Thread Tapping Machine for Aluminium and Cast Iron Radiators: A thread tapping machine used for radiators is a specialized piece of machinery designed for creating internal threads in metal components, primarily for radiator fittings, which require precision and durability. These machines are integral in radiator manufacturing, as they allow for the efficient threading of holes where fittings such as valves, thermostats, or pipe connections are installed. Radiators often have threads on their inlet and outlet ports, and these threads must be accurate to ensure a leak-free and secure connection when attached to heating systems.
Key Features and Components of a Thread Tapping Machine for Radiators
- Machine Design: The thread tapping machine for radiators is typically designed to accommodate a wide variety of radiator materials, including steel, aluminum, and brass. The machine needs to be robust enough to handle the often high-pressure requirements of heating systems while being versatile enough to tap different sizes of threads for various fittings.
- Tapping Mechanism: The core function of a tapping machine is to insert a rotating tool (the tap) into a pre-drilled hole in the radiator. The tap is designed to cut internal threads into the hole. The tapping machine controls the speed, feed rate, and depth of the tap to ensure consistent and accurate threads.
- Tooling: Radiator threading generally requires specific taps, such as spiral-point taps, which are designed for rapid chip removal and to prevent clogging. The tools must also be durable and resistant to wear, as the radiator materials are often tough and require significant force to thread.
- Automation: Modern thread tapping machines used for radiators are often automated or semi-automated. This helps increase production efficiency and reduce human error. Automation can include robotic arms for loading and unloading the radiators, sensors for alignment, and control systems that monitor the tapping process to ensure quality consistency.
- Speed and Precision: Thread tapping machines are designed to provide high-speed operation while maintaining precision. This is critical in radiator production, where thousands of units need to be manufactured in a short amount of time without compromising on the quality of the threads. The precision ensures that the radiator fittings align perfectly, preventing leaks and ensuring optimal performance.
- Cooling and Lubrication: Tapping creates friction, which generates heat and can cause the tap to wear down quickly. To prevent this, thread tapping machines for radiators often include an integrated cooling and lubrication system. The system helps dissipate heat and lubricates the tap, allowing for smoother operation and extending the life of the tapping tools.
- Control Systems: Modern thread tapping machines often incorporate advanced control systems, which allow operators to set and adjust parameters such as tapping speed, depth, and the number of threads. These systems can also store different settings for various radiator models, providing flexibility for manufacturers producing a range of radiator types and sizes.
- Quality Control: Thread tapping machines are typically equipped with monitoring tools to ensure the threads are cut to precise specifications. This can include sensors to check thread depth, pitch, and the overall integrity of the threads. Some machines may also use ultrasonic or other non-destructive testing methods to detect any flaws in the threading process.
- Post-Tapping Operations: After tapping, radiators may undergo additional processes to ensure the threads are clean and free from any debris or metal shavings. This can involve cleaning, deburring, or even surface treatments to enhance the quality of the threads and the overall radiator.
Types of Tapping Machines for Radiators
- Vertical Tapping Machines: These machines have a vertical spindle, where the workpiece is placed on a horizontal table. Vertical tapping is common for radiator components that require threading along a fixed, vertical axis.
- Horizontal Tapping Machines: In horizontal tapping machines, the workpiece is positioned horizontally, and the tool moves in a horizontal direction to cut the threads. This is often used when multiple threads need to be cut at once or when working with larger radiator components.
- CNC Tapping Centers: These machines are equipped with CNC (Computer Numerical Control) technology, which allows for precise and programmable threading. CNC tapping machines for radiators are ideal for large-scale production runs where consistency and efficiency are crucial.
Applications in Radiator Manufacturing
Thread tapping machines for radiators are used throughout the production of various types of radiators, such as:
- Steel Panel Radiators: These radiators typically require tapping for the inlet and outlet connections where pipes are attached.
- Cast Iron Radiators: Cast iron radiators may need more robust tapping machines due to the toughness of the material.
- Aluminum Radiators: These radiators are lighter but still require precise threading for the fittings to be installed.
- Towel Radiators: These radiators, which are often used in bathrooms, also require accurate threading for pipe connections and heating elements.
Advantages of Using Thread Tapping Machines in Radiator Production
- Increased Efficiency: Thread tapping machines can operate at high speeds, allowing manufacturers to process large volumes of radiators in less time. This leads to higher output and cost savings in mass production environments.
- Consistency: Automated tapping machines ensure that each radiator component is threaded to the same specifications, reducing the likelihood of defects or issues during installation. This is critical for maintaining product quality and customer satisfaction.
- Cost Savings: While the initial investment in a thread tapping machine can be significant, the long-term savings in labor costs and reduced waste due to errors can be substantial. Automated systems also minimize downtime, keeping production lines running smoothly.
- Customization: For manufacturers who produce a variety of radiator models, tapping machines can be easily adjusted or reprogrammed to accommodate different thread sizes and configurations. This flexibility makes it easier to cater to diverse customer needs.
- Reduced Manual Labor: By automating the tapping process, manufacturers can reduce the amount of manual labor required, allowing workers to focus on other tasks that may require more expertise or inspection.
Conclusion
The use of thread tapping machines in radiator production is essential for ensuring that the radiator components are fitted with precision threads for connecting pipes and valves. These machines enhance efficiency, precision, and quality control in the manufacturing process, helping to meet the high demands of radiator production. By investing in modern, automated tapping machines, manufacturers can improve productivity while maintaining high standards of quality.
Key Features and Components of a Thread Tapping Machine
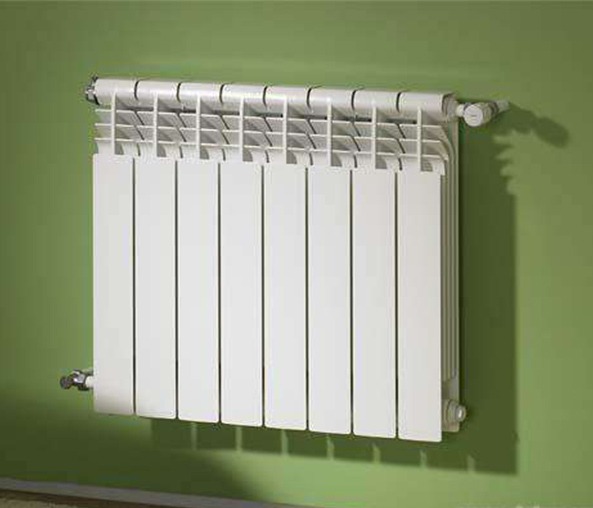
A thread tapping machine for radiators is a specialized piece of machinery used to create internal threads in metal components, which are essential for radiator fittings and connections. Radiators typically require threaded holes for attaching valves, thermostats, or pipe connections, and these threads must be precise to ensure a secure, leak-free fit within the heating system. Thread tapping machines allow manufacturers to efficiently produce these threads with high accuracy, facilitating the assembly of functional and durable radiator systems.
Thread tapping is the process of cutting internal threads into a pre-drilled hole using a rotating tool called a tap. The tap is advanced into the hole under controlled conditions, creating a specific type of thread that allows fittings to be securely screwed into place. Radiators often have threads in the inlet and outlet ports, which connect them to the heating pipes. These threads must meet specific standards in terms of size, pitch, and alignment to ensure compatibility with the pipe fittings and to prevent issues such as leakage or improper sealing.
Thread tapping machines used for radiator production are designed to handle various materials, including steel, aluminum, brass, and sometimes cast iron, which are commonly used in radiator construction. The machine must be sturdy enough to accommodate the strength and resistance of these materials while ensuring that the threads are clean, consistent, and precise. The thread tapping process for radiators also needs to be fast and efficient, as many units must be produced within a short period for high-volume manufacturing.
The tapping process is typically powered by an electric motor that drives the spindle to which the tap is attached. The tap rotates as it advances into the hole, cutting the internal threads with the help of lubrication or cooling fluids to reduce friction and prevent the tap from overheating. The precision of the threads depends on various factors, such as the machine’s speed, the type of tap used, and the material being tapped. The feed rate, or the speed at which the tap moves into the material, is controlled to ensure that the threads are cut to the correct depth and pitch.
Cooling and lubrication play an essential role in the tapping process. As the tap rotates and cuts into the material, it generates heat due to the friction between the tap and the workpiece. This heat can wear down the tap, reduce its lifespan, and affect the quality of the threads. Therefore, tapping machines are often equipped with integrated cooling systems that provide a continuous flow of coolant or lubricant to the cutting area, ensuring that the tap stays cool and the threads are cut smoothly. This helps to improve the efficiency of the machine and extend the life of the tools used in the process.
Automation has become a common feature in modern thread tapping machines. Automated systems help to increase production efficiency by reducing the amount of manual labor required. Automated machines can load and unload radiator components, adjust the tapping speed and feed rate, and monitor the process to ensure consistent quality. These machines may also include sensors that detect any issues with the threading process, such as incorrect thread depth or alignment, and automatically make adjustments to correct the problem. This helps to maintain a high level of precision and consistency, which is crucial for the quality and reliability of the finished radiator.
In addition to automation, many modern tapping machines are controlled by sophisticated computer systems, allowing operators to input precise parameters for different radiator models. These systems can store multiple settings for various thread sizes, depths, and pitches, providing the flexibility to produce a wide range of radiator designs without the need for manual adjustments. This capability is particularly beneficial for manufacturers that produce different types of radiators, as it allows for quick and easy changes between production runs.
Thread tapping machines are essential in producing radiators with threaded connections that meet industry standards. The accuracy and speed of the tapping process help ensure that radiator fittings can be securely attached to the radiator, preventing leaks and ensuring that the radiator performs as expected within the heating system. The machines are capable of working with different materials and thread types, making them versatile tools for radiator manufacturers. Furthermore, the use of automated systems and computer control allows manufacturers to optimize production, reduce labor costs, and increase the overall efficiency of their operations.
The use of thread tapping machines also contributes to the overall quality of the radiators. By ensuring that threads are cut to the correct specifications, manufacturers can reduce the risk of defects and improve the overall functionality of the radiators. Consistent, high-quality threads are essential for the proper functioning of the heating system, as poor-quality threads can lead to issues such as leaks, misalignments, and difficulty in attaching fittings. Therefore, thread tapping machines play a crucial role in ensuring that radiators meet the required performance standards.
As radiator production becomes increasingly automated, thread tapping machines are expected to evolve as well, incorporating more advanced technologies and features. For instance, some machines may integrate artificial intelligence to monitor the tapping process in real-time, identifying potential issues before they become problems. Others may include more sophisticated cooling systems or employ advanced materials for tapping tools to improve the lifespan of the equipment. These advancements will help radiator manufacturers meet the growing demand for high-quality, efficient, and reliable heating solutions.
Overall, thread tapping machines are indispensable for modern radiator manufacturing. They provide the precision, efficiency, and consistency required to produce radiators with reliable threaded connections. By investing in advanced tapping technology, manufacturers can improve their production processes, reduce waste, and ensure that their radiators meet the highest quality standards. The continued development of these machines will further enhance their performance and enable radiator manufacturers to meet the ever-growing demands of the global heating market.
Radiators
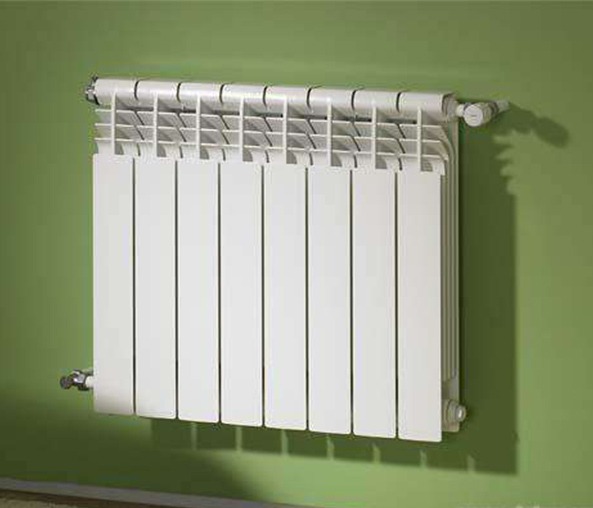
A thread tapping machine is a specialized tool used to create internal threads in metal components, which is particularly crucial for creating the threaded fittings that connect radiators to heating systems. Radiators typically have threaded holes for attaching valves, thermostats, or pipe connections. The process of tapping involves cutting a specific type of thread into a pre-drilled hole using a rotating tool called a tap. This process ensures that the radiator can be securely connected to pipes and fittings without the risk of leaks or poor alignment.
