
Spinning Mandrel of a CNC Metal Spinning Machine: Metal spinning, also known as spin forming or metal turning, is a process used to produce axially symmetric components by rotating a flat metal disc or tube at high speeds while applying localized pressure. This technique forms the metal into a desired shape over a mandrel, often resulting in products such as cones, hemispheres, or cylindrical forms. Its use spans industries from aerospace to automotive, due to its cost-effectiveness and ability to handle both small and large production runs with high precision.
Historical Context The origins of metal spinning date back several centuries, where artisans manually shaped metals for decorative and practical purposes. Historically, the technique was applied to metals like silver and gold to create household items such as bowls, candlesticks, and vases. However, with the advent of industrialization in the 19th and 20th centuries, metal spinning transitioned from a craft-based process to a critical manufacturing technique. With the introduction of powered lathes and automated systems, the process evolved to handle various metals and alloys, enhancing its industrial relevance.
Importance in Modern Manufacturing Today, metal spinning plays a crucial role in modern manufacturing. Its versatility allows for the production of parts across a wide array of sectors, including aerospace, automotive, medical devices, lighting, and energy. Its capacity for producing seamless, strong, and lightweight components makes it particularly valuable in industries that require high-strength, lightweight parts, such as aerospace. The process is also environmentally sustainable, as it minimizes waste compared to other metal-forming methods like casting or stamping.
Metal spinning is not a new technique. The process dates back over 2,000 years, with early examples found in ancient civilizations. Traditional metal spinning involved manually spinning a metal blank on a lathe while applying pressure with a tool to shape it. The process was labor-intensive, requiring highly skilled artisans to produce consistent and precise results.
In the early industrial age, metal spinning evolved with the advent of steam-powered lathes. This reduced some of the manual labor, though the technique still relied heavily on the operator’s skill. Metal spinning was primarily used to create items such as bowls, lampshades, and other simple hollow forms.
1.2 Transition to CNC Metal Spinning
The introduction of CNC technology in the late 20th century revolutionized metal spinning. CNC metal spinning combines the traditional method with computerized controls, allowing for greater precision, consistency, and the ability to handle complex geometries. The need for highly skilled manual operators was reduced, and the automation of processes meant that manufacturers could produce higher volumes of products with minimal human intervention.
With CNC technology, the operator now programs the spinning machine using G-code (a type of numerical control programming language). The code directs the lathe to follow a precise path, manipulating the metal blank with incredible accuracy. As a result, CNC metal spinning opened new possibilities in industries like aerospace, medical devices, automotive, and heavy machinery.
Basics of CNC Metal Spinning
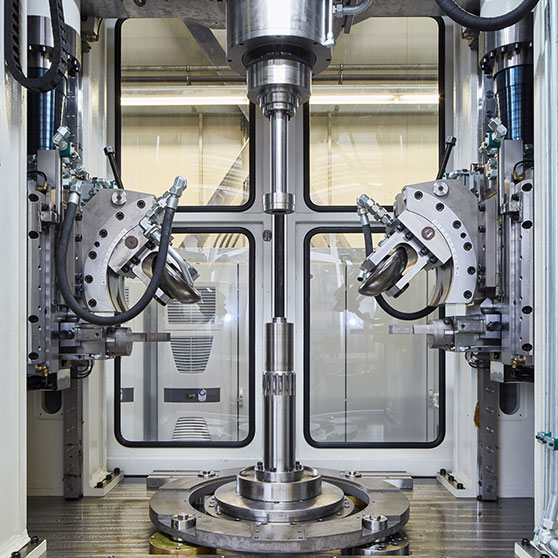
The CNC metal spinning process starts with a flat metal blank, typically circular, which is placed on a spinning lathe. Once the blank is set into motion, it rotates at high speeds. A roller tool, following a pre-programmed path, gradually forms the spinning blank into a desired shape. This transformation occurs through a series of passes, with the roller tool moving in increments to prevent tearing or warping of the material.
CNC metal spinning allows for the creation of symmetrical and asymmetrical shapes. With its ability to produce smooth, accurate, and high-quality finishes, CNC metal spinning is favored for components that require structural integrity and surface smoothness.
2.2 Key Equipment in CNC Metal Spinning
The primary equipment used in CNC metal spinning includes:
- CNC Lathe: The centerpiece of the operation, the lathe rotates the metal blank at controlled speeds.
- Roller Tool: This applies pressure to shape the blank during rotation. Different tools are used based on the material type and desired end shape.
- Clamping System: Holds the blank in place while it spins, ensuring it doesn’t move during the process.
- Computer System: Where the operator inputs the program or G-code that dictates the spinning process.
In a typical CNC metal spinning operation, the machine operator uses CAD (Computer-Aided Design) software to create a model of the component. This model is then converted into G-code, which the CNC machine reads to perform the spinning operation.
2.3 Precision and Quality Control
One of the most significant advantages of CNC metal spinning is the precision it offers. Unlike manual methods, CNC systems ensure that each piece produced is identical, meeting strict tolerances. Quality control is also improved through real-time monitoring systems, which track the machine’s performance and make automatic adjustments to prevent defects.
For industries like aerospace, medical devices, and automotive, where the reliability and precision of parts are critical, CNC metal spinning provides a superior manufacturing option.
Materials Used in CNC Metal Spinning
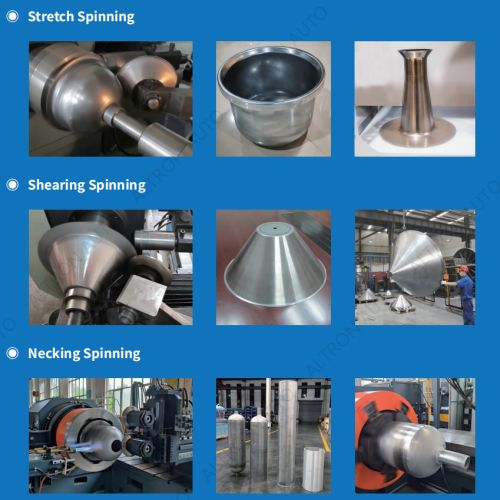
CNC metal spinning is compatible with a variety of metals, each offering unique properties. The most common materials used include:
- Aluminum: Light and highly malleable, aluminum is frequently used for applications requiring corrosion resistance and electrical conductivity, such as in aerospace and electronics.
- Stainless Steel: Known for its strength, durability, and corrosion resistance, stainless steel is used in applications like medical devices, food processing equipment, and chemical containers.
- Copper: Malleable and conductive, copper is commonly used in electrical components and heat exchangers.
- Brass: With its low friction and high resistance to corrosion, brass is ideal for mechanical components and decorative pieces.
- Titanium: Valued for its high strength-to-weight ratio and resistance to extreme temperatures, titanium is often used in aerospace and medical applications.
Each material responds differently to the metal spinning process. For example, harder metals like stainless steel require more force and precision during forming, while softer metals like aluminum can be shaped more easily but may need additional support to prevent wrinkling or distortion.
3.2 Specialty Alloys and Their Applications
Beyond traditional metals, CNC metal spinning can also accommodate a range of specialty alloys designed for specific purposes. These include:
- Inconel: A nickel-chromium alloy known for its heat and corrosion resistance, making it ideal for turbine blades and exhaust systems.
- Monel: Another nickel alloy, Monel is often used in marine and chemical processing applications due to its excellent resistance to saltwater corrosion.
- Hastelloy: Often found in chemical processing equipment, Hastelloy offers superior resistance to chemical corrosion, particularly in highly acidic environments.
The ability to work with these specialized materials has expanded the reach of CNC metal spinning, making it a versatile manufacturing method for industries requiring components with enhanced durability, heat resistance, or corrosion protection
CNC Metal Spinning Techniques and Variations
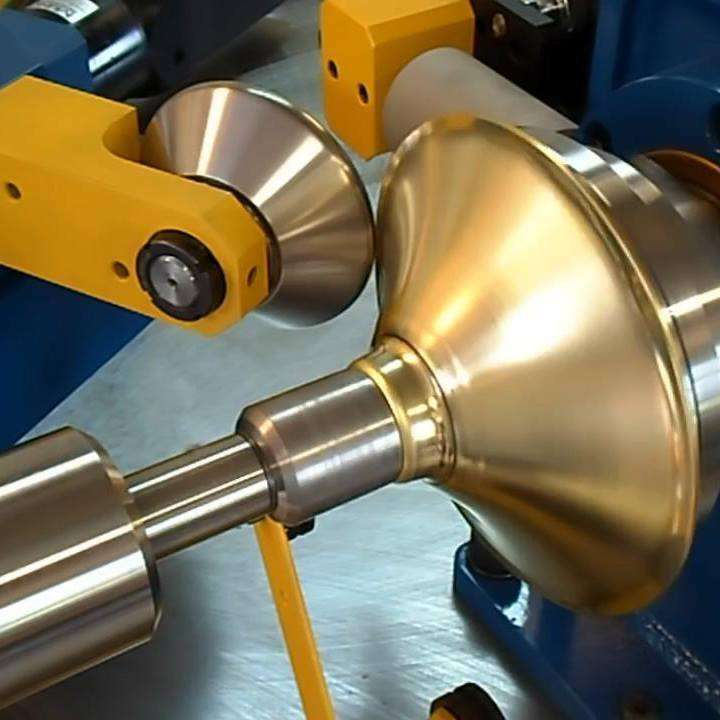
4.1 Shear Forming
Shear forming is a variation of metal spinning that changes the thickness of the metal during the spinning process. This technique is used when parts require specific thickness dimensions in different areas, such as aerospace components that need to be lightweight but strong in certain sections. Shear forming allows for the thinning of metal in some places without sacrificing overall strength.
4.2 Flow Forming
Flow forming is a more advanced variation of CNC metal spinning. It uses axial and radial forces to elongate the metal, producing cylindrical components with extremely thin walls. Flow forming is commonly used for manufacturing tubes, rocket shells, and pressure vessels. The precision offered by this method ensures that the walls of the formed part are uniformly thin, which is crucial in industries where weight reduction is key.
4.3 Hot Spinning vs. Cold Spinning
CNC metal spinning can be performed in either hot or cold conditions, depending on the material and the complexity of the shape being formed:
- Hot Spinning: The metal blank is heated before or during the spinning process. This makes it more malleable, reducing the likelihood of cracking or tearing when working with harder materials. Hot spinning is often used for metals like titanium and stainless steel.
- Cold Spinning: The metal is spun at room temperature. Cold spinning is ideal for softer metals like aluminum and copper, which don’t require the additional heat to be shaped efficiently. Cold spinning also helps to maintain the material’s mechanical properties without altering them through heating.
4.4 Multi-Pass vs. Single-Pass Spinning
CNC metal spinning can be performed using either single-pass or multi-pass techniques, depending on the desired end result. In single-pass spinning, the roller tool forms the entire shape in one continuous motion. This method is faster but less precise and is generally used for simple shapes.
In multi-pass spinning, the tool makes several passes over the blank, gradually shaping it into the final form. This method offers greater precision and is preferred for more complex shapes, where consistent thickness and structural integrity are critical.
Advantages and Limitations of CNC Metal Spinning
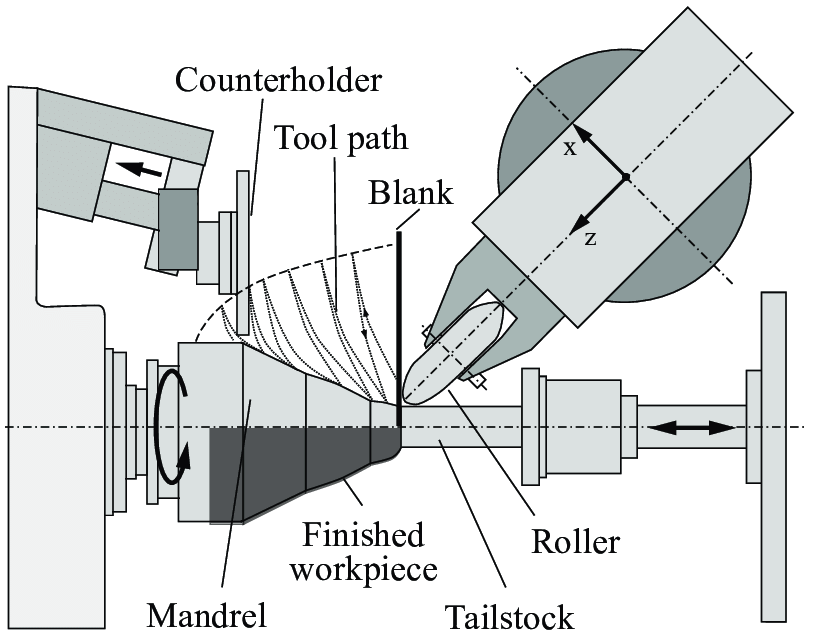
5.1 Advantages
CNC metal spinning offers several key advantages over other metal-forming techniques:
- Precision: With CNC control, manufacturers can achieve extremely tight tolerances and repeatable accuracy in production runs.
- Efficiency: CNC automation reduces the need for manual labor, speeding up production times and lowering costs.
- Versatility: The ability to work with a wide range of metals and create complex geometries makes CNC metal spinning suitable for numerous industries.
- Material Utilization: The spinning process produces very little waste, making it an environmentally friendly option.
- Structural Integrity: Spinning produces parts with smooth surfaces and consistent wall thickness, resulting in components with superior strength and durability.
5.2 Limitations
Despite its many benefits, CNC metal spinning does have some limitations:
- Initial Costs: The investment in CNC equipment and tooling can be high, which may not be economical for small production runs.
- Material Limitations: While CNC spinning works well with malleable metals, harder materials may require additional processing steps like annealing.
- Complexity Constraints: Although CNC machines can handle complex geometries, there are limitations in creating parts with extreme undercuts or sharp internal corners.
- Thickness Variability: While spinning allows for gradual thickness changes, it may not be the best choice for components that require abrupt transitions in wall thickness.
Applications of CNC Metal Spinning
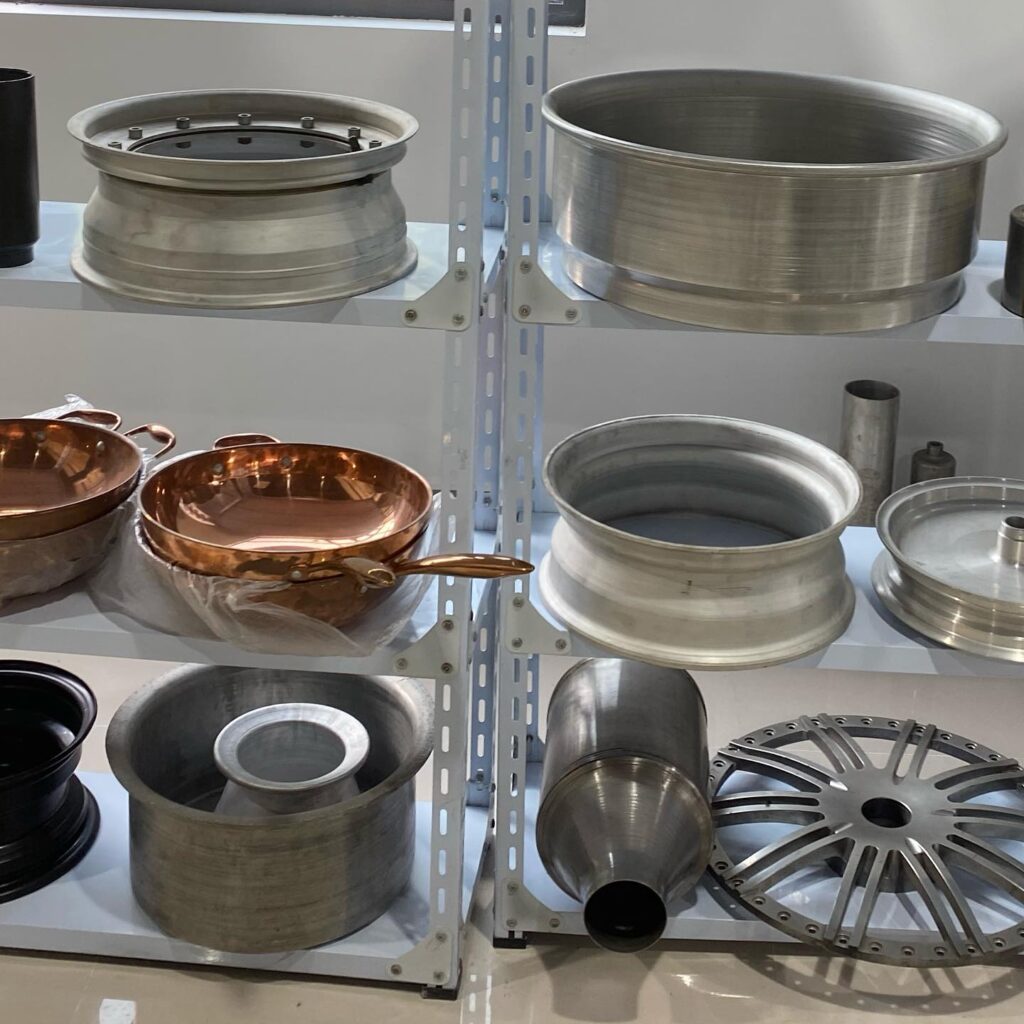
6.1 Aerospace
In the aerospace industry, where weight, precision, and durability are critical, CNC metal spinning is used to create parts such as turbine housings, nose cones, and fuel tanks. The ability to produce lightweight, thin-walled components with high structural integrity makes CNC metal spinning an ideal choice for aerospace manufacturers.
6.2 Automotive
The automotive industry benefits from CNC metal spinning in the production of components such as wheel rims, exhaust systems, and transmission parts. By utilizing spinning, manufacturers can produce high-strength parts with tight tolerances, which are essential for performance and safety in vehicles.
6.3 Medical Devices
CNC metal spinning is also prevalent in the medical field. Stainless steel and titanium, in particular, are commonly used to create surgical instruments, implantable devices, and other critical components. The precision and cleanliness of the spinning process ensure that these devices meet stringent medical standards.
6.4 Industrial and Heavy Machinery
In industrial settings, CNC metal spinning is used to create parts for heavy machinery, such as pressure vessels, pipes, and funnels. The durability and strength of spun metal components are essential in environments where high pressures and extreme temperatures are present.
CNC Metal Spinning vs. Other Metal Forming Methods
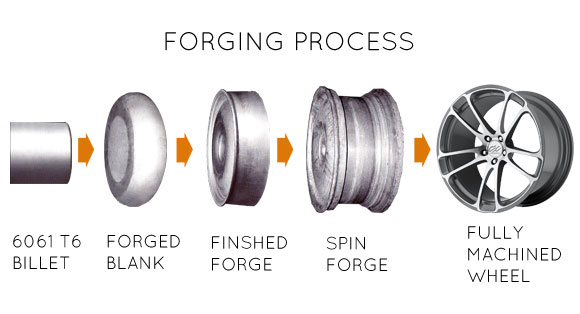
7.1 CNC Metal Spinning vs. Stamping
Stamping is another common metal-forming technique, but it differs significantly from CNC metal spinning. Stamping is ideal for high-volume production runs of small, simple parts, while CNC spinning excels in creating larger, more complex components. Stamping generally produces more waste, whereas spinning is more efficient in material usage.
7.2 CNC Metal Spinning vs. Deep Drawing
Deep drawing is a metal-forming process that stretches a metal blank into a die to create a hollow shape. While deep drawing is well-suited for high-volume production of small to medium-sized parts, CNC metal spinning offers greater flexibility in part size and geometry. Deep drawing can also result in thinning of the material, which may not be ideal for applications where uniform thickness is required.
