as demand for roasting pans increases, the production line can be scaled up to meet higher volumes. This could involve adding more presses or expanding the coating booths to handle a larger number of pans per hour. The modular nature of modern production lines makes it easy to adapt to these demands, enabling manufacturers to quickly adjust without extensive downtime or capital investment.
In conclusion, producing sheet metal roasting pans involves a mix of advanced machinery, automation, and smart manufacturing practices that work together to create a high-quality product at scale. By investing in technology that improves efficiency and consistency, manufacturers can stay competitive in the market while meeting the demands of both consumer and commercial sectors. Would you like more specific advice on automating any part of the process, or help in sourcing the right equipment?
As roasting pan production continues to advance, it’s essential to also consider factors like supply chain integration, sustainability, and market trends to remain competitive and efficient.
The supply chain plays a pivotal role in the overall efficiency and profitability of the production process. Having strong relationships with raw material suppliers is key to ensuring that high-quality stainless steel or aluminum is consistently available. Sourcing materials in bulk can help reduce costs per unit, but it’s important to balance this with storage capacity. For many manufacturers, just-in-time (JIT) inventory systems help to minimize the need for large storage spaces, lowering overhead costs while ensuring that raw materials arrive just when they’re needed. Automated inventory management systems can be integrated with suppliers to ensure real-time tracking of raw materials, making it easier to place orders without overstocking. Additionally, having alternative suppliers can help mitigate risks, especially when dealing with fluctuations in metal prices or potential supply disruptions.
Another aspect of supply chain management is ensuring the consistent quality of the raw materials. Stainless steel and aluminum can vary in quality based on their alloy composition, and it’s critical that these materials meet certain standards for heat resistance, durability, and food safety. Material testing in the early stages of production ensures that the metal meets all specifications before it enters the manufacturing line. This can involve tests for thickness, hardness, and corrosion resistance to guarantee that the pans will perform well under extreme heat and resist degradation over time. Moreover, working closely with certified suppliers can ensure that the materials are food-safe and free from harmful substances.
On the sustainability front, there is increasing consumer demand for eco-friendly and sustainable products, which has led many cookware manufacturers to explore greener production practices. For instance, recycled metals can be used in the production of roasting pans, especially aluminum, which is highly recyclable. By incorporating recycled materials into the production process, manufacturers can reduce the carbon footprint of their products and appeal to environmentally conscious consumers. This practice also helps lower material costs, as recycled metals are often less expensive than virgin materials. Many brands are also looking at reducing their energy consumption during production, particularly in the coating and curing stages, where ovens are used to bake non-stick layers onto pans. Upgrading to energy-efficient ovens or exploring alternative heating methods can help reduce energy costs while also benefiting the environment.
Additionally, packaging materials can be made more sustainable. Using recyclable or biodegradable packaging for roasting pans not only supports sustainability efforts but also aligns with consumer preferences for environmentally friendly products. This could mean shifting away from plastic packaging and using materials such as cardboard, paper wraps, or compostable shrink film. Packaging designs can also be optimized for space-saving, reducing the overall volume and shipping costs. Using smart packaging with printed QR codes or smart labels can provide consumers with detailed product information, such as care instructions, material sourcing, and sustainability credentials, making it easier for them to make informed choices.
The market trends in cookware are constantly evolving, and staying ahead of consumer preferences is key to capturing market share. Non-stick coatings, for instance, have been a major trend in cookware for some time, and their demand continues to grow due to their convenience and ease of use. However, there’s also a growing shift towards health-conscious cooking products, where consumers are more concerned with the materials and chemicals used in non-stick coatings. Some manufacturers are responding by offering ceramic-based non-stick coatings, which are perceived as safer and more natural than traditional PTFE coatings.
There’s also a rising interest in multi-functional cookware, which serves a variety of cooking needs. For example, some roasting pans are being designed with removable inserts or lids, making them versatile for use in baking, roasting, and even serving. This kind of flexibility adds value for consumers, particularly those with limited kitchen space who prefer compact and multi-purpose cookware.
Another important trend is the premiumization of cookware. Many consumers are now willing to pay a premium for higher-quality, long-lasting products that offer both superior performance and aesthetic appeal. Roasting pans made from high-quality stainless steel with high-polish finishes or cast iron roasting pans with enamel coatings are increasingly popular in the high-end market. These products are often marketed as heirloom-quality items, designed to last a lifetime, and are typically positioned as premium products in the retail market.
Furthermore, smart cookware is emerging as a trend in the industry. Some high-tech roasting pans now come equipped with integrated thermometers or even smart sensors that can track cooking temperatures in real-time, providing an enhanced cooking experience. These pans may be designed to sync with smartphone apps, allowing users to monitor their food remotely. While this trend is still in the early stages, it’s a good example of how cookware manufacturers can innovate to meet the increasing consumer desire for connected and smart appliances.
As the demand for premium and multifunctional cookware increases, manufacturers are looking at the possibility of expanding their product offerings beyond basic roasting pans. By diversifying their product lines to include items such as baking sheets, roasting racks, grilling pans, and casserole dishes, cookware companies can tap into new customer segments and boost their sales. Expanding the range allows manufacturers to use existing machinery for different products, which can improve overall production efficiency and reduce downtime.
On the global market front, manufacturers who plan to export their roasting pans should be aware of international standards and certifications. Many countries require specific certifications for cookware products, particularly those with non-stick coatings. In the United States, for example, cookware must meet the FDA’s guidelines for food safety. Additionally, ISO 9001 (quality management) and ISO 14001 (environmental management) certifications can provide credibility to a brand and demonstrate a commitment to high standards of production and sustainability.
Lastly, distribution channels will play a critical role in ensuring that your roasting pans reach the right audience. As the e-commerce industry continues to expand, manufacturers should consider selling directly through online platforms like Amazon, their own websites, or through partnerships with large retailers. Offering attractive shipping options and promotions can help increase sales, while product reviews and customer feedback can enhance visibility and credibility in the marketplace.
By keeping an eye on market trends, ensuring the sustainability of operations, and leveraging automated processes, manufacturers can set themselves up for long-term success in the competitive cookware industry.
Sheet Metal Stock Pot Production Machine
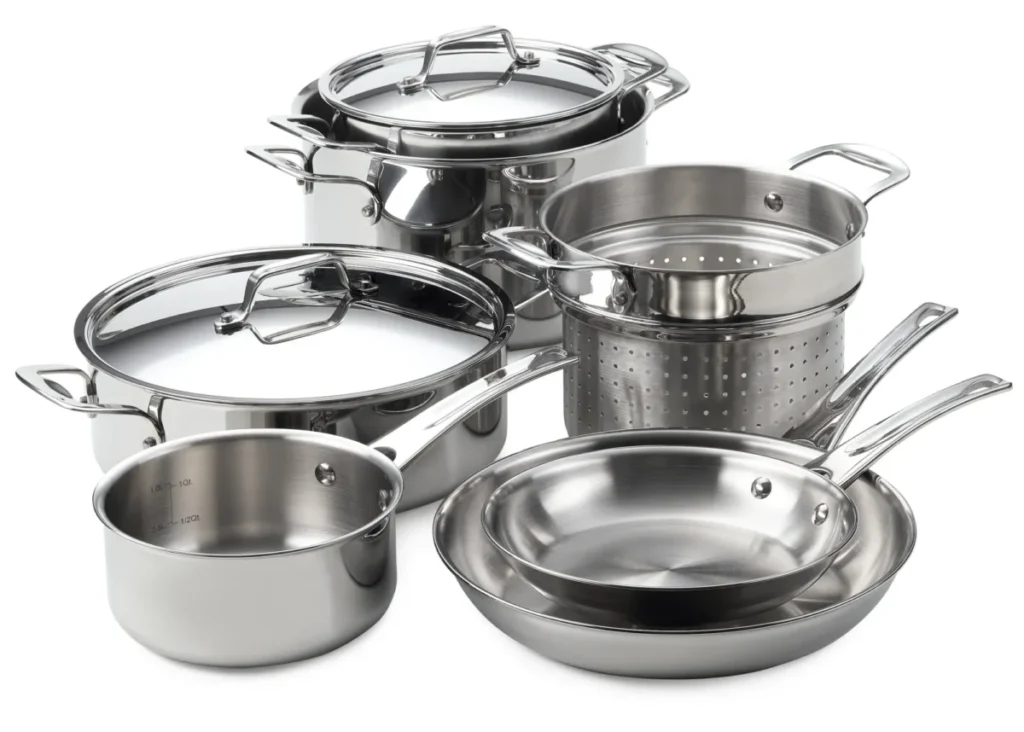
The production of sheet metal stock pots involves similar processes to other cookware items, but the stock pot’s design requires specific machinery and techniques due to its larger size and the need for strong, durable construction to withstand high temperatures and heavy use in kitchens. Here’s an overview of the typical process for manufacturing sheet metal stock pots:
The process begins with the selection of raw material, typically stainless steel or aluminum, depending on the desired durability, weight, and cost considerations. Stainless steel is generally preferred for higher-quality stock pots because of its heat resistance, non-reactivity with food, and corrosion resistance. Aluminum, on the other hand, is lighter and may be used in lower-cost products, though it tends to have a shorter lifespan compared to stainless steel.
- Material Preparation: The raw material, typically in the form of large coils, is loaded onto a decoiler that unwinds the sheet metal to prepare it for cutting. The metal is then fed into slitting machines to cut it into strips of the correct width.
- Blanking: The first step in the forming process is blanking, where the sheet metal is cut into circular or rectangular blanks (depending on the shape of the stock pot). A blanking press is used to create these initial blanks from the metal strips. Stock pots typically have a flat bottom and higher sides, so the blanks are slightly larger than the final size of the pot to allow for the shaping process.
- Deep Drawing: After blanking, the next stage is deep drawing, where the flat metal blank is formed into a shallow bowl shape. A deep-drawing press uses a punch and die system to pull the metal into a mold. This process is crucial to the formation of the pot’s body, which needs to have tall, uniform sides. For larger stock pots, this might be done in multiple stages to ensure the sides are even and smooth.
- Trimming and Edge Forming: After the basic shape of the stock pot is formed, excess material from the edges is trimmed. Edge-forming machines are used to smooth the rough edges, removing any burrs and sharp areas that could be dangerous during handling. Sometimes, the edges are also rolled or rimmed to give them added strength and improve the pot’s overall appearance.
- Handle Attachment: Depending on the design of the stock pot, handles may need to be attached. These can be riveted or welded to the pot. Some manufacturers use spot welding to attach metal handles, while others may use screws or brackets for a sturdier connection. The handles are an important part of the pot’s usability, so ensuring they are securely attached is a key part of the production process.
- Polishing and Surface Finishing: Once the stock pot is shaped, the next step is to finish the surface. If the pot is made from stainless steel, it may go through polishing or brushing to give it a shiny, clean surface. Some stock pots may have a matte finish, while others may be polished to a mirror-like shine. For stock pots with non-stick coatings, the pot will be cleaned thoroughly before applying the coating.
- Non-stick Coating (Optional): For some stock pots, particularly those designed for home use, a non-stick coating may be applied. This typically involves spraying the coating onto the interior surface of the pot. The pot is then baked in a curing oven to ensure the coating adheres properly and is durable enough to withstand high temperatures. The non-stick coating can be PTFE-based (e.g., Teflon) or ceramic-based, depending on the desired performance and the target market.
- Testing and Quality Control: After the stock pot is formed and finished, it undergoes strict quality control checks. This includes inspecting the pot for any defects, such as scratches, dents, or imperfections in the coating. Additionally, the handles and any welded or riveted joints are tested for strength and stability to ensure they will be able to withstand heavy use. Some manufacturers also test the pot’s heat resistance to ensure it performs well under high temperatures.
- Packaging: After passing inspection, the pots are packed and prepared for shipment. Depending on the market, the stock pots may be individually packaged in boxes, which often include branding, care instructions, and product details. In bulk shipments, the pots may be stacked and secured with protective padding to prevent damage during transit.
Key Equipment for Stock Pot Production:
- De-coiler and slitting machines: To unwind and cut raw metal into the appropriate strips.
- Blanking press: For cutting blanks from the metal sheet.
- Deep drawing press: For shaping the pot body from the blank.
- Trimming and edge-forming machines: To clean and smooth the edges of the pot.
- Handle attachment machines: For riveting, welding, or screwing handles onto the pot.
- Polishing and surface finishing machines: To finish the exterior and interior surfaces.
- Spray booths and curing ovens: For applying and curing non-stick coatings.
- Quality control stations: To inspect each product for defects and functional testing.
- Packaging systems: For wrapping, boxing, and preparing the pots for distribution.
To maintain efficiency and ensure a high-quality product, many manufacturers integrate automation at key points in the production process. Automated robotic arms can transport metal blanks from one station to another, minimizing handling time and reducing the potential for human error. Automated polishing machines can also apply a consistent finish to each pot, ensuring that the pots all have a uniform appearance.
Additionally, lean manufacturing principles can help to optimize the production process by reducing waste, improving cycle times, and enhancing the overall efficiency of the production line. Implementing continuous improvement practices, such as Six Sigma, can help identify areas where the production process can be refined, further improving quality and reducing costs.
By incorporating flexible manufacturing systems, it’s possible to quickly adapt to changes in market demand. For example, if a customer demands a specific size of stock pot or a variation in handle design, manufacturers can adjust their production lines to accommodate these requests without significant delays or costs.
The production of sheet metal stock pots requires careful planning and coordination across various stages to ensure the final product is durable, safe, and high-quality. Once the raw material is selected, typically stainless steel or aluminum, the metal sheets are fed into a decoiler, which unrolls the metal for cutting. Blanks are then cut from the metal sheets using a blanking press. These blanks are the base of the stock pot, and from here, the shaping process begins.
In the forming stage, deep drawing presses are used to transform the flat blanks into a deeper shape, allowing for the characteristic high sides of a stock pot. This requires precision to ensure that the sides are even and the shape is consistent. Depending on the design, some stock pots may be deeper or wider, so adjustments to the forming press are made accordingly. After forming, the edges of the stock pot are trimmed to ensure they are smooth and free of burrs. Edge-forming machines or trimming presses are often used at this stage to clean up the edges and ensure the pot is easy to handle.
Once the body of the stock pot is formed, attention turns to handle attachment. Handles are critical for both functionality and safety, so they must be securely attached. Handles can be welded or riveted onto the pot, with the method chosen depending on the design and the intended use of the stock pot. For home kitchens, handles may be ergonomically designed for comfort, while for commercial use, heavy-duty handles may be required for durability under more demanding conditions.
Next, the stock pot undergoes surface finishing. Stainless steel stock pots, for example, may be polished or brushed to achieve the desired finish. The polishing process can give the pot a shiny, smooth surface, while a brushed finish may offer a more matte look that is less prone to showing fingerprints. If the stock pot is designed to have a non-stick interior, a spray booth applies a coating, typically PTFE or ceramic-based. The pot is then placed in a curing oven, where the coating is baked onto the surface to form a durable, non-stick layer.
After the coating, the stock pot undergoes quality control checks. These checks ensure the pot is free of defects such as scratches, dents, or imperfections in the coating. Handles are also tested to verify their strength and security, ensuring that they will not detach under stress. Some manufacturers also perform heat resistance tests to ensure that the pot can handle high temperatures, which is crucial for stock pots used in commercial kitchens or home cooking.
Finally, once the stock pot has passed all inspections, it moves to the packaging stage. Packaging is an important part of the process, as it protects the product during transport and helps with brand visibility. The stock pots may be individually boxed, especially for retail markets, with care instructions and product details included. In bulk shipments, pots are often stacked and secured to prevent damage during transport.
Throughout the production process, automation can greatly enhance efficiency. Robotic arms can transfer metal sheets, blanks, and finished products between stages, reducing labor costs and speeding up production. Automation can also be applied in polishing, coating, and inspection to ensure consistency and reduce human error. Lean manufacturing practices, such as just-in-time inventory, can further optimize production by minimizing material waste and ensuring that raw materials are available when needed.
Sustainability is also a growing consideration. Manufacturers are increasingly using recycled materials in production, especially for aluminum stock pots. Recycled aluminum is not only more environmentally friendly, but it also reduces material costs. Additionally, companies may adopt energy-efficient processes, such as upgrading to more efficient ovens for coating curing or using solar power in manufacturing plants. Packaging materials are another area where sustainability can be improved, with a shift towards recyclable or biodegradable packaging materials becoming more common.
In a competitive market, keeping up with consumer trends is essential. Non-stick coatings, premium finishes, and multifunctional designs are all growing in popularity. Stock pots designed for versatility, such as those with removable inserts or lids, are appealing to customers who want more value for their money. Innovations in materials, such as the use of ceramic coatings that are perceived as safer than traditional non-stick coatings, also cater to health-conscious consumers.
To stay competitive, manufacturers must also consider international standards and certifications. Stock pots, particularly those with non-stick coatings, need to comply with regulatory standards in various countries. For example, the U.S. FDA regulates cookware safety, and European standards ensure that products meet health and safety requirements. Meeting these standards not only ensures compliance but also builds trust with consumers.
The growing trend towards smart cookware is another consideration for manufacturers. Integrating technology, such as temperature sensors or app connectivity, into stock pots can help manufacturers stand out in a crowded market. These advancements may be particularly appealing to tech-savvy consumers who are interested in enhancing their cooking experience.
By incorporating modern manufacturing techniques, sustainability practices, and adapting to consumer trends, manufacturers of sheet metal stock pots can stay ahead in a competitive marketplace. Automation and lean manufacturing principles help keep production efficient, while innovation in materials and design ensures that products meet the evolving demands of consumers.
As stock pot production evolves, it’s essential to further refine the processes, keep up with industry standards, and anticipate market shifts. Customization is one area where manufacturers are seeing increasing demand. Consumers today are looking for cookware that reflects their personal preferences, whether it’s a specific size, color, or even unique features like a built-in strainer or stackable design. Offering custom designs allows manufacturers to appeal to niche markets and cater to specialized needs, such as professional chefs who may require specific dimensions or features for cooking certain dishes.
To address these needs, flexible production lines are becoming more common. Rather than having a fixed line that produces a set range of stock pots, manufacturers can implement a system that allows quick changes in size, shape, or even material type. This requires advanced computer-aided manufacturing (CAM) systems and adjustable tooling that can be reconfigured rapidly, reducing downtime and allowing for a broader product range without significant cost increases.
Supply chain management also plays a crucial role in the success of stock pot production. The consistency and reliability of raw material suppliers are essential to maintain production schedules. Digital supply chain systems are being utilized more to track inventory in real time, allowing manufacturers to better anticipate material needs and minimize stockouts or overstock situations. This level of precision in material management reduces waste and helps to keep production costs low, especially as global supply chains can be impacted by economic changes, natural disasters, or political events.
Another growing concern in cookware production is sustainability, both in terms of raw materials and manufacturing processes. Manufacturers are increasingly using recycled metals, such as aluminum or stainless steel, to reduce the environmental impact of mining new materials. In some regions, governments are offering incentives for manufacturers who commit to sustainable practices, including using recycled content or reducing energy usage in production.
To further improve sustainability, companies are turning to green certifications, such as ISO 14001 for environmental management or B Corp certification, which indicates a company is meeting high standards of social and environmental performance. These certifications not only improve a brand’s reputation but also provide transparency for consumers, many of whom are now prioritizing sustainability when making purchasing decisions.
Additionally, cookware brands are exploring eco-friendly coating options. Traditional non-stick coatings often contain perfluorooctanoic acid (PFOA) or other chemicals that have raised environmental and health concerns. To meet consumer demand for safer, more eco-friendly products, companies are turning to ceramic non-stick coatings. These coatings are often free of harmful chemicals and offer consumers a safer alternative while maintaining the same non-stick benefits that are so popular in cookware. Manufacturers are also investigating eco-friendly non-stick coatings that are both durable and sustainable to maintain consumer trust and respond to the growing demand for healthier alternatives.
Technological integration is another key factor shaping the future of stock pot production. Some manufacturers are adopting Industry 4.0 technologies such as IoT (Internet of Things) devices, which allow production machines to communicate in real-time, enabling predictive maintenance, better quality control, and data-driven decision-making. For example, sensors embedded in deep drawing presses can monitor the temperature and pressure during the forming process, providing instant feedback if something deviates from the desired parameters. This level of precision can reduce errors, improve consistency, and even prevent costly equipment failures.
Robotic automation is also a key advancement. While traditional stock pot production lines might require manual handling of parts between stages, robotic systems can move finished products through various stages faster and more efficiently. In the finishing stages, robots can assist in polishing and coating with high precision, ensuring uniform quality and reducing labor costs. Robots can also handle the packaging process, reducing the need for human intervention in the final stages of production, speeding up packaging times, and minimizing errors in labeling and box preparation.
Consumer preferences are shifting towards products that not only meet functional needs but also look aesthetically appealing. As a result, the design of the stock pot has become a focus of many manufacturers. Customized finishes, such as matte, glossy, or even colored exteriors, help brands cater to consumers’ desire for both beauty and utility. Some companies are experimenting with decorative patterns or unique textures to create stock pots that appeal to consumers looking for something more stylish for their kitchens. Additionally, integrating ergonomic handles that offer better grip and ease of use is becoming a selling point, particularly for customers who value both design and practicality.
The demand for multi-purpose cookware has also grown. Stock pots that can be used in multiple cooking scenarios—like stovetop, oven, and even induction cooking—are increasingly popular. Manufacturers are producing stock pots that are not only versatile in cooking but also compatible with a wider range of heat sources. Many modern stock pots are designed to work with induction cooktops, which require specific types of metal (usually ferrous materials) that can conduct electromagnetic heat. Manufacturers are adapting their materials and designs to meet this new demand, offering more inclusive and flexible products.
Lastly, as globalization continues to influence markets, manufacturers are expanding their reach into international territories. When producing cookware for export, it’s essential to consider the local standards and consumer preferences. For instance, European and American markets have stricter regulations regarding chemical safety and coatings in cookware, while Asian markets may have different preferences regarding the material or weight of the pots. Understanding these regional variations allows manufacturers to adapt their designs, certifications, and marketing strategies to ensure that their products are both compliant and competitive in various global markets.
By leveraging these technological, design, and market insights, manufacturers can stay ahead of the curve in the ever-evolving cookware industry. Whether it’s integrating advanced automation, meeting sustainability goals, or responding to shifting consumer preferences, the future of stock pot production is set to become more efficient, innovative, and responsive to consumer needs.
As the stock pot production industry continues to evolve, manufacturers are exploring additional innovations and strategies to remain competitive and meet the needs of consumers. One significant trend is the growing demand for premium cookware. As more consumers become passionate about home cooking, they are seeking high-quality products that offer superior performance, durability, and aesthetic appeal. For stock pots, this means a focus on luxury materials and finishes, such as copper-clad stainless steel, which offers exceptional heat conduction properties, or tri-ply constructions, where layers of stainless steel, aluminum, and sometimes copper are fused together for optimal heat distribution.
The use of innovative lid designs is also becoming a key point of differentiation for premium stock pots. Lids that lock in steam, feature built-in strainers, or are designed to fit tightly and create a vacuum effect are increasingly popular. This enhances the cooking experience, particularly for slow-cooked dishes or broths, where moisture retention is key.
In line with the growing interest in health-conscious cooking, manufacturers are also responding to consumer preferences by offering stock pots made from materials that are chemical-free and safe. The desire for cookware that is PFOA-free (free of perfluorooctanoic acid), BPA-free, and lead-free has increased dramatically in recent years. Consumers are concerned about the potential for harmful chemicals in non-stick coatings, which has led to a shift towards more natural, safer alternatives like ceramic coatings or non-stick options with improved sustainability profiles. Additionally, the shift away from Teflon and other PTFE-based coatings is driven by environmental concerns, as these substances can break down over time and release harmful chemicals.
The introduction of eco-friendly manufacturing processes is also a focus for many stock pot manufacturers. In particular, there is increasing interest in the energy efficiency of the production process itself. For example, companies are investigating ways to optimize their kiln and furnace operations to reduce energy consumption during the heat treatment and coating processes. Solar energy is being explored as an alternative to traditional fossil fuels in some manufacturing facilities, particularly those located in areas where sunlight is abundant.
Additionally, the packaging of stock pots is seeing an evolution toward minimalist, recyclable designs. As the environmental impact of single-use plastics comes under scrutiny, manufacturers are adopting paper-based packaging or using biodegradable plastic for wrapping and boxing their products. Minimal packaging not only reduces waste but also aligns with the preferences of consumers who are more environmentally conscious and prefer to purchase products with a lower environmental footprint.
In terms of smart cookware, there is potential for integrating digital technology into stock pots, making them “smart.” These innovations include temperature sensors that connect to an app on a smartphone, allowing the user to monitor the temperature of the pot remotely. This type of feature could be particularly appealing to tech-savvy cooks who want more control over their cooking processes. Smart stock pots could even include automatic stirring systems that gently agitate the contents of the pot while cooking, ensuring even heat distribution and preventing burning.
Smart cookware isn’t just about convenience—it also improves cooking accuracy, reducing the margin for error in recipes that require precise temperatures, such as simmering soups or sauces for long periods. This integration of technology could also provide users with alerts when it’s time to stir, add ingredients, or check on cooking progress. With the rise of smart kitchens, the integration of voice control systems, such as those used with Amazon Alexa or Google Assistant, could further enhance the appeal of stock pots as part of the larger smart home ecosystem.
In addition to these technological advancements, the growing popularity of induction cooking is influencing the design and materials used in stock pot production. Induction cooking requires cookware with ferrous metals in order to work properly with induction cooktops, which generate a magnetic field to heat the pot directly. Manufacturers are responding to this trend by designing stock pots that are induction-compatible and have a ferrous bottom layer to ensure efficient heat transfer. As induction cooking becomes more prevalent, particularly in residential kitchens, cookware manufacturers must ensure their products are optimized for this type of heat source.
Another trend in the cookware industry is the increasing demand for multi-functional cookware that serves more than one purpose. For example, stackable stock pots are gaining popularity because they allow users to save space while still being versatile enough to accommodate large meals. These products can be used for boiling, simmering, frying, or steaming in a single pot, making them ideal for consumers with limited kitchen storage space. Manufacturers are creating designs that include interlocking lids, removable dividers, or multi-purpose handles, offering consumers the ability to use the same pot for different types of cooking.
The rise of direct-to-consumer (DTC) models is also shaking up the cookware industry. Traditionally, stock pots and other cookware items were sold through large retail chains, but more manufacturers are opting to sell directly to consumers through online platforms. This shift allows companies to engage more closely with their customer base, offer customizations, and potentially lower prices by cutting out the middleman. It also gives them greater control over branding, customer service, and product feedback. E-commerce has revolutionized the way consumers shop for cookware, with online reviews and social media playing a significant role in influencing purchasing decisions. Companies can use these platforms to provide educational content, cooking tips, and even online cooking demonstrations to create a deeper connection with their audience.
In addition, crowdsourcing and crowdfunding platforms, such as Kickstarter or Indiegogo, have opened up new avenues for manufacturers to fund the development of new stock pot designs. These platforms allow creators to test the market for innovative ideas and gather support from early adopters. Crowdfunding can also help manufacturers gauge the level of interest in new product concepts, whether it’s a new non-stick coating or a completely redesigned stock pot with unique features.
Finally, as global trade continues to grow, manufacturers must stay informed about trade regulations and tariffs, particularly as raw materials or finished products are sourced from different countries. Trade tariffs, environmental regulations, and shifting economic conditions can have a significant impact on production costs. Manufacturers must develop strategies to mitigate these risks, such as sourcing materials from regions with lower tariffs or shifting production to different countries based on regulatory changes.
By embracing these innovations and strategies, stock pot manufacturers can position themselves for success in a rapidly changing market. Whether it’s through embracing new materials and coatings, integrating advanced technology into their products, focusing on sustainability, or adopting direct-to-consumer models, staying ahead of these trends is key to maintaining a competitive edge and meeting the evolving demands of today’s consumers.
Sheet Metal Saucepan Production Machine
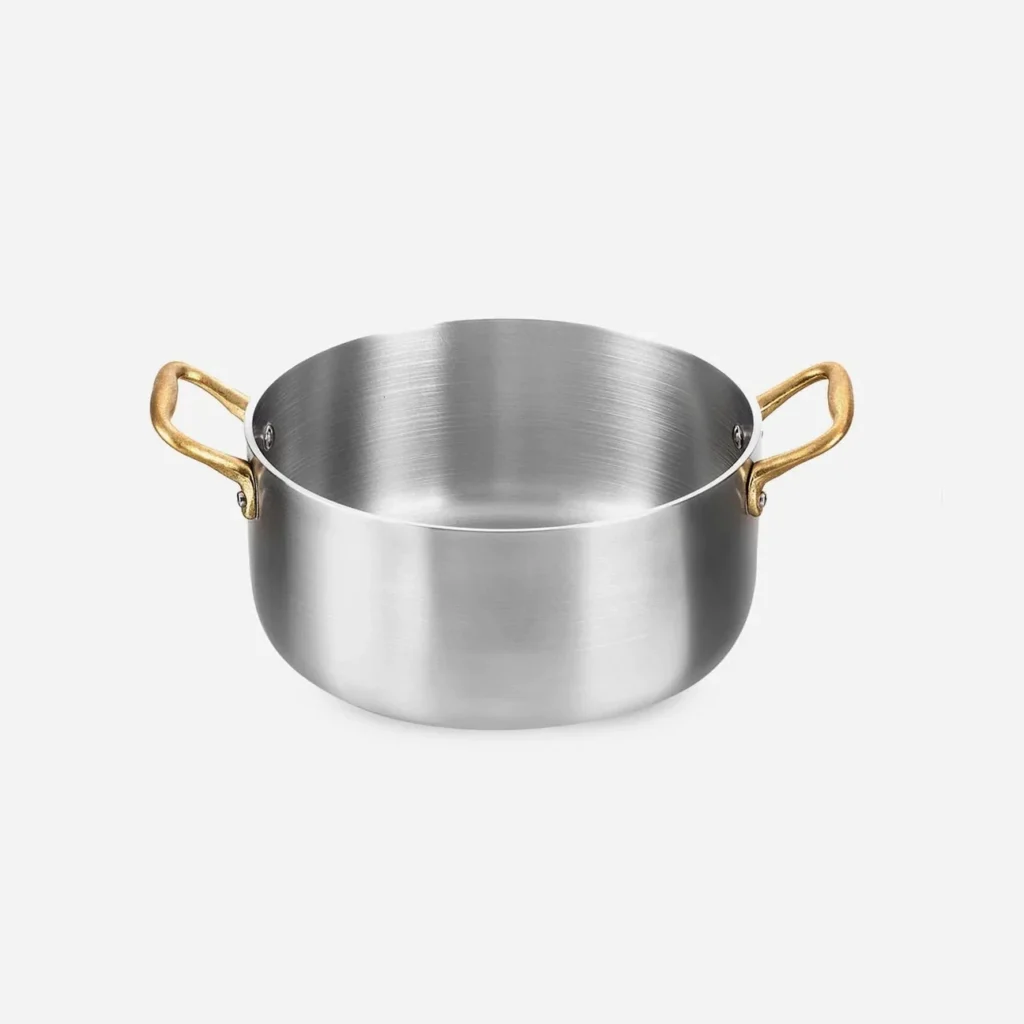
The production of sheet metal saucepans involves a sequence of steps that ensure the finished product is durable, functional, and aesthetically appealing. The machine used for producing saucepans is designed to handle the various stages of manufacturing, from raw material handling to the final packaging of the product. Below is an overview of the machinery involved in the production of sheet metal saucepans:
1. Material Preparation:
- Coil Unwinding Machine (Decoiler): The process begins with a coil of metal (usually stainless steel, aluminum, or carbon steel). The coil is placed into a decoiler, which unwinds the metal sheet as it is fed into the production line.
- Cutting Machine (Blanking Press): The metal sheet is then cut into flat circles or blanks. These blanks are the initial shapes that will be formed into saucepans. A blanking press is used to ensure precise cutting of the sheets.
2. Forming Process:
- Deep Drawing Press: The blank is transferred to a deep drawing press, which forms the body of the saucepan by stretching the metal into a deeper, cup-like shape. The forming process is critical, as it needs to ensure that the walls of the saucepan are even and without defects.
- Stages of Forming: The blank may go through multiple drawing stages to achieve the desired shape and depth. The press can be equipped with dies that determine the shape and size of the saucepan.
- Quality Control: The forming process is closely monitored to avoid defects such as wrinkles, thinning of the metal, or uneven walls.
3. Trimming and Edge Finishing:
- Edge Trimming and Forming Machine: After the body has been drawn, the edges of the saucepan are trimmed to ensure smoothness and uniformity. This is done using an edge trimming machine that removes any excess metal and creates a smooth, consistent edge. The machine can also apply slight forming to round off the edges if necessary.
4. Handle Attachment:
- Handle Welding or Riveting Machine: The next step involves attaching the handles to the saucepan. Handles can be welded, riveted, or mechanically fastened to the body of the saucepan, depending on the design.
- Welding: Some saucepans have handles that are welded onto the body for a strong, permanent attachment. TIG (Tungsten Inert Gas) welding is commonly used in this case, ensuring that the bond is both durable and clean.
- Riveting: For some designs, handles are attached using rivets, which are inserted and deformed to securely hold the handle in place.
5. Surface Finishing:
- Polishing/Brushing Machine: The surface of the saucepan is then treated to improve both its appearance and performance. This may involve polishing or brushing the surface to give it a smooth, shiny, or matte finish.
- Polishing: For high-end saucepans, a polishing machine is used to give the metal a bright, reflective surface.
- Brushing: In other cases, a brushed finish may be applied, which is more matte and can reduce the appearance of fingerprints and scratches.
- Coating Machine (Optional): If the saucepan is to have a non-stick coating, the next stage involves applying the coating. This can be done through spraying or dipping, followed by a curing process.
- Non-Stick Coating: Common coatings include PTFE (polytetrafluoroethylene) or ceramic coatings, which offer non-stick properties for easier cooking and cleaning.
- Surface Curing: The coated saucepan is then placed in a curing oven, where the coating is baked at high temperatures to ensure adhesion and durability.
6. Inspection and Quality Control:
- Automated Inspection System: Throughout the production process, automated inspection systems check for defects such as cracks, warps, surface imperfections, and thickness variations. These systems may use optical sensors or laser scanners to scan the surface of the product for any anomalies.
- Manual Inspection: Additionally, skilled operators perform visual checks to ensure that the handles are secure, the surface finish meets standards, and that the product is free from defects.
7. Packaging:
- Packing Station: Once the saucepan has passed all quality checks, it is ready for packaging. The packaging process involves placing the saucepan in protective materials (like foam or cardboard) to prevent damage during transportation.
- Labeling: Labels are applied with product details, including brand name, instructions, and other relevant information.
- Boxing: The saucepan is then placed into boxes for shipment. Multiple pieces can be stacked together, and the boxes are sealed for safe transport.
8. Automation and Robotics:
- Robotic Arm Systems: To increase efficiency and reduce labor costs, robotic arms are often used to transfer materials, move products between stages, or load and unload products from machines. These robotic systems can handle large quantities of products with precision and speed.