The tapping machine works by driving a tap into a hole, rotating the tool to cut threads as it advances into the material. The precise control over the feed rate and depth ensures that the threads are accurate, uniform, and meet the required specifications. The tap may be cooled and lubricated during the process to reduce friction and prevent overheating, which could cause the tool to wear out prematurely or create imperfect threads. The cooling system helps extend the lifespan of the tapping tools while ensuring that the process remains smooth and efficient.
Thread tapping machines can be automated to improve efficiency, particularly in large-scale production environments. Automation helps reduce the amount of manual labor required, speeds up the production process, and improves the consistency of the final product. Automated systems often include robotic arms for loading and unloading components, sensors to monitor the threading process, and computer control for precise adjustments. These systems ensure that the process remains highly accurate while minimizing the chances of errors or defects.
The use of automation and computer-controlled systems in modern thread tapping machines enables manufacturers to customize the settings for different components. This is particularly useful for companies that produce a variety of metal parts that require threading. The machine can be reprogrammed or adjusted to accommodate different sizes, depths, and types of threads, providing the flexibility to work with various designs. The ability to quickly switch between different production runs makes thread tapping machines an essential tool for manufacturers that produce large quantities of metal parts.
Thread tapping machines are not only efficient but also help improve the overall quality of the parts being produced. By ensuring that threads are cut to the precise specifications, manufacturers can ensure that the fittings and components are correctly aligned, securely attached, and free of defects. This is particularly important in applications such as heating systems, where proper sealing and connection are critical to ensuring safety and functionality. Well-made threads contribute to the durability and reliability of the finished products, which are essential in industries that require high-quality standards.
Thread tapping machines can also be equipped with advanced features such as real-time monitoring and diagnostic systems that can detect any issues during the tapping process. This might include tools for checking the alignment of the tap, monitoring the quality of the threads, or ensuring the correct depth of cut. These features allow operators to address problems before they impact the final product, reducing waste and improving production efficiency.
In addition to their use in large-scale manufacturing, thread tapping machines are also used in various other industries for creating threaded connections in metal parts. They are common in automotive, aerospace, and plumbing industries, as well as in the production of valves, fittings, and other essential components. In all these industries, precision and efficiency are key factors in ensuring that products are functional and meet safety standards.
In summary, thread tapping machines play a critical role in manufacturing threaded components used in various industries. Their ability to cut accurate, high-quality threads quickly and efficiently makes them an invaluable tool in metalworking. With advancements in automation and computer control, these machines continue to evolve, offering manufacturers the ability to produce a wide range of components while maintaining high standards of precision and consistency. The continued development of tapping technology will further enhance manufacturing capabilities and help meet the growing demand for reliable, high-performance parts across many sectors.
Machine Design
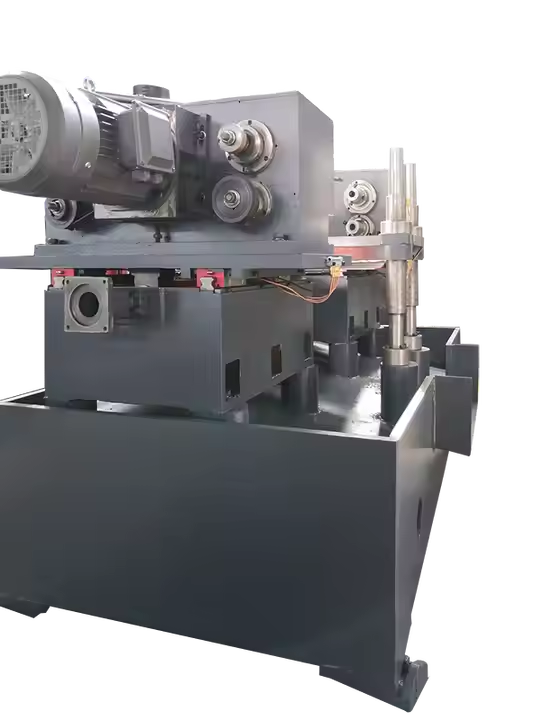
A thread tapping machine for radiator components is built to handle the high demands of threading metal parts with precision and speed. These machines are engineered to cut internal threads into pre-drilled holes, which are essential for securing various radiator fittings such as valves, thermostats, or pipe connections. Thread tapping ensures that these components can be properly connected to a heating system, creating a secure, leak-free bond.
The machine’s main function revolves around driving a rotating tap into the drilled holes in the radiator parts. The tap, which is a specialized tool designed for cutting threads, advances into the hole, gradually creating the internal threads that allow for proper fitting attachment. A precise control system governs the feed rate and depth of the tap’s movement, ensuring that the threads are created with the correct dimensions.
To maintain the quality of the process, thread tapping machines are equipped with mechanisms to reduce friction and heat buildup. When cutting through tough metals like steel, aluminum, or brass, tapping generates significant heat. Without cooling or lubrication, the tap could wear down quickly, affecting the precision of the threads. Therefore, many machines include a cooling or lubrication system that provides a steady flow of fluid to the tap during operation. This helps keep the tapping tool cool and facilitates smoother operation, ultimately improving the longevity of the equipment and ensuring high-quality threads.
Thread tapping machines often feature automated processes to increase production efficiency. With automation, manufacturers can reduce the need for manual labor and speed up the overall process. Robots or conveyor systems are frequently used to load and unload the parts, while sensors monitor the threading process to detect any deviations or errors. These automated systems make the tapping process not only faster but also more consistent, reducing the chances of mistakes that could lead to defective parts.
Advanced control systems allow operators to customize settings based on the size, type, and material of the radiator components being processed. These programmable machines can store multiple settings for different part configurations, making them highly versatile. Operators can easily switch between production runs with minimal downtime, adjusting parameters like feed rate, tap speed, and depth to meet the requirements of each part. This versatility is especially useful for manufacturers producing a variety of radiator models, as the machine can accommodate different thread sizes and configurations without the need for manual adjustments.
The automation and precision built into these machines also contribute to higher-quality results. Consistent, well-formed threads are crucial for ensuring that radiator fittings connect properly, without leaks or misalignment. Poorly threaded holes can result in improper connections, which can lead to functional issues in heating systems. Therefore, ensuring high-quality threads through efficient and precise tapping is critical in radiator manufacturing.
To further improve production efficiency, modern thread tapping machines are also designed to minimize downtime and enhance reliability. They often come equipped with diagnostic tools to detect any mechanical or operational issues before they disrupt the production process. If the machine detects a fault, such as tool wear or misalignment, it can alert the operator, allowing for quick corrections before the issue impacts the final product. This ensures a smooth, continuous production line and reduces the risk of defects.
In addition to providing high-speed and accurate threading, thread tapping machines also play an important role in reducing operational costs. By automating the tapping process, manufacturers can cut down on labor costs and reduce the time required to produce large volumes of parts. The reliability of these machines also decreases the likelihood of production errors, minimizing waste and the need for rework.
In conclusion, thread tapping machines for radiator manufacturing are built with precision, efficiency, and durability in mind. They enable manufacturers to produce high-quality threaded components quickly and consistently, ensuring that radiator fittings are securely attached and function properly within heating systems. With automation, cooling mechanisms, and advanced control systems, these machines continue to play a crucial role in modern radiator production, offering both flexibility and high performance in meeting the demands of the industry.
Tapping Mechanism
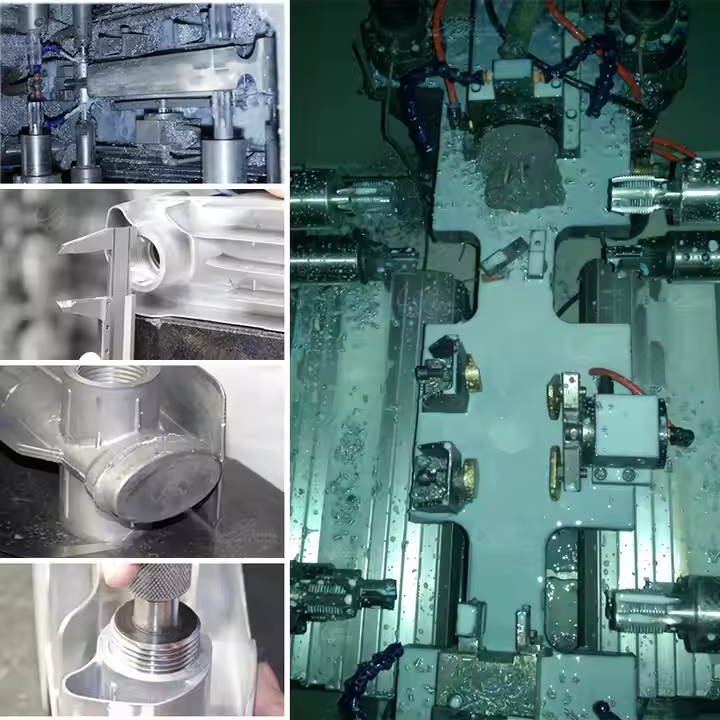
The tapping mechanism in a thread tapping machine is the core system responsible for creating internal threads in the workpiece. This process is essential for manufacturing components with threaded holes, which are required for a variety of industrial applications, including connecting radiator fittings. The mechanism works by rotating a specially designed tool called a tap, which is inserted into a pre-drilled hole. The tap moves into the hole as it rotates, cutting threads into the material to create a clean, accurate interior thread profile.
The tap itself is a cutting tool that has spiral flutes, which are used to remove material from the hole as the tap advances. These flutes also help to channel debris and chips away from the cutting area, preventing them from interfering with the threading process. The speed at which the tap rotates and the force applied to it are carefully controlled to ensure that the threads are cut to the proper depth and pitch. The machine’s control system manages these parameters to ensure consistent results and to avoid damaging the tap or the workpiece.
The tapping process typically involves a rotating motion combined with an axial feed. The tap is fed into the hole at a specific rate, which is called the feed rate. This feed rate is crucial for ensuring that the tap does not cut too deeply or shallowly, creating threads that are either too tight or too loose. The rate at which the tap advances also impacts the quality of the threads, as a slower feed rate may result in cleaner, more precise threads, while a faster rate may generate excess heat and cause the threads to be less accurate.
To avoid issues such as overheating, many thread tapping machines incorporate cooling and lubrication systems. As the tap cuts into the material, friction generates heat, which can wear down the tap and affect the quality of the threads. Cooling systems, often using a flow of oil or coolant, help to reduce this heat buildup, ensuring that the tap remains cool and efficient throughout the operation. This also helps to extend the life of the tap and improve the overall performance of the machine.
In some machines, the tapping mechanism may include automatic reversing capabilities. This feature allows the tap to reverse its direction after it has completed the threading process, which helps to remove the tap from the hole without damaging the threads or the tool. Reversing the tap can also assist in clearing any debris or chips that may have accumulated during the threading process, ensuring that the hole is free of obstructions when the tap is withdrawn.
The tapping mechanism is often integrated with other automated features in modern machines, allowing for faster and more efficient production. For example, robotic systems may be used to load and unload the workpieces, while sensors monitor the tapping process to ensure the correct threading parameters are maintained. The use of such automation reduces the likelihood of errors, enhances precision, and allows for high-volume production without compromising quality.
The ability to adjust the tapping mechanism for different materials and thread specifications is another key feature. Depending on the type of material being tapped, such as steel, aluminum, or brass, the tapping machine can be calibrated to adjust the cutting speed, feed rate, and cooling system to ensure optimal results. This versatility is essential for manufacturers who produce a wide range of components that require threading.