7.3 CNC Metal Spinning vs. Forging
Forging involves heating a metal blank and applying pressure to form a part. While forging is excellent for creating parts with high strength, it lacks the precision of CNC metal spinning. Spinning is also more efficient in producing parts with complex geometries and smoother surfaces.
Innovations in CNC Metal Spinning
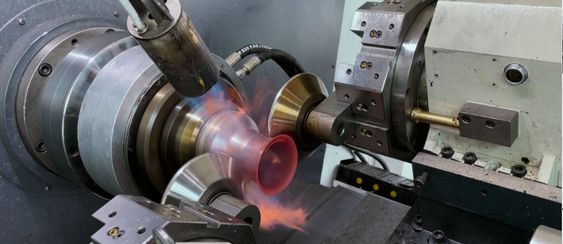
8.1 Automation and Robotics
As CNC metal spinning continues to evolve, the integration of automation and robotics is becoming more common. Automated systems can load and unload blanks, change tools, and even perform quality checks. This reduces the need for human intervention, further increasing efficiency and consistency in production.
8.2 Advanced Materials
The development of new materials, such as superalloys and composites, has expanded the capabilities of CNC metal spinning. These materials offer enhanced properties, such as heat resistance, strength, and corrosion resistance, making them ideal for advanced applications in aerospace, defense, and energy sectors.
8.3 Hybrid Manufacturing Techniques
Some manufacturers are combining CNC metal spinning with other processes, such as additive manufacturing and CNC machining, to create hybrid solutions. These hybrid techniques allow for even greater complexity in part design, combining the strengths of different manufacturing methods.
Future Trends in CNC Metal Spinning
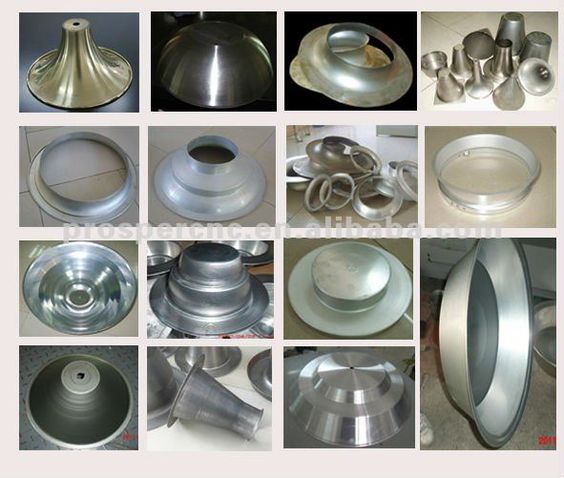
9.1 Increased Use of AI and Machine Learning
The future of CNC metal spinning is likely to see an increased integration of AI and machine learning. These technologies will allow machines to self-optimize, adjusting parameters in real-time based on sensor data and past performance. This will lead to even greater precision, faster production times, and lower defect rates.
9.2 Sustainable Manufacturing
As sustainability becomes a greater focus for manufacturers, CNC metal spinning is poised to play a role in reducing waste and energy consumption. The process already produces minimal waste, and advancements in energy-efficient machines and materials will further enhance its environmental benefits.
9.3 Expanding Applications
With continuous improvements in CNC technology and material science, new applications for CNC metal spinning are expected to emerge. The medical, renewable energy, and transportation sectors are all likely to see increased use of this versatile manufacturing process.
Conclusion
CNC metal spinning has come a long way since its manual beginnings. Today, it is a highly advanced, versatile, and efficient manufacturing process used across industries ranging from aerospace to medical devices. With ongoing advancements in technology, materials, and sustainability, CNC metal spinning is set to remain a cornerstone of modern manufacturing for years to come
The Origins and Evolution of Metal Spinning
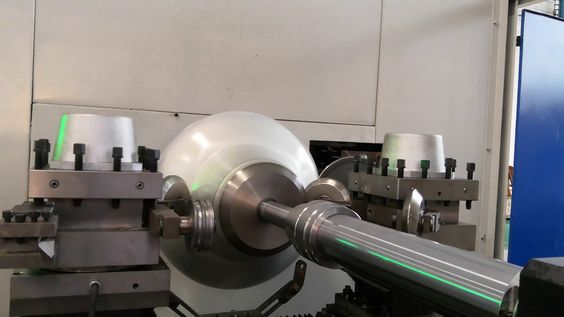
1.3 Manual vs. Modern Techniques: A Detailed Comparison
One of the most notable shifts in metal spinning technology is the move from manual techniques to modern CNC-controlled processes. Manual spinning required years of apprenticeship, where artisans developed a keen understanding of the material’s behavior, using nothing more than their experience and a set of basic tools. While this craftsmanship is still respected today, it has largely been replaced by the more efficient and accurate CNC process.
- Manual Metal Spinning:
- Dependent on operator skill and experience.
- Ideal for custom, one-off pieces or low-volume production.
- Inconsistent precision due to human error.
- High labor costs and slower production times.
- Limited complexity in part design, as intricate forms are difficult to achieve consistently.
- CNC Metal Spinning:
- Automated, ensuring consistency and high precision in mass production.
- Capable of producing both low- and high-volume parts with identical accuracy.
- Lower labor costs due to reduced manual input.
- Can handle more complex geometries, including asymmetrical shapes, which are difficult to achieve manually.
- Integrated quality control features that ensure defects are minimized during the process.
The transition from manual to CNC-based techniques has had profound effects across the manufacturing industry, providing businesses with more flexibility in product design and enabling mass production of parts that meet exacting standards.
1.4 Economic Impact of CNC Metal Spinning
CNC metal spinning has not only revolutionized manufacturing from a technical standpoint but has also had a significant economic impact. The efficiency of CNC processes has reduced production costs for manufacturers, particularly in industries that require large quantities of precision parts. This has led to price reductions in end products, benefiting both manufacturers and consumers.
Additionally, CNC metal spinning supports shorter lead times, meaning that manufacturers can respond more quickly to market demands. This is especially important in sectors like automotive and aerospace, where rapid prototyping and quick production turnaround can offer a competitive edge.
The increasing affordability of CNC equipment has made it more accessible for smaller manufacturing businesses, democratizing the production of high-quality metal components and further boosting the industry’s economic impact
3.3 Surface Treatments and Coatings
While CNC metal spinning produces parts with excellent surface finishes, some applications require additional surface treatments or coatings to enhance the durability, corrosion resistance, or aesthetic appeal of the final product. Common surface treatments and coatings used in conjunction with CNC-spun parts include:
- Anodizing: A process mainly used for aluminum, anodizing increases corrosion resistance and surface hardness. It also allows for the addition of color, making it a popular choice for decorative or branding purposes.
- Powder Coating: Powder coating provides a durable, uniform finish that protects the metal from scratches, corrosion, and wear. It’s frequently used in the automotive and consumer goods industries.
- Electroplating: This involves depositing a thin layer of metal onto the surface of the part to improve appearance, corrosion resistance, or wear resistance. Common electroplated metals include chrome, zinc, and nickel.
- Passivation: Primarily used for stainless steel, passivation is a chemical process that removes contaminants from the metal surface, improving its resistance to corrosion.
- Heat Treatments: In some cases, heat treatments are applied to increase the hardness, strength, or malleability of a spun part. This is particularly useful for metals like titanium or steel, where post-spinning heat treatments can enhance the mechanical properties of the part.
The choice of surface treatment or coating depends on the material used, the environment in which the part will operate, and the desired lifespan of the component.
3.4 Selecting the Right Material for CNC Metal Spinning
Selecting the right material for CNC metal spinning is crucial and depends on various factors, including the application of the part, the required mechanical properties, and the manufacturing budget. For instance, aerospace components often need materials that can withstand high temperatures and stresses, which makes titanium or high-performance alloys like Inconel and Hastelloy suitable choices.
By contrast, applications that prioritize corrosion resistance without needing extreme strength, such as parts for food processing or marine equipment, typically use stainless steel or aluminum. The key factors in material selection include:
- Strength-to-Weight Ratio: For applications like aerospace, lightweight materials with high strength, such as titanium, are essential.
- Corrosion Resistance: For parts exposed to harsh environments or chemicals, materials like stainless steel or copper alloys are preferred.
- Thermal Conductivity: Copper or aluminum is used in applications where heat dissipation is critical, such as in electronics or heat exchangers.
- Cost: While specialty alloys offer enhanced performance, they are typically more expensive. Manufacturers need to balance material costs with performance requirements to choose the most cost-effective solution.
Each material used in CNC metal spinning has its advantages and trade-offs, and the choice of material often dictates the complexity and cost of the manufacturing process.
CNC Metal Spinning Techniques and Variations
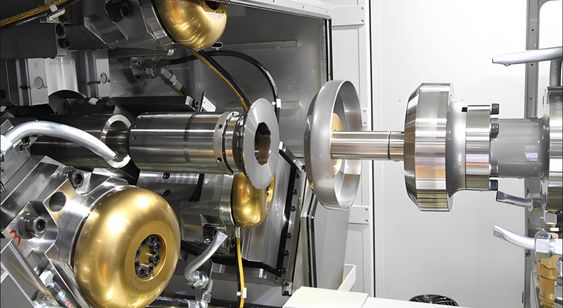
4.5 Hybrid Spinning Techniques
Hybrid techniques combine CNC metal spinning with other metal-forming processes to achieve unique results that would be difficult or impossible to attain with a single technique. These methods enhance flexibility in part design and provide additional material properties that are beneficial for specific applications.
- CNC Spinning with Deep Drawing: This hybrid method combines the precision of CNC spinning with the depth-forming capability of deep drawing. This is particularly useful for creating large, deep parts with uniform wall thicknesses and smooth transitions.
- CNC Spinning with Welding: In some cases, manufacturers combine spinning with welding techniques to produce parts that have both complex shapes and assemblies. For example, after spinning a component, a secondary welding process can be used to attach additional parts or to reinforce specific areas.
- Additive Manufacturing and CNC Spinning: Additive manufacturing (3D printing) is increasingly being combined with traditional metal-forming techniques like CNC spinning. In this hybrid approach, complex structures are first created using additive techniques, and then CNC spinning is used to refine the part, providing a high-quality finish and enhanced mechanical properties.
Hybrid techniques offer expanded possibilities for part design and material manipulation, making them ideal for cutting-edge industries like aerospace and medical device manufacturing.
4.6 Tooling Innovations
Tooling in CNC metal spinning has undergone significant advancements over the years. Traditionally, the roller tools used in the spinning process were limited in terms of shape and material. However, modern advancements in tooling materials and design have led to more versatile and durable options.
- Carbide and Diamond-Coated Tools: Tools made from carbide or coated with diamond offer increased durability and longer tool life, especially when working with hard metals like titanium or Inconel. These tools maintain their cutting edges for longer, reducing the need for frequent replacements and ensuring consistency in part quality.
- Modular Tooling: Modular tooling systems allow for quick changes between different tool heads, which enhances the flexibility of the CNC metal spinning process. This is particularly useful in high-mix, low-volume production environments where part designs may vary significantly between production runs.
- Smart Tooling Systems: New developments in “smart” tooling involve integrating sensors directly into the tooling components. These sensors monitor parameters like force, temperature, and vibration in real time, allowing for immediate adjustments to the process. This results in higher precision and reduced material waste.
Tooling innovations are key to expanding the capabilities of CNC metal spinning, enabling the production of more complex parts while reducing costs and lead times.
Advantages and Limitations of CNC Metal Spinning
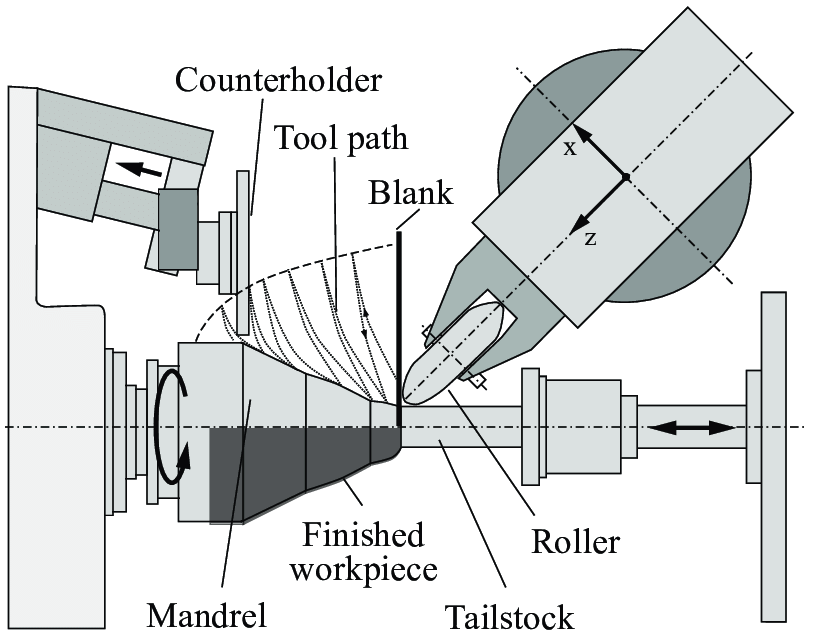
5.3 Addressing the Limitations of CNC Metal Spinning
While CNC metal spinning is a highly effective and versatile process, manufacturers have developed methods to address some of its limitations.
- Initial Costs and Small Runs: To mitigate the high initial costs of CNC equipment, many companies offer metal spinning as a service. This allows smaller manufacturers to produce spun components without investing in expensive equipment. In addition, advances in CNC technology have made smaller, more affordable machines available, increasing access to the technology.
- Material Hardness: To address the challenge of spinning harder materials, manufacturers often use a combination of pre-heating (for hot spinning) and advanced tooling materials like carbide and ceramics. These techniques reduce wear on the tooling and allow for smoother, more precise forming of difficult materials.
- Thickness Transitions: In cases where abrupt thickness changes are needed, CNC metal spinning can be combined with machining processes to fine-tune the thickness after spinning. This hybrid approach allows for the creation of parts with variable thicknesses while maintaining the structural benefits of spun metal.
By addressing these limitations through technological innovations and hybrid techniques, CNC metal spinning continues to expand its applications across industries.
5.4 Case Studies of CNC Metal Spinning Advantages
A deeper look into the real-world application of CNC metal spinning highlights the process’s advantages.
- Aerospace: A major aerospace manufacturer needed lightweight, high-strength nose cones for its aircraft. By using CNC metal spinning, they were able to produce these parts with precise wall thickness and smooth surfaces. The spun nose cones were lighter and more aerodynamic than those made using traditional forging techniques.
- Medical Devices: A medical device company required biocompatible, durable titanium parts for implantable devices. CNC metal spinning allowed them to produce these components with tight tolerances and smooth finishes, meeting the strict standards required for medical devices.
- Automotive: In the automotive sector, CNC metal spinning has been used to create lightweight exhaust systems. By reducing the thickness of certain areas without sacrificing strength, manufacturers were able to lower the overall weight of the exhaust systems, improving fuel efficiency.
These case studies demonstrate the versatility and practicality of CNC metal spinning in producing components that meet stringent requirements for performance and quality.
Applications of CNC Metal Spinning
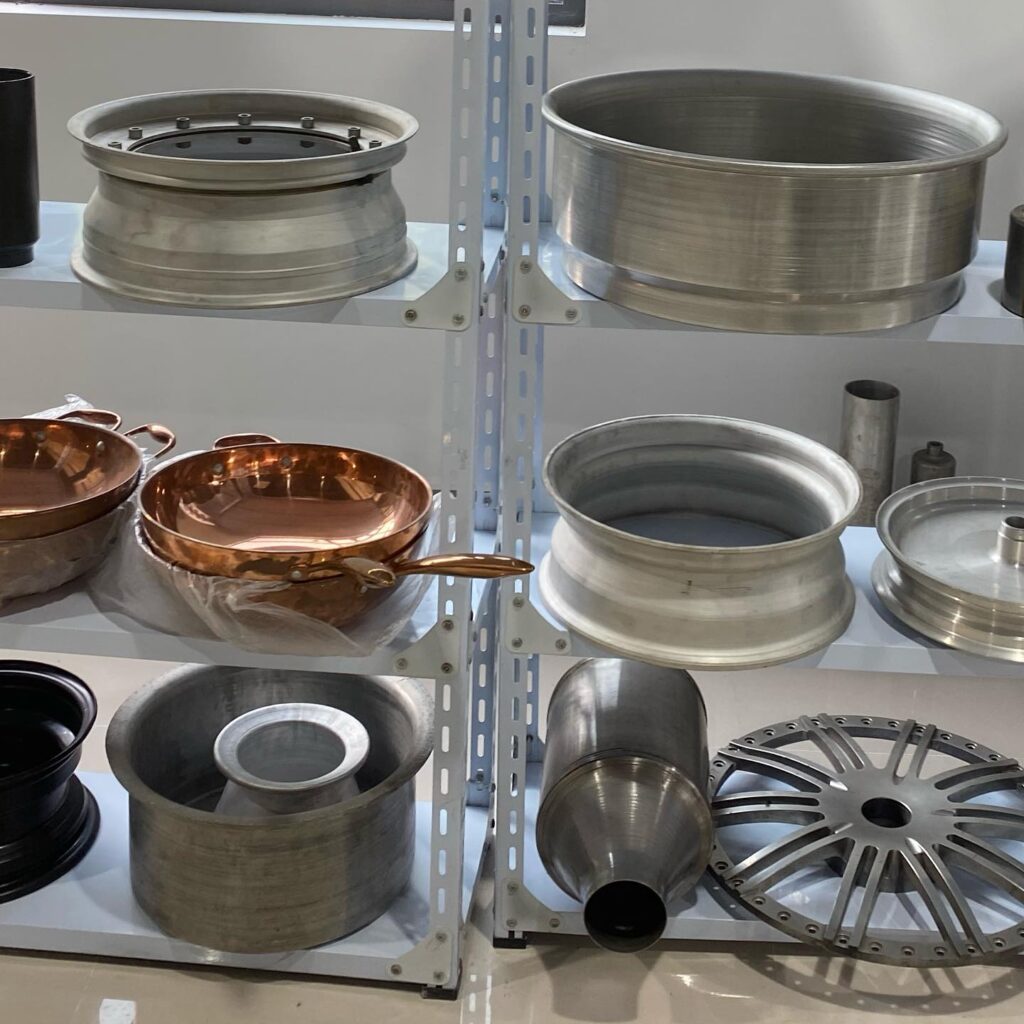
6.5 Renewable Energy
The renewable energy sector is another area where CNC metal spinning is playing a pivotal role. Components for wind turbines, solar energy collectors, and even energy storage systems can be manufactured using this process. For instance:
- Wind Turbines: The nacelles (the housing for the turbine components) and certain parts of the rotor blades can be manufactured using CNC metal spinning. This provides the necessary strength and durability to withstand extreme environmental conditions while reducing weight to improve efficiency.
- Solar Energy: Reflective dishes used in solar power generation systems often require precise geometric shapes to maximize the concentration of sunlight. CNC metal spinning is ideal for producing these components, as it ensures uniformity and surface smoothness, which are critical for optimal performance.
- Energy Storage: CNC metal spinning is also used to create pressure vessels for energy storage systems, such as compressed air energy storage (CAES) systems, where strong, lightweight materials are essential for efficient operation.
6.6 Defense and Military
CNC metal spinning is also used extensively in the defense industry to produce critical components that require high precision and durability. This includes:
- Rocket Casings: Flow-formed rocket casings are produced using CNC metal spinning techniques. These components need to be lightweight, yet strong enough to withstand the extreme forces and temperatures during launch and flight.
- Armor Components: In some cases, CNC metal spinning is used to create armor components, including protective plates for military vehicles or personnel. The process ensures that the metal is dense and strong while remaining relatively lightweight.