- Automated Material Handling: A fully automated production line may also include conveyor systems that move the saucepan components between machines, reducing manual labor and increasing the overall throughput.
9. Energy Efficiency and Sustainability:
- Energy-Efficient Machines: Modern saucepan production lines are designed with energy-efficient machinery to minimize electricity consumption, especially in processes like heating and coating. Some manufacturers also incorporate solar energy or recycled materials into the production process to reduce environmental impact.
- Waste Reduction: Manufacturers are also adopting systems to recycle scrap metal and packaging materials to reduce waste and improve sustainability.
Key Considerations for Saucepan Production:
- Material Selection: Choosing the right material is critical for producing high-quality saucepans. Stainless steel is a popular choice due to its durability, resistance to rust, and non-reactivity with food. Aluminum is often used for its lightweight properties and excellent heat conductivity, though it may need to be coated for strength and durability.
- Design Flexibility: Some machines allow for adjustments in the design, such as different handle styles, lid fittings, or base shapes. This flexibility ensures that manufacturers can meet market demands for various saucepan sizes and designs.
- Heat Treatment and Hardening: In some cases, heat treatment may be applied to harden specific areas of the saucepan, such as the base or handle, for added strength and wear resistance.
Final Thoughts:
The production of sheet metal saucepans relies heavily on a combination of precise machinery and skilled operators to ensure high-quality products. Automation, efficiency, and sustainability are key drivers in modern saucepan manufacturing, and the integration of advanced technologies like robotic systems and automated inspections is helping manufacturers meet the growing demands of both the consumer market and regulatory standards.
In the production of sheet metal saucepans, the overall focus is on achieving a high-quality, durable product that meets both functional and aesthetic requirements. The manufacturing process begins with raw material preparation, where coils of stainless steel or aluminum are unwound and cut into the required shape for the saucepan body. The next crucial step is the deep drawing process, where the metal is formed into the saucepan’s body. This stage requires precise control to prevent defects like wrinkles or thinning of the material. The deep drawing press stretches the metal into a cup-like shape, ensuring uniformity in wall thickness, which is essential for even heat distribution during cooking.
Once the body is formed, the edges of the saucepan are trimmed to smooth out any excess material, and the final shaping is done to ensure that the edges are clean and consistent. The handle attachment process follows, which can involve welding, riveting, or mechanical fastening, depending on the design. Handles are a critical part of the saucepan, not only for comfort and safety but also for ensuring that the product is both functional and ergonomic. Welding methods, like TIG welding, are used to securely attach metal handles, while riveting may be used for certain handle designs that require a more robust connection.
After the handles are attached, the saucepan undergoes various surface finishing processes. This step can involve polishing or brushing the surface to improve its appearance and usability. Some manufacturers apply non-stick coatings to the interior, which requires additional steps like spraying, curing, and baking. The coating process is crucial for enhancing the cooking experience, as non-stick surfaces make it easier to clean and prevent food from sticking during cooking. Manufacturers may opt for coatings that are safer, such as ceramic coatings, as consumers become more conscious of the chemicals used in traditional non-stick surfaces.
Quality control is a continuous process throughout the production line. Automated systems are used to scan and inspect each saucepan for any imperfections, whether they are in the metal forming, coating, or finish. If a defect is detected, the product is removed from the production line and sent for rework. This ensures that only products that meet stringent standards are sent to the next stages, including packaging and distribution.
Packaging, though often seen as the final step, is an integral part of the process, as it ensures that the finished product reaches consumers without damage. Manufacturers utilize various forms of protective packaging materials, like foam inserts or cardboard, to shield the saucepans during transit. Additionally, many brands are shifting toward more sustainable packaging, which not only meets consumer expectations for eco-friendly products but also reduces waste and promotes recycling.
As consumer preferences shift, manufacturers of sheet metal saucepans are increasingly focusing on innovative designs, customization options, and sustainability in production. The demand for eco-friendly materials and manufacturing processes is growing, with many companies investing in energy-efficient machines and greener alternatives like recycled metals. This focus on sustainability extends beyond materials and into the production methods themselves, where manufacturers are looking for ways to reduce energy consumption and minimize waste.
On the technological front, the integration of smart technologies is becoming a significant trend in the cookware industry. Smart saucepans with temperature sensors and app connectivity are being developed to allow for better control over cooking conditions, creating a more seamless cooking experience. This trend is part of the larger smart kitchen movement, where cookware products are expected to interact with other kitchen appliances and even allow remote control or monitoring via smartphone apps.
In conclusion, the production of sheet metal saucepans is an intricate process that requires precision, efficiency, and a keen understanding of consumer needs. As the industry continues to innovate, both in terms of product design and manufacturing techniques, there is a strong emphasis on quality, sustainability, and technology integration to meet the evolving demands of the market. By adapting to these trends, manufacturers can ensure that their products not only remain competitive but also align with the growing expectations of today’s environmentally conscious and tech-savvy consumers.
Continuing from the previous points, the production of sheet metal saucepans is increasingly influenced by a variety of market trends and technological advancements. One such advancement is the integration of induction compatibility. As induction cooking continues to grow in popularity due to its energy efficiency and precise control, manufacturers are ensuring that their saucepans are designed to work seamlessly with induction cooktops. This requires the use of magnetic materials in the saucepan’s base, such as stainless steel or specially designed ferrous metals, to generate the magnetic field needed for induction heating.
In addition, material innovation continues to play a key role in the design of saucepans. There is growing interest in high-performance materials that not only enhance the cooking experience but also make the cookware more durable and long-lasting. For example, some manufacturers are experimenting with tri-ply constructions, where layers of stainless steel are combined with aluminum or copper to provide optimal heat conduction. These multi-layered constructions offer better heat distribution and reduce hot spots, ensuring that food cooks evenly. Similarly, the use of stainless steel alloys with improved corrosion resistance or hardened aluminum is becoming more common to extend the lifespan of the saucepan and reduce the likelihood of wear over time.
Ergonomics is another factor that manufacturers are paying closer attention to. The design of saucepan handles is evolving to enhance comfort and safety. Handles are being made with heat-resistant materials to prevent burns, and ergonomic shapes are incorporated to ensure a secure and comfortable grip during cooking. Additionally, detachable or foldable handles are gaining popularity, as they offer space-saving benefits, particularly for consumers with smaller kitchens or for cookware that needs to be stored in tight spaces.
Smart technology is one of the most significant trends currently shaping the cookware industry. Some of the more advanced saucepans are being designed to incorporate sensors that can track cooking temperatures in real-time, sending this data to a smartphone app. These sensors ensure that the saucepan maintains the desired temperature and can alert users when their food is ready. This feature is particularly useful for dishes that require precise heat control, like sauces or broths. Some high-end models even integrate with voice-activated smart assistants (such as Alexa or Google Assistant), allowing users to control or monitor cooking via voice commands. In the future, this could extend to features like automatic stirring or temperature adjustments, further reducing the need for constant oversight.
The use of sustainability in production processes continues to be a driving factor in the cookware industry. With growing concerns over the environmental impact of manufacturing, many companies are exploring ways to reduce their carbon footprint. Manufacturers are increasingly turning to recycled metals for the production of saucepans, as this not only reduces the reliance on raw materials but also minimizes energy consumption during the production process. For instance, aluminum, which is widely used in cookware, is particularly energy-intensive to produce from raw materials. However, recycled aluminum requires significantly less energy, making it a more sustainable option.
In parallel, manufacturers are focusing on reducing waste generated during production. Advanced CNC (Computer Numerical Control) machines allow for precise cutting and shaping of the metal, ensuring that very little scrap is produced. Some companies are also employing closed-loop systems that collect and recycle scrap metal during production, ensuring that it is reused rather than discarded. This move towards a more circular production model not only reduces waste but also helps meet increasingly stringent environmental regulations.
As demand for premium cookware increases, many manufacturers are emphasizing aesthetic design alongside performance. Consumers are looking for products that not only work well but also fit into their kitchens with a high-end appearance. In response, manufacturers are offering a variety of finishes, such as brushed stainless steel, polished, or even copper-coated saucepans, to appeal to different tastes. The trend toward minimalist and sleek designs is evident in the reduction of extraneous features like excessive branding or overly complex handle structures. Instead, clean lines, simple shapes, and high-quality materials are prioritized.
To enhance the appeal of their products, some manufacturers also offer customization options, allowing consumers to select from a range of finishes, handle materials, or even sizes. These customizations cater to niche markets and enable companies to differentiate themselves from competitors.
In terms of retail and distribution, the landscape is evolving as well. Traditional retail channels, such as department stores and specialty cookware stores, continue to dominate, but the rise of e-commerce has led many manufacturers to explore direct-to-consumer (DTC) models. By selling directly through their websites or platforms like Amazon, manufacturers can offer better prices, collect customer data, and build stronger relationships with their consumers. Moreover, social media marketing has become an essential tool for cookware brands, with influencers and chefs using platforms like Instagram and YouTube to promote cookware lines and demonstrate their use in cooking.
Another area where technology plays a role is in production efficiency. Advanced manufacturing techniques such as robotics and automation have greatly improved production speed and consistency. For example, robotic arms can handle the transfer of parts between machines, while automated systems manage the inspection and quality control process, ensuring a higher level of accuracy. These improvements reduce labor costs and increase production throughput, allowing manufacturers to meet growing demand while maintaining product quality.
Finally, the globalization of the cookware market means that manufacturers are increasingly producing saucepans for international markets with varying consumer preferences. For example, in some regions, there is a growing demand for non-stick saucepans, while others prioritize stainless steel for its durability and traditional appeal. Additionally, the rise of cooking culture in countries around the world has led to a higher demand for high-quality cookware, further expanding the market for premium and specialized saucepans.
In summary, the production of sheet metal saucepans is an evolving process that integrates cutting-edge technologies, material innovations, and consumer preferences. Manufacturers who focus on durability, functionality, sustainability, and design will be best positioned to succeed in an increasingly competitive and environmentally conscious market. As the industry embraces these advancements, the future of saucepan production will continue to reflect a blend of tradition and innovation, catering to both home cooks and professional chefs alike.
Continuing from the earlier discussion, the future of sheet metal saucepan production is increasingly influenced by evolving consumer preferences, advancements in manufacturing techniques, and global market trends. A major focus is on innovation in cooking performance and efficiency. As technology continues to integrate into kitchenware, smart cookware will likely become more commonplace. The use of temperature sensors, heat control mechanisms, and automatic cooking functions is already being explored in high-end models. This could mean that, in the near future, sheet metal saucepans could be equipped with sensors that communicate directly with smart kitchen systems to adjust heat levels, detect cooking progress, and even suggest recipes.
Another development in this area is cookware with multi-functional capabilities. For example, saucepans with detachable handles or stackable designs are becoming increasingly popular, offering space-saving benefits in small kitchens. Similarly, there is a growing interest in modular cookware systems where different pieces can be combined or interchanged to create versatile cooking tools. Manufacturers are also introducing products that function across multiple types of cooktops, including gas, electric, ceramic, and induction, making them more versatile and appealing to a wider audience.
As more consumers gravitate towards sustainable lifestyles, cookware manufacturers are responding by focusing on eco-friendly materials and greener production processes. Beyond the use of recycled metals, manufacturers are seeking alternative ways to reduce the environmental footprint of their production lines. The carbon footprint of manufacturing processes is now being closely monitored, and many companies are investing in energy-efficient machinery and solar-powered facilities to reduce their impact. Moreover, the use of non-toxic, biodegradable coatings for non-stick surfaces is being researched as a more environmentally responsible alternative to traditional coatings that contain PTFE or PFOA, which have been controversial due to their potential health and environmental risks.
Circular economy principles are also beginning to influence cookware design. Instead of traditional production methods that generate excess waste, companies are designing saucepans and other cookware with end-of-life recycling in mind. The idea is that when the product reaches the end of its life cycle, it can be easily recycled or repurposed into new products. Some brands are introducing repairable products, allowing consumers to fix broken handles or damaged parts rather than discarding the entire saucepan, promoting longer product lifespans.
Customization remains a strong trend, as consumers seek cookware that suits their personal preferences and style. Manufacturers are offering bespoke options where customers can choose specific features such as handle materials (e.g., wooden, silicone, or stainless steel handles), surface finishes (e.g., matte, polished, or brushed), or even the color of the cookware. This trend is particularly strong in markets where personalization and premium quality are highly valued. The ability to mix and match colors, sizes, and designs allows consumers to create a personalized cooking experience that aligns with their kitchen aesthetics.
Smart manufacturing processes continue to evolve, with an increasing reliance on artificial intelligence (AI), machine learning, and big data analytics. These technologies enable manufacturers to predict potential defects or inefficiencies in the production process before they occur, enhancing quality control and minimizing waste. AI systems can track every step of the manufacturing process, from material sourcing to final packaging, ensuring that each saucepan meets the required specifications and is free from defects. The use of predictive maintenance is also becoming more common, where machines are monitored for signs of wear and tear, and maintenance is carried out before failures happen, improving uptime and reducing costs.
The advent of direct-to-consumer sales channels is also changing the cookware market. With the rise of e-commerce platforms, consumers are now more accustomed to shopping online, where they can access a wide range of products from global brands. Online retailers and cookware brands have the opportunity to provide personalized customer experiences, from offering product recommendations based on past purchases to offering virtual consultations with chefs or culinary experts. Additionally, subscription services are being explored in the cookware industry, where consumers can receive cookware or related products on a regular basis, such as specialty pans or cooking accessories, which encourages continued brand loyalty.
Global expansion remains an essential focus for cookware manufacturers, particularly as emerging markets in Asia, Latin America, and Africa show increasing interest in high-quality cookware. As economies grow in these regions, so does the demand for durable and aesthetically pleasing cookware. For companies expanding into these markets, it is important to tailor products to local tastes, preferences, and cooking styles. For instance, in some parts of Asia, there is a high demand for cookware that is compatible with traditional woks and steamer baskets, which may require specific adjustments to the saucepan design. In other regions, consumers may prioritize ease of use and versatility, with an emphasis on multi-functional cookware that can be used across various cooking surfaces.
In addition to global market dynamics, manufacturers must also contend with changing regulatory standards. Governments around the world are implementing stricter regulations regarding the safety, health, and environmental impact of products. For cookware, this includes the use of non-toxic materials, chemical regulations, and energy efficiency standards for production processes. Companies that fail to comply with these regulations risk losing access to key markets, which is why ongoing investment in compliance and certification is critical for continued success.
Finally, brand differentiation will remain an essential strategy in a highly competitive market. As more brands enter the cookware space, it becomes crucial for manufacturers to carve out a niche for themselves by offering unique selling points (USPs) that resonate with consumers. Whether it’s through superior heat conduction, non-stick coatings, stylish designs, or eco-friendly production processes, differentiation will play a key role in driving customer loyalty and establishing long-term market presence.
In conclusion, the future of sheet metal saucepan production is characterized by a combination of technological innovation, sustainability, and evolving consumer preferences. Manufacturers are embracing advanced technologies, eco-friendly materials, and customized designs to meet the demands of an increasingly discerning market. As consumer expectations continue to shift toward smarter, more sustainable, and aesthetically pleasing cookware, manufacturers must remain adaptable and forward-thinking to stay ahead of the competition and deliver products that offer both functionality and style.
Sheet Metal Frying Pan Production Machine
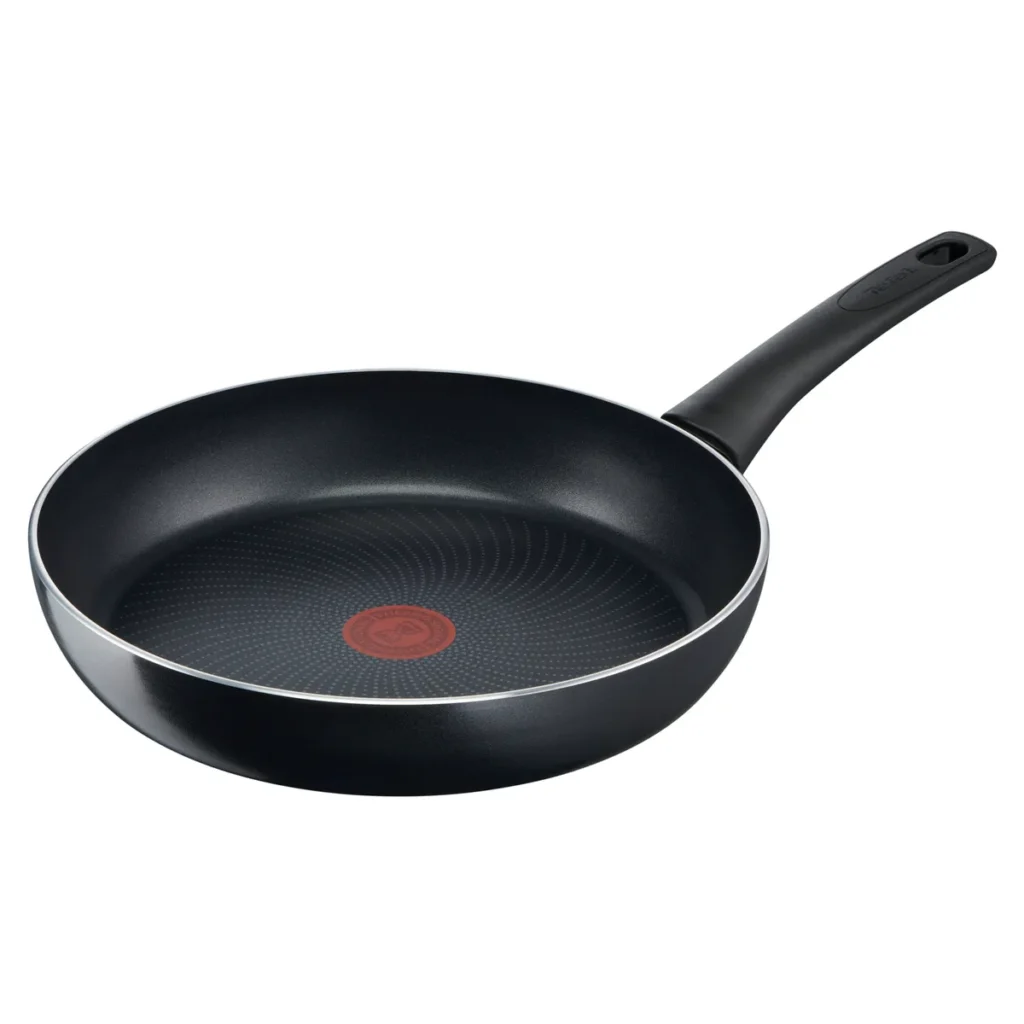
The production of sheet metal frying pans involves a series of well-coordinated steps, utilizing advanced machinery and techniques to create durable, functional, and aesthetically pleasing cookware. The process focuses on ensuring that the frying pan is of high quality, with good heat distribution, non-stick properties (if applicable), and a durable finish. Below is a general breakdown of the production process for a sheet metal frying pan, including the types of machinery and technologies involved:
1. Material Preparation
- Raw Material: The primary material used for frying pans is typically aluminum, stainless steel, or a combination of both, with aluminum being favored for its lightweight and excellent heat conductivity properties. In some cases, carbon steel or cast iron is used, though these materials require slightly different processing methods.
- Coil Unwinding: Large coils of metal are unrolled and cut into the required size for the frying pan. This can involve cutting machines that slice the metal into the desired sheet size based on the frying pan’s diameter.
2. Deep Drawing / Forming
- Deep Drawing: The main body of the frying pan is formed using a deep drawing press. This machine uses a punch and die system to transform flat metal sheets into a shallow cup-like shape. The metal is stretched over a die, ensuring a uniform thickness around the circumference. This stage is crucial for creating the frying pan’s bowl shape, with attention paid to avoid wrinkling or thinning of the metal.
- Trimming and Edge Forming: After the drawing process, the excess material around the edges is trimmed off to ensure smooth and even edges. The edges are often further rolled or beaded to reinforce their strength and prevent sharp or rough edges.
3. Handle Attachment
- Handle Design: Frying pan handles can be made of stainless steel, wood, plastic, or silicone for heat resistance. For stainless steel frying pans, the handle is often welded, riveted, or screwed into place.
- Handle Welding or Riveting: In the case of welded handles, TIG welding (Tungsten Inert Gas) is commonly used to ensure a secure, strong, and seamless attachment to the pan. Alternatively, handles may be riveted to the frying pan using high-tensile steel rivets. In some designs, handles may be detachable for easy storage.
4. Surface Treatment
- Polishing / Brushing: The surface of the frying pan is polished or brushed to achieve the desired finish, which can be matte, brushed stainless steel, or polished. This gives the frying pan its sleek and professional appearance. In some cases, a mirror finish may be applied, especially for high-end products.
- Coating Application: If a non-stick frying pan is being produced, a non-stick coating (such as PTFE or ceramic-based coatings) is applied to the interior of the frying pan. This is typically done through a spraying process followed by a curing oven, where the coating is baked onto the surface to ensure its durability.
- Anodizing or Hardening: For aluminum pans, anodizing may be used to harden the surface, making it more durable and resistant to scratches and corrosion. This process involves an electrochemical treatment that creates a hard, protective layer over the aluminum.
5. Quality Control
- Visual Inspection: After forming and finishing, each frying pan undergoes a detailed visual inspection to ensure there are no defects in the surface, shape, or handle attachment. This is often performed manually or using automated systems that use machine vision to detect imperfections.
- Testing: Frying pans undergo several performance tests, including heat distribution tests and handle strength tests. In non-stick frying pans, adhesion tests are also conducted to ensure that the non-stick coating is securely bonded and durable.
6. Packaging and Shipping
- Packaging: After the frying pans pass inspection, they are carefully packaged to prevent damage during transport. Depending on the manufacturer, this could involve cardboard boxes, foam inserts, or shrink-wrapping. In some cases, eco-friendly packaging is utilized to align with sustainability goals.
- Labeling: Frying pans are labeled with branding, product specifications, and care instructions. If the frying pan is marketed as non-stick or induction compatible, these features will be prominently displayed on the label.
- Shipping: Finally, the frying pans are shipped to retailers or directly to consumers via e-commerce platforms.
Key Machinery in Frying Pan Production:
- Deep Drawing Presses: Used for forming the pan body from flat metal sheets.
- CNC Punching Machines: For precise trimming and shaping.
- Welding Machines: For attaching handles to the frying pan.
- Polishing Machines: For achieving a smooth and high-quality finish.
- Coating Systems: For the application of non-stick coatings or anodizing treatments.
- Inspection Equipment: Including visual inspection systems and automated quality control checks.
Innovations in Frying Pan Production
- Induction Compatibility: Frying pans are increasingly being designed for use with induction cooktops. This requires the base of the frying pan to have a magnetic layer, typically added during the base-forming step, using ferrous metals.
- Ergonomics: There is a growing focus on ergonomically designed handles to ensure comfortable and safe use. Heat-resistant handles made from materials like Bakelite, silicone, or stainless steel are often used to provide comfort during cooking.
- Sustainability: In response to consumer demand, manufacturers are using recycled metals, minimizing the environmental impact of their production processes, and opting for eco-friendly coatings.
In summary, the production of sheet metal frying pans involves advanced processes like deep drawing, handle attachment, surface finishing, and quality control to create high-quality, durable, and functional products. Innovations such as induction compatibility, ergonomic design, and sustainable practices are shaping the future of frying pan manufacturing, ensuring that these kitchen essentials meet both the practical and aesthetic needs of modern consumers.
The production of sheet metal frying pans is a complex process that blends technology, craftsmanship, and precision to create cookware that is both durable and functional. The journey begins with the selection of high-quality raw materials such as stainless steel, aluminum, or a combination of metals that offer excellent heat conductivity. The metal is then unwound from coils and cut into sheets, which are the starting point for the deep drawing process. This step involves using a deep drawing press to form the flat metal sheets into the desired shape of the frying pan. The pan’s body takes form as the metal is stretched over a die to create a shallow, cup-like structure. The precision in this step is critical because any imperfection in the metal at this stage can affect the pan’s ability to cook evenly or compromise its structural integrity.
Once the pan’s shape is formed, attention is given to the edges. They are trimmed to remove any excess metal, creating smooth, clean lines. Often, the edges are reinforced through a rolling or beading process, which not only improves the pan’s appearance but also ensures that it is sturdy and safe to handle. At this point, the frying pan begins to resemble the final product, but further work is needed to enhance its functionality and durability.
The next step involves attaching the handle to the frying pan. Handles are designed to be ergonomic, offering a comfortable and secure grip, as they are one of the most critical aspects of the pan’s usability. Depending on the design, the handle is either welded, riveted, or screwed into place. Welding is typically done using a precise TIG (Tungsten Inert Gas) welding technique, which ensures a strong, seamless bond. Riveting is another common method, particularly for pans with a more traditional design, where high-tensile steel rivets hold the handle in place. Handles may be made from materials such as stainless steel, silicone, or even wood, with each offering different benefits in terms of heat resistance, aesthetics, and comfort.
With the handle securely in place, the frying pan undergoes a surface treatment process to improve its performance and appearance. Polishing or brushing the surface helps to achieve a desired finish, such as a matte or polished surface. This step is essential not just for aesthetics, but also for functional purposes, as it can improve resistance to corrosion and make cleaning easier. For frying pans designed with non-stick surfaces, the interior is coated with materials like PTFE (Teflon) or ceramic-based coatings. These coatings are applied through a spraying process, followed by a curing oven where the coating is baked onto the pan, ensuring that it adheres firmly and lasts through repeated use. Non-stick coatings are crucial for reducing food sticking to the pan during cooking, making it easier to clean and preventing the need for excessive amounts of oil.
In some cases, frying pans may undergo an additional process of anodizing or hardening, especially if the pan is made from aluminum. Anodizing increases the hardness of the surface and enhances the pan’s resistance to scratches and corrosion, improving its overall durability. This process also makes the metal more resistant to staining, which is an important feature for pans used in high-heat cooking situations.
Quality control plays an essential role throughout the production process. After each significant step, frying pans are inspected for defects, ensuring that no imperfections in the metal, coating, or handle are overlooked. Automated systems equipped with visual inspection technology may be employed to detect any irregularities, while manual inspections provide a more thorough check to ensure the product meets the required standards. Frying pans may also undergo performance testing, including checks for heat distribution, handle strength, and coating adhesion. Non-stick frying pans, in particular, undergo tests to ensure that the coating adheres correctly and that it will not peel or wear prematurely under normal use.
Once the frying pans pass quality control, they are packaged carefully for shipping. The packaging process typically involves protective materials such as foam inserts, shrink-wrapping, or cardboard boxes to prevent damage during transport. The packaging often includes the manufacturer’s branding, product information, and care instructions, helping consumers to understand how to properly care for their new cookware. Some manufacturers also use eco-friendly packaging materials to align with growing consumer interest in sustainability.
As trends in cookware manufacturing continue to evolve, there is a growing emphasis on developing products that meet the needs of modern consumers. This includes innovations like induction compatibility, where frying pans are designed with magnetic bases to work on induction cooktops. Additionally, ergonomic handle designs that are heat-resistant and comfortable are being prioritized to enhance the overall cooking experience. As consumer demand for eco-friendly products increases, more manufacturers are exploring the use of recycled metals and non-toxic, biodegradable coatings. Manufacturers are also becoming more mindful of their carbon footprint by adopting energy-efficient production methods and sustainable materials.
In the future, smart technology may become a more prominent feature of frying pan production. Frying pans equipped with temperature sensors or Bluetooth connectivity could allow users to monitor cooking conditions in real-time, adjusting heat levels or receiving alerts when the food is ready. Such innovations would take cooking to a new level of convenience, aligning with the growing trend of smart kitchens.
Moreover, the global market for frying pans continues to grow, driven by consumer interest in high-quality cookware that combines functionality with style. Manufacturers are responding to this demand by offering a wide range of finishes, sizes, and designs, ensuring that frying pans cater to a variety of cooking styles and personal preferences. With the increasing popularity of premium cookware and a focus on sustainability, the production of sheet metal frying pans is likely to evolve in ways that not only improve their performance but also ensure that they meet the ethical, environmental, and aesthetic demands of today’s consumers.
As frying pan production continues to evolve, manufacturers are finding new ways to incorporate emerging technologies and meet shifting consumer preferences. One significant area of development is the integration of smart technology into cookware. As more consumers embrace smart kitchens, the potential for frying pans with built-in sensors or IoT connectivity is growing. These smart frying pans could track the temperature of the pan, alert users when it reaches the ideal cooking temperature, or even provide suggestions for optimal cooking times based on the type of food being prepared. This could be especially valuable for precise cooking methods, such as searing meats or preparing delicate sauces, where temperature control is crucial.
Additionally, frying pans with induction-capable bases are becoming increasingly common. Induction cooking relies on electromagnetic fields to directly heat the pan, making it more energy-efficient and allowing for precise temperature control. To cater to this, frying pans designed for induction cooktops feature a magnetic layer on the base, which is typically applied through a process of bonding ferrous metal to the underside of the pan. This adaptation enables manufacturers to offer versatile frying pans that are compatible with all cooking surfaces, including gas, electric, ceramic, and induction cooktops. The growing popularity of induction cooking is driving demand for these specialized frying pans.
There is also a noticeable shift toward multi-functional cookware. Many frying pans are being designed to serve dual purposes, such as oven-safe frying pans that can transition seamlessly from stovetop to oven. These pans are typically made from materials like cast iron or stainless steel and feature heat-resistant handles and lids that allow users to easily move the pan from one cooking environment to another. This trend toward versatility not only enhances convenience but also appeals to consumers looking for cookware that can handle a wide variety of cooking methods, from sautéing to baking.
With sustainability at the forefront of consumer concerns, frying pan manufacturers are increasingly turning to eco-friendly materials and green production processes. Recycled aluminum, in particular, is gaining popularity as a sustainable option for frying pan production. Using recycled metals reduces the environmental impact of the manufacturing process and lowers energy consumption compared to using raw materials. Some manufacturers are also moving toward non-toxic, environmentally friendly coatings for non-stick frying pans, replacing traditional PTFE-based coatings with alternatives like ceramic coatings. These coatings are free from harmful chemicals like PFOA, and they offer a safer, more environmentally conscious choice for consumers.
In line with this, frying pan brands are exploring eco-conscious packaging. Packaging made from recycled cardboard, biodegradable plastics, and other sustainable materials is becoming more common as consumers demand products that not only deliver on performance but also contribute to environmental conservation. Manufacturers are also streamlining their supply chains to reduce waste, using local sourcing for materials and adopting lean manufacturing techniques to minimize excess production.
In terms of design, there is a growing emphasis on ergonomics and ease of use. Consumers are increasingly looking for frying pans that are not only functional but also comfortable to use. Features like heat-resistant silicone handles, non-slip grips, and lightweight designs are becoming standard in many high-end frying pans. These features make cooking more comfortable and less dangerous, especially when handling hot pans for extended periods.
Another growing trend is the customization of frying pans. While many consumers have historically been satisfied with standard designs, there is now a desire for personalized cookware that fits individual tastes and needs. Some manufacturers are offering customization options where customers can choose everything from the material and finish to the color of the pan’s exterior and handle. This can be particularly appealing to consumers looking for cookware that matches the aesthetics of their kitchen or who want unique, one-of-a-kind products.
The shift toward health-conscious cooking is also influencing frying pan design. Non-stick frying pans, which are often favored for their ability to reduce the amount of oil needed for cooking, continue to evolve. Many manufacturers are focusing on creating durable non-stick surfaces that can withstand higher cooking temperatures without deteriorating. As consumers become more aware of the health implications of certain chemicals used in cookware coatings, there is an increasing demand for chemical-free non-stick coatings that are safer for both cooking and the environment. Ceramic coatings are a popular alternative because they offer non-stick functionality without the risks associated with PTFE-based coatings.
As global markets continue to evolve, international expansion becomes an important factor in the success of frying pan brands. Manufacturers are increasingly adapting their designs and marketing strategies to meet the needs of consumers in different regions. In Asia, for example, frying pans with smaller diameters and deeper sides are favored for stir-frying and cooking rice, while in Europe, there is a preference for larger, flatter pans that are versatile enough to handle a variety of cooking styles. Understanding and catering to regional preferences helps brands penetrate new markets and drive growth.
Frying pan production is also benefiting from the integration of artificial intelligence (AI) and automation. Many manufacturers are now using AI-driven systems for quality control and defect detection. These systems utilize high-resolution cameras and machine learning algorithms to scan frying pans for any imperfections during the production process. The result is a higher level of precision and faster production times, reducing waste and increasing overall efficiency. Robots are also being used in various stages of frying pan assembly, including handle attachment and packaging, which reduces human error and enhances the speed of production.
Lastly, the consumer experience is becoming a central focus for frying pan manufacturers. Many brands are exploring ways to offer more than just a functional product; they are building customer loyalty by providing cooking tips, recipe suggestions, and even digital content such as video tutorials and online cooking classes. Some brands are offering subscription services, where consumers receive new cooking tools or specialty frying pans delivered regularly. This type of customer engagement can foster a deeper connection with the brand and encourage repeat purchases.
In conclusion, the future of sheet metal frying pan production is marked by advancements in material science, smart technology, sustainability, and consumer customization. Manufacturers are continuously exploring new ways to improve the functionality, safety, and convenience of frying pans while also responding to growing demand for eco-friendly products. As cooking technology continues to progress, frying pans will likely become even more versatile, efficient, and tailored to individual cooking preferences. For manufacturers, staying at the forefront of these trends will be key to maintaining a competitive edge in an ever-evolving market.
As the frying pan manufacturing process continues to evolve, manufacturers are increasingly focusing on both technological advancements and consumer trends. This evolution is happening across multiple dimensions, from material innovation to production techniques and beyond. Here’s a deeper look at several key areas of progress:
Smart Cookware Integration: One of the most exciting directions in cookware technology is the integration of smart features into frying pans. While this is still in its early stages, smart frying pans equipped with temperature sensors, Bluetooth connectivity, and other digital features are beginning to hit the market. These pans allow users to monitor and adjust the cooking process remotely, giving real-time feedback about cooking temperatures, ideal cooking times, and even alerts when food is cooked to perfection. Some high-end frying pans may even be designed to sync with cooking apps or smart home assistants like Alexa or Google Home, providing an even more seamless cooking experience. This could lead to precision cooking where the frying pan can automatically adjust its temperature based on the food being cooked, ensuring the perfect outcome every time.
AI in Quality Control and Automation: As artificial intelligence (AI) and machine learning (ML) continue to grow in importance, their application to frying pan production is also becoming more widespread. In production facilities, AI is being used to optimize manufacturing processes by analyzing large datasets to identify inefficiencies and predict maintenance needs. On the production line, machine learning algorithms can be trained to recognize defects in materials and surface imperfections that might otherwise go unnoticed by the human eye. This not only ensures a higher-quality product but also speeds up production by automating the inspection process. AI also helps streamline inventory management and demand forecasting, ensuring that manufacturers can meet fluctuating consumer demand with minimal waste.