In conclusion, the tapping mechanism in a thread tapping machine is responsible for the creation of precise, uniform threads in metal components. Through careful control of the tap’s rotation, feed rate, and cooling, the mechanism ensures that the threads are cut to the required specifications. With the added benefits of automation, cooling systems, and adjustable settings for different materials, the tapping mechanism is a crucial component in producing high-quality threaded parts efficiently and consistently.
Tooling

Tooling in a thread tapping machine refers to the specialized cutting tools used to create threads within a workpiece. The primary tool in the tapping process is the tap, a precision cutting tool designed to form internal threads by cutting into the material as it rotates and advances into the pre-drilled hole. Taps are typically made of high-speed steel (HSS), carbide, or other durable materials capable of withstanding the forces and heat generated during the tapping process. The design and quality of the tap are critical to achieving accurate and durable threads, as well as to maintaining the efficiency and longevity of the threading operation.
Taps come in various designs, each suited for different types of threading tasks. For general tapping purposes, a spiral-point tap is often used, particularly for through-holes, because its design helps push chips forward as it cuts. This reduces the likelihood of chip clogging and ensures smooth operation. For blind holes, where the hole does not pass all the way through the material, spiral-flute taps are preferred. These taps are designed to draw chips out of the hole and prevent clogging at the bottom of the hole.
Another common tap design is the straight-flute tap, which is typically used for tapping in softer materials or when the threading process needs to be performed more slowly. These taps are often employed for precision applications where smooth, fine threads are necessary. Gun taps are another variation, used for high-speed threading in mass production environments, as they are designed to minimize heat buildup and reduce friction during tapping.
The choice of tap depends on several factors, including the material being threaded, the type of hole (through-hole or blind hole), the size and pitch of the threads, and the required thread quality. Properly selecting the tap material and design ensures that the threading process is efficient, and that the finished threads meet the necessary specifications for strength, durability, and precision.
In addition to the taps, other types of tooling are used to assist in the tapping process. For example, collets and chucks are used to securely hold the tap in place as it rotates. These components ensure that the tap remains aligned with the hole and maintains the correct orientation during the threading process. The use of high-quality holding tools is essential for preventing misalignment, which can result in poor thread quality or damage to the workpiece.
To ensure the tapping process remains smooth and effective, it is also important to have coolant or lubricant systems integrated into the tooling setup. These fluids help reduce friction between the tap and the workpiece, preventing the tap from overheating and extending its lifespan. In high-speed tapping applications, using the right lubrication is crucial for maintaining the performance of the tap and avoiding issues like thread misformation or tap breakage.
For specific applications, dies and threading inserts may also be used in conjunction with taps. Dies are often employed in the final stages of threading to refine the thread surface and ensure uniformity. Threading inserts are sometimes used to replace worn-out tap components, ensuring the machine remains operational without needing to replace the entire tap.
In conclusion, the tooling in a thread tapping machine is fundamental to achieving high-quality, accurate threads. The correct selection of taps and other tooling components—such as collets, chucks, lubricants, and dies—ensures that the tapping process runs efficiently and produces consistent results. Choosing the right tools for the material and thread requirements is essential for ensuring that the threads meet the specifications and performance standards required for the finished product.
Automation
Automation in thread tapping machines significantly enhances production efficiency, precision, and consistency. It involves the use of advanced control systems, sensors, and robotic mechanisms to perform the tapping process with minimal human intervention. Automated thread tapping machines are designed to handle repetitive tasks such as loading and unloading parts, adjusting machine settings, monitoring the tapping process, and even correcting minor errors, which makes them invaluable in high-volume manufacturing environments.
One of the key advantages of automation is the reduction in labor requirements. In traditional manual tapping, operators would be responsible for loading and unloading workpieces, adjusting settings, and overseeing the process. With automation, these tasks are handled by robotic arms or conveyor systems, which can load and position parts quickly and precisely. This reduces the chances of human error, such as improper alignment or incorrect feed rate adjustments, which can negatively impact thread quality.
In addition to robotic loading and unloading, automation systems can adjust the machine’s parameters, such as tapping speed, feed rate, and tool alignment, based on real-time feedback from sensors embedded in the machine. These sensors monitor factors such as the position of the tap, the quality of the threads, and the condition of the cutting tools. If any issues are detected, such as misalignment or tool wear, the system can automatically correct these problems by adjusting settings or alerting the operator. This ensures that the tapping process remains consistent and that high-quality threads are produced throughout the entire production run.
Automated thread tapping machines are often integrated with sophisticated computer numerical control (CNC) systems, which allow for precise control over all aspects of the tapping process. These systems can store multiple settings for different types of threads, materials, and workpieces, making it easy to switch between production runs with minimal downtime. Operators can input specific parameters into the machine’s computer interface, and the system will automatically adjust the machine’s speed, feed rate, and other settings accordingly. This flexibility makes it easier for manufacturers to produce a wide range of parts with varying thread specifications, without requiring manual reconfiguration of the machine.
The integration of automation also improves production speed. Automated machines can operate continuously, with minimal breaks, ensuring that tapping operations are completed at a much faster rate than manual methods. Additionally, the consistency provided by automated systems reduces the need for frequent inspections and rework, further improving the overall efficiency of the production process. This makes automated thread tapping machines especially valuable for manufacturers producing large quantities of parts, as they can maintain high throughput while minimizing the risk of defects.
Another benefit of automation is the ability to gather and analyze data from the tapping process in real time. Modern thread tapping machines can be equipped with diagnostic tools that collect data about the machine’s performance, tool wear, and the quality of the threads being produced. This data can be analyzed to optimize the tapping process, identify trends, and predict when maintenance or tool replacements are needed. By continuously monitoring and adjusting the process, manufacturers can avoid unexpected downtime and improve the overall reliability of the machinery.
In conclusion, automation in thread tapping machines plays a crucial role in improving production efficiency, reducing labor costs, and ensuring consistent, high-quality threads. The integration of robotic loading systems, sensor monitoring, CNC control, and real-time data analysis allows for faster, more accurate tapping processes, making these machines ideal for large-scale manufacturing operations. By reducing human intervention and minimizing the risk of errors, automated thread tapping machines help manufacturers meet the demands for high-quality, precision-threaded components while optimizing their production workflows.
Speed and Precision
Speed and precision are critical factors in the performance of thread tapping machines, particularly when manufacturing components that require high-quality threads. Thread tapping machines are designed to produce threads quickly while maintaining high accuracy, ensuring that the components are functional, durable, and meet stringent industry standards.
Speed in thread tapping refers to the ability of the machine to create threads at a rapid pace without compromising the quality of the threads. Efficient machines are capable of completing a high number of parts within a given period, making them ideal for high-volume manufacturing environments. The speed of the tapping process is influenced by factors such as the tapping tool’s material, the type of machine, and the properties of the workpiece material. Advances in automation and CNC (computer numerical control) systems allow for faster adjustments and smooth transitions between different parts, optimizing the tapping process and reducing downtime.
Precision, on the other hand, ensures that the threads created are within tight tolerances, ensuring that components fit together correctly and function as intended. In industries where threaded components are used for critical applications, such as radiator systems, automotive parts, or aerospace equipment, precise threading is vital to avoid issues like misalignment, leaks, or premature wear. Precision in tapping is achieved through careful control of factors such as the tap’s alignment, feed rate, rotation speed, and depth. Modern thread tapping machines feature automated systems that monitor these variables and adjust them in real time to ensure that the threads meet exact specifications.
The combination of speed and precision makes thread tapping machines highly effective in producing high-quality threaded components quickly and consistently. Automated features, such as robotic loading systems and sensor feedback, further enhance this balance by reducing human error, improving the accuracy of each thread, and optimizing production speed. Additionally, the use of cooling and lubrication systems helps manage the heat generated during tapping, which improves the overall performance of the machine and prolongs the life of the taps, ensuring that the threading process remains efficient and precise over extended production runs.
In conclusion, achieving the right balance of speed and precision in thread tapping is essential for ensuring that components are produced quickly while maintaining the quality and functionality required. Modern tapping machines, with their advanced automation and control systems, allow manufacturers to achieve high throughput without sacrificing the accuracy and integrity of the threads. This combination of efficiency and accuracy makes thread tapping machines an indispensable tool in high-volume manufacturing environments, where the demand for consistent and reliable threaded components is critical.
Cooling and Lubrication
Cooling and lubrication are essential aspects of the thread tapping process, particularly when working with hard materials or performing high-speed tapping. These systems help to reduce friction, prevent overheating, and extend the life of the tapping tools, ensuring that the tapping operation runs smoothly and efficiently.
During the tapping process, friction between the tap and the workpiece generates heat, which can cause the tapping tool to wear down more quickly, reduce the quality of the threads, and even cause the workpiece to become damaged. Cooling systems are used to mitigate this heat buildup by circulating coolant or oil around the tap and workpiece. This helps to lower the temperature, allowing the tap to cut through the material more effectively while reducing the risk of thermal damage. The coolant also helps to carry away the chips produced during tapping, preventing them from clogging the flutes of the tap or interfering with the cutting process.
Lubrication, in addition to cooling, plays a critical role in reducing friction between the tap and the material being tapped. A lubricant helps the tap move smoothly through the hole, reducing the chances of wear and tear on both the tool and the workpiece. Proper lubrication is especially important when tapping harder materials, such as steel or titanium, where the friction during cutting is more pronounced. The lubricant also helps prevent the tap from seizing or binding in the hole, ensuring that the threading process remains continuous and efficient.
Both cooling and lubrication can be delivered through different systems depending on the type of tapping machine. For instance, some machines use a flood coolant system, where coolant is continuously sprayed or poured over the cutting area. Others might use a mist or aerosol coolant system that delivers a fine spray of lubricant or coolant directly to the tap and the workpiece. In some cases, especially in high-speed operations, the coolant may be delivered through the tap itself, ensuring that the cutting area remains cool and well-lubricated throughout the process.
The proper selection of cooling and lubrication fluids is also critical. Coolants and lubricants must be chosen based on the material being tapped and the type of tap being used. For example, synthetic or semi-synthetic coolants are often used for tapping operations involving metals like aluminum or steel, while oil-based lubricants might be preferred for harder materials. The right fluid ensures effective cooling, lubrication, and chip removal, all of which contribute to the success of the tapping process.
In conclusion, cooling and lubrication are vital components in the thread tapping process, helping to manage the heat generated during cutting, reduce friction, and ensure that taps perform optimally. Properly designed cooling and lubrication systems contribute to the longevity of the tapping tools, improve the overall quality of the threads, and enhance the efficiency of the production process. Without effective cooling and lubrication, tapping operations would be prone to higher rates of tool wear, poor thread quality, and potential damage to both the machine and the workpieces.
Control Systems
Control systems in thread tapping machines are essential for ensuring that the tapping process is carried out with precision, consistency, and efficiency. These systems regulate various parameters such as tapping speed, feed rate, tool alignment, and depth of cut, allowing the machine to perform at optimal levels and produce threads that meet the required specifications. With the advancements in automation and technology, control systems have become more sophisticated, enabling manufacturers to achieve higher productivity and reduce the likelihood of errors during production.
At the core of most modern thread tapping machines is the computer numerical control (CNC) system, which provides the necessary control over the machine’s operations. The CNC system is programmed with specific instructions regarding the type of thread, material being tapped, and the size and pitch of the thread. Once the parameters are set, the control system continuously monitors the tapping process and adjusts the machine’s movements to ensure that the threads are cut accurately. CNC-controlled machines can perform complex and repetitive tasks with high precision, making them ideal for high-volume production environments.
The control system also governs the feed rate, which refers to the speed at which the tap advances into the workpiece. A precise feed rate is crucial for achieving threads with the correct depth and pitch. If the feed rate is too fast, it may result in undercut or inconsistent threads, while a feed rate that is too slow can cause excessive wear on the tap and reduce efficiency. The control system adjusts the feed rate based on factors such as material type, tool condition, and desired thread characteristics, ensuring that the process runs smoothly.