Future Trends in CNC Metal Spinning
9.4 Customization and On-Demand Manufacturing
As industries continue to push toward customization and on-demand manufacturing, CNC metal spinning is expected to play a key role. With CNC technology, manufacturers can quickly switch between designs, allowing for the efficient production of custom parts without the need for extensive retooling. This is especially valuable in industries where personalization is becoming a norm, such as:
- Automotive: Customized car parts, from exhaust systems to wheels, are becoming more popular among consumers. CNC metal spinning allows manufacturers to meet this demand with high precision.
- Consumer Goods: For items like cookware, lighting fixtures, or even furniture, CNC metal spinning offers a way to produce unique, high-quality designs with minimal lead time.
- Medical Devices: The ability to create custom implants and instruments tailored to individual patients is a significant advancement in the medical field. CNC metal spinning, combined with other manufacturing techniques, will continue to support personalized healthcare solutions.
The trend toward customization is driving innovation in CNC metal spinning, as manufacturers seek to meet the growing demand for tailored, on-demand products.
CNC Metal Spinning vs. Other Metal Forming Methods
7.4 CNC Metal Spinning vs. Hydroforming
Hydroforming is another method used to shape metals into complex geometries, especially in industries that require high precision and structural integrity. However, there are key differences between CNC metal spinning and hydroforming:
- Process Differences: Hydroforming uses high-pressure hydraulic fluid to press metal blanks into a die, forming the desired shape. In contrast, CNC metal spinning applies mechanical force via rollers to shape the metal on a rotating lathe.
- Tooling Costs: Hydroforming typically requires expensive dies, making it less cost-effective for small runs or custom projects. CNC metal spinning, on the other hand, requires simpler tooling setups, which reduces upfront costs and makes it more economical for lower production volumes or prototyping.
- Material Thickness: While both processes can handle a range of material thicknesses, hydroforming is often more suitable for very thin materials, as the high-pressure fluid evenly distributes force across the metal surface. CNC metal spinning can produce thinner walls but might require multiple passes or more advanced techniques, such as shear forming, to achieve similar results.
- Flexibility in Design: CNC metal spinning offers greater flexibility in terms of part design. With spinning, parts can be adjusted or reprogrammed quickly using the CNC system, which is ideal for applications requiring frequent design changes or customization. Hydroforming is generally more suited for high-volume production with stable designs due to the high cost of creating dies for each specific shape.
7.5 CNC Metal Spinning vs. Casting
Casting is a widely used metal-forming process where molten metal is poured into a mold and allowed to cool, taking the shape of the mold. While both casting and CNC metal spinning are used for producing parts, they differ significantly in several key areas:
- Complexity of Shape: Casting is excellent for creating highly intricate shapes with internal geometries, undercuts, and fine details that would be difficult to achieve with CNC spinning. However, casting can result in rougher surfaces and may require post-processing to smooth out the part.
- Surface Finish: CNC metal spinning, on the other hand, typically produces smoother surface finishes right out of the process, with little to no need for secondary machining or finishing operations. This makes it ideal for applications that require high-quality surface finishes, such as reflective components in lighting or aesthetic pieces in consumer products.
- Strength and Durability: While cast parts can have complex geometries, they are often more brittle due to the nature of the cooling process, which can introduce internal stresses and microfractures. CNC-spun parts, in contrast, maintain the inherent strength of the metal due to the mechanical deformation process, which can actually improve the grain structure of the metal, resulting in stronger, more durable components.
- Lead Times: Casting involves longer lead times, especially if custom molds are required. CNC metal spinning, with its flexible tooling and faster setup times, is more suited for projects where quick turnaround is needed.
Each of these metal-forming processes has its own set of advantages and limitations, and the choice between them depends largely on the specific requirements of the part being manufactured, such as the complexity of the shape, the mechanical properties needed, and the budget for tooling and production.
7.6 CNC Metal Spinning vs. Roll Forming
Roll forming is a continuous process used to shape long strips of metal into desired cross-sectional profiles. Here’s how it compares to CNC metal spinning:
- Material Usage: Roll forming is typically used for large volumes of long, uniform sections like beams, rails, or structural supports. It excels in producing parts with constant profiles over long lengths. In contrast, CNC metal spinning is used to create axially symmetric shapes, such as cones, hemispheres, and cylindrical components, making it ideal for hollow parts.
- Production Speed: Roll forming is generally faster than CNC metal spinning, especially for high-volume runs of simple, repetitive shapes. However, the setup costs for roll forming are higher due to the complex tooling required, whereas CNC metal spinning allows for quick retooling and can accommodate more custom shapes without significant setup changes.
- Precision: CNC metal spinning provides tighter tolerances for complex geometries, especially when creating parts with varying wall thicknesses. Roll forming is better suited for parts that require consistent cross-sectional shapes over long lengths but may not provide the same level of precision for complex designs.
- Versatility: CNC metal spinning offers greater versatility in terms of design, material options, and production runs. While roll forming is limited to continuous shapes, CNC metal spinning can create diverse, hollow, and varying designs from a single blank, making it more adaptable for custom manufacturing projects or specialized industries like aerospace and medical devices.
Innovations in CNC Metal Spinning
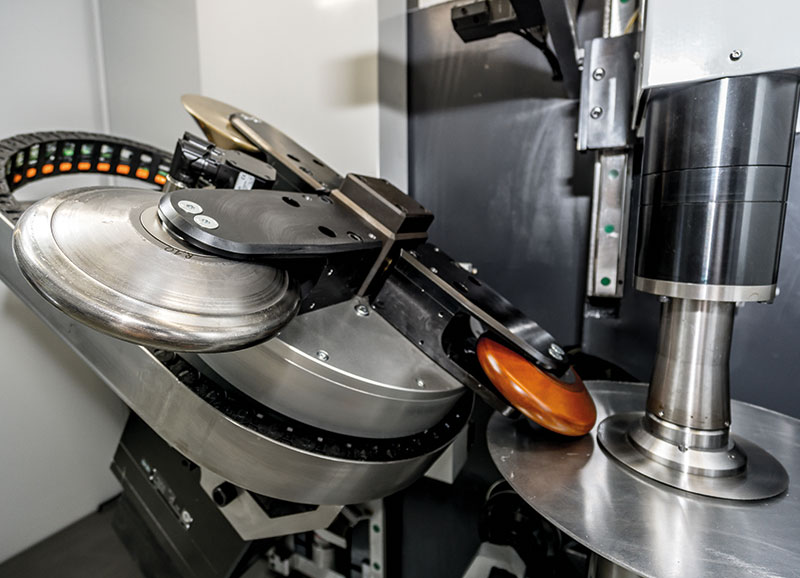
8.4 Integration of CAD/CAM Software
One of the key innovations driving CNC metal spinning technology is the integration of advanced CAD (Computer-Aided Design) and CAM (Computer-Aided Manufacturing) software. These systems allow engineers and designers to create highly detailed models of the parts they need, which can then be translated directly into CNC programming code for the spinning machines. The integration of CAD/CAM software into CNC metal spinning has several benefits:
- Enhanced Precision: Designers can create highly complex geometries in 3D CAD software, ensuring that the final part meets exact specifications. CAM software then translates these designs into G-code that the CNC machine uses to accurately form the metal part.
- Reduced Prototyping Time: With CAD/CAM, engineers can simulate the entire spinning process before the part is produced, identifying potential issues or inefficiencies in the design. This virtual prototyping significantly reduces the time and cost associated with physical prototyping and helps ensure that the first production run is successful.
- Customization Capabilities: For industries like automotive or consumer goods, where customized parts are increasingly in demand, CAD/CAM integration allows for easy adjustments to design files, enabling rapid reprogramming of the CNC machine for different part configurations.
- Data-Driven Manufacturing: The integration of CAD/CAM systems with CNC metal spinning opens up new possibilities for data-driven manufacturing. Engineers can analyze production data in real-time, fine-tuning processes to optimize material usage, minimize waste, and ensure consistency across production runs.
8.5 AI-Powered Optimization
The integration of artificial intelligence (AI) and machine learning into CNC metal spinning is another cutting-edge development that is set to revolutionize the industry. AI algorithms can analyze vast amounts of data collected from CNC machines during the spinning process, allowing the system to make real-time adjustments to the speed, force, and path of the spinning tool. This leads to several benefits:
- Predictive Maintenance: AI systems can predict when a machine is likely to experience wear or breakdown based on historical data. This allows manufacturers to perform maintenance before issues arise, reducing downtime and avoiding costly repairs.
- Process Optimization: AI-powered systems can optimize the spinning process by continuously learning from previous production runs. The AI adjusts parameters to improve efficiency, reduce material waste, and ensure higher-quality parts with fewer defects.
- Customizable Tolerances: AI can help fine-tune tolerances on complex parts, dynamically adjusting the process as needed. This is particularly useful in industries like aerospace and medical devices, where precision is critical and tolerances are extremely tight.
As AI continues to evolve, its integration with CNC metal spinning will only deepen, further enhancing the precision, speed, and efficiency of the manufacturing process.
8.6 Green Manufacturing and Sustainability
Sustainability is becoming an increasingly important consideration in manufacturing, and CNC metal spinning is no exception. Several innovations are helping to make the process more environmentally friendly:
- Material Efficiency: One of the inherent advantages of CNC metal spinning is its minimal waste. Unlike machining, which often involves cutting away material, metal spinning transforms a flat blank into a finished part with very little excess material. New advances in simulation software allow manufacturers to further optimize material usage, reducing waste even more.
- Energy-Efficient Machinery: Modern CNC machines are being designed with energy efficiency in mind. Innovations in motor technology, lubrication systems, and automation have resulted in machines that consume less energy while maintaining high levels of productivity.
- Recycling and Circular Economy: Many manufacturers are now incorporating recycled metals into their production processes. CNC metal spinning can easily accommodate recycled materials, which helps reduce the environmental impact of mining and processing new metals. Additionally, the end products created through CNC spinning can be recycled at the end of their life cycle, contributing to a circular economy.
These innovations are positioning CNC metal spinning as a leader in sustainable manufacturing, ensuring that the process remains competitive in a world where environmental responsibility is increasingly important.
Future Trends in CNC Metal Spinning
9.5 Advanced Materials and Their Potential
The future of CNC metal spinning is closely tied to advancements in material science. As new alloys and composites are developed, CNC metal spinning machines will need to adapt to handle these advanced materials, offering new possibilities for performance and application:
- Superalloys: The development of superalloys, such as Inconel, Hastelloy, and Waspaloy, is allowing for the creation of parts that can withstand extreme temperatures and corrosive environments. These materials are critical in industries such as aerospace, nuclear power, and chemical processing. CNC metal spinning is well-positioned to form these superalloys into complex shapes with precision, making it a valuable tool for manufacturers in these sectors.
- Metal Matrix Composites (MMCs): Metal matrix composites combine metals with other materials (such as ceramics or carbon fibers) to create parts that are both lightweight and incredibly strong. CNC metal spinning is being adapted to handle these materials, which are particularly useful in aerospace, automotive, and defense applications where weight reduction without compromising strength is a priority.
- Biodegradable Metals: In the medical field, researchers are developing biodegradable metals, such as magnesium alloys, for use in implants that dissolve in the body after they have fulfilled their purpose. CNC metal spinning can help shape these materials into precise medical devices, opening new possibilities for temporary implants that do not require surgical removal.
These material advancements will drive the future of CNC metal spinning, as manufacturers look for ways to combine strength, durability, and lightweight properties with sustainability and performance in extreme conditions.
9.6 Industry 4.0 and the Smart Factory
CNC metal spinning is set to be a critical part of the “Industry 4.0” revolution, where smart factories use interconnected systems, real-time data, and automation to enhance production capabilities:
- IoT Integration: In the smart factory, CNC machines are connected to the Internet of Things (IoT), enabling real-time communication between machines, sensors, and software. This allows for automated adjustments to the spinning process based on live data, reducing errors and ensuring optimal performance at all times.
- Digital Twins: One emerging concept in Industry 4.0 is the use of digital twins—virtual replicas of physical machines. Manufacturers can simulate the CNC spinning process in a digital environment, allowing them to predict outcomes, troubleshoot potential issues, and optimize processes before they are implemented on the shop floor.
- Full Automation: With advancements in robotics and AI, the future CNC metal spinning factory will likely see full automation, where machines handle everything from material loading to quality inspection without human intervention. This will further reduce production times and improve accuracy, especially for high-volume, precision-demanding industries.
The integration of CNC metal spinning into smart manufacturing environments will enhance productivity, reduce costs, and position the industry for the future of advanced manufacturing.
Fundamentals of Metal Spinning
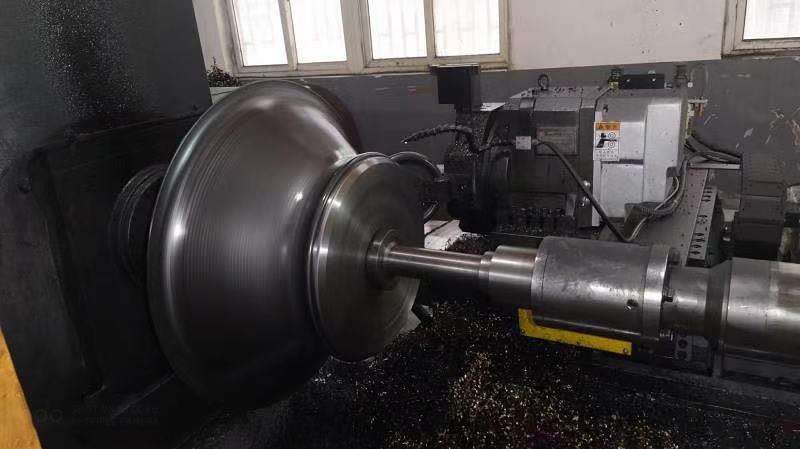
Metal spinning, also known as spin forming or metal turning, is a manufacturing process used to produce axially symmetric parts by rotating a metal workpiece around a central axis and shaping it with a tool. This technique has been used for centuries, dating back to ancient civilizations where manual spinning techniques were employed to form basic metal components. Over time, metal spinning has evolved significantly, from being a craft-based manual process to a highly automated and precision-controlled operation, incorporating computer numerical control (CNC) machines for complex and accurate shaping.
The basic concept of metal spinning remains simple: a flat metal disc, referred to as a blank, is clamped onto a rotating mandrel that mirrors the desired shape. Using rollers or other tools, the metal is incrementally formed around the mandrel as it spins at high speed, resulting in components that are typically round or conical. The process is highly adaptable, suitable for producing parts in a wide range of sizes, thicknesses, and materials.
Traditional vs. Modern Metal Spinning
Historically, metal spinning was a labor-intensive process, requiring highly skilled craftsmen to shape the workpiece by hand. The artisan would rely on their experience to apply force uniformly across the workpiece to achieve a smooth finish. While the basic tools were simple (rollers, levers, and mandrels), the skill needed to maintain consistency made traditional spinning a respected craft.
In contrast, modern metal spinning employs advanced machinery, including CNC systems, which allow for precision forming without the need for direct human intervention. CNC metal spinning machines can produce intricate and consistent parts with tight tolerances, revolutionizing the industry and enabling the production of complex components in large quantities.
Industrial Applications
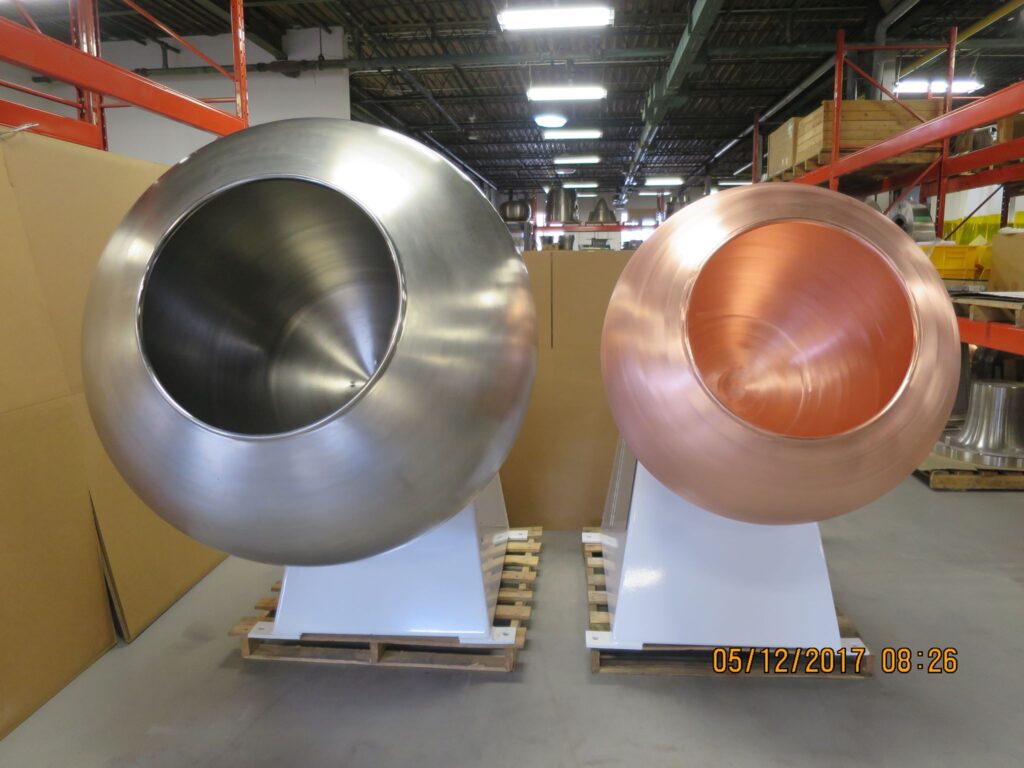
Metal spinning is extensively used in various industries, where it delivers components with superior strength, excellent surface finish, and minimal material waste. Here are some key industrial sectors where metal spinning plays a crucial role:
- Aerospace Industry: The aerospace sector relies heavily on metal spinning for creating lightweight, durable components such as rocket nose cones, turbine housings, and air intake parts. The high precision and strength-to-weight ratio of spun metal components make them ideal for aircraft and spacecraft applications.
- Automotive Industry: In automotive manufacturing, metal spinning is utilized to produce various parts, including wheel rims, brake discs, and exhaust systems. The process provides cost-effective manufacturing solutions for both mass production and custom-designed components.
- Lighting and Architecture: Metal spinning is frequently used to create light fixtures, decorative architectural elements, and reflectors. Its ability to produce seamless, symmetrical shapes lends itself well to aesthetic and functional applications in buildings and industrial lighting systems.
- HVAC (Heating, Ventilation, and Air Conditioning): HVAC systems often utilize metal spinning to manufacture parts such as fan housings, ductwork components, and blower wheels, where air-tight seals and durability are essential.
Advantages of Metal Spinning
Metal spinning offers several key benefits, which have contributed to its continued use and advancement in modern manufacturing processes:
- Material Efficiency and Waste Reduction: One of the most significant advantages of metal spinning is its efficiency in material usage. Unlike other manufacturing processes like stamping or milling, which often result in significant material wastage, metal spinning works by deforming a metal blank into the desired shape without removing excess material. This leads to higher material utilization rates and cost savings, particularly in large-scale production runs.
- Versatility and Production Flexibility: Metal spinning is highly versatile, capable of producing a wide range of shapes and sizes, from small parts like bells and vases to large components such as satellite dishes and tank ends. Furthermore, the process can accommodate different materials, including aluminum, stainless steel, copper, and brass. Whether for prototype production or large-scale manufacturing, metal spinning can adapt to varying production requirements.
- Enhanced Strength and Durability: During the spinning process, the material is subjected to significant compressive forces, which improve the mechanical properties of the final component. This results in a finished product with higher tensile strength, greater resistance to fatigue, and improved durability, making it suitable for applications where structural integrity is critical.