Additionally, robotic systems are becoming a standard part of frying pan production, particularly in the handle attachment and packaging stages. Robots equipped with advanced sensors can position handles accurately, rivet or weld them to the pan, and then place the finished products into packaging for shipment. These systems reduce labor costs and eliminate human error, resulting in a more consistent and efficient production process.
Material Innovation and Sustainability: As sustainability becomes a key focus for both manufacturers and consumers, frying pan producers are looking for innovative ways to reduce their environmental impact. One notable development is the use of recycled metals, particularly recycled aluminum, in frying pan production. Recycling aluminum not only cuts down on energy consumption (recycled aluminum requires significantly less energy to process compared to new aluminum) but also reduces the carbon footprint of the manufacturing process. Recycled stainless steel is also gaining popularity for similar reasons, as it provides a durable and sustainable alternative to virgin materials. The use of sustainable metals can help companies meet growing consumer demand for eco-friendly cookware.
Coating Innovations: The demand for non-toxic, eco-friendly, and durable non-stick coatings continues to drive innovation in frying pan coatings. Traditional non-stick coatings, such as those made from PTFE (Teflon), are being replaced in some products by newer alternatives, such as ceramic coatings or mineral-based coatings. These coatings provide similar non-stick properties without the concerns related to PFOA (perfluorooctanoic acid), which is found in some older non-stick surfaces. Some manufacturers are also developing non-stick coatings that are resistant to high temperatures or durable enough to withstand metal utensils, which extends the lifespan of the pan. Additionally, eco-friendly coating processes are being implemented to reduce the use of chemicals and solvents during the coating application process, making frying pans safer for both the user and the environment.
Induction-Compatible Frying Pans: The rise of induction cooking is another trend influencing frying pan production. Induction cooktops use electromagnetic energy to directly heat the pan, making them highly energy-efficient and offering precise temperature control. For a frying pan to work on an induction cooktop, it must have a magnetic base. As a result, many frying pan manufacturers are developing pans with a layer of ferrous metal at the base, ensuring that they are induction-compatible. This also broadens the market for frying pans, as consumers increasingly opt for induction cooking due to its speed and energy efficiency. Frying pans that can perform well on both traditional and induction cooktops are particularly attractive for their versatility, appealing to a wide range of consumers.
Ergonomics and Comfort: As consumers continue to look for ergonomically designed cookware, frying pan manufacturers are paying more attention to the handles of their products. Heat-resistant handles made from silicone, stainless steel, and Bakelite are becoming more common, offering comfort and safety when handling hot pans. Manufacturers are also designing handles that are easier to grip, reducing the risk of accidents in the kitchen. Many frying pans are now designed with hollow handles or soft-touch grips to minimize heat transfer from the pan’s body, making them more comfortable to use during long cooking sessions. These ergonomic improvements ensure that frying pans are not only practical but also easy and enjoyable to use.
Customization and Personalization: In line with broader trends in consumer products, frying pan manufacturers are exploring the customization and personalization of their cookware. Consumers increasingly want products that reflect their individual tastes, and this includes the appearance and design of their frying pans. Some companies now offer customers the option to choose from different handle styles, colors, or even custom engraving on the pan itself. This trend goes beyond aesthetics—customized cookware also appeals to consumers who are looking for unique, high-end products that feel more personal. Personalized frying pans could also be a premium offering, with manufacturers targeting specific customer segments looking for distinctive kitchen tools.
Global Market Trends: As cooking habits and culinary trends continue to evolve globally, frying pan manufacturers must adapt their products to cater to regional preferences. In Asia, for example, smaller pans with deeper sides are often preferred for stir-frying and wok cooking, while in Europe and North America, frying pans with larger diameters and flatter surfaces are more popular for searing, sauteeing, and pan-frying. Understanding these regional preferences is essential for manufacturers looking to expand into international markets. Some companies are also innovating with multi-functional frying pans that can be used across various cooking styles, providing more flexibility for global consumers.
In addition, global demand for premium cookware is rising. As consumers become more discerning, they are willing to invest in high-quality frying pans that offer better performance, durability, and aesthetics. This has led to the development of high-end frying pans with premium features like hand-forged designs, superior heat distribution, and exclusive non-stick coatings. These pans are often marketed as investments in long-term cooking performance, appealing to professional chefs and home cooking enthusiasts alike.
Challenges and Future Directions: Despite the significant progress made in frying pan production, several challenges remain. One of the key challenges is balancing sustainability with performance. While there is a strong push for more eco-friendly production practices and materials, manufacturers must ensure that these changes do not compromise the performance or durability of the frying pans. The growing demand for affordable cookware also puts pressure on manufacturers to keep production costs low, which can sometimes conflict with efforts to introduce higher-end materials or technologies.
Looking ahead, the future of frying pan production will likely see more cross-industry collaboration, where cookware manufacturers work with material scientists, engineers, and tech companies to create even more innovative products. The integration of AI, IoT, and smart technology will continue to drive change in how frying pans are produced and used, while sustainability efforts will lead to the adoption of greener materials and more efficient manufacturing processes. Ultimately, the frying pan will evolve into a more versatile, durable, and intelligent kitchen tool, catering to a wider range of cooking preferences and consumer needs.
Sheet Metal Ice Bucket Production Machine
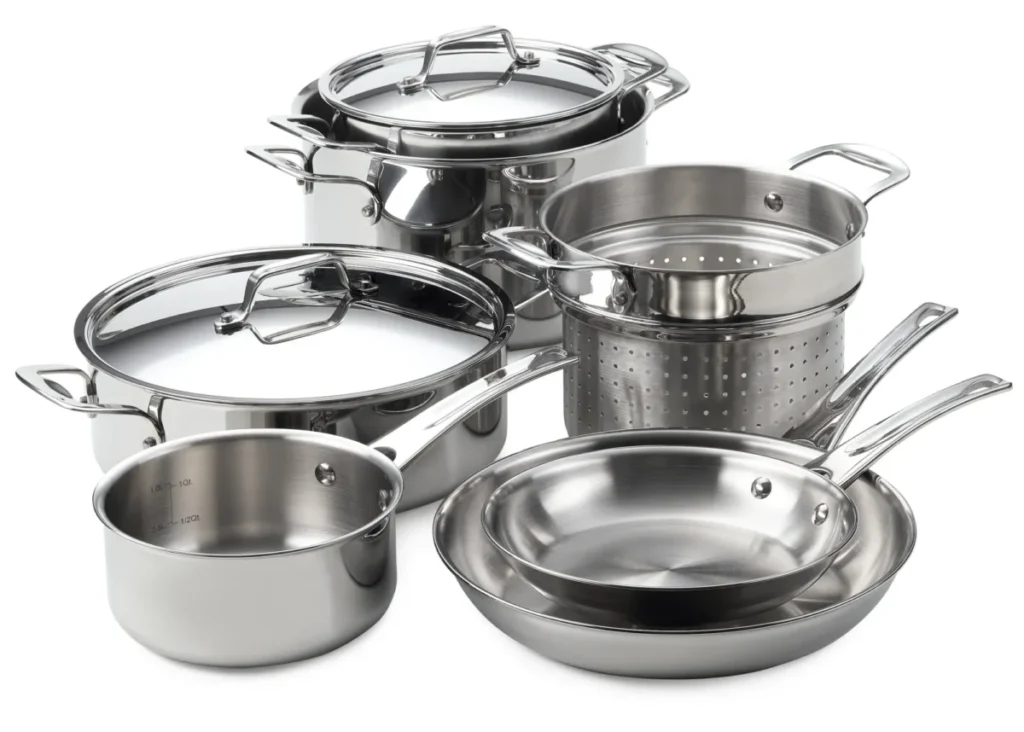
A Sheet Metal Ice Bucket Production Machine is a specialized piece of equipment designed to efficiently manufacture ice buckets from stainless steel, aluminum, or other metal sheets. These machines are widely used by cookware manufacturers, hospitality product suppliers, and OEM metalworking factories. The goal is to produce stylish, durable, and functional ice buckets used in homes, hotels, restaurants, and bars. Here’s a detailed look at how these machines work and the processes involved—without breaking into rigid sections:
The production process typically begins with sheet metal blanking, where coils or sheets of stainless steel or aluminum are fed into a hydraulic or mechanical press fitted with a blanking die. This step cuts the raw material into circular or oval blanks that match the dimensions of the ice bucket to be produced. Depending on the machine’s configuration, this can be fully automated with coil feeders, straighteners, and uncoilers, ensuring consistent blank size and shape.
After blanking, the metal blank moves to the deep drawing stage. A deep drawing press—usually hydraulic due to its precise control and pressure consistency—forms the blank into a cylindrical or bucket shape. The punch descends into a female die, drawing the metal downward without tearing it. For taller ice buckets or those with complex profiles, the process may require multiple drawing stages, known as redrawing, to gradually deepen and refine the bucket’s body.
To improve the strength, appearance, and handle integration, the ice bucket undergoes trimming and flanging. Trimming removes excess material from the drawn part’s rim, ensuring a smooth and uniform edge. Flanging bends the edge outward or inward depending on whether a lid is included or if a double-wall structure will be assembled. These operations are often done in rotary trimming machines or hydraulic presses equipped with precision dies.
In the case of double-walled ice buckets, a second inner shell is drawn and assembled inside the outer wall. The gap between the two walls can act as an insulator to keep ice from melting quickly. This assembly step may include spot welding, laser welding, or adhesive bonding, depending on the design and manufacturer preferences. Once assembled, the bucket may be placed in a hydraulic press for shaping or finishing to ensure both walls are tightly bonded and aligned.
For premium models, spinning is sometimes used to refine the surface or form tapered walls. Metal spinning machines can rotate the bucket body while applying forming tools to shape or thin the metal in specific areas. This is particularly useful for custom designs or high-end ice buckets with elegant curves.
Once the main body is complete, the machine moves on to handle forming and attachment. Handles are usually formed from metal rods or strips, bent into shape using CNC wire benders or hydraulic presses. These handles are then spot welded, riveted, or mounted onto the bucket using press-fit hardware. In automated systems, robotic arms can handle the positioning and joining of handles, especially for large-scale production.
After assembly, the ice buckets go through a surface treatment process. This can include polishing, brushing, or electroplating, depending on the desired finish. Automated polishing machines equipped with buffing wheels and polishing compounds can achieve mirror-like finishes, while brushing systems produce matte or satin textures. Some manufacturers also apply PVD coatings for color variations such as gold, black, or bronze, especially for luxury models.
The final stages involve cleaning, quality inspection, and packaging. Cleaning is done in ultrasonic washers or with high-pressure rinsing to remove oil, debris, and polishing residue. Vision systems and human inspectors check for defects like scratches, uneven seams, or welding marks. Approved products are then packaged—often in foam or cardboard inserts—for shipment to retailers or clients.
A complete sheet metal ice bucket production line integrates PLC control systems, safety enclosures, and HMI (Human-Machine Interface) screens for monitoring production status, switching between sizes, and minimizing downtime. Machines can be semi-automatic for small batch runs or fully automatic for large-scale production, depending on the operation’s budget and capacity needs.
The demand for metal ice buckets continues to grow, particularly in hospitality and lifestyle sectors, and manufacturers are responding with increasingly refined and automated production methods. In modern setups, the ice bucket production machine is often part of a fully integrated line that emphasizes speed, repeatability, and finish quality. Manufacturers are prioritizing not only the functional integrity of the bucket—such as insulation and strength—but also its visual appeal, which plays a significant role in upscale settings like hotels, lounges, and catered events. That’s why the machinery involved focuses heavily on precision and cosmetic perfection from the earliest stage of forming.
After the primary deep drawing and forming steps, some manufacturers may employ metal spinning not only for shaping but also for fine-tuning wall thickness and achieving uniform stress distribution. This process, though more common in artisanal or high-end products, is increasingly being adapted to semi-automated setups to allow for both flexibility and consistency. As consumer preferences shift toward more aesthetically refined designs, details like symmetrical curves, consistent wall tapering, and elegant contours are being engineered directly into machine programming via CNC integration.
Throughout production, temperature and pressure calibration become vital. For instance, drawing operations on stainless steel often require lubricant application and precise control of drawing force to prevent tearing, especially when working with thinner gauges that are common in lightweight or decorative ice buckets. Sophisticated sensors monitor these forces in real time and automatically adjust hydraulic parameters or pause production if tolerances are exceeded. These sensors are part of an increasingly smart production environment, where self-correcting systems help maintain high yields while reducing material waste.
Welding and bonding processes are also advancing. For double-walled or insulated ice buckets, laser welding has become the preferred technique due to its accuracy and low heat distortion, which is essential to maintain a smooth, finished look on the outer shell. In higher-volume lines, robotic arms handle these tasks with remarkable speed and precision, rotating the parts and applying consistent weld beads. The seam is then polished flush using robotic buffing stations, which preserve the bucket’s sleek appearance while removing any trace of the weld.
One major trend influencing machine design is the growing demand for customization. Ice buckets are no longer strictly utilitarian—they’re also brand touchpoints. Many restaurants, hotels, and event venues want their logo or design motif integrated directly into the product. Machines are therefore being equipped with engraving heads, embossing rollers, or even laser marking systems that can apply unique graphics without slowing down the line. This personalization step can happen mid-process—before polishing—or as a final finishing detail, depending on the design requirement.
Manufacturers are also exploring options for minimizing environmental impact throughout production. Recycled stainless steel and aluminum are becoming the default materials in many factories, and machines are being built to handle variations in metal quality without jamming or producing defects. In polishing stations, closed-loop water filtration systems capture metal particles and allow for the reuse of water and polishing compounds, reducing waste and operating costs. Even heat treatments or annealing processes are being optimized for energy efficiency, with induction heaters replacing older resistance-based ovens in some lines.
In terms of ergonomics and user safety, the machines are built with enclosed guards, light curtains, and automatic shutoffs to protect operators while allowing for quick tool changes and maintenance. The use of centralized lubrication systems and predictive maintenance sensors ensures longer machine life and less unplanned downtime. Operators interact with these machines through intuitive touchscreens that display process parameters, diagnostics, and production analytics in real time, helping managers track quality and output without manual logs.
Packaging integration is another feature of advanced production setups. Once the ice bucket is cleaned and inspected, it’s conveyed directly to a labeling or packaging station, where a robotic arm may insert it into a custom-formed insert or apply branded sleeves. If the bucket includes accessories like tongs, lids, or stands, these are automatically sorted and packaged alongside the main product, ready for shipment. Some systems also include automated barcode application and scanning for traceability, which is particularly useful for OEM production or fulfillment centers handling multiple client SKUs.
Ultimately, the evolution of sheet metal ice bucket production machinery reflects a balance between traditional metal forming techniques and modern automation. Whether producing sleek, minimalist models for contemporary bar setups or vintage-inspired hammered-finish buckets for boutique hospitality brands, these machines are being designed for versatility, repeatability, and scalability. As design trends shift and consumer expectations rise, the technology behind these machines will likely continue to integrate more AI, IoT, and energy-efficient systems, setting new standards for both form and function in metal beverageware.
As manufacturers look toward future developments in sheet metal ice bucket production, the role of digital fabrication and smart factory principles becomes even more prominent. Production machinery is now being designed with Industry 4.0 in mind—integrating real-time monitoring, cloud-based analytics, and automated feedback loops. For instance, the forming presses and finishing systems can be networked together so that each station communicates data upstream and downstream. If the deep drawing press detects minor deformation due to a material inconsistency, it can automatically relay compensation instructions to the trimming or spinning station to adjust tolerances. This connected intelligence not only improves quality control but also reduces manual intervention, paving the way for lights-out manufacturing during overnight shifts.
In many of the more advanced production setups, digital twins are used to simulate the behavior of the entire ice bucket production line before physical tools are cut. These simulations allow engineers to test different material grades, wall thicknesses, and handle configurations virtually, helping reduce the time and cost of prototyping. Once the design is finalized, the actual machines are calibrated using this virtual model, ensuring that the first run of buckets meets quality expectations right off the line. The digital twin also plays a role in predictive maintenance, as it can track the wear and performance of tooling components like drawing dies, flanging rings, and trimming blades based on production data and recommend service before any issue arises.
One of the most critical areas of innovation is the surface finish application, which can strongly influence consumer perception and market value. Ice buckets may receive a variety of decorative treatments, from satin brushing and mirror polishing to colored coatings or engraved textures. These treatments are achieved through a combination of mechanical polishing, chemical processes, and advanced PVD (physical vapor deposition) coating chambers. Machines that perform these steps are becoming increasingly automated and programmable, allowing for rapid switching between styles and finishes. For example, a single production line could switch from producing a brushed stainless steel bucket to a glossy black PVD-coated version with minimal downtime, as long as tooling and programming are optimized.
Quality control is also being transformed by automation. High-resolution cameras mounted on inspection stations now use computer vision to detect not only obvious defects like scratches or dents, but also subtler issues like asymmetry, discoloration, or uneven weld polishing. These systems use machine learning to improve their accuracy over time, becoming better at distinguishing between acceptable variation and actual flaws. This reduces the rate of unnecessary rejections while increasing overall quality assurance, especially important when manufacturing for premium or export markets where presentation standards are high.
In terms of flexibility, new machine designs are moving away from rigid one-size-fits-all tooling in favor of modular die sets and quick-change stations. This means that a single machine setup can produce multiple sizes or styles of ice buckets with minimal downtime for retooling. Whether the design calls for small tabletop buckets or larger commercial wine chillers, the system can adapt by swapping punch-and-die sets, handle templates, or embossing rollers in a matter of minutes. This versatility is essential for suppliers who serve both mass retail and custom luxury brands, and it makes small-batch production economically viable without compromising efficiency.
Material innovation continues to play a role in shaping production capabilities. Some manufacturers are experimenting with hybrid materials such as stainless steel exteriors combined with copper or aluminum liners for improved thermal insulation. These dual-metal buckets require highly precise joining and forming techniques, often involving specialized presses or roll-forming systems that can handle differential metal behavior without warping. Additionally, the rise in sustainable production practices means that more operations are exploring water-based lubricants, solvent-free coatings, and recyclable packaging materials that align with eco-conscious branding.
Even the ergonomics and usability of the ice buckets themselves are influencing machine design. Consumers are demanding features like double-wall insulation, integrated drip trays, ergonomic handles, or lids with snug seals—and the machines must be engineered to produce and assemble these components efficiently. For example, sealing gaskets for lids may be installed robotically during final assembly, while ergonomic handles are tested for torque resistance as part of in-line inspection. These enhancements, once considered premium, are now expected even in mid-range products, pushing the production machinery to evolve accordingly.
The competitive landscape is also shaping how these machines are built and sold. Manufacturers offering turnkey solutions—complete lines from blanking to packaging—are gaining an edge by reducing the need for operators to coordinate between multiple equipment vendors. These integrated systems are designed to work seamlessly, reducing bottlenecks and setup complexity. Additionally, many machine builders now offer remote diagnostics and software updates, allowing technicians to troubleshoot or enhance machine performance without being on-site. This is particularly useful for global operations where production sites may be located far from machine service hubs.
Overall, the machinery behind sheet metal ice bucket production is becoming smarter, faster, more adaptable, and more sustainable. As both consumer expectations and global manufacturing standards continue to rise, machine builders and production managers alike are working toward a new benchmark in metalware production—one that blends aesthetic craftsmanship with industrial precision.
As we look further into the horizon of sheet metal ice bucket production, the interplay between automation and craftsmanship continues to define the machinery landscape. Advanced manufacturers are now developing hybrid systems that allow both high-speed automated production and flexible manual override—offering artisans and engineers the chance to inject custom features or unique textures into limited edition runs without requiring an entirely separate process line. This hybrid approach is particularly appealing for boutique brands that want to maintain a handcrafted image while still benefiting from the efficiency and consistency of modern machines.
Another key innovation is in energy management. Smart motors and drives used throughout the machinery are now equipped with regenerative braking systems and power optimization algorithms, reducing overall energy consumption while maintaining high throughput. This is especially valuable for facilities aiming for carbon-neutral certification or those operating in regions with high electricity costs. Some production lines even integrate solar power or energy recovery systems that repurpose heat generated by polishing or welding machines for other parts of the facility, such as heating rinse tanks or pre-warming metal blanks.
On the software side, the integration of MES (Manufacturing Execution Systems) with ERP platforms is creating a more holistic view of the production workflow. Now, when an order is placed for a specific type of ice bucket, the system can automatically schedule the appropriate production batch, load the correct toolset, adjust machine parameters, and even predict the packaging requirements based on real-time inventory levels. This level of coordination eliminates delays, reduces inventory waste, and shortens lead times, allowing manufacturers to be more responsive to changing market demands.
Augmented reality (AR) and virtual reality (VR) technologies are also beginning to influence machine setup and operator training. AR-assisted interfaces help maintenance crews visualize machine internals and component relationships without disassembly, speeding up diagnostics and repairs. Meanwhile, VR simulators are being used to train operators on how to run, troubleshoot, and service complex forming or polishing machines in a safe, immersive environment before they even set foot on the shop floor. This is particularly useful in plants that adopt new machines frequently or serve a broad product range with complex tooling.
Design-wise, machines are being built with smaller footprints and modular casings to fit more easily into constrained factory environments or allow for staged upgrades. A production line might begin with a basic setup—manual feeding, semi-automatic drawing, hand-finishing—and gradually evolve into a fully automated, closed-loop system as production scales. This modularity ensures long-term investment protection while giving smaller manufacturers a way to enter the market with lower upfront costs.
In the context of global supply chains, there’s also a growing emphasis on multi-material compatibility. Some machines are now capable of handling both ferrous and non-ferrous metals, allowing manufacturers to produce not just stainless steel ice buckets but also aluminum or copper variants with the same tooling and setup. This is particularly useful in regions where supply constraints or pricing fluctuations make it necessary to switch materials quickly without affecting output quality.
Noise and vibration reduction is another overlooked but important aspect being addressed in next-gen machinery. Quieter hydraulic systems, vibration-dampened frames, and smoother tooling transitions make the working environment safer and more comfortable for operators, and reduce wear on mechanical parts. This is coupled with real-time acoustic and thermal monitoring to detect abnormal conditions before they lead to mechanical failure.
As brand differentiation becomes more critical, personalization technology within the production machine itself is advancing. Machines can now laser-etch logos, QR codes, or custom messages directly onto the finished bucket—an increasingly popular feature for promotional products, corporate gifting, and luxury retail. Because this marking happens in-line, it doesn’t add significant time to the production cycle and is often done with data pulled directly from customer orders, allowing true mass customization.
Finally, the growing popularity of direct-to-consumer models means that some manufacturers are integrating e-commerce APIs directly into their production software. Orders from websites can be fed directly into the machine’s production queue, triggering real-time scheduling and even sending estimated delivery times back to the customer interface. This tight coupling between the consumer experience and the production process is redefining what it means to manufacture metal goods in the age of digital commerce.
In essence, the sheet metal ice bucket production machine is no longer just a tool for shaping steel or aluminum—it’s a core node in a digitally connected, environmentally conscious, and highly adaptive manufacturing ecosystem. Whether for luxury barware, functional household goods, or branded promotional items, these machines are helping producers meet demand with precision, speed, and style.
Sheet Metal Cocktail Shaker Production Machine
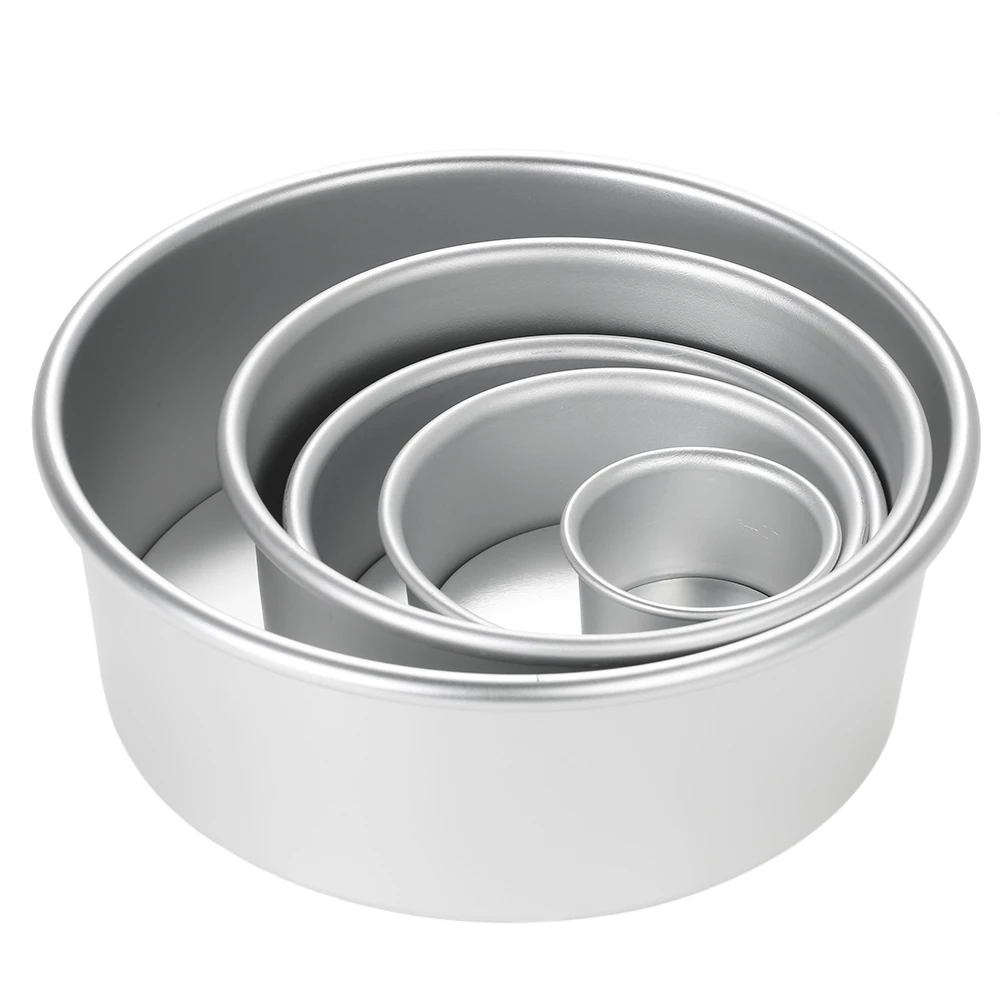
A Sheet Metal Cocktail Shaker Production Machine is a precision-engineered system designed to manufacture high-quality metal cocktail shakers—typically from stainless steel or copper—used in bars, restaurants, and homes. This machine line combines deep drawing, forming, polishing, and assembly technologies to produce classic three-piece shaker sets or modern Boston-style shakers with speed and consistency.
The process typically starts with blanking stainless steel sheets into circular discs using a mechanical or hydraulic press. These blanks are then fed into a deep drawing press that gradually forms them into cylindrical cups with rounded bottoms—the essential body of the shaker. Because cocktail shakers require a smooth, seamless inner surface to prevent liquid retention and ensure easy cleaning, the deep drawing stage is tightly controlled using precise pressure and lubrication.
Next, the machine may perform a redrawing operation to achieve the correct height-to-diameter ratio, followed by trimming the rim to produce a perfectly even edge. This is important for shaker sets that rely on a tight seal between pieces. Once the body is trimmed, it’s passed through a flanging or curling station if the design requires a rolled lip for added strength or aesthetics.
The lid and strainer components are typically drawn separately from thinner blanks and may go through additional shaping operations, including necking (to reduce the diameter for better fit) and hole punching for the strainer segment. These parts are then assembled using press-fitting or spot welding, depending on the design. For Boston-style shakers, which consist of two cup parts (usually metal and glass or two metals), the production machine focuses on achieving perfect tolerances for a snug, spill-free fit.
After forming, all parts move to automated polishing stations. These use rotating buffing wheels, abrasive belts, or robotic arms to create either a mirror finish or brushed texture. Polishing is essential not just for aesthetics but also for hygiene, as smooth surfaces are easier to clean and resist staining.
Laser engraving or branding can be integrated directly into the production line, allowing for custom logos or decorative designs. Quality control systems with vision sensors or dimensional gauges ensure consistency and detect defects before final cleaning and packaging.
Let me know if you’d like a deep dive into Boston-style versus cobbler shaker production, or if you’re curious about how these machines support mass customization or different finishes like matte black or copper plating.
In the world of sheet metal cocktail shaker production, the machines are designed for high efficiency, precision, and adaptability, especially as consumer preferences evolve toward unique, stylish, and customized shakers. Once the body, lid, and strainer components are formed and polished, the final assembly line kicks in. Here, the shakers are carefully checked for alignment, ensuring the parts fit seamlessly. For shaker sets that require a tight seal, the machine uses specialized fixtures to test the pressure and locking mechanism. If needed, automated assembly robots or mechanical presses ensure that the lid snaps onto the body with the right force, allowing for both functional sealing and ease of opening.
One of the essential aspects of cocktail shaker production is ensuring that the parts are uniform and consistent, which is why precision is critical. Any imperfections in the surface finish, like scratches or dents, can compromise both the aesthetics and performance of the shaker, which is why many machines integrate advanced vision systems. These cameras can inspect the surface for flaws and measure key dimensions such as height, width, and lid alignment. If any inconsistencies are detected, the shaker is flagged for manual inspection or sent back through the process for rework.
For custom designs, many machines are equipped with engraving or etching systems, often laser-based, that allow for logos, brand names, or decorative patterns to be added without slowing down the production line. These features not only give cocktail shakers a personalized touch but also provide a significant advantage in sectors like hospitality or retail, where brands seek differentiation through customized products. Laser engraving ensures fine details and sharp contrasts, making it ideal for high-end cocktail shaker designs or promotional products.
Additionally, coating options like PVD (Physical Vapor Deposition) or electroplating are becoming popular for giving the shakers unique finishes—like a sleek matte black or vibrant gold plating. These finishes enhance both the look and durability of the shakers, making them resistant to scratches and corrosion. The coating process involves placing the shakers in a vacuum chamber, where metal vapors bond with the surface of the metal. This creates an ultra-thin, hard, and uniform layer that improves the shaker’s aesthetic appeal and longevity. The process can also add unique colors, allowing manufacturers to produce a wider range of cocktail shaker styles for different market segments.
Once the shakers are polished, coated, and engraved, they go through the final inspection. This may include leak testing or drop testing, especially for the high-end models designed for professional bartenders. These shakers must not only look good but also perform reliably under repeated use. The lids must fit tightly to ensure the contents don’t spill when shaken, and the body must be robust enough to withstand the stress of shaking without warping.
Packaging is another crucial element in the production of cocktail shakers, particularly when dealing with large batches for distribution. Once all parts are assembled, the shakers are either packed individually or in sets, often with extra accessories like strainers, jiggers, or even cocktail recipe guides. The packaging machines are fully automated in modern setups, inserting the shakers into custom foam inserts or cardboard boxes designed to prevent damage during shipping. Some packaging lines also include automated labeling and barcode printing, ensuring each item is tracked and ready for retail distribution.
As consumer demand continues to lean toward sustainable and eco-friendly products, many manufacturers are incorporating recycled metals and environmentally conscious practices into their production processes. Some machines now feature features like water-based lubrication systems and closed-loop water filtration, reducing waste and making the process more environmentally friendly. Additionally, more attention is being paid to using biodegradable or recyclable packaging materials, aligning the product’s branding with eco-conscious consumer values.
The production of sheet metal cocktail shakers, once dominated by manual craftsmanship, has transformed into an advanced, automated operation. This evolution has allowed manufacturers to scale production, offer customized designs, and maintain high standards of quality control—all while meeting the growing demand for aesthetically pleasing and functional cocktail accessories. Through innovations in machinery, production techniques, and material handling, cocktail shaker manufacturing continues to thrive, offering a balance of tradition and modern efficiency in every product.
Looking ahead, the future of sheet metal cocktail shaker production is set to evolve further with the increasing use of smart manufacturing technologies and AI-driven optimization. For example, with the advent of Internet of Things (IoT) sensors, manufacturers can now integrate sensors into every stage of the production process. These sensors allow real-time tracking of performance metrics, material usage, and even environmental conditions within the factory. This data is transmitted to a central system that continuously analyzes production efficiency, detects bottlenecks, and makes predictive recommendations. This not only streamlines operations but also ensures that any irregularities or quality issues are identified early, before they affect the final product. This level of monitoring enhances overall product consistency, reduces waste, and increases throughput by allowing manufacturers to make adjustments dynamically.
As the market for cocktail shakers diversifies with rising demand for premium, artisanal, and branded products, there is a growing interest in creating shakers that combine unique metals with innovative finishes. For example, brushed stainless steel and matte finishes are increasingly popular for their sleek, professional appearance, while materials like copper or brass are being paired with protective coatings to prevent tarnishing. To handle these variations, multi-material production lines are emerging that can seamlessly handle both ferrous and non-ferrous metals without sacrificing precision. In these systems, advanced die sets and tooling can be swapped out to accommodate different metals and finishes, all while maintaining high-quality standards. This flexibility is key for manufacturers looking to cater to both mass-market retailers and niche, high-end customers.
The use of robotics and artificial intelligence (AI) also continues to make its mark in shaker production. Robots equipped with vision systems can handle delicate tasks like final inspection, part handling, and precision assembly. For example, in a production line where cocktail shakers require tight-fitting lids, robots can be programmed to assess the fit using high-precision cameras, ensuring that every shaker passes a stringent quality check before moving to the next stage. AI-driven systems can also optimize workflows—learning from patterns and adjusting machine parameters to minimize downtime and maximize efficiency. These AI systems continuously improve by analyzing historical data from past production runs, which helps streamline processes such as forming, polishing, and final assembly.
With sustainability taking a more prominent role in production, many manufacturers are investing in recyclable materials and closed-loop systems to further reduce their environmental footprint. Some machines are now built with integrated energy-saving modes, ensuring that power consumption is minimized during idle times. Additionally, there’s growing interest in waterless polishing technologies, which eliminate the need for chemicals or water in finishing processes. This makes the production of cocktail shakers not only more sustainable but also reduces costs related to waste treatment and water use.
The increasing demand for customization has driven further innovation in the production process. Today, some machines offer on-demand engraving or custom design options directly within the manufacturing line. Consumers can request their personalized logos, images, or even text, and the production line can integrate these customizations seamlessly. This trend is particularly popular in the promotional products sector, where branded cocktail shakers are a popular gift for corporate events or high-end bars. The ability to produce small batches with individual designs, without requiring a full retooling of machines, represents a significant advantage for businesses aiming to cater to these specialized needs.
On the design side, the trend towards lightweight shakers and ergonomic features continues to shape the machine design. Some shaker models are designed to be easier to handle, with contoured bodies or anti-slip grip areas that improve their use in a busy bar environment. The production machines are being optimized to accommodate these subtle design changes, and ergonomic testing is increasingly part of the production cycle to ensure that the shakers not only look good but are comfortable to use for long periods.
Finally, additive manufacturing (3D printing) is starting to play a role in prototyping and tooling for cocktail shaker production. Instead of relying on traditional metalworking for every prototype, manufacturers can use 3D printing to quickly design, test, and iterate on new shaker shapes or specialized components before committing to full-scale production. This ability to create prototypes rapidly reduces development time, especially for complex designs that may require unique parts like specialized strainer mechanisms or custom lids.