Tool alignment is another critical aspect managed by control systems. Proper alignment ensures that the tap enters the hole at the correct angle and follows the intended path to create accurate threads. If the tap becomes misaligned, it can produce threads that are crooked or incomplete, leading to poor-quality components. The control system continuously monitors the alignment of the tool and makes adjustments as necessary, ensuring that the tap remains on track and produces high-quality results.
In addition to managing the feed rate and tool alignment, modern control systems are equipped with sensor feedback that monitors the overall performance of the tapping process. Sensors can detect issues such as tool wear, misalignment, or deviations in thread quality. If a problem is detected, the control system can trigger an alert or automatically adjust the machine’s settings to correct the issue. For example, if the system detects that the tap is becoming dull, it may slow down the feed rate to reduce wear and ensure that the threads are still cut accurately.
Some advanced control systems are also capable of real-time monitoring and data logging, collecting information about the tapping process and storing it for analysis. This data can provide valuable insights into the performance of the machine, helping operators identify potential issues early and optimize the tapping process for future runs. The ability to track and analyze performance data can lead to improved efficiency, reduced downtime, and enhanced product quality.
In summary, control systems are a crucial part of thread tapping machines, providing the necessary regulation for key aspects of the tapping process such as speed, feed rate, tool alignment, and monitoring. With the integration of CNC technology, sensor feedback, and real-time data analysis, these systems enable manufacturers to produce high-quality threads quickly and efficiently while minimizing the risk of errors. The precision and automation offered by modern control systems are key to maintaining high standards in the production of threaded components.
Post-Tapping Operations
Post-tapping operations are critical steps that follow the initial tapping process to ensure the threads are correctly formed, the workpiece is free from defects, and the part meets quality standards. These operations may involve additional processes to refine the threads, remove excess material, or inspect the finished product. Post-tapping activities are essential for ensuring the threads function properly in their intended application and that the workpiece is ready for final assembly or use.
One of the primary post-tapping operations is deburring, which removes any burrs or sharp edges left around the threaded hole after tapping. Burrs can result from the cutting process and can affect the overall quality of the threaded component. If left untreated, they can interfere with the proper fit of fittings or seals, leading to leaks or misalignment in applications such as radiator connections or automotive parts. Deburring is often done manually or with specialized machines designed to remove burrs efficiently, ensuring smooth and safe edges around the threads.
Thread cleaning is another important post-tapping operation. During the tapping process, chips, debris, or coolant can accumulate in the threaded hole. These contaminants need to be cleaned to ensure that the threads are free of obstruction and that the component will function as intended. Cleaning may involve blowing air through the hole, using a cleaning fluid, or employing a wire brush to clear out any remaining particles that could interfere with the threading or assembly process.
In some cases, thread inspection is carried out to verify the quality and accuracy of the threads. This inspection may include visual checks for imperfections or using specialized tools such as thread gauges to measure the dimensions of the threads and ensure they conform to the required standards. If the threads are out of tolerance, corrective measures may be taken, such as re-tapping the hole or using a die to correct the thread pitch or diameter.
Another post-tapping operation is surface treatment or coating, which may be applied to improve the durability, corrosion resistance, or aesthetic appearance of the workpiece. For example, radiators or automotive components that undergo tapping may be coated with protective layers of paint, rust inhibitors, or other coatings to enhance their resistance to environmental factors like moisture or heat. These treatments can increase the lifespan of the product and improve its overall functionality.
Assembly preparation is another common post-tapping task, especially for components that are part of larger systems. Once the threads have been cleaned and inspected, the workpieces may undergo additional operations, such as inserting threaded inserts, applying sealants, or pre-assembling parts that will be joined together. This step ensures that the tapped component is fully ready for integration into the final product.
In some cases, rework or refinishing may be required if the threads were not formed correctly or if the workpiece was damaged during the tapping process. For example, if the threads are stripped or uneven, the workpiece may need to be re-tapped or the hole enlarged and fitted with a new insert. Rework operations ensure that all components meet the necessary specifications before they are shipped or assembled into the final product.
In summary, post-tapping operations are vital for ensuring that the threads produced during the tapping process are functional, precise, and free of defects. These operations include deburring, cleaning, thread inspection, surface treatment, and assembly preparation, all of which contribute to the overall quality and performance of the finished component. Proper post-tapping operations help to eliminate issues that could arise during later stages of production or in the final use of the part, ensuring that it performs reliably and meets the required standards.
Types of Tapping Machines for Radiators
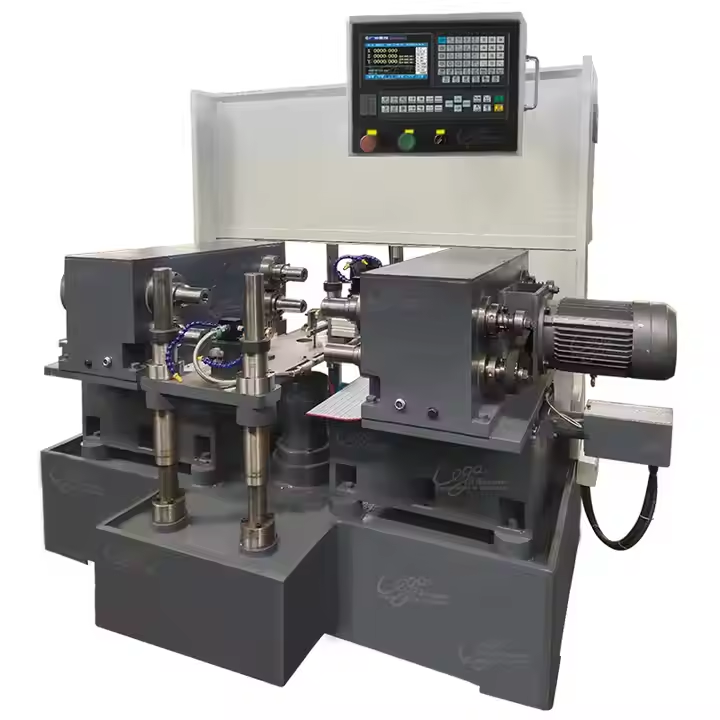
Tapping machines used for radiators are specialized machines designed to create threaded holes in components that are typically made from materials like steel, brass, or aluminum. These machines are critical for ensuring that radiator fittings, valves, and other accessories can be securely attached. The choice of tapping machine depends on factors such as the material of the radiator, the type of threads required, production volume, and precision needed. Various types of tapping machines are employed to handle these tasks, each offering distinct advantages depending on the specific needs of the manufacturer.
Radial Tapping Machines are commonly used for radiator manufacturing due to their versatility and ability to handle a wide range of components. In these machines, the tap is mounted on a rotating spindle that moves radially towards the workpiece. The workpiece is fixed in place, and the tap advances perpendicularly to the surface of the material. This type of tapping machine is ideal for applications where consistent depth and thread accuracy are crucial, as it provides uniform force across the material. Radial tapping machines are often used when multiple holes need to be tapped in a single setup, allowing for efficient and fast operations.
CNC Tapping Machines offer advanced features for precision and automation. These machines are controlled by computer programs, allowing manufacturers to input specific thread dimensions, hole sizes, and other settings required for radiator components. CNC tapping machines are particularly beneficial for high-precision tasks, as they provide tight control over feed rates, tapping speeds, and alignment, ensuring that the threads meet exact specifications. These machines are highly versatile and can easily switch between different types of taps and workpieces without requiring manual adjustments. The automation provided by CNC machines also increases production speed and reduces human error, making them ideal for mass production of radiator components.
Multi-Spindle Tapping Machines are used when high production volumes are required. These machines can tap multiple holes simultaneously, which significantly increases throughput. Each spindle on the machine is equipped with a separate tap, allowing the machine to work on several threads at once. Multi-spindle tapping machines are perfect for tapping large batches of similar radiator parts, where speed and efficiency are prioritized over individual thread precision. The high output of these machines makes them well-suited for applications like tapping numerous valve connections or mounting points on radiators.
Horizontal Tapping Machines are another type used for radiator components, particularly when tapping large or heavy workpieces. These machines are designed with a horizontal axis, where the workpiece is fed into the tapping tool. Horizontal tapping machines are often used when larger components or heavy-duty radiator parts need to be tapped. The advantage of a horizontal setup is that it reduces the risk of distortion or warping that may occur with vertical machines, especially with heavier materials. Additionally, horizontal tapping machines often allow for the use of larger taps and higher cutting forces, which can be necessary when working with tougher materials.
Automatic Tapping Machines are commonly used in environments where consistent, high-volume production is needed. These machines are equipped with automated systems that load, tap, and unload workpieces with minimal human intervention. Sensors and control systems are often integrated into these machines to monitor the tapping process, ensuring that the threads are cut accurately and consistently. The automation of loading and unloading, as well as tool changing, reduces downtime and increases overall production efficiency, making automatic tapping machines ideal for radiator manufacturers who need to produce large quantities of parts quickly and with minimal manual labor.
Pneumatic Tapping Machines use compressed air to drive the tap into the workpiece. These machines are commonly employed for applications that require quick, precise tapping with less force. Pneumatic tapping machines are ideal for use in environments where there is a need for rapid operation and high flexibility. They are often used for tapping smaller radiator components or in applications where a lighter touch is required to avoid damaging delicate materials. The use of compressed air makes pneumatic tapping machines efficient in terms of both speed and energy consumption, as they require less electricity than other electrically driven machines.
In conclusion, the type of tapping machine chosen for radiator manufacturing depends on the specific requirements of the job, including the material being tapped, the desired precision, production volume, and operational efficiency. Radial, CNC, multi-spindle, horizontal, automatic, and pneumatic tapping machines all offer unique benefits that make them suitable for different radiator production needs. By selecting the right tapping machine, manufacturers can ensure that their radiator components are accurately threaded, efficiently produced, and ready for assembly.
Applications in Radiator Manufacturing
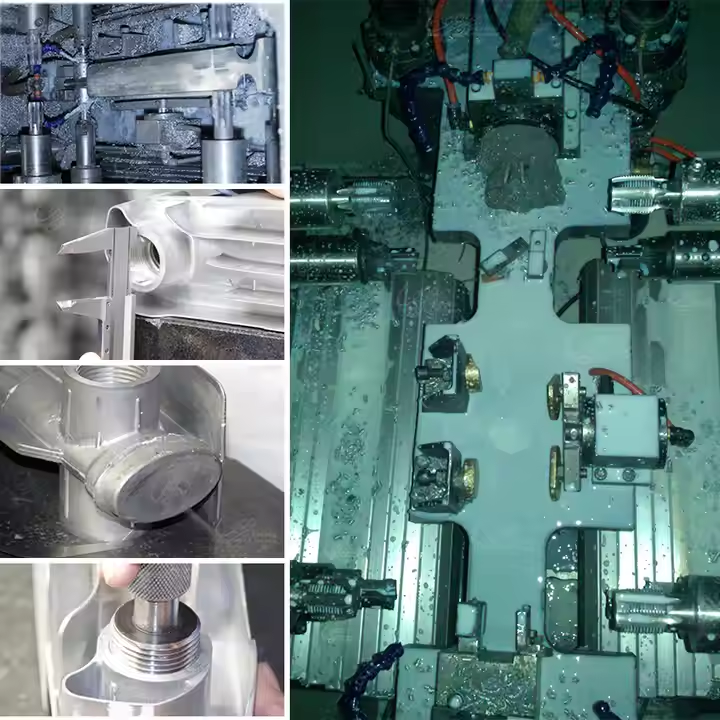
In radiator manufacturing, tapping machines play a crucial role in creating precise threaded holes that allow for the attachment of various components such as valves, fittings, and mounting brackets. These threaded connections are essential for ensuring that the radiator can be properly integrated into heating systems, automotive engines, or other applications that require reliable and secure connections. The tapping process involves cutting threads into pre-drilled holes, allowing for the insertion of screws, bolts, or other fastening elements.