- Reduced Tooling Costs: Compared to other metal forming processes like deep drawing or forging, metal spinning requires relatively low-cost tooling. The process generally requires only a mandrel and simple rollers, reducing the need for expensive dies and molds. This makes it an economical choice, especially for low- to medium-volume production.
The Metal Spinning Process
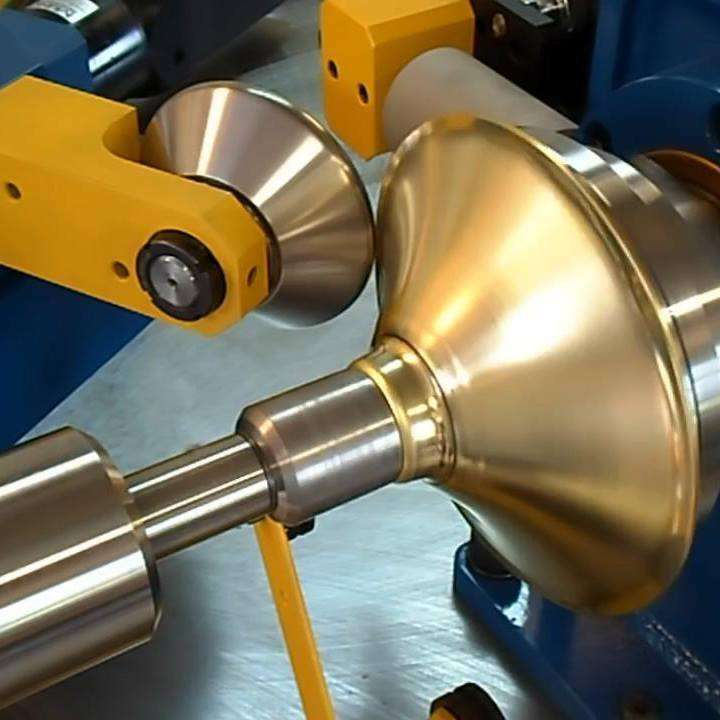
The metal spinning process involves shaping a metal blank into a cylindrical or conical form by applying pressure while rotating the material on a lathe or specialized spinning machine. Though the equipment used today is highly sophisticated, the core principles remain the same as those employed centuries ago. The process can be broken down into several key stages:
- Preparation:
- The first step in metal spinning is selecting the appropriate metal blank. The material is chosen based on the final component’s design requirements, including factors such as strength, ductility, and corrosion resistance. The blank, typically circular and flat, is clamped onto a mandrel that reflects the desired final shape.
- Prior to spinning, the blank may undergo surface treatments such as cleaning, annealing, or coating, depending on the material type and intended use. These treatments ensure that the material can be spun efficiently and with minimal defects.
- Spinning:
- The actual spinning begins once the blank is secured on the mandrel. The mandrel rotates at high speed, and the operator (or CNC machine) applies pressure to the blank using a forming tool, usually a roller. The force causes the metal to flow and conform to the mandrel’s shape, gradually forming the component’s desired geometry.
- Several passes are often required, starting with rough passes to approximate the final shape, followed by finer passes to achieve the desired precision. The process is typically done in a lubricated environment to reduce friction and heat generation, improving surface finish and tool life.
- Finishing:
- After the spinning process is complete, the component may require secondary operations such as trimming, cutting, polishing, or heat treatment. Trimming removes excess material from the edges, while polishing enhances the surface finish. For some applications, further treatments such as anodizing, painting, or powder coating may be applied to improve corrosion resistance or aesthetic appeal.
- Finally, quality checks are performed to ensure that the part meets the required tolerances for size, thickness, and surface quality.
Types of Metal Spinning
There are various metal spinning techniques, each tailored to produce specific types of components and meet particular manufacturing requirements. The key types are as follows:
- Conventional Spinning:
- Conventional spinning, also known as hand spinning, is the most basic form of the process. In this method, the metal blank is spun and formed over a mandrel using rollers or forming tools. The process typically does not involve thinning of the material but instead maintains its original thickness throughout the forming process. This technique is ideal for producing symmetrical parts with simple geometries, such as cones, cylinders, and hemispheres.
- Applications include decorative items, lighting fixtures, and certain automotive components.
- Shear Spinning:
- Shear spinning, also known as power spinning, is an advanced form of metal spinning where the material is deliberately thinned as it is formed. Unlike conventional spinning, where the material retains its original thickness, shear spinning involves a reduction in wall thickness while maintaining the diameter of the blank. This is achieved by applying additional pressure during the spinning process.
- Shear spinning is commonly used for producing components such as missile cones, rocket casings, and other high-strength, lightweight structures.
- Flow Forming:
- Flow forming is a specialized spinning technique used to produce long, thin-walled cylindrical parts, such as tubes and pressure vessels. This method involves pressing a preformed tube or blank against a mandrel while it rotates, progressively reducing its wall thickness while extending its length.
- Flow forming allows for precise control over material thickness and results in a stronger, more uniform structure than conventional processes. It is frequently used in aerospace, defense, and automotive industries for parts such as hydraulic cylinders, drive shafts, and pressure vessels.
- Tube Spinning:
- Tube spinning is a subset of flow forming where tubular blanks are spun and elongated to produce thin-walled cylinders. This process is highly efficient for manufacturing high-strength, lightweight tubular components.
- Applications include automotive parts such as drive shafts and transmission components, as well as specialized pipes for the oil and gas industry.
Materials Used in Metal Spinning
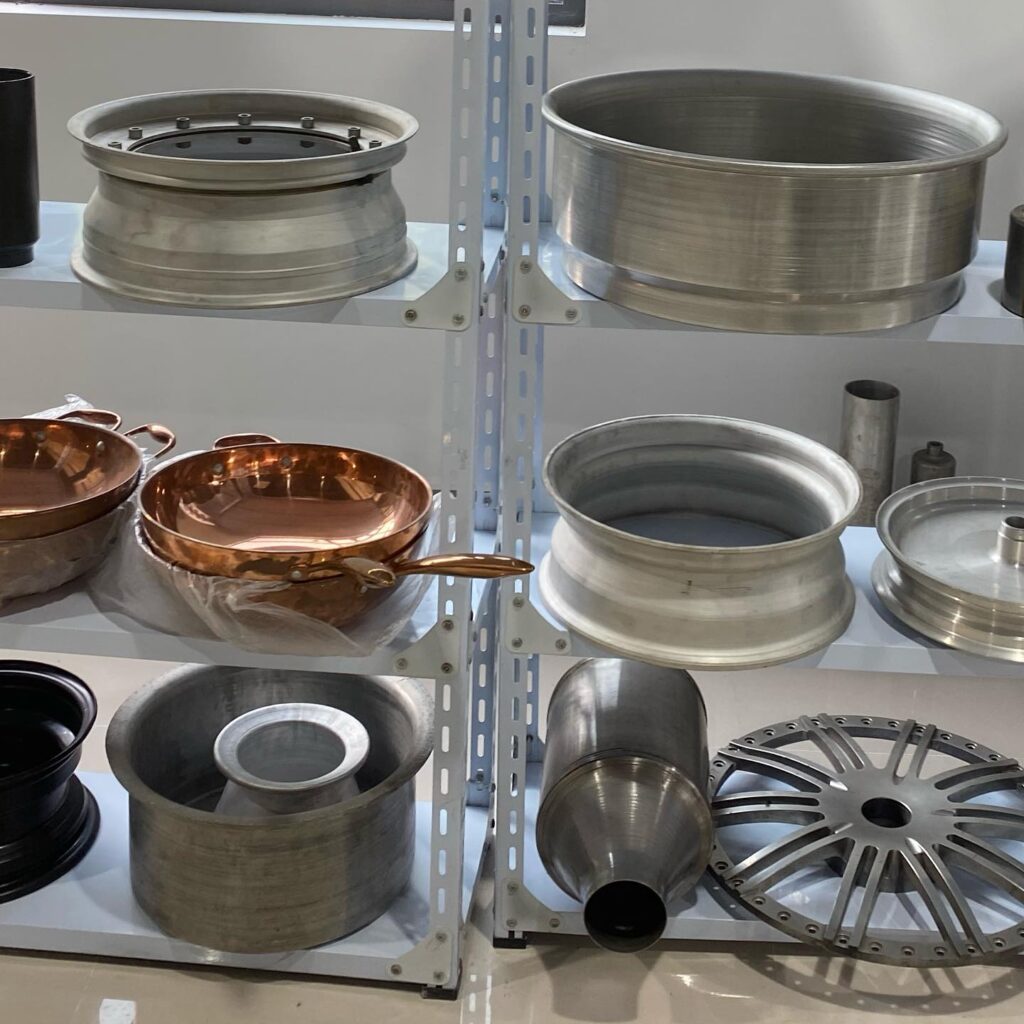
The metal spinning process is highly adaptable to a variety of metals and alloys. The material chosen for a specific application depends on factors such as required strength, corrosion resistance, and thermal properties. Some commonly used materials include:
- Aluminum:
- Aluminum is one of the most commonly spun metals due to its high strength-to-weight ratio, corrosion resistance, and ease of formability. It is used in aerospace, automotive, and decorative applications where lightweight and durability are key considerations.
- Stainless Steel:
- Stainless steel is valued for its corrosion resistance and mechanical strength. It is often used in industries where components must withstand harsh environmental conditions, such as in chemical processing, food and beverage, and marine applications. Due to its toughness, spinning stainless steel requires more force and specialized equipment.
- Copper:
- Copper offers excellent thermal and electrical conductivity, making it ideal for applications in the electronics and energy sectors. It is also highly formable and often used for decorative and architectural components due to its aesthetic appeal.
- Brass:
- Brass is frequently used in decorative and architectural applications because of its bright appearance and formability. Its resistance to corrosion also makes it suitable for use in marine environments.
- Titanium:
- Titanium is favored in aerospace and medical industries due to its exceptional strength, light weight, and biocompatibility. However, spinning titanium can be more challenging due to its high strength and low formability, requiring specialized equipment and processes.
Quality Control and Precision
In metal spinning, achieving dimensional accuracy and maintaining surface quality are critical, particularly for industries such as aerospace and medical manufacturing, where tight tolerances and high precision are necessary.
- Dimensional Tolerance:
- The metal spinning process can achieve high precision in component dimensions, but maintaining tight tolerances depends on various factors, including tool design, machine calibration, and operator skill (in manual spinning). CNC metal spinning machines are particularly useful for producing parts with consistent accuracy across large production runs.
- Surface Finish:
- A good surface finish is vital in applications where the part’s appearance or functionality (such as fluid dynamics) is essential. Surface defects like roughness, scratches, or marks can arise during the spinning process due to tool wear or improper lubrication. Post-processing operations such as polishing and surface coating are used to improve the finish where necessary.
- Non-Destructive Testing (NDT):
- For critical components, such as those used in aerospace or medical applications, non-destructive testing methods like ultrasonic inspection or X-ray imaging are employed to detect internal flaws without damaging the component. These tests ensure that the finished product meets the required structural and performance standards.
Metal Spinning Machines: An Overview
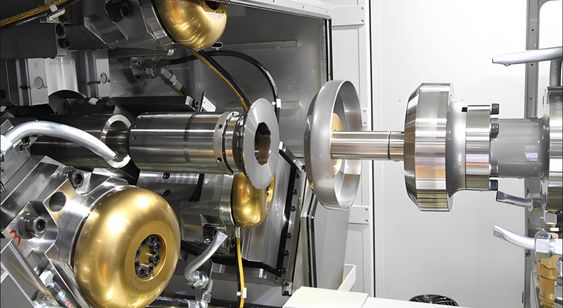
Metal spinning machines play a critical role in transforming flat metal blanks into symmetrical, three-dimensional shapes. The machinery used in metal spinning ranges from simple manual lathes to highly advanced CNC-controlled systems that allow for precision manufacturing at scale. Depending on the complexity of the part being produced, the type of machine used can vary significantly in terms of size, speed, and capability.
At the most basic level, a metal spinning machine consists of a rotating spindle or mandrel, where the metal blank is clamped, and a tool or roller that shapes the material. The mandrel spins at high speed while the tool presses the material onto the mandrel to form the desired shape. Machines are typically categorized based on their degree of automation, configuration (manual or CNC), and specific applications (conventional, shear, or flow spinning).
- Manual vs. Automated (CNC-Controlled) Machines:
- Manual metal spinning machines are the traditional equipment used in small-scale production or for prototyping. They rely on the skill of the operator to control the pressure and speed during the spinning process, making them highly flexible but labor-intensive.
- CNC metal spinning machines, on the other hand, are fully automated and computer-controlled, offering enhanced precision, repeatability, and efficiency. CNC machines are programmed using CAD/CAM software, allowing operators to create complex part geometries with minimal manual intervention. These machines are essential in modern manufacturing, particularly in industries requiring high precision and large production volumes, such as aerospace and automotive.
Key Components of Metal Spinning Machines
While there are various configurations of metal spinning machines, they all share a set of fundamental components that make the spinning process possible. Understanding these key components is essential for optimizing machine performance, ensuring quality output, and conducting routine maintenance.
- Headstock and Tailstock:
- The headstock houses the spindle, which holds the mandrel and rotates at high speed during the spinning process. The headstock must be rigid and stable to ensure precise spinning without vibrations, which can cause surface defects.
- The tailstock supports the other end of the workpiece, keeping the blank or preform in place during spinning. The tailstock can move along the bed to accommodate different lengths and sizes of workpieces, ensuring proper alignment throughout the process.
- Tooling Systems (Roller and Mandrel):
- The mandrel is one of the most critical components of the machine. It serves as the mold or template that the metal blank conforms to during spinning. Mandrels are typically made from durable materials such as hardened steel or aluminum, depending on the specific metal being spun and the complexity of the part.
- Rollers or other forming tools apply pressure to the blank, causing it to flow and take the shape of the mandrel. The rollers are mounted on a tool post, which can be manually or automatically controlled, depending on the machine type. Rollers must be designed to reduce friction and prevent marking on the metal surface.
- Bed and Frame:
- The bed is the foundation of the metal spinning machine, providing support for the headstock, tailstock, and tooling systems. It must be sturdy and well-aligned to ensure smooth operation. Some machines feature adjustable beds that can accommodate different part sizes and configurations.
- The frame of the machine must be rigid to minimize vibrations during the spinning process, as even slight movement can compromise part quality. High-performance machines use heavy-duty steel frames to maximize stability.
- Drive Systems:
- The drive system powers the rotation of the spindle and is typically controlled by an electric motor. CNC machines utilize servo motors for precise control over spindle speed and acceleration, while manual machines may rely on more basic motor setups.
- Advanced CNC systems allow for variable speed control, which is essential for spinning different materials and achieving the desired surface finish and dimensional accuracy.
Machine Configurations and Capabilities
Metal spinning machines come in various configurations, each suited for specific production needs. Understanding these configurations helps manufacturers choose the right machine for their application, whether for prototyping, mass production, or working with specialized materials.
- Vertical vs. Horizontal Configurations:
- Horizontal spinning machines are the most common type, where the workpiece is mounted on a horizontal spindle. These machines are versatile and can handle a wide range of part sizes and shapes, making them the go-to option for general metal spinning applications.
- Vertical spinning machines, while less common, are used for specific applications where gravity assists in the shaping process or where vertical clamping is more efficient for the workpiece geometry. These machines are often used for spinning large, heavy components such as pressure vessels.
- Load Capacities and Maximum Spindle Speeds:
- The capacity of a metal spinning machine is determined by its maximum spindle speed and the size of the workpiece it can accommodate. Machines designed for thin-walled, lightweight components require higher spindle speeds, sometimes exceeding 3,000 RPM. In contrast, machines used for thick-walled parts or heavy materials operate at lower speeds but with higher torque.
- Load capacity also refers to the maximum force that the machine can exert on the blank during spinning. Machines designed for shear spinning or flow forming often feature hydraulic or servo-driven systems that can apply significant pressure without damaging the material.
- Machine Adaptability for Different Materials:
- Different metals require different machine setups due to variations in material properties such as ductility, strength, and hardness. Machines designed for spinning aluminum, for instance, operate at higher speeds and require less force compared to machines that spin stainless steel or titanium, which require more robust motors and stronger frames to handle the increased stress.
- Advanced machines can be customized with interchangeable mandrels, rollers, and tailstock assemblies to accommodate a variety of materials and part sizes. CNC machines are particularly adaptable, with software-controlled settings that adjust tool paths and spinning parameters based on the material being processed.
Advantages of Modern Metal Spinning Machines
The advancements in metal spinning machine technology have brought numerous advantages to modern manufacturing. These benefits make metal spinning a competitive and cost-effective choice for many industries:
- Precision and Repeatability:
- CNC-controlled metal spinning machines offer unparalleled precision, capable of producing parts with tight tolerances and consistent dimensions across large production runs. By eliminating human error, these machines ensure repeatability, making them ideal for industries such as aerospace, automotive, and medical manufacturing, where accuracy is critical.
- Efficiency and Speed:
- Automated machines, especially those integrated with CNC systems, drastically reduce production times. Once programmed, the machine can execute the spinning process with minimal operator intervention, allowing for faster cycle times and higher throughput.
- In addition, modern machines are equipped with multiple tooling stations and automatic tool changers, further enhancing efficiency by reducing setup times between production runs.
- Versatility:
- Modern metal spinning machines are highly versatile, capable of producing parts with a wide range of sizes, shapes, and materials. The ability to spin everything from small, intricate components to large, heavy-duty parts makes these machines adaptable to diverse applications.
- Furthermore, the integration of hybrid technologies, such as combining spinning with other forming processes (e.g., stamping or deep drawing), has expanded the scope of what can be achieved with metal spinning machines.
- Cost Savings:
- Although the initial investment in CNC metal spinning machines can be high, the long-term cost savings are significant due to increased efficiency, reduced labor costs, and lower material waste. In particular, the ability to produce parts with minimal material waste makes metal spinning an eco-friendly and economical manufacturing process, particularly for high-strength alloys and expensive metals.
Types of Metal Spinning Machines
Metal spinning machines come in various types, each tailored to specific manufacturing needs, material properties, and production scales. The diversity of machine types ensures that the metal spinning process can meet the demands of various industries, from custom, low-volume production to high-precision, mass-manufactured components. Below are the main categories of metal spinning machines:
Manual Spinning Machines
Manual metal spinning machines represent the traditional approach to spin forming, requiring an experienced operator to manually guide the forming tools as the blank spins. These machines are relatively simple in design but demand a high level of craftsmanship and expertise to produce consistent, quality parts.
- Operation:
- The operator manually applies pressure using a hand-held forming tool or lever. The workpiece is spun on a lathe, while the operator progressively shapes the metal against a mandrel.
- Manual machines often have limited automation and rely heavily on the operator’s ability to maintain uniform pressure and speed throughout the spinning process.
- Applications:
- Manual spinning machines are typically used for small-scale production, custom parts, or prototyping. They are ideal for creating simple shapes such as bowls, cones, and hemispheres, often for decorative, artistic, or bespoke industrial applications.
- Advantages:
- Flexibility: Manual machines can quickly be set up for small production runs or one-off parts.
- Cost-Effective for Low Volume: Without the need for expensive CNC programming or tooling, manual machines are more affordable for low-volume or customized jobs.
- Limitations:
- Operator Skill Dependent: Achieving consistent quality requires a highly skilled operator, as variations in force application or speed can lead to defects.
- Limited Complexity: Manual spinning is best suited for simpler geometries, as complex shapes and tight tolerances are challenging to achieve without automation.