As demand for cocktail shakers evolves, the machines behind their production are becoming more adaptable, efficient, and innovative. Whether it’s through smart manufacturing, sustainability efforts, or customization capabilities, these production systems are at the forefront of meeting the ever-changing needs of the cocktail industry and consumers alike. The future of cocktail shaker manufacturing promises to be a perfect blend of high-tech automation, artistic craftsmanship, and sustainability.
As the sheet metal cocktail shaker production process continues to advance, the role of consumer-driven design becomes more significant. With the increasing importance of aesthetics and brand identity in the hospitality and home bar markets, manufacturers are investing in design innovation as a critical aspect of production. The design of a cocktail shaker is no longer just about functionality—there’s a growing emphasis on how it feels in the hand, the visual appeal, and how well it reflects the brand or the user’s personal style. As a result, machine tools are becoming more versatile, capable of achieving a wider range of complex shapes, textures, and finishes.
To meet these growing demands, new machines are being introduced that allow for multi-stage shaping and dynamic tooling adjustments. These machines can handle intricate embossing, texturing, and engraving on the metal surface, allowing designers to create unique, signature looks. For example, a cocktail shaker might feature a textured grip pattern that provides extra hold, or a laser-cut logo integrated into the design. Machines equipped with high-powered lasers can now perform detailed etching directly onto the shaker body without sacrificing speed or efficiency, opening new possibilities for brand storytelling through product design.
Modular production lines are gaining popularity, where each station can be adapted for specific product features. This flexibility enables the production of customizable cocktail shakers on-demand, making them ideal for small-batch or limited-edition runs. Instead of changing entire machines for different styles, manufacturers can switch out only the necessary tools or settings to accommodate different shapes, finishes, or materials, improving flexibility and reducing downtime. For instance, a production line that typically creates standard shakers can be quickly reconfigured to produce a limited-edition line with engraved patterns, unique color coatings, or specialized strainer systems without stopping production entirely.
The focus on ergonomics is also driving machine development. With the rise of premium cocktail shakers targeted at professional bartenders and enthusiasts, the emphasis on user comfort has led to machines that can produce shakers with contoured handles, balanced designs, and integrated insulation for a better grip and more efficient shaking. Machines capable of forming these ergonomic shapes with high precision are necessary for creating shakers that provide comfort during repeated use without compromising durability or performance.
As global trade continues to drive demand, manufacturers are adapting to the reality of a globalized supply chain. With production often taking place in one region and assembly or branding occurring in another, there is a growing need for interconnected production lines that allow for seamless integration across different stages. The machines are being designed with this in mind, allowing manufacturers to easily adapt their production lines for international standards, whether it’s meeting specific market needs, regulations, or shipping demands. Supply chain visibility has also become more sophisticated, with RFID tags and tracking systems integrated into the production process to monitor parts at every stage and ensure they meet customer orders.
In the realm of sustainability, the production of cocktail shakers is undergoing a transformation. Manufacturers are investing in technologies that reduce energy consumption and material waste. Machines are increasingly designed to use recyclable materials and can now process metals with minimal scrap, contributing to both economic and environmental benefits. Additionally, energy-efficient machinery, such as servo-driven presses, is becoming standard, reducing the carbon footprint of each shaker produced. These presses consume less energy by only using power when the press is in motion, compared to traditional machines that run continuously, even during idle periods.
With the rising demand for eco-conscious products, many manufacturers are experimenting with new materials that offer similar aesthetic and functional qualities as traditional metals but with a lower environmental impact. Recycled metals or biodegradable coatings are gaining traction, offering consumers the chance to enjoy premium-quality cocktail shakers with a smaller environmental footprint. Production lines designed to work with these new materials require specific tooling and temperature controls, further highlighting the importance of adaptable and efficient machinery in meeting sustainability goals.
At the same time, the packaging process for cocktail shakers is also evolving. Manufacturers are incorporating sustainable packaging options into their production lines, such as recycled cardboard or biodegradable wraps. Some machines now include automated packaging and labeling systems that not only package the shakers but also include eco-friendly labels that showcase the product’s sustainable attributes. As consumers demand transparency about the environmental impact of their purchases, companies are seeking ways to use packaging as an extension of their brand’s sustainability commitment.
Another important trend is the increasing use of augmented reality (AR) and virtual reality (VR) in both the design and manufacturing process. AR and VR tools allow designers and manufacturers to visualize the shaker designs in a virtual environment before committing to physical production. This helps reduce errors and ensures that all features are tested for compatibility, ergonomics, and user experience. VR simulations can also be used for operator training, where new employees can familiarize themselves with the machine settings and workflows in a virtual space before working with the actual equipment.
The intersection of artistry and technology in cocktail shaker production is a reflection of broader trends in consumer goods manufacturing. As brands continue to prioritize uniqueness, sustainability, and high performance, the machines that produce these products are evolving to meet these demands. The future of cocktail shaker production will likely be marked by greater automation, smarter production systems, and innovative materials, all working together to produce products that balance the artistry of the craft with the precision of industrial technology.
Sheet Metal Condiment Holder Production Machine
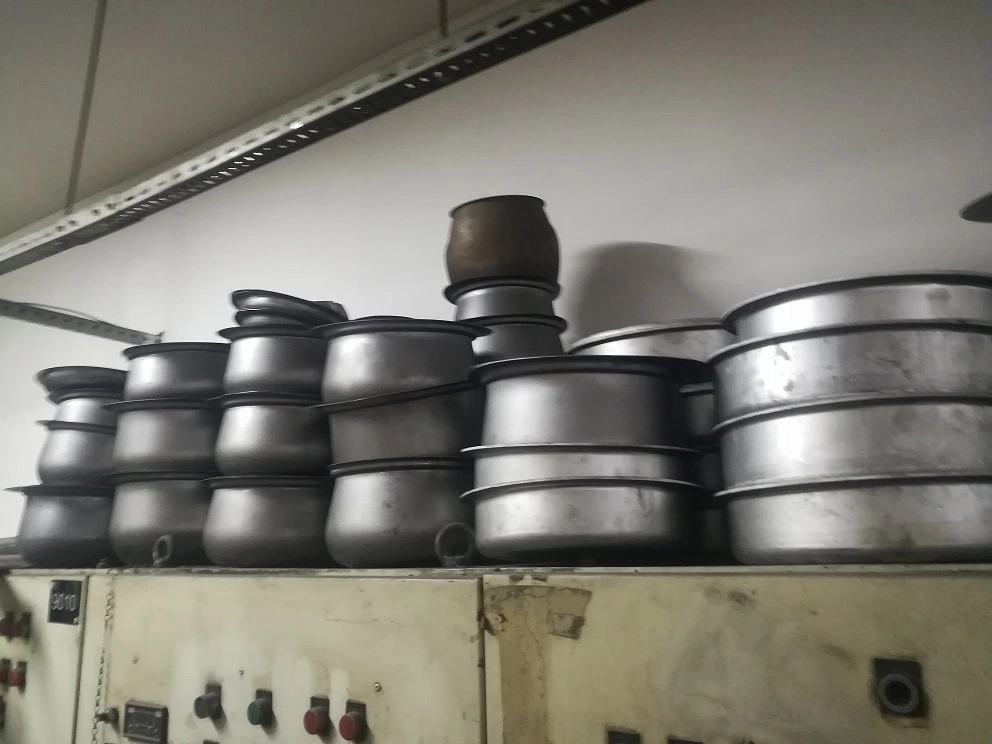
A Sheet Metal Condiment Holder Production Machine is designed to manufacture high-quality condiment holders, typically used in restaurants, cafeterias, and other foodservice establishments. These holders are often made from stainless steel or other durable, food-safe metals that are resistant to corrosion and easy to clean. The production process is a combination of forming, welding, polishing, and assembly, all aimed at creating functional, attractive, and durable condiment holders that can handle frequent use.
The production process usually starts with blanking, where large sheets of metal are cut into the desired shapes using a punch press. This process is highly automated, and the blanking machines are designed to handle various sheet metal thicknesses, ensuring precision and minimal material waste. The blanks are typically round or rectangular, depending on the final design of the condiment holder.
Once the metal blanks are cut, they move on to the forming process. This stage often involves deep drawing, where the metal is gradually shaped into a container or holder using a series of dies and presses. The metal is placed into a die, and a punch applies pressure to draw the metal into the desired shape. This process can be repeated multiple times to achieve the desired dimensions and form, ensuring the holder is both sturdy and capable of holding multiple condiments without compromising structural integrity.
For designs requiring a more complex shape, such as condiment caddies with multiple compartments or a sleek curved design, the roll forming or hydraulic pressing process may be used. This allows manufacturers to create shapes with more intricate curves or folds that are difficult to achieve with traditional deep drawing.
After forming, the edges of the holders are often trimmed and finished to ensure there are no sharp edges that could pose a safety risk. This is usually done with a shearing machine or laser cutting technology, which allows for precise and clean cuts. Some machines also feature automatic deburring mechanisms that remove any leftover material from the edges, providing a smoother finish.
Next comes the welding process, especially for condiment holders with multiple compartments or integrated handles. Spot welding or TIG welding is often used to join the different parts of the holder together. This stage ensures the components are securely fastened and aligned, ensuring that the finished holder can withstand regular use. Welding also helps create seamless joints that are both strong and hygienic, which is crucial for foodservice products.
Once the main structure is complete, the holder moves on to the polishing and finishing stage. In this step, the surface of the condiment holder is polished to remove any rough spots or blemishes left from the forming and welding processes. A brush finish or mirror finish is applied, depending on the intended aesthetic of the product. Some machines are designed to apply an additional coating, such as a PVD coating (Physical Vapor Deposition), which enhances the appearance and adds a layer of protection against corrosion, fingerprints, and staining. This step ensures that the holders are both functional and visually appealing, contributing to the overall cleanliness and attractiveness of the foodservice environment.
If custom branding or personalization is required, such as logos, restaurant names, or decorative patterns, this can be done during the engraving or etching process. Machines equipped with laser engraving technology can mark the surface of the condiment holder with high precision, allowing for intricate designs that add a touch of customization to the product. This is particularly popular in the foodservice industry, where branded items can be used as part of marketing or promotions.
Finally, after polishing, coating, and engraving, the condiment holders are passed through quality control to ensure that all components meet the necessary specifications. This includes checking for any defects in the material, verifying the dimensions, and confirming that the holders meet hygiene standards. Some machines are equipped with vision inspection systems that can detect imperfections such as scratches, dents, or inconsistent finishes, ensuring that only high-quality products make it through to the packaging stage.
The holders are then packaged for shipment. Depending on the size and design, they may be packed individually or in bulk. Automated packaging machines handle the process, wrapping the items in protective materials such as foam or bubble wrap to prevent damage during transit. The packaging line is also responsible for labeling and barcoding, ensuring that the products are traceable and properly cataloged for inventory management.
In recent years, manufacturers have also focused on making the production of condiment holders more sustainable. Energy-efficient machines and water-based lubricants are becoming standard in the industry to reduce the environmental impact of manufacturing processes. Additionally, some machines are now designed to handle recycled metals, allowing manufacturers to produce eco-friendly condiment holders while still maintaining the durability and aesthetic appeal expected by customers.
To cater to growing demand for customization, many modern condiment holder production machines are designed to be more flexible. These machines allow manufacturers to produce different sizes, shapes, and styles of holders in small batches, enabling them to cater to both bulk orders and custom requests without requiring large-scale retooling. This is a significant advantage for businesses that want to offer unique, made-to-order products while maintaining operational efficiency.
Overall, sheet metal condiment holder production machines combine advanced technology and precision engineering to deliver high-quality, durable, and customizable products. Whether designed for a single restaurant or large-scale foodservice chains, these machines help ensure that condiment holders meet both aesthetic and functional requirements while adhering to strict hygiene and safety standards. With ongoing advances in automation, customization, and sustainability, the future of condiment holder production looks to be more efficient, eco-friendly, and adaptable than ever before.
The production of sheet metal condiment holders is evolving with an increased focus on automation and customization, reflecting changes in both consumer demands and industry trends. Advanced manufacturing technologies are playing a pivotal role in enhancing the efficiency of production lines. The integration of robotics in forming, welding, and packaging processes is enabling manufacturers to reduce labor costs while increasing output. These robotic systems can work alongside human operators, performing repetitive tasks with high precision, such as moving parts through the various stages of production, picking up completed holders for inspection, and handling packaging.
The development of smart factories is also changing how sheet metal condiment holders are produced. In a smart factory, machines are connected through the Internet of Things (IoT), which enables real-time monitoring and control of the entire production process. Sensors embedded in machines collect data on machine performance, material usage, and product quality, which is then analyzed to optimize operations. This data-driven approach allows for quick identification of bottlenecks, allowing manufacturers to make adjustments in real-time and maintain high levels of productivity without compromising on quality.
On top of this, additive manufacturing technologies like 3D printing are making waves in the condiment holder production process, particularly in prototyping and tooling. By creating prototypes of new designs, manufacturers can rapidly test and iterate, speeding up the design phase and reducing development costs. This is particularly useful when designing condiment holders with intricate shapes or custom features that may require adjustments to the die tooling used in traditional methods. 3D printing is also useful in creating specialized tooling that helps streamline certain manufacturing stages, particularly when it comes to forming and trimming metal pieces.
As sustainability becomes a bigger concern for manufacturers and consumers alike, the production process for sheet metal condiment holders is being re-engineered to be more eco-friendly. Energy-efficient machines are being deployed, which consume less power during production. These machines are optimized to use less electricity while maintaining high-speed output, reducing the overall energy consumption of the factory. Additionally, manufacturers are turning to recycled metals in the production process, especially for holders that do not require the use of virgin materials for structural integrity. This shift is helping to reduce the environmental footprint of production while meeting the demand for more eco-conscious products.
Another trend driving change in condiment holder production is the focus on customization. As consumers and foodservice providers look for unique and personalized products, manufacturers are increasingly offering customization options. This includes custom engravings, varied shapes, and the option to design holders that reflect specific branding or themes. Machines designed for high flexibility allow for these customizations without requiring a complete overhaul of the production process. For example, machines with laser engraving technology can quickly add logos, text, or other designs onto the surface of condiment holders, catering to both small batch and large-scale orders without slowing down production.
The materials used in condiment holder production are also evolving to meet higher standards for both performance and aesthetics. Stainless steel remains a popular choice due to its durability, resistance to corrosion, and ease of cleaning, but brass and copper are increasingly being used for higher-end, decorative condiment holders. These materials provide a more luxurious finish, often paired with special coatings to prevent tarnishing. To handle these materials effectively, the production machinery is being designed to handle a range of metals, ensuring precision even with materials that require specific handling or finishing.
In addition to changing materials and machinery, consumer expectations around product quality and performance are influencing the design of production machines. For instance, some condiment holders are designed with compartments to separate sauces or spices, which requires precision in both forming and welding to ensure the compartments are even and stable. The latest machines can create intricate divisions within the holder while maintaining the structural integrity needed for frequent use. These developments allow manufacturers to produce condiment holders that are both functional and aesthetic, providing value not just in terms of utility, but also in design.
Finally, automated inspection systems integrated into the production line are now capable of checking the quality of condiment holders throughout every stage of manufacturing. These systems use machine vision to detect defects, irregularities in shape, or flaws in the finish. Whether it’s a small dent, a misaligned weld, or an uneven finish, the inspection system can identify these issues in real-time, ensuring that only the highest quality products make it through the line. This level of automation not only boosts production efficiency but also reduces the risk of human error, ensuring that every batch of condiment holders is consistent and meets the required standards.
The evolution of sheet metal condiment holder production machines represents a broader trend in manufacturing: the integration of technology to increase speed, precision, and sustainability. As these machines become more versatile, intelligent, and eco-friendly, they enable manufacturers to meet growing consumer demand for customized, high-quality, and environmentally conscious products. The future of condiment holder production looks promising, with innovations in automation, material handling, and customization continuing to shape the industry. Whether used in a fast-food setting or at an upscale restaurant, the production of condiment holders will continue to reflect the industry’s ongoing commitment to improving efficiency while delivering stylish, functional products.
As technology and consumer expectations continue to evolve, the future of sheet metal condiment holder production will see even more advancements that focus on both efficiency and creativity. One key area that will likely shape the next phase of production is the integration of advanced automation systems and artificial intelligence (AI). These technologies can not only improve operational efficiency but also enable smarter production processes. AI-driven machines can learn from data collected during production to predict maintenance needs, optimize machine settings, and even suggest adjustments to the production process based on real-time performance metrics. This level of intelligence can drastically reduce downtime, increase throughput, and improve overall production quality.
As demand for unique and high-quality products grows, manufacturers are increasingly focusing on personalized experiences for customers. This is especially true in foodservice, where restaurants and bars are looking to set themselves apart with custom-designed condiment holders. To address this need, manufacturers will likely adopt more flexible production lines that can accommodate smaller runs of customized designs while still maintaining cost-effectiveness. These flexible systems allow for rapid reconfiguration of machines, making it possible to switch between producing standard condiment holders and more unique, bespoke items with ease. For example, customers could request holders with personalized engravings, custom compartment sizes, or even different material finishes, all without slowing down the production process.
The growing trend of sustainability will continue to drive innovations in the way condiment holders are produced. As consumers demand more eco-friendly products, manufacturers are turning to sustainable materials such as recycled metals and biodegradable coatings. Additionally, there’s a rising interest in using waterless or low-emission production processes, particularly in polishing, coating, and cleaning. These environmentally conscious choices not only help reduce the carbon footprint of production but also enable companies to align with the growing consumer demand for green products. Machines capable of using eco-friendly lubricants during the cutting and forming stages are also becoming more common, further reducing the environmental impact of manufacturing.
Moreover, manufacturers are also focusing on reduced material waste during production. With advances in precision cutting technologies such as laser cutting and plasma cutting, it is now possible to make highly accurate cuts with minimal waste. The improved precision allows manufacturers to create more intricate and complex designs while using fewer raw materials, which is especially important in industries where metal costs are high. Additionally, these precision technologies allow for the creation of complex shapes and multi-functional condiment holders, like those with adjustable dividers or removable trays, without the need for additional materials or retooling.
The use of collaborative robots (cobots) is another trend likely to become more widespread in the production of condiment holders. Unlike traditional robots that operate in isolation, cobots work alongside human operators, assisting them with tasks like lifting heavy materials or performing repetitive functions. These robots can be easily integrated into existing production lines and provide a high degree of flexibility. As a result, manufacturers can enhance the productivity of their workers without the need for extensive retraining or investment in entirely new systems.
With consumers placing more value on aesthetics and branding, the demand for luxury condiment holders is expected to rise, particularly in high-end restaurants, bars, and hotels. These premium holders often feature sophisticated materials such as polished stainless steel, brass, or copper finishes, and their production requires machines capable of handling these metals with extreme precision. To produce high-end products, manufacturers will need to invest in advanced finishing technologies like electroplating or PVD coating, which provide a sleek, long-lasting finish that resists tarnishing and corrosion. These processes can also be combined with custom designs like engravings or embossed patterns to make the holders stand out visually.
Augmented reality (AR) and virtual reality (VR) are technologies that could significantly enhance both the design and training aspects of condiment holder production. Designers can use AR and VR tools to visualize new designs, evaluate their feasibility, and make adjustments before committing to physical production. This technology not only speeds up the design process but also helps reduce material waste by allowing designers to test and iterate without creating physical prototypes. Additionally, VR can be used to train operators and engineers on the machine settings and maintenance procedures, providing a more immersive learning experience without the need for physical machines.
In response to the rise of e-commerce, manufacturers are also focusing on improving the packaging and shipping processes for condiment holders. With the increase in online orders, ensuring that each product reaches the consumer without damage is paramount. Advanced automated packaging systems are already in use, where robots carefully wrap each condiment holder in protective material and package it in eco-friendly boxes, ensuring that the holders are not only secure during transit but also presented in a way that aligns with sustainable practices. These systems can also print shipping labels, apply barcodes, and track inventory in real-time, providing manufacturers with greater visibility and control over the supply chain.
Looking further into the future, it is likely that 3D metal printing will play a role in the production of condiment holders, especially in the creation of complex parts or short runs of customized products. With 3D printing, manufacturers can produce intricate designs without the need for traditional molds or dies, offering greater flexibility and design freedom. While 3D printing is still an emerging technology in mass production, its potential for creating customized or highly detailed condiment holders could revolutionize the way manufacturers approach product development and manufacturing.
As the global market for high-quality, customized, and eco-friendly products continues to expand, the sheet metal condiment holder production process will become more advanced and adaptable. Manufacturers who embrace these trends—such as automation, AI-driven processes, sustainability, and customization—will be well-positioned to meet the evolving needs of the foodservice industry. With ongoing improvements in technology, the future of condiment holder production is poised to be more efficient, innovative, and responsive to market demands.
The future of sheet metal condiment holder production is closely tied to broader trends in manufacturing, particularly those focusing on advanced materials, precision engineering, and global supply chain innovation. As businesses increasingly seek to improve their product offerings and respond to market demands for customization and quality, new innovations will emerge that address both operational efficiencies and product differentiation.
A critical area of development is in the advanced materials used to create condiment holders. While stainless steel has long been the material of choice for its durability and resistance to corrosion, the exploration of lightweight alloys, coated metals, and eco-friendly alternatives is gaining traction. Materials like titanium alloys, which offer superior strength-to-weight ratios, are being considered for high-end condiment holders where both performance and aesthetics are crucial. Additionally, biodegradable metals or composites, which can be recycled or repurposed at the end of their lifecycle, are beginning to gain popularity as manufacturers strive for more sustainable practices. These innovations enable manufacturers to provide options that appeal to consumers looking for sustainable products without compromising on the function or appearance of their condiment holders.
Alongside material advances, precision engineering will continue to drive improvements in the production process. The adoption of laser cutting and water jet cutting technologies enables manufacturers to make incredibly precise cuts with minimal waste. This level of precision is essential, especially for condiment holders that require compartments or dividers, as the process ensures that each holder fits together seamlessly and functions as intended. The continued development of multi-axis CNC (Computer Numerical Control) machines will allow for even more intricate designs, allowing manufacturers to create condiment holders with custom shapes, contours, and finishes.
For more complex designs, especially those requiring components to be integrated in multiple steps, modular production systems will become a key trend. These systems consist of interchangeable units that can perform a variety of tasks such as cutting, welding, and finishing. With these systems, manufacturers can adjust the setup based on product requirements, ensuring flexibility while maintaining high efficiency. This adaptability is particularly useful when producing condiment holders with different sizes, styles, or decorative features that may require more time-consuming processes.
As consumers become more accustomed to personalized products, manufacturers will increasingly offer options for customers to design their own condiment holders, whether it’s through online configurators or direct communication with the manufacturer. Such platforms will allow consumers to select their preferred materials, finishes, sizes, and even engraving or embellishment options. This demand for hyper-customization will push manufacturers to streamline production methods without sacrificing quality. The flexibility of modern production machinery and software solutions will ensure that both small batch and large scale runs can be managed efficiently, without long lead times or excessive costs.
Another aspect of future production will be the integration of artificial intelligence in the manufacturing process. AI-powered tools could analyze data across the entire production lifecycle, from design to quality inspection, optimizing the process in real-time. For instance, AI can predict when certain parts of the production line are at risk of failing, allowing for proactive maintenance. This minimizes downtime and keeps production running smoothly. Additionally, AI could assist in visual inspection systems that use machine learning to detect imperfections or inconsistencies in the products that might be invisible to the human eye. This guarantees a high level of quality control throughout the production process and improves overall product consistency.
The continued development of cloud-based software for production scheduling and inventory management will also play a significant role in the evolution of condiment holder manufacturing. By connecting all stages of production—from material sourcing to final packaging—cloud solutions will allow manufacturers to synchronize operations across different facilities, making it easier to manage demand fluctuations, optimize supply chains, and reduce costs. These tools will also enable manufacturers to track real-time data on production performance, helping them make informed decisions that boost operational efficiency. This data-driven approach will help manufacturers respond swiftly to changing consumer preferences, market trends, and global disruptions, such as supply chain challenges or material shortages.
Sustainability will continue to drive change in the manufacturing of condiment holders, with manufacturers striving to minimize their environmental impact. Zero-waste production methods will become increasingly important, where scrap materials from the metal-forming process are either reused or recycled back into the system. Advances in energy recovery systems that capture excess heat or power from machines will also reduce energy consumption, making the entire production line more energy-efficient. Furthermore, as carbon footprint becomes a more important factor for consumers, manufacturers will be expected to adopt and report carbon-neutral production processes. The push for green certifications from suppliers and customers will drive innovation in cleaner, more environmentally friendly methods.
One specific area where sustainability can be enhanced is in the use of eco-friendly coatings. Traditional coatings can often involve harmful chemicals that are difficult to dispose of, but newer technologies such as powder coating or water-based coatings are emerging as safer, more sustainable alternatives. These coatings not only reduce the harmful environmental effects of production but can also extend the life of the product by adding a layer of durability and corrosion resistance. These coatings also contribute to the aesthetic appeal of the condiment holders, giving them a sleek, modern finish without compromising environmental standards.
Moreover, the development of smart packaging is expected to play a role in the evolution of condiment holder production. As e-commerce continues to grow, smart packaging solutions that track products throughout their shipping journey will become more common. By integrating RFID tags and QR codes into the packaging of condiment holders, manufacturers can better manage their inventory and ensure that products are delivered safely. These smart packages can also be used to provide customers with product information, maintenance tips, or even personalized branding experiences.
Looking ahead, the introduction of additive manufacturing (3D printing) for metal components could transform the way condiment holders are produced, especially for custom orders or low-volume production. Metal 3D printing allows manufacturers to produce complex and intricate designs that are difficult or even impossible to achieve through traditional manufacturing methods. Although still in the early stages for high-volume manufacturing, it holds great potential for producing highly customizable products at lower costs and shorter lead times. This can cater to unique designs or specific requests, enabling businesses to offer premium, tailor-made condiment holders without the overhead of traditional molds or tooling costs.
In summary, the future of sheet metal condiment holder production will be shaped by technological advancements in materials, precision engineering, automation, and sustainability. As manufacturers adopt smarter, more adaptable production systems, they will be able to meet the growing demand for personalized, eco-friendly, and high-quality products. With a focus on efficiency, flexibility, and sustainability, the production of condiment holders will continue to evolve, providing consumers and businesses with innovative, durable, and aesthetically pleasing products suited for modern foodservice environments.
Sheet Metal Sugar Container Production Machine
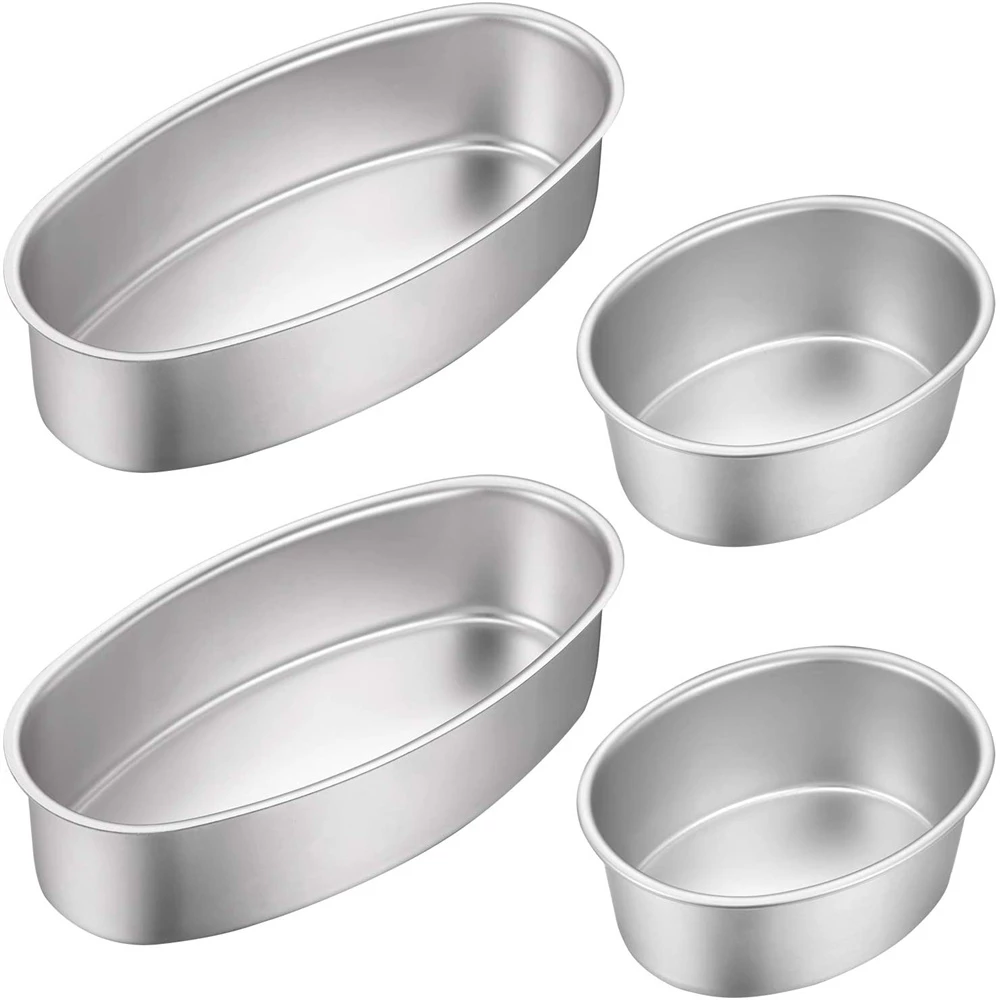
The production of sheet metal sugar containers involves a series of specialized machinery designed to form, assemble, and finish high-quality containers suitable for both retail and industrial applications. These machines need to accommodate the specific design and functional requirements of sugar containers, such as air-tight sealing, smooth finishes, and durable construction. Below is an overview of the key machinery involved in the production of sheet metal sugar containers.
1. Sheet Metal Cutting and Preparation Machines
The process begins with sheet metal cutting machines that prepare the metal sheets for further processing. These machines typically include:
- Laser cutting machines: Highly precise and efficient, laser cutters are used to cut the sheet metal into the required shapes and sizes. These are especially useful for creating intricate designs or adding perforations.
- Plasma cutting machines: These are used for cutting thicker metals and can operate at high speeds, making them ideal for mass production runs.
- Shearing machines: These machines are used for cutting metal sheets into specific sizes or trimming edges before further processing.
2. Forming Machines
Once the metal sheets are prepared, the next step is forming them into the shape of a sugar container. The key machines used in this process include:
- Hydraulic presses: These presses apply force to shape the metal sheets into the desired form, such as cylindrical shapes or other container shapes. The press often uses a die to ensure uniformity in size and shape.
- Roll-forming machines: Used to form the container body into consistent shapes, especially if the container requires specific dimensions or rounded edges.
- Deep drawing presses: These presses are used to stretch and shape metal into deep or tall containers, making them ideal for creating the body of a sugar container.
3. Welding and Joining Machines
To ensure the structural integrity of the sugar container, metal parts must be welded or joined together. Common machines in this category include:
- Spot welding machines: These machines use electrical resistance to join metal parts together, typically in areas that require minimal strength.
- TIG welding (Tungsten Inert Gas welding): This process is used for high-quality, clean welding seams on the container, particularly in areas that require airtight seals.
- Laser welding machines: These machines offer a clean, precise weld and are often used for producing sealed, airtight joints on the sugar container’s lid or seams.
4. Sealing and Closing Machines
For sugar containers, ensuring the lid and the body are sealed tightly is essential to preserve the sugar’s freshness. The following machines are used in this process:
- Lid crimping machines: These machines crimp the lid onto the body of the container, ensuring it is tightly sealed. Crimping also adds an aesthetic finish to the container.
- Capping machines: Automatic capping machines are used to attach screw-on or snap-on lids to the containers, often incorporating torque control to ensure the correct level of tightness.
- Vacuum sealing machines: These machines can be used to remove air from the container, ensuring that the sugar remains sealed in an oxygen-free environment, which helps prolong shelf life.
5. Decoration and Finishing Machines
The aesthetic finish of the sugar container is crucial for branding and consumer appeal. To achieve a professional and polished look, the following machines are used:
- Printing machines: Pad printing or screen printing machines are used to apply logos, labels, and other designs onto the surface of the sugar container.
- Laser engraving machines: These are used for precision engraving of logos or other intricate designs directly onto the surface of the container.
- Polishing and buffing machines: These machines are used to give the sugar container a smooth, shiny finish, especially if it is made from stainless steel or another polished metal. This process enhances the container’s visual appeal and provides a more premium look.
- Coating machines: Powder coating or other protective coatings may be applied to the container’s surface for durability and to provide additional resistance to corrosion.
6. Quality Control Machines
To ensure that the sugar containers meet the highest standards, various inspection and testing machines are used throughout the production process:
- Visual inspection systems: Automated systems using machine vision can detect imperfections in the metal or finish, such as dents, scratches, or inconsistencies in the design.
- Leak testing machines: Used to ensure that the container is air-tight and will protect the sugar inside from moisture or contaminants.
- Dimensional measurement machines: These machines check the dimensions of the finished containers to ensure that they are within tolerance and will fit with lids or other components.
7. Packaging Machines
Once the sugar containers are fully assembled and inspected, they need to be packaged for transport. Packaging machines include:
- Shrink-wrapping machines: These machines wrap the containers in plastic shrink film to protect them during transport and to provide tamper evidence.
- Cartoning machines: These machines automate the packing of containers into boxes or cartons, making it easier to ship them in bulk to retail stores or warehouses.
- Palletizing machines: These robots or machines automatically stack the packed sugar containers onto pallets, ready for shipment.
8. Automation and Control Systems
A modern sugar container production line incorporates sophisticated automation systems that control the operation of various machines. These include:
- Programmable Logic Controllers (PLCs): These controllers are used to automate the sequencing of machine functions, ensuring the production line operates smoothly and efficiently.
- Robotic arms: These arms are often used for tasks such as moving containers through different stages of production, picking and placing lids, and packaging finished products.
- Supervisory Control and Data Acquisition (SCADA) systems: SCADA systems allow for real-time monitoring and control of the production process, enabling operators to ensure smooth operation and quickly address any issues.
9. Customization Options
As consumer preferences continue to evolve, some manufacturers may offer the ability to customize sugar containers based on size, design, or branding. For example, companies might invest in flexible manufacturing systems capable of producing various styles of sugar containers in different materials (e.g., stainless steel, aluminum, or copper). This could be integrated with 3D printing technologies to create prototypes for new designs and customized items.
Summary
The production of sheet metal sugar containers requires a combination of cutting-edge technologies to ensure that each container is functional, durable, and aesthetically appealing. Automation, precision engineering, sustainability, and customization are key aspects driving the evolution of the manufacturing process for sugar containers. As demand for personalized and high-quality products increases, advancements in materials, design, and production machinery will continue to shape the future of the sugar container production industry. By integrating new manufacturing technologies, manufacturers can create sugar containers that are not only efficient to produce but also meet the growing consumer demand for unique and environmentally friendly products.