Tapping machines are used for several specific applications within radiator manufacturing, each designed to handle unique requirements related to thread dimensions, material types, and production volumes.
Valve Connection Threads are one of the most common applications of tapping in radiator manufacturing. Radiators often require threads to connect valves for controlling water or steam flow within the system. These valves are integral to the functioning of radiators, and the threads must be precise to ensure a secure, leak-free connection. Tapping machines are used to create the necessary threads in various parts of the radiator body, such as the inlet and outlet ports, which will later be connected to the radiator valves. Precision is critical here to ensure that the threads align correctly with the valve fittings and maintain their integrity under pressure.
Mounting Point Threads are another key application in radiator production. Radiators need threaded holes for mounting brackets or other components that allow them to be securely installed on walls, floors, or in other locations. Tapping machines are employed to cut threads into the radiator’s frame, providing a reliable anchor point for the mounting hardware. The accuracy of these threads is important to ensure that the radiator is safely and securely fixed in place, which is especially crucial for larger or heavier radiator units.
Expansion and Fitting Connections in radiator systems also require tapping. As radiators are often part of complex heating systems that include multiple pipes and fittings, tapping machines are used to create threads for the expansion joints, pipe connections, and fittings. These threads ensure that the radiator can be seamlessly integrated into the overall system, with tight, leak-proof connections that prevent issues such as fluid or gas escapes. The tapping process must account for the specific thread size and pitch requirements of these fittings, which can vary depending on the type of heating system being used.
Thermostatic Valve Threads are another critical application for tapping machines in radiator manufacturing. Many modern radiators are designed to incorporate thermostatic control valves, which regulate the flow of hot water or steam based on the temperature. The threaded holes for these valves must be carefully tapped to ensure proper installation and function. Since thermostatic valves often require specific thread standards, tapping machines must be capable of handling precise threading operations to create a perfect fit for these advanced components.
Bleed Valve Threads are also commonly created using tapping machines. Bleed valves allow air to be released from radiators, helping to maintain optimal performance by preventing airlocks that can interfere with the heating process. The threaded holes for bleed valves must be accurately tapped to ensure that the valve fits securely and functions correctly without leaks. This application requires tapping machines that can handle both small and precise threads to accommodate the size and design of the bleed valves used in radiators.
Heat Exchanger Threaded Connections are used in certain radiator designs that incorporate heat exchangers or other specialized systems for transferring heat. These connections often require specific types of threads to facilitate secure connections with pipes or other system components. Tapping machines are essential for creating these threaded connections, ensuring that the heat exchanger and the radiator are properly integrated into the larger heating system.
In all these applications, tapping machines are used to ensure that the threads are created with the right size, pitch, and depth, allowing for reliable, secure connections between radiator components and the rest of the heating system. The choice of tapping machine depends on factors such as the material of the radiator, the type of thread required, and the production volume. Whether using CNC, radial, or multi-spindle machines, manufacturers rely on tapping machines to produce high-quality threaded holes that are essential for radiator functionality and durability.
In summary, tapping machines are integral to a variety of applications in radiator manufacturing. From valve connections to mounting points, thermostatic valves to bleed valves, and heat exchanger fittings, tapping ensures that all threaded components fit together securely, contributing to the overall performance and efficiency of the radiator system. The accuracy and precision provided by tapping machines are crucial for ensuring that radiators function properly and meet the rigorous demands of their applications.
Advantages of Using Thread Tapping Machines in Radiator Production
Using thread tapping machines in radiator production offers a variety of advantages that contribute to increased efficiency, precision, and overall quality of the manufacturing process. These machines are essential for ensuring that threaded connections are created quickly and accurately, enabling the production of reliable radiator components that meet industry standards. Below are some of the key benefits of utilizing thread tapping machines in radiator manufacturing.
Increased Precision and Consistency is one of the primary advantages of using thread tapping machines. These machines are designed to create highly accurate threads that meet tight specifications, ensuring that components such as valves, mounting brackets, and bleed valves fit securely and perform as intended. With the automation provided by CNC and other advanced control systems, thread tapping machines can consistently produce threads with minimal variation, reducing the risk of defects and ensuring that all parts are uniform in quality. This high level of precision is essential for ensuring leak-free connections and reliable performance in radiator systems.
Improved Production Speed is another significant advantage of using thread tapping machines. These machines are designed to perform tapping operations quickly and efficiently, allowing manufacturers to produce large volumes of radiator components in a short amount of time. Automated systems and multi-spindle designs can further increase throughput by tapping multiple holes simultaneously, reducing cycle times and increasing the overall output of the production line. This speed is particularly beneficial in high-volume manufacturing environments where meeting production deadlines and maintaining a high level of productivity is crucial.
Cost Efficiency is an important consideration in radiator manufacturing, and thread tapping machines help reduce production costs by automating labor-intensive tasks. The use of automated systems reduces the need for manual labor, minimizing human error and lowering labor costs. Additionally, the precision of thread tapping machines reduces waste by minimizing the chances of producing defective parts that would need to be reworked or discarded. The reduction in material waste and the increased efficiency of the production process help manufacturers keep costs down while maintaining high-quality standards.
Versatility and Flexibility are also key advantages of using thread tapping machines. Modern tapping machines, especially CNC machines, are capable of handling a wide variety of radiator components and thread types. They can be easily reprogrammed to accommodate different sizes, thread pitches, and materials, making them adaptable to changing production requirements. Whether tapping small holes for bleed valves or larger threads for valve connections, thread tapping machines can handle diverse tasks with ease, providing manufacturers with the flexibility to meet different design specifications.
Reduced Risk of Human Error is another important benefit of using thread tapping machines. Manual threading operations are more prone to inconsistencies and errors, especially when producing large volumes of parts. By automating the tapping process, manufacturers can significantly reduce the risk of mistakes, such as misaligned threads or incorrect thread dimensions. Automated machines can monitor the process in real time and make adjustments as needed to maintain precision, ensuring that the final product meets the required quality standards without the need for constant manual oversight.
Enhanced Tool Life is another advantage provided by thread tapping machines. These machines often include advanced cooling and lubrication systems that reduce friction and heat during the tapping process, helping to prolong the life of the taps and other cutting tools. By maintaining optimal cutting conditions, the machine can operate efficiently for longer periods, reducing the frequency of tool replacements and minimizing downtime for maintenance. This can lead to cost savings in terms of tool replacement and maintenance, as well as improved machine availability.
Quality Control and Monitoring are integrated into many modern thread tapping machines, providing manufacturers with real-time feedback on the tapping process. Sensors and control systems monitor key parameters such as tool wear, thread dimensions, and alignment, allowing operators to quickly detect and address any issues that may arise during production. This proactive approach to quality control helps prevent defects before they become widespread, ensuring that the final radiator components are of the highest quality.
In conclusion, the use of thread tapping machines in radiator production offers numerous advantages, including increased precision, improved production speed, cost efficiency, versatility, reduced human error, enhanced tool life, and advanced quality control. These benefits contribute to the overall efficiency and profitability of the manufacturing process, enabling companies to produce high-quality radiator components that meet the demands of the market while maintaining competitive costs and high production standards.
Aluminium Radiator Manufacturing Process
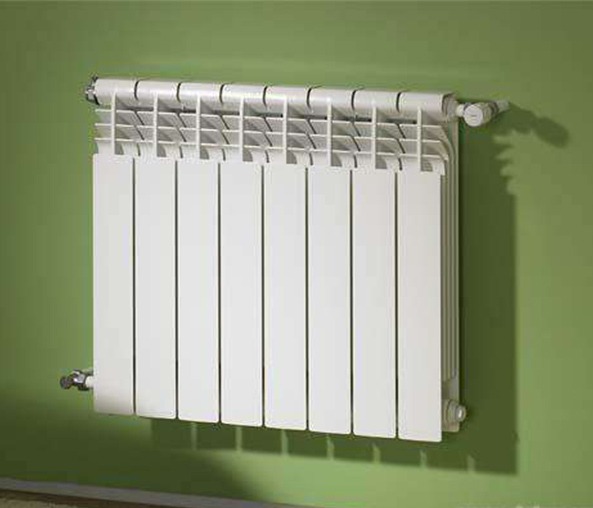
The aluminum radiator manufacturing process involves several key stages, each of which contributes to the creation of a high-quality, durable, and efficient product. Aluminum is a popular choice for radiator production due to its excellent thermal conductivity, lightweight properties, corrosion resistance, and ease of fabrication. The process requires a combination of advanced technologies, skilled labor, and precise operations to produce radiators that meet industry standards and customer specifications. Below is a detailed overview of the steps involved in aluminum radiator manufacturing.
1. Material Selection and Preparation
The first step in the manufacturing process is selecting high-quality aluminum alloys that are suitable for radiator production. The choice of alloy depends on the specific application and desired characteristics, such as strength, thermal conductivity, and corrosion resistance. Aluminum alloys commonly used for radiators include 1050, 1060, and 3003, each offering a balance of performance characteristics. The aluminum is typically supplied in the form of sheets or coils.
Once the material is selected, it is prepared for the next stages of production. This involves cutting the aluminum sheets or coils into specific sizes required for the radiator design. The material is cleaned to remove any contaminants, oils, or residues that may interfere with the manufacturing process or the final product’s quality. Cleaning is usually done using solvents or degreasing agents to ensure that the aluminum surface is free of impurities.
2. Die-Cutting and Shaping
The next step is shaping the aluminum into the components that will form the radiator. This is typically done using a process known as die-cutting or punching. Specialized dies are used to cut the aluminum into the required shapes, such as fins, tubes, and end caps. These components will later be assembled to form the finished radiator.
For heat exchangers, aluminum fins are often cut to size and shaped to maximize the surface area for heat dissipation. The shaping process may include bending or rolling the aluminum sheets to form the correct dimensions and configurations. In some cases, the aluminum is also perforated to allow for the efficient flow of air or fluid, which is crucial for heat transfer performance.
3. Tube and Fin Assembly
One of the most critical parts of the radiator is the tube and fin assembly. The tubes are responsible for carrying the coolant or heat transfer fluid, while the fins increase the surface area for heat exchange. The process of assembling the tubes and fins involves several key steps.
Tube Cutting and Forming: Aluminum tubes, which are often produced through extrusion, are cut to the required lengths. The tubes are then formed into a shape that fits the design of the radiator. This may involve bending the tubes into the appropriate configuration to match the radiator’s design specifications.
Fin Attachment: Aluminum fins are attached to the tubes to increase the radiator’s surface area for efficient heat transfer. Fins are often inserted into grooves or slots on the tubes, and the fins may be welded, brazed, or mechanically pressed into place. The fins are strategically spaced to maximize airflow and heat dissipation. The method of attaching fins depends on the type of radiator and its intended use. In high-performance applications, brazing or welding is often used to ensure a secure and durable connection between the fins and tubes.
4. Brazing and Welding
Brazing is one of the most common methods used in aluminum radiator manufacturing to bond the various components of the radiator together. The process involves heating the aluminum components, including the tubes, fins, and end caps, to a temperature just below the melting point of the aluminum. A filler material is then applied to join the components, forming a strong and durable bond.
Brazing: During the brazing process, the radiator components are placed in a controlled furnace where heat causes the filler material to melt and bond with the aluminum components. This creates a tight and reliable seal, ensuring that the radiator can withstand the pressures and temperatures associated with its operation. Brazing is particularly useful for aluminum radiators because it creates strong joints while maintaining the integrity of the base material.
Welding: In some cases, welding may be used in conjunction with brazing to join thicker aluminum parts or provide additional strength to certain areas of the radiator. Aluminum welding requires specialized equipment, as aluminum is more challenging to weld than other metals due to its low melting point and high thermal conductivity. However, welding can be used effectively to join larger or more complex components of the radiator.