CNC Metal Spinning Machines
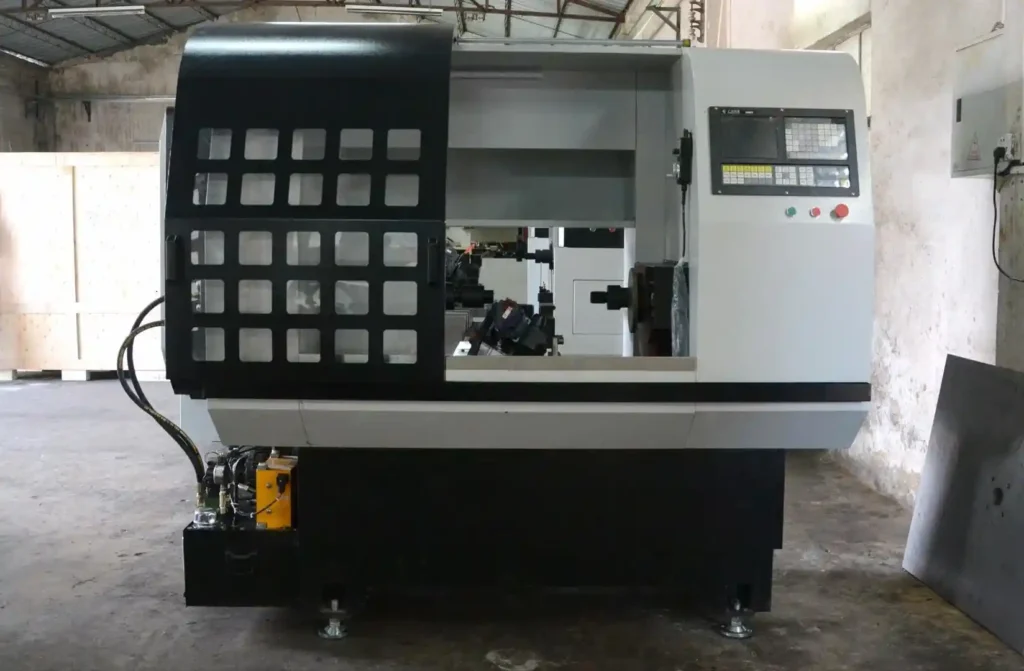
CNC (Computer Numerical Control) metal spinning machines have revolutionized the industry by providing high levels of precision, repeatability, and efficiency. These machines are fully automated and capable of producing intricate parts with minimal human intervention, making them the industry standard for large-scale manufacturing and complex geometries.
- Operation:
- CNC machines are controlled by software, which directs the motion of the spinning tool and the spindle. The operator programs the machine using CAD/CAM software, which generates the necessary G-code for the machine to follow.
- The CNC system controls factors such as spindle speed, tool position, and the amount of force applied during the spinning process. This precision allows for the production of parts with tight tolerances and consistent quality across multiple production runs.
- Applications:
- CNC metal spinning machines are used in industries that require high-precision components, such as aerospace, automotive, medical devices, and defense. Typical applications include aircraft nose cones, satellite dishes, automotive wheels, and high-performance exhaust systems.
- Advantages:
- Precision and Accuracy: CNC machines can produce parts with extremely tight tolerances and smooth surface finishes. The automated nature of these machines reduces the risk of human error, ensuring high-quality output.
- Repeatability: Once programmed, CNC machines can produce identical parts consistently, making them ideal for high-volume production.
- Complex Geometries: CNC systems are capable of producing intricate and complex shapes that would be difficult or impossible to achieve manually.
- Limitations:
- Initial Investment: CNC metal spinning machines are expensive, both in terms of the equipment itself and the programming required. However, this cost is offset by the efficiency and precision offered by the machines, especially in high-volume production.
- Programming Expertise: While the machine performs the spinning automatically, creating and optimizing the CNC program requires technical expertise in CAD/CAM and knowledge of the material being spun.
Hydraulic Metal Spinning Machines
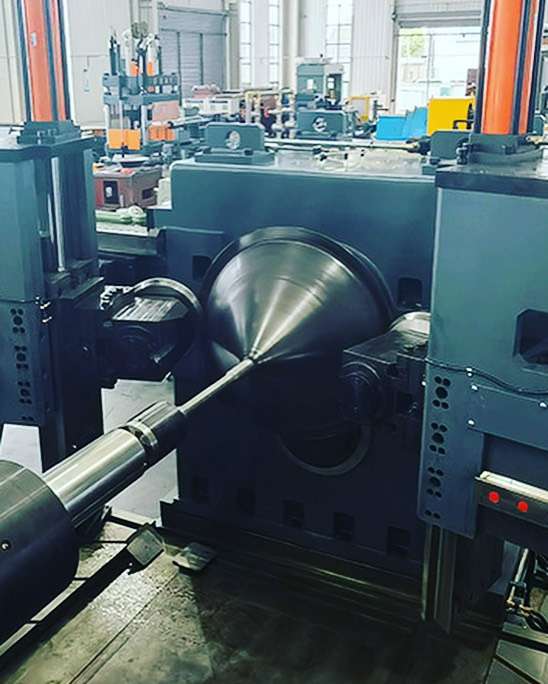
Hydraulic metal spinning machines utilize hydraulic pressure to control the forming tool and apply force to the spinning workpiece. These machines are especially useful for spinning materials that are difficult to shape, such as high-strength alloys, where greater force is required. The hydraulic system allows for precise control over the pressure applied to the workpiece, ensuring uniform material deformation and consistency.
- Operation:
- Hydraulic spinning machines rely on hydraulic cylinders to drive the spinning tools. These machines often feature both manual and automatic controls, allowing operators to fine-tune the process as needed.
- The hydraulic system can be programmed to apply variable pressure during the spinning process, which is particularly useful for materials that exhibit work hardening or require gradual forming.
- Applications:
- Hydraulic spinning machines are used in the production of parts that require significant forming forces, such as large pressure vessels, gas cylinders, and heavy-duty automotive or aerospace components.
- These machines are also suitable for spinning high-strength materials like titanium, stainless steel, and high-strength alloys.
- Advantages:
- High Force Capacity: Hydraulic systems allow for greater control over the amount of force applied, making them ideal for spinning thicker, harder materials.
- Precision Pressure Control: The ability to precisely adjust the forming pressure improves material consistency and reduces the risk of cracking or warping.
- Limitations:
- Slower Cycle Times: Hydraulic systems typically operate more slowly than CNC or manual machines due to the time required to apply and adjust pressure.
- Cost: Hydraulic spinning machines are more expensive than manual machines but generally more affordable than high-end CNC systems.
Single-Head vs. Double-Head Machines
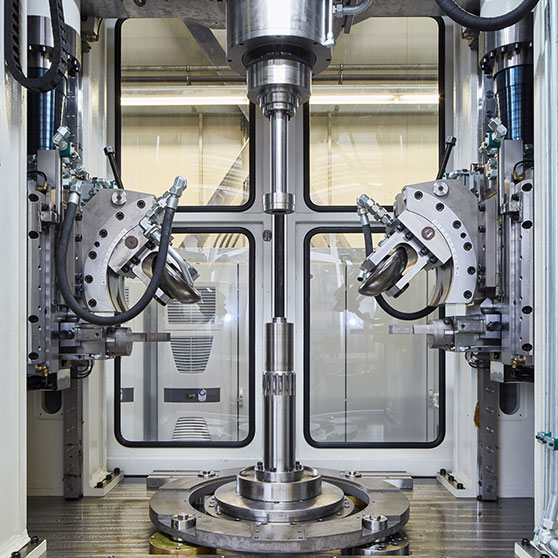
The configuration of metal spinning machines can be classified into single-head and double-head designs, depending on how the tooling is arranged. This configuration impacts the machine’s ability to handle certain types of parts and materials.
- Single-Head Spinning Machines:
- In single-head machines, there is only one set of tools and a single spindle that rotates the workpiece. These machines are commonly used for conventional spinning processes and are suitable for parts with simpler geometries.
- Applications: Single-head machines are typically used for producing items such as bowls, cones, and cylindrical parts that do not require complex forming or intricate detailing.
- Advantages:
- Cost-Effective: Single-head machines are generally more affordable and simpler to operate, making them ideal for low-volume production.
- Simplicity: Their straightforward design means fewer components and less maintenance.
- Limitations:
- Limited to Simple Shapes: Single-head machines struggle with more complex geometries and may require multiple passes or additional tooling to achieve intricate shapes.
- Double-Head Spinning Machines:
- Double-head spinning machines are equipped with two sets of tools that work simultaneously, allowing for more complex shaping and forming. These machines are used for producing parts with detailed geometries or requiring precision on both sides of the workpiece.
- Applications: Double-head machines are ideal for applications where symmetrical or highly detailed parts are required, such as certain aerospace or automotive components.
- Advantages:
- Increased Precision: With two heads working in unison, double-head machines can form more complex parts in fewer passes, improving production efficiency.
- Enhanced Versatility: Double-head machines can handle more intricate parts, making them suitable for advanced applications where complex shapes and high precision are required.
- Limitations:
- Higher Cost: Double-head machines are more expensive due to their advanced tooling and dual-head configuration.
- More Complex Setup: These machines require careful calibration and setup, particularly for complex parts.
Specialized Spinning Machines
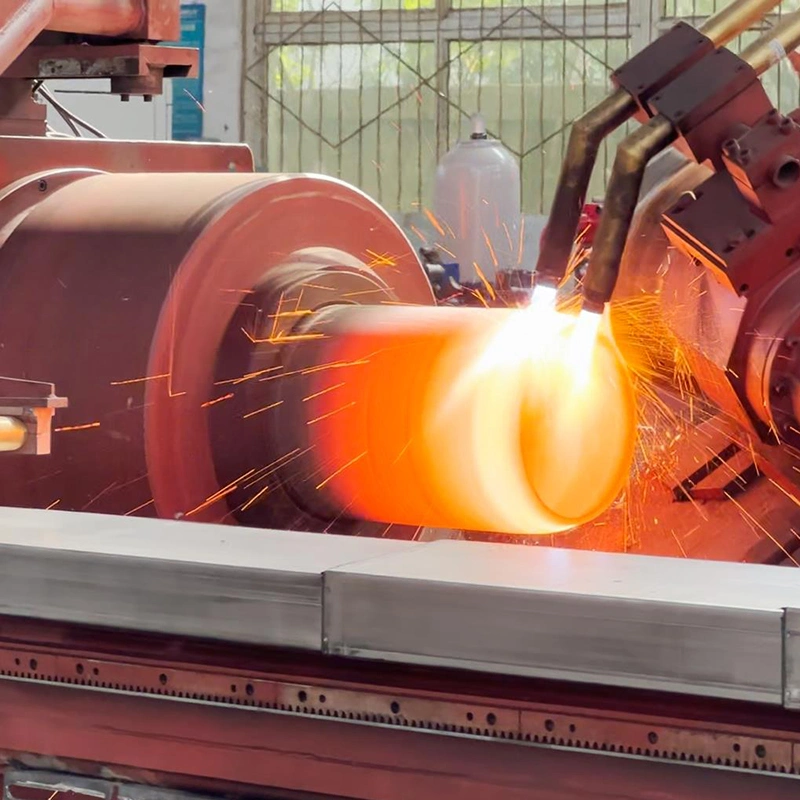
In addition to the general-purpose machines outlined above, there are specialized metal spinning machines designed for specific processes or industry requirements. These machines are typically customized for tasks such as shear spinning, flow forming, or spinning specific materials.
- Shear Spinning Machines:
- These machines are designed to perform shear spinning, a process that reduces the thickness of the workpiece while maintaining its diameter. Shear spinning is commonly used for producing lightweight, high-strength parts with reduced wall thickness, such as rocket cones or pressure vessels.
- Advantages: Shear spinning machines are ideal for applications where weight reduction is critical without compromising structural integrity.
- Flow Forming Machines:
- Flow forming is a specialized spinning process that produces thin-walled cylindrical parts by elongating the workpiece. Flow forming machines are used for manufacturing parts such as tubular structures, pressure vessels, and automotive drive shafts.
- Advantages: These machines are highly efficient at producing cylindrical parts with uniform wall thickness, offering high precision and material strength.
- Tube Spinning Machines:
- Tube spinning machines are used for forming tubular components with thin walls and precise dimensions. These machines are essential for applications such as exhaust systems, hydraulic cylinders, and structural tubing.
- Advantages: Tube spinning machines excel at producing components with consistent wall thickness, high strength, and excellent surface finish.
CNC Metal Spinning Technology

The advent of Computer Numerical Control (CNC) technology has brought significant advancements to the field of metal spinning. CNC metal spinning machines are at the forefront of modern manufacturing, providing precision, efficiency, and automation that traditional manual methods cannot match. This section delves into the architecture, functionality, and benefits of CNC metal spinning technology, along with the challenges it presents.
CNC Machine Architecture and Functionality
CNC metal spinning machines are automated systems driven by digital instructions that dictate the movements and actions of the spinning tools. The architecture of CNC metal spinning machines integrates multiple components designed to work in synchronization for precise shaping of metal parts.
- Spindle Motors:
- The spindle motor is a crucial component of the CNC metal spinning machine, responsible for driving the rotation of the mandrel and the workpiece. High-performance CNC machines often use servo motors to provide variable speed control and maintain consistent torque throughout the spinning process.
- Servo motors offer precise control over the spindle speed, allowing operators to adjust the speed based on the material being spun and the complexity of the part’s geometry.
- Servo Systems:
- In CNC machines, the servo system controls the positioning and movement of the forming tools. Servo motors enable precise, real-time adjustments to tool position, pressure, and speed, ensuring that the spinning process adheres to the programmed specifications.
- Servo-driven systems also allow for greater flexibility in shaping complex geometries, which would be difficult to achieve using manual methods.
- Tooling Mechanism:
- The CNC machine’s tooling mechanism includes rollers, forming tools, and the tool post. These components are controlled via the CNC program to apply the correct force and motion during the spinning process.
- In advanced CNC machines, multiple tools can be used simultaneously, with automatic tool changers to reduce downtime between operations. This multi-tool functionality enables more efficient production and minimizes the need for manual intervention during part forming.
- Drive Systems:
- CNC metal spinning machines typically employ a combination of electric and hydraulic drive systems to power the spindle and control the forming tools. The drive system must be robust enough to handle the forces generated during spinning, particularly for hard materials like stainless steel or titanium.
- High-end machines incorporate hybrid systems, where electric motors control the spindle and hydraulic cylinders provide additional force for the forming tools, allowing for maximum control over both speed and pressure.
- Control Interface:
- The control interface is the user’s point of interaction with the CNC system. Operators use this interface to program the machine, input design parameters, and monitor the spinning process. Modern CNC machines feature intuitive touch-screen controls and user-friendly software that simplifies programming and troubleshooting.
- Many CNC metal spinning machines are now equipped with real-time feedback systems, enabling operators to adjust parameters during the spinning process based on material behavior or tool wear.
CNC Programming for Metal Spinning
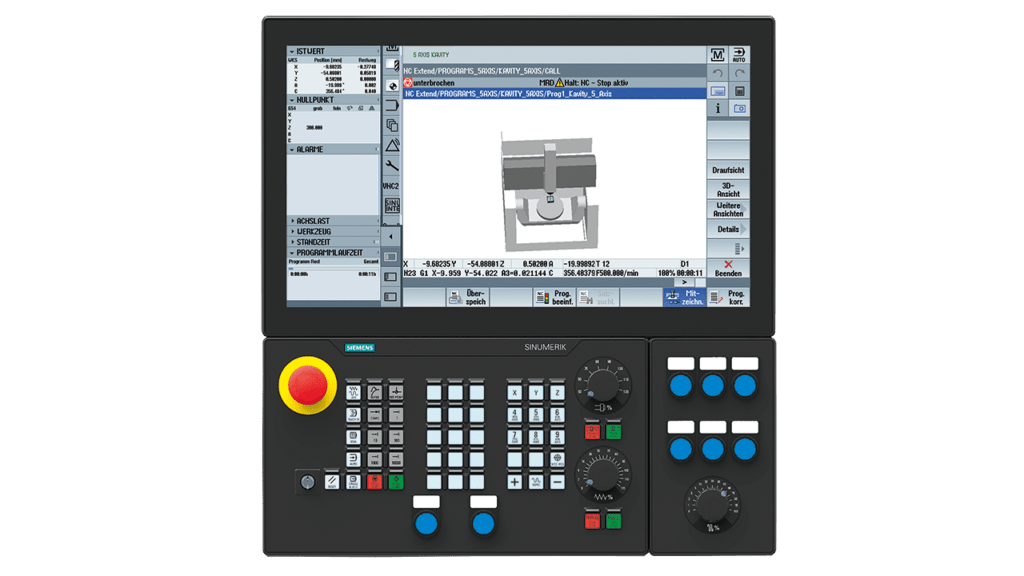
CNC metal spinning machines rely on sophisticated software to program and execute the spinning process. Operators use computer-aided design (CAD) and computer-aided manufacturing (CAM) software to generate the digital instructions that control the machine’s movements.
- G-Code Programming:
- The primary language for CNC machines is G-code, which provides instructions for tool movements, spindle speeds, and other parameters. G-code is generated from CAD models, which define the desired geometry of the part.
- In metal spinning, G-code must account for several critical factors, including material thickness, tool positioning, and the speed of rotation. The software translates the CAD model into a series of commands that direct the CNC machine to follow a precise tool path, shaping the metal to the desired form.
- CAD/CAM Integration:
- CAD/CAM software plays an essential role in CNC metal spinning. The design of the part is first created in CAD, after which the CAM system generates the tool paths and operational instructions for the machine.
- Advanced CAM systems can simulate the spinning process before manufacturing begins, allowing engineers to identify potential issues, such as tool collisions, excessive material thinning, or surface defects. This simulation capability reduces errors and enhances the efficiency of the production process.
- Customization for Materials and Part Geometries:
- CNC programs must be customized based on the material being spun and the complexity of the part geometry. For example, when spinning ductile materials like aluminum, the G-code will dictate faster spindle speeds and lower tool forces. Conversely, for harder materials like stainless steel, slower speeds and higher forces will be programmed to prevent material failure.
- CNC programming also allows for the creation of complex, non-symmetrical geometries, which would be challenging or impossible to achieve manually. By adjusting the tool path dynamically, CNC machines can form intricate shapes with high precision and repeatability.
Advantages of CNC in Metal Spinning
The transition from manual to CNC metal spinning has brought numerous benefits, making CNC machines a vital component of modern manufacturing processes. Below are some of the key advantages of CNC technology in metal spinning:
- Increased Repeatability and Precision:
- One of the most significant benefits of CNC metal spinning is the ability to produce parts with extreme precision. CNC machines follow programmed tool paths with minimal deviation, ensuring that every part produced is consistent in size, shape, and surface quality.
- This level of precision is especially important in industries like aerospace, medical, and automotive, where dimensional accuracy and repeatability are critical. CNC systems can maintain tolerances as tight as a few microns, far beyond what can be achieved with manual spinning.
- Reduced Labor and Operator Error:
- CNC machines require less manual intervention than traditional manual spinning machines. Once programmed, the CNC system executes the spinning process autonomously, allowing operators to focus on monitoring the machine rather than manually controlling the process.
- By automating the spinning process, CNC technology reduces the risk of human error, leading to fewer defects and less material waste. This is particularly beneficial in high-volume production environments, where the cost of defects can be significant.
- Flexibility in Prototyping and Production:
- CNC metal spinning machines are highly flexible, capable of producing one-off prototypes or large production runs with minimal setup changes. This makes CNC spinning ideal for industries that require rapid prototyping and iterative design processes, such as aerospace or automotive manufacturing.
- The ability to quickly reprogram the machine for different parts reduces downtime and improves overall productivity. Manufacturers can switch between different part designs without needing to overhaul the machine’s tooling or setup.
- Complex Geometries:
- CNC technology allows for the creation of highly complex geometries that would be difficult or impossible to achieve using manual methods. By precisely controlling the tool path, CNC machines can produce intricate shapes, including non-circular and asymmetrical parts.
- This capability is essential for industries that require advanced part designs, such as medical implants, turbine components, and custom architectural features.