The production of sheet metal sugar containers is a highly specialized process, blending traditional manufacturing techniques with modern innovations to meet both functional and aesthetic requirements. As with most sheet metal products, the process begins with the careful preparation of raw materials, which involves cutting, shearing, or laser cutting the sheet metal into the appropriate dimensions. Once the metal sheets are prepared, they undergo a series of forming operations to achieve the desired shape, whether that’s a cylindrical form, square container, or another custom design.
The forming process typically involves the use of hydraulic presses or deep drawing presses, which shape the metal through mechanical force, ensuring the container walls are consistent in thickness and form. For containers requiring more intricate designs or additional features, such as multiple compartments or unique lid shapes, advanced machines like roll-forming and multi-axis CNC machines may come into play, offering precise shaping capabilities.
After the forming phase, the next crucial step is the joining of various parts, such as the body and lid of the sugar container. Depending on the design, this may involve welding, crimping, or even the use of threaded components for screw-on lids. Machines like spot welders, TIG welders, and laser welding systems are commonly employed to create strong, reliable seams that can withstand the stresses of handling and storage. In particular, laser welding is gaining popularity for its ability to produce clean, precise seams without the need for excessive finishing.
The sealing of the sugar container is equally important, especially when it comes to preserving the contents. Automated capping systems are often used to ensure the lid is securely attached, creating an airtight seal to keep moisture and contaminants out. In some cases, vacuum sealing may be incorporated to remove air from inside the container, further extending the shelf life of the sugar stored within.
Following the sealing process, attention shifts to the container’s finish. This is where technology meets consumer appeal. Various finishing techniques such as powder coating, polishing, and laser engraving are employed to enhance the container’s durability and appearance. Powder coating is especially popular for providing a smooth, colorful finish that resists scratches and fading over time, while laser engraving allows for intricate designs and logos to be etched directly onto the surface. These finishing processes ensure the sugar containers meet the visual standards expected in the marketplace.
In addition to aesthetics, the final product must undergo rigorous testing to ensure it meets quality standards. This may include visual inspections for defects like scratches or dents, leak testing to ensure the container is airtight, and dimensional checks to confirm that the container meets size specifications. These checks ensure that the containers function as intended and maintain their structural integrity over time.
The packaging of sugar containers for retail or industrial purposes is the final step in the production process. Packaging machinery automates this step, wrapping containers securely in protective film or placing them in cartons ready for shipment. In some cases, smart packaging solutions are incorporated, allowing manufacturers to track inventory or provide consumers with product details via QR codes or RFID tags.
Looking to the future, the sugar container production process is likely to continue evolving, with advancements in materials science, automation, and sustainability playing key roles. For instance, the growing demand for eco-friendly products is pushing manufacturers to explore alternatives to traditional metals, such as recycled materials or biodegradable coatings. The use of artificial intelligence and machine learning in production lines will enable manufacturers to optimize their processes for efficiency and reduce waste, while 3D printing technologies may open up new possibilities for creating highly customized sugar containers on-demand. These innovations will not only improve production efficiency but also allow for greater personalization of sugar containers, catering to the growing trend of consumer choice and customization.
In short, the production of sheet metal sugar containers is a highly dynamic process that balances precision engineering, advanced manufacturing techniques, and aesthetic considerations. As technology advances and consumer preferences evolve, the production process will continue to refine itself, producing sugar containers that are not only functional but also visually appealing and environmentally responsible. This forward-thinking approach will help meet the demands of a changing market while pushing the boundaries of what’s possible in container design and manufacturing.
The evolution of sheet metal sugar container production will also be influenced by trends in consumer behavior and global supply chains. As consumers become increasingly aware of sustainability, manufacturers are expected to adopt green practices in their production processes. This includes reducing energy consumption, utilizing recyclable or renewable materials, and minimizing waste generated during the manufacturing process. In response to growing environmental concerns, the use of eco-friendly coatings or non-toxic finishes will become more common, ensuring that the containers not only serve their purpose of holding sugar but do so in an environmentally responsible manner.
Automation will continue to transform the sugar container production process. As demand for quick turnaround times and consistent product quality increases, manufacturers will invest in smart factories equipped with sensors, machine vision systems, and robotic automation. These technologies can help monitor the production line in real time, ensuring that products are produced to the highest standards without excessive human intervention. For instance, automated quality control systems using machine learning algorithms will be able to identify and address issues such as defects in the metal or finish, reducing the chances of defective containers reaching the market. This can lead to substantial cost savings by reducing waste and improving throughput.
As global trade continues to evolve, manufacturers are likely to look for ways to localize their production facilities. For sugar container manufacturers, this means considering regional production to minimize shipping costs, reduce lead times, and support local economies. At the same time, manufacturers may also rely on global suppliers for raw materials, taking advantage of competitive pricing and ensuring that their production lines remain cost-effective. The shift toward more regionalized production could lead to the development of more flexible manufacturing systems that can quickly adapt to changes in market demand and product specifications. By integrating advanced software tools like cloud-based inventory management and supply chain optimization systems, producers can better track material usage and demand trends, making it easier to adjust production schedules and resources in real time.
Customization will be another major trend driving the production of sheet metal sugar containers. With advancements in digital manufacturing technologies, manufacturers can now offer a wider range of customization options. These could include personalized container designs, sizes, or unique finishes that cater to specific consumer preferences. For example, a consumer might request a sugar container with a custom logo, a specific color finish, or a unique shape that suits their kitchen decor. Additive manufacturing or 3D printing could further complement traditional production methods, allowing for rapid prototyping and limited runs of highly specialized containers. The ability to quickly produce custom products will enable businesses to tap into niche markets, appealing to consumers looking for unique or bespoke kitchenware.
Consumer trends also point to an increased demand for health-conscious products. As a result, sugar containers may evolve to accommodate sugar alternatives, organic sugars, and other specialty products. Manufacturers may design containers with specialized features, such as airtight seals, UV-resistant coatings, or containers with adjustable portions for easy dispensing. The popularity of products like organic and raw sugar may drive manufacturers to offer containers that highlight the quality of the contents while also maintaining their freshness for longer periods.
To address these shifts, manufacturers will likely invest in lean manufacturing techniques to ensure that production is as efficient as possible. Lean principles, such as just-in-time (JIT) inventory systems and continuous improvement methodologies, can help manufacturers reduce excess inventory, improve quality control, and respond quickly to changes in consumer demand. Data analytics will play a significant role in this process, helping manufacturers understand production bottlenecks, identify areas for improvement, and optimize workflows. By using predictive analytics, companies can anticipate demand fluctuations and adjust their production schedules to minimize downtime and avoid overproduction.
Safety and ergonomics will also become important considerations in the manufacturing of sugar containers. Modern factories are placing a higher emphasis on creating safe work environments and ensuring that machinery is designed for easy handling and minimal injury risk. Machines that require manual labor, such as those used for packaging or crimping, will be ergonomically optimized to reduce strain on workers. Furthermore, manufacturers may implement automated systems for high-risk processes, such as lifting or transporting heavy materials, to improve workplace safety.
With the growing importance of e-commerce, sugar container manufacturers will also need to adapt their production lines for online retail distribution. Packaging will be designed to not only protect the product during shipping but also offer a visually appealing presentation for the end consumer. Smart packaging that provides product information or enhances customer interaction will also become more prevalent. For example, a QR code or NFC chip embedded in the packaging could link customers to product care instructions, recipes, or promotional offers, creating a more interactive consumer experience.
As global supply chains become more interconnected, the trend toward supply chain resilience will take center stage. Manufacturers will need to ensure that they can quickly adapt to disruptions, such as shortages in raw materials, changes in shipping costs, or trade restrictions. To mitigate these risks, businesses might opt for diversified sourcing strategies and localization efforts, ensuring that they have access to multiple suppliers and alternative sources of materials.
The rise of consumer-focused trends will also spur manufacturers to focus on brand differentiation. In the highly competitive kitchenware market, sugar containers may be marketed based on unique selling points such as design, quality, or eco-friendliness. Consumers may gravitate toward brands that prioritize sustainability, use high-quality materials, or offer innovative features like easy-to-use dispensing mechanisms or transparent containers that show how much sugar remains.
In conclusion, the future of sheet metal sugar container production will likely be shaped by a combination of advanced technologies, consumer preferences, and global manufacturing trends. As automation, customization, and sustainability become increasingly integral to production strategies, manufacturers will need to stay agile and adopt innovations that enhance both product quality and operational efficiency. The increasing demand for personalized, sustainable, and high-quality kitchenware will drive the evolution of sugar container production, ensuring that it meets the expectations of today’s discerning consumers while also maintaining operational excellence.
As we continue to explore the future of sheet metal sugar container production, it’s important to delve deeper into specific areas where technological advancements, market shifts, and operational improvements will have significant impacts. The key trends we see are sustainability, smart manufacturing, consumer-centric customization, and adaptability in production systems. Let’s examine each of these aspects in more detail.
Sustainability and Eco-friendly Production Practices
Sustainability is increasingly becoming a central concern in the manufacturing industry. With growing awareness of environmental issues, manufacturers are under pressure to reduce their carbon footprint and produce eco-friendly products. For sheet metal sugar containers, this will manifest in several ways:
- Material Sourcing: Manufacturers will increasingly use recycled metals, such as recycled aluminum or stainless steel, to reduce the environmental impact of raw material extraction. This reduces the need for virgin metals, which often come with higher environmental costs, such as energy consumption and water usage. Recycled materials not only help preserve natural resources but also often result in a product with a smaller carbon footprint.
- Energy Efficiency: Advanced energy-efficient machinery and optimized factory layouts will reduce power consumption throughout the production process. Automated systems can help regulate energy use by operating only when necessary, and technologies such as solar power or wind energy can be integrated into the factory to reduce dependency on nonrenewable energy sources.
- Eco-friendly Coatings: With the rising consumer demand for sustainable products, manufacturers are likely to adopt eco-friendly coatings, such as water-based paints and finishes, which are less harmful to the environment than traditional solvent-based coatings. Additionally, biodegradable or recyclable packaging will become more common, aligning with the broader push for sustainable practices.
- Waste Reduction: Zero-waste manufacturing initiatives will become more common, where all byproducts from production are recycled or repurposed. Sheet metal scraps, for instance, can be re-melted and reused in new products, minimizing material waste.
Smart Manufacturing and Industry 4.0
Smart manufacturing technologies, commonly referred to as Industry 4.0, are transforming the production process in many industries, including sheet metal products like sugar containers. These advancements include:
- IoT (Internet of Things) Integration: The integration of sensors into machines will enable the continuous monitoring of key variables, such as temperature, pressure, and production speed. These sensors will send real-time data to centralized management systems, allowing for proactive maintenance, better resource allocation, and the identification of inefficiencies before they become costly problems.
- AI and Predictive Analytics: Artificial intelligence (AI) and machine learning algorithms will analyze vast amounts of production data to predict future outcomes. For example, AI could predict when a machine is likely to fail based on its performance history, enabling manufacturers to schedule maintenance before a breakdown occurs, thus minimizing downtime and improving production efficiency.
- Robotic Automation: The use of robotic arms and autonomous mobile robots (AMRs) will further streamline processes, from moving raw materials to performing precision tasks like assembly and packaging. Collaborative robots (cobots) will work alongside human workers, enhancing both safety and efficiency. They can assist in delicate tasks, such as placing lids on sugar containers, while reducing labor costs and improving throughput.
- Digital Twin Technology: This technology involves creating a virtual model of the entire production line, allowing manufacturers to simulate production processes, identify bottlenecks, and optimize workflow without disrupting actual production. Digital twins will become more prevalent in the design and testing stages, ensuring that any new machinery or processes work seamlessly before being implemented.
Consumer-Centric Customization
Customization has become a powerful driver of consumer choice, and manufacturers are taking notice. With consumer preferences shifting toward personalized products, sugar container manufacturers will need to adapt their production lines to offer more flexibility in design and features:
- Mass Customization: Thanks to digital manufacturing techniques like 3D printing and CNC machining, manufacturers can offer mass customization without sacrificing efficiency. Consumers may be able to choose from a range of colors, sizes, finishes, and even custom logos or artwork for their sugar containers. This allows brands to cater to unique customer needs while still maintaining cost-effectiveness.
- Personalized Features: Beyond aesthetic customization, sugar containers may also be designed to cater to specific user needs. For instance, consumers may choose containers with adjustable portion controls, easy-pour spouts, or integrated measuring spoons for more precise sugar dispensing. Incorporating features that improve user convenience will drive product differentiation.
- Interactive Consumer Engagement: Manufacturers will leverage digital platforms to allow consumers to interact with and design their containers. Virtual customization tools could enable consumers to design their own sugar container online, choosing their preferred shape, finish, and branding. These tools could integrate augmented reality (AR), allowing consumers to see how their container will look in real-life settings before making a purchase.
Adaptability and Resilience in Production Systems
As global markets become increasingly volatile and consumer preferences shift more rapidly, the ability to adapt quickly will be a critical success factor for sugar container manufacturers. Here’s how adaptability can manifest:
- Flexible Manufacturing Systems (FMS): Manufacturers will implement flexible production systems capable of quickly switching between different product types. For instance, a production line designed for sugar containers may also be able to shift to producing different types of kitchenware, such as spice racks or utensil holders, depending on demand. Modular production lines, where machines and equipment can be reconfigured with minimal downtime, will allow manufacturers to adapt to changing market conditions.
- Localized Production: To mitigate risks associated with global supply chain disruptions, manufacturers may increase investment in localized production. This not only ensures quicker response times but also supports regional economies and reduces the environmental impact of long-distance shipping. Manufacturers will likely establish more regional production hubs closer to key markets, improving supply chain resilience.
- On-demand Production: On-demand or just-in-time manufacturing will be more prevalent, as consumers increasingly demand faster delivery times and smaller production batches. With advancements in additive manufacturing (3D printing), manufacturers can produce sugar containers on demand, reducing inventory costs and ensuring a more sustainable approach to production.
- Agile Supply Chains: To better handle disruptions such as raw material shortages, manufacturers will use advanced supply chain management software to monitor and adjust their production plans in real-time. By creating agile supply chains, manufacturers can quickly source raw materials from alternative suppliers and adjust production schedules to ensure minimal downtime.
The Future of Sugar Container Production
Looking ahead, sheet metal sugar container production will likely become more automated, efficient, and customer-focused. As technology evolves and market demands change, manufacturers will need to balance automation with personalization, sustainability with speed, and cost-efficiency with quality. With smart factories, AI-driven optimizations, and eco-conscious production practices, the sugar container industry will continue to evolve in line with consumer expectations, ensuring that manufacturers can provide high-quality, innovative products at competitive prices.
In conclusion, the next wave of sheet metal sugar container production will be marked by the convergence of cutting-edge manufacturing technologies, sustainable practices, and a greater focus on consumer engagement and customization. As manufacturers embrace flexible production systems and data-driven decision-making, they will be well-positioned to navigate the complexities of the future marketplace while meeting the evolving needs of today’s eco-conscious and quality-driven consumers.
Sheet Metal Coffee Pot Production Machine
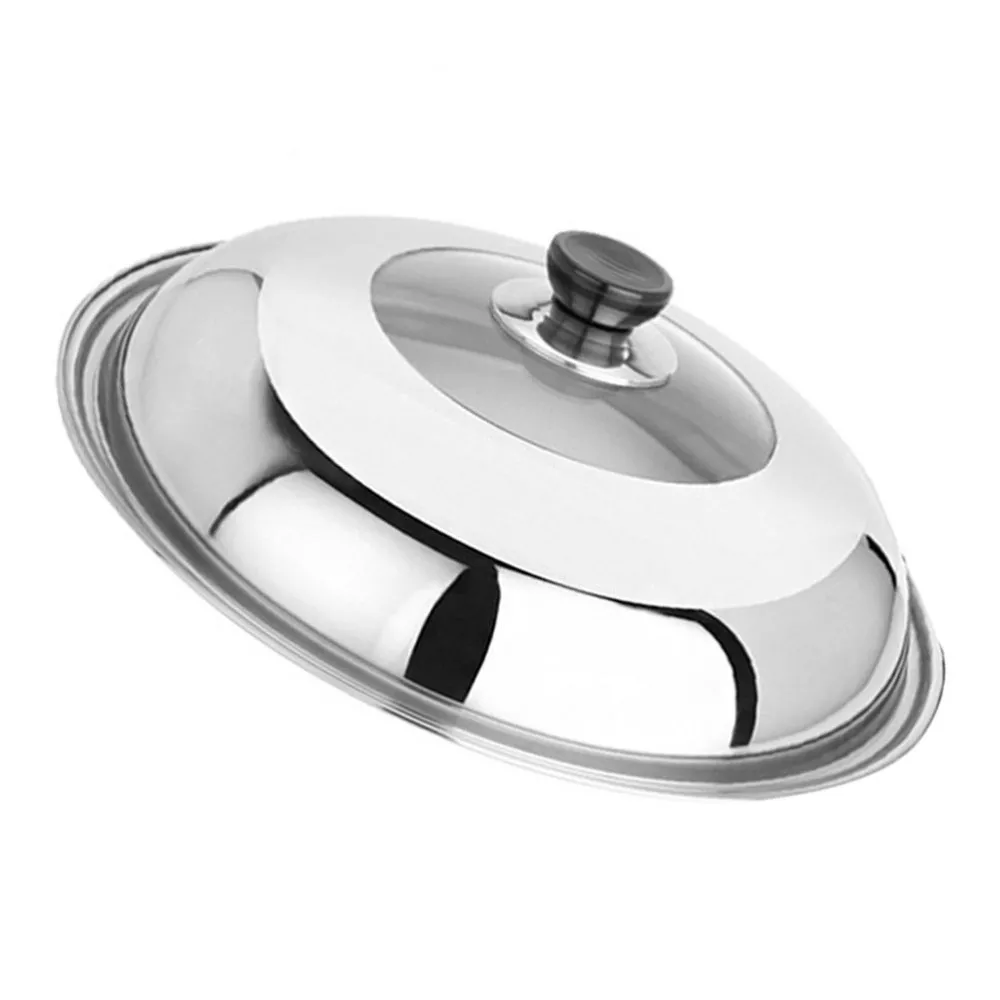
The production of sheet metal coffee pots is a highly specialized process that involves a combination of traditional metalworking techniques and modern manufacturing technologies to produce high-quality, durable, and aesthetically pleasing products. These coffee pots, often crafted from materials like stainless steel, aluminum, or copper, require precision in both design and construction. Below is an overview of the machinery and processes used in the production of sheet metal coffee pots.
1. Material Preparation
The process begins with the selection of high-quality sheet metal. Depending on the desired properties of the coffee pot, materials such as stainless steel or aluminum are chosen for their heat resistance, corrosion resistance, and aesthetic appeal.
- Shearing: Large rolls of sheet metal are first uncoiled and fed into a shearing machine, which cuts the material into the appropriate sizes and shapes for the various components of the coffee pot, such as the base, body, and lid.
- Cutting: In some cases, advanced cutting techniques such as laser cutting or water jet cutting are used to achieve more intricate designs or to create precise holes for handles and spouts.
2. Forming the Body
The coffee pot body is typically formed through deep drawing, a process in which a flat sheet of metal is drawn into a die to form a three-dimensional shape. This is achieved using a deep drawing press.
- Deep Drawing: The sheet metal is placed on a mold, and a punch is used to pull the metal into the mold, shaping it into the desired contour of the coffee pot’s body. This process may require multiple stages of drawing to achieve the final shape without causing deformation or thinning of the metal.
- Stretching and Forming: In some designs, the coffee pot’s body requires additional stretching or curving of the metal to achieve its smooth, cylindrical shape. Machines such as stretching presses or roll-forming machines may be used to achieve this.
3. Welding and Joining
Once the individual components of the coffee pot are shaped, they need to be joined together to create a seamless, sturdy vessel.
- Welding: High-strength welding techniques are used to attach the body, base, and lid of the coffee pot. TIG welding (Tungsten Inert Gas) is commonly used for stainless steel or aluminum coffee pots due to its precision and ability to create clean, strong welds without compromising the aesthetic appeal of the product. Laser welding is also gaining popularity due to its ability to create clean, fine seams with minimal distortion.
- Crimping and Riveting: For specific designs, components like handles or spouts may be crimped or rivet-welded to the body. Crimping machines or rivetting machines ensure that the parts are securely attached and aligned.
4. Handle and Spout Attachment
The coffee pot’s handle and spout are critical to its usability and must be securely and safely attached to the body. These components are often made from materials such as plastic, wood, or metal, and the attachment process is carried out with precision to ensure they remain sturdy during use.
- Handle Attachment: The handle, whether made of metal or another material, is attached using welding, riveting, or screw-fastening techniques. Spot welders are commonly used for metal handles, while riveting machines may be used for wood or plastic handles.
- Spout Attachment: The spout is attached using similar methods as the handle, depending on the design. It must be carefully welded or fitted to ensure it is functional and leak-proof.
5. Polishing and Surface Finishing
After the coffee pot is assembled, the next step involves surface finishing to enhance both its durability and appearance. The goal is to ensure a smooth, reflective surface that resists tarnishing and wear over time.
- Polishing: Machines such as rotary polishers or vibratory tumblers are used to polish the coffee pot’s surface, giving it a smooth, shiny finish. Buffing machines with cloth or felt wheels may also be used to give the coffee pot a mirror-like finish.
- Coating: Some coffee pots may undergo additional treatments such as powder coating or electroplating to enhance their resistance to corrosion and stains. This is especially common with aluminum coffee pots to prevent oxidation and maintain their appearance over time.
6. Quality Control and Testing
Before the coffee pots are packaged and shipped, they undergo a series of quality control tests to ensure they meet both functional and aesthetic standards.
- Leak Testing: The coffee pot is tested for leaks, especially around the spout and lid, to ensure it is airtight and capable of holding hot liquids without risk of leakage.
- Dimensional Inspection: Machines like coordinate measuring machines (CMM) are used to check the dimensions and tolerances of the coffee pot to ensure the pieces fit together precisely.
- Visual Inspection: A visual inspection is conducted to detect any surface defects such as scratches, dents, or imperfections that might affect the product’s overall quality.
7. Packaging and Shipping
Once the coffee pots pass quality control, they are carefully packaged to prevent damage during transportation.
- Packaging Machines: Coffee pots are typically packaged using automated packaging systems that wrap each pot in protective material such as bubble wrap or foam padding. They are then placed in boxes, often with additional cushioning materials to prevent movement.
- Labeling and Final Inspection: The final step in the production process involves labeling each coffee pot with product information and quality certification, followed by a last inspection before being shipped out to retailers or customers.
8. Advancements and Future Technologies
As the manufacturing industry continues to innovate, several emerging technologies may further transform the production of sheet metal coffee pots:
- 3D Printing: In the future, additive manufacturing techniques such as 3D metal printing may be used to create customized or limited-edition coffee pots with intricate designs that would be difficult to achieve with traditional methods.
- Automation and Robotics: Fully automated factories equipped with robotic arms and artificial intelligence will increase production speed and precision while reducing the need for human labor in dangerous or repetitive tasks.
- Sustainability: Manufacturers may continue to innovate in eco-friendly materials, utilizing recycled metals or biodegradable components to make coffee pots that align with the growing demand for sustainable products.
In summary, the production of sheet metal coffee pots involves a combination of traditional metalworking techniques and modern technology to create high-quality, durable, and aesthetically pleasing products. With advancements in automation, sustainability, and customization, the coffee pot manufacturing process will continue to evolve, offering consumers an even wider variety of products that meet both functional and environmental standards.
The production of sheet metal coffee pots is an intricate process that combines precision engineering with aesthetic craftsmanship. The use of high-quality materials such as stainless steel, aluminum, and copper ensures that the final product is both durable and visually appealing. The production process begins with material preparation, where large rolls of sheet metal are uncoiled and cut to size using machines like shears, lasers, or water jets. These cuts are then formed into the shapes required for the coffee pot’s body, base, and lid. Deep drawing presses are commonly used to form the body of the coffee pot, allowing the metal to take on a three-dimensional shape through a punching and stretching process. This method requires careful control to avoid deformation and thinning of the metal.
Once the individual components are formed, they are welded or joined together. Welding techniques such as TIG (Tungsten Inert Gas) welding are often used for precision, especially when working with stainless steel and aluminum. This method creates strong, clean seams without compromising the visual appeal of the product. Other joining techniques like riveting, crimping, or spot welding may be used for attaching handles or spouts. The handle and spout themselves are critical elements, and their attachment needs to be secure to ensure the coffee pot’s functionality. These components are typically made of materials like wood, plastic, or metal, and are either welded or fastened to the body using rivets, screws, or spot welds.
After assembly, the coffee pot undergoes a series of finishing processes designed to enhance both its appearance and functionality. Polishing is typically done using rotary polishers or vibratory tumblers, creating a smooth, shiny surface that resists corrosion and staining. Some coffee pots may also undergo coating processes like powder coating or electroplating to improve their durability and aesthetic qualities. These finishes can help the coffee pot maintain its appearance over time, especially when exposed to high temperatures or frequent use.
Before the coffee pots are packaged, they are rigorously tested for quality assurance. Leak testing ensures that the coffee pot is airtight, while dimensional inspections confirm that the parts fit together precisely. Visual inspections are also conducted to identify any surface defects, such as scratches or imperfections, that may detract from the product’s quality. Once the coffee pots pass these inspections, they are carefully packaged to protect them from damage during transit. Automated packaging systems wrap the coffee pots in protective materials and place them in boxes, ready for shipment to retailers or customers.
Looking ahead, advancements in manufacturing technologies will continue to shape the production of sheet metal coffee pots. Automation, robotics, and artificial intelligence are likely to play an even bigger role in improving efficiency and precision in the production process. These technologies will enable manufacturers to produce more intricate designs at faster speeds, reducing labor costs while maintaining high-quality standards. Additionally, sustainability will remain a key focus, with manufacturers adopting eco-friendly materials and processes to minimize their environmental impact. For example, the use of recycled metals in production, along with energy-efficient machinery and processes, can help reduce the carbon footprint of manufacturing operations.
Customization is another growing trend that is likely to influence the production of coffee pots. As consumer demand for personalized products increases, manufacturers may offer customization options, allowing customers to choose from different finishes, sizes, or even unique designs. This could be facilitated through digital manufacturing techniques like 3D printing or CNC machining, which allow for greater flexibility and precision in creating one-of-a-kind products.
In the future, the use of 3D printing may become more widespread in the production of sheet metal coffee pots, allowing manufacturers to produce complex, intricate designs that would be difficult or impossible to achieve through traditional methods. This could open up new opportunities for limited-edition or bespoke coffee pots, appealing to consumers who are looking for unique, high-quality items.
The evolution of sheet metal coffee pot production will also likely involve a greater focus on supply chain resilience. As global markets continue to experience disruptions, manufacturers will need to adapt by adopting flexible and localized production systems. This may involve using advanced software tools to manage inventory and production schedules, ensuring that factories can quickly respond to changes in demand or supply chain disruptions.
In summary, the production of sheet metal coffee pots is a complex and evolving process that blends traditional craftsmanship with modern technological advancements. As automation, customization, sustainability, and innovation continue to drive change in the manufacturing industry, the production of coffee pots will become more efficient, versatile, and environmentally responsible. Manufacturers will need to remain agile, embracing new technologies and consumer trends to stay competitive in a rapidly changing market.
As the coffee pot manufacturing process evolves, future advancements will likely focus on further integration of cutting-edge technologies, supply chain optimization, and enhancing consumer experience. For instance, the incorporation of smart manufacturing practices will play a pivotal role in the growth of the industry. With the increasing use of Internet of Things (IoT) devices in manufacturing, each step of production can be monitored in real time, providing valuable insights into efficiency, quality control, and overall system performance. Sensors embedded in machines can continuously track variables like temperature, pressure, and material properties, enabling manufacturers to make immediate adjustments to the process and reduce waste or defects. AI-based systems can further enhance this by predicting potential failures before they happen, enabling proactive maintenance, reducing downtime, and keeping production lines running smoothly.
In addition, the rise of digital twins in manufacturing represents another leap forward. A digital twin is a virtual replica of the entire production process or product line, enabling manufacturers to simulate and analyze different production scenarios without disrupting real-world operations. This technology can be particularly useful when optimizing the production of intricate sheet metal coffee pots, as it allows manufacturers to model the effects of design changes, production modifications, and even the impact of material variations on the final product.
Further expanding on sustainability, future innovations will likely revolve around the circular economy—a system where products are designed to be reused, repaired, or recycled, rather than discarded. For the coffee pot industry, this could involve creating products that are easier to disassemble, with recyclable components that could be reused in future production runs. For example, modular designs where parts such as handles or spouts can be easily replaced or recycled might become standard practice. Manufacturers could also invest in sustainable materials that are easier to recycle, like biodegradable coatings or eco-friendly metal alloys, which would further reduce the environmental impact.
On the consumer side, personalization will continue to be a driving factor in product development. Advances in additive manufacturing (3D printing) and CNC machining could enable consumers to create highly personalized coffee pots, allowing for unique shapes, sizes, or engraving that reflect individual tastes. Digital platforms that allow customers to interact with the design process in real time will give them the opportunity to choose or even design their coffee pots from the ground up, selecting finishes, sizes, and features that suit their specific needs. Such customization will not only cater to niche markets but also appeal to consumers looking for special or limited-edition items.
Another aspect of consumer-centric trends that will influence future coffee pot production is the demand for smart kitchenware. With the increasing popularity of connected devices in households, smart coffee pots with embedded sensors for temperature control, real-time brewing data, or automatic notifications when the coffee pot is ready or needs cleaning may become the norm. These features would be particularly useful for the growing IoT ecosystem within kitchens, where appliances and devices work together to create an optimized user experience. Voice-controlled or app-enabled coffee pots could integrate with home automation systems, providing consumers with the ability to control and monitor their coffee pot remotely.
As the global marketplace becomes more interconnected, manufacturers will need to adopt more flexible and responsive production systems. Traditional supply chains, which rely on a rigid structure of suppliers, manufacturers, and distributors, will evolve into more agile and localized networks. This shift will enable faster response times to shifts in demand, and better ability to manage supply chain disruptions, such as those seen in recent years with the COVID-19 pandemic. The adoption of on-demand manufacturing will also allow coffee pot manufacturers to produce items in smaller, more targeted batches, reducing excess inventory and improving overall supply chain efficiency. Just-in-time production models will reduce the reliance on large warehouses and make it possible to deliver products more quickly and efficiently to consumers.
Furthermore, collaborations between brands and consumers are expected to increase. As people seek more meaningful connections with the products they buy, manufacturers will likely embrace crowdsourced designs or open-source product development, allowing consumers to participate in the design process. This may involve offering limited-run coffee pots designed by artists, engineers, or even customers themselves, creating unique offerings that appeal to a sense of ownership and involvement.
Finally, the global market for coffee pots will continue to diversify. As emerging markets in Asia, Africa, and Latin America grow, coffee pot manufacturers will need to adapt their products to fit a broader array of cultural preferences, tastes, and brewing methods. For example, coffee pots designed for specific cultural practices, like Turkish coffee pots or Italian moka pots, may need to evolve to meet local demands while maintaining global appeal. Companies will also have to navigate different regulatory environments and consumer expectations in these diverse regions, requiring a flexible approach to manufacturing and distribution.
The long-term future of sheet metal coffee pot production will likely see the fusion of traditional craftsmanship with advanced digital technologies, creating products that are not only functional but also innovative and sustainable. Manufacturers that can balance these elements—maintaining quality and craftsmanship while embracing new technologies—will be well-positioned to thrive in a rapidly changing market. Ultimately, the evolution of coffee pot manufacturing will continue to focus on efficiency, sustainability, and consumer engagement, ensuring that these everyday kitchen essentials remain relevant and high-quality products for years to come.
As the production of sheet metal coffee pots progresses, the integration of next-generation technologies will undoubtedly become more pronounced. These innovations will shape not only the manufacturing process but also the entire coffee pot lifecycle, from design to end-of-life disposal. The push towards intelligent manufacturing systems will continue to redefine how coffee pots are made, allowing manufacturers to optimize every aspect of production. The future will likely witness an increased reliance on machine learning and artificial intelligence (AI) to automate tasks that currently require human intervention, improving both efficiency and accuracy in the creation of these products.
One major area of development will be the use of AI-driven design. Tools that leverage machine learning algorithms can assist designers by analyzing vast datasets to predict consumer preferences, identify trends, and optimize the structural integrity of coffee pots. These AI tools can simulate different material properties, production processes, and even customer behavior to create coffee pots that are not only functional but also meet specific needs and expectations. Designers could work hand-in-hand with AI systems to refine shapes, optimize material usage, and even suggest new innovative features that could make coffee pots more versatile or sustainable.
At the same time, additive manufacturing (also known as 3D printing) will begin to play a larger role in the production of sheet metal coffee pots. Currently, 3D printing is used in prototyping and producing small, specialized parts, but it could eventually transform the entire process. Metal 3D printing, which involves layer-by-layer deposition of metal, could enable manufacturers to create intricate designs that would be difficult to achieve with traditional methods. This technology offers the potential to produce customized coffee pots on demand, without the need for extensive tooling or molds. This approach could also make production more cost-effective for limited-run or bespoke designs, providing greater flexibility in the types of coffee pots produced.
As the demand for eco-friendly products continues to rise, manufacturers will likely increase their focus on utilizing sustainable materials in coffee pot production. The use of recycled metals will become more prevalent, driven by both consumer preference and environmental regulations. Coffee pot manufacturers may adopt circular design principles, ensuring that all components are easy to disassemble and recycle at the end of the product’s life cycle. This would allow consumers to return their coffee pots for recycling or repurposing, reducing waste and lowering the environmental footprint of coffee pot production.
In addition, biodegradable coatings could be developed for coffee pots, providing a protective layer that doesn’t rely on harmful chemicals or non-renewable resources. Environmentally friendly packaging will also become a focus, with manufacturers adopting recycled cardboard or biodegradable plastic for shipping. These changes will help align the coffee pot industry with broader sustainability goals, addressing both consumer concerns about environmental impact and the growing demand for ethically made products.
With the growing adoption of smart technologies, the coffee pot industry could also see the introduction of Internet of Things (IoT) features in its products. This could include features like temperature control and automated brewing systems, as well as the ability to connect to other devices in the kitchen. For example, a smart coffee pot could be connected to a home automation system, allowing users to control the temperature, monitor brewing status, and even receive notifications on their smartphones when the coffee is ready or when maintenance is required. Voice-activated controls might allow users to operate their coffee pots through digital assistants like Amazon Alexa or Google Assistant, making the brewing process more convenient and accessible.
To further enhance user experience, coffee pot manufacturers may incorporate personalization features that adapt to the needs of individual consumers. Smart systems could remember a user’s preferred brewing settings, adjusting the temperature and brewing time based on their past usage. Some models could even integrate with health-tracking apps, adjusting the brewing process based on the user’s caffeine intake preferences or activity level. These features could appeal to tech-savvy consumers who seek greater control and customization over their brewing experience.