5. Leak Testing and Quality Control
Once the radiator components are assembled and bonded, the next step is leak testing and quality control. This is a crucial step to ensure that the radiator is functioning correctly and free from defects. Radiators are pressurized with air, water, or a similar testing medium to check for leaks at the joints and seams. Any leaks are identified and addressed through repair or re-brazing, ensuring that the radiator can withstand the pressure and fluid flow it will experience during normal operation.
Visual Inspection is also an important part of the quality control process. The radiator is examined for surface defects, such as scratches, dents, or cracks. Any cosmetic imperfections are addressed to maintain the aesthetic quality of the radiator. Radiators are also inspected for alignment, ensuring that the components fit together properly and that the fins are uniformly spaced for optimal heat transfer.
6. Surface Treatment and Coating
To protect the aluminum radiator from corrosion and enhance its appearance, a surface treatment or coating is often applied. Anodizing is one of the most common surface treatments for aluminum radiators. This process involves using an electrolytic process to create a protective oxide layer on the surface of the aluminum. This layer helps to protect the radiator from environmental factors such as moisture, chemicals, and temperature fluctuations.
In addition to anodizing, painting or powder coating may be applied to provide an additional layer of protection and improve the aesthetic appearance of the radiator. These coatings can also help to increase the corrosion resistance and durability of the radiator, ensuring a longer lifespan and better performance in harsh environments.
7. Final Assembly and Packaging
After the radiator has undergone leak testing, quality control, and surface treatments, it is ready for final assembly. During this stage, the radiator may receive additional components such as end caps, mounting brackets, and fittings that are necessary for installation and operation. Once the final components are attached, the radiator is cleaned to remove any residual oils, dust, or other contaminants.
The completed radiators are then packaged for shipment. Packaging materials are selected to protect the radiator during transport, preventing damage from impact or moisture. Radiators are often placed in protective wrapping, cartons, or custom-designed crates to ensure that they arrive at their destination in perfect condition.
8. Shipping and Distribution
The final step in the aluminum radiator manufacturing process is shipping. Radiators are typically shipped to distributors, wholesalers, or directly to customers, depending on the production model. Timely and efficient shipping is critical to ensuring that the radiators reach their destinations on schedule.
Conclusion
The aluminum radiator manufacturing process is a complex and detailed series of steps, each contributing to the overall quality, durability, and performance of the finished product. From material selection and shaping to brazing, leak testing, and final assembly, each stage is carefully controlled to ensure that the radiator meets the required specifications and standards. With aluminum’s lightweight, corrosion-resistant, and thermally efficient properties, it remains a popular choice for radiator production in various industries, including automotive, industrial, and residential heating systems. The combination of advanced technology, skilled labor, and quality control ensures that aluminum radiators continue to meet the demands of modern applications.
Material Selection and Preparation
Material selection and preparation are crucial initial steps in the manufacturing process, particularly for aluminum radiator production, where the material’s properties directly impact the quality, durability, and efficiency of the final product. The choice of material determines not only the radiator’s performance but also its cost, longevity, and ability to withstand various environmental conditions. The process involves selecting the appropriate aluminum alloy, ensuring the material is free from contaminants, and preparing it for subsequent fabrication steps such as shaping, cutting, and assembly.
In aluminum radiator manufacturing, the material most commonly used is aluminum alloy due to its excellent properties, such as high thermal conductivity, corrosion resistance, and lightweight nature. Aluminum’s thermal conductivity is critical in radiator applications, as it allows for efficient heat transfer. The specific aluminum alloys selected often depend on the intended application, with alloys like 1050, 1060, and 3003 being widely used for their ideal combination of strength, malleability, and thermal efficiency. Alloy 1050, for instance, is highly conductive and corrosion-resistant, making it ideal for radiators that need to operate in environments where heat dissipation is crucial. Alloy 3003, on the other hand, is often used for its balance of durability and cost-effectiveness, especially when strength is not the primary concern.
Once the appropriate aluminum alloy is selected, the material undergoes several preparatory steps to ensure it is ready for processing. The first step in the preparation phase is cleaning. Aluminum surfaces can easily accumulate oils, dust, and other contaminants during handling and transportation. These impurities must be removed to ensure proper bonding during later stages such as welding or brazing, as well as to ensure the quality of surface treatments such as anodizing or powder coating. Cleaning typically involves washing the material with solvents, degreasers, or specific cleaning agents designed to remove residues. In some cases, ultrasonic cleaning may be employed to provide a more thorough cleanse, ensuring that the material is free from oils or microscopic debris that might interfere with further processing.
Once cleaned, the aluminum material is inspected for any visible defects or imperfections. These defects could include scratches, dents, or irregularities in the surface, which could negatively affect the final appearance and functionality of the radiator. For critical applications, even minor defects can compromise the integrity of the final product, particularly where heat transfer or structural strength is concerned. The aluminum sheets or coils are carefully examined, and any defective material is either reworked or discarded. This step ensures that only high-quality material proceeds to the next stages of manufacturing.
The next phase of material preparation involves cutting the aluminum into the required shapes and sizes. The material is typically available in sheets or coils, which are then cut into precise dimensions based on the design specifications for the radiator. For radiators, this cutting process involves creating sections that will later be used to form the fins, tubes, and end caps. Depending on the radiator design, the aluminum may need to be cut into thin sheets to form fins that will later be attached to the tubes for heat dissipation. The cutting process needs to be highly accurate, as any deviation from the design can result in misalignment during assembly, affecting the radiator’s overall performance and fit.
Additionally, some aluminum material may require further shaping, especially if the radiator design involves complex geometries. In these cases, the material may be bent or rolled into specific forms to accommodate the necessary design specifications. Bending aluminum is relatively straightforward due to the material’s malleability, but care must be taken to avoid kinks or deformations that could compromise the strength and function of the radiator.
In parallel with the physical preparation of the material, certain treatments or coatings may also be applied to enhance the material’s performance. One such treatment is anodizing, which involves using an electrolytic process to form a protective oxide layer on the aluminum’s surface. This layer provides increased corrosion resistance, improving the longevity and durability of the radiator, especially in environments where moisture, chemicals, or high temperatures are prevalent. Anodizing also gives the aluminum a more aesthetically appealing finish, with options for different colors or finishes to suit the desired product design.
Furthermore, preparation may include the application of a lubricant or cooling agent to the aluminum, especially if the material will undergo processes like cutting, punching, or bending. Lubricants help to reduce friction, preventing the material from overheating or becoming damaged during shaping and cutting operations. The use of the right lubricants ensures that the aluminum retains its integrity and maintains the desired surface quality after machining.
Material preparation is a critical part of aluminum radiator production, as it sets the foundation for all subsequent manufacturing steps. Choosing the correct alloy, thoroughly cleaning and inspecting the material, and accurately cutting or shaping it for the next phases of production ensure that the radiator will meet the necessary performance and quality standards. By paying close attention to these preparation steps, manufacturers can achieve the precise fit, strength, and functionality required for the efficient and reliable operation of aluminum radiators in various applications.
Die-Cutting and Shaping
Die-cutting and shaping are fundamental processes in the production of aluminum radiators, playing a critical role in determining the final design, structure, and efficiency of the product. These processes involve the precise shaping and cutting of aluminum material into components that form the core of the radiator, such as fins, tubes, and end caps. The accuracy and quality of the die-cutting and shaping stages directly affect the performance of the radiator, influencing heat transfer efficiency, structural integrity, and ease of assembly.
Die-cutting is a highly precise process in which specialized tools, known as dies, are used to cut the aluminum material into specific shapes. These dies are custom-designed to match the required dimensions and geometry of the radiator components, ensuring that each piece fits together seamlessly during assembly. The die-cutting process begins with a carefully measured sheet or coil of aluminum, which is loaded into a cutting press. The die, typically made of hardened steel, is then pressed into the material, exerting significant force to cut through the aluminum with high precision. This cutting method allows for the production of complex shapes and patterns with minimal waste and high repeatability, ensuring consistency across large production runs.
The cutting tools used in die-cutting machines are designed to accommodate the specific thickness and hardness of the aluminum alloy being processed. The die’s sharpness and design ensure that the material is cut cleanly, with minimal burrs or rough edges. These imperfections can cause issues during assembly, as they may prevent proper fitting or lead to leaks in the final product. Therefore, the die-cutting process must be carefully calibrated to produce clean, smooth edges, ensuring that each component of the radiator meets stringent quality standards.
Once the aluminum is cut into basic shapes, the next stage involves shaping the material to form the desired components of the radiator. This shaping process may include bending, rolling, or pressing the aluminum into specific configurations that will facilitate heat transfer or structural strength. For example, fins—essential components for increasing the surface area of the radiator and improving heat dissipation—are typically shaped using dies that bend the aluminum sheets into a series of parallel ridges or grooves. These fins are then spaced evenly and attached to the radiator’s tubes, ensuring that air or fluid can pass efficiently over them to maximize heat exchange.
The shaping process also involves the formation of aluminum tubes, which are often extruded into long, uniform shapes. These tubes are then cut to size, and any necessary bends or adjustments are made to match the specific design of the radiator. The tubes serve as the channels through which coolant or heat transfer fluid flows, and their dimensions and integrity are critical for ensuring that the radiator functions properly under varying pressures and temperatures.
In addition to fins and tubes, other components of the radiator, such as end caps or mounting brackets, are also created through die-cutting and shaping. End caps are designed to seal the ends of the radiator’s tubes, preventing fluid leaks and ensuring that the system remains pressurized. These caps are typically stamped or cut from sheets of aluminum and then shaped to fit securely onto the tubes. Similarly, mounting brackets may be shaped to allow for easy installation of the radiator into its intended location, whether in an automotive engine, industrial heating system, or residential setting.
The precision of the die-cutting and shaping processes is vital to the radiator’s performance. Components must be cut and shaped to exact specifications to ensure that they align properly during the assembly stage. If the components are not shaped accurately, the radiator may experience issues such as poor heat transfer, structural weaknesses, or difficulty in fitting and sealing the parts together. Inaccurate die-cutting can also result in excess material waste, leading to higher production costs and environmental impact.
The materials used in the die-cutting process also play an important role in the efficiency of the shaping and cutting stages. Aluminum alloys with varying levels of strength, thickness, and flexibility may require different cutting techniques or die materials. For example, softer alloys may be easier to cut but might not provide the necessary strength for certain applications. Conversely, harder alloys might require more force to cut but offer enhanced durability and resistance to corrosion. Manufacturers must carefully select the appropriate material and cutting technique based on the intended use of the radiator, ensuring that each component is both functional and durable.
Die-cutting and shaping processes also need to account for any post-processing steps such as deburring, cleaning, and surface finishing. After the material is cut and shaped, any rough edges or burrs left from the die-cutting process are typically smoothed out to ensure that the components fit together properly. In some cases, additional treatments such as anodizing or coating may be applied to enhance the aluminum’s resistance to corrosion or improve its appearance.
In summary, die-cutting and shaping are essential steps in the production of aluminum radiators. These processes enable manufacturers to create the individual components—such as fins, tubes, and end caps—that make up the radiator. Precision in both cutting and shaping is critical to ensuring that the radiator functions efficiently, has a long lifespan, and can be easily assembled. By using specialized dies and advanced machinery, manufacturers can produce aluminum radiator components with high accuracy, minimal waste, and superior quality, ensuring that the final product performs optimally in its intended application.
Tube and Fin Assembly
Tube and fin assembly is one of the most critical steps in the manufacturing of aluminum radiators, as it directly affects the efficiency of heat transfer and the overall structural integrity of the final product. The process involves assembling the core components of the radiator—tubes, fins, and other related parts—into a unified structure that can effectively dissipate heat. Proper tube and fin assembly is essential for achieving high thermal performance, durability, and reliability, making it one of the most important stages in the production process.
The process begins with the preparation of the aluminum tubes, which serve as the primary channels for the coolant or heat transfer fluid within the radiator. These tubes are typically made by extruding aluminum, creating long, hollow cylinders that are then cut to the necessary lengths based on the radiator’s design specifications. The tubes must be carefully measured to ensure they fit within the overall framework of the radiator, and any necessary bends or adjustments are made to ensure they align with the fins and other components. The tube’s interior and exterior surfaces must also be free from any impurities or contaminants, as these can impede the flow of fluid or reduce the bond between the tubes and fins during assembly.