- Integration with Industry 4.0 and IoT Systems:
- CNC metal spinning machines are increasingly being integrated into Industry 4.0 and Internet of Things (IoT) systems, allowing for real-time data monitoring, predictive maintenance, and process optimization.
- By connecting CNC machines to a network, manufacturers can gather data on machine performance, tool wear, and production output. This data can be used to identify inefficiencies, reduce downtime, and improve overall manufacturing processes.
Challenges in CNC Spinning
Despite the many advantages, CNC metal spinning also presents several challenges that manufacturers must address to maximize the benefits of the technology.
- Toolpath Optimization for Thin-Walled Components:
- One of the challenges in CNC metal spinning is optimizing the tool path for thin-walled components. If the tool applies too much pressure or moves too quickly, it can cause the material to warp or crack, especially in metals with low ductility.
- Engineers must carefully program the CNC machine to balance speed, force, and material properties, ensuring that the part maintains its structural integrity throughout the spinning process.
- Material Properties and Behavior:
- Different metals behave differently during the spinning process, and CNC machines must account for these variations. For instance, softer metals like aluminum are more forgiving, while harder metals like titanium or stainless steel require precise control over spindle speed, tool pressure, and lubrication to prevent defects.
- CNC programming must be customized for each material, requiring in-depth knowledge of metallurgy and the mechanical properties of the workpiece.
- Balancing Speed and Precision:
- While CNC machines can operate at high speeds, achieving the right balance between speed and precision is essential. In some cases, operating too quickly can compromise the surface finish or dimensional accuracy of the part.
- Engineers must optimize the CNC program to strike the right balance between efficient production and maintaining quality standards. This often requires extensive testing and simulation before full-scale production can begin.
- Initial Setup and Costs:
- CNC metal spinning machines represent a significant investment in terms of both hardware and software. In addition, creating and optimizing CNC programs for complex parts can be time-consuming and require specialized skills.
- For small manufacturers or those with limited production needs, the high upfront cost and learning curve of CNC machines may be prohibitive, though the long-term benefits of increased productivity and precision often justify the expense.
Tooling for Metal Spinning Machines
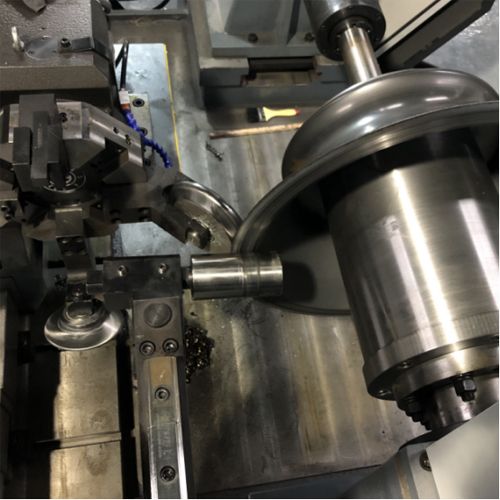
Tooling plays a critical role in metal spinning, directly impacting the quality, precision, and efficiency of the final product. The proper selection and design of tooling components, including mandrels, rollers, and dies, are crucial for achieving the desired part geometry and surface finish. This section explores the different types of tooling used in metal spinning, the material considerations for tooling components, and best practices for tool maintenance.
Types of Tooling
In the metal spinning process, tooling primarily refers to the mandrels and rollers that shape the workpiece. The tooling configuration can vary significantly depending on the part’s geometry, material, and production volume.
- Mandrels:
- Mandrels are the core of the tooling system in metal spinning. They provide the form or mold around which the metal blank is shaped. Mandrels are typically made of durable materials that can withstand the forces exerted during the spinning process, such as hardened steel or aluminum. The mandrel must be precision-engineered to match the exact dimensions of the final part.
- Types of Mandrels:
- Solid Mandrels: Used for standard shapes like cones, cylinders, and hemispheres. Solid mandrels are machined to the desired shape and are commonly used in conventional spinning.
- Segmented Mandrels: These are used when complex geometries or larger components are required. Segmented mandrels consist of multiple parts that can be assembled into intricate shapes, allowing for more flexibility in part design.
- Air-Cooled or Water-Cooled Mandrels: For materials that generate a lot of heat during spinning (such as titanium or stainless steel), mandrels can be equipped with cooling systems. These cooling systems prevent thermal distortion, which could affect part precision and surface finish.
- Rollers:
- Rollers, also known as forming tools, are used to apply pressure to the metal blank, forcing it to conform to the shape of the mandrel. Rollers are typically mounted on tool posts, which control their position and movement during the spinning process. The design and material of the rollers can affect the final surface finish and overall part quality.
- Types of Rollers:
- Round Rollers: The most common type of roller, used for general-purpose spinning where smooth, uniform pressure is needed.
- Flat Rollers: These rollers are designed to create sharp corners or edges on the workpiece. They are commonly used for producing parts with angular features.
- Beading Rollers: Beading rollers are specialized tools used to create beads or ridges on the workpiece, often seen in decorative or architectural applications.
- Dies and Tooling Fixtures:
- While dies are more commonly associated with stamping and forging, they can also be used in some metal spinning applications, particularly for flow forming or shear spinning. In these cases, the die is used to control the material flow and ensure uniform thickness along the workpiece.
- Tooling fixtures such as clamps and supports are used to hold the blank securely in place during the spinning process. Proper clamping and fixture design are essential for preventing slippage and ensuring accurate, repeatable results.
Tool Material Considerations
The material used for tooling components must be carefully selected to balance durability, performance, and cost. The key factors in selecting tooling materials include wear resistance, strength, and the ability to withstand the heat and forces generated during spinning.
- Steel:
- Steel is the most commonly used material for mandrels and rollers due to its strength, durability, and wear resistance. Hardened steel is particularly well-suited for applications where high forces are applied, such as when spinning harder metals like stainless steel or titanium.
- Steel rollers can be surface-treated with coatings such as chrome plating or nitriding to improve wear resistance and reduce friction during the spinning process.
- Aluminum:
- Aluminum is often used for tooling when spinning softer metals like aluminum alloys or copper. Aluminum mandrels are lighter and easier to machine than steel, making them a cost-effective option for lower-volume production runs or prototypes.
- However, aluminum is not as durable as steel, and it is more prone to wear and deformation over time, especially when used with harder metals.
- Carbide and Ceramic Tooling:
- For extreme wear resistance and high-precision applications, carbide or ceramic tooling can be used. These materials are much harder than steel and can maintain their shape and cutting edge for longer periods, even under high stress and heat.
- Carbide rollers are ideal for precision spinning, where surface finish and dimensional accuracy are critical. However, carbide is brittle and can crack if subjected to excessive impact or stress.
- Tool Coatings:
- Coatings such as titanium nitride (TiN), diamond-like carbon (DLC), or chromium can be applied to tooling surfaces to improve hardness, reduce friction, and increase wear resistance. These coatings are especially beneficial for high-volume production, where tooling must withstand extended use without degradation.
- Coated tooling is commonly used in CNC metal spinning, where high-speed operations and tight tolerances demand superior wear resistance and minimal friction.
Tool Design for CNC Spinning
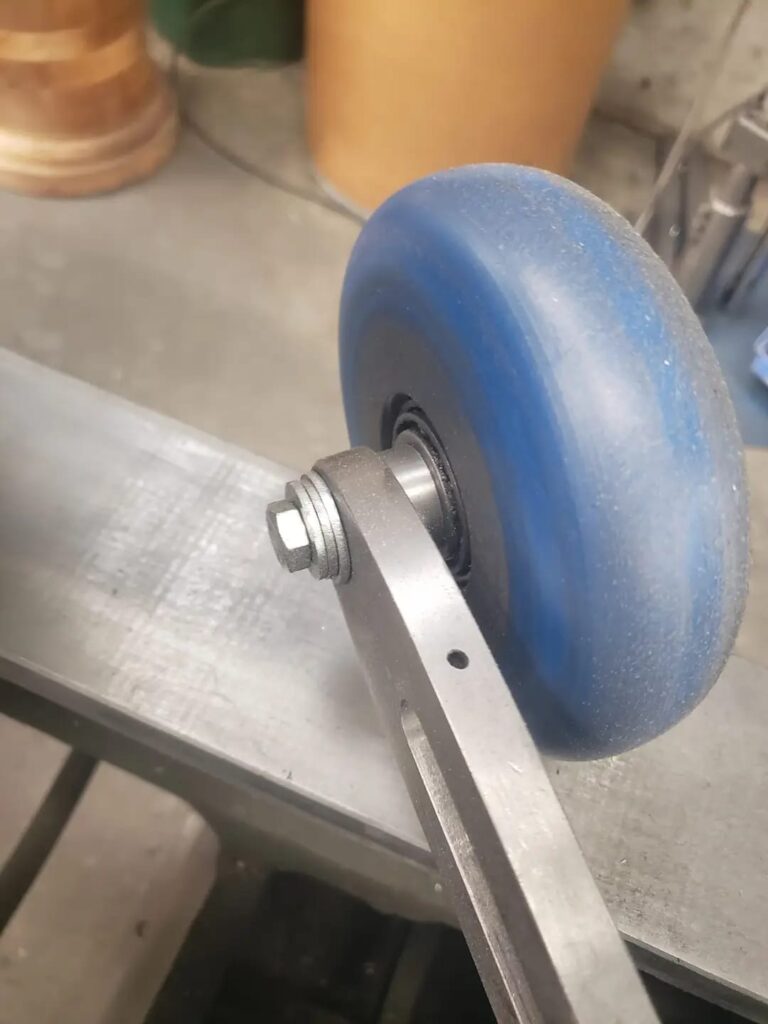
In CNC metal spinning, tool design is even more critical due to the high precision and repeatability required in automated processes. Proper tool design can significantly enhance the performance of the CNC system, reduce production costs, and improve part quality.
- Precision in Mandrel Design:
- Mandrels used in CNC spinning must be designed with a high degree of precision to ensure that the finished part meets the exact specifications of the CAD model. Any deviation in the mandrel’s dimensions can result in dimensional errors or poor surface finish on the final part.
- CNC tooling often incorporates interchangeable mandrels, allowing manufacturers to quickly switch between different part designs without significant machine downtime.
- Optimizing Tool Paths and Pressure:
- The tool path in CNC spinning must be carefully programmed to ensure uniform pressure distribution across the workpiece. Uneven pressure can lead to defects such as thinning, cracking, or warping of the material.
- Multi-axis CNC machines can control the movement of the forming tools with greater precision, allowing for more complex part geometries and smoother transitions between different shapes.
- Impact of Tool Design on Surface Finish:
- The surface finish of the final part is directly influenced by the design and material of the tooling. For high-quality surface finishes, tooling should be polished to reduce friction and prevent surface imperfections on the workpiece.
- Custom tooling may be required for parts with specific surface texture requirements, such as decorative components or functional parts in aerospace or medical applications.
Tooling Maintenance
Proper tooling maintenance is critical to ensuring consistent part quality, prolonging tool life, and minimizing production downtime. A well-maintained tooling system reduces the likelihood of defects and extends the overall lifespan of the machine.
- Tool Wear Monitoring:
- Tool wear can result in dimensional inaccuracies and poor surface finish. Regular inspection of tooling components, particularly rollers and mandrels, is necessary to identify signs of wear, such as scoring, pitting, or deformation.
- CNC machines equipped with tool wear monitoring systems can automatically detect when a tool needs to be replaced or reconditioned. This minimizes unplanned downtime and ensures consistent production quality.
- Lubrication and Cooling:
- Proper lubrication is essential in metal spinning to reduce friction between the tooling and the workpiece. Lubricants also help to prevent heat buildup, which can cause thermal distortion or tool degradation.
- Some high-performance tools incorporate internal cooling systems that circulate water or air to keep the tooling at optimal operating temperatures, particularly in high-speed CNC spinning or when working with high-temperature materials.
- Tool Reconditioning:
- Reconditioning worn tooling, such as grinding or polishing rollers and mandrels, can restore their performance and extend their useful life. Regular reconditioning reduces the cost of replacing tools and helps maintain part quality over time.
- Manufacturers often implement a tooling maintenance schedule based on production volume, material hardness, and other factors to ensure that tools are reconditioned or replaced before significant wear impacts production.
Innovations in Metal Spinning Machine Technology
In recent years, the metal spinning industry has undergone significant advancements, driven by the need for increased efficiency, precision, and adaptability in modern manufacturing. Innovations in automation, materials, and hybrid technologies have expanded the capabilities of metal spinning machines, making the process faster, more sustainable, and suitable for complex geometries. This section explores key innovations in metal spinning technology, from robotics and automation to sustainability and hybrid systems.
Automation and Robotics in Metal Spinning
The integration of automation and robotics into metal spinning has revolutionized the industry, providing unprecedented levels of precision and productivity. Automation minimizes human intervention, reducing errors and increasing efficiency, while robotic systems enhance the flexibility and versatility of metal spinning operations.
- Robotic Arms and Automation Systems:
- Robotic arms can be integrated into metal spinning systems to handle repetitive tasks such as loading and unloading workpieces, changing tools, or repositioning parts during multi-step processes. This reduces the need for manual labor, lowers production costs, and allows for faster cycle times.
- In addition to material handling, robotic systems can also be programmed to assist in the spinning process itself, applying controlled pressure to the workpiece in complex multi-axis movements. This is particularly useful for producing parts with non-symmetrical or intricate geometries.
- CNC-Integrated Automation:
- Automation has also advanced in the form of fully integrated CNC systems, which now include automated tool changers, adaptive control features, and machine learning algorithms that optimize tool paths in real-time. These systems not only enhance precision but also improve machine efficiency by reducing downtime between operations and adjusting settings based on the material’s behavior.
- Automated tool changers allow machines to switch between different forming tools or mandrels without manual intervention, increasing flexibility in production lines where parts of varying shapes and sizes are produced.
- Machine Vision Systems:
- Machine vision systems, combined with automation, are increasingly being used in metal spinning to provide real-time feedback during the process. Cameras and sensors monitor the workpiece for defects, dimensional accuracy, and surface finish, allowing the system to make instant adjustments to ensure quality. These systems help reduce waste and improve production consistency, especially in high-precision industries like aerospace and medical manufacturing.
Advanced Materials and Alloys
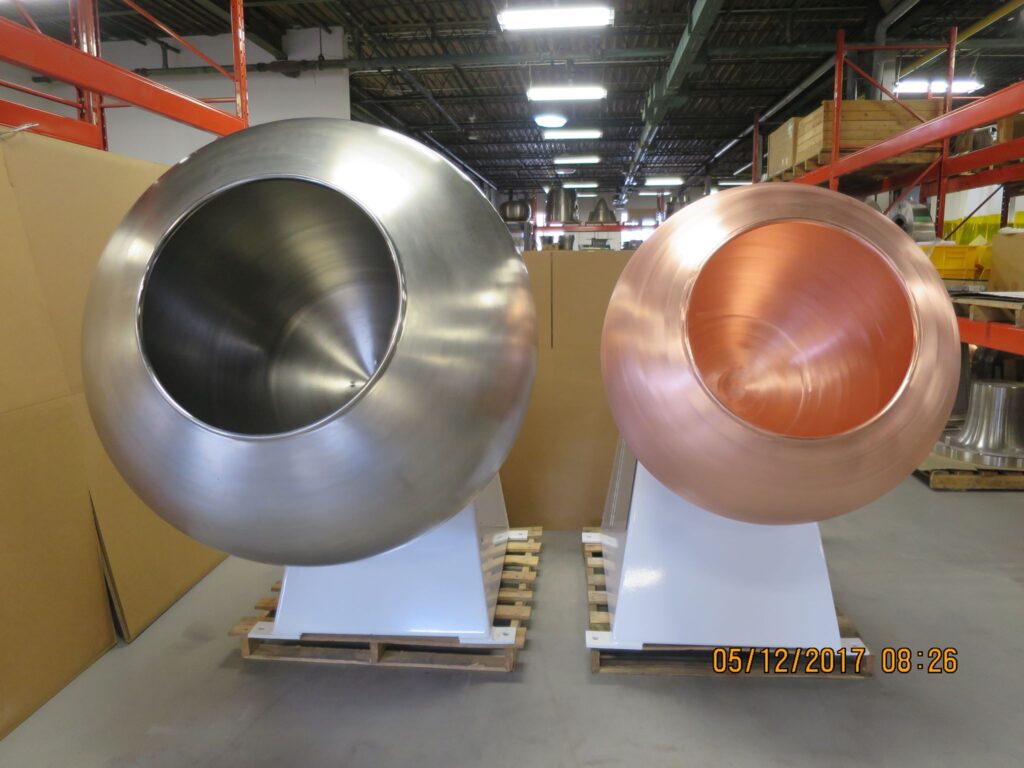
As industries like aerospace, automotive, and medical manufacturing demand lightweight, durable, and high-performance components, metal spinning machines have adapted to accommodate advanced materials and alloys. These new materials offer superior properties such as high strength-to-weight ratios, corrosion resistance, and heat resistance but present unique challenges during the spinning process.
- Lightweight Alloys:
- Materials like aluminum-lithium alloys and magnesium alloys have become increasingly popular in aerospace and automotive applications due to their exceptional strength and lightweight properties. Metal spinning machines must be adapted to spin these materials without compromising their structural integrity, often requiring optimized tooling, pressure control, and spindle speeds.
- High-Strength Alloys:
- High-strength alloys such as titanium and Inconel are essential in industries requiring extreme durability and resistance to harsh environments. Spinning these materials requires machines with greater force capabilities, precise tool control, and enhanced cooling systems to prevent workpiece distortion and tool wear.
- Spinning of Composite Materials:
- Composite materials, though traditionally associated with molding or extrusion processes, are now being explored in metal spinning for hybrid metal-composite components. The challenge lies in developing spinning techniques that maintain the integrity of the composite structure while achieving the desired metal shaping.
- The introduction of metal matrix composites (MMCs), where metal is reinforced with ceramics or other materials, offers potential in high-performance industries. CNC metal spinning machines are being adapted with advanced control systems to handle these hybrid materials without causing defects or delamination.
Hybrid Spinning Technologies
The integration of metal spinning with other manufacturing processes has given rise to hybrid technologies, enabling manufacturers to achieve complex shapes, reduce production steps, and enhance material properties. These innovations allow for greater design flexibility and improved performance of spun components.
- Combination of Spinning and Stamping:
- Spinning-stamping hybrid machines combine the precision of metal spinning with the speed of stamping processes. This allows manufacturers to create components with intricate features, such as deep recesses or detailed edges, while still benefiting from the material efficiency and strength properties of spinning.
- Hybrid systems are particularly useful in industries that require both formability and high-volume production, such as automotive manufacturing, where parts like wheel rims or exhaust components need to be produced quickly but with high dimensional accuracy.
- Laser-Assisted Metal Spinning:
- One of the more cutting-edge innovations in hybrid spinning technology is the use of laser-assisted spinning. In this process, a laser heats the metal workpiece during spinning, making it more malleable and easier to shape, especially for high-strength materials like titanium and steel.
- By localizing heat at specific points on the workpiece, laser-assisted spinning reduces the forces required to form the metal, minimizing tool wear and energy consumption. This process is particularly beneficial for spinning complex geometries and producing parts with tight tolerances, as it enables better control over material flow.
- Spinning with Additive Manufacturing (3D Printing):
- Another innovation involves combining additive manufacturing with metal spinning. Metal 3D printing can create preforms or near-net-shape blanks that are then finished using the metal spinning process. This hybrid approach reduces material waste and production times by combining the strengths of both technologies—additive manufacturing’s design flexibility and metal spinning’s material efficiency.
- This method is gaining traction in industries that require complex, customized parts, such as aerospace, where additive manufacturing allows for the creation of intricate structures, and spinning provides the necessary mechanical properties and surface finish.