Moreover, advanced manufacturing techniques such as robotic assembly and collaborative robots (cobots) will streamline the production of coffee pots. Cobots can work alongside human operators to handle repetitive, physically demanding tasks, such as welding or assembly, improving production speed while reducing the risk of injury. These robots can also be trained to handle delicate or intricate parts, ensuring high-quality finishes and precise assembly without the need for manual intervention. Additionally, automation in areas like packaging and inspection will improve efficiency, reduce labor costs, and allow for a higher volume of production.
One particularly exciting development on the horizon is the potential for customized, on-demand coffee pot production. As consumers increasingly seek personalized products, manufacturers may create platforms where customers can design their coffee pots through online interfaces, choosing elements such as shape, color, material, and even custom engravings. These platforms could incorporate augmented reality (AR), allowing users to visualize their designs in real time, and then order the product to be manufactured on-demand, reducing the need for large inventories and long lead times. This shift could disrupt traditional production models by allowing for more flexible, localized manufacturing and reducing waste.
As the demand for global sustainability and ethical business practices grows, manufacturers will be pressured to adopt fair labor practices and ensure that their production methods minimize harm to workers and the environment. Companies that embrace corporate social responsibility (CSR) by ensuring fair wages, safe working conditions, and transparency in sourcing materials will likely gain consumer trust and loyalty. Companies that show a commitment to ethical sourcing, like using conflict-free materials or ensuring that workers involved in production are treated fairly, will stand out in a competitive market.
In conclusion, the future of sheet metal coffee pot production will be shaped by the convergence of innovative technologies, sustainability goals, consumer-driven customization, and smart manufacturing techniques. Companies that can successfully integrate these advancements into their production processes will not only meet evolving consumer demands but also lead the way in creating efficient, high-quality, and eco-friendly coffee pots. With an eye on automation, sustainability, and consumer engagement, the coffee pot industry will continue to thrive and adapt to the challenges of the 21st century, while delivering products that are functional, innovative, and in tune with the values of modern consumers.
Sheet Metal Tea Pot Production Machine
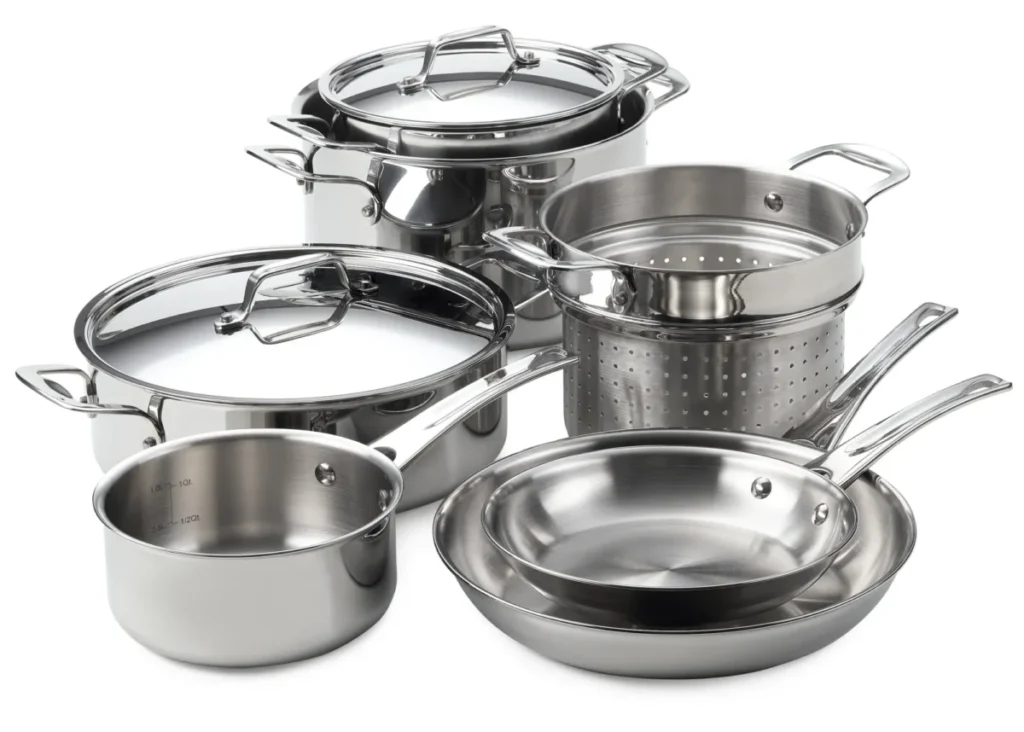
The production of sheet metal teapots involves several precise and technologically advanced processes, combining material preparation, metal forming, joining, finishing, and testing to ensure that the final product is both functional and aesthetically pleasing. Like other sheet metal cookware, tea pot production focuses on durability, design, and ease of use, incorporating both traditional craftsmanship and modern manufacturing techniques. The production machine and processes typically follow these stages:
1. Material Selection and Preparation
The production process begins with the selection of high-quality materials, such as stainless steel, aluminum, or copper, that offer good resistance to corrosion, heat, and wear. The material is usually sourced in large rolls of sheet metal. These rolls are then uncoiled and fed into automated cutting systems. Laser cutters or water jet cutters are often used to create the initial pieces, cutting the sheet metal to the required dimensions for the teapot’s body, spout, handle, and lid. Material thickness is carefully chosen based on the design and intended use of the teapot.
2. Forming the Body and Lid
Once the metal sheets are prepared, deep drawing presses are typically employed to form the body of the teapot. This process involves placing the sheet metal into a mold, where a punch forces the metal into a die to create a three-dimensional shape. Deep drawing is particularly important for creating the rounded shape of the teapot body. After the body is formed, the lid can be created in a similar manner, either by deep drawing or other methods like spinning or stamping, depending on the design complexity.
3. Forming the Spout, Handle, and Other Components
In addition to the body and lid, the spout and handle are crucial elements in the functionality and design of the teapot. These parts are generally made from smaller pieces of sheet metal, which are also formed using techniques like spinning, stamping, or extrusion. The spout, for example, might be formed through spinning, where the metal is rotated and shaped around a mold. Handles can be bent or stamped into the desired shape, ensuring a comfortable grip.
4. Joining and Assembly
After all the components (body, lid, spout, and handle) are formed, they need to be joined together to form the teapot. Common joining techniques for sheet metal tea pots include:
- Welding: TIG (Tungsten Inert Gas) welding is used for precise and clean welding, especially for joining the spout, handle, and lid to the body. This ensures strong, durable seams.
- Riveting: Rivets are used to attach the handle securely to the body, providing strength and stability while allowing for easier disassembly if necessary.
- Soldering or Brazing: In some cases, especially with copper teapots, soldering or brazing is used to join parts, offering a strong bond without the need for high temperatures that could deform the metal.
The joining process is highly critical to ensure that there are no leaks and that the teapot maintains its integrity during use.
5. Finishing Processes
Once the teapot has been assembled, it undergoes a series of finishing processes. These processes not only improve the visual appeal of the teapot but also ensure that the product is smooth, durable, and resistant to stains, rust, and corrosion.
- Polishing: Teapots are polished using rotary polishers or vibratory tumblers to create a smooth and shiny surface. For stainless steel and aluminum teapots, a high-quality mirror finish is often desired.
- Electroplating: For teapots made from metals like copper or aluminum, electroplating may be applied to create a thin layer of protective coating. This layer can improve the teapot’s resistance to tarnishing or oxidation and can also be used to achieve decorative effects.
- Powder Coating: For aesthetic and functional purposes, some teapots undergo powder coating, which provides a durable, colored finish. This process involves applying a dry powder that is baked onto the surface, creating a long-lasting and resistant coating.
6. Quality Control and Testing
Before the teapots are packaged and shipped, they undergo rigorous quality control procedures to ensure they meet all specifications and standards. These tests typically include:
- Leak testing to ensure that no liquid escapes from the teapot’s seams, spout, or lid.
- Dimensional checks to confirm that the teapot’s parts fit together precisely and that there is no warping or deformation in the shape.
- Durability tests to ensure the teapot can withstand heat exposure and repeated use without cracking, warping, or discoloring.
Visual inspections are also carried out to check for defects, scratches, or other imperfections in the surface finish.
7. Packaging and Distribution
After passing quality control, the teapots are carefully packaged. Automated packaging systems wrap the teapots in protective materials like bubble wrap or foam to prevent damage during shipping. The products are then placed in retail packaging, often with clear labeling or branding. Depending on the market, teapots may be packaged individually or in sets, and packaging will also focus on presenting the product attractively to consumers.
Advanced Technologies in Production
- Robotics: Robotic systems play an increasing role in automating repetitive tasks such as handling, assembly, and welding. Robots can ensure precision in tasks like placing handles on teapots or welding the spout, improving production efficiency.
- Additive Manufacturing (3D Printing): Though still limited in traditional sheet metal production, 3D printing may play a role in creating prototypes or intricate parts for limited-run designs. For instance, a company might use 3D printing for custom-designed spouts or unique decorative components.
- IoT and Smart Factory Systems: Internet of Things (IoT) technology is being integrated into manufacturing lines to monitor machine performance in real-time, ensuring optimal efficiency. Smart sensors in machines and production systems track variables such as temperature, pressure, and material integrity to ensure top-quality production and reduce waste.
Sustainable Practices
Sustainability in the production of sheet metal teapots is a growing concern. Manufacturers are looking to reduce their environmental footprint by using recycled metals (like stainless steel) and incorporating eco-friendly finishes like biodegradable coatings or powder coating. Additionally, some manufacturers focus on producing energy-efficient machinery and reducing water and chemical usage in their production processes.
Conclusion
The production of sheet metal teapots is a highly refined process that combines modern manufacturing technologies with traditional craftsmanship. As consumer demands evolve toward customization, sustainability, and innovation, manufacturers will continue to adapt by incorporating smart technologies, sustainable practices, and automation into their production lines. The future of teapot manufacturing is likely to see even greater advancements in efficiency, quality, and consumer engagement, ultimately leading to a more versatile and sustainable product offering for the global market.
The production of sheet metal teapots is continuously evolving, driven by innovations in technology, materials, and consumer demands. As manufacturers seek to meet the needs of modern consumers, the integration of new techniques and sustainable practices will be key. The growing use of automation, robotics, and smart technologies in the production line will enable manufacturers to streamline operations, reduce costs, and increase product consistency. For example, automated robotic arms will help in handling and assembling components with precision, while AI-powered systems monitor the production process in real-time, making adjustments as necessary to optimize efficiency and minimize waste.
The trend toward customization is also becoming more prominent in the tea pot industry, with many consumers seeking products that reflect their personal tastes and preferences. By leveraging advanced 3D printing and digital design tools, manufacturers could offer consumers the ability to personalize teapots with unique shapes, finishes, and features. Consumers may be able to choose everything from the material of the teapot (stainless steel, copper, etc.) to the type of finish (polished, matte, or textured), and even the design elements like handles and spouts. This customization can create a direct connection between the consumer and the product, elevating the user experience while encouraging consumer loyalty.
At the same time, the demand for eco-friendly products will continue to drive changes in production methods. As sustainability becomes a key factor in purchasing decisions, manufacturers are increasingly looking for ways to minimize their environmental footprint. Recycling and circular manufacturing practices are becoming more widespread, with companies focusing on the use of recycled metals and designing teapots that are easier to recycle at the end of their lifecycle. For example, some manufacturers may offer trade-in programs where customers can return old teapots for recycling, or parts that can be reused in new models.
Further pushing the sustainability trend is the growing popularity of energy-efficient production processes. Advances in machine technology have made it possible to produce sheet metal teapots using less energy and fewer resources, reducing overall production costs and environmental impact. Energy-efficient welding techniques and the use of solar-powered machines for specific operations are a few examples of how manufacturers are adapting to a more energy-conscious world.
The integration of IoT (Internet of Things) into the production line and even into the teapots themselves is another trend that will shape the future of tea pot manufacturing. By embedding sensors and connectivity features, teapots can become part of a broader smart home ecosystem, allowing users to control and monitor their brewing process through their smartphones or smart assistants like Amazon Alexa or Google Assistant. This could involve temperature regulation, brewing time, and even alerts for maintenance or cleaning, further enhancing the convenience and usability of the product. Manufacturers who can integrate smart technology into their teapots could provide consumers with a more interactive and efficient tea brewing experience, making the teapot a vital part of the connected home.
The global demand for premium and luxury teapots is also expanding, as consumers increasingly seek high-end products that combine aesthetics with functionality. Teapots made from materials like handcrafted copper, polished stainless steel, or even titanium offer a premium feel and enhanced durability. These teapots are often designed with unique shapes and finishes, adding an element of artistry and sophistication to the traditional teapot. Manufacturers are responding by creating exclusive models with unique patterns, engravings, or limited-edition designs. These high-end models may also feature bespoke elements, such as personalized engravings or custom features like ergonomic handles for improved user comfort.
In line with the demand for luxury items, designer collaborations may also become more frequent, where well-known artists or brands partner with teapot manufacturers to create limited-edition or signature models. These collaborations would appeal to a niche market of collectors and tea enthusiasts looking for something truly special, ensuring that the teapot maintains its place as both a functional and ornamental item in households.
As the teapot production process continues to modernize, manufacturers will need to remain flexible and adaptable to meet changing market demands. Consumer preferences for sustainability, customization, and technological integration will shape the future of teapot design and manufacturing. By embracing these trends, companies can create products that not only meet consumer needs but also align with global movements toward sustainability, energy efficiency, and advanced manufacturing techniques.
As the teapot production industry continues to advance, additional areas will see significant innovation, particularly in the realm of material science and consumer engagement. The ability to harness new materials that improve both performance and aesthetics will be crucial in gaining competitive advantage. For example, carbon fiber composites or ceramic coatings could be integrated into the design of sheet metal teapots to improve their heat retention properties, durability, and overall weight. These materials could help manufacturers create lighter yet robust products that retain heat for longer periods, which is a desirable feature for tea enthusiasts. As demand for premium, lightweight designs increases, manufacturers may explore novel material combinations that balance strength, aesthetics, and practicality.
Another direction for future development is the ergonomics and user-centric design of teapots. Manufacturers are increasingly placing importance on consumer comfort and ease of use, particularly in the handle and spout design. The teapot handle, which often comes into direct contact with the user, will likely evolve in terms of shape and materials. For example, ergonomically designed handles with heat-resistant grips could become more common, preventing discomfort or burns when handling the pot. Similarly, spout designs could be optimized for smoother pouring and better control, eliminating drips and splashes that can occur with traditional spouts.
Additionally, the growing trend of smart home integration will influence teapot designs in significant ways. As consumers continue to embrace connected devices, tea pots could be outfitted with Bluetooth or Wi-Fi capabilities, allowing users to program their brewing times, temperatures, or even control multiple tea pots at once using mobile apps or voice commands. This would appeal not only to tech-savvy consumers but also to those seeking a more convenient, automated experience. Integration with smart kitchen assistants could allow for seamless interaction with other appliances, creating a synchronized brewing process that adjusts according to tea type, desired strength, and time of day.
One of the most significant shifts expected in the tea pot industry will be the increased use of sustainable manufacturing techniques. As environmental consciousness continues to rise among consumers and governments, companies will feel greater pressure to adopt eco-friendly practices. Manufacturers may increasingly look to reduce their carbon footprint by utilizing renewable energy sources in their production processes, such as solar power or wind energy. Additionally, using recycled metals and biodegradable packaging will become standard in efforts to reduce waste and contribute to a more sustainable lifecycle for the product. Manufacturers will likely incorporate a circular economy approach, where products and materials are reused, refurbished, and recycled rather than discarded after their lifespan.
In parallel, advanced manufacturing technologies such as additive manufacturing (3D printing) could play a larger role in producing parts of the teapot. This technology, which allows for the precise, layer-by-layer construction of parts, could enable manufacturers to create more intricate, customized, and unique designs without the need for expensive molds or tooling. 3D printing could also open doors for on-demand production, allowing consumers to order bespoke teapots that fit their unique style and needs.
The future of teapot production also includes an increased focus on globalization and localization. Manufacturers may continue to optimize supply chains to balance global demand with local production needs, reducing transportation costs and the environmental impact of long-distance shipping. Additionally, localization can help companies cater to specific regional preferences for design, size, and material. For instance, in regions where ceramics or cast iron teapots are more popular, manufacturers may develop localized variants of sheet metal teapots that cater to those tastes.
At the same time, as global travel and exposure to various cultures increase, there may be a growing demand for teapots that are influenced by diverse design traditions. This could result in unique products that blend Eastern and Western teapot designs or incorporate features such as multi-functional lids or tea infusers built directly into the teapot. Manufacturers could introduce a wider variety of designs that represent cultural influences, opening up new markets and appealing to consumers looking for something different and innovative.
Customization and personalization will continue to be a driving factor in the production of sheet metal teapots. With the development of online design tools, consumers will be able to directly engage with the design process, choosing their preferred materials, colors, and finishes. This could be particularly popular for special occasions such as weddings or corporate gifts, where bespoke teapots could be produced with personalized engravings or custom designs. The growing trend of limited-edition collections will also likely persist, allowing manufacturers to cater to collectors and enthusiasts who want rare or one-of-a-kind items.
In response to health-conscious consumers, the materials used for tea pots will likely evolve to offer added benefits beyond traditional use. Non-toxic coatings and BPA-free designs will be prioritized, especially for products that come in contact with boiling water or food. Manufacturers could explore nano-coatings or advanced ceramics that reduce bacterial growth or improve temperature regulation, enhancing the quality of the tea or other liquids brewed.
Moreover, the consumer experience will extend beyond just the functional aspects of the teapot. Brands will place greater emphasis on creating a premium unboxing experience, offering packaging that adds to the overall luxury feel of the product. High-quality, sustainable packaging made from recycled materials or minimalist designs that focus on elegance could become a defining feature for high-end teapot brands. As consumers expect a brand story and authenticity, manufacturers will likely share more about their craftsmanship, materials sourcing, and sustainability practices to connect with a growing demographic of socially and environmentally aware consumers.
As manufacturers continue to innovate, the overall teapot market will grow increasingly diverse, with products designed not only for functionality but also to enhance the lifestyle experience of the consumer. Whether through smart technologies, sustainability, ergonomics, or personalization, the future of teapot production will likely see a convergence of artistry, craftsmanship, and cutting-edge manufacturing techniques, positioning sheet metal teapots as both essential kitchen tools and desirable collector’s items. The next generation of teapots will likely offer enhanced performance, unique designs, and greater environmental responsibility, catering to the evolving needs and tastes of the global consumer.
As we look further into the future of sheet metal teapot production, several additional factors are likely to shape the industry, particularly in areas such as automation, global distribution, and consumer engagement.
One major trend will be the integration of automation in the production process. With the ongoing development of Industry 4.0 technologies, manufacturers will increasingly turn to highly automated production lines that are not only faster and more efficient but also more flexible. Machines that are capable of performing multiple tasks — such as multifunctional robotic arms — will become more common. These robots could take over a wide range of activities, from assembling teapots to welding, finishing, and packaging, ensuring a higher level of consistency and reducing the potential for human error. Additionally, automated quality checks that use AI-driven visual inspection systems will allow manufacturers to identify defects or inconsistencies more quickly than traditional manual inspections.
The ability to customize products at scale through advanced automation will be a key differentiator in the market. Automated systems will allow manufacturers to offer on-demand customization for consumers, enabling them to choose specific features, finishes, and even personalized engravings, all while keeping production times reasonable. For instance, a system could automatically adjust the production process based on the customer’s specifications, altering machine settings for cutting, welding, and polishing without needing human intervention at every step. This would open up possibilities for mass customization, giving consumers more control over the final look and feel of their teapot while maintaining the efficiencies of mass production.
In addition to automation, advanced logistics technologies will play a crucial role in improving the supply chain for sheet metal teapot manufacturers. With growing global demand for these products, efficient distribution systems will be vital for ensuring that teapots reach their destinations in the fastest, most cost-effective manner possible. Robotics and drones may be used for more localized delivery, especially in urban centers, where they can quickly navigate traffic and bring teapots directly to consumers. Smart warehouses powered by IoT systems will help track inventory, ensuring that manufacturers always have the right materials on hand and can efficiently manage stock levels, reducing excess inventory and preventing stockouts.
On the consumer engagement front, the future of teapot production is likely to involve greater interaction between brands and consumers. Social media and interactive marketing campaigns will allow companies to build more direct relationships with customers. For example, consumers might be invited to participate in design contests or vote on the features of the next teapot collection. These campaigns will not only help generate excitement around new products but also foster a sense of community among tea lovers and collectors.
Augmented reality (AR) could also play a role in the consumer experience, allowing potential buyers to virtually “test” or “see” how a teapot would look in their home environment before making a purchase. This could be particularly useful for e-commerce platforms, enabling customers to visualize different colors, finishes, and styles directly in their living spaces through their smartphones or AR glasses. With this type of technology, brands can offer more personalized online shopping experiences, helping consumers make decisions with confidence.
Furthermore, the growing importance of sustainability and eco-conscious practices will continue to influence the design and production of sheet metal teapots. Manufacturers will likely adopt zero-waste production techniques, minimizing scrap materials and reusing metal offcuts, thus reducing their environmental footprint. There will also be a stronger push toward using eco-friendly packaging that can be fully recycled or composted, reducing the burden of single-use plastic and non-biodegradable materials.
Circular economy principles will play an increasingly important role, with companies striving to create products that can be easily disassembled and recycled at the end of their life cycle. For example, teapots could be designed with modular components that can be replaced or refurbished, prolonging their lifespan and reducing the need for entirely new products. Manufacturers will also look for innovative ways to reduce energy consumption during production, utilizing renewable energy sources such as solar or wind power in the manufacturing process. This would not only reduce the carbon footprint of production but also appeal to a growing segment of eco-conscious consumers who are keen to support brands that prioritize sustainability.
With rising consumer interest in premium, luxury, and collectible teapots, manufacturers may increasingly focus on creating exclusive, high-end products that cater to niche markets. Collaborations with well-known designers, artists, and celebrities could lead to the creation of limited-edition collections that appeal to collectors and connoisseurs of fine craftsmanship. These exclusive designs could feature unique engraving, luxury materials such as gold-plating, or embellishments like intricate designs or gemstones, enhancing the appeal of teapots as both functional items and ornamental pieces.
As more consumers turn to online shopping, manufacturers may also develop more sophisticated e-commerce platforms and virtual showrooms that offer detailed, high-definition views of their products. These online platforms will allow for interactive browsing, where customers can explore the various features of each teapot, view detailed product descriptions, and access video content that demonstrates how the teapot functions and its quality. This digital presence will be critical for connecting with a global customer base, particularly as online retail continues to dominate in many markets.
Finally, AI and big data will become increasingly integral in the development of sheet metal teapots. Manufacturers could use data analytics to better understand consumer preferences, identifying trends and gaining insights into the most popular styles, materials, and designs. This data could inform everything from the types of metal to be used in production to the design features most in demand, allowing companies to make data-driven decisions that improve their products and marketing strategies.
As the teapot manufacturing industry advances, the integration of these technologies, sustainable practices, and personalized experiences will reshape how sheet metal teapots are produced, marketed, and consumed. The future of teapot production will be characterized by a combination of innovation, luxury, sustainability, and consumer-centric design, ensuring that the humble teapot continues to play a central role in tea culture around the world, while also staying ahead of evolving trends in manufacturing and consumer expectations.
Sheet Metal Soup Ladle Production Machine
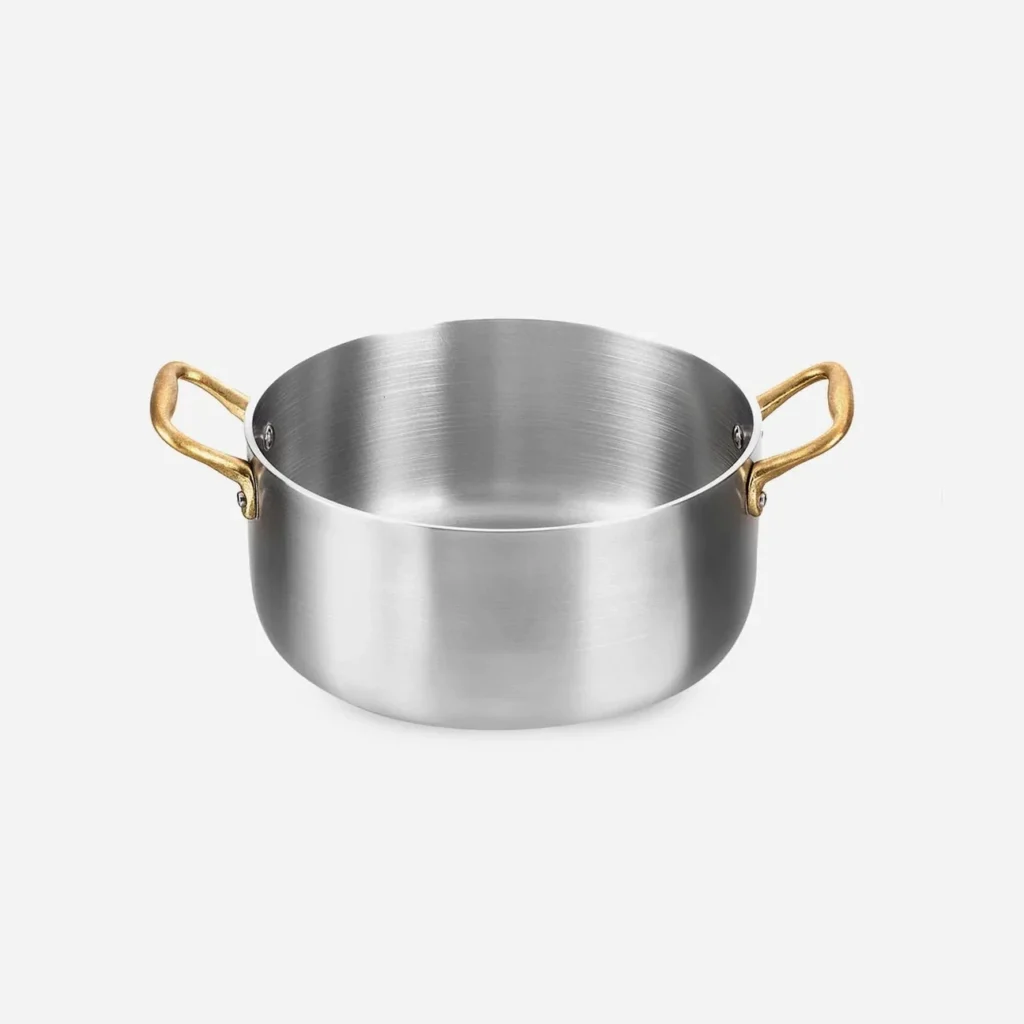
The production of sheet metal soup ladles involves several key processes that can be optimized for both efficiency and quality, ensuring the creation of durable and functional kitchen tools. Below is an outline of the general machinery and processes used in the production of sheet metal soup ladles:
1. Material Selection
The primary material used in the production of soup ladles is stainless steel or aluminum due to their durability, resistance to rust, and ease of cleaning. Stainless steel is often preferred because of its strength and resistance to corrosion, especially for items used with hot liquids. The material typically comes in sheets or coils that are fed into the production machines.
2. Sheet Metal Cutting and Shaping
The first step in the production of a soup ladle is to cut the sheet metal into the required shape. This can be achieved using machines such as:
- CNC Laser Cutters: These machines use a focused laser beam to precisely cut the sheet metal into the desired shape of the ladle’s bowl.
- Hydraulic Presses: These can be used to punch out the initial shape of the ladle bowl from the sheet metal, which is then further formed and shaped.
- Mechanical Shears: For rough cutting the material into blank pieces that can be processed further.
3. Forming the Ladle Bowl
Once the sheet is cut to size, the next process is to form the bowl of the ladle. This can be done using:
- Deep Drawing Machines: These machines help form a bowl shape by pulling the metal sheet into a die with a punch. The metal is stretched, and the bowl shape is formed in the process. This is crucial for ensuring the ladle is both deep and durable enough to hold liquids.
- Spinning Machines: In some cases, spinning machines can be used to form the ladle’s bowl by rotating the sheet metal and applying pressure to mold it into the desired shape.
- Roll Forming: For ladles with a more angular shape or specific edge design, roll forming can be employed to create continuous curves or specialized edges.
4. Handle Formation
The handle of the ladle is typically made from the same material as the bowl but is manufactured separately. The handle can be produced through:
- Stamping: Sheet metal is fed into a die, and a punch forms the handle into the correct dimensions. This process can be done in one or multiple stages depending on the complexity of the handle design.
- Extrusion: For solid handles, extrusion machines can push the metal through a mold to create the desired profile (round, square, or other shapes).
- Bending: If the handle requires bending, hydraulic presses or metal benders can be used to shape it according to specifications.
5. Joining the Bowl and Handle
Once the bowl and handle are formed, they need to be joined together. This can be done through:
- Welding: TIG (Tungsten Inert Gas) or MIG (Metal Inert Gas) welding are commonly used to join the bowl and handle. The joint is typically reinforced for strength and durability.
- Riveting: In some cases, the handle is attached using rivets that provide a strong and secure attachment while maintaining the ladle’s strength.
- Brazing or Soldering: If a more delicate or non-invasive joining method is required, brazing or soldering can be used to bond the handle to the bowl, particularly for smaller or more intricate designs.
6. Finishing and Surface Treatment
Once the ladle is assembled, it requires finishing to enhance its durability, appearance, and resistance to corrosion. Some common finishing processes include:
- Polishing: Polishing machines are used to give the ladle a shiny, smooth surface that is resistant to stains and easy to clean.
- Brushing or Satin Finishing: This process gives the ladle a matte or satin appearance and helps reduce fingerprints.
- Electroplating or Coating: To further enhance the ladle’s corrosion resistance, chrome plating or nickel plating can be applied. Ceramic coatings may also be applied for aesthetic reasons and to add additional non-stick properties to the ladle.
- Anodizing: If aluminum is used, the ladle may undergo an anodizing process to increase the metal’s resistance to corrosion and wear.
7. Quality Control and Inspection
After the production of the soup ladle is complete, it undergoes a series of inspections to ensure it meets quality standards. These include:
- Visual Inspection: Ensuring there are no visible defects such as dents, scratches, or inconsistencies in the surface finish.
- Dimensional Checks: Using specialized tools to ensure the ladle’s dimensions are within the specified tolerances.
- Strength and Durability Testing: Some ladles may be subjected to strength tests to ensure the handle can withstand the forces it will encounter during use.
- Corrosion Resistance Testing: For ladles made from metals like stainless steel, testing ensures the material will withstand the harsh conditions of exposure to liquids, heat, and cleaning agents.
8. Packaging
Once the ladles pass all quality checks, they are carefully packaged for distribution. Packaging is typically designed to protect the product from damage during shipping while highlighting the product’s quality and features. Eco-friendly packaging options may also be considered to appeal to sustainability-conscious consumers.
Production Machinery Considerations:
- Automation: Many of these processes, especially welding, stamping, and forming, are highly automated to reduce labor costs and increase efficiency. Automated systems allow for faster production times and consistent product quality.
- Customization: For high-end or niche markets, there may be a need for customized ladles. In these cases, more flexible machinery that allows for smaller batch production or unique designs might be necessary, such as CNC machines for precision engraving or custom shapes.
- Energy Efficiency: As environmental concerns continue to grow, manufacturers may invest in energy-efficient machines or renewable energy sources for their operations, minimizing the carbon footprint of the production process.
In conclusion, the production of sheet metal soup ladles involves a combination of advanced metalworking techniques, automation, and quality control processes. The combination of these elements ensures the creation of a durable, functional, and aesthetically pleasing product. As trends shift toward sustainability, automation, and customization, manufacturers will need to adapt their production processes accordingly to stay competitive in the global market.
The production of sheet metal soup ladles continues to evolve with advancements in technology, material science, and consumer demands. As manufacturers focus on improving the efficiency, functionality, and aesthetics of ladles, they are increasingly incorporating smart manufacturing techniques to streamline production processes. This includes robotic automation for precise welding, artificial intelligence (AI) for quality control, and advanced CNC machining for intricate design customization.
The demand for eco-friendly products is also growing, and manufacturers are shifting towards sustainable materials and energy-efficient production methods. In this regard, recycled metals may be used to produce ladles without compromising on quality. Additionally, the process may utilize solar or wind energy to power machinery, making the entire production cycle more sustainable. This commitment to sustainability not only reduces environmental impact but also appeals to the growing consumer base that values eco-conscious products.
Another notable development in the production of sheet metal ladles is the use of 3D printing and additive manufacturing. These technologies are allowing manufacturers to produce highly customizable ladles in shorter production runs, catering to consumer preferences for personalized kitchenware. Through 3D printing, unique textures, shapes, or even engraved patterns can be integrated into the ladle’s design without the need for extensive tooling changes. This means that small-batch production and limited-edition designs can be created with minimal lead time, allowing manufacturers to quickly respond to consumer trends or requests for bespoke products.
In the realm of design and functionality, manufacturers are increasingly considering ergonomics and user experience. The handle design, for example, is crucial to the comfort and ease with which the ladle is used. Features like heat-resistant grips, curved handles for better control, and anti-slip coatings are becoming more common. These innovations are aimed at ensuring that the ladle is not only functional but also comfortable for the user, especially when stirring or serving hot liquids.
Moreover, there is an increasing interest in multi-functional ladles that offer more than just the traditional serving purpose. Some designs may incorporate features such as built-in strainers, measuring scales, or collapsible handles to cater to consumers seeking versatile kitchen tools. As people become more interested in efficient kitchen gadgets, the market for innovative and multi-purpose ladles is expanding.
The globalization of the kitchenware market also plays a significant role in shaping the production of sheet metal soup ladles. With more international consumers looking for high-quality products, manufacturers are investing in global supply chains and distribution networks. This ensures that ladles reach diverse markets while maintaining competitive pricing. At the same time, manufacturers are increasingly aware of the regional preferences in terms of design, size, and material. For example, some regions may prefer smaller ladles, while others might opt for larger versions suitable for cooking in bigger pots.
Finally, the integration of smart kitchen technology into everyday kitchenware could bring about a significant shift in soup ladle production. Future soup ladles may feature temperature sensors that alert users when the ladle has reached a certain heat threshold, preventing burns or other injuries. These features could be connected to smartphone apps for real-time tracking of cooking processes, offering a more high-tech and user-friendly experience.
As the production of soup ladles becomes more refined, consumer trends will continue to drive innovation. The combination of advanced manufacturing, sustainable practices, and consumer-driven design will ensure that sheet metal soup ladles remain an essential and evolving tool in kitchens worldwide. Manufacturers who embrace these trends and adapt to changing consumer expectations will remain competitive in an ever-evolving market.