Once the tubes are ready, the next step is to prepare the aluminum fins, which play a crucial role in enhancing the radiator’s heat dissipation capabilities. The fins are typically made by cutting aluminum sheets into thin strips and then shaping them into a series of ridged or louvered patterns that increase the surface area available for heat exchange. The fins are then spaced evenly and arranged to maximize airflow around the tubes, allowing heat to transfer efficiently from the fluid inside the tubes to the surrounding air or cooling medium. The number and design of the fins are tailored to the specific requirements of the radiator, depending on factors such as the desired thermal capacity, airflow conditions, and intended application.
The next step in the tube and fin assembly process is the attachment of the fins to the tubes. This can be done using several methods, including mechanical pressing, brazing, or welding. In some cases, the fins are pressed directly into grooves or slots on the tubes, creating a secure and stable connection. This mechanical attachment ensures that the fins remain in place even under the stresses and vibrations that the radiator will experience during operation. The fin-tube connection must be precise to avoid gaps or misalignments, which could negatively affect heat transfer efficiency.
In more advanced manufacturing processes, the fins and tubes may be joined using brazing, which involves heating the components in a furnace to melt a filler material that bonds the fins to the tubes. This method creates a strong, permanent connection that can withstand high temperatures and pressures, ensuring the radiator’s durability and performance over time. Brazing also improves the thermal conductivity of the joints, further enhancing the overall heat transfer efficiency of the radiator.
In some cases, welding may be employed to join the fins to the tubes, especially in situations where additional strength or durability is required. However, welding aluminum can be more challenging than brazing due to the material’s low melting point and high thermal conductivity. Specialized techniques and equipment are used to ensure that the welding process does not damage the aluminum or create weak spots in the joint. Welding may be used in areas where additional structural reinforcement is necessary, or where high-temperature resistance is critical.
Once the fins are attached to the tubes, the next step is to install the end caps, which seal the radiator’s tube system and prevent leaks. End caps are typically cut from aluminum sheets and shaped to fit snugly over the open ends of the tubes. They are attached to the tubes using brazing, welding, or mechanical fastening methods, depending on the design and manufacturing requirements. The end caps also serve to support the radiator’s structural integrity and are often equipped with mounting holes or brackets that allow the radiator to be easily installed in its intended location.
At this point, the tube and fin assembly is nearly complete, and the structure must undergo several quality control checks to ensure it meets the required standards. The assembly is checked for alignment, ensuring that the tubes and fins are properly spaced and positioned to maximize heat transfer efficiency. Any misalignments or gaps in the assembly can reduce the overall performance of the radiator and must be corrected before proceeding to the next stage. The tubes are also inspected for any leaks or defects, as even small imperfections can lead to failure during operation.
In some cases, additional post-assembly treatments are applied to improve the radiator’s performance and appearance. These treatments may include anodizing, which creates a protective oxide layer on the aluminum surface to increase its resistance to corrosion and wear. Anodizing also improves the aesthetic quality of the radiator, giving it a smooth, uniform finish that enhances its appearance. Other treatments, such as powder coating or painting, may be applied to further protect the radiator from environmental factors such as moisture, chemicals, or high temperatures.
The tube and fin assembly process plays a vital role in the overall performance of aluminum radiators. It ensures that the individual components—tubes, fins, and end caps—are securely and efficiently joined to create a unified structure capable of transferring heat effectively. The methods used to attach the fins to the tubes, such as mechanical pressing, brazing, or welding, are critical to achieving strong, durable connections that will perform reliably under various operating conditions. The precision of this assembly process directly impacts the thermal efficiency, structural integrity, and overall reliability of the finished radiator, making it a key step in the production of high-quality, high-performance aluminum radiators.
Brazing and Welding
Brazing and welding are two critical joining processes used in the manufacturing of aluminum radiators, both of which play a significant role in ensuring the structural integrity, durability, and heat transfer performance of the final product. While both methods are designed to bond metal components together, the choice between brazing and welding depends on factors such as the material, the design requirements, and the specific application of the radiator.
Brazing is a high-temperature joining process that uses a filler material to bond two or more metal parts together. In the case of aluminum radiators, brazing is commonly used to join the tubes and fins. Unlike welding, where the base metal is melted to form the joint, brazing involves heating the parts to a temperature below their melting point and using a filler material—typically a metal alloy with a lower melting point than the base metals. The filler material is applied to the joint area and then heated until it melts, flowing into the space between the parts. As it cools, the filler material solidifies, creating a strong bond between the components.
One of the key advantages of brazing in radiator manufacturing is that it allows for a precise and controlled joining process that does not require the base metals to melt. This is particularly important for aluminum, as it has a relatively low melting point compared to other metals like steel, which makes it more susceptible to distortion or damage during the welding process. Brazing minimizes the risk of warping or weakening the aluminum parts, ensuring that the final product maintains its structural integrity and thermal performance.
Brazing also provides excellent thermal conductivity at the joints. The filler material used in brazing is carefully chosen to match the thermal expansion properties of aluminum, ensuring that the joint does not create resistance to heat transfer. This is particularly important in the radiator manufacturing process, where efficient heat dissipation is the key to the radiator’s performance. Additionally, brazed joints are highly resistant to corrosion, which is a crucial consideration for radiators that are exposed to moisture or chemicals over time. By using the appropriate filler material, brazing can create a long-lasting, reliable bond that can withstand harsh operating conditions.
The brazing process is typically carried out in a controlled furnace environment, where the radiator components are heated to the required temperature. In some cases, a flux may be applied to the joint area to remove any oxidation and promote the flow of the filler material. The components are then held at the desired temperature for a set period, allowing the filler to bond with the base metal. After brazing, the joint is allowed to cool naturally, solidifying the filler and forming a strong bond.
On the other hand, welding is a process that involves melting the base materials to form a joint. This is typically done by applying heat using an electric arc, a laser, or another energy source, depending on the type of welding. In welding, the metal parts are heated to their melting point, causing them to fuse together as they cool. Welding can create very strong joints, often stronger than the base material itself, but it requires careful control to avoid distorting the metal and weakening its properties.
Welding aluminum can be more challenging than brazing due to the material’s low melting point and high thermal conductivity. Aluminum requires specific welding techniques, such as Tungsten Inert Gas (TIG) welding or Metal Inert Gas (MIG) welding, which are designed to provide precise control over the heat input and prevent overheating. TIG welding is often used for its ability to produce high-quality, clean welds, while MIG welding is faster and more suited for larger production runs. Both methods require skilled operators who can carefully control the heat input to avoid damaging the aluminum and ensure a strong, reliable joint.
Welding is often used in radiator manufacturing for components that require additional strength, such as end caps or structural support areas. The welded joints provide a solid, permanent bond that is highly resistant to mechanical stress. However, the heat generated during welding can cause changes to the aluminum’s microstructure, which may affect its strength or thermal conductivity. To mitigate these effects, post-weld heat treatment may be necessary to restore the material’s properties and ensure the joint remains strong and durable.
One disadvantage of welding in aluminum radiator manufacturing is that it can introduce stresses and distortions into the material. The heat from welding can cause the aluminum to expand and contract unevenly, leading to warping or deformation. To avoid these issues, manufacturers must carefully control the welding process and sometimes employ techniques such as heat sinks or clamping to minimize distortion. Additionally, the welded areas may require further post-processing steps, such as grinding or polishing, to smooth the joint and remove any excess material or imperfections.
Both brazing and welding have their respective advantages and limitations, and the choice between the two processes depends largely on the specific needs of the radiator design. Brazing is often preferred for joining components that require minimal distortion, such as fins to tubes, and for applications where thermal efficiency and corrosion resistance are paramount. It is particularly beneficial in aluminum radiator manufacturing, where the material’s susceptibility to damage during high-heat processes can make brazing a more reliable choice.
Welding, on the other hand, is ideal for situations where the joint must withstand significant mechanical stress or where a more permanent bond is required. It is commonly used in areas that require structural strength, such as the attachment of end caps or mounting brackets. While welding can introduce some challenges, such as material distortion and heat-affected zones, its ability to create strong, durable joints makes it an essential part of the radiator manufacturing process.
Ultimately, the decision to use brazing or welding depends on the radiator’s design, intended use, and performance requirements. Both processes are critical for creating reliable, high-performance aluminum radiators, and many manufacturers use a combination of both methods to achieve the desired results. Through careful selection of the appropriate joining technique, manufacturers can ensure that their aluminum radiators provide optimal heat transfer, structural integrity, and durability throughout their lifecycle.
Cast iron radiator manufacturing process
The manufacturing process of cast iron radiators involves several intricate steps, from material preparation to molding, casting, assembly, and finishing. Cast iron radiators, known for their durability and excellent heat retention, are commonly used in both residential and industrial settings. The production of these radiators is a complex, multi-step process that requires precision and attention to detail to ensure the final product performs optimally and lasts for many years.
The process begins with the selection and preparation of cast iron. Cast iron is preferred for radiator manufacturing due to its excellent heat retention properties, strength, and resistance to corrosion. The most common type of cast iron used for radiators is grey cast iron, which contains graphite flakes that enhance its castability and thermal conductivity. The process begins by melting scrap iron, often combined with other alloys, such as silicon, carbon, and manganese, to achieve the desired properties. The molten metal is then poured into molds to form the base of the radiator.
Once the materials are melted, the casting process begins. This is typically done using a sand casting technique, where a mold is created from a mixture of sand and binder materials. The mold is made in two halves, which are then pressed together to form a hollow cavity in the shape of the radiator sections. The molds are carefully designed to match the radiator’s specific design specifications, including the shape and dimensions of the sections, which will later be connected to form the complete radiator. The casting process is highly precise, as even minor variations in the mold or casting can affect the overall functionality and appearance of the final product. Once the mold is ready, the molten cast iron is poured into the cavity, filling it to form the radiator section.
After the mold is filled, the cast iron is allowed to cool and solidify. The cooling time can vary depending on the size of the radiator section, with larger sections requiring more time to cool completely. During this cooling phase, the cast iron undergoes a transformation, solidifying into a rigid structure that retains the shape of the mold. Once cooled, the mold is carefully removed, revealing the cast iron radiator section. At this stage, the castings are still rough, with excess metal, known as flash or gates, that needs to be removed.
Next, the cast iron sections undergo a cleaning and finishing process. The rough edges, excess metal, and imperfections from the mold are removed through processes such as sandblasting, grinding, and polishing. This step not only improves the aesthetic quality of the radiator but also ensures that the edges and joints are smooth and free from any defects that could impact the radiator’s performance. The sections are also checked for any cracks or other structural weaknesses, as even minor flaws can compromise the radiator’s effectiveness and longevity.
Once the individual radiator sections are cleaned and finished, they are ready to be assembled. Cast iron radiators are typically made up of multiple sections, which are joined together to form the desired size and shape. The assembly process involves aligning the sections and connecting them with threaded couplings or bolts. Each section is carefully sealed to prevent leaks, as the radiator will be pressurized during use. Gaskets or seals may be used between sections to ensure a tight, leak-free connection. The sections are then bolted together, forming a complete radiator unit. In some cases, a mounting bracket or support is added to ensure that the radiator can be securely installed in its intended location.
After assembly, the cast iron radiator undergoes a final inspection to ensure it meets quality standards. The radiator is carefully checked for leaks, ensuring that there are no issues with the connections between the sections. The quality of the finish is also inspected, ensuring that there are no surface imperfections, rough patches, or signs of poor craftsmanship. Any necessary adjustments or repairs are made at this stage to ensure the radiator will perform as expected once installed.