Sustainability and Energy Efficiency
Sustainability has become a key focus in modern manufacturing, and metal spinning technology is no exception. New developments in machine design and process optimization aim to reduce energy consumption, minimize waste, and promote eco-friendly manufacturing practices.
- Energy-Efficient Machines:
- Metal spinning machines are being designed with energy-efficient motors, improved cooling systems, and optimized drive systems to reduce power consumption during production. Servo-driven CNC systems are particularly energy-efficient, as they consume less power while maintaining precise control over tool movements.
- The use of regenerative braking systems in modern metal spinning machines helps recapture energy during deceleration, further reducing energy waste and operational costs.
- Reduction of Material Waste:
- One of the inherent benefits of metal spinning is its ability to produce parts with minimal material waste. Recent innovations have focused on enhancing this advantage by improving tooling design and process control, leading to better material utilization and less scrap.
- Near-net-shape spinning is an advanced technique where the workpiece is spun very close to its final dimensions, reducing the need for post-processing operations like trimming or machining, which typically generate waste.
- Use of Recycled Materials:
- The demand for sustainability has also led to increased use of recycled metals in spinning processes. Many manufacturers are now incorporating recycled aluminum, copper, and steel into their production lines, reducing the environmental impact of raw material extraction.
- Advanced CNC machines are capable of adapting to the slightly different properties of recycled metals, ensuring that the final product maintains the same quality as parts made from virgin materials.
Metal Spinning Machine Maintenance and Safety
Proper maintenance and stringent safety protocols are essential for ensuring the efficient and safe operation of metal spinning machines. Regular upkeep reduces the risk of machine failure, enhances productivity, and extends the lifespan of equipment. Additionally, given the high speeds and forces involved in metal spinning, adherence to safety standards is critical to protecting operators from potential hazards. This section outlines the best practices for machine maintenance and safety measures, focusing on routine servicing, troubleshooting common issues, and implementing effective safety protocols.
Routine Maintenance Procedures
Maintaining metal spinning machines involves a set of routine procedures designed to keep the machinery in optimal working condition. Regular maintenance helps avoid unexpected breakdowns and ensures that the machines consistently produce high-quality components.
- Machine Calibration:
- Accurate calibration is crucial for ensuring the precision of metal spinning operations, especially for CNC machines. Calibration involves adjusting the machine’s sensors, spindle alignment, and tool positions to ensure that they operate within the required tolerances.
- Calibration should be performed at regular intervals, particularly after tool changes or when switching between different part designs. Misalignment in the spindle or tooling can lead to defects such as inconsistent thickness or poor surface finish.
- Lubrication:
- Proper lubrication is essential for minimizing friction between moving parts, reducing wear, and preventing overheating. Key components such as the spindle bearings, guide rails, and tool posts must be regularly lubricated with the appropriate oils or greases, as specified by the manufacturer.
- In high-speed operations or when working with hard materials, the friction between the workpiece and tooling can generate significant heat. Lubrication of the workpiece is also critical in these cases to ensure smooth spinning and to prevent surface damage.
- Cleaning:
- Metal spinning machines should be regularly cleaned to remove debris, metal shavings, and dust. These contaminants can accumulate on the machine bed, spindle, and tooling, leading to increased wear or reduced performance over time.
- Cleaning should be performed after every production shift, with a focus on critical areas such as the mandrel, tool posts, and rollers, where debris is most likely to collect.
- Inspection of Wear Parts:
- Rollers, mandrels, and other wear parts must be routinely inspected for signs of wear and tear. Over time, these components may become worn, leading to inconsistencies in the spinning process. For example, worn rollers can cause surface imperfections, while a deformed mandrel can result in out-of-tolerance parts.
- Regular inspection allows for timely replacement or reconditioning of these parts before they negatively impact production quality.
- Spindle and Drive System Maintenance:
- The spindle is a critical component of the spinning machine, responsible for rotating the workpiece at high speeds. It must be inspected regularly for signs of misalignment or wear. Vibration, unusual noises, or changes in speed control can indicate spindle problems that require immediate attention.
- The drive system, including motors and belts, should also be checked for proper tension, wear, and alignment. Failure in the drive system can lead to machine downtime and costly repairs.
Troubleshooting Common Issues
Even with regular maintenance, metal spinning machines may experience operational issues that affect part quality or machine performance. Understanding common problems and how to troubleshoot them can help minimize downtime and prevent defects.
- Misalignment:
- Misalignment of the spindle, tooling, or mandrel can cause dimensional inaccuracies in the final part. Symptoms of misalignment include uneven wall thickness, surface defects, or parts that are out of tolerance.
- To troubleshoot misalignment, check the calibration of the machine and realign the spindle and tooling as necessary. Ensure that the workpiece is properly clamped and that the mandrel is correctly positioned.
- Tool Wear:
- Worn tools, such as rollers and forming tools, can result in poor surface finishes, material tearing, or excessive thinning of the workpiece. Tool wear is often caused by prolonged use, improper lubrication, or spinning hard materials.
- Regular inspection and replacement of worn tools can prevent these issues. Using high-quality tool materials and applying the correct lubrication can also extend tool life and improve overall part quality.
- Overheating:
- High-speed spinning generates heat, which can lead to material warping, surface oxidation, or damage to the tooling. Overheating may occur if the machine is running at too high a speed or if the lubrication system is inadequate.
- To prevent overheating, ensure that the machine’s cooling and lubrication systems are functioning correctly. If overheating persists, reduce spindle speed or adjust the force applied during the spinning process.
- Vibration:
- Excessive vibration during spinning can result in poor surface finishes, reduced dimensional accuracy, and increased wear on the machine components. Vibration is often caused by imbalanced workpieces, worn spindle bearings, or loose components.
- To troubleshoot vibration, ensure that the workpiece is properly centered and balanced on the mandrel. Inspect the spindle bearings and drive system for wear, and tighten any loose components.
Safety Protocols
Safety is paramount in metal spinning operations due to the high forces, speeds, and sharp tooling involved. A comprehensive safety program should be in place to protect operators from potential hazards, prevent accidents, and ensure compliance with industry regulations.
- Operator Training:
- All operators must receive thorough training before using metal spinning machines. This training should cover machine operation, safety procedures, emergency shutdown protocols, and proper use of personal protective equipment (PPE).
- Operators should also be trained to recognize early signs of machine malfunction, such as unusual noises, vibrations, or performance issues, and know how to shut down the machine in case of an emergency.
Types of Metal Spinning
- Manual Metal Spinning: This traditional form relies on the skills of an operator who manually shapes the workpiece using hand-held tools. Though it requires high skill levels, manual spinning is highly effective for low-volume and custom jobs. Operators can adjust the pressure and speed in real time, which allows for a high degree of flexibility in forming complex shapes.
- CNC Metal Spinning: Computer Numerical Control (CNC) spinning automates the metal spinning process. In CNC systems, computers control the rotation speed and tooling, enabling precision, repeatability, and the ability to work with complex geometries. CNC spinning is ideal for large production volumes and offers higher consistency in terms of dimensional accuracy.
- Shear Spinning: In this technique, the metal is thinned as it is spun, allowing for a significant reduction in the material’s thickness while maintaining structural integrity. This process is often used in industries that require lightweight components with high strength, such as aerospace and automotive sectors.
- Flow Forming: Flow forming is a more advanced variation of metal spinning where the workpiece is stretched and thinned simultaneously, allowing for the creation of parts with very specific tolerances and high precision. This method is widely used in the production of high-precision components like drive shafts, missile casings, and pressure vessels.
Materials Used in Metal Spinning The choice of material is crucial in metal spinning as it affects the ease of the process, the final product’s durability, and its mechanical properties. Common materials include:
- Aluminum: Lightweight and easily malleable, aluminum is frequently used for aerospace components and consumer goods like lighting fixtures.
- Steel (both carbon and stainless): Steel is often chosen for its strength and corrosion resistance, making it ideal for automotive parts, cookware, and architectural components.
- Copper and Brass: These materials are softer and often used in decorative or functional applications like musical instruments and industrial equipment.
- Titanium and other superalloys: In high-performance applications, especially in aerospace and military manufacturing, titanium and superalloys are preferred for their high strength-to-weight ratio and ability to withstand extreme conditions.
Basic Tools and Machinery The metal spinning process involves various tools and machinery, each critical to ensuring the accuracy and efficiency of the production process. These include:
- Lathe: The core machine for metal spinning, lathes rotate the workpiece at high speeds, allowing tools to shape it.
- Mandrel: A pre-shaped form over which the metal is spun. Mandrels are custom-designed for each part’s specifications, dictating the final shape of the spun piece.
- Rollers and Tools: Hand-held or machine-powered rollers are used to apply pressure to the metal, gradually pushing it against the mandrel. The shape, size, and material of these rollers vary depending on the workpiece’s dimensions and material.
- Chucks: These hold the workpiece securely in place during spinning, ensuring that the piece remains centered throughout the process.
The Metal Spinning Process
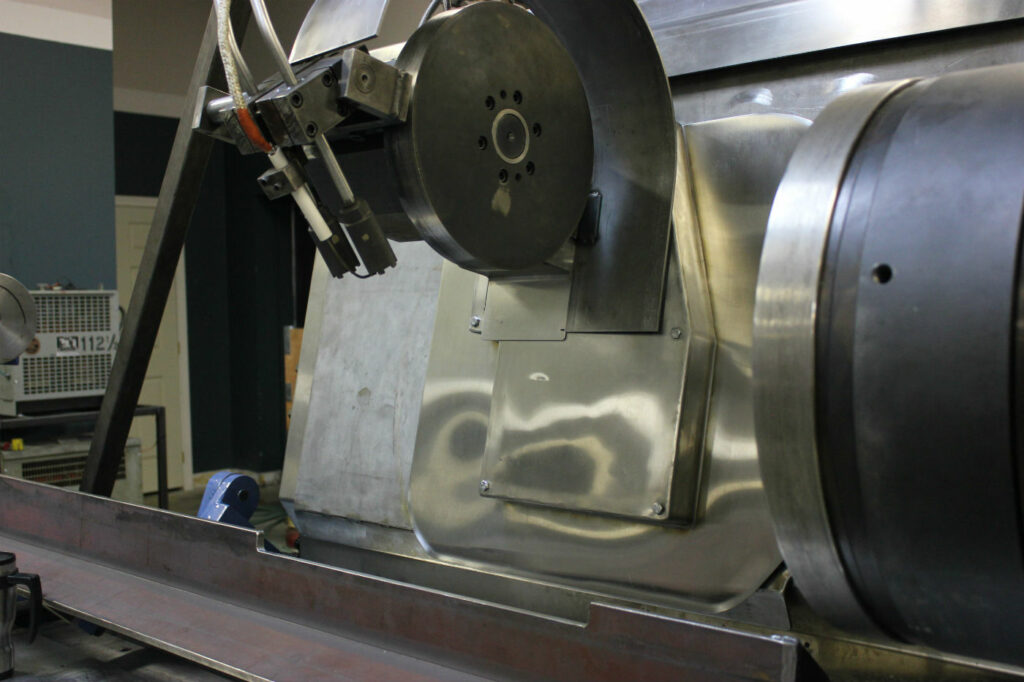
Step-by-Step Breakdown of the Process
- Preparation of Material and Mandrel:
The first step in the metal spinning process is preparing the raw material, which is usually in the form of a flat disc or tube. The material’s thickness, diameter, and type (e.g., aluminum, steel, copper) are selected based on the desired final product. Alongside this, a mandrel—a solid form or mold—must be crafted to match the intended shape of the spun component. This mandrel acts as a guide, allowing the metal to be pressed against it to take the desired shape. - Mounting the Workpiece on the Lathe:
The metal disc or tube is mounted securely onto the lathe using a chuck. The lathe spins the workpiece at high speeds, creating centrifugal force. The speed at which the metal spins varies based on factors such as the material, its thickness, and the complexity of the shape being formed. A typical range is between 500 and 3000 RPM (revolutions per minute). - Tooling and Pressure Application:
With the material spinning, the operator (in manual spinning) or the machine (in CNC spinning) begins applying pressure to the metal using specialized tools or rollers. These tools gradually force the metal against the mandrel, shaping it according to the form. The operator must carefully control the pressure to prevent tearing or wrinkling of the material, ensuring smooth and even deformation. - Progressive Forming and Shaping:
The forming process is not a one-step procedure. The operator applies successive layers of pressure, each pushing the metal closer to the desired shape. In some cases, the process requires intermediate annealing, a heat treatment to soften the metal and prevent it from becoming brittle as it is worked. - Finishing and Trimming:
After the metal has been spun into its final shape, excess material at the edges (known as the flange) is trimmed off. At this stage, the part may undergo additional finishing operations, such as sanding, polishing, or heat treatment, depending on the final application requirements. In some cases, secondary processes such as welding or machining may be necessary for complex components. - Inspection and Quality Control:
The spun part is inspected for defects, dimensional accuracy, and surface finish. This step ensures that the product meets specified tolerances and quality standards. In industrial settings, inspection may involve manual checks or automated methods, including laser scanning and measurement tools, to ensure precise adherence to design specifications.
Comparison with Other Metal Forming Techniques
- Metal Stamping: Unlike metal spinning, which gradually forms the material into a desired shape, stamping involves pressing a metal sheet into a mold in a single operation. While stamping is faster for mass production, it lacks the flexibility of metal spinning in handling custom shapes or low-volume runs.
- Deep Drawing: This method forms a part by stretching metal into a die. While deep drawing is ideal for creating seamless parts like cans or shells, it can lead to thinning of the material. Metal spinning, by contrast, allows for more uniform wall thickness.
- Hydroforming: Hydroforming uses high-pressure fluid to shape the metal against a mold. It’s a highly precise process but more costly than spinning, particularly for large parts. Metal spinning offers a more cost-effective solution for producing cylindrical or conical parts.
Key Parameters in Metal Spinning
- Speed:
The speed of the lathe directly affects the quality of the final product. Higher speeds generate more centrifugal force, which helps shape the metal smoothly around the mandrel. However, excessive speed may cause the material to warp or even crack, especially with brittle materials like stainless steel. - Pressure:
The amount of pressure applied by the roller or tool determines the rate at which the metal is formed. Operators must balance the pressure to ensure the material conforms to the mandrel without buckling or tearing. - Tool Control:
In CNC systems, tool paths are programmed for precise movements, but in manual spinning, the operator controls the movement, angle, and force of the tool. Skilled operators adjust these factors on the fly, allowing for high flexibility in shaping complex geometries.
Types of Metal Spinning Techniques
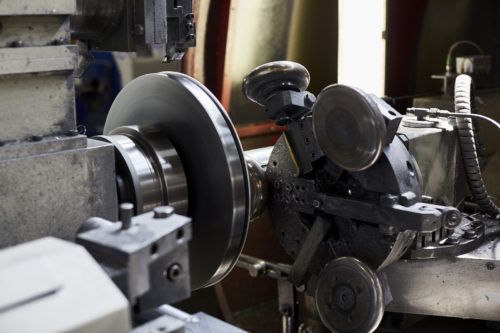
1. Conventional Metal Spinning
This is the most basic form of metal spinning, where a flat metal disc is spun and shaped over a mandrel using manual or CNC techniques. In conventional spinning, the material’s thickness remains relatively constant, as the process is focused on shaping rather than altering the material’s thickness. This method is used for producing symmetric components like domes, cones, and cylinders. It is commonly applied in the production of industrial components, decorative objects, and functional items such as cookware.
2. Shear Spinning
In shear spinning, the metal is not only shaped but also thinned during the process. This method involves spinning the metal over a mandrel while simultaneously applying a shearing force to reduce the material’s thickness. The amount of reduction is carefully controlled, and the thinning typically occurs in a uniform direction. Shear spinning is ideal for applications that require lightweight yet strong parts, such as turbine discs, rocket components, and military applications. The process is more demanding than conventional spinning, requiring precise control of the thinning process to avoid material defects.
3. Tube Spinning
Tube spinning is a specialized technique used to form hollow, cylindrical shapes by spinning a tube or cylinder of metal. In this process, the tube is stretched and shaped over a mandrel, reducing its wall thickness while maintaining its length. Tube spinning is commonly employed in the production of long, tubular components such as drive shafts, pressure vessels, and missile casings. It offers high precision and the ability to produce parts with uniform wall thickness, making it ideal for applications that require both strength and weight savings.
4. Flow Forming
Flow forming is one of the most advanced spinning techniques, combining the principles of both shear spinning and tube spinning. It involves spinning a preform (usually a tube) over a mandrel while applying axial and radial pressure. This process stretches and thins the metal simultaneously, resulting in extremely precise parts with high structural integrity. Flow forming is widely used in industries such as aerospace, defense, and energy, where precision components like rocket motor cases, gas turbine housings, and pressure vessels are required. It is highly automated, often utilizing CNC machines for exceptional accuracy and repeatability.
Differences Between Spinning Techniques
- Conventional spinning focuses on shaping with minimal changes to material thickness, ideal for simpler, symmetrical shapes.
- Shear spinning involves intentional thinning, making it suitable for applications that prioritize weight reduction.
- Tube spinning specializes in cylindrical components, offering precise control over wall thickness.
- Flow forming is the most precise and advanced technique, producing components with exact tolerances and structural integrity.
Applications of Each Technique
- Conventional Spinning: Common in cookware, lighting fixtures, and architectural components.
- Shear Spinning: Ideal for lightweight, high-strength parts in aerospace and automotive industries.
- Tube Spinning: Used for producing drive shafts, missile casings, and pressure vessels.
- Flow Forming: Applied in precision-demanding fields like aerospace, defense, and power generation.
Applications of Metal Spinning
Metal spinning is a versatile and cost-effective manufacturing process used across a variety of industries due to its ability to create complex, high-precision parts. Below are some of the primary industries and specific applications that benefit from this technique.
1. Aerospace Industry The aerospace industry is one of the largest consumers of metal spinning technology due to the need for lightweight yet durable components. Some key applications include:
- Rocket and missile cones: Metal spinning is used to produce seamless, high-strength nose cones for rockets and missiles, where precision and material integrity are critical.
- Jet engine components: Spun parts such as combustion chambers, afterburners, and turbine components are essential in the production of jet engines. The strength-to-weight ratio of these parts plays a crucial role in improving fuel efficiency and overall performance.
- Satellite components: Metal spinning is often employed to manufacture thin-walled, lightweight structures for satellites, including housings, support structures, and antenna reflectors.
2. Automotive Industry In the automotive sector, metal spinning is valued for producing high-strength, durable components with minimal material waste. Key applications include:
- Wheel rims: Spun metal wheels offer superior strength and durability compared to cast or stamped wheels. The process allows for lighter, more fuel-efficient vehicles while maintaining structural integrity.
- Drive shafts and transmission parts: Tube spinning and flow forming techniques are commonly used to manufacture these components, ensuring uniform thickness and excellent mechanical properties.
- Exhaust components: Metal spinning can produce complex exhaust system components, such as cones and bellows, which require precision and high-temperature resistance.
3. Medical Equipment Metal spinning is also important in the production of medical devices and equipment, where material precision and durability are critical:
- Surgical instruments: Precision-spun metal components are used to manufacture medical-grade surgical tools and devices, which require tight tolerances and smooth finishes.
- Prosthetic components: Metal spinning is employed in the production of lightweight, biocompatible components for prosthetics, offering customized solutions for individual patients.
- Medical housings: The process is also used to create custom housings and enclosures for high-tech medical equipment such as MRI machines and diagnostic tools.
4. Lighting and Consumer Goods Metal spinning has a long history in the production of consumer goods, especially in decorative and functional lighting:
- Lighting fixtures: Spun aluminum and steel components are used in modern lighting fixtures, especially for architectural and industrial lighting systems. The spinning process allows for sleek, customizable designs.