As the sheet metal soup ladle production process evolves, we are likely to see further integration of smart technologies and advanced materials that can enhance both the performance and sustainability of these kitchen tools. One exciting development on the horizon is the increased use of smart coatings and nano-coatings that could be applied to ladles. These coatings would provide additional benefits such as non-stick properties, increased resistance to stains and scratches, and improved heat distribution. For instance, ceramic coatings could help maintain the temperature of soups or stews for longer periods, making the ladle even more functional for both cooking and serving. Similarly, anti-microbial coatings could be developed to reduce the growth of bacteria or other pathogens on the ladle’s surface, improving hygiene and ensuring safety when handling food.
Another key development is the growing emphasis on modularity in kitchenware, including ladles. Modular ladles would allow consumers to swap out or replace certain components, such as the handle, based on their specific needs. For example, a long handle might be preferred for use in large pots or cauldrons, while a short handle would be better for everyday use. Additionally, these components could come in a variety of materials, from stainless steel to more ergonomic, heat-resistant plastics or even bamboo, allowing for personalized preferences in terms of grip and comfort.
The evolution of manufacturing techniques will also play a significant role in shaping the future of soup ladle production. As additive manufacturing continues to develop, ladles can be produced with intricate internal structures that would have been difficult to achieve with traditional metalworking techniques. For example, 3D printing could allow for hollow or lightweight ladles without sacrificing durability. This would lead to lighter, more comfortable designs that are easier to handle while also offering the strength and durability associated with metal ladles.
Additionally, as consumer expectations grow in terms of product lifespan and sustainability, companies may move toward circular economy principles in their production processes. This could involve designing ladles with components that are easy to disassemble and recycle, or using fully recyclable metals and materials in the manufacturing process. For example, aluminum ladles could be designed with minimal or no plastic components, making them more environmentally friendly and easier to recycle. As the trend for upcycling and reuse continues to grow, some manufacturers may even consider offering refurbishing services for damaged or worn-out ladles, allowing consumers to send their old ladles back for repair or replacement of worn components.
Another key consideration in future production techniques is energy efficiency. Manufacturers will likely continue to look for ways to reduce energy consumption in the production process, utilizing more efficient machines or renewable energy sources like solar power and wind power to run production lines. The adoption of energy-efficient machinery that uses less power, while maintaining high precision and output, will not only lower costs for manufacturers but also reduce the carbon footprint of production.
As global trade continues to shape the kitchenware market, manufacturers will also need to be prepared for fluctuations in raw material costs and the increasing importance of supply chain resilience. For example, the cost of stainless steel and aluminum can vary based on geopolitical factors and trade agreements. To mitigate these risks, companies may explore alternatives to traditional materials, such as composite metals, which are lighter and more cost-effective, while maintaining the strength and functionality needed for a quality soup ladle. Additionally, building more localized production hubs in key markets could help mitigate some of the risks associated with global supply chains.
With the growing popularity of home cooking and culinary experimentation, we are likely to see more specialized ladles for specific culinary needs. For instance, ladles with integrated strainers for ladling out soups and broths without solids or specialized shapes for use in particular types of cuisine, such as Asian-style ladles for serving broth-based dishes. The ability to customize ladles for particular cooking styles or specific recipes may become a key feature for manufacturers catering to an increasingly diverse global market.
In parallel, digital fabrication tools will play an important role in allowing smaller manufacturers or startups to innovate and create custom ladles with greater precision. This democratization of manufacturing could lead to a surge in bespoke ladles, designed to meet niche requirements that larger manufacturers might not address. These digital fabrication tools, including CNC machines and laser cutters, enable artisans and small-scale manufacturers to produce high-quality ladles in smaller quantities, offering unique designs or custom features like engraved names or specialized handles.
As consumer expectations continue to evolve, the production of sheet metal soup ladles will increasingly focus on functionality, sustainability, and design innovation. The use of smart manufacturing techniques, such as AI-powered production, robotic assembly, and advanced material processing, will ensure that these products remain efficient to produce while meeting the growing demand for customization, quality, and sustainability. At the same time, manufacturers will need to be agile, adapting to rapidly changing market trends and consumer demands, all while maintaining high standards of craftsmanship and durability.
As we continue into the future of sheet metal soup ladle production, there are several more advancements on the horizon that will shape the industry. These developments will not only impact the manufacturing process but will also influence the consumer experience, expanding the capabilities and appeal of kitchen tools.
One of the key areas to focus on is product traceability and transparency. With increasing consumer interest in knowing the origin of materials and the environmental impact of their purchases, manufacturers may adopt blockchain technology to provide detailed product histories. This could include information about where the raw materials were sourced, how the ladles were produced, and what efforts were made to ensure sustainability in the production process. By incorporating these traceability measures, manufacturers can build trust with consumers and cater to the growing demand for ethically produced products.
In the context of customization and personalization, the trend towards offering more tailored kitchen products will continue to grow. Manufacturers may start to offer interactive online platforms where customers can design their own ladles, choosing handle lengths, finishes, shapes, or adding personal engravings. This direct-to-consumer approach, facilitated by advanced manufacturing technologies like 3D printing or laser engraving, will allow for a high degree of personalization, enabling each soup ladle to be uniquely crafted to suit the specific preferences of the user.
Smart kitchen appliances are also expected to become more integrated with traditional kitchen tools, such as soup ladles. We could see innovations like temperature-sensitive ladles that change color based on the temperature of the liquid they are stirring, allowing users to avoid burns or to track cooking progress visually. This could be especially useful in professional kitchens or for home cooks who want to ensure the perfect serving temperature for soups, sauces, or broths. These “smart ladles” might also sync with smartphone apps, providing real-time data on cooking times, temperature, and more.
As more people turn to health-conscious cooking, the demand for non-toxic, eco-friendly, and safe-to-use kitchen products will increase. To meet these demands, manufacturers may introduce non-toxic coatings that are safe to use with hot liquids and easy to clean, without any harmful chemicals or substances leaching into food. Non-stick surfaces made from natural materials, such as ceramic or silicone, could become more common in ladles, offering an alternative to traditional non-stick coatings that may contain harmful substances like PFOA or PTFE.
For multifunctional ladles, innovations could lead to ladles that combine multiple kitchen tools into one. Imagine a ladle with a built-in measuring cup, strainer, or whisking attachment that allows for more efficient and streamlined cooking. This could help save space in kitchens and reduce the need for multiple utensils, which appeals to consumers with smaller kitchens or those who value convenience and versatility. These multifunctional ladles could be tailored to suit specific cooking styles, such as ladles with precise measuring marks for baking or integrated strainers for ladling broth from large cooking pots.
In addition, ergonomics and user-friendly designs will continue to be an area of focus. Given that soup ladles are used in often repetitive motions, comfort and ease of use will remain critical design factors. Innovations in handle shapes, such as ergonomic grips or heat-resistant handles, will be important to reduce hand fatigue and provide a better cooking experience. New materials, such as composite metals, could be used to create ladles that are both lightweight and highly durable. These materials may also offer better resistance to wear, stains, and rust, further extending the lifespan of the ladle.
The development of smart manufacturing will allow for greater flexibility and responsiveness to market needs. Manufacturers may use machine learning algorithms to track consumer preferences and adjust production in real-time. For instance, based on online trends or seasonal demand, manufacturers could quickly produce limited-edition ladles with unique designs or features that cater to emerging consumer desires. Additionally, robotics could be employed to increase precision during the welding and assembly stages, ensuring consistency and reducing human error.
Another potential area of growth lies in the adoption of modular kitchenware systems, where kitchen tools like ladles can be part of a larger set of interchangeable components. For example, a ladle’s handle could be easily swapped out for one with a different size or style depending on the user’s needs. These modular systems would allow consumers to mix and match different parts of their kitchenware, creating a more customizable and adaptable cooking experience. Such systems could also appeal to environmentally conscious consumers by reducing waste and encouraging long-term use of durable, replaceable components.
The integration of sustainable production practices will be vital as the global demand for more responsible manufacturing grows. In addition to using recycled metals and renewable energy, companies may also explore zero-waste manufacturing processes. For example, scrap metal from the ladle production process could be reused in the same production cycle, minimizing waste. Closed-loop manufacturing systems, where waste materials are recycled back into the production line, could be adopted to reduce overall material consumption and environmental impact. Manufacturers will need to stay ahead of increasing regulatory standards for sustainability, ensuring that their products meet consumer expectations for eco-conscious design.
In the future, we may also see interactive features in ladles, such as built-in scales that weigh the contents being ladled or sensors that alert the user when the ladle is too hot or when they are approaching a certain volume of liquid. These innovations would add a new layer of convenience and precision to cooking tasks, allowing for more accurate portion control and improving safety in the kitchen.
In conclusion, the future of sheet metal soup ladle production is poised for exciting advancements that blend technology, sustainability, personalization, and consumer demands. The evolution of materials, manufacturing processes, and design will make soup ladles more versatile, durable, and user-friendly, while also aligning with broader trends in environmental responsibility and product innovation. As these changes unfold, manufacturers will need to adapt quickly to the fast-moving landscape of the kitchenware market, ensuring that they continue to meet the ever-evolving needs of the modern consumer.
Sheet Metal Salad Bowl Production Machine
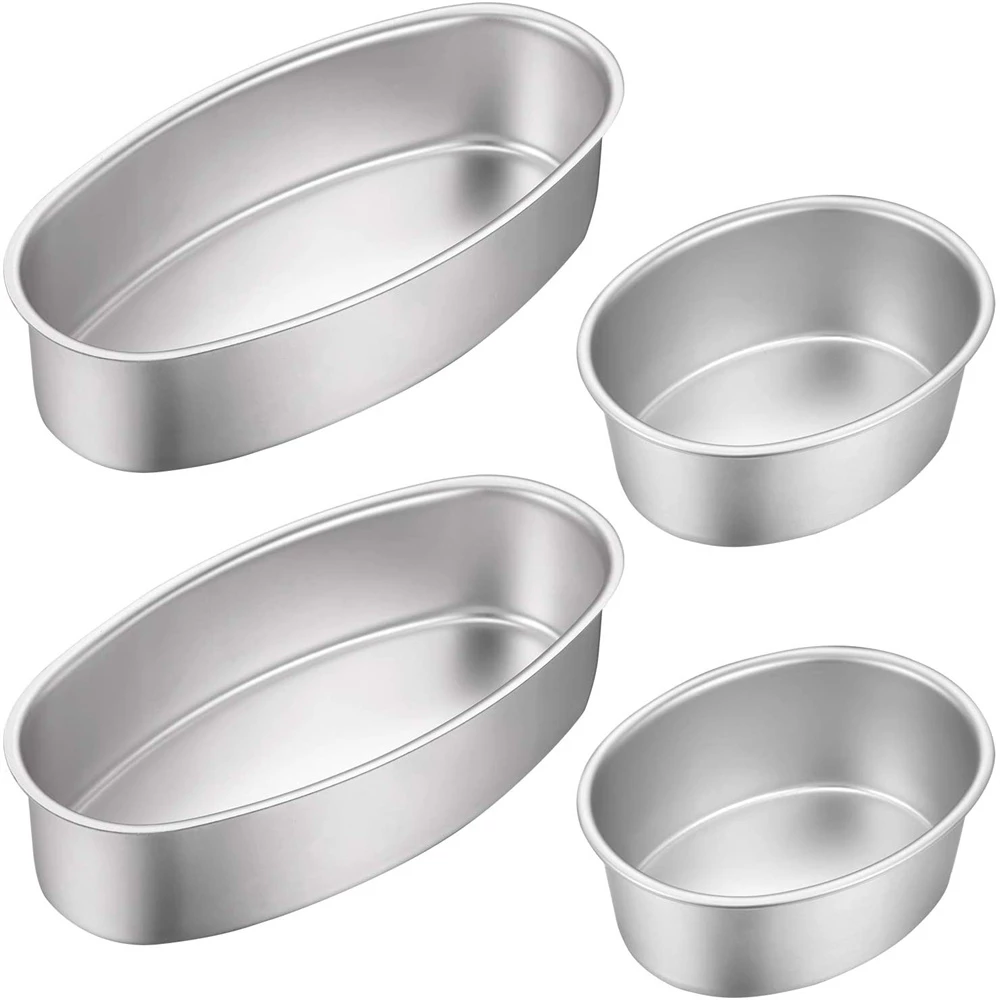
The production of sheet metal salad bowls involves a range of processes designed to create durable, aesthetically appealing, and functional products. Salad bowls made from sheet metal, typically stainless steel, aluminum, or tin-plated steel, are prized for their lightweight, long-lasting nature and ability to retain a sleek, modern appearance. Here is an overview of the production machine and the key stages involved in manufacturing sheet metal salad bowls.
1. Material Selection
The first step in the production of sheet metal salad bowls is selecting the appropriate metal. Stainless steel is commonly used due to its rust resistance, durability, and appealing aesthetic. Other materials like aluminum are sometimes used for lighter bowls. These materials are sourced in sheets of various thicknesses, and the choice of material depends on factors like the desired bowl weight, durability, and cost.
2. Blanking (Cutting the Metal Sheets)
The process begins with blanking, which involves cutting the sheet metal into circular blanks or discs. This is typically done using punching machines or laser cutters. The blank’s diameter must match the desired size of the salad bowl.
- Punching Machines: Hydraulic or mechanical presses with punching dies cut out precise circular blanks from the sheet metal.
- Laser Cutting: A more advanced technique, where a focused laser beam is used to cut the metal sheet, providing more intricate designs or cleaner edges.
3. Deep Drawing (Forming the Bowl Shape)
Once the circular blanks are ready, they are transferred to the deep drawing press, which is the key step in shaping the metal into a bowl. In this process, the blank is fed into a die cavity, where a punch pushes the blank downward to form the bowl’s shape. The metal is stretched and formed as it is drawn into the cavity, creating a smooth, uniform shape.
- Hydraulic Presses: The metal blank is placed between a die and a punch, and the press applies force to stretch the metal and form the bowl shape.
- Mechanical Presses: Similar to hydraulic presses but use mechanical force to create the deep drawing effect. These presses are faster but may be less suited for thicker or harder metals.
During this stage, attention is paid to uniform thickness and smooth surfaces to avoid imperfections, such as wrinkles, which can negatively affect the bowl’s quality.
4. Trimming and Edging
After deep drawing, the edge of the bowl is often trimmed to remove any excess metal from the forming process. This trimming is done with a cutting die or laser cutter to ensure clean, smooth edges.
- Beading: This process involves rolling the metal edge of the bowl to form a stronger, more rigid rim. It also gives the bowl a finished look.
- Flanging: A similar process to beading, but involves folding the edge of the bowl slightly outward to create a smooth and functional lip.
5. Annealing (Heat Treatment)
Some metals, like stainless steel, require heat treatment through annealing. This process softens the metal, making it more malleable for the next steps and relieving stresses caused by deep drawing. Annealing is typically done in a furnace at high temperatures and may be followed by cooling to room temperature.
6. Surface Treatment
To enhance the appearance and durability of the salad bowl, a surface treatment is applied. This could include:
- Polishing: The bowl is polished to give it a shiny, smooth surface, improving both its aesthetic appeal and resistance to corrosion.
- Brushing: A more matte, satin finish may be applied by brushing the surface with abrasive pads. This treatment helps prevent fingerprints and adds a modern, professional look.
- Coating: Some manufacturers may apply a protective coating or powder-coat for enhanced durability and to reduce the chance of rusting (especially for non-stainless steel bowls).
7. Quality Control
Before the salad bowls are packaged and distributed, they go through a rigorous quality control process to check for defects. This includes inspecting:
- Shape and size: Ensuring the bowl matches the specified dimensions and has a uniform shape.
- Surface defects: Checking for scratches, dents, or imperfections in the finish.
- Strength: Ensuring the bowl can withstand normal usage without deforming.
- Edge quality: Ensuring that edges are smooth and free from sharp points or burrs that could be harmful to users.
8. Packaging
After quality control, the bowls are ready for packaging. They are typically stacked together with protective materials (e.g., foam or bubble wrap) to prevent damage during shipping. Custom packaging may also be used for branding purposes or to provide additional protection.
9. Automation in Production
Modern production facilities use a combination of automation and manual labor to ensure both high efficiency and precision. Machines for blanking, deep drawing, trimming, polishing, and coating are often robotically controlled to ensure consistent quality and speed. In some cases, AI-powered quality control systems are implemented to detect defects that might be difficult for humans to spot.
10. Customization Options
With advancements in production technology, customization options are increasingly being offered. Consumers can select different finishes (matte, polished, brushed), bowl sizes, and even specific designs for decorative purposes. Laser engraving allows for personalized engravings on the exterior or interior of the bowl, making these salad bowls suitable for promotional use or as personalized gifts.
In summary, the production of sheet metal salad bowls involves a combination of cutting, forming, finishing, and surface treatment processes. The automation of these processes helps create high-quality bowls with precision, while also allowing for customization in size and finish. Advancements in manufacturing technology continue to make the process more efficient, eco-friendly, and capable of producing a wider range of products tailored to specific consumer needs.
The production of sheet metal salad bowls is a complex process that requires a combination of precision machinery, material handling, and surface treatments to create a high-quality, durable, and aesthetically pleasing product. The process begins with selecting the appropriate material, typically stainless steel, aluminum, or tin-plated steel, which are chosen for their strength, corrosion resistance, and appealing finish. Once the material is selected, the sheet metal is cut into circular blanks, either using punching machines or laser cutters. This step ensures that the raw material is prepared to the exact dimensions needed for the bowl.
The next phase is deep drawing, where the circular blanks are shaped into a bowl form. This is accomplished using a hydraulic or mechanical press, where the blank is drawn into a die cavity by a punch. The force of the press stretches the metal, creating a smooth, uniform bowl shape. Once the bowl is formed, the edges are trimmed and sometimes rolled to create a clean, finished rim. The beading or flanging processes also serve to reinforce the edges, making the bowl more rigid and improving its overall structural integrity.
After the shaping process, some metal types, like stainless steel, require annealing to relieve internal stresses and make the metal more malleable. This heat treatment also enhances the bowl’s durability. Following this, the bowl undergoes surface treatments such as polishing or brushing to improve its appearance and increase resistance to corrosion. Some manufacturers may apply coatings or powder coatings for added protection or aesthetic appeal.
As part of quality control, each bowl is inspected for defects in shape, surface finish, and strength. The goal is to ensure that the bowls are free from scratches, dents, and imperfections and that they meet the required standards for durability. The final bowls are then packaged with care, using protective materials to ensure they arrive in pristine condition.
Automation plays a crucial role in modern salad bowl production, with many of the steps being handled by robotic machinery to ensure consistency and speed. The process is highly efficient, allowing manufacturers to produce large quantities of bowls while maintaining high standards of quality. At the same time, customization options such as personalized engravings, various finishes, and different sizes can be offered to cater to consumer preferences.
The future of sheet metal salad bowl production may see continued advancements in materials, such as the use of more eco-friendly coatings or the incorporation of smart technologies like temperature sensors or built-in weight scales. As consumer demand for sustainable and customizable products grows, manufacturers will need to adapt by implementing greener practices and offering more versatile, personalized products to meet market needs.
As the sheet metal salad bowl production process evolves, the integration of more advanced technologies and materials will continue to improve both the manufacturing efficiency and the functionality of the final product. The next wave of innovation in salad bowl production is likely to center on enhanced material properties, sustainability, and consumer demand for versatility.
One key area of development is the exploration of new, more sustainable materials. As environmental concerns continue to rise, manufacturers may turn to materials that offer superior durability and are easier to recycle. For example, recycled aluminum or stainless steel could become more commonplace, as these materials are durable, resistant to corrosion, and highly recyclable. The use of biodegradable coatings or non-toxic finishes could also become more prevalent, providing a safer, environmentally friendly alternative to traditional chemical-based finishes.
The use of advanced surface treatments could also improve the functionality and appearance of the bowls. Nano-coatings, for instance, could be applied to salad bowls to make them more resistant to stains and scratches, which are common issues with metal products. These coatings could also enhance the bowl’s resistance to rust, ensuring a longer lifespan, even in challenging environments like humid kitchens or outdoor settings. Additionally, hydrophobic coatings might be used to repel liquids, making the bowls easier to clean and preventing buildup of food residues.
With increasing consumer interest in customization and personalization, the demand for bespoke products will likely rise. More advanced laser engraving and 3D printing technologies could allow for detailed custom designs on the surface of salad bowls, ranging from family names to unique artwork. These technologies also allow for smaller, more specialized production runs, giving manufacturers the ability to cater to niche markets and provide customized, high-end options for consumers. This customization could extend to the shape and size of the bowls as well, as consumers may seek smaller, more compact versions for individual servings, or larger ones for family gatherings or parties.
Smart technology may also find its way into the salad bowl production process. Imagine a bowl with an integrated smart sensor that could measure the temperature of the contents, ensuring that salads are served at the optimal temperature for freshness and flavor. Alternatively, digital scales integrated into the base of the bowl could allow users to measure precise portions of ingredients directly in the bowl. These innovations would enhance the user experience and appeal to the growing trend of tech-savvy kitchenware.
Manufacturers will also continue to look for ways to improve production efficiency. With the rise of Industry 4.0 technologies, such as artificial intelligence (AI) and robotic automation, manufacturers will be able to create even more precise, high-quality bowls at faster rates and lower costs. AI could optimize various aspects of production, from material selection to quality control, ensuring that each bowl meets the required standards. Robotics could further reduce labor costs while enhancing precision during the deep drawing, trimming, and finishing stages of production. Additionally, advancements in additive manufacturing (3D printing) could lead to more intricate designs and custom molds that would have been difficult or expensive to achieve with traditional methods.
The sustainability aspect of the production process will also become more important. As consumers demand more environmentally conscious products, manufacturers will need to implement practices like zero-waste production. This could involve using scrap metal from earlier stages of production in subsequent batches, reducing overall waste. The introduction of closed-loop systems, where waste is either reused or repurposed within the same production cycle, will also help reduce the carbon footprint of production. Similarly, energy-efficient machinery and renewable energy sources could help minimize the environmental impact of manufacturing processes.
The global market for salad bowls and kitchenware products will continue to drive innovation in design and functionality. Companies will need to stay agile and responsive to shifting market trends, as consumers seek products that not only perform well but also reflect their values and lifestyles. The trend towards minimalism in design will continue to influence the aesthetic of salad bowls, with simpler, more streamlined designs becoming popular. However, there will also be room for more elaborate and artistic designs for consumers who want their kitchenware to make a statement.
Finally, collaborations with chefs and culinary influencers may become a more common strategy for manufacturers looking to appeal to the growing market of food enthusiasts. By working with industry professionals, manufacturers can ensure that their products meet the high standards expected in the culinary world, while also gaining exposure through endorsements and marketing campaigns.
In conclusion, the future of sheet metal salad bowl production will see a fusion of advanced materials, smart technology, and sustainability. Manufacturers will need to balance innovation with efficiency and consumer demand for customization. The evolution of production methods and the integration of new technologies will shape the next generation of salad bowls, ensuring that they are not only functional but also meet the aesthetic, environmental, and technological expectations of modern consumers.
As we continue to explore the future of sheet metal salad bowl production, the advancements and trends shaping the industry will likely center around enhanced user experience, efficiency, and global demand for high-quality, sustainable products. Manufacturers will continue to adapt to the evolving consumer landscape and integrate cutting-edge technologies to stay competitive.
The rise of personalized and bespoke kitchenware is one of the most significant shifts in consumer preferences. As consumers increasingly look for unique, customized items that reflect their personal style, manufacturers will continue to invest in technologies like laser etching, 3D printing, and automated design software. This will allow them to offer a wide range of customization options, from intricate engraving to bespoke shapes, finishes, and sizes. Personalized salad bowls could even become a popular gift item, with consumers able to add personal touches like names, logos, or family crests. These capabilities will provide a unique selling point for manufacturers who want to differentiate their products in a crowded market.
Sustainability will remain a key driver in the production of sheet metal salad bowls. As the global demand for eco-friendly products continues to grow, manufacturers will need to explore more sustainable production methods. Beyond using recycled materials like stainless steel and aluminum, manufacturers may adopt cleaner production techniques that reduce waste and energy consumption. For example, closed-loop production systems, where material scraps are collected and reused, will minimize waste and ensure that more resources are recycled back into the production process.
In addition to material sustainability, energy-efficient manufacturing will become increasingly important. The use of renewable energy sources, such as solar or wind power, could be integrated into the manufacturing plants, reducing the carbon footprint of production. Low-energy equipment will also help minimize energy consumption throughout the production cycle. These steps will not only appeal to environmentally conscious consumers but also help manufacturers meet stricter global regulations around sustainability and carbon emissions.
Technological advancements in automation and robotics will further streamline the production process. The integration of AI-driven machines into the production line will enable manufacturers to achieve higher precision and faster output while minimizing human error. For example, robotic arms can perform tasks such as grinding, polishing, and trimming, ensuring consistent quality at a high speed. These automation systems will also allow manufacturers to produce smaller batches of custom bowls without sacrificing efficiency or quality. This flexibility will allow companies to meet the growing demand for personalized and niche products while reducing lead times.
Smart manufacturing technologies, including IoT (Internet of Things) devices, will provide real-time monitoring of production processes, allowing manufacturers to track everything from raw material usage to equipment performance. By collecting data from machines and production lines, companies can identify inefficiencies, predict potential breakdowns, and improve the overall quality of their products. The integration of AI and machine learning into the manufacturing process could also help companies predict trends in consumer demand, optimizing production schedules and supply chains for maximum efficiency.
Another trend gaining momentum is multi-functional kitchenware, where products serve multiple purposes in the kitchen. For salad bowls, this could mean the integration of smart sensors that monitor freshness or temperature, ensuring that salads are kept at the ideal temperature for serving. Built-in scales could allow users to measure ingredients directly in the bowl, promoting portion control and healthier eating. Similarly, modular salad bowls could be designed with interchangeable parts, allowing users to add or remove sections or features based on their needs. These innovations would create a more dynamic, multi-functional product that appeals to both home cooks and professional chefs.
The digitalization of the consumer shopping experience is another trend likely to influence the future of salad bowl production. Online customization tools will become more sophisticated, allowing consumers to design their own bowls before purchasing. For example, interactive platforms might allow users to choose from a variety of finishes, shapes, and sizes, while also adding custom engravings or artwork. Additionally, with the growth of e-commerce, manufacturers will need to ensure that their products are optimized for online sales, with clear, detailed descriptions, high-quality images, and easy ordering processes.
In terms of global trends, manufacturers will continue to expand into emerging markets, where there is an increasing demand for high-quality kitchen products. Companies that are able to combine innovation with affordability will be in a prime position to capture this growing market. At the same time, the demand for premium, high-end products will remain strong in developed markets, especially as consumers continue to seek unique, luxurious, and premium-quality kitchenware.
The role of design will also evolve as manufacturers look to align their products with changing consumer tastes. Aesthetics will continue to be important, but with more focus on functional beauty—products that not only look good but also make cooking and serving more enjoyable and efficient. Salad bowls, for example, might feature ergonomic designs that make them easier to handle, or come with stackable features for easier storage. Additionally, minimalist designs will continue to be popular, with clean, simple lines and neutral finishes that can seamlessly integrate into modern kitchen styles.
Collaborations with chefs, influencers, and culinary experts will become increasingly important in the salad bowl market. As consumers become more discerning and knowledgeable about food and cooking, they will look to trusted voices for recommendations on the best products. By collaborating with prominent chefs or influencers in the culinary space, manufacturers can build credibility and increase their products’ visibility in a crowded marketplace.
In summary, the future of sheet metal salad bowl production will be shaped by a combination of technological innovation, sustainability, and consumer demand for customization and functionality. Manufacturers will need to adapt to changing market conditions, integrate new technologies into the production process, and stay ahead of consumer trends to remain competitive. Whether through advanced automation, eco-friendly practices, or smart, personalized products, the industry will continue to evolve and deliver high-quality kitchenware that meets the needs and expectations of modern consumers.
Sheet Metal Buffet Tray Production Machine
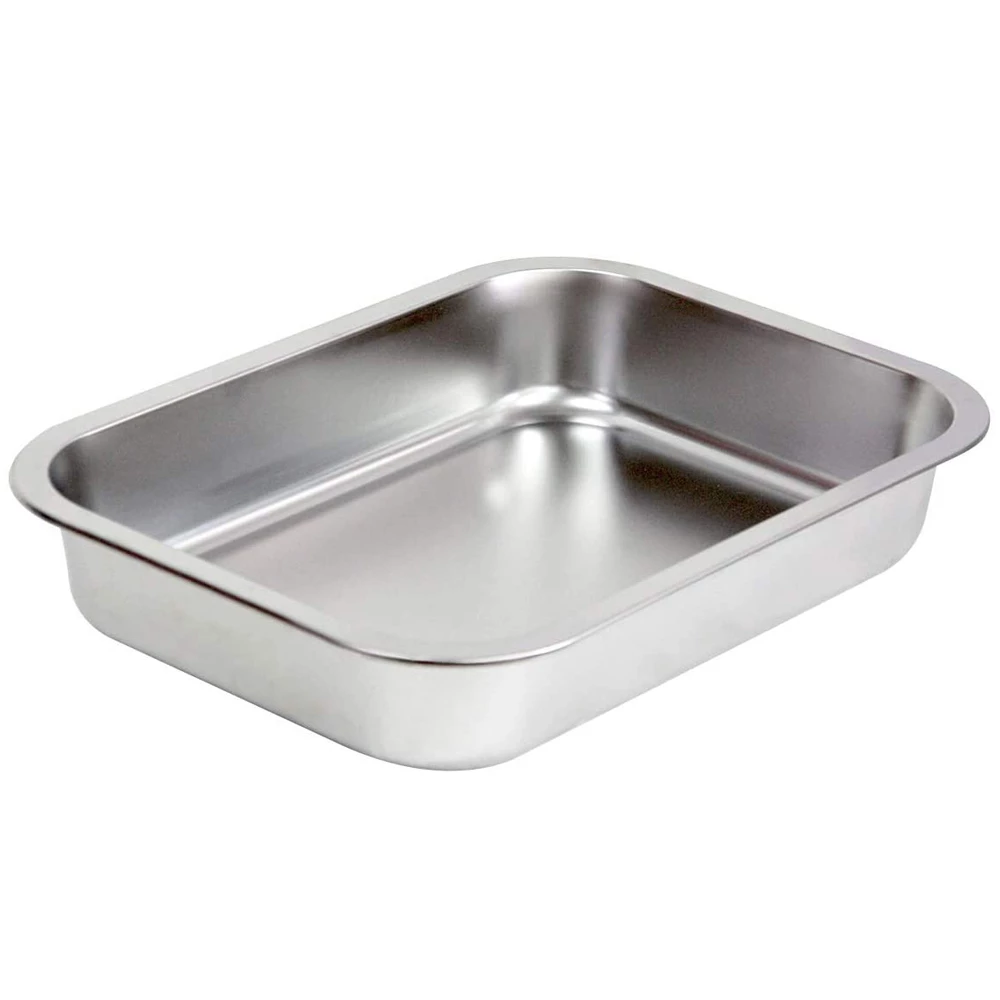
The production of sheet metal buffet trays involves a combination of various processes designed to create high-quality, durable, and aesthetically appealing trays. These trays are typically made from metals like stainless steel, aluminum, or tin-plated steel to ensure strength, resistance to corrosion, and ease of cleaning, making them ideal for use in buffet settings. Here is an overview of the process and the production machinery used for manufacturing sheet metal buffet trays.
The first step in the production of a buffet tray is the selection of the material. Stainless steel is often chosen due to its resistance to rust and its ability to maintain its appearance over time, especially in environments with frequent exposure to moisture. Other materials, like aluminum, are used for lightweight trays, while tin-plated steel can be used for more cost-effective options.
Once the material is selected, it is supplied in the form of sheet metal that is cut into the appropriate shape for the tray. This is typically done using punching machines or laser cutting technology. Laser cutting is particularly useful for more intricate designs, as it can create smooth, clean cuts with high precision.
Next, the cut sheets are fed into a forming press, which shapes the tray into its desired form. Deep drawing presses are commonly used to form the sides of the tray and create the depth required for holding food. A hydraulic press or mechanical press applies force to the sheet metal, pushing it into a die cavity that gives the tray its shape. The force exerted during the drawing process stretches the metal, so special care is taken to ensure that the tray retains its strength and integrity while forming.
After the forming process, the tray undergoes trimming to remove any excess metal from the edges. Cutting dies or laser cutting techniques are used to trim the tray to its final dimensions. The edges may then undergo beading or flanging, which strengthens the edges and prevents any sharp or rough surfaces that could cause injury or damage during handling.
Once the tray is shaped and trimmed, it may go through a surface finishing process. This is an essential step in ensuring the tray is visually appealing and resistant to staining or corrosion. Polishing or brushing may be used to give the tray a smooth, shiny surface. For a matte finish, brushing provides a satin-like texture, which also helps reduce the appearance of fingerprints. Some trays may undergo coating treatments to enhance durability or provide a unique aesthetic. Powder coating or electroplating can be used to add color or additional corrosion resistance, ensuring the tray lasts longer even with frequent exposure to food and moisture.
A crucial step in the production of sheet metal buffet trays is quality control. Each tray is carefully inspected for defects such as scratches, dents, or imperfections in the finish. The trays are tested for strength to ensure they can handle the weight of food without bending or breaking. In some cases, trays are subjected to stress tests to simulate use in high-pressure buffet environments.
Finally, the trays are packaged and prepared for shipping. Packaging materials, such as foam or bubble wrap, are used to protect the trays from damage during transport. Additionally, trays are often stacked or packed in sets, depending on the product design.
Modern automation in buffet tray production has significantly improved efficiency. Robotic arms are often employed to handle the trays during various stages of production, such as transferring them from one machine to another. AI-driven quality control systems also play a role in identifying defects that could be missed by the human eye, further improving product consistency and reducing waste.
The integration of customization options is another growing trend in buffet tray production. Manufacturers can offer trays in different sizes, shapes, and finishes to meet the specific needs of their customers. Customization could include the addition of engraved logos, unique designs, or specific patterns that help distinguish a brand or make the trays more suited for specific events or settings.
Smart features could also be incorporated into buffet trays. For example, trays might feature built-in temperature regulation systems or removable inserts to keep food at an optimal temperature. These advancements would make buffet trays even more versatile and appealing for both professional catering and home use.
In summary, the production of sheet metal buffet trays involves several key steps, including material selection, cutting, forming, trimming, finishing, and quality control. Automation and smart manufacturing technologies are helping to increase the efficiency and precision of the process, while customization and the addition of functional features allow manufacturers to meet evolving consumer needs and market demands. The future of buffet tray production will likely see continued advancements in materials, finishes, and technology, ensuring that these trays remain durable, functional, and aesthetically pleasing in a wide range of settings.
The production of sheet metal buffet trays is a highly specialized process, where each step plays a crucial role in ensuring the final product is durable, functional, and visually appealing. As we move forward in the production process, after the trays have been formed and shaped, they are often subjected to various finishing treatments that not only enhance their appearance but also increase their longevity. These processes are essential for ensuring that the trays maintain their aesthetic appeal in high-use environments like buffets, catering events, or in commercial kitchens.