The finishing process for cast iron radiators is a critical step, both for aesthetic purposes and for corrosion protection. Cast iron is prone to rusting if not properly treated, particularly in environments where the radiator will be exposed to moisture. Therefore, the radiator must undergo a protective coating process to prevent rust and extend its lifespan. The most common finishing method for cast iron radiators is the application of a powder coating or enamel coating. Powder coating involves applying a dry powder to the surface of the radiator, which is then baked in an oven to create a hard, durable finish. This coating provides a smooth, attractive finish and protects the cast iron from corrosion and wear.
Alternatively, enamel coatings may be applied to create a smooth, glossy surface that also offers protection against rust and enhances the radiator’s appearance. These coatings can be applied in multiple layers, with each layer being baked to ensure a strong bond with the metal. In some cases, the radiators may also undergo an additional process of polishing or painting to enhance their appearance, particularly when aesthetic appeal is a key consideration.
The final step in the manufacturing process is testing. Cast iron radiators are tested to ensure they meet the necessary performance standards. This testing typically involves subjecting the radiator to pressure tests to check for leaks and ensure that the radiator can withstand the pressure of the heating system. Additionally, the radiator may be tested for heat retention and distribution efficiency to ensure it performs as intended in its intended application.
Once the radiator passes all tests, it is ready for packaging and shipment. The radiator is carefully packaged to prevent damage during transportation, often with protective materials around the corners and surface. It is then shipped to customers, whether directly to end-users or to retailers, ready to be installed and put to use in heating systems.
In summary, the manufacturing process for cast iron radiators is a multi-step operation that requires careful attention to detail, precision, and quality control at every stage. From the initial melting and casting of the iron to the final inspection and testing, each step is crucial in ensuring that the radiator performs efficiently, is durable, and has a long lifespan. With its superior heat retention, strength, and resistance to corrosion, cast iron remains a popular material for radiator production, particularly in applications where reliability and efficiency are essential.
Continuing from where we left off, cast iron radiators, once manufactured and tested, are ready to be shipped for installation. However, before the radiators are installed in homes, industrial settings, or commercial buildings, there are some important considerations to ensure their optimal functioning and long-term durability.
The installation process of cast iron radiators is just as critical as their manufacturing. Cast iron radiators are heavy, and as a result, proper handling and positioning are necessary to ensure safety during installation. Given their weight, these radiators require solid wall supports or floor brackets to prevent shifting or accidental falls. Before installation, it’s important to check the space where the radiator will be placed to ensure that the proper connections can be made to the heating system, whether it’s a central heating or steam-based system. Cast iron radiators are typically connected using threaded pipes that allow for water or steam to flow through the radiator’s internal channels.
Once in place, the radiator is connected to the heating system through these pipes. The connections should be tightly sealed to prevent any leaks, and proper insulation of the pipes may be needed to maintain heat and ensure energy efficiency. In the case of radiators connected to a steam system, pressure valves are often attached to ensure safe operation and control the temperature and pressure inside the radiator. Proper balancing of the radiator within the system is essential to ensure even heat distribution across all sections of the radiator.
After installation, it’s important to maintain the radiator to prolong its lifespan and ensure continued efficiency. Cast iron radiators are known for their longevity, but they require regular cleaning and occasional inspections. Over time, dust, dirt, and debris can accumulate on the radiator’s surface, particularly between the fins or ribs, reducing its heat transfer efficiency. To keep a cast iron radiator working efficiently, it should be cleaned regularly with a soft brush or cloth. Avoid abrasive cleaning materials that could scratch the protective enamel or powder-coated finish, which could lead to rusting.
It’s also important to inspect the radiator periodically for any signs of wear, cracks, or leaks. Over time, the joints between the cast iron sections may begin to loosen, and the seals can degrade, potentially leading to leaks. If any issues are identified, the radiator should be shut off from the heating system and repaired promptly. Regular maintenance can ensure that the radiator continues to function optimally throughout its life.
As with any heating equipment, the operation of cast iron radiators depends largely on the performance of the surrounding heating system. If the radiator is part of a central heating system, it’s crucial to monitor the overall performance of the system, ensuring that the water or steam temperature is consistent and that the system is not over or under-pressurized. In some cases, the radiator may require bleeding to release any trapped air, which can affect the heat distribution. Bleeding the radiator involves releasing the trapped air via a small valve, allowing the water or steam to flow freely through the system once again.
The durability of cast iron radiators is another key factor contributing to their popularity. Unlike other materials that may corrode or lose their structural integrity over time, cast iron is highly resistant to corrosion, particularly when properly maintained and coated. With proper care, a cast iron radiator can last for several decades, outlasting many other types of radiators. The thick, solid structure of cast iron also allows it to retain heat for extended periods, even after the heating system has been turned off. This characteristic is particularly beneficial in settings where heat retention is crucial, such as in homes and buildings with irregular heating demands.
The aesthetic appeal of cast iron radiators also contributes to their enduring popularity. Their vintage or classical appearance makes them highly desirable for certain design aesthetics, especially in older homes or buildings with historical significance. Many people opt for cast iron radiators because of their distinctive look, often featuring intricate patterns and designs that are both functional and ornamental. As a result, these radiators can serve as both a heating source and a decorative element, adding a touch of character and style to a room.
In recent years, cast iron radiators have seen a resurgence in popularity, as more people seek energy-efficient, durable, and aesthetically pleasing heating solutions. Despite being made from a material that is relatively heavy and requiring more effort for installation compared to lighter alternatives, their thermal efficiency, longevity, and design appeal make them a popular choice for residential, commercial, and industrial applications. Additionally, the increasing emphasis on sustainability and energy efficiency has further boosted the demand for cast iron radiators, as they provide an effective and long-lasting means of heat distribution.
Ultimately, the manufacturing process of cast iron radiators is a meticulous and complex series of steps that ensure the final product is both functional and durable. From selecting the right materials, molding and casting the radiator sections, to final inspection and testing, every aspect of the process contributes to the performance and reliability of the finished radiator. Whether installed in homes, offices, or industrial buildings, cast iron radiators provide efficient and long-lasting heating solutions, maintaining their appeal both for their practical advantages and their aesthetic charm.
Continuing from where we left off, the use of cast iron radiators continues to evolve, and manufacturers are finding new ways to improve the process and enhance the performance and efficiency of these iconic heating devices. Innovation in manufacturing processes, material science, and design has led to modern advancements in the production and performance of cast iron radiators, while still maintaining their traditional advantages.
One of the main areas where innovation has made an impact is in the development of high-efficiency cast iron radiators. Manufacturers have found ways to optimize the design of the radiator sections to improve heat transfer while maintaining the characteristic durability of cast iron. This involves refining the internal channel structure and improving the overall surface area for heat dissipation. By adjusting the geometry of the radiator, it is possible to increase the amount of heat that is transferred from the hot water or steam to the air surrounding the radiator, improving its efficiency without sacrificing its core properties. Additionally, modern coatings have been developed to enhance the heat distribution and prevent oxidation, further improving the radiator’s efficiency and lifespan.
Another area of innovation is in the integration of modern technologies with traditional cast iron radiators. Some manufacturers have begun combining the durability of cast iron with cutting-edge control systems, such as thermostatic radiator valves (TRVs) and smart home integration. TRVs allow users to control the temperature of individual radiators more precisely, improving energy efficiency by ensuring that heat is only delivered to rooms that need it. Smart controls enable users to program the heating system, adjust temperatures remotely, and even connect the radiator to home automation systems for seamless integration with other smart devices. These innovations have helped keep cast iron radiators relevant in an era of modern energy efficiency and control.
In addition to technological innovations, environmental sustainability has become an increasingly important factor in radiator manufacturing. As consumers become more environmentally conscious, manufacturers are focusing on reducing the carbon footprint of the production process. One way this is being achieved is by sourcing more sustainable materials for the casting process, such as recycled cast iron or alloys with a lower environmental impact. By using recycled materials, manufacturers can significantly reduce energy consumption and reduce the demand for virgin raw materials. Additionally, the energy-efficient nature of cast iron radiators contributes to sustainability. Their ability to retain and distribute heat efficiently reduces energy waste, making them an environmentally friendly choice for heating.
As sustainability concerns grow, cast iron radiators are also becoming a more popular option in energy-efficient retrofitting projects. In many older homes and buildings, replacing outdated or inefficient heating systems with more modern, eco-friendly options is a priority. Cast iron radiators, with their energy-efficient properties, are ideal for these retrofitting projects, providing an opportunity to preserve historical aesthetics while upgrading heating efficiency. In fact, many homes or buildings that were originally equipped with cast iron radiators are being renovated to restore or maintain the classic look while also improving energy consumption.
On the aesthetic front, cast iron radiators continue to be a favored choice for homeowners and architects who appreciate their vintage or industrial charm. Radiators are available in a variety of finishes, ranging from classic matte to glossy enameled coatings, and can even be custom-colored to fit the interior design of a space. Many modern manufacturers offer options with sleek, contemporary designs, allowing the radiators to blend seamlessly with both traditional and modern décor. This adaptability in design makes cast iron radiators highly versatile, appealing to a broad range of consumers with different tastes and preferences.
The continued demand for cast iron radiators, coupled with the improvements in technology and design, has led to a growing market for restored or refurbished radiators. In some cases, cast iron radiators that have been in service for decades can be carefully restored to their original state, including sandblasting to remove corrosion and reapplying enamel finishes. This process allows for the reuse of existing radiators, which not only preserves their aesthetic value but also extends their lifespan even further. The market for refurbished cast iron radiators has grown in recent years, as many people are drawn to the history and character they bring to a home or building.
Moreover, in large-scale commercial and industrial applications, cast iron radiators continue to be a reliable and cost-effective solution. Their high heat retention capacity and ability to maintain warmth even after the heating system is turned off make them ideal for large spaces that require consistent and long-lasting heat distribution. In industrial settings where heating systems are in continuous use, cast iron radiators are also preferred for their low-maintenance and robust nature. Their ability to withstand fluctuating temperatures, harsh environments, and high levels of wear and tear further reinforces their popularity in these settings.
While there are other radiator options on the market, such as aluminum, steel, and modern composite materials, cast iron radiators continue to stand out for their unmatched heat retention and longevity. Their heavy-duty construction and superior thermal mass ensure they will remain effective for many years, providing reliable and consistent heat. Additionally, the aesthetics of cast iron radiators continue to be a key selling point. As both functional heating systems and decorative elements, these radiators serve as a focal point in a room or building, adding character, historical value, and charm.
In conclusion, the cast iron radiator manufacturing process has undergone significant developments over the years, with ongoing innovations improving efficiency, performance, and sustainability. While the basic principles of molding, casting, and finishing remain the same, advancements in design, technology, and coatings continue to refine the overall product. Cast iron radiators remain a favored choice for those seeking reliable, long-lasting, and aesthetically pleasing heating solutions, whether in residential, commercial, or industrial applications. Their combination of functionality, durability, and visual appeal ensures that cast iron radiators will remain a staple in heating systems for years to come, contributing to both energy efficiency and comfort.
EMS Metalworking Machinery
We design, manufacture and assembly metalworking machinery such as:
- Hydraulic transfer press
- Glass mosaic press
- Hydraulic deep drawing press
- Casting press
- Hydraulic cold forming press
- Hydroforming press
- Composite press
- Silicone rubber moulding press
- Brake pad press
- Melamine press
- SMC & BMC Press
- Labrotaroy press
- Edge cutting trimming machine
- Edge curling machine
- Trimming beading machine
- Trimming joggling machine
- Cookware production line
- Pipe bending machine
- Profile bending machine
- Bandsaw for metal
- Cylindrical welding machine
- Horizontal pres and cookware
- Kitchenware, hotelware
- Bakeware and cuttlery production machinery
as a complete line as well as an individual machine such as:
- Edge cutting trimming beading machines
- Polishing and grinding machines for pot and pans
- Hydraulic drawing presses
- Circle blanking machines
- Riveting machine
- Hole punching machines
- Press feeding machine
You can check our machinery at work at: EMS Metalworking Machinery – YouTube
Applications:
Flange-punching
Beading and ribbing
Flanging
Trimming
Curling
Lock-seaming
Ribbing