- Cookware: High-end cookware often uses spun metals, such as stainless steel and aluminum, for pots, pans, and kettles. Metal spinning provides excellent heat conductivity and uniform thickness.
- Musical instruments: Some musical instruments, such as cymbals and brass wind instruments, use metal spinning to achieve the precise shape and acoustics required for high-quality sound production.
5. Renewable Energy Sector The push for sustainable energy solutions has also increased the demand for metal spinning in the energy sector:
- Wind turbine components: Large wind turbines require durable, lightweight components such as nacelles and hub covers. Metal spinning allows for the efficient production of these parts while maintaining the required strength.
- Solar reflectors: Spun metal components are used in solar power systems to create reflective dishes and panels, maximizing the efficiency of light capture.
- Hydraulic power generation: Metal spinning is used in the production of high-performance components such as turbine blades, which must withstand intense forces and environmental exposure.
6. Defense and Military Applications The military industry requires high-performance, durable metal components capable of withstanding extreme conditions:
- Weapon casings and ammunition: Metal spinning is used to manufacture cylindrical and conical casings for munitions, ensuring uniform thickness and durability.
- Military vehicles and aircraft: Components such as armored vehicle parts, aircraft components, and fuel tanks benefit from the strength and precision of spun metal.
7. Custom and Niche Applications Metal spinning’s ability to produce customized, one-off, or low-volume parts makes it attractive for specialized industries:
- Architectural and decorative uses: Metal spinning is often employed to create custom metalwork for architectural installations, sculptures, and decorative elements in high-end buildings and interiors.
- Laboratory equipment: Scientific instruments and laboratory apparatus often require precision metal components that can be fabricated through metal spinning.
Advantages of Metal Spinning
Metal spinning offers several advantages over other metal forming techniques, making it a preferred choice in industries requiring precision, efficiency, and cost-effectiveness. Below are some key benefits of this manufacturing process:
1. Cost-Effectiveness One of the primary advantages of metal spinning is its cost-effectiveness, particularly for small to medium production runs. Unlike other processes such as casting or stamping, metal spinning requires minimal setup and tooling costs. This is especially beneficial for custom or low-volume parts where the cost of creating molds and dies can be prohibitive. Additionally, metal spinning reduces material waste by shaping the metal directly over a mandrel, ensuring maximum utilization of the raw material.
2. Flexibility and Customization Metal spinning is a highly flexible process that can accommodate a wide range of materials, shapes, and sizes. From small, intricate components to large, complex geometries, the process can be tailored to meet specific design requirements. Whether manual or CNC spinning is used, operators have a high degree of control over the shaping process, allowing for quick adjustments and customizations during production. This makes metal spinning ideal for prototyping, one-off custom parts, and highly specialized applications.
3. Precision and Dimensional Accuracy CNC-controlled metal spinning allows for exceptional precision and repeatability, making it possible to produce components with tight tolerances and complex geometries. The ability to consistently achieve uniform thickness and smooth surfaces without seams or welds is a significant advantage, particularly in industries like aerospace and medical device manufacturing where precision is critical. The process also produces strong, seamless parts that have a high degree of structural integrity.
4. Strength and Durability Metal spinning enhances the mechanical properties of the material by aligning the grain structure along the direction of the applied force. This results in parts with higher tensile strength and resistance to fatigue and cracking compared to components produced through casting or stamping. The lack of seams or welds also contributes to the durability and structural integrity of spun parts, which is especially important in industries that require high-strength, lightweight components.
5. Versatility in Material Choice Metal spinning works with a wide range of metals, including:
- Aluminum: Popular for its lightweight properties and corrosion resistance, used in aerospace, automotive, and consumer goods.
- Stainless Steel: Valued for its strength, heat resistance, and corrosion resistance, used in cookware, medical devices, and industrial components.
- Copper and Brass: These metals are softer and more malleable, making them ideal for decorative applications and musical instruments.
- Titanium and Superalloys: Preferred in aerospace and defense industries for their high strength-to-weight ratio and ability to withstand extreme environments.
6. Environmental Sustainability Metal spinning is a more environmentally friendly process compared to other metal-forming techniques, such as casting or stamping. The process produces less scrap material since the metal is formed through deformation rather than cutting or removal. This reduction in waste translates into more efficient use of raw materials, contributing to the sustainability of the manufacturing process. Additionally, the ability to produce lightweight components, particularly in aerospace and automotive industries, leads to more fuel-efficient products, which further reduces the environmental impact.
7. Durability of Tooling and Machinery The machinery and tools used in metal spinning, particularly CNC systems, have long lifespans due to the relatively low wear and tear involved in the process. Unlike casting molds, which degrade over time, the mandrels used in metal spinning are typically robust and reusable for long production runs. This durability contributes to the overall cost-effectiveness of the process.
Challenges and Limitations of Metal Spinning
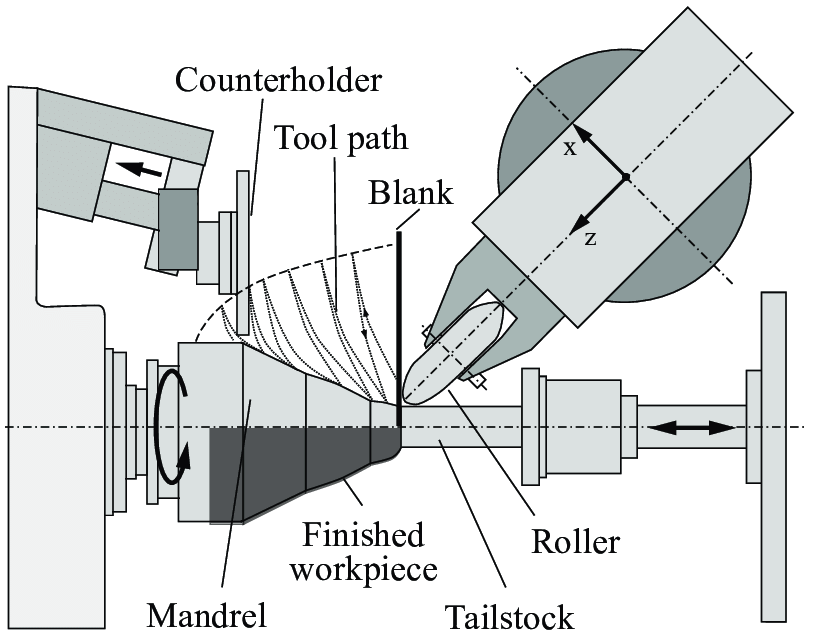
While metal spinning offers many advantages, it also presents several challenges and limitations that manufacturers must consider, particularly when dealing with complex geometries, material properties, and production demands. Below are some of the most common challenges faced in metal spinning.
1. Material Limitations Although metal spinning is compatible with various metals, not all materials are equally suitable for the process. Materials with low ductility, such as certain hardened steels or brittle alloys, can be challenging to spin without causing cracks or fractures. Metals like aluminum, copper, and brass, which are more malleable, are easier to work with, but harder metals require special attention to prevent damage during forming. The operator or CNC program must carefully control parameters such as speed, pressure, and temperature to avoid issues, especially when dealing with superalloys or titanium.
2. Dimensional Constraints Metal spinning is most effective for producing axially symmetric parts such as cones, cylinders, or hemispheres. While the process excels in shaping round, hollow components, it is less suitable for parts with non-symmetrical geometries or sharp angles. Creating complex shapes that deviate from a round profile often requires multiple processes or additional machining, which can increase production time and costs. Furthermore, while metal spinning can produce parts with large diameters, the size of the lathe and the mandrel can limit the maximum dimensions that can be achieved.
3. Surface Finish Concerns One challenge that manufacturers face is achieving a consistent surface finish. The surface of the spun metal may show marks, ridges, or other imperfections depending on the material and tooling used. Manual spinning, in particular, can leave tool marks that require additional finishing processes such as polishing or sanding. CNC spinning improves surface consistency, but for applications where aesthetics are critical, further post-processing may be necessary to achieve a high-quality finish. This can add time and expense to the manufacturing process.
4. Tolerances and Thickness Control Maintaining uniform wall thickness and tight dimensional tolerances during the metal spinning process can be difficult, particularly with complex or large parts. The amount of thinning that occurs during the spinning process must be carefully controlled, especially in shear spinning and flow forming, where the material is deliberately reduced in thickness. Improper control of the spinning parameters can result in uneven wall thickness, which compromises the part’s structural integrity and performance. In high-precision industries like aerospace and medical manufacturing, any deviation from specified tolerances can lead to part rejection, requiring tight process control and quality monitoring.
5. Skill and Expertise Requirements Manual metal spinning is a highly skilled process that requires extensive training and experience. Operators must be able to control the force, pressure, and speed of the tools to achieve the desired shape while avoiding defects such as tearing or warping. This level of expertise is becoming rarer in modern manufacturing, where automation and CNC technology are increasingly preferred for precision and repeatability. However, for low-volume production or custom parts, skilled manual spinners are still in high demand. In CNC spinning, programming expertise is required to ensure the correct tool paths and process parameters are followed, further adding to the technical requirements of the process.
6. High Initial Setup Costs for Complex Parts While metal spinning is cost-effective for small to medium production runs, the initial setup can be expensive for complex parts. Custom mandrels and tooling must be fabricated to match the desired shape, which can increase upfront costs. For simple geometries or high-volume production, this cost is spread across many units, making the process economical. However, for more complex designs or one-off custom parts, the cost of creating specialized tooling can be prohibitive.
Quality Control in Metal Spinning
Ensuring the quality of spun metal parts is critical, especially in industries like aerospace, automotive, and medical devices, where precision and reliability are paramount. Quality control in metal spinning focuses on maintaining dimensional accuracy, material integrity, and surface finish. Below are the key aspects of quality control in metal spinning.
1. Dimensional Tolerances and Accuracy One of the most important factors in quality control is ensuring that the spun part meets the required dimensional tolerances. Even minor deviations can affect the performance or assembly of a component. To control dimensions, manufacturers use precise measuring tools, such as calipers, micrometers, and coordinate measuring machines (CMM), to inspect the final product. CNC spinning machines can enhance accuracy by automating the process and minimizing human error, but manual inspection is still often required to confirm that the part meets design specifications.
2. Material Integrity and Defect Detection Spun metal parts must retain their structural integrity throughout the process to ensure that they meet performance requirements. Common defects such as cracking, tearing, or thinning can compromise the material’s strength and lead to product failure. Inspection methods such as visual checks, ultrasonic testing, and dye penetrant inspections are used to detect surface defects, while non-destructive testing (NDT) methods, such as X-ray and ultrasound, can identify internal flaws. Regular testing ensures that the material maintains its mechanical properties and that the spinning process has not introduced any weaknesses.
3. Surface Finish and Aesthetic Quality In industries where appearance is crucial, such as lighting fixtures, cookware, and architectural applications, surface finish quality is a major concern. Achieving a consistent and smooth finish without marks or tool scratches can be challenging, particularly in manual spinning processes. Quality control involves visual inspection and, in some cases, profilometers to measure surface roughness. In CNC spinning, the finish can be controlled more consistently, but additional polishing, sanding, or coating may still be required to meet aesthetic standards.
4. Automation and Advanced Quality Control Systems With advancements in technology, automation is increasingly integrated into quality control processes. In CNC metal spinning, automated systems such as in-process monitoring and feedback mechanisms can track and adjust parameters like speed, pressure, and temperature to ensure precision throughout production. Some systems are even equipped with AI-powered sensors that can detect anomalies in real time and correct them during the process. This reduces the likelihood of defects and improves overall product consistency, especially in high-volume production.
5. Operator Skill and Inspection in Manual Spinning In manual metal spinning, the operator’s experience and skill play a key role in quality control. Skilled operators can detect issues during the spinning process and make adjustments as needed. Post-production inspection is equally critical, as manually spun parts may require more extensive checks to ensure that they meet specifications. Operators often perform visual inspections, and specialized equipment can be used to verify thickness, roundness, and other critical measurements.
Future Trends in Metal Spinning
As manufacturing technologies evolve, metal spinning is seeing significant advancements, driven by innovations in automation, materials, and design capabilities. These trends are transforming the industry and expanding the applications of metal spinning into new frontiers. Below are some of the key future trends shaping the metal spinning landscape.
1. Integration of Robotics and Automation One of the most transformative trends in metal spinning is the increasing integration of robotics and automation into the process. Traditional manual spinning requires a high level of skill and experience, but automated systems, especially CNC-controlled spinning, allow manufacturers to produce complex parts with greater precision, speed, and repeatability.
- Robotic Arms and Automation Systems: Automated systems equipped with robotic arms can handle the loading and unloading of workpieces, reducing the reliance on human labor for repetitive tasks. These systems can be programmed to follow precise tool paths, ensuring consistency across production runs. This not only increases efficiency but also reduces the risk of human error, leading to higher-quality finished products.
- Fully Automated Spinning Cells: In the future, more manufacturers are likely to adopt fully automated spinning cells, where multiple lathes, robotic arms, and inspection systems work in unison. These cells can operate 24/7, boosting productivity and enabling manufacturers to meet the growing demand for high-volume production while maintaining tight tolerances.
2. Advancements in CNC Technology CNC metal spinning technology continues to advance, offering greater levels of precision and flexibility. Modern CNC machines are capable of producing parts with complex geometries, which were previously difficult or impossible to achieve with manual spinning techniques.
- Multi-Axis CNC Machines: Traditional CNC spinning machines typically work with two or three axes, but multi-axis machines are now becoming more common. These machines allow for more intricate tool paths, enabling the creation of parts with intricate curves, flanges, and recesses. As CNC technology advances, it’s expected that more manufacturers will adopt multi-axis systems to broaden the range of shapes that can be spun.
- CNC Integration with Artificial Intelligence (AI): The integration of AI and machine learning algorithms is starting to play a role in optimizing CNC spinning processes. AI-powered systems can analyze data from previous runs to predict optimal parameters such as speed, pressure, and tool angles. These systems can adjust in real-time to compensate for variations in material properties or tool wear, leading to improved efficiency and fewer defects. Over time, AI will likely enable greater autonomy in metal spinning operations, reducing the need for operator intervention.
3. Material Innovations As industries like aerospace, automotive, and defense seek materials with better performance characteristics, there has been a growing interest in exploring new alloys and composites for metal spinning. Traditionally, materials like aluminum, steel, and copper have been the primary choices, but newer, more advanced materials are emerging as viable options.
- High-Temperature Superalloys: Superalloys, which are known for their ability to maintain strength at high temperatures, are becoming increasingly popular in aerospace and energy applications. These materials are often challenging to form using conventional methods, but advancements in CNC spinning and flow forming have made it possible to spin superalloys with precision. These materials are essential for components that must withstand extreme heat and stress, such as turbine blades and exhaust nozzles.
- Titanium and Magnesium Alloys: Titanium alloys are favored for their high strength-to-weight ratio, making them ideal for aerospace and medical applications. However, spinning titanium presents unique challenges due to its work-hardening properties. New heat-assisted spinning techniques and improved tooling have made it easier to work with titanium. Similarly, magnesium alloys are gaining traction due to their lightweight properties, particularly in automotive applications where weight reduction is key to improving fuel efficiency.
- Composite Materials: The use of composite materials in metal spinning is still in its early stages, but it represents a promising area of future development. Hybrid materials, such as metal matrix composites (MMCs), offer enhanced properties such as increased strength, reduced weight, and improved corrosion resistance. Developing the capability to spin composite materials could unlock new applications, particularly in industries focused on lightweight and high-performance components.
4. Industry 4.0 and Digitalization Industry 4.0, also known as the Fourth Industrial Revolution, is a trend that emphasizes the use of digital technologies to enhance manufacturing processes. Metal spinning is set to benefit from Industry 4.0 advancements, particularly in the areas of process monitoring, data analytics, and predictive maintenance.
- Real-Time Monitoring and Data Analytics: The use of sensors and monitoring systems in CNC spinning machines is becoming more prevalent. These systems collect data in real-time, allowing manufacturers to monitor parameters such as force, speed, temperature, and tool wear. This data can be analyzed to optimize the process, identify potential issues before they lead to defects, and improve overall efficiency.
- Predictive Maintenance: Another key trend in digitalization is the implementation of predictive maintenance systems. By analyzing data on machine performance and component wear, manufacturers can predict when equipment will need maintenance, preventing unexpected downtime and reducing costs. This is particularly important in high-volume production environments where machine availability is critical.
5. Additive Manufacturing (3D Printing) and Metal Spinning Additive manufacturing, or 3D printing, is making its mark on many industries, and its combination with traditional metal forming processes like spinning is opening up new possibilities. While 3D printing excels in creating complex geometries, it has limitations in terms of material strength and surface finish. Metal spinning, on the other hand, produces strong, seamless parts.
- Hybrid Manufacturing: By combining 3D printing with metal spinning, manufacturers can take advantage of the strengths of both processes. For example, 3D-printed preforms can be used as a starting point for metal spinning, allowing for the creation of intricate base shapes that can then be refined and strengthened through spinning. This hybrid approach offers new possibilities for producing parts with complex geometries while maintaining the mechanical properties of spun metal.
Conclusion
Metal spinning is a time-tested manufacturing process that continues to evolve with advancements in technology, materials, and digitalization. Its ability to produce high-strength, seamless, and precise components makes it invaluable in industries such as aerospace, automotive, defense, and renewable energy.
One of the key advantages of metal spinning is its versatility. Whether used for prototyping custom parts or mass-producing high-volume components, metal spinning provides flexibility in both design and production. CNC spinning, in particular, has revolutionized the process by offering increased precision, consistency, and the ability to handle complex geometries that were once considered unfeasible.
At the same time, metal spinning faces certain challenges, such as material limitations and surface finish concerns. However, ongoing innovations—especially in automation, CNC technology, and AI—are addressing these issues, enabling manufacturers to push the boundaries of what is possible with spun metal parts. Additionally, the use of advanced materials like superalloys and titanium, coupled with new heat-assisted techniques, is expanding the range of applications in high-performance industries.
As the manufacturing world moves towards Industry 4.0, the role of real-time monitoring, predictive maintenance, and data analytics will continue to grow, enhancing the efficiency and reliability of metal spinning operations. The integration of additive manufacturing with metal spinning also opens new doors for hybrid processes, combining the strengths of 3D printing and traditional metal forming.
In conclusion, metal spinning remains a vital and evolving manufacturing process with a bright future. The ongoing development of new techniques, materials, and technologies will allow metal spinning to meet the demands of increasingly complex and high-performance applications, ensuring its continued relevance in modern manufacturing. As industries strive for more efficient, lightweight, and durable components, metal spinning is well-positioned to remain a cornerstone in the production of critical parts for years to come.
EMS Metalworking Machines
We design, manufacture and assembly metalworking machinery such as:
- Hydraulic transfer press
- Glass mosaic press
- Hydraulic deep drawing press
- Casting press
- Hydraulic cold forming press
- Hydroforming press
- Composite press
- Silicone rubber moulding press
- Brake pad press
- Melamine press
- SMC & BMC Press
- Labrotaroy press
- Edge cutting trimming machine
- Edge curling machine
- Trimming beading machine
- Trimming joggling machine
- Cookware production line
- Pipe bending machine
- Profile bending machine
- Bandsaw for metal
- Cylindrical welding machine
- Horizontal pres and cookware
- Kitchenware, hotelware
- Bakeware and cuttlery production machinery
as a complete line as well as an individual machine such as:
- Edge cutting trimming beading machines
- Polishing and grinding machines for pot and pans
- Hydraulic drawing presses
- Circle blanking machines
- Riveting machine
- Hole punching machines
- Press feeding machine
You can check our machinery at work at: EMS Metalworking Machinery – YouTube
Applications:
Flange-punching
Beading and ribbing
Flanging
Trimming
Curling
Lock-seaming
Ribbing