Once the tray is trimmed and any excess material is removed, a surface finish is applied to the metal. This can include processes such as polishing, which gives the tray a shiny, reflective surface, or brushing, which provides a matte, satin-like finish. Polishing is particularly popular in buffet trays that are used in high-end settings or upscale catering events, where the visual appeal is just as important as functionality. Brushed finishes, on the other hand, are often chosen for their practicality, as they tend to show fewer fingerprints and smudges, making them ideal for more frequent handling in busy buffet environments.
Additionally, coatings may be applied to enhance the tray’s resistance to staining, corrosion, and scratching. Powder coating, a process in which a dry powder is applied to the surface of the tray and then cured with heat, is one such treatment. It creates a tough, durable layer that helps protect the tray from environmental factors, extending its lifespan. Some trays are also subjected to electroplating or anodizing, which not only adds an additional layer of protection but can also provide a distinctive aesthetic finish, such as gold, bronze, or other metallic looks.
The next crucial step involves quality control, which ensures that every tray meets the required standards of durability, strength, and visual appeal. This involves checking for imperfections such as scratches, dents, or inconsistencies in the finish. Some companies implement automated inspection systems using machine vision technology, which scans the trays for flaws with higher precision and speed than manual inspections. The strength and integrity of the tray are also assessed through various tests to make sure it can withstand the weight of food without warping or bending. This stage is essential for ensuring that the trays are both functional and safe to use in buffet settings, where they are subject to repeated handling and load-bearing stresses.
The final assembly phase involves any additional touches or customizations that the tray might require. Some trays may include handles, which are either welded or fastened onto the sides for easier transportation. These handles must be securely attached to prevent them from coming loose, as the trays will frequently be moved with substantial weight. In some cases, logos or branding may be engraved or stamped onto the tray to give it a personalized or professional touch. This is particularly common for commercial customers, like hotels or catering companies, who want to showcase their branding on their buffetware.
Once the trays pass inspection, they are packaged for shipment. Packaging must be carefully done to prevent any damage during transport, as these trays are often made of metal and can be prone to scratches and dents. Protective materials such as foam or bubble wrap are used to cushion the trays, and they are often packed in sets or stacks to save space and improve handling efficiency. Proper packaging also helps minimize the risk of breakage during shipping and delivery.
Automation has increasingly played a major role in improving the efficiency and precision of the production process. Robotics are used in many stages, from handling raw materials to moving the trays through different stages of production. Robots can load and unload trays from machines, handle the trays more quickly and safely, and reduce labor costs. Additionally, AI-powered systems are used to improve precision during cutting, forming, and finishing, ensuring each tray has the correct dimensions and a smooth, flawless surface.
Looking forward, the demand for customization in the buffet tray market will continue to grow. Manufacturers are responding by offering a wider range of sizes, finishes, and design options to suit different event themes or customer preferences. Some companies are even adopting 3D printing technologies for prototyping new tray designs, enabling them to quickly develop customized molds for limited production runs or special orders. With the growing trend towards personalization, more consumers will be able to select their preferred finishes, engravings, and even colors for their trays, allowing for unique and tailored buffetware.
The future of buffet tray production will also likely see a shift towards sustainability. As consumers and businesses become more environmentally conscious, the demand for products made with recycled materials or those that are easy to recycle after use will continue to rise. Many manufacturers are already implementing zero-waste production systems, where metal scraps from cutting and forming are reused in the production of future trays. This reduces material waste and improves resource efficiency, aligning with global efforts to reduce environmental impact.
Additionally, the integration of smart features in buffet trays could become a trend. Temperature-regulated trays, for example, could maintain the ideal serving temperature for hot or cold foods, offering enhanced convenience in buffet settings. Trays with built-in sensors could monitor food temperature or detect when the tray needs refilling, providing catering staff with real-time data to improve service efficiency. These smart features could revolutionize buffet service, offering new functionalities beyond traditional tray design.
In conclusion, the production of sheet metal buffet trays is a highly detailed and automated process that combines precision manufacturing with robust quality control. The industry is continuously evolving to meet growing demand for customization, sustainability, and technology integration. As trends shift toward more personalized, functional, and eco-friendly products, manufacturers will need to stay ahead of market demands by adapting their processes and incorporating new technologies that improve both the production process and the end product’s performance.
As we continue exploring the future of sheet metal buffet tray production, there are several additional trends and developments that will likely shape the industry moving forward.
One such trend is the increasing focus on ergonomics and ease of use in product design. While the primary function of a buffet tray is to hold and serve food, its usability for the person handling it is equally important. The integration of ergonomic handles and lightweight designs will make these trays easier to carry, especially in large-scale catering or buffet settings where trays are constantly moved and filled with food. Manufacturers are likely to adopt advanced CAD (computer-aided design) software to develop trays that optimize balance and user comfort while maintaining the necessary strength to hold food without bending.
Another area of development will be the integration of multi-functional designs. Buffet trays of the future could feature built-in components like modular sections that allow different types of food to be served in separate compartments. This would help organize food more effectively and prevent cross-contamination of items, especially in settings with dietary restrictions or a variety of food types. Additionally, trays could include removable inserts or lids that can be easily swapped out to accommodate different types of food, making them versatile for various buffet setups.
The foodservice industry’s demand for high-quality, durable trays is pushing manufacturers to use more advanced alloys and composite materials that provide even greater strength and resistance to wear and tear. Stainless steel alloys that are reinforced with materials such as titanium or nickel could offer even better corrosion resistance and improved longevity, especially in environments that involve frequent washing and exposure to acidic foods. These hybrid materials would be ideal for buffet trays that need to withstand a lot of handling and maintain their appearance over time.
Furthermore, the trend toward smart manufacturing will continue to shape the production of sheet metal buffet trays. With IoT-enabled machines, manufacturers can monitor equipment performance in real-time, track inventory, and even adjust production schedules to optimize efficiency. Real-time data collection could help identify potential problems early, such as machine malfunctions, and allow for preventive maintenance, reducing the risk of production delays. By integrating these smart technologies into production lines, manufacturers can improve their lead times, maintain high levels of quality, and increase overall output without sacrificing precision.
As manufacturers strive for greater energy efficiency in their operations, they will explore alternative power sources like solar or wind energy to reduce the environmental impact of their factories. The trend towards renewable energy adoption is becoming more prevalent in manufacturing industries, and solar-powered factories or energy-efficient machinery will likely be part of the future of buffet tray production. Additionally, energy recovery systems, such as heat exchangers or regenerative braking systems, may be incorporated into machines to reduce overall energy consumption during production, leading to significant cost savings and more sustainable practices.
The growing consumer preference for sustainable and eco-friendly products will also influence how buffet trays are manufactured. As the foodservice and hospitality industries are increasingly focused on reducing waste, companies producing buffet trays will explore innovative ways to make their products more eco-conscious. For example, trays could be designed for easy disassembly to facilitate recycling after their useful life. Manufacturers might also investigate the use of biodegradable coatings or other materials that can help reduce the environmental impact of their products.
Another significant area of growth for buffet tray manufacturers is in emerging markets. As disposable incomes rise in countries across Africa, Asia, and South America, the demand for high-quality buffet trays will increase, especially in hotel chains, resorts, and catering businesses. These regions are experiencing significant urbanization, and with it, a growing middle class that values convenience, quality, and functionality in the products they purchase. Manufacturers who can adapt to these markets by offering cost-effective, high-quality buffet trays will be well-positioned to capture this expanding customer base.
Lastly, customization will continue to be a significant driver of growth in the buffet tray market. Beyond simple engraving and logo placement, manufacturers will likely explore more intricate and personalized options, such as unique pattern designs or even trays that reflect specific cultural motifs. This could be a key selling point for businesses looking to create a memorable dining experience for their customers. For example, bespoke buffet trays for wedding events or corporate parties may be designed with customized finishes, logos, and other personalized features that reflect the theme or branding of the event. This kind of flexibility can create a competitive edge for manufacturers that offer a high level of customization.
In conclusion, the future of sheet metal buffet tray production will be shaped by advancements in design, materials, automation, and sustainability. As consumer preferences evolve and the foodservice industry grows, manufacturers will need to stay ahead of trends by creating innovative, functional, and environmentally friendly products. Automation and smart manufacturing will play a key role in improving efficiency and precision, while customization and ergonomics will cater to the specific needs of modern consumers. The combination of technology, design, and sustainability will drive the future of buffet tray production, ensuring that these products continue to meet the demands of both commercial and residential customers worldwide.
As we look deeper into the future of sheet metal buffet tray production, there are several other aspects that will play a significant role in shaping the industry and its operations. These factors extend beyond material innovation and smart manufacturing to include broader trends that reflect both technological advancement and changing consumer behavior.
One of the key technological innovations that will impact buffet tray production is 3D metal printing. While still in its early stages for mass production, 3D printing technology is becoming increasingly important in industries like aerospace and automotive, and its applications are now expanding to metal fabrication for more intricate and customized product designs. Manufacturers may eventually adopt additive manufacturing methods for creating highly complex tray designs, including those with built-in features like compartments or integrated heating elements. This approach could allow for hyper-customization of buffet trays, where consumers can request specialized designs that might have been difficult or cost-prohibitive with traditional manufacturing techniques.
Furthermore, artificial intelligence (AI) and machine learning will continue to advance within production environments. AI systems could be employed to analyze the performance and efficiency of each production line in real-time, adjusting processes to improve yield and minimize defects. This predictive capability extends to maintenance schedules as well, where AI can foresee potential equipment failures based on machine data, preventing unscheduled downtime. Machine learning could also aid in optimizing the design of trays by analyzing customer feedback and market trends, leading to products that are not only more functional but more aligned with current consumer desires.
Robotic automation is already widely used in manufacturing, but it will become even more sophisticated. Robots could perform tasks like precision welding, automated polishing, and even inspection of trays for imperfections. Collaborative robots (cobots) could work alongside human operators in the production line, offering flexibility and improving efficiency without the need for extensive reconfiguration of the factory floor. As the technology matures, robotic systems will be capable of handling more delicate operations, such as the placement of handles, custom engravings, or the final finishing touches that require a human touch but with greater speed and accuracy.
Another aspect that will influence the future of buffet tray production is the increasing demand for sustainability throughout the supply chain. Consumers, as well as businesses, are becoming more conscious of the environmental impacts of their purchases. This demand for sustainability will push manufacturers to seek green certifications and reduce their carbon footprints. For example, producers may opt for recycled metals in the production process, using materials that are not only environmentally friendly but also cost-effective. Closed-loop recycling systems can be implemented to ensure that scrap metal and waste from the production process are repurposed for new products, reducing waste sent to landfills.
Additionally, there is an increasing push for zero-waste manufacturing. By adopting methods such as lean manufacturing or just-in-time production, manufacturers can optimize their use of materials, reducing waste and conserving resources. These practices not only contribute to sustainability but can also help reduce costs, making it a win-win for both the environment and the bottom line. Manufacturers that emphasize these principles may appeal to environmentally conscious consumers and businesses that are prioritizing eco-friendly practices.
The ongoing digitalization of the manufacturing industry is also expected to have a profound impact on buffet tray production. Digital twins, which are virtual replicas of physical assets, will allow manufacturers to simulate the production process, monitor tray designs, and test for potential weaknesses before physically producing the trays. This digital innovation not only saves time and reduces errors but also allows for continuous improvement in the design and manufacturing process.
The Internet of Things (IoT) will also play a larger role in optimizing production. With IoT sensors embedded in equipment and materials, real-time data can be collected and used to monitor production conditions like temperature, humidity, and machine performance. This will help ensure that trays are made under optimal conditions, and any adjustments can be made on the fly to avoid defects. It will also enable manufacturers to monitor the efficiency of each production line, reducing bottlenecks and ensuring a steady output of products.
The impact of consumer behavior will remain a critical driver of change. The rise of online shopping and direct-to-consumer sales channels means that manufacturers will need to cater to a growing demand for personalized products. Custom buffet trays can be designed based on specific consumer needs, including design features like engravings, logos, or unique patterns. Moreover, as more consumers opt for eco-conscious or health-conscious food choices, manufacturers may begin to incorporate design features that support these trends, such as compartments for different types of foods or features that help keep hot foods warm and cold foods chilled, appealing to the needs of a modern, health-aware market.
The rise of globalization and the increasing popularity of destination dining experiences also presents opportunities for buffet tray manufacturers. High-end hotels, resorts, and cruise lines are constantly looking for ways to enhance the dining experience. This presents a niche market for bespoke buffet trays, which could be designed to reflect the destination or theme of the dining experience. For example, trays used in beachfront resorts may have unique features or finishes that complement the tropical setting, or luxury cruises may require trays with elegant, high-end finishes to suit their upscale clientele.
Lastly, regulatory standards surrounding food safety and hygiene will continue to evolve. Trays made from non-toxic materials, with antimicrobial finishes, could become more prevalent, especially as health and food safety concerns grow. Manufacturers may need to comply with more stringent regulations in terms of the materials used in food contact surfaces and the types of coatings applied to these surfaces. Keeping pace with these regulations will ensure that buffet trays remain safe, durable, and effective for use in foodservice environments.
In summary, the future of sheet metal buffet tray production will be shaped by continued advancements in technology, material science, and consumer preferences. The incorporation of 3D printing, AI, robotic automation, and sustainability into manufacturing processes will make production faster, more efficient, and more environmentally friendly. At the same time, customization, smart features, and ergonomics will cater to the evolving needs of consumers and businesses. As the global market for buffet trays continues to grow, manufacturers will need to stay agile and innovative to remain competitive in an increasingly demanding marketplace.
The production of sheet metal serving trays involves a highly specialized manufacturing process, combining several stages of metalworking to create functional, durable, and aesthetically pleasing products. Sheet metal serving trays are widely used in various industries, particularly in the hospitality, restaurant, and catering sectors, and their production process involves key stages such as material preparation, cutting, forming, finishing, and packaging. Here is a breakdown of the production process for sheet metal serving trays.
1. Material Selection and Preparation
The first step in manufacturing sheet metal serving trays is selecting the appropriate type of metal. Stainless steel, aluminum, and carbon steel are the most common materials used due to their durability, resistance to corrosion, and ease of cleaning. Stainless steel is particularly popular for its resistance to staining and rust, making it ideal for use in environments where the tray will be exposed to moisture and food acids.
- The selected metal is supplied in rolls or sheets, which are of the correct thickness for the trays.
- The metal is then checked for quality, ensuring that there are no defects such as warping, uneven thickness, or surface blemishes.
- Coil slitting may be done if the material is in a coil form to ensure the correct dimensions for the trays.
2. Cutting the Metal
Once the material is prepared, the next step is to cut it into the appropriate shape for the tray. There are several methods that can be used, depending on the design requirements and material type:
- Laser cutting: A highly accurate method where a laser beam is used to cut the metal into the desired shape. Laser cutting ensures precise dimensions and smooth edges, reducing the need for additional finishing work.
- Shearing: A mechanical process where a straight blade cuts the metal sheet into the desired shape. This method is commonly used for simpler tray designs.
- Water jet cutting: Uses high-pressure water mixed with abrasive particles to cut the sheet metal. Water jet cutting is often used for materials that are difficult to cut with other methods and provides a high level of precision.
3. Forming and Shaping
After the tray has been cut to the correct dimensions, it is shaped to its final form. Deep drawing or press forming is typically used to shape the tray. These processes involve pressing the metal into molds to form the desired geometry.
- Deep drawing: This is the primary method used to create trays with deeper shapes or sides, like a round tray or rectangular tray. In this process, the sheet metal is placed in a die, and a punch presses the metal down to form the sides of the tray. The process is repeated if necessary to achieve the desired depth and shape.
- Bending and folding: For simpler tray designs or trays with shallow edges, bending or folding machines are used to form the sides of the tray at a consistent angle.
4. Edge Treatment and Reinforcement
After the tray is formed, attention is given to the edges. Sheet metal edges can be sharp after cutting and forming, which can make handling the tray difficult or unsafe.
- Edge trimming: The sharp edges are smoothed and trimmed using grinders or burr-removal machines to ensure that the tray is safe to handle.
- Reinforcement of edges: Some trays may require additional support around the edges, such as adding a rolled edge for reinforcement. This is particularly common in large serving trays that need extra strength.
5. Surface Treatment and Finishing
The next stage is surface finishing, which not only enhances the appearance of the tray but also adds durability. Several treatments can be applied depending on the aesthetic or functional requirements of the tray:
- Polishing: Trays made of stainless steel or aluminum are often polished to give them a shiny, reflective surface. This can be done using specialized polishing machines or abrasive pads.
- Brushing: For a matte, non-reflective finish, brushing is applied. This is done by passing the metal surface under a rotating wire brush or abrasive pad.
- Powder coating: If the tray needs a colored finish, powder coating can be applied. This method involves spraying a fine powder onto the tray’s surface, which is then cured in an oven to create a durable, smooth, and colorful finish.
- Electroplating: In some cases, trays may be electroplated with a thin layer of another metal, like chrome, for additional durability and aesthetic appeal.
6. Assembly and Customization
For trays that include handles, branding, or other custom features, this is where assembly comes in. Handles may be attached by welding, riveting, or screwing, depending on the design requirements.
- Handle placement: Handles are typically positioned on the sides of the tray for ease of transport. The material and design of the handle are chosen based on the weight capacity of the tray and aesthetic preferences.
- Custom branding: Some manufacturers provide engraving or embossing services to add logos or branding to the tray. This can be done using laser engraving or stamp pressing to create permanent markings on the surface.
7. Quality Control
Before the trays are packed and shipped, each one undergoes a thorough quality control inspection to ensure that it meets the necessary standards for durability, finish, and function. This typically includes:
- Dimensional checks: Ensuring that each tray meets the specified dimensions, including checking the flatness, depth, and shape.
- Surface inspection: Checking for any defects such as scratches, dents, or inconsistencies in the finish.
- Strength tests: Some trays, especially larger ones, may undergo strength testing to ensure they can handle the weight of food and other items without warping or breaking.
8. Packaging and Shipping
After passing quality control, the trays are carefully packaged to prevent damage during transport. This often involves:
- Protective packaging: Trays are often wrapped in foam or bubble wrap and placed in cardboard boxes or custom-designed packaging to prevent scratches and dents.
- Bulk packaging: Depending on the order, trays may be packed in sets or stacks, especially for large commercial orders.
- Shipping: Once packaged, trays are labeled and prepared for shipping, either through direct-to-consumer channels or to wholesalers or retailers.
Automation in Production
To increase efficiency, many sheet metal serving tray production facilities are moving towards automation. Robotic arms and automated loading/unloading systems are often used to handle the raw material, move parts through the production line, and even handle finished trays. Automated systems for quality inspection using cameras or machine vision technology can quickly detect flaws in trays, improving the precision and speed of the production process.
Future Trends in Sheet Metal Serving Tray Production
- Smart features: As demand for smart products grows, future serving trays may incorporate built-in sensors to monitor the temperature of food or include LED lights for visual appeal.
- Sustainability: There will likely be a greater emphasis on producing trays from recycled metals or using eco-friendly coatings.
- Customization: Advances in 3D printing may allow for more intricate designs and personalized serving trays, catering to specific consumer preferences or branding requirements.
In conclusion, sheet metal serving tray production is a complex process that involves multiple stages, from material selection to finishing and packaging. The use of advanced manufacturing technologies, such as laser cutting, press forming, and robotic automation, ensures that these trays meet the demanding standards of durability and functionality expected in the foodservice and hospitality industries. As trends towards sustainability, smart products, and customization continue to rise, manufacturers will need to adapt to meet the evolving needs of consumers and businesses.
As the sheet metal tray production industry continues to evolve, innovation in both manufacturing processes and materials will remain crucial. One of the most significant shifts expected in the industry is the increased integration of advanced robotics and automation throughout the production line. Automated systems can dramatically increase efficiency and consistency, especially in tasks like material handling, welding, and finishing. These systems also reduce human error, resulting in higher-quality products that require less rework.
The evolution of materials is another area of focus for future production. Manufacturers are increasingly turning to alloyed metals that combine the benefits of traditional materials like stainless steel and aluminum with enhanced properties such as greater strength, lighter weight, and resistance to corrosion. The development of these hybrid materials can offer even greater durability and performance in environments where serving trays are subjected to frequent handling and exposure to high temperatures.
3D metal printing is another innovation that is beginning to reshape the production landscape. While still in its early stages, this technology holds the potential to allow for the creation of more complex and customizable designs that would have been difficult or impossible to achieve with traditional metalworking techniques. 3D printing allows manufacturers to create trays with intricate patterns, shapes, or features that were previously too costly or time-consuming to produce.
Beyond the manufacturing floor, the sustainability of production practices will continue to be a priority. Manufacturers are already seeking ways to reduce their carbon footprint by using recycled metals in production and optimizing their energy consumption during the manufacturing process. Advances in renewable energy sources like solar and wind power will likely be incorporated into production lines, particularly as consumer demand for environmentally responsible products grows.
The growing demand for customization in the foodservice and hospitality industries will also drive changes in the production of sheet metal trays. More businesses are looking to create unique, brand-specific products that reflect their identity, whether through custom logos, colors, or even tray shapes and sizes. To meet this demand, manufacturers will increasingly offer personalized options, using techniques such as laser engraving and embossing to add logos or unique designs to trays. Additionally, advancements in laser cutting and water jet cutting will allow for intricate, detailed designs that can be tailored to specific customer needs.
As the global economy becomes more interconnected, the demand for sheet metal trays is expected to grow, especially in emerging markets. As urbanization increases in regions like Asia, Africa, and Latin America, the demand for high-quality foodservice products, including buffet trays, is rising. Manufacturers will need to meet these demands by expanding their production capabilities, exploring local supply chains, and designing products that are tailored to regional preferences and price points.
In the future, the digitalization of manufacturing will continue to advance, allowing for more seamless integration of technology throughout the production process. Tools like IoT (Internet of Things) devices will enable manufacturers to monitor machine performance in real-time, while cloud-based systems will provide greater visibility into the entire production chain, improving collaboration, data analysis, and supply chain management. This digital transformation will also contribute to faster, more responsive production cycles, allowing manufacturers to meet customer demands more efficiently.
With the increasing focus on health and safety in foodservice environments, there may also be growing interest in antimicrobial coatings for sheet metal trays. These coatings could help reduce the spread of germs and bacteria, particularly in environments like restaurants, catering services, and healthcare facilities. Manufacturers may need to adapt their designs to incorporate these features, ensuring that their trays not only look good and perform well but also meet stringent health regulations.
Lastly, as consumer behavior continues to evolve, the overall aesthetics of sheet metal trays may become more important. Customers may increasingly seek trays that reflect their personal style or the theme of their events. Manufacturers will likely respond to this by offering a wider range of finishes, from sleek, modern designs to vintage or rustic looks that appeal to different consumer tastes. Additionally, eco-friendly finishes, like natural patinas or bio-based coatings, will become more desirable as consumers become more concerned with the environmental impact of their purchases.
As the sheet metal tray production industry moves forward, it will continue to innovate in design, materials, and manufacturing techniques, driven by advances in technology, changes in consumer preferences, and the growing demand for sustainability. The future of production in this sector looks bright, with opportunities to create products that are more functional, customizable, eco-friendly, and cost-effective than ever before. By embracing these trends, manufacturers will be well-positioned to meet the needs of an increasingly diverse and demanding marketplace.
The sheet metal tray production industry will increasingly focus on adopting smart manufacturing technologies. This includes the integration of artificial intelligence (AI) and machine learning (ML) to improve various aspects of production, from design to quality control. AI algorithms can analyze vast amounts of production data in real-time to optimize manufacturing processes, detect potential issues before they occur, and improve product consistency. AI can also be used to predict maintenance needs for machinery, preventing unexpected downtimes and reducing repair costs.
In addition to AI, the rise of augmented reality (AR) and virtual reality (VR) technologies could transform the way designers, engineers, and production teams collaborate. These tools could be used for product prototyping, allowing designers to visualize tray designs in 3D before creating physical prototypes. VR can also help train workers, allowing them to experience simulated environments and processes without risk or cost. This can be particularly useful for complex tasks like metal forming or quality inspection, where skill and precision are crucial.
Another trend that will likely shape the future of sheet metal tray production is advanced welding and joining techniques. The continued development of technologies like laser welding and ultrasonic welding offers the potential to create stronger, more reliable joints in tray components. These methods reduce the risk of defects while also increasing the speed of production. Laser welding, for instance, can precisely control heat input, minimizing warping and ensuring a consistent seam, which is critical for the durability and safety of trays.
The growing emphasis on sustainability will also encourage manufacturers to explore biodegradable and non-toxic coatings for sheet metal trays, especially for food-related applications. Materials such as biodegradable plastics or plant-based coatings could be applied to reduce environmental impact without compromising the tray’s function. Innovations in green chemistry may enable manufacturers to create coatings that are both safe for food contact and eco-friendly, appealing to the growing market of environmentally conscious consumers.
Manufacturers will also need to stay ahead of changing regulations related to product safety, especially as international markets become more interconnected. These regulations often govern materials used in food-related products, including metals, coatings, and finishes. Manufacturers will need to keep track of evolving standards and adapt their processes accordingly. This could include compliance with FDA and EU regulations on food contact materials, which could involve testing and certification to ensure the safety of the products.
With more people seeking personalized and unique products, sheet metal tray production is likely to see an increase in demand for limited-edition or bespoke designs. This could involve offering special finishes, customized engravings, or even entirely personalized shapes to match specific themes or branding. The flexibility of automated laser engraving or water jet cutting technologies will make it easier to offer these customizations on a larger scale, making the manufacturing process adaptable to small batch production and individual customer requests.
The global supply chain is also a crucial factor in the future of sheet metal tray production. Manufacturers will need to optimize their sourcing strategies to mitigate risks posed by global disruptions, such as natural disasters or geopolitical tensions. This may involve developing more local supply chains or sourcing from multiple suppliers to ensure a steady supply of materials. Additionally, with the increasing popularity of online retail, manufacturers will need to consider direct-to-consumer models or improve logistics to meet the growing demand for fast delivery.
One of the more promising developments in the sheet metal tray production industry is the move toward smart products. As technology continues to evolve, trays may be designed with built-in sensors to monitor temperature, humidity, or other environmental factors. For example, insulated trays with temperature sensors could alert catering services if food is getting too cold or too hot, improving food safety standards and making the dining experience more efficient. These smart features will become especially appealing in settings like luxury hotels, restaurants, or catering events where food quality and temperature are critical.
The consumer-driven trend of minimalism and sleek, modern design will continue to influence tray aesthetics. Trays that are lightweight, easy to handle, and feature smooth, minimalist lines will gain popularity. The use of fine-grade materials like brushed stainless steel or anodized aluminum, which have both functional and aesthetic benefits, will likely increase. Additionally, the rise of multi-functional trays that can be used for various purposes (serving, storage, display) will push manufacturers to develop more versatile products that can be used in a variety of settings.
As the foodservice industry becomes more globalized, catering to diverse cultural preferences and practices will become a key focus for manufacturers. Sheet metal trays may need to accommodate various types of cuisine or presentation styles, which could lead to specialized designs catering to specific food cultures or events. For example, trays designed for buffets might feature modular compartments, while trays intended for picnics or barbecues may require designs that are durable and portable.
The increase in automation and the focus on lean manufacturing will also lead to faster production times, allowing manufacturers to produce trays more efficiently and at a lower cost. By minimizing waste, optimizing labor usage, and reducing energy consumption, manufacturers can pass on cost savings to consumers while maintaining high product quality. These operational improvements will make sheet metal trays more affordable for a wider range of consumers, from small restaurants to large-scale catering services.
In terms of quality assurance, the continued development of non-destructive testing (NDT) technologies will enable manufacturers to inspect their trays for flaws without compromising their integrity. Techniques such as ultrasonic testing, X-ray inspection, and eddy current testing will help detect defects like cracks, voids, or weak points in the metal. This ensures that trays meet safety and durability standards, even before they undergo final finishing processes.
As the industry moves forward, the production of sheet metal trays will increasingly emphasize a balance between innovation, quality, sustainability, and cost-effectiveness. Manufacturers will need to remain agile, embracing new technologies, responding to changing consumer demands, and staying ahead of regulatory changes. The result will be a diverse range of trays that meet the needs of consumers, caterers, restaurants, and foodservice providers, all while reducing environmental impact and improving efficiency throughout the production process. The future of sheet metal tray production looks promising, with new advancements ensuring that these products will continue to evolve and thrive in an ever-changing marketplace.
As the sheet metal tray production industry advances, the integration of sustainability practices and eco-conscious manufacturing processes will be central to its future development. Consumers are increasingly aware of the environmental impact of their purchases, and as such, manufacturers are looking for ways to reduce the carbon footprint of their products. The use of recycled metals will become even more common as the industry embraces the circular economy, which emphasizes reusing materials rather than discarding them. The adoption of closed-loop recycling systems, where used products can be returned, melted down, and reprocessed into new trays, will further enhance sustainability.
In addition to using recycled materials, manufacturers will seek ways to optimize energy consumption throughout the production process. Energy-efficient machinery, smart automation systems, and renewable energy sources like solar and wind will likely be incorporated into production lines. These steps not only help to reduce energy usage but also align with the growing push towards green manufacturing that minimizes environmental impact across the supply chain.
The future of sheet metal tray production will also see a shift towards smart production systems, where machines are connected via the Internet of Things (IoT) to allow for real-time monitoring and optimization. Sensors embedded in machines can detect anomalies, such as a dip in performance or signs of wear, allowing operators to conduct predictive maintenance before any failure occurs. This reduces downtime, improves production efficiency, and helps extend the life of expensive manufacturing equipment. Furthermore, data analytics can be used to assess production efficiency and identify areas for improvement, leading to better decision-making and cost savings.
As global supply chains become more complex, manufacturers will need to adapt to a changing landscape by implementing more flexible and adaptive supply chain strategies. This could involve partnering with suppliers in various regions to diversify sources of raw materials, reducing dependence on any one market. To mitigate risks associated with disruptions in global trade, manufacturers may look to nearshoring or onshoring, moving parts of the production process closer to key markets or building regional manufacturing hubs.
Another trend driving innovation in tray production will be the integration of customization technologies. While automation and mass production have traditionally been focused on producing standard trays in high volumes, demand for personalized or uniquely designed products is growing. Advanced techniques like 3D printing could enable the creation of bespoke tray designs for small-scale orders, allowing manufacturers to cater to niche markets, such as high-end restaurants, luxury hotels, and events that require unique designs. 3D printing could also allow for rapid prototyping, enabling manufacturers to test new tray designs without investing in costly molds or tooling.
Alongside customization, branding and personalization will continue to be important. Trays are often used in environments where presentation matters—whether in restaurants, catering services, or hotels—so creating trays with personalized logos or designs will appeal to businesses looking to strengthen their brand identity. Techniques such as laser engraving and screen printing will enable manufacturers to offer custom designs at a relatively low cost, even for small orders. These personalized touches could be applied to handles, tray bottoms, or the edges of the trays, making them an excellent choice for businesses looking to stand out.
The emphasis on health and safety in foodservice environments will also influence tray designs and materials. There will likely be a growing demand for trays with built-in antibacterial properties or coatings that prevent the growth of harmful microorganisms. Manufacturers may incorporate nano-coatings or other advanced materials to make trays more resistant to bacteria, mold, and mildew. This feature would be especially important in environments where trays are frequently exposed to food, moisture, and high temperatures.
In line with the trend toward health-consciousness, there may also be a push for eco-friendly finishes, such as water-based paints or natural wax coatings, which are safer for both consumers and the environment. Trays could also be designed with more ergonomic features, such as contoured handles or lightweight materials, making them easier to carry and reducing strain on workers in busy foodservice environments.
Another exciting area of development is the use of biodegradable or compostable materials. While still relatively new to the sheet metal industry, manufacturers are experimenting with alternative materials such as bioplastics or composite materials that can mimic the properties of metal trays while offering a more sustainable option. These materials may be ideal for disposable trays used in catering events or fast food services, where single-use products are common. By investing in alternative materials, manufacturers can meet the growing demand for environmentally friendly products while still delivering the durability and performance that sheet metal trays are known for.
Manufacturers will also continue to explore the potential of multi-functional designs that serve more than one purpose. For example, serving trays with detachable compartments that can be used separately, or trays with built-in cooling or heating elements, could meet a broader range of consumer needs. Trays designed with stackability in mind may also become more popular, especially in environments where space is limited, and efficient storage is a key consideration.
The industry will also see more emphasis on quality control through advanced techniques such as machine vision systems and AI-driven inspection systems. These systems can automatically detect defects, such as scratches, dents, or inconsistencies in the tray’s finish, before the products move further down the production line. Automated inspection can catch issues that may be invisible to the human eye, ensuring that only the highest-quality products reach customers.
To ensure compliance with increasingly stringent food safety regulations, manufacturers will also need to stay up-to-date with industry standards. For instance, in the U.S., FDA regulations on food-grade materials are continuously updated, and manufacturers will need to ensure that their trays meet these requirements for safe food contact. Similarly, in Europe, manufacturers must comply with EU regulations for food safety, which could influence material choices and coating processes. International certification may become more important, and certifications such as ISO 9001 (Quality Management Systems) and ISO 14001 (Environmental Management) will likely become more common in the industry.
With technological advancements and demand for diverse products driving the future of sheet metal tray production, manufacturers will need to remain innovative. Staying ahead of consumer trends, integrating sustainability in design and production, and enhancing product quality through new technologies will help manufacturers navigate the competitive landscape. By embracing these opportunities, the industry will continue to produce functional, customizable, and eco-friendly trays that serve a variety of purposes in homes, restaurants, hotels, and catering services worldwide.
As consumer demand for aesthetics, functionality, and sustainability grows, the tray production industry will be well-positioned to meet these evolving needs. Whether through smart features, customization options, or environmentally friendly innovations, sheet metal trays will continue to play a critical role in the foodservice sector and beyond, offering an ever-expanding array of designs and functionalities to suit a diverse range of applications.
EMS Metalworking Machines
We design, manufacture and assembly metalworking machinery such as:
- Hydraulic transfer press
- Glass mosaic press
- Hydraulic deep drawing press
- Casting press
- Hydraulic cold forming press
- Hydroforming press
- Composite press
- Silicone rubber moulding press
- Brake pad press
- Melamine press
- SMC & BMC Press
- Labrotaroy press
- Edge cutting trimming machine
- Edge curling machine
- Trimming beading machine
- Trimming joggling machine
- Cookware production line
- Pipe bending machine
- Profile bending machine
- Bandsaw for metal
- Cylindrical welding machine
- Horizontal pres and cookware
- Kitchenware, hotelware
- Bakeware and cuttlery production machinery
as a complete line as well as an individual machine such as:
- Edge cutting trimming beading machines
- Polishing and grinding machines for pot and pans
- Hydraulic drawing presses
- Circle blanking machines
- Riveting machine
- Hole punching machines
- Press feeding machine
You can check our machinery at work at: EMS Metalworking Machinery – YouTube
Applications:
Flange-punching
Beading and ribbing
Flanging
Trimming
Curling
Lock-seaming
Ribbing